选矿过程中矿石的破碎与磨矿
破碎与磨矿(磨矿与分级)

补加钢球制度: 方法一:简单补球法 这也是最常用的一种补球方法,由于补加球是定 期地连续补加,故即使定期只补加一种大球,由 于磨损的原因也会使先后加入的球按顺序形成一 个自然的大小配比。初装球无论是加一种大球, 或是加多种混合球,经历一段时间后初装球必然 因磨损而自然消失,因此,磨内的球荷组成终究 是由补加球形成的。这样,就出现了初装球时装 多种球及补加时加一种大球的简单装补方法。
30 26 23 21
方法二:对待磨物料进行筛析分级,按矿 料的粒度组成确定初装球比。 具体做法是把待磨矿料筛析后分成粒度级 别窄的若干组(一般为3—5组),再分别 求出各组粒度需要的球径。 计算球径的公式有多个。
常用公式为
Db kd
式中:Db—所需的钢球尺寸; d—该粒级的平均粒度; k—比例系数,根据经验取值,取值 大小为2.5—130。
简单补球法的补加球量由钢耗量决定。 补加球量G=Q×W 式中 G—钢球补加量,kg; Q—前一天的矿石处理量,t; W—处理1t矿石的钢耗量,kg/t。 补球的频率一般为1天/次,也可以是1周/次。
方法二:精确化补球法 (1)对待磨矿料(包括新给矿及返砂)进行筛 析,确定待磨矿料的粒度组成,并将其进行分组。 (2)用公式计算最大球径及各组矿料所需的球 径。 (3)根据待磨矿料的粒度组成定出钢球的球荷 组成。方法是每种钢球的产率与适合它磨碎的矿 粒组产率大致相当,另外,还要根据磨矿的目的, 对需要加强磨碎的级别应在装球时增加其破碎概 率,对不需要破碎的级别减小其破碎概率。 补加球方案可以用作图法确定补加球。
2.确定初装球比 方法一:根据矿石的硬度、给料粒度、产 品粒度确定初装球比,具体参数见下表
把物料磨到0.2—0.3mm时的原始球荷
铝土矿选矿工艺流程

铝土矿选矿工艺流程铝土矿的选矿主要涉及矿石的破碎、磨矿、分选、选后处理等过程。
接下来,我们详细了解每一个步骤。
一、破碎选矿的第一步是破碎。
铝土矿的硬度较高,需要使用颚式破碎机、圆锥破碎机等设备进行初步破碎。
破碎的目的在于将大块的矿石破碎成小块,以便于后续的磨矿过程。
二、磨矿经过破碎后,矿石被送入磨矿阶段。
磨矿的目的是使矿石中的矿物颗粒达到适合分选的粒度。
通常使用球磨机、棒磨机等设备进行磨矿,以将矿石磨成粉末状。
磨矿过程中需添加水和化学药剂,以促进磨矿效率并方便后续的分选。
三、分选在经过破碎和磨矿后,矿石进入分选阶段。
这一阶段的目标是利用矿物间的物理化学性质差异,将有价值的矿物与脉石矿物分离。
分选的方法包括重力分选、浮选、磁选等。
重力分选:对于比重差异较大的矿物,可以利用不同比重矿物在水中的沉降速度不同来进行分离。
这种方法主要用于铝土矿中的铁矿物的分离。
浮选:这是铝土矿选矿中常用的方法。
主要利用铝土矿与脉石矿物的表面物理化学性质差异,通过添加特定的浮选药剂,使铝土矿颗粒附着在气泡上并浮到水面,从而达到分离的目的。
磁选:对于具有磁性的矿物,可以利用磁场将其从非磁性矿物中分离出来。
这种方法在铝土矿选矿中不常用,但如果矿石中含有磁铁矿物,就需要采用磁选法进行分离。
四、选后处理经过分选后,有价值的矿物得到富集。
此时需要进行脱水、脱泥、浓缩等处理,以提高矿物的品位并方便后续的加工利用。
这一阶段还涉及尾矿的处理和堆放,需要合理规划以减少对环境的影响。
总结:铝土矿的选矿工艺流程包括破碎、磨矿、分选和选后处理等步骤。
每个步骤都至关重要,需精心操作以确保获得高质量的铝土矿产品。
矿山矿石破碎与磨矿技术

分级:将磨好的粉末按粒度 大小进行分级
添加标题
浮选:利用浮选机将非铁矿 石中的非铁元素分离出来
过滤:将浓缩后的矿浆进行 过滤,得到干燥的矿粉
添加标题
添加标题
添加标题
添加标题
磨矿:将小颗粒矿石磨成更 细的粉末
添加标题
磁选:利用磁选机将铁矿石 中的铁元素分离出来
添加标题
干燥:将过滤后的矿粉进行 干燥,得到成品矿粉
降低能耗:采用节能型破碎与磨矿设备可以降低能耗,减少生产成本。
提高产品质量:采用先进的破碎与磨矿技术可以提高产品质量,提高产品附加值。
提高市场竞争力:采用先进的破碎与磨矿技术可以提高企业的市场竞争力,提高企业的经济效 益。
提高资源利用率,降低生产成本
提升产品质量,增强国际竞争力
添加标题
添加标题
添加标题
添加标题
促进相关产业发展,增加就业机会
推动科技进步,促进产业升级
汇报人:
磨矿:将小块矿石磨成细粉, 便于后续选矿
选矿:将磨矿后的细粉进行选 矿,提取有用矿物
冶炼:将选矿后的有用矿物进 行冶炼,制成金属产品
非金属矿石的筛分:将磨好的 粉末进行筛分,得到不同粒度 的产品
非金属矿石的磨矿:将小块矿 石磨成粉末,便于后续加工
非金属矿石的破碎:将大块矿 石破碎成小块,便于后续磨矿
安全可靠:采 用安全可靠的 设备和工艺, 保障生产安全
创新研发:加 强环保型破碎 与磨矿技术的 研发和创新, 推动行业的可
持续发展
PART SIX
减少能源消耗:采用节能型破 碎与磨矿设备,减少能源消耗, 降低生产成本。
提高生产效率:通过优化破碎 与磨矿技术,提高生产效率, 降低生产成本。
破碎与磨矿
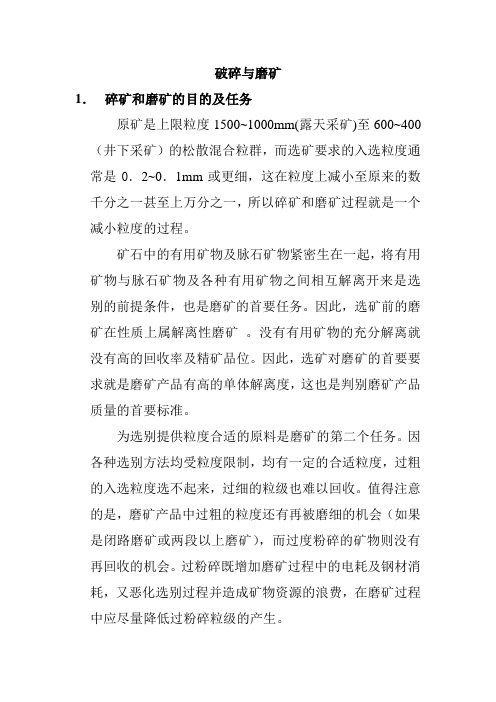
破碎与磨矿1.碎矿和磨矿的目的及任务原矿是上限粒度1500~1000mm(露天采矿)至600~400(井下采矿)的松散混合粒群,而选矿要求的入选粒度通常是0.2~0.1mm或更细,这在粒度上减小至原来的数千分之一甚至上万分之一,所以碎矿和磨矿过程就是一个减小粒度的过程。
矿石中的有用矿物及脉石矿物紧密生在一起,将有用矿物与脉石矿物及各种有用矿物之间相互解离开来是选别的前提条件,也是磨矿的首要任务。
因此,选矿前的磨矿在性质上属解离性磨矿。
没有有用矿物的充分解离就没有高的回收率及精矿品位。
因此,选矿对磨矿的首要要求就是磨矿产品有高的单体解离度,这也是判别磨矿产品质量的首要标准。
为选别提供粒度合适的原料是磨矿的第二个任务。
因各种选别方法均受粒度限制,均有一定的合适粒度,过粗的入选粒度选不起来,过细的粒级也难以回收。
值得注意的是,磨矿产品中过粗的粒度还有再被磨细的机会(如果是闭路磨矿或两段以上磨矿),而过度粉碎的矿物则没有再回收的机会。
过粉碎既增加磨矿过程中的电耗及钢材消耗,又恶化选别过程并造成矿物资源的浪费,在磨矿过程中应尽量降低过粉碎粒级的产生。
碎矿和磨矿的目的及任务是,使矿石中的有用矿物充分单体解离及粒度适合选别要求,并且过粉碎尽量轻,产品粒度均匀。
2.碎矿和磨矿的地位及重要性碎矿和磨矿是选矿厂的领头工序,选矿厂生产能力的大小实际上是由磨矿决定的。
选矿厂中的碎矿和磨矿的投资占全厂总投资的60 %左右,电耗也占选矿的50%~60%,生产经营费用也占选厂的40%以上。
磨矿作业产品质量的高低也直接影响着选矿指标的高低。
因此,碎矿和磨矿工段设计及操作的好坏,直接影响到选矿厂的技术经济指标,经济而合理的完成碎矿和磨矿的基本任务,是每个选矿工作者的职责。
碎矿和磨矿其阶段粒度划分大致是5mm, 碎矿的产品粒度大于5mm,而且破碎力以压碎为主。
磨矿的给矿粒度为5mm以下,以冲击及磨剥为主。
碎矿分粗碎、中碎及细碎,磨矿分为粗磨和细磨。
选矿厂流程
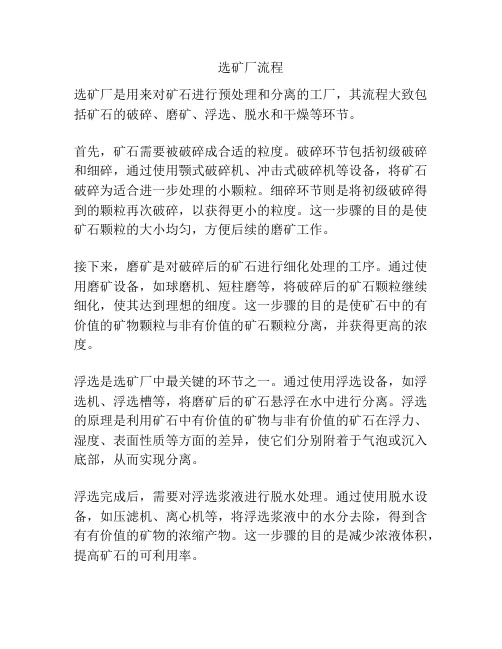
选矿厂流程选矿厂是用来对矿石进行预处理和分离的工厂,其流程大致包括矿石的破碎、磨矿、浮选、脱水和干燥等环节。
首先,矿石需要被破碎成合适的粒度。
破碎环节包括初级破碎和细碎,通过使用颚式破碎机、冲击式破碎机等设备,将矿石破碎为适合进一步处理的小颗粒。
细碎环节则是将初级破碎得到的颗粒再次破碎,以获得更小的粒度。
这一步骤的目的是使矿石颗粒的大小均匀,方便后续的磨矿工作。
接下来,磨矿是对破碎后的矿石进行细化处理的工序。
通过使用磨矿设备,如球磨机、短柱磨等,将破碎后的矿石颗粒继续细化,使其达到理想的细度。
这一步骤的目的是使矿石中的有价值的矿物颗粒与非有价值的矿石颗粒分离,并获得更高的浓度。
浮选是选矿厂中最关键的环节之一。
通过使用浮选设备,如浮选机、浮选槽等,将磨矿后的矿石悬浮在水中进行分离。
浮选的原理是利用矿石中有价值的矿物与非有价值的矿石在浮力、湿度、表面性质等方面的差异,使它们分别附着于气泡或沉入底部,从而实现分离。
浮选完成后,需要对浮选浆液进行脱水处理。
通过使用脱水设备,如压滤机、离心机等,将浮选浆液中的水分去除,得到含有有价值的矿物的浓缩产物。
这一步骤的目的是减少浓液体积,提高矿石的可利用率。
最后,脱水后的浓缩产物需要进行干燥,以降低其含水率。
通过使用干燥设备,如干燥机、闪蒸干燥器等,将浓缩产物进行热处理,使其含水率降低到可接受的水平。
这一步骤的目的是减少运输和储存过程中的能耗和成本。
选矿厂流程中的各个环节相互配合,协调运作,以达到对矿石进行高效预处理和分离的目的。
其中,磨矿和浮选是整个流程中的关键环节,对产品的质量和收益具有重要影响。
同时,脱水和干燥环节的优化也是提高工作效率和节约能源的重要措施。
通过不断探索和改进,选矿厂流程可以进一步提高整体效益,实现可持续发展。
选矿厂矿物的破碎、筛分、分级流程
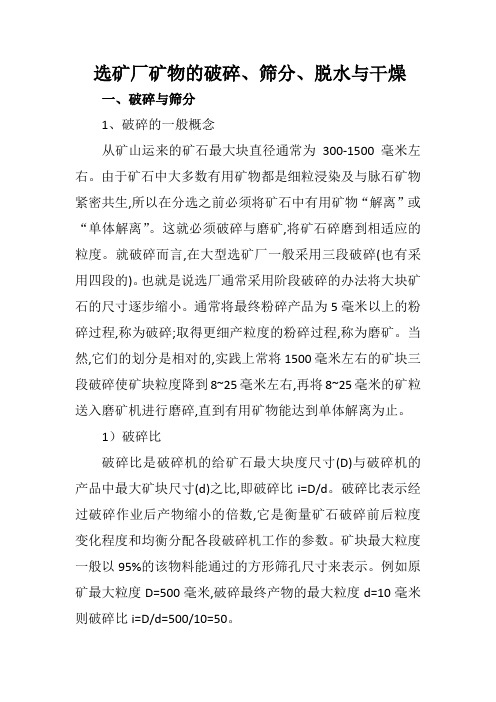
选矿厂矿物的破碎、筛分、脱水与干燥一、破碎与筛分1、破碎的一般概念从矿山运来的矿石最大块直径通常为300-1500毫米左右。
由于矿石中大多数有用矿物都是细粒浸染及与脉石矿物紧密共生,所以在分选之前必须将矿石中有用矿物“解离”或“单体解离”。
这就必须破碎与磨矿,将矿石碎磨到相适应的粒度。
就破碎而言,在大型选矿厂一般采用三段破碎(也有采用四段的)。
也就是说选厂通常采用阶段破碎的办法将大块矿石的尺寸逐步缩小。
通常将最终粉碎产品为5毫米以上的粉碎过程,称为破碎;取得更细产粒度的粉碎过程,称为磨矿。
当然,它们的划分是相对的,实践上常将1500毫米左右的矿块三段破碎使矿块粒度降到8~25毫米左右,再将8~25毫米的矿粒送入磨矿机进行磨碎,直到有用矿物能达到单体解离为止。
1)破碎比破碎比是破碎机的给矿石最大块度尺寸(D)与破碎机的产品中最大矿块尺寸(d)之比,即破碎比i=D/d。
破碎比表示经过破碎作业后产物缩小的倍数,它是衡量矿石破碎前后粒度变化程度和均衡分配各段破碎机工作的参数。
矿块最大粒度一般以95%的该物料能通过的方形筛孔尺寸来表示。
例如原矿最大粒度D=500毫米,破碎最终产物的最大粒度d=10毫米则破碎比i=D/d=500/10=50。
2)破碎段目前,任何一种常规破碎设备都难以达到50的破碎比。
因此,破碎过程通常需分段进行。
所谓破碎阶段的段数就是物料经过破碎的次数,在生产实践中,通常情况下采三段破碎,即谓粗碎、中碎、细碎。
粗碎、中碎、细碎又可分别称为第一段破碎、第二段破碎、第三段破碎。
段破碎的粒度范围如表11-1所示表11-1各破碎段粒度范围3)各段破碎比及其与总破碎比的关系各段破碎机给矿的最大粒度与排矿的最大粒度之比称为该段的破碎比。
作业总破石于各段破碎比的乘积。
如采用三段破碎,各段破碎比分别以il、i2、i3表示,则总破碎比i总=il*i2*i3。
一定的破碎设备,其破碎比范围固定。
因此,总破碎比往往决定了破碎段数。
选矿的流程

选矿的流程选矿是指通过一系列的物理和化学处理手段,将矿石中所含有用矿物分离出来,从而提高矿石的品位和回收率的过程。
这个过程被广泛应用于矿石的开采和矿石的后续加工过程中。
选矿的流程一般包括以下几个主要步骤:矿石的破碎、矿石的磨矿、矿石的浮选、矿石的筛选和矿石的尾矿处理。
首先,矿石的破碎是选矿过程的第一步。
矿石通常比较坚硬,需要通过破碎设备将其破碎成适当的大小。
破碎设备可以是颚式破碎机、圆锥破碎机等,其主要作用是将矿石从原始的大块变成小块,以便后续处理。
接下来,矿石的磨矿是选矿过程的第二步。
矿石经过破碎后,通常含有较高的杂质含量,需要进一步磨矿以提高矿石的品位。
磨矿设备一般采用球磨机、短轴搅拌磨等,通过磨矿设备的摩擦和冲击作用,使矿石中的杂质与有用矿物分离。
然后,矿石的浮选是选矿过程的核心步骤。
浮选是利用物理和化学方法,通过气泡和矿石颗粒之间的吸附和附着作用,选择性地将有用矿物提升到矿浆中的泡沫层上,从而实现矿石的分离。
浮选设备一般采用浮选机、浮选槽等,通过调整浮选剂的种类和浓度,控制气泡的大小和数量,可以实现矿石中有用矿物的高效分离。
接着,矿石的筛选是选矿过程的第四步。
筛选设备一般采用振动筛、离心筛等,通过分级和筛分作用,将矿石中的不同粒度的矿物分开。
这样可以有选择性地收集和处理特定粒度的有用矿物,从而提高矿石的回收率和品位。
最后,矿石的尾矿处理是选矿过程的最后一步。
尾矿处理是指对选矿过程中产生的废渣进行处理和利用,以减少环境污染和资源浪费。
目前常见的尾矿处理方法有干堆、砂浆填埋、尾矿综合利用等。
这些处理方法可以降低尾矿的含水率,减少尾矿的体积,并从中回收有用矿物,实现资源的循环利用。
综上所述,选矿的流程包括矿石的破碎、磨矿、浮选、筛选和尾矿处理等多个步骤。
通过这些步骤的组合和调整,可以高效地将矿石中的有用矿物分离出来,提高矿石的品位和回收率,为矿石的后续加工和利用奠定基础。
选矿技术的不断创新和发展,将进一步提高选矿的效率和环境友好性,促进矿产资源的可持续利用和利益最大化。
大冶铁矿选矿工艺流程

大冶铁矿选矿工艺流程大冶铁矿是中国重要的铁矿石资源之一,其选矿工艺流程对于提高矿石的品位和回收率至关重要。
本文将介绍大冶铁矿的选矿工艺流程,包括矿石的破碎、磨矿、磁选和浮选等环节。
一、矿石的破碎和磨矿大冶铁矿的矿石首先经过破碎环节,将其破碎成适当的粒度。
破碎后的矿石经过进一步的磨矿处理,以提高磨矿细度,为后续的磁选和浮选过程做好准备。
二、磁选磁选是大冶铁矿选矿的关键环节之一。
磁选主要通过磁性物质对矿石中的铁矿石进行分离,常用的磁选设备有湿式磁选机和干式磁选机。
矿石经过磁选后,磁性较强的铁矿石会被磁选机吸附,而非磁性的杂质则会被排除。
三、浮选浮选是将矿石中的有用矿物通过气泡的作用使其浮起,从而实现矿石的分离。
在大冶铁矿选矿中,浮选主要用于分离矿石中的硅酸盐矿物,如石英等。
浮选过程中,矿石首先经过粗浮选,将较粗的矿物浮起,然后通过细浮选进一步分离细粒度的矿物。
四、脱硫大冶铁矿中的矿石中常含有一定量的硫化物矿物,如黄铁矿等。
脱除硫化物矿物的目的是减少矿石中的硫含量,提高矿石的品位。
常用的脱硫方法有浮选法、氧化法和焙烧法等。
五、脱磷大冶铁矿中的矿石中也常含有一定量的磷酸盐矿物,如磷灰石等。
脱除磷酸盐矿物的目的是降低矿石中的磷含量,以满足冶炼的要求。
常用的脱磷方法有磷酸浸出法、化学浸出法和浮选法等。
六、尾矿处理选矿过程中产生的尾矿需要进行处理。
尾矿中常含有一定量的有价值的矿物,如铁矿石和硅酸盐矿物等。
通过合适的方法对尾矿进行处理,可以实现对有价值矿物的回收,提高资源利用率。
大冶铁矿的选矿工艺流程包括矿石的破碎、磨矿、磁选、浮选、脱硫、脱磷和尾矿处理等环节。
通过这些工艺,可以实现对矿石中的有用矿物的有效分离和回收,提高矿石的品位和回收率,最终为冶炼和利用提供高品质的铁矿石原料。
大冶铁矿选矿工艺的不断改进和优化,将进一步提高选矿效果,推动矿石资源的可持续利用。
选矿工艺流程

选矿工艺流程选矿工艺流程是指对矿石进行处理和分离的一系列工艺步骤。
选矿工艺流程的目的是通过物理、化学和机械方法,将矿石中的有用矿物从废石中分离出来,以提高矿石的品位和回收率。
一般来说,选矿工艺流程可以分为四个主要步骤:矿石破碎、矿石磨矿、矿石浮选和矿石脱水。
下面将详细介绍这些步骤。
首先是矿石破碎。
矿石通常是以较大的块状或颗粒状存在的,需要经过破碎过程将其破碎成适当的大小。
破碎的方法可以是机械式破碎、冲击破碎或者压碎等。
破碎后的矿石颗粒变得更小,便于后续的处理步骤。
接下来是矿石磨矿。
矿石磨矿是将矿石颗粒细化的过程。
通常采用磨矿机械设备,如球磨机、砂磨机等,对矿石进行磨矿处理。
磨矿的目的是使矿石颗粒更加细小,增加其与浮选剂的接触面积,提高浮选效果。
然后是矿石浮选。
矿石浮选是选矿过程中最重要的一步。
浮选是利用矿物与浮选剂的不同亲水性,通过气泡附着在矿石颗粒表面,使有用矿物颗粒浮起来,从而实现矿石的分离。
在浮选过程中,通常会添加浮选剂和调节剂,以改变矿石表面的性质,使矿物颗粒能够更好地被气泡附着。
最后是矿石脱水。
矿石脱水是将浮选后的矿石浆料中的水分去除的过程。
通常采用脱水设备,如压滤机、离心机等,对浮选浆料进行脱水处理。
脱水的目的是使浮选浆料中的水分减少,从而得到含水量较低的矿石产品。
除了这些主要步骤之外,选矿工艺流程还可能包括预处理、矿石干燥、矿石烧结等其他步骤,具体的工艺流程会根据矿石的性质和选矿目标而有所不同。
总的来说,选矿工艺流程是通过一系列的处理步骤将矿石中的有用矿物从废石中分离出来的过程。
这个过程包括矿石破碎、矿石磨矿、矿石浮选和矿石脱水等主要步骤。
通过合理设计和优化这些步骤,可以实现对矿石的高效处理和分离,提高矿石的品位和回收率,从而达到经济效益和环境保护的双重目标。
铜矿矿石的破碎与磨矿工艺

优化实践案例
某铜矿破碎工艺优化:采用高效破 碎机,提高破碎效率,降低能耗
某铜矿破碎与磨矿工艺联合优化:采 用先进的破碎与磨矿设备,实现破碎 与磨矿工艺的协同优化,提高生产效 率,降低能耗
半自磨机磨矿:利用矿石 和钢球的冲击和磨剥作用 进行磨矿
砾磨机磨矿:利用砾石的 冲击和磨剥作用进行磨矿
振动磨矿机磨矿:利用振 动产生的高频振动进行磨 矿
磨矿设备
自磨机:用于粗磨和细磨, 效率较高,但能耗较高
棒磨机:用于粗磨,效率较 低,但能耗较低
球磨机:用于粗磨和细磨, 效率高,能耗低
砾磨机:用于粗磨,效率较 高,但能耗较高
生产效率等
优化方案:根据 经济效益的比较 结果,选择最优 的破碎与磨矿工
艺方案
破碎与磨矿工艺 的优化
工艺优化的必要性
提高生产效率:优化工艺可以提高 破碎与磨矿的效率,降低生产成本。
降低能耗:优化工艺可以降低破碎 与磨矿过程中的能耗,减少环境污 染。
添加标题
添加标题
添加标题
添加标题
提高产品质量:优化工艺可以提高 铜矿矿石的品质,提高产品的市场 竞争力。
磨矿效果
磨矿细度:直接影响矿石的选别效果和 后续加工工艺
磨矿效率:影响生产效率和能耗
磨矿粒度分布:影响选别效果和后续加 工工艺
磨矿时间:影响生产效率和能耗 磨矿介质:影响磨矿效果和能耗 磨矿温度:影响磨矿效果和能耗
破碎与磨矿工艺 的比较与选择
工艺比较
选矿中磨矿和碎矿的作用
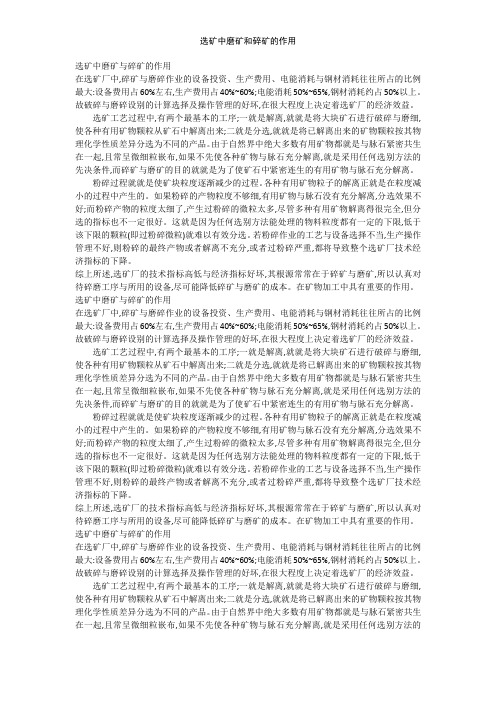
选矿中磨矿与碎矿的作用在选矿厂中,碎矿与磨碎作业的设备投资、生产费用、电能消耗与钢材消耗往往所占的比例最大:设备费用占60%左右,生产费用占40%~60%;电能消耗50%~65%,钢材消耗约占50%以上。
故破碎与磨碎设别的计算选择及操作管理的好坏,在很大程度上决定着选矿厂的经济效益。
选矿工艺过程中,有两个最基本的工序;一就是解离,就就是将大块矿石进行破碎与磨细,使各种有用矿物颗粒从矿石中解离出来;二就是分选,就就是将已解离出来的矿物颗粒按其物理化学性质差异分选为不同的产品。
由于自然界中绝大多数有用矿物都就是与脉石紧密共生在一起,且常呈微细粒嵌布,如果不先使各种矿物与脉石充分解离,就是采用任何选别方法的先决条件,而碎矿与磨矿的目的就就是为了使矿石中紧密连生的有用矿物与脉石充分解离。
粉碎过程就就是使矿块粒度逐渐减少的过程。
各种有用矿物粒子的解离正就是在粒度减小的过程中产生的。
如果粉碎的产物粒度不够细,有用矿物与脉石没有充分解离,分选效果不好;而粉碎产物的粒度太细了,产生过粉碎的微粒太多,尽管多种有用矿物解离得很完全,但分选的指标也不一定很好。
这就是因为任何选别方法能处理的物料粒度都有一定的下限,低于该下限的颗粒(即过粉碎微粒)就难以有效分选。
若粉碎作业的工艺与设备选择不当,生产操作管理不好,则粉碎的最终产物或者解离不充分,或者过粉碎严重,都将导致整个选矿厂技术经济指标的下降。
综上所述,选矿厂的技术指标高低与经济指标好坏,其根源常常在于碎矿与磨矿,所以认真对待碎磨工序与所用的设备,尽可能降低碎矿与磨矿的成本。
在矿物加工中具有重要的作用。
选矿中磨矿与碎矿的作用在选矿厂中,碎矿与磨碎作业的设备投资、生产费用、电能消耗与钢材消耗往往所占的比例最大:设备费用占60%左右,生产费用占40%~60%;电能消耗50%~65%,钢材消耗约占50%以上。
故破碎与磨碎设别的计算选择及操作管理的好坏,在很大程度上决定着选矿厂的经济效益。
矿石选矿设备工作流程
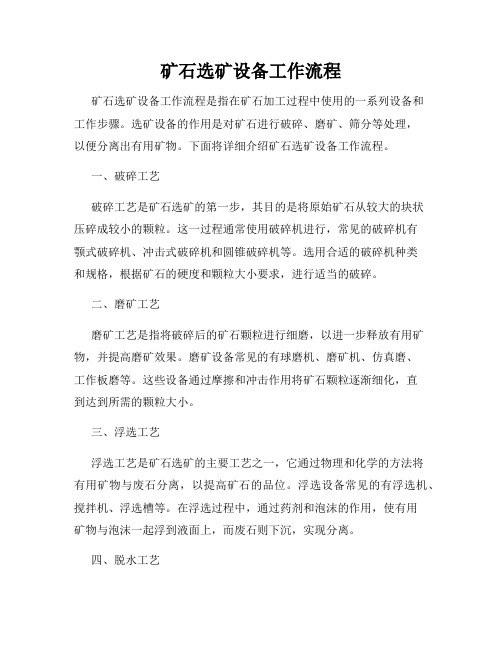
矿石选矿设备工作流程矿石选矿设备工作流程是指在矿石加工过程中使用的一系列设备和工作步骤。
选矿设备的作用是对矿石进行破碎、磨矿、筛分等处理,以便分离出有用矿物。
下面将详细介绍矿石选矿设备工作流程。
一、破碎工艺破碎工艺是矿石选矿的第一步,其目的是将原始矿石从较大的块状压碎成较小的颗粒。
这一过程通常使用破碎机进行,常见的破碎机有颚式破碎机、冲击式破碎机和圆锥破碎机等。
选用合适的破碎机种类和规格,根据矿石的硬度和颗粒大小要求,进行适当的破碎。
二、磨矿工艺磨矿工艺是指将破碎后的矿石颗粒进行细磨,以进一步释放有用矿物,并提高磨矿效果。
磨矿设备常见的有球磨机、磨矿机、仿真磨、工作板磨等。
这些设备通过摩擦和冲击作用将矿石颗粒逐渐细化,直到达到所需的颗粒大小。
三、浮选工艺浮选工艺是矿石选矿的主要工艺之一,它通过物理和化学的方法将有用矿物与废石分离,以提高矿石的品位。
浮选设备常见的有浮选机、搅拌机、浮选槽等。
在浮选过程中,通过药剂和泡沫的作用,使有用矿物与泡沫一起浮到液面上,而废石则下沉,实现分离。
四、脱水工艺脱水工艺是指将浮选后得到的浮选泥浆进行固液分离,以减少水分含量和提高产品的质量。
常见的脱水设备有压滤机、离心机、真空过滤机等。
这些设备通过压力、离心力或真空,将泥浆中的水分挤出,使得泥浆变得更干燥,方便后续处理和运输。
五、筛分工艺筛分工艺是指将磨矿和浮选过程中得到的矿石颗粒进行分级,以满足产品的粒度和品位要求。
常用的筛分设备有振动筛、鼓式筛、线性筛等。
这些设备通过筛网的振动、回转或线性移动,将矿石颗粒按照不同的大小分离出来,得到符合要求的产品。
六、制浆工艺制浆工艺是指将矿石颗粒与药剂进行混合,形成浓度适宜的矿浆,以便进行后续处理。
制浆设备主要有搅拌桶、混合机等。
在制浆过程中,矿石颗粒和药剂按照一定比例混合,形成稳定的浆料,以便于后续处理步骤的进行。
七、储运工艺储运工艺是指将选矿后的产品进行储存和运输。
这一过程通常需要使用储存设备和输送设备,如料仓、输送机和皮带输送机等。
采矿业中的矿石选矿与矿石加工

采矿业中的矿石选矿与矿石加工矿石选矿与矿石加工是采矿业中的重要环节,它们对于提取有用矿物和材料至关重要。
本文将探讨矿石选矿的过程和方法,以及矿石加工的技术和应用。
一、矿石选矿矿石选矿是指根据矿石的特性和属性,采用不同的方法将其中有用矿物与废石分离的过程。
这一过程通常包括矿石的破碎、磨矿、浮选、重选等步骤。
1. 矿石的破碎矿石破碎是将原始矿石从大块状变为相对较小的颗粒,以为后续的处理步骤提供条件。
常见的破碎设备有颚式破碎机、圆锥破碎机等。
2. 矿石的磨矿磨矿是将矿石细化为适当的颗粒大小,以便于浮选和重选等后续处理。
常见的磨矿设备有球磨机、矩形磨机等。
3. 矿石的浮选浮选是根据矿石的物理和化学特性,利用气泡将有用矿物浮出水面,而废石则下沉的过程。
浮选通常包括接触、吸附、浮起、分离等阶段。
4. 矿石的重选重选是对浮选尾矿进行进一步处理,进一步提高矿石中有用矿物的品位和回收率。
重选方式包括重力选矿、磁选、电选等。
二、矿石加工矿石加工是指将选矿后的矿石进行细化和加工,以满足不同的工业应用需求。
矿石加工涉及的技术和方法各异,根据矿石的性质和用途选择不同的加工方案。
1. 矿石烧结与熔炼矿石烧结与熔炼是将矿石加热至高温,使其中的有用矿物转化为金属或合金。
常见的矿石烧结与熔炼设备有高炉、电炉等。
2. 矿石的粉碎和精炼粉碎和精炼是将矿石进一步细化,以得到所需的细粉和纯度更高的矿石产品。
常见的设备有磨机、液固分离设备等。
3. 矿石的浸出和溶解浸出和溶解是将矿石中的有用矿物通过化学反应溶解出来,以得到目标金属或化合物。
浸出和溶解过程中需要使用化学试剂和设备。
4. 矿石的冶金处理冶金处理是将矿石中的有用金属进行进一步提纯和加工,以满足不同的工业需求。
常见的冶金处理技术包括电解、铸造、合金制备等。
总之,矿石选矿与矿石加工是采矿业中不可或缺的环节。
矿石选矿旨在将其中有用矿物与废石分离,而矿石加工则是将选矿后的矿石进行进一步细化和加工,以得到所需的金属和材料。
铁矿的选矿工艺

铁矿的选矿工艺铁矿是一种重要的矿石资源,广泛用于冶金、建筑、机械等行业。
然而,铁矿中常常含有其他杂质,如硅酸盐、硫化物等,需要通过选矿工艺进行提纯。
选矿工艺是指通过物理、化学等方法对矿石进行处理,使其达到冶金要求的工艺过程。
铁矿的选矿工艺主要包括矿石破碎、矿石磨矿、矿石脱泥、矿石浮选等环节。
首先,矿石破碎是将原始矿石分解成一定粒度的碎石,以便后续工艺的进行。
矿石破碎通常通过颚式破碎机、圆锥破碎机等设备完成,将矿石从大块破碎为小块。
接下来是矿石磨矿环节,即将破碎后的矿石细化至所需粒度。
矿石磨矿一般采用球磨机、砂石磨等设备,通过摩擦和撞击的作用,使矿石颗粒逐渐细化。
矿石磨矿的目的是增加矿石表面积,提高矿石与选矿药剂的接触面积,以便更好地进行后续工艺。
然后是矿石脱泥环节,即将矿石中的泥土、石灰石等杂质去除。
矿石脱泥一般采用湿式选矿方法,通过水的作用将泥土等杂质从矿石中分离出来。
脱泥设备常用的有螺旋分选机、湿选筛等。
矿石脱泥的目的是提高矿石的品位,减少后续工艺的能耗。
最后是矿石浮选环节,即通过选矿药剂的作用,使铁矿与其他杂质分离。
矿石浮选是一种重要的选矿方法,通过调整选矿药剂的种类和用量,使铁矿石与其他杂质的亲水性和疏水性差异达到分离的目的。
矿石浮选一般采用浮选机、磁选机等设备,将矿石浮选浓缩为铁精矿。
除了上述主要环节,铁矿选矿过程中还包括矿石预处理、尾矿处理等环节。
矿石预处理是指对原始矿石进行破碎、磨矿等处理,以提高选矿效果;尾矿处理是指对选矿过程中产生的废弃物进行处理,减少对环境的影响。
铁矿的选矿工艺是一个复杂的过程,需要根据矿石的特性、冶金要求等因素进行合理选择。
同时,选矿工艺也在不断创新和改进,以提高选矿效率、降低能耗和环境影响。
随着科学技术的进步,新的选矿工艺和设备不断涌现,为铁矿选矿提供了更多的选择。
铁矿的选矿工艺是提纯铁矿石的关键环节,通过矿石破碎、磨矿、脱泥、浮选等工艺,可以将铁矿与其他杂质分离,得到纯度较高的铁精矿。
采矿业中的矿石选矿与矿石加工

采矿业中的矿石选矿与矿石加工矿石选矿和矿石加工是采矿业中至关重要的环节。
通过对原矿石进行选矿处理和加工,可以提高矿石的品位和综合利用率,从而实现资源的最大化利用。
本文将重点讨论采矿业中的矿石选矿和矿石加工的过程和方法。
一、矿石的选矿过程1. 破碎和磨矿矿石进入选矿厂后,首先需要经过破碎和磨矿的过程。
通过破碎将较大的矿石分解成适当大小的颗粒,然后经过磨矿将颗粒细化,以便更好地进行后续处理。
2. 粗选在破碎和磨矿之后,矿石中的矿石矿物和废石矿物被分开。
这一步骤通常使用重介质分选法或浮选法,通过差异密度或浮力将矿石矿物与废石矿物进行分离。
3. 中选粗选之后,仍然有一部分的矿石矿物和废石矿物混合在一起。
为了进一步提高矿石品位,需要进行中选。
常用的中选方法包括磁选、重选和浮选等,通过这些方法可以将矿石中的有用矿物分离出来。
4. 精选精选是选矿过程中的最后一步,也是最关键的一步。
通过精选,可以将矿石中的有用矿物进一步提纯,得到更高品位的矿石。
精选方法有很多种,常见的有浮选、重选、磁选和电选等,根据不同矿石的特性选择合适的精选方法。
二、矿石的加工方法1. 冶炼在选矿过程中,通过精选得到的高品位矿石可以直接用于冶炼。
冶炼是将矿石中的金属矿物进行高温加热,使其熔化并进一步提炼出有用金属的过程。
冶炼方法有很多种,常见的有火法冶炼、电解法冶炼和湿法冶炼等。
2. 细化加工有些矿石在经过精选后只能得到含有金属矿物的浓缩物,需要进行进一步的细化加工才能得到有用金属。
细化加工的方法多种多样,包括高温烧结、浸出、化学还原、电解精炼等。
3. 考虑环境保护的加工方法随着对环境保护要求的提高,矿石加工中的环保问题也越来越受到重视。
目前,有很多新兴的环保型矿石加工技术出现,例如湿法氧化还原法、生物浸出法和微生物氧化法等,这些方法在矿石加工过程中能够有效减少对环境的污染。
三、矿石选矿与加工的意义1. 提高矿石的品位通过选矿和加工,可以将矿石中杂质和废石矿物去除,从而提高矿石的品位。
金矿选矿工艺流程

金矿选矿工艺流程1.矿石破碎:金矿选矿的第一步是将原材料矿石破碎成小颗粒。
这可以通过机械碎石机完成,将大块矿石压碎成较小的颗粒。
2.矿石磨矿:磨矿是将矿石颗粒进一步细化的过程。
矿石通常和水混合在球磨机中,通过摩擦和碰撞使矿石颗粒进一步细化。
3.矿浆分级:磨矿后的矿浆中颗粒大小不均匀,需要进行分级。
分级是通过不同大小的筛网过滤矿浆,将颗粒按照大小分为不同的等级。
4.选矿初步:分级后的矿浆进入浮选机或重选机,这是一种常用的选矿方法。
重选机通过震动将矿浆中的重金属颗粒沉降到底部,轻金属颗粒则浮在上方。
震动可以调整,以便根据金的重量将金颗粒与其他杂质颗粒分离开来。
5.浮选分离:浮选机操作时,通过利用矿物与油脂或其他化学药剂的亲油性或亲水性差异进行分离。
加入气泡和分散剂使有价金属与泡沫结合,从而产生浮力,使有价金属颗粒浮在上层,而不重要的矿物则沉入底层。
6.磁选:如果矿石中含有含铁的金属矿物,可以应用磁选工艺。
通过在磁场中通过矿浆,将带有铁矿的颗粒吸附在磁场中,从而将其分离出来。
7.热选:热选是一种用于分离矿石中含硫的金属矿物的方法。
将矿石加热到一定温度,将硫矿物进行氧化,产生二氧化硫气体,并使金属矿物颗粒更易于分离。
8.精矿生成:通过上述工艺步骤,我们将矿石中的金属颗粒从矿石中分离出来,并生成精矿。
精矿是含有较高金属含量的矿石,可以进行后续的提炼和冶炼,以获得纯金。
9.精矿处理:对生成的精矿进行进一步处理,以去除其中的杂质和无价金属。
这通常包括熔炼、电解、重熔和其他物理化学处理过程。
10.金属提取:最后一步是从精矿中提取金属。
常见的方法包括水浸法、化学溶解和电解。
根据不同的金属含量和纯度要求,选择合适的提取方法。
以上是金矿选矿工艺流程的一般步骤,实际操作时可能会因矿石性质和金属含量的不同而有所调整。
通过综合运用各种工艺方法,可以高效地从金矿中提取金属,并获得较高纯度的金属。
采矿工程中的矿石破碎与磨矿技术

采矿工程中的矿石破碎与磨矿技术矿石破碎与磨矿技术在采矿工程中起着至关重要的作用。
本文将介绍矿石破碎与磨矿的概念、作用和常用技术,并探讨其在采矿过程中的应用。
1. 矿石破碎技术矿石破碎是将原生态的矿石从原位中分离出来,并以适合后续处理工艺的粒度进行处理的过程。
其目的是将原生态的矿石转化为适合磨矿和选矿操作的细颗粒矿石。
矿石破碎技术的主要方法有物理方法和化学方法。
1.1 物理方法物理方法是指通过物理力学原理来进行石头的破碎。
常见的物理方法包括冲击式破碎机、压力式破碎机和剪切式破碎机。
冲击式破碎机适用于破碎脆性材料,将物料投入破碎室后由由高速旋转的锤头对物料进行冲击破碎。
压力式破碎机适用于破碎硬质材料,将物料放入破碎腔内,通过较大的应力将其破碎。
剪切式破碎机则适用于破碎中硬质材料,通过物料与一对旋转刀叶相对高速相对剪切来实现破碎。
1.2 化学方法化学方法主要是通过化学反应来改变矿石的物化性质,使其易于破碎。
常见的化学方法有氧化和还原。
氧化是将一些难以破碎的矿石经过氧化反应后,使其变得更脆性,易于破碎。
还原则是在矿石中添加还原剂,通过还原反应改变矿石的物性,使其更容易进行破碎。
2. 矿石磨矿技术矿石磨矿是指通过机械力学原理将破碎后的矿石颗粒继续细化,使其达到所需的粒度大小的工艺过程。
磨矿的主要目的是使矿石更易于选矿和提高选矿效果。
常用的磨矿设备包括球磨机和矿石磨机。
2.1 球磨机球磨机是一种广泛应用于磨矿工业的设备。
它主要通过转动的钢球和矿石之间产生的冲击和摩擦力来进行磨矿操作。
球磨机适用于各种硬度的矿石,具有磨矿效果好、能耗低、生产能力强等优点。
2.2 矿石磨机矿石磨机也是一种常见的磨矿设备,它通过转动的磨盘将矿石进行研磨。
矿石磨机适用于粘土矿石或其他较难破碎的矿石,具有磨矿效率高、选矿效果好等特点。
3. 矿石破碎与磨矿技术在采矿工程中的应用矿石破碎与磨矿技术在采矿工程中起着至关重要的作用。
首先,破碎与磨矿技术能够将原生态的矿石转化为适合选矿操作的细颗粒矿石,提高选矿效果。
- 1、下载文档前请自行甄别文档内容的完整性,平台不提供额外的编辑、内容补充、找答案等附加服务。
- 2、"仅部分预览"的文档,不可在线预览部分如存在完整性等问题,可反馈申请退款(可完整预览的文档不适用该条件!)。
- 3、如文档侵犯您的权益,请联系客服反馈,我们会尽快为您处理(人工客服工作时间:9:00-18:30)。
选矿过程中矿石的破碎与磨矿
选矿的前提条件是要使矿石中的有用矿物达到单体分离,由于有用矿物以单体存在的粒度是很小的,往往需要将矿石磨得很细,才能使某种有用矿物达到单体分离。
矿石的破碎和磨碎是选别前的准备作业。
耐磨钢球主要是用在选矿的磨矿阶段,将破碎后的矿石研磨成粉末。
从采场出来的矿石块度很大,如露采的供矿块度最大可达1000~1500毫米左右,所以要把大至1500毫米的矿块破碎到只有几十微米的细粒,往往要分几个阶段才能完成。
以破碎来说,在大型选厂一般采用粗、中、细三段破碎(也有采用四段的),使矿块的粒度逐渐缩小到8~25毫米左右,然后再送到磨矿机中进行研磨。
直到有用矿物颗粒能达到单体分离为止,磨矿通常是一段或两段,有时也可达三段。
破碎与磨矿的段数划分大致如表2—3所示。
选矿的目的是除去矿石中所含的大量脉石及有害元素,使有用矿物得到富集,或使共生的各种有用矿物彼此分离,得到一种或几种有用矿物的精矿产品,供下一步利用。
选矿对开发矿产,充分利用矿产资源有着十分重要的意义。
在重视专业技术和营销手段的今天,钢球销售人员对于基本的选矿知识应该要十分清楚,这样在与客户交谈时,才能显示自己的专业性,才会让客户更加认可。
开源耐磨公司十分重视对销售人员技术与专业知识的培训,用各种方式方法提高销售员开发矿山的能力。