转炉炼钢使用石灰石造渣的合理性和可行性
对石灰石在炼钢中应用的几点思考

218管理及其他M anagement and other对石灰石在炼钢中应用的几点思考郭 慧(山东钢铁集团日照有限公司,山东 日照 276800)摘 要:石灰炼钢的过程中会带走大量的物理热量,导致炼钢过程中能量损耗,同时还会释放大量的二氧化碳,造成环境污染问题。
采用石灰石替代石灰炼钢,再对炼钢工艺加以改造,不仅可以降低石灰造渣炼钢的综合成本和二氧化碳的排放,还能提高石灰的利用率及炼钢过程中的热效率。
从市场角度分析,石灰石替代石灰在炼钢中的应用还符合经济全球化背景下企业强化市场竞争力及可持续发展的需求。
基于石灰石在炼钢中的应用优势及其市场需求,本文第一部分介绍了石灰石炼钢工艺及其吸热情况;第二部分分析了石灰石转炉造渣的机理;第三部分探讨了石灰石在炼钢中的应用实践;第四部分讨论并分析石灰石在炼钢中的应用效果及其价值。
旨在为石灰石炼钢实践应用提供一些参考。
关键词:石灰石;炼钢;应用;思考中图分类号:TF702 文献标识码:A 文章编号:11-5004(2021)11-0218-2收稿日期:2021-06作者简介:郭慧,女,生于1986年,汉族,山东泰安人,硕士研究生,工程师,研究方向:钢铁冶金。
钢铁是一种应用及其广泛的材料。
根据世界钢铁协会的统计,全球2021年钢铁需量预计达到17.17亿吨,其中中国钢铁需求量最大。
同时,我国还是世界上钢铁生产量最大的国家。
钢铁生产作为高污染、高能耗的工业产业,生产排放的污染物类型较多,污染量巨大。
平均每年产生的二氧化硫占全国总量的7%,烟尘占全国总量的8%,粉尘占全国总量的15%,固废占全国总量的13%,废水占全国总量的8%。
此外,还包括烧结所产生的N 2、CO 2、CO、自由氧等。
这些污染物给生态环境造成了负担,加剧了全球温室效应的发展。
在全球钢铁需求背景下,中国作为世界上最大的钢铁生产国和消耗国,其生产工艺节能优化迫在眉睫。
研究石灰石在炼钢中的应用及其应用效果对促进国内传统炼钢行业向绿色化转型有着重要的意义。
氧气转炉用石灰石代替石灰造渣炼钢分析
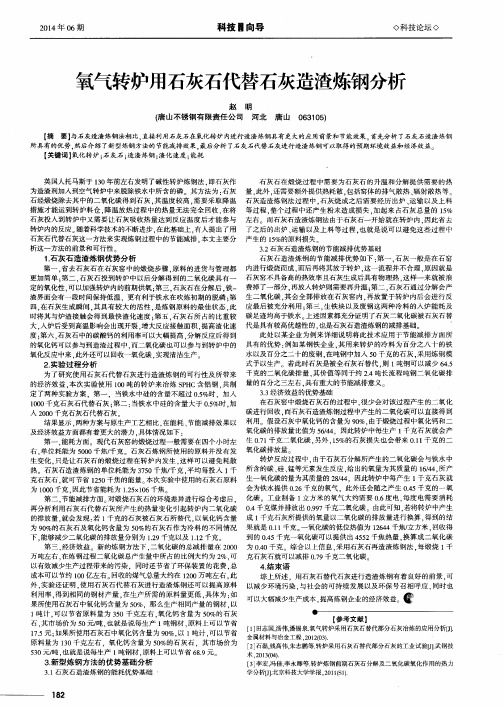
石 灰石在煅烧 过程 中需要 为石 灰石 的升温 和分解提供需要 的热 量, 此外 , 还需要额外提供热耗散 , 包括窑体的排气散热 、 辐射 散热等 。 石灰造渣炼钢法过程 中 . 石灰烧成 之后需要经历 出炉 、 运输 以及上料 等过程 . 量 的 1 5 % 左右 而石灰石造渣炼钢法 由于石灰石一开始就在转 炉内 . 因此省去
2 . 实验 过程 分 析 为 了研 究使用石 灰石代替石灰进行 造渣炼钢 的可行性及所带 来
的经济效益 . 本 次实验使用 1 0 0吨的转炉来 冶炼 S P H C含 铝钢 . 共 制 定 了两种实验方案 ,第一 .当铁水 中硅 的含量 不超过 0 . 5 %时 . 加 入 1 0 0 0 千克 石灰石代替石灰 : 第二: 当铁水 中硅的含量 大于 O . 5 %时 . 加 入2 0 0 0千克石灰石代替石灰 结果显示 , 两种方案与原生产工艺相 比, 在能耗 、 节能减排效 果以 及经济效益方 面都有着更大 的潜力 . 具体情况如下 : 第一 . 能耗方 面 现代石灰窑的煅烧过程一般需要在 四个小 时左 右, 单位耗能为 5 0 0 0千焦/ 千克 。石灰 石炼钢所使用 的原料并没 有发 生变化 . 只是让石灰石 的煅烧过程 在转炉 内发生 . 这样可 以避免 耗散 热 石灰石造渣炼钢 的单位耗能 为 3 7 5 0千焦/ 千克 . 平均每 投入 1 千 克石灰石 . 就可节 省 1 2 5 0千焦的能量 本次实验 中使用的石灰石原料 为1 0 0 0千克. 因此节省能耗 为 1 . 2 5 x 1 0 6千焦 第二 . 节能减排方 面 对锻烧石灰石 的环境差异进行综合考虑后 . 再分析利用石灰石 代替石灰所 产生的热量变化 引起转炉 内二氧化碳 的排 放量 , 就会 发现 : 若 1 千克 的石灰被石灰石所 替代 , 以氧化钙含量 为9 0 %的石灰 石及氧化钙含量为 5 0 %的石灰石 作为冷料 的不同情况 下. 能够 减少二 氧化碳 的排放量分别 为 1 . 2 9千克 以及 1 . 1 2千克 第三 . 经济效益 新 的炼 钢方法下 . 二氧化碳 的总减排 量在 2 0 0 0 万吨左右 . 在炼 钢过程二 氧化碳 总产 生量 中所 占的比例大约 为 2 %. 可 以有效减少 生产过程 带来 的污染 .同时还节省 了环保 装置的花费 . 总 成本可 以 节约 1 0 0 亿左右 回收 的煤气总量大约在 1 2 0 0 万吨左 右 此 外, 实验还证 明 . 使 用石灰石代 替石灰进行造 渣炼钢还可 以提高原料 利用率 . 得到相 同的钢材产量 , 在生产所需 的原料量更低 , 具 体为 : 如 果所使用石灰石中氧化钙含量为 5 0 %.那么生产相 同产量的钢材 . 以 1吨计 . 可以节省原料 量为 3 5 0千克左右 . 氧化钙含 量为 5 0 %的石 灰 石. 其市场价 为 5 0元, 吨. 也就是说每生产 1吨钢 材 . 原料上可 以节 省 1 7 . 5 元; 如果所使用石灰石中氧化钙含量为 9 0 %. 以1 吨计 . 可 以节省 原料量 为 1 3 0千克左右 ,氧化 钙含量为 5 0 %的石灰 石 .其市场价 为 5 3 0元/ 吨, 也就是说每生产 1 吨钢材 . 原料上可以节省 6 8 . 9 元
石灰石代替石灰在转炉炼钢中的应用实践分析

石灰石代替石灰在转炉炼钢中的应用实践分析近年来,在炼钢行业中发现,相比于传统模式中用石灰在转炉炼钢,利用石灰石代替石灰能够取得高效的炼钢质量和效率,降低石灰消耗量,进而降低炼钢成本,为企业获得更高收益。
文章就围绕石灰石代替石灰在转炉炼钢中的应用实践进行分析探究。
标签:石灰石;转炉炼钢;降温材料前言随着可持续发展战略的进一步加深,各行各业都越加重视能源节约问题,在炼钢生产领域,对于炼钢成本的控制也提出了更高的要求。
2013年,西钢炼钢厂率先选用石灰石代替石灰,投入到转炉炼钢生产当中,不但实现了转炉内多余热量的有效利用,而且起到较好的节能减耗效果,进一步提升了企业的经济收益。
1理论支撑1.1 石灰石代替石灰在现代炼钢行业当中,通常是选用石灰作为转炉炼钢的主要造渣材料,而石灰属于石灰石经过高温煅烧后形成的产物。
2013年,西岗炼钢厂通过技术革新,率先在转炉炼钢中直接投入石灰石,用石灰石取代石灰作为转炉炼钢材料工作,也就是将石灰石煅烧过程与转炉炼钢过程有效结合到一起,并取得不错效果。
究其本质原因,由于转炉在正常工作状态下,炉内温度通常会保持在1300℃与1400℃中间范围内,因此,将石灰石投入转炉后会直接受到的1300℃至1400℃的高温煅烧,瞬间升温会导致石灰石外表层的碳化钙会进行化学分解反应,这高温情况下,使得原本应需达到2-5小时的分解过程能够迅速完成。
1.2 利用石灰石降温在传统的炼钢领域中,除了转炉炼钢过程较长问题之外,还存在降温材料资源较少而且材料成本较高的问题,这同样严重阻碍了转炉炼钢工作的正常开展,各炼钢企业都在迫切尋求寻找成本较低、来源丰富且降温作用明显的新型材料,以解决现有的降温材料问题。
从理论角度来讲,石灰石在投入转炉后,会在高温煅烧情况下产生化学反应,生产氧化钙和大量的二氧化碳,在这过程中,会消耗大量的热能。
由此可见,将石灰石应用到转炉炼钢中,不但能够取代石灰满足转炉的碱性需求,另外还能够有效消耗转炉内多余的热能,起到降温材料所应当发挥的效果,进而降低用于降温的金属材料的用量,不但能够为企业大幅压缩用于降温材料的生产成本,还能够有效环节能源短缺问题,具有十分可靠的应用可行性[1]。
石灰石对转炉冶炼效果的影响

石灰石对转炉冶炼效果的影响摘要:在19世纪50年代,贝塞默最初提出了炼钢方法,为炼钢的发展奠定了基础。
经过几十年的炼钢技术的不断研究和发展,现代冶炼技术在早期边缘概念的基础上得到了创新和发展。
自20世纪以来,冶炼行业的不断进步和冶炼技术的不断发展,解决了早期想象中冶炼热量不足的问题,开辟了LD转炉冶炼,为冶炼技术的创新和发展提供了技术基础。
在此基础上,除转炉冶炼石灰石的特殊性质外,在转炉冶炼中加入石灰石替代传统冶炼材料,实现有效、安全、绿色的冶炼,在保证冶炼效率的同时保护环境。
因此,石灰石在转炉冶炼中的作用和影响值得我们关注和研究。
关键词:石灰石;转炉冶炼;影响引言在实验室条件下研究了转炉初渣中石灰石和石灰石的溶解。
结果表明,在1550℃时,石灰石与一些初始渣发生反应,初始渣仍为固相,不形成液相。
石灰石在转炉初渣中完全溶解,形成均匀的液态渣。
在工业试验中,分别考察了石灰石在转炉前、中、后期的熔融状态和除磷效果。
结果表明,初期形成的炉渣碱度转炉很低,约为1.5,吹渣碱度最终只能达到预期目标,前期除磷效果较差,但中后期有所改善,有利于保持稳定的脱磷效果。
一、传统转炉冶炼存在的问题传统的转炉冶炼由于内部温度不足,往往在转炉冶炼中加入石灰,以帮助采伐过程。
然而,随着时代的进步和冶炼需求的增加,传统的以石灰为主体的转炉冶炼方式暴露出许多弊端和问题。
(一)石灰产量供不应求石灰作为传统转炉冶炼的重要组成部分,在转炉冶炼中占有重要地位。
然而,由于社会各界对石灰的需求不断增加,石灰的生产已成为石灰供应不足的关键问题。
此外,我国石灰生产技术还存在不足,效率不高,不能满足社会对大量石灰的需求。
因此,由于上述原因,我国传统冶炼石灰供应不能满足需求,难以保证传统转炉冶炼的正常运行,不利于冶炼行业的长期发展。
(二)传统转炉冶炼环境污染严重采用石灰作为结渣剂,促进了传统的转炉冶炼。
但在冶炼过程中,由于石灰的特殊化学性质,容易产生有害气体,对人体和自然环境都会产生不利影响。
钙镁石灰石在转炉生产中的多方面应用研究
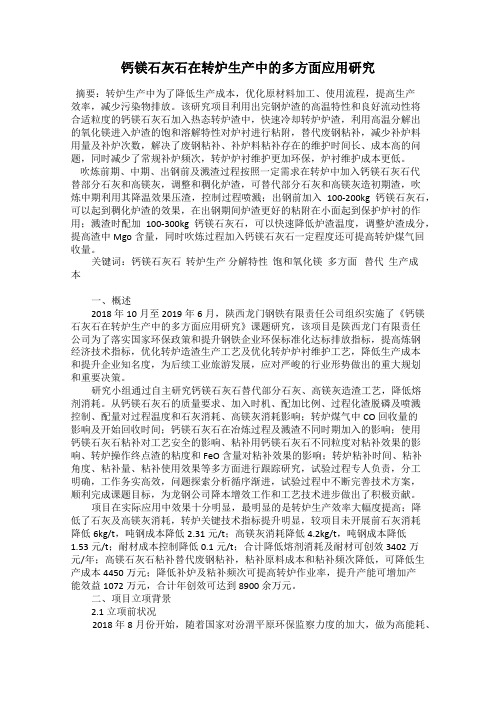
钙镁石灰石在转炉生产中的多方面应用研究摘要:转炉生产中为了降低生产成本,优化原材料加工、使用流程,提高生产效率,减少污染物排放。
该研究项目利用出完钢炉渣的高温特性和良好流动性将合适粒度的钙镁石灰石加入热态转炉渣中,快速冷却转炉炉渣,利用高温分解出的氧化镁进入炉渣的饱和溶解特性对炉衬进行粘附,替代废钢粘补,减少补炉料用量及补炉次数,解决了废钢粘补、补炉料粘补存在的维护时间长、成本高的问题,同时减少了常规补炉频次,转炉炉衬维护更加环保,炉衬维护成本更低。
吹炼前期、中期、出钢前及溅渣过程按照一定需求在转炉中加入钙镁石灰石代替部分石灰和高镁灰,调整和稠化炉渣,可替代部分石灰和高镁灰造初期渣,吹炼中期利用其降温效果压渣,控制过程喷溅;出钢前加入100-200kg钙镁石灰石,可以起到稠化炉渣的效果,在出钢期间炉渣更好的粘附在小面起到保护炉衬的作用;溅渣时配加100-300kg钙镁石灰石,可以快速降低炉渣温度,调整炉渣成分,提高渣中Mgo含量,同时吹炼过程加入钙镁石灰石一定程度还可提高转炉煤气回收量。
关键词:钙镁石灰石转炉生产分解特性饱和氧化镁多方面替代生产成本一、概述2018年10月至2019年6月,陕西龙门钢铁有限责任公司组织实施了《钙镁石灰石在转炉生产中的多方面应用研究》课题研究,该项目是陕西龙门有限责任公司为了落实国家环保政策和提升钢铁企业环保标准化达标排放指标,提高炼钢经济技术指标,优化转炉造渣生产工艺及优化转炉炉衬维护工艺,降低生产成本和提升企业知名度,为后续工业旅游发展,应对严峻的行业形势做出的重大规划和重要决策。
研究小组通过自主研究钙镁石灰石替代部分石灰、高镁灰造渣工艺,降低熔剂消耗。
从钙镁石灰石的质量要求、加入时机、配加比例、过程化渣脱磷及喷溅控制、配量对过程温度和石灰消耗、高镁灰消耗影响;转炉煤气中CO回收量的影响及开始回收时间;钙镁石灰石在冶炼过程及溅渣不同时期加入的影响;使用钙镁石灰石粘补对工艺安全的影响、粘补用钙镁石灰石不同粒度对粘补效果的影响、转炉操作终点渣的粘度和FeO含量对粘补效果的影响;转炉粘补时间、粘补角度、粘补量、粘补使用效果等多方面进行跟踪研究,试验过程专人负责,分工明确,工作务实高效,问题探索分析循序渐进,试验过程中不断完善技术方案,顺利完成课题目标,为龙钢公司降本增效工作和工艺技术进步做出了积极贡献。
关于石灰石在转炉炼钢中的应用实践研究
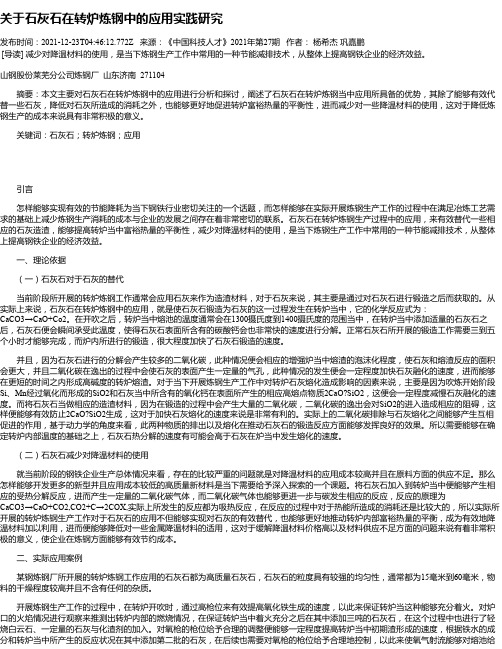
关于石灰石在转炉炼钢中的应用实践研究发布时间:2021-12-23T04:46:12.772Z 来源:《中国科技人才》2021年第27期作者:杨希杰巩嘉鹏[导读] 减少对降温材料的使用,是当下炼钢生产工作中常用的一种节能减排技术,从整体上提高钢铁企业的经济效益。
山钢股份莱芜分公司炼钢厂山东济南 271104摘要:本文主要对石灰石在转炉炼钢中的应用进行分析和探讨,阐述了石灰石在转炉炼钢当中应用所具备的优势,其除了能够有效代替一些石灰,降低对石灰所造成的消耗之外,也能够更好地促进转炉富裕热量的平衡性,进而减少对一些降温材料的使用,这对于降低炼钢生产的成本来说具有非常积极的意义。
关键词:石灰石;转炉炼钢;应用引言怎样能够实现有效的节能降耗为当下钢铁行业密切关注的一个话题,而怎样能够在实际开展炼钢生产工作的过程中在满足冶炼工艺需求的基础上减少炼钢生产消耗的成本与企业的发展之间存在着非常密切的联系。
石灰石在转炉炼钢生产过程中的应用,来有效替代一些相应的石灰造渣,能够提高转炉当中富裕热量的平衡性,减少对降温材料的使用,是当下炼钢生产工作中常用的一种节能减排技术,从整体上提高钢铁企业的经济效益。
一、理论依据(一)石灰石对于石灰的替代当前阶段所开展的转炉炼钢工作通常会应用石灰来作为造渣材料,对于石灰来说,其主要是通过对石灰石进行锻造之后而获取的。
从实际上来说,石灰石在转炉炼钢中的应用,就是使石灰石锻造为石灰的这一过程发生在转炉当中,它的化学反应式为:CaCO3→CaO+Co2。
在开吹之后,转炉当中熔池的温度通常会在1300摄氏度到1400摄氏度的范围当中,在转炉当中添加适量的石灰石之后,石灰石便会瞬间承受此温度,使得石灰石表面所含有的碳酸钙会也非常快的速度进行分解。
正常石灰石所开展的锻造工作需要三到五个小时才能够完成,而炉内所进行的锻造,很大程度加快了石灰石锻造的速度。
并且,因为石灰石进行的分解会产生较多的二氧化碳,此种情况便会相应的增强炉当中熔渣的泡沫化程度,使石灰和熔渣反应的面积会更大,并且二氧化碳在逸出的过程中会使石灰的表面产生一定量的气孔,此种情况的发生便会一定程度加快石灰融化的速度,进而能够在更短的时间之内形成高碱度的转炉熔渣。
石灰石在100吨转炉冶炼过程中的应用实践

1
前 言
石灰 石 的 主要Байду номын сангаас 分 是 C a C O , , 经 煅烧 分 解成
上单 位 质 量 的石 灰 石 将 分 解 出 5 6%的 C a O和
统计 和实 际应用 经验 得 出 , 转 炉使 用部 分石 灰石 替 代活 性石 灰炼 钢 。 有 利 于进 一步 降低 活性 石灰
消耗、 增 加转 炉煤 气生 产量 , 促 进转 炉炼 钢 生产 , 实 现稳定 、 高效 、 低耗、 节能 、 环保 。
水 钢科 技 S HU I G A NG S C I E N C E& T E C HN O L O GY
第1 4 2期
石灰石在 1 o o吨转炉 冶炼 过程 中的应 用实践
周玉杭
( 首钢 水钢 炼钢 厂 贵 州 六盘 水 5 5 3 0 2 8 )
摘
要: 阐 述 了 石灰 石 用 于 转 炉 生 产 的 优越 性 , 既 可 以 部 分 代 替 石 灰 减 少 石 灰 消耗 , 还 可 以平 衡
关键词 : 转炉 ; 石灰石 ; 成 本
Ap p l i c a t i o n P r a c t i c e o f L i me s t o n e i n S t e e l ma k i n g i n 1 0 0 T C o n v e r t e r
o n l y r e p l a c e a p a r t o f i l me S O a 8 t o r e d u c e l i me c o n s u mp i t o n b u t a l s o b a l a n c e o u t s u r p l u s h e a t S O a s
石灰石在转炉炼钢工艺上的应用

石灰石在转炉炼钢工艺上的应用张杰新阮铭重庆钢铁股份公司二炼钢厂1.前言提高生产工艺技术水平,降低生产成本,是目前产能过剩导致钢材价格低迷,钢铁企业处于微薄利润或亏损状态下须走的必经之路。
生产规模的降低,铁水消耗的升高,导致炉内热量富余加剧,为使用石灰石炼钢创造了条件。
使用石灰石炼钢不仅可以造渣,也可以达到平衡热量的目的,促使炼钢成本的降低。
2、可行性分析2.1使用石灰石的理论依据石灰石加入转炉后,其反应为[1]:CaCO3(s) =CaO(s)+CO2(g)△Gθ=169120-144.6T,J•mol−1 (1)由式(1)的热力学数据可知,在炼钢温度下,石灰石的分解属于自发反应△Gθ <0,且分解温度在900℃左右。
另外,石灰石分解产生的CO2 气体具有氧化性,可以与金属发生发应,其反应式为[2,3]:CO2(g)+Fe(l)=CO(g)+FeO(s)△Gθ =4343-13.653T,J•mol−1 (2)由式(2)的热力学数据可知,在炉内温度条件下,该反应可以自发进行△Gθ <0,其产物使渣中FeO 含量增加,有利于前期造渣脱磷。
石灰石加入炉内的反应过程①使原来在2个反应器中进行的反应在1个反应器里完成,因而减少了工序②石灰煅烧快速完成无功热耗散极小③分解出CO2与[M]反应生成CO可回收④转炉内生成石灰无须出炉转运不浪费其物理热⑤但转炉内需要增加热供给,以减少冷铁料加入维持热平衡为宜石灰石分解与煅烧时间的关系☐石灰石块在1400℃下的分解速度比1100℃大很多,1400℃下30mm左右的块度仅5分钟即可分解73.6 %。
如图1所示。
☐图1 分解率与煅烧时间的关系2.2生产条件要求☐石灰石的冷却效应是废钢的3.0-4.0倍[4],其分解需要吸收大量的热量,为此,热铁水消耗或铁水温度要高,以满足炉内热量平衡。
☐由于石灰石的表面比石灰硬,且石灰石在转炉内分解需要一定的时间,因此,入炉的石灰石的粒度最好在20-40mm之间。
转炉炼钢造渣材料结构优化探讨

转炉炼钢造渣材料结构优化探讨结合转炉炼钢造渣问题,文章提出利用石灰石、生白云石和磁选渣分别进行石灰、轻烧白云石和萤石等材料的替代,实现造渣材料结构优化。
从优化效果来看,可以提高脱磷率,并带来一定经济效益。
标签:转炉炼钢;造渣材料;磁选Abstract:In order to optimize the structure of slagging materials,limestone,raw dolomite and magnetic separation slag are used to replace lime,light burned dolomite and fluorite,respectively,according to the slagging problem of converter steelmaking. From the optimization effect,it can improve the dephosphorization rate,and bring some economic benefits.Keywords:converter steelmaking;slagging materials;magnetic separation引言伴随着国家节能减排政策的逐步落实,降本增效、节能生产的问题开始引起钢铁行业的重视。
在转炉炼钢造渣生产方面,为实现运营转型,还要实现造渣材料结构的优化,以便得到消耗更低的造渣方案。
因此,还应加强对转炉炼钢造渣材料结构优化问题的分析,从而为钢铁行业带来更多的效益。
1 转炉炼钢造渣问题分析在转炉炼钢方面,一般采用石灰进行造渣脱磷。
石灰需要通过在石灰窑中对石灰石进行高温煅烧获得,需要采用焦炭和煤作为燃料,得到的石灰拥有较高硫含量,容易吸水,难以保证活性度,同时也将产生较多的粉尘,无法满足低碳环保生产要求。
在转炉炼钢生产中,每吨钢需要消耗30-70kg石灰,达到40%-60%的脱磷效率,最终得到的炉渣脱磷能力依然较高,导致炼钢渣量过多,炉渣铁损过大。
石灰石在炼钢工业中的应用

石灰石在炼钢工业中的应用前言石灰是转炉炼钢的主要造渣剂,它是由石灰石在一定条件下烧制而成。
而石灰石(CaCO3)既是石灰(CaO)的提供者,也是CO2气体的直接携带者,在炼钢领域应用价值不言而喻。
近年来,为降低转炉炼钢成本,减少活性石灰断供对生产的影响,实现二氧化碳减排等目的,鞍钢、邯钢、宝钢湛江等各大钢厂均试验过石灰石造渣工艺。
据研究成果来看,石灰石部分代替石灰炼钢的效果和节能减排所产生的经济价值是十分值得肯定的。
01石灰石炼钢工艺石灰石炼钢工艺是从石灰造渣炼钢工艺升级而来。
石灰石炼钢工艺,是指直接将石灰石投入转炉内集中反应,利用石灰石表层碳酸钙分解作用吸收转炉内温度并对转炉内外进行降温,辅助炼钢生产的过程。
据季德静研究表明,石灰石替代部分石灰冶炼可满足脱磷的要求,可降低氧气消耗量,可提高吨钢煤气回收量,缩短冶炼周期。
02石灰石在炼钢工业中的应用2.1在铁水预处理中的应用炼钢过程中需要通过搅拌来加速渣钢的反应,也改善夹杂物上浮问题。
采用石灰石替代石灰作为溶剂炼钢,石灰石表层的碳酸钙在分解过程中强烈的化学反应产生的二氧化碳气体能够形成气体搅拌作用。
而且,二氧化碳代替价格较高的氩气搅拌铁水,直接降低了炼钢成本。
另外,CaCO3密度比CaO大,向钢水喷吹过程中CaCO3粒子容易穿入钢液,混合更加均匀。
2.2在顶底复合吹炼中的应用与采用石灰冶炼相比,加入石灰石渣量减少,生产成本明显降低。
秦登平研究显示,在保证脱磷率的前提下,石灰石造渣工艺总体入炉CaO量减少28.6%,吨钢造渣物料加入量减少,直接减少吨钢转炉渣量,有利于降低成本和节能减排。
从原理上看,是对氧化钙进行精炼。
在炼钢过程中将煅烧石灰石的温度升高到高于石灰石分解的温度,以此保持或提升氧化钙的活性。
新产生的氧化钙暴露在反应最前端,能在较短的时间内快速地完成石灰溶解造渣,实现钢铁精炼和脱硫的作用。
这就是石灰石在炼钢中能够减少废渣的排量的重要因素之一。
石灰石加入转炉造渣炼钢过程的行为初探

石灰石加入转炉造渣炼钢过程的行为初探李自权李宏郭洛方严鹏程(北京科技大学冶金与生态工程学院,北京,100083)董大西梁孜王恭亮张红卫李胜利(石家庄钢铁有限责任公司,石家庄,050031)摘要:本文结合实验室和工业试验的数据,讨论了转炉炼钢用石灰石代替石灰造渣过程中石灰石的行为,结果认为,转炉炼钢前期直接加入石灰石做造渣原料,可以很快完成煅烧化渣过程,并且在某些方面比使用石灰有利;用石灰石造渣能够达到希望的结果,石灰石分解大概在5~6分钟内完成;高温有利于碳酸钙的快速分解,1400℃与1100℃相比,虽然温度只差300℃,分解率大3~4倍,因此分解化渣与前期温度密切相关。
关键字:转炉炼钢石灰石分解造渣温度Primary research on the behavior of limestone charged into converter during making slag processLI Zi-quan,LI hong,GUO Luo-fang,YAN Peng-cheng(School of Metallurgical and Ecological Engineering, University of Science and Technology Beijing, Beijing100083, China)DONG Da-xi,LIANG Zi,WANG Gong-liang,ZHANG Hong-wei,LI Sheng-li(Shijiazhuang Iron Steel Co.,Ltd.,Shijiazhuang 050031,Hebei,China)Abstract:The behavior of limestone which is utilized for slagging instead of lime during converter steelmaking process was discussed with the data collected from laboratorial and industrial. The result can be concluded that: limestone which is directly charged into converter as slag-forming material during early period of steelmaking process can be quickly decomposed and participate in making slag, in addition, it has more advantages over lime in several respects; the anticipant result can be got using limestone to make slag, and limestone is completely decomposed during 5~6 minutes in converter steelmaking process; high temperature is propitious to calcium carbonate decomposing, just as the result of laboratory experiments shows that the decomposition rate of CaCO3 at 1400℃is 3~4 times greater than that at 1100℃in spite of only 300℃difference, therefore, the early period temperature has a great effect on the decomposition and slagging processes.Key words: steelmaking in BOF limestone decomposing slag making temperature 北京科技大学提出了一种新的炼钢方法[1],用石灰石代替石灰加入转炉造渣炼钢,已在国内两个钢铁公司进行工业试验取得了成功,这一方法是对氧气转炉炼钢工艺的大变革,在低碳炼钢节能减排方面具有重要的意义[2,3]。
石灰石代替石灰在转炉炼钢中的应用实践

当前 钢铁 企 业 生 产 中 , 普 遍 存 在 着 降 温 材 料 成 本高 昂且 原 料 短 缺 问题 。如 何 开 发 出新 的 , 价
1 理 论 依 据
1 .1 石灰石 替代 石灰 的应 用
格 低廉且 具 良好 降 温效 果 的新 材 料 , 成 为 降 低 炼
n 0耽 i x i n
( X i l i n I r o n& S t e e l C o . L t d ., Y i c h u n , H e i l o n g j i a n g , 1 5 3 0 2 5 C h i n a )
Abs t r a c t: Th e e ne r g y c o n s u mp t i o n a n d c h a r a c t e r i s t i c s o f t h e p r o c e s s o f t h e r ma l d e c o mp o s i t i o n r e a c t i o n we r e a n a l y z e d wh e n t h e l i me s t o ne wa s a d d e d t o t h e e o n v e r t e r s l a g a n d t h e de c o mpo s i t i o n pr o c e s s h a p—
降温料的使用量 , 为炼钢生产节约了成本 , 创造 了更大利润空间。
关键 词 : 转炉 ; 石 灰 石 ;成 本
Li me s t o ne i ns t e a d o f l i me u s i n g i n c o n v e r t e r s t e e l ma k i n g p r a c t i c e
转炉石灰石代替石灰造渣炼钢研究现状及展望

转炉石灰石代替石灰造渣炼钢研究现状及展望摘要:钢铁行业作为重要的基础产业,其生产过程中能源消耗大、环境污染严重。
为实现可持续发展,石灰石替代石灰在转炉炼钢中的应用逐渐受到关注。
本文从石灰石替代石灰的基本原理、炼钢过程中的作用、实验研究与技术创新、以及未来发展趋势等方面进行了详细论述。
结论指出,石灰石替代石灰在转炉炼钢中具有显著的优势和广阔的发展前景,是推动钢铁行业可持续发展和环境友好转型的重要技术创新。
关键词:石灰石;石灰;转炉炼钢;替代;可持续发展;环境友好一、引言随着全球工业化进程的加速,钢铁作为基础建设和制造业的关键材料,需求量逐年上升。
转炉炼钢法是目前钢铁生产中最为广泛采用的方法之一,由于其较高的生产效率和较低的成本,深受钢铁企业的青睐。
然而,在传统的转炉炼钢法中,石灰作为造渣剂的使用,不仅会带来能源消耗与成本问题,还会对环境产生一定的负面影响。
因此,研究石灰的替代品成为了业界关注的焦点。
在这一背景下,石灰石作为石灰的一种替代品,逐渐引起了学者和工程师们的关注。
石灰石与石灰在化学成分上有一定的相似性,但石灰石的价格更低、资源更丰富,这使得石灰石在转炉炼钢中的应用具有很大的潜力。
然而,由于石灰石的物理性质与石灰有所差异,如何在保证钢铁生产质量和效率的前提下,实现石灰石在转炉炼钢中的替代,仍是一个亟待解决的问题。
本文旨在分析石灰石在转炉炼钢中替代石灰的研究现状,并探讨其环境、经济和技术方面的前景。
首先,通过对比石灰与石灰石的化学成分、物理性质和反应机理,阐述石灰石替代石灰的可能性与挑战。
其次,对现有的实验研究与技术创新进行分析,总结石灰石替代石灰的关键技术与优化措施。
然后,从环境与可持续性的角度,评估石灰石替代石灰对碳排放、渣的回收与再利用等方面的影响。
最后,对石灰石替代石灰的经济效益进行分析,展望其在钢铁市场中的应用前景与潜力。
二、石灰石替代石灰的优势在深入了解了石灰石与石灰的化学成分、物理性质和反应机理的差异之后。
氧气转炉用石灰石代替石灰造渣炼钢
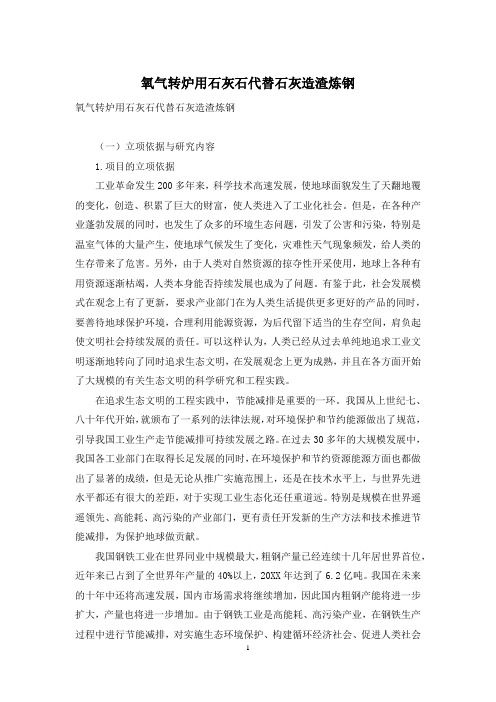
氧气转炉用石灰石代替石灰造渣炼钢氧气转炉用石灰石代替石灰造渣炼钢(一)立项依据与研究内容1.项目的立项依据工业革命发生200多年来,科学技术高速发展,使地球面貌发生了天翻地覆的变化,创造、积累了巨大的财富,使人类进入了工业化社会。
但是,在各种产业蓬勃发展的同时,也发生了众多的环境生态问题,引发了公害和污染,特别是温室气体的大量产生,使地球气候发生了变化,灾难性天气现象频发,给人类的生存带来了危害。
另外,由于人类对自然资源的掠夺性开采使用,地球上各种有用资源逐渐枯竭,人类本身能否持续发展也成为了问题。
有鉴于此,社会发展模式在观念上有了更新,要求产业部门在为人类生活提供更多更好的产品的同时,要善待地球保护环境,合理利用能源资源,为后代留下适当的生存空间,肩负起使文明社会持续发展的责任。
可以这样认为,人类已经从过去单纯地追求工业文明逐渐地转向了同时追求生态文明,在发展观念上更为成熟,并且在各方面开始了大规模的有关生态文明的科学研究和工程实践。
在追求生态文明的工程实践中,节能减排是重要的一环。
我国从上世纪七、八十年代开始,就颁布了一系列的法律法规,对环境保护和节约能源做出了规范,引导我国工业生产走节能减排可持续发展之路。
在过去30多年的大规模发展中,我国各工业部门在取得长足发展的同时,在环境保护和节约资源能源方面也都做出了显著的成绩,但是无论从推广实施范围上,还是在技术水平上,与世界先进水平都还有很大的差距,对于实现工业生态化还任重道远。
特别是规模在世界遥遥领先、高能耗、高污染的产业部门,更有责任开发新的生产方法和技术推进节能减排,为保护地球做贡献。
我国钢铁工业在世界同业中规模最大,粗钢产量已经连续十几年居世界首位,近年来已占到了全世界年产量的40%以上,20XX年达到了6.2亿吨。
我国在未来的十年中还将高速发展,国内市场需求将继续增加,因此国内粗钢产能将进一步扩大,产量也将进一步增加。
由于钢铁工业是高能耗、高污染产业,在钢铁生产过程中进行节能减排,对实施生态环境保护、构建循环经济社会、促进人类社会可持续发展都有重要的意义。
回转窑生产转炉炼钢用高质量石灰的研究

回转窑生产转炉炼钢用高质量石灰的研究摘要:随着钢铁质量和产量的持续提升,炼钢过程中对于石灰质量的要求也在持续提升,在这种情况下,活性石灰被广泛应用于炼铁过程中。
基于此,本文对活性石灰特性及在炼钢中的作用进行了分析,阐述了活性石灰的煅烧机理,总结了国内外先进石灰窑型的生产特点及炼钢用石灰质量的提高途径,加深企业对“活性石灰”的认识,为冶金企业建设“活性石灰”生产线起到良好的借鉴和参考作用。
关键词:活性石灰;特性及作用;煅烧机理;石灰窑引言冶金石灰作为炼钢用的“造渣剂”,它的重要性已逐步得到人们的重视和认知。
它不仅影响着钢水的冶炼过程,还直接影响钢水的最终质量。
国际上已广泛采用品质好、反应快、造渣彻底的优质“活性石灰”取代过去使用的“普通石灰”为冶炼优质钢水奠定了基础。
活性石灰的应用,加快了冶炼造渣速度、缩短了冶炼时间、降低了吨钢石灰消耗、减少了杂质带入、大大提高了钢水的质量,给企业带来了显著的综合效益,在钢铁行业已形成共识。
20年代末至今,国内各大钢铁企业,纷纷建设一流活性石灰生产线,石灰窑配套的主体设施均采用引进或消化外来技术自行建造,石灰产品质量明显优于传统式窑生产的产品。
所以活性石灰的应用正成为大趋势在飞速普及发展。
1.活性石灰特性及在炼钢中的作用1.1活性石灰的特性活性石灰是一种化学性能活泼、反应能力强,在炼钢造渣过程中熔解速度快,含 S、P 等有害元素少的优质软烧石灰。
它的质量优劣主要采用“活性度”这一指标来衡量。
活性度体现了石灰在熔渣中与其它物质的反应能力,表观现象为石灰在熔渣中的熔化速度。
由于直接在钢水中测定较困难,所以一般以测试石灰在水中的反应速度来代替,即以石灰水活性来表示。
活性度的测试方法为:取50g 试样,与水混匀成饱和溶液再加入酚酞试剂后呈粉红色,再用浓度为4N( 摩尔) 的 HCl( 盐酸) 在40℃±1℃的环境温度下,连续10min( 分钟) 滴定,彻底中和后滴入HCl 的毫升数( 滴定值) 即为“活性度”值。
石灰石在炼钢中的作用

非金属料一、造渣材料1.石灰炼钢对石灰的要求:◆Ca0含量高,Si02和S含量尽可能低。
Si02消耗石灰中的Ca0,降低石灰的有效Ca0含量;S能进入钢中,增加炼钢脱硫负担。
◆应具有合适的块度。
转炉石灰的块度以5~40mm为宜;电炉石灰的化学成分及块度要求见表7—5。
表7—5 电炉石灰的成分及块度要求石灰块度过大,石灰熔化缓慢,不能及时成渣并发挥作用;块度过小或粉末过多,容易被炉气带走,还会降低电炉砖砌炉盖的使用寿命。
◆烧减率控制在合适的范围内(4%~7%)。
◆活性度高。
活性度是衡量石灰与炉渣的反应能力,即石灰在炉渣中溶解速度的指标。
活性度高,则石灰熔化快,成渣迅速,反应能力强。
石灰石的煅烧过程:◆选择优质石灰石原料,低硫、低灰分燃料。
◆合适的煅烧温度。
煅烧温度控制在1050~11500C的范围。
◆先进的煅烧设备,如回转窑、气烧窑等。
根据煅烧温度和时间的不同,石灰可分以下几种:◆生烧石灰。
煅烧温度过低或煅烧时间过短,含有较多未分解的CaC03的石灰称为生烧石灰;◆过烧石灰。
煅烧温度过高或煅烧时间过长而获得的晶粒大、气孔率低以及体积密度大的石灰称为过烧石灰;◆软烧石灰。
煅烧温度在1100℃左右而获得的晶粒小、气孔率高、体积密度小、反应能力高的石灰称为软烧石灰或活性石灰。
生烧和过烧石灰的反应性差,成渣也慢。
活性石灰是优质冶金石灰,它有利于提高炼钢生产能力,减少造渣材料消耗,提高脱磷、脱硫效果并能减少炉内热量消耗。
2.萤石萤石的特征:◆主要成分为CaF2。
◆熔点很低(约930℃)。
◆改善碱性熔渣流动性且又不降低碱度的稀释剂,又称助熔造渣剂。
◆增强渣钢间的界面反应能力。
◆大量使用萤石会增加转炉喷溅,加剧对炉衬的侵蚀。
炼钢使用的萤石要求:◆CaF2的含量越高越好,而Si02的含量要适当,其他杂质如S、Fe等含量要尽量低。
◆块度要合适,并且干燥清洁。
冶炼优质钢用的萤石使用前要在60~100℃低温下烘烤8h以上。
转炉应用石灰石炼钢技术实践

转炉应用石灰石炼钢技术实践标签:转炉炼钢;炼钢技术;石灰石;转炉技术引言转炉炼钢过程所依靠的主要材料就是石灰,而石灰是我们日常随处可见的石灰石所炼制而来的。
然而随着科技应用的进步,石灰石的使用范围越来越大,所以现在石灰石正面临着资源枯竭的危机。
也就是现在的转炉炼钢过程成本增加,从而威胁到现在的钢铁企业生存。
幸运的是各大炼钢厂,都在近期完成了对新型石灰石工艺的研制,使得现在的石灰成本得到下降。
根据研究表明,现在的钢铁业市场比以往已经高出了20%的经济效益。
1利用石灰石代替石灰造渣的概述在使用造渣进行工业生产的时候,主要是防止金属液内部混有P和S这两种元素。
可以保证钢铁容器内部的流动性以及酸碱度。
在快速形成炉渣这一方面我们应该注意温度的考量以及对渣化的紧急控制,一旦出现转换现象,就要立刻进行添加剂,防止渣化退去。
温度的控制是炼钢过程最重要的一环,通过控制温度可以提升钢材质量,保证炼钢过程的稳定进行。
但是每种钢的温度控制都不一样,因此也需要根据每个钢的特点来进行准确的温度控制。
并且为了更好的应用炼钢过程中产生出的其他热量,就要通过添加适量的降温物质类似于铁矿石等等,确定钢材的余热被充分利用。
石灰石的主要成分为CaCOa,煅烧成为石灰的温度一般在1000~1200℃。
因此,烧成的石灰携带了较多的热能,高温石灰必须降温后才能运输,通过皮带到达转炉料仓进入转炉时己接近常温,然后石灰在转炉中再吸热升温化渣。
很明显,这一过程石灰先降温再升温存在能量浪费。
而公司受入炉冷料不足的影响,冶炼过程存在较高的富裕热量,大量的矿石需要在冶炼后期加入,过程存在回收率低、成本高的现象。
石灰石中CaCOa含有44%质量的C02,在炼钢前期,这部分C02受热分解出来后,可以与lFe]、[si]、[Mn]、[c]等发生氧化反应,起到良好的助熔搅拌作用,并且符合转炉低温、高碱度脱磷的相关条件。
2转炉应用石灰石炼钢技术实践探讨2.1炼钢造渣工艺原理转炉炼钢过程中主要工艺操作之一就是造渣工艺。
氧气转炉使用石灰石造渣炼钢.ppt

2019/11/26
12
3.研究结果与讨论
2019/11/26
13
迄今为止进行的主要研究工作
石灰石全部代替石灰造渣炼钢的可能性探讨 石灰石急速煅烧过程探索 铁水表面PCO2与低温高碳铁水平衡关系的推导 石灰石直接装入造渣炼钢工业试验结果 转炉内石灰石化渣过程探讨 两种方法煅烧石灰的能耗比较 用铁水替代废钢减排CO2量的计算 石灰石造渣炼钢法减排CO2的综合效益
2019/11/26
7
2.3石灰石具有氧化性更符合炼钢原理
炼钢是一个氧化熔炼的过程,生产中需强制供
氧吹炼。石灰石中CaCO3含有44%质量的CO2, 在炼钢前期,这部分CO2分解出来后可以与Fe、 [Si]、[Mn]、[C]等发生氧化反应,对炼钢过程 强化冶炼减少氧气消耗是有利的。但是(完全
烧成的)石灰中已没有CO2,不具有氧化性, 因此炼钢过程中直接加入具有氧化性的石灰石
4Hale Waihona Puke 2. 基本原理2019/11/26
5
2.1消除降温—升温的能量浪费
石灰石煅烧成为石灰的温度一般在1000~1200 ℃, 因此烧成石灰都携带较多的热能,但高温石灰必 须降温后才能运输,到达转炉料仓及至进入转炉 时已接近常温,然后石灰在转炉中再吸热升温化 渣,最后出钢时温度要达1600 ℃以上。很明显, 这一过程中石灰先降温再升温是在浪费能量,本 方法把石灰煅烧直接放在转炉中进行,从而消除 了这一浪费。
2019/11/26
6
2.2减少石灰资源浪费
- 1、下载文档前请自行甄别文档内容的完整性,平台不提供额外的编辑、内容补充、找答案等附加服务。
- 2、"仅部分预览"的文档,不可在线预览部分如存在完整性等问题,可反馈申请退款(可完整预览的文档不适用该条件!)。
- 3、如文档侵犯您的权益,请联系客服反馈,我们会尽快为您处理(人工客服工作时间:9:00-18:30)。
转炉炼钢使用石灰石造渣的合理性和可行性
任云婵
(河钢宣钢一钢轧厂,河北张家口
075100)
摘
要:近几年,我国炼钢工作受到了广泛重视,为了有效提升产量减少炼钢成本,多数部门会将石灰石直接投
入转炉,以取代原有生石灰的作用,能进一步顺应减排环保的管理需求。
文章分析了炼钢渣中石灰的作用和基本应用要求进行了分析,集中阐释了转炉炼钢使用石灰石造渣的合理性和可行性,仅供参考。
关键词:转炉炼钢;石灰石;造渣;合理性;可行性
作者简介:任云婵(1980-),女,河北张家口人,工程师,研究方向:炼钢。
Metallurgy and materials
1炼钢渣中石灰的作用和基本要求
1.1炼钢渣中石灰的作用
在炼钢工作开始后,要结合实际应用要求和管控要
点完善相应工作,确保能提升不同物质的应用价值和综合水平。
最关键的是,要在氧气转炉炼钢的过程中集中对各个物质进行综合监督,尤其是铁水中的硒元素、锰元素以及磷元素等都会被氧气直接作用形成对应的氧化物,这些氧化物本身就呈现出微酸性,因此,此时加入微碱性的物质就能进行化学中和。
生石灰是较为廉价且来源广泛的碱性物质,其中氧化钙的含量超过90%,因此,炼钢沼渣材料中生石灰不可获取。
而对于钢
水物质而言,尤其要减少磷元素和硫元素,以避免对环境造成严重的危害,就会借助碱性的氧化钙完成对应的反应,保证氧化钙和五氧化二磷能形成化学反应生成复合氧化物被有效保留在钢渣中。
另外,钢水中还存在硫元素和氧化钙形成硫化钙的情况,为了有效完善脱磷和脱硫处理,石灰的加入量要得到有效的约束和控制,一般保证氧化钙和二氧化硅的比例在3.0~3.5之间即可。
1.2炼钢渣中石灰应用的基本要求
在早期的炼钢管理工作中,一般会选取一些竖窑中
煅烧工艺残留的石灰作为处理药品,但是,因为竖窑本身存在气流分布不均匀的问题,这就是的局部温度会出现增高的现象,最关键的是,欠烧和过烧问题都较为严重。
要想从根本上保证石灰石能充分分解,就要结合煅烧工艺进行综合处理,有效保证石灰的活性和成渣效率。
基于此,从上世纪70年代开始,平炉炼钢工艺逐渐没落,利用氧气顶吹转炉炼钢法处理方式能有效替代传统工艺体系,且能有效缩短原有平炉法炼钢的时间。
在技术不断发展的背景下,对石灰成渣的速度及反应活性就提出了更高的要求,尤其是活性石灰的应用。
相关研究人员对实际应用过程进行了集中分析,判定石灰的活性与石灰石煅烧温度之间有着较为紧密的
联系,在活性石灰生产的过程中,石灰石在700~900℃间进行预热处理,然后集中利用1100~1200℃的温度环境完成快速煅烧,具体时间要结合设备进行判定。
目前,多数处理方式都会采取回转窑或者是套筒窑进行,保证了产量的基础上也对质量予以良好的约束和管理。
结合我国冶金行业管理制度和相关要求可知,在冶金石灰管理项目中,要依据相关标准进行质量监管,达到一级标准的石灰活性度要控制在320mL 以上,并且活性度能有效反映石灰在熔渣中的快速溶解能力。
需要指出的是,相关人员不能借助简单的方式直接对社会熔渣中的融化能力进行测定和分析,工业上一般会利用测定石灰在水中消化速度的方式完成相应的工作。
基于此,多数操作处理部门会借助冶金石灰物理检验方法进行综合监督和管理,也就是说,要完善对应的石灰物理检验操作,才能投入使用,具体的操作流程如下:①保证新烧石灰破碎筛分过程中,能对1~5mm 的试样进行筛分控制,取50g ;②向其最终加入2000nL 水,并且添加酚酞试剂,完成对应的消化处理工作;③利用浓度为4N 的稀盐酸溶液进行处理,在39~41℃的环境中进行连续滴定处理;④滴定过程一般为10min ,消耗的稀盐酸要按照毫升数进行综合监管,有效对活性度指标数值予以系统化判定。
依据相应试验完成后可获得活性石灰,其中氧化钙的晶粒较为细小,并且因为二氧化碳会从石灰石晶体结构中逸出,因此会留下较多的微气孔,无论是气孔率还是比表面积都能满足相应的应用要求。
值得一提的是,较好的活性石灰要满足具体参数要求,首先,体积密度要在1.5~1.7g/cm 3。
其次,气孔率要在50%以上。
再次,比表面积要在1.5~2.0m 2/kg ,且结晶较
为细小。
最后,活性度要在300mL 以上。
2转炉炼钢使用石灰石造渣的合理性和可行性
在全面分析了转炉炼钢使用石灰石造渣要求和具
176
第2期
(上接第175页)波形图中不规则冲击的频率加剧明显,同时冲击幅值上升较快,静态分析中的“RMS”,“Crest Factor”数值出现大幅跃升。
振动分析发现解调谱“D谱”中线性谱中水平方向的1X幅值最大值为
3.49g。
综合超声分析及振动分析得出结论:电机驱动端轴承中度磨损。
通知运行DCS监盘人员及专业人员密切关注轴承温度及电机电流等参数的变化。
3.5轴承故障发展第四阶段
超声波动态分析表明该阶段电机驱动端轴承时域波形图中的不规则冲击转变成周期为0.0319s的规律性冲击,电机周围伴随有异常响声。
振动分析发现解调谱“D谱”中线性谱水平方向的1X、2X幅值大幅跃升,最大值为17.97g,解调波形“DW”中振动冲击值高达131.95g。
电机驱动端轴承劣化严重,轴承重度磨损,通过下达设备预警通知单,要求电气专业停止风机电机运行进行解体检修。
3.6一次风机电机轴承电腐蚀原因分析和解决方案
一次风机电机轴承解体后发现,电机前、后轴承均出现较严重的电腐蚀,滚柱体、深沟球轴承内、外圈均存在凹凸不平的灰黑色斑痕,滚柱、滚珠表面也呈现为灰黑色,轴承保持架磨损严重并垮塌,轴承游隙过大。
电机尾轴的风扇叶轮由于振动大出现松动,导致前面第四阶段超声分析中的出现规则性冲击。
该电机在变频改造后,电机端电压高次谐波分量大幅增加,电源三相输出电压的矢量和不为零,产生零序电压分量(共模电压),通过定子铁芯和定子线圈之间的杂散电容,在定子铁芯上产生电位,转子是通过联轴器和风机相连并可靠接地,这样定子铁芯的电位和转子电位就有差异形成电位差即轴电压,使轴承局部烧熔,被烧熔的轴承合金在碾压力的作用下飞溅,于是在轴承内表面上烧出小凹坑从而造成轴承电腐蚀。
原因查明后,电气专业提出通过更换电机前后轴为绝缘轴承或电机轴颈上安装碳刷并可靠接地将轴电流导入大地两种解决方案。
4结语
在对转机设备进行健康工况评估时,要综合超声检测和振动频谱分析等技术手段,相互验证,在长期的数据监测条件下建立单一设备的趋势跟踪和同类设备的对比分析,不能用一种恒定不变的标准去判定不同类型,不同厂家的设备而忽视设备的差异化,在设备缺陷的查找和处理时一定要对症下药,做到标本兼治。
参考文献
[1]王维,冷祥洪,胡庆军.变频电机轴电流产生因素分析及对策[J].电气传动,2017,(6):11-12.
[2]王孚懋,任勇生,韩宝坤.机械振动与噪声分析基础[M].
北京:国防工业出版社,2006.
体应用要点后,就要结合实际工艺流程判定相应理论推导过程的合理性和实际操作的可行性,从而实现技术的大范围推广,提升相应工序的时效性,真正发挥技术优势的同时,提升炼钢工作的环保价值和经济效益。
一般而言,借助石灰石代替活性石灰进行炼钢和传统的工艺存在较大的差异,这种操作机制中要求石灰是能瞬时进入到1350~1500℃的环境中,就会马上形成升温分解,转变为石灰形态。
(1)在应用石灰石替代石灰的过程中,煅烧过程就已经转移到了转炉设备中,形成碳酸钙分解为氧化钙和二氧化碳。
石灰石加入转炉煅烧过程需要较高的热量,因此,炉内的热平衡就会受到影响,石灰石的额外热量不仅涉及石灰石升温过程中吸收的热量,也包括石灰石分级过程中吸收的热量,而在现代化的氧气转炉设备中,本身就是负能炼钢,这就使得热量较为富余,这部分能量正适宜抵消石灰石代替石灰进行炼钢造成的额外热量支出,能有效提升相应的处理工序和管理效率。
最关键的是,吸热比值能被控制在一定的数据范围内,提升了操作工序的合理性和综合价值。
基于此,石灰石的分解反应较为关键,本身会产生较多的二氧化碳,能有效助力逸出过程形成石灰表面的气孔,对于后续形成熔渣具有较为突出的作用,所以在转炉炼钢工序中应用石灰石代替石灰具有一定的合理性。
灰石煅烧,活性度能维持在320mL以上,这就使得相应物质的质量标准能满足要求。
并且在1200~1500℃石灰石的转化率本身就会随着温度升高而升高,煅烧时间的增长必然会增加转化率,甚至趋近100%。
因此,转炉炼钢使用石灰石造渣能在减少降温材料使用量的同时,保证脱磷效果满足安全管理的标准要求,整体管控结构较为便利,也能维护产量和基础质量,转炉炼钢使用石灰石造渣具有可行性。
3结语
总而言之,在低碳经济不断发展进步的时代背景下,转炉炼钢使用石灰石造渣能顺应环保要求,具有一定的合理性和可行性,能在降低炼钢成本的同时,真正打造节能减排的管理工序,因此,全面推广应用具有较好的前景,为进一步实现相应工作的全面发展,技术部门也要对技术予以多元化升级改良。
参考文献
[1]茹继龙.氧气转炉炼钢用石灰石代替石灰节能减排初探[J].南方农机,2018,(11):47.
[2]张小伟,虎晓东,王攀峰,等.新造渣模式下转炉炼钢成渣路线的研究[J].现代冶金,2018,(5):32-34.
[3]李晨晓,郝华强,王书桓,等.唐钢60t转炉石灰石替代部分石灰造渣炼钢的工业试验[J].特殊钢,2017,(6):16-18.
177。