铜氧化矿的鼓风炉还原熔炼
多枪顶吹连续吹炼炉高浓度富氧炼铜生产工艺

多枪顶吹连续吹炼炉高浓度富氧炼铜生产工艺
多枪顶吹连续吹炼炉高浓度富氧炼铜生产工艺是一种现代化的铜矿冶炼工艺,主要包括以下步骤:
1. 矿石破碎和浸出:将铜矿石经过破碎和浸出处理,将铜含量较高的矿石得到提取出来。
2. 富氧化:将得到的矿石放入多枪顶吹连续吹炼炉中,通过高浓度富氧对矿石进行氧化处理,将铜矿石中的硫化铜转化为氧化铜。
3. 炉内反应:在炼炉内进行高温反应,将氧化铜和其他杂质分离出来,得到纯净的铜水。
4. 熔炼和精炼:将得到的铜水进行进一步的熔炼和精炼处理,以提高铜的纯度。
5. 铜的成品生产:最终得到的纯净铜液可用于生产各种铜制品,如铜管、铜板等。
这种工艺具有高效、节能、环保等优点,被广泛应用于现代铜矿冶炼生产中。
铜冶炼的分类与方法
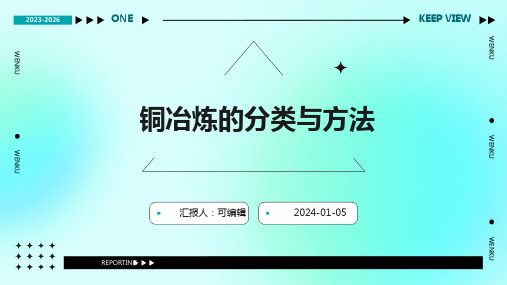
湿法冶铜
湿法冶铜是利用化学反应将铜 从矿石中提取出来的方法。
该方法适用于处理氧化铜和硫 化铜矿石,通过添加适当的还 原剂和调整溶液的酸碱度,使 铜离子还原为金属铜。
湿法冶铜的环境污染较小,但 出法和氯化浸出 法等。
电积法
电积法是利用电解的方法将 铜从溶液中提取出来的方法
固体废物处理
废物分类
对铜冶炼过程中产生的固体废物进行分类收集和处理,根据废物 的性质和来源进行分类。
资源化利用
对有价值的固体废物进行资源化利用,如回收重金属、生产建筑 材料等。
安全处置
对无利用价值的固体废物进行安全处置,如填埋、焚烧等,确保 不会对环境和人体健康造成危害。
PART 05
铜冶炼的技术发展与趋势
直接炼铜法
直接炼铜技术
通过直接利用某些矿物原料或工业废物,不经中间环节直接 提取铜的方法。例如,硫化铜精矿的直接酸浸出提取铜、含 铜废料的直接利用等。
生物炼铜技术
利用微生物浸出提取铜的方法,具有环保、低成本和资源利 用率高等优点。
PART 03
铜冶炼的工艺流程
铜精矿的准备
原料来源
01
铜精矿主要来源于矿山开采,经过选矿得到品位较高的铜矿石
。
1
该方法适用于处理含铜溶液 ,如硫酸铜溶液、氯化铜溶 液等,通过电解使铜离子在
阴极还原为金属铜。
电积法的环境污染较小,但 需要消耗大量的电能和酸碱 ,生产成本较高。
常见的电积法工艺包括硫酸 盐电积法和氯化物电积法等 。
PART 02
铜冶炼的方法
传统炼铜法
火法炼铜
利用高温还原铜矿石中的铜,主要流 程包括采矿、选矿、熔炼、吹炼和粗 铜火法精炼等。
新材料和新技术的应用将推动铜冶炼行业的科技创新和技术进步,促进产业升级 和转型,实现更加高效、环保、可持续的生产方式。
铜冶炼高砷烟尘浸出渣鼓风炉熔炼烟气治理环保工艺探索及生产实践

炉主要处置铜冶炼烟尘湿法处理后产生的浸出渣。 为使烟气得到彻底治理,薪冶公司采用重力除尘 - 电收尘 - 动力波除尘 - 氨法除尘脱硫四级环保除尘 脱硫系统,此除尘系统是目前国内罕见的烟气治理 工艺。 2 鼓风炉工艺流程 2 1 原料主要成分 薪冶公司处理的铜冶炼烟尘浸出渣组分见表 1 。
表2 干法除尘烟灰成分 元素 含量 / % P b 2 2 0 0 C u 2 4 7 B i 1 8 4 A s 2 6 6 1 Z n 6 7 9 C d 2 5 2
4 1 2 湿法除尘 由于烟气中部分的砷及少量的铅、硫等易挥发元 素难以用干法去除,因此第三级设置湿法洗涤器。烟 气湿法除尘设备采用湍流逆喷旋液塔,此设备是一种 新型气体净化设备,属动力波设备改进型。烟气由电 除尘器进入引风机,加压进入湍流逆喷旋液塔洗涤 器,烟气中的细小烟尘及砷尘被酸性洗涤液洗涤进入 液相;烟气温度由 1 2 0 ~ 2 8 0℃降至约 5 5 ℃。 湍流逆喷旋液塔的吸收原理为:在湍流逆喷旋 液塔逆喷管内,烟气从顶部进入,与下部旋流喷入 的吸收液逆向碰撞接触,形成了持续不断的高湍流 泡沫区,该泡沫区内液体表面以极快的速率更新, 在液沫面气体中的烟尘被洗涤进入液体,从而被捕 集下来。逆喷管内气液混合物落入塔体下部循环槽 内,由于气速降低,液滴落入下部槽体,所收集的 洗涤液经循环泵返回逆喷头,进行循环吸收。气体 通过槽体上部排出。 烟气经洗涤塔除尘后进入第二级湿法除尘设备 —填料塔,填料塔设有液相移热设备板式换热器, 烟气与冷洗涤液在填料中接触降温,温度由 5 5 ℃ 降温至 4 2 ℃左右进入一级脱硫塔。 4 1 3 烟尘调浆 洗涤塔洗涤循环泵分流部分洗涤液至斜管沉降 — 8 2—
李龙仙 ( 昆明西科工贸有限公司,云南 昆明 6 5 0 1 0 2 ) 摘 要:对鼓风炉烟气特性进行分析,通过采用重力除尘 - 电收尘 - 动力波湿法除尘 - 氨法脱硫工艺 及环保设施进行收尘、脱硫,有效消除了对环境的污染,使鼓风炉烟气排放满足 《 铅、锌工业污染物排 放标准》 ( G B 2 5 4 6 6- 2 0 1 0 ) 的要求。 关键词:鼓风炉烟气;重力沉降;电收尘;动力波;氨法除硫;实践 中图分类号:X 7 5 1 文献标识码:A 文章编号: 1 6 7 3- 9 6 5 5( 2 0 1 4 )0 2- 0 0 8 1- 0 4
密闭鼓风炉富氧熔炼

新 疆 有 色 金 属
1 3 7
密闭鼓风炉富氧熔炼
吴 建 军
( 新疆众鑫矿业股份有限责任公 司 哈密 8 3 9 0 0 0 )
摘 要 关 键 词 本 文介绍了众鑫镍冶炼厂密闭鼓风炉 富氧熔炼前后 炉况 出现的变化和渣型的调整。 密 闭鼓 风炉 富氧熔炼 床能率 本床 精矿 渣 型 金 属回收率
项目 N i C u F e
工艺依据质检部 的各家精矿化验单数据 , 进行 分析 、 对 比。根据众鑫鼓风炉的特性进行配料 , 把易 熔 和难熔精矿 以一定 比例 , 进行混合 , 调配处适合众 鑫矿业鼓风炉的混合精矿 。表 2 为混合后精矿化验 结果。
表 2 混合后精矿化验结果表
合亚克斯采、 选厂, 收购周边选厂的镍精矿产品, 为 型的目的, 就是尽量降低渣含金属, 提高金属回收
卧式转炉吹炼 , 产品为水淬金属化高冰镍。众鑫 2 生产原料
冶炼厂于 2 0 0 7 年5 月投产 , 当年 投 产 即打 通 生 产 工
艺, 产 出合 格产品 。当时鼓风炉是空气熔炼 。空气 熔炼造成鼓风炉床能率低下 , 前、 本床温度低 。金属 产 品 产 量 偏 低 。随 着 周 边 选 厂 的增 加 和 扩产 , 镍精 矿产 品供应量大于众鑫熔炼要求 。在这种情况下公
和鑫
镜儿泉
5 . 2 9
O . 8 3 0 . 2 4 9 4 2 . 0 2 2 8 . 1 2 6 . 8 2
1 . 3 8
4 . 1 9
2 。 3 原料的物理特性 这五家精矿 , 都是 细粉状 矿 , 色泽 灰 、 黑。其 中 四家含水分一般都 在 1 3 %~ 1 4 . 5 %之 间 , 只有详论精 矿最湿 , 含水分 2 4 . 7 %。 2 . 4 精 矿 配料 和调 配后 的精 矿成 分
鼓风炉富氧熔炼炼铜

铜氧化矿的鼓风炉还原熔炼
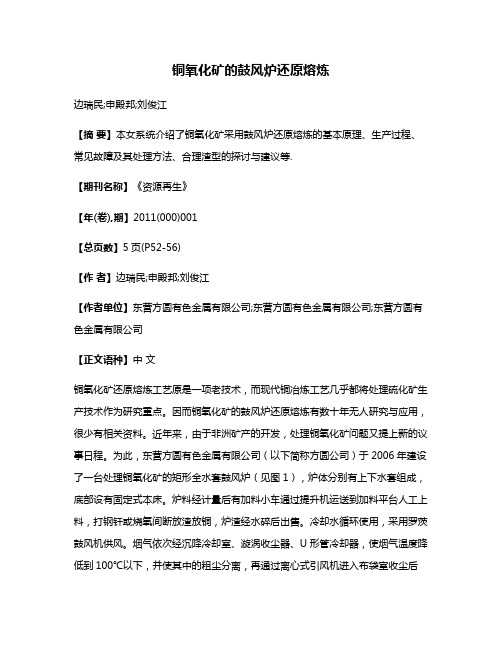
铜氧化矿的鼓风炉还原熔炼边瑞民;申殿邦;刘俊江【摘要】本女系统介绍了铜氧化矿采用鼓风炉还原熔炼的基本原理、生产过程、常见故障及其处理方法、合理渣型的探讨与建议等.【期刊名称】《资源再生》【年(卷),期】2011(000)001【总页数】5页(P52-56)【作者】边瑞民;申殿邦;刘俊江【作者单位】东营方圆有色金属有限公司;东营方圆有色金属有限公司;东营方圆有色金属有限公司【正文语种】中文铜氧化矿还原熔炼工艺原是一项老技术,而现代铜冶炼工艺几乎都将处理硫化矿生产技术作为研究重点。
因而铜氧化矿的鼓风炉还原熔炼有数十年无人研究与应用,很少有相关资料。
近年来,由于非洲矿产的开发,处理铜氧化矿问题又提上新的议事日程。
为此,东营方圆有色金属有限公司(以下简称方圆公司)于2006年建设了一台处理铜氧化矿的矩形全水套鼓风炉(见图1),炉体分别有上下水套组成,底部设有固定式本床。
炉料经计量后有加料小车通过提升机运送到加料平台人工上料,打钢钎或烧氧间断放渣放铜,炉渣经水碎后出售。
冷却水循环使用,采用罗茨鼓风机供风。
烟气依次经沉降冷却室、漩涡收尘器、U形管冷却器,使烟气温度降低到100℃以下,并使其中的粗尘分离,再通过离心式引风机进入布袋室收尘后达标排空,其工艺流程(见图2)。
炉子系负压操作,车间内外基本无烟尘,清洁环保,劳动环境优越。
方圆公司当时尚未建设铜的粗炼系统,而阳极炉产生的精炼渣无适当的设备进行处理,只能廉价出售。
铜氧化矿还原熔炼鼓风炉建成投产后,将精炼渣以适当的比例配入氧化矿中处理,效果很好。
该鼓风炉的原料主要有两种,从南非等地进口的铜氧化矿以及自产的铜阳极炉精炼渣,属连续作业,年开炉时间330天,处理料量50 000吨,其中铜氧化矿40 000吨,铜精炼渣10 000吨,生产粗铜10 000吨。
经多年的反复生产实践,技术条件不断优化,工艺操作日趋成熟。
目前,炉子生产运行稳定,并实现了连续生产,大幅提高了炉子的作业率及处理能力,有效降低了生产成本。
铜密闭鼓风炉熔炼技术操作条件
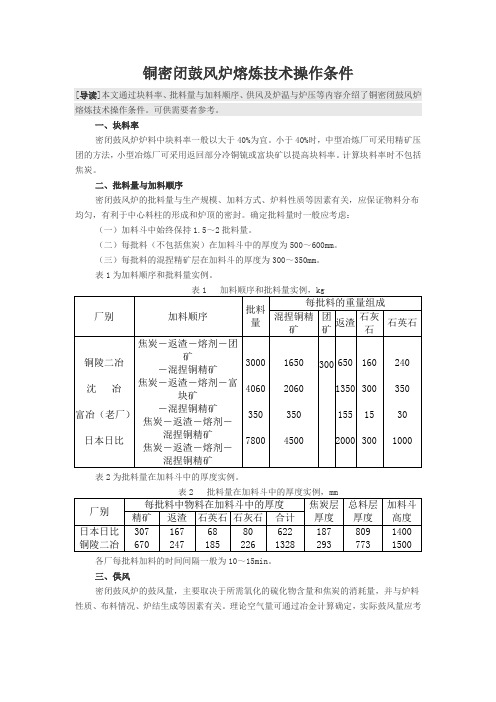
密闭鼓风炉的批料量与生产规模、加料方式、炉料性质等因素有关,应保证物料分布均匀,有利于中心料柱的形成和炉顶的密封。确定批料量时一般应考虑:
(一)加料斗中始终保持1.5~2批料量。
(二)每批料(不包括焦炭)在加料斗中的厚度为500~600mm。
(三)每批料的混捏精矿层在加料斗的厚度为300~350mm。
铜密闭鼓风炉熔炼技术操作条件
[导读]本文通过块料率、批料量与加料顺序、供风及炉温与炉压等内容介绍了铜密闭鼓风炉熔炼技术操作条件。可供需要者参考。
一、块料率
密闭鼓风炉炉料中块料率一般以大于40%为宜。小于40%时,中型冶炼厂可采用精矿压团的方法,小型冶炼厂可采用返回部分冷铜锍或富块矿以提高块料率。计算块料率时不包括焦炭。
340
420
470
烟气单体硫含量,g/m³0.78
0.35
密闭鼓风炉炉顶负压过高,漏入空气量增加,降低了烟气中二氧化硫浓度。但负压过低又会造成炉顶操作条件恶化,一般控制在50~100Pa为宜。表11为炉顶负压与烟气二氧化硫浓度的测定值。
表11 炉顶负压与烟气二氧化硫浓度的测定值
㎡
t/(㎡·d)
m³/min
%
m³/(㎡·d)
m³/t
10.5
38~45
390~400
21
30~38
~1400
10
40~45
330~400
21
33~40
~1240
2
40~45
75~80
21
38~40
~1320
1.5
45~50
50~55
21
33~37
~1060
2、风压 密闭鼓风炉的鼓风压力主要取决于炉内阻力,在一定范围内增加风压对熔炼过程有利。但风压过高会增加烟尘率和料层穿孔而跑空风。目前各厂的鼓风压力一般控制在8~10kPa。表4为鼓风压力实例。
2次鼓风炉富氧熔炼炼铜

鼓风炉富氧熔炼简介鼓风炉炼铜是一种古老的炼铜方法。
铜炉料与熔剂、焦炭在鼓风炉内熔炼产出铜锍(或粗铜)和炉渣的铜熔炼方法。
铜炉料可以是混捏铜精矿、铜精矿烧结块或其他含铜块料。
根据炉内不同的气相成分,鼓风炉炼铜可分为氧化炼铜和还原炼铜。
氧化炼铜用于处理硫化矿,还原炼铜用于处理氧化矿或再生铜料。
这种熔炼工艺简单,床能力大,热效率高,渣含铜低,投资省,建设快;在20世纪30年代以前一直是世界上主要的炼铜方法。
在中国,20世纪50年代以前,这种方法几乎是矿铜生产的唯一方法。
60年代,苏联成功地采取了处理团矿或块矿的料钟式密闭鼓风炉富氧自热熔炼工艺。
同期,波兰有2座料钟式密闭富氧熔炼鼓风炉投产。
60年代中期,中国成功地进行了料封式密闭鼓风炉工业试验后,相继用以改造敞开式鼓风炉。
1986年中国铜陵有色金属公司在料封式密闭鼓风炉基础上采用团块富氧熔炼。
1993年设计建成了富春江冶炼厂料封式富氧熔炼密闭鼓风炉。
鼓风炉炼铜的一般特征有:一:燃料在炉内燃烧,炉料与高温炉气成逆流运动,因而热交换条件好,热利用率高达70%以上。
二:鼓风炉的最高温度带集中在风口稍上的焦炭或硫化物激烈燃烧的所谓焦点区,焦点区最高温度可达1723K。
几乎所有的焦炭都是在焦点区依靠鼓风中的氧来燃烧。
在焦点区内,被氧化的硫化物主要是FeS,其氧化产物随即与炉料中的SiO2造渣。
此外,在SO2存在的条件下,入炉转炉渣中的Fe3O4和预备区形成的Fe3O4成为FeS的固体氧化剂,反应(1)的热效应大于反应(2)的热效应,即焦炭燃烧的热效应大于FeS氧化造渣的热效应。
从热力学观点看,在焦点区焦炭优先被氧化。
而且,焦炭是以灼热固体状态进入焦点区,在被烧尽以前始终保持固态不变;而FeS则以熔体状态通过焦点区,迅速地向下流动。
由于液体硫化物在焦点区停留时间很短,从动力学观点看,在焦点区FeS争夺鼓风中氧的能力远远不如焦炭。
所以硫化物的氧化主要在预备区进行,它在焦点区被氧化的程度,主要取决于该处的焦炭量,亦即取决于焦率。
鼓风炉还原熔炼的基本原理

4.4.2 熔炼过程发生的主要过程
碳质燃料燃烧;
金属氧化物还原; 脉石及氧化锌成分造渣等过程; 可能还发生硫化物形成锍、砷化物形成黄渣过程; 上述熔体产物的沉淀分离过程
4.4.3 铅鼓风炉还原熔炼的理论基础
氧化铅还原热力学 (根据炉内上下区域温度)
327℃ :PbO(s)+CO=Pb(s)+CO2+63625J 327~883℃:PbO(s)+CO=Pb(l)+CO2+58183J >883℃: PbO(l)+CO=Pb(l)+CO2+67895J 均为放热反应,反应的平衡常数方程为 lgKp=3250/T+0.417×10-3T+0.3
如表4-4。
块度:50~120mm,小于50mm和大于120mm的不大于25%;空隙度:不小于 50%~60%;强度:烧结块的转鼓率为28%~40%,或从1.5m高处三次自然落
至水泥地面或钢板上,经筛分后,小于10mm的重量低于15%~20%。铅鼓风炉
用焦炭性质实例
4-2
4-3
鼓风炉中一般不加返渣(占用炉子生产能力,增加焦炭的消耗)。铁、硅、钙熔剂 和萤石应严格拒绝入炉,只作炉况不好,渣型变化时临时措施之用。
铁;
As, Sb, Bi部分以低价氧化物 挥发,部分被还原进入粗铅。
图4-1
4.4 鼓风炉炼铅
4.4.1 铅烧结块鼓风炉还原熔炼的目的 和少量的PbS、金属Pb及PbSO4形态存在,此外还含有伴存的Cu、Zn、Bi等 有价金属和贵金属Ag、Au以及一些脉石氧化物。 最大限度地将烧结块中的铅还原出来获得金属铅,同时将Au、Ag、 Bi等贵 金属富集其中; 将铜还原进入粗铅;若烧结块中含Cu、S 都高时,则使铜呈Cu2S形态进入 铅锍(俗称铅冰铜)中,以便下一步回收; 如果炉料中含有Ni、Co时,使其还原进入黄渣(俗称砷冰铜); 将烧结块中一些易挥发的有价金属化合物(CdO)富集于烟尘中,便于进一 步综合回收; 使脉石成分(SiO2、FeO、CaO、MgO、Al2O3)造渣,锌也以ZnO形态入渣, 便于回收。
铜密闭鼓风炉熔炼概述

70~94
>50
70~94
50
90
50
60~80
45~50
90
50
三
1
2
3
4
5
6
78技术操作条件 Nhomakorabea块料率,%
批料量,t/批
焦炭,kg
返渣,kg
石英石,kg
石灰石,kg
富块团矿,kg
混捏精矿,kg
共计,kg
鼓入空气量,km3/h
鼓入氧量,km3/h
风口区鼓风强度,m³/(㎡·min)
空气含氧浓度,%
35~40
0.28~0.32
32~34
34~36
41~43
45
8~10
5~10
31(电收尘出口)
4.57(干基)
(电收尘出口)
7.04(干基)
10.28(干基)
1.86(干基)
76.25(干基)
9.0
300
(电收尘出口)
30~35
0.28~0.3
32~34
34~36
40~45
40~45
8~10
6~8
铜密闭鼓风炉熔炼概述
[导读]本文主要介绍密闭鼓风炉熔炼工艺的优点和缺点及国内密闭鼓风炉生产各厂综合技术经济指标。详细内容请见文中。
传统的铜锍熔炼鼓风炉的炉顶是敞开的,只能处理烧结矿或块矿,烟气含SO2浓度低,仅0.5%左右,难以回收,造成环境污染。20世纪50年代以后,国外、国内冶炼厂相继开发了料封式密闭鼓风炉,直接处理铜精矿,并采用了富氧熔炼。
铜陵二冶
铜陵一冶
富冶
(老厂)
烟台厂
富冶
(新厂)
一
鼓风炉熔炼再生铜(5)

书山有路勤为径,学海无涯苦作舟鼓风炉熔炼再生铜(5)鼓风炉熔炼的配料计算鼓风炉熔炼时需根据原料性质计算出所加熔剂量,常用的方法有两种。
一、有效熔剂法原料为含铜炉渣。
(1)已知条件a、含铜炉渣的化学成分为SiO2 21.50%、CaO 2.20%、FeO 14.40%、其他61.90%。
b、石英石成分为SiO2 92.4%、CaO 1.2%、FeO 0.3%。
c、石灰石成分为SiO2 1.3%、CaO 54%、FeO 0.5%。
d、选择的渣型为SiO2 30%、CaO 28%、FeO 14%。
(2)配料计算以100kg 含铜炉渣为计算基础a、计算石英石和石灰石的有效溶剂率100kg 石英石中含有1.2kg CaO,炉渣中CaO 与SiO2 之比是28:30 1.2kg CaO 造渣需1.2×30/28=1.2kg SiO2 100kg 石英石中游离的SiO2=92.4-1.29=91.11kg,即石英石的有效熔剂率为91.11%。
同样,100kg 石灰石中有1.3kg SiO2,因此石灰石中有1.3×28/30=1.2kg CaO 与SiO2 造渣,故石灰石的有效熔剂率为(54-1.2)÷100=52.8% b、计算炉渣量和各组成的量通过渣型和铜炉渣中含FeO 量计算出渣量为14.4/14×100=103kg 渣型各组成的量如下SiO2=103×0.30=30.9kgCaO=103×0.28=28.84kgFeO=103×0.14=14.40kg c、计算补加的石英石和石灰石量除去原料中SiO2、CaO 的含量,炉渣中还缺的量为SiO2=30.9-21.5=9.4kgCaO=28.8-2.2=26.64kg 需补加的石英石熔剂为9.4/91.11%=10.3kg 补加的石灰石熔剂为26.64/52.8%=10.3kg 故造渣率为103/ (100+10.3+50.5)×100%=64% 当熔剂质量稳定且加入量不大时,可近似取石英石的有效熔剂率为92%,石灰石的有效熔剂率为53%。
铜冶炼的工艺流程及原理

铜冶炼技术的发展经历了漫长的过程,但至今铜的冶炼仍以火法冶炼为主,其产量约占世界铜总产量的85%。
1)火法冶炼一般是先将含铜百分之几或千分之几的原矿石,通过选矿提高到20-30%,作为铜精矿,在密闭鼓风炉、反射炉、电炉或闪速炉进行造锍熔炼,产出的熔锍(冰铜)接着送入转炉进行吹炼成粗铜,再在另一种反射炉内经过氧化精炼脱杂,或铸成阳极板进行电解,获得品位高达99。
9%的电解铜。
该流程简短、适应性强,铜的回收率可达95%,但因矿石中的硫在造锍和吹炼两阶段作为二氧化硫废气排出,不易回收,易造成污染。
近年来出现如白银法、诺兰达法等熔池熔炼以及日本的三菱法等、火法冶炼逐渐向连续化、自动化发展。
2)现代湿法冶炼有硫酸化焙烧-浸出-电积,浸出-萃取-电积,细菌浸出等法,适于低品位复杂矿、氧化铜矿、含铜废矿石的堆浸、槽浸选用或就地浸出。
湿法冶炼技术正在逐步推广,预计本世纪末可达总产量的20%,湿法冶炼的推出使铜的冶炼成本大大降低. 向左转|向右转电解铝的基本原理和工艺过程: 电解铝就是通过电解得到金属铝。
现代电解铝工业生产采用冰晶石—氧化铝熔融电解法。
熔融冰晶石是溶剂,氧化铝是溶质,以碳素体作为阳极,铝液作为阴极,通入强大的直流电后,在950℃~970℃下,在电解槽内进行电化学反应。
阳极主要产物是二氧化碳和一氧化碳气体,其中含有一定量的氟化氢等有害气体和固体粉尘,该气体需经过净化处理后排空。
阴极产物是铝液,铝液通过真空抬包从电解槽内抽出,送至铸造车间,在保温炉内经净化澄清后,浇铸成铝锭或直接加工成线坯、型材等生产工艺流程其生产工艺流程如下图:氧化铝氟化盐碳阳极直流电↓ ↓ ↓ ↓ ↓排出阳极气体-——--—电解槽↑ ↓ ↓ 废气← 气体净化铝液↓ ↓ 回收氟化物净化澄清----—-————-———-—————-——↓ ↓ ↓ 返回电解槽浇注轧制或铸造↓ ↓ 铝锭线坯或型材方程电解铝就是通过电解得到的铝。
重要通过这个方程进行:2Al2O3==4Al+3O2。
氧化顶吹浸没熔炼法

立志当早,存高远氧化顶吹浸没熔炼法氧化顶吹浸没熔炼法是20 世纪70 年代澳大利亚开发成功的铜冶炼技术,后移植于铅的冶炼。
该熔炼技术是在一个圆桶形的炉内,通过炉子顶端斜烟道的开孔,插入一支由空气冷却的钢制喷枪。
喷枪位于内衬耐火材料的炉膛中央,头部埋于熔体中,燃料和空气通过喷枪直接喷射到高温熔融渣层中,产生燃烧反应并造成熔体的剧烈搅动,进行物料的氧化脱硫,产出部分粗铅和富铅渣。
这样,在一个小空间内加入的炉料被迅速加热熔化并完成化学反应。
调整喷枪的插入深度可以控制熔体搅拌强度,操作灵活,炉子能在较长时间内保持热稳定。
熔炼产出的富铅渣经过铸渣机浇注成渣块,再送入鼓风炉还原熔炼,生产粗铅和炉渣。
喷枪是该炉子的核心部件,它为双层套管结构,上段材质为45#钢,下段喷口为不锈钢。
内管通过燃料即油或用定量空气携带的煤粉。
内外管间设有螺旋形导流片,助燃空气(或富氧空气)从此通道中以大于两倍音速呈旋涡状流出,加大了枪体与气体间的传热,从而在喷枪外表面形成一层冷却的渣壳,此渣壳保护喷枪,延长了喷枪的使用寿命。
顶吹熔池熔炼炉对入炉物料要求不高,不论是粒状物料还是粉状精矿、烟尘返料等,只要水分小于10%,均可直接入炉。
若为粉状物料,经配料、制粒后入炉有利于降低烟尘率。
该法由于主体设备结构简单,辅助、附属设备不复杂,与基夫赛特法、QSL 法相比,基建投资较低。
氧气顶吹浸没熔炼法属于二段炉炼铅法,用氧化炉熔炼取代了传统炼铅工艺的烧结,氧化炉烟气量小、烟气SO2 浓度高,解决了烧结过程低浓度SO2 的污染问题,90%以上的硫得到回收利用,对环境污染小,且劳动卫生条件比传统法有很大改善。
但由于氧化段只有约40%的铅以粗铅形式产出,富铅渣不能直接还原而必须浇注成渣块,。
鼓风炉炼铜工艺操作规程

鼓风炉炼铜工艺操作规程鼓风炉炼铜是一种常用的冶金工艺,下面是一份鼓风炉炼铜工艺操作规程,包括操作步骤、安全要求和工艺参数等。
一、操作步骤1. 准备工作:(1) 确保鼓风炉的设备完好,检查炉体、炉门、炉衬等部位是否有损坏。
(2) 准备足够的原料和草木灰作为还原剂。
(3) 检查鼓风机的运行情况,确保正常工作。
(4) 将铜料和还原剂按炉子容量的比例放入鼓风炉中。
2. 点火:(1) 打开鼓风机,确保有足够的氧气供给。
(2) 在鼓风炉的底部放入易燃物质,点火点燃。
(3) 等待火焰彻底燃烧后,逐渐加大鼓风机的风力,使火焰达到合适的温度。
3. 加热和处理:(1) 在火焰稳定后,逐渐加入铜料。
(2) 观察铜料的熔化情况,根据需要调整鼓风机的风力和炉温。
(3) 当铜料熔化后,根据需要加入其他合金元素。
(4) 在炉温达到所需温度时,进行合金的调整和均匀搅拌。
(5) 根据需要,逐渐加入除杂剂,并进行除渣操作。
4. 浇铸:(1) 确保合金熔池中没有杂质和渣滓后,进行浇铸操作。
(2) 将熔融的合金从鼓风炉中倒入预先准备好的铸模中。
5. 冷却和取出:(1) 等待铸件冷却,并确保冷却完全后再取出铸件。
(2) 对铸件进行必要的后处理,例如去除表面氧化皮等。
二、安全要求1. 在操作鼓风炉时,必须佩戴防护眼镜、防火服等个人防护用品。
2. 确保炉体周围的通风良好,以防止有毒气体积聚。
3. 操作时要保持清醒,避免酒精等物质的影响。
4. 加热时要小心熔融物溅出造成烫伤,使用合适的工具进行操作。
5. 遵循电力安全操作规程,确保电气设备的接地和绝缘良好。
三、工艺参数1. 炉温:根据需要决定,一般在1000-1200摄氏度之间。
2. 风力:根据铜料的熔化情况和操作要求适当调整,通常在30-80立方米/小时之间。
3. 加铜速度:根据铜料的熔化情况和炉子容量确定,一般控制在10-20千克/小时之间。
4. 加合金元素和除杂剂的比例和时间根据具体合金的需求而定,需谨慎操作。
3鼓风炉熔炼

二、密闭鼓风炉熔炼的基本原理
1、密闭鼓风炉的热工特性 、 铜精矿密闭鼓风炉熔炼属于半自热氧化熔炼, 铜精矿密闭鼓风炉熔炼属于半自热氧化熔炼,炉气 中含有较多的游离氧,炉内为氧化性气氛。 中含有较多的游离氧,炉内为氧化性气氛。冶炼过程所 需的热量由焦炭燃烧和冶炼过程本身的放热反应供给。 需的热量由焦炭燃烧和冶炼过程本身的放热反应供给。 密闭鼓风炉的炉料由混捏铜精矿、 密闭鼓风炉的炉料由混捏铜精矿、熔剂和固体转炉 渣。块料的容积比应在50%左右。 块料的容积比应在 %左右。
9
(3)本床区 ) 本床区位于焦点区下部,是汇集熔体和最后调整熔 本床区位于焦点区下部,是汇集熔体和最后调整熔 体成分的区域 在调整熔体成分的过程中, 的区域。 体成分的区域。在调整熔体成分的过程中,最主要的反 应是溶于炉渣中的少量Cu O被冰铜中的 被冰铜中的FeS再硫化 再硫化。 应是溶于炉渣中的少量Cu2O被冰铜中的FeS再硫化。 调整后的熔体经咽喉口流入前床。 调整后的熔体经咽喉口流入前床。
5
(1)预备区 ) 预备区位于炉子上部,温度大致从 预备区位于炉子上部,温度大致从250~600℃到 ℃ 1000~1100 ℃。两侧料柱温度比中心料柱温度高。 两侧料柱温度比中心料柱温度高。 在这一区域上部主要进行炉料的干燥和预热。 在这一区域上部主要进行炉料的干燥和预热。中心料柱 上部主要进行炉料的干燥和预热 只在中下部位发生炉料的干燥和预热。 只在中下部位发生炉料的干燥和预热。侧料柱中部和下 部,铜和铁的高价硫化物将发生分解。 铜和铁的高价硫化物将发生分解。 预备区为氧化气氛,部分固态硫化物将发生氧化,中心 预备区为氧化气氛,部分固态硫化物将发生氧化, 氧化气氛 料柱的氧化过程只在预备区下部才大理进行。 料柱的氧化过主要技术经济指标 、 密闭鼓风炉的主要技术经济指标是床能率、 密闭鼓风炉的主要技术经济指标是床能率、焦率和 铜的回收率。 铜的回收率。 床能率是以一昼夜内, 床能率是以一昼夜内,在单位风口区面积床面上熔 炼的炉料量(包括铜精矿、熔剂和转炉渣)来表示。它 炼的炉料量(包括铜精矿、熔剂和转炉渣)来表示。 主要取决于入炉风量、炉料的透气性和炉渣成分。 主要取决于入炉风量、炉料的透气性和炉渣成分。 焦率是用焦炭量与干炉料总量之百分比来表示的。 焦率是用焦炭量与干炉料总量之百分比来表示的。 焦率过低或过高均影响冶炼指标, 焦率过低或过高均影响冶炼指标,应在保证热平衡的条 件下,尽力降低焦率。 件下,尽力降低焦率。 下表列出了某些工厂的主要技术经济指标。 下表列出了某些工厂的主要技术经济指标。
铜精炼渣鼓风炉还原熔炼实践

铜精炼渣鼓风炉还原熔炼实践7·铜精炼渣鼓风炉还原熔炼实践西安铜材厂韩瑜瑛提要本文系统地介绍了鼓风炉处理铜精炼渣的开炉、进料、管理、停炉以及故障排除等经验,探讨了渣型选择间题。
量压风风我厂用于还原熔炼铜精炼渣的鼓凤炉为圆形:风口区截面积0.4m2。
炉子下部为4块轴对称冷却水套,上部铁炉壳内衬耐火砖,底部为活动式本床。
采用罗茨风机供风。
炉料经计量后由加料小车自动_L料人炉,烟气30%进收尘器回收氧化锌,其余排空,炉渣水淬后堆放,冷却水循环使用,打眼放渣出铜‘液体粗铜自流冷却成块,送料场存放。
我厂鼓风炉主要用千本厂铜阴、阳极炉所产炉渣的还原熔炼,属间断作业,年处理渣量800吨左右,开炉时间60多天。
经十多年的反复实践,不断摸素。
目前炉子生产情况良好,工艺日趋完善,炉渣基本定型,各项指标比较稳定。
主要技术经济指标如下:床能率65吨/米2·日粗铜品位85%焦率29%弃渣含铜1%铜直收率95%电耗40度/吨渣熔剂率23%加工成本10。
元/吨渣300公斤,开风并打开出铜口15分钟,接着停风炯烧15~20分钟,加入第三批焦炭300公斤,开风机并再开出铜口15~20分钟,待出铜口发红,焦炭喷出时停风炯烧15分钟。
炯烧结束后,开风并加人返回渣3~5批,每批返回料组成为(公斤):焦炭70,鼓风炉渣160,石灰石5,萤石2。
当渣从放铜口流‘出后,堵住出铜口,加人焦炭150公斤,接着开始加正规炉料,并准备放渣,加人正规料10批后,开始放第一次铜。
至此开炉已告结束,接通收尘系统转人正常生产。
(二)正常操作正常作业主要是进料、排渣、放铜,其工艺操作包括原料、熔剂、燃料、风口、铜口、渣口、料柱、水套等的控制。
技术条件如下:料量170公斤/批焦炭70公斤/批石灰石40公斤/批萤石3公斤/批进料间隔8分钟放铜间隔10。
分钟放渣间隔一、鼓风炉还原熔炼的操作(一)开炉装配炉子各部及配套设施,检查符合要求后,用木柴生火,加人焦炭烘烤炉缸24~36小时,并定时清除炉缸内积灰。
铜氧化矿的鼓风炉还原熔炼

銅氧化礦的鼓風爐還原熔煉Smelting Reduction of Copper Oxide Ore Blast Furnace文/邊瑞民 申殿邦 劉俊江東營方圓有色金屬有限公司摘要:本文系統介紹了銅氧化礦採用鼓風爐還原熔煉的基本原理、生產過程、常見故障及其處理方法、合理渣型的探討與建議等。
銅氧化礦還原熔煉工藝原是一項老技術,而現代銅冶煉工藝幾乎都將處理硫化礦生產技術作為研究重點。
因而銅氧化礦的鼓風爐還原熔煉有數十年無人研究與應用,很少有相關資料。
近年來,由於非洲礦產的開發,處理銅氧化礦問題又提上新的議事日程。
為此,東營方圓有色金屬有限公司(以下簡稱方圓公司)於2006年建設了依台處理銅氧化礦的舉行全水套鼓風爐(見圖1),爐體分別有上下水套組成,底部設有固定式本床。
爐料經計量後有加料小車通過提升機運送到加料平台人工上料,打鋼釬或燒氧間斷放渣放銅,爐渣經水碎後出售。
冷卻水循環使用,採用羅茨鼓風機供風。
煙氣依次經沉降冷卻室、漩渦收塵器、U型管冷卻器,使煙氣溫度降低到100℃以下,並使用其中的粗塵分離,再通過離心式引風機進入布袋室收塵後達標排空,其工藝流程(見圖2)。
爐子系負壓操作,車兼內外基本無煙塵,清潔環保,勞動環境優越。
圖1 銅氧化礦還原熔煉鼓風爐圖2 銅氧化礦還原熔煉流程圖方圓公司當時尚未建設銅的粗煉系統,而陽極爐產生的精煉渣無適當的設備進行處理,只能廉價出售。
銅氧化礦還原熔煉鼓風爐建成投產後,將精煉渣以適當的比例配入氧化礦中處理,效果很好。
該鼓風爐的原料主要有兩種,從南非等地進口的銅氧化礦以及自產的銅陽極爐精煉渣,屬連續作業,年開爐時間330天,處理料量50,000噸,其中銅氧化礦40,000噸,銅精煉渣10,000噸,生產粗銅10,000噸。
經多年的反覆生產實踐,技術條件不斷優化,工藝操作日趨成熟。
目前,爐子生產運行穩定,並實現了連續生產,大幅提升了爐子的作業率及處理能力,有效降低了生產成本。
阳极铜的生产工艺火法

阳极铜的生产工艺——火法
一、铜精矿熔炼
铜精矿熔炼是阳极铜生产的第一步,主要目的是将铜精矿中的有价成分最大限度地提取出来,形成粗铜。
这个过程通常在高温和有还原气氛的条件下进行,使用的设备为反射炉或电炉。
铜精矿熔炼的主要化学反应是将铜的硫化物氧化物还原为金属铜,同时分离其他杂质。
二、吹炼
在粗铜的制备完成后,需要进行吹炼以进一步从粗铜中去除杂质。
吹炼过程在转炉中进行,通过鼓入空气或富氧空气,使粗铜中的杂质氧化并从铜液中分离。
在吹炼过程中,部分铜也会被氧化,但随后会在还原阶段被还原回金属铜。
三、火法精炼
火法精炼的主要目的是进一步去除铜中的杂质,使铜的纯度达到电解精炼的要求。
这个过程通常在高温和有还原气氛的条件下进行,使用的设备为反射炉。
火法精炼过程中,会向铜液中加入特定的熔剂,以去除铜中的杂质。
然后通过液态金属的静置、分层和结晶,将高纯度的铜从液态金属中分离出来。
四、电解精炼
电解精炼是生产高纯度阳极铜的最后一道工序。
经过火法精炼的铜液被倒入电解槽中,通过电解过程将铜从铜液中
析出,形成阳极铜。
在这个过程中,阳极铜中的杂质会以沉淀物的形式留在电解液中,而纯度较高的铜则会作为阳极被析出。
电解精炼能够进一步降低阳极铜中的杂质含量,提高其纯度。
- 1、下载文档前请自行甄别文档内容的完整性,平台不提供额外的编辑、内容补充、找答案等附加服务。
- 2、"仅部分预览"的文档,不可在线预览部分如存在完整性等问题,可反馈申请退款(可完整预览的文档不适用该条件!)。
- 3、如文档侵犯您的权益,请联系客服反馈,我们会尽快为您处理(人工客服工作时间:9:00-18:30)。
銅氧化礦的鼓風爐還原熔煉Smelting Reduction of Copper Oxide Ore Blast Furnace文/邊瑞民 申殿邦 劉俊江東營方圓有色金屬有限公司摘要:本文系統介紹了銅氧化礦採用鼓風爐還原熔煉的基本原理、生產過程、常見故障及其處理方法、合理渣型的探討與建議等。
銅氧化礦還原熔煉工藝原是一項老技術,而現代銅冶煉工藝幾乎都將處理硫化礦生產技術作為研究重點。
因而銅氧化礦的鼓風爐還原熔煉有數十年無人研究與應用,很少有相關資料。
近年來,由於非洲礦產的開發,處理銅氧化礦問題又提上新的議事日程。
為此,東營方圓有色金屬有限公司(以下簡稱方圓公司)於2006年建設了依台處理銅氧化礦的舉行全水套鼓風爐(見圖1),爐體分別有上下水套組成,底部設有固定式本床。
爐料經計量後有加料小車通過提升機運送到加料平台人工上料,打鋼釬或燒氧間斷放渣放銅,爐渣經水碎後出售。
冷卻水循環使用,採用羅茨鼓風機供風。
煙氣依次經沉降冷卻室、漩渦收塵器、U型管冷卻器,使煙氣溫度降低到100℃以下,並使用其中的粗塵分離,再通過離心式引風機進入布袋室收塵後達標排空,其工藝流程(見圖2)。
爐子系負壓操作,車兼內外基本無煙塵,清潔環保,勞動環境優越。
圖1 銅氧化礦還原熔煉鼓風爐圖2 銅氧化礦還原熔煉流程圖方圓公司當時尚未建設銅的粗煉系統,而陽極爐產生的精煉渣無適當的設備進行處理,只能廉價出售。
銅氧化礦還原熔煉鼓風爐建成投產後,將精煉渣以適當的比例配入氧化礦中處理,效果很好。
該鼓風爐的原料主要有兩種,從南非等地進口的銅氧化礦以及自產的銅陽極爐精煉渣,屬連續作業,年開爐時間330天,處理料量50,000噸,其中銅氧化礦40,000噸,銅精煉渣10,000噸,生產粗銅10,000噸。
經多年的反覆生產實踐,技術條件不斷優化,工藝操作日趨成熟。
目前,爐子生產運行穩定,並實現了連續生產,大幅提升了爐子的作業率及處理能力,有效降低了生產成本。
其主要經濟指標見表1。
表1 鼓風爐主要技術經濟指標床能力t/m2.d 54 總回收率% 98.70 粗銅品位% 92%~8%焦率% 20~25 煙塵率% 2.77 電單耗kwh/t.渣 40熔劑率% 19~33 水碎渣含銅%0.26-0.60 水單耗m3/t.Cu 4.60銅直收率% 95.20 加工成本 元t.Cu / 2765.06一、還原熔煉的基本原理熔煉時鼓風爐中的爐料逐漸自加料口下降到風口帶。
含有大量CO的上升氣流與爐料相對運動,自150℃時開始,他將銅的氧化物CuO和Cu2O還原成銅。
爐料下降時,還原的銅顆粒首先熔化,往下就是渣熔化。
在風口帶全部熔融物都與鼓風爐的空氣相遇。
部分已還原的銅又被氧化為Cu2O,並以硅酸鹽的型態轉入渣中。
在這種情況下獲得的兩種產物,即粗銅和爐渣。
銅氧化礦中除銅的氧化物中,尚有其他金屬(如鐵、鉛、砷、銻等)的氧化物,還原熔煉時,后者不可避免的會有部分還原,被還原的其他金屬與銅熔合在一起並使銅的品位降低,謂之粗銅。
在鼓風爐的熔煉過程中,對銅氧化物的還原而言,焦炭是較好的還原劑。
由於他對氧的親和勢大,且其親和勢隨溫度的升高而增加,從而除CuO等少數金屬氧化物外,都能被碳還原。
由此可知,Cu2O、CaO、PbO、NiO、CoO、SnO、As2O3等屬於易還原氧化物,而Cu2O最終被還原成金屬Cu。
某些金屬的氧勢RT ln(po2/pΘ)(或△fG O(Meo))與溫度的關係見圖3。
圖3 某些金屬的氧勢RT ln(po2/pΘ)(或△fGO(Meo))與溫度的關係圖二、生產過程1.開爐:烘爐:開爐前通過檢查鼓風爐及其附屬裝置等配套系統符合開爐要求後,即可按照工藝要求開始點火烘爐。
首先用小木柴文火烘烤爐缸32小時使其烘透。
清除積灰後,第二次點火加入中木柴,並按照小─中─大控制火勢,繼續烘烤12小時。
從風口觀察爐缸磚體顏色發紅,即可投入大木柴迅速提高爐溫,最後一批木柴必須加至風口區0.5m以上,並要求木柴平均分布,不准有高低不平現象。
約2小時後,發現風口木柴基本充分燃燒時,即可加入底焦,底焦共加2,000kg,分四批加入,待第一批焦炭從風口內觀察發紅時,開始送風10~15分鐘,風壓100mmHg,接著停風悶燒5~15分鐘,再送風,等到最後一批焦炭加完後停風悶燒10分鐘,再持續送風,風壓為150mmHg,並觀察風口焦炭燃燒至發白,從加料口觀察焦碳燃燒至發紅,火苗全部上齊,便開始投返渣料,即烘爐宣告結束。
投返渣料:一般投入返渣料的數量為7-10批,每批返渣料的組成為:焦炭200kg,鼓風爐旱渣800kg,石灰石45kg,螢石15kg,焦率23%。
加返渣料的過程中,嚴禁隨意調動風閥,應使風壓隨料註布斷的提高而自然上升。
同時注意觀察銅口是否有渣子流出,若發現渣子流出,應立即塞入黃泥打進鋼釬。
當從風口底不發現有 火苗跳動時蘭火苗跳動時,立即從渣口打入鋼釬放渣。
返渣料加畢,隨即加入正規爐料,待正歸爐料加入10批後,開始第一次放銅,至此開爐宣告結束,即可轉入正常生產。
2.正常生產:鼓風爐的正常作業主要包括加料、排渣與放銅,其工藝操作包括原料、焦炭、熔劑、風口、銅口、渣口、料口、料柱、水套等項內容。
其主要工藝配方與技術條件見表2。
表2 主要工藝配方與技術條件配料名稱 數量(公斤/批) 技術條件 數值氧化礦 600 風壓(mmHg) 550~900精煉渣 150 風量(m3/min) 70~110焦炭 250 料口負壓(pa) 50~150石灰石 200 水套溫度(℃) 45~55石英石 80 布袋進口溫度(℃) 50~100螢石 5 料柱高度(m) 3.5~5.0煙灰 10落地銅 5●加料:物料入爐前首先嚴格按照原料、焦炭、熔劑的質量標準精心選料,然後依據工藝配方要求準確計算後,分層均勻加入爐內,其裝料順序為焦炭─熔劑─爐料。
粉料入爐前應加適量的水並拌勻。
料面要裝成平整的形狀,絕不允許有七高八低的現象。
料柱的高低與爐料的透氣性有關,塊率高、粉料少,則透氣性強,料柱就高一些,反之就低一些。
但無論哪一種情況,爐子的風壓宇風量必須保持穩定。
原料、焦炭、熔劑的質量標準如表3所示。
●風口:風口就是鼓風爐的眼睛,在生產過程中,他的狀況優劣在一定程度上可標誌著爐況的好壞。
爐況正常時,打開風口蓋板向裡窺視,可觀查到風口底部有一層均勻的黑色網狀渣殼,殼面上布有發出白色亮光的小孔。
當爐況惡化時,風口內網狀渣殼厚薄不均,殼面上的小孔發紅,甚至發黑,有時風口內網狀渣殼消失並出現深棚現象,甚至風口結死,風送不進去。
因此,對風口的管理要時刻認真觀察,發現病態應即時處理。
●渣口:渣口的操作開始階段是間斷放渣,用黃泥配合鋼釬堵塞。
每次放渣時間一班持續30分鐘左右,間隔時間一般控制在15~20分鐘。
目前已經做到連續放渣。
排出的渣(含銅0.26%~0.60%)經水碎後至渣斗,再用叉車運送到渣場存放,然後售給水泥廠作原料。
●銅口:銅口的管理也室件段操作,打出鋼釬放銅,個別時候也需燒氧放銅,用黃泥配合鋼釬堵塞。
放銅的頻率與數量,是跟據爐料含銅的高低及爐缸盛銅的多少進行掌握,每班(8小時)一般控制在2~5次,其數量為3~8塊(每塊550kg左右)。
圖4為現場放銅的圖片。
●料柱:對於鼓風爐的還原熔煉來說,料柱是熔煉制度的一項重要內容,他的高低主要依據爐料的物理規格及化學成分等狀況來進行調整,確保風壓穩定,並使爐料在爐內有一定的停留時間。
由於我公司爐身較高,可根據爐料粉料的多少和塊率的高低進行靈活掌握。
在實際生產中,料柱一般控制在3.2~5.0m。
●水套:水套是鼓風爐最關鍵的結構部件,方圓公司鼓風爐水套是用鍋爐鋼板冷壓焊接製成的。
其使用壽命與冷卻水的水質及溫度關係密切,冷卻水的水質好,溫度控制得當(一般控制在45~55℃),水套的使用壽命就長,否則易於損壞,甚至發生安全事故。
因此,在實際生產中要密切觀察水套的進出水情況,確保合格的水質與合理的水溫,研進超壓或缺水。
如遇停泵,必須立即打開備用高為水箱冷卻,並相應調低風量,防止回水管蒸氣噴射傷人。
此外還要定期排污,以防水套結垢。
表3 原料、焦炭、熔劑的質量標準銅氧化礦 銅精煉渣 石灰石 石英石 螢石 焦炭 Cu≧15% 15%≦Cu≦20% CaO≧50% SiO2≧95% CaF2≧85% 固定碳≧83% S≦0.8% Al2O3≦0.5% MgO<1% H2O<3% H2O<3% 揮發份<1.5% MgO≧2% H2O<3% 灰份<15% Al2O3≦0.5% S<0.5% ZnO≦2%粒度≦120 粒度30~150 粒度30~60 粒度50~80 粒度50~120 粒度40~12圖4 放銅現場圖3.停爐:●短期停爐:方圓公司根據實際生產經驗,規定在兩個班即16小時以內視為短期停爐。
首先將料柱提高0.5m左右,並適當提高焦率,然後再停風(先停鼓風機、後停引風機)。
同時用黃泥堵嚴風口,並放進爐內的液態產物,以待恢復生產。
●長期停爐:首先停止正規加料,然後加入9~12批返渣料,並適當提高焦率進行洗爐。
此時應繼續供風,直至銅口液態產物及少並伴有焦炭吹出時即可停風。
三、常見故障及其處理1.上燃上燃是氧化礦與精煉渣還原熔煉的常見故障,特別是單煉精煉渣或其比例過高時,由於廖住的透氣性太強產生上燃;再就是布料的不均勻,型成料柱空洞,也易產生上燃。
通常防止和處理的方法是:粉料與塊料合理搭配;加料前對爐料噴上適量的水份;布料一定要做到均勻。
一旦發生上燃,應採取先大幅降低料柱,在快速連續加到原有高度的措施來處理。
2.棚料棚料現象實際上是高熔點物質在風口區上方半熔狀物質的堆積與凝結,從而破壞了正常的爐料下降制度,嚴重時可被迫停爐。
產生的主要原因有:爐料中MgO、Al2O3、ZnO難熔組分過多時生成的鎂尖晶石或鋅尖晶石以固體狀態析出,使渣的熔點升高、黏度增大;粉料過多及布料不均,容易引起辦熔狀物質的凝結;銅精煉渣中耐火料過多,使渣的熔點升高等。
通常處理的方法是:嚴把進料關,使爐料中MgO、ZnO含量均控制在1%以下, Al2O3控制在0.5%以下,減少鎂尖晶石或鋅尖晶石等高熔點物質的產生;塊礦與粉料合理搭配,提高布料的均勻性,防止爐料半熔狀物質的凝結;對各分廠所產銅精煉渣提出質量標準,出廠前必須進行徹底分撿,絕不允許有耐火料混入。
一般棚料故障的發生是有預兆的,主要表現在風口溫度偏低、網狀渣殼亮點變暗、焦點區上移、渣流動性變差以及風壓升高等。
當發生這種現象時,應立即組織人員用鋼釬打料棚,適當降低料柱,適當提高焦率,適當提高渣硅酸度。
將溫度低的風口調低風量,焦點區上移的風口停止供風,必要時可適當加入部分熔點滴的返渣料洗爐。