制程检验管理程序(含表格)
制程检验程序(含表格)

制程检验程序(ISO9001:2015)1.0目的为规范制程检验,预防产出批量不合格的产品,减少(杜绝)制程异常的发生。
不断降低生产制程不良率,提升产品品质,确保产品品质符合客户要求。
2.0范围适用于本公司生产制程品质检验控制。
3.0定义3.1首件:指生产制程中加工生产的产品,判定符合要求后,拟批量生产前的第一台(个)产品(半成品,成品)。
3.2全检:对制程中的产品或产品的某些检验项目进行100%检验。
3.3巡检:对生产过程中影响产品品质的因素(工位)进行随机抽样检验,确认。
4.0权责4.1品质部4.1.1负责制程中产品外观,检验流程,检验标准,检验规范,检验工位的编制和设置。
4.1.2IPQC:负责对产品,物料首件确认的主导工作,并对产品首件做出合格与否的判定;制程品质检控,品质异常的确认与追踪;主导不合格品或品质异常问题的提出,跟进,落实及改善效果确认。
4.2项目部4.2.1新产品首件的确认,负责制程中电气/结构性能测试流程,测试工位的编制和设置;品质异常,不合格品原因的分析及改善对策的提出。
4.2.2负责制程中设备,仪器的使用规范的制订;机器,设备,仪器,仪表,治夹具,工具运行状况的监控,正常运转的巡视及点检/保养工作的监督。
4.3生产部4.3.1负责首件的制作与送样确认;全检工位的人员配置。
4.3.2制程中4M1E的落实及制程过程的监控,配合IPQC与PE的工作;品质异常的受理与改善,改善对策的具体实施。
4.3.3负责制程中设备,仪器,仪表,治夹具,工具的日常点检/保养工作。
5.0程序5.1生产,检验前作业准备5.1.1生产部5.1.1.1在开拉生产前进行自我核查,发现不符合项及异常,采取措施,立即纠正。
5.1.1.2在开拉生产前须查核领用物料是否与[生产计划排程表]相符,是否有相应的BOM,技术规范;生产环境是否符合产品需求,各作业工位是否悬挂对应的SOP,作业人员对作业方法,产品品质是否清楚了解。
制程检验管理程序doc

1.目的为有效控制生产制程质量,降低制造不良,特制订本程序。
2.适用范围适用于本公司产品制程检验作业。
3.权责3.1 本程序由品质部制定和实施,相关部门配合。
3.2 生产组长及各机位师傅:负责各工序之“首件”确认,按制程检验员的提出的品质要求进行调整,直到达到有关要求。
3.3 制程检验员:制程巡回检验,对各工位师傅提出改进要求,按制程检验指导书要求实施相关工位的首检和制程检验。
3.4 品质部经理:负责审核巡检员的检验报告,对不合格提出处理决定。
4.定义4.1首件检验:指对制程各工序的第一件之检验;操作条件变更或制品规格变换、批量生产之前首件制品的检验,需要在工单上记录。
4.2自检:作业员对自己生产的产品进行检查,不需作记录。
4.3巡检:在生产过程中对各生产工序之产品进行巡回检查,需要作制程检验记录。
4.4全检:在生产过程中对产品进行全面检查。
5.作业程序:5.1 制程检验员质量判定基准以样品、图纸及各检验规范、作业指导书为依据。
5.2 生产组长及各工位师傅对工序产品进行首件检验,确认OK后,方可生产。
5.3 生产过程中,作业员对自己生产的产品自查,若产品OK,顺利流转下一工序;经检验后不合格的产品,做上相应标识,并将不合格品存放在“不合格品”区按《不合格品控制程序》处理不合格品。
5.4 巡检员依制程检验规范的步骤要求进行检验,并将检验结果如实记录于“制程巡检记录表”上,品质部经理予以签认。
若巡检时查出不合格品需开立“品质异常单”,要求责任部门提出改善措施进行相应的改善。
5.5 制程检验员在巡回检验/全检时发现由于大批量(抽检整批不合格时或巡检超过十个不良样品)或重大材料不良(材料使用错误)、操作不当、设备故障等原因而产生质量异常时,须要求相关人员予以改善,并开立“品质异常处理报告”,要求权责单位予以改善,制程检验员跟进改善成效。
制程出现不良时,机位师傅应按制程检验员提出的质量要求,调机后方可生产,若调机无法达到要求的,应根据“品质异常处理报告”上的处理决定进行处理。
PQC检验程序(含表格)
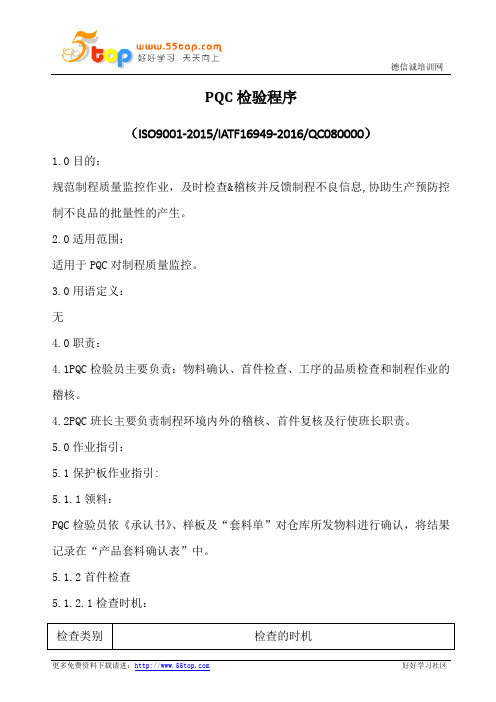
PQC检验程序(ISO9001-2015/IATF16949-2016/QC080000)1.0目的:规范制程质量监控作业,及时检查&稽核并反馈制程不良信息,协助生产预防控制不良品的批量性的产生。
2.0适用范围:适用于PQC对制程质量监控。
3.0用语定义:无4.0职责:4.1PQC检验员主要负责:物料确认、首件检查、工序的品质检查和制程作业的稽核。
4.2PQC班长主要负责制程环境内外的稽核、首件复核及行使班长职责。
5.0作业指引:5.1保护板作业指引:5.1.1领料:PQC检验员依《承认书》、样板及“套料单”对仓库所发物料进行确认,将结果记录在“产品套料确认表”中。
5.1.2首件检查5.1.2.1检查时机:5.1.2.2检查项目5.1.3注意事项:PQC检验员在领料确认时及检查首件时:1)检查产品所有物料的品牌、型号、规格、封装及环保标识是否与《承认书》中“材料清单”规定的是否一致。
2)核对受控样板,确认产品所用的PCB版本、颜色和产品上的材料型号、版本(丝印)颜色、外形是否和样板一致。
5.1.4检查不合格处理:若发现产品有不合格时,知会生产,对其不合格产品进行隔离,加红色拒收标签标识清楚不良原因,按《不合格品控制程序》规定进行处理。
5.2制程检验5.2.1检查标准依《SMT外观检验标准》5.2.2检验方式/要求a.佩戴防静电手环或防静电手套。
b.使用放大镜、显微镜、万用表、电子负载、恒流源、保护板测试仪等检验仪器。
c.目视外观时采用由上而下、由左而右,从90度、45度等多视角进行外观检验。
d.若发现不良缺陷,在不良缺陷处或不良品上贴上红色不良箭头标签。
e.检验项目及标准:检验依照《SMT外观检验标准》、《保护板性能测试QC作业指引》、《承认书》内容及受控样板标准检验。
f.异常反馈/处理:抽检中如果发现有严重品质异常和品质隐患时,必须及时向PQC/生产班长反馈,组织相关部门人员现场分析改善,品质部门进行记录与追踪结果确认。
检验管理程序(含表格)

检验管理程序(ISO9001-2015)1. 目的:为使产品实现的每个过程得到有效控制,满足产品和客户的要求。
2. 范围:含进料检验、制程检验、成品和出货检验。
3. 定义:检验:在使用规定的方法和准则,对产品进行的检查、确认的过程。
4. 流程:见附件5. 作业内容:5.1供方交货:供方按照采购部的《订货单》的要求如期交货。
如有要求附带《材质证明》或《检验报告》一并和本批次材料交货。
5.2进料检验:5.2.1品管员依据《检验规范》、图纸和《抽样检验标准》对来料进行检验。
并将检验结果记录在《进料检验记录表》中。
5.2.2进料检验结果的判定依据《检验规范》的要求和《抽样检验标准》的允收范围,以及区分缺陷的轻重,和实际组装检查结果来综合判定。
判定合格品以《合格品标示卡》标示。
5.2.3进料检验的其它方法:5.2.3.1如在需要的时机,客户到供方实地确认,判定结果依据客户的要求。
或者品管部派品管员到供方实地检验,对材料或产品进行确认,并记录于《进料检验记录表》中。
5.2.3.2如果有的材料需要对其功能、材质等方面的验证,可以由具有国家认可的实验室出据检验报告,作为验收的依据。
5.2.3.3如材料无法在收料时间内作出准确的判定,品管员有权对该批材料暂收,暂收后在24小时内对本批材料作出判定。
5.2.4材料的放行规定:5.2.4.1任何未经品管部检验的材料或零部件,任何单位不得私自取用生产。
5.2.4.2只有经理级别人员方可在生产紧急情况下有权对材料特殊放行,但必须在《进料不合格处理单》上备注并签字,以示负责和追溯。
5.3进料不合格处理:5.3.1当来料不良时,品管员用《不合格品标示卡》标示隔离,并按照《不合格品管理程序》处理。
5.3.2纠正和预防措施:出现品质异常时,供方在《进料不合格处理单》中回复发生原因和改善措施,在规定的时间内回传品管部,以作品质改善的追踪。
5.3.3如客户投诉品质问题属于供方原因造成,则向供方追缴因品质问题而发生的有关费用。
过程、成品检验管理流程表模板
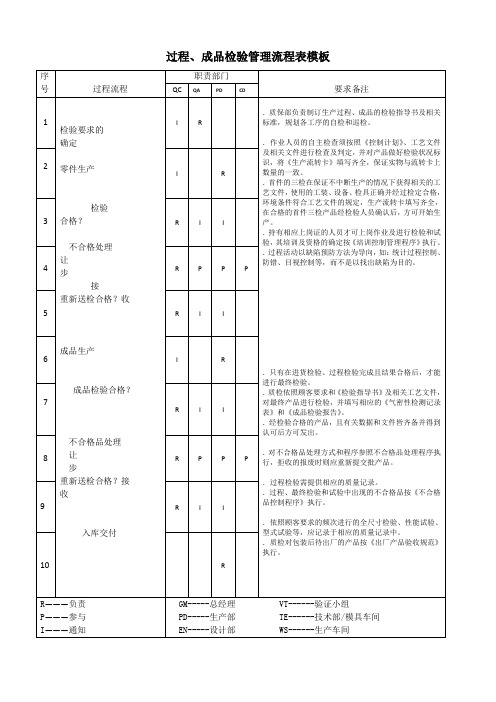
10
R
R———负责
P———参与
I———通知
GM-----总经理VT------验证小组
PD-----生产部TE------技术部/模具车间
EN-----设计部WS------生产车间
.首件的三检在保证不中断生产的情况下获得相关的工艺文件,使用的工装、设备、检具正确并经过检定合格,环境条件符合工艺文件的规定,生产流转卡填写齐全,在合格的首件三检产品经检验人员确认后,方可开始生产。
.持有相应上岗证的人员才可上岗作业及进行检验和试验,其培训及资格的确定按《培训控制管理程序》执行。
.过程活动以缺陷预防方法为导向,如:统计过程控制、防错、目视控制等,而不是以找出缺陷为目的。
.只有在进货检验、过程检验完成且结果合格后,才能进行最终检验。
.质检依照顾客要求和《检验指导书》及相关工艺文件,对最终产品进行检验,并填写相应的《气密性检测记录表》和《成品检验报告》。
.经检验合格的产品,且有关数据和文件皆齐备并得到认可后方可发出。
.对不合格品处理方式和程序参照不合格品处理程序执行,拒收的报废时则应重新提交批产品。
.过程检验需提供相应的质量记录。
.过程、最终检验和试验中出现的不合格品按《不合格品控制程序》执行。
.依照顾客要求的频次进行的全尺寸检验、性能试验、型式试验等,应记录于相应的质量记录中。
.质检对包装后待出厂的产品按《出厂产品验收规范》执行。
2IBiblioteka R3RI
I
4
R
P
P
P
5
R
I
I
6
I
R
7
R
I
I
8
R
P
P
P
9
制程及成品检验管理程序(含表格)

制程及成品检验管理程序(IATF16949/ISO9001-2015)1、目的为确保生产制程及成品的质量能有效管理,以满足客户要求,特制订本程序。
2、范围适用于本公司生产现场所生产之半成品、加工品、成品等检验的管理。
3、术语和定义 (无)4、制程及成品检验管理过程乌龟图制程及成品检验管理过程过程输出/Process output1、已检/试验的产品2、检验/试验记录3、不合格品的处理记录4、纠正预防措施处理单过程输入/Process input 1、检验规范 2、控制计划3、图纸4、样件5、抽样接收准则 过程衡量指标/Process measurement indicator: 1、漏检率如何做(方法, 程序, 技术)/how to do(method, procedure, technology): 1、制程及成品检验管理程序 2、产品标识与追溯程序 3、不合格品管理程序 4.纠正与预防措施程序使用资源/Resource1、监视测量2、检验场地3、检测室过程拥有者(责任者)/Process owner:1、质量管理部部长5、 工作流程和内容编号 作业流程图权责部门/人作业要求 使用表单5.1制造部班/线长 5.1生产前对来料进行确认,确认内容包括:零部件/半成品种类,质量状况,外观,数量等相关信息 5.2制造部5.2.1首件生产时间: a.每日刚开始生产时;b.换机、换人、换产品生产时。
c.修机、异常处理后重新生产时。
5.3制造部5.3.1 自检负责人:线组长/线组长指定的员工 5.3.2首件生产完后依照工艺卡执行首件自检,并按照要求填写自检记录 5.3.3 自检不合格执行《不合格品管理程序》 5.3.4自检合格交与质量管理部进行首件确认5.3.5 质量管理部在首件确认前,制造部不得进行批量生产《自检记录表》5.4质量管理部 5.4.1首件确认人员可包括:巡检员/下线检验员/质量工程师5.4.2首件确认人员胜任要求:对产品故障模式熟悉,对产品的质量要求非常熟悉,了解产品市场故障动态5.4.3质量管理部在执行首件确认后务必按实填写《巡检表》中的首件确认栏5.4.4首件确认合格后通知制造部投入批量生产,并做好《首检合格标签》,在生产线指定区域悬挂首件,当班生产完成,首件随当班产品入库。
PQC制程检验作业指导书(含表格)

PQC制程检验作业指导书(ISO9001:2015)1. 目的:为明确制程检验PQC的工作职责与权限,提高检验人员的工作能力及工作效率,以利于更好的对产品制程质量作管控。
2. 适用范围:2.1 首件检验。
2.2 制程巡检。
2.3 退料检验。
2.4 异常及数据处理。
3. 名词定义:3.1 不合格:不符合规定之要求。
4. 管理重点:4.1 首件检验:4.1.1 生产线于规定的时间内完成首件制作并开立送验单交 PQC 人员进行检验。
4.1.1.1 插配线:新机种前三批送首件且于上线后30分钟内送出。
4.1.1.2 装配及合并线须每批送验且于上线前1H送出。
4.1.2 PQC人员于首件检验前工作:4.1.2.1 核对生产排程并确认该线生产机种须与排程相符。
4.1.2.2 从工程部借出该机种的BOM,从品保部借出该机种的QC工程图,并查阅该机种质量检验规范、及相关的工程变更、技术指令、工程图面等相关数据,并对上述资料作详细了解。
4.1.2.3 依据(2)项资料对生产线各站别材料之规格、版本、SOP及有变更后之材料做确认.4.1.2.4 接到首件后并依之进行检验4.1.3 进行检验:4.1.3.1 依“检验记录表”及首件,确认“检验记录表”所填写的机种名称、品号、批号等内容必须正确,否则退单给生产线更正。
4.1.3.2 依BOM确认首件所用各种包装材料、附件、说明书、保证卡等材料的规格、版本是否正确,如有:错、漏、多、少等仍一不良则判定NG。
4.1.3.3 依质量检验规范检验首件的外观、实际各项功能做检测,以确保质量能符合产品规格要求。
4.1.3.4 将各项检验的结果如实、客观、正确地填写在“检验记录表”上,并作出综合判定。
4.1.3.5 将判定结果告知生产线线长(如NG则需和线长当面确认),并会签认可。
4.1.3.6 PQC首件检验须在1H内完成并送审单位主管。
4.1.4 判定及处理4.1.4.1 若判定OK,生产线即可进行量产。
制程检验管理作业程序

制程檢驗管理作業程序
文件編號:
SV-28-04
制訂部門:
品保部
制訂日期:
20070305
文件制修訂記錄
發行日期
修訂申請書編號
制修訂內容
修訂頁次
版本
01
02
03
04
05
06
07
08
09
10
核准
審核
制订
發行章
注:每次文件修訂,請文管中心將修改位置、主要修改內容予以記錄,以便對照使用。
1.目的:
確保所有在制程中的產品,都符合標準或客戶需求,防止不良品流至下工序而影響最終產品之品質。
2.範圍:
適用於公司產品之各生產制程檢驗。
3.定義:
無。
4.權責:
制程中檢驗執行:品保人员;
5.作業內容:
5.1批量生產前,作業人員依作業標準書核對,第一批產品進行自主檢查後交由現場管理人員和品保IPQC做首件確認,首件確認內容包括物料料號核對、各工序組裝之正確性、成品外觀,尺寸,光學檢查,確認完畢後填寫〖首件確認記錄表〗,前5pcs檢驗OK後方可批量生產,若是新產品還必須同時由製造、品保、工程人員一致確認OK後方可生產; IPQC之檢驗結果記錄,分白班,夜班進行;品保人員於每次交接班時需填寫當日制程情況於〖交接班通知單〗,交予接班人知悉。
5.3製造部作業員對其生產出的成品進行自檢後,再由品保FQC人員進行全檢,檢驗結果記錄
于〖FQC检验报告〗中.
6.相關文件:
6.1【制程管理作業程序】SV-27-07
6.2【矯正與預防措施管理作業程序】SV-28-10
6.3【不合格品管理作業程序】SV-28-06
6.4【品質記錄管理作業程序】SV-24-02
制程管理程序(含表格)

制程管理程序(IATF16949-2016)1.0目的为了使生产有序进行,协调各部门之间相互关系,使部门之间能相互协作,提高产品质量和劳动生产率。
2.0适用范围适用于本公司产品实现过程中从原材料到成品出货的全过程。
3.0职责3.1生产部负责整个生产过程的调度,对计划任务的安排,对工艺、技术要求的具体执行。
3.2品质部负责对生产过程进行测量、监督、指导。
3.3行政人事部负责生产过程中人力资源进行控制。
3.4物料部负责确保零配件和材料供应满足生产需求。
3.5工程部负责对产品加工工艺的设定及标准的制定。
4.0定义(无)5.0工作程序5.1生产准备5.1.1合同评审后,市场部向生产部下达《工程单》。
除了生产计划或指令外,控制计划,制程控制是制程控制的重要文件,相关的制程必须有相应的控制计划并按其执行.作业指导书:操作人员应严格按照作业指导书的要求进行作业,特别是规定的特殊特性.5.1.2生产部依据《工程单》作出实际生产计划、安排生产。
确认物料、辅助材料工装夹具是否齐备,如库存不足时,应及时向采购部提出申请,填写《申请采购单》,物料购根据《采购管理程序》进行作业。
5.1.3生产部应对工程图纸设计合理性进行确认,如对其设定的工艺或标准产生质疑,或自身工艺无法满足时,需马上向工程部提出工程变更申请,经工程确认后进行变更,确保生产的及时进行。
5.1.4生产部根据图纸的特性对测量系统进行分析,确认测量系统(量、检具)是否可以满足生产的需求,如无法满足时,则需及时向采购部出申请,填写《请购单》,采购根据《采购管理程序》进行作业。
5.1.5生产部在生产前,须对生产的相关人员开展以下工作:a.按《工程单》的要求领取生产所需物料(包括相关的模具)。
b.生产部负责人依据生产所需的技朮资料,就生产过程中的操作问题向生产班长或作业员讲解说明和指导,以保证每个工序的作业人员清楚了解本岗位(工序)的作业要求。
c.技术员或操作员须针对生产所需的设备、工具仪器等做好保养工作,并将保养状况记录在相关设备的《设备保养记录表》中。
制程检验作业流程(附表单)

制程检验作业流程(附表单)说明:1.此⽂件为正式运⾏⽂件,该⽂件负责部门为品质部,其主要职责是维护该⽂件的运⾏、检查、培训指导、问题点收集、处理;2.运⾏过程中若同公司旧⽂件有冲突时,⼀律依本⽂件执⾏。
⽂件编制/更改⼀览表版本编制/更改内容⽇期编制/更改⼈ A/0 ⽂件运⾏评审栏会签市场部研发部设计部⾃控部资料室采购部⼈⼒资源部仓储部⽣产部 PMC部品质部战略发展部财务部项⽬部电⼯部售后服务部制定:审核:审批:1.0⽬的保证产品品质在制造过程得到有效控制,确保产品满⾜规定的要求,防⽌不合格品流通,减少⽣产返⼯及产品报废,特制定本流程。
2.0适⽤范围适⽤于产品从原料投放、加⼯制作到完⼯出货全过程的检验和测量控制。
3.0职责3.1品质部:负责制程品质的检验和制程品质管控,负责相关品质检验数据的记录和统计分析,负责品质责任认定和责任追究,负责品质改善监督和进度跟进。
3.2⽣产部:负责制程品质的⾸末件检验、报检、⾃检、互检、巡检及品质异常的反馈和处理。
3.3其它部门:负责协助品质部和⽣产部按本流程执⾏相关作业。
4.0作业程序4.1关键⼯序的识别在以下情况时,应对其作为关键或特殊⼯序予以识别和对待:4.1.1⼯序的结果不能通过其后的检验和试验完全验证,或者加⼯后⽆法测量或需要实施破坏性实验才能得出结果;4.1.2⼯序对最终产品的安全质量、主要性能有重⼤影响。
4.2⾸件检验4.2.1各车间各⼯序依据⽣产排期计划、⼯艺流程、作业指导书、产品图纸、品质标准等进⾏⾸件检验。
4.2.2必须进⾏⾸件检验的⼯序:机加件(如挂具、挂钩、齿轮、轴承、研发样件)4.2.3上述⼯序出现以下情况时必须进⾏⾸件检验:开⼯⽣产时、更换⼯件、换料、换模、修模、设备维修、更换⼯装夹具、⽣产⼈员变更、加⼯⽅法变更及其它需要⾸检的情况。
4.2.4各⼯序/机台操作员根据⽣产排期计划及对应的加⼯⼯件的⼯艺流程、作业指导书、产品图纸、品质标准等进⾏⾸件⽣产,经⾃检合格后向品管送检。
制程检验控制程序2-013(非常详细-附有流程图)

5.1首件确认时机
新产品生产、产品间断性生产、换材料、换人、机器故障、更换机台.
5.2首件品生产
5.2.1生产部门在生产首件品时,至少提前半小时完成首件品的生产并认真对首件品进行自检,确认OK后,再填写《IPQC首件检查项目表》.最将《IPQC首件检查项目表》和首件确认品交IPQC进行品质确认,
1.0目的
对整个制程中产品质量进行有效控制,确保生产顺利进行和确保产品质量符合客户的要求。
2.0范围
适用于本公司制程品质检验作业.
3.0职责
3.1 IPQC:首件确认、制程巡检、品质判定、作业指导、异常分析及反馈与跟踪、检验结果记录.
3.2 FQC: 对产线完成品进行全检作业.
3.3 Q E:制定或修订产品检验标准、制程品质异常分析、异常跟踪及作业指导。
5.3.2因部分产品需做特性测试,试验时间较长而影响生产, IPQC需及时向部门领导反映,征得同意后方可通知生产部门量产,若试验结果NG,IPQC应及时要求生产部门停止生产并对已生产的产品标识隔离.
5.3.3确认项目:材料/加工工艺/ 尺寸/外观/特性/包装等方面进行品质确认,及时发现问题,避免在量产时造成批量性的不良.
5.7制程异常的追踪确认
针对在巡检中所发现的不良品或不良批次,IPQC除标识隔离外,还需对不良品的流向及处理方式进行追踪确认,对责任单位回复的《制程品质异常报告》进行确认,(如原因分析是否正确,改善对策制定是否合理等),若回复不符要求则退回责任单位重新分析,责任单位在改善过程中IPQC应进行全程跟踪验证.
5.10制程中发现原材料不良之处理方式
上线前若生产部门发现材料不良情形,生产部应及时反馈给制程IPQC确认,在生产过程中生产单位及时发现原材料不良问题,应及时通知现场IPQC确认,此时IPQC需对已做好的半制品或成品进行标识隔离,同时品保部需发出《制程品质异常报告》给生产单位,同时品质部需及时通知IQC对此款材料的库存进行品质再确认,经确认在库材料不良,需标识隔离,同时品质部需及时开出《制程品质异常报告》知会相关单位和通知供应商改善。
制程检验控制程序(含表格)

制程检验控制程序(IATF16949-2016/ISO9001-2015)1.0目的:通过对制程检验与测试进行管制,确保产品在制程中处于受控状态,使产品品质满足规定要求。
2.0范围:适用于生产过程中的所有产品的品质控制。
3.0术语和定义:3.1检验:通过观察和判断,适当时结合测量、试验所进行的符合性评价。
3.2首件检验:对批量加工的第一件产品所进行的自检和检验员专检的活动。
3.3首件鉴定:对试生产的第一件(批)零部(组)件进行全面的过程和成品检查,以确定生产条件能否保证生产出符合设计要求的产品。
3.4首末件检查:将上一张/批生产任务单最后生产出的产品与同一条件下生产出的本张/批任务单的第一件产品进行对比确认。
3.5 巡检:在生产线经首检确认后正式生产中,指定巡检者对生产线上所有工序中的产品依据检验规范所做的重要质量特性及其参数的例行检验,并做好相关记录。
3.6不合格品:不符合顾客要求和规范的产品或材料。
3.7可疑的产品或材料:任何检验和试验状态不确定的产品或材料。
3.8计数型数据:可以用来记录和分析的定性数据。
计数型数据通常用合格或不合格的形式收集。
3.9计数型量具:就是把各个零件与某些指定限值比较,如果满足限值则接受该零件否则拒收。
4.0职责和权限:4.1归口管理部门:4.1.1品质管理中心:1)负责根据顾客的品质要求,制定相关产品的检验标准或规范。
2)负责按检验标准或规范对在制品进行检验和判定。
3)负责各制程不合格异常产品的追踪处理和效果验证。
4)负责产品申请紧急放行时的审批。
4.2相关责任部门:4.2.1生产制造中心:1)负责按工艺要求对产品进行制造。
2)负责对制程中不合格异常进行原因分析并提出纠正及预防措施。
4.2.2工程研发中心:1)负责根据顾客要求的品质及工艺,制定产品工艺参数和操作指导书。
5.0工作内容:5.1工作流程:无5.2工作说明:5.2.1通则:1)汽车产品,计数型数据抽样计划的接收准则必须是零缺陷(即C=0)。
制程检验管理程序

文件编号
FY-QP-19
文件名称
制程检验管理程序
页 码
1/2
版 本
A/0
1.目的:
为了使制造过程中之产品检验有章可循,保证检验工作的有效性.
2.范围:
制程中的在制品、半成品之检验。
3.权责:
3.1生产部负责自检工作,并同品质部一道做好首件检查.
3.2品质部负责首件检查、巡回检查、半成品的检验。
xxx有限公司
文件编号
FY-QP-19
文件名称
制程检验管理程序
页 码
2
生产部组作业员要在生产中进行自主检验.,将自主检验的结果记入“生产检查表”中.自主检查中作业员如发现产品质量异常时,应及时停止作业,并向组长报告,寻求改善对策.
5.1.3巡回检验
a.每2H由IPQC负责抽检一次,每次每台机抽2PCS进行尺寸,10PCS进行外观检验,并将检验结果记录于《IPQC巡检报告》中。尺寸判定标准为AC:0,RE:1,外观判定标准为主要缺陷和严重缺陷AC:0,RE:1,轻微缺陷AC:1,RE:2。巡查中发现的不合格品应做好标识并隔离。
e.制程中的不合格品按《不合格品管理程序》处理。
6.参考文件:
6.1不合格品管理程序
6.2 抽样计划规范
7.品质记录:
7.1首件确认表
7.2《IPQC巡检报告》
7.3生产检查表
7.4纠正和预防措施报告
8.附件:
无
4.定义:
无
5.作业程序:
5.1过程检验
5.1.1首件检查
a.在转换新产品、换模、换料、换机、修模或修机时,需作首件确认。
b.生产单位负责初步确认并填写《首件确认表》后将自检OK品1-3PCS送QC做首件检查,首件检查结果记录于“《IPQC巡检报告》”中。
制程检验管制程序

1.目的本标准对公司的生产过程检验作业给以体系化规定,以提高检查效率,保证制程品质稳定。
2.范围本标准适用于公司生产产品检验作业。
3.权责3.1品保首、末件检验、制程巡检、异常处理。
3.2仓库3.2.1负责各项物料于搬运、储存、包装、保存与交货中均能以妥善之方式作业。
3.2.2依材料放置区存放及标示清楚,并做先进先出之领料作业。
3.3生产部3.3.1生产符合规格的产品。
3.4 工程部3.4.1以品质、效率为中心设计出正确的工艺。
3.4.2督促作业员按照工艺要求进行作业。
4.定义4.1首件检验:调机、换线、更换材料、白夜班切换条件下对机台首模生产出来的产品进行确认的检验动作。
4.2巡回检验:依据QC工程图所定义的频率对生产各工序依对应之SIP、图纸、限度样品进行尺寸检查、外观检验。
4.3末件检验:调机、换线、更换材料、白夜班切换条件下对机台末模生产出来的产品进行确认的检验动作。
5.作业内容5.1作业流程图:(附件一)5.1.1首件检验5.1.1.1首件检验:调机、换线、更换材料、白夜班切换后作业员取首模生产出来的产品对照《SOP》进行自检,经当班生产负责人确认后送样给品保课IPQC进行首件确认,产品尺寸按照工程图纸上标注的尺寸来进行测量,并将检验结果记录于《首末件检验报表》内,首件确认OK后生产方可批量进行生产。
5.1.2制程巡检5.1.2.1制程巡检:按照《QC工程图》定义的频率进行每日定期对重要制程之在制品检验其品质是否符合规格进行制程巡检(一般为2小时一次)。
每次数随机抽取5pcs进行检验。
外观要求全检,产品尺寸的确认必须测量到每一个模穴。
将检验结果正确记录于《IPQC巡检记录表》。
5.1.3末件检验生产完成后作业员取机台最后一模生产出来的产品对照《SOP》进行自检,经当班负责人确认后送样给品保课IPQC进行末件确认,检查合格后产品流入下道工序。
5.2制程条件确认作业5.2.1作业现场管理人员每天需对车间温湿度、洁净度作确认,发现异常时及时处理,IPQC监督执行。
制程检验管理程序
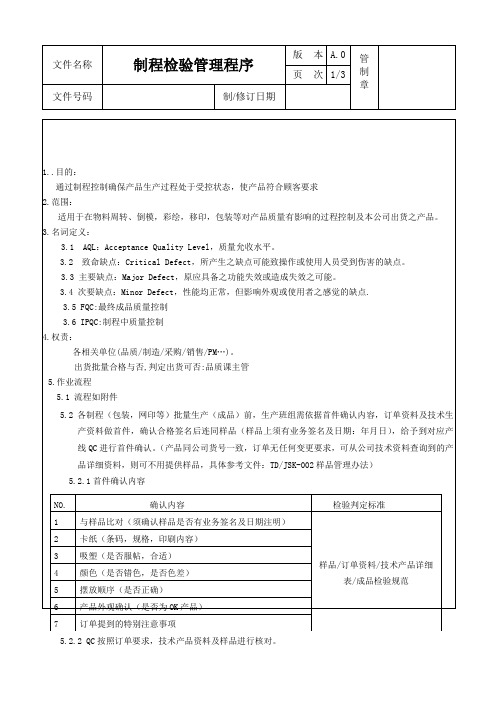
生产人员生产过程中应对产品进行自主检查,良品即流入次工程,NG品则注明并做好标识隔离(对于不良需另投入工时选别/返工则由制造班组长提出异常工时)
5.5 FQC最终成品管制检查:制造包装完成后成品FQC依成品检验规范进行检验,OK后入成品库房
5.5.1制造完工之成品,重工之成品按批量通知FQC检验
NO.
确认内容
检验判定标准
1
与样品比对(须确认样品是否有业务签名及日期注明)
样品/订单资料/技术产品详细表/成品检验规范
2
卡纸(条码,规格,印刷内容)
3
吸塑(是否服帖,合适)
4
颜色(是否错色,是否色差)
5
摆放顺序(是否正确)
6
产品外观确认(是否为OK产品)
7
订单提到的特别注意事项
5.2.1首件确认内容
5.5.2.FQC按以下表及<<成品检验规范>进行抽验
阶 段
批 量
Audit检验水平
试样
全 数 检 验(目前打样班执行)
进入量产,当良率达到96%时可依下面抽样计划进行抽检
量产
产量2h/LOT
外观依抽样计划GB/T 2828 II ,AQL:C=0,MAJ1.0.MIN:2.5(未包装)/4.0(已包装) 其他性能检测:GB/T 2828 II S-2 AQL 1.0
5.7.各项检查之不合格品,依不合格品管制程序进行之
5.7.1 生产之被判退批由产线安排人员进行处置(选别/返工),QC开出选别/返工费用表,并跟踪确认判退批是否按要求处置。
5.7.2 选别/返工全检出之良品,通知FQC,按原退货之项目抽验,合格后送后工程(包装)车间
(注:检出多少良品就送多少,不得补足原批量之数量)。
制程检验管理程序(含记录)
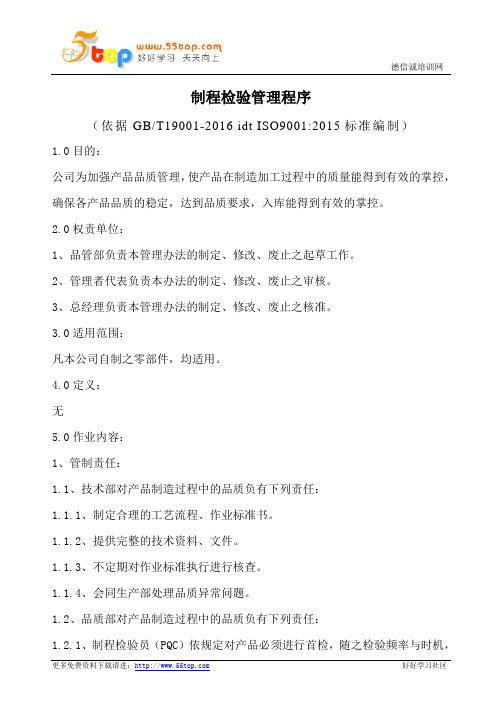
制程检验管理程序(依据GB/T19001-2016 idt ISO9001:2015标准编制)1.0目的:公司为加强产品品质管理,使产品在制造加工过程中的质量能得到有效的掌控,确保各产品品质的稳定,达到品质要求,入库能得到有效的掌控。
2.0权责单位:1、品管部负责本管理办法的制定、修改、废止之起草工作。
2、管理者代表负责本办法的制定、修改、废止之审核。
3、总经理负责本管理办法的制定、修改、废止之核准。
3.0适用范围:凡本公司自制之零部件,均适用。
4.0定义:无5.0作业内容:1、管制责任:1.1、技术部对产品制造过程中的品质负有下列责任:1.1.1、制定合理的工艺流程、作业标准书。
1.1.2、提供完整的技术资料、文件。
1.1.3、不定期对作业标准执行进行核查。
1.1.4、会同生产部处理品质异常问题。
1.2、品质部对产品制造过程中的品质负有下列责任:1.2.1、制程检验员(PQC)依规定对产品必须进行首检,随之检验频率与时机,对每一个工作环节进行逐一查核、指导,纠正作业动作,即实施制程巡检。
1.2.2、记录、分析全检站及巡检所发现之不良品,采取必要之纠正或防范措施。
1.2.3、及时发现显在或潜在之品质异常,并追踪处理结果。
1.3、生产部对产品制造过程中的品质负有下列责任:1.3.1、维护、保养设备与工装,确保正常动作。
1.3.2、不定期对作业标准执行与设备使用进行核查。
1.3.3、作业人员应随时自我查对,检查是否符合作业规定与品质标准,即开展自检工作。
1.3.4、下工程(序)人员有责任对上工程(序)人员之作业品质进行查核、监督,即开展互检工作。
1.3.5、本公司精加工车间应设立全检站,由专职人员依规定之检验规范实施全检工件,确保产品的重要品质项目符合标准,并作不良记录。
1.3.6、生产部各级管理应随时查核作业品质状况,对异常进行及时排除或协助相关部门排除。
2、制程检验工作程序:制程品质管制人员,也称PQC,其工作程序规定如下:2.1、制程检验员(PQC)人员应于下班前了解次日所负责之制造单位的生产计划状况,以提前准备相关资料。
制程检验管理程序

版本/次
A9
制程檢驗管理程序
頁
碼
第 1頁 共 3 頁
1. 目的﹕使本公司産品品質得到有效控制﹐防止制程中各工序的不良品流入
下一道工序。
2. 範圍﹕適用于本公司所有制程中的材料﹑半成品與成品。
3. 定義(無)
4. 權責
4.1 生産單位負責自主檢驗。
4.2 IPQC 負責巡迴檢驗。
5. 內容
5.1 流程圖(附件 1)
5.2 流程說明
5.2.1 IPQC 巡回檢驗
a.品保 IPQC 根據作業指導書等對生產之産品及制程進行檢驗﹐以達到及早
發現不良品與異常狀況﹔檢驗結果記錄在《IPQC 查檢表》上。
b. IPQC 巡檢員發現異常不良時﹐經生産班長確認後﹐如程度較輕﹐由巡
檢員直接記錄表中;如屬重大不良開出《不合格品處理單》或《品質異
7.3 《不合格品處理單》(不合格管理程序)
8. 附件﹕《流程圖》
程序文件
附件 1:
制程檢驗管理程序 流程圖
責任者
流程圖
版本/次
A9
頁)
生産
生産
生産 品保
生産
生産 品保 倉管
OK
NG
不合格品 處理
報廢申請
NG
巡檢
《IPQC 查檢表》
《不合格品處理單》
NG
自主檢驗
《品質異常改善 追蹤單》
管理程序》及相關作業指導執行。
5.2.6 制程檢驗中之不合格品按《不合格品管理程序》處理。
5.2.7 制程檢驗的記錄按《品質記錄管理程序》保存及管理。
5.2.8 不合格品的標識按《産品標識與追溯管理程序》實施。
5.2.9 制程中出現品質異常時﹐依據《矯正措施管理程序》執行。
- 1、下载文档前请自行甄别文档内容的完整性,平台不提供额外的编辑、内容补充、找答案等附加服务。
- 2、"仅部分预览"的文档,不可在线预览部分如存在完整性等问题,可反馈申请退款(可完整预览的文档不适用该条件!)。
- 3、如文档侵犯您的权益,请联系客服反馈,我们会尽快为您处理(人工客服工作时间:9:00-18:30)。
制程检验管理程序
(ISO9001:2015)
1.0 目的
确定制程检验程序,确保制程产品质量符合顾客要求。
2.0 适用范围
适用于本公司产品从样品到批量生产的整个过程。
3.0 职责
3.1 品质部
3.1.1 负责对品质问题进行审批、检查、总结和指示。
3.1.2 根据品质异常的状况,决定是否向责任部门发出《纠正和预防措施报告书》,并跟踪其执行和改善效果。
3.1.3 负责跟进生产过程中物料和工艺的更改。
3.2 品质部IPQC
3.2.1 IPQC负责各生产部门制程内半成品巡检,并填写检查记录。
3.2.2 品质部FPQC负责制程内工序转移中半成品的检查,并填写检查记录。
3.3 QE
3.3.1 根据各类记录汇总后编写品质周报、月报。
3.3.2 确保适当的SPC的采用。
3.3.3 《检验作业指导书》等标准和技术文件的编写。
3.3.4 组织和参加相关的品质会议,完善和维护制程内品质管理体系。
3.3.5 对产品品质问题及品质目标未达成时提出和建议解决办法。
3.4 各生产部门主管负责对应和改善制程内出现的品质问题。
4.0 定义
4.1 制程:指从原材料投入生产,至最终成品纳入的整个过程,不包括外发加工过程。
4.2 IPQC:In-Procedure Quality Control的缩写,即从事制程内检验的人员。
4.3 OQC:Outgoing Quality Control的缩写,即从事成品检验和出货检验人员的人员。
4.4 QE:Quality Engineer品质工程师,即从事与品质管理相关的工程技术人员。
5.0 工作程序
5.1 调机检查
5.1.1 生产部门调机员调机过程中和调机完成后,须对调机产品进行初步检查,并将所有调机不合格产品放置在红色胶盆里,与待检品、OK品明确区分开,并标识清楚。
5.1.2 调机员或操作员自主检查合格后,应通知品质部IPQC作首件检查。
5.2 首件检查
5.2.1 IPQC抽取第1件样本作首件检查,检测数据记录于《首件检查记录》中。
5.2.2 通过IPQC首件检查确认合格后,生产部门才可安排批量生产。
5.3 制程巡检
5.3.1 在正常量产过程中,IPQC按照工序流程的要求,对半成品进行抽样检查。
5.3.2 IPQC的检查频度为每1个工作时巡检一次,各部门可视实际需要加严调整检查频度。
每次抽检2个样品,对于重要尺寸和不稳定机床,应增加抽检频度和数量。
5.3.3 检测数据和判定结果记录于《巡检记录》中。
5.3.4 经检验不合格,执行《不合格管理程序》。
5.3.5 IPQC七大职能:
a. 立即停止生产:当发现的错误导致连续不断生产不良时,先要求关机、后通报。
b. 要求立即改正:当发现违反指导书或操作工艺的情况时,就地要求改正。
c. 要求限期改正:过程参数不良,控制图显示有问题时,要求限期改正。
d. 警告:偶尔违反操作规程,但未造成不良时,发出警告。
e. 发行《纠正和预防措施报告书》:对于前三种情况出现时必须发出。
f. 跟踪效果:于采取措施后的适当时间进行结果和效果的确认。
g. 通报反馈:将措施事项向上级或关联部门反馈和通报。
5.4 操作员自主检查
5.4.1 操作员应协助IPQC对一些重要尺寸作自主检查,在发现问题后,应及时向生产部门调机员或主管和IPQC反映。
5.4.2 操作员将一个转移箱中的产品加工完成后,必须按规定要求如实填写《产品工艺流程卡》中相应内容,调机员或主管对操作员的填写内容进行核实。
5.5 品质部转移检查
5.5.1 需转往下个部门或工序进行后续加工的产品,应该经过IPQC作转移检。