刀具文献摘要
车刀上的负倒棱论文:浅谈车刀上的负倒棱

车刀上的负倒棱论文:浅谈车刀上的负倒棱摘要:通过对刀具负倒棱的详细分析,逐步找出一种最好效果的负倒棱,来增加刀刃强度和提高刀具耐用度,从而提高生产效率和增加经济效益。
关键词:车刀;负倒棱;分析;利用“车工七分刀具,三分操作”这句话说明了刀具在车床切削加工中的重要地位。
下面就车刀上常被我们忽视的一个要素——负倒棱作如下分析。
一、负倒棱在车刀上的作用当我们用硬质合金车刀车削钢件等塑性材料时,为了保证切削顺利进行,切屑能自行断落,一般在前刀面上磨有断屑槽,则刀刃处前角有15°左右,而其后角又在6°左右,构成的楔角为β0=90°-(15°+6°)=69°(如图1)。
根据硬质合金材料的特点,抗弯强度只有高速钢的1/3~1/2左右,韧性差(约为淬火钢的30%~50%),刃磨时刀口处极易崩刃。
如何解决崩刃问题呢?有人认为增大楔角,把车刀磨成零度前角(如图1b),但其切屑呈长条状排出,极不安全。
把车刀磨负前角,使刀刃强度大大提高了,但切削力和切削热也大大增加。
现采用综合办法,在磨断屑槽车刀的刀刃上磨一窄小负前角平面,因在刀刃处,我们把他称为倒棱。
由于倒棱前角取副值故又称负倒棱。
这样切削力增加甚少,而刀刃强度和散热能力大大提高,刀具耐用度可提高几倍和几十倍,这就是负倒棱的作用(如图2)。
二、负倒棱的刃磨有了负倒棱的存在,能解决前后刀面交界刃口崩刃,对刀具刃磨就方便多了。
原主切削刃是磨前刀面和后刀面以后二刀面相交自然而形成的。
这就要求前刀面和后刀面仔细刃磨,但切削刃仍难保证平直,其粗糙度更难以保证,在放大镜下甚至目测都可以看到刃口上的锯齿状这对切削十分不利,刀具形成早期磨损和刃口崩裂,影响加工工件的表面质量,有了负倒棱后,刀具前刀面和后刀面要求可适当降低,由于负倒棱面积很小,所以可仔细修磨,能保证很高表面质量。
三、负倒棱的受力分析以图1a为例,当γ=15°,α0=6°,其角β0=69°,切削时,刀刃部位承受的是弯曲应力。
刀具材料PCD

XX大学2014~2015 学年秋季学期研究生课程考试课程名称:课程编号:论文题目:刀具材料PCD概述研究生:学号:论文评语:成绩:任课教师:评阅日期:刀具材料PCD概述摘要:好的刀具材料是制造出好的刀具的前提,更是加工出好的产品的关键。
随着制造业的快速发展,金刚石刀具的生产和应用正在逐年增加。
天然金刚石价格昂贵,金刚石广泛应用于切削加工的还是PCD。
本文针对刀具材料PCD做了比较系统的论述,主要包括PCD材料的介绍,PCD复合片及刀具的制造技术,PCD 复合片的主要优缺点以及PCD刀具材料的应用。
关键词:PCD;材料;刀具The overview about cutting tool materials of PCDAbstract:Good tool material is a prerequisite to create a good tool, it is also a key processing of making a good product .With the sharp development of making industry, production and application of diamond tools is increasing year by year.Natural diamonds are expensive,PCD is widely used in cutting .This paper makes a systematic introduction of tool material PCD,including the introduction of PCD materials ,the manufacturing techniques of PCD composite sheet and tool, the main advantages and disadvantages of PCD composite sheet materials and the application of PCD tools.Key words:PCD;Materials ; Tool1引言随着人类生活、生产水平的提高,高速钢刀具已不能满足高加工效率和高加工质量的新要求。
中国最早车床刀具汇编

中国最早车床刀具汇编摘要:1.中国古代车床刀具的发展历程2.车床刀具的类型及用途3.车床刀具的制作工艺与材料4.车床刀具在古代制造业中的重要地位5.车床刀具的传承与发展正文:中国古代车床刀具的发展历程车床刀具在我国历史悠久,可以追溯到新石器时代。
在那时,人们已经开始使用石头和骨头制作简单的刀具。
随着时代的发展,到了青铜器时代,人们开始使用青铜制作刀具。
在战国时期,钢铁冶炼技术逐渐成熟,钢铁刀具开始广泛应用。
秦汉时期,车床技术得到了进一步的发展,出现了专门用于制造刀具的车床。
到了明清时期,车床刀具的制作工艺已经相当成熟,种类和规格也越来越丰富。
车床刀具的类型及用途古代车床刀具有很多种类,如铣刀、钻头、锯片等。
铣刀主要用于铣平表面,钻头用于钻孔,锯片用于切割。
这些刀具在古代制造业中广泛应用,如木材加工、金属加工、玉器加工等。
车床刀具的制作工艺与材料古代车床刀具的制作工艺十分讲究。
首先要选择优质的钢材,经过反复加热、锻打、淬火等过程,使其达到所需的硬度和韧性。
然后进行打磨、开刃等工序,使刀具更加锋利。
最后,对刀具进行装配,确保其与车床的配合无误。
车床刀具在古代制造业中的重要地位在古代,车床刀具在制造业中具有举足轻重的地位。
它们的出现和发展推动了制造业的进步,提高了生产效率。
同时,车床刀具的质量直接关系到产品的质量,因此,刀具制作工匠的地位也相当高。
车床刀具的传承与发展随着现代科技的飞速发展,数控机床等先进设备逐渐取代了传统车床。
然而,古代车床刀具的制作技艺仍然具有很高的历史价值和文化价值。
硬质合金铣刀在铣削钛合金过程中的磨损实验研究

硬质合金铣刀在铣削钛合金过程中的磨损实验研究
卞航涛;方从富;林海洋
【期刊名称】《农业装备与车辆工程》
【年(卷),期】2024(62)3
【摘要】针对硬质合金刀具在铣削钛合金过程中容易失效而导致平均寿命低的问题,开发了0.5μm WC颗粒和12%Co配比的新型硬质合金材料刀具,与市场上2种主流刀具进行钛合金湿式铣削磨损对比实验。
根据拍摄的刀具前后刀面磨损形貌,
分析了3种刀具的失效形式及磨损机理。
结果表明,在铣削前期新型刀具圆周后刀
面呈现出均匀的磨损带,磨损以粘结磨损和磨粒磨损为主,在铣削后期出现裂纹、崩
缺等不均匀磨损;整个磨损过程主要经历初期磨损、稳定磨损和急剧磨损3个阶段。
与对比刀具相比,新型材料刀具平均寿命更高、抗崩性能更好、更利于钛合金的加工。
【总页数】5页(P131-135)
【作者】卞航涛;方从富;林海洋
【作者单位】华侨大学机电及自动化学院;厦门慧至拓数字制造技术研究院
【正文语种】中文
【中图分类】TG54
【相关文献】
1.TiAlN涂层硬质合金可转位刀具快速铣削钛合金刀片磨损研究
2.高效铣削钛合金涂层硬质合金刀具优选及磨损试验研究
3.TC18钛合金铣削加工专用硬质合金平底
立铣刀参数化设计4.铣削覆膜砂用微型硬质合金铣刀磨损规律的研究5.高速干铣削钛合金时涂层硬质合金刀具磨损机理研究
因版权原因,仅展示原文概要,查看原文内容请购买。
机械加工刀具发展现状与对策

机械加工刀具发展现状与对策浙江大学城市学院张润晨摘要:众所周知,机械加工离不开机床。
在目前的科技水平,机床又离不开刀具,刀具虽小,作用巨大。
随着科技的进步和生产的发展,机械产品金额机械制造技术的内涵正在不断地发生变化。
这对刀具的要求也越来越精密。
关键词:刀具;精密;涂层;发展我国的刀具制造业已有较长的历史,并已发展到相当大的规模,不仅有数量较多的专业刀具厂,而且还有大量的机械制造厂工具车间也生产刀具。
我国现在的生产总值和制造业规模,仅次于美国、日本,最近又超过了德国。
但是技术方面我们还差的很远,我们是要向德国学习的,不仅仅是学习他们的技术,最重要的是学习德国人严谨的思维和精神。
由于技术和材料的原因,我国年消耗刀具近20亿美元,其中很多都是浪费了的。
据估计,切削加工约占机械制造工作量的30%~40%,全世界每年约有1亿吨钢料通过刀具切削而成为切屑,全世界每年切削加工耗资约2500 亿美元。
与世界先进水平相比,目前我国的切削加工技术水平还是比较低,所以要努力研究和开发高速切削、硬切削、干切削、精密切削、虚拟切削等先进切削加工技术,还有新刀具的研发,这些对于提高我国机械制造技术水平和机电产品性能、质量及市场竞争力,推动先进制造技术的发展都具有重要意义。
目前我们学习的刀具主要有:车刀、刨刀、孔加工刀具、铣刀、拉刀、螺纹刀具、数控刀具、成形齿轮刀具、齿轮滚刀、加工蜗轮用刀具、插齿刀及梳齿到、剃齿刀、直齿锥齿轮加工刀具、曲线锥齿齿轮加工刀具、非渐开线齿轮刀具。
现在的数控加工主要有数控铣床和数控车床。
数控铣床的刀具种类有立铣刀、球铣刀、环形铣刀、机夹可转位铣刀。
数控车床一般都有自动回转刀架,,而且都采用6到12工位转塔式刀架。
数控车床的刀具一般分为三类,尖形车刀、圆弧车刀和成形车刀。
在世界切削刀具的近代发展中,上世纪70年代在西方广泛应用的硬质合金刀具方面发生了刀具结构与工艺的两次“革命”,一次起源于美国,将焊接刀片变革为机夹可转位刀片;另一次起源于欧洲,诞生了刀具涂层工艺。
关于对车刀几何参数的选择分析

关于对车刀几何参数的选择分析【摘要】刀具的几何参数对切削过程中的金属切削变形、切削力、切削温度、工件的加工质量及刀具的磨损都有显著的影响。
选择合理的刀具几何参数,可使刀具潜在的切削能力得到充分发挥,降低生产成本,提高切削效率。
【关键词】车刀;几何参数;选择车刀刃磨水平的高低直接关系到产品的生产效率、加工质量、设备能耗和产品成本,甚至关系到操作者的人身安全,也反映出操作者对加工主体的特性和切削用量的灵活应变能力。
合理选择车刀的几何参数是决定刃磨质量的关键,其主要体现于对车刀角度和前面形状的合理选择。
两者既相互依赖又相互制约,一把车刀不能只有一个角度,如果只有一个角度选择合理,它的切削效果也不一定理想,操作者必须根据工件材料、车刀材料、切削用量,以及工件、车刀、夹具和车床的刚性等各方面因素,全面分析,找出切削过程中的主要矛盾,合理选择车刀的角度和前面形状。
刀具几何参数包含切削刃的形状、切削区的剖面形式、刀面形式和刀具几何角度四个方面,这里主要讨论刀具几何角度的合理选择,即前角、后角、副后角、主偏角、副偏角及刃倾角的合理选择。
1.前角的选择前角r0是车刀切削部分的一个最主要的角度,车刀是否锋利主要取决于前角的大小。
一般增大前角时可以减小切削变形,减小切屑和前刀面的摩擦,使切削力降低,加工起来很轻快。
增大前角还可以使前刀面上承受切削力的位置后移,改善切削刃受力情况,同时还可以抑制积屑瘤的产生。
减小前角可增强刀尖强度,但切削变形和切削力都会增大。
前角的选择主要遵循以下原则:(1)加工塑性材料时,前角应取较大值;加工脆性材料时,应选用较小的前角;(2)工件材料的强度、硬度较低时,选用较大的前角;反之,选用较小的前角;(3)刀具材料韧性好时,前角应选大些,如高速钢车刀;刀具材料韧性差时,如硬质合金车刀;(4)粗加工和断续切削时应选较小的前角,横加工时应选较大的前角;(5)车床一夹具一工件—刀具系统刚度差时,应选较大的前角。
刀具几何角度对切削加工的影响及其选择
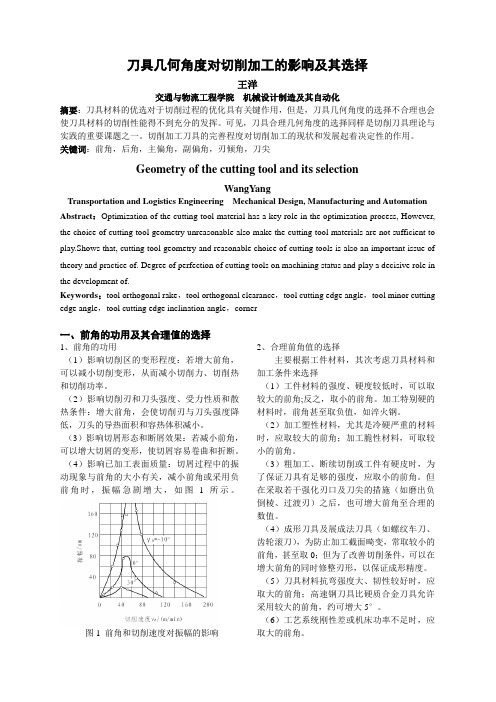
刀具几何角度对切削加工的影响及其选择王洋交通与物流工程学院机械设计制造及其自动化摘要:刀具材料的优选对于切削过程的优化具有关键作用,但是,刀具几何角度的选择不合理也会使刀具材料的切削性能得不到充分的发挥。
可见,刀具合理几何角度的选择同样是切削刀具理论与实践的重要课题之一。
切削加工刀具的完善程度对切削加工的现状和发展起着决定性的作用。
关键词:前角,后角,主偏角,副偏角,刃倾角,刀尖Geometry of the cutting tool and its selectionWangYangTransportation and Logistics Engineering Mechanical Design, Manufacturing and Automation Abstract:Optimization of the cutting tool material has a key role in the optimization process, However, the choice of cutting tool geometry unreasonable also make the cutting tool materials are not sufficient to play.Shows that, cutting tool geometry and reasonable choice of cutting tools is also an important issue of theory and practice of. Degree of perfection of cutting tools on machining status and play a decisive role in the development of.Keywords:tool orthogonal rake,tool orthogonal clearance,tool cutting edge angle,tool minor cutting edge angle,tool cutting edge inclination angle,corner一、前角的功用及其合理值的选择1、前角的功用(1)影响切削区的变形程度:若增大前角,可以减小切削变形,从而减小切削力、切削热和切削功率。
车刀的选择与使用
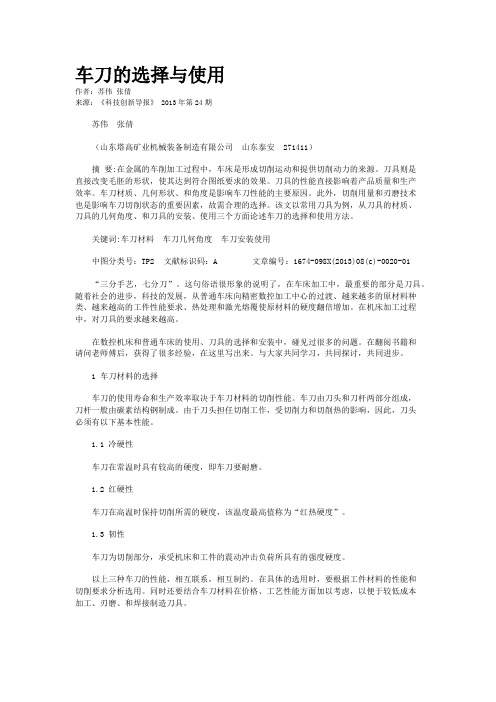
车刀的选择与使用作者:苏伟张倩来源:《科技创新导报》 2013年第24期苏伟张倩(山东塔高矿业机械装备制造有限公司山东泰安 271411)摘要:在金属的车削加工过程中,车床是形成切削运动和提供切削动力的来源。
刀具则是直接改变毛胚的形状,使其达到符合图纸要求的效果。
刀具的性能直接影响着产品质量和生产效率。
车刀材质、几何形状、和角度是影响车刀性能的主要原因。
此外,切削用量和刃磨技术也是影响车刀切削状态的重要因素,故需合理的选择。
该文以常用刀具为例,从刀具的材质、刀具的几何角度、和刀具的安装、使用三个方面论述车刀的选择和使用方法。
关键词:车刀材料车刀几何角度车刀安装使用中图分类号:TP2 文献标识码:A 文章编号:1674-098X(2013)08(c)-0020-01“三分手艺,七分刀”。
这句俗语很形象的说明了,在车床加工中,最重要的部分是刀具。
随着社会的进步,科技的发展,从普通车床向精密数控加工中心的过渡、越来越多的原材料种类、越来越高的工件性能要求、热处理和激光熔覆使原材料的硬度翻倍增加。
在机床加工过程中,对刀具的要求越来越高。
在数控机床和普通车床的使用、刀具的选择和安装中,碰见过很多的问题。
在翻阅书籍和请问老师傅后,获得了很多经验,在这里写出来。
与大家共同学习,共同探讨,共同进步。
1 车刀材料的选择车刀的使用寿命和生产效率取决于车刀材料的切削性能。
车刀由刀头和刀杆两部分组成,刀杆一般由碳素结构钢制成。
由于刀头担任切削工作,受切削力和切削热的影响,因此,刀头必须有以下基本性能。
1.1 冷硬性车刀在常温时具有较高的硬度,即车刀要耐磨。
1.2 红硬性车刀在高温时保持切削所需的硬度,该温度最高值称为“红热硬度”。
1.3 韧性车刀为切削部分,承受机床和工件的震动冲击负荷所具有的强度硬度。
以上三种车刀的性能,相互联系,相互制约。
在具体的选用时,要根据工件材料的性能和切削要求分析选用。
同时还要结合车刀材料在价格、工艺性能方面加以考虑,以便于较低成本加工、刃磨、和焊接制造刀具。
硬质合金刀具材料性能和特点
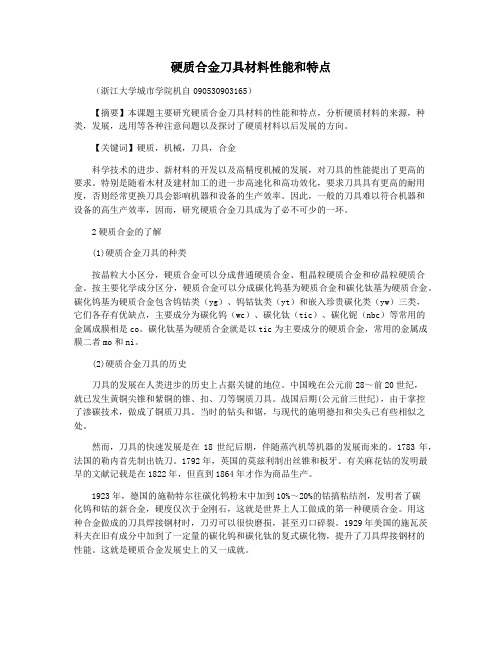
硬质合金刀具材料性能和特点(浙江大学城市学院机自************)【摘要】本课题主要研究硬质合金刀具材料的性能和特点,分析硬质材料的来源,种类,发展,选用等各种注意问题以及探讨了硬质材料以后发展的方向。
【关键词】硬质,机械,刀具,合金科学技术的进步、新材料的开发以及高精度机械的发展,对刀具的性能提出了更高的要求。
特别是随着木材及建材加工的进一步高速化和高功效化,要求刀具具有更高的耐用度,否则经常更换刀具会影响机器和设备的生产效率。
因此,一般的刀具难以符合机器和设备的高生产效率,因而,研究硬质合金刀具成为了必不可少的一环。
2硬质合金的了解(1)硬质合金刀具的种类按晶粒大小区分,硬质合金可以分成普通硬质合金、粗晶粒硬质合金和矽晶粒硬质合金。
按主要化学成分区分,硬质合金可以分成碳化钨基为硬质合金和碳化钛基为硬质合金。
碳化钨基为硬质合金包含钨钴类(yg)、钨钴钛类(yt)和嵌入珍贵碳化类(yw)三类,它们各存有优缺点,主要成分为碳化钨(wc)、碳化钛(tic)、碳化铌(nbc)等常用的金属成膜相是co。
碳化钛基为硬质合金就是以tic为主要成分的硬质合金,常用的金属成膜二者mo和ni。
(2)硬质合金刀具的历史刀具的发展在人类进步的历史上占据关键的地位。
中国晚在公元前28~前20世纪,就已发生黄铜尖锥和紫铜的锥、扣、刀等铜质刀具。
战国后期(公元前三世纪),由于掌控了渗碳技术,做成了铜质刀具。
当时的钻头和锯,与现代的施明德扣和尖头已有些相似之处。
然而,刀具的快速发展是在18世纪后期,伴随蒸汽机等机器的发展而来的。
1783年,法国的勒内首先制出铣刀。
1792年,英国的莫兹利制出丝锥和板牙。
有关麻花钻的发明最早的文献记载是在1822年,但直到1864年才作为商品生产。
1923年,德国的施勒特尔往碳化钨粉末中加到10%~20%的钴搞粘结剂,发明者了碳化钨和钴的新合金,硬度仅次于金刚石,这就是世界上人工做成的第一种硬质合金。
摘要分析当前各种刀具材料的优缺点

摘要分析当前各种刀具材料的优缺点回顾氮化碳的历史分析氮化碳涂层在刀具上应用的可行性通过研究氮化碳刀具的实用效果认为氮化碳刀具将具有广阔的应用前景。
机械加工中常用的刀具按材料分类有高速钢刀具、硬质合金刀具、氮化钛刀具、立方氮化硼刀具、金刚石刀具、陶瓷刀具等。
这些刀具材料各具优缺点不能完全互相取代。
对于硬质面的简单加工如车削可用硬质合金、立方氮化硼等刀具但对于形状复杂工件如齿轮等的硬质面加工硬质合金、立方氮化硼等刀具则无能为力需要寻求其它的加工手段如磨削、电火花加工等。
但这些加工方法加工效率低电火花加工更有成本高的缺点而且有些复杂工件无法采用上述方法如果找到一种方法使得刀具能够以切代磨则能大大提高工效降低成本。
1 氮化碳的历史和性能氮化碳是90年代初才出现的新型超硬材料。
80年代后期Cohen等人通过理论计算预言类似b-Si3N4结构的化合物b-C3N4可能具有超过金刚石的硬度此说立即引起国内外研究人员的广泛关注。
1993 年Niu首先宣布用激光烧蚀法得到了b-C3N4薄膜。
随后研究人员用电子回旋共振- 化学气相沉积ECR - CVD、热丝CVD、反应磁控溅射等方法成功合成了氮化碳薄膜。
合成的氮化碳薄膜的硬度也在不断提高。
日本的Fujimoto等用粒子束混合沉积法在碳化物衬底上形成的CNx膜硬度达到63GPa。
武汉大学自1994年起研究氮化碳的合成方法。
先后用射频CVD、磁控溅射等方法成功合成了氮化碳薄膜并研究了氮化碳薄膜在高速钢衬底上的镀膜工艺。
根据现有资料在刀具上镀氮化碳薄膜在世界上还是首次。
表1 各种材料硬度比较材料高速钢硬质合金TiN立方氮化硼金钢石氮化碳HRC 6266 7481 - - - - HV GPa 89 1318 21 47 800 50 氮化碳的超硬特性是其在刀具上应用的关键。
由表1可知将氮化碳镀在刀具表面将极大提高刀具的表面硬度。
氮化碳还具有较好的热稳定性。
用热失重TG- 差热分析DTA 研究氮化碳在室温至1200℃的热稳定性发现石墨相含量较小的样品在上述范围内无明显的热失重证明氮化碳薄膜具有较好的热稳定性见图1。
金刚石刀具

金刚石的刀具发展与技术侯文文0840202211摘要:本文主要对金刚石刀具的分类、加工方法、金刚石刀具的发展现状及应用领域作了简单的介绍,对聚晶金刚石刀具的刃磨技术作了详细的研究分析。
1、引言:随着现代加工制造业对高速切削加工的要求不断提高,对于各种难切削复合材料、工程陶瓷材料等,传统的切削加工刀具已不能满足高速切削的需要,而超硬切削刀具是解决以上问题的有效手段,其中,金刚石刀具的应用较为广泛。
金刚石具有极高的硬度、良好的耐磨性和导热性、低摩擦系数和热膨胀系数,在现代切削加工中体现出难以替代的优越性,被誉为当代提高生产率最有希望的刀具材料之一。
目前,金刚石刀具在机械加工中的应用日渐普及,已成为现代材料加工中不可或缺的重要工具。
2、金刚石刀具的基本介绍2.1 天然金刚石(ND)刀具为天然金刚石拉蔓峰谱,具有以下特征:(1)1332尖锋处显示存在金刚石。
(2)波型幅度(FWHM)为4.1cm-1显示为纯金刚石。
ND是目前已知矿物中最硬的物质,主要用于制备刀具车刀。
天然金刚石刀具精细研磨后刃口半径可达0.01~0.002µm。
其中天然单晶金刚石(Single Crystalline Diamond,SCD)刀具切削刃部位经高倍放大1500倍仍然观察到刀刃光滑。
SCD车削铝制活塞时Ra可达到4µm,而在同样切削条件下用PCD 刀具加工时的表面粗糙时的Ra为15~50µm。
故采用SCD刀具配合精密车床进行精密和超精密加工,可获得镜面表面。
2.2 聚晶金刚石(PCD)刀具PCD是高温超高压条件下通过钴等金属结合剂将金刚石微粉聚集烧结合成的多晶体材料,又称烧结金刚石。
聚晶金刚石刀具整体烧结成铣刀,用于铣削加工,PCD晶粒呈无序排列状态,属各向同性,硬度均匀,石墨化温度为550℃。
刀具具有高硬度、高导热性、低热胀系数、高弹性模量和低摩擦系数。
刀刃非常锋利等特点。
切削刀具的发展现状与趋势及对策
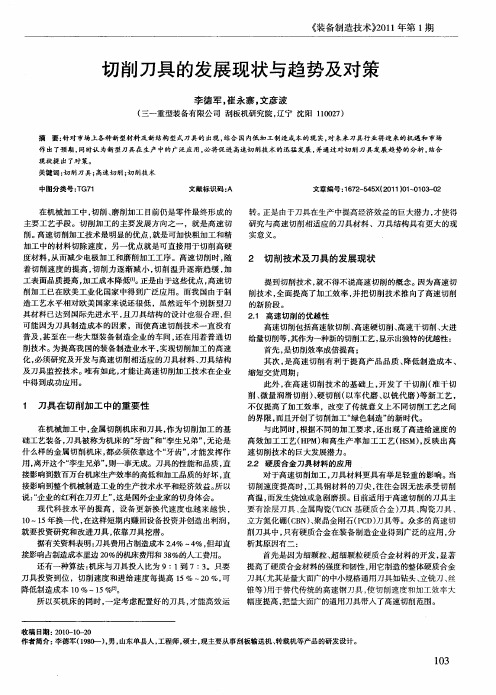
现代科 技水平 的提高 ,设 备更新换 代速度也越 来越 快 , 1 0~1 5年换 一代 , 在这样短期 内赚 回设备投资并创造 出利润 ,
就要投资研究和改进刀具 , 依靠刀具挖潜。 据有关资料表 明: 刀具费用占制造成本 2 % ~ % , . 4 4 但却直 接 影 响 占制造 成本 里 边 2 % 的机床 费 用 和 3 % ̄A3 费用 。 0 8 2 还有一种算法 : 机床与刀具投入 比为 9: 到 7: 。只要 1 3
削技术 。 为提高我 国的装备制造业水平 , 实现切削加工 的高速 化, 必须研究及开发与高速切削相适应 的刀具材料 、 刀具结 构
及 刀具监控技术 。 唯有如此 , 才能让高速切削加工技术 在企业
中得 到 成 功 应 用 。
1 刀具在 切 削加 工 中的重 要性
在机械加工 中, 金属切削机床和刀具 , 为切削加工 的基 作
刀具投资到位 ,切 削速度 和进 给速 度每提高 1 2 5% O%, 可
降低制造成本 1 ~1 0% 5%田 。
础工艺装备 , 刀具被称为机床 的“ 牙齿 ” 孪生兄 弟” 无论是 和“ , 什么样的金属切削机床 , 都必须依 靠这个“ 牙齿 ” 才能发挥作 ,
用, 离开这个“ 孪生兄弟 ”则一事无成 。刀具的性能和品质 , , 直
高效加工 工艺 ( P 和高生产率 加工工 艺 ( s , H M) H M) 反映 出高 速切削技术 的巨大发展潜力 。
高速切削包括高速软切削、 高速硬 切削 、 高速干切削、 大进 给量切削等 , 其作为一种新的切削工艺 , 显示出独特的优越性: 首先 , 是切削效率成倍提高 ; 其次 , 高速切削有利 于提高产 品 品质 、 是 降低 制造成本 、 缩短交货周期 ; 此外 , 高速 切削技术 的基础上 , 发了干切 削( 在 开 准干切 削、 微量 润滑切削 )硬切削 ( 、 以车代磨 、 以铣代磨 ) 等新工艺 , 不仅提高 了加工效率 ,改变 了传统意 义上 不同切削工艺之间 的界限 , 而且开创 了切削加工“ 绿色制造” 的新 时代 。 与此同时 , 根据不 同的加 工要求 , 出现了高进给速度的 还
木工刀具分析报告范文

木工刀具分析报告范文摘要本报告对木工刀具进行了详细的分析。
首先介绍了木工刀具的种类和用途,然后对其主要的组成部分进行了解析。
接着,对常见的木工刀具进行了分类和说明。
最后,还对木工刀具的选购和使用注意事项进行了介绍。
1. 引言木工刀具是木工在工作中必不可少的工具之一。
它们可以用来切割、刮削、雕刻和打磨木材等操作。
正确使用和选购木工刀具不仅可以提高工作效率,还能保证木工的安全。
2. 木工刀具的组成木工刀具一般由刀刃、刀柄和固定装置组成。
刀刃是木工刀具最重要的部分,它负责直接接触木材并完成切割和刮削等工作。
刀刃的质量和形状将直接影响木工的工作效果。
刀柄则用于握持刀具,在工作中提供稳定的控制和转动力。
刀柄材料一般选择木质或塑料,具有良好的手感和防滑性能。
固定装置则用于连接刀刃和刀柄,通常采用螺钉或胶水等方式进行固定。
固定装置的牢固性将直接影响刀具的安全和稳定性。
3. 木工刀具的分类根据用途的不同,木工刀具可以分为以下几类:3.1 锯类刀具锯类刀具主要用于切割木材。
常见的锯类刀具包括手锯、电动锯和链锯等。
手锯适用于小块木材的切割,电动锯和链锯适用于大块木材或需要快速切割的工作。
3.2 刨类刀具刨类刀具主要用于刮削木材表面,平整木材并去除不平整或粗糙的地方。
常见的刨类刀具有手动刨和电动刨。
手动刨适用于小块木材或需要精细刮削的工作,电动刨适用于大块木材或需要快速刮削的工作。
3.3 雕刻刀具雕刻刀具主要用于对木材进行雕刻和削减。
常见的雕刻刀具有尖刀、凿子和刨刀等。
这些刀具可以根据雕刻的需要选择不同的形状和尺寸。
3.4 打磨刀具打磨刀具主要用于打磨木材的表面,使其光滑。
常见的打磨刀具有砂纸、砂轮和砂布等。
这些刀具可以根据木材的硬度和需要选择不同的粗细度。
4. 木工刀具的选购和使用注意事项为了选购和使用合适的木工刀具,以下是一些重要的注意事项:1. 选择适合的材质和质量:选择刀刃质地较硬且锋利的刀具,可以提高工作效果和安全性。
210984066_丝锥刀具旋转磨粒流去毛刺和钝化抛光技术

第52卷第3期表面技术2023年3月SURFACE TECHNOLOGY·299·丝锥刀具旋转磨粒流去毛刺和钝化抛光技术高航1,郭天博1,彭灿1,王宣平1,李伟秋2,林海生2(1.大连理工大学 a.机械工程学院 b.精密与特种加工教育部重点实验室,辽宁 大连 116024;2.汇专科技集团股份有限公司,广州 510662)摘要:目的高效、低成本地消除丝锥、铰刀、钻头、铣刀等金属加工刀具磨削后产生的表面毛刺、亚表面烧伤等加工缺陷,实现刀具的高效钝化抛光。
方法基于磨粒流加工(AFM)技术,提出一种刀具旋转磨粒流抛光(R–AFM)原理和方法。
通过模拟仿真方法获得优化的刀具运动轨迹,进一步研发可装夹40把刀具的多工位旋转磨粒流高效抛光专用设备;以高速钢丝锥为研究对象,选用新研制的GC磨料介质作为钝化抛光介质,采用正交实验设计法, 通过极差分析和方差分析,探究工件转速、加工时间、磨粒粒径及磨粒质量分数等工艺参数对刃口钝圆半径的影响规律;再选用正交试验获得的工艺参数组合,采用自主研制的WS 和GC磨料介质,分别对丝锥刀具进行钝化抛光试验,分析2种新型磨料介质的钝化抛光特性;最后,基于前面的实验结果和理论分析,优选刀具钝化抛光复合加工的工艺参数,并验证刀具的钝化抛光效果。
结果各工艺参数对刀具刃口钝圆半径的影响程度依次为刀具回转速度、钝化抛光时间、磨粒质量分数和粒度。
高硬度的GC磨料介质具有材料去除率高、对刃口的钝化能力较强等特点。
在保持切削刃锋利度的前提下,采用低硬度的WS磨料介质,其毛刺去除效果更好。
采用优化的工艺参数和自主研制的WS、GC磨料介质,对新加工的丝锥分别进行了1.5 min和1 min的组合抛光,加工后丝锥表面的毛刺得以完全去除,表面磨削烧伤痕迹显著消减,表面粗糙度Sa可从0.73 μm降至0.26 μm,刃口圆角半径可控制在企业要求的5 μm以内,刃口得到了有效修整,且避免了刀具刃口的“过顿”现象,抛光效率平均可达20支/min。
浅析古代铁质刀剑、剪刀文物制造工艺及组织结构特征——以中国刀剪剑博物馆馆藏为例

The world fa ir,文博天地浅析古代铁质刀剑、剪刀文物制造工艺及组织结构特征—以屮丨五丨刀锊剑博物馆馆藏为例张璐黄琦樊孝林(杭州工艺美术博物馆(杭州中国刀剪剑、扇业、伞业博物馆),浙江杭州310015)【摘要】铁质刀剑、剪刀文物是中国古代铁质文物的重要种类,它们由于自身的功能性质,成为历史时期高水平铁器制造的反映。
通过观察、研究现有实物,结合文献资料,可知古代铁质刀剑、剪刀制造工艺大致可分为渗碳锻打和铸造两种主要方式。
汉代以后,随着古代冶铁技术的逐渐成熟,前者以百炼钢为代表,后者以铸铁脱碳钢、展性铸铁为代表。
相比之下,百炼钢的滲碳和组织 结构更为均匀,同时也粍费更多的人力和工时;铸铁件可以实现一定的规模生产,也能达到刃具所具有的强度和相应的加工性能,但组织的均匀程度则不如百炼钢。
这两种工艺支配着古代铁质刀剑、剪刀的生产,使它们在质量与产量间各取所需,形成了古 代铁质刀剑、剪刀文物多样化的面貌。
【关键词】铁质刀剑文物;铁质剪刀文物;制造工艺;组织结构【本文著录格式】K87 【文献标识码】A【文章编号】1007-4198 (2021 ) 08-207-04【本文著录格式】张璐,黄琦,樊孝林.浅析古代铁质刀剑、剪刀文物制造工艺及组织结构特征——以中国刀剪剑博物馆馆藏 为例[J]•中国民族博览,2021,04 (08): 207-210.在人类最早认识和利用的工具之中,刀具占有重要地位。
春秋时期,中国开始出现冶铸“块炼铁”的技术,铁质刀具 的制作和应用日益广泛。
它们中的一部分作为兵器,很快取 代青铜刀剑,成为主战武器,另一部分成为适应各种日常需 要的生产生活用具,进人千家万户。
在今天留存下来的古代 铁质刀具文物中,以刀剑和剪刀最为常见。
中国现存的铁质刀剑文物最早可追溯到春秋时期,1975 年在湖南长沙一座春秋晚期墓中出土有一把钢铁剑和一把铁 削111;中国现存铁剪文物最早出现在西汉前期,以广州淘金 坑出土实物为代表。
金属切削刀具可靠性的研究毕业论文 (1)

金属切削刀具可靠性的研究毕业论文年级:学号:姓名:专业:指导老师:摘要金属切削刀具的切削性与几何参数有非常重要的关系,但能够决定刀具材料切削性能的基本身的强度和韧性。
硬度和耐磨性,耐热性等。
本文详细介绍了金属切削刀具的常用材料及其金属切削刀具的基本识的这些特征的分析使人们详细的了解每种刀具材料适宜加工的工件的材料,有助于帮助使用者合理的选择,以充分发挥刀具的切削性能和对金属切削刀具的可靠性研究AbstractThe cutting of metal cutting tool geometry parameter and a very important relationship, but to determine cutting tool material the basic body strength and toughness. The hardness and wear resistance, heat resistance. This paper introduces the commonly used metal cutting tool material and its typical brand of these features make it a detailed understanding of each tool material suitable for processing the workpiece material, to help users choose reasonable, so as to give full play to the cutting performance of the cutting tool and the cutting tool reliability research目录摘要 (2)Abstract (3)第一章金属切削刀具的基本识 (5)1.1切削运动及切削要素 (5)1.2 切削用量 (6)1.3切削层参数 (8)1.4刀具的组成部分 (9)1.5刀具的分类 (10)第二章金属切削刀具的可靠性 (11)2.1.1金属切削的技术特点 (11)2.1.2金属切削刀具可靠性 (14)第三章金属切削刀具材料现状及其展望 (15)3.1 金属切削刀具材料现状及其展望 (15)3.2 金属切削超硬刀具材料 (18)结论 (20)致谢 (21)参考文献 (22)一、零件表面的形成及切削运动第一节切削运动及切削要素机器零件的形状主要由下列几种表面组成:(1)外圆面(2)内圆面(孔):外圆面和内圆面(孔)是以某一直线为母线,以圆为轨迹,作旋转运动所形成的表面。
- 1、下载文档前请自行甄别文档内容的完整性,平台不提供额外的编辑、内容补充、找答案等附加服务。
- 2、"仅部分预览"的文档,不可在线预览部分如存在完整性等问题,可反馈申请退款(可完整预览的文档不适用该条件!)。
- 3、如文档侵犯您的权益,请联系客服反馈,我们会尽快为您处理(人工客服工作时间:9:00-18:30)。
刀具文献摘要
《金刚石刀具技术的发展状况》宗文俊2003
天然金刚石特点:硬度高、耐磨性好、强度高、导热性好、与有色金属摩擦系数低、可以刃磨出极其锋利的刀刃等优良特性。
金刚石晶体定向:
(1)人工目测晶体定向法
特点:只能作粗略的晶体定向,定向精度较低,且可重复性差,一般在初次定晶面时采用。
(2)X 射线晶体定向法
X射线晶体定向原理:一定波长的X射线透过金刚石晶体,光子祷能量传给晶体内的原子,促也较使晶体内原子振动而对X射线产生不同方向的反射,引起不同方向光强的变化,在光强增加到一定程度的方向会产生衍射图案。
根据金刚石不同晶面上具有不同的网面密度(即原子数量不同),对X射线产生反射所形成的光强分布就会不同,最后得到的衍射图案不同来定向。
特点:此种定向方法精度较高,可对金刚石晶体进行重复定向,可重复性好,缺点是仪器设备昂贵,且X射线对人体有害,操作时需用防护设施。
(3)激光晶体定向法
原理:利用金刚石的不同晶面对激光照射会产生不同的衍射图案的原理来定向的。
根据这一工作原理所制成的激光定向仪结构示意图见下图:
一般规律:如果要求
金刚石刀具获得最高的强
度,应选用(100)晶面作为
刀具的前后刀面;如果要
求金刚石刀具抗机械磨损,
则选用(110)晶面作为刀具
的前后刀面;如果要求金刚石刀具抗化学磨损,则宜采用(110)晶面作刀具的前刀面,(100)晶面作后刀面,或者前后刀面都采用(100)晶面。
(特定取向的晶面必定与晶体中对应的一组互相平行的平面点阵
相平行。
可以规定一套整数hkl来反映某特定晶面及其相应平面点阵组的取向,这一套整数称为晶面指标。
晶面(或平面点阵组)指标的严格定义是晶面在三个晶轴上的倒易截数之比。
设a、b、c为晶体的一套基向量,晶面在a轴、b轴、c轴上所截长度分别为ra、sb、tc,则r、s、t为晶面在三个晶轴上的截数,而1/r、1/s、1/t为倒易截数。
将晶面在三个晶轴上倒易截数之比化为一组互质整数,即1/r∶1/s∶1/t=h∶k∶l,则这一套互质整数即为晶面指标,用(hkl)符号来表示——百度文库)
金刚石刀具刃磨工艺
(1)机械研磨法
原理:传统的机械研磨方法一般在直径为3O~40cm 的铸铁研磨盘上涂上一层混有尺寸为1~5O m 的金刚石粉末研磨膏进行预研,
使金刚石粉末嵌入铸铁研磨盘微孔,然后采用50r/min典型转速对
金刚石刀具进行研磨,其本质就是金刚石与金刚石的对研。
特点:传统的机械研磨方法由于磨盘转速高,正压力大,研磨时的摩擦力大,故研磨效率高。
但由于这种研磨方法具有不连续的冲击作用,得到的金刚石刀具锯齿度和变质层厚度较大,表面粗糙度
值(Ra)也较大,一般为0.O5~1 um。
(2)离子束溅蚀法
原理:采用高能氩离子轰击金刚石刀具表面的碳原子,使刀具碳原子逐个排除的微细加工方法,适用于加工微小金刚石刀具,所得到的金刚石刀具表面粗糙度值(Ra)为几个纳米。
(3)热化学抛光法
原理:热化学抛光法一般是在流动氢气(或4 H +96 Ar)气氛中、75O~1050‘C高温下,金刚石刀具表面与低碳钢(或纯铁)研磨盘接触并滑移,金刚石刀具表面活化碳原子扩散到低碳钢(或纯铁)晶体中而达到刀具材料去除目的。
扩散到低碳钢(或纯铁)中的碳原子与周围的氢气反应生成甲烷并随气流排出。
特点:效率取决于碳原子的扩散速率,影响因素有温度、正压力、磨盘转速等。
该方法可使金刚石刀具表面粗糙度值(Ra)达到几个纳米,表面变质层较浅。
(4)无损伤机械化学抛光法
原理:在NaoH溶液中加入适量的微细金刚石粉末和更加细的硅粉,通过强静电作用使硅粉吸附在金刚石粉末之上,然后把它们涂覆在多孔制铸铁研磨盘上对金刚石刀具进行研磨,其实质是微细硅粉
和金刚石刀具表面碳原子发生化学反应,通过硅微粉的微磨削作用把反应层刮掉。
特点:磨削效率极低,约每分钟一个原子层。
(5)真空等离子化学抛光法
图2是真空等离子化学抛光法的加工原理图。
转动的研磨盘被中间的高真空区分为左右两部分,左边为沉淀区,表面是采用真空等离子物理气相沉积(PVD)所制得的氧化硅镀层,右边为金刚石刀具研磨区。
刀具材料去除过程是金刚石刀具表面
活化碳原子在研磨区被氧化硅所氧化,生
成C0或C02后由真空泵抽出。
该方法研
磨出的金刚石刀具刃口质量非常高,但刀
具材料去除率比较低,一般约为每秒
0.25~750个原子层。
(6)化学辅助机械抛光与光整法
原理:该方法是先对金刚石刀具进行传统的机械研磨,得到表面比较粗糙(Ra<1um)和尺寸精度不太高的刀具原形后再对其进行化学
抛光和光整。
化学抛光和光整是将坩埚中的KN03。
晶体加热到650--~900℃,使其变成熔融的液体后倒到旋转的Al2 03。
研磨盘上,然后把金刚石刀具研磨部分浸入熔融的KNO3。
液体中。
高温液体中的金刚石表面碳原子发生活化,与高氧化性的KN03。
进行氧化反应,生成C0 或
C02气体排出。
该过程的氧化作用在金刚石刀具与研磨盘接触的表面
波峰处比较激烈,即波峰处材料去除率高,以此达到化学抛光、光整的目的,可得到质量很高的金刚石刀具,表面粗糙度值(Ra)可达几个纳米。
(7)氧化刻蚀珐
该方法采用高纯度氧气或含氧水蒸气,使金刚石表面碳原子在高温作用下(纯氧1100℃,含氧水蒸气6o0~900 C)发生氧化反应形成
碳氧化物,并随氧气流或水蒸气流一起排出。
用此方法加工后的金刚石表面粗糙度值(Ra)可达几个纳米。
(8)激光刘蚀珐
该方法采用1~100Hz的单束或多束Nd—YAG激光照射金刚石表面使其在局部高温作用下发生烧蚀。
考虑到多晶金刚石晶体的晶界对加工精度有影响,所以本方法只适合对单晶体金刚石表面进行粗加工。
经过刻蚀后的金刚石表面粗糙度值(Ra)可达几十纳米。
高精度金刚石车刀刃磨指标:刃口钝圆半径≤0.05um,刃口
及刀面表面粗糙度值Ra≤0.01um或更小,线轮廓度和圆轮廓度不大于0.05um 或更小。
金刚石刀具刃口检测
方法见右表。