CY7C1041DV33资料
CY7C64713资料
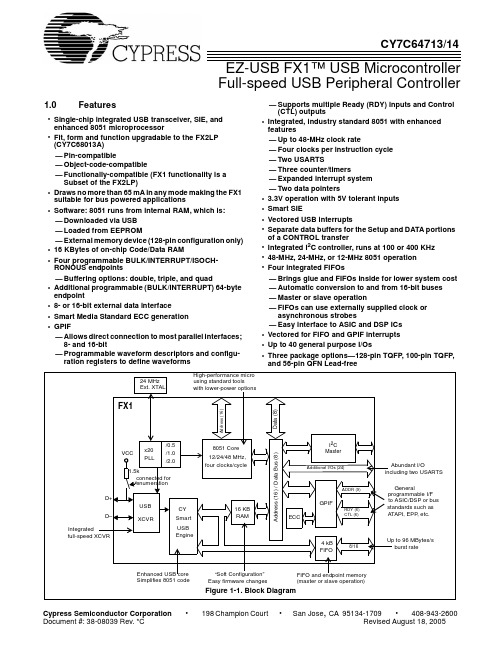
The 8051 microprocessor embedded in the FX1 family has 256 bytes of register RAM, an expanded interrupt system, three timer/counters, and two USARTs. 4.2.1 8051 Clock Frequency
24 MHz Ext. XTAL High-performance micro using standard tools with lower-power options
• • • • • • •
• • •
— Supports multiple Ready (RDY) inputs and Control (CTL) outputs Integrated, industry standard 8051 with enhanced features — Up to 48-MHz clock rate — Four clocks per instruction cycle — Two USARTS — Three counter/timers — Expanded interrupt system — Two data pointers 3.3V operation with 5V tolerant inputs Smart SIE Vectored USB interrupts Separate data buffers for the Setup and DATA portions of a CONTROL transfer Integrated I2C controller, runs at 100 or 400 KHz 48-MHz, 24-MHz, or 12-MHz 8051 operation Four integrated FIFOs — Brings glue and FIFOs inside for lower system cost — Automatic conversion to and from 16-bit buses — Master or slave operation — FIFOs can use externally supplied clock or asynchronous strobes — Easy interface to ASIC and DSP ICs Vectored for FIFO and GPIF interrupts Up to 40 general purpose I/Os Three package options—128-pin TQFP, 100-pin TQFP, and 56-pin QFN Lead-free
CY7C1051DV33芯片手册

PRELIMINARY 8-Mbit (512K x 16) Static RAMCY7C1051DV33Features•High speed —t AA = 10 ns •Low active power—I CC = 110 mA @ 10 ns •Low CMOS standby power —I SB2 = 20 mA •2.0V data retention•Automatic power-down when deselected •TTL-compatible inputs and outputs•Easy memory expansion with CE and OE features•Available in lead-free 48-ball FBGA and 44-pin TSOP II packagesFunctional Description [1]The CY7C1051DV33 is a high-performance CMOS Static RAM organized as 512K words by 16 bits.Write to the device by taking Chip Enable (CE) and Write Enable (WE) inputs LOW. If Byte LOW Enable (BLE) is LOW,then data from IO pins (IO 0–IO 7), is written into the location specified on the address pins (A 0–A 18). If Byte HIGH Enable (BHE) is LOW, then data from IO pins (IO 8–IO 15) is written into the location specified on the address pins (A 0–A 18).Read from the device by taking Chip Enable (CE) and Output Enable (OE) LOW while forcing the Write Enable (WE) HIGH.If Byte LOW Enable (BLE) is LOW, then data from the memory location specified by the address pins will appear on IO 0–IO 7.If Byte HIGH Enable (BHE) is LOW, then data from memory will appear on IO 8 to IO 15. See the “Truth Table” on page 8 for a complete description of Read and Write modes.The input/output pins (IO 0–IO 15) are placed in a high-impedance state when the device is deselected (CE HIGH), the outputs are disabled (OE HIGH), the BHE and BLE are disabled (BHE, BLE HIGH), or a Write operation (CE LOW,and WE LOW) is in progress.The CY7C1051DV33 is available in a 44-pin TSOP II package with center power and ground (revolutionary) pinout, as well as a 48-ball fine-pitch ball grid array (FBGA) package.Note1.For guidelines on SRAM system design, please refer to the “System Design Guidelines” Cypress application note, available on the internet at .1415Logic Block DiagramA 1A 2A 3A 4A 5A 6A 7A 8COLUMN DECODERR O W D E C O D E RS E N S E A M P SINPUT BUFFER512K × 16ARRAYA 0A 11A 13A 12A A A 16A 17A 18A 9A 10IO 0–IO 7OE IO 8–IO 15CE WE BLEBHEPRELIMINARY CY7C1051DV33Selection Guide–10Unit Maximum Access Time 10ns Maximum Operating Current 110mA Maximum CMOS Standby Current20mAPin Configurations [2]48-ball Mini FBGAWE V CC A 11A 10NC A 6A 0A 3CE IO 10IO 8IO 9A 4A 5IO 11IO 13IO 12IO 14IO 15V SS A 9A 8OE V SS A 7IO 0BHE NC A 17A 2A 1BLE V CC IO 2IO 1IO 3IO 4IO 5IO 6IO 7A 15A 14A 13A 12NC A 18NC326541D E B A C F G HA 16(Top View)TSOP IIWE 1234567891011143132363534333740393812134144434216152930V CC A 5A 6A 7A 8A 0A 1OE V SS A 17IO 15A 2CE IO 2IO 0IO 1BHE A 3A 418172019IO 32728252622212324V SS IO 6IO 4IO 5IO 7A 16A 15BLE V CC IO 14IO 13IO 12IO 11IO 10IO 9IO 8A 14A 13A 12A 11A 9A 10A 18(Top View)Note2.NC pins are not connected on the diePRELIMINARY CY7C1051DV33Maximum Ratings(Exceeding the maximum ratings may impair the useful life of the device. These are for user guidelines, they are not tested.)Storage Temperature .................................–65°C to +150°C Ambient Temperature withPower Applied.............................................–55°C to +125°C Supply Voltage on V CC to Relative GND [3]....–0.5V to +4.6V DC Voltage Applied to Outputsin High-Z State [3]....................................–0.3V to V CC + 0.3V DC Input Voltage [3].................................–0.3V to V CC + 0.3VCurrent into Outputs (LOW).........................................20 mA Static Discharge Voltage............................................>2001V (per MIL-STD-883, Method 3015)Latch-up Current......................................................>200 mAOperating RangeRange Ambient Temperature V CC Industrial–40°C to +85°C3.3V ± 0.3VDC Electrical Characteristics Over the Operating RangeParameter DescriptionTest Conditions–10Unit Min MaxV OH Output HIGH Voltage V CC = Min, I OH = –4.0 mA 2.4V V OL Output LOW Voltage V CC = Min, I OL = 8.0 mA0.4V V IH Input HIGH Voltage 2.0V CC + 0.3V V IL [3]Input LOW Voltage –0.30.8V I IX Input Leakage Current GND < V I < V CC–1+1μA I OZ Output Leakage Current GND < V OUT < V CC , Output Disabled –1+1μA I CCV CC Operating Supply CurrentV CC = Max, f = f MAX = 1/t RC100 MHz 110mA83 MHz 100 66 MHz 9040 MHz80I SB1Automatic CE Power Down Current —TTL Inputs Max V CC , CE > V IH V IN > V IH or V IN < V IL , f = f MAX 40mA I SB2Automatic CE Power Down Current —CMOS Inputs Max V CC , CE > V CC – 0.3V,V IN > V CC – 0.3V or V IN < 0.3V, f = 020mACapacitance [4]Parameter DescriptionTest ConditionsMax.Unit C IN Input Capacitance T A = 25°C, f = 1 MHz, V CC = 3.3V12pF C OUTIO Capacitance12pFNotes3.V IL (min) = –2.0V and V IH (max) = V CC + 2.0V for pulse durations of less than 20 ns.4.Tested initially and after any design or process changes that may affect these parametersThermal Resistance [4]ParameterDescription Test ConditionsFBGA PackageTSOP II PackageUnit ΘJA Thermal Resistance (Junction to Ambient)Still Air, soldered on a 3 × 4.5 inch, four-layer printed circuit board28.3151.43°C/W ΘJCThermal Resistance (Junction to Case)11.415.8°C/WPRELIMINARYCY7C1051DV33AC Test Loads and Waveforms [5]AC Switching Characteristics [6] Over the Operating RangeParameterDescription–10UnitMinMaxRead Cycle t power [7]V CC (typical) to the first access 100μs t RC Read Cycle Time 10ns t AA Address to Data Valid10ns t OHA Data Hold from Address Change 3ns t ACE CE LOW to Data Valid 10ns t DOE OE LOW to Data Valid 5ns t LZOE OE LOW to Low-Z 0ns t HZOE OE HIGH to High-Z [8, 9]5ns t LZCE CE LOW to Low-Z [9]3ns t HZCE CE HIGH to High-Z [8, 9]5ns t PU CE LOW to Power Up 0ns t PD CE HIGH to Power Down 10ns t DBE Byte Enable to Data Valid 5ns t LZBE Byte Enable to Low-Z 0ns t HZBEByte Disable to High-Z6nsNotes5.AC characteristics (except High-Z) are tested using the load conditions shown in Figure (a). High-Z characteristics are tested for all speeds using the test loadshown in Figure (c).6.Test conditions assume signal transition time of 3 ns or less, timing reference levels of 1.5V, input pulse levels of 0 to 3.0V.7.t POWER gives the minimum amount of time that the power supply should be at typical V CC values until the first memory access can be performed.8.t HZOE , t HZCE , t HZBE and t HZWE are specified with a load capacitance of 5 pF as in part (d) of AC Test Loads.Transition is measured when the outputs enter ahigh impedance state.9.At any given temperature and voltage condition, t HZCE is less than t LZCE , t HZOE is less than t LZOE , t HZBE is less than t LZBE , and t HZWE is less than t LZWE for anygiven device.90%10%3.0VGND90%10%ALL INPUT PULSES * CAPACITIVE LOAD CONSISTS OF ALL COMPONENTS OF THE TEST ENVIRONMENTRise Time: 1 V/nsFall Time: 1 V/ns30 pF*OUTPUTZ = 50Ω50Ω1.5V (a)3.3V OUTPUT5 pF(c)R 317ΩR2351ΩHigh-Z Characteristics(b)PRELIMINARY CY7C1051DV33Data Retention WaveformWrite Cycle [10, 11]t WC Write Cycle Time 10ns t SCE CE LOW to Write End 7ns t AW Address Setup to Write End 7ns t HA Address Hold from Write End 0ns t SA Address Setup to Write Start 0ns t PWE WE Pulse Width 7ns t SD Data Setup to Write End 5ns t HD Data Hold from Write End 0ns t LZWE WE HIGH to Low-Z [9]3ns t HZWE WE LOW to High-Z [8, 9]5ns t BWByte Enable to End of Write7nsData Retention Characteristics Over the Operating RangeParameter DescriptionConditions [12]Min MaxUnit V DR V CC for Data Retention 2.0V I CCDR Data Retention CurrentV CC = V DR = 2.0V , CE > V CC – 0.3V , V IN > V CC – 0.3V or V IN < 0.3V20mA t CDR [4]Chip Deselect to Data Retention Time 0ns t R [13]Operation Recovery Timet RCnsAC Switching Characteristics [6] Over the Operating Range (continued)ParameterDescription–10UnitMinMax3.0V 3.0V t CDRV DR > 2VDATA RETENTION MODEt RCEV CC Notes10.The internal Write time of the memory is defined by the overlap of CE LOW, and WE LOW. CE and WE must be LOW to initiate a Write, and the transition ofeither of these signals can terminate the Write. The input data setup and hold timing should be referenced to the leading edge of the signal that terminates the Write.11.The minimum Write cycle time for Write Cycle No. 3 (WE controlled, OE LOW) is the sum of t HZWE and t SD .12.No inputs may exceed V CC + 0.3V13.Full device operation requires linear V CC ramp from V DR to V CC (min) > 50 μs or stable at V CC (min) > 50 μs.PRELIMINARY CY7C1051DV33Switching WaveformsRead Cycle No. 1[14, 15]Read Cycle No. 2 (OE Controlled)[15, 16]Notes14.Device is continuously selected. OE, CE, BHE or BHE or both= V IL .15.WE is HIGH for Read cycle.16.Address valid prior to or coincident with CE transition LOW.PREVIOUS DATA VALIDDATA VALIDt RCt AAt OHAADDRESSDATA OUT50%50%DATA VALIDt RCt ACEt DOE t LZOE t LZCE t PUHIGH IMPEDANCEt HZOEt HZBEt PDHIGHOE CEICC ISB IMPEDANCEADDRESSDATA OUT V CC SUPPLY t DBE t LZBEt HZCE BHE,BLECURRENTI CCI SBPRELIMINARY CY7C1051DV33Write Cycle No. 1 (CE Controlled)[17, 18]Write Cycle No. 2 (BLE or BHE Controlled)Notes17.Data I/O is high-impedance if OE or BHE or BLE or both = V IH .18.If CE goes HIGH simultaneously with WE going HIGH, the output remains in a high-impedance state.Switching Waveforms (continued)t HDt SDt SCEt SA t HAt AWt PWEt WCBWDATAI/OADDRESSCEWEBHE,BLEt t HDt SDt BWt SA t HAt AWt PWEt WCt SCEDATAI/OADDRESSBHE,BLEWECEPRELIMINARY CY7C1051DV33Write Cycle No. 3 (WE Controlled, OE LOW)Switching Waveforms (continued)t HDt SDt SCEt HAt AWt PWEt WCt BWDATA I/OADDRESSCEWEBHE,BLEt SAt LZWEt HZWETruth TableCE OE WE BLE BHE I/O 0–I/O 7I/O 8–I/O 15ModePower H X X X X High-Z High-Z Power-down Standby (I SB )L L H L L Data Out Data Out Read All Bits Active (I CC )L L H L H Data Out High-Z Read Lower Bits Only Active (I CC )L L H H L High-Z Data Out Read Upper Bits Only Active (I CC )L X L L L Data In Data In Write All Bits Active (I CC )L X L L H Data In High-Z Write Lower Bits Only Active (I CC )L X L H L High-Z Data In Write Upper Bits Only Active (I CC )LHHXXHigh-ZHigh-ZSelected, Outputs DisabledActive (I CC )Ordering InformationSpeed (ns)Ordering Code Package Diagram Package TypeOperating Range 10CY7C1051DV33-10BAXI 51-8510648-ball FBGA (Pb-Free)IndustrialCY7C1051DV33-10ZSXI51-8508744-pin TSOP II (Pb-Free)Please contact your local Cypress sales representative for availability of these parts.PRELIMINARY CY7C1051DV33 Package DiagramsPRELIMINARY CY7C1051DV33Document #: 001-00063 Rev. *C Page 10 of 11© Cypress Semiconductor Corporation, 2006-2007. The information contained herein is subject to change without notice. Cypress Semiconductor Corporation assumes no responsibility for the All products and company names mentioned in this document may be the trademarks of their respective holders.Figure 2. 44-pin TSOP II (51-85087)Package Diagrams (continued)51-85087-*APRELIMINARY CY7C1051DV33Document #: 001-00063 Rev. *C Page 11 of 11Document History Page Document Title: CY7C1051DV33 8-Mbit (512K x 16) Static RAM Document Number: 001-00063REV.ECN NO.Issue Date Orig. of Change Description of Change **342195See ECN PCI New Data Sheet *A 380574See ECN SYT Redefined I CC values for Com’l and Ind’l temperature rangesI CC (Com’l): Changed from 110, 90 and 80 mA to 110, 100 and 95 mA for 8, 10and 12 ns speed bins respectivelyI CC (Ind’l): Changed from 110, 90 and 80 mA to 120, 110 and 105 mA for 8, 10and 12 ns speed bins respectivelyChanged the Capacitance values from 8 pF to 10 pF on Page # 3*B 485796See ECN NXR Changed address of Cypress Semiconductor Corporation on Page# 1 from“3901 North First Street” to “198 Champion Court”Removed -8 and -12 Speed bins from product offering,Removed Commercial Operating Range option,Modified Maximum Ratings for DC input voltage from -0.5V to -0.3V andV CC + 0.5V to V CC + 0.3VChanged the Description of I IX from Input Load Current toInput Leakage Current.Changed t HZBE from 5 ns to 6 nsUpdated footnote #7 on High-Z parameter measurementAdded footnote #11Updated the Ordering Information table and Replaced Package Name columnwith Package Diagram.*C 866000See ECN NXRChanged ball E3 from V SS to NC in FBGA pin configuration [+] FeedbThis datasheet has been downloaded from:Free DownloadDaily Updated Database100% Free Datasheet Search Site100% Free IC Replacement Search SiteConvenient Electronic DictionaryFast Search SystemAll Datasheets Cannot Be Modified Without PermissionCopyright © Each Manufacturing Company。
CY7C1041DV33中文资料

元器件交易网
CY7C1041DV33
Contents
Selection Guide ................................................................ 3 Pin Configuration ............................................................. 3 Maximum Ratings ............................................................. 4 Operating Range ............................................................... 4 DC Electrical Characteristics .......................................... 4 Capacitance ...................................................................... 5 Thermal Resistance .......................................................... 5 AC Test Loads and Waveforms ....................................... 5 Data Retention Characteristics ....................................... 6 Data Retention Waveform ................................................ 6 AC Switching Characteristics ......................................... 7 Switching Waveforms ...................................................... 8 Truth Table ...................................................................... 11 Ordering Information ...................................................... 12 Ordering Code Definitions ......................................... 12 Package Diagrams .......................................................... 13 Acronyms ........................................................................ 15 Document Conventions ................................................. 15 Units of Measure ....................................................... 15 Document History Page ................................................. 16 Sales, Solutions, and Legal Information ...................... 18 Worldwide Sales and Design Support ....................... 18 Products .................................................................... 18 PSoC® Solutions ...................................................... 18 Cypress Developer Community ................................. 18 Technical Support ..................................................... 18
CY7C1470BV25资料

72-Mbit (2M x 36/4M x 18/1M x 72)Pipelined SRAM with NoBL™ ArchitectureCY7C1470BV25CY7C1472BV25, CY7C1474BV25Features■Pin-compatible and functionally equivalent to ZBT™ ■Supports 250 MHz bus operations with zero wait states ❐Available speed grades are 250, 200, and 167 MHz■Internally self-timed output buffer control to eliminate the need to use asynchronous OE■Fully registered (inputs and outputs) for pipelined operation■Byte Write capability ■Single 2.5V power supply ■2.5V IO supply (V DDQ )■Fast clock-to-output times ❐3.0 ns (for 250-MHz device)■Clock Enable (CEN) pin to suspend operation ■Synchronous self-timed writes■CY7C1470BV25, CY7C1472BV25 available inJEDEC-standard Pb-free 100-pin TQFP , Pb-free and non-Pb-free 165-ball FBGA package. CY7C1474BV25available in Pb-free and non-Pb-free 209-ball FBGA package ■IEEE 1149.1 JTAG Boundary Scan compatible ■Burst capability—linear or interleaved burst order ■“ZZ” Sleep Mode option and Stop Clock optionFunctional DescriptionThe CY7C1470BV25, CY7C1472BV25, and CY7C1474BV25are 2.5V, 2M x 36/4M x 18/1M x 72 synchronous pipelined burst SRAMs with No Bus Latency™ (NoBL ™) logic, respectively.They are designed to support unlimited true back-to-back read or write operations with no wait states. The CY7C1470BV25,CY7C1472BV25, and CY7C1474BV25 are equipped with the advanced (NoBL) logic required to enable consecutive read or write operations with data being transferred on every clock cycle.This feature dramatically improves the throughput of data in systems that require frequent read or write transitions. The CY7C1470BV25, CY7C1472BV25, and CY7C1474BV25 are pin-compatible and functionally equivalent to ZBT devices.All synchronous inputs pass through input registers controlled by the rising edge of the clock. All data outputs pass through output registers controlled by the rising edge of the clock. The clock input is qualified by the Clock Enable (CEN) signal, which when deasserted suspends operation and extends the previous clock cycle. Write operations are controlled by the Byte Write Selects (BW a –BW d for CY7C1470BV25, BW a –BW b for CY7C1472BV25, and BW a –BW h for CY7C1474BV25) and a Write Enable (WE) input. All writes are conducted with on-chip synchronous self-timed write circuitry.Three synchronous Chip Enables (CE 1, CE 2, CE 3) and an asynchronous Output Enable (OE) provide for easy bank selection and output tri-state control. To avoid bus contention,the output drivers are synchronously tri-stated during the data portion of a write sequence.Selection GuideDescription250 MHz 200 MHz 167 MHz Unit Maximum Access Time3.0 3.0 3.4ns Maximum Operating Current450450400mA Maximum CMOS Standby Current120120120mALogic Block Diagram – CY7C1470BV25 (2M x 36)Logic Block Diagram – CY7C1472BV25 (4M x 18)Logic Block Diagram – CY7C1474BV25 (1M x 72)Pin ConfigurationsA A A A A 1A 0V S SV D DA A A A A AV DDQ V SSDQb DQb DQb V SS V DDQDQb DQb V SSNCV DDDQaDQa V DDQ V SSDQa DQa V SS V DDQ V DDQV SS DQc DQc V SS V DDQ DQc V DD V SS DQd DQd V DDQ V SS DQd DQd DQd V SS V DDQ A A C E 1C E 2B W aC E 3V D DV S SC L K W E C E N O E A A123456789101112131415161718192021222324252627282930313233343536373839404142434445464748495080797877767574737271706968676665646362616059585756555453525110099989796959493929190898887868584838281A AA D V /L D ZZCY7C1470BV25A A A A A 1A 0V S SV D DA A A A A AA NC NC V DDQ V SS NC DQPa DQa DQa V SS V DDQ DQa DQa V SS NC V DD DQa DQa V DDQ V SS DQa DQa NC NC V SS V DDQ NC NC NCNC NC NC V DDQ V SS NC NC DQb DQb V SS V DDQDQb DQbV DD V SS DQb DQb V DDQV SS DQb DQb DQPbNC V SS V DDQNC NC NCA A C E 1C E 2N C N C B W b B W a C E 3V D DV S SC L K W E C E N O E A A123456789101112131415161718192021222324252627282930313233343536373839404142434445464748495080797877767574737271706968676665646362616059585756555453525110099989796959493929190898887868584838281A AA D V /L D ZZ M O D E CY7C1472BV25B W d M O D E B W c DQc DQc DQc DQc DQPc DQd DQd DQd DQPb DQb DQa DQaDQa DQaDQPa DQb DQb (2M × 36)(4M × 18)B W b NC NC NC DQc NC N C (288)N C (144)N C (288)N C (144)DQPdA A A A A A Figure 1. 100-Pin TQFP PinoutPin Configurations (continued)165-Ball FBGA (15 x 17 x 1.4 mm) PinoutCY7C1470BV25 (2M x 36)CY7C1472BV25 (4M x 18)2345671A B C D E F G H J K L M N P RTDO NC/576M NC/1G DQP c DQ c DQP d NC DQ d A CE 1BW b CE 3BW c CEN A CE2DQ c DQ d DQ d MODENC DQ c DQ c DQ d DQ d DQ d AV DDQ BW d BW a CLKWEV SS V SS V SS V SS V DDQ V SS V DD V SS V SS V SS NC V SS V SS V SS V SS V DDQ V DDQ NC V DDQ V DDQ V DDQ V DDQ A AV DD V SS V DD V SS V SS V DDQ V DD V SS V DD V SS V DD V SS V SS V SS V DD V DD V SS V DD V SS V SS NC TCKA0V SS TDIAA DQ c V SS DQ c V SS DQ c DQ c NC V SS V SS V SS V SS NC V SS A1DQ d DQ d NC/144M NCV DDQ V SS TMS891011NC/288MAA ADV/LDNC OE A A NC V SS V DDQ NC DQP b V DDQ V DD DQ b DQ b DQ b NC DQ b NC DQ a DQ a V DD V DDQ V DD V DDQ DQ b V DD NC V DD DQ a V DD V DDQ DQ a V DDQ V DD V DD V DDQ V DD V DDQ DQ a V DDQ AAV SS AAADQ b DQ b DQ b ZZ DQ a DQ a DQP aDQ a A V DDQ AA 2345671A B C D E F G H J K L M N P RTDO NC/576M NC/1G NC NC DQP b NC DQ b A CE 1CE 3BW b CEN A CE2NC DQ b DQ b MODENC DQ b DQ b NC NC NC AV DDQ BW a CLKWE V SS V SS V SS V SSV DDQ V SS V DD V SS V SS V SS NC V SS V SS V SS V SS V DDQ V DDQ NC V DDQ V DDQ V DDQ V DDQ A AV DD V SS V DD V SS V SS V DDQ V DD V SS V DD V SS V DD V SS V SS V SS V DD V DD V SS V DD V SS V SS NC TCKA0V SS TDIAA DQ b V SS NC V SS DQ b NC NC V SS V SS V SS V SS NC V SS A1DQ b NC NC/144M NCV DDQ V SS TMS891011NC/288MAA ADV/LDA OE A A NC V SSV DDQ NC DQPa V DDQ V DD NC DQ a DQ a NC NC NC DQ a NC V DD V DDQ V DD V DDQ DQ a V DD NC V DD NC V DD V DDQ DQ a V DDQ V DD V DD V DDQ V DD V DDQ NC V DDQ AAV SS AAADQ a NC NC ZZ DQ a NC NCDQ a A V DDQ AA NC NCPin Configurations (continued)CY7C1474BV25 (1M × 72)209-Ball FBGA (14 x 22 x 1.76 mm) PinoutA B C D E F G H J K L M N P R T U V W1234567891110DQgDQgDQgDQgDQgDQgDQgDQgDQcDQcDQcDQcNCDQPgDQhDQhDQhDQhDQdDQdDQdDQdDQPdDQPcDQcDQcDQcDQcNCDQhDQhDQhDQhDQPhDQdDQdDQdDQdDQbDQbDQbDQbDQbDQbDQbDQbDQfDQfDQfDQfNCDQPfDQaDQaDQaDQaDQeDQeDQeDQeDQPaDQPbDQfDQfDQfDQfNCDQaDQaDQaDQaDQPeDQeDQeDQeDQeA A A ANC NCNC/144M A A NC/288MA A AA A A A1A0A A AA AANC/576MNCNCNC NCNCBWS b BWS fBWS e BWS aBWS c BWS gBWS dBWS hTMS TDI TDO TCKNCNC MODE NCCEN V SSNCCLK NC V SSV DD V DD V DDV DDV DDV DDV DDV DDV DDV DDV DDV DDV DDV SS V SSV SSV SSV SSV SS V SSV SSNC/1GV DDNCOECE3CE1CE2ADV/LDWEV SSV SSV SSV SS V SS V SS VSSZZV SS V SS V SS V SSNCV DDQV SSV SS NC V SS V SSV SS V SS VSSV SSNCV SSV DDQ V DDQ V DDQ V DDQV DDQ NC V DDQ VDDQV DDQ V DDQ NC V DDQ V DDQV DDQ V DDQ NC V DDQ VDDQV DDQV DDQV DDQ V DDQV DDQ VDDQV DDQ V DDQTable 1. Pin DefinitionsPin Name IO Type Pin DescriptionA0 A1 AInput-SynchronousAddress Inputs Used to Select One of the Address Locations. Sampled at the rising edge of theCLK.BW a BW b BW c BW d BW e BW f BW g BW hInput-SynchronousByte Write Select Inputs, Active LOW. Qualified with WE to conduct writes to the SRAM. Sampledon the rising edge of CLK. BW a controls DQ a and DQP a, BW b controls DQ b and DQP b, BW c controlsDQ c and DQP c, BW d controls DQ d and DQP d, BW e controls DQ e and DQP e, BW f controls DQ f andDQP f, BW g controls DQ g and DQP g, BW h controls DQ h and DQP h.WE Input-Synchronous Write Enable Input, Active LOW. Sampled on the rising edge of CLK if CEN is active LOW. This signal must be asserted LOW to initiate a write sequence.ADV/LD Input-Synchronous Advance/Load Input Used to Advance the On-Chip Address Counter or Load a New Address. When HIGH (and CEN is asserted LOW) the internal burst counter is advanced. When LOW, a new address can be loaded into the device for an access. After being deselected, ADV/LD must be driven LOW to load a new address.CLK Input-Clock Clock Input. Used to capture all synchronous inputs to the device. CLK is qualified with CEN. CLK is only recognized if CEN is active LOW.CE1Input-Synchronous Chip Enable 1 Input, Active LOW. Sampled on the rising edge of CLK. Used in conjunction with CE2 and CE3 to select/deselect the device.CE2Input-Synchronous Chip Enable 2 Input, Active HIGH. Sampled on the rising edge of CLK. Used in conjunction with CE1 and CE3 to select/deselect the device.CE3Input-Synchronous Chip Enable 3 Input, Active LOW. Sampled on the rising edge of CLK. Used in conjunction with CE1 and CE2 to select/deselect the device.OE Input-Asynchronous Output Enable, Active LOW. Combined with the synchronous logic block inside the device to control the direction of the IO pins. When LOW, the IO pins can behave as outputs. When deasserted HIGH, IO pins are tri-stated, and act as input data pins. OE is masked during the data portion of a write sequence, during the first clock when emerging from a deselected state and when the device has been deselected.CEN Input-Synchronous Clock Enable Input, Active LOW. When asserted LOW the clock signal is recognized by the SRAM. When deasserted HIGH the clock signal is masked. Since deasserting CEN does not deselect the device, CEN can be used to extend the previous cycle when required.DQ s IO-Synchronous Bidirectional Data IO Lines. As inputs, they feed into an on-chip data register that is triggered by the rising edge of CLK. As outputs, they deliver the data contained in the memory location specified by A[18:0] during the previous clock rise of the read cycle. The direction of the pins is controlled by OE and the internal control logic. When OE is asserted LOW, the pins can behave as outputs. When HIGH, DQ a–DQ h are placed in a tri-state condition. The outputs are automatically tri-stated during the data portion of a write sequence, during the first clock when emerging from a deselected state, and when the device is deselected, regardless of the state of OE.DQP X IO-Synchronous Bidirectional Data Parity IO Lines. Functionally, these signals are identical to DQ[71:0]. During write sequences, DQP a is controlled by BW a, DQP b is controlled by BW b, DQP c is controlled by BW c, and DQP d is controlled by BW d, DQP e is controlled by BW e, DQP f is controlled by BW f, DQP g is controlled by BW g, DQP h is controlled by BW h.MODE Input Strap Pin Mode Input. Selects the burst order of the device. Tied HIGH selects the interleaved burst order.Pulled LOW selects the linear burst order. MODE must not change states during operation. Whenleft floating MODE defaults HIGH, to an interleaved burst order.TDO JTAG SerialOutputSynchronousSerial Data Out to the JTAG Circuit. Delivers data on the negative edge of TCK.TDI JTAG Serial InputSynchronousSerial Data In to the JTAG Circuit. Sampled on the rising edge of TCK.Functional OverviewThe CY7C1470BV25, CY7C1472BV25, and CY7C1474BV25 are synchronous-pipelined Burst NoBL SRAMs designed specif-ically to eliminate wait states during read or write transitions. All synchronous inputs pass through input registers controlled by the rising edge of the clock. The clock signal is qualified with the Clock Enable input signal (CEN). If CEN is HIGH, the clock signal is not recognized and all internal states are maintained. All synchronous operations are qualified with CEN. All data outputs pass through output registers controlled by the rising edge of the clock. Maximum access delay from the clock rise (t CO) is 3.0 ns (250-MHz device).Accesses can be initiated by asserting all three Chip Enables (CE1, CE2, CE3) active at the rising edge of the clock. If CEN is active LOW and ADV/LD is asserted LOW, the address presented to the device is latched. The access can either be a read or write operation, depending on the status of the Write Enable (WE). BW[x] can be used to conduct Byte Write opera-tions.Write operations are qualified by the Write Enable (WE). All writes are simplified with on-chip synchronous self-timed write circuitry.Three synchronous Chip Enables (CE1, CE2, CE3) and an asynchronous Output Enable (OE) simplify depth expansion. All operations (reads, writes, and deselects) are pipelined. ADV/LD must be driven LOW after the device is deselected to load a new address for the next operation.Single Read AccessesA read access is initiated when the following conditions are satisfied at clock rise: (1) CEN is asserted LOW, (2) CE1, CE2, and CE3 are ALL asserted active, (3) the input signal WE is deasserted HIGH, and (4) ADV/LD is asserted LOW. The address presented to the address inputs is latched into the Address Register and presented to the memory core and control logic. The control logic determines that a read access is in progress and allows the requested data to propagate to the input of the output register. At the rising edge of the next clock the requested data is allowed to propagate through the output register and onto the data bus within 2.6 ns (250-MHz device) provided OE is active LOW. After the first clock of the read access the output buffers are controlled by OE and the internal control logic. OE must be driven LOW to drive out the requested data. During the second clock, a subsequent operation (read, write, or deselect) can be initiated. Deselecting the device is also pipelined. Therefore, when the SRAM is deselected at clock rise by one of the chip enable signals, its output tri-states following the next clock rise.Burst Read AccessesThe CY7C1470BV25, CY7C1472BV25, and CY7C1474BV25 have an on-chip burst counter that enables the user to supply a single address and conduct up to four reads without reasserting the address inputs. ADV/LD must be driven LOW to load a new address into the SRAM, as described in the Single Read Accesses section. The sequence of the burst counter is deter-mined by the MODE input signal. A LOW input on MODE selects a linear burst mode, a HIGH selects an interleaved burst sequence. Both burst counters use A0 and A1 in the burst sequence, and wraps around when incremented sufficiently. A HIGH input on ADV/LD increments the internal burst counter regardless of the state of chip enables inputs or WE. WE is latched at the beginning of a burst cycle. Therefore, the type of access (read or write) is maintained throughout the burst sequence.Single Write AccessesWrite accesses are initiated when the following conditions are satisfied at clock rise: (1) CEN is asserted LOW, (2) CE1, CE2, and CE3 are ALL asserted active, and (3) the signal WE is asserted LOW. The address presented to the address inputs is loaded into the Address Register. The write signals are latched into the Control Logic block.On the subsequent clock rise the data lines are automatically tri-stated regardless of the state of the OE input signal. This allows the external logic to present the data on DQ and DQP (DQ a,b,c,d/DQP a,b,c,d for CY7C1470BV25, DQ a,b/DQP a,b for CY7C1472BV25, and DQ a,b,c,d,e,f,g,h/DQP a,b,c,d,e,f,g,h for CY7C1474BV25). In addition, the address for the subsequentTMS Test Mode SelectSynchronousTMS Pin Controls the Test Access Port State Machine. Sampled on the rising edge of TCK. TCK JTAG Clock Clock Input to the JTAG Circuitry.V DD Power Supply Power Supply Inputs to the Core of the Device.V DDQ IO Power Supply Power Supply for the IO Circuitry.V SS Ground Ground for the Device. Must be connected to ground of the system.NC–No Connects. This pin is not connected to the die.NC(144M, 288M, 576M, 1G)–These Pins are Not Connected. They are used for expansion to the 144M, 288M, 576M, and 1G densities.ZZ Input-Asynchronous ZZ “Sleep” Input. This active HIGH input places the device in a non-time critical “sleep” condition with data integrity preserved. For normal operation, this pin has must be LOW or left floating.ZZ pin has an internal pull down.Table 1. Pin Definitions (continued)Pin Name IO Type Pin Descriptionaccess (read, write, or deselect) is latched into the Address Register (provided the appropriate control signals are asserted). On the next clock rise the data presented to DQ and DQP (DQ a,b,c,d/DQP a,b,c,d for CY7C1470BV25, DQ a,b/DQP a,b for CY7C1472BV25, DQ a,b,c,d,e,f,g,h/DQP a,b,c,d,e,f,g,h for CY7C1474BV25) (or a subset for Byte Write operations, see “Partial Write Cycle Description” on page11 for details) inputs is latched into the device and the Write is complete.The data written during the Write operation is controlled by BW (BW a,b,c,d for CY7C1470BV25, BW a,b for CY7C1472BV25, and BW a,b,c,d,e,f,g,h for CY7C1474BV25) signals. The CY7C1470BV25, CY7C1472BV25, and CY7C1474BV25 provides Byte Write capability that is described in “Partial Write Cycle Description” on page11. Asserting the WE input with the selected BW input selectively writes to only the desired bytes. Bytes not selected during a Byte Write operation remain unaltered. A synchronous self-timed write mechanism has been provided to simplify the write operations. Byte Write capability has been included to greatly simplify read, modify, or write sequences, which can be reduced to simple Byte Write opera-tions.Because the CY7C1470BV25, CY7C1472BV25, and CY7C1474BV25 are common IO devices, data must not be driven into the device while the outputs are active. OE can be deasserted HIGH before presenting data to the DQ and DQP (DQ a,b,c,d/DQP a,b,c,d for CY7C1470BV25, DQ a,b/DQP a,b for CY7C1472BV25, and DQ a,b,c,d,e,f,g,h/DQP a,b,c,d,e,f,g,h for CY7C1474BV25) inputs. Doing so tri-states the output drivers. As a safety precaution, DQ and DQP (DQ a,b,c,d/DQP a,b,c,d for CY7C1470BV25, DQ a,b/DQP a,b for CY7C1472BV25, and DQ a,b,c,d,e,f,g,h/DQP a,b,c,d,e,f,g,h for CY7C1474BV25) are automatically tri-stated during the data portion of a write cycle, regardless of the state of OE.Burst Write AccessesThe CY7C1470BV25, CY7C1472BV25, and CY7C1474BV25 has an on-chip burst counter that enables the user to supply a single address and conduct up to four write operations without reasserting the address inputs. ADV/LD must be driven LOW to load the initial address, as described in “Single Write Accesses”on page8. When ADV/LD is driven HIGH on the subsequent clock rise, the Chip Enables (CE1, CE2, and CE3) and WE inputs are ignored and the burst counter is incremented. The correct BW (BW a,b,c,d for CY7C1470BV25, BW a,b for CY7C1472BV25, and BW a,b,c,d,e,f,g,h for CY7C1474BV25) inputs must be driven in each cycle of the burst write to write the correct bytes of data. Sleep ModeThe ZZ input pin is an asynchronous input. Asserting ZZ places the SRAM in a power conservation “sleep” mode. Two clock cycles are required to enter into or exit from this “sleep” mode. While in this mode, data integrity is guaranteed. Accesses pending when entering the “sleep” mode are not considered valid nor is the completion of the operation guaranteed. The device must be deselected before entering the “sleep” mode. CE1, CE2, and CE3, must remain inactive for the duration of t ZZREC after the ZZ input returns LOW.Table 2. Linear Burst Address Table (MODE = GND) FirstAddressSecondAddressThirdAddressFourthAddress A1,A0A1,A0A1,A0A1,A000011011011011001011000111000110Table 3. Interleaved Burst Address Table(MODE = Floating or V DD)FirstAddressSecondAddressThirdAddressFourthAddress A1,A0A1,A0A1,A0A1,A000011011010011101011000111100100ZZ Mode Electrical CharacteristicsParameter Description Test Conditions Min Max Unit I DDZZ Sleep mode standby current ZZ > V DD − 0.2V120mA t ZZS Device operation to ZZ ZZ > V DD− 0.2V2t CYC ns t ZZREC ZZ recovery time ZZ < 0.2V2t CYC ns t ZZI ZZ active to sleep current This parameter is sampled2t CYC ns t RZZI ZZ Inactive to exit sleep current This parameter is sampled0nsTable 4. Truth TableThe truth table for CY7C1470BV25, CY7C1472BV25, and CY7C1474BV25 follows.[1, 2, 3, 4, 5, 6, 7]Operation AddressUsed CE ZZ ADV/LD WE BW x OE CEN CLK DQ Deselect Cycle None H L L X X X L L-H Tri-State Continue Deselect Cycle None X L H X X X L L-H Tri-StateExternal L L L H X L L L-H Data Out (Q) Read Cycle(Begin Burst)Next X L H X X L L L-H Data Out (Q) Read Cycle(Continue Burst)External L L L H X H L L-H Tri-State NOP/Dummy Read(Begin Burst)Next X L H X X H L L-H Tri-State Dummy Read(Continue Burst)External L L L L L X L L-H Data In (D) Write Cycle(Begin Burst)Next X L H X L X L L-H Data In (D) Write Cycle(Continue Burst)None L L L L H X L L-H Tri-State NOP/Write Abort(Begin Burst)Next X L H X H X L L-H Tri-State Write Abort(Continue Burst)Ignore Clock Edge (Stall)Current X L X X X X H L-H–Sleep Mode None X H X X X X X X Tri-StateNotes1.X = “Don't Care”, H = Logic HIGH, L = Logic LOW, CE stands for ALL Chip Enables active. BW x = L signifies at least one Byte Write Select is active, BW x = Validsignifies that the desired Byte Write Selects are asserted, see “Partial Write Cycle Description” on page11 for details.2.[a:d]. See “Partial Write Cycle Description” on page11 for details.3.When a write cycle is detected, all IOs are tri-stated, even during Byte Writes.4.The DQ and DQP pins are controlled by the current cycle and the OE signal.5.6.Device powers up deselected with the IOs in a tri-state condition, regardless of OE.7.OE is asynchronous and is not sampled with the clock rise. It is masked internally during write cycles.During a Read cycle DQ s and DQP[a:d] = tri-state when OE isinactive or when the device is deselected, and DQ s = data when OE is active.Table 5. Partial Write Cycle DescriptionThe partial write cycle description for CY7C1470BV25, CY7C1472BV25, and CY7C1474BV25 follows.[1, 2, 3, 8]Function (CY7C1470BV25)WE BW d BW c BW b BW a Read H X X X X Write – No bytes written L H H H H Write Byte a – (DQ a and DQP a)L H H H L Write Byte b – (DQ b and DQP b)L H H L H Write Bytes b, a L H H L L Write Byte c – (DQ c and DQP c)L H L H H Write Bytes c, a L H L H L Write Bytes c, b L H LL L H Write Bytes c, b, a L H L L L Write Byte d – (DQ d and DQP d)L L H H H Write Bytes d, a L L H H L Write Bytes d, b L L H L H Write Bytes d, b, a L L H L L Write Bytes d, c L L L H H Write Bytes d, c, a L L L H L Write Bytes d, c, b L L L L H Write All Bytes L L L L LFunction (CY7C1472BV25)WE BW b BW aRead H x xWrite – No Bytes Written L H HWrite Byte a – (DQ a and DQP a)L H LWrite Byte b – (DQ b and DQP b)L L HWrite Both Bytes L L LFunction (CY7C1474BV25)WE BW xRead H xWrite – No Bytes Written L HWrite Byte X − (DQ x and DQP x)L LWrite All Bytes L All BW = LNote8.Table lists only a partial listing of the Byte Write combinations. Any combination of BW[a:d] is valid. Appropriate write is based on which Byte Write is active.IEEE 1149.1 Serial Boundary Scan (JTAG) The CY7C1470BV25, CY7C1472BV25, and CY7C1474BV25incorporates a serial boundary scan test access port (TAP). This port operates in accordance with IEEE Standard 1149.1-1990 but does not have the set of functions required for full 1149.1 compliance. These functions from the IEEE specification are excluded because their inclusion places an added delay in the critical speed path of the SRAM. Note that the TAP controller functions in a manner that does not conflict with the operation of other devices using 1149.1 fully compliant TAPs. The TAP operates using JEDEC-standard 2.5V IO logic levels.The CY7C1470BV25, CY7C1472BV25, and CY7C1474BV25 contains a TAP controller, instruction register, boundary scan register, bypass register, and ID register.Disabling the JTAG FeatureIt is possible to operate the SRAM without using the JTAG feature. To disable the TAP controller, TCK must be tied LOW (V SS) to prevent clocking of the device. TDI and TMS are inter-nally pulled up and may be unconnected. They may alternately be connected to V DD through a pull up resistor. TDO must be left unconnected. During power up, the device comes up in a reset state, which does not interfere with the operation of the device. The 0/1 next to each state represents the value of TMS at therising edge of TCK.Test Access Port (TAP)Test Clock (TCK)The test clock is used only with the TAP controller. All inputs are captured on the rising edge of TCK. All outputs are driven from the falling edge of TCK.Test MODE SELECT (TMS)The TMS input is used to give commands to the TAP controller and is sampled on the rising edge of TCK. It is allowable to leave this ball unconnected if the TAP is not used. The ball is pulled up internally, resulting in a logic HIGH level.Test Data-In (TDI)The TDI ball is used to serially input information into the registers and can be connected to the input of any of the registers. The register between TDI and TDO is chosen by the instruction that is loaded into the TAP instruction register. For information about loading the instruction register, see the TAP Controller State Diagram. TDI is internally pulled up and can be unconnected if the TAP is unused in an application. TDI is connected to the most significant bit (MSB) of any register. (See TAP Controller Block Diagram.)Test Data-Out (TDO)The TDO output ball is used to serially clock data-out from the registers. The output is active depending upon the current state of the TAP state machine. The output changes on the falling edge of TCK. TDO is connected to the least significant bit (LSB) of any register. (See TAP Controller State Diagram.)Performing a TAP ResetA RESET is performed by forcing TMS HIGH (V DD) for five rising edges of TCK. This RESET does not affect the operation of the SRAM and may be performed while the SRAM is operating. During power up, the TAP is reset internally to ensure that TDO comes up in a High-Z state.TAP RegistersRegisters are connected between the TDI and TDO balls to scan the data in and out of the SRAM test circuitry. Only one register can be selected at a time through the instruction register. Data is serially loaded into the TDI ball on the rising edge of TCK. Data is output on the TDO ball on the falling edge of TCK.Figure 2. TAP Controller State DiagramFigure 3. TAP Controller Block DiagramInstruction RegisterThree-bit instructions can be serially loaded into the instruction register. This register is loaded when it is placed between the TDI and TDO balls as shown in the “TAP Controller Block Diagram”on page12. During power up, the instruction register is loaded with the IDCODE instruction. It is also loaded with the IDCODE instruction if the controller is placed in a reset state as described in the previous section.When the TAP controller is in the Capture-IR state, the two least significant bits are loaded with a binary ‘01’ pattern to enable fault isolation of the board-level serial test data path.Bypass RegisterTo save time when serially shifting data through registers, it is sometimes advantageous to skip certain chips. The bypass register is a single-bit register that can be placed between the TDI and TDO balls. This shifts the data through the SRAM with minimal delay. The bypass register is set LOW (V SS) when the BYPASS instruction is executed.Boundary Scan RegisterThe boundary scan register is connected to all the input and bidirectional balls on the SRAM.The boundary scan register is loaded with the contents of the RAM IO ring when the TAP controller is in the Capture-DR state and is then placed between the TDI and TDO balls when the controller is moved to the Shift-DR state. The EXTEST, SAMPLE/PRELOAD and SAMPLE Z instructions can be used to capture the contents of the IO ring.The Boundary Scan Order tables on page 17 show the order in which the bits are connected. Each bit corresponds to one of the bumps on the SRAM package. The MSB of the register is connected to TDI and the LSB is connected to TDO. Identification (ID) RegisterThe ID register is loaded with a vendor-specific, 32-bit code during the Capture-DR state when the IDCODE command is loaded in the instruction register. The IDCODE is hardwired into the SRAM and can be shifted out when the TAP controller is in the Shift-DR state. The ID register has a vendor code and other information described in “Identification Register Definitions” on page16.TAP Instruction SetOverviewEight different instructions are possible with the three-bit instruction register. All combinations are listed in “Identification Codes” on page17. Three of these instructions are listed as RESERVED and must not be used. The other five instructions are described in this section in detail.The TAP controller used in this SRAM is not fully compliant to the 1149.1 convention because some of the mandatory 1149.1 instructions are not fully implemented.The TAP controller cannot be used to load address data or control signals into the SRAM and cannot preload the IO buffers. The SRAM does not implement the 1149.1 commands EXTEST or INTEST or the PRELOAD portion of SAMPLE/PRELOAD; rather, it performs a capture of the IO ring when these instruc-tions are executed.Instructions are loaded into the TAP controller during the Shift-IR state when the instruction register is placed between TDI and TDO. During this state, instructions are shifted through the instruction register through the TDI and TDO balls. To execute the instruction after it is shifted in, the TAP controller must be moved into the Update-IR state.EXTESTEXTEST is a mandatory 1149.1 instruction which is executed whenever the instruction register is loaded with all 0s. EXTEST is not implemented in this SRAM TAP controller, and therefore this device is not compliant to 1149.1. The TAP controller does recognize an all-0 instruction.When an EXTEST instruction is loaded into the instruction register, the SRAM responds as if a SAMPLE/PRELOAD instruction has been loaded. There is one difference between the two instructions. Unlike the SAMPLE/PRELOAD instruction, EXTEST places the SRAM outputs in a High-Z state.IDCODEThe IDCODE instruction loads a vendor-specific, 32-bit code into the instruction register. It also places the instruction register between the TDI and TDO balls and shifts the IDCODE out of the device when the TAP controller enters the Shift-DR state.The IDCODE instruction is loaded into the instruction register during power up or whenever the TAP controller is in a test logic reset state.SAMPLE ZThe SAMPLE Z instruction connects the boundary scan register between the TDI and TDO pins when the TAP controller is in a Shift-DR state. It also places all SRAM outputs into a High-Z state.SAMPLE/PRELOADSAMPLE/PRELOAD is a 1149.1 mandatory instruction. The PRELOAD portion of this instruction is not implemented, so the device TAP controller is not fully 1149.1 compliant.When the SAMPLE/PRELOAD instruction is loaded into the instruction register and the TAP controller is in the Capture-DR state, a snapshot of data on the inputs and bidirectional balls is captured in the boundary scan register.The user must be aware that the TAP controller clock can only operate at a frequency up to 20 MHz, while the SRAM clock operates more than an order of magnitude faster. Because there is a large difference in the clock frequencies, it is possible that during the Capture-DR state, an input or output may undergo a transition. The TAP may then try to capture a signal while in transition (metastable state). This does not harm the device, but there is no guarantee as to the value that is captured. Repeatable results may not be possible.To guarantee that the boundary scan register captures the correct value of a signal, the SRAM signal must be stabilized long enough to meet the TAP controller’s capture setup plus hold time (t CS plus t CH).The SRAM clock input might not be captured correctly if there is no way in a design to stop (or slow) the clock during a SAMPLE/PRELOAD instruction. If this is an issue, it is still。
CY7C1338G-133AXC资料

PRELIMINARY4-Mbit (128K x 32) Flow-Through Sync SRAMCY7C1338GFeatures•128K X 32 common I/O•3.3V –5% and +10% core power supply (V DD)•2.5V or 3.3V I/O supply (V DDQ)•Fast clock-to-output times—6.5 ns (133-MHz version)—7.5 ns (117-MHz version)—8.0 ns (100-MHz version)•Provide high-performance 2-1-1-1 access rate •User-selectable burst counter supporting Intel®Pentium® interleaved or linear burst sequences •Separate processor and controller address strobes •Synchronous self-timed write•Asynchronous output enable•Lead-Free 100-pin TQFP and 119-ball BGA packages •“ZZ” Sleep Mode option Functional Description[1]The CY7C1338G is a 131,072 x 32 synchronous cache RAM designed to interface with high-speed microprocessors with minimum glue logic. Maximum access delay from clock rise is 6.5 ns (133-MHz version). A 2-bit on-chip counter captures the first address in a burst and increments the address automati-cally for the rest of the burst access. All synchronous inputs are gated by registers controlled by a positive-edge-triggered Clock Input (CLK). The synchronous inputs include all addresses, all data inputs, address-pipelining Chip Enable (CE1), depth-expansion Chip Enables (CE2 and CE3), Burst Control inputs (ADSC, ADSP, and ADV), Write Enables(BW[A:D], and BWE), and Global Write (GW). Asynchronous i nputs include the Output Enable (OE) and the ZZ pin.The CY7C1338G allows either interleaved or linear burst sequences, selected by the MODE input pin. A HIGH selects an interleaved burst sequence, while a LOW selects a linear burst sequence. Burst accesses can be initiated with the Processor Address Strobe (ADSP) or the cache Controller Address Strobe (ADSC) inputs. Address advancement is controlled by the Address Advancement (ADV) input. Addresses and chip enables are registered at rising edge of clock when either Address Strobe Processor (ADSP) or Address Strobe Controller (ADSC) are active. Subsequent burst addresses can be internally generated as controlled by the Advance pin (ADV).The CY7C1338G operates from a +3.3V core power supply while all outputs may operate with either a +2.5 or +3.3V supply. All inputs and outputs are JEDEC-standard JESD8-5-compatible.Note:1.For best–practices recommendations, please refer to the Cypress application note System Design Guidelines on .Selection Guide133 MHz 117 MHz 100 MHz Unit Maximum Access Time6.57.58.0ns Maximum Operating Current 225220205mA Maximum Standby Current404040mAShaded areas contain advance information. Please contact your local Cypress sales representative for availability of these parts.Pin Configurations100-Pin TQFPAAAAA 1A 0N C N CV S SV D DN C A AAAA ANC DQ B V DDQ V SSQ DQ B DQ B DQ B DQ B V SSQ V DDQ DQ B DQ B V SS NC V DD DQ A DQ A V DDQ V SSQ DQ A DQ A DQ A DQ A V SSQ V DDQ DQ A DQ A NCNC DQ C DQ C V DDQ V SSQ DQ C DQ CDQ C DQ C V SSQ V DDQ DQ C DQ C NC V DD NC V SS DQ D DQ D V DDQ V SSQ DQ D DQ D DQ D DQ D V SSQ V DDQ DQ D DQ D NCAAC E 1C E 2B W DB W CB W BB W AC E 3V D DV S SC L KG WB W EO E A D S P A A123456789101112131415161718192021222324252627282930313233343536373839404142434445464748495080797877767574737271706968676665646362616059585756555453525110099989796959493929190898887868584838281BYTE ABYTE CAA D V A D S C ZZ M O D E N C BYTE BDQ B BYTE DCY7C1338GPin DefinitionsName I/O DescriptionA0, A1, A Input-Synchronous Address Inputs used to select one of the 128K address location s. Sampled at the rising edge of the CLK if ADSP or ADSC is active LOW, and CE1,CE2, and CE3 are sampled active. A[1:0] feed the 2-bit counter.BW A,BW B BW C,BW DInput-SynchronousByte Write Select Inputs, active LOW. Qualified with BWE to conduct byte writes to the SRAM.Sampled on the rising edge of CLK.GW Input-Synchronous Global Write Enable Input, active LOW. When asserted LOW on the rising edge of CLK, a global write is conducted (ALL bytes are written, regardless of the values on BW[A:D] and BWE).BWE Input-Synchronous Byte Write Enable Input, active LOW. Sampled on the rising edge of CLK. This signal must be asserted LOW to conduct a byte write.CLK Input-Clock Clock Input. Used to capture all synchronous inputs to the device. Also used to increment the burst counter when ADV is asserted LOW, during a burst operation.CE1Input-Synchronous Chip Enable 1 Input, active LOW. Sampled on the rising edge of CLK. Used in conjunction with CE2 and CE3 to select/deselect the device. ADSP is ignored if CE1 is HIGH.CE1 is sampled only when a new external address is loaded.CE2Input-Synchronous Chip Enable 2 Input, active HIGH. Sampled on the rising edge of CLK. Used in conjunction with CE1 and CE3 to select/deselect the device. CE2 is sampled only when a new external address is loaded.CE3Input-Synchronous Chip Enable 3 Input, active LOW. Sampled on the rising edge of CLK. Used in conjunction with CE1 and CE2 to select/deselect the device. CE3 is sampled only when a new external address is loaded.OE Input-Asynchronous Output Enable, asynchronous input, active LOW. Controls the direction of the I/O pins. When LOW, the I/O pins behave as outputs. When deasserted HIGH, I/O pins are tri-stated, and act as input data pins. OE is masked during the first clock of a read cycle when emerging from a deselected state.ADV Input-Synchronous Advance Input signal, sampled on the rising edge of CLK. When asserted, it automatically increments the address in a burst cycle.Pin Configurations (continued)2345671A B C D E F G H J K L M N P R T U V DDQNCNCNCDQ CDQ DDQ CDQ DA A A AADSP V DDQ CE2ADQ CV DDQDQ CV DDQV DDQV DDQDQ DDQ DNCNCV DDQV DDCLKV DDV SSV SSV SSV SSV SSV SSV SSV SSNCNCNCNCNCNCNCNCNCNCNCV DDQV DDQV DDQA A AANCAAAAAAA0A1DQ A DQ CDQ ADQ ADQ ADQ BDQ BDQ BDQ BDQ BDQ BDQ BDQ ADQ ADQ ADQ ADQ BV DDDQ CDQ CDQ CV DDDQ DDQ DDQ DDQ DADSCNCCE1OEADVGWV SSV SSV SSV SSV SSV SSV SSV SS NCMODENCNCBW BBW CNC V DD NCBW ANCBWEBW DZZ119-Ball BGAFunctional OverviewAll synchronous inputs pass through input registers controlled by the rising edge of the clock. Maximum access delay from the clock rise (t C0) is 6.5 ns (133-MHz device).The CY7C1338G supports secondary cache in systems utilizing either a linear or interleaved burst sequence. The interleaved burst order supports Pentium ® and i486™processors. The linear burst sequence is suited for processors that utilize a linear burst sequence. The burst order is user-selectable, and is determined by sampling the MODE input. Accesses can be initiated with either the Processor Address Strobe (ADSP) or the Controller Address Strobe (ADSC). Address advancement through the burst sequence is controlled by the ADV input. A two-bit on-chip wraparound burst counter captures the first address in a burst sequence and automatically increments the address for the rest of the burst access.Byte write operations are qualified with the Byte Write Enable (BWE) and Byte Write Select (BW [A:D]) inputs. A Global Write Enable (GW) overrides all byte write inputs and writes data to all four bytes. All writes are simplified with on-chip synchronous self-timed write circuitry.Three synchronous Chip Selects (CE 1, CE 2, CE 3) and an asynchronous Output Enable (OE) provide for easy bank selection and output tri-state control. ADSP is ignored if CE 1is HIGH.Single Read AccessesA single read access is initiated when the following conditions are satisfied at clock rise: (1) CE 1, CE 2, and CE 3 are all asserted active, and (2) ADSP or ADSC is asserted LOW (if the access is initiated by ADSC, the write inputs must be deasserted during this first cycle). The address presented to the address inputs is latched into the address register and the burst counter/control logic and presented to the memory core.If the OE input is asserted LOW, the requested data will be available at the data outputs a maximum to t CDV after clock rise. ADSP is ignored if CE 1 is HIGH.Single Write Accesses Initiated by ADSPThis access is initiated when the following conditions are satisfied at clock rise: (1) CE 1, CE 2, CE 3 are all asserted active, and (2) ADSP is asserted LOW. The addresses presented are loaded into the address register and the burst inputs (GW, BWE, and BW[A:D ])are ignored during this first clock cycle. If the write inputs are asserted active (see Write Cycle Descriptions table for appropriate states that indicate a write) on the next clock rise, the appropriate data will be latched and written into the device. Byte writes are allowed.During byte writes, BW A controls DQ A and BWB controls DQ B .BWC controls DQ C , and BW D controls DQ D . All I/Os are tri-stated during a byte write.Since this is a common I/O device, the asynchronous OE input signal must be deasserted and the I/Os must be tri-stated prior to the presentation of data to DQs. As a safety precaution, the data lines are tri-stated once a write cycle is detected, regardless of the state of OE.ADSPInput-Synchronous Address Strobe from Processor, sampled on the rising edge of CLK, active LOW . Whenasserted LOW, addresses presented to the device are captured in the address registers. A [1:0] arealso loaded into the burst counter. When ADSP and ADSC are both asserted, only ADSP is recog-nized. ASDP is ignored when CE 1 is deasserted HIGHADSC Input-Synchronous Address Strobe from Controller, sampled on the rising edge of CLK, active LOW . When assertedLOW, addresses presented to the device are captured in the address registers. A [1:0] are also loadedinto the burst counter. When ADSP and ADSC are both asserted, only ADSP is recognized.ZZInput-Asynchronous ZZ “sleep” Input, active HIGH . When asserted HIGH places the device in a non-time-critical “sleep”condition with data integrity preserved. For normal operation, this pin has to be LOW or left floating.ZZ pin has an internal pull-down.DQsI/O-Synchronous Bidirectional Data I/O lines . As inputs, they feed into an on-chip data register that is triggered bythe rising edge of CLK. As outputs, they deliver the data contained in the memory location specifiedby the addresses presented during the previous clock rise of the read cycle. The direction of the pins is controlled by OE . When OE is asserted LOW, the pins behave as outputs. When HIGH, DQs are placed in a tri-state condition.V DD Power Supply Power supply inputs to the core of the device .V SS GroundGround for the core of the device .V DDQ I/O Power SupplyPower supply for the I/O circuitry . V SSQ I/O Ground Ground for the I/O circuitry . MODEInput-StaticSelects Burst Order . When tied to GND selects linear burst sequence. When tied to V DD or left floating selects interleaved burst sequence. This is a strap pin and should remain static during device operation. Mode Pin has an internal pull-up.NCNo Connects . Not Internally connected to the die.Pin Definitions (continued)Name I/ODescriptionSingle Write Accesses Initiated by ADSCThis write access is initiated when the following conditions are satisfied at clock rise: (1) CE1, CE2, and CE3 are all asserted active, (2) ADSC is asserted LOW, (3) ADSP is deasserted HIGH, and (4) the write input signals (GW, BWE, and BW[A:D]) indicate a write access. ADSC is ignored if ADSP is active LOW.The addresses presented are loaded into the address register and the burst counter/control logic and delivered to the memory core. The information presented to DQ[A:D] will be written into the specified address location. Byte writes are allowed. During byte writes, BW A controls DQ A, BW B controls DQ B, BW C controls DQ C, and BW D controls DQ D. All I/Os are tri-stated when a write is detected, even a byte write. Since this is a common I/O device, the asynchronous OE input signal must be deasserted and the I/Os must be tri-stated prior to the presentation of data to DQs. As a safety precaution, the data lines are tri-stated once a write cycle is detected, regardless of the state of OE.Burst SequencesThe CY7C1338G provides an on-chip two-bit wraparound burst counter inside the SRAM. The burst counter is fed by A[1:0], and can follow either a linear or interleaved burst order. The burst order is determined by the state of the MODE input.A LOW on MODE will select a linear burst sequence. A HIGH on MODE will select an interleaved burst order. Leaving MODE unconnected will cause the device to default to a inter-leaved burst sequence.Sleep ModeThe ZZ input pin is an asynchronous input. Asserting ZZ places the SRAM in a power conservation “sleep” mode. Two clock cycles are required to enter into or exit from this “sleep”mode. While in this mode, data integrity is guaranteed. Accesses pending when entering the “sleep” mode are not considered valid nor is the completion of the operation guaranteed. The device must be deselected prior to entering the “sleep” mode. CEs, ADSP, and ADSC must remain inactive for the duration of t ZZREC after the ZZ input returns LOW.Interleaved Burst Address Table(MODE = Floating or V DD)FirstAddressA1, A0SecondAddressA1, A0ThirdAddressA1, A0FourthAddressA1, A0 00011011010011101011000111100100 Linear Burst Address Table (MODE = GND) FirstAddressA1,A0SecondAddressA1,A0ThirdAddressA1,A0FourthAddressA1,A0 00011011011011001011000111000110ZZ Mode Electrical CharacteristicsParameter Description Test Conditions Min.Max.Unit I DDZZ Snooze mode standby current ZZ > V DD– 0.2V40mA t ZZS Device operation to ZZ ZZ > V DD – 0.2V2t CYC ns t ZZREC ZZ recovery time ZZ < 0.2V2t CYC ns t ZZI ZZ active to snooze current This parameter is sampled2t CYC ns t RZZI ZZ Inactive to exit snooze current This parameter is sampled0nsTruth Table[2, 3, 4, 5, 6]Cycle Description AddressUsed CE1CE2CE3ZZ ADSP ADSC ADV WRITE OE CLK DQDeselected Cycle, Power-down None H X X L X L X X X L-H tri-state Deselected Cycle, Power-down None L L X L L X X X X L-H tri-state Deselected Cycle, Power-down None L X H L L X X X X L-H tri-state Deselected Cycle, Power-down None L L X L H L X X X L-H tri-state Deselected Cycle, Power-down None X X X L H L X X X L-H tri-state Snooze Mode, Power-down None X X X H X X X X X X tri-state Read Cycle, Begin Burst External L H L L L X X X L L-H QRead Cycle, Begin Burst External L H L L L X X X H L-H tri-state Write Cycle, Begin Burst External L H L L H L X L X L-H DRead Cycle, Begin Burst External L H L L H L X H L L-H QRead Cycle, Begin Burst External L H L L H L X H H L-H tri-state Read Cycle, Continue Burst Next X X X L H H L H L L-H QRead Cycle, Continue Burst Next X X X L H H L H H L-H tri-state Read Cycle, Continue Burst Next H X X L X H L H L L-H QRead Cycle, Continue Burst Next H X X L X H L H H L-H tri-state Write Cycle, Continue Burst Next X X X L H H L L X L-H DWrite Cycle, Continue Burst Next H X X L X H L L X L-H DRead Cycle, Suspend Burst Current X X X L H H H H L L-H QRead Cycle, Suspend Burst Current X X X L H H H H H L-H tri-state Read Cycle, Suspend Burst Current H X X L X H H H L L-H QRead Cycle, Suspend Burst Current H X X L X H H H H L-H tri-state Write Cycle, Suspend Burst Current X X X L H H H L X L-H DWrite Cycle, Suspend Burst Current H X X L X H H L X L-H D Notes:2.X = “Don't Care.” H = Logic HIGH, L = Logic LOW.3.WRITE = L when any one or more Byte Write enable signals (BW A, BW B, BW C, BW D) and BWE = L or GW= L. WRITE = H when all Byte write enable signalsA B C D4.The DQ pins are controlled by the current cycle and the OE signal. OE is asynchronous and is not sampled with the clock.5.The SRAM always initiates a read cycle when ADSP is asserted, regardless of the state of GW, BWE, or BW X. Writes may occur only on subsequent clocksafter the or with the assertion of ADSC. As a result, OE must be driven HIGH prior to the start of the write cycle to allow the outputs to tri-state. OE is a don't care for the remainder of the write cycle.6.OE is asynchronous and is not sampled with the clock rise. It is masked internally during write cycles. During a read cycle all data bits are tri-state when OE isinactive or when the device is deselected, and all data bits behave as output when OE is active (LOW).Partial Truth Table for Read/Write[2, 7]Function GW BWE BW D BW C BW B BW A Read H H X X X X Read H L H H H H Write Byte A H L H H H L Write Byte B H L H H L H Write Bytes B, A H L H H L L Write Byte C H L H L H H Write Bytes C, A H L H L H L Write Bytes C, B H L H L L H Write Bytes C, B, A H L H L L L Write Byte D H L L H H H Write Bytes D, A H L L H H L Write Bytes D, B H L L H L H Write Bytes D, B, A H L L H L L Write Bytes D, B H L L L H H Write Bytes D, B, A H L L L H L Write Bytes D,C,A H L L L L H Write All Bytes H L L L L L Write All Bytes L X X X X X Note:7.Table only lists a partial listing of the byte write combinations. Any combination of BW X is valid. Appropriate write will be done based on which byte write is active.Maximum Ratings(Above which the useful life may be impaired. For user guide-lines, not tested.)Storage Temperature .................................–65°C to +150°C Ambient Temperature withPower Applied.............................................–55°C to +125°C Supply Voltage on V DD Relative to GND........–0.5V to +4.6V DC Voltage Applied to Outputsin tri-state............................................–0.5V to V DDQ + 0.5V DC Input Voltage....................................–0.5V to V DD + 0.5V Current into Outputs (LOW).........................................20 mA Static Discharge Voltage........................................... >2001V (per MIL-STD-883, Method 3015)Latch-up Current..................................................... >200 mA Operating RangeRangeAmbientTemperature]V DD V DDQ Commercial0°C to +70°C 3.3V −5%/+10% 2.5V –5%to V DD Industrial–40°C to +85°CElectrical Characteristics Over the Operating Range[8, 9]Parameter Description Test ConditionsCY7C1338GUnit Min.Max.V DD Power Supply Voltage 3.135 3.6V V DDQ I/O Supply Voltage 2.375V DD V V OH Output HIGH Voltage V DDQ = 3.3V, V DD = Min., I OH = –4.0 mA 2.4VV DDQ = 2.5V, V DD = Min., I OH = –1.0 mA 2.0V V OL Output LOW Voltage V DDQ = 3.3V, V DD = Min., I OL = 8.0 mA0.4VV DDQ = 2.5V, V DD = Min., I OL = 1.0 mA0.4V V IH Input HIGH Voltage V DDQ = 3.3V 2.0V DD + 0.3V VV DDQ = 2.5V 1.7V DD + 0.3V V V IL Input LOW Voltage[8]V DDQ = 3.3V–0.30.8VV DDQ = 2.5V–0.30.7V I X Input Load Current (except ZZ andMODE)GND ≤ V I≤ V DDQ−55µA Input Current of MODE Input = V SS–30µAInput = V DD5µA Input Current of ZZ Input = V SS–5µAInput = V DD30µA I OZ Output Leakage Current GND ≤ V I≤ V DD, Output Disabled–55µA I OS Output Short Circuit Current V DD = Max., V OUT = GND–300µAI DD V DD Operating Supply Current V DD = Max., I OUT = 0 mA,f = f MAX= 1/t CYC 7.5-ns cycle, 133 MHz225mA8.0-ns cycle, 117 MHz220mA 10-ns cycle, 100 MHz205mAI SB1Automatic CE Power-DownCurrent—TTL Inputs Max. V DD, Device Deselected,V IN≥ V IH or V IN≤ V IL, f = f MAX,inputs switching7.5-ns cycle, 133 MHz90mA8.0-ns cycle, 117 MHz85mA10-ns cycle, 100 MHz80mAI SB2Automatic CE Power-DownCurrent—CMOS Inputs Max. V DD, Device Deselected,V IN≥ V DD – 0.3V or V IN≤ 0.3V,f = 0, inputs staticAll speeds40mAI SB3Automatic CE Power-DownCurrent—CMOS Inputs Max. V DD, Device Deselected,V IN≥V DDQ – 0.3V or V IN≤ 0.3V,f = f MAX, inputs switching7.5-ns cycle, 133 MHz75mA8.0-ns cycle, 117 MHz70mA10-ns cycle, 100 MHz65mAI SB4Automatic CE Power-DownCurrent—TTL Inputs Max. V DD, Device Deselected,V IN≥ V DD – 0.3V or V IN≤ 0.3V,f=0, inputs staticAll speeds45mAShaded areas contain advance information.Notes:8.Overshoot: V IH(AC) < V DD +1.5V (Pulse width less than t CYC/2), undershoot: V IL(AC) > -2V (Pulse width less than t CYC/2).9.TPower-up: Assumes a linear ramp from 0v to V DD(min.) within 200ms. During this time V IH < V DD and V DDQ < V DD.Thermal Resistance [10]Parameter DescriptionTest ConditionsTQFP PackageBGA PackageUnit ΘJAThermal Resistance (Junction to Ambient)Test conditions follow standard test methods and procedures formeasuring thermal impedance, per EIA / JESD51.TBD TBD °C/W ΘJC Thermal Resistance(Junction to Case)TBDTBD°C/WCapacitance [10]Parameter DescriptionTest Conditions TQFP PackageBGA Package UnitC IN Input Capacitance T A = 25°C, f = 1 MHz,V DD = 3.3V. V DDQ = 3.3V55pF C CLK Clock Input Capacitance 55pF C I/OInput/Output Capacitance57pFAC Test Loads and WaveformsSwitching Characteristics Over the Operating Range [11, 12, 13, 14, 15, 16]Parameter Description133 MHz117 MHz 100 MHz Unit Min.Max.Min.Max.Min.Max.t POWER V DD (Typical) to the first Access [11]111msClock t CYC Clock Cycle Time 7.58.510ns t CH Clock HIGH 2.5 3.0 4.0ns t CLClock LOW2.53.04.0nsOutput Times t CDV Data Output Valid After CLK Rise 6.57.58.0ns t DOHData Output Hold After CLK Rise2.02.02.0nsShaded areas contain advance information.Notes:10.Tested initially and after any design or process change that may affect these parameters.11.This part has a voltage regulator internally; t POWER is the time that the power needs to be supplied above V DD (minimum) initially before a read or write operationcan be initiated.12.t CHZ , t CLZ ,t OELZ , and t OEHZ are specified with AC test conditions shown in part (b) of AC Test Loads. Transition is measured ± 200 mV from steady-state voltage.13.At any given voltage and temperature, t OEHZ is less than t OELZ and t CHZ is less than t CLZ to eliminate bus contention between SRAMs when sharing the samedata bus. These specifications do not imply a bus contention condition, but reflect parameters guaranteed over worst case user conditions. Device is designed to achieve High-Z prior to Low-Z under the same system conditions.14.This parameter is sampled and not 100% tested.15.Timing reference level is 1.5V when V DDQ = 3.3V and is 1.25V when V DDQ = 2.5V.16.Test conditions shown in (a) of AC Test Loads unless otherwise noted.OUTPUTR = 317ΩR = 351Ω5pFINCLUDING JIG AND SCOPE (a)(b)OUTPUTR L = 50ΩZ 0= 50ΩV T = 1.5V3.3VALL INPUT PULSESV DDQ GND90%10%90%10%≤1ns≤1ns(c)OUTPUTR = 1667ΩR =1538Ω5pFINCLUDING JIG AND SCOPE(a)(b)OUTPUTR L = 50ΩZ 0= 50ΩV T = 1.25V2.5VALL INPUT PULSES V DDQGND90%10%90%10%≤1ns≤1ns(c)3.3V I/O Test Load2.5V I/O Test Loadt CLZ Clock to Low-Z [12, 13, 14]0ns t CHZ Clock to High-Z [12, 13, 14] 3.5 3.5 3.5ns t OEV OE LOW to Output Valid3.53.5 3.5ns t OELZ OE LOW to Output Low-Z [12, 13, 14]0ns t OEHZOE HIGH to Output High-Z [12, 13, 14]3.53.53.5ns Setup Times t AS Address Set-up Before CLK Rise 1.5 2.0 2.0ns t ADS ADSP , ADSC Set-up Before CLK Rise 1.5 2.0 2.0ns t ADVS ADV Set-up Before CLK Rise1.52.0 2.0ns t WES GW, BWE, BW X Set-up Before CLK Rise 1.5 2.0 2.0ns t DS Data Input Set-up Before CLK Rise 1.5 1.5 1.5ns t CESChip Enable Set-up1.52.02.0ns Hold Times t AH Address Hold After CLK Rise 0.50.50.5ns t ADH ADSP , ADSC Hold After CLK Rise 0.50.50.5ns t WEH GW ,BWE , BW X Hold After CLK Rise 0.50.50.5ns t ADVH ADV Hold After CLK Rise 0.50.50.5ns t DH Data Input Hold After CLK Rise 0.50.50.5ns t CEHChip Enable Hold After CLK Rise0.50.50.5nsSwitching Characteristics Over the Operating Range (continued)[11, 12, 13, 14, 15, 16]Parameter Description133 MHz117 MHz 100 MHz Unit Min.Max.Min.Max.Min.Max.Timing Diagrams[17]Timing Diagrams (continued)[17, 18]Timing Diagrams (continued)[17, 19, 20]ZZ Mode Timing [21, 22]Ordering InformationSpeed (MHz)Ordering Code Package Name Package TypeOperating Range 133CY7C1338G-133AXC A101Lead-Free 100-Lead Thin Quad Flat Pack (14 x 20 x 1.4mm)CommercialCY7C1338G-133BGC BG119119-Ball PBGA (14 x 22 x 2.4mm)CY7C1338G-133BGXC BG119Lead-Free 119-Ball PBGA (14 x 22 x 2.4mm)CY7C1338G-133AXI A101Lead-Free 100-Lead Thin Quad Flat Pack (14 x 20 x 1.4mm)Industrial CY7C1338G-133BGI BG119119-Ball PBGA (14 x 22 x 2.4mm)CY7C1338G-133BGXIBG119Lead-Free 119-Ball PBGA (14 x 22 x 2.4mm)117CY7C1338G-117AXC A101Lead-Free 100-Lead Thin Quad Flat Pack (14 x 20 x 1.4mm)Commercial CY7C1338G-117BGC BG119119-Ball PBGA (14 x 22 x 2.4mm)CY7C1338G-117BGXCBG119Lead-Free 119-Ball PBGA (14 x 22 x 2.4mm)CY7C1338G-117AXI A101Lead-Free 100-Lead Thin Quad Flat Pack (14 x 20 x 1.4mm)Industrial CY7C1338G-117BGI BG119119-Ball PBGA (14 x 22 x 2.4mm)CY7C1338G-117BGXIBG119Lead-Free 119-Ball PBGA (14 x 22 x 2.4mm)100CY7C1338G-100AXC A101Lead-Free 100-Lead Thin Quad Flat Pack (14 x 20 x 1.4mm)Commercial CY7C1338G-100BGC BG119119-Ball PBGA (14 x 22 x 2.4mm)CY7C1338G-100BGXC BG119Lead-Free 119-Ball PBGA (14 x 22 x 2.4mm)CY7C1338G-100AXI A101Lead-Free 100-Lead Thin Quad Flat Pack (14 x 20 x 1.4mm)Industrial CY7C1338G-100BGI BG119119-Ball PBGA (14 x 22 x 2.4mm)CY7C1338G-100BGXIBG119Lead-Free 119-Ball PBGA (14 x 22 x 2.4mm)Shaded areas contain advance information. Please contact your local Cypress sales representative for availability of these parts. Lead-Free BGX package will be available in 2005.Notes:21.Device must be deselected when entering ZZ mode. See Cycle Descriptions table for all possible signal conditions to deselect the device.22.DQs are in high-Z when exiting ZZ sleep mode.Timing Diagrams (continued)Package DiagramsDocument #: 38-05521 Rev. *A Page 16 of 17Intel and Pentium are registered trademarks of Intel Corporation. All product and company names mentioned in this document may be the trademarks of their respective holders.Package Diagrams(continued)Document History PageDocument Title: CY7C1338G 4-Mbit (128K x 32) Flow-Through Sync SRAM Document Number: 38-05521REV.ECN NO.Issue Date Orig. ofChange Description of Change**224369See ECN RKF New data sheet*A278513See ECN VBL Deleted 66 MHzChanged TQFP to PB-Free TQFP in Ordering Info sectionAdded PB-Free BG package。
CY7C1041CV33-10ZXI中文资料

Industrial
100
95
Automotive-A
100
Automotive-E
Commercial/
10
10
Industrial
Automotive-A
10
Automotive-E
48-ball FBGA
(Top View)
12
3
4
5
6
CY7C1041CV33
-15
-20
Unit
15
20
ns
80
28
A6, E3, G2, H1, No Connect No Connects. This pin is not connected to the die
H6
17
G5
Input/Control Write Enable Input, active LOW. When selected LOW, a
A5 18 A6 19 A7 20 A8 21 A9 22
44 A17 43 A16 42 A15 41 OE
40 BHE 39 BLE
38 I/O15 37 I/O14 36 I/O13 35 I/O12 34 VSS 33 VCC 32 I/O11 31 I/O10 30 I/O9 29 I/O8 28 NC
WRITE is conducted. When selected HIGH, a READ is
conducted.
6
ห้องสมุดไป่ตู้B5
Input/Control Chip Enable Input, active LOW. When LOW, selects the chip.
When HIGH, deselects the chip.
CY7C63723-PC中文资料
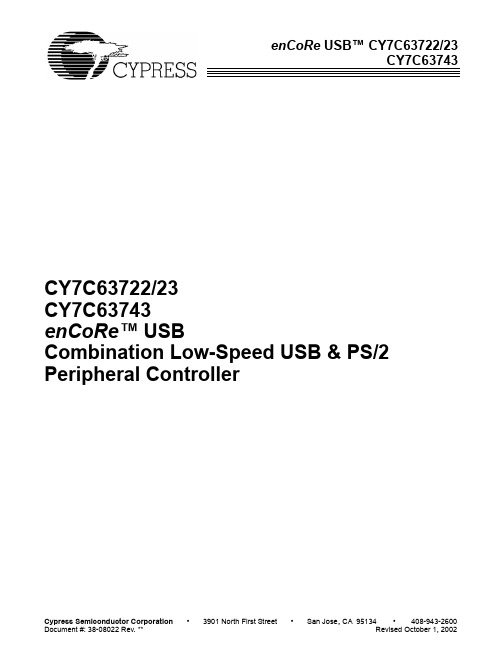
元器件交易网CY7C63743CY7C63722/23CY7C63743enCoRe™ USBCombination Low-Speed USB & PS/2Peripheral ControllerTABLE OF CONTENTS1.0 FEATURES (5)2.0 FUNCTIONAL OVERVIEW (6)2.1 enCoRe USB - The New USB Standard (6)3.0 LOGIC BLOCK DIAGRAM (7)4.0 PIN CONFIGURATIONS (7)5.0 PIN ASSIGNMENTS (7)6.0 PROGRAMMING MODEL (8)6.1 Program Counter (PC) (8)6.2 8-bit Accumulator (A) (8)6.3 8-bit Index Register (X) (8)6.4 8-bit Program Stack Pointer (PSP) (8)6.5 8-bit Data Stack Pointer (DSP) (9)6.6 Address Modes (9)6.6.1 Data (9)6.6.2 Direct (9)6.6.3 Indexed (9)7.0 INSTRUCTION SET SUMMARY (10)8.0 MEMORY ORGANIZATION (11)8.1 Program Memory Organization (11)8.2 Data Memory Organization (12)8.3 I/O Register Summary (13)9.0 CLOCKING (14)9.1 Internal/External Oscillator Operation (15)9.2 External Oscillator (16)10.0 RESET (16)10.1 Low-voltage Reset (LVR) (16)10.2 Brown Out Reset (BOR) (16)10.3 Watchdog Reset (WDR) (17)11.0 SUSPEND MODE (17)11.1 Clocking Mode on Wake-up from Suspend (18)11.2 Wake-up Timer (18)12.0 GENERAL PURPOSE I/O PORTS (18)12.1 Auxiliary Input Port (21)13.0 USB SERIAL INTERFACE ENGINE (SIE) (22)13.1 USB Enumeration (22)13.2 USB Port Status and Control (22)14.0 USB DEVICE (24)14.1 USB Address Register (24)14.2 USB Control Endpoint (24)14.3 USB Non-control Endpoints (25)14.4 USB Endpoint Counter Registers (26)15.0 USB REGULATOR OUTPUT (27)16.0 PS/2 OPERATION (27)17.0 SERIAL PERIPHERAL INTERFACE (SPI) (28)17.1 Operation as an SPI Master (29)17.2 Master SCK Selection (29)17.3 Operation as an SPI Slave (29)17.4 SPI Status and Control (30)17.5 SPI Interrupt (31)17.6 SPI Modes for GPIO Pins (31)18.0 12-BIT FREE-RUNNING TIMER (31)19.0 TIMER CAPTURE REGISTERS (32)20.0 PROCESSOR STATUS AND CONTROL REGISTER (35)21.0 INTERRUPTS (36)21.1 Interrupt Vectors (37)21.2 Interrupt Latency (37)21.3 Interrupt Sources (37)22.0 USB MODE TABLES (42)23.0 REGISTER SUMMARY (47)24.0 ABSOLUTE MAXIMUM RATINGS (48)25.0 DC CHARACTERISTICS (48)26.0 SWITCHING CHARACTERISTICS (50)27.0 ORDERING INFORMATION (55)28.0 PACKAGE DIAGRAMS (55)LIST OF FIGURESFigure 8-1. Program Memory Space with Interrupt Vector Table (11)Figure 8-2. Data Memory Organization (12)Figure 9-1. Clock Oscillator On-chip Circuit (14)Figure 9-2. Clock Configuration Register (Address 0xF8) (14)Figure 10-1. Watchdog Reset (WDR, Address 0x26) (17)Figure 12-1. Block Diagram of GPIO Port (one pin shown) (19)Figure 12-2. Port 0 Data (Address 0x00) (19)Figure 12-3. Port 1 Data (Address 0x01) (19)Figure 12-4. GPIO Port 0 Mode0 Register (Address 0x0A) (20)Figure 12-5. GPIO Port 0 Mode1 Register (Address 0x0B) (20)Figure 12-6. GPIO Port 1 Mode0 Register (Address 0x0C) (20)Figure 12-7. GPIO Port 1 Mode1 Register (Address 0x0D) (20)Figure 12-8. Port 2 Data Register (Address 0x02) (21)Figure 13-1. USB Status and Control Register (Address 0x1F) (23)Figure 14-1. USB Device Address Register (Address 0x10) (24)Figure 14-2. Endpoint 0 Mode Register (Address 0x12) (25)Figure 14-3. USB Endpoint EP1, EP2 Mode Registers (Addresses 0x14 and 0x16) (26)Figure 14-4. Endpoint 0,1,2 Counter Registers (Addresses 0x11, 0x13 and 0x15) (26)Figure 17-1. SPI Block Diagram (28)Figure 16-1. Diagram of USB-PS/2 System Connections (28)Figure 17-2. SPI Data Register (Address 0x60) (29)Figure 17-3. SPI Control Register (Address 0x61) (30)Figure 17-4. SPI Data Timing (31)Figure 18-1. Timer LSB Register (Address 0x24) (31)Figure 18-2. Timer MSB Register (Address 0x25) (32)Figure 18-3. Timer Block Diagram (32)Figure 19-1. Capture Timers Block Diagram (33)Figure 19-2. Capture Timer A-Rising, Data Register (Address 0x40) (33)Figure 19-3. Capture Timer A-Falling, Data Register (Address 0x41) (34)Figure 19-4. Capture Timer B-Rising, Data Register (Address 0x42) (34)Figure 19-5. Capture Timer B-Falling, Data Register (Address 0x43) (34)Figure 19-6. Capture Timer Status Register (Address 0x45) (34)Figure 19-7. Capture Timer Configuration Register (Address 0x44) (34)Figure 20-1. Processor Status and Control Register (Address 0xFF) (35)Figure 21-1. Global Interrupt Enable Register (Address 0x20) (38)Figure 21-2. Endpoint Interrupt Enable Register (Address 0x21) (39)Figure 21-3. Interrupt Controller Logic Block Diagram (40)Figure 21-4. Port 0 Interrupt Enable Register (Address 0x04) (40)Figure 21-5. Port 1 Interrupt Enable Register (Address 0x05) (40)Figure 21-6. Port 0 Interrupt Polarity Register (Address 0x06) (41)Figure 21-7. Port 1 Interrupt Polarity Register (Address 0x07) (41)Figure 21-8. GPIO Interrupt Diagram (41)Figure 26-1. Clock Timing (51)Figure 26-2. USB Data Signal Timing (51)Figure 26-3. Receiver Jitter Tolerance (52)Figure 26-4. Differential to EOP Transition Skew and EOP Width (52)Figure 26-5. Differential Data Jitter (52)Figure 26-7. SPI Slave Timing, CPHA = 0 (53)Figure 26-6. SPI Master Timing, CPHA = 0 (53)Figure 26-8. SPI Master Timing, CPHA = 1 (54)Figure 26-9. SPI Slave Timing, CPHA = 1 (54)LIST OF TABLESTable 8-1. I/O Register Summary (13)Table 11-1. Wake-up Timer Adjust Settings (18)Table 12-1. Ports 0 and 1 Output Control Truth Table (21)Table 13-1. Control Modes to Force D+/D– Outputs (24)Table 17-1. SPI Pin Assignments (31)Table 19-1. Capture Timer Prescalar Settings (Step size and range for FCLK = 6 MHz) (35)Table 21-1. Interrupt Vector Assignments (37)Table 22-1. USB Register Mode Encoding for Control and Non-Control Endpoints (42)Table 22-2. Decode table for Table 22-3: “Details of Modes for Differing Traffic Conditions” (44)Table 22-3. Details of Modes for Differing Traffic Conditions (45)Table 28-1. CY7C63722-XC Probe Pad Coordinates in microns ((0,0) to bond pad centers) (57)1.0 Features•enCoRe™ USB - enhanced Component Reduction—Internal oscillator eliminates the need for an external crystal or resonator—Interface can auto-configure to operate as PS/2 or USB without the need for external components to switch between modes (no GPIO pins needed to manage dual mode capability)—Internal 3.3V regulator for USB pull-up resistor—Configurable GPIO for real-world interface without external components•Flexible, cost-effective solution for applications that combine PS/2 and low-speed USB, such as mice, gamepads, joysticks, and many others.•USB Specification Compliance—Conforms to USB Specification, Version 2.0—Conforms to USB HID Specification, Version 1.1—Supports 1 Low-Speed USB device address and 3 data endpoints—Integrated USB transceiver—3.3V regulated output for USB pull-up resistor•8-bit RISC microcontroller—Harvard architecture—6-MHz external ceramic resonator or internal clock mode—12-MHz internal CPU clock—Internal memory—256 bytes of RAM—8 Kbytes of EPROM—Interface can auto-configure to operate as PS/2 or USB—No external components for switching between PS/2 and USB modes—No GPIO pins needed to manage dual mode capability•I/O ports—Up to 16 versatile General Purpose I/O (GPIO) pins, individually configurable—High current drive on any GPIO pin: 50 mA/pin current sink—Each GPIO pin supports high-impedance inputs, internal pull-ups, open drain outputs or traditional CMOS outputs —Maskable interrupts on all I/O pins•SPI serial communication block—Master or slave operation—2 Mbit/s transfers•Four 8-bit Input Capture registers—Two registers each for two input pins—Capture timer setting with 5 prescaler settings—Separate registers for rising and falling edge capture—Simplifies interface to RF inputs for wireless applications•Internal low-power wake-up timer during suspend mode—Periodic wake-up with no external components•Optional 6-MHz internal oscillator mode—Allows fast start-up from suspend mode•Watchdog Reset (WDR)•Low-voltage Reset at 3.75V•Internal brown-out reset for suspend mode•Improved output drivers to reduce EMI•Operating voltage from 4.0V to 5.5VDC•Operating temperature from 0 to 70 degrees Celsius•CY7C63723 available in 18-pin SOIC, 18-pin PDIP•CY7C63743 available in 24-pin SOIC, 24-pin PDIP•CY7C63722 available in DIE form•Industry standard programmer support2.0 Functional Overview2.1enCoRe USB - The New USB StandardCypress has re-invented its leadership position in the low-speed USB market with a new family of innovative microcontrollers. Introducing...enCoRe USB—“enhanced Component Reduction.” Cypress has leveraged its design expertise in USB solutions to create a new family of low-speed USB microcontrollers that enables peripheral developers to design new products with a minimum number of components. At the heart of the enCoRe USB technology is the breakthrough design of a crystal-less oscillator. By integrating the oscillator into our chip, an external crystal or resonator is no longer needed. We have also integrated other external components commonly found in low-speed USB applications such as pull-up resistors, wake-up circuitry, and a 3.3V regulator. All of this adds up to a lower system cost.The CY7C637xx is an 8-bit RISC One Time Programmable (OTP) microcontroller. The instruction set has been optimized specif-ically for USB and PS/2 operations, although the microcontrollers can be used for a variety of other embedded applications. The CY7C637xx features up to 16 general purpose I/O (GPIO) pins to support USB, PS/2 and other applications. The I/O pins are grouped into two ports (Port 0 to 1) where each pin can be individually configured as inputs with internal pull-ups, open drain outputs, or traditional CMOS outputs with programmable drive strength of up to 50 mA output drive. Additionally, each I/O pin can be used to generate a GPIO interrupt to the microcontroller. Note the GPIO interrupts all share the same “GPIO” interrupt vector. The CY7C637xx microcontrollers feature an internal oscillator. With the presence of USB traffic, the internal oscillator can be set to precisely tune to USB timing requirements (6 MHz ±1.5%). Optionally, an external 6-MHz ceramic resonator can be used to provide a higher precision reference for USB operation. This clock generator reduces the clock-related noise emissions (EMI). The clock generator provides the 6- and 12-MHz clocks that remain internal to the microcontroller.The CY7C637xx has 8 Kbytes of EPROM and 256 bytes of data RAM for stack space, user variables, and USB FIFOs.These parts include low-voltage reset logic, a watchdog timer, a vectored interrupt controller, a 12-bit free-running timer, and capture timers. The low-voltage reset (LVR) logic detects when power is applied to the device, resets the logic to a known state, and begins executing instructions at EPROM address 0x0000. LVR will also reset the part when V CC drops below the operating voltage range. The watchdog timer can be used to ensure the firmware never gets stalled for more than approximately 8 ms. The microcontroller supports 10 maskable interrupts in the vectored interrupt controller. Interrupt sources include the USB Bus-Reset, the 128-µs and 1.024-ms outputs from the free-running timer, three USB endpoints, two capture timers, an internal wake-up timer and the GPIO ports. The timers bits cause periodic interrupts when enabled. The USB endpoints interrupt after USB transactions complete on the bus. The capture timers interrupt whenever a new timer value is saved due to a selected GPIO edge event. The GPIO ports have a level of masking to select which GPIO inputs can cause a GPIO interrupt. For additional flexibility, the input transition polarity that causes an interrupt is programmable for each GPIO pin. The interrupt polarity can be either rising or falling edge.The free-running 12-bit timer clocked at 1 MHz provides two interrupt sources as noted above (128 µs and 1.024 ms). The timer can be used to measure the duration of an event under firmware control by reading the timer at the start and end of an event, and subtracting the two values. The four capture timers save a programmable 8 bit range of the free-running timer when a GPIO edge occurs on the two capture pins (P0.0, P0.1).The CY7C637xx includes an integrated USB serial interface engine (SIE) that supports the integrated peripherals. The hardware supports one USB device address with three endpoints. The SIE allows the USB host to communicate with the function integrated into the microcontroller. A 3.3V regulated output pin provides a pull-up source for the external USB resistor on the D– pin.The USB D+ and D– USB pins can alternately be used as PS/2 SCLK and SDATA signals, so that products can be designed to respond to either USB or PS/2 modes of operation. PS/2 operation is supported with internal pull-up resistors on SCLK and SDATA, the ability to disable the regulator output pin, and an interrupt to signal the start of PS/2 activity. No external components are necessary for dual USB and PS/2 systems, and no GPIO pins need to be dedicated to switching between modes. Slow edge rates operate in both modes to reduce EMI.3.0 Logic Block Diagram4.0 Pin Configurations5.0 Pin AssignmentsNameI/O CY7C63723CY7C63743CY7C63722Description18-Pin 24-Pin 25-Pad D–/SDATA,D+/SCLK I/O 121315161617USB differential data lines (D– and D+), or PS/2 clock and data signals (SDATA and SCLK)P0[7:0]I/O1, 2, 3, 4,15, 16, 17, 181, 2, 3, 4,21, 22, 23, 241, 2, 3, 4,22, 23, 24, 25GPIO Port 0 capable of sinking up to 50 mA/pin, or sinking controlled low or high programmable current.Can also source 2 mA current, provide a resistive pull-up, or serve as a high-impedance input. P0.0 and P0.1 provide inputs to Capture Timers A and B, respec-tively.P1[7:0]I/O5, 145, 6, 7, 8,17, 18, 19, 205, 6, 7, 8,18, 19, 20, 21IO Port 1 capable of sinking up to 50 mA/pin, or sinking controlled low or high programmable current. Can alsosource 2 mA current, provide a resistive pull-up, or serve as a high-impedance input.Wake-Up 12-bit Timer USB &D+,D–P1.0–P1.7Interrupt ControllerPort 0P0.0–P0.7GPIO8-bit RISC Xtal RAM 256 Byte EPROM 8K ByteCoreBrown-out Reset XcvrWatch Timer Dog 3.3V Port 1GPIO Capture TimersUSB Engine PS/2Internal Oscillator Oscillator Low ResetVoltage RegulatorTimerSPIXTALOUTXTALIN/P2.1VREG/P2.01234569111516171819202221P0.0P0.1P0.2P0.3P1.0P1.2VSS VREG/P2.0P0.6P1.5P1.1P1.3D+/SCLK P1.7D–/SDATA VCC14P0.710VPPXTALIN/P2.1XTALOUT121378P1.4P1.62423P0.4P0.524-pin SOIC/PDIPCY7C6374312346781011121315161817P0.0P0.1P0.2P0.3VSS VREG/P2.0P0.4P0.6P0.7D+/SCLK D–/SDATA VCC18-pin SOIC/PDIPP0.59VPPXTALIN/P2.1XTALOUTCY7C63723514P1.0P1.1Top View4 5 6 7 8 93 P 0.21 P 0.0 2 P 0.125 P 0.4 24 P 0.523 P 0.622 21 20 19 1811121314151617P0.3P1.0P1.2P1.4P1.6 VSS VSS V P P X T A L I N /P 2.1V R E G X T A L O U T V C C D -/S D A T A D+/SCLK P0.7P1.1P1.3P1.5P1.7CY7C63722-XCDIE106.0 Programming ModelRefer to the CYASM Assembler User’s Guide for more details on firmware operation with the CY7C637xx microcontrollers.6.1Program Counter (PC)The 14-bit program counter (PC) allows access for up to 8 Kbytes of EPROM using the CY7C637xx architecture. The program counter is cleared during reset, such that the first instruction executed after a reset is at address 0x0000. This instruction is typically a jump instruction to a reset handler that initializes the application.The lower 8 bits of the program counter are incremented as instructions are loaded and executed. The upper 6 bits of the program counter are incremented by executing an XPAGE instruction. As a result, the last instruction executed within a 256-byte “page”of sequential code should be an XPAGE instruction. The assembler directive “XPAGEON” will cause the assembler to insert XPAGE instructions automatically. As instructions can be either one or two bytes long, the assembler may occasionally need to insert a NOP followed by an XPAGE for correct execution.The program counter of the next instruction to be executed, carry flag, and zero flag are saved as two bytes on the program stack during an interrupt acknowledge or a CALL instruction. The program counter, carry flag, and zero flag are restored from the program stack only during a RETI instruction.Please note the program counter cannot be accessed directly by the firmware. The program stack can be examined by reading SRAM from location 0x00 and up.6.28-bit Accumulator (A)The accumulator is the general-purpose, do everything register in the architecture where results are usually calculated.6.38-bit Index Register (X)The index register “X” is available to the firmware as an auxiliary accumulator. The X register also allows the processor to perform indexed operations by loading an index value into X.6.48-bit Program Stack Pointer (PSP)During a reset, the program stack pointer (PSP) is set to zero. This means the program “stack” starts at RAM address 0x00 and “grows” upward from there. Note that the program stack pointer is directly addressable under firmware control, using the MOV PSP ,A instruction. The PSP supports interrupt service under hardware control and CALL, RET, and RETI instructions under firmware control.During an interrupt acknowledge, interrupts are disabled and the program counter, carry flag, and zero flag are written as two bytes of data memory. The first byte is stored in the memory addressed by the program stack pointer, then the PSP is incremented.The second byte is stored in memory addressed by the program stack pointer and the PSP is incremented again. The net effect is to store the program counter and flags on the program “stack” and increment the program stack pointer by two.The return from interrupt (RETI) instruction decrements the program stack pointer, then restores the second byte from memory addressed by the PSP . The program stack pointer is decremented again and the first byte is restored from memory addressed by the PSP . After the program counter and flags have been restored from stack, the interrupts are enabled. The effect is to restore the program counter and flags from the program stack, decrement the program stack pointer by two, and re-enable interrupts.The call subroutine (CALL) instruction stores the program counter and flags on the program stack and increments the PSP by two.XTALIN/P2.1IN 912136-MHz ceramic resonator or external clock input, or P2.1 inputXTALOUT OUT1013146-MHz ceramic resonator return pin or internal oscillator outputV PP 71011Programming voltage supply, ground for normal operation V CC111415Voltage supplyVREG/P2.0 81112Voltage supply for 1.3-k Ω USB pull-up resistor (3.3V nominal). Also serves as P2.0 input.V SS699, 10Ground5.0 Pin Assignments (continued)NameI/O CY7C63723CY7C63743CY7C63722Description18-Pin 24-Pin 25-PadThe return from subroutine (RET) instruction restores the program counter, but not the flags, from program stack and decrements the PSP by two.Note that there are restrictions in using the JMP, CALL, and INDEX instructions across the 4-KB boundary of the program memory. Refer to the CYASM Assembler User’s Guide for a detailed description.6.58-bit Data Stack Pointer (DSP)The data stack pointer (DSP) supports PUSH and POP instructions that use the data stack for temporary storage. A PUSH instruction will pre-decrement the DSP, then write data to the memory location addressed by the DSP. A POP instruction will read data from the memory location addressed by the DSP, then post-increment the DSP.During a reset, the Data Stack Pointer will be set to zero. A PUSH instruction when DSP equals zero will write data at the top of the data RAM (address 0xFF). This would write data to the memory area reserved for a FIFO for USB endpoint 0. In non-USB applications, this works fine and is not a problem.For USB applications, the firmware should set the DSP to an appropriate location to avoid a memory conflict with RAM dedicated to USB FIFOs. The memory requirements for the USB endpoints are shown in Section 8.2. For example, assembly instructions to set the DSP to 20h (giving 32 bytes for program and data stack combined) are shown below:MOV A,20h; Move 20 hex into Accumulator (must be D8h or less to avoid USB FIFOs)SWAP A,DSP; swap accumulator value into DSP register6.6Address ModesThe CY7C637xx microcontrollers support three addressing modes for instructions that require data operands: data, direct, and indexed.6.6.1DataThe “Data” address mode refers to a data operand that is actually a constant encoded in the instruction. As an example, consider the instruction that loads A with the constant 0x30:•MOV A, 30hThis instruction will require two bytes of code where the first byte identifies the “MOV A” instruction with a data operand as the second byte. The second byte of the instruction will be the constant “0xE8h”. A constant may be referred to by name if a prior “EQU” statement assigns the constant value to the name. For example, the following code is equivalent to the example shown above:•DSPINIT: EQU 30h•MOV A,DSPINIT6.6.2Direct“Direct” address mode is used when the data operand is a variable stored in SRAM. In that case, the one byte address of the variable is encoded in the instruction. As an example, consider an instruction that loads A with the contents of memory address location 0x10h:•MOV A, [10h]In normal usage, variable names are assigned to variable addresses using “EQU” statements to improve the readability of the assembler source code. As an example, the following code is equivalent to the example shown above:•buttons: EQU 10h•MOV A,[buttons]6.6.3Indexed“Indexed” address mode allows the firmware to manipulate arrays of data stored in SRAM. The address of the data operand is the sum of a constant encoded in the instruction and the contents of the “X” register. In normal usage, the constant will be the “base” address of an array of data and the X register will contain an index that indicates which element of the array is actually addressed:•array: EQU 10h•MOV X,3•MOV A,[x+array]This would have the effect of loading A with the fourth element of the SRAM “array” that begins at address 0x10h. The fourth element would be at address 0x13h.7.0 Instruction Set SummaryRefer to the CYASM Assembler User’s Guide for detailed information on these instructions. Note that conditional jump instructions (i.e., JC, JNC, JZ, JNZ) take 5 cycles if jump is taken, 4 cycles if no jump.MNEMONIC Operand Opcode Cycles MNEMONIC Operand Opcode Cycles HALT 007NOP 204ADD A,expr data014INC A acc214ADD A,[expr] direct026INC X x224ADD A,[X+expr] index037INC [expr] direct237ADC A,expr data044INC [X+expr] index248ADC A,[expr] direct056DEC A acc254ADC A,[X+expr] index067DEC X x264SUB A,expr data074DEC [expr] direct277SUB A,[expr] direct086DEC [X+expr] index288SUB A,[X+expr] index097IORD expr address295SBB A,expr data0A4IOWR expr address2A5SBB A,[expr] direct0B6POP A2B4SBB A,[X+expr] index0C7POP X2C4OR A,expr data0D4PUSH A2D5OR A,[expr] direct0E6PUSH X2E5OR A,[X+expr] index0F7SWAP A,X2F5AND A,expr data104SWAP A,DSP305AND A,[expr] direct116MOV [expr],A direct315AND A,[X+expr] index127MOV [X+expr],A index326XOR A,expr data134OR [expr],A direct337XOR A,[expr] direct146OR [X+expr],A index348XOR A,[X+expr] index157AND [expr],A direct357CMP A,expr data165AND [X+expr],A index368CMP A,[expr] direct177XOR [expr],A direct377CMP A,[X+expr] index188XOR [X+expr],A index388MOV A,expr data194IOWX [X+expr] index396MOV A,[expr] direct1A5CPL 3A4MOV A,[X+expr] index1B6ASL 3B4MOV X,expr data1C4ASR 3C4MOV X,[expr] direct1D5RLC 3D4reserved 1E RRC 3E4XPAGE 1F4RET 3F8MOV A,X404DI 704MOV X,A414EI 724MOV PSP,A604RETI 738CALL addr50 - 5F10JMP addr80-8F5JC addr C0-CF 5 (or 4) CALL addr90-9F10JNC addr D0-DF 5 (or 4)JZ addr A0-AF 5 (or 4)JACC addr E0-EF7JNZ addr B0-BF 5 (or 4)INDEX addr F0-FF148.0 Memory Organization8.1Program Memory Organization[1]After reset Address14 -bit PC0x0000Program execution begins here after a reset.0x0002USB Bus Reset interrupt vector0x0004128-µs timer interrupt vector0x0006 1.024-ms timer interrupt vector0x0008USB endpoint 0 interrupt vector0x000A USB endpoint 1 interrupt vector0x000C USB endpoint 2 interrupt vector0x000E SPI interrupt vector0x0010Capture timer A interrupt Vector0x0012Capture timer B interrupt vector0x0014GPIO interrupt vector0x0016Wake-up interrupt vector0x0018Program Memory begins here0x1FDF8 KB PROM ends here (8K - 32 bytes). See Note below Figure 8-1. Program Memory Space with Interrupt Vector TableNote:1.The upper 32 bytes of the 8K PROM are reserved. Therefore, the user’s program must not overwrite this space.8.2Data Memory OrganizationThe CY7C637xx microcontrollers provide 256 bytes of data RAM. In normal usage, the SRAM is partitioned into four areas: program stack, data stack, user variables and USB endpoint FIFOs as shown below:After reset Address8-bit DSP8-bit PSP0x00Program Stack Growth(User’s firmware movesDSP)8-bit DSP User Selected Data Stack GrowthUser Variables0xE8USB FIFO for Address A endpoint 20xF0USB FIFO for Address A endpoint 10xF8USB FIFO for Address A endpoint 0Top of RAM Memory0xFFFigure 8-2. Data Memory Organization8.3I/O Register SummaryI/O registers are accessed via the I/O Read (IORD) and I/O Write (IOWR, IOWX) instructions. IORD reads the selected port into the accumulator. IOWR writes data from the accumulator to the selected port. Indexed I/O Write (IOWX) adds the contents of X to the address in the instruction to form the port address and writes data from the accumulator to the specified port. Note that specifying address 0 with IOWX (e.g., IOWX 0h) means the I/O port is selected solely by the contents of X.Note:All bits of all registers are cleared to all zeros on reset, except the Processor Status and Control Register (Figure20-1). All registers not listed are reserved, and should never be written by firmware. All bits marked as reserved should always be written as 0 and be treated as undefined by reads.Table 8-1. I/O Register SummaryRegister Name I/O Address Read/Write Function Fig. Port 0 Data0x00R/W GPIO Port 012-2 Port 1 Data0x01R/W GPIO Port 112-3 Port 2 Data0x02R Auxiliary input register for D+, D–, VREG, XTALIN 12-8 Port 0 Interrupt Enable0x04W Interrupt enable for pins in Port 021-4 Port 1 Interrupt Enable0x05W Interrupt enable for pins in Port 121-5 Port 0 Interrupt Polarity 0x06W Interrupt polarity for pins in Port 021-6 Port 1 Interrupt Polarity 0x07W Interrupt polarity for pins in Port 121-7 Port 0 Mode0 0x0A W Controls output configuration for Port 012-4 Port 0 Mode10x0B W12-5 Port 1 Mode00x0C W Controls output configuration for Port 112-6 Port 1 Mode10x0D W12-7 USB Device Address0x10R/W USB Device Address register14-1 EP0 Counter Register0x11R/W USB Endpoint 0 counter register14-4 EP0 Mode Register0x12R/W USB Endpoint 0 configuration register14-2 EP1 Counter Register0x13R/W USB Endpoint 1 counter register14-4 EP1 Mode Register0x14R/W USB Endpoint 1 configuration register14-3 EP2 Counter Register0x15R/W USB Endpoint 2 counter register14-4 EP2 Mode Register0x16R/W USB Endpoint 2 configuration register14-3 USB Status & Control0x1F R/W USB status and control register13-1 Global Interrupt Enable0x20R/W Global interrupt enable register21-1 Endpoint Interrupt Enable0x21R/W USB endpoint interrupt enables21-2 Timer (LSB)0x24R Lower 8 bits of free-running timer (1 MHz)18-1 Timer (MSB)0x25R Upper 4 bits of free-running timer18-2 WDR Clear0x26W Watchdog Reset clear-Capture Timer A Rising0x40R Rising edge Capture Timer A data register19-2 Capture Timer A Falling0x41R Falling edge Capture Timer A data register19-3 Capture Timer B Rising0x42R Rising edge Capture Timer B data register19-4 Capture Timer B Falling0x43R Falling edge Capture Timer B data register19-5 Capture TImer Configuration0x44R/W Capture Timer configuration register19-7 Capture Timer Status0x45R Capture Timer status register19-6 SPI Data0x60R/W SPI read and write data register17-2 SPI Control0x61R/W SPI status and control register17-3 Clock Configuration0xF8R/W Internal / External Clock configuration register9-2 Processor Status & Control0xFF R/W Processor status and control20-1。
凯马牌汽车主要技术参数表讲解
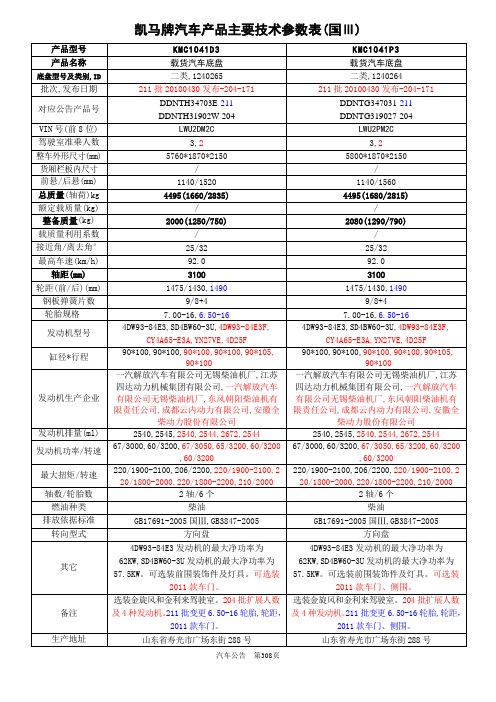
90*100,90*100,90*100,90*100,90*105,90*100
90*100,90*100,90*100,90*100,90*105,90*100
发动机生产企业
一汽解放汽车有限公司无锡柴油机厂,江苏四达动力机械集团有限公司,一汽解放汽车有限公司无锡柴油机厂,东风朝阳柴油机有限责任公司,成都云内动力有限公司,安徽全柴动力股份有限公司
选装金旋风和金利来驾驶室,瓦椤厢和平板厢两种货厢。204批扩展人数及4种发动机。211批随底盘变更6.50-16轮胎,轮距。
生产地址
山东省寿光市广场东街288号
山东省寿光市广场东街288号
凯马牌汽车产品主要技术参数表(国Ⅲ)
产品型号
KMC5041CSD3
KMC5041CSP3
产品名称
仓栅式运输车
仓栅式运输车
385958595859585889010085959010085958595发动机生产企业江苏四达动力机械集团有限公司扬动股份有限公司江苏四达动力机械集团有限公司一汽解放汽车有限公司无锡柴油机厂一汽解放汽车有限公司无锡柴油机厂东风朝阳柴油机有限责任公司安徽全柴动力股份有限公司江苏四达动力机械集团有限公司扬动股份有限公司江苏四达动力机械集团有限公司一汽解放汽车有限公司无锡柴油机厂一汽解放汽车有限公司无锡柴油机厂东风朝阳柴油机有限责任公司安徽全柴动力股份有限公司发动机排量m
220/1900-2100,206/2200,220/1900-2100,220/1800-2000,220/1800-2200,210/2000
轴数/轮胎数
2轴/6个
2轴/6个
燃油种类
柴油
柴油
排放依据标准
GB17691-2005国Ⅲ,GB3847-2005
CY7C131中文资料

1K x 8 Dual-Port Static RAMCY7C130/CY7C131CY7C140/CY7C141Features•True Dual-Ported memory cells which allow simulta-neous reads of the same memory location •1K x 8 organization•0.65-micron CMOS for optimum speed/power •High-speed access: 15 ns•Low operating power: I CC = 110 mA (max.)•Fully asynchronous operation •Automatic power-down•Master CY7C130/CY7C131 easily expands data bus width to 16 or more bits using slave CY7C140/CY7C141•BUSY output flag on CY7C130/CY7C131; BUSY input on CY7C140/CY7C141•INT flag for port-to-port communication•Available in 48-pin DIP (CY7C130/140), 52-pin PLCC, 52-Pin TQFP .•Pb-Free packages availableFunctional DescriptionThe CY7C130/CY7C131/CY7C140 and CY7C141 are high-speed CMOS 1K by 8 dual-port static RAMs. Two ports are provided permitting independent access to any location in memory. The CY7C130/ CY7C131 can be utilized as either a standalone 8-bit dual-port static RAM or as a master dual-port RAM in conjunction with the CY7C140/CY7C141 slave dual-port device in systems requiring 16-bit or greater word widths. It is the solution to applications requiring shared or buffered data, such as cache memory for DSP , bit-slice, or multiprocessor designs.Each port has independent control pins; chip enable (CE), write enable (R/W), and output enable (OE). Two flags are provided on each port, BUSY and INT. BUSY signals that the port is trying to access the same location currently being accessed by the other port. INT is an interrupt flag indicating that data has been placed in a unique location (3FF for the left port and 3FE for the right port). An automatic power-down feature is controlled independently on each port by the chip enable (CE) pins.The CY7C130 and CY7C140 are available in 48-pin DIP . The CY7C131 and CY7C141 are available in 52-pin PLCC, 52-pin Pb-free PLCC, 52-pin PQFP and 52-pin Pb-free PQFP .Note:1.CY7C130/CY7C131 (Master): BUSY is open drain output and requires pull-up resistor2.Open drain outputs: pull-up resistor required.Logic Block DiagramPin Configurations131415161718192021222326272832313029333635342425GND123456789101138394044434241454847461237R/W L CE L BUSY L INT L OE L A 0L A 1L A 2L A 3L A 4L A 5L A 6L A 7L A 8L A 9L I/O 0L I/O 1L I/O 2L I/O 3L I/O 4L I/O 5L I/O 6L I/O 7L CE R R/W R BUSY R INT R OE R A 0R A 1R A 2R A 3R A 4R A 5R A 6R A 7R A 8R A 9R I/O 7R I/O 6R I/O 5R I/O 4R I/O 3R I/O 2R I/O 1R I/O 0RV CCDIP Top View7C1307C140R/W L BUSY LCE L OE LA 9L A 0LA 0RA 9R R/W R CE R OE RCE R OE R CE L OE L R/W LR/W RI/O 7L I/O 0L I/O 7R I/O 0R BUSY RINT LINT RARBITRATIONLOGIC(7C130/7C131ONLY)ANDINTERRUPT LOGICCONTROL I/O CONTROLI/O MEMORY ARRAYADDRESS DECODERADDRESS DECODER[1][2][2]Pin Configuration (continued )1V C CTop ViewPLCC OE R A 0R 8910111213141516171819204645444342414039383736353421222324252627282930313233765432525150494847A 1R A 2R A 3R A 4R A 5R A 6R A 7R A 8R A 9R NC I/O 7RA 1LA 2L A 3L A 4L A 5L A 6L A 7L A 8L A 9L I/O 0L I/O 1L I/O 2L I/O 3LI /O I /O I /O I /O I /O I /O I /O I /O I /O I /O I /O 4L 5L6L 7L0R 1R2R 3R 4R5R 6RN C G N DO E B U S Y I N T A N C R /W C E R /W B U S Y I N T N C0LL L LL L C E R R R R7C1317C14146123456789101112133938373635343332313029282714151617181920212223242526525150494847454443424140Top ViewPQFPV C CO E B U S Y I N T A N C R /W C E R /W B U S Y I N T N C0LL L LL L C E R R R ROE R A 0R A 1R A 2R A 3R A 4R A 5R A 6R A 7R A 8R A 9R NC I/O 7RA 1L A 2L A 3L A 4L A 5L A 6L A 7L A 8L A 9L I/O 0L I/O 1L I/O 2L I/O 3LI /O I /O I /O I /O I /O I /O I /O I /O I /O I /O I /O 4L 5L6L 7L0R 1R2R 3R 4R5R 6RN C G N D 7C1317C141Pin DefinitionsLeft PortRight PortDescriptionCE L CE R Chip Enable R/W L R/W R Read/Write Enable OE LOE ROutput Enable A 0L –A 11/12L A 0R –A 11/12R AddressI/O 0L –I/O 15/17L I/O 0R –I/O 15/17R Data Bus Input/Output INT L INT R Interrupt Flag BUSY L BUSY RBusy Flag V CC Power GNDGroundSelection Guide7C131-15[3]7C141-157C131-25[3]7C141-257C130-307C131-307C140-307C141-307C130-357C131-357C140-357C141-357C130-457C131-457C140-457C141-457C130-557C131-557C140-557C141-55Unit Maximum Access Time 152530354555ns Maximum Operating CurrentCom’l/Ind 190170170120120110mAMilitary 170170120Maximum Standby CurrentCom’l/Ind 756565454535mAMilitary656545Shaded areas contain preliminary information.Note:3.15 and 25-ns version available only in PLCC/PQFP packages.Maximum Ratings[4](Above which the useful life may be impaired. For user guide-lines, not tested.)Storage Temperature .................................–65°C to +150°C Ambient Temperature withPower Applied.............................................–55°C to +125°C Supply Voltage to Ground Potential(Pin 48 to Pin 24)...........................................–0.5V to +7.0V DC Voltage Applied to Outputsin High Z State...............................................–0.5V to +7.0V DC Input Voltage............................................–3.5V to +7.0V Output Current into Outputs (LOW).............................20 mA Static Discharge Voltage........................................... >2001V (per MIL-STD-883, Method 3015)Latch-Up Current.................................................... >200 mA Operating RangeRangeAmbientTemperature V CC Commercial0°C to +70°C 5V ± 10% Industrial–40°C to +85°C 5V ± 10% Military[5]–55°C to +125°C 5V ± 10%Electrical Characteristics Over the Operating Range[6]Parameter Description Test Conditions 7C131-15[3]7C141-157C130-30[3]7C131-25,307C140-307C141-25,307C130-35,457C131-35,457C140-35,457C141-35,457C130-557C131-557C140-557C141-55Unit Min.Max.Min.Max.Min.Max.Min.Max.V OH Output HIGHVoltageV CC = Min., I OH = –4.0 mA 2.4 2.4 2.4 2.4VV OL Output LOWVoltage I OL = 4.0 mA0.40.40.40.4V I OL = 16.0 mA[7]0.50.50.50.5V IH Input HIGH Voltage 2.2 2.2 2.2 2.2V V IL Input LOW Voltage0.80.80.80.8V I IX Input LeakageCurrentGND < V I < V CC–5+5–5+5–5+5–5+5µAI OZ Output LeakageCurrent GND < V O < V CC,Output Disabled–5+5–5+5–5+5–5+5µAI OS Output ShortCircuit Current[8, 9]V CC = Max.,V OUT = GND–350–350–350–350mAI CC V CC OperatingSupply Current CE = V IL,Outputs Open,f = f MAX[10]Com’l190170120110mAMil170120I SB1Standby CurrentBoth Ports,TTL Inputs CE L and CE R >V IH, f = f MAX[10]Com’l75654535mAMil6545I SB2Standby CurrentOne Port,TTL Inputs CE L or CE R > V IH,Active Port OutputsOpen,f = f MAX[10]Com’l1351159075mAMil11590I SB3Standby CurrentBoth Ports,CMOS Inputs Both Ports CE L andCE R >V CC – 0.2V,V IN > V CC – 0.2Vor V IN < 0.2V, f = 0Com’l15151515mAMil1515Shaded areas contain preliminary information.Note:4.The Voltage on any input or I/O pin cannot exceed the power pin during power-up.5.T A is the “instant on” case temperature6.See the last page of this specification for Group A subgroup testing information.7.BUSY and INT pins only.8.Duration of the short circuit should not exceed 30 seconds.9.This parameter is guaranteed but not tested.10.At f = f MAX, address and data inputs are cycling at the maximum frequency of read cycle of 1/t RC and using AC Test Waveforms input levels of GND to 3V.I SB4Standby Current One Port, CMOS InputsOne Port CE L or CE R > V CC – 0.2V,V IN > V CC – 0.2V or V IN < 0.2V, Active Port Outputs Open, f = f MAX [10]Com’l 1251058570mAMil10585Capacitance [9]Parameter DescriptionTest ConditionsMax.Unit C IN Input Capacitance T A = 25°C, f = 1 MHz, V CC = 5.0V15pF C OUTOutput Capacitance10pFElectrical Characteristics Over the Operating Range [6] (continued)Parameter Description Test Conditions 7C131-15[3]7C141-157C130-30[3]7C131-25,307C140-307C141-25,307C130-35,457C131-35,457C140-35,457C141-35,457C130-557C131-557C140-557C141-55Unit Min.Max.Min.Max.Min.Max.Min.Max.AC Test Loads and Waveforms3.0V 5V OUTPUTR1 893ΩR2347Ω30pF INCLUDING JIGAND SCOPEGND90%90%10%≤ 5ns≤5ns5V OUTPUTR1 893ΩR2347Ω5pFINCLUDING JIGAND SCOPE(a)(b)OUTPUT1.40VEquivalent to:THÉVENIN EQUIVALENT5V 281Ω30pFBUSY OR INT(CY7C130/CY7C131ONLY)10%ALL INPUT PULSES 250ΩSwitching Characteristics Over the Operating Range[6, 11]Parameter Description7C131-15[3]7C141-157C130-25[3]7C131-257C140-257C141-257C130-307C131-307C140-307C141-30Unit Min.Max.Min.Max.Min.Max.READ CYCLEt RC Read Cycle Time152530ns t AA Address to Data Valid[12]152530ns t OHA Data Hold from Address Change000ns t ACE CE LOW to Data Valid[12]152530ns t DOE OE LOW to Data Valid[12]101520ns t LZOE OE LOW to Low Z[9, 13, 14]333ns t HZOE OE HIGH to High Z[9, 13, 14]101515ns t LZCE CE LOW to Low Z[9, 13, 14]355ns t HZCE CE HIGH to High Z[9, 13, 14]101515ns t PU CE LOW to Power-Up[9]000ns t PD CE HIGH to Power-Down[9]152525ns WRITE CYCLE[15]t WC Write Cycle Time152530ns t SCE CE LOW to Write End122025ns t AW Address Set-Up to Write End122025ns t HA Address Hold from Write End222ns t SA Address Set-Up to Write Start000ns t PWE R/W Pulse Width121525ns t SD Data Set-Up to Write End101515ns t HD Data Hold from Write End000ns t HZWE R/W LOW to High Z[14]101515ns t LZWE R/W HIGH to Low Z[14]000ns Shaded areas contain preliminary information.Note:11.Test conditions assume signal transition times of 5 ns or less, timing reference levels of 1.5V, input pulse levels of 0 to 3.0V and output loading of the specifiedI OL/I OH, and 30-pF load capacitance.12.AC Test Conditions use V OH = 1.6V and V OL = 1.4V.13.At any given temperature and voltage condition for any given device, t HZCE is less than t LZCE and t HZOE is less than t LZOE.14.t LZCE, t LZWE, t HZOE, t LZOE, t HZCE and t HZWE are tested with C L = 5pF as in part (b) of AC Test Loads. Transition is measured ±500 mV from steady state voltage.15.The internal write time of the memory is defined by the overlap of CS LOW and R/W LOW. Both signals must be low to initiate a write and either signal canterminate a write by going high. The data input set-up and hold timing should be referenced to the rising edge of the signal that terminates the write.BUSY/INTERRUPT TIMING t BLA BUSY LOW from Address Match 152020ns t BHA BUSY HIGH from Address Mismatch [16]152020ns t BLC BUSY LOW from CE LOW 152020ns t BHC BUSY HIGH from CE HIGH [16]152020ns t PS Port Set Up for Priority 555ns t WB [17]R/W LOW after BUSY LOW 000ns t WH R/W HIGH after BUSY HIGH 132030ns t BDD BUSY HIGH to Valid Data152530ns t DDD Write Data Valid to Read Data Valid Note 18Note 18Note 18ns t WDD Write Pulse to Data Delay Note 18Note 18Note 18ns INTERRUPT TIMINGt WINS R/W to INTERRUPT Set Time 152525ns t EINS CE to INTERRUPT Set Time 152525ns t INS Address to INTERRUPT Set Time 152525ns t OINR OE to INTERRUPT Reset Time [16]152525ns t EINR CE to INTERRUPT Reset Time [16]152525ns t INRAddress to INTERRUPT Reset Time [16]152525nsShaded areas contain preliminary information.Note:16.These parameters are measured from the input signal changing, until the output pin goes to a high-impedance state.17.CY7C140/CY7C141 only.18.A write operation on Port A, where Port A has priority, leaves the data on Port B’s outputs undisturbed until one access time after one of the following:BUSY on Port B goes HIGH. Port B’s address is toggled. CE for Port B is toggled.R/W for Port B is toggled during valid read.Switching Characteristics Over the Operating Range [6, 11] (continued)ParameterDescription7C131-15[3]7C141-157C130-25[3]7C131-257C140-257C141-257C130-307C131-307C140-307C141-30UnitMin.Max.Min.Max.Min.Max.Switching Characteristics Over the Operating Range [6,11]Parameter Description7C130-357C131-357C140-357C141-357C130-457C131-457C140-457C141-457C130-557C131-557C140-557C141-55UnitMin.Max.Min.Max.Min.Max.READ CYCLE t RC Read Cycle Time 354555ns t AA Address to Data Valid [12]354555ns t OHA Data Hold from Address Change 0ns t ACE CE LOW to Data Valid [12]354555ns t DOE OE LOW to Data Valid [12]202525ns t LZOE OE LOW to Low Z [9, 13, 14]333ns t HZOE OE HIGH to High Z [9, 13, 14]202025ns t LZCECE LOW to Low Z [9, 13, 14]555nst HZCE CE HIGH to High Z [9, 13, 14]202025ns t PU CE LOW to Power-Up [9]0ns t PD CE HIGH to Power-Down [9]353535ns WRITE CYCLE [15]t WC Write Cycle Time 354555ns t SCE CE LOW to Write End 303540ns t AW Address Set-Up to Write End 303540ns t HA Address Hold from Write End 222ns t SA Address Set-Up to Write Start 000ns t PWE R/W Pulse Width253030ns t SD Data Set-Up to Write End 152020ns t HD Data Hold from Write End 0ns t HZWE R/W LOW to High Z [14]202025ns t LZWE R/W HIGH to Low Z [14]ns BUSY/INTERRUPT TIMINGt BLA BUSY LOW from Address Match 202530ns t BHA BUSY HIGH from Address Mismatch [16]202530ns t BLC BUSY LOW from CE LOW 202530ns t BHC BUSY HIGH from CE HIGH [16]202530ns t PS Port Set Up for Priority 555ns t WB [17]R/W LOW after BUSY LOW 000ns t WH R/W HIGH after BUSY HIGH 303535ns t BDD BUSY HIGH to Valid Data354545ns t DDD Write Data Valid to Read Data Valid Note 18Note 18Note 18ns t WDDWrite Pulse to Data DelayNote 18Note 18Note 18nsINTERRUPT TIMING t WINS R/W to INTERRUPT Set Time 253545ns t EINS CE to INTERRUPT Set Time 253545ns t INS Address to INTERRUPT Set Time 253545ns t OINR OE to INTERRUPT Reset Time [16]253545ns t EINR CE to INTERRUPT Reset Time [16]253545ns t INRAddress to INTERRUPT Reset Time [16]253545nsSwitching Characteristics Over the Operating Range [6,11] (continued)Parameter Description7C130-357C131-357C140-357C141-357C130-457C131-457C140-457C141-457C130-557C131-557C140-557C141-55Unit Min.Max.Min.Max.Min.Max.Switching WaveformsRead Cycle No. 1[19, 20]Read Cycle No. 2[19, 21]Read Cycle No. 3[20]Notes:19.R/W is HIGH for read cycle.20.Device is continuously selected, CE = V IL and OE = V IL .21.Address valid prior to or coincident with CE transition LOW.t RCt AAt OHADATA VALIDPREVIOUS DATA VALIDDATA OUTADDRESSEither Port Address Accesst ACEt LZOEt DOEt HZOEt HZCEDATA VALIDDATA OUTCE OEt LZCEt PUI CC I SBt PDEither Port CE/OE Accesst BHAt BDDVALIDt DDDt WDDADDRESS MATCHADDRESS MATCHR/W R ADDRESS RD INRADDRESS LBUSY LDOUT Lt PSt BLARead with BUSY , Master: CY7C130 and CY7C131t RCt PWEVALIDt HDWrite Cycle No. 1 (OE Three-States Data I/Os—Either Port [15, 22]Write Cycle No. 2 (R/W Three-States Data I/Os—Either Port)[16, 23]Notes:22.PWE or t HZWE + t SD to allow the data I/O pins to enter high impedanceand for data to be placed on the bus for the required t SD .23.If the CE LOW transition occurs simultaneously with or after the R/W LOW transition, the outputs remain in the high-impedance state.Switching Waveforms (continued)t AWt WCDATA VALIDHIGH IMPEDANCEt SCEt SAt PWEt HDt SDt HACER/WADDRESSt HZOEOED OUTDATA INEither Portt AWt WCt SCEt SAt PWEt HDt SDt HZWEt HAHIGH IMPEDANCEDATA VALIDt LZWEADDRESSCER/WDATA OUTDATA INBusy Timing Diagram No. 1 (CE Arbitration)Busy Timing Diagram No. 2 (Address Arbitration)Switching Waveforms (continued)ADDRESS MATCHt PSCE L Valid First:t BLCt BHCADDRESS MATCHt PSt BLCt BHCADDRESS L,RBUSY RCE LCE RBUSY LCE RCE LADDRESS L,RCE R Valid First:Left Address Valid First:ADDRESS MATCHt PSADDRESS LBUSY RADDRESS MISMATCHt RC or t WC t BLA t BHAADDRESS RADDRESS MATCHADDRESS MISMATCHt PSADDRESS LBUSY Lt RC or t WC t BLA t BHAADDRESS RRight Address Valid First:Switching Waveforms (continued)Busy Timing Diagram No. 3Write with BUSY (Slave:CY7C140/CY7C141)CEt PWER/Wt WB t WH BUSYInterrupt Timing Diagrams Switching Waveforms (continued)WRITE 3FFt INSt WCt EINSRight Side Clears INT Rt HAt SAt WINSREAD 3FF t RCt EINRt HAt INTt OINRWRITE 3FEt INSt WCt EINSt HAt SAt WINSRight Side Sets INT LLeft Side Sets INT RLeft Side Clears INT LREAD 3FE t EINRt HAt INRt OINRt RC ADDR RCE LR/W L INT LOE LADDR RR/W R CE RINT LADDR RCE RR/W R INT ROE RADDR LR/W LCE LINT RTypical DC and AC Characteristics1.41.00.44.04.55.05.56.0–55251251.21.01201008060402001.02.03.04.0O U T P U T S O U R C E C U R R E N T (m A )SUPPLY VOLTAGE (V)NORMALIZED SUPPLY CURRENTvs. SUPPLY VOLTAGENORMALIZED SUPPLY CURRENT vs. AMBIENT TEMPERATURE AMBIENT TEMPERATURE (°C)OUTPUT VOLTAGE (V)OUTPUT SOURCE CURRENT vs. OUTPUT VOLTAGE 0.00.80.80.60.6N O R M A L I Z E D I C C , I S BV CC = 5.0V V IN = 5.0V V CC = 5.0V T A = 25°C0I CC1.61.41.21.00.8–55125N O R M A L I Z E D t A ANORMALIZED ACCESS TIME vs. AMBIENT TEMPERATURE AMBIENT TEMPERATURE (°C)1.41.31.21.00.94.04.55.05.56.0N O R M A L I Z E D t A ASUPPLY VOLTAGE (V)NORMALIZED ACCESS TIME vs. SUPPLY VOLTAGE 120140*********0.01.02.03.04.0O U T P U T S I N K C U R R E N T (m A )080OUTPUT VOLTAGE (V)OUTPUT SINK CURRENT vs. OUTPUT VOLTAGE0.60.8 1.251.00.751040N O R M A L I Z E D I C C0.50NORMALIZED I CC vs. CYCLE TIME CYCLE FREQUENCY (MHz)3.02.52.01.50.501.02.03.05.0N O R M A L I Z E D t P C25.030.020.010.05.00200400600800D E L T A t A A (n s )015.00.0SUPPLY VOLTAGE (V)TYPICAL POWER-ON CURRENT vs. SUPPLY VOLTAGE CAPACITANCE (pF)TYPICAL ACCESS TIME CHANGE vs. OUTPUT LOADING4.010001.020300.20.61.2I SB30.20.4251.1V V IN = 0.5VN O R M A L I Z E D I C C , I S BI CCI SB3T A = 25°CV CC = 5.0VV CC = 5.0V T A = 25°CT A = 25°CCC = 4.5V V CC = 4.5V T A = 25°COrdering InformationSpeed(ns)Ordering Code PackageName Package TypeOperatingRange30CY7C130-30PC P2548-Lead (600-Mil) Molded DIP Commercial CY7C130-30PI P2548-Lead (600-Mil) Molded DIP Industrial 35CY7C130-35PC P2548-Lead (600-Mil) Molded DIP Commercial CY7C130-35PI P2548-Lead (600-Mil) Molded DIP Industrial CY7C130-35DMB D2648-Lead (600-Mil) Sidebraze DIP Military45CY7C130-45PC P2548-Lead (600-Mil) Molded DIP Commercial CY7C130-45PI P2548-Lead (600-Mil) Molded DIP Industrial CY7C130-45DMB D2648-Lead (600-Mil) Sidebraze DIP Military55CY7C130-55PC P2548-Lead (600-Mil) Molded DIP Commercial CY7C130-55PI P2548-Lead (600-Mil) Molded DIP Industrial CY7C130-55DMB D2648-Lead (600-Mil) Sidebraze DIP Military15CY7C131-15JC J6952-Lead Plastic Leaded Chip Carrier Commercial CY7C131-15JXC J6952-Lead Pb-Free Plastic Leaded Chip CarrierCY7C131-15NC N5252-Pin Plastic Quad FlatpackCY7C131-15JI J6952-Lead Plastic Leaded Chip Carrier Industrial CY7C131-15JXI J6952-Lead Pb-Free Plastic Leaded Chip Carrier25CY7C131-25JC J6952-Lead Plastic Leaded Chip Carrier Commercial CY7C131-25JXC J6952-Lead Pb-Free Plastic Leaded Chip CarrierCY7C131-25NC N5252-Pin Plastic Quad FlatpackCY7C131-25NXC N5252-Pin Pb-Free Plastic Quad FlatpackCY7C131-25JI J6952-Lead Plastic Leaded Chip Carrier Industrial CY7C131-25NI N5252-Pin Plastic Quad Flatpack30CY7C131-30JC J6952-Lead Plastic Leaded Chip Carrier Commercial CY7C131-30NC N5252-Pin Plastic Quad FlatpackCY7C131-30JI J6952-Lead Plastic Leaded Chip Carrier Industrial 35CY7C131-35JC J6952-Lead Plastic Leaded Chip Carrier Commercial CY7C131-35NC N5252-Pin Plastic Quad FlatpackCY7C131-35JI J6952-Lead Plastic Leaded Chip Carrier Industrial CY7C131-35NI N5252-Pin Plastic Quad Flatpack45CY7C131-45JC J6952-Lead Plastic Leaded Chip Carrier Commercial CY7C131-45NC N5252-Pin Plastic Quad FlatpackCY7C131-45JI J6952-Lead Plastic Leaded Chip Carrier Industrial CY7C131-45NI N5252-Pin Plastic Quad Flatpack55CY7C131-55JC J6952-Lead Plastic Leaded Chip Carrier Commercial CY7C131-55JXC J6952-Lead Pb-Free Plastic Leaded Chip CarrierCY7C131-55NC N5252-Pin Plastic Quad FlatpackCY7C131-55NXC N5252-Pin Pb-Free Plastic Quad FlatpackCY7C131-55JI J6952-Lead Plastic Leaded Chip Carrier Industrial CY7C131-55JXI J6952-Lead Pb-Free Plastic Leaded Chip CarrierCY7C131-55NI N5252-Pin Plastic Quad Flatpack30CY7C140-30PC P2548-Lead (600-Mil) Molded DIP Commercial CY7C140-30PI P2548-Lead (600-Mil) Molded DIP Industrial 35CY7C140-35PC P2548-Lead (600-Mil) Molded DIP Commercial CY7C140-35PI P2548-Lead (600-Mil) Molded DIP Industrial CY7C140-35DMBD2648-Lead (600-Mil) Sidebraze DIP Military 45CY7C140-45PC P2548-Lead (600-Mil) Molded DIP Commercial CY7C140-45PI P2548-Lead (600-Mil) Molded DIP Industrial CY7C140-45DMBD2648-Lead (600-Mil) Sidebraze DIP Military 55CY7C140-55PC P2548-Lead (600-Mil) Molded DIP Commercial CY7C140-55PI P2548-Lead (600-Mil) Molded DIP Industrial CY7C140-55DMBD2648-Lead (600-Mil) Sidebraze DIP Military 15CY7C141-15JC J6952-Lead Plastic Leaded Chip Carrier CommercialCY7C141-15NC N5252-Pin Plastic Quad Flatpack 25CY7C141-25JC J6952-Lead Plastic Leaded Chip Carrier Commercial CY7C141-25JXC J6952-Lead Pb-Free Plastic Leaded Chip Carrier CY7C141-25NC N5252-Pin Plastic Quad Flatpack CY7C141-25JI J6952-Lead Plastic Leaded Chip Carrier Industrial CY7C141-25NIN5252-Pin Plastic Quad Flatpack 30CY7C141-30JC J6952-Lead Plastic Leaded Chip Carrier Commercial CY7C141-30NC N5252-Pin Plastic Quad Flatpack CY7C141-30JIJ6952-Lead Plastic Leaded Chip Carrier Industrial 35CY7C141-35JC J6952-Lead Plastic Leaded Chip Carrier Commercial CY7C141-35NC N5252-Pin Plastic Quad Flatpack CY7C141-35JI J6952-Lead Plastic Leaded Chip Carrier Industrial CY7C141-35NIN5252-Pin Plastic Quad Flatpack 45CY7C141-45JC J6952-Lead Plastic Leaded Chip Carrier Commercial CY7C141-45NC N5252-Pin Plastic Quad Flatpack CY7C141-45JI J6952-Lead Plastic Leaded Chip Carrier Industrial CY7C141-45NIN5252-Pin Plastic Quad Flatpack 55CY7C141-55JC J6952-Lead Plastic Leaded Chip Carrier Commercial CY7C141-55NC N5252-Pin Plastic Quad Flatpack CY7C141-55JI J6952-Lead Plastic Leaded Chip Carrier Industrial CY7C141-55NIN5252-Pin Plastic Quad FlatpackOrdering Information (continued)Speed (ns)Ordering Code Package Name Package TypeOperating RangeMILITARY SPECIFICATIONS Group A Subgroup Testing Note:24.CY7C140/CY7C141 only.DC CharacteristicsParameterSubgroups V OH 1, 2, 3V OL 1, 2, 3V IH 1, 2, 3V IL Max.1, 2, 3I IX 1, 2, 3I OZ 1, 2, 3I CC 1, 2, 3I SB11, 2, 3I SB21, 2, 3I SB31, 2, 3I SB41, 2, 3Switching CharacteristicsParameterSubgroups READ CYCLEt RC 7, 8, 9, 10, 11t AA 7, 8, 9, 10, 11t ACE 7, 8, 9, 10, 11t DOE7, 8, 9, 10, 11WRITE CYCLEt WC 7, 8, 9, 10, 11t SCE 7, 8, 9, 10, 11t AW 7, 8, 9, 10, 11t HA 7, 8, 9, 10, 11t SA 7, 8, 9, 10, 11t PWE 7, 8, 9, 10, 11t SD 7, 8, 9, 10, 11t HD7, 8, 9, 10, 11BUSY/INTERRUPT TIMINGt BLA 7, 8, 9, 10, 11t BHA 7, 8, 9, 10, 11t BLC 7, 8, 9, 10, 11t BHC 7, 8, 9, 10, 11t PS 7, 8, 9, 10, 11t WINS 7, 8, 9, 10, 11t EINS 7, 8, 9, 10, 11t INS 7, 8, 9, 10, 11t OINR 7, 8, 9, 10, 11t EINR 7, 8, 9, 10, 11t INR7, 8, 9, 10, 11BUSY TIMINGt WB [24]7, 8, 9, 10, 11t WH 7, 8, 9, 10, 11t BDD7, 8, 9, 10, 11Package Diagrams48-Lead (600-Mil) Sidebraze DIP D26MIL-STD-1835 D-14 Config. C51-80044 **Document #: 38-06002 Rev. *DPage 18 of 19All products and company names mentioned in this document may be the trademarks of their respective holders.Package Diagrams (continued)51-85020-*A48-Lead (600-Mil) Molded DIP P2551-85042-**52-Lead Pb-Free Plastic Quad Flatpack N5252-Lead Plastic Quad Flatpack N52Document History PageDocument Title: CY7C130/CY7C131/CY7C140/CY7C141 1K x 8 Dual-Port Static RAM Document Number: 38-06002REV.ECN NO.IssueDateOrig. ofChange Description of Change**11016909/29/01SZV Change from Spec number: 38-00027 to 38-06002*A12225512/26/02RBI Power up requirements added to Maximum Ratings Information*B236751See ECN YDT Removed cross information from features section*C325936See ECN RUY Added pin definitions table, 52-pin PQFP package diagram and Pb-freeinformation*D393153See ECN YIM Added CY7C131-15JI to ordering informationAdded Pb-Free parts to ordering information:CY7C131-15JXI。
CY7C1417AV18资料

Errata Revision: *CMay 02, 2007RAM9 QDR-I/DDR-I/QDR-II/DDR- II ErrataCY7C129*DV18/CY7C130*DV25CY7C130*BV18/CY7C130*BV25/CY7C132*BV25CY7C131*BV18 / CY7C132*BV18/CY7C139*BV18CY7C191*BV18/CY7C141*AV18 / CY7C142*AV18/CY7C151*V18 /CY7C152*V18This document describes the DOFF issue for QDRII/DDRII and the Output Buffer and JTAG issues for QDRI/DDRI/QDRII/DDRII. Details include trigger conditions, possible workarounds and silicon revision applicability.This document should be used to compare to the respective datasheet for the devices to fully describe the device functionality.Please contact your local Cypress Sales Representative for availability of the fixed devices and any other questions.Devices AffectedTable 1. List of Affected devicesProduct StatusAll of the above densities and revisions are available in sample as well as production quantities.QDR/DDR DOFF Pin, Output Buffer and JTAG Issues Errata SummaryThe following table defines the issues and the fix status for the different devices which are affected.Density & Revision Part Numbers Architecture 9Mb - Ram9(90 nm)CY7C130*DV25QDRI/DDRI 9Mb - Ram9(90 nm)CY7C129*DV18QDRII 18Mb - Ram9(90nm)CY7C130*BV18CY7C130*BV25CY7C132*BV25QDRI/DDRI18Mb - Ram9(90nm)CY7C131*BV18CY7C132*BV18CY7C139*BV18CY7C191*BV18QDRII/DDRII36Mb - Ram9(90nm)CY7C141*AV18CY7C142*AV18QDRII/DDRII 72Mb -Ram9(90nm)CY7C151*V18CY7C152*V18QDRII/DDRIIItemIssueDeviceFix Status1.DOFF pin is used for enabling/dis-abling the DLL circuitry within the SRAM. To enable the DLL circuitry, DOFF pin must be externally tied HIGH. The QDR-II/DDR-II devices have an internal pull down resistor of ~5K . The value of the external pull-up resistor should be 500 or less in order to ensure DLL is enabled.9Mb - “D” Rev - Ram918Mb - “B” Rev - Ram936Mb - “A” Rev - Ram972Mb - Ram9QDR-II/DDR-II DevicesThe fix involved removing the in-ternal pull-down resistor on the DOFF pin. The fix has been im-plemented on the new revision and is now available.ΩΩTable 2.Issue Definition and fix status for different devices1. DOFF Pin Issue•ISSUE DEFINITIONThis issue involves the DLL not turning ON properly if a large resistor is used (eg:-10K ) as an external pullup resistor to enable the DLL. If a 10K or higher pullup resistor is used externally, the voltage on DOFF is not high enough to enable the DLL.•PARAMETERS AFFECTEDThe functionality of the device will be affected because of the DLL is not turning ON properly. When the DLL is enabled, all AC and DC parameters on the datasheet are met. •TRIGGER CONDITION(S)Having a 10K or higher external pullup resistor for disabling the DOFF pin.•SCOPE OF IMPACTThis issue will alter the normal functionality of the QDRII/DDRII devices when the DLL is disabled.•EXPLANATION OF ISSUEFigure 1 shows the DOFF pin circuit with an internal 5K internal resistor. The fix planned is to disable the internal 5K leaker.•WORKAROUND2.O/P Buffer enters a locked up unde-fined state after controls or clocks are left floating. No proper read/write access can be done on the device until a dummy read is performed.9Mb - “D” Rev - Ram918Mb - “B” Rev - Ram936Mb - “A” Rev - Ram972Mb - Ram9QDR-I/DDR-I/QDR-II/DDR-II Devices The fix has been implemented onthe new revision and is now avail-able.3.The EXTEST function in the JTAG test fails when input K clock is floating in the JTAG mode.9Mb - “D” Rev - Ram918Mb - “B” Rev - Ram936Mb - “A” Rev - Ram972Mb - Ram9QDR-I/DDR-I/QDR-II/DDR-II DevicesThe fix involved bypassing the ZQ circuitry in JTAG mode. This was done by overriding the ZQ circuit-ry by the JTAG signal. The fix has been implemented on the new re-vision and is now available.Figure 1.DOFF pin with the 5K internal resistorItemIssueDeviceFix StatusΩΩΩΩΩΩThe workaround is to have a low value of external pullup resistor for the DOFF pin (recommended value is <500). When DOFF pins from multiple QDR devices are connected through the same pull-up resistors on the board, it is recommended that this DOFF pin be directly connected to Vdd due to the lower effective resistance since the "leakers" are in parallel.Figure 2 shows the proposed workaround and the fix planned.•FIXSTATUSFix involved removing the internal pull-down resistor on the DOFF pin. The fix has been implemented on the new revision and is now available. The new revision is an increment of the existing revision. The following table lists the devices affected, current revision and the new revision after the fix.Table 3.List of Affected Devices and the new revison2.Output Buffer IssueFigure 2.Proposed workaround with the 500 external pullupCurrent Revision New Revision after the FixCY7C129*DV18CY7C129*EV18CY7C131*BV18CY7C131*CV18CY7C132*BV18CY7C132*CV18CY7C139*BV18CY7C139*CV18CY7C191*BV18CY7C191*CV18CY7C141*AV18CY7C141*BV18CY7C142*AV18CY7C142*BV18CY7C151*V18CY7C151*AV18CY7C152*V18CY7C152*AV18ΩΩ•ISSUE DEFINITIONThis issue involves the output buffer entering an unidentified state when the input signals (only Control signals or Clocks) are floating during reset or initialization of the memory controller after power up. •PARAMETERS AFFECTEDNo timing parameters are affected. The device may drive the outputs even though the read operation is not enabled. A dummy read is performed to clear this condition.•TRIGGER CONDITION(S)Input signals(namely RPS# for QDR-I/QDRII , WE# and LD# for DDR-I/DDRII) or Clocks (K/K# and/or C/C#) are floating during reset or initialization of the memory controller after power up.•SCOPE OF IMPACTThis issue will jeopardize any number of writes or reads which take place after the controls or clock are left floating. This can occur anywhere in the SRAM access ( all the way from power up of the memory device to transitions taking place for read/write accesses to the memory device) if the above trigger conditions are met.•EXPLANATION OF ISSUEFigure 3 shows the output register Reset circuit with an SR Latch circled. This latch has two inputs with one of them coming from some logic affected by the clock and RPS#(QDR) or WE# and LD#(DDR).The issue happens when clocks are glitching/toggling with controls floating. This will cause the SR latch to be taken into an unidentified state. The SR Latch will need to be reset by a dummy read operation if this happens. Array•WORKAROUNDThis is viable only if the customer has the trigger conditions met during reset or initialization of the memory controller after power up. In order for the workaround to perform properly, Cypress recommends the insertion of a minimum of 16 “dummy” READ operations to every SRAM device on the board prior to writing any meaningful data into the SRAM. After this one “dummy” READ operation, the device will perform properly.“Dummy” READ is defined as a read operation to the device that is not meant to retrieve required data. The “dummy” READ can be to any address location in the SRAM. Refer to Figure 4 for the dummy read implemen-tation.In systems where multiple SRAMs with multiple RPS# lines are used, a dummy read operation will have to be performed on every SRAM on the board. Below is an example sequence of events that can be performed before valid access can be performed on the SRAM.1) Initialize the Memory Controller2) Assert RPS# Low for each of the memory devicesNote:For all devices with x9 bus configuration, the following sequence needs to be performed:1) For the 72M / 36M / 18M x9 devices drive address pin A2 / A10 / A3 low respectively and perform dummyread.2) For the 72M / 36M / 18M x9 devices drive address pin A2 / A10 / A3 high respectively and perform dummyread.If the customer has the trigger conditions met during normal access to the memory then there is no workaround at this point.•FIX STATUSThe fix has been implemented on the new revision and is now available. The new revision is an increment of the existing revision. Please refer to Table 4 for the list of devices affected, current revision and the new revision after the fix.3. JTAG Mode Issue•ISSUE DEFINITIONIf the input clock (K Clock) is left floating when the device is in JTAG mode, spurious high frequency noise on this input can be interpreted by the device as valid clocks. This could cause the impedance matching circuitry (ZQ) on the QDR/DDR devices to periodically load itself with incorrect values. These incorrect values in the ZQ register could force the outputs into a High-Impedance state. The ZQ circuitry requires at least 1000 valid K clock cycles to drive the outputs from high impedance to low impedance levels.•PARAMETERS AFFECTEDThis issue only affects the EXTEST command when the device is in the JTAG mode. The normal functionality of the device will not be affected.•TRIGGER CONDITION(S)EXTEST command executed immediately after power-up without providing any K clock cycles.•SCOPE OF IMPACTThis issue only impacts the EXTEST command when device is tested in the JTAG mode. Normal functionality of the device is not affected. •EXPLANATION OF ISSUEImpedance matching circuitry (ZQ) is present on the QDR/DDR devices to set the desired impedance on the outputs. This ZQ circuitry is updated every 1000 clock cycles of K clock to ensure that the impedance of the O/P is set to valid state. However, when the device is operated in the JTAG mode immediately after power-up, high frequency noise on the input K clock can be treated by the ZQ circuitry as valid clocks thereby setting the outputs in to a high-impedance mode. If a minimum of 1000 valid K clocks are applied before performing the JTAG test, this should clear the ZQ circuitry and ensure that the outputs are driven to valid impedance levels.•WORKAROUNDElimination of the issue: After power-up, before any valid operations are performed on the device, insert a minimum of 1000 valid clocks on K input.•FIX STATUSThe fix involved bypassing the ZQ circuitry in JTAG mode. This was done by overriding the ZQ circuitry by the JTAG signal. The fix has been implemented on the new revision and is now available. The new revision is an increment of the existing revision. Please refer to Table 4 for the list of devices affected, current revision and the new revision after the fix..Table 4.List of Affected devices and the new revisionCurrent Revision New Revision after the FixCY7C129*DV18CY7C129*EV18CY7C130*DV25CY7C130*EV25CY7C130*BV18CY7C130*CV18CY7C130*BV25CY7C130*CV25CY7C132*BV25CY7C132*CV25CY7C131*BV18CY7C131*CV18CY7C132*BV18CY7C132*CV18CY7C139*BV18CY7C139*CV18CY7C191*BV18CY7C191*CV18CY7C141*AV18CY7C141*BV18CY7C142*AV18CY7C142*BV18CY7C151*V18CY7C151*AV18CY7C152*V18CY7C152*AV18ReferencesAll 90nm QDRI/DDRI/QDRII/DDRII datasheets:-Table 5.List of Datasheet spec# for the Affected devicesSpec#Part#DensityArchitecture38-05628CY7C1304DV259-MBIT QDR(TM) SRAM 4-WORD BURST 38-05632CY7C1308DV259-MBIT DDR-I SRAM 4-WORD BURST 001-00350CY7C1292DV18/1294DV189-MBIT QDR- II(TM) SRAM 2-WORD BURST 38-05621CY7C1316BV18/1916BV18/1318BV18/1320BV1818-MBIT DDR-II SRAM 2-WORD BURST 38-05622CY7C1317BV18/1917BV18/1319BV18/1321BV1818-MBIT DDR-II SRAM 4-WORD BURST 38-05623CY7C1392BV18/1393BV18/1394BV1818-MBIT DDR-II SIO SRAM 2-WORD BURST 38-05631CY7C1323BV2518-MBIT DDR-I SRAM 4-WORD BURST 38-05630CY7C1305BV25/1307BV2518-MBIT QDR(TM) SRAM 4-WORD BURST 38-05627CY7C1303BV25/1306BV2518-MBIT QDR(TM) SRAM 2-WORD BURST 38-05629CY7C1305BV18/1307BV1818-MBIT QDR(TM) SRAM 4-WORD BURST 38-05626CY7C1303BV18/1306BV1818-MBIT QDR(TM) SRAM 2-WORD BURST 38-05619CY7C1310BV18/1910BV18/1312BV18/1314BV1818-MBIT QDR - II (TM) SRAM 2-WORD BURST 38-05620CY7C1311BV18/1911BV18/1313BV18/1315BV1818-MBIT QDR - II SRAM 4-WORD BURST 38-05615CY7C1410AV18/1425AV18/1412AV18/1414AV1836-MBIT QDR-II(TM) SRAM 2-WORD BURST 38-05614CY7C1411AV18/1426AV18/1413AV18/1415AV1836-MBIT QDR(TM)-II SRAM 4-WORD BURST 38-05616CY7C1416AV18/1427AV18/1418AV18/1420AV1836-MBIT DDR-II SRAM 2-WORD BURST 38-05618CY7C1417AV18/1428AV18/1419AV18/1421AV1836-MBIT DDR-II SRAM 4-WORD BURST 38-05617CY7C1422AV18/1429AV18/1423AV18/1424AV1836-MBIT DDR-II SIO SRAM 2-WORD BURST 38-05489CY7C1510V18/1525V18/1512V18/1514V1872-MBIT QDR-II SRAM 2-WORD BURST 38-05363CY7C1511V18/1526V18/1513V18/1515V1872-MBIT QDR(TM)-II SRAM 4-WORD BURST 38-05563CY7C1516V18/1527V18/1518V18/1520V1872-MBIT DDR-II SRAM 2-WORD BURST 38-05565CY7C1517V18/1528V18/1519V18/1521V1872-MBIT DDR-II SRAM 4-WORD BURST 38-05564CY7C1522V18/1529V18/1523V18/1524V1872-MBITDDR-II SIO SRAM 2-WORD BURSTDocument History PageDocument Title: RAM9 QDR-I/DDR-I/QDR-II/DDR- II Errata Document #: 001-06217 Rev. *CREV.ECN NO.IssueDateOrig. ofChange Description of Change**419849See ECN REF New errata for Ram9 QDR2/DDR2 SRAMs.*A493936See ECN QKS Added Output buffer and JTAG mode issues, Item#2 and #3Added 9Mb QDR-II Burst of 2 and QDR-1/DDR-I part numbers.*B733176See ECN NJY Added missing part numbers in the title for Spec#’s 38-05615,38-05614,38-05363,38-05563 on Table 5 on page 7.*C1030020 See ECN TBE Updated the fix status of the three issues, and modified the description forthe Output Buffer workaround for x9 devices on page 5.。
CY7C1314V18-133BZC资料

Errata Revision: [**]CY7C1312V18CY7C1314V18CONFIDENTIAL11/14/03Errata Document for CY7C1312V18 & CY7C1314V18This document describes errata for the CY7C1312V18 and CY7C1314V18. Details include errata trigger conditions,available workarounds, and silicon revision applicability. This document should be used as a suplement to the existing datasheet.Please contact your local Cypress Sales Representative if you have further questions.Part Numbers AffectedCY7C1312V18 & CY7C1314V18 Qualification StatusThese parts are currently available as Engineering Samples.The reliability report is available on our website, , QTP# 032105CY7C1312V18 & CY7C1314V18 Errata SummaryThe following table defines the errata applicability to the CY7C1312V18 and CY7C1314V18. .1. ADDRESS 7C ERRATA•PROBLEM DEFINITION In a given clock cycle:•The read address is provided on the rising edge of K •The write address is provided on the rising edge of K#•If the read and write address are the same, data is forwarded from the input port to the output port and the data from the memory array is ignored. This feature is called the data forwarding feature and it ensures that the most current data is always output from the device.In the event that address 7C is the only address that changes between the read address, and the write address in a given clock cycle, and if address 7C is changing from "1" to "0", then the data forwarding may be errone-ously activated. The data from the memory array may be ignored and the data from the input bus may be improperly forwarded.•PARAMETERS AFFECTEDThis errata impacts the integrity of the data. It does not impact any timing or operating parameters.•TRIGGER CONDITION(S)This errata can occur across all datasheet operating conditions.Part Number Architecture Confguration Clock FrequencyCY7C1312V18-133BZC QDR-II Burst of 2 1 M x 18133 MHz CY7C1312V18-167BZC QDR-II Burst of 2 1 M x 18167 MHz CY7C1314V18-133BZC QDR-II Burst of 2512 K x 36133 MHz CY7C1314V18-167BZCQDR-II Burst of 2512 K x 36167 MHzItemsCY7C1312V18CY7C1314V18Fix Status1. Address 7C Errata X X Cypress plans to fix this errata withchanges to the silicon.2. First Clock Cycle ErrataXXCypress does not plan to fix this errata. Contact your local Cypress sales office for additional information.元器件交易网CY7C1312V18CY7C1314V18CONFIDENTIALErrata Document•SCOPE OF IMPACTThis issue only applies to the burst of 2 arhcitecture only. QDR-II. Burst of 4 devices are NOT affected by this issue. This errata affects the output of the data from the device. It does not affect the data integrity in the memory array.The impact this has in an application has two components. First, it is dependent on how often the failing condition occurs. Second, it is dependent on the system’s ability to recover from the occurance of incorrect data.In applications with truly random access of the memory, it will occur at a rate of 2 PPM for the CY7C1312V18and 4 PPM for the CY7C1314V18. However, it will occur more frequently in applications where the failing conditions occur more frequently.•WORKAROUNDProhibit the failing conditions in the SRAM controller’s software.•FIX STATUSCypress has identified a change to the silicon that will eliminate this errata.2. FIRST CLOCK CYCLE ERRATA•PROBLEM DEFINITIONIn the first clock cylce seen by the device, it is possible for data to be written into the memory array incorrectly. Specificlly, the first word may be written to the second burst address and the second word may be written to the first burst address. This can only occur in the first clock cycle seen by the device and will not occur in subsequent clock cycles.To date, Cypress is unaware of any applications that have experienced this issue.•PARAMETERS AFFECTEDThis errata impacts the integrity of the data. It does not impact any timing or operating parameters.•TRIGGER CONDITION(S)This errata will only occur during the first clock cycle seen by the device. It will not occur after the second rising edges of the K and K# clocks. Therefore, if the device sees any clock cycles during power up, this errata will not occur.This errata occurs under the following conditions:(1) V DD reaches 1.7 V at t 0,(2) K# rises from low to high after t 0 + 25 ns,(3) K# rises from low to high before the first rising edge of K.A timing diagram for these trigger conditions is shown below:Timing Diagram For First Clock Cycle Errata Trigger ConditionsCONFIDENTIALErrata DocumentCY7C1312V18CY7C1314V18•SCOPE OF IMPACTThis errata only impacts the data integrity of data written during the first clock cycle seen by the device. All subsequent writes will be written correctly.To date, none of our customers have reported seeing this failure mechanism in an application.A timing diagram describing device operation after the first clock cycle errata is triggered is shown below.•WORKAROUNDThere are numerous available workarounds to this errata. These include the following:1. Wait until after the first clock cycle to write to the device.2. Ensure that K rises high before K# (Shown Below)Timing Diagram For Ensuring K Rises Before K#CY7C1312V18CY7C1314V18Errata DocumentCONFIDENTIAL© Cypress Semiconductor Corporation, 2003. The information contained herein is subject to change without notice. Cypress Semicon ductor Corporation assumes no responsibility for the use3. Bring K# input high prior to t0 + 25 ns.•FIX STATUSCypress does not have a plan to correct this errata. If your application cannot accommodate the suggestedworkarounds, please contact your Cypress FAE.References[1] Document # 38-05180,CY7C1310V18/CY7C1312V18/CY7C1314V18: 18-Mb QDR(TM)-II SRAM Two-wordBurst Architecture (Preliminary)Timing Diagram For Bringing K# High Prior to t0 + 25 ns元器件交易网CY7C1312V18CY7C1314V18CONFIDENTIALErrata DocumentDocument History PageDocument Title: CY7C1312V18 & CY7C1314V18 Errata Document Number: 38-17005REV.ECN NO.Issue Date Orig. ofChange Description of Change**13128411/14/03RCS1.New Document元器件交易网。
CY7C1515AV18资料

Page 2 of 31 [+] Feedback
元器件交易网
Logic Block Diagram (CY7C1513AV18)
CY7C1511AV18, CY7C1526AV18 CY7C1513AV18, CY7C1515AV18
18 D[17:0]
A(19:0) 20
■ Variable drive HSTL output buffers
■ JTAG 1149.1 compatible test access port
■ Delay Lock Loop (DLL) for accurate data placement
Configurations
CY7C1511AV18 – 8M x 8 CY7C1526AV18 – 8M x 9 CY7C1513AV18 – 4M x 18 CY7C1515AV18 – 2M x 36
Address Register
21
A(20:0)
2M x 8 Array 2M x 8 Array 2M x 8 Array 2M x 8 Array
Read Data Reg. 32 16
16
Control Logic
RPS
C C
Reg.
Reg. 8 8
Reg.
8
8
8
CQ CQ Q[7:0]
Logic Block Diagram (CY7C1526AV18)
Address Register
21
A(20:0)
2M x 9 Array 2M x 9 Array 2M x 9 Array 2M x 9 Array
Read Data Reg. 36 18
CY7C344资料

Multiple Array Matrix High-Density EPLDSfax id: 6100CY7C340 EPLD FamilyFeatures•Erasable, user-configurable CMOS EPLDs capable of implementing high-density custom logic functions •0.8-micron double-metal CMOS EPROM technology (CY7C34X)•Advanced 0.65-micron CMOS technology to increase performance (CY7C34XB)•Multiple Array MatriX architecture optimized for speed, density, and straightforward design implementation —Programmable Interconnect Array (PIA) simplifies routing —Flexible macrocells increase utilization —Programmable clock control—Expander product terms implement complex logic functions •Warp2®—Low-cost VHDL compiler for CPLDs and PLDs —IEEE 1164-compliant VHDL —Available on PC and Sun platforms •Warp3®—VHDL synthesis —ViewLogic graphical user interface —Schematic capture (ViewDraw™)—VHDL simulation (ViewSim™)—Available on PC and Sun platformsGeneral DescriptionThe Cypress Multiple Array Matrix (MAX®) family of EPLDs provides a user-configurable, high-density solution to gener-al-purpose logic integration requirements. With the combina-tion of innovative architecture and state-of-the-art process, the MAX EPLDs offer LSI density without sacrificing speed.The MAX architecture makes it ideal for replacing large amounts of TTL SSI and MSI logic. For example, a 74161counter utilizes only 3% of the 128 macrocells available in the CY7C342B. Similarly, a 74151 8-to-1 multiplexer consumes less than 1% of the over 1,000 product terms in the CY7C342B. This allows the designer to replace 50 or more TTL packages with just one MAX EPLD. The family comes in a range of densities, shown below. By standardizing on a few MAX building blocks, the designer can replace hundreds of different 7400 series part numbers currently used in most dig-ital systems.The family is based on an architecture of flexible macrocells grouped together into Logic Array Blocks (LABs). Within the LAB is a group of additional product terms called expander product terms. These expanders are used and shared by the macrocells, allowing complex functions of up to 35 product terms to be easily implemented in a single macrocell. A Pro-grammable Interconnect Array (PIA) globally routes all signals within devices containing more than one LAB. This architec-ture is fabricated on the Cypress 0.8-micron, double-lay-er-metal CMOS EPROM process, yielding devices with signif-icantly higher integration, density and system clock speed than the largest of previous generation EPLDs. The CY7C34XB de-vices are 0.65-micron shrinks of the original 0.8-micron family.The CY7C34XBs offer faster speed bins for each device in the Cypress MAX family.The density and performance of the CY7C340 family is ac-cessed using Cypress’s Warp2 and Warp3 design software.Warp2 provides state-of-the-art VHDL synthesis for MAX and F LASH 370™ at a very low cost. Warp3 is a sophisticated CAE tool that includes schematic capture (ViewDraw) and timing simulation (ViewSim) in addition to VHDL synthesis.Consult the Warp2 and Warp3 datasheets for more informa-tion about the development tools.Max Family MembersFeature CY7C344(B)CY7C343(B)CY7C342BCY7C346(B)CY7C341BMacrocells 3264128128192MAX Flip-Flops 3264128128192MAX Latches [1]64128256256384MAX Inputs [2]2335598471MAX Outputs 1628526464Packages28H,J,W,P44H,J68H,J,R84H,J 100R,N84H,J,RKey:P—Plastic DIP; H—Windowed Ceramic Leaded Chip Carrier; J—Plastic J-Lead Chip Carrier; R—Windowed Pin Grid Array;W—Windowed Ceramic DIP; N—Plastic Quad Flat PackNotes:1.When all expander product terms are used to implement latches.2.With one output.PAL is a registered trademark of Advanced Micro Devices.MAX is a registered trademark of Altera Corporation.F LASH 370 is a trademark of Cypress Semiconductor Corporation.Warp2 and Warp3 are registered trademarks of Cypress Semiconductor Corporation.ViewDraw and ViewSim are trademarks of ViewLogic Corp.DEDICATED INPUTSLOGICBLOCKARRAY(LAB)EXPANDER PRODUCT TERMSDUALI/OFEEDBACKMULTIPLEARRAYS(LABS) MACROCELLSPROGRAMMABLEINTERCONNECTARRAY (PIA)C340–1Figure 1.Key MAX FeaturesFunctional DescriptionThe Logic Array BlockThe logic array block, shown in Figure 2, is the heart of the MAX architecture. It consists of a macrocell array, expand-er product term array, and an I/O block. The number of macrocells, expanders, and I/O vary, depending upon the device used. Global feedback of all signals is provided within a LAB, giving each functional block complete access to the LAB resources. The LAB itself is fed by the program-mable interconnect array and dedicated input bus. The feedbacks of the macrocells and I/O pins feed the PIA, pro-viding access to them through other LABs in the device.The members of the CY7C340 family of EPLDs that have a single LAB use a global bus, so a PIA is not needed (see Figure 3).The MAX MacrocellTraditionally, PLDs have been divided into either PLA (pro-grammable AND, programmable OR), or PAL® (programma-ble AND, fixed OR) architectures. PLDs of the latter type provide faster input-to-output delays, but can be inefficient due to fixed allocation of product terms. Statistical analysis of PLD logic designs has shown that 70% of all logic func-tions (per macrocell) require three product terms or less.The macrocell structure of MAX has been optimized to handle variable product term requirements. As shown in Figure 4,each macrocell consists of a product term array and a con-figurable register. In the macrocell, combinatorial logic is implemented with three product terms ORed together,which then feeds an XOR gate. The second input to the XOR gate is also controlled by a product term, providing the ability to control active HIGH or active LOW logic and to implement T- and JK-type flip-flops.If more product terms are required to implement a given func-tion, they may be added to the macrocell from the expander product term array. These additional product terms may be added to any macrocell, allowing the designer to build gate-in-tensive logic, such as address decoders, adders, compara-tors, and complex state machines, without using extra macro-cells.The register within the macrocell may be programmed for ei-ther D, T , JK, or RS operation. It may alternately be configured as a flow-through latch for minimum input-to-output delays, or bypassed entirely for purely combinatorial logic. In addition,each register supports both asynchronous preset and clear,allowing asynchronous loading of counters of shift registers,as found in many standard TTL functions. These registers may be clocked with a synchronous system clock, or clocked inde-pendently from the logic array.Expander Product TermsThe expander product terms, as shown in Figure 5, are fed by the dedicated input bus, the programmable interconnect array, the macrocell feedback, the expanders themselves,and the I/O pin feedbacks. The outputs of the expanders then go to each and every product term in the macrocell array. This allows expanders to be “shared” by the product terms in the logic array block. One expander may feed all macrocells in the LAB, or even multiple product terms in the same macrocell. Since these expanders feed the second-ary product terms (preset, clear, clock, and output enable)of each macrocell, complex logic functions may be imple-mented without utilizing another macrocell. Likewise, ex-panders may feed and be shared by other expanders, to implement complex multilevel logic and input latches.Figure 2.Typical LAB Block Diagram Figure 3.7C344 LAB Block DiagramI N P U T SP I AMACROCELLARRAYEXPANDER PRODUCT TERM ARRAYI/O BLOCKI/O PINSPROGRAMMABLE INTERCONNECTARRAYC340–2I N P U T SMACROCELL ARRAYEXPANDER PRODUCT TERM ARRAYI/O BLOCKI/O PINSC340–3Figure 4.Macrocell Block DiagramFigure 5.Expander Product Terms Figure 6.I/O Block DiagramDEDICATED INPUTSPROGRAMMABLE INTERCONNECTEXPANDER PRODUCT TERMS 16MACROCELL FEEDBACKS I/O OUTPUT ENABLEARRAY CLOCKCLEARPRESETTOI/O CONTROLNOTE: ONE SYSTEM CL OCK PER LABPQ CD PROGRAMMABLEFLIP–FLOP(D,T,JK,SR)D REGISTEREDORFLOW–THROUGH–LA TCH OPERATION DPROGRAMMABLECLOCKD ASYNCCLEARANDPRESETMACROCELL FEEDBACK8(32 FOR 7C344)32(64 FOR 7C344)SIGNALSTO PIAC340–4EXPANDER P-TERMSMACROCELL P-TERMSC340–5TO PIA (LAB FOR 7C344)I/O OUTPUT ENABLEFROM MACROCELL IN LABI/O PADTHREE–STATE BUFFERC340–6I/O BlockSeparate from the macrocell array is the I/O control block of the LAB. Figure 6 shows the I/O block diagram. The three-state buffer is controlled by a macrocell product term and the drives the I/O pad. The input of this buffer comes from a macrocell within the associated LAB. The feedback path from the I/O pin may feed other blocks within the LAB, as well as the PIA. By decoupling the I/O pins from the flip-flops, all the registers in the LAB are “buried,” allowing the I/O pins to be used as dedicated outputs, bidirectional outputs, or as additional dedicated inputs. Therefore, applications requiring many buried flip-flops, such as counters, shift registers, and state machines, no longer consume both the macrocell regis-ter and the associated I/O pin, as in earlier devices.The Programmable Interconnect ArrayPLD density and speed has traditionally been limited by signal routing; i.e., getting signals from one macrocell to another. For smaller devices, a single array is used and all signals are avail-able to all macrocells. But as the devices increase in density, the number of signals being routed becomes very large, in-creasing the amount of silicon used for interconnections. Also, because the signal must be global, the added loading on the internal connection path reducesthe overall speed performance of the device. The MAX archi-tecture solves these problems. It is based on the concept of small, flexible logic array blocks that, in the larger devices, are interconnected by a PIA.The PIA solves interconnect limitations by routing only the sig-nals needed by each LAB. The architecture is designed so that every signal on the chip is within the PIA. The PIA is then programmed to give each LAB access to the signals that it requires. Consequently, each LAB receives only the signals needed. This effectively solves any routing problems that may arise in a design without degrading the performance of the device. Unlike masked or programmable gate arrays, which induce variable delays dependent on routing, the PIA has a fixed delay from point to point. This eliminates undesired skews among logic signals, which may cause glitches in inter-nal or external logic.Development Software SupportWarp2Warp2 is a state-of-the-art VHDL compiler for designing with Cypress PLDs and CPLDs. Warp2 utilizes a proper subset of IEEE 1164 VHDL as its Hardware Description Language (HDL) for design entry. VHDL provides a number of significant benefits for the design entry process. Warp2 accepts VHDL input, synthesizes and optimizes the entered design, and out-puts a JEDEC map for the desired device. For functional sim-ulation, Warp2/ provides a graphical waveform simulator (NOVA).VHDL (VHSIC Hardware Description Language) is an open, powerful, non-proprietary language that is a standard for be-havioral design entry and simulation. It is already mandated for use by the Department of Defense, and supported by every major vendor of CAE tools. VHDL allows designers to learn a single language that is useful for all facets of the design pro-cess.Warp3Warp3 is a sophisticated design tool that is based on the latest version of ViewLogic’s CAE design environment. Warp3 fea-tures schematic capture (ViewDraw), VHDL waveform simula-tion (ViewSim), a VHDL debugger, and VHDL synthesis, all integrated in a graphical design environment. Warp3 is avail-able on PCs using Windows 3.1 or subsequent versions, and on Sun and HP workstations.For further information on Warp software, see the Warp2and Warp3 datasheets contained in this data book.Third-Party SoftwareCypress maintains a very strong commitment to third-party de-sign software vendors. All major third-party software vendors provide support for the MAX family of devices. T o expedite this support, Cypress supplies vendors with all pertinent architec-tural information as well as design fitters for our products. ProgrammingThe Impulse3™device programmers from Cypress will pro-gram all Cypress PLDs, CPLDs, FPGAs, and PROMs. The unit is a standalone programmer that connects to any IBM-compatible PC via the printer port.Third-Party ProgrammersAs with development software, Cypress strongly supports third-party programmers. All major third-party programmers support the MAX family.Cross ReferenceALTERA CYPRESSPREFIX EPM PREFIX: CYPREFIX: EP PREFIX: PALC22V10–10C PALC22V10D–7C22V10–10C PALC22V10D–10C22V10–10C PAL22V10C–7C+22V10–10C PAL22V10C–10C+22V10–15C PALC22V10B–15C22V10–15C PALC22V10D–15C5032DC7C344–25WC5032DC–27C344–20WC5032DC–157C344–15WC5032DC–17Call Factory5032DC–207C344–20WC5032DC–257C344–25WC5032DM7C344–25WMB5032DM–257C344–25WMB5032JC7C344–25HC5032JC–27C344–20HC5032JC–157C344–15HC5032JC–17Call Factory5032JC–207C344–20HC5032JC–257C344–25HC© Cypress Semiconductor Corporation, 1995. The information contained herein is subject to change without notice. Cypress Semiconductor Corporation assumes no responsibility for the use of any circuitry other than circuitry embodied in a Cypress Semiconductor product. Nor does it convey or imply any license under patent or other rights. Cypress Semiconductor does not authorize its products for use as critical components in life-support systems where a malfunction or failure may reasonably be expected to result in significant injury to the user. The inclusion of Cypress Document #: 38-00087-D5032JM 7C344–25HMB 5032JM–257C344–25HMB 5032LC 7C344–25JC 5032LC–27C344–20JC 5032LC–157C344–15JC 5032LC–17Call Factory 5032LC–207C344–20JC 5032LC–257C344–25JC 5032PC 7C344–25PC 5032PC–27C344–20PC 5032PC–157C344–15PC 5032PC–17Call Factory 5032PC–207C344–20PC 5032PC–257C344–25PC 5064JC 7C343–35HC 5064JC–17C343–25HC 5064JC–27C343–30HC 5064JI 7C343–35HI 5064JM 7C343–35HMB 5064LC 7C343–35JC 5064LC–17C343–25JC 5064LC–27C343–30JC 5128AGC–127C342B–12RC 5128AGC–157C342B–15RC 5128AGC–207C342B–20RC 5128AJC–127C342B–12HC 5128AJC–157C342B–15HC 5128AJC–207C342B–20HC 5128ALC–127C342B–12JC 5128ALC–157C342B–15JC 5128ALC–207C342B–20JC 5128GC 7C342–35RC 5128GC–17C342–25RC 5128GC–27C342–30RC 5128GM 7C342–35RMB 5128JC 7C342–35HC 5128JC–17C342–25HC 5128JC–27C342–30HC 5128JI 7C342–35HI 5128JI–27C342–30HI 5128JM 7C342–35HMB 5128LC 7C342–35JC 5128LC–17C342–25JC 5128LC–27C342–30JCCross Reference (continued)ALTERA CYPRESS 5128LI 7C342–35JI 5128LI–27C342–30HI 5130GC 7C346–35RC 5130GC–17C346–25RC 5130GC–27C346–30RC 5130GM 7C346–35RM 5130JC 7C346–35HC 5130JC–17C346–25HC 5130JC–27C346–30HC 5130JM 7C346–35HM 5130LC 7C346–35JC 5130LC–17C346–25JC 5130LC–27C346–30JC 5130LI 7C346–35JI 5130LI–27C346–30JI 5130QC 7C346–35NC 5130QC–17C346–25NC 5130QC–27C346–30NC 5130QI 7C346–35NI 5192AGC–157C341B–15RC 5192AGC–207C341B–20RC 5192AJC–157C341B–15HC 5192AJC–207C341B–20HC 5192ALC–17C341B–15JC 5192ALC–27C341B–20JC 5192GC 7C341–35RC 5192GC–17C341–25RC 5192GC–27C341–30RC 5192JM 7C341–35HM 5192JC 7C341–35HC 5192JC–17C341–25HC 5192JC–27C341–30HC 5192GM 7C341–35RM 5192JI 7C341–35HI 5192LC 7C341–35JC 5192LC–17C341–25JC 5192LC–27C341–30JCCross Reference (continued)ALTERA CYPRESS。
cy7c1041cv33_SRAM数据手册

Pin Configuration
Figure 1. 44-Pin SOJ/TSOP II (Top View) [1] Figure 2. 48-Ball FBGA Pinout (Top View) [1]
A0 A1 A2 A3 A4 CE IO0 IO1 IO2 IO3 VCC VSS IO4 IO5 IO6 IO7 WE A5 A6 A7 A8 A9
1 BLE IO0 IO1E IO2 IO3 IO4 IO5 NC A8
3 A0 A3 A5 A17 NC A14 A12 A9
4 A1 A4 A6 A7 A16 A15 A13 A10
5 A2 CE IO10
6 NC IO8 IO9 A B C D E F G H
Temperature ranges ❐ Commercial: 0°C to 70°C ❐ Industrial: –40°C to 85°C ❐ Automotive-A: –40°C to 85°C ❐ Automotive-E: –40°C to 125°C Pin and function compatible with CY7C1041BV33 High speed ❐ tAA = 10 ns (Commercial, Industrial and Automotive-A) ❐ tAA = 12 ns (Automotive-E) Low active power ❐ 324 mW (max) 2.0V data retention Automatic power down when deselected TTL-compatible inputs and outputs Easy memory expansion with CE and OE features Available in Pb-free and non Pb-free 44-pin 400 Mil SOJ, 44-pin TSOP II and 48-Ball FBGA packages
800MHz客车列尾和列车防护报警系统

800M机车电台主机组成框图
LBJ主机由电源单元、控制单元、备用电池、信道机、连接线缆、接口等组成:
电源板
13.8V
电池控制板
主控板
CPU及外围电路 POCSAG编码电路 FFSK编解码电路
串口扩展电路
TK980电台
12V2.5Ah充 电电池
电源 输入
双刀 双制 开关
LED显示板
控制 盒接 口1
控制 TAX/C 盒接 IR接 口2 口
866.2375 FFSK 间歇循环发射
列车防护报警信息
800M机车电台
故障列车
列车防护报警 工作过程
(事故列车)按下控制盒上的报警按键,LBJ 每5~10s 随机发送一次列车防护报警信息并进行记录。发送报 警信息时,状态指示灯每1s 闪亮一次,同时扬声器发 出提示音。
邻近列车的LBJ 接收到列车防护报警信息后进行记录, 同时显示报警信息包含的公里标,每5s发出一次提示 语音。按下“确认”键,应停止播放提示语音。LBJ 接收到列车防护报警解除信息,或者连续30s 以上未 再次收到列车防护报警信息时,恢复守候接收状态
外置方式:1、800M机车电台置于CIR外部;2、CIR的控制盒 替代了800M机车电台控制盒;3、仍从TAX/CIR接口获取机车 综合信息(TAX信息)
800M机车电台安装 (3 内置CIR)
内置CIR方式: 1、800M机车电台置于CIR内部;2、CIR的控制盒替 代了800M机车电台控制盒;3、从TAX/CIR接口获取机车综合信息 (TAX信息) 应符合《CIR与LBJ整合的技术方案 》要求;
补机机车的LBJ 不发送列车接近预警信息 道口报警设备、施工防护报警设备和预警器接
收到列车接近预警信息后,发出声光提示。
- 1、下载文档前请自行甄别文档内容的完整性,平台不提供额外的编辑、内容补充、找答案等附加服务。
- 2、"仅部分预览"的文档,不可在线预览部分如存在完整性等问题,可反馈申请退款(可完整预览的文档不适用该条件!)。
- 3、如文档侵犯您的权益,请联系客服反馈,我们会尽快为您处理(人工客服工作时间:9:00-18:30)。
4-Mbit (256K x 16) Static RAMCY7C1041DV33Features•Pin- and function-compatible with CY7C1041CV33•High speed —t AA =10 ns •Low active power—I CC = 90 mA @ 10 ns (Industrial)•Low CMOS standby power —I SB2 = 10 mA •2.0 V data retention•Automatic power-down when deselected •TTL-compatible inputs and outputs•Easy memory expansion with CE and OE features•Available in lead-free 48-ball VFBGA, 44-lead (400-mil) Molded SOJ and 44-pin TSOP II packagesFunctional Description [1]The CY7C1041DV33 is a high-performance CMOS Static RAM organized as 256K words by 16 bits. Writing to the device is accomplished by taking Chip Enable (CE) and Write Enable (WE) inputs LOW. If Byte LOW Enable (BLE) is LOW, then data from I/O pins (I/O 0–I/O 7), is written into the location specified on the address pins (A 0–A 17). If Byte HIGH Enable (BHE) is LOW, then data from I/O pins (I/O 8–I/O 15) is written into the location specified on the address pins (A 0–A 17).Reading from the device is accomplished by taking Chip Enable (CE) and Output Enable (OE) LOW while forcing the Write Enable (WE) HIGH. If Byte LOW Enable (BLE) is LOW,then data from the memory location specified by the address pins will appear on I/O 0 – I/O 7. If Byte HIGH Enable (BHE) is LOW, then data from memory will appear on I/O 8 to I/O 15. See the truth table at the back of this data sheet for a complete description of Read and Write modes.The input/output pins (I/O 0–I/O 15) are placed in a high-impedance state when the device is deselected (CE HIGH), the outputs are disabled (OE HIGH), the BHE and BLE are disabled (BHE, BLE HIGH), or during a Write operation (CE LOW, and WE LOW).The CY7C1041DV33 is available in a standard 44-pin 400-mil-wide body width SOJ and 44-pin TSOP II package with center power and ground (revolutionary) pinout, as well as a 48-ball fine-pitch ball grid array (FBGA) package.Note1.For guidelines on SRAM system design, please refer to the “System Design Guidelines” Cypress application note, available on the internet at .1415Logic Block DiagramA 1A 2A 3A 4A 5A 6A 7A 8COLUMN DECODERR O W D E C O D E RS E N S E A M P SINPUT BUFFER256K × 16A 0A 11A 13A 12A A A 16A 17A 9A 10I/O 0–I/O 7OE I/O 8–I/O 15CE WE BLEBHESelection Guide–10 (Industrial)–12 (Automotive)[2]Unit Maximum Access Time 1012ns Maximum Operating Current 9095mA Maximum CMOS Standby Current1015mAPin ConfigurationsNote2.Automotive product information is Preliminary.48-ball Mini FBGAWE V CC A 11A 10NC A 6A 0A 3CE I/O 2I/O 0I/O 1A 4A 5I/O 3I/O 5I/O 4I/O 6I/O 7V SS A 9A 8OE V SSA 7I/O 8BHE NC A 17A 2A 1BLE V CC I/O 9I/O 10I/O 11I/O 12I/O 13I/O 14I/O 15A 15A 14A 13A 12NC NCNC326541D E B A C F G HA 16Top ViewSOJTSOP II WE 1234567891011143132363534333740393812134144434216152930V CC A 5A 6A 7A 8A 0A 1OE V SS A 17I/O 15A 2CE I/O 2I/O 0I/O 1BHE A 3A 418172019I/O 32728252622212324V SS I/O 6I/O 4I/O 5I/O 7A 16A 15BLE V CC I/O 14I/O 13I/O 12I/O 11I/O 10I/O 9I/O 8A 14A 13A 12A 11A 9A 10NC (Top View)Maximum Ratings(Above which the useful life may be impaired. For user guide-lines, not tested.)Storage Temperature .................................–65°C to +150°C Ambient Temperature withPower Applied.............................................–55°C to +125°C Supply Voltage on V CC to Relative GND [3]....–0.3V to +4.6V DC Voltage Applied to Outputsin High-Z State [3].....................................–0.3V to V CC +0.3V DC Input Voltage [3]..................................–0.3V to V CC +0.3VCurrent into Outputs (LOW).........................................20 mA Static Discharge Voltage............................................>2001V (per MIL-STD-883, Method 3015)Latch-up Current......................................................>200 mAOperating RangeRange Ambient Temperature V CC Speed Industrial –40°C to +85°C 3.3V ± 0.3V 10 ns Automotive–40°C to +125°C3.3V ± 0.3V12 nsNote3.Minimum voltage is–2.0V and V IH (max) = V CC + 2V for pulse durations of less than 20 ns.DC Electrical Characteristics Over the Operating RangeParameter Description Test Conditions–10 (Industrial)–12 (Automotive)Unit Min.Max.Min.Max.V OH Output HIGH Voltage V CC = Min., I OH = –4.0 mA 2.42.4V V OL Output LOW Voltage V CC = Min., I OL = 8.0 mA0.40.4V V IH [3]Input HIGH Voltage2.0V CC + 0.3 2.0V CC + 0.3V V IL [3]Input LOW Voltage–0.30.8–0.30.8V I IX Input Leakage Current GND < V I < V CC –1+1–1+1µA I OZ Output Leakage Current GND < V OUT < V CC , Output Disabled –1+1–1+1µA I CCV CC Operating Supply CurrentV CC = Max., f = f MAX = 1/t RC 100MHz90-mA 83MHz 8095mA 66MHz 7085mA 40MHz6075mA I SB1Automatic CE Power-downCurrent—TTL InputsMax. V CC , CE > V IH V IN > V IH orV IN < V IL , f = f MAX2025mAI SB2Automatic CE Power-down Current—CMOS Inputs Max. V CC , CE > V CC – 0.3V,V IN > V CC – 0.3V,or V IN < 0.3V, f = 01015mACapacitance [4]Parameter DescriptionTest ConditionsMax.Unit C IN Input Capacitance T A = 25°C, f = 1 MHz, V CC = 3.3V8pF C OUTI/O Capacitance8pFThermal Resistance [4]ParameterDescription Test Conditions FBGA Package SOJ Package TSOP II Package Unit ΘJA Thermal Resistance (Junction to Ambient)Still Air, soldered on a3 × 4.5 inch,four-layer printed circuitboard27.8957.9150.66°C/W ΘJCThermal Resistance (Junction to Case)14.7436.7317.17°C/WAC Test Loads and Waveforms [5]90%10%3.0V GND90%10%ALL INPUT PULSES * CAPACITIVE LOAD CONSISTS OF ALL COMPONENTS OF THE TEST ENVIRONMENT Rise Time: 1 V/nsFall Time: 1 V/ns30 pF*OUTPUTZ = 50Ω50Ω1.5V(b)(a)3.3V OUTPUT5 pF(c)R 317ΩR2351ΩHigh-Z Characteristics10 ns deviceNotes4.Tested initially and after any design or process changes that may affect these parameters.5.AC characteristics (except High-Z) are tested using the load conditions shown in Figure (a). High-Z characteristics are tested for all speeds using the test load shown in Figure (c).AC Switching Characteristics Over the Operating Range[6]Parameter Description–10 (Industrial)–12 (Automotive)Unit Min.Max.Min.Max.Read Cyclet power[7]V CC(typical) to the first access100100µst RC Read Cycle Time1012nst AA Address to Data Valid1012nst OHA Data Hold from Address Change33nst ACE CE LOW to Data Valid1012nst DOE OE LOW to Data Valid56nst LZOE OE LOW to Low-Z00nst HZOE OE HIGH to High-Z[8, 9]56nst LZCE CE LOW to Low-Z[9]33nst HZCE CE HIGH to High-Z[8, 9]56nst PU CE LOW to Power-Up00nst PD CE HIGH to Power-Down1012nst DBE Byte Enable to Data Valid56nst LZBE Byte Enable to Low-Z00nst HZBE Byte Disable to High-Z66ns Notes6.Test conditions assume signal transition time of 3 ns or less, timing reference levels of 1.5V, input pulse levels of 0 to 3.0V, and output loading of the specifiedI OL/I OH and 30-pF load capacitance.7.t POWER gives the minimum amount of time that the power supply should be at typical V CC values until the first memory access can be performed.8.t HZOE, t HZCE,t HZBE and t HZWE are specified with a load capacitance of 5 pF as in part (c) of AC Test Loads. Transition is measured when the outputs enter a highimpedance state.9.At any given temperature and voltage condition, t HZCE is less than t LZCE, t HZOE is less than t LZOE, t HZBE is less than t LZBE, and t HZWE is less than t LZWE for anygiven device.Write Cycle [10, 11]t WC Write Cycle Time 1012ns t SCE CE LOW to Write End 78ns t AW Address Set-Up to Write End 78ns t HA Address Hold from Write End 00ns t SA Address Set-Up to Write Start 00ns t PWE WE Pulse Width78ns t SD Data Set-Up to Write End 56ns t HD Data Hold from Write End 00ns t LZWE WE HIGH to Low-Z [9]33ns t HZWE WE LOW to High-Z [8, 9]56ns t BWByte Enable to End of Write78nsData Retention Characteristics Over the Operating RangeParameter DescriptionConditions [12]Min.Max.Unit V DR V CC for Data Retention 2.0V I CCDRData Retention CurrentV CC = V DR = 2.0V,CE > V CC – 0.3V,V IN > V CC – 0.3V or V IN < 0.3VInd’l 10mA Auto15mA t CDR [4]Chip Deselect to Data Retention Time 0ns t R[13]Operation Recovery Timet RCnsData Retention WaveformAC Switching Characteristics Over the Operating Range [6](continued)ParameterDescription–10 (Industrial)–12 (Automotive)UnitMin.Max.Min.Max.3.0V 3.0V t CDRV DR >2VDATA RETENTION MODEt RCEV CC Notes10.The internal Write time of the memory is defined by the overlap of CE LOW, and WE LOW. CE and WE must be LOW to initiate a Write, and the transition ofeither of these signals can terminate the Write. The input data set-up and hold timing should be referenced to the leading edge of the signal that terminates the Write.11.The minimum Write cycle time for Write Cycle No. 4 (WE controlled, OE LOW) is the sum of t HZWE and t SD .12.No input may exceed V CC + 0.3V.13.Full device operation requires linear V CC ramp from V DR to V CC(min.) > 50 µs or stable at V CC(min.) > 50 µsSwitching WaveformsRead Cycle No. 1[14, 15]Read Cycle No. 2 (OE Controlled)[15, 16]PREVIOUS DATA VALIDDATA VALIDt RCt AAt OHAADDRESSDATA OUT50%50%DATA VALIDt RCt ACEt DOE t LZOE t LZCE t PUHIGH IMPEDANCEt HZOEt HZBEt PDHIGHOE CEICC ISB IMPEDANCEADDRESSDATA OUT V CC SUPPLY t DBE t LZBEt HZCE BHE,BLECURRENTI CCI SBNotes14.Device is continuously selected. OE, CE, BHE and/or BHE = V IL .15.WE is HIGH for Read cycle.16.Address valid prior to or coincident with CE transition LOW.Write Cycle No. 1 (CE Controlled)[17, 18]Switching Waveforms (continued)t HDt SDt SCEt SA t HAt AWt PWEt WCBWDATAI/OADDRESSCEWEBHE,BLEt Notes17.Data I/O is high-impedance if OE or BHE and/or BLE = V IH .18.If CE goes HIGH simultaneously with WE going HIGH, the output remains in a high-impedance state.Write Cycle No. 2 (BLE or BHE Controlled)Write Cycle No. 3 (WE Controlled, OE HIGH During Write)[17, 18]Switching Waveforms (continued)t HDt SDt BWt SA t HAt AWt PWEt WCt SCEDATAI/OADDRESSBHE,BLEWECEt HDtSDt PWEt SAt HAt AWt SCEt WCtHZOEDATA IN VALIDCEADDRESSWEDATA I/OOENOTE 19BHE,BLENote19.During this period the I/Os are in the output state and input signals should not be applied.Write Cycle No. 4 (WE Controlled, OE LOW)Truth TableCE OE WE BLE BHE I/O 0–I/O 7I/O 8–I/O 15ModePower H X X X X High-Z High-Z Power-down Standby (I SB )L L H L L Data Out Data Out Read All Bits Active (I CC )L L H L H Data Out High-Z Read Lower Bits Only Active (I CC )L L H H L High-Z Data Out Read Upper Bits Only Active (I CC )L X L L L Data In Data In Write All Bits Active (I CC )L X L L H Data In High-Z Write Lower Bits Only Active (I CC )L X L H L High-Z Data In Write Upper Bits Only Active (I CC )LHHXXHigh-ZHigh-ZSelected, Outputs DisabledActive (I CC )Switching Waveforms (continued)t HDt SDt SCEt HAt AWt PWEt WCt BWDATA I/OADDRESSCEWEBHE,BLEt SAt LZWEt HZWENOTE 19BHE,BLE Ordering InformationSpeed (ns)Ordering Code Package Diagram Package TypeOperating Range 10CY7C1041DV33-10BVI 51-8515048-ball VFBGAIndustrialCY7C1041DV33-10BVXI 48-ball VFBGA (Pb-Free)CY7C1041DV33-10VXI 51-8508244-lead (400-mil) Molded SOJ (Pb-Free)CY7C1041DV33-10ZSXI51-8508744-pin TSOP II (Pb-Free)12CY7C1041DV33-12BVXE 51-8515048-ball VFBGA (Pb-Free)AutomotiveCY7C1041DV33-12VXE 51-8508244-lead (400-mil) Molded SOJ (Pb-Free)CY7C1041DV33-12ZSXE51-8508744-pin TSOP II (Pb-Free)Please contact your local Cypress sales representative for availability of these partsOrdering InformationSpeed (ns)Ordering Code Package Diagram Package TypeOperating Range Package DiagramsPackage Diagrams(continued)Figure 2. 44-lead (400-mil) Molded SOJ (51-85082)51-85082-*BPackage Diagrams(continued)Figure 3. 44-pin TSOP II (51-85087)51-85087-*AAll products and company names mentioned in this document may be the trademarks of their respective holders.Document #: 38-05473 Rev. *D Page 13 of 14© Cypress Semiconductor Corporation, 2006. The information contained herein is subject to change without notice. Cypress Semiconductor Corporation assumes no responsibility for the useDocument History PageDocument Title: CY7C1041DV33 4-Mbit (256K x 16) Static RAMDocument Number: 38-05473REV.ECN NO.Issue Date Orig. ofChange Description of Change **201560See ECN SWI Advance Data sheet for C9 IPP*A233729See ECN RKF 1.AC, DC parameters are modified as per EROS(Spec # 01-2165)2.Pb-free offering in the ‘Ordering information’*B351117See ECN PCI Changed from Advance to PreliminaryRemoved 15 and 20 ns Speed binCorrected DC voltage (min) value in maximum ratings section from - 0.5 to- 0.3VRedefined I CC values for Com’l and Ind’l temperature rangesI CC (Com’l):Changed from 100, 80 and 67 mA to 90, 80 and 75 mA for 8, 10and 12ns speed bins respectivelyI CC (Ind’l): Changed from 80 and 67 mA to 90 and 85 mA for 10 and 12nsspeed bins respectivelyAdded Static Discharge Voltage and latch-up current specAdded V IH(max)spec in Note# 2Changed Note# 4 on AC Test LoadsChanged reference voltage level for measurement of Hi-Z parameters from±500 mV to ±200 mVAdded Data Retention Characteristics/Waveform and footnote # 11, 12Added Write Cycle (WE Controlled, OE HIGH During Write) Timing DiagramChanged Package Diagram name from 44-pin TSOP II Z44 to 44-pin TSOPII ZS44 and from 44-lead (400-mil) Molded SOJ V34 to 44-lead (400-mil)Molded SOJ V44Changed part names from Z to ZS in the Ordering Information TableAdded 8 ns Product InformationAdded Lead-Free Ordering InformationShaded Ordering Information Table*C446328See ECN NXR Converted from Preliminary to FinalRemoved -8 speed binRemoved Commercial Operating Range product informationIncluded Automotive Operating Range product informationUpdated Thermal Resistance tableUpdated footnote #8 on High-Z parameter measurementUpdated the ordering information and replaced Package Name column withPackage Diagram in the Ordering Information Table *D480177See ECN VKN Added -10BVI product ordering code in the Ordering Information table。