复杂模具设计与技巧
汽车零件生产中的模具设计和制造技术

汽车零件生产中的模具设计和制造技术在汽车制造业中,模具设计和制造技术起着至关重要的作用。
汽车零件的制造过程中,为了保证产品的质量和效率,需要依赖于高精确度和复杂形状的模具。
本文将探讨汽车零件生产中的模具设计和制造技术,并介绍其在整个汽车制造过程中的重要性和应用。
一、模具设计的重要性模具是用于制造零件的工具,能够给予材料以特定的形状和尺寸。
在汽车零件生产中,模具的设计决定了零件的精确度、质量和生产效率。
一个优良的模具设计能够最大程度地优化制造过程,减少材料浪费和加工工时,并确保零件的尺寸精确度符合要求。
因此,合理、高效的模具设计对于汽车零件生产至关重要。
二、模具设计的原则1. 简化和标准化模具设计需要以简化和标准化为原则。
简化设计可以减少加工工序和工时,提高生产效率;标准化设计可以降低模具制造和维护的成本,提高模具的通用性和重复使用性。
2. 精确度和稳定性模具的设计应追求高精确度和稳定性。
高精确度可以保证零件的尺寸和质量符合要求,减少后续加工的次数和工时;稳定性可以保证模具在长时间生产过程中不失效,提高生产效率和经济性。
3. 强度和刚度模具在生产过程中承受着较大的压力和力矩,因此其设计应具备足够的强度和刚度,以保证模具的使用寿命和安全性。
4. 可维护性和易操作性模具设计应具备较好的可维护性和易操作性。
良好的可维护性可以减少模具故障的发生和维修时间,提高生产效率;易操作性可以降低操作人员的劳动强度和错误率。
三、模具制造技术的应用1. CAD/CAM技术计算机辅助设计(CAD)和计算机辅助制造(CAM)技术在模具设计和制造中得到广泛应用。
CAD技术可以帮助设计师快速、准确地完成模具的三维建模和工程图纸绘制;CAM技术可以实现自动化的数控加工,提高制造的精度和效率。
2. 数控机床技术数控机床技术是现代模具制造中必不可少的一部分。
通过数控机床,可以实现对模具各个零部件的精密加工和装配,大大提高了制造的精度和效率。
CimatronE五金模具设计针对复杂曲面展开的解决方法

CimatronE五金模具设计针对复杂曲面展开的解决方法3D平台的五金模具设计是一项新颖设计理念,面对日新月异的替换性市场的更新,钣金产品零件设计越来越复杂,这就注定传统式的2D五金设计平台必然遇到无法解决的瓶颈,例如钣金零件复杂型位展开,钣金零件冲压精度,更重要的是交付周期的日益缩减;同时这也是五金模具设计生产的发展的重大难点之一。
CimatronE软件五金模具解决方案在客户使用群体中深得广泛好评,尤其在专业钣金展开功能中特具特点——操作简单,展开精准,效率奇高。
针对复杂异性的钣金成型零件展开与冲压有限元分析,CimatronE拥有简单非凡的解决方法。
下面以一个案例简述如何进行异性复杂曲面的钣金展开。
1、见上图零件档案,整个图档均为非规则曲面,没有一处地方是平直曲面。
通过级进模向导进入级进模设计系统,并设定材料的类型为:SPCC;材料厚度为2mm。
2、选取,新增一个工步。
3、通过选取钣金零件的上表面或者下表面作为展开的参考基准面。
这时CimatronE钣金展开的系统会自动侦测钣金零件的材料厚度,上面的步骤我们所设定的2mm和实际的图档的厚度1.6mm有差异,系统会自动提醒用户需要更新材料厚度。
4、在新增的工位中,我们把所有孔部分通过CimatronE的曲面修补功能快速修补曲面上的孔位。
5、同时在该工位中把补好孔位的曲面通过,把曲面分配相应的“Trimming Punch”冲压属性,其余的曲面分配为“Fix”冲压属性,以便在后期设计中区分其冲压的工序。
(可以根据个人偏好修改冲压属性的表达方式)6、完成以上步骤,继续选取。
在上一个工位基础上再增加一个工位。
此时,把刚才所归属“Trimming Punch”冲压属性的曲面合并在“Fix”冲压属性中,增加钣金零件右边的曲面为“Formming Punch”冲压属性。
7、继续基于前个工序增加新一个工站。
并把“Formming Punch”冲压属性(即黄色部分曲面)的曲面删除。
复杂飞机蒙皮拉伸成形模具设计方法分析
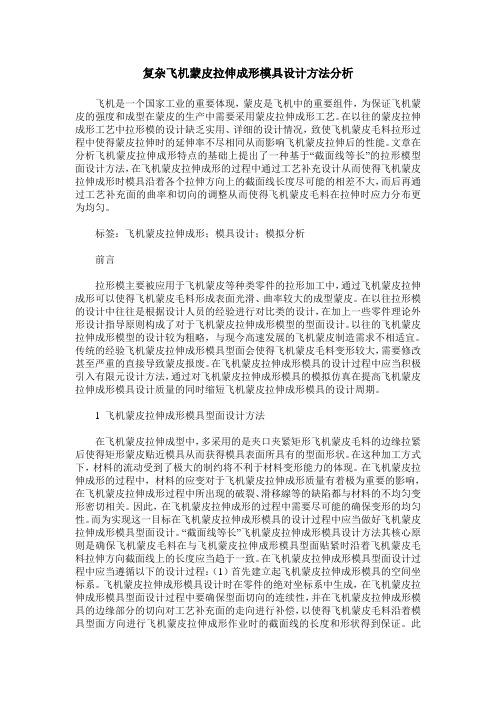
复杂飞机蒙皮拉伸成形模具设计方法分析飞机是一个国家工业的重要体现,蒙皮是飞机中的重要组件,为保证飞机蒙皮的强度和成型在蒙皮的生产中需要采用蒙皮拉伸成形工艺。
在以往的蒙皮拉伸成形工艺中拉形模的设计缺乏实用、详细的设计情况,致使飞机蒙皮毛料拉形过程中使得蒙皮拉伸时的延伸率不尽相同从而影响飞机蒙皮拉伸后的性能。
文章在分析飞机蒙皮拉伸成形特点的基础上提出了一种基于“截面线等长”的拉形模型面设计方法,在飞机蒙皮拉伸成形的过程中通过工艺补充设计从而使得飞机蒙皮拉伸成形时模具沿着各个拉伸方向上的截面线长度尽可能的相差不大,而后再通过工艺补充面的曲率和切向的调整从而使得飞机蒙皮毛料在拉伸时应力分布更为均匀。
标签:飞机蒙皮拉伸成形;模具设计;模拟分析前言拉形模主要被应用于飞机蒙皮等种类零件的拉形加工中,通过飞机蒙皮拉伸成形可以使得飞机蒙皮毛料形成表面光滑、曲率较大的成型蒙皮。
在以往拉形模的设计中往往是根据设计人员的经验进行对比类的设计,在加上一些零件理论外形设计指导原则构成了对于飞机蒙皮拉伸成形模型的型面设计。
以往的飞机蒙皮拉伸成形模型的设计较为粗略,与现今高速发展的飞机蒙皮制造需求不相适宜。
传统的经验飞机蒙皮拉伸成形模具型面会使得飞机蒙皮毛料变形较大,需要修改甚至严重的直接导致蒙皮报废。
在飞机蒙皮拉伸成形模具的设计过程中应当积极引入有限元设计方法,通过对飞机蒙皮拉伸成形模具的模拟仿真在提高飞机蒙皮拉伸成形模具设计质量的同时缩短飞机蒙皮拉伸成形模具的设计周期。
1 飞机蒙皮拉伸成形模具型面设计方法在飞机蒙皮拉伸成型中,多采用的是夹口夹紧矩形飞机蒙皮毛料的边缘拉紧后使得矩形蒙皮贴近模具从而获得模具表面所具有的型面形状。
在这种加工方式下,材料的流动受到了极大的制约将不利于材料变形能力的体现。
在飞机蒙皮拉伸成形的过程中,材料的应变对于飞机蒙皮拉伸成形质量有着极为重要的影响,在飞机蒙皮拉伸成形过程中所出现的破裂、滑移線等的缺陷都与材料的不均匀变形密切相关。
最全注塑模具设计步骤以及注意事项的讲解
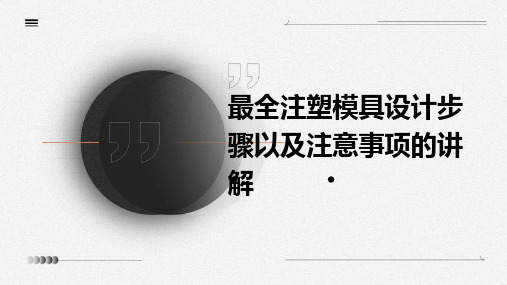
控铣削等加工方法,确保型芯、型腔的加工精度和表面质量。
02
浇口套、定位圈等关键零件加工工艺
采用高精度磨削、研磨等加工方法,保证零件的尺寸精度和形位公差。
03
导柱、导套等导向零件加工工艺
采用无心磨床、外圆磨床等高精度磨削设备,确保导向零件的精度和耐
磨性。
装配顺序和调试方法论述
装配顺序
遵循先下后上、先内后外的原则,先进行模架等支撑零件的装配,再进行型芯、型腔等成型零件的装配,最后进 行浇口套、定位圈等关键零件的装配。
根据模具结构确定加热装置的安装位置, 确保加热均匀且不影响模具其他功能。
油温机/水温机:适用于大型模具,加热 均匀,稳定性好。
03
06
考虑加热装置与冷却系统的协调,避免相 互干扰。
温度控制精度要求及实现途径
01
温度控制精度要求
02
根据制品要求确定温度控制精度,一般要求在±2℃ 以内。
03
对于高精度制品,温度控制精度要求更高,可达 ±1℃以内。
03
04
加强与客户和同行的沟 通和合作,不断提升服 务水平和市场竞争力。
培养高素质的人才队伍 ,为公司的可持续发展 提供有力保障。
感谢观看
THANKS
常见故障排查技巧和经验分享
常见故障排查技巧
介绍常见的注塑模具故障排查技巧,如检查模具磨损、清洗模具等。
经验分享
分享行业专家在注塑模具故障排除方面的经验和案例,提高读者解决问题的能力。
预防性维护策略推广
预防性维护策略
阐述预防性维护在注塑模具管理中的重要性 ,提出定期维护、保养和检查等策略。
推广实施
调试方法
在装配过程中,采用试装、试模等方法进行调试,确保模具各部件的配合精度和动作顺畅。对于复杂模具,还需 进行多次试模和调整,以达到最佳状态。
模具设计原理及考虑

制件设计的一般考虑工程塑料制品大部分是用注射成型方法加工而成的,制件的设计必须在满足使用要求和符合塑料本身的特性前提下,尽可能简化结构和模具、节省材料、便于成型。
制件设计中应分别考虑如下因素:一、制件的形状应尽量简单、便于成型。
在保证使用要求前提下,力求简单、便于脱模,尽量避免或减少抽芯机构,如采用下图例中(b)的结构,不仅可大大简化模具结构,便于成型,且能提高生产效率。
二、制件的壁厚确定应合理。
塑料制件的壁厚取决于塑件的使用要求,太薄会造成制品的强度和刚度不足,受力后容易产生翘曲变形,成型时流动阻力大,大型复杂的制品就难以充满型腔。
反之,壁厚过大,不但浪费材料,而且加长成型周期,降低生产率,还容易产生气泡、缩孔、翘曲等疵病。
因此制件设计时确定制件壁厚应注意以下几点:1.在满足使用要求的前提下,尽量减小壁厚;2.制件的各部位壁厚尽量均匀,以减小内应力和变形;3.承受紧固力部位必须保证压缩强度;4.避免过厚部位产生缩孔和凹陷;5.成型顶出时能承受冲击力的冲击。
国外的一些常用塑料的推荐壁厚如下表:三、必须设置必要的脱模斜度为确保制件成型时能顺利脱模,设计时必须在脱模方向设置脱模斜度,其大小与塑料性能、制件的收缩率和几何形状有关,对于工程塑料的结构件来说,一般应在保证顺利脱模的前提下,尽量减小脱模斜度。
下表为根据不同材料而推荐的脱模斜度:具体确定脱模斜度时应考虑以下几点:1.对于收缩率大的塑料制件应选用较大的脱模斜度;2.对于大尺寸制件或尺寸精度要求高的制件应采用较小的脱模斜度;3.制件壁厚较厚时,成型收缩增大,因此脱模斜度应取大;4.对于增强塑料脱模斜度宜取大;5.含自润滑剂等易脱模塑料可取小;6.一般情况下脱模斜度不包括在制件公差范围内。
四.强度和刚度不足可考虑设计加强筋为满足制件的使用所需的强度和刚度单用增加壁厚的办法,往往是不合理的,不仅大幅增加了制件的重量,而且易产生缩孔、凹痕等疵病,在制件设计时应考虑设置加强筋,这样能满意地解决这些问题,它能提高制件的强度、防止和避免塑料的变形和翘曲。
大型复杂截面铝型材模具的宽展结构设计

大型复杂截面铝型材模具的宽展结构设计李明环唐性宇广东华昌铝厂有限公司(广东佛山 528231)摘要:本文通过实际例子说明了铝合金型材挤压宽展模具设计原理的应用,采用宽展结构的模具可以使挤压机的工作潜能发挥到最大程度,较好的解决了“小机出大料”的生产难题。
关键词:铝型材、宽展结构、模具设计1、前言目前,国内铝挤压行业发展迅猛,市场对大尺寸截面铝型材的需求量正逐年上升,但是,由于5000吨以上的大型挤压机的设备投资较大,并且,大型挤压机的挤压生产成本较高,因此,国内目前只有少数大企业才装备有5000吨以上的大型挤压机。
而绝大多数铝型材生产企业所装备的挤压机都是以4000吨以下的中小型挤压机为主。
用中小型挤压机生产几何尺寸较大的型材时,由于受到挤压筒直径的限制,这类型材的挤压生产难度非常大,小机出大料问题一直是困扰铝挤压模具行业的技术难题。
本文通过几个具体的模具设计实例,谈谈复杂型材宽展模具的设计体会。
2、宽展设计原理宽展模具就是在模具前端设置一个具有宽展功能的导流板,挤压时使圆铸锭产生一次预变形,变形后的铸锭截面大致接近于宽厚比大的型材截面尺寸,使导流板的导流孔的宽度逐渐增大到接近或大于圆挤压筒的内径,金属再经过二次变形流出模孔,以生产出外接圆尺寸超过圆挤压筒直径的大尺寸型材。
在进行宽展模的设计过程中,要用到宽展率δB和宽展角β。
导流板的宽展率δB:×100%,δB。
导流板的宽展角β为:式中:δ----导流板的宽展率(通常在15%~35%范围较合适);β----导流板的宽展角(一般β角小于30°);B2----为宽展直径;B1----为进料直径;H B----为导流板的厚度。
宽展角在一般情况下都选择在30度以内,如果宽展角过大,金属将出现填充不良现象,但是,在特殊的情况下,采用特殊的模具结构,可以突破常规极限,使宽展角设计的更大。
3、宽展模设计实例设计实例一:工程料大装饰板(如图1)模具设计基本参数:挤压机吨位2500T,挤压筒直径φ236mm,挤压系数18,模具直径:460-480℃,挤压速度8~15m/min 。
复杂注塑模具设计新方法及案例

复杂注塑模具设计新方法及案例:一、设计方法:1. 分型面的选择:分型面的设计是注塑模具设计中的重要环节,它决定了模具的成型效果和脱模的难易程度。
在设计分型面时,需要考虑产品的形状、尺寸、精度要求以及模具的结构和制造工艺等因素。
2. 抽芯机构的设计:对于一些产品,如带有侧孔或侧凸台的产品,需要设计抽芯机构以实现侧向脱模。
抽芯机构的设计需要充分考虑产品的结构和尺寸,以及模具的加工能力和装配工艺。
3. 脱模机构的设计:脱模机构的主要作用是使产品从模具中顺利脱出。
在设计脱模机构时,需要考虑产品的形状和尺寸,以及模具的制造工艺和装配工艺。
4. 冷却系统的设计:冷却系统的主要作用是控制模具的温度,保证注塑过程中的冷却均匀,提高产品的成型质量和生产效率。
冷却系统的设计需要考虑模具的结构和尺寸,以及冷却介质的选择和流动路径的优化。
5. 浇注系统的设计:浇注系统的主要作用是将熔融塑料注入模具型腔,保证注塑过程的稳定性和产品的成型质量。
浇注系统的设计需要考虑产品的形状和尺寸,以及塑料的流动特性和模具的结构。
二、案例分析:以下是一个复杂注塑模具设计的案例分析:1. 产品分析:该产品是一个汽车零部件,具有复杂的形状和尺寸要求,需要进行精密成型和严格的质量控制。
2. 模具结构设计:根据产品的形状和尺寸,设计了相应的模具结构。
该模具采用了分型面和抽芯机构的设计,以实现复杂形状的成型和侧向脱模。
同时,模具还设计了合理的浇注系统和冷却系统,以保证注塑过程的稳定性和产品的成型质量。
3. 制造与装配:根据模具的设计图纸,进行了相应的制造和装配工作。
在制造过程中,采用了高精度的加工设备和工艺,保证了模具各部件的精度和表面质量。
在装配过程中,严格按照设计图纸和技术要求进行组装,确保了模具的整体性能和稳定性。
4. 试模与调整:完成模具制造和装配后,进行了试模工作。
通过试模,对模具的性能和产品的成型质量进行了评估和检测。
针对试模过程中出现的问题,进行了相应的调整和完善,最终实现了模具的正常运行和产品的合格产出。
模具结构设计
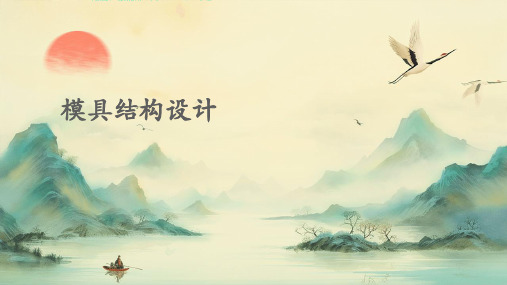
VS
详细描述
锻造模具结构设计需要考虑锻造工艺参数 、锻造材料特性、模具寿命和制造成本等 因素。在设计中,应注重优化模膛设计、 导向装置、顶出装置等部分,以确保锻造 生产的顺利进行和产品质量。
05
模具结构设计软件与应用
CAD/CAE/CAM技术在模具结构设计中的应用
01
CAD(计算机辅助 设计)
利用CAD软件进行模具的三维建 模,实现模具零件的精确设计和 定位。
低热膨胀系数
模具材料的热膨胀系数应尽可能小,以减小 温度变化对模具尺寸的影响。
04
模具结构设计实例分析
注塑模具结构设计实例
总结词
注塑模具结构设计是模具设计中的重要一环,需要考虑多方面因素,如塑考虑塑料的收缩率、流动性、结晶性等特性,以及模具的强度、刚度、寿命等因素。同时, 还需要考虑注塑机参数,如注射量、注射压力、模具安装尺寸等。在设计中,应注重优化浇注系统、冷却系统、 顶出系统等部分,以提高生产效率和产品质量。
浇注系统设计
浇注系统是模具的重要组成部分,其 设计的好坏直接影响到制品的质量和 生产效率。
浇注系统的结构形式有多种,应根据 制品的大小、形状和材料特性选择合 适的结构形式。
浇注系统的设计应遵循“快速、等高 、等流量”的原则,确保金属液能够 均匀地充满型腔。
浇注系统的尺寸和位置对制品的尺寸 精度和模具的加工制造也有很大影响, 需要仔细考虑。
02
CAE(计算机辅助 工程)
通过CAE技术对模具结构进行有 限元分析,预测模具的应力分布、 变形和寿命等性能。
03
CAM(计算机辅助 制造)
将模具设计数据导入CAM软件, 生成数控加工代码,控制机床完 成模具的加工制造。
常用模具结构设计软件介绍
基于Pro/E复杂分型面的模具型腔设计

0 引言
在注塑模具 的三维设计 中,分型面 的设 计 十分关键 。在设计分型面之前 ,应将零件 的表 面 区分为3 :模具型腔的表面 、靠破孔 的表面 种 和两者的组合表面 。通常所说 的分型面是指模 具的外分型面 ,即动 、定模块 的直接接触 面 。 分型的基本原理是 :寻找分型线 ,构 建内 、外 分型面 ,分离只属于型腔或 型芯 的单一表面 , 分割共 同属于型腔 、型芯或 滑块 的表面 ,并分 别缝补 ,组合成复合式 的分型 面。利用分型面 分割模具主体 积块 ,抽取模具元件 。
徐 云 杰
( 浙江林学院工程学院
摘
机 电系,浙江
杭州
3 10 ) 13 0
要 :通 过对 一般 注 塑模 具型 腔 分 型 面的的设 计 方 法 ,介
绍 了生 成模 具型 腔 的 过程 ,解 决 了复杂模 具 型 腔 分型 难 的 问题 。实 践证 明该 方 法对其 它 复
表面和靠破孔表面 ,分型 面设计较 复杂 ,必须
1 2 3 4 5 6
利用 曲线特征及 曲面操 控命令 来进行 ,下面以
连 接体 为例 说 明 。连 接 体 三维 模 型 如 图 l 示 , 所
图2 动 、定 模 的 内分 型面
维普资讯
3 8
Di n udT c n lg 2 20 ea dMo l eh oo yNo 07
.
文章编号:10—942 0)203 .3 0 1 3(070—0 8 4 0
基 于P oE r / 复杂分 型 面 的模 具 型腔 设 计
可得 到 动 、定模 的 内 分型 面 ( 图2)。
橡塑模具加工方法

橡塑模具加工方法橡塑模具是制作橡胶和塑料制品的重要工具,它的加工方法对产品的质量和生产效率有着直接的影响。
本文将介绍橡塑模具加工的一些常用方法和技巧。
一、模具设计模具的设计是橡塑模具加工的第一步,它决定了产品的形状和尺寸。
模具设计要考虑到产品的用途和制作工艺,合理确定模具的结构和材料。
在设计过程中,需要充分考虑产品的结构特点和工艺要求,以及模具的制造工艺和使用寿命。
二、模具材料选择模具材料的选择直接关系到模具的使用寿命和加工效果。
常用的模具材料有钢、铝和塑料等。
钢材具有高强度和硬度,适用于大批量生产;铝材轻便易加工,适用于小批量生产和试制;塑料模具具有成本低、制造周期短的特点,适用于快速成型和样品制作。
三、模具加工工艺橡塑模具加工工艺包括模具结构加工、模具零件加工和模具总装等过程。
模具结构加工是将设计好的模具结构进行切割、打磨和修整,形成模具的基本形状。
模具零件加工是将模具结构的各个零件进行加工和装配,使其达到设计要求。
模具总装是将各个零部件进行组装和调试,确保模具的正常运行。
四、模具加工设备橡塑模具加工需要使用各种设备和工具,包括数控加工中心、电火花加工机、线切割机等。
数控加工中心能够实现高精度的切削加工,适用于复杂形状和高精度的模具加工;电火花加工机和线切割机能够实现对硬质材料的加工,适用于模具的细部加工和修整。
五、模具加工技巧橡塑模具加工需要掌握一些技巧和经验,以提高加工效率和产品质量。
首先,要合理选择切削工艺和刀具,以减少切削力和切削温度,提高切削效率。
其次,要掌握好加工参数和加工顺序,以确保模具的加工精度和表面质量。
最后,要注意模具的保养和维护,定期清洁和润滑模具,延长模具的使用寿命。
六、模具加工质量控制橡塑模具加工质量控制是确保产品质量的关键环节。
在加工过程中,要进行严格的质量检查和控制,及时发现和解决问题。
常用的质量控制方法包括尺寸测量、外观检查和功能测试等。
同时,要建立健全的质量管理体系,加强对加工过程的监控和控制,确保模具的加工质量和一致性。
模具设计与制造工艺

模具设计与制造工艺1.引言1.1 概述概述:模具设计与制造工艺是现代制造业中不可或缺的重要环节。
模具是用于制造各种产品的工具,它的设计和制造质量直接关系到产品的成型质量和生产效率。
模具设计和制造工艺的优化能够提高产品质量、降低成本,提高生产效率,对于企业的发展具有重要意义。
本文将对模具设计与制造工艺进行系统的介绍和分析。
首先,我们会概述模具设计与制造工艺的基本概念和作用。
其次,我们会详细介绍模具设计的原则和要素,包括模具的结构、材料选择等方面的内容。
然后,我们将重点介绍模具制造的工艺流程和材料选择,在这一部分中,我们会讨论模具的加工工艺和技术难点,以及如何选择合适的材料来制造模具。
最后,我们将对整篇文章进行总结与回顾,并展望模具设计与制造工艺的未来发展趋势。
通过阅读本文,读者将了解到模具设计与制造工艺的基本概念和作用,掌握模具设计和制造的原则和要素,以及了解模具制造的工艺流程和材料选择。
这对于相关从业人员来说是非常有价值的,也有助于提高企业的生产效率和产品质量。
在接下来的章节中,我们将深入探讨模具设计与制造工艺的各个方面,并带领读者一步步了解这一重要领域的知识和技术。
让我们一同进入模具设计与制造工艺的精彩世界!1.2文章结构文章结构部分的内容可以描述整篇文章按照何种顺序和组织框架进行撰写和组织。
以下是一种可能的写法:1.2 文章结构本文将按照以下结构进行组织和撰写:引言部分(章节1)将先对模具设计与制造工艺进行概述,介绍主要内容和背景,然后给出文章的目的和目标。
通过引言,读者能够明确理解本文的主要论述方向和意义。
正文部分(章节2)将分为两个主要部分:模具设计和制造工艺。
- 模具设计部分(章节2.1)将首先介绍设计模具的原则,即设计中应遵循的基本原则和规范,以确保设计的模具具备所需功能和性能。
随后,我们将详细探讨模具设计的要素,涵盖设计中需要考虑的各个方面和因素,如结构设计、尺寸规格、模具材料等等。
典型复杂造型PMMA把手热流道模具优化设计

61
2 2 注 塑 工艺参数 设 定 .
根据 本 制 品特 点 、 似 制 品生 产 经 验 和 材 料 供 类 应商 推荐 的工 艺参 数 , 用 较 高 的 模 温 以提 高 材 料 采
流动性 , 采用较长 的保压 时间以降低 收缩率 。由于 冷却 时间越 长 , 品体 积收 缩 的机会 越 大 , 制 故应 尽 可 能提高冷却速率 , 降低冷却时 间。模 流分析工艺参
2 3 模 拟 分析 .
() 1 填充 过程
填充 过 程如 图 4所 示 。从 图 4可 看 出 , 中心 从 直接 进浇 充 填进 展顺 利 , 但有 些 不平衡 , 主要 原 因是
成降解现象。
把手 内芯与外缘筋条 的充填速度 不一致 , 筋条位充
填较 快 , 造成 整 体充 填 不平 衡 。 由于 筋 条 是 用 来 增 强把 手 的扭力 值 的 , 故不 能取 消 。多 增 加 几 条 筋 条
和注射 周期延 长 。根 据模 拟 结 果 , 者 找 出 了收 缩 笔
该 工艺 的缺 点是模 具 制 造周 期 长 , 角形 状 很 难保 棱 证 。而采用铍 铜材 料挤压 成 型动 、 模镶件 , 定 则可 缩 短 5天 以上 的制模 时 问 , 提 高 了棱 角 的形 状 精 度 并 及 表 面光亮 度 。铍 铜挤 压工艺 的原理 如 图 1 0所示 。
最 大剪 切 速 率 分 布 见 图 6 由 图 6可 以看 出 , 。 最 大剪 切速 率 出现在 浇 口处 , 数值 为 8 4 . ~, 7 13s 小 于 材料 的最 大剪 切速 率 2 0 一, 1 0s 因此 可 以判 断浇 0 口的设计 比较合 理 , 会 产 生 因剪切 速率 过 高 而 造 不
模具设计与制造的技术创新

模具设计与制造的技术创新模具设计与制造是现代工业生产中至关重要的一环。
模具的设计与制造水平直接关系到产品质量、生产效率和经济效益。
随着科技的进步和市场需求的不断变化,模具设计与制造也在不断创新与完善。
本文将从材料、技术和制造流程等方面,探讨模具设计与制造的技术创新。
一、材料创新模具的材料选择直接影响到模具的使用寿命和产品质量。
传统的模具材料主要是钢材,其优点是强度高、耐磨性好,但存在密度大、加工难度大、成本高等问题。
近年来,随着金属材料与复合材料的结合,模具材料得到了更多的选择。
1. 铝合金模具材料:铝合金模具材料具有密度低、导热性好的特点,可实现快速传热和节能效果。
同时,铝合金还具有较好的加工性能,易于切削和成型。
而且,铝合金模具材料的成本相对较低,适用于中小型模具的制造。
2. 聚合物模具材料:聚合物模具材料是一种非金属材料,具有密度低、成本低、加工性好、自重轻等优点。
同时,聚合物材料还具有良好的耐磨性、抗撞击性和耐寒性。
适用于小型和中型模具的制造,尤其是对产品高度精密要求的模具。
3. 纳米材料模具:纳米材料模具具有高强度、高韧性和高硬度的特点,能提高模具的耐磨性和寿命。
纳米材料模具的应用有助于提高产品质量和制造效率,但目前其成本还较高,限制了其大规模应用。
二、技术创新模具设计与制造的技术创新对于提高生产效率、降低生产成本和提高产品质量都具有重要意义。
以下是一些技术创新的例子:1. CAD/CAE/CAM技术:计算机辅助设计(CAD)、计算机辅助工程(CAE)和计算机辅助制造(CAM)技术的应用,使得模具设计与制造过程实现了数字化、网络化和智能化。
CAD技术可以提高模具设计的精确度和效率,CAE技术可以模拟和优化模具设计,CAM技术可以实现自动化制造和加工。
2. 快速成型技术:快速成型技术是一种通过激光熔化或熔接增材制造方式快速制造模具的方法。
这种技术可以大幅度缩短模具制造周期,降低制造成本,适用于小批量、多变形和复杂结构的模具。
注塑模具结构及设计-8(斜顶强脱)
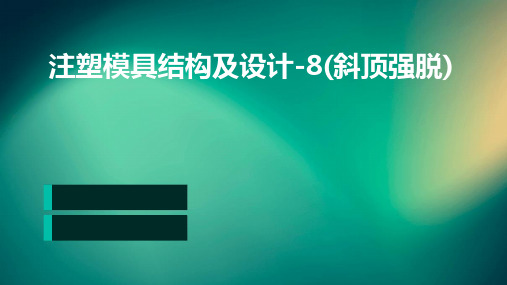
02 注塑模具的基本结构
主流道设计
01
主流道是模具中直接与注塑机喷 嘴接触的部分,通常设计为圆锥 形,便于塑料流动。
02
主流道应与喷嘴紧密配合,防止 溢料,同时要求耐磨、耐高温。
分流道设计
分流道是连接主流道与模具型腔的通 道,用于将塑料均匀分配到各个型腔 。
分流道截面形状有圆形、梯形、U形 等,长度和截面尺寸根据塑料性质和 模具大小而定。
详细描述
斜顶行程的计算需要精确,因为行程过大会导致塑料件顶出时位置不稳定,行程过小则可能导致斜顶无法完全顶 出塑料件。计算斜顶行程时,需要考虑塑料件的高度、模具的开模距离以及斜顶的角度和长度等因素。
斜顶的润滑与排气
总结词
斜顶的润滑和排气是提高模具使用寿命 和确保塑料件质量的重要措施。
VS
详细描述
为了减小摩擦和磨损,提高斜顶的滑动顺 畅度,需要定期对斜顶进行润滑。同时, 为了防止气体在模具腔内积聚,影响塑料 件的成型质量,需要合理设计排气结构, 确保气体能够顺利排出模具。
05 斜顶强脱结构的实例分析
实例一:手机外壳模具设计
总结词
复杂度高、尺寸精度要求高
详细描述
手机外壳模具设计通常采用斜顶强脱结构,因为手机外壳的形状复杂,需要高精度的尺 寸和形状。斜顶强脱结构能够满足高复杂度和高精度要求,确保生产出的手机外壳符合
设计要求。
实例二:汽车零件模具设计
总结词
大型、结构复杂
斜顶强脱结构通过斜向顶出元件的顶 出力,在塑件与型腔表面之间形成分 力,以强制分离塑件。斜顶的倾斜角 度通常为30°~45°,
斜顶强脱结构适用于形状复杂、不易 自动脱落的塑件,尤其在中小型精密 塑件的生产中应用广泛。
基于RE的复杂曲面零件模具的快速设计与制造
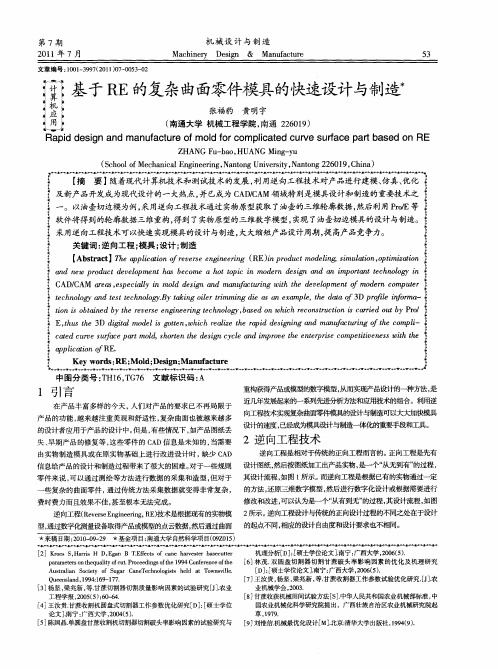
近几 年发展 起来的一系列魁
应用技术的 组合。利用逆
向工程技术实现复杂曲面零件模具的设计与制造可以大大加快模具 设计的速度 , 已经成为模具设计与制造—体化的重要手段和工具。
2逆 向工程技术
逆向工程是相对于传统的正向工程而言的。 正向工程是先有
然后按图纸加工出产品实物 , 是—个“ 从无到有 ” 的过程 , 信息给产品的设计和制造过程带来 了很 大的困难。 对于一些规则 设计图纸,
}软件将得到的轮廓数据三维重构, 得到了实 物原型的三维数字 模型, 现了 实 油壶切边模具的 设计与制造。{
l采用逆向工程技术可以快速 实现模具的设计与制造, 大大缩短产品设计周期 , 高产品竞争力。 提 } 关键词: 逆向工程; 模具; 设计; 制造 2 {
l
【bt c Teplao or ee nien R ) ou oen s utnot i i A sat h a itnfe r g e i Eip dcmdlg i li , iz o i r 】 pc i v se n rg( n r t i, m ao pm a n t
ltnsb i d yh r ee n nen cno , e h he nr tns ai ty r i tn ee r g e i thog b d n i c sui re o o o io a e b t v sei rge l a o w c ro tco ic rd ub P /i y s
设计复杂模具的步骤

设计水平分型面
• 特征—型腔组件—曲面—创建—平整—完 成
• ADTM1 草绘,方向默认 • 使用选取工具,选择环
确定,生成曲面
设计垂直分型面
• 特征—型腔组件—曲面—创建—平整—完 成--MOLD_FRONT草绘,方向默认--使用 选取工具,选择 单个
每天只看目标,别老想障碍
•
3、
。20.1 1.1300: 40:240 0:40Nov -2013-Nov-20
宁愿辛苦一阵子,不要辛苦一辈子
•
4、
。00:4 0:2400: 40:240 0:40Friday, November 13, 2020
• •
积极向上的心态,是成功者的最基本要素 5、
。20.1 1.1320. 11.130 0:40:24 00:40:2 4November 13, 2020
ProE Tutorial Lesson 7
Tornados Zhang
端盖模具设计
• 提要 1、多个零件参照的创建方法 2、利用切除特征创建浇道的方法 3、水线的创建方法 4、滑块的创建方法 5、聚合砂芯的创建方法 6、高级模具体积块的创建方法
端盖的零件设计
• 单位:mmns • Top草绘,Right 右
• 创建如图所示平面
创建滑块
• 插入—模型几何—模具体积块—选择拉伸 工具—MAIN_PARTING_PLN草绘平面, 定向缺省
• 绘制如图草图
确定,退出草图
• 两侧拉伸,一侧5,一侧55
• 特征—型腔组件—特征操作—复制--镜像— 从属—完成—选取—镜像面--完成
创建砂芯
• 插入—模型几何—模具体积块—选择拉伸 工具—MAIN_PARTING_PLN草绘平面, 定向缺省
- 1、下载文档前请自行甄别文档内容的完整性,平台不提供额外的编辑、内容补充、找答案等附加服务。
- 2、"仅部分预览"的文档,不可在线预览部分如存在完整性等问题,可反馈申请退款(可完整预览的文档不适用该条件!)。
- 3、如文档侵犯您的权益,请联系客服反馈,我们会尽快为您处理(人工客服工作时间:9:00-18:30)。
图中热流道线槽,避空 和倒角不处理好很容易弄断电线
弹簧内置较好,省空 间,且部件不易撞坏 (此图仅示意)
斜顶联杆导套的设计,怎样做才能避免加工误差的影响?
返回目录
原身斜顶,优先做左图形式,而不是右图形式
圆弧状联接可以补偿斜顶角 度加工误差,运动顺畅
工艺性不好,易卡死的斜顶 结构(空间狭小时也使用,但 斜顶角度不宜太大)
设计水准的提高可以用“水到渠成”四字来形容。 一般的模具能做到90~95分,复杂模具就不成问题。
本次培训的目的在于介绍经验,让大家少走弯路。希望对大家有帮助。
有不足的地方欢迎大家提出宝贵意见。
技术部 刘鑫 2012.04
课件大纲
本次培训分为以下几个部分,从各个角度阐述模具设计的技巧
第一章.模具设计基本原则 第二章.模具设计技巧 模具结构篇 第三章.模具设计技巧 2d设计篇 第四章.模具设计技巧 3d设计篇 第五章.模具设计技巧 易犯错误篇 第六章.模具设计技巧 经验分享篇
第一章.模具设计基本原则
先谈谈一些模具设计原则,这是总结的一些内容,希望能抛砖引玉,在观念上启发大家。 其中的举例只是说明一些主题,请勿着重于知识点而忽略主题。
1.将生产(加工/装配/注塑)的安全与方便放在第一位。 “顾客就是上帝”不止是服务业的宗旨,也是我们的宗旨。 对于注塑生产,首先要匹配,其次要方便。
R角代替尖角,以CNC代替EDM,省加工时间。 设计时用尽可能少的顶针直径种类,方便钻孔,少换钻头。 易装配如:零件设计拔出用工艺螺丝孔,配模用工艺螺丝孔。 易维护如:油缸顶出系统设计内部油孔代替外接软管,避免泄漏,更好维护。
传统斜导柱杯头有倒扣, CNC加工需要摆斜,优化后 不需摆斜
传统的止口耐磨块槽,CNC 加工需要摆斜,优化后可从 侧面加工,不需摆斜
针对每套模具,还需留意制品要求与取件方式等
使用公司内部标准的好处: 1).可以节省成本。比如很多零件都有库存,再或者便于加工。 2).可靠性。公司内部标准在很大程度上是一些经验积累的产物.都经过验证的,不容 易出错。
客户标准与公司内部标准的对比 以边锁(直身锁/导柱辅助器)为例:
Strack边锁, 一般用于欧洲 模具
DME边锁, 一般用于美国 模具
三片式边锁,
制造成本低,客户 无要求时适用
公司内部标准的另一层含义: 设计要满足加工要求,不能超过机床与刀具范围
本公司10mm深孔钻头,最大钻孔深度为1550mm 孔深度超过此尺寸考虑从两面钻。
3.工艺性(也就是人性化的设计) 主要包含防损,方便操作,弥补误差等几个方面内容。
5.保证强度与寿命
提高模具强度也是为了提高模具寿命。 整体强度不可能无限制提高,要在强度与成本间作权衡。 而局部强度可以设法优化。合理设计撑头,铲鸡加厚或设计反铲,设计整圈止口等都 是强化模具的措施。
优化前
优化后,模具强度更好
模芯中部内凹,用加钢料支撑 的方式防止模芯向中间变形
镶件较高,装配时可能会向外倒,
吊环大小要认真核对 考虑吊模平衡
水、电、油系统的接头都 要能顺利快速接插
易撞坏的部件,要加装保护装置
集水块的水嘴不好接插
水嘴不好接插
最优方案: 水嘴好接插 同时不超出底面板范围
2.遵循客户标准要求。 如果客户没有要求,遵循公司内部标准。
客户标准的重点: 1).模具钢材和配件材质、硬度要求 2).模具与注塑机的接口.(水\电\油接口\码模\KO孔\定位圈\射嘴部位尺寸) 3).模具吊运要求(吊平衡等) 4).模具标准件的品牌.(注意需要原装还是仿制) 5).模具各部分结构的基本做法,如运水要求,滑块\斜顶形式,浇口形式等 6).有时需留意螺纹要求.(紧固螺纹和管螺纹) 7).极少数情况下客户提供的图纸与我们常用的第三视角不同
复杂模具设计技巧
前言
本次培训的内容是复杂模具设计技巧。 复杂可以理解为模具机构和动作复杂,也可以理解为模具大,各种结构共存,设计难 度高。
不管是什么模具,它的本质是多种结构的综合体,而且是一个有机整体。
简单模具和复杂模具,本质区别并不大,也没有一定界限,所以技巧是互通的。 这次提到的大多数技巧都适用于任何模具。 我们应着眼于设计技巧而不是复杂二字。
带杆斜顶,与上页同样原则
万向斜顶座 好
固定式斜顶座 不好
导柱长度的设计: 保护开合模的同时,能够“站 立”,方便钳工作业
滑块分型线在外观的情况下,滑块 需要放在前模修整夹线,可以大大 降低修配难度,缩短周期,避免重 复修模/试模。
压线板的布置:
拐角处电线易翘起,是重点要压的 位置。 否则电线翘起装模时会压坏电线。
设计分型面避空、根部大R角,可以使用 大刀具加工,节省加工、装配时间。
7.换位思考原则 要设计出优秀的模具,一定要多角度考虑。
装配
如果我是装配钳工,怎 样做才能有利于配模与 装配,做事又好又快, 不用返工?
改善措施为设计一个燕尾结构(里大 外小) 此方法还适用于斜顶等
B板与顶针、司筒、斜顶等的配合位做 一段避空,防止零件与模具摩擦面过 多,寿命减短,易烧死。
顶针孔破边, 模具容易损坏。 避免这种设计。
正面镶件槽,做两面 斜度,多次装拆也不 易塌边
6.尽可能降低成本
成本降低就代表着利润增加。 设计时在保证模具强度的前提下,尽可能压缩模具体积。 另外,尽可能用标准件,库存零件与库存呆料,可以节约成本。
所有棱角倒角(特别是孔口/槽 边),避免钳工作业时割伤手。
防呆的概念:即避免装错。导柱偏孔就是一种防呆。
扁顶针的削边防呆 (ቤተ መጻሕፍቲ ባይዱ是防转)
吊模块的偏孔防呆
特例:顶块联杆底部削两 面,不用防呆。如果削一 面防呆反而会装错(上部)
4.结构尽量简单合理,易加工,易装配维护(包括吊运,翻模等) 越简单就越可靠, 节约成本,缩短交期 易加工如:分型面尽量用平面代替曲面,省编程也省加工
顶块或斜顶与杆的防转:可以修改成避空 圆角以避免EDM清角。 (直接倒R的话,杆上要加工,也不太好)
每一处跨越模板之间的电线都 使用小型快速接头.这样拆模板 变得很方便.
关于DME滑块行程锁(PSM式),定位销的安装以右图所示为优, 可以在不拆导轨的前提下将滑块拆出. (销子上有拔出用螺纹,销子用基米螺丝固定.)