面向21世纪造型制芯材料的发展
国内外铸造技术发展现状
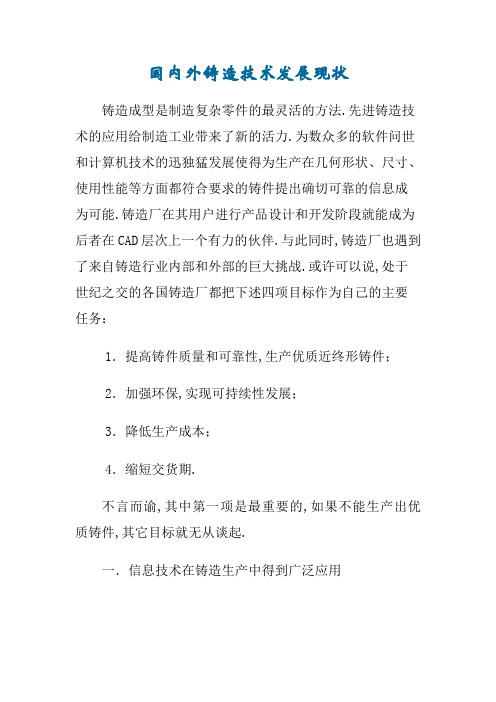
国内外铸造技术发展现状铸造成型是制造复杂零件的最灵活的方法.先进铸造技术的应用给制造工业带来了新的活力.为数众多的软件问世和计算机技术的迅独猛发展使得为生产在几何形状、尺寸、使用性能等方面都符合要求的铸件提出确切可靠的信息成为可能.铸造厂在其用户进行产品设计和开发阶段就能成为后者在CAD层次上一个有力的伙伴.与此同时,铸造厂也遇到了来自铸造行业内部和外部的巨大挑战.或许可以说,处于世纪之交的各国铸造厂都把下述四项目标作为自己的主要任务:1.提高铸件质量和可靠性,生产优质近终形铸件;2.加强环保,实现可持续性发展;3.降低生产成本;4.缩短交货期.不言而谕,其中第一项是最重要的,如果不能生产出优质铸件,其它目标就无从谈起.一.信息技术在铸造生产中得到广泛应用由计算机、网络技术、传感技术、人工智能等所构成的信息技术近年来在铸造生产中得到更为广泛的应用.这正在改变着铸造生产的面貌.可以说,现代铸造技术的主要特征就是将传统的铸造工艺与信息技术溶于一体.铸件充型和凝固模拟在世界各国铸造厂中得到越来越多的实际应用.据不完全统计,仅仅包括MAGMASOFT、AFS SOLIDFICATION SYSTEM3D在内的欧美八种软件共已销售出1200多套.为了优化铸造厂的生产组织和车间设计,铸造工作者已经着手对铸造生产过程进行仿真研究.人们可以通过在屏幕上进行整个铸造厂或其中某一局部的生产,以找出其中的薄弱环节,提出优化生产组织和车间设计的方案.这已在美国、瑞典的一些铸造厂中得到应用,取得了良好结果.德国Laempe公司、Honttinger公司、西班牙Loramandi公司等对其用户的制芯工段也进行三维仿真的实现优化设计.造型、制芯过程的数值模拟正在成为国际铸造界关注的前沿领域之一.清华大学、日本新东工业等对湿型粘土砂紧实过程进行了数值模拟.德国亚琛工业大学、清华大学等正在对射芯过程进行数值模拟.计算机网络技术的发展改变了铸造厂进行管理和经营的方式.例如,美国福特汽车公司的铸造部位于底特律郊区,它通过互联网与其所管辖的分别位于美国、加拿大、英国、澳大利亚、新西兰境内的多家铸造厂进行技术管理、策划扩建或技术革新,并解决各厂的关键技术问题.又如,隶属于法国Valfond集团的位于德国萨尔布吕肯的Halberg铸造厂,通过互联网与其所生产发动机铸件的用户厂、模具供应厂、大学及研究机械进行联系从而大大缩短了新产品开发周期,提高了在市场上的竞争能力.快速原型技术在铸造生产中的应用也有了新的发展.它除了可应用于制造新产品试制用的模样及熔模铸造的蜡模外,还可用于直接造出酚醛树脂壳型、壳芯,它们可直接用来装配成砂型.德国AC Tech公司采用这种直接壳型法与快速原形来为客户生产样品铸件,该公司在接到客户提供的三维CAD数据后,根据铸件尺寸和复杂程度的不同在达到3周时间内为客户提供1~5个铸件.西班牙Loramandi公司推出了砂芯人工视图技术,它采用三维数值化仪建立砂芯的图像,然后由一软件通过云纹法来对所制出的砂芯表面质量进行分析.该系统可自动地识别出不合格的砂芯.德国Honttinger公司也开发了称为砂芯观察Core-Vision的检验砂芯质量的技术,其工作原理较简单:一摄像机在不同方向的光源下对每个砂芯采集最多五个图像.然后计算机对这些图像与合格砂芯标准图像进行对比并指出任何明显的差别表明在砂芯上出现缺陷.二.粘土砂湿型造型设备有新的提高由于粘土砂湿型铸造具有造型材料成本低及造型生产率高等优点,在工业化国家中目前铸件总产量的65%~70%是用粘土砂湿型工艺所生产.德国铸造学会VDG对比了1999年与1994年在德国生产中使用的各类造型线按其生产能力每小时所造砂型体积m3/h的百分率分布表1:表1由表1可见,在德国震压造型正在逐步被其它先进的造型设备所取代.而到1999年垂直分型无箱射压造型、气流一压实造型、空气冲击造型这三类造型线的生产能力之和已占有77%,居于主导地位.在GIFA’99上,Georg Fischer Disa公司展出了其新产品GFD DISA230垂直分型无箱射压造型机,其生产能力为500型/小时无砂芯时.由于增加了机器刚度,其合型精度为≤0.1mm.这样高精度的造型机可以带来以下优点:1.减少对铸件后处理的要求,这意味着降低成本;2.主油缸活塞行程十分精确能生产出薄壁铸件,这意味着减少铸件重量.在展览会上,该公司还展出了GFD Gompac 530系列动态预紧实、高压压实终紧实的水平分型有箱造型机.动态预紧实的特点是砂型紧实度在型腔部位高而朝砂型背面方向逐渐降低.高压压实则反之.将两者相结合就使整个砂型紧实度既高又均匀.该机在动态预紧实方面采用了一项新技术:折线型的升压曲线,其特点是开始升压速率很低,而随后升压速率增大以达到较高的气体压力.这样既能使型砂能很好地充填很深的吊砂部位又能得到有效的预紧实.型砂的终紧实是用柔性压实进行高压压实来完成.目前在世界各国的铸造厂中已由300多套Georg Fischer Disa公司的水平分型冲击造型系统在运行着.HWS公司展出了其气流——压实造型系列化产品,该公司的水平分型气流预紧实、高压终紧实的造型系统也有300多套在世界各国的铸造中运行着.日本新东工业公司早在十年前即推出了以空气冲击预紧实、高压压实终紧实的APK系列水平分型有箱造型机.这种造型机在进行气流预紧实时其余隙中的空气升压速率达到40Mpa/s,因此其实质上属于空气冲击紧实.三.型砂处理向智能化质量控制方向发展为造型机提供性能好而稳定的型砂是生产优质铸件的必要的条件.对用于包括空气冲击、气流一压实、垂直分型无箱射压等造型方法的型砂,其性能有以下要求:1.在紧实率为40%时型砂湿压强度约为200kpa.砂箱尺寸越大,湿压强度也要越高.2.上述推荐的湿压强度应在较低的膨润土含量条件下获得,这意味着型砂应当很好混制即应保证足够的混碾时间.型砂混制是非常重要的,不可忽视.与此同时,建议采用优质特别是耐用性好的膨润土.钙基膨润土应进行苏打活化.3.理想的型砂MB膨润土亚甲基兰膨润土含量不超过9%,含泥量不超过12%.4.在造型机处的紧实率在35%-40%之间.为保证所需的型砂性能,现代化的砂处理系统首先其工艺流程要合理.型砂处理的关键是旧砂处理.旧砂处理的难点是热砂冷却,即将回用砂的温度降到不高于室温10℃,目前,在生产中使用的各种热砂冷却装置,都是利用水的蒸发潜热来带走旧砂所含热量使之降温的.国外近年来在智能化型砂质量控制方面有很大发展,特点是利用计算机辅助对型砂质量进行预防性控制.预防性型砂质量控制的主要点是:砂处理是一循环系统.砂处理系统的基本任务是保持系统砂各组成物料的动态平衡.由于浇注不同的铸件时砂铁比不同,砂芯量及所用芯砂不同,浇注后型砂各组分爱热烧损及混入型砂中的芯砂量也不一样.因此应根据所浇铸件的具体情况来确定新砂、膨润土、煤粉的补加量,并排除适量的旧砂,从而使砂系统的组分保持不变.由于计算机应用的迅速发展,目前国内外的一些铸造厂已实现了按模板所浇注的铸件品种来调整向混砂机加料的配比,由此来实现使系统砂的组分保持动态平衡.为了实现砂处理的闭环控制,对型砂性能进行在线检测是必不可少的重要环节.因为只有既保持砂系统组分的稳定又保证型砂主要性能波动范围窄,才能使型砂质量持久地符合生产优质铸件的要求.经过三十多年的探索,国内外市场已经推出了多种型砂性能在线检测装置,它们的一些共同特点是:检测的项目主要是紧实率和湿强度并采用气动.四.树脂自硬砂工艺及设备日趋完善树脂自硬砂特别适合于单件和中、小批量生产中、大型铸件,机床、矿山、重型、石油、造船、通用等机械行业的铸造厂只需配备相对简单的设备即可组成机械化生产.国外在五十年代末以来,随着树脂砂应用的不断扩大和技术进步,所需用的成套设备日趋齐全和完善,其中包括砂型落砂、砂块破碎、过筛、磁选、再生、除尘、调温、树脂砂混制、砂型紧实、翻箱、起模、上涂料、干燥、合型等工艺设备,以及新砂与旧砂运输、砂型运输等设备.近二十年来,树脂自硬砂在我国铸造生产中逐步得到推广应用.五.冷芯盒制芯用量在增加在成批、大量生产铸件中,三乙胺冷芯盒制芯的芯砂用量最大.1997/98年在德国其用量已达到总芯砂用量的57%,见表2.表2 1997/98年德国批量生产中使用化学粘结剂的分布情况冷芯盒砂芯由于它是常温下在芯盒中硬化后取芯的,所以它可以达到很高的尺寸精度.这种砂芯还可用来进行组芯造型,即装配成精确的砂型,它特别造于近终形铝合金复杂铸件如缸体、缸盖的生产.这种工艺被称精确砂型铸造Precission sand casting.作者1996年先后访问了Ford汽车公司在加拿大境内的温莎铸铝厂及德国联合铝业公司VAW 在Dillingen的铸铝厂,它们都采用这种工艺生产缸体、缸盖.作者1996年访问位于德国萨尔布吕肯的Halberg Guss 铸造厂时,见到该厂用空气冲击造型线生产并为德国大众汽车公司提供的轿车发动机铸铁缸体,其大部分壁厚〈3mm,水套空腔最窄处仅2mm,所用的砂芯也是由冷芯盒法所制.制芯设备近年来有不小的变化.如果说射芯机构本身变化并不大的话,但制芯机的“外围设备”包括去除飞边、砂芯组装、粘结或紧固、浸涂料等设备组合而成.造芯中心的某些工艺过程及工序间运输过去主要采用专用机械手来完成,但近年来已普遍采用通用机器人来实现.现代化的制芯中心是由微机通过可编程控器进行控制的.现代化制芯中心的复杂程度与造型自动线是相当的,有的甚至超出了后者.六.清理设备不断改进对铸件进行表面清理主要采用抛丸清理机.铸造生产对清理设备的主要要求是:1迅速地将铸件内外表面全部清理干净;2零部件的使用寿命长.可以说抛丸清理设备基本上就是围绕这两个要求而不断发展的.由于表面清理是铸件后处理过程的一个重要环节,因此清理不同的铸件要有不同工艺参数.即使对于清理小铸件的连续式抛丸清理机来讲,也需要根据被清理铸件的材质是灰铸铁还是球墨铸铁等等及几何形状来设定铸件在抛丸区内逗留的时间和抛丸量等参数,以便使抛丸清理过程达到最优化.对于一些专用高效抛丸清理机,工艺参数的设定就更重要了.以一种水平转盘式抛丸清理机为例,在清理铸件时,机械手带动缸体自转的转速是可变的.缸体的顶端和底端在通过抛射区时其自转转速很低甚至可以暂停旋转,以便使弹丸射流有充分时间将铸件复杂的内腔粘砂抛打干净.抛丸清理设备主要由抛丸器、丸砂分离系统、除尘系统、铸件运载系统及弹丸循环系统五个部分组成.前三者大都采用通用部件,弹丸循环系统则由螺旋输送机或振动输送机及斗式提升机组成,大都也属定型部件.因此,开发一种新的抛丸清理设备的一个主要任务就是研制其铸件运载系统.只有采用完全干净的优质弹丸,才能实现抛丸机在技术上与经济上的最优化,弹丸中含砂增多将降低抛丸效率并急剧增加机器本身的磨损.因此丸砂分离系统是抛丸清理设备中十分重要的组成部分.应按照回用的弹丸中含砂量的多少,采用不同结构的分离系统如风选十磁选,二次风选,风选.七.结束语近十年来铸造技术有重大的发展,世际之交的各国铸造行业在不同程度上遇到来自行业内部和外部的巨大挑战.积极地将信息技术应用到铸造生产中看来是铸造厂使自己能在21世纪激烈的竞争中生存和发展的一个关键措施.。
c1x 芯片工艺

c1x 芯片工艺1.引言1.1 概述概述部分的内容:芯片工艺是指通过一系列工艺步骤将晶体硅上的电子元件按照设计要求逐步制造出来的过程。
随着科技的快速发展,芯片工艺已经成为信息产业和高科技领域的重要基础。
芯片工艺的发展不仅推动了计算机、通信、嵌入式系统等领域的飞速发展,也在电子产品的微型化和智能化方面发挥着重要作用。
芯片工艺的核心目标是实现更小、更快、更强的芯片。
通过不断优化制造工艺,芯片的功能不断提升,同时尺寸不断缩小,性能得到提高。
芯片工艺的关键技术包括晶圆制备、光刻、沉积、清洗等多个方面,每一个步骤都需要精密的设备和严格的工艺流程来完成。
目前,芯片工艺已经进入了纳米级别,制造出了纳米级别的芯片。
这些芯片具有更高的集成度和更快的运算速度,已经成为现代科技领域的核心组成部分。
随着新材料、新工艺的不断涌现,芯片工艺也在不断创新,未来的芯片工艺将会更加精细和高效。
本篇文章将介绍芯片工艺的概述、发展历程以及对未来的展望,希望能为读者提供一个全面了解和认识芯片工艺的视角,同时也展示出芯片工艺在现代社会中的重要性和影响力。
1.2 文章结构文章结构部分的内容应该包括以下信息:文章结构部分旨在介绍整篇文章的组织结构,通过明确的文章结构让读者能够更好地理解和阅读文章内容。
本文按照以下几个部分进行组织:引言部分:本部分主要概述了整篇文章的背景和目的。
首先,我们会介绍C1X芯片工艺的重要性和广泛应用的背景,使读者对C1X芯片工艺有一个初步的认识。
接着,我们将详细阐述本文的结构和目标,即通过研究C1X芯片工艺的概述、发展历程和未来展望,深入探讨芯片工艺的关键问题。
正文部分:本部分是本文的核心内容,主要分为两个小节。
首先,我们将详细介绍C1X芯片工艺的概述,包括其基本原理和特点。
我们将探讨C1X芯片工艺在当前市场的地位和应用领域,并举例说明其在实际应用中的重要性和优势。
其次,我们将回顾C1X芯片工艺的发展历程,包括其起源、发展阶段和关键里程碑事件。
面向21世纪的我国药芯焊丝制造技术的研究与发展趋势

锰 钢 修 复 药 芯 焊 丝 和 列 车 车 轮 堆 焊 药 芯 焊 丝 等 品 造 技 术 进 人 了 新 的 阶 段 。 以 “ T 与 2 W O 1世 纪 ”
种 。但 由 于 设 备生 产 能 力 极 小 ,不 能 大 批 量 生 产 以 为 背 景 的 我 国药 芯 焊 丝 发 展 进 人 第 三 阶段 。 我 国经 及 其 他 原 因 ,该 项 目没 有 巩 固 下 来 。 在 北 京 地 区 , 济 将 全 方 位 融 人 国际 经 济 体 系 ,努 力 学 习 和 灵 活 应
— —
药 芯 焊 丝 研 究 与 生 产 的专 家 、教 授 和 生 产 企 业 公 司 “ 密 接 触 ” 亲 ;第 一 次 在 展 览 会 上 见 到 了 由瑞
的 同 行 们 ,为此 付 出 了 巨大 的努 力 ,为 我 国药 芯 焊 典 万 莎 公 司 推 出 的 药 芯 焊 丝 生 产 线 样 机 和 其 他 国外
开 局 之 年 ,同 时 又 迎 来 “ 七 届 北 京 ・ 森 焊 接 与 第 埃
近 1 5年来 ,经 过 国 内 焊 接 工 作 者 不 断 地 探 索
7年 “ 一届 北 京 与实 践 ,我 国药 芯 焊 丝 得 到 了较 为 迅 速 的 发展 。 但 第
维普资讯
面 向 21 - e的 我 国 药 芯 焊 丝 t .  ̄g
制 造 技 术 的 研 究 与 发 展 趋 势
北 京英 世 恒瑞 焊业 有 限公 司 (0 4 1 110 ) 杨 建 东 王 有 平
迈 人 新 世 纪 ,当 我 们 回顾 起 我 国 药 芯 焊 丝 几 十 北 京 顺 利 召 开 以来 ,使 国 内 众 多 焊 接 同 行 第 一 次 看 年 来 不 平 凡 的 发展 历 程 ,不 少 从 事 中 国焊 接 新 材 料 到 如 此 盛 大规 模 的 展 览 会 ;第 一 次 与 国 外 著 名 焊 接
半导体材料发展史
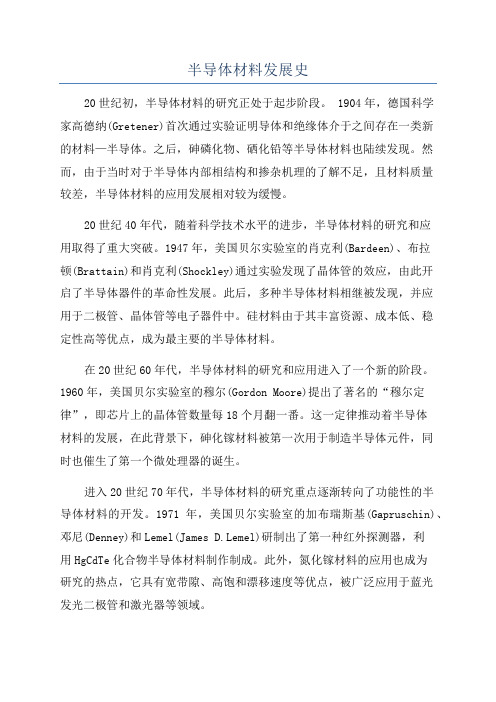
半导体材料发展史20世纪初,半导体材料的研究正处于起步阶段。
1904年,德国科学家高德纳(Gretener)首次通过实验证明导体和绝缘体介于之间存在一类新的材料—半导体。
之后,砷磷化物、硒化铅等半导体材料也陆续发现。
然而,由于当时对于半导体内部相结构和掺杂机理的了解不足,且材料质量较差,半导体材料的应用发展相对较为缓慢。
20世纪40年代,随着科学技术水平的进步,半导体材料的研究和应用取得了重大突破。
1947年,美国贝尔实验室的肖克利(Bardeen)、布拉顿(Brattain)和肖克利(Shockley)通过实验发现了晶体管的效应,由此开启了半导体器件的革命性发展。
此后,多种半导体材料相继被发现,并应用于二极管、晶体管等电子器件中。
硅材料由于其丰富资源、成本低、稳定性高等优点,成为最主要的半导体材料。
在20世纪60年代,半导体材料的研究和应用进入了一个新的阶段。
1960年,美国贝尔实验室的穆尔(Gordon Moore)提出了著名的“穆尔定律”,即芯片上的晶体管数量每18个月翻一番。
这一定律推动着半导体材料的发展,在此背景下,砷化镓材料被第一次用于制造半导体元件,同时也催生了第一个微处理器的诞生。
进入20世纪70年代,半导体材料的研究重点逐渐转向了功能性的半导体材料的开发。
1971年,美国贝尔实验室的加布瑞斯基(Gapruschin)、邓尼(Denney)和Lemel(James D.Lemel)研制出了第一种红外探测器,利用HgCdTe化合物半导体材料制作制成。
此外,氮化镓材料的应用也成为研究的热点,它具有宽带隙、高饱和漂移速度等优点,被广泛应用于蓝光发光二极管和激光器等领域。
到了20世纪80年代,半导体材料逐渐进入集成电路阶段。
1984年,美国IBM公司的潘尼[1]开发出集成电路中用于存储信息的随机存储器(SRAM),使得集成电路的存储容量大大提高。
同时,砷化镓材料的研究也取得了重要突破,首次在低温下制备出了高质量的砷化镓薄膜。
《材料与社会》参考论文:浅谈材料在人类社会发展过程中的作用

浅谈材料在人类社会发展过程中的作用材料是人民生活水平提高不可或缺的物质基础,是开发能源和治理环境污染的重要保障。
在人类历史中,生产材料的更新换代推动了人类社会的变革,促进了人类文明的发展。
在一轮又一轮的技术革命中,材料作为主导力量一次又一次推到着科技文明的发展。
18世纪中叶发生于英国的第一次科技革命,为人类社会的发展掀开了新的篇章。
这起遍及欧洲和北美国家的技术革命以钢铁和铜等新材料的开发为基础,以纺织机械革新为起点,以蒸汽机的广泛使用为标志,实现了工业生产从手工工具到机械化的转变,使以机器为主体的工厂制度代替了以手工技术为基础的手工工场,从而把人类带进了蒸汽时代。
随后,兴起于19世纪末到20世纪中叶的第二次技术革命,以石油开发和新能源广泛使用为突破口,以电的发明和广泛应用为标志,大力发展飞机、汽车和其他工业。
支持这个时期产业革命的仍然是新材料开发,如合金钢、铝合金以及各种非金属材料的发展。
而起于20世纪中叶的第三次技术革命更是以原子能应用为标志,实现了合成材料、半导体材料等大规模工业化、民用化。
以民航机的发展历程为例,油耗逐年下降的可喜变化一方面是设计与机型的扩大所致,另一方面就在于材料的不断改进,而PWA客机每减重一千克,就多赢利104美元。
到如今,在航空航天领域,飞机、导弹、卫星与飞船的发展,材料依然是关键。
战斗机性能的提高三分之二靠材料;发动机性能的提高,材料占二分之一。
对空间飞行器来说,由于材料的改进,收益更为显著。
然而,材料的开发不仅推动了技术革命的发展,还给农业生产带来了新的保障。
在19世纪以前,农业上所需氮肥的来源主要来自有机物的副产品,如粪类、种子饼及绿肥。
随着农业的发展,对氮肥的需求量在迅速增长。
直到1909年,著名德国物理化学家哈伯(Haber) 利用锇作为催化剂合成了氨,使之成为促进农作物生长的重要肥料。
另外,1940年,除草剂的发明成功,配合采取灌溉、农膜育苗及机械化作业等措施,同样使粮食大幅度增产,使农民的生活得到极大改善。
21世纪新型材料

高强高模纤维目前,尼龙和涤纶的拉伸断裂强力仅为其理论值的约5%。
今后开发的高聚物纤维,拉伸断裂强力将为其理论值的40%,抗拉模量将为其理论值的90%。
随着高聚物技术的发展以及有机与无机化合物结合的进展,极有可能开发出达40%理论强力的纤维。
开发这种纤维的瓶颈是成本。
这种纤维将适用于要求高强力、轻质量的各种设备。
高耐热纤维人们致力于开发能够在450℃下连续使用的耐热高聚物材料。
具有与常规高聚物纤维等同的形状稳定性和加工性能以及很高耐热能力的纤维将会出现。
它们的应用领域将包括过滤器、高温工艺和太空开发等。
超轻纤维目前已经开发出一些轻质纤维,如:低密度的丙纶纤维和涤纶多孔(孔的比例为40%)纤维。
人们预计今后将会开发出用于老年服装的超轻和具有良好保暖性能的纤维。
开发这种纤维要以新技术为基础,即在进行变形加工的工艺过程中,不会使孔的部分断裂。
高导电纤维在21世纪,人们将开发出在室温下与铜的导电性能相当的、用于电料和电子材料的高聚物纤维。
开发这类纤维的关键是开发这种高聚物的回收技术。
可生物降解纤维目前,作为重要可生物降解纤维的聚乳酸纤维还没有足够的结果来证明其实际性能,其耐热性能尚需进一步提高。
另外,仍需在强力保持性能和可生物降解性能之间加以权衡。
因此,这种纤维的应用有很大局限性。
而开发在一定时间内能够降解的可生物降解纤维将是解决该问题的一种答案。
新纤维素纤维今后将会出现新型再生纤维素纤维。
它们将以阔叶树、竹子和建筑材料碎片为原料,并充分利用生物技术。
生物纤维通过将蜘蛛丝成功地溶解,Wyoming大学已经克隆出蜘蛛丝的基因。
蜘蛛丝具有化学纤维不可比拟的良好性能。
将蜘蛛丝基因转移到蚕体内,蚕将不再生产蚕丝,而使生产蜘蛛丝变为现实。
蜘蛛丝极其结实,其断裂伸长率为35%。
具有传感和康复功能的纤维人们将开发具有传感功能的温湿度调节材料、康复用神经刺激材料和肌肉力量支持类服装。
今后还将开发出具有传感功能的睡衣,用来检测温度和相对湿度,以防止那些丧失温、湿度感觉的老年人受到类似“低温烧伤”的伤害。
我国精密加工的现状及发展趋势

我国精密加工的现状及发展趋势内容摘要:近十年来,美国十分注重发展精密热加工和提高性能一体化技术。
如:铝锂合金粉制件精密热成形可使零件比刚度提高30%;碳化硅/铝复合材料可使零件的比刚度提高30%一75%;单晶叶片精铸可以提高涡轮温度55℃、节省燃料10%;快速凝固粉末层压式涡轮叶片,可使发动机涡轮温度提高220℃、油耗降低8.4%、飞机起飞质量降低7.4%,发动机推重比提高30%一50%。
发展精密热加工技术,并与提高零部件性能研究一体化,符合我国国防科技发展对关键基础加工技术研究所提出的要求。
正文:一、精密和超精密加工的概念与范畴通常,按加工精度划分,机械加工可分为一般加工、精密加工、超精密加工三个阶段。
目前,精密加工是指加工精度为1~0.1?;m,表面粗糙度为Ra0.1~0.01?;m的加工技术,但这个界限是随着加工技术的进步不断变化的,今天的精密加工可能就是明天的一般加工。
精密加工所要解决的问题,一是加工精度,包括形位公差、尺寸精度及表面状况;二是加工效率,有些加工可以取得较好的加工精度,却难以取得高的加工效率。
精密加工包括微细加工和超微细加工、光整加工等加工技术。
传统的精密加工方法有砂带磨削、精密切削、珩磨、精密研磨与抛光等。
a.砂带磨削是用粘有磨料的混纺布为磨具对工件进行加工,属于涂附磨具磨削加工的范畴,有生产率高、表面质量好、使用范围广等特点。
b.精密切削,也称金刚石刀具切削(SPDT),用高精密的机床和单晶金刚石刀具进行切削加工,主要用于铜、铝等不宜磨削加工的软金属的精密加工,如计算机用的磁鼓、磁盘及大功率激光用的金属反光镜等,比一般切削加工精度要高1~2个等级。
c.珩磨,用油石砂条组成的珩磨头,在一定压力下沿工件表面往复运动,加工后的表面粗糙度可达Ra0.4~0.1?;m,最好可到Ra0.025?;m,主要用来加工铸铁及钢,不宜用来加工硬度小、韧性好的有色金属。
d.精密研磨与抛光通过介于工件和工具间的磨料及加工液,工件及研具作相互机械摩擦,使工件达到所要求的尺寸与精度的加工方法。
中国芯的发展历程

中国芯的发展历程中国芯是指中国自主研发和生产的集成电路芯片。
中国芯的发展历程可以追溯到上世纪50年代末60年代初。
本文将从中国芯的起步阶段、发展阶段和现阶段分别进行阐述。
一、起步阶段(上世纪50年代末60年代初)中国芯的起步阶段可以追溯到上世纪50年代末60年代初,当时中国刚刚建立起自己的计算机科学体系,并开始进行集成电路的研究。
上海华东计算技术研究所、北京计算机研究所等单位纷纷成立了集成电路实验室,开始进行芯片的研发工作。
然而,由于当时国内技术和设备水平相对较低,加之受制于国际环境,中国芯的起步阶段进展较为缓慢。
二、发展阶段(上世纪70年代-21世纪初)上世纪70年代至80年代,中国芯进入了发展阶段。
中国政府高度重视集成电路产业的发展,开始大力投资和支持相关研究和生产。
1973年,中国自主研制成功了第一台“红旗”系列计算机,标志着中国芯在计算机领域取得了突破。
80年代初,中国成立了第一个芯片设计研究所——北京中芯国际集成电路设计有限公司,开始进行芯片设计和生产。
此后,中国陆续成立了一批集成电路设计和制造企业,如华为、中兴通讯等。
然而,在发展过程中,中国芯也面临着一系列的挑战。
首先,技术水平仍然相对较低,与国际先进水平存在一定差距。
其次,市场竞争激烈,国内企业难以与国际巨头竞争。
此外,缺乏核心技术和自主知识产权也是制约中国芯发展的瓶颈。
三、现阶段(21世纪至今)21世纪初,中国芯进入了新的发展阶段。
中国政府再次提出了促进芯片产业发展的战略,将其作为国家战略进行推进。
2000年,中国启动了“千分之一”大规模集成电路设计制造项目,旨在培育和发展国内集成电路产业。
2001年,中国成功研制出第一颗8位全定制芯片,标志着中国芯在全定制芯片领域取得突破。
随着技术的发展和政策的支持,中国芯在近年来取得了长足的进展。
中国的集成电路设计和制造企业逐渐崭露头角,一些企业在国内外市场上取得了重要的地位。
例如,华为和中兴通讯等企业在全球通信领域占据重要地位,展现了中国芯的实力。
21世纪新材料发展趋势

新材料发展趋势冶金建筑研究院冶金与焊接材料专家教授级高工唐伯钢21世纪将是科技高速发展的世纪。
焊接材料就世界范围而言,一方面在21 世纪前期,仍将在目前传统焊材产品框架内继续增长与改进;另一方面,已开始出现某些重大变革的前奏,这种变革可能将在21 世纪20 年代左右,对焊材产业将产生重大影响。
1、适应焊接自动化和高效焊接的潮流进行产品结构调整21世纪前期,我国钢材的品质将随着冶金工艺的进步,特别是“纯洁化、微合金化和控轧控冷”等技术在各重点钢铁企业的推广,将使各种用焊接的钢材可焊性更好,不易产生焊接裂纹并且可以采用大线能量焊接,因而将在目前传统焊接技术框架内,全力追求焊接自动化和高效焊接。
我国造船系统已率先提出,到2005 年我国船厂的焊接高效化率要达到80% 以上,其中CO 2 气保护焊的应用率达到55% ,焊接机械化自动化率达到70% 左右。
预测到2005 年,我国消费的焊接材料中,可能焊条占60% — 70% 、气保护实芯焊丝约占20% ,药芯焊丝占2% — 5% ,埋弧焊用焊丝和焊剂占10% — 12% 。
因此我国的焊材产业,应适应消费需求变化的潮流,进行产业结构的调整。
在气保护焊用实心焊丝、药芯焊丝、埋弧焊丝和烧结焊剂等方面形成规模效益和高质量产品。
2、气保护实心焊丝向低飞溅高性能方向发展CO2气保护实心焊丝,影响产品质量有两个关键问题,一是焊丝的化学成分,二是镀铜和绕卷。
近年来,为降低CO 2 焊的飞溅和提高焊缝金属的性能,国外对焊丝的化学成分作了大量研究工作,包括在标准的较宽的成分范围内,规定较窄的内控标准及加入各种微量合金元素,取得了降低焊接飞溅量50% 以上,减少焊接烟尘量25% 以上的好成绩。
因此在继续关注焊丝生产规模效益,希望重点企业建立“年产 1 — 3 万t 以上镀铜焊丝生产线”的同时,必须关注焊丝成分的改进,期望有关钢厂与有关重点焊丝生产企业合作进行这方面的工作。
3、药芯焊丝向“宽电流幅度”、“低尘低飞溅”、“快速焊”的方向发展4、埋弧焊用焊丝和焊剂向高效率多品种方向发展埋弧焊用焊丝,发展了低锰、中锰、高锰的系列产品和与锰硅相配合的加入不同镍、钼、铬含量的多种产品,并在此基础上,向“纯净化、微合金化”的方向发展。
半导体技术的发展现状与趋势
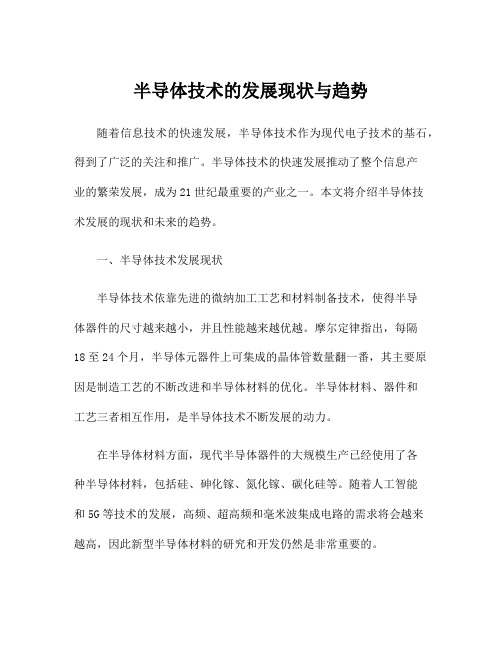
半导体技术的发展现状与趋势随着信息技术的快速发展,半导体技术作为现代电子技术的基石,得到了广泛的关注和推广。
半导体技术的快速发展推动了整个信息产业的繁荣发展,成为21世纪最重要的产业之一。
本文将介绍半导体技术发展的现状和未来的趋势。
一、半导体技术发展现状半导体技术依靠先进的微纳加工工艺和材料制备技术,使得半导体器件的尺寸越来越小,并且性能越来越优越。
摩尔定律指出,每隔18至24个月,半导体元器件上可集成的晶体管数量翻一番,其主要原因是制造工艺的不断改进和半导体材料的优化。
半导体材料、器件和工艺三者相互作用,是半导体技术不断发展的动力。
在半导体材料方面,现代半导体器件的大规模生产已经使用了各种半导体材料,包括硅、砷化镓、氮化镓、碳化硅等。
随着人工智能和5G等技术的发展,高频、超高频和毫米波集成电路的需求将会越来越高,因此新型半导体材料的研究和开发仍然是非常重要的。
在半导体器件方面,CMOS技术是目前最常用的半导体器件技术,以其高密度、低功耗等优越的性能而被广泛应用。
随着新模拟和多媒体应用的需求增加,各种新型CMOS器件也得到了广泛的关注。
比如如今半导体领域发展趋势之一是MEMS,其通过微机械加工在芯片上制造了微观的机械元件,可用于传感器、加速度计、惯性导航等方面。
在半导体工艺方面,微纳加工工艺是现代半导体加工的主要手段,这种工艺将光刻、腐蚀、镀膜、离子注入、退火等多种步骤有机地结合起来。
各种新型的工艺流程的出现为半导体器件的制造提供了新的技术保障,比如CVD、ALD等化学气相沉积技术,可以制造出更高性能、特殊结构的器件,而纳米加工技术则可以把器件的尺寸缩小到更细微的尺度,从而增强器件的性能,进而使得芯片的计算速度更高。
二、半导体技术发展趋势(1)新型半导体材料的快速发展半导体材料是半导体器件发展的基础。
随着科学技术的发展,人们不断寻找、开发新型材料,以满足不同领域的需求。
例如,氮化镓、碳化硅、氮化铝等材料具有其它材料所不具备的优越性能,因此它们被广泛用于高功率电子和高频电子器件中。
芯片制造的技术发展和趋势

芯片制造的技术发展和趋势【绪论】芯片制造是当今信息技术中最基础的领域之一,它的重要性在于芯片的性能和质量决定了计算机和通信设备性能和稳定性,更进一步说,也影响了整个信息及科技产业的发展。
本文旨在梳理芯片制造技术的发展历程、目前的进展和未来趋势。
【芯片制造技术的发展历程】从20世纪50年代开始,芯片制造技术就逐步发展,经历了多个阶段:一、晶体管单元元件阶段在这一阶段,晶体管的单元元件是由通过化学腐蚀和数控机床切割硅晶体制成的,元件面积很小、型号很少,每张晶圆的单位单元很少。
所以,它们只能制造出非常简单的数字电路,占据极少的市场份额。
1960年,晶体管单元元件技术逐步被体延式集成电路技术所取代。
二、集成电路阶段20世纪60年代初,随着集成电路技术成熟,芯片尺寸和复杂度逐渐增加。
尤其是在1970年代中期,芯片中的晶体管数量超过了5000个,技术水平跨入了大规模集成电路时代。
人们开始采用“光刻-刻蚀”工艺,提高了芯片的制造效率和良率。
1980年以后,微处理器技术的快速发展加速了集成电路技术的进步。
三、超大规模集成电路阶段20世纪90年代开始,出现了超大规模集成电路技术,它的特点是单个芯片上能集成上千万个晶体管。
这是由于微电子学技术的发展和半导体材料技术的进步所带来的。
此外,减少线路电阻、移动通信革命等也为超大规模集成电路的发展打下了基础。
四、先进的微纳工艺进入21世纪后,芯片制造技术一直在向更加微小化、更加先进的方向发展。
微纳工艺成为当今芯片制造技术的关键,其主要特点包括:高纯硅材料、心理制作、立体构筑和高分辨率等。
这一阶段的重要技术包括了一系列先进的技术,如158nm光刻技术、多晶硅薄膜材料、深紫外(DUV)光刻技术、硬掩模技术、双重抛光技术等,这些技术的出现都极大地提高了芯片的制造质量和生产效率。
【目前的趋势及未来展望】目前,芯片制造行业面临一个新的环境:1.芯片制造难度日益增大;2.产生废弃物的量日益增大;3.晶圆直径从前的8英寸发展到今天的12英寸/300毫米以上,设备规模、单片芯片面积等的增长使得设备成本和投资增加;4.更加严格的能源消耗限制。
国产芯片发展史 -回复

国产芯片发展史-回复中国芯片产业的发展史可以追溯到上世纪六十年代,中国刚刚建国的时候。
那个时候,中国面临经济和科技的发展困境。
这导致了中国政府提出了自力更生和科技独立的重要战略,尤其是在核武器和航天领域。
在这种背景下,中国芯片产业开始了自己的发展历程。
首先,我将从上世纪六十年代开始,介绍中国芯片产业的初步发展。
当时中国政府意识到芯片是现代电子技术的核心,为实现科技独立,决定自主研发和生产芯片。
1964年,中国成功研制出第一批二极管和晶体管。
这一进展为中国芯片产业的发展奠定了基础。
接下来,我将谈谈中国芯片产业在上世纪七十年代取得的进展。
上世纪七十年代,中国加强了对芯片产业的投资和研发工作。
1973年,中国成功研制出了自己的第一款集成电路,这标志着中国芯片产业进入了自主设计开发的阶段。
此后,中国开始了芯片产业链的构建,包括设计、制造和封装测试等环节。
然而,由于长期受制于技术和市场等方面的限制,中国芯片产业发展缓慢。
在80年代,中国经历了改革开放的浪潮,这为芯片产业的发展创造了新的机遇。
政府鼓励引进外国技术和设备,并鼓励国内企业进行技术创新。
这为中国芯片产业的快速发展提供了契机。
在90年代,中国芯片产业进一步发展,特别是在设计和制造方面取得了重要突破。
1996年,中国成功研发了自己的第一款高性能处理器,这是中国芯片产业的里程碑。
此外,中国还成立了一些先进制造设备和材料的研究机构,以提高芯片制造的质量和效率。
进入21世纪,中国芯片产业迎来了一个全新的发展阶段。
中国政府进一步加大了对芯片产业的支持力度,并提出了自主创新的重要战略。
2001年,中国成立了中芯国际,这是中国第一个具备世界先进水平的集成电路制造企业。
中芯国际的成立填补了中国芯片制造的空白,标志着中国芯片产业实现了从设计到制造的重要突破。
自那时以来,中国政府不断加大对芯片产业的投资力度,同时支持和鼓励国内企业进行技术研发和创新。
在中国政府的支持下,中国芯片产业取得了长足的发展。
面向21世纪的反坦克弹药

面向21世纪的反坦克弹药现代战争中,坦克已成为地面部队的主要突击装备。
随着坦克装甲技术的日新月异的发展,反装甲弹药已成为现代战争中用得较多的弹种之一。
20世纪70年代后期至90年代,各国研制装备的坦克已不是一味地在追求增加装甲厚度上下功夫,大都采用防护能力强的间隙装甲、屏蔽装甲、复合装甲和爆炸反应装甲,不但减轻了坦克重量,而且有效地提高了抗弹能力。
因此,21世纪坦克战对反坦克武器弹药提出了更高的要求,只有提高反坦克弹药的威力,改进战斗部装药结构,采用探测、导引和抗干扰的高新技术,发挥多种反坦克弹药的作用,才能对付铺天盖地来犯的坦克集群。
为了对付现已装备先进防护装甲的主战坦克,世界很多国家都在致力于研制和装备各种先进装药结构的反坦克弹药。
众所周知,21世纪主战坦克的装甲防护技术将会提高到一个新的水平,反坦克武器弹药也将随之高速发展。
新型战斗部技术和末制导技术的发展和应用,将使反坦克武器弹药的性能获得新的突破,这是21世纪反坦克武器弹药发展的重要方向。
努力提高反坦克破甲弹的威力为了提高空心装药的破甲威力,当前主要的途径是采用爆炸能量更高的炸药装药,战斗部前端加探杆以改善炸高,增大装药直径以增加装药量以及改进装药结构等。
20世纪50年代,美国在反坦克破甲战斗部中采用的装药主要是B炸药,60年代,改用了70%奥克托金和30%梯恩梯组成的奥克托尔混合炸药,使炸药装药的爆速由7900m/s提高到8377m/s。
70年代,又采用了LX-14高聚物粘结炸药,其爆速已达8837m/s。
LX-14的爆轰压比B炸药提高了22.3%,比奥克托尔提高了8.5%,加之采用先进的装药工艺,在提高装药密度的同时,提高装药密度的均匀性,减少药型罩的壁厚差,从而大幅度提高了战斗部的破甲深度,使战斗部的威力显著提高。
例如,美国”蝮蛇”反坦克火箭破甲战斗部,弹径70mm,装0.425kgLX-14高聚物粘结炸药,破甲深度400mm,比美国M28式88.9mm反坦克火箭弹破甲战斗部弹径(88.9mm)小,装药量(装0.870kgB炸药)少,其破甲深度却提高近40%。
集成光学芯片技术的发展与应用

集成光学芯片技术的发展与应用随着信息技术的发展和数据通信的日益普及,人们对更高速和更多容量的通信方式和数据存储方式的需求也越来越大。
为此,集成光学芯片技术应运而生,成为满足这些需求的重要途径之一。
本文将介绍集成光学芯片技术的基础概念、发展历程以及相关应用。
一、集成光学芯片技术的基础概念集成光学芯片技术,顾名思义,指将光学芯片集成到一个芯片上的技术,从而实现多个功能的集成化。
这些光学功能包括光源、调制器、耦合器、分束器、滤波器、放大器等。
通过集成,可以实现高速数据传输、节约空间、降低成本等效果。
集成光学芯片是一种微观器件,其结构复杂、制造难度大,需要应用多种高科技生产工艺,包括微影、离子注入、薄膜沉积、光刻等。
此外,由于集成光学芯片直接使用光学信号进行通信,因此对环境的要求也比较高,工作需要在光纤、光源、FPCB等器件的支持下完成。
二、集成光学芯片技术的发展历程集成光学芯片技术的历史可以追溯到上世纪70年代。
1970年美国Bell实验室的Miller首先提出将半导体材料应用于光学器件中的研究。
随着半导体技术的飞速发展,越来越多的光学器件采用半导体材料代替传统的玻璃等材料,这为集成光学芯片技术的发展奠定了基础。
20世纪80年代初,美国AT&T贝尔实验室的Alferness博士和日本NEC公司的Suzuki博士分别研制出了惠普波导和电离DBR 激光器。
这两个发明标志着集成光学芯片技术开始进入实用化阶段。
此外,20世纪90年代以来,欧洲、亚洲等地的许多研究机构也分别推出了各自的集成光学芯片方案。
21世纪,随着科技和资本的全球化,集成光学芯片技术开始进入高速发展期。
在美国,Cisco、Juniper、Alcatel-Lucent等公司相继推出了各自的100G/400G产品;在中国,华为、中兴通讯、烽火通信等国内公司也相继推出了相关产品。
这些产品的推出,不仅使得集成光学芯片技术在通信领域得以广泛应用,同时也进一步促进了集成光学芯片技术的发展。
造型材料
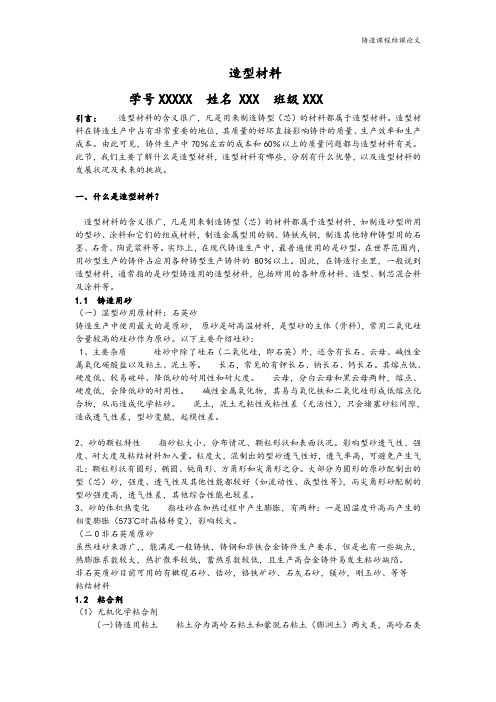
造型材料学号XXXXX 姓名 XXX 班级XXX引言:造型材料的含义很广,凡是用来制造铸型(芯)的材料都属于造型材料。
造型材料在铸造生产中占有非常重要的地位,其质量的好坏直接影响铸件的质量、生产效率和生产成本。
由此可见,铸件生产中70%左右的成本和60%以上的质量问题都与造型材料有关。
此节,我们主要了解什么是造型材料,造型材料有哪些,分别有什么优势,以及造型材料的发展状况及未来的挑战。
一、什么是造型材料?造型材料的含义很广,凡是用来制造铸型(芯)的材料都属于造型材料,如制造砂型所用的型砂、涂料和它们的组成材料,制造金属型用的钢、铸铁或铜,制造其他特种铸型用的石墨、石膏、陶瓷浆料等。
实际上,在现代铸造生产中,最普遍使用的是砂型。
在世界范围内,用砂型生产的铸件占应用各种铸型生产铸件的80%以上。
因此,在铸造行业里,一般说到造型材料,通常指的是砂型铸造用的造型材料,包括所用的各种原材料、造型、制芯混合料及涂料等。
1.1 铸造用砂(一)湿型砂用原材料:石英砂铸造生产中使用最大的是原砂,原砂是耐高温材料,是型砂的主体(骨料),常用二氧化硅含量较高的硅砂作为原砂。
以下主要介绍硅砂:1、主要杂质硅砂中除了硅石(二氧化硅,即石英)外,还含有长石、云母、碱性金属氧化碳酸盐以及粘土、泥土等。
长石,常见的有钾长石、钠长石、钙长石。
其熔点低、硬度低、较易破碎、降低砂的耐用性和耐火度。
云母,分白云母和黑云母两种,熔点、硬度低,会降低砂的耐用性。
碱性金属氧化物,其易与氧化铁和二氧化硅形成低熔点化合物,从而造成化学粘砂。
泥土,泥土无粘性或粘性差(无活性),只会堵塞砂粒间隙,造成透气性差,型砂变脆,起模性差。
2、砂的颗粒特性指砂粒大小、分布情况、颗粒形状和表面状况。
影响型砂透气性、强度、耐火度及粘结材料加入量。
粒度大,混制出的型砂透气性好,透气率高,可避免产生气孔;颗粒形状有圆形、椭圆、钝角形、方角形和尖角形之分。
大部分为圆形的原砂配制出的型(芯)砂,强度、透气性及其他性能都较好(如流动性、成型性等),而尖角形砂配制的型砂强度高,透气性差,其他综合性能也较差。
覆膜砂铸造材料及工艺知识大全
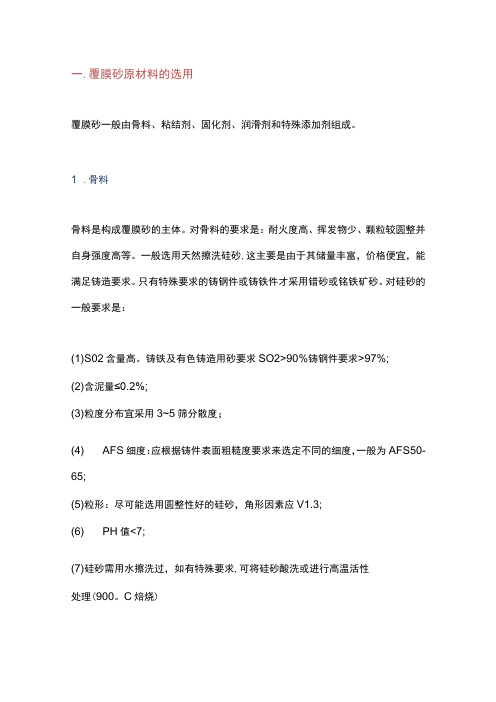
一.覆膜砂原材料的选用覆膜砂一般由骨料、粘结剂、固化剂、润滑剂和特殊添加剂组成。
1 .骨料骨料是构成覆膜砂的主体。
对骨料的要求是:耐火度高、挥发物少、颗粒较圆整并自身强度高等。
一般选用天然擦洗硅砂,这主要是由于其储量丰富,价格便宜,能满足铸造要求。
只有特殊要求的铸钢件或铸铁件才采用错砂或铭铁矿砂。
对硅砂的一般要求是:(1)S02含量高。
铸铁及有色铸造用砂要求SO2>90%铸钢件要求>97%;(2)含泥量≤0.2%;(3)粒度分布宜采用3~5筛分散度;(4) AFS细度:应根据铸件表面粗糙度要求来选定不同的细度,一般为AFS50-65;(5)粒形:尽可能选用圆整性好的硅砂,角形因素应V1.3;(6) PH值<7;(7)硅砂需用水擦洗过,如有特殊要求,可将硅砂酸洗或进行高温活性处理(900。
C焙烧)目前普遍采用酚醛类树脂作为粘结剂。
酚醛类树脂有固体和液体、热固性和热塑性之分。
目前制作覆膜砂通常采用热塑性固态酚醛树脂。
对其性能要求是:(D聚合速度(热板法):25~27s;(2)软化点(环球法):90~105°C;(3)流动性(斜板法):60~IlOmm;(4)游离酚含量(浪化法):≤4%β粘结剂的性能对覆膜砂的品质有很大的影响,人们一直在致力于研究如何提高酚醛树脂的性能,以及寻找酚醛树脂的替代品。
国外已开发出不同性能的专用树脂,如高强度低发气树脂、易溃散树脂,也有采用改性聚酯树脂的报道,但未得到全面推广,至今普遍采用的仍是改性酚醛树脂。
国内近年来在覆膜砂专用酚醛树脂的研究开发方面发展较快,已开发出不同的改性酚醛树脂供生产使用。
3.固化剂、润滑剂、添加剂固化剂通常采用乌洛托品即六亚甲基四胺,分子式为(CH2)6N4,要求为工业一级品。
润滑剂一般采用硬脂酸钙。
其作用是防止覆膜砂结块,增加流动性,使型、芯表面致密及改善砂型(芯)的脱模性。
添加剂的主要作用是改善覆膜砂的性能。
目前采用的添加剂主要有:耐高温添加剂(如含碳材料或其他惰性材料)、易贵散添加剂(如二氧化镒、重铝酸钾、高镒酸钾、已内酰胺等)、增强增韧添加剂(如超短玻璃纤维材料、有机硅烷KH-550等)以及防粘砂添加剂和抗老化添二、覆膜砂的分类随着覆膜砂应用范围的不断扩展,不同铸造工艺、不同材质要求以及不同结构的铸件对覆膜砂提出了不同的性能要求。
半导体技术的发展历程

半导体技术的发展历程随着科技的不断进步,半导体技术在当今的信息时代扮演着重要的角色。
从最早的晶体管到如今的集成电路,半导体技术经历了一个漫长而辉煌的发展历程。
本文将从半导体的起源开始,梳理出半导体技术的发展脉络。
20世纪初,半导体技术的雏形开始显露出来。
当时,人们对电子运动的研究已经取得了一定的成果,而半导体材料的特殊性质引起了科学家们的兴趣。
1904年,德国物理学家赫尔曼·冯·辛诺发现了半导体材料的电导率与温度之间的关系,为后来的半导体研究奠定了基础。
1926年,美国物理学家朱利安·赫尔茨发现了硅晶体的半导体性质,并提出了半导体理论。
这一发现引发了人们对半导体材料的深入研究。
然而,在当时,由于材料制备和加工工艺的限制,半导体技术的应用范围非常有限。
直到1947年,贝尔实验室的威廉·肖克利和沃尔特·布拉顿偶然发现了晶体管效应,半导体技术才真正进入了实用化阶段。
晶体管的发明使得电子设备的体积大大减小,性能得到了极大的提升。
这一发现被誉为电子技术史上的重大突破,也为半导体技术的快速发展奠定了基础。
20世纪50年代,半导体技术开始进入了集成电路时代。
1958年,杰克·基尔比发明了第一块集成电路,将多个晶体管集成在一块芯片上。
这一突破彻底改变了电子设备的制造方式,使得电子产品的性能提升和体积缩小成为可能。
随后的几十年间,半导体技术不断取得突破。
1960年代,人们开始尝试使用光刻技术制造集成电路,从而提高了电路的复杂度和可靠性。
1971年,英特尔公司推出了第一款微处理器,开创了个人电脑时代。
微处理器的问世将计算能力集成到了一个芯片上,为电子产品的普及奠定了基础。
20世纪80年代和90年代,半导体技术迎来了飞速发展。
制程工艺的不断进步使得集成电路的集成度越来越高,功耗和体积也得到了大幅度的降低。
此外,半导体材料的研究也取得了重要进展,如硅基光电子技术和新型半导体材料的应用,进一步拓宽了半导体技术的应用领域。
- 1、下载文档前请自行甄别文档内容的完整性,平台不提供额外的编辑、内容补充、找答案等附加服务。
- 2、"仅部分预览"的文档,不可在线预览部分如存在完整性等问题,可反馈申请退款(可完整预览的文档不适用该条件!)。
- 3、如文档侵犯您的权益,请联系客服反馈,我们会尽快为您处理(人工客服工作时间:9:00-18:30)。
分复杂, 前很难弄清其化学组成。此外, 目 采用醋化 反应改性 , 即使醇分子上的轻基与动物胶侧链上的 梭基进行酷化反应, 使动物胶分子侧链进一步延长, 形成立体网状结构, 也能提高动物胶的粘结强度。 一 影响动物胶粘结性能的因素, 除了化学改性外, 还有原砂的质量 ,粒形、 ( 微粉含量、 酸耗值等)促硬 、 剂和成膜剂等的种类和加入量, , 因此 在优选型芯砂 配方时, 应在最大限度内发挥动物胶的粘接性能。 通过生产性试验指出如下制芯工艺规范: 芯砂 中动物胶水溶液加人量 15 . %, .-2。 压缩空气的射 芯压力 03 . a模具温度 ̄20 保温时间 . 5 , -0 MP 0' C,
合并长大 , 以致下沉的十分有效的措施。
的耐火骨料和液体载体产生相分离的沉淀现象, 获 得高表面质量的涂层和铸件; 而且还可使徐料具有 所要求的流变特性 , 提供优异的使用性能。然而, 目 前国产的醇基涂料的悬浮剂很难满足上述要求, 这 是国产醇基涂料性能较差, 与国外进 口涂料差距较 大的主要原因。 因此, 研究开发在醇溶液中具有悬浮 稳定性好、 分散度高、 流平涂刷性优异的新型悬浮 剂, 是我国生产优质的醉基快干涂料的关键。 . 人们把 N ‘ , 最初, a 基膨润土作为醇基徐料的悬 浮剂_ , 这是由于它资源广、 成本低的缘故。但是这种 材料在醇溶液中悬浮效果差, 加人量又多, 从而破坏
图 2 抗热裂的试验结果
1 原吠喃树脂砂;. . 2 低硫改性吠喃树脂砂;. 3 碱性酚醛树脂砂
放出来S Z Z, , S苯、 O , S (H ) 、 甲苯和苯酚等许多有 H C Z
从图可知 , 容易产生热裂缺陷的铸钢中, 如果采
专 i - A 芝 }  ̄ Q v -
八 “ n 乙
n U
用新型低硫改性的吠喃树脂 自硬砂时 , 与传统未改 性吠喃树脂砂 比较, 其热裂倾 向可减少 7 0, 0 0与碱 性酚醛树脂砂相同。 因此, 新开发的低硫改性吠喃树 脂砂在铸钢、 球铁件上有广泛应用前景。 众所周知 吠喃树脂的固化反应系其分子上活 , 泼氢与9甲基、 轻甲基与轻 甲基之间发生缩聚反应 和吠喃环上的双键打开产生加成聚合反应 , 形成三 维网状结构的固体树脂的原故 , 这种反应必须在强 酸, 如磺酸、 磷酸等条件下才能进行。 可是, 新开发的 低硫固化剂中, 是将部分有机经基酸化合物取代磺 酸, 由于酸的强度的降低, 导致吠喃树脂砂的固化速 度减慢, 强度下降, 给造型制芯工作带来一定的困 难。 解决的办法就是对原吠喃树脂进行改性 , 即加入 某种促硬剂 , 见图 3 所示。
毒的气体等可达十多种, 其中一氧化碳、 含硫的化合 物等 , 经常超过国家允许极限含量 , 这不仅污染作业 环境, 影响了工人的身心健康 ; 而且由于固化剂的热 分解使铸件表面增硫和热节处硫的富集, 增加了铸 件产生热裂的倾向, 从而严重影响了该工艺进一步 推广应用。 98 日 19 年 本花王株式会社开发出低硫改 性吠喃树脂自 硬砂, 并开发出N - 。 F 20 系列低硫 0 的吠喃树脂用固化剂, 根据铸件的大小、 新旧两种固 化剂的热分解 s , o 析出量见图 1 0 浇 注 时 sor 发 生 娥
墓 ) 侧 半 绷 豁 蒸
40 0
总之, 自 树脂 硬砂的引入, 对于改变我国铸造生 产落后方式, 提高铸件质量 , 增强企业产品竞争力, 扩大铸件和机械产品的出口创汇, 均起了积极的作
用。
30 0
20 0
10 0 0
1 2 3
但是 , 吠喃树脂 自硬砂最大的缺点是 : 在混砂、 造型、 制芯时, 挥发出甲醛、 糠醇等有害气体。在浇 注、 冷却和落砂过程中, 由于吠喃树脂的热分解, 释
粘结剂 , 成功地浇注了一些铸铁件 , 取得了令人满意 的效果。 作者认为, 动物胶在造型、 制芯、 浇注和落砂 过程中不析出有毒、 有害气体 , 原材料资源丰富, 价
‘. 压
n U
应用
构, 导致它性能的变化, 这是可对它进行化学改性的
热芯盒法是一种芯砂硬化速度快、 树脂砂成本 主要依据。粘结强度高、 芯砂溃散性好, 特别适合于 内腔复杂的铸铁件和铝、 镁合金铸件的生产。 我们是采用淀粉对动物胶进行接枝反应的, 即 以在支链上含有经基的淀粉聚合物和在端基上含有 竣基的动物胶聚合物, 在一定的反应条件下( 温度
4 -5 万吨 。 0 0
从图 1 可看出, 铸件越大 , 吠喃树脂砂浇注时产 生的 S : O 有毒气体越多。不过 , 采用新开发的低硫 改性吠喃树脂砂时, 浇注产生 S : O 的数量可降低 6 0 -8 %。 0 o这不仅明显改善了铸造车间的作业环境 , 而 且还大大地减少了铸钢件产生热裂, 球墨铸铁件产 生球化不良的铸造缺陷, 2 图 表示低硫固化剂对铸 钢件热裂的影响。
1 5 . n . O , -2 mi
3 在醉基涂料中应用的无机纳米悬浮剂 醇基徐料主要由耐火骨料、 液体载体、 悬浮剂、 粘结剂和附加物等五部分组成 , 其中悬浮剂在醇基
涂料中起了至关重要的作用。一种优 良的悬浮剂不 仅能有效地保证涂料各组分的均一性 , 防止高密度
降。其次, 得到稳定醇溶液悬浮体系的条件有三个: 胶粒的 合 一电位, 与胶粒相联系的反离子扩散层的 水化作用和稳定剂的存在。 大量试验指出, 凡是能提 高分散胶粒的 6 一电位和增加胶 团水化作用的因 素, 均能增加胶体体系的稳定性。同时 , 加入适量的 超细分散稳定剂 , 又称胶溶剂, 使之吸附于胶粒表 面, 防止其 S 一电位及水化作用的降低和醇溶液胶 体体系的破坏, 这也是防止胶体粒子( 锉基膨润土)
低和混砂设备简单的高效制芯工艺。 我国从 16 年 96
开始应用脉醛树脂和糠醇单体作粘结剂, 用此工艺 成功浇注了进排气管等铸铁件后 , 17 年相继开 从 90 发了许多热芯盒树脂 , 使这一工艺在我国汽车、 拖拉 机、 柴油机等铸造车间得到了广泛的应用。但是 , 热 芯盒树脂中存在游离甲醛高( . )气味大的问 >15 o、 0 题, 一直困扰该工艺的推广应用。 因为游离甲醛对人 体的损害较大 , 国对其作业环境处 甲醛最大允许 英 含量控制在 2p 以下, , pm 可是 我国为数不少的树脂
Pm2 P)
} 训: J ,
中 们;
大件
图 1 峡喃树脂砂浇注时释放出的 S 2 0 气体数i
艺 用 取 粘 砂 艺,使 铁 尺 精 提 。来 代 土 工 可 铸 件 寸 度 高
二级 , 表面质量提高 1 级, -2 废品率明显减少, 现已 成为我国不少企业增加产品市场竞争能力的重要手 段。 9 年代 , 到 0 我国已建成树脂砂生产线 20 0 多条 , 峡喃树脂年用量约 2 万吨, -3 用其生产的铸件达
7^8', 0-0 反应时间2 h C -5 和酸性催化剂) 进行接枝
共聚反应 , 使淀粉分子嫁接到动物胶分子上, 形成动 物胶一淀粉络合物, 使动物胶形成更大的高分子化 合物, 我们采用了红外光谱分析, 也充分证实了上述 接枝反应的存在。 通过上述化学改性 , 可使动物胶的
《 山东机械}01 第G ; 0年 2 期
强度提高一倍以上 , 仑与 综 主 七 过程 中, 涂料中锉土胶团易于失水和 s 电位下降 一 而失去悬浮作用, 致使涂料中耐火骨料下沉结块, 形 成“ 死沉淀”甚至使之报废 。 , 为什么锉基膨润土持久稳定性差 , 又如何克服 其缺点 , 我们可从胶体化学的知识得以解释。首先 , 只有当分散相在溶液中呈胶体状态时 , 它才能赋予 醇基涂料具有 良好的分散稳定性和流变触变性能, 可是 , 锉基膨润土在醇溶液中不是以胶体状态存在, 这种粗粒子很容易聚集长大 , 使醇溶液的分散度下
厂 生产 的热 芯盒 树 脂 中游 离 甲醛 含 量 在 05 .- 20 . %之间。 在我国高度重视环保的今天和我国即将
加入 WT , O 产品竞争日趋激烈的时候, 要求减少铸 造车间的环境污染、 日实现“ 早 清洁生产” 的呼声也 日 益强烈, 因此, 急待开发一种无毒、 无污染、 低成本 的、 又能满足铸造生产中各种复杂型芯工艺要求的 绿色粘结剂 , 于是, 动物胶砂芯粘结剂 19 年在美 96 国应运而生。我国吉林工大将动物胶直接用作砂芯
《 山东机械》01 20 年第6 期
专 勃 与 综 述 考
面向 2 世纪造型制芯材料的发展 1
沈阳铸造研究所 周静一
2 世纪是我国高新技术迅猛发展和产品质量、 1 资源利用、 环境保护和生产成本激烈竞争的时代。 近 年来 , 随着人们环保意识的增强, 各企业必须按照国 家有关环境法则来组织生产, 才可生存和发展。 而铸 造是机械制造行业中劳动强度最大、 环境污染最严 重的部门, 而其主要污染源之一是造型、 制芯, 特别 是来 自粘结剂和固化剂体系, 它是直接影响铸件质 量、 制造成本、 生产效率、 劳动强度和环境污染的关 键因素。 因此, 合理选用现有的造型制芯材料和用高 新技术改进和开发新型粘结剂— 固化剂体系, 具 有极大的现实应用价值 , 也引起了世界各国铸造工 作者的高度关注。本文仅就沈阳铸造研究所正在研 究开发的部分科研项 目, 简要地介绍如下, 以便铸造 同仁相互交流。 1 新型改性峡喃树脂自 硬砂的开发 从 7 年代开始, 0 在我国酸硬化吠喃树脂作为型 芯砂粘结剂在铸造生产中, 特别是机床、 通用机械、 造船和机车车辆等企业已得到广泛的应用。 0 2 多年 来, 由于工艺的不断完善, 优质原辅材料的成套供 应, 致使之成为一种可生产结构复杂、 质量要求很高 的、 而且技术较成熟、 经验积累较多的造型制芯工
《 山东机械》01 20 年
第6 期
格便宜, 是一种很有发展前途的绿色型芯砂粘结剂。 但是, 直到今天 , 国内外均没有对动物胶进行改性 , 而是直接应用, 从而在使用过程中出现两大问题 : 其 ( 念 .生 一, 动物胶在室温下由于较强氢键的作用, 而呈凝胶 国 的固态, 给混砂造型带来极大的不便 。其二 , 由于动 侧 系 物胶没有改性 , 它本身的粘结能力未得到充分的发 田 编 挥, 以致使其在型砂中加入量偏高。 沈阳铸造研究所 品 夔 为了大幅度提高动物胶的潜在粘结强度, 采用了酷 东 化反应和接枝共聚等办法, 对动物胶进行了化学改 性, , 目前 可使 15 . %动物胶溶液( 浓度 5 0) 5o的硅砂 1 2 3 4 5 0 0 0 0 0 印 促硬剂加人量 ( ) 笼 的抗拉强度达到 20 a为我国热芯盒工艺 . 25 , 一 . MP 图 3 促硬剂对峡喃树脂砂 1O 强度影响 . h 进一步推广应用 , 开辟了美好的发展前景 。 从图可见, 加入促硬剂的改性吠喃树脂, 明显提 目 前常用的动物胶为骨胶, 它是胶原经过简单 高了树脂砂的硬化速度 , 弥补了低硫固化剂的不足 ; 的部分水解而得的蛋白质衍生物。其中胶原主要来 而且 , 还可减少固化剂的加入量, 进一步减少硫的析 自猪、 牛和羊等动物的皮、 肌键和骨骼 , 故原料丰富, 出。 目前, 这种新型吠喃树脂砂已在德国、 本、 日 美国 价格较低, 其化学组成为:1H4 3 3 C0 101 1 2 9 N 。动物胶具 和英国等国家铸造生产中应用, 对于满足 2 世纪提 1 有很多特点, 最主要的有 : 水溶性好, 胶体特性强, 这 出的环保、 高效的造型制芯要求, 提供了一条有效途 是它具有较高的粘结性能的主要原因。 润湿性好, 相 径。 溶性强, 它能与许多物质混合, 良好的互溶性 , 具有 2 高强度、 无污染改性动物胶粘结剂在热芯盒法中 并能在一定的条件下, 进行反应 , 改变它的分子结