蓄热式燃烧单双预热对比
预热式加热炉和蓄热式加热炉的应用对比

预热式加热炉和蓄热式加热炉的应用对比1. 前言- 对预热式加热炉和蓄热式加热炉这两种不同类型的加热设备进行介绍;- 说明论文的目的和意义。
2. 预热式加热炉的原理及应用- 介绍预热式加热炉的工作原理和特点;- 分析预热式加热炉的应用领域和优缺点;- 举例说明预热式加热炉的应用效果。
3. 蓄热式加热炉的原理及应用- 介绍蓄热式加热炉的工作原理和特点;- 分析蓄热式加热炉的应用领域和优缺点;- 举例说明蓄热式加热炉的应用效果。
4. 预热式加热炉与蓄热式加热炉的对比- 从能耗、效率、使用寿命、应用场景等多个角度,对预热式加热炉和蓄热式加热炉进行对比分析;- 探讨预热式加热炉和蓄热式加热炉各自的优劣势。
5. 结论与建议- 总结预热式加热炉和蓄热式加热炉的应用对比;- 提出未来研究的方向和可行性建议。
第一章前言加热炉是工业生产中一个重要的热能设备,广泛应用于冶金、化工、纺织、造纸等行业。
随着我国工业化的发展和对环保的重视,加热炉的能耗和效率越来越受到关注。
在推进绿色、低碳、节能的方针下,预热式加热炉和蓄热式加热炉慢慢地成为了替代传统加热炉的一种新型加热设备。
本文将对这两种加热炉进行对比分析,以期为加热设备的选择提供一些参考。
第二章预热式加热炉的原理及应用预热式加热炉,又称为预热炉,是一种基于工作介质的热能储存和传递原理的加热设备。
其原理大致是:将工作介质(如氧气、氮气等)通过加热器中流动,在加热器中与高温燃烧产生的废气进行热交换。
当工作介质达到一定温度时,即可进入下一步工艺要求的加热状态,从而实现节能效果。
预热式加热炉存在广泛的应用领域,适用于液态、气态等不同状态的介质加热。
在石油、石化、化工等行业中,预热式加热炉可以用于原料的加热、再生制氢等特殊工艺,达到提高生产效率和降低成本的目的。
在电力、钢铁等行业中,预热式加热炉也广泛应用于焙烧窑、炉前加热以及环保降低排放等方面。
预热式加热炉有其独特的优缺点。
由于采用了工作介质的热能存储转换原理,使得其能够满足不同介质的加热要求,具有较高的加热效率,节约了能源成本,并且减少了环境污染。
RTO蓄热式燃烧介绍及设计一般规定

RTO蓄热式燃烧介绍及设计一般规定RTO蓄热式燃烧介绍及设计规定在废气治理设备的设计中,应考虑留出一定的设计余量,根据各个厂家的实际设计经验和专家意见,治理设备设计风量的余量宜≥5%。
RTO的净化效率非常高,多室和旋转式RTO可以达到98%以上。
但是,两室RTO在换向阀切换时会产生一定的废气逃逸,虽然时间很短(一般只有几秒钟),但会造成排口浓度的瞬时升高,从而降低平均净化效率。
因此,两室RTO的处理效率在95%左右。
规定两室RTO的净化效率一般不宜低于95%,多室和旋转式RTO的净化效率一般不宜低于98%。
根据调研,国内现有的RTO设计热回收效率一般为95%。
但是,实地调研、测试和相关技术人员沟通交流表明,一般很难达到这一标准,一般在90%左右。
因此,规定热回收效率一般不低于90%。
工艺路线选择废气组成、温度、压力、污染物的性质、污染物的含量和废气流量等参数是进行蓄热燃烧法治理工艺路线选择的基本因素。
因此,蓄热燃烧法治理工艺路线应通过对废气的组成、温度、压力、污染等情况的分析而选择。
RTO可分为固定式和旋转式。
前者又可根据蓄热体床层的数量分为两室或多室。
旋转式RTO的蓄热体是固定的,利用旋转式气体分配器来改变进入蓄热体气流的方向,其外形大多呈圆筒状。
下面分别对其工艺原理进行介绍。
两室RTO系统工作原理为含VOCs的有机废气进入RTO 系统后,首先进入蓄热室一(该蓄热室已被前一个循环的净化气加热),废气从蓄热室一吸收热量使温度升高,然后进入燃烧室,VOCs在燃烧室内被氧化为二氧化碳和水,废气从而得到净化。
燃烧后的高温净化气离开燃烧室,进入另一个冷的蓄热室二,该蓄热室从净化的烟气中吸收热量,并储存起来(用来预热下一个阶段进入系统的有机废气),并使净化烟气的温度降低。
经过一段设定的时间,进入该周期的第二阶段,气体流动方向逆转,有机废气从蓄热室二进入系统,净化气体从蓄热室一排出。
气流流向在周期内改变两次,蓄热室也不断地吸收和放出热量,实现了高效热能回收,热回收率可达90%以上。
几种常见的工业废气焚烧工艺
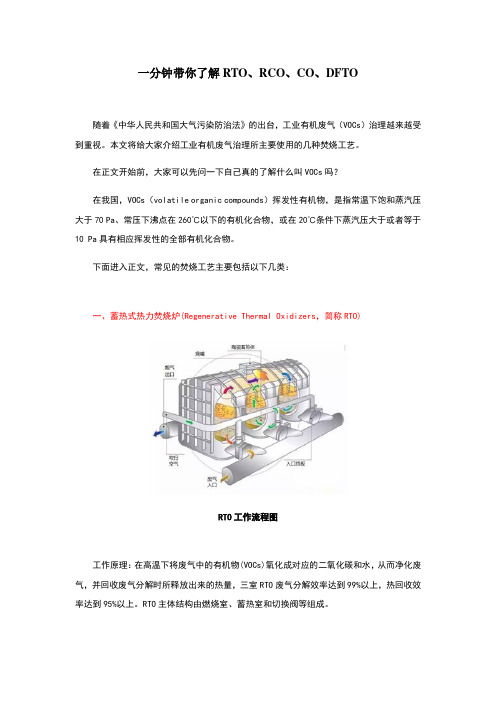
一分钟带你了解RTO、RCO、CO、DFTO随着《中华人民共和国大气污染防治法》的出台,工业有机废气(VOCs)治理越来越受到重视。
本文将给大家介绍工业有机废气治理所主要使用的几种焚烧工艺。
在正文开始前,大家可以先问一下自己真的了解什么叫VOCs吗?在我国,VOCs(volatile organic compounds)挥发性有机物,是指常温下饱和蒸汽压大于70 Pa、常压下沸点在260℃以下的有机化合物,或在20℃条件下蒸汽压大于或者等于10 Pa具有相应挥发性的全部有机化合物。
下面进入正文,常见的焚烧工艺主要包括以下几类:一、蓄热式热力焚烧炉(Regenerative Thermal Oxidizers,简称RTO)RTO工作流程图工作原理:在高温下将废气中的有机物(VOCs)氧化成对应的二氧化碳和水,从而净化废气,并回收废气分解时所释放出来的热量,三室RTO废气分解效率达到99%以上,热回收效率达到95%以上。
RTO主体结构由燃烧室、蓄热室和切换阀等组成。
氧化产生的高温气体流经特制的陶瓷蓄热体,使陶瓷体升温而“蓄热”,此“蓄热”用于预热后续进入的有机废气。
从而节省废气升温的燃料消耗。
陶瓷蓄热室应分成两个(含两个)以上,每个蓄热室依次经历蓄热-放热-清扫等程序,周而复始,连续工作。
蓄热室“放热”后应立即引入适量洁净空气对该蓄热室进行清扫(以保证VOC去除率在98%以上),只有待清扫完成后才能进入“蓄热”程序。
否则残留的VOCS随烟气排放到烟囱从而降低处理效率。
二、蓄热式催化氧化焚烧炉(Regenerative Catalytic Oxidation,简称RCO)RCO工作流程图工作原理:排放自工艺含VOCs的废气进入双槽RCO,三向切换风阀将此废气导入RCO 的蓄热槽而预热此废气,含污染的废气被蓄热陶块渐渐地加热后进入催化床,VOCs在经催化剂分解被氧化而放出热能于第二蓄热槽中之陶块,用以减少辅助燃料的消耗。
蓄热式燃烧技术目前存在的几点不足分享
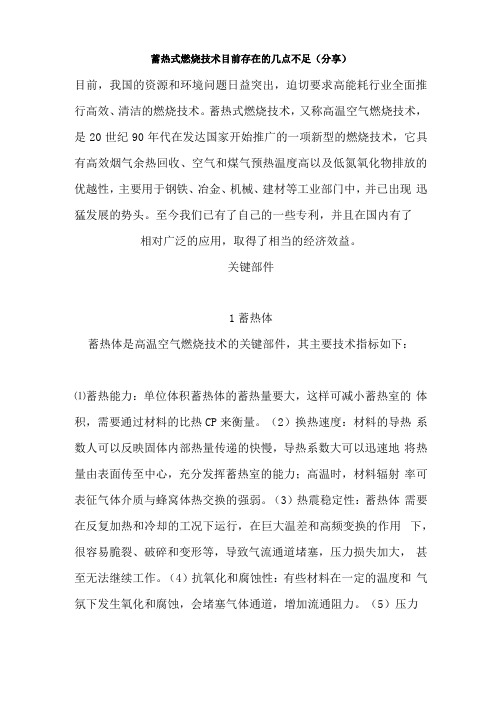
蓄热式燃烧技术目前存在的几点不足(分享)目前,我国的资源和环境问题日益突出,迫切要求高能耗行业全面推行高效、清洁的燃烧技术。
蓄热式燃烧技术,又称高温空气燃烧技术,是20世纪90年代在发达国家开始推广的一项新型的燃烧技术,它具有高效烟气余热回收、空气和煤气预热温度高以及低氮氧化物排放的优越性,主要用于钢铁、冶金、机械、建材等工业部门中,并已出现迅猛发展的势头。
至今我们已有了自己的一些专利,并且在国内有了相对广泛的应用,取得了相当的经济效益。
关键部件1蓄热体蓄热体是高温空气燃烧技术的关键部件,其主要技术指标如下:⑴蓄热能力:单位体积蓄热体的蓄热量要大,这样可减小蓄热室的体积,需要通过材料的比热CP来衡量。
(2)换热速度:材料的导热系数人可以反映固体内部热量传递的快慢,导热系数大可以迅速地将热量由表面传至中心,充分发挥蓄热室的能力;高温时,材料辐射率可表征气体介质与蜂窝体热交换的强弱。
(3)热震稳定性:蓄热体需要在反复加热和冷却的工况下运行,在巨大温差和高频变换的作用下,很容易脆裂、破碎和变形等,导致气流通道堵塞,压力损失加大,甚至无法继续工作。
(4)抗氧化和腐蚀性:有些材料在一定的温度和气氛下发生氧化和腐蚀,会堵塞气体通道,增加流通阻力。
(5)压力损失:在气体通过蜂窝体通道时,会产生摩擦阻力损失,在流经两块蜂窝体交界面时因流通面积突变和各个通道之间可能发生交错而产生局部阻力损失;前者对传热有利,后者对传热是不利的,因此应尽力减少局部阻力损失来降低风机的动力消耗。
(6)经济性:它是一个重要的指标,一种蜂窝体如果各种性能都好,但成本很高,推广和应用会受到限制。
2换向阀由于必须在一定的时间间隔内实现空气、煤气与烟气的频繁切换,换向阀也成为与余热回收率密切相关的关键部件之一。
尽管经换热后的烟气温度很低,对换向阀材料无特殊要求,但必须考虑换向阀的工作寿命和可靠性。
因为烟气中含有较多的微小粉尘以及频繁动作,势必对部件造成磨损,这些因素应当在选用换向阀时加以考虑。
蓄热式焚烧炉具有哪些特点?

蓄热式焚烧炉具有哪些特点?
蓄热式焚烧炉是一种利用烟气对炉壁进行辐射加热,将烟气中的热量存储到炉壁中,以实现立体辐射的焚烧方式。
相对传统的立式燃烧炉,蓄热式焚烧炉具有以下几个特点:
1. 高效节能
蓄热式焚烧炉具有很高的热效率,燃烧内部的二次燃烧技术可以充分燃烧烟气中的残余有害物质,减少化学污染物的排放,避免了传统的焚烧炉为了达到排放标准所消耗的大量能源。
2. 改善室内环境
相比传统的焚烧炉,蓄热式焚烧炉的燃烧更加充分,烟气排放更为纯净,减少对室内环境和居民健康的危害。
同时,由于蓄热式焚烧炉采用红外线辐射加热,燃烧烟气与室内空气隔离,减少了燃烧过程中产生的烟味。
3. 占地面积小
传统的燃烧炉需要较大的燃烧室和烟气排放系统,使得它们占地面积较大。
而蓄热式焚烧炉的燃烧室体积小,排放气体的管道短,占地面积更小,适合于小型家庭使用和环保产品推广。
4. 安全性高
传统的燃烧炉使用的是明火加热的方式,使用过程中极易引发火灾或燃气泄漏事故。
而蓄热式焚烧炉采用的是闭合式燃烧方式,安装时接入天然气或液化气供应管道,使用起来更加稳定,操作起来更加安全。
总之,蓄热式焚烧炉是一种集高效节能、改善室内环境、占地面积小和安全性高于一体的环保产品,目前正在逐步得到广泛的应用和推广。
蓄热式加热炉(教学参考)

蓄热式加热炉一、蓄热式加热炉的分类和特点:1、分类蓄热式加热炉按预热介质种类分为如下两种方式:同时预热空气和煤气式和空气单预热方式。
按结构型式来分,则蓄热式加热炉分为烧嘴式和通道式。
其中烧嘴式又分为全分散换向和群组换向两种;通道式也可分为单通道和双通道两种方式。
按运料方式来分,蓄热式加热炉分为推钢式和步进式。
全分散换向烧嘴式蓄热式加热炉能够实现单个烧嘴自动控制,与常规加热炉操作类似,能够满足各钢种对炉温的不同要求,实现炉温的灵活控制;群组换向蓄热式加热炉一般将某一段的烧嘴作为一个整体进行集中控制,这种控制方式能够实现各段炉温的灵活控制,也能满足大多数钢种对炉温的不同要求;通道式蓄热式加热炉一般是全通道整体控制,不能实现炉温的灵活调整,只能满足少数钢种(如普碳钢)的加热要求,而不能满足大多数钢种(如合金钢)加热的需求。
2、蓄热式加热炉的优点蓄热式加热炉有如下优点:①能将空气、煤气预热到800~1000℃的高温,有利于低热值燃料的利用;②充分利用烟气余热,节约燃料;③排烟温度低,氮氧化物含量少,环境污染少;④每对烧嘴交替燃烧,炉内温度均匀,可提高钢坯加热质量。
二、蓄热式加热炉燃烧系统简介1、蓄热式加热炉的蓄热体蓄热式加热炉的蓄热体有两种型式,一种是陶瓷小球,另一种是陶瓷蜂窝体。
蜂窝体单位体积的换热面积大,在相同条件下,蜂窝体的传热能力是陶瓷小球的4~5倍。
同样换热能力时,蜂窝状蓄热体的体积只需陶瓷小球蓄热体1/3~1/4。
采用蜂窝体的烧嘴结构紧凑轻巧。
蜂窝体体内气流通道是直通道,而陶瓷小球蓄热体的通道是迷宫式的,因此蜂窝体的阻力较小,陶瓷小球蓄热体阻力较大,前者仅为后者的1/3左右。
蜂窝体壁薄,仅为0.5~1.2mm,透热深度小,蓄热放热速度快,换向时间仅需40~80秒,换向时间短,被预热介质的平均温度高,热回收效率高。
由于换向时间短,因此换热周期内的炉温波动小,有利于炉温和钢坯加热温度的控制。
蜂窝体内部是直通道,在高速气流的正吹反吹的频繁作用下,通道不容易积灰和堵塞。
蓄热式燃烧运行原理

蓄热式燃烧,又称作RTO,是一种高效有机废气治理设备。
原理是在高温下将可燃废气氧化成对应的氧化物和水,从而净化废气,并回收废气分解时所释放出来的热量,废气分解效率达到99%以上,热回收效率达到95%以上。
RTO 主体结构由燃烧室、陶瓷填料床和切换阀等组成。
根据客户实际需求,选择不同的热能回收方式和切换阀方式,本文将具体为您进行说明,希望能够对您有所帮助。
一、工作原理在开工时先用新鲜空气代替有机废气,借燃烧器将蓄热室加热到一定温度。
由于蓄热体具有极高的储热性能,所以从一个冷的RTO加热到800-850℃,并且还要达到正常的温度分布,一般要经过几天时间(目前也有缩短到以小时计)。
在正常操作时,比如蓄热室A已在前一个操作循环(或称周期)中存储了热量,有机废气首先从底部进人蓄热室A,废气通过蓄热体床层被预热到接近燃烧室温度,而蓄热体同时逐渐被冷却;接着,预热后的废气进人顶部燃烧室(即主反应区,气体在燃烧室中的停留时间约为1s),在燃烧室中有机化合物被氧化后,即作为高温净化气进人蓄热室B。
此时,净化气将热量传给蓄热体,蓄热体床层逐渐被加热,而净化气则被冷却后排出。
当蓄热室A冷却到尚可允许的温度水平时,就应切换气流的流向,即完成1个循环。
切换流向后,有机废气进入已被加热过的蓄热室B,反应后的净化气则将热量传给已冷却的蓄热室A,如上所述一样,完成第2个循环。
这样通过不断反复循环操作来实现废气的净化和热量的充分利用。
一个循环时间,即切换时间大约为30-120s (两个切换时间就是一个全周期时间)。
如果废气中可燃物浓度达到自供热操作的水平,那么燃烧器只需在开工时使用,在正常运转时可以关闭。
若对有机废气的净化率要求很高,则可采用两种方法:一种是延长循环时间的操作方法,但这样会使热效率降低;另一种常用的方法是增加一台冲洗用蓄热室,即采用三室RTO装置。
二、优点1.几乎可以处理所有含有机化合物的废气;2.可以处理风量大、浓度低的有机废气;3.处理有机废气流量的弹性很大(从气体名义流量的20%-120%);4.可以适应废气中voc的组成和浓度的变化、波动;5.对废气中夹带少量灰尘、固体颗粒不敏感;6.在所有热力燃烧净化法中热效率最高(>95%);7.在合适的废气浓度条件下(一般>2-3g/m3,视VOC的热值而定)无需添加辅助燃料而实现自供热操作;8.净化率较高(三室>99%,两室95%-98%);9.维护工作量少、操作安全可靠;10.有机沉积物可周期性地清除,蓄热体可更换;11.整个装置的压力损失较小(RTO装置系统总压力损失一般<3000Pa,随所用蓄热体的结构类型、气体速度而变);12.装置使用寿命较长。
RTO蓄热式燃烧介绍及设计一般规定

RTO蓄热式燃烧介绍及设计一般规定在通常的废气治理设备中都会考虑留出一定的设计余量。
根据各个厂家的实际设计经验,结合专家意见,治理设备设计风量的余量宜≥5%。
在一般情况下,RTO 的净化效率非常高,多室和旋转式RTO 可以达到98%以上。
两室RTO 由于系统本身的设计特点,在换向阀切换时,会产生一定的废气逃逸,虽然持续时间不长(一般只有几秒钟),但会造成排口浓度的瞬时升高,在一定程度上降低了平均净化效率。
一般而言,两室RTO 的处理效率在95%左右。
在此规定,两室RTO 的净化效率一般不宜低于95%,多室和旋转式RTO 的净化效率一般不宜低于98%。
根据调研,国内现有的RTO 设计热回收效率一般为95%,但根据实地调研、测试和相关技术人员沟通交流,一般很难达到,在90%左右,故在此规定热回收效率一般不低于90%。
工艺路线的选择废气组成、温度、压力、污染物的性质、污染物的含量和废气流量等参数是进行蓄热燃烧法治理工艺路线选择的基本因素,蓄热燃烧法治理工艺路线应通过对废气的组成、温度、压力、污染等情况的分析而选择。
RTO可分为固定式和旋转式,而前者又可根据蓄热体床层的数量分为两室或多室。
旋转式RTO的蓄热体是固定的,利用旋转式气体分配器来改变进入蓄热体气流的方向,其外形大多呈圆筒状。
下面分别对其工艺原理进行介绍。
两室RTO系统工作原理为含VOCs的有机废气进入RTO系统后,首先进入蓄热室一(该蓄热室已被前一个循环的净化气加热),废气从蓄热室一吸收热量使温度升高,然后进入燃烧室,VOCs在燃烧室内被氧化为二氧化碳和水,废气从而得到净化。
燃烧后的高温净化气离开燃烧室,进入另一个冷的蓄热室二,该蓄热室从净化的烟气中吸收热量,并储存起来(用来预热下一个阶段进入系统的有机废气),并使净化烟气的温度降低。
经过一段设定的时间,进入该周期的第二阶段,气体流动方向逆转,有机废气从蓄热室二进入系统,净化气体从蓄热室一排出。
rco蓄热式催化燃烧法
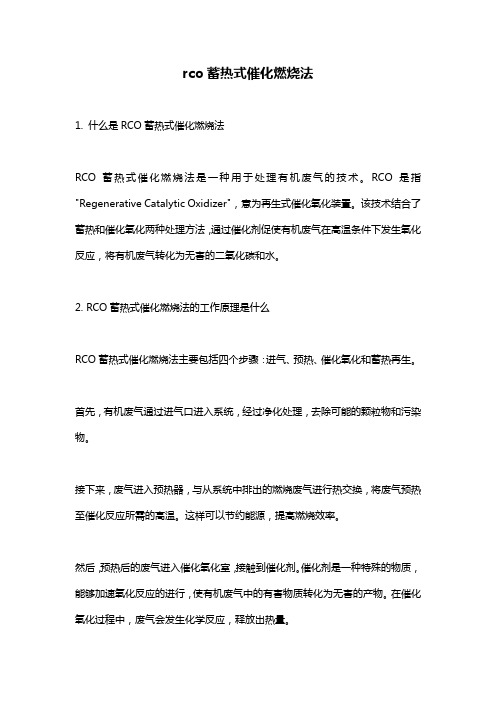
rco蓄热式催化燃烧法1. 什么是RCO蓄热式催化燃烧法RCO蓄热式催化燃烧法是一种用于处理有机废气的技术。
RCO是指"Regenerative Catalytic Oxidizer",意为再生式催化氧化装置。
该技术结合了蓄热和催化氧化两种处理方法,通过催化剂促使有机废气在高温条件下发生氧化反应,将有机废气转化为无害的二氧化碳和水。
2. RCO蓄热式催化燃烧法的工作原理是什么RCO蓄热式催化燃烧法主要包括四个步骤:进气、预热、催化氧化和蓄热再生。
首先,有机废气通过进气口进入系统,经过净化处理,去除可能的颗粒物和污染物。
接下来,废气进入预热器,与从系统中排出的燃烧废气进行热交换,将废气预热至催化反应所需的高温。
这样可以节约能源,提高燃烧效率。
然后,预热后的废气进入催化氧化室,接触到催化剂。
催化剂是一种特殊的物质,能够加速氧化反应的进行,使有机废气中的有害物质转化为无害的产物。
在催化氧化过程中,废气会发生化学反应,释放出热量。
最后,经过催化氧化后的废气进入蓄热器,其中的热量被吸收并储存下来。
然后,系统会周期性地改变进气和排气的方向,利用蓄热器释放储存的热量,再次加热进入的废气。
这样可以减少能源的消耗,并提高系统的热效率。
3. RCO蓄热式催化燃烧法的优势是什么RCO蓄热式催化燃烧法相比其他废气处理技术具有以下优势:a. 高效处理:催化剂的存在使得废气在较低的温度下就能发生氧化反应,从而提高了处理效率。
b. 节能环保:通过蓄热再生的方式,可以将废气中的热能回收利用,减少了能源消耗。
c. 安全可靠:催化燃烧过程中,温度控制较为精确,不会产生高温燃烧或副产物,减少了对环境和设备的损害。
d. 适用性强:RCO技术适用于处理各种有机废气,无论是低浓度还是高浓度,都能有效去除有害物质。
e. 操作维护简单:RCO系统结构简单,操作和维护相对容易,不需要频繁更换催化剂,降低了运行成本。
综上所述,RCO蓄热式催化燃烧法是一种高效、节能、环保的有机废气处理技术,通过催化剂和蓄热再生的方式将有机废气转化为无害的二氧化碳和水。
蓄热式加热炉

蓄热式加热炉、蓄热式加热炉的分类和特点:1、分类蓄热式加热炉按预热介质种类分为如下两种方式:同时预热空热方式。
按结构型式来分,则蓄热式加热炉分为烧嘴式和通道式。
其中向和群组换向两种;通道式也可分为单通道和双通道两种方式按运料方式来分,蓄热式加热炉分为推钢式和步进式。
全分散换向烧嘴式蓄热式加热炉能够实现单个烧嘴自动控制,能够满足各钢种对炉温的不同要求,实现炉温的灵活控制;群组换向蓄热式加热炉一般将某一段的烧嘴作为一个整体进行集中控制,这种控制方式能够实现各段炉温的灵活控制,也能满足大多数钢种对炉温的不同要求;通道式蓄热式加热炉一般是全通道整体控制,不能实现炉温的灵活调整,只能满足少数钢种(如普碳钢)的加热要求,而不能满足大多数钢种(如合金钢)加热的需求。
2、蓄热式加热炉的优点蓄热式加热炉有如下优点:①能将空气、煤气预热②充分利用烟气余热,③排烟温度低,氮氧化④每对烧嘴交替燃烧,到800~1000C的高温,有利于低热值燃料的利用; 节约燃料;物含量少,环境污染少; 炉内温度均匀,可提高钢坯加热质量。
二、蓄热式加热炉燃烧系统简介1、蓄热式加热炉的蓄热体蓄热式加热炉的蓄热体有两种型式,一种是陶瓷小球,另一种是陶瓷蜂窝体。
蜂窝体单位体积的换热面积大,在相同条件下,蜂窝体的传热能力是陶瓷小球的4〜5倍。
同样换热能力时,蜂窝状蓄热体的体积只需陶瓷小球蓄热体1/3〜1/4。
采用蜂窝体的烧嘴结构紧凑轻巧。
蜂窝体体内气流通道是直通道,而陶瓷小球蓄热体的通道是迷宫式的,因此蜂窝体的阻力较小,陶瓷小球蓄热体阻力较大,前者仅为后者的1/3 左右。
蜂窝体壁薄,仅为0.5〜1.2mm,透热深度小,蓄热放热速度快,换向时间仅需40〜80 秒,换向时间短,被预热介质的平均温度高,热回收效率高。
气和煤气式和空气单预烧嘴式又分为全分散换与常规加热炉操作类似,由于换向时间短,因此换热周期内的炉温波动小,有利于炉温和钢坯加热温度的控制。
RTO和RCO性能比较
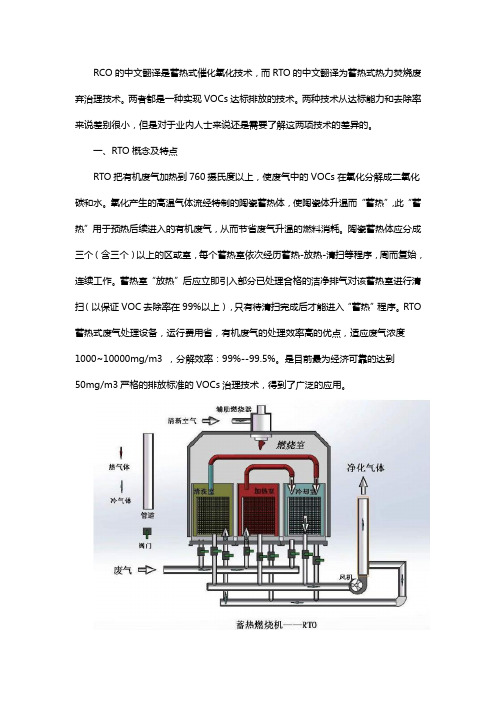
RCO的中文翻译是蓄热式催化氧化技术,而RTO的中文翻译为蓄热式热力焚烧废弃治理技术。
两者都是一种实现VOCs达标排放的技术。
两种技术从达标能力和去除率来说差别很小,但是对于业内人士来说还是需要了解这两项技术的差异的。
一、RTO概念及特点RTO把有机废气加热到760摄氏度以上,使废气中的VOCs在氧化分解成二氧化碳和水。
氧化产生的高温气体流经特制的陶瓷蓄热体,使陶瓷体升温而“蓄热”,此“蓄热”用于预热后续进入的有机废气,从而节省废气升温的燃料消耗。
陶瓷蓄热体应分成三个(含三个)以上的区或室,每个蓄热室依次经历蓄热-放热-清扫等程序,周而复始,连续工作。
蓄热室“放热”后应立即引入部分已处理合格的洁净排气对该蓄热室进行清扫(以保证VOC去除率在99%以上),只有待清扫完成后才能进入“蓄热”程序。
RTO 蓄热式废气处理设备,运行费用省,有机废气的处理效率高的优点,适应废气浓度1000~10000mg/m3 ,分解效率:99%--99.5%。
是目前最为经济可靠的达到50mg/m3严格的排放标准的VOCs治理技术,得到了广泛的应用。
二、RCO概念及特点RCO蓄热式催化燃烧法作用原理是:结合蓄热式氧化及触媒氧化,在陶瓷蓄热体上部填充催化剂,借助催化剂使有机废气在相对较低的起燃温度(280-500℃)下氧化分解成CO2和H2O,氧化产生的高温气体流经另一个蓄热室继续催化氧化反应放热,使陶瓷体升温而“蓄热”,此蓄热用于预热后续进入的有机废气。
RCO装置与RTO 装置相类似,多采用床式设计,蓄热室底部填充陶瓷蓄热体,催化剂填充在陶瓷蓄热体与氧化室之间。
RTO与RCO性能对比表(处理风量30000m3/h)三、综合处理能力及成本分析1)达标性1 RCO常用为堇青石陶瓷蜂窝为载体的贵金属蜂窝催化剂,贵金Pd、Pt为活性组分。
由于催化剂对废气成分具有选择性,而烟包印刷采用多种成分溶剂混合使用,因此任何一种催化剂都不能确保所有成分VOC都能够彻底氧化分解。
蓄热式燃烧处理技术(RTO) :两床式、三床式、旋转式的区别

蓄热式燃烧处理技术(RTO):两床式、三床式、旋转式的区别1、RTO概述蓄热氧化技术RTO(RegenerativeThermal Oxidizer,简称RTO)把有机废气加热到760℃以上,使废气中的挥发性有机物(VOCs,Volatile Organic Compounds)在燃烧室中氧化分解成CO2和H2O。
氧化产生的高温气体流经特制的陶瓷蓄热体,使陶瓷体升温而“蓄热”,下个过程是废气从已经“蓄热”的陶瓷经过,将陶瓷的热量传递给废气,有机废气通过陶瓷作为换热器载体,反复进行热交换,从而节省废气升温的燃料消耗,降低运行成本,热回收效率高达95%。
在中高浓度的条件下,RTO可以对外输出余热,通过蒸汽、热风、热水等形式加以利用,在满足环保目标的同时,实现经济效益。
RTO设备分为两床式、三床式与旋转式。
在两床RTO产品的基础上,经过升级换代,两床RTO现升级为多床式、旋转式RTO,各有优劣。
1.1两床式RTO介绍两床式RTO由两个陶瓷蓄热体填料床组成,以最简单的一进一出过程完成“蓄热”和“放热”过程的切换。
两床式RTO有2个蓄热室,工作时2个蓄热室大约1min-2min切换一次状态(进口-出口),风门在切换过程中大约有0.3s-0.6s 的时间直接将高浓度的废气排到排放口,且当前进气蓄热室底部残留的未分解废气也被直接排出。
大量工程应用表明:两床式RTO的VOCs的最大分解效率为95%,最大综合热效率为90%,进出口温差高达45℃。
在阀切换时,废气管道内的压力波动范围为±500pa。
1.2三床式RTO介绍三床式RTO同样是采用阀门切换式,由三个或多个陶瓷填充床组成, 在两床式RTO的基础上增加了“吹扫”功能,大大的提高了废气分解效率。
以三床式RTO为例:阶段一:废气通过蓄热床A被预热,然后进入燃烧室燃烧,蓄热床C中残留未处理废气被净化后的气体反吹回燃烧室进行焚烧处理(吹扫功能),分解后的废气经过蓄热床B排出,同时蓄热床B被加热。
rco蓄热式催化燃烧设备的燃烧值

rco蓄热式催化燃烧设备的燃烧值在本文中,我将从简单到复杂地探讨rco蓄热式催化燃烧设备的燃烧值,并根据您的要求对其进行全面评估。
让我们从了解rco蓄热式催化燃烧设备的基本原理开始。
1. RCO蓄热式催化燃烧设备RCO蓄热式催化燃烧设备是指在催化剂床中,通过燃烧热空气将废气中的有机废气燃烧成二氧化碳和水,同时将废气中的热量储存到蓄热材料中,然后利用这部分储热能量对再生热风进行加热,从而达到空气预热和蓄热的目的,提高设备热效率的一种技术。
这种设备被广泛应用于化工、印染、印刷、制药等行业的有机废气处理过程中。
2. 燃烧值的概念燃烧值是指每单位质量或体积燃料在完全燃烧时所释放的能量,一般用于衡量燃料的能量含量。
在燃烧过程中,化学能被释放成热能,而燃烧值就是衡量这种能量转化的指标。
3. RCO蓄热式催化燃烧设备的燃烧值评估在评估RCO蓄热式催化燃烧设备的燃烧值时,我们需要考虑多方面的因素。
首先是废气中有机废气的种类和浓度,不同的有机废气在燃烧过程中释放的能量是不同的。
需要对废气的成分进行分析,以确定其燃烧值。
蓄热式催化燃烧设备的设计参数和运行条件也会影响其燃烧值。
包括催化剂的选择、燃烧温度、空气与废气的比例等都会对燃烧值产生影响。
在评估设备的燃烧值时,需要考虑这些因素,并根据实际的操作参数进行评估。
4. 对RCO蓄热式催化燃烧设备燃烧值的个人观点和理解作为一种先进的废气处理技术,RCO蓄热式催化燃烧设备的燃烧值对于其性能和效率至关重要。
我的个人观点是,通过对其燃烧值的全面评估和优化,可以进一步提高设备的废气处理效率,减少对环境的污染,降低能源消耗并提高经济效益。
对于企业而言,要重视对RCO蓄热式催化燃烧设备燃烧值的评估和管理,以确保其稳定、高效地运行。
总结:通过本文的探讨,我对RCO蓄热式催化燃烧设备的燃烧值有了更深入的理解。
了解废气成分、设备设计参数和个人观点都为我对这一主题的全面理解提供了帮助。
通过本文的撰写,希望您可以更全面地理解RCO蓄热式催化燃烧设备的燃烧值,以及如何进行评估和优化。
rto蓄热式焚烧炉工作原理
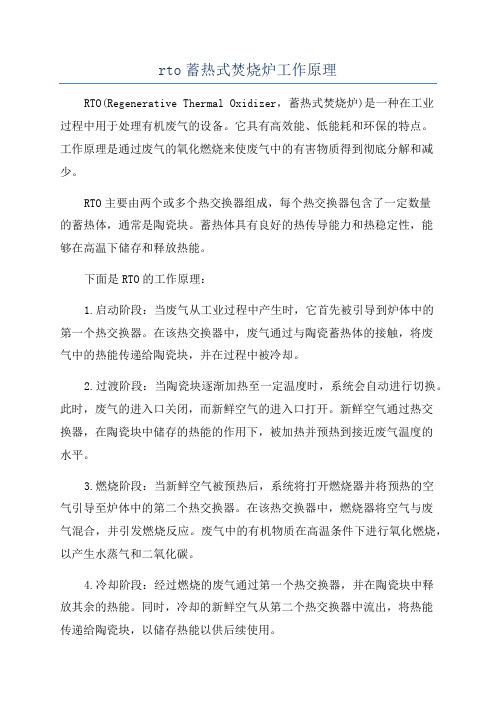
rto蓄热式焚烧炉工作原理RTO(Regenerative Thermal Oxidizer,蓄热式焚烧炉)是一种在工业过程中用于处理有机废气的设备。
它具有高效能、低能耗和环保的特点。
工作原理是通过废气的氧化燃烧来使废气中的有害物质得到彻底分解和减少。
RTO主要由两个或多个热交换器组成,每个热交换器包含了一定数量的蓄热体,通常是陶瓷块。
蓄热体具有良好的热传导能力和热稳定性,能够在高温下储存和释放热能。
下面是RTO的工作原理:1.启动阶段:当废气从工业过程中产生时,它首先被引导到炉体中的第一个热交换器。
在该热交换器中,废气通过与陶瓷蓄热体的接触,将废气中的热能传递给陶瓷块,并在过程中被冷却。
2.过渡阶段:当陶瓷块逐渐加热至一定温度时,系统会自动进行切换。
此时,废气的进入口关闭,而新鲜空气的进入口打开。
新鲜空气通过热交换器,在陶瓷块中储存的热能的作用下,被加热并预热到接近废气温度的水平。
3.燃烧阶段:当新鲜空气被预热后,系统将打开燃烧器并将预热的空气引导至炉体中的第二个热交换器。
在该热交换器中,燃烧器将空气与废气混合,并引发燃烧反应。
废气中的有机物质在高温条件下进行氧化燃烧,以产生水蒸气和二氧化碳。
4.冷却阶段:经过燃烧的废气通过第一个热交换器,并在陶瓷块中释放其余的热能。
同时,冷却的新鲜空气从第二个热交换器中流出,将热能传递给陶瓷块,以储存热能以供后续使用。
以上是RTO的一个循环。
RTO通过交替利用废气中的热能和新鲜空气之间的热交换,实现了高效率的热能利用,从而降低了能耗并节省了运行成本。
RTO同样也能有效地处理低浓度的有机废气,并通过废气处理的过程中产生的副产物进行排放控制,实现了环境友好。
此外,RTO还可以通过自动控制系统来监测和调节设备的运行状态,提高了设备的稳定性和安全性。
总而言之,RTO蓄热式焚烧炉通过利用陶瓷块的热储存和释放特性,实现了高效能、低能耗和环保的有机废气处理。
其工作原理有助于减少有机废气的排放量,改善环境质量,并提高工业过程的能源利用效率。
低氮蓄热式燃烧技术原理

低氮蓄热式燃烧技术原理今天来聊聊低氮蓄热式燃烧技术原理吧。
你们有没有见过那种老式的烧煤取暖的炉子呀?火在炉膛里呼呼地烧,产生的烟就直接排出去了。
这传统的燃烧就像咱们人类呼吸一样,吸进氧气,呼出废气,但是传统燃烧方式在能源利用效率上有点像“大手大脚的人”,浪费了好多能源呢。
而且呀,就像咱们做饭的时候如果火太大,油烟就很多一样,传统燃烧还会因为燃烧不完产生氮氧化物等污染物。
这就要说到低氮蓄热式燃烧技术的神奇之处了。
它就像是一个特别聪明的“小管家”。
在低氮蓄热式燃烧系统里,有个蓄热室就像是一个储蓄罐。
燃烧后的高温废气经过蓄热室的时候,就像把自己的热量“存”进了储蓄罐里。
那些热量可不会浪费,等会儿新的燃气和空气要进来燃烧的时候,这个蓄热室就会把之前存好的热量拿出来“分享”,用这个热量先把燃气和空气预热一下。
这样一预热呀,就像是跑步前先做热身运动,燃气和空气混合得更好了,燃烧的时候就更充分了。
那为什么叫低氮呢?打个比方吧,传统燃烧像那种杂乱无章的一群人在拔河,很容易出现捣乱的情况,导致燃烧不完全产生氮氧化物,就像拔河的时候有人用力方向不对。
而低氮蓄热式燃烧,它在燃烧过程中巧妙地控制温度和空气流量等参数,就好比找到了一个好的拔河“策略”,大家齐心协力,让燃烧按照最优化的路线走,氮氧化物的产生就大大减少了。
有意思的是,我一开始也不明白为什么控制温度就能减少氮氧化物呢。
后来深入学习才知道,这背后有个化学平衡的理论,氮氧化物的生成和燃烧温度密切相关,在一定温度范围内才会较少产生。
从实际应用上来看呢,就像一些大型的工业窑炉,采用了低氮蓄热式燃烧技术后,节能效果非常明显,污染物排放也大大降低了。
说到这里,你可能会问,那这项技术要不要很复杂的设备呢?其实设备确实有一定复杂性,但是带来的效益也是巨大的。
在应用的时候也有一些注意事项哦,比如说对蓄热体的材质是有要求的,要耐高温、耐腐蚀等等。
这项技术的原理现在大家是不是觉得挺有趣呢?当然我也还在不断学习更多关于它的知识,也希望大家都可以一起讨论,说不定你们也会有一些新的思路。
常规燃烧与蓄热燃烧对比

常规燃烧(单预热或双预热)
蓄热燃烧(集中换向,单蓄热或双蓄热)
系统组成
常规烧嘴+助燃风机+空煤气管道+嘴前阀门+段自控阀门+段流量孔板+换热器+烟道闸板+烟道+混凝土烟囱
蓄热烧嘴+助燃风机+空煤气管道+排烟管道+嘴前阀门+换向阀+排烟调节阀+段自控阀门+段流量孔板+排烟风机+钢制烟囱+常规烟道烟囱(单蓄热辅助排烟)
烟气横向交替流动,空煤气扩散燃烧导致烟气成分条状分部,炉压波动稍大
加热工艺
工艺适应性较广,可满足各种加热工艺要求
因入炉段温度较高(双蓄热),不太适合轴承钢等对入炉温度有较严格限制的钢种加热
综合评价
系统构成较复杂,建设投资较高,运行操作方便,维护成本低,燃耗一般,环保较好
系统构成复杂,建设投资较高,运行操作较方便,维护成本一般,燃耗较低,环保一般
投资工期
投资一般,工期较长பைடு நூலகம்
投资稍大,工期较长
运行维护
点火起炉方便,炉压较低且稳定,设备工作可靠,现场环境较较好,燃烧系统控制简单可靠,备品备件较少,大修维护成本较小
需设置点火烘炉烧嘴来起炉,炉压较高且有波动,设备工作较可靠,现场工作环境稍差,燃烧控制系统较复杂,备品备件较多,中大修维护成本稍高
节能环保
高品质煤气紧张的钢铁企业
技术发展
由于常规燃烧技术使用早且广泛,目前技术发展已经成熟,无大的变革,改进余地较少
随着蓄热材料性能及寿命提高、换向阀寿命及密封改善、控制理论及技术发展,目前蓄热燃烧系统,在运行维护和节能环保上已和常规燃烧不差上下,且有着燃耗低等优势,非常适合高品质煤气紧张的钢厂使用。
- 1、下载文档前请自行甄别文档内容的完整性,平台不提供额外的编辑、内容补充、找答案等附加服务。
- 2、"仅部分预览"的文档,不可在线预览部分如存在完整性等问题,可反馈申请退款(可完整预览的文档不适用该条件!)。
- 3、如文档侵犯您的权益,请联系客服反馈,我们会尽快为您处理(人工客服工作时间:9:00-18:30)。
双预热和单预热的比较1、双预热烘烤装置示意图2、双预热装置原理说明如上图所示为双预热蓄热式烘烤器的工作原理示意图。
在烘烤装置上有二对四个蓄热体,每一对为一个空气/煤气组合式蓄热体,中间被阻断。
当其中一对工作时,另一对排放高温烟气并蓄热;空气/煤气通过一个三位八通换向阀或二组三位四通换向阀来现实转换。
空气和煤气进入各自的蓄热体内被加热到相当高的温度(能否加热到800℃~1000℃则不一定),从蓄热体中喷出,在二者喷出的下方面(实际已经开始了强制性混合燃烧)制作一个空腔,收缩后向包内喷出,此时,另一组蓄热体则承担了排烟的任务,在排出烟气的同时将烟气内的热量提取,蓄热体被加热。
然后进行第二次换向。
3、单预热烘烤装置示意图4、单预热装置原理说明单蓄热式的工作原理与双预热式基本相同,只是它只将空气预热到设计温度而不预热煤气。
一对二个蓄热体,一个工作则另一个蓄热。
在蓄热体的中部安装了专用的烧嘴,通过一个三位六通或一个双层换向阀来现实空气/煤气/烟气的转换。
A/B交替工作。
5、二者比较单预热蓄热式燃烧和双预热蓄热式燃烧并无谁更先进或谁更好之分,只有适合与不适合之分。
特别是在具体运用到单台设备上时,就存在了一个选择的问题。
只有在根据设备的差异性分析,在经过严谨的科学的计算、评估后才可以确定哪种方式更适合。
不能因为其先进就无限制引用。
特别是在烘烤器上使用,如果不对其进行详细的分析,强行引入,不但起不到所期望的效果,还会给以后的生产和维护带来诸多麻烦,那样的话,双预热就只不过是个噱头了。
总的来说,蓄热式燃烧作为钢铁生产中的一项节能减排技术是值得在更多的企业里推广应用的,但在推广过程中必须注意结合各企业现有设备情况,因地制宜地建设实施,才能取得满意的效果。
3、单(双)预热装置的特点和存在的问题作为一种新型的高温燃烧技术,它们都具备了蓄热式高温燃烧技术的大部分特点如:节能降耗/提高燃烧利用率/包内温度均匀/提高内衬寿命/减少有害气体的排放等。
蓄热式燃烧技术引进国内后,许多的研究机构和企业都极积地参与到这一新型的节能技术的开发和拓展中,在90年中期,首次把双预热引入到钢包烘烤器上,经过几年的摸索和实践,到2001年前后,双预热蓄热式燃烧方式基本上退出了在钢(中)包烘烤器上的应用。
从相关的技术文献资料的检索中也可以看到,2002年以后就很少有关于双预热在钢包烘烤器应用方面的专题研究报告,更没有发现在中包上应用的报告。
但在加热炉/热风炉方面的应用则在不断地发扬光大。
究其原因,有以下几个方面:①蓄热体的寿命问题。
虽然这个问题首先是和蓄热体的材质相关,但在双预热式燃烧中,不可避免的“二次燃烧”,必将对蓄热体造成极大的伤害。
所谓“二次燃烧”是指在煤气蓄热体中,在换向时不可避免地会残留一定的煤气,当这一蓄热体开始蓄热时,所抽取的烟气中也不可避免地有残余的氧气,二者在蓄热体内再次产生燃烧的现象,就是“二次燃烧”。
在二次燃烧时,烟气中的残余氧和蓄热体内的残余煤气都具有很高的温度(煤气约在500℃左右,烟气约在1000℃左右)。
而且受燃烧空间限制。
此时的理论燃烧温度可达2200℃以上,虽然这部分热量不会损失太多(仍被蓄热体吸收),但蓄热体的耐火度和抗热震性能是有限度的,长时间且频繁的“二次燃烧”(一般为30秒~60秒左右换一次向)是蓄热体无法承受的。
目前国内多家研究机构都在投入大量精力开发新型的蓄热体来应对这一现象,但收效甚微。
②因蓄热体的内部阻力较大,一旦高炉煤气的压力不稳定,在蓄热体内可能会残留过量的CO,相对应的则是包内的空气余量也会相应增多,此时换向是相当危险的。
③换向阀的问题。
目前虽然有多项专利或专有技术都声称能解决换向阀的诸多问题,但其实每项技术都仅仅是解决了某一个关键性的问题,而不是整体的问题,如有的解决了多位换向过程中的密封性问题;有的解决了其中的防尘问题;也有的解决了动作同步和反应速度的问题;而作为蓄热式燃烧的一个关键部件,特别是在双预热中换向阀的问题就显得特别突出。
除了阀本身的问题外,还有一个就是上述的二次燃烧也会增加烟气温度从而给换向阀带来损害。
在大型加热炉上,因为有足够的空间可以施展,设计人员将空气换向和煤气换向分开,采用分散换向来解决这个安全隐患。
但在钢(中)包烘烤器上的狭小空间,很难展开。
④空气和煤气同时预热到很高的温度时,单个的气体分子获得了极高的内能,虽然这种活跃对空气和煤气的混合有利,但也会不可避免地造成燃烧的喘振现象,这对于低热值的燃气来说是极为不利的。
如果是在加热炉上,则对炉压会产生很大的影响。
⑤热工平衡问题。
★每台设备的空气和煤气消耗量在具体的时间段上都是一定的。
★也就是说它所产生的烟气量也是一定,烟气所携带的显热也是一定的。
★确切地说可以回收多少热量也是有限度的。
★这些热量能把多少空气或煤气从常温预热到多少度同样是可以计算出来的。
★要把这些热量蓄积在蓄热体中,根据蓄热体的热物理参数也可以计算出蓄热体的体积。
★★根据以上计算可能得到二种结果:其一是烟气的显热、蓄热体的蓄热能力、空气的预热温度正好达到一个平衡。
如果是这样,再增加煤气预热除了使投资增加,维护难度和费用上升外就没有别的了。
其二是烟气的显热有富余,也就是说经过蓄热体后的排烟温度仍超过设计值(280℃以上),蓄热式的效果就不明显了。
造成这一现象的原因有三种:1、是烟气量大,温度高,所含显热超出了助燃空气所需;2、是蓄热体蓄热能力不够或已损坏,造成余热浪费;3、是系统设计不合理,对蓄热式燃烧的原理不理解,无法在系统中设置两条曲线的工作程序;上述三种情况下(不论是在设计中或是在工况下,都可以通过计算来判断是哪种原因),只有第一种可以考虑采用双预热,因为这种情况是在假定蓄热体工况完全正常,只要有足够的蓄热体,且足以蓄积烟气所含显热的80%~90%以上,就可以实现双预热。
此时要增加煤气的预热就必须增加另一组(一对)蓄热体〖有些做法是在原有的蓄热体中加一隔板,一半走空气,另一半走煤气,也称之为“双预热”,是极不严谨的。
〗此时增加煤气预热必然带来五个方面的问题。
1、蓄热体体积增加,在包盖上完成布置很困难;(前期投入增加)2、因其寿命问题,维护费用增加;(后期投入增加)3、对换向阀提出了很高的要求,集中换向或是分散换向在小小的包盖上很不好决策;(前后期投入都增加)4、特别是对高炉煤气的预热,安全防护的要求必然提高;(前后期投入都增加)5、空气/煤气双预热后,烧嘴燃烧能力下降的补偿问题。
补偿的途径有三条,都是增加设备投入为主。
所以,是否对煤气进行预热则在于对整个系统的综合平衡进行评估。
⑥煤气含水问题对蓄热体的影响。
高炉煤气含水的问题是蓄热式烘烤上很难解决的一个难题,因其是小型设备的节能改造,和加热炉不同,其投入有限。
在改造中不可能涉及到排水问题(最多只在网管的设计或改造上考虑安装排水装置),双预热中冷煤气进入高温蓄热体,其中所含水份给蓄热体造成的伤害是相当严重的;而在单预热中,这部分水份在包内被加热,是和高温烟气一起在被排出时经过蓄热体,而且是以过饱和状态通过的,虽然也会对蓄热体造成影响,但与前者相比,则小得多。
⑦烧嘴燃烧能力的问题;不管是预热空气或是煤气,烧嘴的燃烧能力都会下降,它与预热气体所达到的热力学温度函数的平方根成反比。
一般在设计中充分考虑到这一点并进行补偿(三种补偿途径),这几种补偿都是以提高设备配置为基础的。
另外,为了增加煤气预热热,且达到所希望的效果,则必须增加专用的煤气换热的蓄热体,必然导致阻力增加。
燃烧能力进一步下降。
如果处理不当,最终可能会使温度升不起来(Q入﹤Q出)或升温时间大幅度延长。
⑧双预热在理论上的优势:★在同等工况下,高炉煤气的物理热(显热)比空气物理热的大8%~10%;★在其它工况相同时,助燃空气每提升100℃,理论燃烧温度升高约32℃~35℃;高炉煤气每提升100℃,理论燃烧温度升高约48~55℃;★高炉煤气预热后,点火更容易实现;⑨理论分析:以上有关煤气参与预热的理论都成立,但不能作为双预热的理由:以下我们对理论燃烧温度进行分析:上式为在一定空气系数下,高炉煤气燃烧时的实际理论燃烧温度如上式:式中参数说明:1、t理-理论燃烧温度,℃;2、QDW-煤气低发热量,kJ/m3;3、Q空-助燃空气显热,kJ/m3;4、Q煤-煤气显热,kJ/m3;5、Q吸-空气和煤气中湿成分分解带走的热量,kJ/(m3·℃);6、V产-燃烧产物中各组分的体积量,m3/h;7、C产-燃烧产物在t(理)时的平均比热容, kJ/(m3·℃)。
式中,2、5、6、7基本固定,提高T理的途径是增加3、4两项。
●如果∑max Q空气﹥∑max(Q空气+Q煤气)说明余热热量不多,只须预热空气(或高炉煤气)即可。
(此说法仅限于高炉煤气等低热值煤气)●如果∑max Q空气=∑max(Q空气+Q煤气),此时不管是预热空气或是预热煤气并不产产吸煤空理CV QQQQt DW⊕++=会带来本质上变化。
从安全性和投入上考虑只须预热空气即可。
●如果∑max Q空气﹤∑max(Q空气+Q煤气),说明余热热量有富余,此时可以增加煤气预热(即采用双预热),但要评估实施的可能性及经济性。