立体循环一体化氧化沟
科技成果——立体循环一体化氧化沟技术
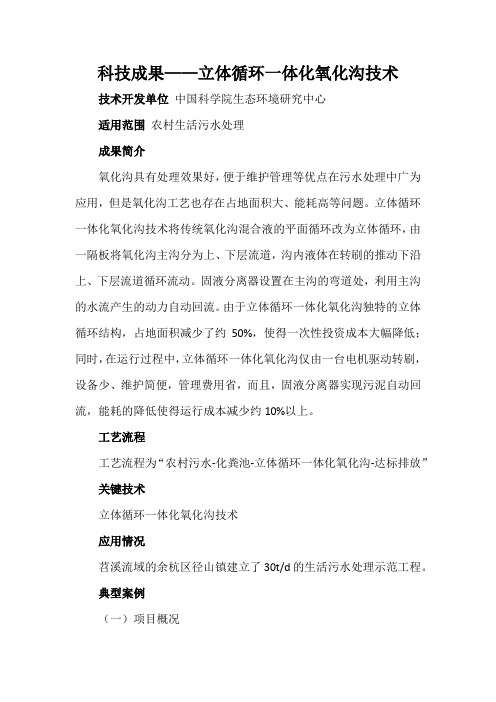
科技成果——立体循环一体化氧化沟技术技术开发单位中国科学院生态环境研究中心适用范围农村生活污水处理成果简介氧化沟具有处理效果好,便于维护管理等优点在污水处理中广为应用,但是氧化沟工艺也存在占地面积大、能耗高等问题。
立体循环一体化氧化沟技术将传统氧化沟混合液的平面循环改为立体循环,由一隔板将氧化沟主沟分为上、下层流道,沟内液体在转刷的推动下沿上、下层流道循环流动。
固液分离器设置在主沟的弯道处,利用主沟的水流产生的动力自动回流。
由于立体循环一体化氧化沟独特的立体循环结构,占地面积减少了约50%,使得一次性投资成本大幅降低;同时,在运行过程中,立体循环一体化氧化沟仅由一台电机驱动转刷,设备少、维护简便,管理费用省,而且,固液分离器实现污泥自动回流,能耗的降低使得运行成本减少约10%以上。
工艺流程工艺流程为“农村污水-化粪池-立体循环一体化氧化沟-达标排放”关键技术立体循环一体化氧化沟技术应用情况苕溪流域的余杭区径山镇建立了30t/d的生活污水处理示范工程。
典型案例(一)项目概况苕溪流域的余杭区径山镇漕桥村生活污水处理施设计日处理水量30m3/d,污水来源于村落的生活污水,2010年开工建设,于2011年06月完成调试并建成投产。
(二)技术指标根据课题第三方的检测数据,该工程主要污染物出水指标达到《城镇污水处理厂污染物排放标准》(GB18918-2002)中的一级标准中B级标准。
(三)投资费用吨水设备投资费用为5500元。
主体设备寿命20年以上。
(四)运行费用根据2012年06月-2012年12月实际运行情况,年处理污水300t,吨水运行费用为0.53元。
常见氧化沟

常见氧化沟常见氧化沟目录常见氧化沟 (1)1.Carrousel(卡罗赛尔)型氧化沟 (1)2.Orbal(奥贝尔)型氧化沟 (2)3.一体化氧化沟 (3)4.交替式氧化沟 (4)5.其他氧化沟系统 (6)1.Carrousel(卡罗赛尔)型氧化沟Carrousel型氧化沟是一多沟串联系统,进水与回流污泥混合后,共同沿水流方向在沟内做不停的循环流动,沟内在池的一端安装立式表曝机,每组沟安装一个,工艺示意图见图。
Carrousel型氧化沟曝气机均安装在沟的一端,因此形成了靠近曝气机下游富氧区和曝气机上游的缺氧区。
设计有效深度一般为4.0~4.5M,沟中的流速0.3m/s,由于曝气机周围的局部区域的能量强度比传统活性污泥法曝气池中的强度高的多,因此氧的转移率大大提高。
2.Orbal(奥贝尔)型氧化沟Orbal型氧化沟是由几条同心圆或椭圆形的沟渠组成,沟渠之间采用隔墙分开,形成多条环形渠道,每一条渠道相当于单独的反应器。
Orbal型氧化沟设计深度一般为 4.0M以内,采用转盘曝气,转盘浸没深度控制在230~530MM。
沟中水平流速为0.3~0.6 m/s 运行时,污水先进入氧化沟最外层的渠道,在其中不断循环的同时,依次进入下一个渠道,最后从中心渠道排出混合液,进入沉淀池。
因此,Orbal型氧化沟相当于串联的一系列完全混合反应器的组合。
Orbal型氧化沟组成示意图见图。
Orbal型氧化沟可根据需要分设两条沟渠,三条沟渠和四条沟渠。
常用的为三条沟渠形式。
对设三条沟渠系统,第一条沟的体积约为总体积的60%,第二条沟的体积占总体积的20%~30%,第三条沟渠占总体积的10%左右。
运行中保持第二,第三条沟的溶解氧浓度依次递增,通常为0 m/L,1.0 m/L,2.0 m/L。
以达到除碳,除氮,节省能量的作用。
Orbal型氧化沟有三个相对独立的沟道,进水方式灵活。
在暴雨期间,进水可以超越外沟道,直接进入中沟道或内沟道,由外沟道保留大部分活性污泥,利于系统恢复。
立体循环一体化氧化沟处理城市污水研究
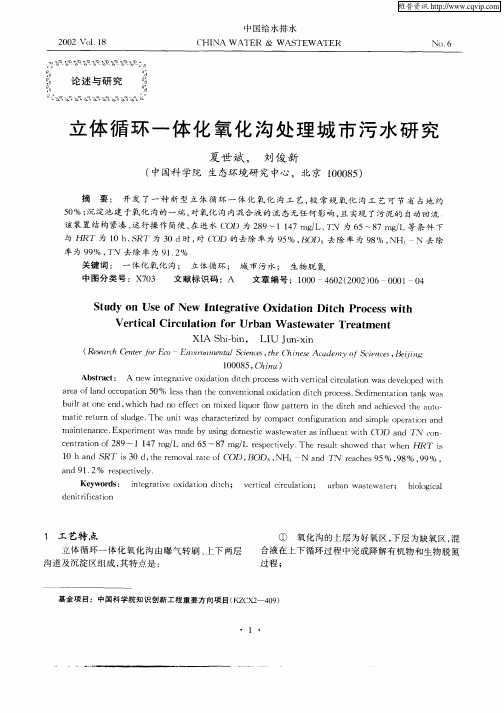
( 中国科 学院 生态环境研 究 中心 ,北京 10 8 ) 0 0 5
摘 要 : 开 发 了一 种 新 型 立 体 循 环 一 体 化 氧 化 沟 工 艺 , 常 规 氧 化 沟 工 艺 可 节 省 占地 约 较
5 % ; 淀池 建 于氧 化 沟的 一端 , 0 沉 对氧化 沟 内混合 液 的流 态无任 何 影 响 , 实现 了污泥 的 自动 回流 且
,
a nd 91. 2% r s c i ey. e pe tv l
Ke wo d : i t g a ie o ia i n d t h; v r i lcr u a i n u b n wa t wa e ; b oo ia y r s n e r t x d t i e t a i lr ; v o c c c o r a se t r i lg c 1 d n tic r n e i f al r i o
10 8 , n 0 0 5 C i a)
Ab ta t A e i tg a i eo i a i n d t h p o e sw i e tc l ic l t n wa e eo e t sr c : n w e r tv x d to i r c s t v r ia r u a i sd v lp d wih n c h c o a e fln c u a i n 5 r a o d o c p t 0% ls h n t ec n e t n l x d t n d t h p o e s S d me t t n t n s a o e st a h o v n i a o i a i i r c s e i n a i a k wa o o c o
.
b i to e e d, ih h d n f c n m i e i u r f w a t r n t e d t h a d a h e e h u o u l a n n wh c a o e f to x d l o l p te n i h i n c iv d t e a t t e q o c
氧化沟简介及氧化沟的主要优点

氧化沟简介及氧化沟的主要优点一、氧化沟简介氧化沟利用循环环式反应池(Continuous Loop Reator)作为生物反应池,并使用一种带方向控制的曝气和搅动装置向反应池中液体传递水平速度,从而使液体在池中循环。
氧化沟是活性污泥法的一种变型,在水力流态上不同于传统的活性污泥法,氧化沟是一种首尾相连的循环流动曝气沟渠。
最早的氧化沟渠是土沟渠,间歇进水、间歇曝气,从这一点上来说,氧化沟最早是以序批方式处理污水的。
1954年荷兰建成了世界上第一座氧化沟污水处理厂,为一个环形跑道,斜坡式池壁反应池,采用间歇运行方式,白天做曝气池用,晚上做沉淀池用,结构简单,处理效果好。
氧化沟处理污水的整个过程如进水、曝气、沉淀、污泥稳定和出水全部集中在氧化沟内完成,最早的氧化沟不需要设初次沉淀池、二沉池和污泥回流设备,采用延时曝气、连续进出水,所产生的污泥在污水净化的同时得到稳定,处理设施大大简化。
在我国,氧化沟技术的研究和工程实践始于20世纪70年代,目前氧化沟以其经济简便的突出优势已成为中小型城市污水厂的首选工艺。
氧化沟一般由沟体、曝气设备、进出水装置、导流和混合设备组成,沟体的平面形状一般呈椭圆形,也可以是方形的、圆形的或其他形状的,沟截面形状多为矩形和梯形。
二、氧化沟的主要优点1.氧化沟法由于具有较长的水力停留时间和较长的污泥龄,因此相比传统活性污泥法,有的还可以省略二沉池。
氧化沟能保证较好的处理效果,这主要是因为结合了CLR形式和曝气装置的特定的定位布置,使得氧化沟具有独特的水力学特征和工作特性。
2.氧化沟结合了推流和完全混合的特点,有利于克服短路,提高缓冲能力。
氧化沟内的污水在短期内(如一个循环)呈推流状态,能使入流至少经历一个循环而避免短路;在长时期内(污水在池内一般会经过几十圈的循环多次循环),污水呈混合状态,即使某个时刻有高浓度和有毒废水进入,进入沟内的高浓度和有毒废水会被大量循环液所混合稀释,因此氧化沟系统又具有很强的耐冲击负荷能力。
组合式一体化奥贝尔(Orbal)氧化沟设计原理及实例
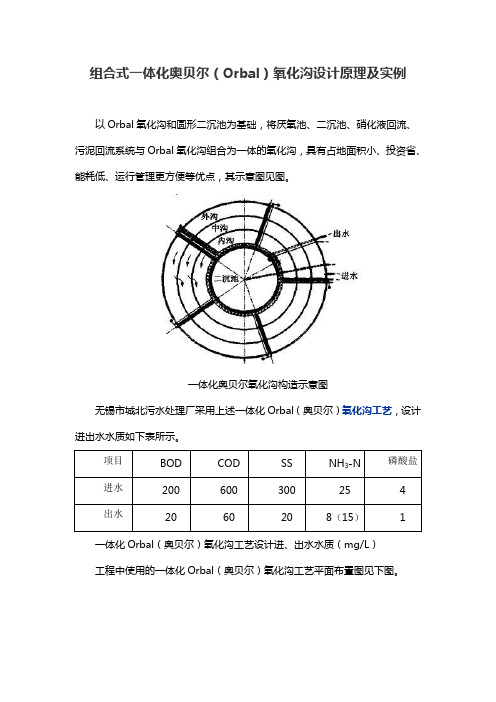
组合式一体化奥贝尔(Orbal)氧化沟设计原理及实例以Orbal氧化沟和圆形二沉池为基础,将厌氧池、二沉池、硝化液回流、污泥回流系统与Orbal氧化沟组合为一体的氧化沟,具有占地面积小、投资省、能耗低、运行管理更方便等优点,其示意图见图。
一体化奥贝尔氧化沟构造示意图无锡市城北污水处理厂采用上述一体化Orbal(奥贝尔)氧化沟工艺,设计进出水水质如下表所示。
一体化Orbal(奥贝尔)氧化沟工艺设计进、出水水质(mg/L)工程中使用的一体化Orbal(奥贝尔)氧化沟工艺平面布置图见下图。
污水处理厂一体化Orbal(奥贝尔)氧化沟工艺平面布置图1)工艺组成设计采用组合厌氧池Orbal(奥贝尔)氧化沟,包括中心岛、外沟、中沟、内沟。
考虑到有较高的除磷脱氮要求,利用其中心岛所占的体积作为厌氧反应器,将污水和回流污泥在其中进行厌氧混合强化释磷。
中心岛沟为一条狭长形渠道,其余三沟均为环状渠道。
生物处理系统包括中心岛厌氧区④、外沟①、中沟②、内沟③;周进周出辐流沉淀池⑤,位于中沟外壁与外沟内壁之间,与外沟内壁共享半圆墙体;利用中沟外壁、外沟内壁与二沉池间的空余空间分隔为4个区,一侧设置传统的外回流系统,分为进水、泥水混合区⑥和污泥回流区⑦;另一侧设置传统的内同流系统,分为氧化沟出水区⑧和硝化液同流区⑨。
2)工艺流程原水先进入泥水混合区,与从污泥回流区回流的活性污泥混合后通过管道进入中心岛厌氧区,依次进入Orbal(奥贝尔)氧化沟的外沟、中沟、内沟,完成有机物的降解、脱氮和除磷生物处理过程。
内沟的混合液通过管道分别进入出水区和硝化液回流区,进入氧化沟出水区的混合液通过调节堰门进入沉淀区进行泥水分离,在沉淀区内完成泥水分离后,出水排放。
而混合液通过安装在外沟内壁的水下推进器(内回流泵)同流至外沟。
沉淀区污泥在静水压力的作用下进入污泥回流区,大部分通过污泥回流泵回流至进水泥水混合区,小部分由剩余污泥泵排出至污泥处理系统。
氧化沟的主要形式及特点
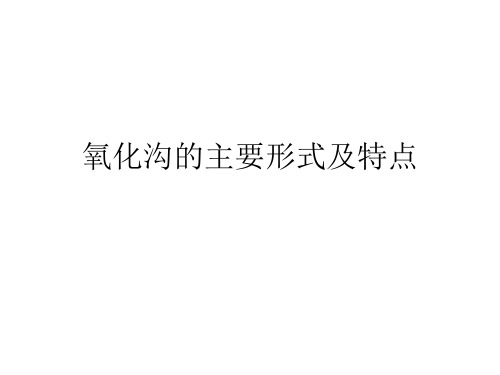
氧化沟的定义:
氧化沟(oxidation ditch)是活性污泥法一种变形工艺,一 般不需要初沉池,并且通常采用延迟曝气,其曝气池呈封 闭的沟渠形,污水和活性污泥混合液在其中循环流动,因 此被称为“氧化沟”或“氧化渠”,又称“连续循环曝气 池”。
原污水 原污水 转刷曝气器 表面曝 气器 回流污泥 处理水(去二沉池) 污泥泵房 干化设备 转刷 二沉池 处理水
奥贝尔(Orbal)氧化沟特点
• 多沟串联圆形或椭圆形的沟道,沟道断面形状多为矩形或 梯形,更好地利用水流惯性,减少水流短路现象,降低能 耗; • 对三沟同心式氧化沟而言,三沟道内形成较大的DO浓度 差,故充氧率高; • 耐冲击负荷强。与标准单沟道氧化沟对比,需氧量可节省 20%~35%,降低了能耗,操作控制简单,维护管理方便; • MLSS高,运行中一般为4~6g/L,对排泥设备要求严格,需 要特殊的工艺和结构设计,才能保证Orbal氧化沟的整体工 艺优势。
奥贝尔(Orbal)氧化沟
典 型 orbal 氧 化 沟 由 三 个 同心沟道组成,分别为外、 中、内沟。各沟道宽度有 工艺确定,一般不大于 9m;有效水深4~4.3m。 原水和回流污泥可以进入 三个沟道,通常先进入外 沟道,在不断循环中通过 淹没式传输孔流入中沟及 内沟。
典型的奥贝尔型氧化沟
奥贝尔(Orbal)氧化沟
出水
出水堰 导流墙 溶解氧传感器
双速(高速,低速) 转刷 单速 ( 高速 ) 转刷
污泥脱 水 污泥泵 站 进水
进水配水 井
交替式工作氧化沟特点
• 不需设二沉池和污泥回流和混合液回流系统
• 提高了转刷表面曝气机的利用率(达到58%)
• 良好的BOD去除效果和脱氮能力
论一体化氧化沟处理技术
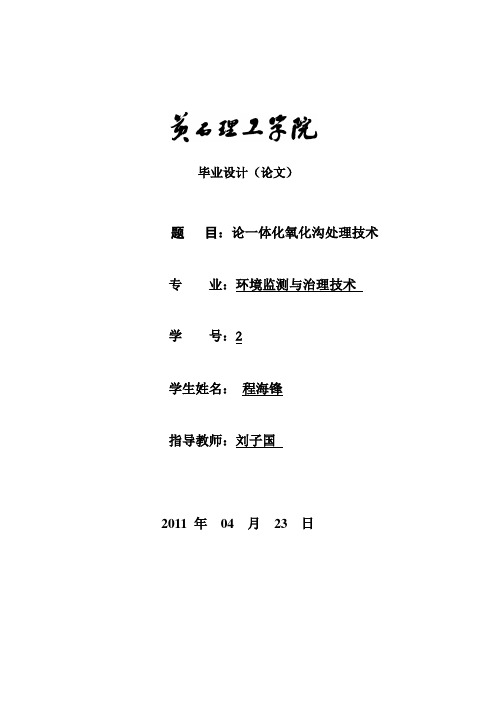
毕业设计(论文)题目:论一体化氧化沟处理技术专业:环境监测与治理技术学号:2学生姓名:程海锋指导教师:刘子国2011 年04 月23 日目录一、氧化沟 (1)1、氧化沟技术的发展和特点 (1)2、各类型氧化沟特点 (2)3、氧化沟的发展前景 (5)二、一体化氧化沟 (5)2.1沟内式固液分离器型一体化氧化沟 (5)2.2边墙式固液分离器型一体化氧化沟 (6)2.3中心岛式固液分离器型一体化氧化沟 (7)三、一体化氧化沟的运用 (8)3.1立体循环一体化氧化沟处理城市污水研究 (8)3.2.船形一体化氧化沟的处理城市污水研究 (13)四、一体化氧化沟的优势 (21)五、一体化氧化沟运行中存在的问题 (22)结论 (23)参考资料 (24)氧化沟一体化的前景展望1.氧化沟氧化沟(oxidation ditch)又名氧化渠,实际上它是活性污泥的一种变型。
因为污水和活性污泥的混合液在环状的曝气渠道中不断循环流动,有人称其为“循环曝气池”、“ 无终端的曝气系统”。
氧化沟的主要类型有卡鲁塞尔型(Carroussel)、奥贝尔型(Orbal)、交替式工作型、一体化氧化沟(Integrated oxidation ditch)。
1.1氧化沟技术的发展和特点1.1.1氧化沟技术的发展氧化沟工艺是20世纪50年代由荷兰卫生工程研究所(TNO)的帕斯维尔(A.Pasveer)博士通过研究和设计首先开发的。
第一座氧化沟污水处理厂是帕斯维尔于1954年在荷兰的伏肖汀(Voorshoten)建造的,服务人口仅为360人[1]。
它将曝气、沉淀和污泥稳定等处理过程集于一体,间歇运行,BOD5去除率高达97﹪,管理十分方便,运行效果稳定,适用于中小村镇的污水处理。
这种类型的氧化沟因其设计者而被命名为“帕斯维尔沟”。
60年代起,这项技术在欧洲、大洋洲、北美和南非等各国得到了迅速推广和应用,工艺上和构造上也有了很大的发展和改进。
据不完全统计,目前英国业已兴建了300多座氧化沟污水处理厂,美国已有500多座这样的污水处理厂。
立体循环一体化氧化沟
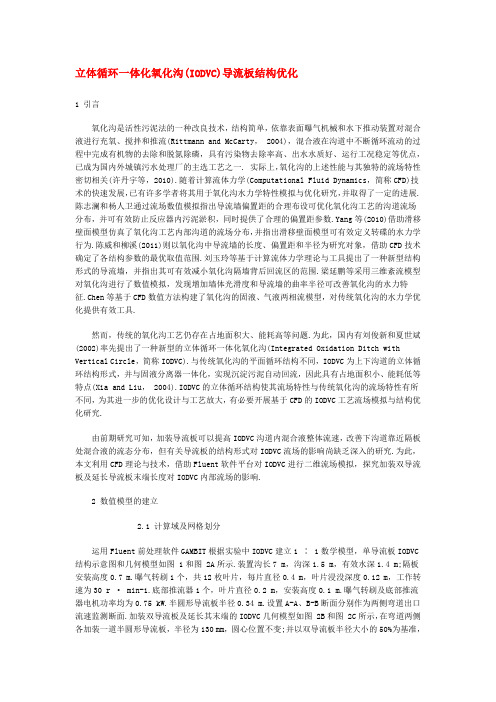
立体循环一体化氧化沟(IODVC)导流板结构优化1 引言氧化沟是活性污泥法的一种改良技术,结构简单,依靠表面曝气机械和水下推动装置对混合液进行充氧、搅拌和推流(Rittmann and McCarty, 2004),混合液在沟道中不断循环流动的过程中完成有机物的去除和脱氮除磷,具有污染物去除率高、出水水质好、运行工况稳定等优点,已成为国内外城镇污水处理厂的主选工艺之一. 实际上,氧化沟的上述性能与其独特的流场特性密切相关(许丹宇等,2010).随着计算流体力学(Computational Fluid Dynamics,简称CFD)技术的快速发展,已有许多学者将其用于氧化沟水力学特性模拟与优化研究,并取得了一定的进展.陈志澜和杨人卫通过流场数值模拟指出导流墙偏置距的合理布设可优化氧化沟工艺的沟道流场分布,并可有效防止反应器内污泥淤积,同时提供了合理的偏置距参数.Yang等(2010)借助滑移壁面模型仿真了氧化沟工艺内部沟道的流场分布,并指出滑移壁面模型可有效定义转碟的水力学行为.陈威和柳溪(2011)则以氧化沟中导流墙的长度、偏置距和半径为研究对象,借助CFD技术确定了各结构参数的最优取值范围.刘玉玲等基于计算流体力学理论与工具提出了一种新型结构形式的导流墙,并指出其可有效减小氧化沟隔墙背后回流区的范围.梁延鹏等采用三维紊流模型对氧化沟进行了数值模拟,发现增加墙体光滑度和导流墙的曲率半径可改善氧化沟的水力特征.Chen等基于CFD数值方法构建了氧化沟的固液、气液两相流模型,对传统氧化沟的水力学优化提供有效工具.然而,传统的氧化沟工艺仍存在占地面积大、能耗高等问题.为此,国内有刘俊新和夏世斌(2002)率先提出了一种新型的立体循环一体化氧化沟(Integrated Oxidation Ditch with Vertical Circle,简称IODVC).与传统氧化沟的平面循环结构不同,IODVC为上下沟道的立体循环结构形式,并与固液分离器一体化,实现沉淀污泥自动回流,因此具有占地面积小、能耗低等特点(Xia and Liu, 2004).IODVC的立体循环结构使其流场特性与传统氧化沟的流场特性有所不同,为其进一步的优化设计与工艺放大,有必要开展基于CFD的IODVC工艺流场模拟与结构优化研究.由前期研究可知,加装导流板可以提高IODVC沟道内混合液整体流速,改善下沟道靠近隔板处混合液的流态分布,但有关导流板的结构形式对IODVC流场的影响尚缺乏深入的研究.为此,本文利用CFD理论与技术,借助Fluent软件平台对IODVC进行二维流场模拟,探究加装双导流板及延长导流板末端长度对IODVC内部流场的影响.2 数值模型的建立2.1 计算域及网格划分运用Fluent前处理软件GAMBIT根据实验中IODVC建立1 ∶ 1数学模型,单导流板IODVC 结构示意图和几何模型如图 1和图 2A所示.装置沟长7 m,沟深1.5 m,有效水深1.4 m;隔板安装高度0.7 m.曝气转刷1个,共12枚叶片,每片直径0.4 m,叶片浸没深度0.12 m,工作转速为30 r · min-1.底部推流器1个,叶片直径0.2 m,安装高度0.1 m.曝气转刷及底部推流器电机功率均为0.75 kW.半圆形导流板半径0.34 m.设置A-A、B-B断面分别作为两侧弯道出口流速监测断面.加装双导流板及延长其末端的IODVC几何模型如图 2B和图 2C所示,在弯道两侧各加装一道半圆形导流板,半径为130 mm,圆心位置不变;并以双导流板半径大小的50%为基准,10%为递增单元,依次增加导流板末端的长度至其半径的130%,然后进行后续建模与结果分析.IODVC模型中流体所在部分为数值模拟的计算范围,转刷叶片只取浸入混合液中部分纳入计算域.此外,本文采用单相流模型模拟混合液在IODVC内流动行为.图1 IODVC结构示意图图2 IODVC几何模型(A. 单导流板; B. 双导流板; C. 延长双导流板) 有关网格划分,许丹宇等(2007)研究认为在氧化沟的不同计算域上应该采用不同类型和密度的网格.本文采用非结构化三角形网格对IODVC不同区域进行了不同密度的网格划分.其中,转刷转动区域内流场变化较为剧烈,采用Interval Size=4 mm的非结构化三角形网格,静止区域采用分块网格划分方式,在包络转刷转动的区域进行适当加密,采用Interval Size=8 mm的非结构化三角形网格,推流器附近区域采用Interval Size=5 mm的非结构化三角形网格,其余静止区域采用Interval Size=10 mm的非结构化三角形网格,全尺度IODVC网格划分在精度意义上满足计算和实际要求.2.2 湍流模型在氧化沟数值模拟中应用较多的湍流模型有k-ε双方程模型和Reynolds应力模型,其中k-ε双方程模型有3种,分别是标准k-ε模型,RNG k-ε模型和Realizable k-ε模型.根据4种湍流模型各自的应用特点,以及前期对IODVC采用不同湍流模型与实验的对比,本文选择RNG k-ε模型进行数值模拟.2.3 边界条件IODVC入口边界根据质量守恒定律和无旋假设,假定流速、湍动能k以及耗散率ε在入口截面上均匀分布.出口边界采用压力出口边界,出口压力设置为当前一个大气压水平.自由液面采用刚盖假定,液面近似为水平面,不考虑液面的波动,压强为标准大气压强值,液面垂向流速为零,其它变量的法向梯度为零.底面和壁面使用Launder和Spalding(1974)提议的标准壁面函数,垂向壁面的水平流速的法向梯度为零,底部壁面的垂向流速的法向梯度为零,满足壁面质量通量为零的条件.曝气转刷采用多重参考系模型,在转刷叶片半径范围内的流体区域建立独立的旋转参考系并定义转轴原点、旋转方向和转速,叶片与该转动区域内流体的相对速度为零,转动和静止区域重合的两个边界设置为interface.推流器借助风扇模型,定义为无限薄的理想推流器,主要作用是使流体获得轴向速度,对其引起的混合液旋转运动不作考虑.2.4 离散方法和求解算法对控制方程组的离散方法采用有限体积法,差分格式采用二阶迎风.求解方法采用Fluent提供的压力基隐式算法对IODVC流场进行稳态模拟,压力-速度耦合方法采用SIMPLE算法.计算中考虑重力影响,重力加速度设置为9.81 m · s-2.收敛标准设置为所有方程的残差绝对值小于10-4.3 数值模拟结果与分析3.1 单导流板IODVC流场模拟与问题分析在氧化沟工艺中,为了获得良好的混合和处理效果,氧化沟中混合液体循环流动的最小流速应该是0.15 m · s-1,而为了防止沟道中污泥的沉积,则沟道中混合液平均流速应该大于0.25 m · s-1(De Clercq et al.,1999).本文借助FLUENT对IODVC进行全沟道模拟后,利用后处理模块将IODVC计算域划分为4个不同流速大小的区域(<0.05、0.05~0.15、0.15~0.25、>0.25 m · s-1),进而统计各区域比例,得到单导流板IODVC的沟道中混合液的流速分布图(图 3).由图可见,混合液流速小于0.15 m · s-1的区域占总计算域的比例较高,达到41.53%,而相应流速大于0.25 m · s-1的区域占比较低,约为总计算域的32%.由此可见,在此流速分布情况下IODVC沟道内部混合液的整体混合效果不理想,低流速区域的大范围存在可能导致活性污泥的沉降和淤积,从而影响IODVC反应器的处理效果.图 4是单导流板IODVC的速度分布云图.由图可见,在IODVC两侧导流板的凹凸侧、左侧弯道出口处(隔板左侧上方)以及下沟道的上部区域(隔板下方)存在大范围的低速区,这是由于弯道出口处的混合液会由于惯性作用有向外扩散的趋势所致.图3 单导流板时IODVC速度分布图图4 单导流板时速度分布云图(m · s-1)由于IODVC采用上下沟道的结构设置,虽然导流板凹凸侧及下沟道的污泥沉降到底部会被高速循环的混合液冲击而不发生淤积,但大范围的低速区势必会造成回流现象,导致混合液逆向流动而造成动力消耗.为此,本文尝试通过加装双导流板及延长导流板末端长度来解决上述问题.3.2 加装双导流板对IODVC流场的优化研究双导流板的流场速度分布结果如图 5所示.对比图 3可知,双导流板使IODVC沟道中混合液低流速区域占比明显下降,相应高流速区域占比有较大幅度提高,其中混合液流速小于0.15 m · s-1的区域占比由41.53%下降至34%,流速大于0.25 m · s-1的区域占比由32%增加至41.5%,IODVC沟道中整体混合效果明显改善.通过图 6(双导流板IODVC速度分布云图)和图 4对比可知,双导流板可以有效提高下沟道特别是靠近隔板下方处混合液的流速,使下沟道内混合液流速分布更加均匀,减小了此处回流区范围,而且导流板凹凸两侧的低速区域较单导流板有明显改善,特别是在右侧导流板凹凸两侧处,由于高速液流的冲击,使IODVC弯道断面的流速分布更加均匀,混合液在上下沟道的过渡更加平稳,有利于整体流场的稳定.此外,在左侧弯道出口处(隔板左侧上方),由于双导流板的存在,回流区几乎全部消失.由此可见,双导流板减小了凹侧流道的宽度,改变了弯道处的流场特性,加剧了水流的紊流程度,增大了流速.图5 双导流板时IODVC速度分布图图6 双导流板的速度分布云图(m · s-1)3.3 延长导流板末端长度对IODVC流场的优化研究图 7是导流板末端不同长度时混合液流速大于0.25 m · s-1的区域占比.由图可见,当导流板末端延长至导流板半径的50%~100%时,沟道中混合液流速大于0.25 m · s-1的区域占比随导流板长度增加而增大;继续增加导流板长度,则占比呈减小趋势.其中,当导流板延长的长度等于导流板半径时,流速大于0.25 m · s-1的区域占比达到最大44.21%.图 8为导流板末端延长的长度等于导流板半径时的IODVC速度分布云图.由图可见,当导流板末端延长时,下沟道上部(隔板下方)及右侧弯道出口处的混合液流速较不延长(图 6)时有所提高,低速区范围明显缩减.可见,导流板末端延长的长度等于导流板半径时,IODVC内部流场更加趋于均匀,相应结构的优化更加趋于完善.图7 导流板不同延长长度时流速>0.25 m · s-1 区域占比图8 导流板延长长度等于导流板半径速度分布云图(m · s-1)在上述研究基础之上,进一步分析单导流板、双导流板和延长导流板(其长度等于导流板半径)等3种结构情况下弯道出口A-A、B-B断面流速分布,其结果见图 9.由图 9A可知,与单导流板相比,双导流板的断面流速分布更加均匀,在垂向坐标0.7~0.88 m范围内,流速明显升高,流速最大达到0.2 m · s-1,可有效防止此处形成回流;而延长导流板可使流速进一步提高.随着垂向坐标继续增加,双导流板及延长导流板的流速分布均接近直线上升趋势,其中在垂向坐标1.05 m附近,延长导流板使流速曲线有所波动,可能是导流板的末端和所取断面A-A比较靠近所致.由图 9B可知,在垂向坐标0~0.35 m范围内,三者流速分布相似,但在垂向坐标0.35~0.7 m范围内,对比3条曲线可知,双导流板和延长导流板可使此区域流速均值保持在0.15 m · s-1以上,整个断面流速分布优于单导流板的情况.具体参见污水宝商城资料或更多相关技术文档。
立体循环一体化氧化沟处理城市污水研究

立体循环一体化氧化沟处理城市污水研究1 工艺特点立体循环一体化氧化沟由曝气转刷、上下两层沟道及沉淀区组成,其特点是:①化沟的上层为好氧区,下层为缺氧区,混合液在上下循环过程中完成降解有机物和生物脱氮过程;②氧区在底层不与大气接触,缺氧环境形成快。
与常规氧化沟相比,采取上下两层沟道立体循环方式减少占地面积约50%;③淀区与氧化沟合建(建在氧化沟的一端),沉淀的污泥可自动回流到氧化沟内,无需污泥回流设备,节省了投资和能耗,并对氧化沟内混合液的流态无任何影响;④构紧凑,运行操作简便。
立体循环一体化氧化沟结构形式如图1所示。
该装置由有机玻璃制成,总有效容积为33L。
2 试验条件与方法原水取自城市污水检查井。
试验期间的水质见表1。
在试验过程中,装置内混合液的温度随季节而变化,基本维持在11~28℃。
在试验系统内混合液的循环流动由转刷推动。
转刷的功能一是充氧,二是使混合液循环流动,底部不发生污泥沉积。
根据设计要求,当转刷淹没深度确定后调节转刷转动速度可以保证沟内DO浓度及水流速度的要求。
试验期间氧化沟上层沟道的DO≥2mg/L,下层沟道保持缺氧状态。
混合液的循环流速平均为0.25m/s,未出现污泥沉积现象。
试验初期进水量为0.33L/h,逐渐增至6L/h,污泥浓度由0.9g/L逐渐增至5.0g/L。
在稳定运行期间污泥浓度保持在2.0~4.9 g/L,污泥负荷为0.08~0.14kgBOD5/(kgVSS·d)。
每天监测温度、进水流量、DO和pH值,进出水中的SS、COD、NH3-N、NO3-N、NO2-N、TN等项目每周测2次,分析方法采用标准方法。
pH值用PHS-3C型pH计测定;DO用YSI52型DO仪测定;NO3-N和NO2-N等采用离子色谱分析仪测定;COD和BOD5分别用CTL-12型化学需氧量快速测试仪和BODTrakTM型生化需氧量测定仪测定。
3 结果与讨论3.1 对有机物的去除稳定运行期间系统对COD的去除效果见图2(系统SRT=30 d,HRT=10 h)。
0215.ICC型一体化氧化沟介绍
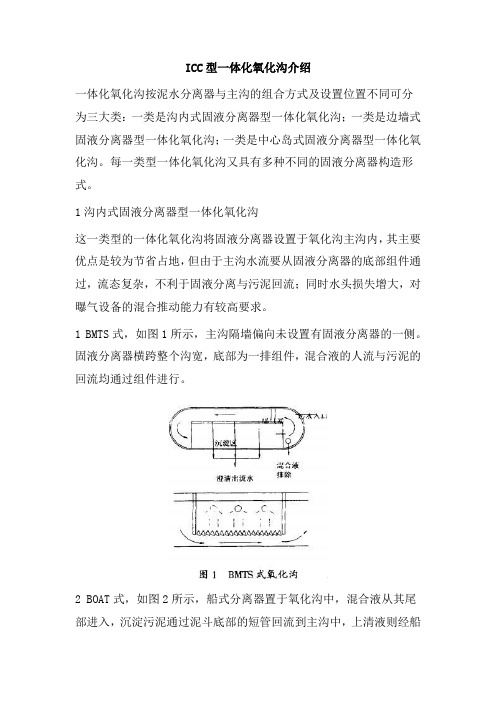
ICC型一体化氧化沟介绍一体化氧化沟按泥水分离器与主沟的组合方式及设置位置不同可分为三大类:一类是沟内式固液分离器型一体化氧化沟;一类是边墙式固液分离器型一体化氧化沟;一类是中心岛式固液分离器型一体化氧化沟。
每一类型一体化氧化沟又具有多种不同的固液分离器构造形式。
1沟内式固液分离器型一体化氧化沟这一类型的一体化氧化沟将固液分离器设置于氧化沟主沟内,其主要优点是较为节省占地,但由于主沟水流要从固液分离器的底部组件通过,流态复杂,不利于固液分离与污泥回流;同时水头损失增大,对曝气设备的混合推动能力有较高要求。
1 BMTS式,如图1所示,主沟隔墙偏向未设置有固液分离器的一侧。
固液分离器横跨整个沟宽,底部为一排组件,混合液的人流与污泥的回流均通过组件进行。
2 BOAT式,如图2所示,船式分离器置于氧化沟中,混合液从其尾部进入,沉淀污泥通过泥斗底部的短管回流到主沟中,上清液则经船式分离器头部的溢流堰排出。
3 C型沟内式,如图3所示,澄清区所处沟断面有一横向倾斜隔板,隔板上部为分隔的澄清区,下部为沟内混合液循环流动通道。
混合液先经过输入控制闸门进入澄清区前部,澄清区后部设集水槽收集出水,沉淀污泥由行车式刮泥机刮入回流孔返回沟流中。
4 D型沟内式,如图4所示,澄清区占据整个沟断面,在澄清区下设一V型穿越管曝气器。
澄清区也可设在沟外(穿越管进出口之间仍然隔断)。
澄清区无论是设在沟内还是沟外,都依靠穿越管曝气器在澄清区和曝气区之间产生水头差,这一水头差使行车式虹吸器形成虹吸,将污泥回流至主沟。
5管式,如图5所示,澄清区横跨氧化沟一侧,混合液沿管式沉淀器进入澄清池,上清液经上部出水槽收集后排出,分离的污泥通过管式沉淀器向下流到澄清区底部回流到氧化沟中。
6 多斗式,如图6所示,混合液从分离器前部经挡板消能布水进入澄清区,分离后的污泥经斗底回流孔进入氧化沟,上清液则在分离器后上部经穿孔管或三角堰排出。
2边墙式固液分离器型一体化氧化沟这一类型的一体化氧化沟将固液分离器设置在氧化沟的边墙上或外侧。
四川省城市污水处理示范工程_一体化氧化沟_邓荣森
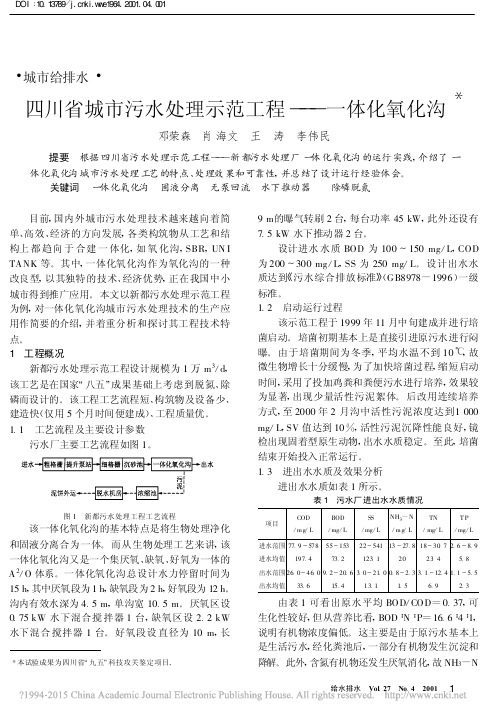
深 、减少占地的目的得以实现 。
值得一提的是 , 该污水厂全部设备为国产化设
备 , 节省了投资 , 与我国提倡的城市污水处理设备国
产化 、成套化的方针政策一致 。 该示范工程建造和
以充氧的功能为主 , 混合推动的功能则主要由水下
推动器承担 , 防止沟中产生沉积 。 该污水厂的运行
情况表明 , 当只有两台转刷运行时 , 沟内有一定的污
泥沉积 。 当一台转刷和 两台水下 推动器组 合运行
时 , 混合状况良好 。 而水下推动器的功率密度仅为 3 W/ m3 , 故既达到了节能的目的 , 同时也使增大沟
众所周知一体化氧化沟是集生物处理与固液分 离于一体 。 在本工艺中 , 固液分离是在氧化沟的侧 沟与中心岛的固液分离器中进行的(见图 2), 它们 是一体化氧化沟技术的关键 , 同时具有固液分离和 污泥回流两大功能 , 直接决定着出水水质的好坏 。
图 2 固液分离器示意
2.1.1 固液分离器工作原理 侧沟与中心岛固液分离器具有与二沉池相同的
表 2 侧沟 固液分离效果
Q / m3/ d
NA / m3/(m2·d)
M LSS / mg/ L
SV I / m L/ g
出水 SS / mg/ L
11 100
52.8
2 075
55
12.1
10 500
50.0
1 886
79
8.1
11 500
54.8
1 879
80
10.3
7 500
35.7
2 046
该污水处理厂内一体化氧化沟采用连续流间歇 曝气的运行方式 , 即曝气转刷周期性的开停 , 间歇向 沟内充氧 , 而水下推动器则连续开启 , 维持沟中流速 并起混合搅拌作用 , 防止污泥的沉积 。曝气转刷的 启闭是由沟内的溶解氧(DO)浓度决定的 。 该污水 处理厂于 2000 年 3 月 ~ 5 月在对氧化沟调试期间 , 进行了连续曝气和间歇曝气两种运行方式的对比试 验 。试验结果表明 :采用连续流间歇曝气运行方式 , 其有 机 物 去 除 效 果 与 连 续 曝 气 运 行 方 式 相 当 , NH3 -N去除效果 也基本相同 , 但总氮的去 除率有 明显提高 。 这说明投入较少的能量能收到相同 , 甚 至更好的 C , N 去除效果 , 这在工程应用上有着重大 的经济意义 。这在理论上也是成立的 :首先 , 系统间
- 1、下载文档前请自行甄别文档内容的完整性,平台不提供额外的编辑、内容补充、找答案等附加服务。
- 2、"仅部分预览"的文档,不可在线预览部分如存在完整性等问题,可反馈申请退款(可完整预览的文档不适用该条件!)。
- 3、如文档侵犯您的权益,请联系客服反馈,我们会尽快为您处理(人工客服工作时间:9:00-18:30)。
立体循环一体化氧化沟(IODVC)导流板结构优化1 引言氧化沟是活性污泥法的一种改良技术,结构简单,依靠表面曝气机械和水下推动装置对混合液进行充氧、搅拌和推流(Rittmann and McCarty, 2004),混合液在沟道中不断循环流动的过程中完成有机物的去除和脱氮除磷,具有污染物去除率高、出水水质好、运行工况稳定等优点,已成为国内外城镇污水处理厂的主选工艺之一. 实际上,氧化沟的上述性能与其独特的流场特性密切相关(许丹宇等,2010).随着计算流体力学(Computational Fluid Dynamics,简称CFD)技术的快速发展,已有许多学者将其用于氧化沟水力学特性模拟与优化研究,并取得了一定的进展.陈志澜和杨人卫通过流场数值模拟指出导流墙偏置距的合理布设可优化氧化沟工艺的沟道流场分布,并可有效防止反应器内污泥淤积,同时提供了合理的偏置距参数.Yang等(2010)借助滑移壁面模型仿真了氧化沟工艺内部沟道的流场分布,并指出滑移壁面模型可有效定义转碟的水力学行为.陈威和柳溪(2011)则以氧化沟中导流墙的长度、偏置距和半径为研究对象,借助CFD技术确定了各结构参数的最优取值范围.刘玉玲等基于计算流体力学理论与工具提出了一种新型结构形式的导流墙,并指出其可有效减小氧化沟隔墙背后回流区的范围.梁延鹏等采用三维紊流模型对氧化沟进行了数值模拟,发现增加墙体光滑度和导流墙的曲率半径可改善氧化沟的水力特征.Chen等基于CFD数值方法构建了氧化沟的固液、气液两相流模型,对传统氧化沟的水力学优化提供有效工具.然而,传统的氧化沟工艺仍存在占地面积大、能耗高等问题.为此,国内有刘俊新和夏世斌(2002)率先提出了一种新型的立体循环一体化氧化沟(Integrated Oxidation Ditch with Vertical Circle,简称IODVC).与传统氧化沟的平面循环结构不同,IODVC为上下沟道的立体循环结构形式,并与固液分离器一体化,实现沉淀污泥自动回流,因此具有占地面积小、能耗低等特点(Xia and Liu, 2004).IODVC的立体循环结构使其流场特性与传统氧化沟的流场特性有所不同,为其进一步的优化设计与工艺放大,有必要开展基于CFD的IODVC工艺流场模拟与结构优化研究.由前期研究可知,加装导流板可以提高IODVC沟道内混合液整体流速,改善下沟道靠近隔板处混合液的流态分布,但有关导流板的结构形式对IODVC流场的影响尚缺乏深入的研究.为此,本文利用CFD理论与技术,借助Fluent软件平台对IODVC进行二维流场模拟,探究加装双导流板及延长导流板末端长度对IODVC内部流场的影响.2 数值模型的建立2.1 计算域及网格划分运用Fluent前处理软件GAMBIT根据实验中IODVC建立1 ∶ 1数学模型,单导流板IODVC 结构示意图和几何模型如图 1和图 2A所示.装置沟长7 m,沟深1.5 m,有效水深1.4 m;隔板安装高度0.7 m.曝气转刷1个,共12枚叶片,每片直径0.4 m,叶片浸没深度0.12 m,工作转速为30 r · min-1.底部推流器1个,叶片直径0.2 m,安装高度0.1 m.曝气转刷及底部推流器电机功率均为0.75 kW.半圆形导流板半径0.34 m.设置A-A、B-B断面分别作为两侧弯道出口流速监测断面.加装双导流板及延长其末端的IODVC几何模型如图 2B和图 2C所示,在弯道两侧各加装一道半圆形导流板,半径为130 mm,圆心位置不变;并以双导流板半径大小的50%为基准,10%为递增单元,依次增加导流板末端的长度至其半径的130%,然后进行后续建模与结果分析.IODVC模型中流体所在部分为数值模拟的计算范围,转刷叶片只取浸入混合液中部分纳入计算域.此外,本文采用单相流模型模拟混合液在IODVC内流动行为.图1 IODVC结构示意图图2 IODVC几何模型(A. 单导流板; B. 双导流板; C. 延长双导流板) 有关网格划分,许丹宇等(2007)研究认为在氧化沟的不同计算域上应该采用不同类型和密度的网格.本文采用非结构化三角形网格对IODVC不同区域进行了不同密度的网格划分.其中,转刷转动区域内流场变化较为剧烈,采用Interval Size=4 mm的非结构化三角形网格,静止区域采用分块网格划分方式,在包络转刷转动的区域进行适当加密,采用Interval Size=8 mm的非结构化三角形网格,推流器附近区域采用Interval Size=5 mm的非结构化三角形网格,其余静止区域采用Interval Size=10 mm的非结构化三角形网格,全尺度IODVC网格划分在精度意义上满足计算和实际要求.2.2 湍流模型在氧化沟数值模拟中应用较多的湍流模型有k-ε双方程模型和Reynolds应力模型,其中k-ε双方程模型有3种,分别是标准k-ε模型,RNG k-ε模型和Realizable k-ε模型.根据4种湍流模型各自的应用特点,以及前期对IODVC采用不同湍流模型与实验的对比,本文选择RNG k-ε模型进行数值模拟.2.3 边界条件IODVC入口边界根据质量守恒定律和无旋假设,假定流速、湍动能k以及耗散率ε在入口截面上均匀分布.出口边界采用压力出口边界,出口压力设置为当前一个大气压水平.自由液面采用刚盖假定,液面近似为水平面,不考虑液面的波动,压强为标准大气压强值,液面垂向流速为零,其它变量的法向梯度为零.底面和壁面使用Launder和Spalding(1974)提议的标准壁面函数,垂向壁面的水平流速的法向梯度为零,底部壁面的垂向流速的法向梯度为零,满足壁面质量通量为零的条件.曝气转刷采用多重参考系模型,在转刷叶片半径范围内的流体区域建立独立的旋转参考系并定义转轴原点、旋转方向和转速,叶片与该转动区域内流体的相对速度为零,转动和静止区域重合的两个边界设置为interface.推流器借助风扇模型,定义为无限薄的理想推流器,主要作用是使流体获得轴向速度,对其引起的混合液旋转运动不作考虑.2.4 离散方法和求解算法对控制方程组的离散方法采用有限体积法,差分格式采用二阶迎风.求解方法采用Fluent提供的压力基隐式算法对IODVC流场进行稳态模拟,压力-速度耦合方法采用SIMPLE算法.计算中考虑重力影响,重力加速度设置为9.81 m · s-2.收敛标准设置为所有方程的残差绝对值小于10-4.3 数值模拟结果与分析3.1 单导流板IODVC流场模拟与问题分析在氧化沟工艺中,为了获得良好的混合和处理效果,氧化沟中混合液体循环流动的最小流速应该是0.15 m · s-1,而为了防止沟道中污泥的沉积,则沟道中混合液平均流速应该大于0.25 m · s-1(De Clercq et al.,1999).本文借助FLUENT对IODVC进行全沟道模拟后,利用后处理模块将IODVC计算域划分为4个不同流速大小的区域(<0.05、0.05~0.15、0.15~0.25、>0.25 m · s-1),进而统计各区域比例,得到单导流板IODVC的沟道中混合液的流速分布图(图 3).由图可见,混合液流速小于0.15 m · s-1的区域占总计算域的比例较高,达到41.53%,而相应流速大于0.25 m · s-1的区域占比较低,约为总计算域的32%.由此可见,在此流速分布情况下IODVC沟道内部混合液的整体混合效果不理想,低流速区域的大范围存在可能导致活性污泥的沉降和淤积,从而影响IODVC反应器的处理效果.图 4是单导流板IODVC的速度分布云图.由图可见,在IODVC两侧导流板的凹凸侧、左侧弯道出口处(隔板左侧上方)以及下沟道的上部区域(隔板下方)存在大范围的低速区,这是由于弯道出口处的混合液会由于惯性作用有向外扩散的趋势所致.图3 单导流板时IODVC速度分布图图4 单导流板时速度分布云图(m · s-1)由于IODVC采用上下沟道的结构设置,虽然导流板凹凸侧及下沟道的污泥沉降到底部会被高速循环的混合液冲击而不发生淤积,但大范围的低速区势必会造成回流现象,导致混合液逆向流动而造成动力消耗.为此,本文尝试通过加装双导流板及延长导流板末端长度来解决上述问题.3.2 加装双导流板对IODVC流场的优化研究双导流板的流场速度分布结果如图 5所示.对比图 3可知,双导流板使IODVC沟道中混合液低流速区域占比明显下降,相应高流速区域占比有较大幅度提高,其中混合液流速小于0.15 m · s-1的区域占比由41.53%下降至34%,流速大于0.25 m · s-1的区域占比由32%增加至41.5%,IODVC沟道中整体混合效果明显改善.通过图 6(双导流板IODVC速度分布云图)和图 4对比可知,双导流板可以有效提高下沟道特别是靠近隔板下方处混合液的流速,使下沟道内混合液流速分布更加均匀,减小了此处回流区范围,而且导流板凹凸两侧的低速区域较单导流板有明显改善,特别是在右侧导流板凹凸两侧处,由于高速液流的冲击,使IODVC弯道断面的流速分布更加均匀,混合液在上下沟道的过渡更加平稳,有利于整体流场的稳定.此外,在左侧弯道出口处(隔板左侧上方),由于双导流板的存在,回流区几乎全部消失.由此可见,双导流板减小了凹侧流道的宽度,改变了弯道处的流场特性,加剧了水流的紊流程度,增大了流速.图5 双导流板时IODVC速度分布图图6 双导流板的速度分布云图(m · s-1)3.3 延长导流板末端长度对IODVC流场的优化研究图 7是导流板末端不同长度时混合液流速大于0.25 m · s-1的区域占比.由图可见,当导流板末端延长至导流板半径的50%~100%时,沟道中混合液流速大于0.25 m · s-1的区域占比随导流板长度增加而增大;继续增加导流板长度,则占比呈减小趋势.其中,当导流板延长的长度等于导流板半径时,流速大于0.25 m · s-1的区域占比达到最大44.21%.图 8为导流板末端延长的长度等于导流板半径时的IODVC速度分布云图.由图可见,当导流板末端延长时,下沟道上部(隔板下方)及右侧弯道出口处的混合液流速较不延长(图 6)时有所提高,低速区范围明显缩减.可见,导流板末端延长的长度等于导流板半径时,IODVC内部流场更加趋于均匀,相应结构的优化更加趋于完善.图7 导流板不同延长长度时流速>0.25 m · s-1 区域占比图8 导流板延长长度等于导流板半径速度分布云图(m · s-1)在上述研究基础之上,进一步分析单导流板、双导流板和延长导流板(其长度等于导流板半径)等3种结构情况下弯道出口A-A、B-B断面流速分布,其结果见图 9.由图 9A可知,与单导流板相比,双导流板的断面流速分布更加均匀,在垂向坐标0.7~0.88 m范围内,流速明显升高,流速最大达到0.2 m · s-1,可有效防止此处形成回流;而延长导流板可使流速进一步提高.随着垂向坐标继续增加,双导流板及延长导流板的流速分布均接近直线上升趋势,其中在垂向坐标1.05 m附近,延长导流板使流速曲线有所波动,可能是导流板的末端和所取断面A-A比较靠近所致.由图 9B可知,在垂向坐标0~0.35 m范围内,三者流速分布相似,但在垂向坐标0.35~0.7 m范围内,对比3条曲线可知,双导流板和延长导流板可使此区域流速均值保持在0.15 m · s-1以上,整个断面流速分布优于单导流板的情况.具体参见污水宝商城资料或更多相关技术文档。