离心通风机叶轮工艺规程
玻璃钢离心通风机叶轮加强工艺
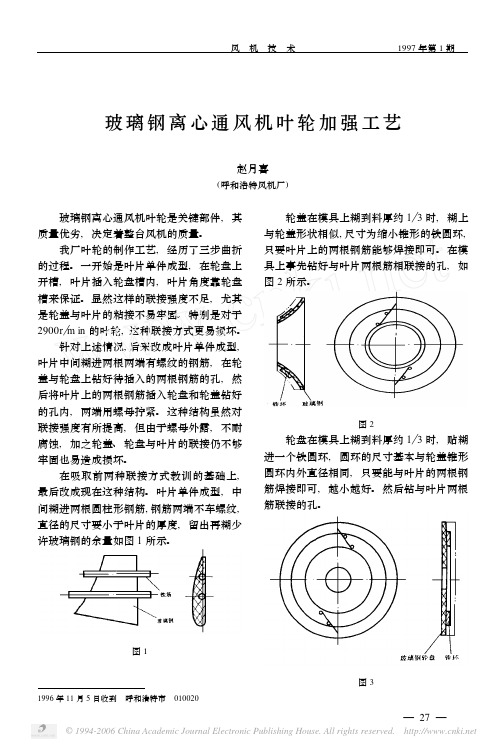
轮盖在模具上糊到料厚约 1 3 时, 糊上 与轮盖形状相似, 尺寸为缩小锥形的铁圆环, 只要叶片上的两根钢筋能够焊接即可。 在模 具上事先钻好与叶片两根筋相联接的孔, 如 图 2 所示。
针对上述情况, 后来改成叶片单件成型, 叶片中间糊进两根两端有螺纹的钢筋, 在轮 盖与轮盘上钻好待插入的两根钢筋的孔, 然 后将叶片上的两根钢筋插入轮盘和轮盖钻好 的孔内, 两端用螺母拧紧。 这种结构虽然对 联接强度有所提高, 但由于螺母外露, 不耐 腐蚀, 加之轮盖、 轮盘与叶片的联接仍不够 牢固也易造成损坏。
这种叶轮加强工艺虽然较复杂, 但强度 高, 金属件不外露, 保证即使叶轮达 2900r m in 也不会损坏。通过一年多的实践证明, 效 果良好, 无一用户反映质量问题。
图 4 Hale Waihona Puke 图 5单齿鼓风机研制成功
1996 年 10 月 18 日, 天津市经委委托市机电工业总公司在我厂通过了市经委九六年“产 学研”项目之一——DC80b 单齿鼓风机的样机鉴定会。市经委, 市科委, 机电总公司的领导 和来自各地的专家学者及用户代表五十余人参加了鉴定会。
样机完成后, 进行了性能试验和 500 小时连续运行试验, 结果表明样机主要技术性能指 标达到了设计要求, 并能适应长期连续运行的要求。
鉴定委员会认为: DC80b 单齿鼓风机技术全新、结构合理, 填补了国内空白, 并在性能 上接近 90 年代国际先进水平, 是一种值得推广的先进的节能产品。
单齿鼓风机的开发与应用, 填补了我国的一项空白。 必将受到广大用户的欢迎。
离心式风机操作规程
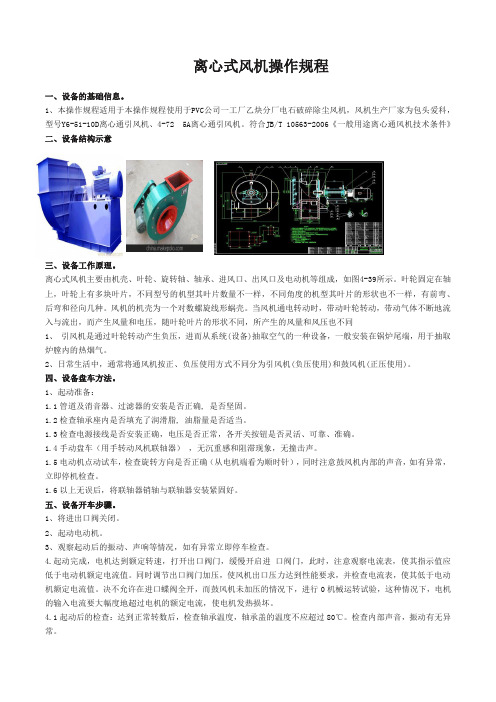
离心式风机操作规程一、设备的基础信息。
1、本操作规程适用于本操作规程使用于PVC公司一工厂乙炔分厂电石破碎除尘风机,风机生产厂家为包头爱科,型号Y6-51-10D离心通引风机、4-72 5A离心通引风机。
符合JB/T 10563-2006《一般用途离心通风机技术条件》二、设备结构示意三、设备工作原理。
离心式风机主要由机壳、叶轮、旋转轴、轴承、进风口、出风口及电动机等组成,如图4-39所示。
叶轮固定在轴上,叶轮上有多块叶片,不同型号的机型其叶片数量不一样,不同角度的机型其叶片的形状也不一样,有前弯、后弯和径向几种。
风机的机壳为一个对数螺旋线形蜗壳。
当风机通电转动时,带动叶轮转动,带动气体不断地流入与流出,而产生风量和电压,随叶轮叶片的形状不同,所产生的风量和风压也不同1、引风机是通过叶轮转动产生负压,进而从系统(设备)抽取空气的一种设备,一般安装在锅炉尾端,用于抽取炉膛内的热烟气。
2、日常生活中,通常将通风机按正、负压使用方式不同分为引风机(负压使用)和鼓风机(正压使用)。
四、设备盘车方法。
1、起动准备:1.1管道及消音器、过滤器的安装是否正确, 是否坚固。
1.2检查轴承座内是否填充了润滑脂, 油脂量是否适当。
1.3检查电源接线是否安装正确,电压是否正常,各开关按钮是否灵活、可靠、准确。
1.4手动盘车(用手转动风机联轴器),无沉重感和阻滞现象,无撞击声。
1.5电动机点动试车,检查旋转方向是否正确(从电机端看为顺时针),同时注意鼓风机内部的声音,如有异常,立即停机检查。
1.6以上无误后,将联轴器销轴与联轴器安装紧固好。
五、设备开车步骤。
1、将进出口阀关闭。
2、起动电动机。
3、观察起动后的振动、声响等情况,如有异常立即停车检查。
4.起动完成,电机达到额定转速,打开出口阀门,缓慢开启进口阀门,此时,注意观察电流表,使其指示值应低于电动机额定电流值。
同时调节出口阀门加压,使风机出口压力达到性能要求,并检查电流表,使其低于电动机额定电流值。
离心叶轮加工工艺

离心叶轮加工工艺一、主要材料及加工工艺:1,前盘:材料:LY12,数量:1件,1.1,切割成形,尺寸精度不到可车加工到位;1.2, 钻孔:专用分度盘钻孔;2,叶片:材料:LY12,数量:根据要求制作n件,2.1,剪板长料:一般长度为1000,宽度为:展开宽度+3;2.2落料:落料模冲切成条形;2.3成形:成形模冲制成形;2.4钻孔:钻模钻孔;3,后盘:材料:LY12,数量:1件,3.1,切割成形,内外圆车加工到位,3.2,钻孔:专用分度盘钻孔;4,轮毂:组合件:轮毂本体、法兰焊接后加工:4.1轮毂本体:材料Q235,4.1.1下料:棒料:(ФE+5)×(L+5);4.1.2粗车:光出端面基准及外圆ФE;4.2法兰:4.2.1下料:气割板料按δ(L2+10)×ФD×ФE;4.2.2车加工:法兰内圆车倒角C4-C5;4.3焊接:组对按图示L1定位法兰焊接点,先点焊,再满环焊;4.4车加工:4.4.1以一端端面为基准,夹本体外圆,车内圆,另一端端面,R,一端法兰平面;4.4.2反身,车另一法兰平面,R,端面;4.5划线、钻孔、攻丝完成;4.6刨键槽;4.7外协镀锌;二、装配:2.1前盘、后盘及叶片铆接:用LY12铝铆钉铆接,铆钉铆接后头部应规整、光滑,不允许有裂纹、歪斜、未铆紧及明显的铆痕缺陷;2.2铆接件与轮毂铆接;三、试验:具体按试验大纲进行3.1静、动平衡试验;3.2超速试验;附:DN-20双进风叶轮加工工艺:一、主要材料及加工工艺:1,前盘:材料:LY12,数量:2件,1.1,切割成形,尺寸精度不到可车加工到位;1.2, 钻孔:专用分度盘钻孔;2,叶片:材料:LY12,数量:根据要求制作n件,2.1,剪板长料:一般长度为1000,宽度为:展开宽度+3;2.2落料:落料模冲切成条形;2.3成形:成形模冲制成形;2.4钻孔:钻模钻孔;3,后盘:材料:LY12,数量:1件,3.1,切割成形,内外圆车加工到位,3.2,钻孔:专用分度盘钻孔;3.3,冲孔:专用冲模冲叶片定位嵌孔;4,轮毂:组合件:轮毂本体、法兰焊接后加工:4.1轮毂本体:材料Q235,4.1.1下料:棒料:(ФE+5)×(L+5);4.1.2粗车:光出端面基准及外圆ФE;4.2法兰:4.2.1下料:气割板料按δ(L2+10)×ФD×ФE;4.2.2车加工:法兰内圆车倒角C4-C5;4.3焊接:组对按图示L1定位法兰焊接点,先点焊,再满环焊;4.4车加工:4.4.1以一端端面为基准,夹本体外圆,车内圆,另一端端面,R,一端法兰平面;4.4.2反身,车另一法兰平面,R,端面;4.5划线、钻孔、攻丝完成;4.6刨键槽;4.7外协镀锌;四、装配:2.1二前盘及叶片铆接:用LY12铝铆钉铆接,铆钉铆接后头部应规整、光滑,不允许有裂纹、歪斜、未铆紧及明显的铆痕缺陷;2.2叶片纵向中心处划后盘固定位置;2.3后盘与轮毂对位铆接;2.4按叶片中心位置安装后盘和轮毂;2.5叶片和后盘焊接牢固;五、试验:具体按试验大纲进行3.1静、动平衡试验;3.2超速试验;。
离心式通风机操作规程

离心式通风机操作规程结构离心式通风机主要由叶轮、机壳、进风机口等部分配直联电机组成。
2原理、用途2.1原理离心通风机是利用旋转叶轮产生的离心力来排送气体。
2.2用途可作为工厂室内通风换气,输送空气和其它不自然的,对人体无害的,对钢铁材料无腐蚀性的气体。
气体内不许有粘性物质,所含的尘土及硬质颗粒物不大于150mg/ms,气体温度不得超过50℃。
3操作1开车前的准备(1)将进风调节门关闭,出风调节门稍开。
(2)检查风机各部间隙尺寸,转动部分与固定部分无碰撞及磨擦现象。
2开车(1)起动按钮进行试转,运行正常后可正式使用。
(2)将进风调节门打开,出风口调节门开至适当位置。
(3)在运转过程中经常检查轴承温度是否正常,轴承温升不得大于40℃,表温不得大于70℃,如发现风机有特殊噪音、振动撞击,轴承温度剧烈上升等反常现象时,必须立即紧急3停车关闭进风调节阀,按停止按钮。
4安全操作注意事项(1)只有在风机设备完全正常的情况下方可运转。
(2)如果风机设备在检修后开动时,则要注意风机各部位是否正常。
(3)为确保人身安全,风机维护必须在停机时进行。
4维护4.1定期清除风机内部积尘、污垢等杂质,防止锈蚀,保持设备清洁。
4.2除每次拆修后更换润滑剂外,正常情况下根据实际情况定期更换润滑剂,变速箱内保持正常油位。
4.3保持油漆完整,防止脱落、锈蚀。
4.4地脚螺丝、联轴器及各部联接处应紧固、可靠。
4.5各部密封应良好,在风机开、停及运转过程中应进行检查,检查发现的小故障应及时查明原因设法清除,如发现大故障应停机检查维修。
5常见故障及排除方法。
离心通风机叶轮的设计方法简述

离心通风机叶轮的设计方法简述如何设计高效、工艺简单的离心通风机一直是科研人员研究的主要问题,设计高效叶轮叶片是解决这一问题的主要途径。
叶轮是风机的核心气动部件,叶轮内部流诱导风机动的好坏直接决定着整机的性能和效率。
因此国内外学者为了了解叶轮内部的真实流动状况,改进叶轮设计以提高叶轮的性能和效率,作了大量的工作。
为了设计出高效的离心叶轮, 科研工作者们从各种角度来研究气体在叶轮内的流动规律, 寻求最佳的叶轮设计方法。
最早使用的是一元设计方法[1] ,通过大量的统计数据和一定的理论分析,获得离心通风机各个关键截面气动和结构参数的选择规律。
在一元方法使用的初期,可以简单地通过对风机各个关键截面的平均速度计算,确定离心叶轮和蜗壳的关键参数,而且一般叶片型线采用简单的单圆弧成型。
这种方法非常粗糙,设计的风机性能需要设计人员有非常丰富的经验,有时可以获得性能不错的风机,但是,大部分情况下,设计的通风机效率低下。
为了改进,研究人员对叶轮轮盖的子午面型线采用过流断面的概念进行设计[2-3] ,如此设计出来的离心叶轮的轮盖为两段或多段圆弧,这种方法设计的叶轮虽然比前一种一元设计方法效率略有提高,但是该方法设计的风机轮盖加工难度大,成本高,很难用于大型风机和非标风机的生产。
另外一个重要方面就是改进叶片设计,对于二元叶片的改进方法主要为采用等减速方法和等扩张度方法等[4] ,还有采用给定叶轮内相对速度W 沿平均流线m 分布[5] 的方法。
等减速方法从损失的角度考虑,气流相对速度在叶轮流道内的流动过程中以同一速率均匀变化,能减少流动损失,进而提高叶轮效率;等扩张度方法是为了避免局部地区过大的扩张角而提出的方法。
给定的叶轮内相对速度W 沿平均流线m 的分布是柜式风机通过控制相对平均流速沿流线m 的变化规律,通过简单几何关系,就可以得到叶片型线沿半径的分布。
以上方法虽然简单,但也需要比较复杂的数值计算。
随着数值计算以及电子计算机的高速发展,可以采用更加复杂的方法设计离心通风机叶片。
叶轮的加工工序

叶轮的加工工序如下:工序1:根据叶轮加工必须以流道找正的原则, 工序 1 采用三爪自定心卡盘反撑叶轮进口流道的装夹方式,实现以进口流道找正,然后先车叶轮大外圆,再粗车内孔。
由于叶轮外圆尺寸相对较大,中间部分有叶片形成断续切削,因此切削速度较慢,进给量较小。
工序2:为了保证以叶轮出水口流道作为加工基准,我们设计了专用三爪夹紧定位机构。
定位块为圆锥形,在弹簧力的作用下可以保证其和叶轮流道两侧接触并可上下移动,以弥补叶轮出水口流道宽度尺寸在铸造过程中产生的误差。
这种定位机构定位精度高,速度快,使用方便,大大缩短了装夹找正时间。
此工序可完成叶轮后盖板,中心孔及其他部位的全部加工。
工序3:为了保证叶轮入口外径对孔的跳动要求。
此工序采用专用软三爪装夹。
在加工前先用三爪夹住一个圆柱体对软爪夹紧部位的内孔和底面进行校正加工,加工后的直径尺寸要和叶轮的外径基本相同,这一点非常重要。
因为三爪自定心卡盘上决定卡盘定位精度的平面螺纹精度并不很高,完全利用三爪本身的定位精度不能满足叶轮的形位公差设计要求,因此,必须根据叶轮直径的大小,校正软爪的夹紧部位,这样便能使软爪的夹紧部位与车床的回转中心重合。
如果改变加工叶轮的规格且外径变化较大,则应重新校正,这样便可避免由于卡盘平面螺纹工作部位的改变而影响卡盘的装夹定位精度。
叶轮装夹时,要把叶轮已加工成的后盖板平面紧靠已校正的软爪底面,这样加工可保证叶轮的形位公差。
轴的加工工艺:1、先装装夹卡盘;2、装轴,用卡盘和顶尖将轴固定;3、外圆找正;4、先车用于固定中心架处的轴颈,保留一定的加工余量;5、固定中心架;6、车轴的一端面,切长短成,钻中心孔;7、掉头车轴的另一端面,切长短成,钻中心孔;8、按图纸要求车轴的各表面,车螺纹成活,磨部位保留0.5mm加工余量;9、划键槽线;10、铣键槽;11、按图纸要求磨各个部位。
离心风机叶轮装配改良工艺

江苏双保空调有限公司
离心风机叶轮装配改良工艺
高速运转的离心风机叶轮,在断裂严重时叶片会飞入被冷却的主电机,给设备造成直接经济损失,因叶轮粉碎后增加了风机的维修量和备件的替代用度。
从而造成主电机事故,为了提高产品质量和给用户造成不必要的经济损失,介绍相干的技术改善方案。
离心风机改良时必须要保证了以下几点:
(1)以保证叶轮与进风口的保险间隔;新叶轮的宽度≤原叶轮的宽度。
(2)保证能顺利安装;新叶轮的外径≤原叶轮的外径。
加工工艺性能优于原叶轮的工艺机能,必须利于各配件的加工成型及叶片与轮盘、轮盖的总装,新叶轮叶片数量少于原叶轮叶片的数目。
(3)同时满足风机运行所必须的保险系数;全部叶轮的强度、刚度大于原叶轮。
配装新叶轮风机的氛围动力性能优于组装原叶轮的风机。
履行具体的阐发、计算与理论验证,阐发以上各点要求。
以保证新设计叶轮的保险可靠性和氛围动力机能。
(4)保证叶轮正确的旋向及各叶片与轮盘、轮盖的垂直度后,改良前叶轮在铆接组装时需要注意:将叶轮两端的凸耳部分穿入轮盘、轮盖上相应的装配定位孔。
盘曲叶片两头的凸耳部分,将4个凸耳分袂与轮盘、轮盖铆接紧密而成。
离心风机叶轮制作工艺流程

离心风机叶轮制作工艺流程英文回答:Centrifugal fan impeller manufacturing process involves several steps to ensure the production of high-quality impellers. The process can be divided into the following stages:1. Design and Engineering: The first step in manufacturing a centrifugal fan impeller is designing and engineering the impeller. This involves determining the impeller size, shape, and blade angle based on the specific requirements of the fan system. Computer-aided design (CAD) software is often used in this stage to create a detailed design.2. Material Selection: Once the impeller design is finalized, the next step is to select the appropriate material for manufacturing the impeller. Common materials used for impeller manufacturing include aluminum, steel,and plastic. The material selection is based on factorssuch as cost, strength, and corrosion resistance.3. Pattern Making: In this stage, a pattern of the impeller is created using wood, metal, or plastic. The pattern is an exact replica of the final impeller and is used to create the mold for casting or forging the impeller.4. Casting or Forging: The pattern is used to create a mold, which is then used for casting or forging the impeller. Casting involves pouring molten metal into the mold and allowing it to solidify. Forging, on the other hand, involves shaping the metal by applying pressure and heat. Both casting and forging methods can be used to manufacture impellers, depending on the material and design requirements.5. Machining: After the impeller is cast or forged, it undergoes machining to achieve the final shape and dimensions. Machining processes such as turning, milling, and drilling are used to remove excess material and create the desired shape. This stage requires precision andaccuracy to ensure the impeller meets the design specifications.6. Balancing: Balancing is a critical step in impeller manufacturing to ensure smooth operation and minimize vibrations. The impeller is balanced by removing material from specific areas or adding weights to achieve the desired balance. Dynamic balancing machines are used to measure and correct any imbalance in the impeller.7. Surface Treatment: The final step in the manufacturing process is surface treatment. This involves applying coatings or finishes to protect the impeller from corrosion and improve its appearance. Common surface treatments for impellers include painting, powder coating, or anodizing.中文回答:离心风机叶轮的制作工艺流程包括以下几个步骤,以确保生产出高质量的叶轮:1. 设计与工程,制作离心风机叶轮的第一步是设计和工程化叶轮。
风机叶轮加工工艺流程

风机叶轮加工工艺流程下载温馨提示:该文档是我店铺精心编制而成,希望大家下载以后,能够帮助大家解决实际的问题。
文档下载后可定制随意修改,请根据实际需要进行相应的调整和使用,谢谢!Download tips: This document is carefully compiled by theeditor. l hope that after you downloadthem,they can help yousolve practical problems. The document can be customized andmodified afterdownloading,please adjust and use it according toactual needs, thank you!风机叶轮加工工艺流程简述如下:设计与原料准备阶段:①设计图纸:依据使用需求,完成叶轮的结构设计及强度校核。
②选材:根据设计要求选择合适材质,如铝合金、钢材或复合材料。
制造阶段:①原料处理:对材料进行预处理,如合金配料、塑料粉料混合。
②成型加工:a.铸造/锻造:对于金属材料,可通过铸造或锻造形成初步形状;b.注塑成型:塑料叶轮则通过注塑机注入模具成型。
③机械加工:使用CNC等机床进行粗加工与精加工,确保尺寸与形状精度。
④热处理:对金属叶轮进行热处理增强其力学性能。
动平衡与检验阶段:①动平衡调整:通过测振传感器与转速传感器检测,调整叶轮重量分布,确保运转平稳。
②超速试验:进行叶轮超速试验,验证高速运转下的安全性。
③表面处理:喷漆或防腐处理,提升叶轮耐候性。
组装与测试阶段:①组装:将叶轮与轴、轴承等部件组装成完整风机单元。
②性能测试:在试验台上进行风量、风压、效率及噪音等测试,确保符合设计标准。
包装与发货:①最终检验:进行全面质量检验,确保产品符合出厂要求。
②包装:对叶轮或整机进行适当防护包装。
③发货:根据订单安排物流,将产品安全运输至客户指定地点。
离心风机叶轮制作工艺流程

离心风机叶轮制作工艺流程The manufacturing process of centrifugal fan impellers involves several steps. First, the design of the impelleris created using computer-aided design (CAD) software. This includes determining the dimensions, shape, and number of blades for the impeller.离心风机叶轮的制作工艺包括几个步骤。
使用计算机辅助设计(CAD)软件进行叶轮的设计。
这包括确定叶轮的尺寸、形状和叶片数量。
Once the design is finalized, a pattern or mold is createdto produce the impeller. This can be done through various methods such as casting or machining. In casting, a pattern is made from wood, resin, or metal and then used to createa mold. The mold is then filled with molten metal such as aluminum or stainless steel to create the impeller shape.一旦设计完成,就会制作一个模型或模具来生产叶轮。
这可以通过各种方法实现,比如铸造或加工。
在铸造过程中,用木材、树脂或金属制作模型,并用它来制作模具。
然后,将铝或不锈钢等熔融金属注入模具中,以得到叶轮形状。
After casting, the impeller may go through additional processes such as heat treatment to improve its strength and durability. This involves subjecting the impeller to controlled heating and cooling cycles to modify its microstructure.在铸造完成后,叶轮可能需要经过其他工艺处理,比如热处理,以提高其强度和耐久性。
离心风机叶轮导风板制作工艺流程
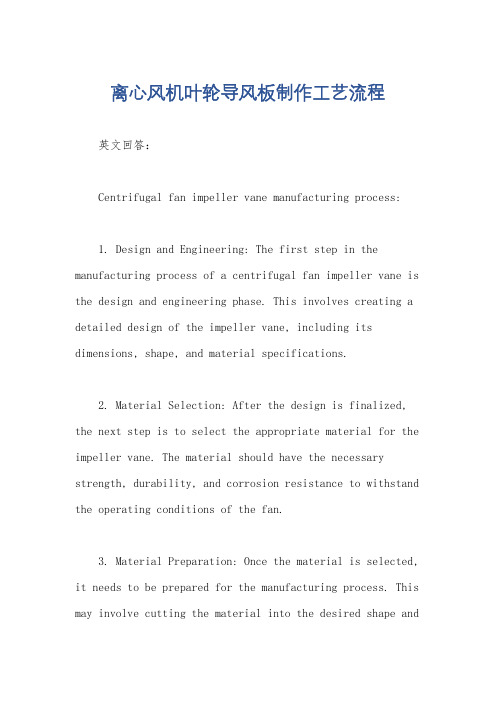
离心风机叶轮导风板制作工艺流程英文回答:Centrifugal fan impeller vane manufacturing process:1. Design and Engineering: The first step in the manufacturing process of a centrifugal fan impeller vane is the design and engineering phase. This involves creating a detailed design of the impeller vane, including its dimensions, shape, and material specifications.2. Material Selection: After the design is finalized, the next step is to select the appropriate material for the impeller vane. The material should have the necessary strength, durability, and corrosion resistance to withstand the operating conditions of the fan.3. Material Preparation: Once the material is selected, it needs to be prepared for the manufacturing process. This may involve cutting the material into the desired shape andsize or shaping it through casting or forging.4. Machining: The prepared material is then subjected to machining processes to achieve the final shape and dimensions of the impeller vane. This may involve turning, milling, drilling, or grinding operations.5. Balancing: Balancing is a critical step in the manufacturing process of a centrifugal fan impeller vane. It ensures that the impeller vane rotates smoothly without causing any vibration or imbalance. Balancing can be achieved through dynamic balancing techniques.6. Assembly: Once the impeller vane is machined and balanced, it is ready for assembly. The impeller vane is typically attached to a central hub using bolts or welding, depending on the design and material of the impeller vane.7. Quality Control: Throughout the manufacturing process, strict quality control measures should be implemented to ensure the final product meets the required specifications and standards. This may involve inspections,testing, and documentation of the manufacturing process.中文回答:离心风机叶轮导风板制作工艺流程:1. 设计与工程,离心风机叶轮导风板制作工艺的第一步是设计与工程阶段。
风机叶轮加工工艺流程

风机叶轮加工工艺流程英文回答:The manufacturing process of a fan impeller involves several steps to ensure precision and quality. Here is a general overview of the process:1. Design and Engineering: The first step is to design the impeller based on the specific requirements and specifications. This includes determining the size, shape, and number of blades, as well as the material to be used.2. Material Selection: Once the design is finalized, the appropriate material is selected. Common materials used for fan impellers include aluminum, stainless steel, and composite materials.3. Cutting and Machining: The selected material is then cut into the desired shape using CNC (Computer Numerical Control) machines. This process involves using variouscutting tools to remove excess material and create thebasic shape of the impeller.4. Balancing: Balancing is a crucial step to ensure smooth operation and minimize vibration. The impeller is placed on a balancing machine, and any excess material is removed from specific areas to achieve the required balance.5. Surface Finishing: The impeller is then subjected to surface finishing processes like polishing, grinding, or sandblasting. This helps to improve the appearance, remove any imperfections, and prepare the surface for subsequent treatments.6. Heat Treatment: Some materials may require heat treatment to enhance their mechanical properties. This process involves heating the impeller to a specific temperature and then cooling it down gradually to achievethe desired hardness and strength.7. Quality Inspection: Before assembly, the impeller undergoes a thorough quality inspection. This includesdimensional checks, visual inspection for any defects or damage, and testing for balance and performance.8. Assembly: Once the impeller passes the quality inspection, it is ready for assembly. This involves attaching it to the fan shaft and securing it with appropriate fasteners.9. Testing: After assembly, the fan with the impeller is subjected to performance testing. This includes checking factors like airflow, pressure, and noise levels to ensure that the fan meets the required specifications.10. Packaging and Shipping: Finally, the finished fan with the impeller is carefully packaged to prevent any damage during transportation and shipped to the customer.中文回答:风机叶轮的加工工艺流程包括以下几个步骤,以确保精度和质量:1. 设计与工程,首先需要根据具体要求和规格设计叶轮。
供风机叶轮加工工艺流程

供风机叶轮加工工艺流程Manufacturing the impeller of a centrifugal fan requires a precise and complex process to ensure efficiency and durability. 风机叶轮的加工需要进行精密而复杂的工艺流程,以确保其效率和耐久性。
From casting to final machining, every step plays a crucial role in shaping the impeller's performance. 从铸造到最终加工,每一个步骤都在塑造叶轮的性能方面发挥着至关重要的作用。
The first step in the process is casting, where the impeller shape is formed through a mold and molten metal. 过程的第一步是铸造,在这一步中,通过模具和熔化的金属形成叶轮的形状。
This step is vital as it determines the initial shape and design of the impeller before any further processing. 这一步至关重要,因为它决定了叶轮在任何进一步加工之前的初始形状和设计。
After casting, the impeller undergoes various machining processes to refine its shape and improve its performance. 铸造后,叶轮将经过各种加工过程,以完善其形状并提高其性能。
This includes processes such as turning, milling, drilling, and grinding to ensure precise dimensionsand smooth surfaces. 这包括车削、铣削、钻削和磨削等过程,以确保精确的尺寸和光滑的表面。
离心通风机叶轮工艺规程

离心通风机叶轮工艺规程1、备料:备齐叶轮的所有零部件,外购件和标准件,检查材料、旋向是否正确。
2、定位后盘:将后盘固定于平台上;3、点叶片:将叶片按重量选配,对称放置,找正垂直度,确定旋向正确后点焊;任意三个相邻叶片,出口端的两弦长之差8#及以下<1.5mm,8#以上<3mm。
4、检验:检验叶片垂直度,叶尖尺寸、叶片外圆符合图纸;5、点焊前盘:找正、压紧后点焊;6、检验:检验叶轮旋向、尺寸符合要求;7、焊接;先焊接叶片和后盘的角焊缝,再焊叶片和前盘的角焊缝,对称施焊以保证后盘平面度;8、铆轮毂:后盘与轮毂配做孔,铆轮毂,铆接件间隙在两倍铆钉直径范围内不得大于0.1mm,其余部位不得大于0.3mm。
铆钉严禁松动,其头部应光滑平整。
8、校形:校正前后盘平面度、圆跳动符合要求。
9、振动时效处理。
10、车(割):加工叶轮外圆、进口处直径、端面符合要求。
11、检验:检验叶轮尺寸符合要求;12、标识:在轮毂上进行标识。
13、平衡:叶轮动平衡校正轮盘轮盖外圆分别为左右校正平面,平衡配重在同一平面不得超过两块,相对相位差不得大于90%%d,平衡配重块外边缘与叶轮校正平面外边缘距离为10mm。
配重块厚度不得大于被焊盘厚度,外形整洁,材质与母材相同。
14、检验:跟踪检验平衡过程,叶轮平衡达到要求精度要求。
15、叶轮的超速试验(可以在整机检验时进行)。
16、表面喷涂:清除风机上的油污,多肉、毛刺、锈蚀,按要求进行表面喷涂,并符合产品要求。
17、检验:检验表面喷涂符合产品要求离心通风机前盘压制工艺规程1、下料:按图样要求选择材质及材料厚度,依据相应的工艺图样尺寸进行划线及割制,并进行去刺及铁瘤处理。
2、卷锥:按相应的工艺图样要求卷锥,并保证台锥对接口处对接平齐,然后方可两个面均应进行满焊,焊接要求依据JB/T10213-2000之转动件的焊接标准进行。
焊接完毕后两面应磨平。
3、校锥:按照相应的工艺图样要求进行校整型处理,保证工件对称,上下圆的◎≤5‰,保证工件表面光滑无压痕及锤迹等缺陷。
离心通风机工艺守则
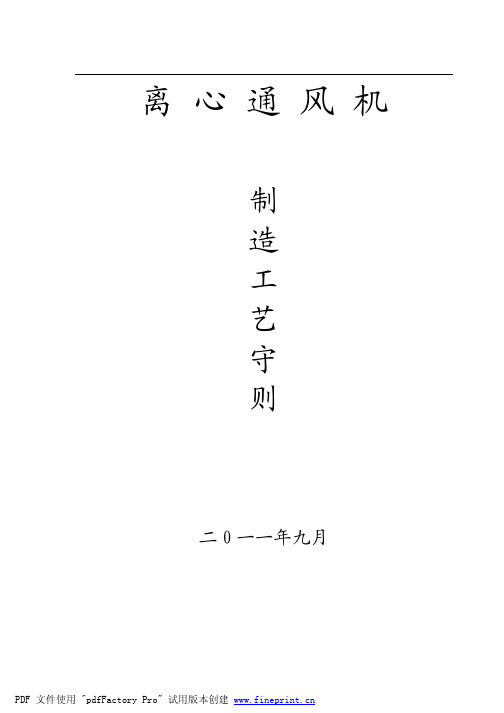
留余量单边 15mm 留余量单边 20mm
留余量单边 15mm 留余量单边 20mm
(2) 叶轮后盘毛坯尺寸内、外圆根据净尺寸:
机号规格
内孔
外圆
≤6.3
留余量单边 5mm
留余量单边 6mm
≥7.1~12.5
留余量单边 6mm
留余量单边 8mm
≥14~20
留余量单边 8mm
留余量单边 10mm
(3)前盘、后盘的内孔、外圆毛坯尺寸误差均按 JS15。
铁水溅进割嘴发生回火或灭火。 4 工作时按规定穿戴防护用品。
第五章 调平、校正工艺守则
PDF 文件使用 "pdfFactory Pro" 试用版本创建
1、 使用压力机调平校正时工作台必须清洁,不允许在压力机工作台上
用手锤敲击。使用手锤校正时,应检查锤头与锤柄是否坚固完好。 严禁带手套操作大锤。
4、 按已划好的实样制作样板,并考虑工艺留量和焊接收缩量。
A:工艺留量:
(1) 叶轮前盘毛坯尺寸内、外圆根据展开净尺寸:
机号规格
内圆
外圆
≤6.3
留余量单边 10mm 留余量单边 10mm
PDF 文件使用 "pdfFactory Pro" 试用版本创建
≥7.1~12.5 ≥14~20
2
放样、号料工艺守则 ······ · ··
3
剪切工艺守则 · · · · · · · · · · · ·
7
气割、气焊工艺守则 · · · · · · · 10
调平、调正工艺守则 · · · · · · · · 12
钻孔、冲裁、压型工艺守则 · · · · 13
手工电弧焊工艺守则 · · · · · · · 16
离心风机工程技术规范(20210419225943)

基本设计1.离心风机(包括辅助设备)应按照使用寿命至少20年(不包括正常易损件),预期不间断地运行至少3 年进行设计和制造。
除买方作出特殊书而批准外,卖方提供的产品应在卖方的设冲和制造经验范闱内,并且至少应有同样或相似型号的产品在相同或相似操作条件下成功运行两年或者更长时间的业绩。
2.离心风机机器辅助设备应适用于指定的环境条件。
除另有规定外,离心风机及其辅助设备应适用于户外自动和连续操作。
3.买方应在离心风机数据表中规定设备的正常操作点、额外操作点以及其他操作点,数据表格式参见附录A。
4.离心风机应满足离心风机数据表上规定的所有操作条件,并能在规定的工况下连续稳定运行。
5.离心风机机组(包括联轴器,齿轮变速器等)的设计应保证其在跳闸速度和安全阀设定值以下安全运行。
6.所有电气设备、仪表、元件及材料的选择与安装应符合买方技术文件上规定的危险场所的要求。
危险场所类别、气体组别和温度组别按GB 3836或IEC电气设备维修场所分类标准划分。
如果采用NFPAStd70-2005 第500、501、502和504条或其他标准,则应经买方认可。
7.驱动机的额定功率应大于或者等于离心风机额定工况点功率(包括各种机械损失)的110轧8.风机的供货范围参见附录B,卖方的供货范围最终应由买卖双方共同商定。
9.买方和卖方应共同探讨风机的布置,包括管道和辅助设备。
布置时应考虑操作和维修所需的空间区域和安全通道。
10.符合以下任何一条,宜采用两端支撑的风机,轴承安装在独立的支撑机架上:a.鼓风机(压力送风机)叶轮直径大于1500mm;b.驱动机额定功率大于或等于200Kw;c.转速大于1800r/min:d.设计温度大于或等于220r:f.输送腐蚀性或者磨蚀性介质:g.输送可能导致转子不平衡的含沉淀污垢的介质。
11.风机性能应基于风机进口与出口法兰处的静压力升值。
卖方有责任提供卖方供货范围内所有相关零部件的压力损失值。
12.除另有规定外,风机应具有在60席额定流量或更小流量下连续运转的能力。
离心式风机安装工艺标准

离心式风机安装工艺标准火电工程工艺标准版本№.1 专业标准号Q/GHG-104-20-2001 工艺标准名称离心式风机安装工艺标准工艺质量标准确保工艺流程规范化、质量标准统一化,安装质量优良化序号工艺步骤施工工艺标准图示说明1 施工准备1.1 技术准备1.1.1 编写施工作业指导书按作业指导书编制要求1.1.2提出加工件(垫铁)计划数量准确齐全1.2 施工准备1.2.1 设备清点数量齐全1.2.2 基础复查基础外形尺寸符合图纸要求基础定位尺寸基础标高尺寸地脚螺栓孔及埋件数量尺寸1.2.3 垫铁布置布置合理、放置面凿平1.2.4 设备基础清理无油污、杂物1.2.5 地脚螺栓检查清理无锈蚀、油污、外观损伤叶轮旋转方向、叶符合图纸2.1片弯曲方向2.2 叶片焊缝无裂纹、砂眼、咬边及未焊透2.3 叶轮与轴配合紧密无松动2.4 叶轮晃度轴向不大于2㎜径向2.5 机壳检查无裂纹、法兰面平整、耐磨衬板牢固、平整2.6机壳进出口位置及角度与叶轮一致、符合图纸2.7 检查主轴无弯曲、加工面光洁2.8 调节档板检查无变形、损伤、动作灵活、同步固定牢固3 基础划线基础纵横中心线偏差±10㎜中心线距离偏差±3㎜地脚螺栓偏差±10㎜标高偏差±5㎜4 基架轴承座安装基架与基础纵横中心线偏差±10㎜轴承座标高偏差±5㎜轴承座水平度偏差≤0.1㎜5 风机机壳安装下半部机壳垂直度偏差符合图纸中心及标高偏差法兰面密封涂密封胶、嵌入石棉绳,螺栓紧力一致,螺栓露出长度一致6 转子安装转子标高偏差不大于±10㎜转子中心与基础中心偏差不大于±10㎜转子轴承水平度偏差不大于0.1㎜/m全长不大于0.1㎜转子与轴承座同心度偏差≤5㎜轴承座洼窝检查符合图纸轴承膨胀间隙检查符合图纸轴承推力间隙检查0.3~0.4轴承座油室清理检查清洁、无尘、锈蚀轴承冷却室水压试验严密不漏转子与机壳轴封的径向间隙2~3㎜7 集流器安装集流器与叶轮间装配符合图纸叶轮与外壳间间隙叶轮与机壳之间轴向间隙8 调节档板门安装调节挡板开启及开度开启灵活、开度一致调节挡板固定牢靠调节挡板与机2~3㎜9 电机安装电机轴瓦接触角60°~75°电机轴瓦接触面≥1点/㎝2轴承型号及间隙符合设计电动机磁力中心偏差联轴器中心找正符号验标炉3~10规定见《厂供油箱安装工艺标10 润滑油站安装准》符合《规范》(锅炉篇)炉11 分部试运7.4.1.4条规定。
- 1、下载文档前请自行甄别文档内容的完整性,平台不提供额外的编辑、内容补充、找答案等附加服务。
- 2、"仅部分预览"的文档,不可在线预览部分如存在完整性等问题,可反馈申请退款(可完整预览的文档不适用该条件!)。
- 3、如文档侵犯您的权益,请联系客服反馈,我们会尽快为您处理(人工客服工作时间:9:00-18:30)。
离心通风机叶轮工艺规程
1、备料:备齐叶轮的所有零部件,外购件和标准件,检查材料、旋向是否正确。
2、定位后盘:将后盘固定于平台上;
3、点叶片:将叶片按重量选配,对称放置,找正垂直度,确定旋向正确后点焊;任意三个
相邻叶片,出口端的两弦长之差8#及以下<1.5mm,8#以上<3mm。
4、检验:检验叶片垂直度,叶尖尺寸、叶片外圆符合图纸;
5、点焊前盘:找正、压紧后点焊;
6、检验:检验叶轮旋向、尺寸符合要求;
7、焊接;先焊接叶片和后盘的角焊缝,再焊叶片和前盘的角焊缝,对称施焊以保证后盘平
面度;
8、铆轮毂:后盘与轮毂配做孔,铆轮毂,铆接件间隙在两倍铆钉直径范围内不得大于0.1mm,
其余部位不得大于0.3mm。
铆钉严禁松动,其头部应光滑平整。
8、校形:校正前后盘平面度、圆跳动符合要求。
9、振动时效处理。
10、车(割):加工叶轮外圆、进口处直径、端面符合要求。
11、检验:检验叶轮尺寸符合要求;
12、标识:在轮毂上进行标识。
13、平衡:叶轮动平衡校正轮盘轮盖外圆分别为左右校正平面,平衡配重在同一平面不得超
过两块,相对相位差不得大于90%%d,平衡配重块外边缘与叶轮校正平面外边缘
距离为10mm。
配重块厚度不得大于被焊盘厚度,外形整洁,材质与母材相同。
14、检验:跟踪检验平衡过程,叶轮平衡达到要求精度要求。
15、叶轮的超速试验(可以在整机检验时进行)。
16、表面喷涂:清除风机上的油污,多肉、毛刺、锈蚀,按要求进行表面喷涂,并符合产
品要求。
17、检验:检验表面喷涂符合产品要求
离心通风机前盘压制工艺规程
1、下料:按图样要求选择材质及材料厚度,依据相应的工艺图样尺寸进行划线及割制,并
进行去刺及铁瘤处理。
2、卷锥:按相应的工艺图样要求卷锥,并保证台锥对接口处对接平齐,然后方可两个面均
应进行满焊,焊接要求依据JB/T10213-2000之转动件的焊接标准进行。
焊接完
毕后两面应磨平。
3、校锥:按照相应的工艺图样要求进行校整型处理,保证工件对称,上下圆的◎≤5‰,
保证工件表面光滑无压痕及锤迹等缺陷。
4、压弧:按图样要求选用相关的模具及设备(油压机、冲床)进行压制。
(1)若要一次性压制成型(平板式及锥体式)
就要选用相应的工艺前盘及油压机设备以及相应的模具进行一次性压成型。
(2)若要分段局部压制则应选用相应的工艺前盘及模具在冲床设备上按以下要求进行压制:
A.按其相应的模具,在冲压设备上按装模具进行调试,保证上下模合模后的凸凹
模板分别平齐固定好上下模具。
B.在其设备上调滑块及上模,使其在设备滑块在使用状态的上止点后能方便的放
进未压的工件,并保证其旋转方便。
(保证其上下往复运行正常,不让有碰撞及
其它有损模具及设备的现象存在)
C.按照图样要求的弧型弦高的1/5-1/10下调滑机构,按所需的位置高度支撑好
支撑架,使工件在下模的最高点上平行于工作台。
使工件能在压制时方便旋转
压制。
D.启动设备开始压制,压制时应使工件均匀的旋转,旋转行程在工件的外圆上的
旋长为10-25mm,使工件均匀的旋
转360º。
E.压完一周后(即旋转360º)订机,然后松掉其设备的锁紧机构,向下调整滑块及上
模,调整的行程同样使工件弧型高的1/5-1/10后,锁紧机构启动设备,同样均匀
旋转行程使工件外圆上弦长的10-25mm进行压制。
F.如此反复5-10次压制后,停机取出工件进行检查,测量工件外径大于图样尺寸的
5-10mm之内,(在直径上)即Ød-(3-8mm);弧锥高度大于图样尺寸的5
mm,即H+5mm;凡保证以上要求的均为合格。
G.如未达到F所要求的尺寸范围,特别是进口处和外径即弧锥高度尺寸,可将工件放
回模具,再次进行压制,在此同时还可上调支架高度的5-10mm,使让工件样图
样和F的要求即ØD+(5-10mm);Ød+(3-8mm)H+5mm的要求为合格。
5、检验:按其加工要求F及图样的其它要求的,并保证工件平整,及外径和内孔的加工尺
寸之要求的均为合格,检验合格后做记转序。
离心通风机叶片加工工艺规程
1、下料:根据图纸要求选择材料,切割(剪切)成形;
2、称重:称叶片重量,记录标识。
3、成形:按图纸要求弯曲成形,注意叶轮旋向。
4、检验:检验叶片形线与样板误差<1mm。