2.3 塑件的工艺性
(完整版)塑料及加工工艺
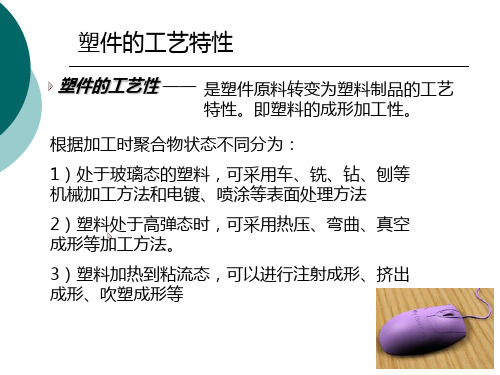
吹塑
一步法 挤—拉—吹瓶工艺流程图 1—挤出管坯;1—管坯定型;3—型坯移至拉伸吹塑模具; 4—拉伸吹塑;5—脱模
22
吹塑
吹塑成型工艺演示
23
吹塑
拉伸吹塑工艺控制 : ✓1、原材料的选择:由于拉伸制品要求具有较高的拉伸强度、 冲击强度、刚性、透明度和光泽、对氧气、二氧化碳和水蒸气 的阻隔性。主要应用的材料有:PET、PVC、PP、PC等。 ✓2、型坯成பைடு நூலகம்:透明度高,均质,内部无应变、外观无缺点 ✓3、拉伸工艺 :拉伸温度、拉伸倍率
装置、卷取装置
控制系统
3、压注成型
主要用于热固性塑料的成型方法,有模压和层压法两种。 1)模压成形:压塑成形,原理将定量的塑料原料置于金 属模具中,闭合模具,加热加压,是塑料原料塑化流动充 满模腔,同时发生化学反应固化成形。
模具闭合 热固性塑料放入加料 室 受热熔融 塑料在压力下经 浇注系统充满型腔 固化成型 开模取件
注射成型优点
1)可一次成形出外形复杂,尺寸精确和带嵌 件制品 2)可以方便的利用一套模具,成批生产尺寸、 形状、性能完全相同的产品。 3)生产性能好,成形周期短,一般制件3060秒成形。可实现自动化或半自动化作业。 4)较高的生产效率和技术经济指标。
2 挤出成型
挤出成型原理
又称挤塑成形,主要适合热塑性塑料成形,也适合一 部分流动性比较好的热固性塑料和增强塑料成形。
压注成型特点
1.加料前模具处于闭合状态。
2.塑件飞边很薄,尺寸准确,性能均匀,质量较高。 3.可以成型深孔、形状复杂、带有精细或易碎嵌件 的塑件。 4.模具结构相对复杂,制造成本较高,成型压力较 大,操作复杂,耗料比压缩模多。 5.气体难排除,一定要在模具上开设排气槽。
塑件制件结构工艺特性 3
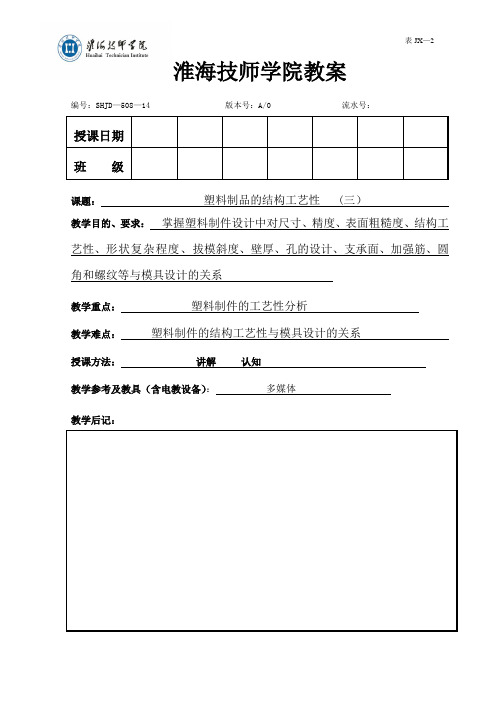
表JX—2淮海技师学院教案编号:SHJD—508—14 版本号:A/0 流水号:课题:塑料制品的结构工艺性 (三)教学重点:塑料制件的工艺性分析教学难点:塑料制件的结构工艺性与模具设计的关系授课方法:讲解认知教学参考及教具(含电教设备):多媒体教学后记:板书设计塑料制件的结构工艺性(3)【组织教学】【回顾旧课】1、塑件的形状如何设计?2、塑件的壁厚如何设计?3、什么是脱模斜度?如何设计?引言:塑料制件由于使用要求的不同,其种类繁多、形状各异,而塑料注塑成型工艺条件、注射成型设备与注射成型模具却有一定的规范要求的。
制件的结构工艺性能,是指塑料制件成型生产时对模具结构、成型工艺的适应程度。
塑料制件结构工艺性能的合理与否主要取决于制件设计。
塑料制件结构工艺性合理,即可使成型工艺稳定,保证制件质量,提高生产效率,又可使模具结构简单化,降低模具设计与制造成本。
因此,在设计制件时应充分考虑其结构工艺性能。
新课讲解:(一)塑料制品的加强肋1、目的:增加塑料制品的强度和刚度。
2、设计原则(二)塑料制品的支承面1、设计原则:(三)塑料制品的圆角(四)塑料制品上孔的设计(五)塑料制品的花纹、标记、符号及文字【课后小结】1、塑件的加强肋、支承面、圆角、孔的设计2、塑料制品的花纹、标记、符号及文字【练习与作业】1、塑件的加强肋、支承面、圆角如何设计?2、塑件的花纹、标记、符号及文字如何设计?注:要求以一块黑板的版面来进行板书设计教案纸教学过程学生活动学时分配塑料制件的结构工艺性(3)【组织教学】【回顾旧课】1、塑件的形状如何设计?2、塑件的壁厚如何设计?3、什么是脱模斜度?如何设计?引言:塑料制件由于使用要求的不同,其种类繁多、形状各异,而塑料注塑成型工艺条件、注射成型设备与注射成型模具却有一定的规范要求的。
制件的结构工艺性能,是指塑料制件成型生产时对模具结构、成型工艺的适应程度。
塑料制件结构工艺性能的合理与否主要取决于制件设计。
(塑料制品)质量验收标准
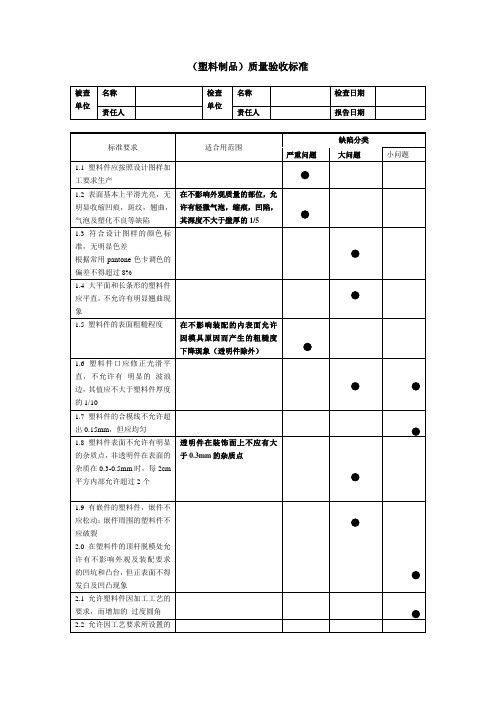
被查
单位
名称
检查
单位
名称
检查日期
责任人
责任人
报告日期
标准要求
适合用范围
缺陷分类
严重问题
大问题
小问题
1.1塑料件应按照设计图样加工要求生产
1.2表面基本上平滑光亮,无明显收缩凹痕,斑纹,翘曲,气泡及塑化不良等缺陷
在不影响外观质量的部位,允许有轻微气泡,缩痕,凹陷Байду номын сангаас其深度不大于壁厚的1/5
2.5拉伸强度
被测件承受5KG的拉力或者重力,无变形或者裂缝
2.6材料:
在没有客户特别指定或者成本需求的情况下,厂房不得给我方所需产品使用回料
2.7运输包装
不得因包装而产生的塑料件的剧烈碰撞,摔箱后,外箱或包装应封箱完好,没有过分的开裂以至于使产品或部件从中溢出(就是破孔,箱盖摔开,撕裂/破裂等)和产品损坏
注明:在产品生产完成100%,包装完成80%时,进行终期验货,执行AQL level 1.5/4.0
核查人员:
日期:
1.3符合设计图样的颜色标准,无明显色差
根据常用pantone色卡调色的偏差不得超过8%
1.4大平面和长条形的塑料件应平直,不允许有明显翘曲现象
1.5塑料件的表面粗糙程度
在不影响装配的内表面允许因模具原因而产生的粗糙度下降现象(透明件除外)
1.6塑料件口应修正光滑平直,不允许有明显的波浪边,其值应不大于塑料件厚度的1/10
1.7塑料件的合模线不允许超出0.15mm,但应均匀
1.8塑料件表面不允许有明显的杂质点,非透明件在表面的杂质在0.3-0.5mm时,每2cm平方内部允许超过2个
透明件在装饰面上不应有大于0.3mm的杂质点
注塑工艺分类
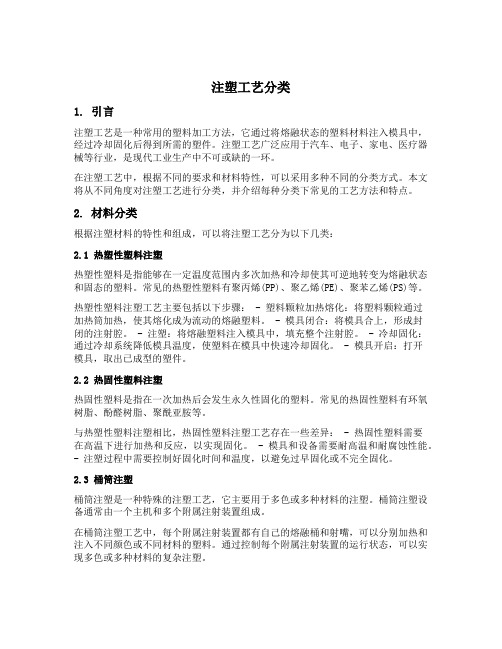
注塑工艺分类1. 引言注塑工艺是一种常用的塑料加工方法,它通过将熔融状态的塑料材料注入模具中,经过冷却固化后得到所需的塑件。
注塑工艺广泛应用于汽车、电子、家电、医疗器械等行业,是现代工业生产中不可或缺的一环。
在注塑工艺中,根据不同的要求和材料特性,可以采用多种不同的分类方式。
本文将从不同角度对注塑工艺进行分类,并介绍每种分类下常见的工艺方法和特点。
2. 材料分类根据注塑材料的特性和组成,可以将注塑工艺分为以下几类:2.1 热塑性塑料注塑热塑性塑料是指能够在一定温度范围内多次加热和冷却使其可逆地转变为熔融状态和固态的塑料。
常见的热塑性塑料有聚丙烯(PP)、聚乙烯(PE)、聚苯乙烯(PS)等。
热塑性塑料注塑工艺主要包括以下步骤: - 塑料颗粒加热熔化:将塑料颗粒通过加热筒加热,使其熔化成为流动的熔融塑料。
- 模具闭合:将模具合上,形成封闭的注射腔。
- 注塑:将熔融塑料注入模具中,填充整个注射腔。
- 冷却固化:通过冷却系统降低模具温度,使塑料在模具中快速冷却固化。
- 模具开启:打开模具,取出已成型的塑件。
2.2 热固性塑料注塑热固性塑料是指在一次加热后会发生永久性固化的塑料。
常见的热固性塑料有环氧树脂、酚醛树脂、聚酰亚胺等。
与热塑性塑料注塑相比,热固性塑料注塑工艺存在一些差异: - 热固性塑料需要在高温下进行加热和反应,以实现固化。
- 模具和设备需要耐高温和耐腐蚀性能。
- 注塑过程中需要控制好固化时间和温度,以避免过早固化或不完全固化。
2.3 桶筒注塑桶筒注塑是一种特殊的注塑工艺,它主要用于多色或多种材料的注塑。
桶筒注塑设备通常由一个主机和多个附属注射装置组成。
在桶筒注塑工艺中,每个附属注射装置都有自己的熔融桶和射嘴,可以分别加热和注入不同颜色或不同材料的塑料。
通过控制每个附属注射装置的运行状态,可以实现多色或多种材料的复杂注塑。
3. 工艺特点不同的注塑工艺具有不同的特点和适用范围,下面将介绍几种常见工艺的特点:3.1 热流道注塑热流道注塑是一种通过加热系统控制熔融塑料流动路径的工艺。
塑料注塑工艺标准

塑料注塑工艺标准1、PP塑料制品:1.1概述:聚丙烯,英文简称PP,为一种白色蜡状材料,密度0.90g/cm3。
PP具有良好的电性能和化学稳定性,其机械性能、耐热性均高于PE,经过增强的PP可用做工程材料。
PP成纤性好,耐疲劳性好,用其制成的铰链几十万次不断;PP低温冲击性不好,成型收缩率大,产品精度不高。
1.2加工:1.2.1成型特性:1.2.1.1结晶性料,吸湿性小,可能发生熔融破裂,长期与热金属接触易发生分解。
1.2.1.2流动性极好,溢边值0.03mm左右。
1.2.1.3冷动速度快,浇注系统及冷却系统应散热缓慢。
1.2.1.4成型收缩范围大,收缩率大,易发生缩孔、凹痕、变形、方向性强。
1.2.1.5注意控制成型温度,料温低方向性明显,尤其是低温高压时更明显,模温低于50℃以下塑件不光泽,易发生熔接不良、流痕;90℃以上时易发生翘曲、变形。
1.2.1.6塑件应壁厚均匀,避免缺口、尖角,以避免应力集中。
1.2.1.7注塑模及注塑制品:A、最小脱模斜度30’---1°。
B、最小壁厚0.85mm。
C、流程与壁厚的关系: ,其中t为壁厚(mm),l为流程(mm)。
D、塑件转接处均应有不小于0.5---1mm的圆角。
E、塑件壁厚应尽可能均匀一致,以防制品结构缩水和翘曲、变形。
1. 3注塑工艺条件:1.2.3.1干燥温度和时间:封袋PP无须干燥即可注塑,预热温度和时间:80---100℃/1---2h。
1.2.3.2料筒温度:200---230℃。
1.2.3.3射嘴温度:180---190℃。
1.2.3.4模温:20---60℃。
1.2.3.5注射压力:≤69---98Mpa1.2.3.6注射时间(包括保压时间):≤20---60S。
1.2.3.7冷却时间:≤20---90S。
1.2.3.8螺杆转速:≤80rpm。
2、PE塑料制品:2.1概述:聚乙烯,英文简称PE,有低密度聚乙烯(LDPE)、高密度聚乙烯(HDPE)及线性低密度聚乙烯(LLDPE)三种。
塑件结构工艺性分析
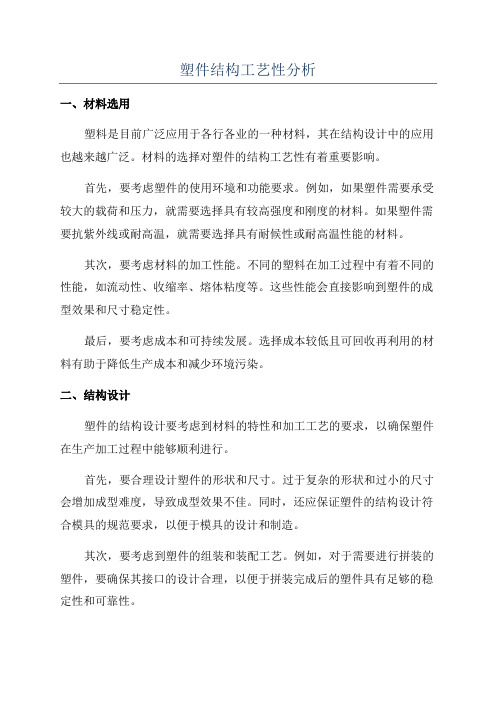
塑件结构工艺性分析一、材料选用塑料是目前广泛应用于各行各业的一种材料,其在结构设计中的应用也越来越广泛。
材料的选择对塑件的结构工艺性有着重要影响。
首先,要考虑塑件的使用环境和功能要求。
例如,如果塑件需要承受较大的载荷和压力,就需要选择具有较高强度和刚度的材料。
如果塑件需要抗紫外线或耐高温,就需要选择具有耐候性或耐高温性能的材料。
其次,要考虑材料的加工性能。
不同的塑料在加工过程中有着不同的性能,如流动性、收缩率、熔体粘度等。
这些性能会直接影响到塑件的成型效果和尺寸稳定性。
最后,要考虑成本和可持续发展。
选择成本较低且可回收再利用的材料有助于降低生产成本和减少环境污染。
二、结构设计塑件的结构设计要考虑到材料的特性和加工工艺的要求,以确保塑件在生产加工过程中能够顺利进行。
首先,要合理设计塑件的形状和尺寸。
过于复杂的形状和过小的尺寸会增加成型难度,导致成型效果不佳。
同时,还应保证塑件的结构设计符合模具的规范要求,以便于模具的设计和制造。
其次,要考虑到塑件的组装和装配工艺。
例如,对于需要进行拼装的塑件,要确保其接口的设计合理,以便于拼装完成后的塑件具有足够的稳定性和可靠性。
最后,还应考虑到塑件的成型和冷却等工艺要求。
合理设计成型孔、冷却孔和浇口等结构,有利于塑件的快速成型和降低成型过程中的内应力,从而提高产品质量和生产效率。
三、加工工艺塑件的加工工艺包括模具设计、塑料注射成型、相关配套工艺等,其中模具设计是塑件结构工艺性的重要环节。
首先,模具的设计和制造要符合塑件的结构设计要求。
模具的结构应简单、密封性好、易于脱模,以便于塑件的成型和脱模。
其次,要根据不同材料的特性确定合适的注射工艺参数。
不同材料的熔体粘度和流动性不同,因此注射温度、注射压力和注射时间等参数需要进行合理调整,以确保塑件的成型效果和尺寸稳定性。
最后,要对塑件进行后续处理。
例如,塑料件常常需要进行去毛刺、修边、抛光、喷涂等处理,以提高产品的表面质量和装饰效果。
模流分析报告
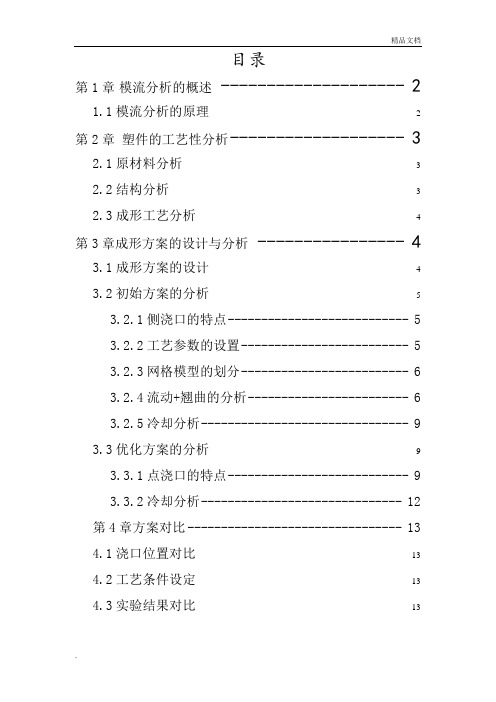
目录第1章模流分析的概述 -------------------- 21.1模流分析的原理------------------------------------------------------------------------- 2第2章塑件的工艺性分析------------------- 32.1原材料分析 ---------------------------------------------------------------------------------- 32.2结构分析 --------------------------------------------------------------------------------------- 32.3成形工艺分析------------------------------------------------------------------------------ 4第3章成形方案的设计与分析 ---------------- 43.1成形方案的设计------------------------------------------------------------------------- 43.2初始方案的分析------------------------------------------------------------------------- 53.2.1侧浇口的特点--------------------------- 53.2.2工艺参数的设置------------------------- 53.2.3网格模型的划分------------------------- 63.2.4流动+翘曲的分析------------------------ 63.2.5冷却分析------------------------------- 93.3优化方案的分析------------------------------------------------------------------------- 93.3.1点浇口的特点--------------------------- 93.3.2冷却分析------------------------------ 12第4章方案对比-------------------------------- 134.1浇口位置对比----------------------------------------------------------------------------- 134.2工艺条件设定----------------------------------------------------------------------------- 134.3实验结果对比----------------------------------------------------------------------------- 13第1章模流分析的概述1.1模流分析的原理1. 粘性流体力学的基本方程1)广义牛顿定律,反映了一般工程问题范围内粘性流体的应力张量与应变速率张量之间的关系,数学表达式为本构方程。
模具设计与制造专业毕业论文--瓶盖注塑模具设计
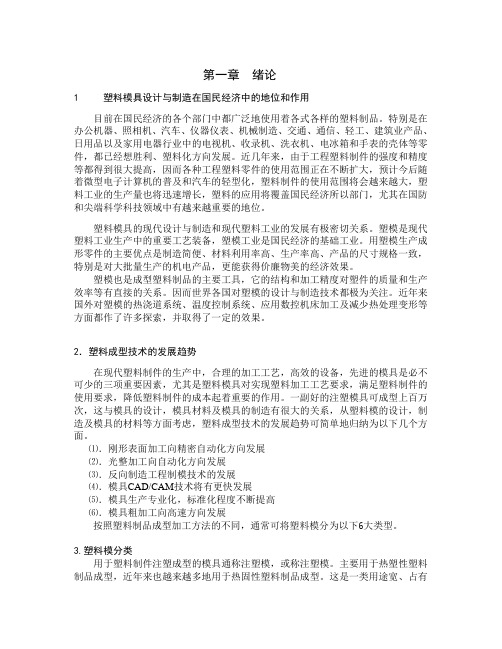
第一章绪论1塑料模具设计与制造在国民经济中的地位和作用目前在国民经济的各个部门中都广泛地使用着各式各样的塑料制品。
特别是在办公机器、照相机、汽车、仪器仪表、机械制造、交通、通信、轻工、建筑业产品、日用品以及家用电器行业中的电视机、收录机、洗衣机、电冰箱和手表的壳体等零件,都已经想胜利、塑料化方向发展。
近几年来,由于工程塑料制件的强度和精度等都得到很大提高,因而各种工程塑料零件的使用范围正在不断扩大,预计今后随着微型电子计算机的普及和汽车的轻型化,塑料制件的使用范围将会越来越大,塑料工业的生产量也将迅速增长,塑料的应用将覆盖国民经济所以部门,尤其在国防和尖端科学科技领域中有越来越重要的地位。
塑料模具的现代设计与制造和现代塑料工业的发展有极密切关系。
塑模是现代塑料工业生产中的重要工艺装备,塑模工业是国民经济的基础工业。
用塑模生产成形零件的主要优点是制造简便、材料利用率高、生产率高、产品的尺寸规格一致,特别是对大批量生产的机电产品,更能获得价廉物美的经济效果。
塑模也是成型塑料制品的主要工具,它的结构和加工精度对塑件的质量和生产效率等有直接的关系。
因而世界各国对塑模的设计与制造技术都极为关注。
近年来国外对塑模的热浇道系统、温度控制系统、应用数控机床加工及减少热处理变形等方面都作了许多探索,并取得了一定的效果。
2.塑料成型技术的发展趋势在现代塑料制件的生产中,合理的加工工艺,高效的设备,先进的模具是必不可少的三项重要因素,尤其是塑料模具对实现塑料加工工艺要求,满足塑料制件的使用要求,降低塑料制件的成本起着重要的作用。
一副好的注塑模具可成型上百万次,这与模具的设计,模具材料及模具的制造有很大的关系,从塑料模的设计,制造及模具的材料等方面考虑,塑料成型技术的发展趋势可简单地归纳为以下几个方面。
⑴.刚形表面加工向精密自动化方向发展⑵.光整加工向自动化方向发展⑶.反向制造工程制模技术的发展⑷.模具CAD/CAM技术将有更快发展⑸.模具生产专业化,标准化程度不断提高⑹.模具粗加工向高速方向发展按照塑料制品成型加工方法的不同,通常可将塑料模分为以下6大类型。
塑件工艺性分析

一、原始材料分析1.1塑件工艺性分析饮水机水嘴采用ABS材料,壁厚较厚,故注塑压力应采用70-100mpa,由于是多型腔模,点浇口能均衡各型腔的进料速度。
同时由于点浇口小可以提高注射速率,所以选择点浇口。
由于水嘴有侧凹所以需要侧抽机构。
成型材料性能分析1.2ABS的一般性能1.热塑性材料2外观为不透明呈象牙色颗粒,无毒无味,吸水率低制品可制成各种颜色,表面光泽度高。
3好的易加工性4低蠕变性和优异的尺寸稳定性。
5非结晶无定形聚合物,无明显熔点。
6化学稳定性好,对酸碱盐等一般有机溶剂都很稳定。
7有良好的力学性能,抗冲击性强,耐磨。
8粘度高,流动性差,收缩率为0.4-0.6%成型压力密度1.05g/cm³9熔融温度195-140,成型模温38-93.1.3材料成型性能及条件[1]吸水率极低有良好的阻湿性,成型前省去干燥工序。
熔体粘度随温度升高而降低成型加工温度范围大,成型加工性能极好。
ABS塑料的成型条件二、注塑机选择2.1塑件体积及质量计算单个塑件;体积v=6.83cm³质量m=7.717g两个塑件加浇注系统;总体积V∁∁两个塑件及浇注系统;总体积V=1.6*2*6.83=21.856 cm³质量M=1.6*2*7.717=24.694g塑件在分型面上的投影面积为284cm²所以总面积为2.7*284=766.8 cm²锁模力计算取模腔压力P=70mpa锁模力为F=70*766.8=53676N由于ABS是无定形材料故注射系数α=0.85G>=24.694/0.85=29.052g V>=21.856/0.85=25.723cm³F>=53676/0.85=63148.235N2.2注塑机的选择[1]查表注塑机选取XS-ZY125三、注塑模的结构设计经过分析塑件采用点浇口进料形式,所以采用三板式。
这个模具的结构设计主要包括确定型腔数目、排布、分型面、浇注系统成型零件、脱模机构、导向机构、排气机构等设计。
塑件的结构工艺性
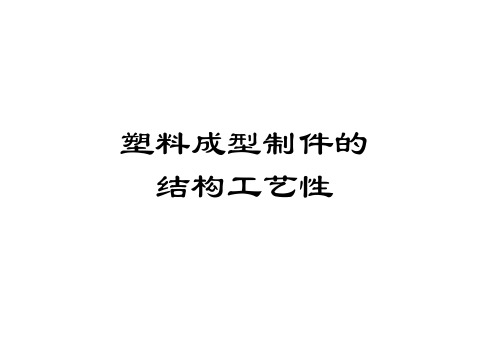
四、塑料制件的结构设计
一)成型工艺对塑件几何形状的要求
– 塑料制件的形状,首先是保证制件的使用结 构要求,并结合人们的审美观点而设计出来 的几何形状。
– 因而,随着设计者的构思方案不同,同一用 途的制件,其形状也会有不同,对此我们不 做深入讨论。
– 我们所着重论述的是有关制件设计的工艺性 与经济性,即我们设计的塑件内外表面形状 要设计得易于模塑成型。
a)不合理
b)合理
图 加强筋与支撑面
2)应避免或减小塑料的局部聚积,否 则会产生缩孔、气泡。在设计时可将实心 部位改为空心结构。
缩孔或气泡
a)不合理
b)合理
图3.6 加强筋的布排应注意避免塑料局部聚积
3)筋条排列要注意排列互相错开,这样才 能防止收缩不均匀,变形较小。
a)不合理
b)合理
图3.6 加强筋的排列方向
要能满足塑件的使用要求,应将塑件设计的尽量 紧凑、尺寸小巧一些。
2. 塑件的尺寸精度 – 是指所获得的塑件尺寸与产品图纸尺寸的符 合程度,即所获塑件尺寸的准确度。 – 影响塑件精度的因素较为复杂,塑件尺寸误 差的产生是多种因素综合影响的结果,因此, 在一般情况下塑件要达到金属制件那样的精 度是非常困难的。
l 对于模具设计者来说,在考虑塑件的结构及有关使用要 求时,还必须与成型该塑件的成型模具的相应结构结合 起来考虑,既要使塑料制件能按使用要求加工出来,保 证制件的质量,而又要使模具结构合理、经济。
在塑件结构工艺性设计时,应考虑以下几方面 的因素:
(1)塑料的各项性能特点; (2)在保证各项使用性能的前提下,塑件结 构形状力求简单,且有利于充模流动、排气、补 缩和高效冷却硬化(热塑性塑料制件)或快速受 热固化(热固性塑料制件); (3)模具的总体结构应使模具零件易于制造, 特别是抽芯和脱模机构。
塑胶件应力形成的原因

塑胶件应力形成的原因引言:塑胶件是指通过塑料材料加工而成的各种形状的产品,广泛应用于日常生活和工业生产中。
塑胶件在加工过程中,往往会出现应力现象,这种应力可能对产品的使用性能和寿命产生不良影响。
本文将从塑胶件的材料特性、加工工艺以及产品设计等方面探讨塑胶件应力形成的原因。
一、材料特性:1.1塑料材料的流变性:塑料具有可塑性和可压性的特性,容易受外力作用而发生变形。
在塑胶件加工过程中,由于注塑或挤出等成型工艺的复杂性,塑料材料会经历多次变形和冷却,使得材料内部产生残余应力。
这种残余应力会导致塑胶件在使用过程中产生应力集中和应力松弛现象。
1.2材料粘度和分子结构:塑料材料的粘度和分子结构也会对塑胶件的应力形成产生影响。
粘度较高的塑料流动性差,容易产生应力积累现象;而分子结构复杂的塑料,如聚合物材料,由于分子链的交联和纠缠,容易导致塑胶件产生内应力。
二、加工工艺:2.1成型工艺参数:塑料件的成型工艺参数,如温度、压力和速度等,对于塑胶件的应力形成有重要影响。
温度过高或过低、压力过大或过小、注射速度过快或过慢等都可能引起应力集中和应力积累现象。
例如,温度过高会导致材料熔化不充分,形成含气孔的塑胶件,从而产生内应力。
2.2成型工艺选择:不同的成型工艺对塑胶件的应力形成也有不同的影响。
常见的成型工艺有注塑、挤出、吹塑等,每种工艺的特点和应用领域不同,其应力形成的机理也不同。
例如,注塑工艺易于产生内应力,而挤出工艺易于产生表面应力。
2.3产品尺寸和形状:塑胶件的尺寸和形状设计是影响应力形成的重要因素之一、当塑胶件的尺寸较大或形状复杂时,由于塑料材料的热胀冷缩和冷却不均匀等原因,易导致内部应力集中。
此外,塑胶件的壁厚也会对应力形成产生影响,过大或过小的壁厚都可能引起应力积累现象。
三、产品设计:3.1断面形状:塑胶件的断面形状对于应力形成具有重要影响。
常见的塑胶件断面形状有矩形、圆形、梯形等,不同形状的断面对应力分布有不同的影响。
塑料模具设计与制造

2.添加剂 ⑶稳定剂 凡能阻缓材料变质的物质称为稳定剂。 分类: 热稳定剂:它的主要作用就是抑制或防止树脂在加工或使用过程中受热而降解。 光稳定剂:它的主要作用是阻止树脂在光的作用下降解(塑料变色、力学性能下降等等)。 抗氧化剂:延缓或抑制塑料氧化速度
第二章 塑料及塑件工艺性
第二章 塑料及塑件工艺性
7.相容性(共混性) 相容性——指两种或两种以上不同品种的塑料在熔融状态下不产生相分离现象的能力。 8.塑料状态与加工性 熔融纺丝成型 注射成型 薄膜吹塑成型 挤出成型 压延成型 中空成型 真空和压力成型
第二章 塑料及塑件工艺性
二、热固性塑料的工艺性能 1.收缩性 热固性塑料收缩的表现形式、影响因素和计算方法与热塑性塑料基本相同。 2.流动性 热固性塑料流动性通常以拉西格流动性(以毫米计)来表示,数值大则流动性好。
塑料模具设计与制造
第二章 塑料及塑件工艺性
学无常师,道在则是 ——晋·潘岳 <归田赋>
第二章 塑料及塑件工艺性
问题: 1.什么是模具?什么是塑料模具? 2.塑件成型加工的三要素是什么? 3.塑料常用的成型方法有哪些?
基本内容: 1.理解塑料的概念、分类、成份; 2.理解热固性、热塑性塑料两个概念,二者的区别; 3.了解塑料的特性及用途。 重点难点: 1.重点:塑料的概念、成份、分类 2.难点:对概念的理解
第二章 塑料及塑件工艺性
材料变化
热固性塑料及其成型方法
热塑性树脂及其成型方法
材料在模具 内的行为
由于加热、加压、熔融或粘度下降 ↓ 流动 ↓ 赋性 ↓ 继续加热交联硬化
由于加热、加压、塑化或熔融 ↓ 流动 ↓ 赋性 ↓ 冷却固化
第二章 塑料及塑件工艺性
塑件的结构工艺性

塑件的结构工艺性塑件的结构工艺性是指塑件设计的结构是否符合塑料制品加工的工艺要求。
塑料制品加工过程中,考虑到成型性、冷却性、顶出性、模具等因素,设计人员需要合理地设计塑料制品的结构,以提高制品的质量和生产效率。
首先,塑件的结构应具备成型性。
成型性是指塑料在加热融化后能够在模具中形成所需形状的能力。
因此,设计人员应根据塑料材料的特性,合理选择塑胶制品的结构形式,避免在注塑过程中发生热分解、气泡和熔接线等缺陷。
其次,塑件的结构应具备良好的冷却性。
冷却性是指在塑料制品注塑过程中,塑料材料能够迅速冷却并固化。
设计人员应考虑到塑胶制品的结构形状、壁厚以及冷却系统的设置等因素,以确保塑料制品在注塑过程中能够均匀地冷却,避免出现变形和缩水等问题。
此外,塑件的结构应具备良好的顶出性。
顶出性是指塑胶制品在顶出系统的作用下,能够顺利地从模具中取出。
设计人员应注意到塑料制品的结构形状和顶出系统的设计,避免塑件在顶出过程中出现变形、折断和卡死等情况。
最后,塑件的结构应考虑到模具的制造和使用。
模具的制造和使用对塑料制品的质量和生产效率有着重要的影响。
设计人员应根据塑料制品的结构形状、尺寸和要求,合理设计模具的结构和尺寸,以便于模具的制造和使用,提高模具的寿命和生产效率。
总之,塑件的结构工艺性是塑料制品设计中需要考虑的重要因素之一。
设计人员应根据塑料材料的特性和加工工艺要求,合理设计塑料制品的结构,以提高制品的质量和生产效率。
同时,设计人员还应注意到成型性、冷却性、顶出性和模具等因素对塑料制品的影响,以确保塑料制品能够顺利地生产并符合质量要求。
塑料制品在现代工业生产中得到了广泛的应用,其轻便、耐用、成本低廉的特点使得塑料制品成为替代传统材料的理想选择。
然而,要确保塑料制品的质量和生产效率,需要充分考虑塑件的结构工艺性。
下面将继续探讨塑件的结构工艺性的相关内容。
首先,塑件的结构形式对于成型性的影响非常重要。
不同的塑件形式对于塑料材料的流动和填充具有不同的要求。
塑件结构工艺性
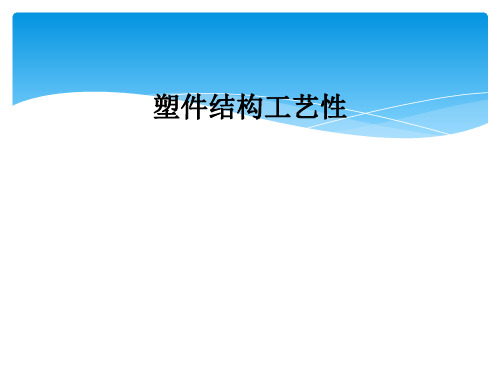
(4)塑件支承面的设计
当塑件上有一面作为支承面来使用时,将该 面设计为一个整面是不合理的,应采用如图319所示结构。
因为平板状在成型收缩后很容易翘曲变形, 稍许不平都会影响良好的支承作用,故以边框 式或底脚(三点或四点)结构设计塑件支承面。 如下图塑料盘所示。
对于细长型芯,为防止其弯曲变形,在 不影响塑件的条件下,可在塑件的下方设 支承柱来支撑。如图3-25所示。
斜孔或形状复杂的孔可采用拼合的型 芯来成型。如图7.5所示
5 带嵌件塑件的设计
在塑件内嵌入其他零件形成不可卸的连接,所嵌入 的零件即称嵌件。嵌件材料一般为金属材料,也有用 非金属材料的,例如玻璃、木材或已成型的塑件。 1、塑件中镶入嵌件的目的:
3.1 形状
当塑件的内外侧凹陷较浅,同时成 型塑件的塑料为聚乙烯、聚丙烯、聚 甲醛这类仍带有足够弹性的塑料时, 模具可采取强制脱模。
3 形状和结构设计
3.2 结构设计
为使强制脱模时的脱模阻力不要过大引 起塑件损坏和变形,塑件侧凹深度必须 在要求的合理范围内,见p222图7.2下 面的说明(公式),同时还要重视将凹凸起 伏处设计为圆角或斜面过渡结构。
增加局部强度、硬度、耐磨、导磁、导电性能,加 强塑件尺寸精度和形状的稳定性,起装饰作用等。 2、嵌件结构有柱状、针杆状、片状和框架等如图334所示。
5 带嵌件塑件的设计
3、嵌件设计的要点: ⑴ 嵌件应可靠地固定在塑件中,防止嵌
件在塑件中转动或被抽离。柱状嵌件可 在外形滚直纹并切出沟槽,或在外表面 滚菱形花纹。针杆状嵌件可切口或冲孔。 如图3-34所示。
3.5.3 模塑螺纹的结构设计
- 1、下载文档前请自行甄别文档内容的完整性,平台不提供额外的编辑、内容补充、找答案等附加服务。
- 2、"仅部分预览"的文档,不可在线预览部分如存在完整性等问题,可反馈申请退款(可完整预览的文档不适用该条件!)。
- 3、如文档侵犯您的权益,请联系客服反馈,我们会尽快为您处理(人工客服工作时间:9:00-18:30)。
问题 目的和要求
3.塑件的壁厚 改善壁厚练习:
重点难点
一、塑料选材
二、尺寸精度 及表面粗糙度
三、结构设计
练习题
2020/3/9
第二章 塑料及模塑成型工艺 2020/3/9 2.3塑件的工艺性
二、塑件的几何形状
问题 目的和要求
重点难点 一、塑料选材 二、尺寸精度 及表面粗糙度 三、结构设计
练习题
4.塑件的加强筋
二、塑件的几何形状
问题 目的和要求
重点难点 一、塑料选材
7.塑件的凸台与角撑
凸台 —— 是用来增强孔或装配附件、或为塑件提 供支撑的截锥台或支撑块
凸台设计要点:
二、尺寸精度 及表面粗糙度
凸台一般应位于边角部位
三、结构设计 练习题
其几何尺寸应小 其高度不应超过直径的两倍
第二章 塑料及模塑成型工艺
2.3塑件的工艺性
二、塑件的几何形状
问题 目的和要求
重点难点 一、塑料选材 二、尺寸精度 及表面粗糙度 三、结构设计
练习题
2.脱模斜度 脱模斜度设计要点:
含润滑剂的塑料采用较小脱模斜度
从留模方位考虑: 留在型芯,内表面脱模斜度﹤外表面 留在型腔,外表面脱模斜度﹤内表面
3.塑件的壁厚 壁厚过小
强度及刚度不足,塑料流动 困难
二、尺寸精度 及表面粗糙度
三、结构设计
一般圆角半径不应小于0.5mm 壁厚不等的两壁转角可按平均壁厚确定内、外圆
练习题
角半径
理想的内圆角半径应为壁厚的1/3以上
第二章 塑料及模塑成型工艺 2020/3/9 2.3塑件的工艺性
二、塑件的几何形状
问题 目的和要求
重点难点
6.塑件的支承面 通常塑件一般不以整个平面作为支承面,而是
第二章 塑料及模塑成型工艺 2020/3/9
问题 目的和要求
重点难点 一、塑料选材 二、尺寸精度 及表面粗糙度 三、结构设计
练习题
君子壹教,弟子壹学,亟成!
第二章 塑料及模塑成型工艺 2020/3/9
问题 目的和要求
重点难点 一、塑料选材 二、尺寸精度 及表面粗糙度 三、结构设计
练习题
问题:
1.什么是塑料的收缩性?影响收缩率的因素有哪些? 2.什么是塑料的流动性?影响流动性的因素有哪些? 3.什么是塑料的相容性?用在什么地方? 4.热固性塑料的水分及挥发物的来源?有什么危害?怎么防止?
二、塑件的几何形状
7.塑件的凸台与角撑
问题 目的和要求
重点难点 一、塑料选材 二、尺寸精度 及表面粗糙度 三、结构设计
练习题
凸台设计实例
2020/3/9
第二章 塑料及模塑成型工艺 2020/3/9 2.3塑件的工艺性
二、塑件的几何形状
问题 目的和要求
7.塑件的凸台与角撑 角撑 —— 塑件上边角或凸台的支撑部分
2.塑件的精度 尺寸精度的确定:
重点难点
一、塑料选材 二、尺寸精度 及表面粗糙度 三、结构设计
模塑件公差代号为MT (附录E) MT1级精度最高(一般不采用) MT7级精度最低
练习题
会根据教材表2-5(常用材料模塑件公差等
级和选用)选择塑件公差等级
第二章 塑料及模塑成型工艺
2.3塑件的工艺性
一、塑件的尺寸、精度和表面粗糙度
直接模塑出来 模塑成盲孔再钻孔通 塑件成型后再钻孔
三、结构设计 练习题
⑵常见孔的设计要求:
模塑通孔要求孔径比(长度与孔径的比值)
要小些
第二章 塑料及模塑成型工艺 2020/3/9 2.3塑件的工艺性
二、塑件的几何形状
问题 目的和要求
重点难点 一、塑料选材
8.塑件上的孔(槽) ⑵常见孔的设计要求:
当通孔孔径﹤1.5mm,由于型芯易弯曲折 断,不适于模塑成型。
须在塑件内外表面脱模方向上留有足够的斜度α,
在模具上称为脱模斜度。
脱模斜度取决于 塑件的形状、壁厚 及塑料的收缩率,
一般取30 ′~
1°30′。
第二章 塑料及模塑成型工艺
2.3塑件的工艺性
二、塑件的几何形状
2.脱模斜度
问题
目的和要求
脱
重点难点
模
一、塑料选材
斜
度
二、尺寸精度 及表面粗糙度
方
向
三、结构设计
练习题
塑料的流动性(大而薄的塑件充模困难) 设备的工作能力(注射量、锁模力、工作台面)
第二章 塑料及模塑成型工艺 2020/3/9 2.3塑件的工艺性
二、塑件的尺寸、精度和表面粗糙度
问题
目的和要求 重点难点
一、塑料选材 二、尺寸精度 及表面粗糙度
2.塑件的精度 塑件的尺寸精度是指所获得的塑件尺寸与产品
重点难点
一、塑料选材 二、尺寸精度 及表面粗糙度 三、结构设计
T——制品壁厚 D=T C=2T
练习题
A=0.8T
B=2A
第二章 塑料及模塑成型工艺 2020/3/9 2.3塑件的工艺性
二、塑件的几何形状
问题
目的和要求 重点难点
一、塑料选材 二、尺寸精度 及表面粗糙度
8.塑件上的孔(槽) ⑴塑件的孔三种成型加工方法:
可能设计成圆角,或者用圆弧过渡。
⑴圆角的作用:
圆角可避免应力集中,提 高制件强度
圆角可有利于充模和脱模
圆角有利于模具制造,提 高模具强度
第二章 塑料及模塑成型工艺 2020/3/9 2.3塑件的工艺性
二、塑件的几何形状
5.圆角
问题
⑵圆角的确定:
目的和要求 重点难点
一、塑料选材
内壁圆角半径应为壁厚的一半 外壁圆角半径可为壁厚的1.5倍
壁厚过大
原料浪费,冷却时间长,易 产生缺陷
第二章 塑料及模塑成型工艺 2020/3/9 2.3塑件的工艺性
二、塑件的几何形状
问题 目的和要求
重点难点 一、塑料选材 二、尺寸精度 及表面粗糙度 三、结构设计
3.塑件的壁厚 塑件壁厚设计原则: 满足塑件结构和使用性能要求下取小壁厚 能承受推出机构等的冲击和振动 制品连接紧固处、嵌件埋入处等具有足够的厚度 保证贮存、搬运过程中强度所需的壁厚
重点难点 一、塑料选材 二、尺寸精度 及表面粗糙度 三、结构设计
练习题
2.塑件的精度 尺寸精度的确定:
对于塑件上孔的公差可采用基准孔,可取表
中数值冠以(+)号。
对于塑件上轴的公差可采用基准轴,可取表
中数值冠以(-)号。
一般配合部分尺寸精度高于非配合部分尺寸 精度。
模具尺寸精度比塑件尺寸精度高2-3级。
练习题
不同选材 )
按用途进行分类 (按应用领域 、功能 )
第二章 塑料及模塑成型工艺 2020/3/9 2.3塑件的工艺性
二、塑件的尺寸、精度和表面粗糙度
问题 目的和要求
1.塑件的尺寸
塑件的尺寸 —— 指塑件的总体尺寸
重点难点 一、塑料选材
塑件的尺寸受下面两个因素影响:
二、尺寸精度 及表面粗糙度
三、结构设计
练习题
满足成型时熔体充模所需的壁厚
厚薄适中 均匀壁厚
第二章 塑料及模塑成型工艺
2.3塑件的工艺性
二、塑件的几何形状
问题 目的和要求
3.塑件的壁厚 改善壁厚典型实例:
重点难点
一、塑料选材
二、尺寸精度 及表面粗糙度
三、结构设计
练习题
2020/3/9
第二章 塑料及模塑成型工艺
2.3塑件的工艺性
二、塑件的几何形状
问题 目的和要求
重点难点 一、塑料选材 二、尺寸精度 及表面粗糙度 三、结构设计
练习题
塑件的工艺性 ——是塑件对成型加工的适应性
塑件工艺性设计包括 :塑料材料选择、尺寸精 度和表面粗糙度、塑件结构
塑件工艺性设计的特点:应当满足使用性能和 成形工艺的要求,力求做到结构合理、造型美 观、便于制造。
第二章 塑料及模塑成型工艺 2020/3/9 2.3塑件的工艺性
重点难点
一、塑料选材
二、尺寸精度 及表面粗糙度
加强筋厚度小 于壁厚
三、结构设计
练习题
加强筋与支承 面间留有间隙
2020/3/9
第二章 塑料及模塑成型工艺 2020/3/9 2.3塑件的工艺性
二、塑件的几何形状
问题 目的和要求
重点难点 一、塑料选材 二、尺寸精度 及表面粗糙度 三、结构设计
练习题
5.圆角 在满足使用要求的前提下,制件的所有的转角尽
一、塑料材料的选择(分析)
塑料的选材包括:选定塑料基体聚合物(树脂)
问题 目的和要求
重点难点
种类、塑料具体牌号、添加剂种类与用量等 塑料原料选择方法:
一、塑料选材
使用环境(不同的温度、湿度及介质条件、不同的受
二、尺寸精度 及表面粗糙度
力类型选择不同的塑料)
三、结构设计
使用对象(根据国别、地区、民族和具体使用者的
第二章 塑料及模塑ห้องสมุดไป่ตู้型工艺 2020/3/9
问题 目的和要求
重点难点 一、塑料选材 二、尺寸精度 及表面粗糙度 三、结构设计
练习题
内容简介: 1.掌握塑件的尺寸精度和表面粗糙度; 2.掌握塑件的结构设计(脱模斜度、加强筋、圆 角设计、支承面及凸台)。
重点难点: 会分析产品的工艺性能
第二章 塑料及模塑成型工艺 2020/3/9 2.3塑件的工艺性
2.塑件的精度
问题
目的和要求
重点难点
一、塑料选材 二、尺寸精度 及表面粗糙度 三、结构设计
练习题
2020/3/9
A项:不受模具活动部分影响的尺寸公差值 B项:受模具活动部分影响的尺寸公差值