塑件结构工艺性分析(ppt 21页)
第三章塑料制品工艺

广东省技师学院 邓万国主编 电子工业出版社出版
2006.6.1
第三章 塑料制品的工艺性
3.1 塑料制品的结构工艺性
3.1.4 塑料制品的壁厚 2. 减小壁厚差的方法:
(1)将塑件制品过厚部分挖空; (2)将塑件制品分解; (3)为保证顶部质量,应使a>b,
以保证顶部不产生熔接痕。
广东省技师学院 邓万国主编 电子工业出版社出版
2006.6.1
第三章 塑料制品的工艺性
3.1 塑料制品的结构工艺性
3.1.5 圆角
塑料制品的面与面之间一般均应采用圆弧过渡,这样不仅可避免塑 料制品尖角处的应力集中,提高塑料制品强度,而且可改善物料的 流动状态,降低充模阻力,便于充模。塑料制品转角处的圆角半径 通常不要小于0.5~1mm,在不影响塑料制品使用的前提下应尽量 取大些。对于内外表面的转角处,
3.1.6 支承面
当塑料制品需有一个支承 面时,在使用时不宜采用整个底面 作为支承面,因为稍许的翘曲或变 形就会使整个底面不平,影响塑料 制品的使用性能。应该注意环形凸 边支承面或支承底脚高度不应小于 0.5mm,否则底面变形也会使塑料 制品不能平稳地放置。
当塑料制品底部有加强筋时, 支承面的高度应高于加强筋0.5mm。
形状复杂、不易脱模的制品,应取较大的脱模斜度; 制品上的凸起或加强筋 单边应有4°~5°斜度。
侧壁带皮革花纹应有4°~6°的斜度; 每0.025mm花纹深度要取1°以上的脱 模斜度;制品壁厚大的应选较大的脱模斜度。
壳类塑料制品上有成排网格孔板时,要取4°多,成本增加,成型周期长;
过大: 易产生气泡、缩孔、凹痕、翘曲等.
热固性塑料:小型件:1~2mm,大型件:3~8mm;
塑件壁厚的取值
产品工艺性分析

新利達紋路
MT紋路
相對應出模角
#120
#MT-1100
3°
#1304
5°
#121
#MT-11010
3°
#1306
5°
#122
\
3°
#1327
7°
#124
#MT-11020
5°
#1701
2°
#125
\
6°
#1702
3°
#126
\
7°
#2207
3°
#600
\
1°
#பைடு நூலகம்224
2°
#800
\
1°
#2225
PPO+20GF
1.0035
PPS(R4)
1.002
透明ABS
1.003
GE/C1200
1.004
ULTEM 2200
1.003
軟膠
TPE
1.015
ABS+PC
1.004
RYTON R-4
1.002
SILICONE RUBBER 50%
1.015
9)另產品結構是大窗口(即多窗口碰穿)縮水率相對降低千分之二點,比如通常縮水率是
子(圖9-4所示)
3)落曲面上的孔,孔口要倒圓角,以避免出現尖銳的膠位,圖(9-5)所示,做模時,盡量前模
原裝出.
4) T形面的接合面會產生凹陷,要在模呵(Core)側邊設置鍥角減薄膠位(圖9-6)所示
5)加強筋高度的預留(圖9-7)
6)要對大於基本膠厚的部分作吊空膠處理,保證基本內厚一致,並考慮冷卻問題(9-8)
2°
#1000
塑件结构工艺性分析
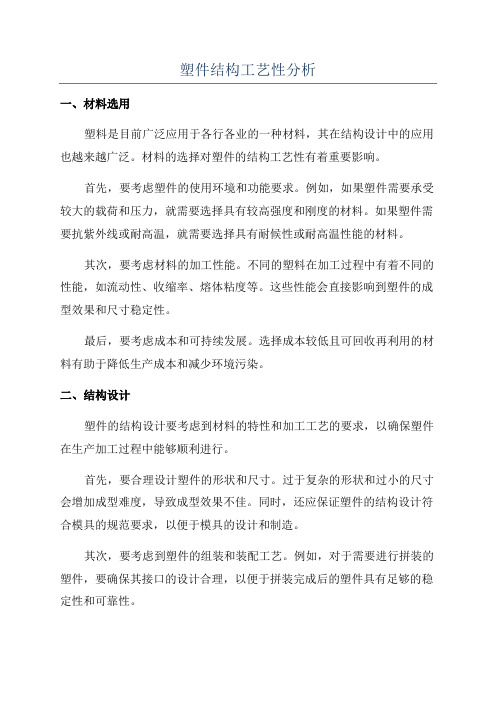
塑件结构工艺性分析一、材料选用塑料是目前广泛应用于各行各业的一种材料,其在结构设计中的应用也越来越广泛。
材料的选择对塑件的结构工艺性有着重要影响。
首先,要考虑塑件的使用环境和功能要求。
例如,如果塑件需要承受较大的载荷和压力,就需要选择具有较高强度和刚度的材料。
如果塑件需要抗紫外线或耐高温,就需要选择具有耐候性或耐高温性能的材料。
其次,要考虑材料的加工性能。
不同的塑料在加工过程中有着不同的性能,如流动性、收缩率、熔体粘度等。
这些性能会直接影响到塑件的成型效果和尺寸稳定性。
最后,要考虑成本和可持续发展。
选择成本较低且可回收再利用的材料有助于降低生产成本和减少环境污染。
二、结构设计塑件的结构设计要考虑到材料的特性和加工工艺的要求,以确保塑件在生产加工过程中能够顺利进行。
首先,要合理设计塑件的形状和尺寸。
过于复杂的形状和过小的尺寸会增加成型难度,导致成型效果不佳。
同时,还应保证塑件的结构设计符合模具的规范要求,以便于模具的设计和制造。
其次,要考虑到塑件的组装和装配工艺。
例如,对于需要进行拼装的塑件,要确保其接口的设计合理,以便于拼装完成后的塑件具有足够的稳定性和可靠性。
最后,还应考虑到塑件的成型和冷却等工艺要求。
合理设计成型孔、冷却孔和浇口等结构,有利于塑件的快速成型和降低成型过程中的内应力,从而提高产品质量和生产效率。
三、加工工艺塑件的加工工艺包括模具设计、塑料注射成型、相关配套工艺等,其中模具设计是塑件结构工艺性的重要环节。
首先,模具的设计和制造要符合塑件的结构设计要求。
模具的结构应简单、密封性好、易于脱模,以便于塑件的成型和脱模。
其次,要根据不同材料的特性确定合适的注射工艺参数。
不同材料的熔体粘度和流动性不同,因此注射温度、注射压力和注射时间等参数需要进行合理调整,以确保塑件的成型效果和尺寸稳定性。
最后,要对塑件进行后续处理。
例如,塑料件常常需要进行去毛刺、修边、抛光、喷涂等处理,以提高产品的表面质量和装饰效果。
塑胶件结构设计
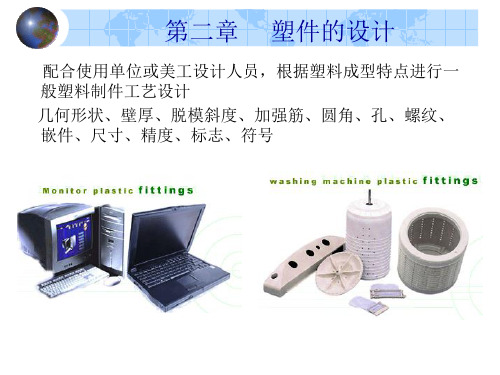
第十节 标记、符号、文字
塑件上直接塑出文字、符号或花纹
可以作成三种形式
一、凸型文字、符号、或花纹 二、凹型字迹 三、凸起的文字设在凹坑内,在模具上镶上
刻颗有字迹的块
塑件上成型的文字符号要求: 凸出高度≥0.2mm 线条宽度≥0.3mm 一般0.8mm 两条线间距≥0.4mm 边框可比字体高出>0.3mm 字体或符号的脱模斜度>10°
复杂件>简单件 壁厚>壁薄件 精度低>精度高 塑件内表面> 外表面(塑件留在型腔) 较高较大尺寸可取较小脱模斜度 收缩率大应取较大脱模斜度
三、 取斜度的方向
外径(D):以大端为基准放脱模斜度,斜度由缩小方向取得 内径(d):以小端为基准,斜度由扩大方向取得
α′>α (内>外) 塑件留在型腔
一般取1°~1.5 ° 也可小到0.5° (若有特殊要求时)斜度可取外表面5′,内表面10′~20′ 凸边、凹凸条纹、加强筋,取4°~5° 塑件高度不大——允许不放脱模斜度
四、模具结构 (1)浇口大小:浇口大时收缩小,浇口小收缩大。 (2)料流方向:与料流方向平行尺寸收缩的,与之垂直的尺寸收缩小。 (3)分型面决定了飞边的位置,飞边使垂直于分型面的尺寸产生误差 (4)型芯、推杆等滑动部分的固定方法及模具的拼合方式、加工方法
等直接影响塑件的尺寸精度 (5)磨损:成型零件在使用中的磨损也使塑件产生误差。
角或锐角,以利于均匀收缩,防止局部应力。
4.嵌件周围的塑料层要有足够的厚度 以保证强度,防止塑件开裂
酚醛类及相似的热固性塑料,嵌件周围料 层最小厚度C,顶部塑料层最小厚度H与嵌 件直径D的关系推荐值如下:
D <4 4~8 8~12 12~16 16~25 H 1 1.5 2 2.5 3
塑件工艺性分析

一、原始材料分析1.1塑件工艺性分析饮水机水嘴采用ABS材料,壁厚较厚,故注塑压力应采用70-100mpa,由于是多型腔模,点浇口能均衡各型腔的进料速度。
同时由于点浇口小可以提高注射速率,所以选择点浇口。
由于水嘴有侧凹所以需要侧抽机构。
成型材料性能分析1.2ABS的一般性能1.热塑性材料2外观为不透明呈象牙色颗粒,无毒无味,吸水率低制品可制成各种颜色,表面光泽度高。
3好的易加工性4低蠕变性和优异的尺寸稳定性。
5非结晶无定形聚合物,无明显熔点。
6化学稳定性好,对酸碱盐等一般有机溶剂都很稳定。
7有良好的力学性能,抗冲击性强,耐磨。
8粘度高,流动性差,收缩率为0.4-0.6%成型压力密度1.05g/cm³9熔融温度195-140,成型模温38-93.1.3材料成型性能及条件[1]吸水率极低有良好的阻湿性,成型前省去干燥工序。
熔体粘度随温度升高而降低成型加工温度范围大,成型加工性能极好。
ABS塑料的成型条件二、注塑机选择2.1塑件体积及质量计算单个塑件;体积v=6.83cm³质量m=7.717g两个塑件加浇注系统;总体积V∁∁两个塑件及浇注系统;总体积V=1.6*2*6.83=21.856 cm³质量M=1.6*2*7.717=24.694g塑件在分型面上的投影面积为284cm²所以总面积为2.7*284=766.8 cm²锁模力计算取模腔压力P=70mpa锁模力为F=70*766.8=53676N由于ABS是无定形材料故注射系数α=0.85G>=24.694/0.85=29.052g V>=21.856/0.85=25.723cm³F>=53676/0.85=63148.235N2.2注塑机的选择[1]查表注塑机选取XS-ZY125三、注塑模的结构设计经过分析塑件采用点浇口进料形式,所以采用三板式。
这个模具的结构设计主要包括确定型腔数目、排布、分型面、浇注系统成型零件、脱模机构、导向机构、排气机构等设计。
塑件的结构工艺性
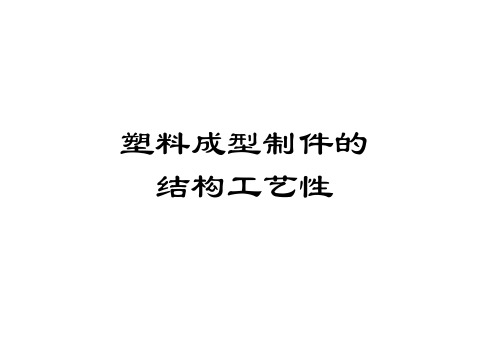
四、塑料制件的结构设计
一)成型工艺对塑件几何形状的要求
– 塑料制件的形状,首先是保证制件的使用结 构要求,并结合人们的审美观点而设计出来 的几何形状。
– 因而,随着设计者的构思方案不同,同一用 途的制件,其形状也会有不同,对此我们不 做深入讨论。
– 我们所着重论述的是有关制件设计的工艺性 与经济性,即我们设计的塑件内外表面形状 要设计得易于模塑成型。
a)不合理
b)合理
图 加强筋与支撑面
2)应避免或减小塑料的局部聚积,否 则会产生缩孔、气泡。在设计时可将实心 部位改为空心结构。
缩孔或气泡
a)不合理
b)合理
图3.6 加强筋的布排应注意避免塑料局部聚积
3)筋条排列要注意排列互相错开,这样才 能防止收缩不均匀,变形较小。
a)不合理
b)合理
图3.6 加强筋的排列方向
要能满足塑件的使用要求,应将塑件设计的尽量 紧凑、尺寸小巧一些。
2. 塑件的尺寸精度 – 是指所获得的塑件尺寸与产品图纸尺寸的符 合程度,即所获塑件尺寸的准确度。 – 影响塑件精度的因素较为复杂,塑件尺寸误 差的产生是多种因素综合影响的结果,因此, 在一般情况下塑件要达到金属制件那样的精 度是非常困难的。
l 对于模具设计者来说,在考虑塑件的结构及有关使用要 求时,还必须与成型该塑件的成型模具的相应结构结合 起来考虑,既要使塑料制件能按使用要求加工出来,保 证制件的质量,而又要使模具结构合理、经济。
在塑件结构工艺性设计时,应考虑以下几方面 的因素:
(1)塑料的各项性能特点; (2)在保证各项使用性能的前提下,塑件结 构形状力求简单,且有利于充模流动、排气、补 缩和高效冷却硬化(热塑性塑料制件)或快速受 热固化(热固性塑料制件); (3)模具的总体结构应使模具零件易于制造, 特别是抽芯和脱模机构。
第3章塑料制品的结构设计

4.圆角:
大小: 外圆角:R=1.5t; 内圆角:r=0.5t
4.圆角:
5.孔:
⑴塑件的孔三种成型加工方法: 直接模塑出来; 模塑成盲孔再钻通孔; 塑件成型后再钻孔。
当通孔孔径﹤1.5mm,由于型芯易弯曲折断,不适于模塑成型。 肓孔的深度:h ﹤(3~5)d
d﹤1.5mm时, h ﹤3d
较困难。 塑件壁厚过大,则不但浪费塑料原料,而且还给成型带来困难,尤其降低了
塑件的生产率,还给塑件带来内部气孔、外部凹陷等缺陷。 所以正确设计塑件的壁厚非常重要。壁厚取值应当合理。
常用:2-4mm(最小:0.25,最大:8-10)
原则:1、满足装配使用收力要求要求下,取小壁厚;
2、脱模顶出时零件不变形;
平板类零件加强筋方
2.
向与料流方向平行
加强筋设计要点:
3.
加强筋厚度小 于制品壁厚
4.
加强筋与支承 面间留有间隙
间距(2-3)t
加强筋设计要点:
增加刚性减少变形的其他措施:
①将薄壳状的塑件设计为球面,拱曲面等,可以有效地增加刚性、减少变形。
增加刚性减少变形的其他措施:
②薄壁容器的沿口是强度、刚性薄弱处赐于开裂变形损坏,故应
~ ~
二、塑料制品的结构设计
主要:
脱模斜度、壁厚、加强筋、圆角、孔、支撑面、 装饰标志、嵌件、分型面、强制脱模等。
1.脱模斜度:减小开模力和脱模力。
当塑件成型后因塑料收缩而包紧型芯,若塑件外形较 复杂时,塑件的多个面与型芯紧贴,从而脱模阻力较大。 为防止脱模时塑件的表面被檫伤和推顶变形,需设脱模斜度。
油
行喷涂处理
不同的光泽状
明显提高塑料件表面的外观档次,
塑件的结构工艺性

塑件的结构工艺性塑件的结构工艺性是指塑件设计的结构是否符合塑料制品加工的工艺要求。
塑料制品加工过程中,考虑到成型性、冷却性、顶出性、模具等因素,设计人员需要合理地设计塑料制品的结构,以提高制品的质量和生产效率。
首先,塑件的结构应具备成型性。
成型性是指塑料在加热融化后能够在模具中形成所需形状的能力。
因此,设计人员应根据塑料材料的特性,合理选择塑胶制品的结构形式,避免在注塑过程中发生热分解、气泡和熔接线等缺陷。
其次,塑件的结构应具备良好的冷却性。
冷却性是指在塑料制品注塑过程中,塑料材料能够迅速冷却并固化。
设计人员应考虑到塑胶制品的结构形状、壁厚以及冷却系统的设置等因素,以确保塑料制品在注塑过程中能够均匀地冷却,避免出现变形和缩水等问题。
此外,塑件的结构应具备良好的顶出性。
顶出性是指塑胶制品在顶出系统的作用下,能够顺利地从模具中取出。
设计人员应注意到塑料制品的结构形状和顶出系统的设计,避免塑件在顶出过程中出现变形、折断和卡死等情况。
最后,塑件的结构应考虑到模具的制造和使用。
模具的制造和使用对塑料制品的质量和生产效率有着重要的影响。
设计人员应根据塑料制品的结构形状、尺寸和要求,合理设计模具的结构和尺寸,以便于模具的制造和使用,提高模具的寿命和生产效率。
总之,塑件的结构工艺性是塑料制品设计中需要考虑的重要因素之一。
设计人员应根据塑料材料的特性和加工工艺要求,合理设计塑料制品的结构,以提高制品的质量和生产效率。
同时,设计人员还应注意到成型性、冷却性、顶出性和模具等因素对塑料制品的影响,以确保塑料制品能够顺利地生产并符合质量要求。
塑料制品在现代工业生产中得到了广泛的应用,其轻便、耐用、成本低廉的特点使得塑料制品成为替代传统材料的理想选择。
然而,要确保塑料制品的质量和生产效率,需要充分考虑塑件的结构工艺性。
下面将继续探讨塑件的结构工艺性的相关内容。
首先,塑件的结构形式对于成型性的影响非常重要。
不同的塑件形式对于塑料材料的流动和填充具有不同的要求。
零件结构的工艺性分析教材PPT(共 47张)

第五节 零件结构的工艺性分析
增设加强肋板
第五节 零件结构的工艺性分析
增设加强肋板
第五节 零件结构的工艺性分析
第五节 零件结构的工艺性分析
1、零件整体的结构工艺性
3) 有利于保证加工精度、减少辅助工艺时间, 提高生产率
(1)同类结构要素应尽量统一
第五节 零件结构的工艺性分析
第五节 零件结构的工艺性分析
尽量减少加工困难
析 方 法
零件装配拆卸的 结构工艺性
表面形状尽量和刀具形状一致 尽量采用标准化参数
合理使用组合件
•
1、不是井里没有水,而是你挖的不够深。不是成功来得慢,而是你努力的不够多。
•
2、孤单一人的时间使自己变得优秀,给来的人一个惊喜,也给自己一个好的交代。
•
3、命运给你一个比别人低的起点是想告诉你,让你用你的一生去奋斗出一个绝地反击的故事,所以有什么理由不努力!
•
4、心中没有过分的贪求,自然苦就少。口里不说多余的话,自然祸就少。腹内的食物能减少,自然病就少。思绪中没有过分欲,自然忧就少。大悲是无泪的,同样大悟无言。缘来尽量要惜,缘尽就放。人生本来就空,对人家笑笑,对自己笑笑,笑着看天下,看日出日落,花谢花开,岂不自在,哪里来的尘埃!
•
5、心情就像衣服,脏了就拿去洗洗,晒晒,阳光自然就会蔓延开来。阳光那么好,何必自寻烦恼,过好每一个当下,一万个美丽的未来抵不过一个温暖的现在。
第五节 零件结构的工艺性分析
一、零件结构的工艺性概念 二、零件结构的工艺性分析方法 三、具体实例分析
第五节 零件结构的工艺性分析
一、零件结构的工艺性概念
零件结构的工艺性 是指这种结构的零件被加 工的难易程度。
零件结构的工艺性良好,是指所设计的零件, 在保证使用要求的的前提下,能较经济、高效、 合格地加工出来。
塑件结构工艺性
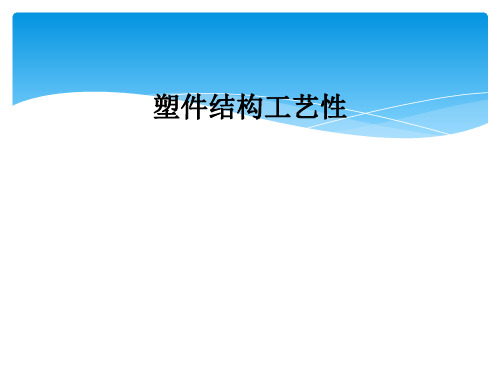
(4)塑件支承面的设计
当塑件上有一面作为支承面来使用时,将该 面设计为一个整面是不合理的,应采用如图319所示结构。
因为平板状在成型收缩后很容易翘曲变形, 稍许不平都会影响良好的支承作用,故以边框 式或底脚(三点或四点)结构设计塑件支承面。 如下图塑料盘所示。
对于细长型芯,为防止其弯曲变形,在 不影响塑件的条件下,可在塑件的下方设 支承柱来支撑。如图3-25所示。
斜孔或形状复杂的孔可采用拼合的型 芯来成型。如图7.5所示
5 带嵌件塑件的设计
在塑件内嵌入其他零件形成不可卸的连接,所嵌入 的零件即称嵌件。嵌件材料一般为金属材料,也有用 非金属材料的,例如玻璃、木材或已成型的塑件。 1、塑件中镶入嵌件的目的:
3.1 形状
当塑件的内外侧凹陷较浅,同时成 型塑件的塑料为聚乙烯、聚丙烯、聚 甲醛这类仍带有足够弹性的塑料时, 模具可采取强制脱模。
3 形状和结构设计
3.2 结构设计
为使强制脱模时的脱模阻力不要过大引 起塑件损坏和变形,塑件侧凹深度必须 在要求的合理范围内,见p222图7.2下 面的说明(公式),同时还要重视将凹凸起 伏处设计为圆角或斜面过渡结构。
增加局部强度、硬度、耐磨、导磁、导电性能,加 强塑件尺寸精度和形状的稳定性,起装饰作用等。 2、嵌件结构有柱状、针杆状、片状和框架等如图334所示。
5 带嵌件塑件的设计
3、嵌件设计的要点: ⑴ 嵌件应可靠地固定在塑件中,防止嵌
件在塑件中转动或被抽离。柱状嵌件可 在外形滚直纹并切出沟槽,或在外表面 滚菱形花纹。针杆状嵌件可切口或冲孔。 如图3-34所示。
3.5.3 模塑螺纹的结构设计
注塑模具结构最清晰讲解--图文含动画

模具结构概览
7
上固定板(S55C)
母模板(S55C)
母模仁 (P20\NAK80\420\S136 \SKD61\S13) 上定位块(SKD61) 塑胶制品 顶针(SKD61) 回位销(SUJ2) 导套(SUJ2) 斜顶(SKD61) 引导块(SKD61) 斜顶座(SKD61\SK3) 耐磨块(SKD61\SK3\PDS) 模脚(S55C) 下固定板(S55C)
编写目的,则是为了让年轻产品工程师更好认识注塑模具,了解模具包含哪些结构,模具结构的动作怎么进行,模具工件怎么 加工出来等;当遇到新项目设计时,能大致评估零件注塑的可行性和难度系数;当遇到零件变更或改善时,能大致评估改动的 模具工件以及调整费用。知其然并知所以然。
主讲人:
IVU
Ye
注塑模具结构讲解
01 产品分模/流道系统 02 模具结构概览 03 斜顶机构原理 04 滑块机构原理 05 冷却系统 06 产品顶出 07 典型模具零件加工及设备
2
IVU
Ye
产品分模
3
正面
背面 产品3D图
正面
背面 分模图
分模线,公母模仁结合面。 本产品的背面槽穴非常多,因此把 背面定为公模,顶针将从公模向外 顶出,易于脱模。
IVU
Ye
产品顶出
21
母模
复位弹簧
锁死合模状态(正面)
公模 锁死合模状态(侧面)
公模后退
开模过程:母模不动,公模后退一段距离不动,此时注塑机的推杆带动推板使得顶针一起向前,拉料杆保持不 动(倒钩结构可将产品向下拉扯),从而顺利将产品顶出。 合模过程:产品掉落后,注塑机推杆收回,推板在复位弹簧作用下回缩,公模向母模前进,进入下一个循环。
前模芯,与后模共同形成产品特征。 后模芯,与前模共同形成产品特征。
- 1、下载文档前请自行甄别文档内容的完整性,平台不提供额外的编辑、内容补充、找答案等附加服务。
- 2、"仅部分预览"的文档,不可在线预览部分如存在完整性等问题,可反馈申请退款(可完整预览的文档不适用该条件!)。
- 3、如文档侵犯您的权益,请联系客服反馈,我们会尽快为您处理(人工客服工作时间:9:00-18:30)。
一
项目导入
二
相关知识
三
项目实施
一、 项目引入
灯座(如图1-1所示)塑件和电流线圈架(如图1-13所示)的结 构工艺性能是否合理,并能对塑件的结构不合理的地方进行修改。
图1-1 灯座二维图形
图1-13 电流线圈架零件图
二、相关知识
(一)塑件设计基本原则
1、塑料制件的尺寸
指塑料制件的总体尺寸: 塑料流动性 现有的成型设备规格、参数
二、相关知识
(一)塑件设计基本原则
2. 塑料制件的尺寸精度
塑件尺寸公差代号MT,分7级, 每一级分A、B两部分: A为不受模具活动影响的尺寸公差;B为受模具活动影响的尺寸公差 每一种塑料分3个精度等级 表中只规定了公差值,上、下偏差可根据塑件的配合性质来分配。
通常偏差根据“凸负凹正,中心对正”
二、相关知识
二、相关知识
(二)塑件局部结构设计
1.加强筋与防变形机构
设计原则:
为了提高塑件的强度和刚度,不能仅仅采用增大壁厚的方法,而常采用改 变塑件的结构、增设加强筋的方法来满足其强度、刚度的要求。
采用增设加强筋的方法优点
1、 有时还能降低物料的充模阻力 2、 保证塑件的强度、刚度,而且还避免了塑件壁厚的不均匀
加强筋布置的注意事项
1、 加强筋应设在受力大,易变形的部位,其分布尽量均匀 2、 避免设加强筋后塑件局部壁厚过大 3、 尽量沿着塑料流向布置。以降低充模阻力 4、 设计成球面、或拱面,也可有效增加刚性和防止变形
二、相关知识
(二)塑件局部结构设计
2.支承面
设计原则:
当塑件需有一个支承面时,不能用整个底面作为支承面,因为稍许的 翘曲或变形就会使整个底面不平。设计塑件时通常采用凸边或几个凸起的支 脚作为支承面。当底部有加强筋时,支承面的高度应略高于加强筋。
直接成型 设计注意事项:
1、
直径——为便于螺纹型芯和螺纹型环的加工,塑件的直径不应太小,一般外螺纹直径不小于 4mm,内螺纹直径不小于2mm。
2、
螺距——螺距不能太小,一般选用公制标准螺纹,M6以上才可选用1级细牙螺纹,M10以上 可选用2级细牙螺纹,M18以上可选用3级细牙螺纹,M30以上可选用4级细牙螺纹
2、塑料制件的尺寸精度
为满足塑料制件的装配要求和零件的互换性要求 模具的制造误差 塑料材料的成型收缩率波动 模具在使用过程中的磨损 飞边厚薄的变化 型腔的变形模具零件相互之间的安装定位误差 模具的结构(浇口尺寸和位置、分型面位置、模具的拼合方式) 成型后的条件(测量误差、存放条件)
影响因素众多,设计塑件时需综合考虑 塑件的尺寸公差GB/T14486-1993
设计原则: 塑件的壁厚应根据塑件的使用要求来确定。尽量做到壁厚均匀,一
般为1~4mm范围
壁厚 材料消耗增大,成型效率降低,使塑件成本提高。而且还容易 过厚 产生气泡、缩孔、翘曲等缺陷
壁厚 易脱模变形或破裂,不能满足使用要求,且难以充满,成型困 过薄 难——最小壁厚(见经验表格 )
推荐值:热固性塑料制品——参见表3-5 热塑性塑料制品——参见表3-6
(一)塑件设计基本原则 2.塑件的表面质量及表面粗糙度
选择原则:
塑件的表面粗糙度值大小,主要取决于模具型腔(凸凹模)的表面粗 糙度。一般模具型腔的表面粗糙度应比塑件的表面粗糙度值小1~2级。
从塑件的外观和塑件的充模流动角度考虑:
通常应小于Ra 0.8 , 有时需小于Ra 0.1。
为便于加工(降低加工成本):
二、相关知识
(一)塑件设计基本原则
4.脱模斜度
塑料在模腔中冷却收缩,便包紧型芯或型腔中的 凸起部分,为了便于脱模和抽拔,避免脱模和抽拔时 塑件产生划痕、拉毛、变形等缺陷,设计塑件时,沿 脱模和抽拔方向其内外表面均需有一定的斜度。称为
脱模斜度。一般斜度取 30 ′~ 1˚ 30 ′。
设计脱模斜度遵循原则:
( 1 )塑料的收缩率大,壁厚,斜度应取偏大值 ( 2 )塑件结构复杂,斜度应取偏大值 ( 3 )型芯长或深型腔为了便于脱模,在满足制件的使用和尺寸公差要求的前提下斜度值 取大值 ( 4 ) 一般外表面的斜度小于内表面的 ( 5 )热固性塑料小于热塑性塑料
二、相关知识
(一)塑件设计基本原则 5.壁厚
3.圆角 设计原则:
塑件的面与面之间一般均采用圆弧过渡,这样不仅可避免塑件 尖角处的应力集中,提高塑件强度、而且可改善物料的流动状态, 降低充模阻力,便于充模。另外可便于模具的加工制造及模具强度 的提高,避免模具在淬火或使用时应力开裂。
二、相关知识
(二)塑件局部结构设计
4.孔的设计 设计原则:
根据使用要求(固定、装配)塑件一常需设有孔。孔的位置,应不至 影响塑件的强度,故孔与孔之间、孔与边缘之间应留一定的距离。为了便于 成型及满足孔的质量要求,直接成型的孔的深度不能过大。
避免侧孔或 侧凹
改变侧孔斜度,避免 侧抽芯机构
改变塑件角度,避免 侧抽芯机构
菱形纹改为直条纹, 避免瓣合模机构
有侧凸、侧 凹的强 制脱模的
条件
1.塑件具有足够的弹性 (如PE、PP、POM等塑料) 2. ( A-B )/ B ≤ 5 %或 ( A - B ) /C ≤ 5 % 否则用侧向分型抽芯等结构
3、 精度——由于影响塑件螺纹精度的因素较多,在满足使用要求的前提下,精度宜取低
4、
配合长——如果在确定模具上螺纹的螺距时没有考虑塑料的成型收缩率,当不同材料的塑件 螺纹相配合时,其配合长度应不超过7-8牙。
5、
螺纹始端末的形状——为防止塑件螺纹第一扣崩裂或变形,同时便于螺纹的旋合,内螺纹、 外螺纹的两端均应设计无牙段,螺纹的始末部分均有应过渡段),过渡段长度见表2-15
塑件上的固定孔与其它受力孔的周围应采用凸边予以加强。
成型塑件孔的型芯的安 装方式通常有三种:
通孔 盲孔(注射 h<4d) 特殊孔
二、相关知识
(二)塑件局部结构设计
5.螺纹的设计
设计原则:
塑件上的螺纹可以在模塑时直接成型,也可在模塑后用机械切削方式加工,对经常装拆和受力 较大的螺纹,可使用金属的螺纹嵌件。
对于非透明的塑件,可将外观要求不高的内侧表面粗糙度值取大些。而 透明的塑件,内、外侧表面粗糙度值应相同。
二、相关知识
(一)塑件设计基本原使用要求外,还应尽可能使其所对应的模具 结构简单便于加工。(避免侧抽芯机构、避免瓣合模机构)
改变侧孔形状,避免 侧抽芯机构