总装组装工程标准工时线平衡表格
标准工时库(例表)

序 号
1 2 3 4 5 6 7 8 9 10 11 单位
编号
C000222302 XXXX XXXX XXXX XXXX XXXX XXXX XXXX XXXX XXXX XXXXBiblioteka 品名Z2QC3BMX
车间 灶具总装
年度基准 标准工时 分钟/个 100.06
1月 标准工时 分钟/个 24.49 线平衡率 % 75.10% 节拍 秒 57.32 标准产能 个/小时 63 人力 人 29 标准工时 分钟/个 22.5955 线平衡率 % 81.67%
2月 节拍 秒 51.92 标准产能 个/小时 69 人力 人 29 标准工时 分钟/个 线平衡率 %
3月 节拍 秒
4月 标准产能 个/小时 人力 人 标准工时 分钟/个 线平衡率 % 节拍 秒 标准产能 个/小时 人力 人 标准工时 分钟/个 线平衡率 %
5月 节拍 秒 标准产能 个/小时 人力 人 标准工时 分钟/个 线平衡率 %
6月 节拍 秒 标准产能 个/小时 人力 人 标准工时 分钟/个 线平衡率 %
7月
7月 节拍 秒 标准产能 个/小时 人力 人 标准工时 分钟/个 线平衡率 %
8月 节拍 秒 标准产能 个/小时 人力 人 标准工时 分钟/个 线平衡率 %
9月 节拍 秒 标准产能 个/小时 人力 人 标准工时 分钟/个 线平衡率 %
10月 节拍 秒 标准产能 个/小时 人力 人 标准工时 分钟/个
11月 线平衡率 % 节拍 秒 标准产能 个/小时 人力 人 标准工时 分钟/个 线平衡率 %
12月 节拍 秒 标准产能 个/小时 人力 人
下一年基准 标准工时 分钟/个
备注
线平衡计算 标准工时表

件/小時
1
1.42
5.17
6.58
3.29 18.23
1
0.67
1.50
2.17
2.17 27.69
1
2.00
6.67
8.67
2.17 27.69
1
3.00
0.00
3.00
2.50 24.00
1
0.50
0.00
0.50
2.50 24.00
设备 台数
2.00 1.00 4.00 0.00 0.20
人数 日班 夜班
版本:1 备注
3.0
3.0 测量者:
1.0
1.0 A:
4.0
4.0 A:
1.2
1.2 B:
1.0
1.0 清洗、包检:
备注:工序设备平衡时间=总分钟/设备台数 工序人工平衡时间=总分钟×人数
汇总
■ 总观测时间: ■ 人力: ■ 循环时间(最佳): ■ 85%产出/班
20.9 总分钟(分钟)■ 瓶颈时间 (SOP Rate3):.29
料号: 57壳体
工序
站別 / 说明
210 车外圆内孔、铣扁方
220 车另一端外圆内孔
230
铣外轮廓
240
去毛刺
250
清洗
标准工时表/线平衡
机器设备 & 治工具
车铣复合 数控车床 数控铣床
人工 清洗机
57-210 57-220 57-230
N/A 清洗篮日期时间:2来自19/9/4标准工時件/站
辅助时间 设备时间 总分钟 平衡时间 (分钟) (分钟) (分钟) (分钟)
10 人
■ 线平衡效率:
88.3
IE标准工时及线平衡

61.8
65.77
40.00
12.7
0.00 1 2 3 4 5 6 7 8 9 10 11 12 13 14 15 16
备注:
产线布局图(Line Layout)
工序 2-2
宽放率:人工8%,设备(治具)10%
TOTAL工序时间:'Tc'=Σ Tc' 节拍时间(s):'Ts'=Max('C/T') 标准工时(s/PCS):'ST'='Ts'*'N' 22547.9 156.26 39845.1 23.0 255.0 0.1 0.4
23 29 37 40 43 53 58
160.00
156.3
151.3
140.00 123.8 120.00 100.5 90.5 83.8 80.00 68.5
61.8 60.00 43.1 70.8 93.4
104.0
100.00
98.0
51 39 36 58 84 283 35 24 55
20.00
生产线平衡率计算表
Doc. NO.文件编号 Schedule Qty 数量(PCS/11Hr): NO.of pro工序编号 1 2 3 4 5 6 7 8 9 10 11 12 13 14 15 16 ProcessName 工序名称 253.4 Time of Pro工序时间(S) TC 1562.6 5324.7 784.0 1266.8 1257.3 205.5 247.1 2972.0 373.4 1708.1 803.2 560.3 229.0 3537.4 1058.8 657.70 No.of Operators 人员安排 Model (型号): T/T (节拍): Cycle time 周期时间 (S)C/T 156.3 UPH 每小时产量 (PCS/Hr) Labour(人力) Machine Requirement 设备 需求
标准工时及产能测算表

标准工时及产能测算表
表格编号:XX/QR-SC-014A 说明:本文档主要用于测算某一生产线各工序的标准工时以及标准产能,同时可以用来进行生产线工序平衡分析。
本表格对标准工时、瓶颈工时、产线平衡率、人均产能等关键数据的计算方式进行了详细说明,且在表格中以自动函数形式呈现。
(表格中内含自动计算公式,只需录入部分基本数据即可。
)
3.标准工时=实测时间(即表格中平均工时)×评比系数×(1+宽放率) 4.总标准工时=各工序标准工时之和;
5.瓶颈工时=所有工序中标准工时最大值(工位平衡时间最大值); 6.产线平衡率=总标准工时/(瓶颈工时×直接人力总数);
7.不平衡损失=瓶颈工时×直接人力总数-总标准工时; 8.损失率=(1-产线平衡率)*100%
9. 生产线每小时产能(最大产能)=3600/瓶颈工时; 10.每小时人均产能=3600/(瓶颈工时×直接人力总数)。
标准工时统一表格(模板)
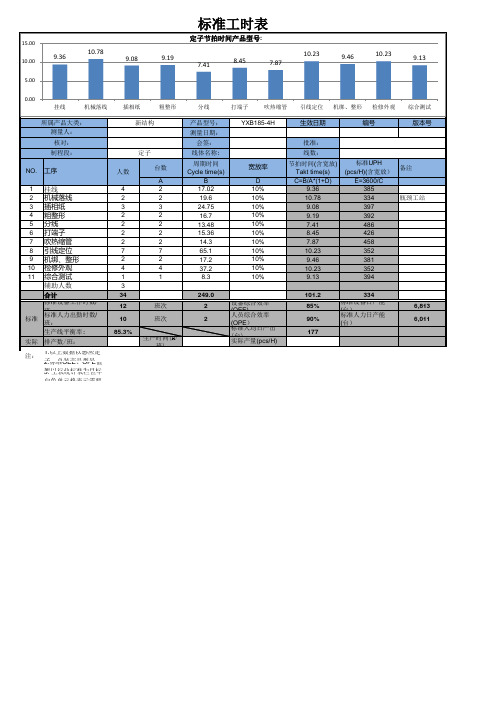
标准UPH (pcs/H)(含宽放)
E=3600/C 385 334 397 392 486 426 458 352 381 352 394
备注 瓶颈工站
101.2 85% 90% 177
334 标准设备日产能
(标台准)人力日产能
(台)
6,813 6,011
新结构
定子
人数
4 2 3 2 2 2 2 7 2 4 1 3 34
12
10
85.3%
台数
A 2 2 3 2 2 2 2 7 2 4 1
班次 班次
生产时间(H/ 班)
产品型号: 测量日期:
会签:
线体名称: 周期时间 Cycle time(s)
B 17.02 19.6 24.75 16.7 13.48 15.36 14.3 65.1 17.2 37.2
1 挂线 2 机械落线 3 插相纸 4 粗整形 5 分线 6 打端子 7 吹热缩管 8 引线定位 9 机绑、整形 10 检修外观 11 综合测试
辅助人数
标准
合计 标准设备工作时数/ 班标: 准人力出勤时数/ 班:
生产线平衡率:
实际 排产数/班:
注:
1.以上数据以感应定 子2.标、准总O装E产E、品O型P号E值 暂3. 以上行表业统标计准表为栏目位标中 白色单元格表示需要
15.00
10.78
10.00
9.36
9.08
5.00
标准工时表
定子节拍时间产品型号:
9.19
7.41
8.45
7.87
10.23
9.46
10.23
9.13
0.00
挂线
机械落线
插相纸
标准工时产能表

标准工时表依据公司近期内实际生产和目标,制定如下标准:补充说明:一﹑优化生产线1.降低生产成本:包括人工成本﹑管理成本及物料搬运成本等﹐并且由于产量之提高﹐使分摊之各项间接费用也随之降低﹒2.提高工作效率:由于各站工作之固定化﹐不必要之寻找﹑思考等心力工作大幅减少﹐使工作效率提高﹒3.简化管理工作:包括人员训练﹑工作督导﹑产量计算﹑品质追踪等等管理工作都能简化.4.减少物料搬运:由于生产线之制造流程和搬运路径相同﹐并且常使用定路径之搬运设备(例如输送带﹑定轨式吊车﹑台车﹑吊蓝)搬运﹐因此物料搬运量减少﹒5.能满足大量生产之需要:在各种复杂性产品之生产技术中以生产线技术之大量生产投资及单位生产成本最低﹒除衣衫五项以外,采用生产线还可以节省厂房面积﹐减少半成品中间库存﹐并且还可以使员工容易产生认同感和归属感之优点﹒二、生产线有关名词之解说﹕生产线有关名词极多﹐以下仅选择较常用的名词说明﹕1、工作站(WORK STATION)﹕又称作业站﹐是在生产线上执行一项工作或一组工作之工作单位,生产线系由若干工作站所组成﹐在工作站上执行工作之人员称为工作员﹐作业员或操作员,每作业站之作业人员通常为一人和一组作业员﹐视实际需要调派﹐生产线上所含工作站之数目以K代表﹒2、单元(WORK ELEMENT OR WORK UNIT)﹕生产线上每一工作站通常都包括若干工作项目,每一工作项目称为一个工作单元﹒一般而言公共单元之划分以能够独立成一工作为原则.常用之代号U或E﹐第I个工作单元称为Ui或Ei,大的工作单元有部分可划分为较小工作单元﹐部分则较困难﹒3、作单元时间(performance time):每一工作单元执行一件工作所需之时间称为工作单元时间﹐常用代号为ti.工作单元时间一般受制造程序之影响﹐当程序之安排足以影响该工作单元之执行时﹐工作时间将增加﹒4、作业站时间(station time): 指每一工作生产一件产品所需要之时间而言,亦即一工作站处理所含工作单元所需时间之总和﹐使用之代号为T﹒5、周期时间(cycle time):生产线生产一件产品所需之时间,亦即两产品进入(或离开)生产线之间隔时间﹐常用代号C﹒生产线周期通常等于生产线上最长作业站时间﹐亦即:C=Tmax.6、线长(line length):指生产线之长度而言﹐单位为呎或米﹐采用之代号为L.7、线速(line speed):产品在生产线上移动之速度,单位为每分钟若干米或若干呎﹒通用代号为S﹒8、在线制品:在生产线上流通之产品﹐以N代表﹒在线制品通常均较工作站数为多﹐即N大于K﹒9、呆滞在线制品:生产线上之在线制品理论上只有K件(即每一工位只有一件)﹐但实际作业上往往大于K.大于之理由有以下几个﹕(1)在生产线上往往有复合作业站存在﹐若一复合作业站拥有五个工作单元﹐则在生产作业中可能同时拥有五个在线制品﹒(2)有空白作业站存在,在生产线中若输送带过长或作业站过少时﹐生产线上会发生闲置之在线制品.(3)生产线上制品之输送以批次搬运(以集中搬运方式搬运)时﹐在线制品将大于生产线之站数,在线制品大于作业站部分称为呆滞在线制品﹐以I为代号﹒10、在线时间:任何一产品自进入至离开生产线所花之时间﹒若欲求平均在线时间则尚需视批次(lot)之多寡而定﹒生产线上线速﹑线长﹑在线制品﹑在线时间之相关性如下﹕(1)线速=线长/(在线制品*周期)即S=L/CN(2)线长=周期*在线制品*线速即L=CNS(3)周期=线长/(在线制品*线速)即C=L/NS(4)在线制品=线长/(线速*周期)即N=L/CS=I+K=在线呆滞制品+作业站数(5)在线时间=(在线存货+在线制品)/线速=(B+K+I)/S11、作业顺序圈(Procedure diagram):制品制造程序表示法之一种﹐与一般制程分析圈相似﹒(1) (2) (3)(0) (4) (6) (7) (9) (10)(12) (11) (13) (14) (15) (16)(8)12、瓶颈(Bottleneck)﹕在生产线中最慢之工作站﹐亦即是生产联机操作粘时间最长之作业粘﹐称为生产线之瓶颈﹒瓶颈在一般生产线中几乎永远存在﹐消除一个瓶颈又产生另一个瓶颈﹐而瓶颈之宽窄决定生产线之产量及效率﹒13、闲置时间(idle time):任一工作站执行一工作(即生产一件产品)所浪费的时间﹒闲置时间常用代号为D﹒限制时间等于生产线周期减去各作业粘之站时间﹐即D=C-T ﹒14、平衡(Balance)﹕生产线各工作站工作速度相近情形﹐称为生产线平衡﹐或指生产线达到所需生产速度而言﹒理论上﹐完全之平衡绝对无法存在﹐因此通常所谓平衡多指合乎需要之生产速度﹐或合乎需要之生产效率而言﹒研究﹑分析或处理生产线平衡之工作称为生产线平衡作业﹒15、平衡闲置时间(balance delay)﹕在生产线平衡状况下各站闲置时间常用代号BD.平衡闲置时间与总生产时间之比率称为平衡闲置时间率﹐常用代号为d﹒计算公式如下﹕BD=KC-ΣtiD=TBD/K.C=(KC-Σti)/(K.C)16、平衡系数(smoothness index):表示平衡状况之系数﹐亦即各作业粘时间之标准差﹐但一般标准差之计算方法是以平均值为基础﹐平衡系数之计算则以工作站时间之最大值(即生产线周期)为基础﹒计算公式如下﹕Σ(C-Ti)2S.I.=K三、生产线之设计与建立1﹑生产过程之考虑﹕以生产线制造的产品﹐其制造过程基本上是属于流程型工厂)FLOW SHOP)之生产类型﹒这种生产过程我们可以再加以细分成下列三种﹕(1)线型过程﹕这是比较简单的产品制造过程﹐较常见于制造型生产线﹐这种生产过程中没有分支﹐也没有中间投入之物料零件(如图2-1A)﹒(2)构型生产过程﹕这种过程最为常见﹐一般装配性发品之制造都可以属于这一种(如图2-1B)﹒(3)网络型生产过程﹕生产过程为网络型﹐见于较复杂产品之制造(如图2-1C)﹒直线型生产过程1 2 3 4 11 13 16 17 5 6 7 9一般生产线之设计及平衡编排﹕2﹑一般型生产线设计之参考原则﹕生产线设计以能增加生产产量,提高机器使用率,简化管理﹐工作降低生产成本为目的﹐因此在设计工作中应循下列原则﹕(1)可能减少产品在线上之移动距离﹒(2)持产品在生产线上稳定之流通﹒(3)个作业站工作分配合理﹐尽可能做到责任分明﹑工作分配平均之程度﹒(4)尽可能一条生产线生产一种产品或一个产品系统﹒(5)各站各工作单元之作业顺序尽可能固定﹒(6)线上产品愈少愈佳﹐产品在线上时间愈短愈好﹐必要时可使用支线﹒(7)各站之作业时间愈接近愈好﹐并尽可能使各作业站是工作接近同步﹒(8)生产线调整弹性良好﹒四﹑生产线改善技术﹕1.产品布置平衡的先决条件﹕在研讨产品布置的平衡时﹐必须先研究下列三个先决条件﹕(1)测定标准工时﹒各操作应先将方法标准化,然后利用各种测时的技术,订出各操作的标准工时﹐作为计算平衡时的依据﹒(2)决定不平衡率﹒虽然目的是在求其平衡,然而欲使不平衡率达0%,事实上是不可能的﹐但如大于30%-40%,则时间的损失亦甚为惊人,故通常应订出一允许不平衡率,作为调整平衡时的参考﹒一般求不平衡的公式为﹕不平衡率=(3)管理者的观念﹒有人重视控制产品周期时间于某一定值,如此当可稳定一天的产量,但也有人注意控制作业人数于某一定数,如此则分派人员时必须尽量能获得最小的周期时间,亦即能有较多的产出﹒2.生产线布置平衡常用的方法﹒生产线布置的平衡,并无任何公式能计算设备特殊的平衡,可是工作的经验,以及工作情形的分析常是最好的求平衡的方法﹐至于一般的求平衡的方法约有下列几种﹕(1)改善工作方法﹕对各费时较多的工作站,利用改善工作方法的技巧改善其工作方法,并设计夹具与改良工具﹐以缩短其所需时间﹒(2)调整工作﹕将整个程序内的各操作重予组合﹐以求其平衡﹒(3)需时间较长者分割﹕凡工作站需时较长者,分由两台或两台以上的机器或人员去作,以求各工作站间时间的平衡﹒(4)最小公倍数法﹕求各工作站所需时间的最小公倍数,为调整机器设备或人员的根据,此法常须增添机器设备与人员﹐且增加其产量﹐故须视资金及市场状况才能决定﹒(5)将若干需时较少者合并﹕将需时较少的若干工作站合并,不但可获得较佳的平衡,同时亦可获得较少工作人员的结果﹒(6)工作人员的选择﹕选用效率特优人员担任工作较多需时较多工作站的工作,效率较差人员担任工作较少工作站的工作﹒(7)增加其它零碎工作﹕如对工作较少的工作站,确无其它方法平衡时,则可增加其它零碎工作,一面操作人员发生等待﹒(8)设置替班人员﹕最好能设置副线长或线长助理等替班人员,平时可协助线长担任线上工作的督导并可担任领料发料等供应工作,遇有人员缺勤时可临时替补,以免影响整个线上平衡.通常因无替班人员的设置,常将缺勤人员的工作,分配其前后工作点担任,如此﹐则势必将影响整个线上的平衡及产出﹒3、生产线编成效率改善例举:假设某一生产线之各工作站之作业顺序及发生工时如下:13+4+4+7+7+8+9+58个人每人的工作时间;a)此共8工作站8人的分业作业生产方式,暂存与特料随之发生相当多,Line编成效率非常坏.一般Line编成效率或不平衡率,如前述之计算公式:(8*13)-(13+4+4+7+7+8+9+5) 104-57Line不平衡率= = *100﹪8*13 104=45.2%(2)若将上叙之各工程加以分配,使人员之负荷增加,则Line之可能组合有下列几种情况,而平衡率之变化也因此产生差异:请试算当中上个工作站分割时,则其Line编成效率为何?(3)由上叙一中,假设1人1日每日实际作业时间为7HR/日则1人1日之生产量与Line 之总生产量之变化如下: (表二)●由上叙二中,2人编成之总生产量为8人编成之总生产量之868÷1936=44.8%●由表二中,若2人编成之Line以4条Line生产即8人生产再与8人编成之Line比较: (868×4)÷1936=3472÷1936=179%即产量可UP179%(4)由表一与表二中可发现:○1Line之编成效率与Line之Neckpoint(瓶颈)有关○2产量之多寡与人员之编成有关○3要提高Line之效率,必须使Line Balance○4要提高总产量,则以效率高之组合来编成○5Line之编成,必须以产量为基准,求出时间标尺实际作时间7×60×60时间标尺===13sec产量193813+4+4+7+7+8+9+5 57人员数===4.4人13 1314也即以5人编成Line较合理,较具弹性,四、合理化重点改善:(1)由Line编成效率之流程图中,显而易见此工作站系整个Line瓶颈(Neckpoint)若将A工作站加以作业改善或设备性能使之降为9sec,则整个Line之效率变化为:(与8人之改善前比较)9+4+4+7+7+8+9+5○1Line效率==73.6%9×8比较:来54.8% 73.6% UP 18.8%○2产量:7×60×60÷9=2800台/日比较:2800-1936=864台/日UP 864台/日。
标准工时及线平衡率

确定标准时间
制造管理系统精益管理培训课程
1 标准工时—秒表测时
◆秒表测时的步骤
获取资料 作业分解 确定观测次数
测时 剔除异常值
评比系数: 人的动作可能比标准动作快,也可能比标准动作慢,
所以必须利用评比系数进行修正 正常时间=测量时间平均值*评比系数
国际公认评定基准: 1) 60MIN步行4.8KM 2) 0.5MIN将52张扑克牌发成4堆 3 )0.41MIN将30各销子插进30个孔
4 3.63 13.17 3.58 20.18 2.65 9.10 29.65 2.72 10.35 22.28 4.05 20.71 22.35 5.69 30.65 7.87 16.58 15.28 4.25 23.77 4.21 14.62 13.28 10.00 18.65 7.68 24.65 11.68 16.00 22.52 40.36 16.68 20.95 120.68 36.85 8.54 22.54 7.68 21.25 33.79 3.65 9.92 9.18 33.68 40.65
在可靠度为95%,精确度为5%时,测量次数为
案例:设在测时中,现对某操作单元观测10次,得其时间分别为7S、5S、6S、 8S、7S、6S、7S、6S、7S,要求可靠度95%,精确度5%,求观测次数?
解:据10次观测结果,可求得:∑X=65, ∑Xi²=429,n=10 n‘=(40S/X)^2)=28次
固定档热板
取水汽联动阀,取下防尘盖
火排-水汽联动阀 组装
固定火排,水汽联动阀,点火针
放火排-水汽联动阀组件
固定出水管
固定火排-水汽联 动阀组件
固定火排-水汽联动阀组件
穿螺钉*4
放进气接头,进水接头并拧紧 固定进水管
标准工时及产能计算表

#DIV/0!
20
#DIV/0!
1
10% #DIV/0!
#DIV/0!
21
#DIV/0!
1
10% #DIV/0!
#DIV/0!
22
#DIV/0!
1
10% #DIV/0!
#DIV/0!
23
#DIV/0!
1
10% #DIV/0!
#DIV/0!
24
#DIV/0!
1
10% #DIV/0!
#DIV/0!
25
#DIV/0!
工序 1
作业内容
实测作业时间(s/pcs)
实测1 实测2 实测3 实测4 实测5 实测6 实测7 实测8 实测9
实测 10
平均工时 (s)
#DIV/0!
评定系 数
宽放率
标准工时 (s)
1
10% #DIV/0!人力配置 (人)工源自标准工 时(s)#DIV/0!
2
#DIV/0!
1
10% #DIV/0!
#DIV/0!
#DIV/0!
9
#DIV/0!
1
10% #DIV/0!
#DIV/0!
10
#DIV/0!
1
10% #DIV/0!
#DIV/0!
11
#DIV/0!
1
10% #DIV/0!
#DIV/0!
12
#DIV/0!
1
10% #DIV/0!
#DIV/0!
13
#DIV/0!
1
10% #DIV/0!
#DIV/0!
14
#DIV/0!
3
#DIV/0!
1
标准工时计算表(适用于流水线)

制 定:
日 期: 页 次: 版 本:
线平衡率
标准工时(H/PCS)
每日总产 量(PCS)
工作量
备注
卡螺外母观簧检带查轮/包装 &端子压接
产品标准工时表
工序 代码
1
产品型号 产品名称 相关产品 生产单元 工序号
WS-Wahoo Bike-100
工序名称 定子铁芯浸漆
每日计划产量(PCS)
每日最大产量(PCS)
每日工作时间(H)
每时最大产量(PCS)
目标周期时间(S)
标准工时合计(S)
最长周期时间(S)
使用人数总计
观测时间 (S)
宽放率(%)
标准工时 (S)
电脑建议 人数
分配使用 人数
每人均分 每小时总 工时(S) 产量(PCS)
2
WS-Wahoo Bike-105
装骨架
3
WS-Wahoo Bike-110
定子绕线
4
WS-Wahoo Bike-115
分线/去漆
5
WS-Wahoo Bike-120
并头/接线
6
WS-Wahoo Bike-125
绑线/外观检/综测
7
WS-Wahoo Bike-127
定子浸漆
WS-Wahoo Bike-128
浸漆定子清洁
9
WS-Wahoo Bike-130/1
清洁螺钉孔
10
WS-Wahoo Bike-130/2
涂胶装飞轮盖
11
WS-Wahoo Bike-130/3
组装线生产线平衡和排位图(exe自动生成)

每日实际完成量:
天
320 34.51%
台
台
预计工作天数: 预计工作天数: 7
ቤተ መጻሕፍቲ ባይዱ
每日实际完成率:
部件
位第No. 位第No. No 第一道工序 第二道工序 第三道工序 第四道工序 第五道工序 第六道工序 第七道工序 第八道工序 第九道工序 第十道工序 第十一道工序 第十二道工序 第十三道工序 第十四道工序 第十五道工序 第十六道工序 第十七道工序 第十八道工序 第二十道工序 第二十一道工序 第二十二道工序 第二十三道工序 第二十四道工序 第二十五道工序 第二十六道工序 第二十七道工序 第二十八道工序 第二十九道工序 第三十道工序 第三十一道工序 第三十二道工序 第三十三道工序 第三十四道工序 第三十六道工序 第三十七道工序 第三十八道工序 第三十九道工序 第四十道工序 第四十一道工序
68404153.xls 生产线平衡 2011-11-5 20:54
第 1 頁,共 1 頁
操作人数 操作人数 1 1 1 1 1 2 2 1 1 1 1 1
操作员工 操作员工 1 2 3 4 5 6 7 8 9 10 11 12
工序号 A/CE-01 CE- A/CE-05 CE- A/CE-25 CE- A/CE-10 CE- A/CE-15 CE- A/CE-20 CE- A/CE-35 CE- A/CE-36 CE- A/CE-60 CE- A/CE-45 CE- A/CE-50 CE- A/CE-61 CE-
各工序 A/CE-01
A/CE-05
A/CE-25
A/CE-10
A/CE-15
A/CE-20
A/CE-35
A/CE-36
A/CE-60
A/CE-45
工时平衡表xls

#DIV/0!
前加工標准工時(SEC) 0.00 產品標准工時(SEC) 0.0
生效日期
裝配線標准
注:多個工站配合平衡時﹐平衡損失率以10%計算﹔ 產能
裝配線標准
產能
#DIV/0! #DIV/0!
SBU:
單站工時
裝配線工時
人數 平衡工時 #DIV/0! #DIV/0! #DIV/0! #DIV/0! #DIV/0! #DIV/0! #DIV/0! #DIV/0! #DIV/0! #DIV/0! #DIV/0! #DIV/0! #DIV/0! #DIV/0! #DIV/0! #DIV/0! #DIV/0! #DIV/0!
實際平衡損失率
標准平衡損失率 寬放率:
C.T.TIME(SEC.) 裝配線排配人數(人)
換線工時(分) 成型標准工時(SEC)
人均產能(PC/8H)
#DIV/0!
10.0% 10% #DIV/0! 0.0 0.00 0.00 #DIV/0!
File Name:
適用 產品
制造程序與工時平衡表(裝配段)
Rev:
0
產品系列
序 號
工站名稱
使用材料
方法
1 2 3 4 5 6 8 7 9 10 11 12 13 14 15 16 17 18 19 20
核定
審核 制定 IE
裝配線單站 總用時(時
0.00
裝配線標准 產能
标准工时设定与生产线平衡

第三阶段:新方法按ECRS原则展开
第四阶段——新方法的实施
第一阶段: 作业分解 ------全部操作项目明细化
▪ 搬送作业、机械作业、手作业全部项目明细化
第二阶段: 1.对每个项目明细化进行自问5WIH法
2、同时进行以下9个自问:
材料、机械、设备、道具(工具、夹具、 计测器)设计、配置、动作、安全、整理、 整顿 3、应用动作经济性原则、流程经济性原则 作为着眼点与实施手段
产品工艺流程线路
1. 路线最短原则 2. 禁止孤岛加工 3. 禁止局域路线分离 4. 减少停滞的原则 5. 禁止重复的停滞 6. 禁止交叉
7. 禁止逆行生产线 8. 减少物流前后摇摆 9. 减少无谓移动 10. 去除工序间隔 11. I/O一致原则 12. 物料上下移动减少
作业流程
▪ 1.线路最短原则
11
选 择
Select (ST)
12 思 考
Plan (PN)
13 预 定 位
PrePosition
(PP)
14
定 位
Position (P)
指定选择 物的箭头 形状
B
多个物品中选择需要物品 的五官动作
手放头部 思考的形 状
B
作业中决定下一步工作的 思考与计划
保龄球立 直的形状
B
物体定位前先将物体定置 到预定位置,又称预定
物品放在 手的前端 的形状
将物体放置于所需的正确 B 位置为目的而进行的动作,
又称对准
1 保 Hold 5 持 (H)
1 休 (Rest) 6 息 (R)
1 7
迟 Unavoidab 延 le Delay
标准工时--MOD时间分析表(生产线平衡实例)

NO
工作内容
1 信号线投入分线 2 焊线四 3 焊线三 4 焊线二 5 焊线一 6 剪脚/点热熔胶 7 后壳与PCB组装 8 装按键/点黄胶 9 装按键/盖上盖 10 锁螺丝 11 贴脚垫 12 外观检查 13 摆栈板 14 15 16 17 18 19 20 21 22 23 24 25
生产线平衡状况表
Hale Waihona Puke 评比 宽放人数1 1 1 1 1 1 1 1 1 1 1 1 1
作业时间 第一次 第二次 第三次
DATE:
平均值 标准工时 平衡工时
12.0 17.2 17.2 17.2 13.3 11.9 10.4 9.7 8.9 12.2 9.7 14.8 5.1
12.0 17.2 17.2 17.2 13.3 11.9 10.4 9.7 8.9 12.2 9.7 14.8 5.1
总人数: 13
总值:
159.60
20.0
15.0
10.0
5.0
0.0
1
2
3
4
5
6
7
8
9
10 11 12 13 14
系列1
备 注 1.以上线平衡为: :
2.标准产能:
71.37%
209
PCE
3.管理人数:
人
管理工时:
0.00
秒
4.总工时:
#VALUE!
秒
制定:
确认:
生产线改善报告
机种:EAGLE-POD
如上表数据所示进行生产线改善方案
序 号
作业项目
问题点
最大时间值
DATE:200 6.11.15
改善方案 实施动作