mb851_revc_schematic
MB85502-015资料
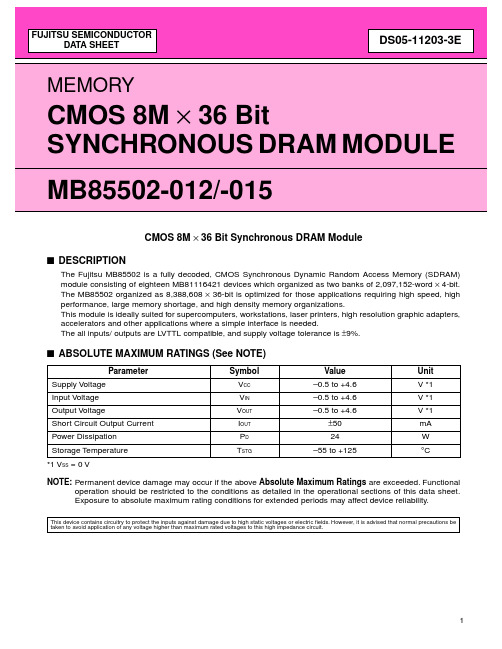
436 mW max. (ADD=L)
• LVTTL compatible I/O • Programmable burst type • Programmable burst length • Auto and Self-refresh • CKE power down mode • Output Enable and Input Data Mask
CLK A0 to A11 RAS
DQM
CKE
4M × 4
CS
chip 1
CAS WE
DQ DQ DQ DQ
CLK A0 to A11 RAS
DQM
CKE
4M × 4
CS
chip 2
CAS WE
DQ DQ DQ DQ
CLK A0 to A11 RAS
DQM
CKE
4M × 4
CS
chip 3
CAS WE
s ABSOLUTE MAXIMUM RATINGS (See NOTE)
Parameter Supply Voltage Input Voltage Output Voltage Short Circuit Output Current Power Dissipation Storage Temperature *1 VSS = 0 V
Ambient Oprating
Temp. 0°C to +70 °C
s CAPACITANCE
Parameter Input Capacitance, A0 to A11 Input Capacitance, RAS, CAS, WE Input Capacitance, CLK Input Capacitance, DQM0, DQM1 Input Capacitance, CKE0, CKE1 Input Capacitance, CS0, CS1 I/O Capacitance, (DQ0 to DQ35)
MAX8510 MAX8511 MAX8512 极低噪声、低掉电的线性调压器说明说明书

General DescriptionThe MAX8510/MAX8511/MAX8512 ultra-low-noise, low-dropout (LDO) linear regulators are designed to deliver up to 120mA continuous output current. These regulators achieve a low 120mV dropout for 120mA load current. The MAX8510 uses an advanced architecture to achieve ultra-low output voltage noise of 11μV RMS and PSRR of 54dB at 100kHz.The MAX8511 does not require a bypass capacitor, hence achieving the smallest PC board area. The MAX8512’s output voltage can be adjusted with an external divider.The MAX8510/MAX8511 are preset to a variety of voltag-es in the 1.5V to 4.5V range. Designed with a P-channel MOSFET series pass transistor, the MAX8510/MAX8511/MAX8512 maintain very low ground current (40μA).The regulators are designed and optimized to work with low-value, low-cost ceramic capacitors. The MAX8510 requires only 1μF (typ) of output capacitance for stability with any load. When disabled, current consumption drops to below 1μA.Package options include a 5-pin SC70 and a tiny 2mm x 2mm x 0.8mm TDFN package.Applications●Cellular and Cordless Phones ●PDA and Palmtop Computers ●Base Stations●Bluetooth Portable Radios and Accessories ●Wireless LANs ●Digital Cameras ●Personal Stereos●Portable and Battery-Powered EquipmentFeatures●Space-Saving SC70 and TDFN (2mm x 2mm) Packages ●11μV RMS Output Noise at 100Hz to 100kHzBandwidth (MAX8510)●78dB PSRR at 1kHz (MAX8510) ●120mV Dropout at 120mA Load●Stable with 1μF Ceramic Capacitor for Any Load ●Guaranteed 120mA Output●Only Need Input and Output Capacitors (MAX8511) ●Output Voltages: 1.5V, 1.8V, 2.5V, 2.6V, 2.7V, 2.8V,2.85V, 3V,3.3V,4.5V (MAX8510/MAX8511) and Adjustable (MAX8512) ●Low 40μA Ground Current ●Excellent Load/Line Transient●Overcurrent and Thermal Protection19-2732; Rev 5; 5/19Output Voltage Selector Guide appears at end of data sheet.Ordering Information continued at end of data sheet.*xy is the output voltage code (see Output Voltage Selector Guide). Other versions between 1.5V and 4.5V are available in 100mV increments. Contact factory for other versions.+Denotes a lead(Pb)-free/RoHS-compliant package.T = Tape and reel.PART*TEMP RANGE PIN-PACKAGEMAX8510EXKxy+T -40°C to +85°C 5 SC70MAX8510/MAX8511/MAX8512Ultra-Low-Noise, High PSRR,Low-Dropout, 120mA Linear RegulatorsOrdering InformationClick here for production status of specific part numbers.IN to GND ................................................................-0.3V to +7V Output Short-Circuit Duration ...........................................Infinite OUT, SHDN to GND .....................................-0.3V to (IN + 0.3V)FB, BP , N.C. to GND ................................-0.3V to (OUT + 0.3V)Continuous Power Dissipation (T A = +70°C)5-Pin SC70 (derate 3.1mW/°C above +70°C) .............0.247W 8-Pin TDFN (derate 11.9mW/°C above = 70°C) .........0.953W Operating Temperature Range ...........................-40°C to +85°CMilitary Operating Temperature Range .............-55°C to +110°C Junction Temperature ......................................................+150°C Storage Temperature Range ............................-65°C to +150°C Lead Temperature (soldering, 10s) .................................+300°C Soldering Temperature (reflow) .......................................+260°C Lead (Pb)-free packages .................................................+260°C Packages containing lead (Pb) .......................................+240°C(Note 1)SC70Junction-to-Ambient Thermal Resistance (θJA ) ........324°C/W Junction-to-Case Thermal Resistance (θJC ) .............115°C/WTDFNJunction-to-Ambient Thermal Resistance (θJA ) .......83.9°C/W Junction-to-Case Thermal Resistance (θJC ) ...............37°C/W(V IN = V OUT + 0.5V, T A = -40°C to +85°C, unless otherwise noted. C IN = 1μF, C OUT = 1μF, C BP = 10nF. Typical values are at +25°C; the MAX8512 is tested with 2.45V output, unless otherwise noted.) (Note 2)PARAMETER SYMBOL CONDITIONSMIN TYPMAX UNITS Input Voltage Range V IN26VOutput Voltage Accuracy I OUT = 1mA, T A = +25°C-1+1%I OUT = 100µA to 80mA, T A = +25°C -2+2I OUT = 100µA to 80mA-3+3Maximum Output Current I OUT 120mA Current LimitI LIMV OUT = 90% of nominal value 130200300mA Dropout Voltage (Note 3)V OUT ≥ 3V, I OUT = 80mA 80170mVV OUT ≥ 3V, I OUT = 120mA1202.5V ≤ V OUT < 3V, I OUT = 80mA 902002.5V ≤ V OUT < 3V, I OUT = 120mA 1352V ≤ V OUT < 2.5V, I OUT = 80mA 1202502V ≤ V OUT < 2.5V, I OUT = 120mA180Ground Current I Q I OUT = 0.05mA4090µA V IN = V OUT (nom) - 0.1V, I OUT = 0mA 220500Line Regulation V LNR V IN = (V OUT + 0.5V) to 6V, I OUT = 0.1mA 0.001%/V Load RegulationV LDR I OUT = 1mA to 80mA 0.003%/mA Shutdown Supply CurrentI SHDNV SHDN = 0VT A = +25°C 0.0031µAT A = +85°C 0.05Ripple RejectionPSRRf = 1kHz, I OUT = 10mAMAX851078dBMAX8511/MAX851272f = 10kHz, I OUT = 10mA MAX851075MAX8511/MAX851265f = 100kHz, I OUT = 10mAMAX851054MAX8511/ MAX851246MAX8512Low-Dropout, 120mA Linear RegulatorsAbsolute Maximum RatingsStresses beyond those listed under “Absolute Maximum Ratings” may cause permanent damage to the device. These are stress ratings only, and functional operation of the device at these or any other conditions beyond those indicated in the operational sections of the specifications is not implied. Exposure to absolute maximum rating conditions for extended periods may affect device reliability.Electrical CharacteristicsPackage Thermal Characteristics Note 1: Package thermal resistances were obtained using the method described in JEDEC specification JESD51-7, using a four-layerboard. For detailed information on package thermal considerations, refer to /thermal-tutorial .(V IN = V OUT + 0.5V, T A = -40°C to +85°C, unless otherwise noted. C IN = 1μF, C OUT = 1μF, C BP = 10nF. Typical values are at +25°C; the MAX8512 is tested with 2.45V output, unless otherwise noted.) (Note 2)Note 2: Limits are 100% tested at +25°C. Limits over operating temperature range are guaranteed by design.Note 3: Dropout is defined as V IN - V OUT when V OUT is 100mV below the value of V OUT for V IN = V OUT + 0.5V.Note 4: Time needed for V OUT to reach 90% of final value.(V IN = V OUT + 0.5V, C IN = 1μF, C OUT = 1μF, C BP = 10nF, T A = +25°C, unless otherwise noted.)PARAMETER SYMBOLCONDITIONSMINTYP MAXUNITSOutput Noise Voltage (RMS)f = 100Hz to 100kHz, I LOAD = 10mA MAX851011µVMAX8511/MAX8512230f = 100Hz to 100kHz, I LOAD = 80mA MAX851013MAX8511/MAX8512230Shutdown Exit Delay R LOAD = 50Ω (Note 4)300µs SHDN Logic Low Level V IN = 2V to 6V 0.4V SHDN Logic High Level V IN = 2V to 6V 1.5V SHDN Input Bias Current V IN = 6V, V SHDN = 0V or 6VT A = +25°C µA T A = +85°C 0.01FB Input Bias Current (MAX8512)V IN = 6V,V FB = 1.3VT A = +25°C 0.0060.1µA T A = +85°C0.01Thermal Shutdown 160°C Thermal-Shutdown Hysteresis10°C MAX8510OUTPUT VOLTAGE ACCURACYvs. LOAD CURRENTM A X 8510 t o c 02LOAD CURRENT (mA)% D E V I A T I O N (%)10080604020-0.4-0.200.20.40.6-0.60120MAX8510OUTPUT VOLTAGE ACCURACYvs. TEMPERATURETEMPERATURE (°C)% D E V I A T I O N (%)603510-15-0.8-0.6-0.4-0.200.20.40.60.81.0-1.0-4085MAX8510OUTPUT VOLTAGE vs. INPUT VOLTAGEINPUT VOLTAGE (V)O U T P U T V O L T A G E (V )543210.51.01.52.02.53.00.06MAX8512Low-Dropout, 120mA Linear RegulatorsElectrical Characteristics (continued)Typical Operating Characteristics(V IN = V OUT + 0.5V, C IN = 1μF, C OUT = 1μF, C BP = 10nF, T A = +25°C, unless otherwise noted.)MAX8510DROPOUT VOLTAGE vs. OUTPUT VOLTAGEOUTPUT (V)D R O P O U T V O L T A G E (m V )3.02.82.62.42.2501001502002502.03.2MAX8510GROUND PIN CURRENT vs. TEMPERATUREM A X 8510 t o c 08TEMPERATURE (°C)G R O U N D P I N C U R R E N T (µA )603510-153540455030-4085MAX8510OUTPUT NOISE400µs/divMAX8510GROUND PIN CURRENT vs. INPUT VOLTAGEINPUT VOLTAGE (V)G R O U N D P I N C U R R E N T (µA )43211502005010025030035005MAX8510PSRR vs. FREQUENCYFREQUENCY (kHz)P S R R (d B )1101000.14050601020307080900.011000MAX8510OUTPUT NOISE SPECTRAL DENSITYvs. FREQUENCYMAX8510 toc12FREQUENCY (kHz)O U T P U T N O I S E D E N S I T Y (n V /H z )0.11101001.E+031.E+021.E+041.E+010.011000MAX8510DROPOUT VOLTAGE vs. LOAD CURRENTLOAD CURRENT (mA)D R O P O U T V O L T A G E (m V )1008060402030609012015000120MAX8510GROUND PIN CURRENT vs. LOAD CURRENTLOAD CURRENT (mA)G R O U N D P I N C U R R E N T (µA )10080604020408012016020024000120MAX8511PSRR vs. FREQUENCYFREQUENCY (kHz)P S R R (d B )0.111010040506010203070809000.011000MAX8512Low-Dropout, 120mA Linear RegulatorsTypical Operating Characteristics (continued)(V IN = V OUT + 0.5V, C IN = 1μF, C OUT = 1μF, C BP = 10nF, T A= +25°C, unless otherwise noted.)MAX8510LOAD TRANSIENT RESPONSE1ms/div V OUT 10mV/divMAX8510EXITING SHUTDOWN WAVEFORM20µs/divV OUT = 2.85VR LOAD = 47ΩOUTPUT VOLTAGE 2V/divSHUTDOWN VOLTAGEMAX8510LOAD TRANSIENT RESPONSE NEAR DROPOUT1ms/divV OUT 10mV/divMAX8510ENTERING SHUTDOWN DELAY40µs/divC BP = 0.01µFOUTPUT VOLTAGE 2V/divSHUTDOWN VOLTAGEMAX8510REGION OF STABLE C OUT ESRvs. LOAD CURRENTM A X 8510 t o c 20LOAD CURRENT (mA)C O U T E S R (Ω)806040200.11101000.01120100STABLE REGIONMAX8510OUTPUT NOISE vs. BP CAPACITANCEM A X 8510 t o c 13BP CAPACITANCE (nF)O U T P U T N O I S E (µV )1051015202501100MAX8510LINE TRANSIENT RESPONSE200µs/divV IN = 3.5V TO 4VV OUT 2mV/divMAX8510SHUTDOWN EXIT DELAY20µs/divV OUT 1V/divSHUTDOWN VOLTAGEV OUT = 3V C BP = 100nFMAX8512Low-Dropout, 120mA Linear RegulatorsTypical Operating Characteristics (continued)Detailed DescriptionThe MAX8510/MAX8511/MAX8512 are ultra-low-noise, low-dropout, low-quiescent current linear regulators designed for space-restricted applications. The parts are available with preset output voltages ranging from 1.5V to 4.5V in 100mV increments. These devices can supply loads up to 120mA. As shown in the Functional Diagram , the MAX8510/MAX8511 consist of an innovative bandgap core and noise bypass circuit, error amplifier, P-channel pass transistor, and internal feedback voltage-divider. The MAX8512 allows for adjustable output with an external feedback network.The 1.225V bandgap reference is connected to the error amplifier’s inverting input. The error amplifier compares this reference with the feedback voltage and amplifies the difference. If the feedback voltage is lower than the refer-ence voltage, the pass-transistor gate is pulled low. This allows more current to pass to the output and increases the output voltage. If the feedback voltage is too high, the pass transistor gate is pulled high, allowing less cur-rent to pass to the output. The output voltage is fed back through an internal resistor voltage-divider connected to the OUT pin.An external bypass capacitor connected to BP (MAX8510) reduces noise at the output. Additional blocks include a current limiter, thermal sensor, and shutdown logic.Internal P-Channel Pass TransistorThe MAX8510/MAX8511/MAX8512 feature a 1Ω (typ) P-channel MOSFET pass transistor. This provides sev-eral advantages over similar designs using a PNP pass transistor, including longer battery life. The P-channel MOSFET requires no base drive, which considerably reduces quiescent current. PNP-based regulators waste considerable current in dropout when the pass transistor saturates. They also use high base-drive current under heavy loads. The MAX8510/MAX8511/MAX8512 do not suffer from these problems and consume only 40μA of quiescent current in light load and 220μA in dropout (see the Typical Operating Characteristics ).Output Voltage SelectionThe MAX8510/MAX8511 are supplied with factory-set output voltages from 1.5V to 4.5V, in 100mV increments (see Ordering Information ). The MAX8512 features a user-adjustable output through an external feedback net-work (see the Typical Operating Circuits ).To set the output of the MAX8512, use the following equa-tion:OUT REF V R1R2X -1V=where R2 is chosen to be less than 240kΩ and V REF = 1.225V. Use 1% or better resistors.PINNAMEFUNCTIONMAX8510MAX8511MAX8512SC70TDFN -EP SC70TDFN -EP SC70TDFN -EP 151515IN Unregulated Input Supply 232323GNDGround343434SHDN Shutdown. Pull low to disable the regulator.42————BP Noise Bypass for Low-Noise Operation. Connect a 10nF capacitor from BP to OUT. BP is shorted to OUT in shutdown mode.————42FB Adjustable Output Feedback Point575757OUT Regulated Output Voltage. Bypass with a capacitor to GND. See the Capacitor Selection and Regulator Stability section for more details.—1, 6, 841, 2, 6,—1, 6, 8N.C.No connection. Not internally connected.——————EPExposed Pad (TDFN Only). Internally connected to GND. Connect to a large ground plane to maximize thermal performance. Not intended as an electrical connection point.MAX8512Low-Dropout, 120mA Linear RegulatorsPin DescriptionShutdownThe MAX8510/MAX8511/MAX8512 feature a low-power shutdown mode that reduces quiescent current less than 1μA. Driving SHDN low disables the voltage reference, error amplifier, gate-drive circuitry, and pass transistor (see the Functional Diagram), and the device output enters a high-impedance state. Connect SHDN to IN for normal operation.Current LimitThe MAX8510/MAX8511/MAX8512 include a current lim-iter, which monitors and controls the pass transistor’s gate voltage, limiting the output current to 200mA. For design purposes, consider the current limit to be 130mA (min) to 300mA (max). The output can be shorted to ground for an indefinite amount of time without damaging the part. Thermal-Overload ProtectionThermal-overload protection limits total power dissipation in the MAX8510/MAX8511/MAX8512. When the junction temperature exceeds T J = +160°C, the thermal sensor signals the shutdown logic, turning off the pass transis-tor and allowing the IC to cool down. The thermal sensor turns the pass transistor on again after the IC’s junction temperature drops by 10°C, resulting in a pulsed output during continuous thermal-overload conditions.Thermal-overload protection is designed to protect the MAX8510/MAX8511/MAX8512 in the event of a fault con-dition. For continual operation, do not exceed the abso-lute maximum junction temperature rating of T J = +150°C. Operating Region and Power DissipationThe MAX8510/MAX8511/MAX8512 maximum power dis-sipation depends on the thermal resistance of the case and circuit board, the temperature difference between the die junction and ambient, and the rate of airflow. The power dissipation across the device is:P = I OUT (V IN - V OUT)The maximum power dissipation is:P MAX = (T J - T A) / (θJC + θCA)where T J - T A is the temperature difference between the MAX8510/MAX8511/MAX8512 die junction and the sur-rounding air, θJC is the thermal resistance of the package, and θCA is the thermal resistance through the PC board, copper traces, and other materials to the surrounding air. The GND pin of the MAX8510/MAX8511/MAX8512 per-forms the dual function of providing an electrical connec-tion to ground and channeling heat away. Connect the GND pin to ground using a large pad or ground plane.Noise ReductionFor the MAX8510, an external 0.01μF bypass capaci-tor between BP and OUT with innovative noise bypass scheme reduces output noises dramatically, exhibiting 11μV RMS of output voltage noise with C BP = 0.01μF and C OUT = 1μF. Startup time is minimized by a poweron cir-cuit that precharges the bypass capacitor. Applications InformationCapacitor Selectionand Regulator StabilityUse a 1μF capacitor on the MAX8510/MAX8511/MAX8512 input and a 1μF capacitor on the output. Larger input capacitor values and lower ESRs provide better noise rejection and line-transient response. Reduce output noise and improve load-transient response, stability, and power-supply rejection by using large output capacitors. Note that some ceramic dielectrics exhibit large capaci-tance and ESR variation with temperature. With dielec-trics such as Z5U and Y5V, it may be necessary to use a 2.2μF or larger output capacitor to ensure stability at temperatures below -10°C. With X7R or X5R dielectrics, 1μF is sufficient at all operating temperatures. A graph of the region of stable C OUT ESR vs. load current is shown in the Typical Operating Characteristics.Use a 0.01μF bypass capacitor at BP (MAX8510) for low-output voltage noise. The leakage current going into the BP pin should be less than 10nA. Increasing the capaci-tance slightly decreases the output noise. Values above 0.1μF and below 0.001μF are not recommended. Noise, PSRR, and Transient ResponseThe MAX8510/MAX8511/MAX8512 are designed to deliv-er ultra-low noise and high PSRR, as well as low dropout and low quiescent currents in battery-powered systems. The MAX8510 power-supply rejection is 78dB at 1kHz and 54dB at 100kHz. The MAX8511/MAX8512 PSRR is 72dB at 1kHz and 46dB at 100kHz (see the Power-Supply Rejection Ratio vs. Frequency graph in the Typical Operating Characteristics).When operating from sources other than batteries, improved supply-noise rejection and transient response can be achieved by increasing the values of the input and output bypass capacitors, and through passive filter-ing techniques. The Typical Operating Characteristics show the MAX8510/MAX8511/MAX8512 line- and load-transient responses.MAX8512Low-Dropout, 120mA Linear RegulatorsDropout VoltageA regulator’s minimum dropout voltage determines the lowest usable supply voltage. In battery-powered sys-tems, this determines the useful end-of-life battery volt-age. Because the MAX8510/MAX8511/MAX8512 use aP-channel MOSFET pass transistor, their dropout voltage is a function of drain-to-source on-resistance (RDS(ON)) multiplied by the load current (see the Typical Operating Characteristics ).MAX8512Low-Dropout, 120mA Linear RegulatorsFunctional Diagram*xy is the output voltage code (see Output Voltage Selector Guide). Other versions between 1.5V and 4.5V are available in 100mV increments. Contact factory for other versions.**EP = Exposed pad.+Denotes a lead(Pb)-free/RoHS-compliant package.T = Tape and reel.(Note: Standard output voltage options, shown in bold , are available. Contact the factory for other output voltages between 1.5V and 4.5V. Minimum order quantity is 15,000 units.)PART*TEMP RANGE PIN-PACKAGE MAX8510MXK33/PR3+-55°C to +110°C 5 SC70MAX8510ETAxy+T -40°C to +85°C 8 TDFN-EP** 2mm x 2mm MAX8511EXKxy+T -40°C to +85°C 5 SC70MAX8511ETAxy+T -40°C to +85°C 8 TDFN-EP** 2mm x 2mm MAX8512EXK+T -40°C to +85°C 5 SC70MAX8512ETA+T-40°C to +85°C8 TDFN-EP** 2mm x 2mmPARTV OUT (V)TOP MARKMAX8510EXK16+T 1.6AEX MAX8510EXK18+T 1.8AEA MAX8510ETA25+T 2.5AAO MAX8510EXK27+T 2.7ATD MAX8510ETA28+T 2.8AAR MAX8510EXK29+T 2.85ADS MAX8510MXK33/PR3+ 3.3AUV MAX8510ETA30+T 3AAS MAX8510ETA33+T 3.3AAT MAX8510ETA45+T 4.5AAU MAX8510MXK33/PR3+ 3.3AUV MAX8511EXK15+T 1.5ADU MAX8511ETA18+T 1.8AAV MAX8511ETA25+T 2.5AAP MAX8511ETA26+T 2.6AAW MAX8511EXK28+T 2.8AFA MAX8511ETA29+T 2.85AAX MAX8511EXK89+T 2.9AEH MAX8511EXK31+T 3.1ARS MAX8511ETA33+T 3.3AAY MAX8511EXK45+T4.5AEJ MAX8512ETA+TAdjustableAAQPACKAGE TYPE PACKAGE CODE OUTLINE ND PATTERN NO.8 TDFN T822+121-016890-00645 SC70X5+121-007690-0188MAX8512Low-Dropout, 120mA Linear RegulatorsTypical Operating Circuits (continued)Ordering Information (continued)Output Voltage Selector GuidePackage InformationFor the latest package outline information and land patterns (footprints), go to /packages . Note that a “+”, “#”, or “-” in the package code indicates RoHS status only. Package drawings may show a different suffix character, but the drawing pertains to the package regardless of RoHS status.Chip InformationPROCESS: BiCMOSREVISION NUMBERREVISION DATE DESCRIPTIONPAGES CHANGED 48/11Corrected errors and added lead-free packages 1, 2, 3, 6, 955/19Updated Output Voltage Selector Guide9Maxim Integrated cannot assume responsibility for use of any circuitry other than circuitry entirely embodied in a Maxim Integrated product. No circuit patent licenses are implied. Maxim Integrated reserves the right to change the circuitry and specifications without notice at any time. The parametric values (min and max limits) shown in the Electrical Characteristics table are guaranteed. Other parametric values quoted in this data sheet are provided for guidance.MAX8512Low-Dropout, 120mA Linear RegulatorsRevision HistoryFor pricing, delivery, and ordering information, please visit Maxim Integrated’s online storefront at https:///en/storefront/storefront.html.。
RPM851中文资料

RPM851A Series
FApplication example
655
元器件交易网 Communication ICs
FRecommended values (at VCC = 3V)
RPM851A Series
656
元器件交易网 Communication ICs
FOptical characteristics (unless otherwise noted, LEDVCC = VCC = PDVCC = 3V, Ta = 25_C)
Байду номын сангаас654
元器件交易网 Communication ICs
FCircuit operation Timing charts
RPM851A Series
S Better to be placed more than 1.0cm in radius from photo diode (pin13) and also away from the parts which generates noise, such as DC / DC converter. Digital signal line, such as clock pulse, bus etc, are also away more than 1.0cm in radius from photo diode. S As for C1, C2 and, GND should be close to pin7 and placed close to pins11, 12 and 13 (within 5mm). (3) Please be sure to set up the TXD (pin6) input to be “L” (under 0.5 [V]) except transmitting data (for < 90 µ s. ON Duty < 20%). (4) Powerdown current might increase if exposed by strong light (ex. direct sunlight) at powerdown mode. (5) Please use by the signal form which is specified by IrDA Ver1.0. There might be on error if used by different signal form.
低电压检测器BL8518产品说明书
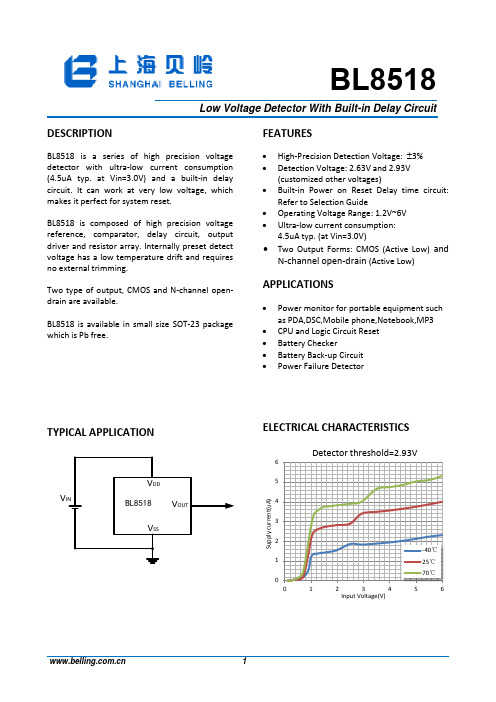
Low Voltage Detector With Built-in Delay CircuitBL8518DESCRIPTIONBL8518 is a series of high precision voltage detector with ultra-low current consumption (4.5uA typ. at Vin=3.0V) and a built-in delay circuit. It can work at very low voltage, which makes it perfect for system reset.BL8518 is composed of high precision voltage reference, comparator, delay circuit, output driver and resistor array. Internally preset detect voltage has a low temperature drift and requires no external trimming.Two type of output, CMOS and N-channel open-drain are available.BL8518 is available in small size SOT-23 package which is Pb free.FEATURES∙ High-Precision Detection Voltage: ±3% ∙ Detection Voltage: 2.63V and 2.93V(customized other voltages)∙ Built-in Power on Reset Delay time circuit:Refer to Selection Guide∙ Operating Voltage Range: 1.2V~6V ∙ Ultra-low current consumption:4.5uA typ. (at Vin=3.0V)∙ Two Output Forms: CMOS (Active Low) and N-channel open-drain (Active Low)APPLICATIONS∙ Power monitor for portable equipment suchas PDA,DSC,Mobile phone,Notebook,MP3 ∙ CPU and Logic Circuit Reset ∙ Battery Checker∙ Battery Back-up Circuit ∙ Power Failure DetectorTYPICAL APPLICATIONVELECTRICAL CHARACTERISTICS0 123 4 56123 456S u p p l y c u r r e n t (u A )Input Voltage(V)Detector threshold=2.93V-40℃25℃ 70℃ORDERING INFORMATION123456ABSOLUTE MAXIMUM RATINGNote:Exceed these limits to damage to the device.Exposure to absolute maximum rating conditions may affect device reliability. RECOMMENDED WORK CONDITIONSELECTRICAL CHARACTERISTICSBL8518CXXTR263DC/N(2.63V)BL8518CXXTR293DC/N(2.93V)ELECTRICAL CHARACTERISTICS BY OUTPUT DELAY TIMEBLOCK DIAGRAMVoutV DDN Channel Open DrainVssVoutV DDCMOS OutputFUNCTION DESCRIPTIONVssVoutDDHigh precision low temperature co-efficiency reference voltage is applied to the negative input of a comparator. Input voltage, divided by resistor array of Ra and Rb, is applied to the positive input of the comparator. Output of the comparator passes a delay circuit and a series of buffer to drive the output CMOS pair.VDET =VREF*(1+Ra/Rb)VssVssTEST CIRCUITS(1) Supply current test circuit(2) Detector threshold test circuitV SSVOUTLC9018V DDV INV OUT(3) NCH Drive Output Current Test Circuit(4) PCH Drive Output Current Test CircuitV V DSV - V DSDDBL8518BL8518TYPICAL PERFORMANCE CHARACTERISTICS1) Supply current VS. Input voltage3) Nch Driver Output Current VS. VDS5) PCH Driver Output Current vs. Input Current4) NCH Driver Output Current vs. Input Voltage0 1 23 4 5 6 0123 456S u p p l y c u r r e n t (u A )Input Voltage(V)Detector threshold=2.93V-40℃25℃ 70℃0 2 4 6 8 10 12 14 16 18 20 0.00.51.01.52.02.53.0O u t p u t C u r r e n t (m A )VDS(V)Detector threshold=2.93VVDD=2V VDD=1V 0 5101520 25123 4O u t p u t C u r r e n t (m A )Input Voltage Vin(V)Detector threshold=2.93V-40℃ 25℃ 70℃0 5 10 15 20 25 30 35 40 0123 4 5 67O u t p u t C u r r e n t (m A )Input Voltage Vin(V)Detector threshold=2.93VVds=0.5V Vds=1.0V Vds=1.5V Vds=2.0VPACKAGE LINE。
BM85调试

可编程BM85调试报告一、SA85卡的安装计算机通过SA85卡(需ISA插槽)接入MBPLUS网。
推荐使用如下设定:memory address = CE800 (内存地址)hardware interrupt NONE (硬件中断)设定如下图:图 1|-----------------------------------------------------------|| LED || || NA8 || . || . || . || NA1 || || .. IR7 SM8 d || .. IR6 7 u || .. IR5 6 d || .. IR4 5 u || .. IR3 4 u |-+ | .. IR2 3 u |+-+ | -- 2 d | | | 1 d | | | |+-+ +--------- -------------|-+ | || | | | | | | | | | | | | | | | | | | |IR 2-7: 最低短接,即选择无中断。
SM 1-8: 内存地址选择 CE800. 'd' = down ; 'u' = up NA 1-8: 地址开关。
朝左为1,朝右为零。
1 2 3 4 5 6 7 8Address 1 0 0 0 0 0 0 - -2 1 0 0 0 0 0 - -3 0 1 0 0 0 0 - -4 1 1 0 0 0 0 - -. . . . . . . . . .63 0 1 1 1 1 1 - -64 1 1 1 1 1 1 - -SA85卡的驱动程序有16位和32位两种。
此次调试在NT Workstation4.0上进行。
由于下载软件bm85load.exe需要16位驱动程序(在DOS下格式为:bm85load /s5c /re000 /p4.4 bm85.exe) 。
所以需安装SA85卡的16位驱动程序。
851-300 Rev. B 设备说明书

851-300 Rev. BSet-up, Operation& Maintenance ManualTable of ContentsWarnings – General Safety 2. . . . . . . . . . . . . . . . . . . . Introduction 2. . . . . . . . . . . . . . . . . . . . . . . . . . . . . . . . Product Description 3. . . . . . . . . . . . . . . . . . . . . . . . . . Specifications 3. . . . . . . . . . . . . . . . . . . . . . . . . . . . . . . Installation 4. . . . . . . . . . . . . . . . . . . . . . . . . . . . . . . . . Required Tools 4. . . . . . . . . . . . . . . . . . . . . . . . . . . . Mounting 4. . . . . . . . . . . . . . . . . . . . . . . . . . . . . . . . Preventative Maintenance & Adjustment 6. . . . . . . . . Required Tools 6. . . . . . . . . . . . . . . . . . . . . . . . . . . . Timing Belt Tensioning 6. . . . . . . . . . . . . . . . . . . . . Timing Belt Replacement 6. . . . . . . . . . . . . . . . . . . Drive or Driven Pulley Replacement 7. . . . . . . . . . . Gearmotor Replacement 7. . . . . . . . . . . . . . . . . . . . Service Parts 9. . . . . . . . . . . . . . . . . . . . . . . . . . . . . . . Return Policy 10. . . . . . . . . . . . . . . . . . . . . . . . . . . . . .2100, 4100, 6100 Series Bottom Mount Drive Package for Light Load 50 Hz Gearmotors SOMM851-300 Rev. B 2Dorner Mfg. Corp.IntroductionIMPORTANT: Some illustrations may showguards removed. Do NOT operate equipment with-out guards.Upon receipt of shipment:D Compare shipment with packing slip. Contact factory regarding discrepancies.D Inspect packages for shipping damage. Contact carrier regarding damage.D Accessories may be shipped loose. See accessory in-structions for installation.Dorner 2100 Series conveyors are covered by the following patent numbers: 5131529, 5174435, and corresponding patents and patent applications in other countries.Dorner 4100 Series conveyors are covered by patent number 3923148 and corresponding patents and patent applications in other countries.Dorner 6100 Series conveyors are covered by patent number 5174435 and corresponding patents and patent applications in other countries.Dorner ’s Limited Warranty applies.Dorner reserves the right to make changes at any time without notice or obligation.Warnings – General Safety2100, 4100, 6100 Series Bottom Mount Drive Package for Light Load 50 Hz Gearmotors SOMMDorner Mfg. Corp.3851-300 Rev. BRefer to Figure 1 for typical components.A ConveyorB Mounting BracketC GearmotorD Belt TensionerE CoverF Timing BeltG Drive Pulley HDriven PulleyTypical ComponentsFigure 1ABCDEFG H SpecificationsGearmotor Mounting Package Models:Example:4 = 4100 Series Conveyor 6 = 6100 Series Conveyor– = flat belt, A through J = cleated belt )Driven Pulley (see Table 2)* See “Ordering and Specifications ” Catalog for details.Table 1: Gearmotor SpecificationsProduct Description2100, 4100, 6100 Series Bottom Mount Drive Package for Light Load 50 Hz Gearmotors SOMM851-300 Rev. B 4Dorner Mfg. Corp.Table 2: Belt Speeds for Light Load Fixed Speed Parallel Shaft 50 Hz Gearmotors(vp) = voltage and phase 21 = 230 V, 1-phase 23 = 230 V, 3-phase 43 = 400 V, 3-phaseNOTE: 203 through 610 mm wide conveyors withlight load drives should be limited to 2438 mm length.NOTE: For belt speed other than those listed, con-tact factory for details.InstallationRequired ToolsD Hex key wrenches:2.5 mm, 3 mm & 5 mm D Straight edge D Torque wrenchInstallation Component ListI Bottom Mount Assembly J Driven Pulley K CoverL M4 Socket Head Screws (4x)M Timing Belt N KeyOM6 Socket Head Screws (2x)Mounting1.Typical components (Figure 2)Figure 2NKMJLOISpecifications2100, 4100, 6100 Series Bottom Mount Drive Package for Light Load 50 Hz Gearmotors SOMMDorner Mfg. Corp.5851-300 Rev. BNOTE: 6100 conveyor shown, 2100 & 4100 similar.2.Locate drive output shaft (P of Figure 3) and removetwo (2) screws (Q).Figure 3QP3.Attach mount assembly (I of Figure 4) with screws(O). Tighten screws to 9 Nm.Figure 4OI4.Install key (N of Figure 5).Figure 5NRM5.Wrap timing belt (M) around driven pulley (J) anddrive pulley (R). Install driven pulley (J) onto conveyor shaft.ing a straight edge (S of Figure 6), align drivenpulley (J) with drive pulley (R). Tighten driven pulley set screws (T).Figure 6SJTR7.Depending on conveyor belt travel (direction 1 or 2),locate timing belt tensioner (U of Figure 7) as shown.Tension timing belt to obtain 3 mm deflection for 456grams of force at timing belt mid-point (V). Tightentensioner screw to 12 Nm.21VUFigure 78.Install cover (K of Figure 8) with four (4) screws (L).Tighten to 4 Nm.Figure 8KLLInstallation2100, 4100, 6100 Series Bottom Mount Drive Package for Light Load 50 Hz Gearmotors SOMM851-300 Rev. B 6Dorner Mfg. Corp.Required ToolsD Hex key wrenches:2.5 mm, 3 mm, 5 mm D Straight edgeD Screwdriver (for terminal box screws)D Torque wrenchTiming Belt Tensioning1.Remove four (4) screws (L of Figure 9) and removecover (K).Figure 9KLL2.Loosen tensioner (U of Figure 10).Figure 10U3.Depending on conveyor belt travel (direction 1 or 2),locate timing belt tensioner (U of Figure 11) as shown.Tension timing belt to obtain 3 mm deflection for 456grams of force at timing belt mid-point (V). Tighten tensioner screw to 12 Nm.21VUFigure 114.Install cover (K of Figure 9) with four (4) screws (L).Tighten screws to 4 Nm.Timing Belt Replacement1.Remove four (4) screws (L of Figure 9) and removecover (K).2.Loosen tensioner (U of Figure 10).3.Remove timing belt (M of Figure 12).NOTE: If timing belt does not slide over pulleyflange, loosen driven pulley set screws (T of Figure 12) and remove pulley with belt. For re-installation,see steps 5 through 8 on page 5.Figure 12TM4.Install new timing belt.Preventive Maintenance and Adjustment2100, 4100, 6100 Series Bottom Mount Drive Package for Light Load 50 Hz Gearmotors SOMMDorner Mfg. Corp.7851-300 Rev. B5.Depending on conveyor belt travel (direction 1 or 2),locate timing belt tensioner (U of Figure 11) as shown. Tension timing belt to obtain 3 mm deflection for 456 grams of force at timing belt mid-point (V). Tighten tensioner screw to 12 Nm.6.Install cover (K of Figure 9) with four (4) screws (L).Tighten screws to 4 Nm.Drive or Driven Pulley Replacementplete steps 1 through 3 of “Timing BeltReplacement ” section on page 6.2.Loosen set screws and remove drive or driven pulley.NOTE: If drive pulley (R of Figure 13) is replaced,wrap timing belt (M) around drive pulley and complete step 3.Figure 13Mplete steps 5 through 8 of “Installation ” sectionon page 5.Gearmotor ReplacementNOTE: Single phase gearmotor shown, three phasesimilar.1.For single phase motor:a .Loosen terminal box screws (W of Figure 14) andremove cover (X).Figure 14WXPreventive Maintenance and Adjustment2100, 4100, 6100 Series Bottom Mount Drive Package for Light Load 50 Hz Gearmotors SOMM851-300 Rev. B 8Dorner Mfg. Corp.b .(Figure 15). Loosen terminals U1, W1and ground and remove wires.Figure 15c .Loosen cord grip (Y of Figure 15) and removecord.1.For three phase motor:a .Loosen terminal box screws (W of Figure 14) andremove cover (X).b .(Figure 16). Loosen terminals U1, V1,W1 and ground and remove wires.Figure 16c .Loosen cord grip (Y of Figure 16) and removecord.2.Remove four (4) screws (L of Figure 9) and remove cover (K).3.Loosen tensioner (U of Figure 10).4.Remove timing belt (M of Figure 12).NOTE: If timing belt does not slide over pulleyflange, loosen driven pulley set screws (T of Figure 17) and remove pulley with belt (M). For re-installation, see steps 5 through 8 on page 5.Figure 17TM5.Loosen two (2) set screws (T of Figure 18). Removedrive pulley (R).Figure 18ADADRT6.Remove four (4) screws (AD) and detach gearmotor.7.Mount new gearmotor with four (4) screws (AD).Tighten to 5 Nm.8.Replace drive pulley (R of Figure 18) and tighten setscrews (T).plete steps 5 through 8 of “Installation ” sectionon page 5.10.Replace wiring:D For a single phase motor, reverse step 1 on page 7.D For a three phase motor, reverse step 1 on this page.Preventive Maintenance and Adjustment2100, 4100, 6100 Series Bottom Mount Drive Package for Light Load 50 Hz Gearmotors SOMMDorner Mfg. Corp.9851-300 Rev. BNOTE: For replacement parts other than thoseshown on this page, contact an authorized Dorner Service Center or the factory.Figure 195,63,421Service PartsNo returns will be accepted without prior written factory authorization. When calling for authorization, please have the following information ready for the Dorner Factory representative or your local distributor: and address of customer.2.Item(s) being returned.3.Reason for return.4.Customer’s original order number used when ordering the item(s).5.Dorner or distributor invoice number.A representative will discuss action to be taken on the Returned items and provide a Returned Goods Authorization Number to reference.There will be a 15% restocking charge on all new items returned for credit where Dorner was not at fault. These will not be accepted after 60 days from original invoice date. The restocking charge covers inspection, cleaning,disassembly, and reissuing to inventory.If a replacement is needed prior to evaluation of returned item, a purchase order must be issued. Credit (if any) is issued only after return and evaluation is complete.Dorner has representatives throughout the world. Feel free to contact Dorner for the name of your local representative. Our technical sales and service staff will gladly help with your questions on Dorner products.For a copy of Dorner’s Limited Warranty, contact factory, distributor, service center or visit our website at 851-300 Rev. BPrinted in U.S.A.400Return Policy。
PC851-高电压光耦
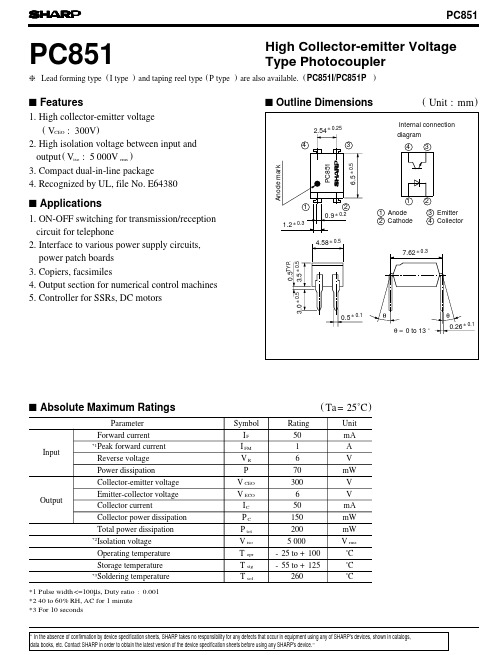
PC851
PC851
s Features
1. High collector-emitter voltage ( VCEO : 300V) 2. High isolation voltage between input and output ( Viso : 5 000V rms ) 3. Compact dual-in-line package 4. Recognized by UL, file No. E64380
( Unit : mm )
Internal connection
Anode mark
s Applications
1. ON-OFF switching for transmission/reception circuit for telephone 2. Interface to various power supply circuits, power patch boards 3. Copiers, facsimiles 4. Output section for numerical control machines 5. Controller for SSRs, DC motors
MB85RC16V(5V%2016KBit)

FUJITSU SEMICONDUCTORDATA SHEETCopyright©2011 FUJITSU SEMICONDUCTOR LIMITED All rights reserved 2011.8Memory FRAM16 K (2 K × 8) Bit I 2CMB85RC16V■DESCRIPTIONThe MB85RC16V is an FRAM (F erroelectric Random Access Memory) chip in a configuration of 2,048 words × 8 bits, using the ferroelectric process and silicon gate CMOS process technologies for forming the nonvolatile memory cells.Unlike SRAM, the MB85RC16V is able to retain data without using a data backup battery.The memory cells used in the MB85RC16V have at least 1010 Read/Write operation endurance per bit, which is a significant improvement over the number of read and write operations supported by other nonvolatile memory products.The MB85RC16V can provide writing in one byte units because the long writing time is not required unlike Flash memory and E 2PROM. Therefore, the writing completion waiting sequence like a write busy state is not required.■FEATURES•Bit configuration : 2,048 words × 8 bits •Operating power supply voltage : 3.0 V to 5.5 V •Operating frequency : 400 kHz (Max) •T wo-wire serial interface : Fully controllable by two ports: serial clock (SCL) and serial data (SDA).•Operating temperature range : − 40 °C to + 85 °C •Data retention : 10 years ( + 75 °C) •Read/Write endurance : 1010 times •Package : Plastic / SOP , 8-pin (FPT -8P-M02)•Low power consumption : Operating current 80 μA (Max: @400 kHz), Standby current 5 μA (Typ)DS501-00010-0v01-EMB85RC16V■PIN FUNCTIONAL DESCRIPTIONSPinNumberPin Name Functional Description1 to 3NC No Connect pins Leave it unconnected.4VSS Ground pin5SDA Serial Data I/O pinThis is an I/O pin of serial data for performing bidirectional communication of mem-ory address and writing or reading data. It is possible to connect some devices. It is an open drain output, so a pull-up resistance is required to be connected to the external circuit.6SCL Serial Clock pinThis is a clock input pin for input/output timing serial data. Data is sampled on the rising edge of the clock and output on the falling edge.7WP Write Protect pinWhen Write Protect pin is “H” level, writing operation is disabled. When Write Pro-tect pin is “L” level, the entire memory region can be overwritten. Reading operation is always enabled regardless of the Write Protect pin state. The write protect pin is internally pulled down to the VSS pin and that is recognized as the “L” level (write enabled) when the pin is the open state.8VDD Supply Voltage pinMB85RC16V■I2C (Inter-Integrated Circuit)The MB85RC16V has the two-wire serial interface and the I2C bus, and operates as a slave device.The I2C bus defines communication roles of “master” and “slave” devices, with the master side holding the authority to initiate control. Furthermore, a I2C bus connection is possible where a single master device is connected to multiple slave devices in a party-line configuration.2MB85RC16V■I2C COMMUNICATION PROTOCOLThe I2C bus provides communication by two wires only, therefore, the SDA input should change while SCL is the “L” level. However, when starting and stopping the communication sequence, SDA is allowed to change while SCL is the “H” level.•Start ConditionTo start read or write operations by the I2C bus, change the SDA input from the “H” level to the “L” level while the SCL input is in the “H” level.•Stop ConditionTo stop the I2C bus communication, change the SDA input from the “L” level to the “H” level while the SCL input is in the “H” level. In the reading operation, inputting the stop condition finishes reading and enters the standby state. In the writing operation, inputting the stop condition finishes inputting the rewrite data and enters the standby state.Note : The FRAM device does not need the programming wait time (t WC) after issuing the Stop Condition during the write operation.MB85RC16V ■ACKNOWLEDGE (ACK)In the I2C bus, serial data including memory address or memory information is sent in units of 8 bits. The acknowledge signal indicates that every 8 bits of the data is successfully sent and received. The receiver side usually outputs the “L” level every time on the 9th SCL clock after every 8 bits are successfully trans-mitted. On the transmitter side, the bus is temporarily released on this 9th clock to allow the acknowledge signal to be received and checked. During this released period, the receiver side pulls the SDA line down to indicate that the communication works correctly.If the receiver side receives the stop condition before transmitting the acknowledge “L” level, the read operation ends and the I2C bus enters the standby state. If the acknowledge “L” level is not detected, and the Stop condition is not sent, the bus remains in the released state without doing anything.■MEMORY ADDRESS STRUCTUREThe MB85RC16V has the memory address buffer to store the 11-bit information for the memory address.As for byte write, page write and random read commands, the complete 11-bit memory address is configured by inputting the memory upper address (3 bits) and the memory lower address (8 bits), and saving to the memory address buffer and access to the memory is performed.As for a current address read command, the complete 11-bit memory address is configured by inputting the memory upper address (3 bits) and by the memory address lower 8-bit which has saved in the memory address buffer, and saving to the memory address buffer and access to the memory is performed.MB85RC16V■DEVICE ADDRESS WORDF ollowing the start condition, the 8 bit device address word is input. Inputting the device address word decideswhether the master or the slave drives the data line. However, the clock is always driven by the master. The device address word (8bits) consists of a device T ype code (4bits), memory upper address code (3bits), anda Read/Write code (1bit).•Device Type Code (4bits)The upper 4 bits of the device address word are a device type code that identifies the device type, and are fixed at “1010” for the MB85RC16V.•Memory Upper Address Code (3bits)Following the device type code, the 3 bits of the memory upper address code are input.The slave address selection is not performed by the external pin setting on this device. These 3 bits are not the setting bits for the slave address, but the upper 3-bit setting bits for the memory address.•Read/Write Code (1bit)The 8th bit of the device address word is the R/W (Read/Write) code. When the R/W code is “0” input, a write operation is enabled, and the R/W code is “1” input, a read operation is enabled for the MB85RC16V.If the device code is not “1010”, the Read/Write operation is not performed and the standby state is chosen.MB85RC16V ■DATA STRUCTUREThe master inputs the device address word (8 bits) following the start condition, and then the slave outputs the Acknowledge “L” level on the ninth bit. After confirming the Acknowledge response, the sequential 8-bit memory lower address is input, to the byte write, page write and random read commands.As for the current address read command, inputting the memory lower address is not performed, and the address buffer lower 8-bit is used as the memory lower address.When inputting the memory lower address finishes, the slave outputs the Acknowledge “L” level on the ninth bit again.Afterwards, the input and the output data continue in 8-bit units, and then the Acknowledge “L” level is output for every 8-bit data.MB85RC16V■FRAM ACKNOWLEDGE -- POLLING NOT REQUIREDThe MB85RC16V performs the high speed write operations, so any waiting time for an ACK* by the acknowl-edge polling does not occur.*: In Flash memory and E2PROM, the Acknowledge Polling is performed as a progress check whether rewriting is executed or not. It is normal to judge by the 9th bit of Acknowledge whether rewriting is performed or not after inputting the start condition and then the device address word (8 bits) during rewriting.■WRITE PROTECT (WP)The entire memory array can be write protected by setting the WP pin to the “H” level. When the WP pin is set to the “L” level, the entire memory array will be rewritten. Reading is allowed regardless of the WP pin's “H” level or “L” level.Do not change the WP signal level during the communication period from the start condition to the stop condition.Note : The WP pin is pulled down internally to the VSS pin, therefore if the WP pin is open, the pin status is recognized as the “L” level (write enabled).MB85RC16V ■COMMAND•Byte WriteIf the device address word (R/W “0” input) is sent after the start condition, an ACK responds from the slave.After this ACK, write memory addresses and write data are sent in the same way, and the write ends by•Page WriteIf data is continuously sent after the following address when the same command (expect stop condition) as Byte Write was sent, a page write is performed. The memory address rolls over to first memory address (000H)at the end of the address. Therefore, if more than 2 Kbytes are sent, the data is overwritten in orderMB85RC16V•Current Address ReadIf the last write or read operation finishes correctly up to the end of stop condition, the memory address that was accessed last remains in the memory address buffer (the length is 11 bits).When sending this command without turning the power off, it is possible to read from the memory address n+1 which adds 1 to the total 11-bit memory address n, which consists of the memory upper address 3-bit from the device address word input and the lower 8-bit of the memory address buffer. If the memory address n is the last address, it is possible to read with rolling over to the head of the memory address (000H). The current address (address that the memory address buffer indicates) is undefined immediately after turning•Random ReadAfter specifying the address as well as for write system command, issuing another start condition, by trans-mitting Device Address Word (R/W “1” input), the one byte data from the memory address saved in the memory address buffer can be read synchronously to SCL.Setting values for the first and the second memory upper address codes should be the same (The figure below shows the input example).The final NACK (SDA is the “H” level) is issued by the receiver that receives the data. In this case, this bit is•Sequential ReadData can be received continuously following the Device address word (R/W “1” input) after specifying the address in the same way as for Random Read. If the read reaches the end of address, the read address■ABSOLUTE MAXIMUM RATINGS*: These parameters are based on the condition that Vss is 0 V .WARNING:Semiconductor devices can be permanently damaged by application of stress (voltage, current,temperature, etc.) in excess of absolute maximum ratings. Do not exceed these ratings.■RECOMMENDED OPERATING CONDITIONS*: These parameters are based on the condition that Vss is 0 V .WARNING:The recommended operating conditions are required in order to ensure the normal operation ofthe semiconductor device. All of the device's electrical characteristics are warranted when the device is operated within these ranges.Always use semiconductor devices within their recommended operating condition ranges.Operation outside these ranges may adversely affect reliability and could result in device failure.No warranty is made with respect to uses, operating conditions, or combinations not represented on the data sheet. Users considering application outside the listed conditions are advised to contact their representatives beforehand.ParameterSymbol RatingUnit Min Max Power supply voltage*V DD − 0.5 + 6.0V Input voltage*V IN − 0.5V DD + 0.5 ( ≤ 6.0)V Output voltage*V OUT − 0.5V DD + 0.5 ( ≤ 6.0)V Ambient temperature T A − 40 + 85 °C Storage temperatureT STG− 40+ 125°CParameterSymbol ValueUnit Min Typ Max Power supply voltage*V DD 3.0⎯ 5.5V “H” level input voltage*V IH V DD × 0.8⎯ 5.5V “L” level input voltage*V IL V SS ⎯V DD × 0.2V Ambient temperatureT A− 40⎯+ 85°C■ELECTRICAL CHARACTERISTICS1.DC Characteristics(within recommended operating conditions)*1: Applicable pin: SCL,SDA *2: Applicable pin: SDAParameterSymbol ConditionValueUnit Min Typ Max Input leakage current*1|I LI |V IN = 0 V to V DD ⎯⎯1μA Output leakage current*2|I LO |V OUT = 0 V to V DD ⎯⎯1μA Operating power supply current I CC SCL = 400 kHz⎯4080μA Standby current I SB SCL, SDA = V DDWP = 0V or V DD or OPEN T A = + 25 °C in stop condi-tion⎯510μA “L” level output voltage V OL I OL = 2 mA ⎯⎯0.4V Input resistance for WP pin R INV IN = V IL (Max)50⎯⎯k ΩV IN = V IH (Min)1⎯⎯M Ω2.AC Characteristics(within recommended operating conditions)AC characteristics were measured under the following measurement conditions.Power supply voltage : 3.0 V to 5.5 V Operating temperature : − 40 °C to + 85 °C Input voltage amplitude : V DD × 0.2 to V DD × 0.8 Input rise time : 5 ns Input fall time : 5 ns Input judge level : V DD /2 Output judge level: V DD /2ParameterSymbolValueUnitSTANDARD MODE FAST MODE MinMax Min Max SCL clock frequency FSCL 01000400kHz Clock high time T HIGH 4.0⎯0.6⎯μs Clock low time T LOW 4.7⎯ 1.3⎯μs SCL/SDA rise time T r ⎯1000⎯300ns SCL/SDA fall time T f ⎯300⎯300ns Start condition hold T HD:STA 4.0⎯0.6⎯μs Start condition setup T SU:STA 4.7⎯0.6⎯μs SDA input hold T HD:DAT 0⎯0⎯ns SDA input setup T SU:DAT 250⎯100⎯ns SDA output hold T DH:DAT 0⎯0⎯ns Stop condition setupT SU:STO 4.0⎯0.6⎯μs SDA output access after SCL fall T AA ⎯3⎯0.9μs Pre-charge timeT BUF 4.7⎯ 1.3⎯μs Noise suppression time constant on SCL, SDAT SP⎯50⎯50ns4.Pin capacitanceParameter Symbol Conditions ValueUnit Min Typ Max I/O capacitance C I/O V DD = V IN = V OUT = 0V, f = 1 MHz, T A = + 25 °C⎯⎯15pF Input capacitanceC IN⎯⎯15pF■NOTES ON USE•Data written before performing IR reflow is not guaranteed after IR reflow.•VDD is required to be rising from 0 V because turning the power on from an intermediate level may cause malfunctions, when the power is turned on.ParameterSymbol ValueUnit Min Max SDA, SCL level hold time during power down tpd 85⎯ ns SDA, SCL level hold time during power up tpu 85⎯ ns Power supply rise time tr 0.550ms Power supply fall time tf 0.0150ms Power off timetOFF50⎯ms■ORDERING INFORMATIONPart number Package RemarksMB85RC16VPNF-G-JNE1 8-pin, plastic SOP (FPT-8P-M02)MB85RC16VPNF-G-JNERE1 8-pin, plastic SOP(FPT-8P-M02)Embossed Carrier tape■PACKAGE DIMENSIONPlease check the latest package dimension at the following URL. /package/en-search/MEMOFUJITSU SEMICONDUCTOR LIMITED Nomura Fudosan Shin-yokohama Bldg. 10-23, Shin-yokohama 2-Chome, Kohoku-ku Y okohama Kanagawa 222-0033, JapanT el: +81-45-415-5858/fsl/en/For further information please contact:North and South AmericaFUJITSU SEMICONDUCTOR AMERICA, INC. 1250 E. Arques Avenue, M/S 333Sunnyvale, CA 94085-5401, U.S.A.T el: +1-408-737-5600 Fax: +1-408-737-5999 /micro/EuropeFUJITSU SEMICONDUCTOR EUROPE GmbH Pittlerstrasse 47, 63225 Langen, GermanyT el: +49-6103-690-0 Fax: +49-6103-690-122 /semiconductor/KoreaFUJITSU SEMICONDUCTOR KOREA LTD.902 Kosmo T ower Building, 1002 Daechi-Dong, Gangnam-Gu, Seoul 135-280, Republic of Korea T el: +82-2-3484-7100 Fax: +82-2-3484-7111 /fsk/Asia PacificFUJITSU SEMICONDUCTOR ASIA PTE. LTD.151 Lorong Chuan,#05-08 New T ech Park 556741 SingaporeT el : +65-6281-0770 Fax : +65-6281-0220/semiconductor/FUJITSU SEMICONDUCTOR SHANGHAI CO., LTD. Rm. 3102, Bund Center, No.222 Y an An Road (E), Shanghai 200002, ChinaT el : +86-21-6146-3688 Fax : +86-21-6335-1605 /fss/FUJITSU SEMICONDUCTOR P ACIFIC ASIA LTD. 10/F., World Commerce Centre, 11 Canton Road, Tsimshatsui, Kowloon, Hong KongT el : +852-2377-0226 Fax : +852-2376-3269/fsp/Specifications are subject to change without notice. For further information please contact each office.All Rights Reserved.The contents of this document are subject to change without notice.Customers are advised to consult with sales representatives before ordering.The information, such as descriptions of function and application circuit examples, in this document are presented solely for the purpose of reference to show examples of operations and uses of FUJITSU SEMICONDUCTOR device; FUJITSU SEMICONDUCTOR does not warrant proper operation of the device with respect to use based on such information. When you develop equipment incorporating the device based on such information, you must assume any responsibility arising out of such use of the information.FUJITSU SEMICONDUCTOR assumes no liability for any damages whatsoever arising out of the use of the information.Any information in this document, including descriptions of function and schematic diagrams, shall not be construed as license of the use or exercise of any intellectual property right, such as patent right or copyright, or any other right of FUJITSU SEMICONDUCTOR or any third party or does FUJITSU SEMICONDUCTOR warrant non-infringement of any third-party's intellectual property right or other right by using such information. FUJITSU SEMICONDUCTOR assumes no liability for any infringement of the intellectual property rights or other rights of third parties which would result from the use of information contained herein.The products described in this document are designed, developed and manufactured as contemplated for general use, including without limitation, ordinary industrial use, general office use, personal use, and household use, but are not designed, developed and manufactured as contemplated (1) for use accompanying fatal risks or dangers that, unless extremely high safety is secured, could have a serious effect to the public, and could lead directly to death, personal injury, severe physical damage or other loss (i.e., nuclear reaction control in nuclear facility, aircraft flight control, air traffic control, mass transport control, medical life support system, missile launch control in weapon system), or (2) for use requiring extremely high reliability (i.e., submersible repeater and artificial satellite).Please note that FUJITSU SEMICONDUCTOR will not be liable against you and/or any third party for any claims or damages aris-ing in connection with above-mentioned uses of the products.Any semiconductor devices have an inherent chance of failure. You must protect against injury, damage or loss from such failures by incorporating safety design measures into your facility and equipment such as redundancy, fire protection, and prevention of over-current levels and other abnormal operating conditions.Exportation/release of any products described in this document may require necessary procedures in accordance with the regulations of the Foreign Exchange and Foreign Trade Control Law of Japan and/or US export control laws.The company names and brand names herein are the trademarks or registered trademarks of their respective owners.Edited: Sales Promotion Department。
tl851芯片用法 -回复

tl851芯片用法-回复首先,我们先了解一下TL851芯片的基本概念和用途。
TL851芯片是一种高性能微控制单元(MCU),它由德州仪器(Texas Instruments)公司开发和生产。
这款芯片具有强大的处理能力和丰富的外设接口,广泛应用于各种电子设备和系统中。
TL851芯片主要用于控制和管理电子设备以及实现各种功能。
它可以运行各种软件程序,并通过外部接口与其他电子组件进行数据交互。
基于TL851芯片的系统可以实现各种功能,如智能家居控制、工业自动化、医疗设备、通信设备等。
接下来,我们将一步一步回答有关TL851芯片的用法。
第一步:选择合适的开发环境和工具在开始编程和应用TL851芯片之前,我们需要选择合适的开发环境和工具。
德州仪器公司提供了一整套的开发工具和软件,如Code Composer Studio(CCS)集成开发环境、TL851系列开发板、调试器和编译器等。
我们可以根据自己的需求和经验选择合适的开发环境和工具。
第二步:编写程序代码一旦有了合适的开发环境和工具,我们就可以开始编写TL851芯片的程序代码了。
使用C语言或汇编语言等高级语言编程,我们可以利用TL851芯片的丰富外设接口,实现各种功能和控制。
编写程序代码时,我们需要了解TL851芯片的寄存器和功能特性,以便正确地配置和使用。
第三步:连接外设和资源配置TL851芯片具有多个GPIO引脚和外设接口,我们可以根据实际需求连接外设和配置相关资源。
例如,如果我们需要使用串口通信功能,我们可以将TL851芯片的串口引脚连接到外部串口设备,并配置相应的寄存器和参数。
同样,如果我们需要使用ADC(模数转换器)功能,我们可以连接外部传感器,并配置ADC转换参数。
第四步:调试和测试在编写程序代码和配置外设之后,我们需要对TL851芯片进行调试和测试,以确保程序的正确性和性能。
通过连接调试器和编译器,我们可以在开发环境中进行单步调试、变量监视和性能分析。
KB851资料

Features1.High collector-emitter voltage.(Vceo:350V)2.High isolation voltage between input and output .(Viso:5000Vrms)pact dual-in-line package .4.Rohs compliant.Applications1.ON-OFF switching for transmission/reception circuit for telephone.2.Interface to various power supply circuits, power patch boards.3.Copiers,facsimiles.4.Output section for numerical control machines.5.Controller for SSRs, DC motors .UNIT : MM[INCH]TOLERANCE : ±0.5[±0.02] UNLESS OTHERWISE NOTED.*Absolute Maximum Ratings (Ta=25°C)*Electro-optical CharacteristicsParameter Symbol Conditions Min.Typ.Max.Input Forward voltage V F I F=20mA- 1.2 1.4 Peak forward voltage V FM I FM=0.5A-- 3.0 Reverse current I R V R=4V--10Output Collector dark current I CEO Vce=200V IF=0--10-6Transfer charact-eristics Current transfer ration CTR IF=5mA Vce=5V-80-Collector-emitter saturation voltage VCE (sat)IF=20mA IC=1mA-0.10.3 ResponsetimeRise time trtr-418Fall time318Vce=2V IC=2mARL=100ΩUnitVVuAA%VuSuS Parameter Symbol Rating UnitInput Forward current I F50mA Reverse voltage V R6V Power dissipation P70mWOutput Collector-emitter voltage V CEO350V Emitter-collector voltage V ECO7V Collector current IC50mA Collector power dissipation P C150mWTotal power dissipation P tot200mW *1 Isolation voltage V iso5000Vrms Operating temperature T opr-30 to +100°C Storage temperature T stg-55 to +125°CT sol260°C *2 Soldering temperature*1 40 to 60%RH, AC for1 minute.*2 For 10 seconds.Fig. 1 Forward Current vs. Ambient Temperature Fig. 2 Collector Power Dissipation VS Ambient TemperatureFig. 3 Current Transfer Ration vs. Forward Current Fig. 4 Forward Current vs. Forward voltageFig. 5 Collector Current vs.Collector-emitter Voltage Fig. 6 Relative Current Transfer Ratio vs. Ambient TemperatureFig. 7 Response Time vs.Load ResistanceFig. 8 Collector-emitter SaturationVoltage vs. Ambient Temperature。
VSC8514評估板用戶指南说明书
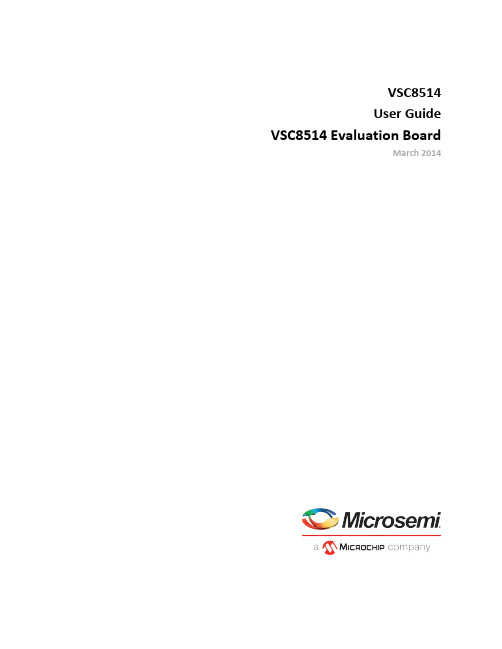
VSC8514User Guide VSC8514 Evaluation BoardMarch 2014Contents1Revision History (1)1.1Revision 1.0 (1)2Introduction (2)3General Description (3)3.1Key Features (3)3.1.1Copper Port RJ45 Connections (3)3.1.2Zarlink ZL30343 SyncE G.8262/SETS (3)3.1.3External RefClk Option (4)3.1.4Recovered Clocks (4)4Quick Start (5)4.1Connecting the Power Supply (5)4.2PC Software Installation (5)4.3Connecting to the Board to the PC (5)4.3.1Changing the IP Address of the Board (5)4.4Using the Control Software (6)4.4.1Board Initialization (7)4.4.2Copper Media Operation (Auto-negotiation Enabled) (7)4.4.3Sync-E Operation (8)4.5Useful Registers (8)4.5.1Ethernet Packet Generator (8)4.5.2Copper PHY Error Counters (8)4.5.3Near-End Loopback (8)4.5.4Far-End Loopback (8)4.5.5QSGMII SerDes Loopback (8)5Additional Information (9)1Revision HistoryThe revision history describes the changes that were implemented in this document. The changes arelisted by revision, starting with the most current publication.1.1Revision 1.0Revision 1.0 of this datasheet was published in March 2014. This was the first publication of thedocument.2IntroductionThe VSC8514 device is a low-power, quad-port Gigabit Ethernet transceiver with copper mediainterfaces. The device includes an integrated quad two-wire serial multiplexer (MUX) to control powerover Ethernet (PoE) modules. It features low electromagnetic interference (EMI) line drivers andintegrated line side termination resistors that conserve both power and board space. Dual recoveredclock outputs are available to support Synchronous Ethernet (Sync-E) applications, each withprogrammable squelch options.This document describes the architecture and usage of the VSC8514 Evaluation Board (VSC8514EV). TheQuick Start section describes how to install and run the graphical user interface (GUI) to fully control theevaluation board.Figure 1 • VSC8514 Evaluation BoardAdditional VSC8514 collateral for both the VSC8514 device and VSC8514EV, including schematics,layout, GUI, and application notes can be found on the VSC8514 product web page at: https://www./products/product.php?number=VSC8514.3General DescriptionThe evaluation board, shown in Figure 1, provides the user a way to evaluate the VSC8514 device inmultiple configurations. Four RJ-45 connectors are provided for copper media interfaces. The MACinterface is exposed via SMA connectors.For access to all of the features of the device, an external microcontroller is used to configure the on-board clock chip via a two wire serial bus and the VSC8514 via the MDIO bus. The GUI enables the userto read and write device registers.3.1Key Features3.1.1Copper Port RJ45 ConnectionsPHY ports 2 and 3 use the UDE RTA 1648BAK1A with integrated magnetic while PHY ports 0 and 1 usegeneric RJ45 connectors with discrete Pulse H5008NL magnetics.SGMII/QSGMII MAC SMAThe QSGMII differential input port is available through SMA connectors J1 and J2, while the output portis available through SMA connectors J4 and J5. Both of them are AC coupled.Switch Block ControlSW1 controls COMA_MODE, CLK_SQUELCH_IN and REFCLKSEL_[1:0]. The default configuration is withall switches set to low as shown in the figure below.Figure 2 • SW1 Switch Control3.1.2Zarlink ZL30343 SyncE G.8262/SETSThe Silabs F311 micro-controller is pre-programmed to configure the Zarlink ZL30343 to provide a 125MHz differential LVPECL clock to the VSC8514 REFCLK input, either based on the 20 MHz on-boardcrystal, or RCVRDCLK1 from the VSC8514 (Sync-E mode). When RCVRDCLK1 is enabled to output aproper 125 MHz clock, the ZL30343 will generate a 125 MHz output clock synchronized to theRCVRDCLK1 and will switch from HOLDOVER mode to LOCK mode as indicated by LEDs D33 and D34 asshown in the figure below.The left side of the illustration shows the HoldOver mode and the right side shows the Lock mode.Figure 3 • ZL30343 LED Indication3.1.3External RefClk OptionThe user may choose to provide an external PHY REFCLK via SMA connections to J21 and J23 (as shownin Figure 3 above). To route the SMA signals to the device the user must reorient the zero ohm resistors,R151, and R152.3.1.4Recovered ClocksThere are two recovered clocks available from the VSC8514, through J22 and J24. In the defaultconfiguration, CLK_SQUELCH_IN is pulled down, which disables the clock squelching and RCVRDCLK1 isconnected to the Zarlink device while RCVRDCLK2 is connected to SMA connector J24. RCVRDCLK1 andRCVRDCLK2 connections can be reconfigured by replacing the zero ohm resistors, R19, and R22,respectively.Network Interface Microcontroller CardA “Rabbit” microcontroller card is included to facilitate a software interface to the registers on theVSC8514. The controller card has a hard coded static IP address. Refer to the label on the card for thevalue. This address is required by the user to initiate communications via the board and the GUI.10.9.70.193The factory programmed Rabbit board IP address is: .1. 2. 3. 1. 2. 3. 4. 5. 6. 7. 8. 9. 10. 11. 4Quick Start This section shows the quick start for VSC8514.4.1Connecting the Power SupplyThe evaluation board uses 5 VDC to power the on-board regulators creating the 3.3 V, 2.5 V, and 1.0 V rails which drive the devices as well as modules. The evaluation board can be powered using the power pack which provides the 5 VDC. Simply plug the AC adaptor into a wall socket and the barrel end into J67 (see the upper right corner of Figure 1). Immediately the user should see several LEDs turn on.The user may alternately connect the board to a bench style power supply by connecting the red banana plug to 5 VDC and the black banana plug to ground. If the supply provides 3 A the board should come alive as described above.4.2PC Software InstallationDownload the ZIP file to the PC’s root directory, normally C:\.Extract to C:\Double click the icon to launch the GUI (It is acceptable to drag the icon to the desktop)4.3Connecting to the Board to the PCThe Rabbit board can interface with a PC either through a direct connection to the PC or if configured properly through a local area network. The latter option requires the user to configure the Rabbit’s IP address so as to properly reside on the user’s network.The IP address of the board should be written on the Rabbit network interface daughter board card. The default value should be 10.9.70.193. You will need to use this IP address to initially access the board for operation or to change its IP address.4.3.1Changing the IP Address of the BoardDetermine and write down the new unique IP address you wish to change the board to.Directly connect an Ethernet cable from a PC to the Rabbit board.: Some older PCs do not support auto-crossover on the Ethernet connection so a cross-over NOTE cable may be unch a DOS command window by clicking on the Start->Run button and typing “cmd”.Within the DOS command window type “Telnet”.In the Telnet window, connect to the Rabbit board’s address using the open command by typing open 10.9.70.193, as this is the factory default address.You should have a prompt and be able to type help to get a list of commands available on the Rabbit.a.) If you are unable to connect, then most likely you will need to change the IP address of the connected PC to have the first 3 octets similar to the board by following the subsequent steps.b.) On the PC under Windows -> Control Panel ->Network Connections -> Local Area Connection, right mouse click for Properties. Under the General tab highlight Internet Protocol (TCP/IP) and click on Properties. From there enter the new PC IP address such as 10.9.70.yyy where yyy is a unique value and NOT the same as the Rabbit board. Once complete, return to step 4.From the Telnet window, update the IP address by typing set ip <new IP address> <Enter>, where <new IP address> is in the form of xxx.xxx.xxx.xxx.After hitting <Enter> the IP address will change and the Rabbit will save the value and reboot which may take approximately 1 minute.The Telnet session will disconnect from the board.Change your PC IP address to the same IP network as the Rabbit board.Telnet to the Rabbit e the following commands to complete configuration of the Rabbit board configuration:a) set netmask xxx.xxx.xxx.xxx b) set gateway xxx.xxx.xxx.xxx c) save envPlease record and inform Microsemi of the new IP address of the board when you return so that11. 12. Please record and inform Microsemi of the new IP address of the board when you return so that Microsemi can connect to and reconfigure the board.Re-label the Rabbit board with the new IP.4.4Using the Control SoftwareConnect the VSC8514EV Rabbit microcontroller’s RJ-45 directly to the PC or through a network switch if properly configured. Apply 5 VDC to the EVB.Launch the GUI by double clicking the GUI shortcut located in C:\EliseGUI_4_67 or on the desktop if it has been moved there. The GUI connection window shown in the figure below should appear.Figure 4 • GUI Connection WindowTo make a connection to the EVB, click “Rabbit” and enter the IP address of the EVB, then click on “Connect”. The display next to the IP address window should change to “Connected”. If it does not, check the IP address, or your network configuration until the connection with the EVB can be successfully established.Double click on “MII Registers” and the window shown in the following figure should appear:1. Double click on “MII Registers” and the window shown in the following figure should appear:Figure 5 • MII Registers GUI WindowBe sure the device is up and running by reading MII Register 0. It should read back 0 × 1040. Reading back all 0’s or all 1’s indicates a problem. A checked box means the bit is set to “1,” if unchecked it is “0.”4.4.1Board InitializationOnce the evaluation board connectivity has been established and confirmed, the PHY should be initialized. Initialization can be accomplished by running an init-script sequence, such as performed by the pre- and post-reset functions of the PHY API standalone app.While the init-script sequence may not be required for specific operational modes, an init-script sequence is highly recommended to ensure correct performance over the greatest set of user scenarios for the PHY. After initialization is performed, refer to the PHY datasheet section on configuring the PHY and PHY Interfaces for the desired application.4.4.2Copper Media Operation (Auto-negotiation Enabled)A single register write and some external coax cables enables 1 G Ethernet traffic to be received by the VSC8514 RJ-45 port(s), routed through the VSC8514 and externally looped back via coax cables through the QSGMII interface and transmitted back to the traffic source on the same copper port(s).The following steps are used to setup an external QSGMII loopback:Set up the copper traffic source (i.e., IXIA or Smartbits)1. 2. 3. 4. 5. 6. 7. Set up the copper traffic source (i.e., IXIA or Smartbits)Connect Ethernet cable(s) to a single or multiple RJ-45 ports.Connect two matched coax cables, J1 - J4 and J2 - J5.Write using the "Micro Page Registers" window: 19'd 0 × 400F.Write using the "Micro Page Registers" window: 18'd 0 × 80E0.When "Micro Page" 18'd is read back, bit 15 will clear.Linkup bit is in MII Reg 1, bit 2 (MII 1.2), read twice to update.Traffic should be the following:4.4.3Sync-E OperationTo enable 12 MHz Sync-E operation on this evaluation board a few register writes are required. Write 0 × 8101 on register 23’d of the “Micro Page Registers” to enable RCVRDCLK1 with PHY0 as the clock source when PHY0’s link is up in a non-EEE mode and not 1000BT master or 10BT. To select a different port as the clock source or enable a recovered clock for EEE mode, refer to register 23 G in the datasheet for the programming detail. Set MII Reg.9 bit 12 to enable manual slave configuration then issue an auto negotiation restart through reg.0 bit 9.4.5Useful Registers 4.5.1Ethernet Packet GeneratorExtMII 29E is the Ethernet Packet Generator register. Refer to the datasheet for configuration options.A good CRC packet counter is in ExtMII 18.13:0. A read of the register reads back the good CRC packets and then clears the register so the subsequent reads will be 0 if no traffic has been received. If traffic has been received since the last read, bit 15 will be set.4.5.2Copper PHY Error CountersIdle errors = MII 10.7:0RX errors = MII 19.7:0False carrier = MII 20.7:0Disconnects = MII 21.7:0CRC errors = ExtMII 23.7:04.5.3Near-End LoopbackWhen the near-end loopback test feature is enabled, the transmitted data is looped back in the PCS block on the receive data signals. To enable the loopback, set register bit.0.14 to 1.4.5.4Far-End LoopbackWhen the far-end loopback test feature is enabled, incoming data from a link partner on the Copper interface to be transmitted back to the link partner on the Copper interface. To enable the loopback, set register bit.23.3 to 1.4.5.5QSGMII SerDes LoopbackThere are 3 different types of loopback that occurs in the SerDes block:Input loopback: loops serial data from TDP/N onto RDP/N by writing 0 × 9022 to reg.18G Facility loopback: loops de-serialized data from TDP/N back to the serialized data onto RDP/N by writing 0 × 9022 to reg.18G Equipment loopback: similar to far-end loop but occurs in the SerDes block, by writing 0 × 9042 to reg.18G5Additional InformationFor any additional information or questions regarding the devices mentioned in this document, contactyour local sales representative.Microsemi HeadquartersOne Enterprise, Aliso Viejo,CA 92656 USAWithin the USA: +1 (800) 713-4113Outside the USA: +1 (949) 380-6100Sales: +1 (949) 380-6136Fax: +1 (949) 215-4996Email:***************************© Microsemi. All rights reserved. Microsemi and the Microsemi logo are trademarks of Microsemi Corporation. All other trademarks and service marks are the property of their respective owners.Microsemi makes no warranty, representation, or guarantee regarding the information contained herein or the suitability of its products and services for any particular purpose, nor does Microsemi assume any liability whatsoever arising out of the application or use of any product or circuit. The products sold hereunder and any other products sold by Microsemi have been subject to limited testing and should not be used in conjunction with mission-critical equipment or applications. Any performance specifications are believed to be reliable but are not verified, and Buyer must conduct and complete all performance and other testing of the products, alone and together with, or installed in, any end-products. Buyer shall not rely on any data and performance specifications or parameters provided by Microsemi. It is the Buyer's responsibility to independently determine suitability of any products and to test and verify the same. The information provided by Microsemi hereunder is provided "as is, where is" and with all faults, and the entire risk associated with such information is entirely with the Buyer. Microsemi does not grant, explicitly or implicitly, to any party any patent rights, licenses, or any other IP rights, whether with regard to such information itself or anything described by such information. Information provided in this document is proprietary to Microsemi, and Microsemi reserves the right to make any changes to the information in this document or to any products and services at any time without notice.Microsemi, a wholly owned subsidiary of Microchip Technology Inc. (Nasdaq: MCHP), offers a comprehensive portfolio of semiconductor and system solutions for aerospace & defense, communications, data center and industrial markets. Products include high-performance and radiation-hardened analog mixed-signal integrated circuits, FPGAs, SoCs and ASICs; power management products; timing and synchronization devices and precise time solutions, setting the world's standard for time; voice processing devices; RF solutions; discrete components; enterprise storage and communication solutions; security technologies and scalable anti-tamper products; Ethernet solutions; Power-over-Ethernet ICs and midspans; as well as custom design capabilities and services. Microsemi is headquartered in Aliso Viejo, California, and has approximately 4,800 employees globally. Learn more at www. .VPPD-03695。
(完整版)MB85RC64中文

(完整版)MB85RC64中⽂铁电存储器MB85RC64(8K×8)1.概述MB85RC64了FRAM(铁电随机存取记忆体)独⽴芯⽚配置了8192×8位,形成铁电⼯艺和硅栅CMOS⼯艺技术⾮易失性内存中的细胞。
MB85RC64采⽤两线串⾏接⼝(与世界标准的I2C总线兼容)。
与SRAM不同的MB85RC64是⽆需使⽤数据备份电池,能够保留数据。
MB85RC64的读写次数10亿次,与EPROM和FLASH相⽐,有显著的改善。
⽽且不在向写完存储器后,不需要查询序列。
2.特性●位操作:8192×8位●⼯作电压:2.7V—3.3V●⼯作频率:400KHz●两串⾏总线:I2C总线2.1标准版,⽀持标准模式和快速模式,由SCL和SDA控制。
●⼯作温度范围:-40℃—85℃●数据保持:10年(55℃)●读写寿命:⾄少每位10亿次●封装:Plastic / SOP, 8-pin (FPT-8P-M02)●低电压消耗:⼯作电流0.15mA,待机电流5uA3.管脚分配3.管脚功能描述4.模块框图5.I2C电路MB85RC64有两线串⾏接⼝,⽀持I2C总线,并作为从器件⼯作。
I2C总线定义的“主机”和“从机”设备的沟通⾓⾊,主机启动总线控制权。
此外,通过I2C总线,在⼀个主机可以连接多个从器件。
在这种情况下,必须给从器件分配⼀个唯⼀的设备地址。
6.I2C通信协议I2C总线是双线串⾏接⼝,采⽤了双向数据总线(SDA)和串⾏时钟(SCL)。
数据传输只能由总线主机,这也将提供串⾏时钟的同步启动。
SCL为低电平时,SDA信号应该改变。
然⽽,作为⼀种例外,启动和停⽌时的通信序列,SDA被允许改变当SCL为⾼电平。
●启动条件:开始时,SCL为稳定⾼电平,SDA产⽣下降沿。
●停⽌条件:停⽌时,SCL为稳定低电平,SDA产⽣上升沿。
停⽌条件是终⽌从设备和主机通信。
MB85RC64不需要像内部写存储器像E2PROM花时间去查询序列,因此当写停⽌命令结束,设备进⼊待机模式。
固定速度交流电机操作与安装指南:0-1
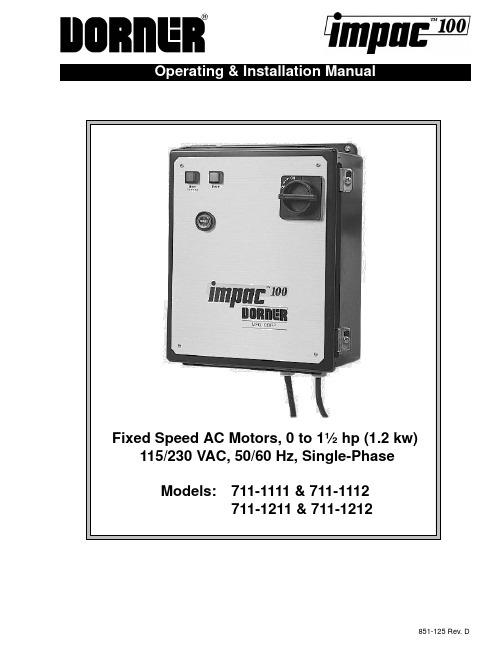
851-125 Rev. DTable of Contents. . . . . . . . . . . . . . . . . . . . . . . . . . . . . . . . . . . . . . . .1.0Safety Considerations3. . . . . . . . . . . . . . . . . . . . . . . . . . . . . . . . . . . . . . . . . . .1.1Grounding3. . . . . . . . . . . . . . . . . . . . . . . . . . . . . . . . . . . . . . . . . . . . . . .1.2Fusing3. . . . . . . . . . . . . . . . . . . . . . . . . . . . .1.3Power Wiring to Controller3. . . . . . . . . . . . . . . . . . . . . . . . . . . . . . . . . . . . . . . . . . . . . . . . .2.0Introduction3. . . . . . . . . . . . . . . . . . . . . . . . . . . . . . . . . . . . . . . . . .3.0Product Description3. . . . . . . . . . . . . . . . . . . . . . . . . . . . . . . . . . . . . . . .4.0Product Specifications4. . . . . . . . . . . . . . . . . . . . . . . . . . . . . . .5.0Conveyor Controller Installation55.1Inspecting the Controller5. . . . . . . . . . . . . . . . . . . . . . . . . . . . . . .. . . . . . . . . . . . . . . . . . . . . . . . . . . . . . . .5.2Mounting the Controller5. . . . . . . . . . . . . . . . . . . . . . . .5.3Power Connections to Controller6. . . . . . . . . . . . . . . . . . .5.4Motor Overload Setting and Checking6. . . . . . . . . . . . . . . . . . . . . . . . . . . .5.5Controller Power-up Testing6. . . . . . . . . . . . . . .5.6Motor Connections to Conveyor Controller65.7Motor and Conveyor Controller Power-up Testing6. . . . . . . . .. . . . . . . . . . . . . . . . . . . .6.0Implementing Conveyor Control Applications7. . . . . . . . . . . . . . . . . . . . . . . . . . . . .7.0Operating the Conveyor Controller97.1Starting the Controller9. . . . . . . . . . . . . . . . . . . . . . . . . . . . . . . . .. . . . . . . . . . . . . . . . . . . . . . . . . . . . . . . .7.2Stopping the Controller9. . . . . . . . . . . . . . . . . . . . . . . . . . . . . . . . . . . . . .7.3Controller Reset9. . . . . . . . . . . . . . . . . . . . . . . . . . . . . . . . . . . . . . . . . . . .8.0Troubleshooting10. . . . . . . . . . . . . . . . . . . . . . . . . . . . . . . . . . . . . .9.0Replacement Parts List11851-125 Rev. D2PD0996PD09973851-125 Rev. D1.0Safety Considerations1.1Grounding1.2Fusing1.3Power Wiring to ControllerThis manual contains the information needed to install,operate, and troubleshoot the Dorner impac 100 Conveyor Controller. It is organized in a step-by-step fashion so that the Conveyor Controller may be safely set-up, in the shortest possible time.3.0Product DescriptionThe impac 100 Conveyor Controller is a low-cost Industrial Multi-Purpose Application Controller that can be used to control a Conveyor motor on/off operation as well as vary the speed of the motor. The Conveyor Controller is user-installable with control options that allow it to meet the needs of a wide range of Conveyor control applications (indexing, jogging, accumulation,variable speed, automatic end-stop, emergency-stop,clutch-brake, merging of Conveyors, linking multiple Conveyors,...etc.). The Conveyor Controller can be ordered for Conveyors with fixed or variable speed AC or DC motors.The impac 100 Conveyor Controller’s motor control circuit is designed to support electrical interconnections to a variety of accessory kits (photo-eyes, E-stops, jog buttons, foot switches, E-stop pull cord units, process machine/PLC/PC dry contact interface, and more). Each kit includes brackets for mounting the unit to a Dorner 2100/3100 conveyor,cabling to wire the unit to an impac 100 Conveyor Controller,and instructions for mounting/wiring/operating the unit. The kits are connected to the impac 100 Conveyor Controller using convenient terminal point connections, inside the Controller.This allows the user to configure the kits to fit specific application needs and to re-configure the kits to perform new functions.The impac 100 Conveyor Controller comes with mounting hardware to allow mounting to a Dorner 2100 or 3100 Conveyor side rail (or Conveyor stand). The unit is housed in an NEMA 12/IP54 enclosure with Power “ON” and Motor “RUNNING”LED’s, a locking “ON/OFF” switch, a 24 volts D.C. power supply, adjustable motor overloads with manual reset, and pre-wired motor and AC line cords. The Conveyor Controller supports both fixed and variable speed AC motors using 115/230/460 volts A.C., 50/60Hz, 1-3 Phase, and variable speed 130/180 volts D.C. motors (with 115/230 volts A.C. input).Overall Conveyor system reliability is enhanced by the impac 100design features. Components meet applicable ANSI/NEC/IEC machine safety standards. Local on/off control and built-in motor & circuit overload protection enhance operator and application safety. Low voltage (24 volts D.C.) control circuits reduce installation and maintenance time as well as increase safety. A complete Conveyor Controller wiring schematic and troubleshooting guide are attached to the inside of the Conveyor Controller cover.851-125 Rev. D4PD09974.0Product Specificationsimpac 100711-1111711-1112711-1211711-1212Input Voltage 115 volts A.C. ± 10% 50/60 Hz230 volts A.C. ± 10% 50/60 HzInput Line Fuse (1) 10 Ampere (1) 15 Ampere (2) 10 Ampere (2) 15 Ampere Input Current 4 Amperes9 Amperes4 Amperes9 AmperesOverload Relay Class 10 Protection, Phase Loss Detection (for 3-Phase impac 100’s)Visible Trip Indication, External Reset Button Overload Range 1.5 to 4.5Amperes 3.7 to 12Amperes 0.9 to 2.9Amperes 3.7 to 12Amperes Motor Range 0 to1/3 HP 1 to 249 WattsAbove 1/3 to 1/2 HP 250 to 374 Watts0 to 1/3 HP 1 to 249 WattsAbove 1/3 to 1-1/2 HP 0.25 to 1.2 KilowattsOperating Temperature0 to 40° C to 95% Humidity (Non-condensing)A.C. Line Cord 8 Ft (2.4 m) Pre-Wired with molded NEMA 5-15P Plug 8 Ft (2.4 m) Pre-Wired with molded NEMA 6-15P Plug Motor Cord 5 Ft (1.5 m) Pre-Wiredwith molded NEMA 5-15R Receptacle5 Ft (1.5 m) Pre-Wiredwith molded NEMA 6-15R ReceptacleEnclosure NEMA Type 12 / IP54 Continuous Hinge, Weight: 21 lb (9.5 kg)Dimensions: 12″ (305 mm) High x 10″ (254 mm) Wide x 5″ (127 mm) DeepInternal Power Supply 24 volts D.C. 1.1 AmpereOver-current and Short Circuit-protectedStandard FeaturesD Lockable Disconnect Switch D Line Fuses(s)D Angled Terminal Block for Easy Field ConnectionsD ****************************************************D Power “ON” and Motor “RUNNING” Indicator Lights D Mounting Brackets and Hardware D Pre-wired Motor and AC Line Cords D Schematic Diagram Inside of DoorD Four (4) 1/2″ NPT Knockouts at Bottom of Enclosure with NEMA 12 PlugsNOTE:For additional information, refer to the following Dorner Publications:D impac 100 Catalog (Dorner Publication # 851-151)D impac 100 Accessory Kits Setup & Installation Guides (Dorner Publication # 851-108 through # 851-123)D impac 100 Application Guide (Dorner Publication # 851-124)PD09975851-125 Rev. D5.0Conveyor ControllerInstallation5.1Inspecting the ControllerCarefully examine your Controller (and any option kits, if ordered), for shipping damage. Check to be certain that the controller you ordered is the one you received. Also check any optional accessory kits which you received.5.2Mounting the ControllerSelect the desired location and mount the impac 100enclosure to the conveyor T-slot channel (Figure 2) or an aluminum support stand leg (Figure 3) or steel support stand leg (Figure 4), using the hardware provided.Figure 1: Drop-in T-bar Installation Detail Mounting in Conveyor T-slota.Insert the two Single Drop-in T -bars into conveyor T -slot by rolling each one into position (Figure 1).b.Select the desired location and attach the impac 100enclosure (in the same way it was packaged, when shipped) to the conveyor T -slot in the manner shown in Figure 2 using the two (2) M6 x 8 mm Button Head Cap Screws through the clearance hole in each Mounting Bar. Tighten the Screws with a 4 mm Hex Key Wrench.2− Single Drop-in T-bars (2 each)3− Mounting Bars (2 each)Figure 2: Conveyor T-slot Attachment DetailMounting to Aluminum Support Stand Lega.For an Aluminum Support Stand Leg, refer to Figure 3and detach, rotate and re-attach the Mounting Bars to the impac 100 enclosure in the horizontal position.b.Select the desired mounting location and insert the two Single Drop-in T -bars into Leg channel by rolling each of them into position (see Figure 1).c.Then, attach the impac 100 enclosure to the two Single Drop-in T -bars, using the M6 x 8 mm Button Head Cap Screws. Tighten Screws with a 4 mm Hex Key Wrench.2− Mounting Bars (2 each)3− Single Drop-in T-bars (2 each)Figure 3: Aluminum Leg Attachment Detail Mounting to Steel Support Stand Lega.For the Steel Support Stand Leg, refer to Figure 4 and detach, rotate and re-attach the Mounting Bars to the impac 100 enclosure in the horizontal position.b.Then, attach the impac 100 enclosure to the M6 Spring Nuts, using the M6 x 18 mm Button Head Cap Screws through the clearance hole in each Mounting Bar.1− M6 x 8 mm Button Head Cap Screws (4 each)2− Mounting Bars (2 each)3− M6 x 18 mm Button Head Cap Screws (2 each)4− M6 Spring Nuts (2 each)Figure 4: Steel Leg Attachment Detail851-125 Rev. D6PD09975.3Power Connections to ControllerEach Conveyor Controller has a pre-wired plug for power.The type of plug is dependent on the Controller voltage.5.4Motor OverloadSetting and CheckingWhen the impac 100 was factory tested, the motor overload was set up in one of the following configurations:1.If a motor was ordered with the impac 100, then the motor overload was set to match that motor.2.If the impac 100 was ordered without a motor, then the overload was set to a minimum value and the Conveyor Controller was tagged informing the user that the overload has not been set.NOTE:BE SURE to verify that the motor nameplate ampere rat-ing matches the setting on the overload relay.3.Look at the AMPERE rating on the motor nameplate. Be sure to select the rating based on the correct motor voltage.Example:c.If the nameplate reads “VOLTS: 115/230 AMPS:2.0/1.0”, then the Motor Amp rating is 2.0 Amps at 115 V olts. (listed first in each category) and 1.0 Amp at 230 V olts. (listed second in each category).d.Examine the setting on the motor overload relay. The overload relay is located inside the Conveyor Con-troller. The overload setting is the blue dial on the left side of the relay, the arrow should point to the value found on the motor nameplate. If the settings do not match, turn dial to the correct value.5.5Controller Power-up TestingTest the Conveyor Controller before the motor is connected,and before any impac accessory kits are installed. Plug the Controller into the appropriate power source and turn the Controller disconnect switch ON. The Power “ON” and the Motor “RUNNING” indicator lights, on the front of the impac Conveyor Controller, should illuminate.5.6Motor Connections to Conveyor ControllerPlug the motor cord into the impac Conveyor Controller receptacle cord. Each Conveyor Controller has a pre-wired cord with a receptacle for a motor. The type of receptacle is dependent on the Controller voltage. If a motor was ordered along with the Controller, then the motor was pre-wired with a mating power plug. The motor can also be hard-wired to the Controller by first removing the receptacle and wiring directly to the terminals “T1”, “T2”, and “GND”, inside the Controller. See the Controller panel layout (Figure 5) and the schematic diagrams (Figures 6 & 7) for more information.1− 230 VAC unit onlyFigure 5: Sample Control Panel Layout5.7Motor and Conveyor ControllerPower-up TestingAfter motor connections are made to the impac Conveyor Controller, plug the Controller into the appropriate power source and turn the Controller disconnect switch ON. The motor should run and the conveyor belt will move. The Power “ON” and the Motor “RUNNING” indicator lights, on the front on the Controller, should illuminate.PD09977851-125 Rev. DFigure 6: Schematic Diagram for 115 volts A.C. Controller6.0 Implementing ConveyorControl ApplicationsThe impac 100 control circuit is designed to support electrical interconnections to a variety of accessory kits (photo-eyes,E-stops, jog buttons, foot switches, E-stop pull cord units,process machine/PLC/PC dry contact interface, and more).The kits are connected to the impac 100 using convenient terminal point connections inside the controller. This allows the user to interconnect the kits to fit specific application control needs.A simplified version of the impac 100 control circuit is shown in figure 4. Four groupings of terminal point connections have been provided for connecting all impac accessory kits.1.The first group (COM-24V ) provides 24 volts D.C.power for any accessory kits that need power (photo-eyes, illuminated pushbuttons, etc.).2.The next group (PE1-PE2, ES1-ES2, and RR1-RR2)provide three sets of control points for wiring accessory kits into the impac 100 control circuit. Each group is configured with a jumper when the impac 100 controller is shipped. When an accessory kit is to be installed the jumper is removed and the kit connected. Each set ofcontrol points represents a “series” connection to the impac 100 control circuit. When accessory kits are wired in “series” it means that all connected accessories must be “on” for the conveyor to run. For example, if an accessory kit is wired to PE1-PE2 and another accessory kit is wired to ES1-ES2, then both accessories must be “on” for the conveyor to run.The impac 100 controller also supports wiring impac accessory kits in “parallel”. When an accessory kit is wired in “parallel” it means “if either” accessory kit is “on” the conveyor will run. Accessories connected in parallel are connected to the same impac 100 terminal points.For example, if two accessory kits are wired to PE1-PE2 then when either kit is “on” the conveyor will run. Any number of impac accessories can be configured in any of the above series and parallel combinations.3.The third group of terminals (MR1-MR2) provide an output contact (dry contact) that is closed when the conveyor is running. This can be used to link multiple conveyor operations together or to provide status back to a host controller.851-125 Rev. D8PD0997Figure 7: Schematic Diagram for 230 volts A.C. Controller4.The last group of terminals (SP1-SP2) are two spare terminal points that the user can use for extra termination points for accessory kit wiring.To select, configure, and implement a conveyor control application using the impac 100 Conveyor Controller and impac Accessory Kits the user should use the following steps.1.Remove power to the impac Conveyor Controller.Before installing and wiring any accessory kits, Remove power to the impac controller by unplugging the impac controller from the power source.2.Select Desired Control Application from the Dorner impac 100 Application Guide.Included with the impac 100 Application Guide are a list of conveyor control application examples that detail the following for many different conveyor control applications:D A description of the conveyor application controlrequirementsD An illustration of the conveyor with the impac 100controller and impac accessory kits mountedD A list of hardware required to implement the control application describedD A description of the conveyor operation D Detailed conveyor control setup instructionsDIllustration that shows how all accessory devices are connected to the impac 100 controllerBased on review of the Dorner impac 100 Application Guide select the application example that meets the needs of the end-user application. If required, make any final adjustments to the application accessory kit control connections needed by your particular application.3.Install all required impac accessory kitsInstall all accessory kits required for the application.The selected Application Example in the Dorner impac 100 Application Guide will show the general area of were the kits are to be located on the conveyor. Follow the impac Accessory kit Setup & Installation Guide for mounting and cable routing details.PD09979851-125 Rev. DEach impac accessory kit includes: Setup & Installation Guide; brackets for mounting; cabling to wire the unit to an impac 100 controller; and instructions for mounting/wiring/operating the unit. There are two 1/2″NPT knockouts available for accessory kit installation at the bottom on the controller. Remove the rubber seal,and install the accessory kit cable using the cord grip provided with the kit. The only wiring that is required will be at the accessory terminal block inside the controller. A 1/8″ (3 mm) flat blade screwdriver is shipped with the controller for wiring to the terminal block.4.Connect the impac accessory kits to the impac 100Conveyor Controller From the selected Application Example in the Dorner impac 100 Application Guide Connect the impac accessory kit cables to the impac controller terminal block as detailed in the application “Setup” description.5.Verify proper conveyor operationTest and operate the application based on the information detailed in the selected application “Operation & Test” description.6.File copy of the Control Application Documentation Place a copy of the Conveyor Control Application Example, that was used in step 4, inside impac 100controller.7.0Operating the ConveyorController7.1Starting the ControllerThe conveyor will be “ready to run” when the impac ON/OFF disconnect switch is turned ON. The Power “ON” light will be ON whenever power is applied to the Conveyor Controller and the ON/OFF disconnect switch is turned ON. If there are no impac accessory kits installed, the conveyor will run. If there is(are) any installed accessory kit(s), the conveyor may run depending on the “on/off” state of the accessory kits.When an accessory kit or kits allow the conveyor to run, the Motor “RUNNING” light will be ON and the motor will run.7.2Stopping the ControllerThe conveyor will be stopped when the impac ON/OFF disconnect switch is turned OFF. The Power “ON” light will be OFF whenever power is removed from the Conveyor Controller or the ON/OFF disconnect switch is turned OFF. If there are installed accessory kit(s), the conveyor may stop running, depending on the state of the accessory kits. When an accessory kit prohibits the conveyor from running, the Motor “RUNNING” light will turn OFF and the motor will stop.7.3Controller ResetIf a motor overload condition exists or the motor overload is set incorrectly, the overload relay will trip. The Power “ON”light will remain ON, and the Motor “RUNNING” light will turn OFF. Pressing the “RESET” button, on the front of the Conveyor Controller, will reset the overload relay. Before resetting, wait a few minutes to allow the relay to “cool” after the overload relay trips.851-125 Rev. D10PD09978.0TroubleshootingPROBLEMCAUSECORRECTIONMotor will not run and Motor “RUNNING” indicator is ON and “POWER” indicator is illuminatedOpen wiring connection between impac 100 & motor.Remove any power and, using appropriate means, check continuity and integrity of wiring.Motor Cord is not connected to motorProperly connect motor cord.Defective motorReplace motor.Motor will not run and Motor “RUNNING” indicator is OFF ,“POWER” indicator is illuminated and Power Supply LED is ON.Motor overload has tripped.Depress impac 100 “RESET”button to reset breaker.One or more accessory kits are not working properly and thus causing an OPEN contact.Check and properly install and wire accessory kits per the Setup & Installation Guide information provided with kit.One or more accessory kit jumpers, at impac 100 are removed and kit Devices are not installed, or incorrectly installed.Properly install and wire accessory kits per the Setup &Installation Guide information provided with kit.Motor will not run and Motor “RUNNING” indicator is OFF ,“POWER” indicator is illuminated and Power Supply LED is OFF .Power supply fuse has blown.Replace with correct amperage and type of fuse.One or more accessory kits are incorrectly installed and thus shutting-down the power supply.Properly install and wire accessory kits per the Setup &Installation Guide information provided with kit.Motor will not run and Motor “RUNNING” indicator is OFF and “POWER” indicator is not illuminated.No power to impac 100 or impac 100 is not plugged-in.Check all related wiring and make sure impac 100 power cord is plugged-in.Blown line fuse FU1 and/or FU2.Replace with correct amperage and type of fuse.Motor runs unexpectedly and Motor “RUNNING” indicator is ON and “POWER” indicator is illuminated.One or more accessory kits are incorrectly installed.Properly install and wire accessory kits per the Setup &Installation Guide information provided with kit.One or more accessory kit jumpers, at impac 100, are not correctly installed.Properly install and wire appropriate jumpers per the Setup & Installation Guide information provided with kit.9.0Replacement Parts ListItem Description DornerPart Number 1Power Supply831-110 2Terminal Block Assembly676266P 3Contactor805-800 4Motor Overload model 711-1111805-803model 711-1112, model 711-1212805-798model 711-1211805-802 5Fuse Holder model 711-1111, model 711-1112819-134model 711-1211, model 711-1212819-133 6Fuse model 711-1112, model 711-1212819-103model 711-1111, model 711-1212891-113 7Disconnect Switch805-724 8Amber Pilot Light Assembly830-133 9Green Pilot Light Assembly830-134 10Reset Pushbutton830-125PD099711851-125 Rev. DFor replacement parts, contact an authorized Dorner Service Center or the factory.。
Agilent Technologies 8514A B, 8515A, 8517A B, 8511
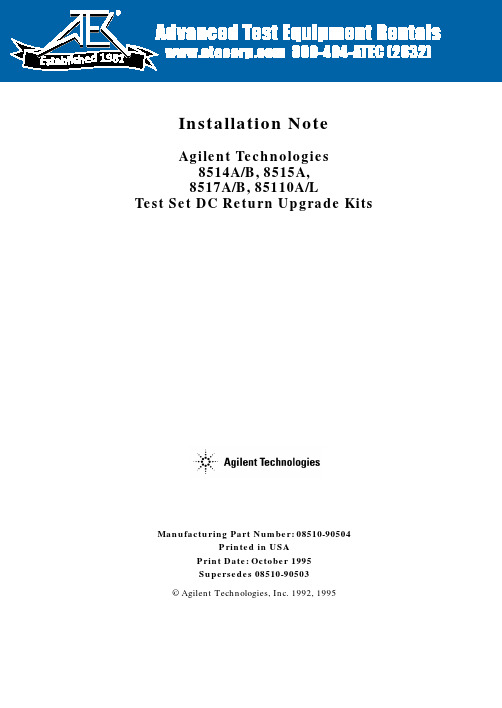
1981Installation NoteAgilent Technologies8514A/B, 8515A,8517A/B, 85110A/LTest Set DC Return Upgrade KitsManufacturing Part Number:08510-90504Printed in USAPrint Date: October 1995Supersedes 08510-90503© Agilent Technologies, Inc. 1992, 1995Hewlett-Packard to Agilent Technologies Transition This manual may contain references to HP or Hewlett-Packard. Please note thatHewlett-Packard's former test and measurement, semiconductor products and chemical analysis businesses are now part of Agilent Technologies. To reduce potential confusion, the only change to product numbers and names has been in the company name prefix: where a product number/name was HP XXXX the current name/number is now Agilent XXXX. For example, model number HP 8514A is now model number Agilent 8514A.Documentation WarrantyTHE MATERIAL CONTAINED IN THIS DOCUMENT IS PROVIDED "AS IS," AND IS SUBJECT TO BEING CHANGED, WITHOUT NOTICE, IN FUTURE EDITIONS. FUR-THER, TO THE MAXIMUM EXTENT PERMITTED BY APPLICABLE LAW, AGILENT DISCLAIMS ALL WARRANTIES, EITHER EXPRESS OR IMPLIED WITH REGARD TO THIS MANUAL AND ANY INFORMATION CONTAINED HEREIN, INCLUDING BUT NOT LIMITED TO THE IMPLIED WARRANTIES OF MERCHANTABILITY AND FIT-NESS FOR A PARTICULAR PURPOSE. AGILENT SHALL NOT BE LIABLE FOR ERRORS OR FOR INCIDENTAL OR CONSEQUENTIAL DAMAGES IN CONNECTION WITH THE FURNISHING, USE, OR PERFORMANCE OF THIS DOCUMENT OR ANY INFORMATION CONTAINED HEREIN. SHOULD AGILENT AND THE USER HAVE A SEPARATE WRITTEN AGREEMENT WITH WARRANTY TERMS COVERING THE MATERIAL IN THIS DOCUMENT THAT CONFLICT WITH THESE TERMS, THE WAR-RANTY TERMS IN THE SEPARATE AGREEMENT WILL CONTROL.DFARS/Restricted Rights NoticeIf software is for use in the performance of a U.S. Government prime contract or subcontract, Software is delivered and licensed as “Commercial computer software” as defined in DFAR 252.227-7014 (June 1995), or as a “commercial item” as defined in FAR 2.101(a) or as “Restricted computer software” as defined in FAR 52.227-19 (June 1987) or any equivalent agency regulation or contract clause. Use, duplication or disclosure of Software is subject to Agilent Technologies’ standard commercial license terms, andnon-DOD Departments and Agencies of the U.S. Government will receive no greater than Restricted Rights as defined in FAR 52.227-19(c)(1-2) (June 1987). U.S. Government users will receive no greater than Limited Rights as defined in FAR 52.227-14 (June 1987) or DFAR 252.227-7015 (b)(2) (November 1995), as applicable in any technical data.Printing Copies of Documentation from the WebTo print copies of documentation from the Web, download the PDF file from the Agilent web site:•Go to .•Enter the document’s part number (located on the title page) in the Quick Search box.•Click GO.•Click on the hyperlink for the document.•Click the printer icon located in the tool bar.Contacting AgilentThis information supersedes all prior HP contact information. Online assistance:/find/assistAmericasBrazil(tel) (+55) 11 3351 7012 (fax) (+55) 11 3351 7024Canada(tel) +1 877 894 4414(alt) +1 303 662 3369(fax) +1 800 746 4866Mexico(tel)180****2440(fax)180****4222United States(tel)800 829 4444(alt)(+1) 303 662 3998(fax)800 829 4433 Asia Pacific and JapanAustralia(tel) 1 800 802 540 (fax) 1 800 681 776 (fax) 1 800 225 539China(tel) 800 810 0508(fax) 800 810 0507Hong Kong(tel) 800 933 229(fax) 800 900 701India(tel) 1600 112 626(fax) 1600 113 040Japan (Bench) (tel) 0120 421 345 (alt) (+81) 426 56 7832 (fax) 0120 01 2144Japan (On-Site)(tel) 0120 421 345(alt) (+81) 426 56 7832(fax) 0120 012 114Singapore(tel)180****0880(fax) (+65) 6755 1214South Korea(tel) 080 778 0011(fax) 080 778 0013Taiwan(tel) 0800 047 669 (fax) 0800 047 667 (fax) 886 3492 0779Thailand(tel) 1 800 2758 5822(fax) 1 800 656 336Malaysia(tel) 1800 880 399(fax) 1800 801 054EuropeAustria(tel) 0820 87 44 11* (fax) 0820 87 44 22Belgium(tel) (+32) (0)2 404 9340(fax) (+32) (0)2 404 9395Denmark(tel) (+45) 7013 1515(fax) (+45) 7013 1555Finland(tel) (+358) 10 855 2100(fax) (+358) (0) 10 855 2923France(tel) 0825 010 700* (fax) 0825 010 701*Germany(tel) 01805 24 6333*(fax) 01805 24 6336*Ireland(tel) (+353) (0)1 890 924 204(fax)(+353) (0)1 890 924 024Israel(tel) (+972) 3 9288 504(alt) (+972) 3 9288 544(fax) (+972) 3 9288 520Italy(tel) (+39) (0)2 9260 8484 (fax) (+39) (0)2 9544 1175Luxemburg(tel) (+32) (0)2 404 9340(fax) (+32) (0)2 404 9395Netherlands(tel) (+31) (0)20 547 2111(fax) (+31) (0)20 547 2190Russia(tel) (+7) 095 797 3963(alt) (+7) 095 797 3900(fax) (+7) 095 797 3902Spain(tel) (+34) 91 631 3300 (fax) (+34) 91 631 3301Sweden(tel) 0200 88 22 55*(alt) (+46) (0)8 5064 8686(fax) 020 120 2266*Switzerland (French)(tel) 0800 80 5353 opt. 2*(fax) (+41) (0)22 567 5313Switzerland (German)(tel) 0800 80 5353 opt. 1*(fax) (+41) (0)1 272 7373Switzerland (Italian) (tel) 0800 80 5353 opt. 3* (fax) (+41) (0)22 567 5314United Kingdom(tel) (+44) (0)7004 666666 (fax) (+44) (0)7004 444555(tel) = primary telephone number; (alt) = alternate telephone number; (fax) = FAX number; * = in country number 5/6/05。
51单片机命名规则

51单片机命名规则89C518代表8位单片机9代表falsh存储器,此位置为0代表无rom,7代表eprom存储器c代表CMOS工艺,此位置为S代表ISP编程方式1代表片内程序存储器容量,容量大小对应为该位数字*4KB89C52:8KB容量at89s51_&_stc89c51命名规则本文介绍了最常见的两种厂家的单片机的命名规则.]以后见了stc和atmel的单片机看看型号就知道,什么配置了.先说ATMEL公司的AT系列单片机89系列单片机的型号编码由三个部分组成,它们是前缀、型号和后缀。
格式如下:AT89C XXXXXXXX其中,AT是前缀,89CXXXX是型号,XXXX是后缀。
下面分别对这三个部分进行说明,并且对其中有关参数的表示和意义作相应的解释。
(l)前缀由字母“AT”组成,表示该器件是ATMEL公司的产品。
(2)型号由“89CXXXX”或“89LVXXXX”或“89SXXXX”等表示。
`“89CXXXX”中,9是表示内部含Flash存储器,C表示为CMOS产品。
“89LVXXXX”中,LV表示低压产品。
“89SXXXX”中,S表示含有串行下载Flash存储器。
在这个部分的“XXXX”表示器件型号数,如51、1051、8252等。
(3)后缀由“XXXX”四个参数组成,每个参数的表示和意义不同。
在型号与后缀部分有“—”号隔开。
后缀中的第一个参数X用于表示速度,它的意义如下:X=12,表示速度为12 MHz。
X=20,表示速度为20 MHz。
X=16,表示速度为16 MHz。
X=24,表示速度为24 MHz。
后缀中的第二个参数X用于表示封装,它的意义如下:X=D,表示陶瓷封装。
X=Q,表示PQFP封装。
’【X=J,表示PLCC封装。
X=A,表示TQFP封装。
X=P,表示塑料双列直插DIP封装。
X=W,表示裸芯片。
X=S,表示SOIC封装。
后缀中第三个参数X用于表示温度范围,它的意义如下:X=C,表示商业用产品,温度范围为0~十70℃。
MB85RS256

CS
SCK
SI
7
6
5
4
3
2
1
0
MSB
SPI Mode 0
LSB
CS
SCK
SI
7
6
5
4
3
2
1
0
MSB
LSB
SPI Mode 3
4
DS05-13105-3E
MB85RS256
■ SERIAL PERIPHERAL INTERFACE (SPI)
MB85RS256 works as a slave of SPI. More than 2 devices can be connected by using microcontroller equipped with SPI port. By using a microcontroller not equipped with SPI port, SI and SO can be bus connected to use.
BP0
1
WEL
0
0
Function
Status Register Write Protect This is a bit composed of nonvolatile memories (FRAM). WPEN is related to WP input to protect writing to a status register (refer to “■ WRITING PROTECT”). Writing with the WRSR command and reading with the RDSR command are possible.
Write Enable Latch This indicates FRAM memory and status register are writable. The WREN command is for setting, and the WRDI command is for resetting. With the RDSR command, reading is possible but writing is not possible with the WRSR command. WEL is reset after the following operations.
OldEnglishFlashCards1
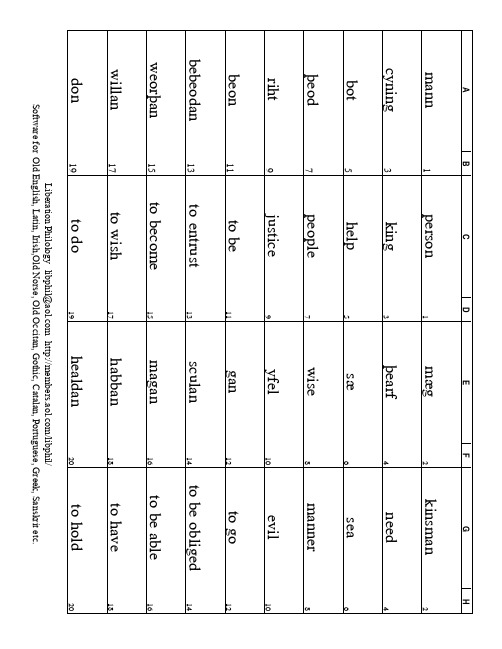
A
B
C
D
E
F
G
H
fultum
161
help
161
cniht
162
boy
162
bryne
163
burning
163
f¾r
164
journey
164
spr¾c
165
speech
165
geard
166 enclosure
166
¹eaw
167
custom
167
feond
168
enemy
168
beam
169
119
bryd
120
bride
120
Liberation Philology libphil@ /libphil/ Software for Old English, Latin, Irish,Old Norse, Old Occitan, Gothic, Catalan, Portuguese, Greek, Sanskrit etc.
A
B
C
D
E
F
G
H
agan
41
to own
41
cuman
42
to come
42
witan
43 to know
43 understondan 44 to perceive
44
gelimpan
45 to happen
45
unnan
46 to allow
46
¹olian
47 to suffer
47
l¾ran
A
MB85R1001A资料

• Package
: 48-pin plastic TSOP (1)
Copyright©2011 FUJITSU SEMICONDUCTOR LIMITED All rights reserved 2011.7
MB85R1001A
■ PIN ASSIGNMENTS
A11 1 A9 2 NC 3 A8 4
■ PIN DESCRIPTIONS
Pin Number 1, 2, 4, 5, 8, 18 to 26, 28, 29, 45
33 to 35, 38 to 42 44 7 6 48
10, 16, 37
13, 27, 46
3, 9, 11, 12, 14, 15, 17, 30 to 32, 36, 43, 47
A13 5 WE 6 CE2 7 A15 8 NC 9 VDD 10 NC 11 NC 12 VSS 13 NC 14 NC 15 VDD 16 NC 17 A16 18 A14 19 A12 20 A7 21 A6 22 A5 23 A4 24
(TOP VIEW) (FPT-48P-M48)
48 OE 47 NC 46 VSS 45 A10 44 CE1 43 NC 42 I/O8 41 I/O7 40 I/O6 39 I/O5 38 I/O4 37 VDD 36 NC 35 I/O3 34 I/O2 33 I/O1 32 NC 31 NC 30 NC 29 A0 28 A1 27 VSS 26 A2 25 A3
Pin Name A0 to A16 I/O1 to I/O8
CE1 CE2 WE OE VDD
VSS
NC
Functional Description Address Input pins Data Input/Output pins Chip Enable 1 Input pin Chip Enable 2 Input pin Write Enable Input pin Output Enable Input pin Supply Voltage pins Connect all three pins to the power supply. Ground pins Connect all three pins to ground.