吹塑薄膜时出现大量的晶点解决办法
降解吹膜袋疑难6问:膜泡不稳定、褶皱、晶点、偏厚、跑卷……

降解吹膜袋疑难6问:膜泡不稳定、褶皱、晶点、偏厚、跑卷……一、吹膜时膜泡不稳定膜泡不稳定会导致薄膜厚度和宽度波动、擦痕等问题,不稳定如拉伸共振(沙漏状)、螺旋不稳定(蛇形)以及膜泡下垂、撕裂、颤动等。
膜泡不稳定与原料挤出温度、材料自身特性和吹膜气流稳定性有密切关系。
1、挤出温度挤出温度过高,会造成材料熔融流动性太大,粘度过小,容易产生波动。
挤出温度过低,会使得吹膜料的出料量太少。
2、材料自身特性材料自身特性会影响材料的熔融流动性,有两个衡量指数。
溶体强度熔体强度是影响聚合物可发泡性的重要物性参数。
是指聚合物在熔融状态下支持自身质量的能力。
一般来说,熔体强度高的产品比较适合挤出,熔体强度低的产品比较适合注塑。
熔融指数熔流指数,全称熔液流动指数,或熔体流动指数、熔融指数,是一种表示塑胶材料加工时的流动性的数值。
它是美国量测标准协会(ASTM)根据美国杜邦公司(DuPont)惯用的鉴定塑料特性的方法制定而成,其测试方法是:先让塑料粒在一定时间(10分钟)内、一定温度及压力(各种材料标准不同)下,熔化成塑料流体,然后通过一直径为2.1mm圆管所流出的克(g)数。
其值越大,表示该塑胶材料的加工流动性越佳,反之则越差。
熔体强度和熔指在数值上是成相反方向的,也就是说熔体强度越高,熔指越低。
熔体强度不光和分子量有关,和分子中的支链数量和长度关系很大,一般说来分子中的支链越多、长度越长,材料的熔体强度越高,稳定性强,而流动性弱。
想要增加材料的分子链,可使用扩链剂。
3、吹膜气流稳定性吹膜气流的稳定性直接影响了膜泡的稳定性,需要控制冷却风环保持稳定,另外,外来较强气流也会对吹膜有较大干扰。
二、熔体压力或熔体温度过高熔体压力过高会引起漏料风险。
可以考虑如下方法:提高设定温度,增加熔体的流动性。
使用宽模口间隙,降低模头压力。
使用目数较少的滤网。
降低挤出量。
熔体温度过高会导致生物降解材料降解,导致氧化交联,形成晶点。
同时影响膜泡的稳定性,导致厚薄偏差较大,影响产量。
塑料制品黑点-晶点分析报告
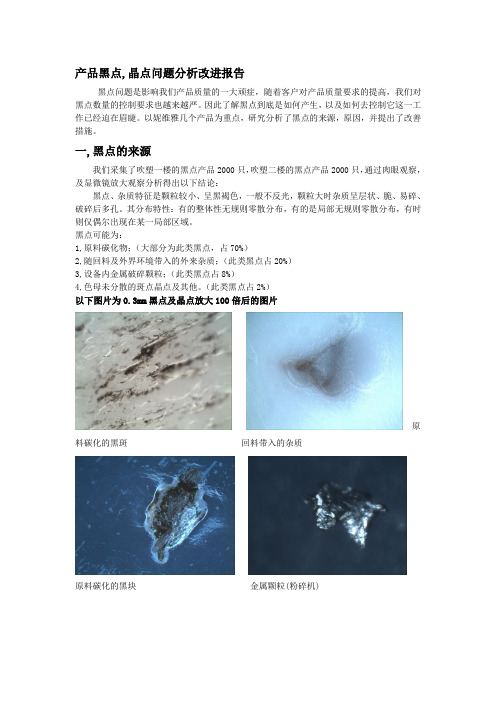
产品黑点,晶点问题分析改进报告黑点问题是影响我们产品质量的一大顽症,随着客户对产品质量要求的提高,我们对黑点数量的控制要求也越来越严。
因此了解黑点到底是如何产生,以及如何去控制它这一工作已经迫在眉睫。
以妮维雅几个产品为重点,研究分析了黑点的来源,原因,并提出了改善措施。
一,黑点的来源我们采集了吹塑一楼的黑点产品2000只,吹塑二楼的黑点产品2000只,通过肉眼观察,及显微镜放大观察分析得出以下结论:黑点、杂质特征是颗粒较小、呈黑褐色,一般不反光,颗粒大时杂质呈层状、脆、易碎、破碎后多孔。
其分布特性:有的整体性无规则零散分布,有的是局部无规则零散分布,有时则仅偶尔出现在某一局部区域。
黑点可能为:1,原料碳化物;(大部分为此类黑点,占70%)2,随回料及外界环境带入的外来杂质;(此类黑点占20%)3,设备内金属破碎颗粒;(此类黑点占8%)4,色母未分散的斑点晶点及其他。
(此类黑点占2%)以下图片为0.3mm黑点及晶点放大100倍后的图片原料碳化的黑斑回料带入的杂质原料碳化的黑块金属颗粒(粉碎机)色粉积垢(流道) 原料碳化物色粉积垢(流道) 金属颗粒(粉碎机)流道色粉积垢(流道处)珠光色母团聚(晶点)原料碳化二、黑点的成因从影响质量的五大因素(人、机、料、法、环)入手,分析了黑点成因:人人这一因素是最重要的,也是最难控制的。
车间由主管到一线的员工是过程的直接控制者,也是对过程最了解的人,积极主动的一起去发现问题,解决问题,黑点也能有效控制。
机机就是设备,很多黑点问题都是来源于设备上的缺陷:由于设备老化,且保养不当,常会出现设备故障,一旦出现设备故障,就要停机处理,这样一来可能造成螺筒内物料炭化。
由于螺杆或料筒的长期使用造成间隙过大使熔料卡入而屯积,经受长时间固定加热造成分解,产生碳化物料。
设备套件磨损或里面有金属异物,在设备强力剪切下碎裂产生黑点。
塑料在料筒内受到高热而交联焦化,在几乎维持原来颗粒形状情形下,难以熔融,被螺杆压破碎后夹带进入制件。
吹塑薄膜成型故障的产生原因及排除方法

吹塑薄膜成型故障的产生原因及排除方法一、吹塑薄膜成型常见故障的排查1、引膜困难故障分析及排除方法:(1)机头温度控制不当。
当机头温度太高或太低时,都会引起牵引困难,应适当调整机头温度。
(2)口模出料不均匀。
应调整口模间隙,使周边间隙均匀。
同时,适当调节机头连接器温度,使之与机身温度相协调。
(3)熔料中含有焦料杂质。
应净化原料及清理机头和螺杆。
(4)挤出工艺条件控制不当。
应适当调整工艺条件。
几种常用塑料吹塑薄膜的挤出工艺条件如表3-1所示。
2、泡管歪斜故障分析及排除方法:(1)机身及口模温度太高。
应适当降低。
(2)机头连接器温度太高。
应适当降低。
(3)口模出料不均匀,薄膜厚薄不均。
应适当调整口模间隙及机头连接器温度。
表3-1 几种常用塑料吹塑薄膜的挤出工艺条件故障分析及排除方法:(1)泡管呈规律性的葫芦形是由于牵引辊的夹紧力太小,或牵引辊的转速受到机械传动阻力规律性变化的影响所致。
对此,应适当增加牵引辊的夹紧力,检修牵引装置的机械传动部分,使牵引辊的转速平稳。
(2)泡管呈无规律的葫芦形是由于牵引速度不稳定,以及冷却风环的风压太大。
对此,应调整牵引速度,使其运行稳定;风环的风压应适当降低。
4、泡管摆动故障分析及排除方法:(1)熔料温度太高。
应适当降低机身及机头温度。
(2)冷却风环的冷却效率太低。
应提高冷却系统的冷却效率,可适当加大风环的风压和风量。
(3)泡管与人字夹板的摩擦力太大。
应适当加大人字板夹角,减小泡管与夹板的接触面积。
(4)机头温度太低,出料困难,膜泡跳动。
应适当提高机头温度及增加螺杆转速。
5、薄膜表面发花故障分析及排除方法:(1)机身或机头温度偏低,熔料塑化不良。
应适当提高机身或机头温度。
(2)螺杆转速太快。
应适当减慢。
(3)螺杆温度太高或太低。
应通过调整螺杆内冷却介质的流量,将螺杆温度控制在适宜的温度范围内。
6、挂料线明显故障分析及排除方法:(1)口模出料口处有分解物料或杂质粘附。
应用铜铲将杂质或焦料刮除,严重时应顶出芯棒进行清理。
吹膜不正常现象原因及解决方法

不正常现象
主要原因
解决方法
泡管倾斜
1.机身、口模温度过高
2.连接器温度过高
3.薄膜厚度不均匀
1.适当降低机身、口模温度
2.适当降低连接器温度
3.调整薄膜厚度
透明度差
1.机身或机头温度过低;
2.冷却不够
1.提高机身或机头温度
2.加强冷却
薄膜厚度不均匀
1.机头设计不合理
2.芯棒“偏中”变形
1.干燥原料
薄膜不稳定
1.冻结线过高
2.四周环境气周环境
横向丝纹
1.薄膜横向取向度太低
2.薄膜厚度不均匀
3.口模及稳泡器表面有伤痕,刮伤薄膜表面
1.应适当加大吹胀比
2.应调整薄膜厚度
3.应修磨口模及稳泡器,使口模及稳泡器表面具有较高光洁度
厚薄不均
1.口模间隙调整不当
7.卷取辊张力不稳定
1.校正机头
2.调整薄膜厚度
3.调整冷却装置和降低生产速度
4.对准中心线
5.减少人字板夹角
6.调解牵引辊
7.调节卷取辊磨擦粒大小
接缝线明显
1.机头或连接器温度过高
2.机头设计不合理
3.芯棒分流处物料分解
1.适当降低相应温度
2.修改机头工艺参数
3.修改芯棒分流处结构
有气泡
1.原料潮湿
3.机头四周温度不均
4.吹胀比太大
5.四周冷却不均匀
6.压缩空气不稳定
1.修改机头工艺参数
2.更换芯棒
3.检修机头加热圈
4.减小吹胀比
5.调整冷却介质流量及风环间隙
6.检修空气压缩机
薄膜皱折
1.机头安装不平
聚乙烯(LDPE)吹塑薄膜生产过程中的问题和解决方法

聚乙烯(LDPE)吹塑薄膜生产过程中的问题和解决方法大多数热塑性塑料都可以用吹塑法来生产吹塑薄膜,吹塑薄膜是将塑料挤成薄管,然后趁热用压缩空气将塑料吹胀,再经冷却定型后而得到的筒状薄膜制品,这种薄膜的性能处于定向膜同流延膜之间:强度比流延膜好,热封性比流延膜差。
吹塑法生产的薄膜品种有很多,比如低密度聚乙烯(LDPE)、聚丙烯(PP)、高密度聚乙烯(HDPE)、尼龙(PA)、乙烯一乙酸乙烯共聚物(EVA)等,这里我们就对常用的低密度聚乙烯(LDPE)薄膜的吹塑生产工艺及其常见故障进行简单的介绍。
聚乙烯吹塑薄膜材料的选择1.选用的原料应当是用吹膜级的聚乙烯树脂粒子,含有适量的爽滑剂,保证薄膜的开口性。
2.树脂粒子的熔融指数(MI)不能太大,熔融指数(MI)太大,则熔融树脂的粘度太小,加工范围窄,加工条件难以控制,树脂的成膜性差,不容易加工成膜;此外,熔融指数(MI)太大,聚合物相对分子量分布太窄,薄膜的强度较差。
因此,应当选用熔融指数(MI)较小,且相对分子量分布较宽的树脂原料,这样既能满足薄膜的性能要求,又能保证树脂的加工特性。
吹塑聚乙烯薄膜一般选用熔融指数(MI)在2~6g/10min范围之间的聚乙烯原料。
吹塑工艺控制要点吹塑薄膜工艺流程大致如下:料斗上料一物料塑化挤出→吹胀牵引→风环冷却→人字夹板→牵引辊牵引→电晕处理→薄膜收卷但是,值得指出的是,吹塑薄膜的性能跟生产工艺参数有着很大的关系,因此,在吹膜过程中,必须要加强对工艺参数的控制,规范工艺操作,保证生产的顺利进行,并获得高质量的薄膜产品。
在聚乙烯吹塑薄膜生产过程中,主要是做好以下几项工艺参数的控制:1.挤出机温度吹塑低密度聚乙烯(LDPE)薄膜时,挤出温度一般控制在160℃~170℃之间,且必须保证机头温度均匀,挤出温度过高,树脂容易分解,且薄膜发脆,尤其使纵向拉伸强度显著下降;温度过低,则树脂塑化不良,不能圆滑地进行膨胀拉伸,薄膜的拉伸强度较低,且表面的光泽性和透明度差,甚至出现像木材年轮般的花纹以及未熔化的晶核(鱼眼)。
如何解决塑料薄膜产生的晶点?
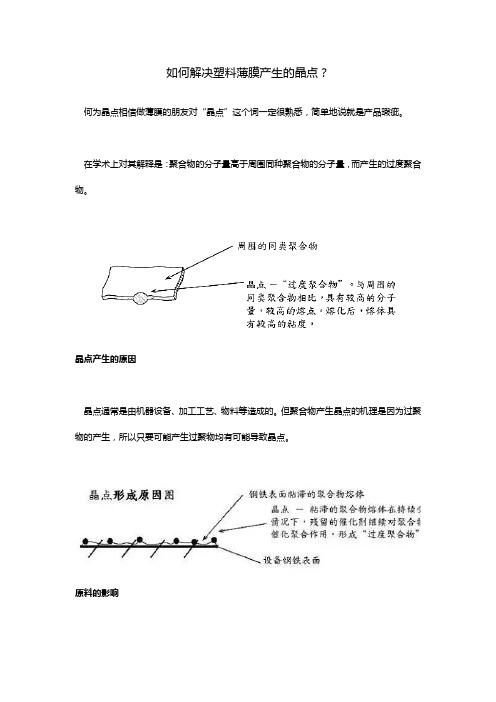
如何解决塑料薄膜产生的晶点?何为晶点相信做薄膜的朋友对“晶点”这个词一定很熟悉,简单地说就是产品瑕疵。
在学术上对其解释是:聚合物的分子量高于周围同种聚合物的分子量,而产生的过度聚合物。
晶点产生的原因晶点通常是由机器设备、加工工艺、物料等造成的。
但聚合物产生晶点的机理是因为过聚物的产生,所以只要可能产生过聚物均有可能导致晶点。
原料的影响1.说是原料的影响其实是指原料的残留催化剂影响。
聚合物生产时会有些催化剂残留,在成型加工过程中,含有催化剂的聚合物熔体粘滞于生产设备表面,在高温下,残留的催化剂对聚合物继续进行催化聚合作用,因此会形成过度聚合物。
不同树脂厂家的聚合设备及工艺不同,对残留的催化剂处理纯度有差异,其对聚合物在成膜中产生晶点有不同的影响,例如聚合物中残留的催化剂含量低,设备结构好,原料本身所含的晶点就少。
2.聚合物中氧的影响这主要是加工温度较高时,氧会使聚合物氧化产生自由基吸附在口模壁,自由基作为活性中心引发其他聚合物分子链反应,在此处形成高浓度的不稳定聚合物,在高温下变成杂色点。
加入一定数量的抗氧剂,有防止氧对晶点的产生作用。
3.加工工艺、设备的影响加工工艺主要是温度控制等影响,原料长时间受热、过度聚合、降解会导致晶点产生。
其实很多时候是设备导致的,例如:1.吹膜机模头部位设计欠佳、存在死角,造成少量原料长时间受热、过度聚合、降解;2.吹模机械的长径比配置、模头设计欠佳等;3.螺杆上面或螺筒内壁上面由于长期的积累,产生一些炭化的东西,而这些炭化的东西可以作为凝胶点,不断的吸附更多的杂质到它上面,同时也不断的沾到薄膜上面造成所谓的晶点。
总而言之,成型设备定期清洗有利于减少晶点产生。
4.颜填料、色母粒等影响现在薄膜生产习惯添加色母粒,色母粒的分散欠佳会导致晶点等不良缺陷,例如色母中选用的颜料表面处理不稳定,在色母加工过程中“团聚”,形成“粉点”;色母的载体树脂与成膜原料相容性欠佳。
减少或消除晶点的方法了解以上晶点的形成原因,便可很容易对其控制,为您列出以下四种方法:1、原料选择纯化好的树脂,减少催化剂的影响;2、薄膜成型工艺中增加滤网细度,勤换滤网(尤其是陈旧设备),有利于晶点减少;3、抗氧剂等适量添加;4、在生产过程中添加钢铁表面润滑剂,减少聚合物熔体粘滞在设备表面。
吹膜出现严重晶点和熔化不均匀现象
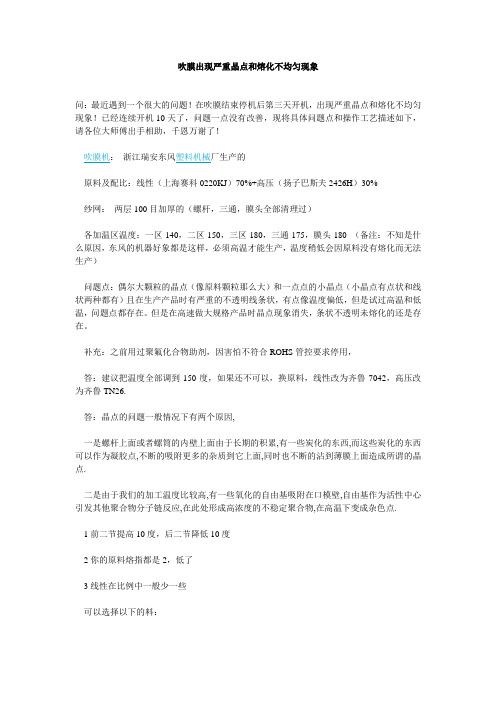
吹膜出现严重晶点和熔化不均匀现象问:最近遇到一个很大的问题!在吹膜结束停机后第三天开机,出现严重晶点和熔化不均匀现象!已经连续开机10天了,问题一点没有改善,现将具体问题点和操作工艺描述如下,请各位大师傅出手相助,千恩万谢了!吹膜机:浙江瑞安东风塑料机械厂生产的原料及配比:线性(上海赛科0220KJ)70%+高压(扬子巴斯夫2426H)30%纱网:两层100目加厚的(螺杆,三通,膜头全部清理过)各加温区温度:一区140,二区150,三区180,三通175,膜头180 (备注:不知是什么原因,东风的机器好象都是这样,必须高温才能生产,温度稍低会因原料没有熔化而无法生产)问题点:偶尔大颗粒的晶点(像原料颗粒那么大)和一点点的小晶点(小晶点有点状和线状两种都有)且在生产产品时有严重的不透明线条状,有点像温度偏低,但是试过高温和低温,问题点都存在。
但是在高速做大规格产品时晶点现象消失,条状不透明未熔化的还是存在。
补充:之前用过聚氟化合物助剂,因害怕不符合ROHS管控要求停用,答:建议把温度全部调到150度,如果还不可以,换原料,线性改为齐鲁7042,高压改为齐鲁TN26.答:晶点的问题一般情况下有两个原因,一是螺杆上面或者螺筒的内壁上面由于长期的积累,有一些炭化的东西,而这些炭化的东西可以作为凝胶点,不断的吸附更多的杂质到它上面,同时也不断的沾到薄膜上面造成所谓的晶点.二是由于我们的加工温度比较高,有一些氧化的自由基吸附在口模壁,自由基作为活性中心引发其他聚合物分子链反应,在此处形成高浓度的不稳定聚合物,在高温下变成杂色点.1前二节提高10度,后二节降低10度2你的原料熔指都是2,低了3线性在比例中一般少一些可以选择以下的料:LLDPE7144熔指为17LDPE:1F7B为7都不错的答:这个问题我的客户也经常出现,是螺杆上面或者螺筒的内壁上面由于长期的积累,有一些炭化的东西,而这些炭化的东西可以作为凝胶点,不断的吸附更多的杂质到它上面,同时也不断的沾到薄膜上面造成所谓的晶点.我可以给你寄一些我们的母料,可以解决你的问题。
pe薄膜晶点的形成与解决方法
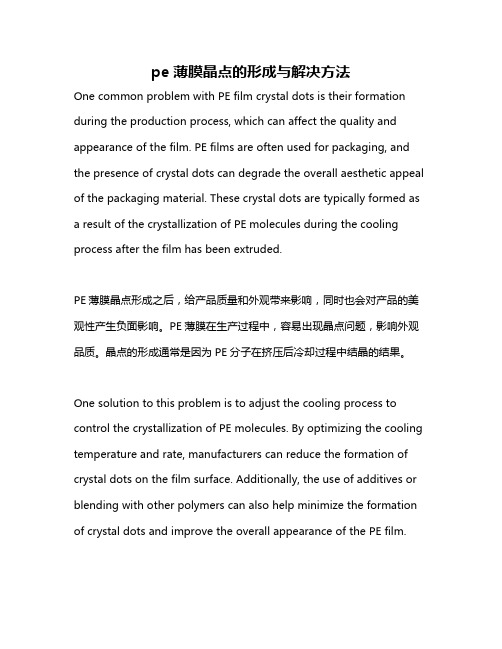
pe薄膜晶点的形成与解决方法One common problem with PE film crystal dots is their formation during the production process, which can affect the quality and appearance of the film. PE films are often used for packaging, and the presence of crystal dots can degrade the overall aesthetic appeal of the packaging material. These crystal dots are typically formed as a result of the crystallization of PE molecules during the cooling process after the film has been extruded.PE薄膜晶点形成之后,给产品质量和外观带来影响,同时也会对产品的美观性产生负面影响。
PE薄膜在生产过程中,容易出现晶点问题,影响外观品质。
晶点的形成通常是因为PE分子在挤压后冷却过程中结晶的结果。
One solution to this problem is to adjust the cooling process to control the crystallization of PE molecules. By optimizing the cooling temperature and rate, manufacturers can reduce the formation of crystal dots on the film surface. Additionally, the use of additives or blending with other polymers can also help minimize the formation of crystal dots and improve the overall appearance of the PE film.解决方法之一是调整冷却过程来控制PE分子的结晶。
吹膜异常问题及处理方法

吹膜异常问题及处理⽅法⾼密度聚⼄烯吹塑薄膜常见的异常现象、产⽣原因及其解决办法。
1、开始吹模时薄膜损失量太多。
产⽣原因:1、稳泡器尺⼨不合适。
2、稳泡器过冷。
解决办法:1、更换尺⼨适宜的稳泡器。
2、需要预热或绕上毯类物。
2、薄膜厚度不均。
产⽣原因:1、⼝膜间隙不均。
2、稳泡器未处垂直状态。
3、吹塑空⽓量不均匀。
4、机头温度不均。
稳泡器尺⼨不适当。
解决办法:1、调整⼝模间隙。
2、很好地系紧,如⽀持棒弯曲需进⾏更换。
3、检查空冷环的⽔平管有⽆偏处。
4、检查加热器是否短路。
5、更换尺⼨适宜的稳泡器。
3、膜泡不稳定。
产⽣原因:1、冷固线过⾼。
2、冷却空⽓乱流。
解决办法:1、调整⾄适当⾼度(勿下降太多)。
2、检查⿎风机、管及外部冷却装置。
4、膜泡断裂。
产⽣原因:1、混⼊异物。
2、薄膜厚度不均。
3、内稳泡器粗⼤或带有斜度。
4、成型温度底。
5、牵引速度快。
解决办法:1、更换滤⽹,清理机头。
2、参照序号2。
3、换适宜尺⼨的稳泡器,⾼速时使⽤直筒型。
4、适当提⾼成型的温度。
5、降低牵引速度。
5、薄膜有纵向裂纹。
产⽣原因:1、横向取向度低。
2、厚度不均。
3、膜⾯存在的伤痕。
解决办法:1、缩⼩⼝模直径(即提⾼吹胀⽐)提⾼冷固线如稳泡器直径过⼤予以更换。
2、参照序号2。
3、检查⼝模、稳泡器有⽆损伤。
6、薄膜强度不够。
产⽣原因:1、吹胀⽐不当。
2、冷固线偏低。
3、牵引速度慢。
解决办法:1、将吹胀⽐调⾄3~5。
2、降低冷却风。
3、增加牵引速度。
7、薄膜中央起皱。
产⽣原因:1、冷固线⾄夹辊距离太长。
2、稳定板张开⾓⼩。
解决办法:1、升⾼冷固线或降低夹棍。
2、调⼤稳定板开⾓。
8、薄膜边缘松弛。
产⽣原因:1、冷固线⾄夹辊距离短。
解决办法:降低冷固线或升⾼夹辊。
分切、制袋⼯序中常见质量问题及解决⽅法在软包装材料(包括单质薄膜与复合膜)的⽣产⼯序中,分切作为承上启下的“特殊”⼯序,对内部影响下道制袋⼯序的质量及正品率,对外部顾客提供事先约定的、不同规格的卷材产品交付顾客使⽤,分切的质量就显得特别重要。
聚丙烯PP吹塑薄膜成型故障的处理

聚丙烯PP 吹塑薄膜成型故障的处理一、膜面局部出现白斑1。
由模头挤出的膜管未接触到水环冷却水,就会出现白斑。
应校准水环的水平度,同时将水环中心和模头中心的同心度校准在同一位置。
最后校准水环四周的溢水量保持平衡。
2。
水环内壁有污染物。
水环长时间不用,空气中的油脂或灰尘会黏附在水环内壁,造成水流不均。
应该用洗涤剂进行清洗,保持水流均衡。
3。
膜管内充气不足。
膜泡内充气不足,会使膜管脱离水环,需要及时补气,保证膜管和水环的接触良好。
4。
薄膜厚薄不均。
膜管最薄的部位膨胀加剧,经骤冷后形成白斑。
应及时调整模口间隙,使薄膜厚薄均匀。
二、合流纹:合流纹是薄膜成型后,在薄膜表面出现深浅不一的竖向条纹,对薄膜表面的光洁度产生较大影响。
原因是:1。
机头设计不合理,出现规律性的合流纹。
一般是由于内螺旋体设计或加工不到位,应改进或重置模头。
2。
模头局部损伤,总在薄膜的同一个位置出现合流纹,应对模头进行整修。
3。
模头或机身温度太高,合流纹总出现在某一个部位,调整温度(适当降低),使模头温度控制在195--210度之间为好。
4。
模具里有杂物,特别是模口里存有异物,应及时清理。
5。
模口表面有结痂,这是模口长期不清理或清理不到位所致,残余原料在长期高温下焦化积碳,造成模口粗糙,影响薄膜成形,需及时清理到位。
三、横向厚度不均匀:薄膜圆筒一周测量厚薄不一致称为横向厚度不均匀,原因是:1)模头模口间隙不一致,需要及时调整模口间隙。
2)模具四周温度不一致,电加热圈的规格和加工精度(绕制加热圈电热丝间隔距离误差太大),加热圈接口安装分布不匀,冷却风环吹制的冷却风是否影响模口温度,或加热圈部分损坏。
逐一检查排除故障。
3)冷却水环安装位置不当,水环出水量不均匀,应调整水环位置和水流,确保一致。
4)冷却风环位置不当或出风量不一致,应调整风环位置和确保四周出风量完全一致。
5)模头出料口有异物,应及时拆卸清理模具。
6)混合原料配置不当,添加辅助原料的熔融指数差异太大,流动性不一致。
浅析TPU薄膜晶点的影响因素及解决办法
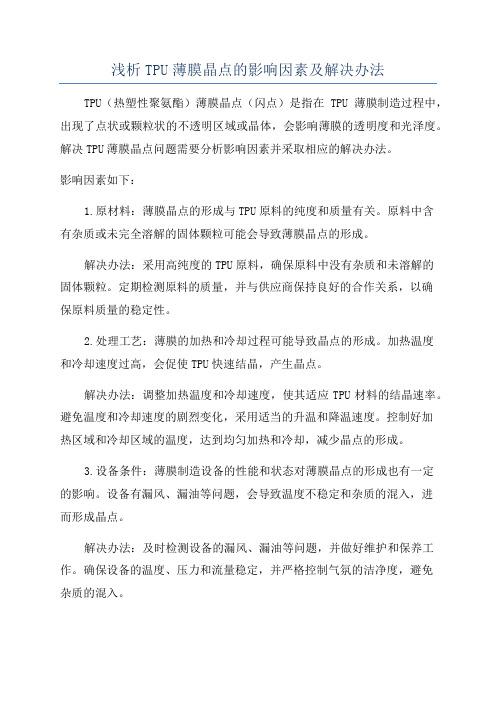
浅析TPU薄膜晶点的影响因素及解决办法TPU(热塑性聚氨酯)薄膜晶点(闪点)是指在TPU薄膜制造过程中,出现了点状或颗粒状的不透明区域或晶体,会影响薄膜的透明度和光泽度。
解决TPU薄膜晶点问题需要分析影响因素并采取相应的解决办法。
影响因素如下:1.原材料:薄膜晶点的形成与TPU原料的纯度和质量有关。
原料中含有杂质或未完全溶解的固体颗粒可能会导致薄膜晶点的形成。
解决办法:采用高纯度的TPU原料,确保原料中没有杂质和未溶解的固体颗粒。
定期检测原料的质量,并与供应商保持良好的合作关系,以确保原料质量的稳定性。
2.处理工艺:薄膜的加热和冷却过程可能导致晶点的形成。
加热温度和冷却速度过高,会促使TPU快速结晶,产生晶点。
解决办法:调整加热温度和冷却速度,使其适应TPU材料的结晶速率。
避免温度和冷却速度的剧烈变化,采用适当的升温和降温速度。
控制好加热区域和冷却区域的温度,达到均匀加热和冷却,减少晶点的形成。
3.设备条件:薄膜制造设备的性能和状态对薄膜晶点的形成也有一定的影响。
设备有漏风、漏油等问题,会导致温度不稳定和杂质的混入,进而形成晶点。
解决办法:及时检测设备的漏风、漏油等问题,并做好维护和保养工作。
确保设备的温度、压力和流量稳定,并严格控制气氛的洁净度,避免杂质的混入。
4.外界环境:外界环境的温度和湿度也会对TPU薄膜晶点的形成产生影响。
高温和高湿度的环境会促使水分的吸收和TPU的结晶,形成晶点。
解决办法:保持生产车间的温度和湿度在适宜的范围内。
加强车间的通风和湿度控制,避免高温和高湿度的环境对薄膜质量的影响。
总结起来,解决TPU薄膜晶点问题需要从原材料、处理工艺、设备条件和外界环境等多个方面综合考虑。
采取适当的措施保证原料的纯度和质量、调整处理工艺参数以及做好设备维护和环境控制工作,可以有效降低TPU薄膜晶点的发生率,提高产品的质量和性能。
PE吹膜晶点怎么办

PE吹膜晶点怎么办关于晶点的形成原因及消除方法晶点是塑料袋工业普遍存在的技术问题。
对透明塑料袋来说,晶点明显影响透明塑料袋的外观。
对要求印刷品质较高的塑料袋来说,晶点是造成印刷“白点”的主要原因。
特别是大面子的塑料袋印刷,晶点所造成的“白点”废次品,是塑料袋的工业生产工艺上的一项较大比例的损耗。
因此,控制晶点的产生,消除晶点的成因,是提高塑料袋工业技术水平的重要工艺环节。
(1)晶点晶点实际上是“过度聚合物”,即“晶点”部位聚合物的分子量高于周围同种聚合物的分子量。
由于分子量高,因此,晶点部位聚合物具有较高的熔点。
在熔化时,熔体具有较高的黏度。
晶点部位聚合物在吹成薄膜时,不能与周围的同种聚合物相互均匀分散/混合,并在熔体吹成薄膜后,先于周围的同种聚合物凝固。
因此,形成“箭头状”或“球状”过度聚合物的凝固体。
习惯上被称为“晶点”。
(2)晶点产生的原因聚合物之所以产生晶点,是因为:1. 聚合物中有残留的催化剂2. 聚合物熔体黏滞于生产设备(包括聚合物设备及吹膜设备)钢铁表面,在高温下,残留的氧化剂对聚合物继续进行催化聚合作用,因此形成过度聚合物3. 聚合物中所含氧,也会使聚合物熔体产生晶点(李工加入一定数量的抗氧剂,有防止氧对晶点的产生作用,但不在此处讨论)。
晶点来自两个方面:1. 由聚合工艺所造成的晶点,不同的聚合设备及工艺,对晶点的生成有不同的影响。
例如:一些名厂原料,因生产技术高,聚合物中残留的催化剂含量低,设备结构好,因此原料本身所含的晶点少,但一些品质差的原料,因生产技术及设备问题,造成原料本身所含晶点多2. 由吹膜工艺所造成的晶点。
例如:好的吹膜设备所吹制的薄膜,晶点少,差的吹膜设备所吹制的薄膜,晶点多。
减少或基本消除晶点的方法综上所述,在薄膜吹制工艺中消除晶点,主要有两个途径:(1)提高加工设备的滤网目数,(2)在生产过程中添加钢铁表面润滑剂,使被加工的聚合物熔体不能粘滞于吹膜设备表面.从生产工艺上来说,虽使用较细的滤网可滤掉大部份聚合物中的晶点,同时亦可滤除吹膜设备螺杆及炮筒部位因聚合物粘滞于钢铁表面所造成的晶点,但问题是设备背压因此提高,对某些陈旧设备来说,难以做到.因此依靠换滤网,也能对控制晶点提供帮助.到目前为止,在国际上,最有效的晶点控制手段是采用高科技润滑剂,高科技钢铁表面润滑剂,由于它的聚合物分子具有高极性的特点,使它能从烯烃类聚合物熔体中逸出,并粘附于设备的钢铁表面,从而消除了聚合物熔体在设备钢铁表面的粘滞层,因此聚合物熔体能持续匀速地被推动前进,消除了粘滞于钢铁表面的聚合物熔体过长时间受热现象,防止了残留的催化剂对聚合物的持续聚合,最终防止了在薄膜吹塑加工工艺中所产生的晶点.另一方面,由于高科技润滑剂也能粘附于滤网表面,使聚合物熔体流经滤网的阴力下降.因此,高科技润滑剂的使用,为采用较细的滤网提供了工艺条件,而较细滤网的采用,对滤除由聚合物生产时所产生的原生晶点,是重要的工艺措施李工解决方法:1选择晶点少的原料2选择流动性好的原料3加工温度不能过高4螺杆及机筒要干净5加工中可加入加工助剂。
薄膜表面有晶点
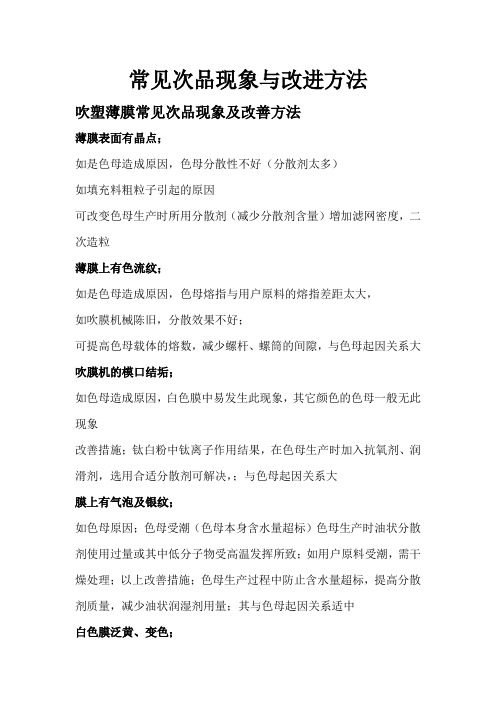
常见次品现象与改进方法吹塑薄膜常见次品现象及改善方法薄膜表面有晶点;如是色母造成原因,色母分散性不好(分散剂太多)如填充料粗粒子引起的原因可改变色母生产时所用分散剂(减少分散剂含量)增加滤网密度,二次造粒薄膜上有色流纹;如是色母造成原因,色母熔指与用户原料的熔指差距太大,如吹膜机械陈旧,分散效果不好;可提高色母载体的熔数,减少螺杆、螺筒的间隙,与色母起因关系大吹膜机的模口结垢;如色母造成原因,白色膜中易发生此现象,其它颜色的色母一般无此现象改善措施;钛白粉中钛离子作用结果,在色母生产时加入抗氧剂、润滑剂,选用合适分散剂可解决,;与色母起因关系大膜上有气泡及银纹;如色母原因;色母受潮(色母本身含水量超标)色母生产时油状分散剂使用过量或其中低分子物受高温发挥所致;如用户原料受潮,需干燥处理;以上改善措施;色母生产过程中防止含水量超标,提高分散剂质量,减少油状润湿剂用量;其与色母起因关系适中白色膜泛黄、变色;如色母造成原因;白色母中钛白粉质量有问题,或是用户原料存在问题,一些PE原料生产厂家在PE中加入了酚类或受阻酚类抗氧剂造成的此种原因造成的,此时即使不加色母的膜,放置一些日子也会变黄。
改善措施;改变钛白粉质量,重做色母,在生产时添加一些助剂,以利其与PE中酚类抗氧剂中和后一种原因造成的情况往往被栽在白色母上。
其与色母起因关系小。
吹成膜有异味:如色母原因;色母生产时,采用分散剂有问题,如聚乙烯蜡中混入了动物脂肪类东西或添加的偶联剂有问题,改善措施;可改进色母生产时所用分散剂及偶联剂的质量,其与色母起因关系大塑料编织淋膜布常见次品现象及改善方法涂塑淋膜布次品现象淋色膜后布上时有明显黑点如色母造成原因,色母中颜料分散不好,有结块现象,此时淋膜布前颜色会比原来的浅,甚至不均匀,或是因为螺杆、螺筒、模头没清洗干净,螺筒内有料情况下,长时间高温烘烤,使一部分色母助剂挥发,淋膜塑料中有杂质其改善措施;淋膜停机换色时应清洗干净,不应挨到第二天再洗机换色;调换优良品质色母,清洗淋膜机螺杆、螺筒,其与色母起因关系大淋色膜后布上产生地图状深浅不一的不均匀色斑(花纹)如色母原因;色母分散性不好,色母熔指与涂膜料熔指不相符,造成彼此流动性不一致,色母中部分颜料经不住高温而褪色,或非色母造成原因;淋膜机温度没有调正确,使一部分色母没有熔化、分散,淋膜机模头出料厚薄不一致,没有调整好;其改善措施;调换优良品质色母,使用熔指与涂膜料熔指相符之色母,色母中颜料粉选择耐高温分散好的色粉,调整好淋膜机各段温度,其与色母起因关系大淋色膜后布上的沟条状白斑(没有淋上色膜)如色母原因;个别色母粒没有熔化分解,或色母中有杂质,或被烤焦后卡在淋膜机模头上,如非色母原因;淋膜机螺杆、螺筒没清洗干净,特别是隔夜的料没有及时清洗,第二天开机时受热时间较长,闷在内的部分色母烤焦了,塑料原料中有颗粒状杂质或熔指不一样塑料混入淋膜料中;其改善措施;调换优良品质色母,使用熔指与涂膜料熔指相符之色母,色母中颜料粉选择耐高温分散好的色粉,调整好淋膜机各段温度,其与金色母起因关系适中淋膜布经日晒后很快会褪色如色母原因;色母中颜料粉的耐晒级别太低,经不起紫外线照射;其改善措施;不能用此类抵档色母,其与色母起因完全有关系淋膜布在使用中颜色会跟出来如色母原因;色母中颜料粉使用不当,颜料粉在迁移。
吹塑工艺中的常见问题、原因和解决办法
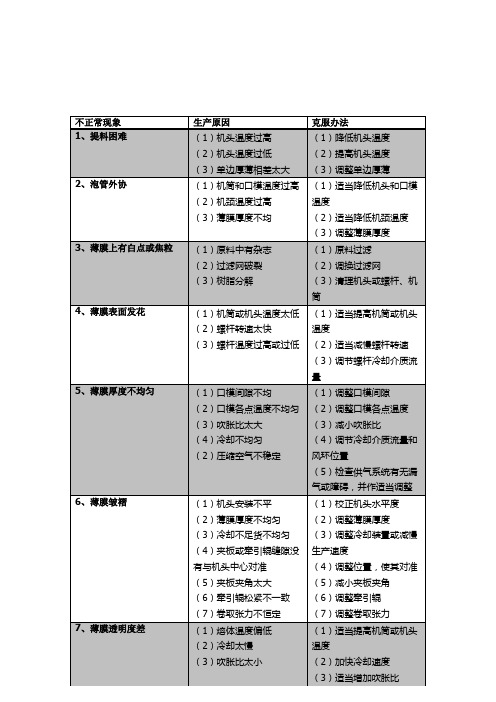
(7)卷取张力不恒定
(1)校正机头水平度
(2)调整薄膜厚度
(3)调整冷却装置或减慢生产速度
(4)调整位置,使其对准
(5)减小夹板夹角
(6)调整牵引辊
(7)调整卷取张力
7、薄膜透明度差
(1)熔体温度偏低
(2)冷却太慢
(3)吹胀比太小
(1)适当提高机筒或机头温度
(2)加快冷却速度
(3)适当增加吹胀比
(3)吹胀比太大
(4)冷却不均匀
(2)压缩空气不稳定
(1)调整口模间隙
(2)调整口模各点温度
(3)减小吹胀比
(4)调节冷却介质流量和风环位置
(5)检查供气系统有无漏气或障碍,并作适当调整
6、薄膜皱褶
(1)机头安装不平
(2)薄膜厚度不均匀
(3)冷却不足货不均匀
(4)夹板或牵引辊缝隙没有与机头中心对准
(5)夹板夹角太大
8、薄膜有气泡
原料中有水分
树脂燥
9、薄膜粘闭
(1)冷却不够
(2)牵引速度太快
(3)树脂未加开口剂
(1)加强冷却
(2)降低牵引速度
(3)选用加油开口剂的树脂
不正常现象
生产原因
克服办法
1、提料困难
(1)机头温度过高
(2)机头温度过低
(3)单边厚薄相差太大
(1)降低机头温度
(2)提高机头温度
(3)调整单边厚薄
2、泡管外协
(1)机筒和口模温度过高
(2)机颈温度过高
(3)薄膜厚度不均
(1)适当降低机头和口模温度
(2)适当降低机颈温度
(3)调整薄膜厚度
3、薄膜上有白点或焦粒
(1)原料中有杂志
关于晶点的形成原因和消除方法
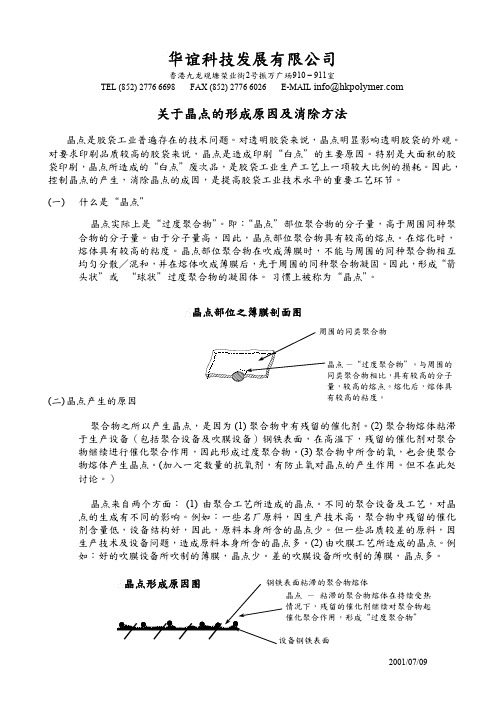
华谊科技发展有限公司香港九龙观塘荣业街2号振万广场910 – 911室TEL (852) 2776 6698 FAX (852) 2776 6026 E-MAIL info@关于晶点的形成原因及消除方法晶点是胶袋工业普遍存在的技术问题。
对透明胶袋来说,晶点明显影响透明胶袋的外观。
对要求印刷品质较高的胶袋来说,晶点是造成印刷“白点”的主要原因。
特别是大面积的胶袋印刷,晶点所造成的“白点”废次品,是胶袋工业生产工艺上一项较大比例的损耗。
因此,控制晶点的产生,消除晶点的成因,是提高胶袋工业技术水平的重要工艺环节。
(一)什么是“晶点”晶点实际上是“过度聚合物”。
即:“晶点”部位聚合物的分子量,高于周围同种聚合物的分子量。
由于分子量高,因此,晶点部位聚合物具有较高的熔点。
在熔化时,熔体具有较高的粘度。
晶点部位聚合物在吹成薄膜时,不能与周围的同种聚合物相互均匀分散/混和,并在熔体吹成薄膜后,先于周围的同种聚合物凝固。
因此,形成“箭头状”或 “球状”过度聚合物的凝固体。
习惯上被称为“晶点”。
(二) 晶点产生的原因聚合物之所以产生晶点,是因为 (1) 聚合物中有残留的催化剂。
(2) 聚合物熔体粘滞于生产设备(包括聚合设备及吹膜设备)钢铁表面,在高温下,残留的催化剂对聚合物继续进行催化聚合作用,因此形成过度聚合物。
(3) 聚合物中所含的氧,也会使聚合物熔体产生晶点。
(加入一定数量的抗氧剂,有防止氧对晶点的产生作用。
但不在此处讨论。
)晶点来自两个方面: (1) 由聚合工艺所造成的晶点。
不同的聚合设备及工艺,对晶点的生成有不同的影响。
例如:一些名厂原料,因生产技术高,聚合物中残留的催化由吹膜工艺所造成的晶点。
例晶点部位之薄膜剖面图-“过度聚合物”。
与周围的具有较高的分子2001/07/09(三) 减少或基本消除晶点的方法综上所述,在薄膜吹制工艺中消除晶点,主要有两个途径: (1) 提高加工设备的滤网细度 (例如:将滤网改为 80 目,甚或 150 目-用于超薄膜吹制)。
遇到塑料薄膜晶点问题 这里看过来
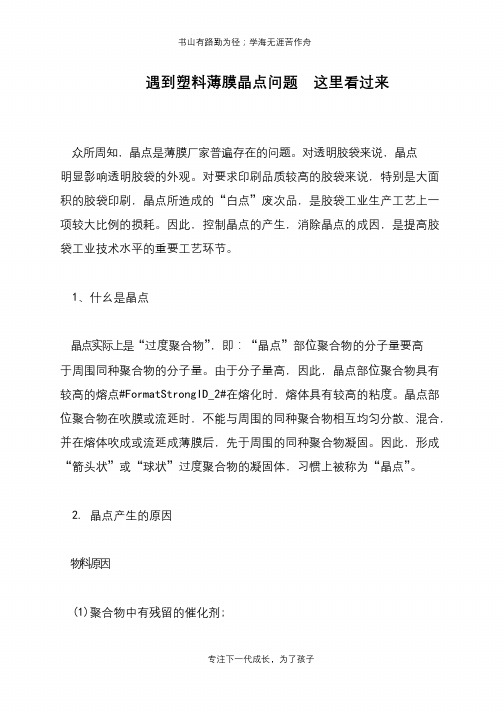
书山有路勤为径;学海无涯苦作舟
遇到塑料薄膜晶点问题这里看过来
众所周知,晶点是薄膜厂家普遍存在的问题。
对透明胶袋来说,晶点
明显影响透明胶袋的外观。
对要求印刷品质较高的胶袋来说,特别是大面积的胶袋印刷,晶点所造成的“白点”废次品,是胶袋工业生产工艺上一
项较大比例的损耗。
因此,控制晶点的产生,消除晶点的成因,是提高胶袋工业技术水平的重要工艺环节。
1、什幺是晶点
晶点实际上是“过度聚合物”,即:“晶点”部位聚合物的分子量要高
于周围同种聚合物的分子量。
由于分子量高,因此,晶点部位聚合物具有较高的熔点#FormatStrongID_2#在熔化时,熔体具有较高的粘度。
晶点部位聚合物在吹膜或流延时,不能与周围的同种聚合物相互均匀分散、混合,并在熔体吹成或流延成薄膜后,先于周围的同种聚合物凝固。
因此,形成“箭头状”或“球状”过度聚合物的凝固体,习惯上被称为“晶点”。
2. 晶点产生的原因
物料原因
(1)聚合物中有残留的催化剂;
专注下一代成长,为了孩子。
(整理)LDPE吹塑薄膜常见故障及解决方法.
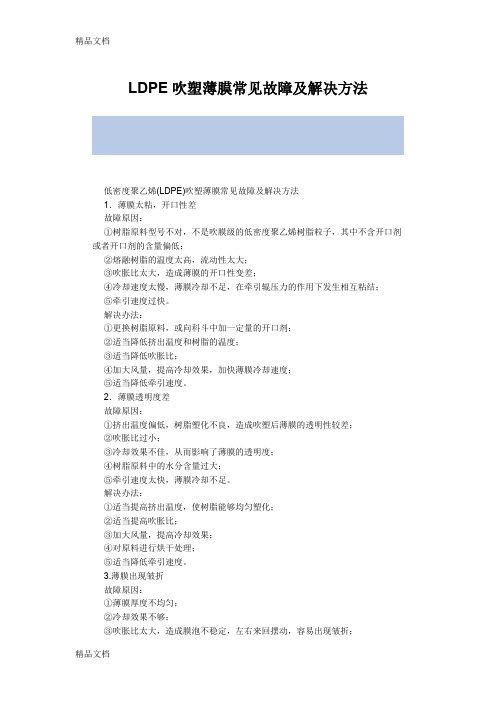
LDPE吹塑薄膜常见故障及解决方法低密度聚乙烯(LDPE)吹塑薄膜常见故障及解决方法1.薄膜太粘,开口性差故障原因:①树脂原料型号不对,不是吹膜级的低密度聚乙烯树脂粒子,其中不含开口剂或者开口剂的含量偏低;②熔融树脂的温度太高,流动性太大;③吹胀比太大,造成薄膜的开口性变差;④冷却速度太慢,薄膜冷却不足,在牵引辊压力的作用下发生相互粘结;⑤牵引速度过快。
解决办法:①更换树脂原料,或向科斗中加一定量的开口剂;②适当降低挤出温度和树脂的温度;③适当降低吹胀比;④加大风量,提高冷却效果,加快薄膜冷却速度;⑤适当降低牵引速度。
2.薄膜透明度差故障原因:①挤出温度偏低,树脂塑化不良,造成吹塑后薄膜的透明性较差;②吹胀比过小;③冷却效果不佳,从而影响了薄膜的透明度;④树脂原料中的水分含量过大;⑤牵引速度太快,薄膜冷却不足。
解决办法:①适当提高挤出温度,使树脂能够均匀塑化;②适当提高吹胀比;③加大风量,提高冷却效果;④对原料进行烘干处理;⑤适当降低牵引速度。
3.薄膜出现皱折故障原因:①薄膜厚度不均匀;②冷却效果不够;③吹胀比太大,造成膜泡不稳定,左右来回摆动,容易出现皱折;④人字夹板的夹角过大,膜泡在短距离内被压扁,因此薄膜也容易出现皱折;⑤牵引辊两边的压力不一致,一边高一边低;⑥各导向辊之间的轴线不平行,影响薄膜的稳定性和平展性,从而出现皱折。
解决办法:①调整薄膜的厚度,保证厚度均匀一致;②提高冷却效果,保证薄膜能够充分冷却;③适当降低吹胀比;④适当减小人字夹板的夹角;⑤调整牵引辊的压力,保证薄膜受力均匀;⑥检查各导向轴的轴线,并使之相互平行。
4,薄膜有雾状水纹故障原因:①挤出温度偏低,树脂塑化不良;②树脂受潮,水分含量过高。
解决办法:①调整挤出机的温度设置,并适当提高挤出温度。
②将树脂原料烘干,一般要求树脂的含水量不能超过0.3%。
5.薄膜厚度不均匀故障原因:①模口间隙的均匀性直接影响薄膜厚度的均匀性,如果模口间隙不均匀,有的部位间隙大一些,有的部位间隙小一些,从而造成挤出量有多有少,因此,所形成的薄膜厚度也就不一致,有的部位薄,有的部位厚;②模口温度分布不均匀,有高有低,从而使吹塑后的薄膜薄厚不均;③冷却风环四周的送风量不一致,造成冷却效果的不均匀,从而使薄膜的厚度出现不均匀现象;④吹胀比和牵引比不合适,使膜泡厚度不易控制;⑤牵引速度不恒定,不断地发生变化,这当然就会影响到薄膜的厚度。
吹塑薄膜易出现的质量问题及解决办法

吹塑薄膜易出现的质量问题及解决办法五、吹塑薄膜易出现的质量问题及解决办法5.1 拉不上牵引(管坯易拉断)原因:机头温度过高或过低,解决办法:调整温度.单边厚度相差大调整单边厚度机器不出料调整检查5.2 泡管歪斜原因:成型温度过高,冷却速度跟不上,薄膜厚薄不均匀,解决办法:调整模头牵引夹辊两端夹力不平衡调整夹力冷却风环出风口未调平衡调整它5.3 晶点多原因:材料本身分子量大小不均,解决办法:选择对型号的原料加工tC偏低调整TC过滤网稀或破洞更换机器本身LD过小适当提高tC5.4 皱纹多原因:模头加工精度不高,解决办法:提高光洁度分解物粘污,口模周边清理5.5道痕原因:因有杂物和焦化物夹于模口内,解决办法:挖掉5.6 水绞原因:TC低塑化不好,解决办法:提高TC .5.7薄膜厚薄不均匀原因:模头偏中,解决办法:调整模头周边温度不均匀调整吹胀比过大减小人字牌与模头中心不对中调整模管园周外来空气影响管坯摆动隔离5.8皱折原因:机头与人字牌中心不对中,解决办法:调整薄膜厚薄不均匀调整冷却不均匀调整人字牌夹角大小不适应调整牵引夹辊两边夹力不平衡调整卷曲张力不恒定调整5.9透明度差原因:机身、机头温度偏低,解决办法:调整冷却速率低加大风量5.10合缝线痕迹明显原因:模头流通设计不合理,合缝阻力大,解决办法:修正模头压缩比设计不合理,压缩比过小修正模口内含有杂物卡住挖掉5.11有疆块原因:原料分子量分布过宽,解决办法:换之加工温度过低提高5.12 膜管成竹节状原因:牵引速度有波动,解决办法:调整5.13膜面粘联原因:原料不对型号,解决办法:调换加工温度过高降低冷却速率低加大吹塑薄膜机组开车应注意的事项一、开车前的准备工作1、检查主机马达是否处在低速位置,特别是整流子电机要分外注意,高速启动会损坏电机,或者高速启动会扭断螺杆。
2、检查机身的温度是否达到控制温度,开车前最好用玻璃管温度计校核一下,防止假像温度,对T℃要校正调好。
吹塑薄膜时出现大量的晶点解决办法
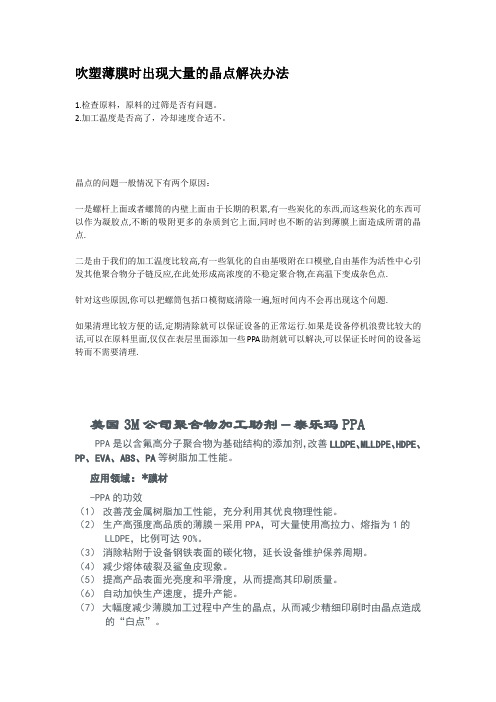
吹塑薄膜时出现大量的晶点解决办法1.检查原料,原料的过筛是否有问题。
2.加工温度是否高了,冷却速度合适不。
晶点的问题一般情况下有两个原因:一是螺杆上面或者螺筒的内壁上面由于长期的积累,有一些炭化的东西,而这些炭化的东西可以作为凝胶点,不断的吸附更多的杂质到它上面,同时也不断的沾到薄膜上面造成所谓的晶点.二是由于我们的加工温度比较高,有一些氧化的自由基吸附在口模壁,自由基作为活性中心引发其他聚合物分子链反应,在此处形成高浓度的不稳定聚合物,在高温下变成杂色点.针对这些原因,你可以把螺筒包括口模彻底清除一遍,短时间内不会再出现这个问题.如果清理比较方便的话,定期清除就可以保证设备的正常运行.如果是设备停机浪费比较大的话,可以在原料里面,仅仅在表层里面添加一些PPA助剂就可以解决,可以保证长时间的设备运转而不需要清理.美国3M公司聚合物加工助剂-泰乐玛PPAPPA是以含氟高分子聚合物为基础结构的添加剂,改善LLDPE、MLLDPE、HDPE、PP、EVA、ABS、PA等树脂加工性能。
应用领域:*膜材-PPA的功效(1)改善茂金属树脂加工性能,充分利用其优良物理性能。
(2)生产高强度高品质的薄膜-采用PPA,可大量使用高拉力、熔指为1的LLDPE,比例可达90%。
(3)消除粘附于设备钢铁表面的碳化物,延长设备维护保养周期。
(4)减少熔体破裂及鲨鱼皮现象。
(5)提高产品表面光亮度和平滑度,从而提高其印刷质量。
(6)自动加快生产速度,提升产能。
(7)大幅度减少薄膜加工过程中产生的晶点,从而减少精细印刷时由晶点造成的“白点”。
(8)消除由模头或设备传动部件对薄膜表面所造成的纵向拖痕。
(9)提高薄膜厚度的均匀性及稳定性。
(10)降低模头温度,保证吹膜泡体的稳定性。
(11)提高颜料着色性,缩短颜色切换时间,延长连续生产时间。
-PPA的添加为保证好的分散,PPA以母料形式加入,通过调整母料加入量,来调整配方中PPA的最终含量。
吹膜常出现问题及原因及解决方法

4、对准中心线
5、减小夹板夹角
6、调整牵引辊
7、调节摩擦力大小
六
拉不上牵引
1、机头温度过高或过低
2、单边厚薄相差太大
1、调整机温度
2、调整单边厚薄
吹膜机常见故障解决排除方法
序号
不正常现象
产生原因
解决办法
一
泡管歪斜
1、机身、口膜温度过高
2、边接器温度过高
3、薄膜厚度不均匀
1、降低机身温度、口膜温度
2、适当降低边接器温度
3、调节薄膜厚度
二
有点白或胶粒
1、原料中有杂质
2、过滤网破裂
3、颗粒混料不均匀
1、原料过筛
2、调换过滤网
3、严格控制捏和、膜温度过低
2、螺杆转速太快
3、螺杆温度过高或过低
4、聚乙烯配方不合理(铅盐稳定剂过多或耐寒塑剂过多)
1、适当升高机身和口膜温度
2、适当降低转速
3、调整螺杆冷却介质流量
4、改进配方
四
薄膜厚度不均匀
1、机头设计不合理
2、芯棒偏中变形
3、机头四周温度不均匀
4、吹胀比太大
5、冷却不均匀
6、压缩空气不稳定
1、修正改进机头工艺参数
2、调换芯棒
3、检查机头加热器
4、改小吹胀比
5、调节冷却介质流量
6、检修压缩泵
五
皱折
1、机头安装不平
2、薄膜厚度不均匀
3、冷却不够或者不均匀
4、夹板或牵引辊与机头中心未对准
5、夹板夹角太大
6、牵引辊的松紧不一致
7、卷取张力不恒定
1、校正机头水平度
2、调整薄膜厚度
- 1、下载文档前请自行甄别文档内容的完整性,平台不提供额外的编辑、内容补充、找答案等附加服务。
- 2、"仅部分预览"的文档,不可在线预览部分如存在完整性等问题,可反馈申请退款(可完整预览的文档不适用该条件!)。
- 3、如文档侵犯您的权益,请联系客服反馈,我们会尽快为您处理(人工客服工作时间:9:00-18:30)。
吹塑薄膜时出现大量的晶点解决办法
1.检查原料,原料的过筛是否有问题。
2.加工温度是否高了,冷却速度合适不。
晶点的问题一般情况下有两个原因:
一是螺杆上面或者螺筒的内壁上面由于长期的积累,有一些炭化的东西,而这些炭化的东西可以作为凝胶点,不断的吸附更多的杂质到它上面,同时也不断的沾到薄膜上面造成所谓的晶点.
二是由于我们的加工温度比较高,有一些氧化的自由基吸附在口模壁,自由基作为活性中心引发其他聚合物分子链反应,在此处形成高浓度的不稳定聚合物,在高温下变成杂色点.
针对这些原因,你可以把螺筒包括口模彻底清除一遍,短时间内不会再出现这个问题.
如果清理比较方便的话,定期清除就可以保证设备的正常运行.如果是设备停机浪费比较大的话,可以在原料里面,仅仅在表层里面添加一些PPA助剂就可以解决,可以保证长时间的设备运转而不需要清理.
美国3M公司聚合物加工助剂-泰乐玛PPA
PPA是以含氟高分子聚合物为基础结构的添加剂,改善LLDPE、MLLDPE、HDPE、PP、EVA、ABS、PA等树脂加工性能。
应用领域:*膜材
-PPA的功效
(1)改善茂金属树脂加工性能,充分利用其优良物理性能。
(2)生产高强度高品质的薄膜-采用PPA,可大量使用高拉力、熔指为1的LLDPE,比例可达90%。
(3)消除粘附于设备钢铁表面的碳化物,延长设备维护保养周期。
(4)减少熔体破裂及鲨鱼皮现象。
(5)提高产品表面光亮度和平滑度,从而提高其印刷质量。
(6)自动加快生产速度,提升产能。
(7)大幅度减少薄膜加工过程中产生的晶点,从而减少精细印刷时由晶点造成的“白点”。
(8)消除由模头或设备传动部件对薄膜表面所造成的纵向拖痕。
(9)提高薄膜厚度的均匀性及稳定性。
(10)降低模头温度,保证吹膜泡体的稳定性。
(11)提高颜料着色性,缩短颜色切换时间,延长连续生产时间。
-PPA的添加
为保证好的分散,PPA以母料形式加入,通过调整母料加入量,来调整配方中PPA的最终含量。
第一步:以5%的PPA母料与原料混合,加工60分钟,建立钢铁表面的加工助剂涂层。
第二步:以2%的添加量正常生产,以后根据产品情况可逐步减少添加量;长期连续使用,添加量为1%左右。
注:根据经验,在初始阶段,可能因为PPA开始在吹塑设备的钢铁表面建立润滑层而将以往粘附于钢铁表面的大量“晶点”或杂质“洗脱”,并随膜材的继续吹塑或压延而带出。
所以对一些比较陈旧的吹膜机或压延设备,在开始使用时,可能会发现大量晶点出现于膜材表面。
这是完全正常的。
所以建议在使用PPA
之前尽量先把机器清洗一下。
(PPA做食品包装时不宜使用)。