灰球铸铁铸件检验标准完成版
铸件外观检查一般标准
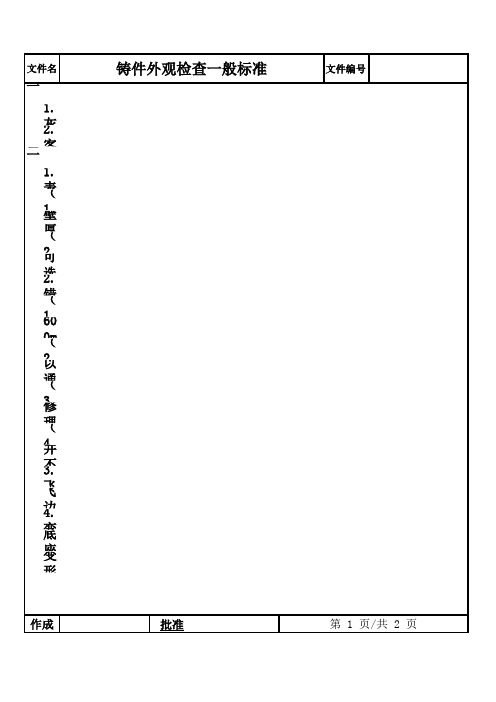
一.适用范围:1.灰铸铁和球墨铸铁件;2.客户有专门要求的以客户要求为准。
二.细 则:1.表面粗糙度:(1)表面粗糙度的凸凹高度差:壁厚10mm 以下要小于0.3mm;壁厚10mm以上要小于0.5mm。
局部超标可以打磨,打磨后再抛丸。
(2)表面粗糙度越细越好,但里面和外面,平面和垂直面要均匀。
可选用典型产品作为比照样板。
2.错箱和涨箱:(1)铸件分型面最大尺寸100mm以内,错箱要小于1mm;100至600mm错箱要小于2mm;600mm以上错箱要小于3.5mm。
(2)如果产品在本厂加工,而且错箱超差能够通过加工修正的,可以通过加工重新修正,但这些产品要分开管理。
(3)非加工面的涨箱,如果能够通过打磨或简单加工去除的,可以修理,但修理后要再抛丸。
(4)加工面出现的涨箱(指在本厂加工的加工面),只要能够去除并不影响其它尺寸,可以算合格毛坯。
3.飞边毛刺:飞边毛刺打磨残留量在0.5mm以下即可。
4.变形、翘曲:底座、盖板类的变形挠度允许量:自由状态放置在平台上,其最大变形量要保证在总长度的0.5%以下,比如600mm长可以3mm以下。
作成第 1 页/共 2 页批准5.气孔、渣眼、砂眼类:(1)加工面不允许有此类缺陷。
在本厂加工的产品,加工面孔眼不超过加工量,可以通过加工去除。
(2)非加工面的孔眼可以修补(铁基修补胶)、焊补,但必须符合以下范围:深度小于该部壁厚的三分之一、长或宽小于该部壁厚;数量5处以下。
需要电镀、热镀、粉体涂漆、电泳涂漆的不在此列。
6.表面皱纹:皱纹深度小于0.5mm,长度小于四倍壁厚,可以通过打磨方法处理。
7.冷隔、浇不足:冷隔(汤境)浇不足为废品,不能修补。
8.多肉:掉砂多肉通过铲磨不能恢复原形状的为废品。
9.缺肉:掉砂碰伤浇口根部缺肉,参考孔眼类的修补范围。
10.打磨修补:(1)打磨后残留量保证在0.5mm以下,不允许过度打磨。
(2)局部打磨过度的限度:深1mm长度不超过该部壁厚。
铸造件通用检验标准

铸造件通用检验标准前言铸造件的检验,以图纸为依据,如本标准与图纸不符,以图纸为检验标准。
为了使检验工作走向标准化,加强中间过程质量控制,特制定本检验标准。
1.范围本标准适用于本公司产品压铸件及机加工的检验、验收。
2.引用标准本标准引用了下列标准的条款.本标准发布时,这些引用标准均为有效版本.所有标准将进行修定,因此,鼓励依据本标准达成协议的各方尽可能采用下列标准的最新版本.GB4054—83 金属涂覆层外观分级GB/T 9286—88 色漆和清漆划痕试验GB/T 6739—96 涂膜硬度铅笔测定法GB/T 1733—93 漆膜耐水性测定法GB/T6742—93 漆膜弯曲试验(园柱轴)GB/T1732-93 漆膜耐冲击测定法GB/T1771—91 色漆和清漆耐中性盐污性能的测定GB 5267—85 螺纹紧固件电镀层GB 2792—81 压敏胶带180°剥离强度测定方法GB5935—86 轻工产品金属镀层的孔隙率测试方法GB6463—86 金属和其它无机覆盖层厚度测量方法评述GB10125-97 《人造气氛腐蚀试验盐雾试验》GB5270-86 金属覆盖层结合力及脆性测试GB/T1182-96 形状和位置公差GB4208-2008 外壳防护等级(IP代码)3.目的3.1确保压铸件判定的统一标准;3.2指引QC检验,将所有检验动作标准化。
4.定义磨花/磨痕:产品表面由于摩擦而造成的擦花痕刮伤/划伤:产品表面由于与尖硬物摩擦而造成的刮痕/划痕。
刀痕:因用锉刀或机加工时刀具所留下的痕迹砂带痕:因用砂带打磨所留下的痕迹拉模伤:顺着出模方向遗留在铸件表面上的拉伤痕迹。
凹陷:平滑表面上凹瘪的部分或者成型过程中填充不完整的部位压伤:切边模冲压或机加工时挤压所留下的痕迹碰伤:产品表面,边角受碰撞引起的变形痕迹顶针印:铸件表面由于模具顶针而形成凸出或凹下的痕迹行位印:铸件表面由于模具抽芯/镶块而形成凸出或凹下的痕迹冷隔:金属流对接未完全熔合形成的不规则下陷线性纹路,在外力作用下有发展趋势可能冷纹:肉眼可见与金属基体颜色不一样的纹络,无发展趋势印痕:铸件表面由于模具型腔磕碰挤压而形成凸出或凹下的痕迹流痕:表面上用手感觉得出的局部下陷的纹路,无发展趋势孔穴:气孔,缩孔和夹杂物等缺陷所形成的孔洞针孔:喷涂时表面产生的像针尖一样的小孔缺料/崩缺:外力敲击水口或切边模产生的缺损裂纹/裂痕:模具表面有呈直线状或波浪形的纹路,狭小而长,在外力的左右下有发展趋势龟裂纹:模具型腔表面龟裂形成的产品表面凸起或凹陷痕迹披锋:压铸件在分型面边缘出现的薄片毛边:边缘轮廓上因涂料堆积出现的边缘涂层不整齐现象斑点/麻点:产品表面形成的凸起颗粒或突出性杂物污点/脏点:颜色与正常表面不一致的色斑印迹气泡:涂层覆盖部分气体在烘烤时产生的泡状凸起缺陷桔皮/橘皮:涂层表面呈现出许多半圆状高低不平的桔子皮形状突起,易造成脱落起皮色差/异色:产品与色板的颜色差异露底/掉漆:局部无涂层或涂层缺失/覆盖不平露出底材积漆/溢漆:表面有较多漆团或漆点烧焦/发黄:喷涂烘烤不良造成表面留下的烧痕迹少漆/薄漆:喷涂不到位或涂层流动而造成的厚度不均匀补漆:因涂层损伤而用涂料所作的局部遮盖补救A 级面:指该表面位于工件或组装后经常看到的外表面,或客户日常操作能近距离视角接触,并直接正视关注的产品表面和商标文字和图案丝印表面B 级面:指该表面位于工件或组装背面,或不经常看到但在一定条件下能看到的面,或客户不明显关注的外观表面,或不易被客户直接视角接触正视的外部表面C 级面:指该表面位于工件或组装不可视面,或客户一般不易观察并关注到的内外部表面,或只有在装配过程中才能看到的面,或经其他工件覆盖需拆卸才能被客户直接视角接触正视的内外部表面5.内容5.1外观检验5.2性能检验5.3包装防护标识5.4机加工尺寸选用下表中等级-M级。
国家标准《GBT_9439-2009_灰铸铁件》修订说明

20年来世界科学技术的发展及对于清洁生产的迫切化, 提高了对铸件的要求,促进了铸造技术(工艺、材质、 铸造方法、装备及控制等)及铸造工厂现代管理的快速 发展。
全面落实国家标准的维护和管理任务, 建立相应的管理机制,从根本上提高国 家标准的时效性。
2,中华人民共和国国家标准
GB/T 9439-XXXX 代替GB/T 9439-1988
灰铸铁件 grey iron castings
与ISO 185:2005相比的
Байду номын сангаас主要技术内容差异
——在结构上作了较大的编辑性修改; ——删除了ISO 185:2005中重复性的表注和部分技术要求,增加
楔压强度。
增加了两个牌号
HT225 HT275
灰铸铁的牌号和力学性能
灰铸铁单铸试棒的抗拉强度和硬度
抗拉强度与主要壁厚之间的关系
灰铸铁的硬度牌号
感谢全国铸造标准化技术委员会 全体委员的辛勤工作!
与GB/T 9439-1988相比 主要技术内容的修订
——增加了两个牌号; ——增加了拉伸试样规格; ——增加了取样批次的规定; ——增加了灰铸铁件壁厚和硬度的对应值; ——增加了硬度和抗拉强度的关系图; ——增加了壁厚和抗拉强度的关系图; ——删除原标准的附录D,增加新的附录D
经济全球化的发展使中国的铸造业已经进入国际竞争的 阶段,出现了“国际竞争国内化和国内竞争国际化”的状 况。中国的铸件已经销往世界上大多数制造业大国。因 此我们的国家标准也应该与相应的国际标准接轨。
铸件质量检验标准

铸件质量检验标准一、目的:为了确保外协毛坯铸件、采购毛坯铸件、标准铸件、成品铸件质量符合工艺、技术要求,为了满足产品特性,结合相关文件特制定本标准。
二、适用范围:本标准适用于我公司产品外协、采购、生产、装配过程中,全部铸件质量检验标准。
三、检验标准:3.1 铸件结构要符合设计要求或加工工艺要求。
无特殊要求时按铸件通用标准执行。
通用标准等级分为:交货验收技术条件标准;铸件质量分等通则(合格品、一等品、优等品)材质、检验方法;工艺和材料规格等一般性规则。
3.2 铸件成品检验。
铸件成品检验包括:铸件的内部质量检验和外观质量检验。
铸件内部质量检验包括:化学成分、机械性能等。
铸件外观质量检验包括:表面质量、粗糙度、铸件尺寸、重量等。
3.2.1 铸件内部质量检验①化学成分:表1②机械性能表23.2.2 铸件外观质量检验①表面质量检验。
机械加工生产一线人员在工艺过程中对铸造毛坯的检验主要是对其外观铸造缺陷(如有无砂眼、砂孔、疏松、浇不足、铸造裂纹等)的检验;以及毛坯加工余量是否满足加工要求的检验。
表3 铸件外观质量检验项目(GB6060.1-1997)②粗糙度检验。
表4 铸件表面粗糙度(Ra值μm)(GB6060.1-1997)③铸件尺寸检验。
主要一种是采用划线法检查毛坯的加工余量是否足够。
另一种方法是:用毛坯的参考基准面(也称工艺基准面)作为毛坯的检验基准面的相对测量法(需要测量相对基准面的尺寸及进行简单换算)。
表5 铸件尺寸公差数值(mm)(GBT 6414-1997)1)在等级CT1~CT15中对壁厚采用粗一级公差。
2)对于不超过16mm的尺寸,不采用CT13~CT16的一般公差,对于这些尺寸应标注个别公差。
3)等级CT16仅适用于一般公差规定为CT15的壁厚。
表6 单件、小批量生产的铸件公差等级(GBT 6414-1997)注:1)表中所列出的公差等级是小批量的或单件生产的砂型铸件通常能够达到的公差等级。
铸件检验标准

为保证铸件的表面质量,检验要求一般规定如下。
在铸件上不允许有裂纹、通孔、穿透性的冷隔和穿透性的缩松、夹渣缺陷。
铸件非加工表面的毛刺、披锋、粘砂应清理至与铸件面同样平整。
铸件待加工表面,允许有不超过加工余量范围内的任何缺陷存在,但裂纹缺陷应予清除。
a)为铸件生产和管理部门提供质量信息;保证产品质量。
b)铸件的检验主要包括铸件表面质量检验、铸件内在质量检验以及铸件质量的综合鉴定。其中,铸件的表面质量包括铸件的表面缺陷、尺寸精度、质量偏差、表面粗糙度等。
4:铸件外观质量的检验
检验的依据是铸件的有关标准、技术条件和图样。铸件的表面质量主要包括铸件的表面缺陷、尺寸精度、质量偏差、形状偏差、表面粗糙度和铸件表面清理质量等多方面内容。
对铸件铸造缺陷的一般要求为:
铸件不允许存在裂纹、冷隔和浇不足等铸造缺陷;
当铸造缺陷位于铸件的加工面上,通过机械加工余量可以去除时;
在非加工面上,缺陷的深度不超过铸件该处厚度的1/10~1/5时(重要铸件或铸件的重要部位取小值,一般铸件或铸件的一般部位取大值)
铸件质量检验是铸造生产的重要工序,其主要职能是:
a) 合金浇铸温度过低,流动性差。
b)浇铸过程曾有中断,浇铸系统的形状和尺寸不合适。
错箱
铸型在分型面上错开
上、下模未对正,砂箱定位销不准,合箱时上、下箱有错动。
浇不足
铸件未浇满
浇铸温度太低,浇铸速度太慢或浇铸中曾有中断,浇口位置开设不当或浇口太小。
包砂
铸件中夹有一层薄砂壳或铸件表面有一条沟槽
金属液冲刷型壁的时间太长,造型材料中粘土的收缩性大,大平面铸件一般容易产生包砂。
铸铁件检验规范
3.
铸件出现铸造缺陷后,并非都是废品,应根据铸件的具体技术要求判断,判断原则如下:
GBT 7216-2009 灰铸铁金相检验(最新修订说明)

新修订的四项 铸铁国家标准东南大学材料学院 孙国雄新修订的四项铸铁国家标准GB/T 1348-(2009) 球墨铸铁件 GB/T 9439-(2009) 灰 铸 铁 件 GB/T 9441 -(2009) 球墨铸铁金相检验 GB/T 7216 -(2009) 灰铸铁金相检验原标准已经迫切需要修订原标准分别修订于20年前(灰铸铁金相标准修订于 1987年,其余三项修订于1988年)。
20年来中国的铸 造业无论从规模、产量、技术、装备及管理都有了极大 的变化与发展。
2001年起我国就已经成为世界铸件产量 最大的国家。
20年来世界科学技术的发展及对于清洁生产的迫切化, 提高了对铸件的要求,促进了铸造技术(工艺、材质、 铸造方法、装备及控制等)及铸造工厂现代管理的快速 发展。
经济全球化的发展使中国的铸造业已经进入国际竞争的 阶段,出现了“国际竞争国内化和国内竞争国际化”的状 况。
中国的铸件已经销往世界上大多数制造业大国。
因 此我们的国家标准也应该与相应的国际标准接轨。
修订国际标准的目的:解决我国国家标准总体技术水平低、市 场适应性差、体系结构不合理等问题; 建立先进科学、适应社会主义市场经济 体制的标准体系 ; 全面落实国家标准的维护和管理任务, 建立相应的管理机制,从根本上提高国 家标准的时效性。
4,中华人民共和国国家标准GB/T 7216-XXXX 代替GB/T 7216-1987灰铸铁金相检验 Metallographic test for gray cast iron与ISO/DIS 945-1:2005相比的 技术性差异——修改采用了ISO/DIS 945-1:2005中的Ⅰ型石 墨部分,并在结构上作了编辑性修改; ——本标准增加了石墨分布形状F型,代替 ISO/DIS 945-1:2005标准附录B的C′型。
——石墨分布形状的说明中增加F型的说明。
——增加了珠光体数量、碳化物数量、磷共晶 数量、共晶团数量的评定方法及相应评级图。
019铸件毛坯验收技术标准(球墨铸铁)

铸件毛坯验收技术条件第一版受控状态:分发号:持有者:2016-9-21 发布2016-9-21山东良鑫机械制造有限公司发球墨铸铁实施拟制:审核:审批:随着客户要求的不断提高特别是拖拉机变速箱,应相应地提高其零部件质量,加强零部件的质量检查。
为此特制订《铸件毛坯验收技术条件球磨铸铁》。
本标准作为我公司灰球铸铁件的制造和厂内验收依据。
质量部门在球磨铸铁件验收时依据本标准执行。
本标准包含了:1、对外协件的金相组织检验要求;2、对单铸、附铸试块限制的要求;3、对球墨铸铁件的加工定位点的要求;4、增加了附录D(球墨铸铁抗拉强度与屈服强度的近似关系式);5、附录E(球墨铸铁抗拉强度与硬度的近似关系)。
本标准主要起草单位:山东良鑫机械制造有限公司铸造工艺技术部。
本标准主要起草人:姚念勇1 范围本标准规定了我公司铸造的球墨铸铁件毛坯验收技术条件。
外协件检查可以此为依据。
本标准适用于我公司用砂型或导热性与砂型相当的铸型铸造的柴油机球墨铸铁件毛坯的验收。
2 规范性引用文件下列文件中的条款通过本标准的引用而成为本标准的条款。
凡是注日期的引用文件,其随后所有的修改单( 不包括勘误的内容 ) 或修订版均不适用于本标准,然而,鼓励本标准达成协议的各方研究是否可使用这些文件的最新版本。
凡是不注日期的引用文件,其最新版本适用于本标准。
GB/T228—2002GB/T231.1 —2002GB/T1348-1988GB/T5612—1985GB/T6060.1—1997GB/T6414—1999GB/T9441—1988GB/T11351-1989Q/LC C-02-0013 球墨铸铁牌号金属拉伸试验方法金属布氏硬度试验第1部分:试验方法球墨铸铁件铸铁牌号表示方法表面粗糙度比较样块铸造表面铸件尺寸公差与机械加工余量球墨铸铁金相检验铸件重量公差铸造毛坯验收技术条件灰铸铁铸件所用材质应符合产品技术图样规定。
球铁的牌号应符合 GB/T5612《铸铁牌号表示方法》的规定,并分为单铸试块和附铸试块两类。
灰铸铁金相检验标准

灰铸铁金相检验标准灰铸铁是一种广泛用于机械制造的铸铁材料,其性能直接关系到零部件的质量和使用寿命。
金相检验是对灰铸铁材料进行质量检测的重要手段,通过金相检验可以了解材料的组织结构、缺陷情况和性能特点,为生产工艺和质量控制提供重要依据。
本文将介绍灰铸铁金相检验的标准内容和要点,以便于相关人员进行准确、规范的检验工作。
一、金相检验的目的。
灰铸铁金相检验的主要目的是了解材料的组织结构和性能特点,包括晶粒大小、石墨形态、基体组织、缺陷情况等。
通过金相检验可以评定材料的组织均匀性、强度和硬度等性能指标,为材料的选用和工艺设计提供依据。
二、金相检验的标准。
1. 样品的制备,样品的制备是金相检验的第一步,样品的制备质量直接关系到检验结果的准确性。
样品的制备应符合相关标准要求,包括样品的切割、研磨、腐蚀和清洗等步骤。
2. 显微组织观察,金相检验的核心是对样品的显微组织进行观察和分析。
观察时应选取代表性的区域,包括铁素体、珠光体、渗碳体和石墨等组织结构,以了解材料的组织均匀性和形貌特征。
3. 组织定量分析,除了显微组织观察外,金相检验还需要对组织结构进行定量分析,包括晶粒大小、石墨形态、基体组织比例等参数的测定,以便于对材料性能进行评定。
4. 缺陷检测,金相检验还需要对材料的缺陷情况进行检测,包括气孔、夹杂、裂纹等缺陷的类型和分布情况,以评定材料的质量状况。
三、金相检验的要点。
1. 样品的制备应符合标准要求,避免制备过程对样品组织结构的影响。
2. 显微组织观察时应选取代表性的区域,避免观察结果的片面性和不准确性。
3. 组织定量分析需要准确的测试方法和仪器设备,以确保分析结果的准确性和可靠性。
4. 缺陷检测需要综合运用不同的检测方法,对材料的缺陷进行全面、深入的分析。
四、金相检验的意义。
灰铸铁金相检验是对材料质量进行评定的重要手段,通过金相检验可以了解材料的组织结构、性能特点和缺陷情况,为材料的选用和工艺设计提供依据。
资料│球铁铸件验收标准

资料│球铁铸件验收标准一、引用标准GB9441-88 球墨铸铁金相检验GB6060.1-85 表面粗糙度比较样块铸造表面 GB321-81 硬度试验二、技术要求三、机械性能机械性能为铸态毛坯本体试块测试值。
1、金相组织按GB9441-88《球墨铸铁金相检验》2、石墨铸件毛坯本体的球化率在60%以上,球化级别80%为1-3级,最差部位不低于5级,球径为5-7级。
3、基体(参考)铸件本体的基础组织为:铁素体80%以上,碳化物含量小于2%。
4、几何形状与尺寸铸件应符合相应的毛坯图尺寸规定。
铸件错型≤0.5mm,砂芯歪斜量≤0.8mm。
5、表面质量①铸件毛坯表面应无粘砂、氧化皮等缺陷,铸件毛坯表面的浇冒口、出气孔、多肉、飞边、毛刺等清除干净。
②铸件毛坯不允许有裂纹、缩孔、疏松、冷隔等影响使用性能的铸造缺陷。
③铸造毛坯非加工表面粗糙度R a≤100粗糙度评定按GB6060.1-85的规定进行。
④铸造毛坯不允许有锈蚀。
⑤铸件外表气孔和渣孔加工部位:直径≤Φ3mm,最大深度≤1.5mm,Φ2mm以上气孔数量每侧面不多于4个,Φ2mm以下气孔数量每侧面不多于7个。
非加工部位:直径≤Φ2mm,最大深度≤1.5mm,Φ2mm以上气孔数量不多于2个,Φ2mm以下气孔数量不多于5个。
6、铸件上的缺陷不允许修补。
7、批次的标识铸件毛坯必须在其本体的表面铸出永久性炉次标志即炉号。
炉号用六位组成。
第一位表示年号,取年号尾数,第二、三位表示月号,第四、五位为H号,第六位为流水号(当一炉铁水分作多包球化浇注时)× ×× ×× ×年号尾数月号日号流水号四、检验方法1、在提供最处样件时,铸件必须经解剖检测,X射线检测或Y射线检测无缩孔、缩松、裂纹等缺陷;在正常生产时,为确保质量稳定,要定期进行上述方式检测。
并且抽1‰铸件进行解剖检测。
生产设备改变、材料改变、更换模具、更改工艺或更换操作者时,铸件必须经以上解剖与检测。
灰铸铁件标准

灰铸铁件标准嘿,咱今儿就来唠唠灰铸铁件标准这档子事儿!你说这灰铸铁件啊,就像是咱生活里的老伙计。
你想想看,那汽车发动机里有它,各种机械装备里也少不了它。
它虽然不起眼,可作用大着呢!咱先说说这灰铸铁件的质量要求吧。
那可不能含糊呀!就好比咱盖房子,根基得打牢不是?这灰铸铁件也得有个结实的身板儿。
它得有合适的化学成分,该有的碳呀、硅呀啥的都得在点儿上,不然咋能保证它的性能呢?这就跟人一样,营养得均衡,不然就得病啦!再看看它的金相组织,这可是关键哟!不能有那些乱七八糟的缺陷,得整整齐齐、规规矩矩的。
要是金相组织不行,那不就跟那歪瓜裂枣似的,能好用吗?还有啊,尺寸精度也得讲究。
你说要是一个零件这儿大点儿那儿小点儿,那还能装得上去吗?那不就成笑话啦!这就好像你去买双鞋,尺码不合适,你能穿得舒服吗?咱平常生活里用的那些东西,好多都离不开灰铸铁件呢。
你说要是这些个标准都不达标,那会咋样?那不得三天两头出毛病呀!就像你骑个自行车,要是零件不行,那不是老掉链子就是嘎吱嘎吱响,多烦人呐!咱再来说说这灰铸铁件的生产过程。
那也是马虎不得呀!从原材料的选择到熔炼、浇注,每个环节都得用心。
这就跟做饭似的,食材得新鲜,火候得掌握好,不然做出来的菜能好吃吗?熔炼的时候得注意温度呀,高了不行低了也不行,就跟那水温洗澡一样,太烫了烫得慌,太凉了又冷得哆嗦。
浇注的时候也得小心,不能洒了漏了的,那不就浪费啦?而且啊,生产完了还得检测呢!可不能随随便便就拿出去用了。
这检测就好比给它做个体检,有啥毛病都得查出来。
要是有问题的零件流出去了,那不是坑人嘛!你说这灰铸铁件标准重要不重要?那肯定重要呀!它关系到咱用的那些东西质量好不好,耐不耐用。
咱可不希望买个东西回来没几天就坏了吧?所以啊,咱得重视这灰铸铁件标准。
厂家得严格按照标准来生产,咱消费者也得有点常识,知道怎么挑好的灰铸铁件。
这样,咱的生活才能更顺溜,那些机械装备啥的才能更好地为咱服务呀!这道理不是明摆着的嘛!原创不易,请尊重原创,谢谢!。
灰球铸铁铸件检验标准完成版
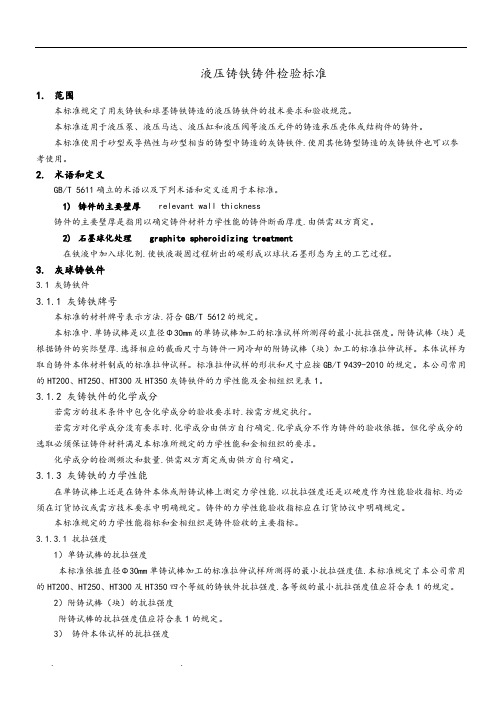
液压铸铁铸件检验标准1.范围本标准规定了用灰铸铁和球墨铸铁铸造的液压铸铁件的技术要求和验收规范。
本标准适用于液压泵、液压马达、液压缸和液压阀等液压元件的铸造承压壳体或结构件的铸件。
本标准使用于砂型或导热性与砂型相当的铸型中铸造的灰铸铁件.使用其他铸型铸造的灰铸铁件也可以参考使用。
2.术语和定义GB/T 5611确立的术语以及下列术语和定义适用于本标准。
1)铸件的主要壁厚 relevant wall thickness铸件的主要壁厚是指用以确定铸件材料力学性能的铸件断面厚度.由供需双方商定。
2)石墨球化处理 graphite spheroidizing treatment在铁液中加入球化剂.使铁液凝固过程析出的碳形成以球状石墨形态为主的工艺过程。
3.灰球铸铁件3.1 灰铸铁件3.1.1 灰铸铁牌号本标准的材料牌号表示方法.符合GB/T 5612的规定。
本标准中.单铸试棒是以直径Φ30mm的单铸试棒加工的标准试样所测得的最小抗拉强度。
附铸试棒(块)是根据铸件的实际壁厚.选择相应的截面尺寸与铸件一同冷却的附铸试棒(块)加工的标准拉伸试样。
本体试样为取自铸件本体材料制成的标准拉伸试样。
标准拉伸试样的形状和尺寸应按GB/T 9439-2010的规定。
本公司常用的HT200、HT250、HT300及HT350灰铸铁件的力学性能及金相组织见表1。
3.1.2 灰铸铁件的化学成分若需方的技术条件中包含化学成分的验收要求时.按需方规定执行。
若需方对化学成分没有要求时.化学成分由供方自行确定.化学成分不作为铸件的验收依据。
但化学成分的选取必须保证铸件材料满足本标准所规定的力学性能和金相组织的要求。
化学成分的检测频次和数量.供需双方商定或由供方自行确定。
3.1.3 灰铸铁的力学性能在单铸试棒上还是在铸件本体或附铸试棒上测定力学性能.以抗拉强度还是以硬度作为性能验收指标.均必须在订货协议或需方技术要求中明确规定。
铸件的力学性能验收指标应在订货协议中明确规定。
灰铸铁、球墨铸铁件通用技术条件

灰铸铁、球墨铸铁件通用技术条件之阿布丰王创作1适应范围1.2铸件毛坯应符合图纸及有关技术文件的规定,图纸及技术文件未注明的按本技术条件的有关规定执行.2.概况质量2.1铸件概况不允许有冷隔、裂纹、铁豆、缩孔及影响外观的残缺类缺陷(如欠铸、机械损伤)2.2铸件的型砂、芯沙、芯骨、浇冒口和飞边应清除干净,非加工面的浇冒口残留、多肉、粘沙应铲磨平整2.3非加工面均需喷丸或滚筒处置.3.铸件毛坯公差按下表(单元mm)基本尺寸公差基本尺寸公差基本尺寸公差≤10±>63~100 ±3 >630~1000 ±>10~16 ±>100~160 ±>1000~1600 ±>16~25 ±>160~250 ±4 >1600~2500 ±>25~40 ±>250~400 ±>2500~4000 ±>40~63 ±>400~630 ±54、拔模斜度4.1起模斜度在铸件的加工面上时以增加铸件尺寸的形式,即基本尺寸定在起模斜度的小端4.2起模斜度在铸件的非加工概况上时以减少铸件尺寸的形式,即基本尺寸定在起模斜度的年夜端起模面高度≤10>10~40 >40~100 >100~160 >160~250 >25起模斜度≤2°55′1°25′40′30′25′25′正切值起模面高度>400~630 >630~1000 >1000~1600 >1600~2500 >2500起模斜度≤20′20′20′15′15′正切值mm,且不得与上表的公差值相加.6、加工余量6.1 确定回转体的加工余量时,基本尺寸可取其直径或高度中的较年夜值.6.3 直径小于50mm的孔可以不铸出.6.4 加工余量值见下表,表中每栏两个加工余量值,上面的数值以一侧为基准进行单侧加工的加工余量值;下面是双侧加工每侧的加工余量值..基本尺寸加工余量基本尺寸加工余量基本尺寸加工余量≤100 5 >250~400 >1000~1600 1512>100~1605 >400~630 11 >1600~2500 1713>160~250 86 >630~1000 1310>2500~4000 19157.内在质量要求7.1 铸件毛坯的机械性能应符合GB/T9439《灰铸铁件》和GB/T1348 《球墨铸铁件》的相应要求.7.2 铸件经加工的相对运动配合概况不得有缩松、气孔、沙眼和裂纹等缺陷存在.7.3铸件非外露的其它加工面上允许有轻微的缩松和非聚集的缺陷孔眼,其最年夜尺寸不年夜于4mm,深度不年夜于3mm 且不年夜于壁厚的1/4,在100mm×100mm范围内不很多于2个,相互间距或距边缘不小于10mm,且一个概况未几于10个.。
铸造件通用检验标准

. . .. ..铸造件通用检验标准前言铸造件的检验,以图纸为依据,如本标准与图纸不符,以图纸为检验标准。
为了使检验工作走向标准化,加强中间过程质量控制,特制定本检验标准。
. . .. ..1.范围本标准适用于本公司产品压铸件及机加工的检验、验收。
2.引用标准本标准引用了下列标准的条款.本标准发布时,这些引用标准均为有效版本.所有标准将进行修定,因此,鼓励依据本标准达成协议的各方尽可能采用下列标准的最新版本.GB4054—83 金属涂覆层外观分级GB/T 9286—88 色漆和清漆划痕试验GB/T 6739—96 涂膜硬度铅笔测定法GB/T 1733—93 漆膜耐水性测定法GB/T6742—93 漆膜弯曲试验(园柱轴)GB/T1732-93 漆膜耐冲击测定法GB/T1771—91 色漆和清漆耐中性盐污性能的测定GB 5267—85 螺纹紧固件电镀层GB 2792—81 压敏胶带180°剥离强度测定方法GB5935—86 轻工产品金属镀层的孔隙率测试方法GB6463—86 金属和其它无机覆盖层厚度测量方法评述GB10125-97 《人造气氛腐蚀试验盐雾试验》GB5270-86 金属覆盖层结合力及脆性测试GB/T1182-96 形状和位置公差GB4208-2008 外壳防护等级(IP代码)3.目的3.1确保压铸件判定的统一标准;3.2指引QC检验,将所有检验动作标准化。
4.定义磨花/磨痕:产品表面由于摩擦而造成的擦花痕刮伤/划伤:产品表面由于与尖硬物摩擦而造成的刮痕/划痕。
刀痕:因用锉刀或机加工时刀具所留下的痕迹. . .. ..砂带痕:因用砂带打磨所留下的痕迹拉模伤:顺着出模方向遗留在铸件表面上的拉伤痕迹。
凹陷:平滑表面上凹瘪的部分或者成型过程中填充不完整的部位压伤:切边模冲压或机加工时挤压所留下的痕迹碰伤:产品表面,边角受碰撞引起的变形痕迹顶针印:铸件表面由于模具顶针而形成凸出或凹下的痕迹行位印:铸件表面由于模具抽芯/镶块而形成凸出或凹下的痕迹冷隔:金属流对接未完全熔合形成的不规则下陷线性纹路,在外力作用下有发展趋势可能冷纹:肉眼可见与金属基体颜色不一样的纹络,无发展趋势印痕:铸件表面由于模具型腔磕碰挤压而形成凸出或凹下的痕迹流痕:表面上用手感觉得出的局部下陷的纹路,无发展趋势孔穴:气孔,缩孔和夹杂物等缺陷所形成的孔洞针孔:喷涂时表面产生的像针尖一样的小孔缺料/崩缺:外力敲击水口或切边模产生的缺损裂纹/裂痕:模具表面有呈直线状或波浪形的纹路,狭小而长,在外力的左右下有发展趋势龟裂纹:模具型腔表面龟裂形成的产品表面凸起或凹陷痕迹披锋:压铸件在分型面边缘出现的薄片毛边:边缘轮廓上因涂料堆积出现的边缘涂层不整齐现象斑点/麻点:产品表面形成的凸起颗粒或突出性杂物污点/脏点:颜色与正常表面不一致的色斑印迹气泡:涂层覆盖部分气体在烘烤时产生的泡状凸起缺陷桔皮/橘皮:涂层表面呈现出许多半圆状高低不平的桔子皮形状突起,易造成脱落起皮色差/异色:产品与色板的颜色差异露底/掉漆:局部无涂层或涂层缺失/覆盖不平露出底材积漆/溢漆:表面有较多漆团或漆点烧焦/发黄:喷涂烘烤不良造成表面留下的烧痕迹. . .. ..少漆/薄漆:喷涂不到位或涂层流动而造成的厚度不均匀补漆:因涂层损伤而用涂料所作的局部遮盖补救A 级面:指该表面位于工件或组装后经常看到的外表面,或客户日常操作能近距离视角接触,并直接正视关注的产品表面和商标文字和图案丝印表面B 级面:指该表面位于工件或组装背面,或不经常看到但在一定条件下能看到的面,或客户不明显关注的外观表面,或不易被客户直接视角接触正视的外部表面C 级面:指该表面位于工件或组装不可视面,或客户一般不易观察并关注到的内外部表面,或只有在装配过程中才能看到的面,或经其他工件覆盖需拆卸才能被客户直接视角接触正视的内外部表面5.内容5.1外观检验. . .. ..5.2性能检验5.3包装防护标识. . .. ..5.4机加工尺寸选用下表中等级-M级。
铸造公司原材料成品检验标准

铸造公司原材料成品检验标准铸造公司原材料、成品检验标准审批:一、原材料进厂检验对EPC消失模铸件生产中原材料:灰铸铁用生铁、球墨铸铁用生铁、硅铁、锰铁、铬铁、废钢;聚苯乙烯;石英砂和炉衬材料进厂检验规定如下:采用标准:GB/T718—2005《灰铸铁件用生铁》GB1412—85《球墨铸铁件用生铁》GB/T2272—2022《硅铁》GB/T3795—2006《电炉锰铁》GB/T5683—2022《铬铁》GB719—84《生铁化学分析用试样制取方法》GB/T4010—94《铁合金化学分析用试样的采取和制备》Q/BAML002-2022《CF4AL感应电炉酸性炉衬耐火材料》——**环宇石英砂企业标准Q/BAML001-2022《精制石英砂〔粉〕》——**环宇石英砂企业标准1、灰铸铁用生铁的检验:1.1灰铸铁用生铁的检验依据GB/718—2005《灰铸铁件用生铁》标准进行检验,其中化学成分如表1所示,要求C含量不得低于4.1%。
1.2要求对进厂每批灰铸铁用生铁进行检验。
由理化室依照GB/719—84《生铁化学分析用试样制取方法》现场抽样,并制取试样;化验分析后出具《原材料进厂检测及化学分析报告单》。
分析结果合格方能入库,不合格应明确标识,由技术部门负责人决定是让步接受还是退货后进行处理。
表1 灰铸铁用生铁〔摘自GB/T718—2005〕铁号牌号铸34铸30铸26铸22铸18铸14代号Z34Z30Z26Z22Z18Z14化学成分〔%〕C>、4.1Si>3.20~3.60>2.80~3.20>2.40~2.80>2.00~2.40>1.60~2.00>1.25~1.60Mn1组≤0.052>0.50~0.90组3组>0.90~1.30P1级≤0.062级>0.06~0.103级>0.10~0.204级>0.20~0.405级>0.40~0.90S1类≤0.03≤0.042类≤0.04≤0.053类≤0.05≤0.061.3外观质量:规整平滑,根本无毛边。
灰铁、球铁砂型铸件尺寸公差及表面质量

灰铁、球铁砂型铸件尺寸公差及表面质量1.0范围本标准规定了基本的表面质量要求,蓝图未注的基本的铸件公差及为库伯工业供应的灰铁及球铁砂型铸件的精加工余量。
2.0铸件表面质量2.1外观应抛光,无灰尘残留,零件号、炉号及铸造标识易辨认。
2.2结块或胀砂应在下述规定范围内:最大铸件尺寸最大结块或胀砂最大影响区域0”至5”+ 1/32” 3 平方英寸5”至10”+ 1/16” 4 平方英寸10”至18”+ 3/32”8 平方英寸18”以上+ 1/8”10 平方英寸若可行,大于以上公差的受影响区域可由铸造厂去除。
(蓝图规定的公差为验收的最终决定因素。
)2.3表面缩孔应清理干净无异物,不能有油灰或其它填充物。
缺陷深度不能超过壁厚的25%,最大不超过3/8英寸。
如果缺陷直径很小,深度不大(深度陡降面),库伯质控人员可要求对其进行打磨圆滑过渡。
缺陷的数量及尺寸在很大程度上影响了铸件质量。
缺陷数量和尺寸应控制在最小可接受的水平,具体可由库伯质量控制人员和供应商一起协商。
协商应基于一下几方面:缺陷位置,铸件的关键性,最终客户对此缺陷可见度的要求。
2.4在保留规定壁厚的前提下去除浇道,冒口及披缝。
去除浇冒口后的表面应与周围铸态表面情况相当。
铸件表面及轮廓应满足下列要求:最大铸件尺寸公差0”至10”± 0.030”10” 至20” -- 0.030” + 0.060” 20” 至 50” -- 0.060” + 0.090”50” 以上 -- 0.060” + 0.120”2.5 在得到库伯高级质量控制的书面授权之后方可进行焊补。
需提交对于焊修区域的详细描述,包括建议的焊修工艺方可得到书面授权。
3.0 精加工余量:3.1 如果铸件尺寸未包含加工余量,蓝图中用f 或√标注的需进行加工。
平面,曲面或 圆弧面的加工余量如下:3.1.1 加工面加工余量:3.1.2 内径加工余量直径 0” 至 1” 1” 至 5” 每侧0.100 5” 至 12” 每侧0.187 12” 至20” 每侧0.250 20” 以上 每侧0.375注:制作模具时应使铸件尺寸尽量达到上述精度要求。
- 1、下载文档前请自行甄别文档内容的完整性,平台不提供额外的编辑、内容补充、找答案等附加服务。
- 2、"仅部分预览"的文档,不可在线预览部分如存在完整性等问题,可反馈申请退款(可完整预览的文档不适用该条件!)。
- 3、如文档侵犯您的权益,请联系客服反馈,我们会尽快为您处理(人工客服工作时间:9:00-18:30)。
液压铸铁铸件检验标准1.范围本标准规定了用灰铸铁和球墨铸铁铸造的液压铸铁件的技术要求和验收规范。
本标准适用于液压泵、液压马达、液压缸和液压阀等液压元件的铸造承压壳体或结构件的铸件。
本标准使用于砂型或导热性与砂型相当的铸型中铸造的灰铸铁件,使用其他铸型铸造的灰铸铁件也可以参考使用。
2.术语和定义GB/T 5611确立的术语以及下列术语和定义适用于本标准。
1)铸件的主要壁厚relevant wall thickness铸件的主要壁厚是指用以确定铸件材料力学性能的铸件断面厚度,由供需双方商定。
2)石墨球化处理graphite spheroidizing treatment在铁液中加入球化剂,使铁液凝固过程析出的碳形成以球状石墨形态为主的工艺过程。
3.灰球铸铁件灰铸铁件灰铸铁牌号本标准的材料牌号表示方法,符合GB/T 5612的规定。
本标准中,单铸试棒是以直径Φ30mm的单铸试棒加工的标准试样所测得的最小抗拉强度。
附铸试棒(块)是根据铸件的实际壁厚,选择相应的截面尺寸与铸件一同冷却的附铸试棒(块)加工的标准拉伸试样。
本体试样为取自铸件本体材料制成的标准拉伸试样。
标准拉伸试样的形状和尺寸应按GB/T 9439-2010的规定。
本公司常用的HT200、HT250、HT300及HT350灰铸铁件的力学性能及金相组织见表1。
灰铸铁件的化学成分若需方的技术条件中包含化学成分的验收要求时,按需方规定执行。
若需方对化学成分没有要求时,化学成分由供方自行确定,化学成分不作为铸件的验收依据。
但化学成分的选取必须保证铸件材料满足本标准所规定的力学性能和金相组织的要求。
化学成分的检测频次和数量,供需双方商定或由供方自行确定。
灰铸铁的力学性能在单铸试棒上还是在铸件本体或附铸试棒上测定力学性能,以抗拉强度还是以硬度作为性能验收指标,均必须在订货协议或需方技术要求中明确规定。
铸件的力学性能验收指标应在订货协议中明确规定。
本标准规定的力学性能指标和金相组织是铸件验收的主要指标。
抗拉强度1)单铸试棒的抗拉强度本标准依据直径Φ30mm单铸试棒加工的标准拉伸试样所测得的最小抗拉强度值,本标准规定了本公司常用的HT200、HT250、HT300及HT350四个等级的铸铁件抗拉强度,各等级的最小抗拉强度值应符合表1的规定。
2)附铸试棒(块)的抗拉强度附铸试棒的抗拉强度值应符合表1的规定。
3)铸件本体试样的抗拉强度铸件本体试棒的抗拉强度值应符合表1的规定。
表1 灰铸铁件的牌号和力学性能硬度等级及铸件硬度灰铸铁的硬度等级分为六个等级,见表2。
各硬度等级的硬度是指主要壁厚t>40mm且壁厚t≤80mm的上限硬度值。
如果需方要求将硬度作为验收指标时,硬度的检测频次和数量由供需双方商定,并选用如下之一的验收规则:1)铸件本体的硬度值应符合表2的规定;2)在单铸试棒加工的试样上测定材料的硬度时,应符合表1的规定。
若需方对铸件本体的测试部位及硬度值有明确规定时,应符合需方图样及技术要求。
注1:硬度等级分类适用于以机械加工性能和以抗磨性能为主的铸件。
注2.对于主要壁厚t>80mm的铸件,不按硬度进行分级。
表2 灰铸铁的硬度等级及铸件硬度金相组织灰铸铁金相组织中的石墨以片状为主,其分布形态应符合GB/T 7216-2009的规定,以A型为主,少量D型和E型(见图1和表3所示)。
石墨的长度应符合GB/T 7216-2009规定的4~6级(见表4所示),特殊要求由供需双方商定。
基体组织应符合表2的规定,其中碳化物数量和磷共晶数量应符合或严于GB/T 7216-2009规定的“碳1”和“磷1”的要求,即按大多数视场中,碳化物数量和磷共晶数量约占1%,(试样用2~5%硝酸酒精溶液浸蚀,放大100倍)。
当需方对金相组织及其各检测项目的数值、分布、级别及取样位置有明确要求时,应按需方提供的图样及技术要求执行。
表3 石墨的分布形态表4 石墨长度分级1 石长100 >100 5 石长9>6~122 石长75 >50~100 6 石长>3~63 石长38 >25~50 7 石长>~34 石长18 >12~15 8 石长≤注:评定时,用未浸蚀的试样,在放大100倍的显微镜下观察,选择有代表性的视场,按其中最长的三条以上的石墨长度的平均值评定。
图1 石墨分布形状图(100×)球墨铸铁件球墨铸铁牌号铸件材料牌号是通过测定下列试样的力学性能而确定的:—单铸试样:从单铸试块上截取加工而成的试样。
单铸试样可以采用U形单铸试块或Y形单铸试块,本公司采用Y形单铸试块。
单铸试块的形状和尺寸见图3。
—附铸试样:从附铸在铸件或浇注系统上的试块截取加工而成的试样。
—本体试样:从铸件本体上截取加工而成的试样。
铸件材料号等级是依照从单铸试样、附铸试样、本体试样测出的力学性能而定义的。
表5 球墨铸铁件单铸试样的力学性能及主要基体组织表6 球墨铸铁件附铸试样和本体试样的力学性能及主要基体组织球墨铸铁件的生产方法和化学成分球墨铸铁的生产方法和化学成分由供方自行决定,生产方法和化学成分的选取必须要保证铸件材料满足本标准所规定的性能指标。
球墨铸铁的化学成分不作为铸件验收的依据。
当需方对铸件由特殊要求时,材料的化学成分和热处理方式由供需双方协商确定。
球墨铸铁的力学性能球墨铸铁单铸试样的力学性能1)总则单铸试样可以采用U形单铸试块或Y形单铸试块,本公司采用Y形单铸试块。
单铸试块的形状和尺寸见图3。
球墨铸铁单铸试样的力学性能见表5。
如需方有要求时,冲击性能应符合表7的规定。
球墨铸铁件的力学性能以抗拉强度和伸长率两个指标为验收指标。
除特殊情况外,一般不做屈服强度试验。
但当需方对屈服强度有要求时,经供需双方商定,屈服强度也可作为验收指标。
抗拉强度和硬度是相互关联的,当需方认为硬度性能对使用很重要时,硬度指标也可作为检验项目。
硬度的检验按附录C的规定执行。
2)冲击试验表7给出了室温和低温下的冲击功。
球墨铸铁附铸试样的力学性能1)总则球墨铸铁附铸试样的力学性能见表6,如需方要求,冲击功应符合2)及表8的规定。
2)冲击试验3)表8给出了室温和低温下的冲击功。
如果需方要求时,可以做冲击试验。
铸件本体试样性能取样部位及达到的性能指标,由供需双方商定。
本体试样的屈服强度的参考值见附录D。
注1:铸件本体的性能值无法统一一致,因其决定于铸件的复杂程度以及铸件壁厚的变化。
注2:表5~表8用于铸件力学性能的指导值,铸件本体性能值也许等于或低于表5~表8所给定的值。
球墨铸铁硬度等级如果需方要求将硬度作为验收指标时,硬度的检测频次和数量由供需双方商定,并选用如下之一的验收规则:1)在单铸试棒加工的试样上测定材料的硬度时,应符合表5的规定;2)铸件本体的硬度值应符合表6的规定。
若需方对铸件本体的测试部位及硬度值有明确规定时,应符合需方图样及技术要求。
只有供需双方协商一致后,才可按硬度进行分类。
球墨铸铁硬度等级见附录C。
如果需方将硬度作为重要要求,则硬度的检验方法按附录C的规定执行。
金相组织石墨以球状为主,球化级别(见表9所示)应符合GB/9441-2009规定的1级~3级(见图所示)。
石墨大小(见表10所示)应符合GB/9441-2009规定的4级~7级(见图所示)的要求。
特殊要求由供需双方商定。
基体组织应符合表5或表6的规定,其中碳化物数量和磷共晶数量应符合或严于GB/9441-2009规定的“碳1”和“磷1”要求。
当需方对金相组织及其各检测项目的数据、分布、级别及取样位置有明确要求时,应按需方提供的图样及技术要求执行。
表9 球化分级表10 石墨大小分级4.技术要求几何形状和尺寸铸件的几何形状和尺寸应符合图样或技术要求。
尺寸公差铸件尺寸公差应符合需方图样或技术要求。
若需方无特殊要求时,按表11规定的CT8-CT10执行。
铸件加工余量铸件加工余量应符合需方图样或技术要求。
若需方无特殊要求时,按表12的规定执行。
重量偏差铸件重量偏差应符合需方图样或技术要求。
若需方无特殊要求时,按表13的规定执行。
铸件表面质量铸件的表面质量包括外表面和内表面质量。
铸件的铸造表面粗糙度应符合GB/T 的规定或需方的图样和技术要求。
铸件应清理干净,修整多余部分,去除浇冒口残余、粘砂及内腔残余物等。
铸件允许的浇冒口残余、披缝、飞边残余、内腔清洁度等,应符合需方图样、技术要求双方订货协定。
除另有规定外,铸件均以铸态交货。
铸件的缺陷不允许有影响铸件使用性能的缺陷存在,如裂纹、冷隔、缩孔等。
铸件加工面上允许存在加工范围内的表面缺陷。
铸件非加工面上及铸件内部允许存在的缺陷种类、范围、数量应符合需方图样、技术要求或供需双方的订货协定。
特殊要求需方对磁粉探伤、超声波检验、射线检验等有要求时,由供需双方商定。
5.取样拉伸试样单铸试棒单铸试棒应在与铸件相同的铸型或导热性能相当的铸型中单独铸造。
试棒的落砂温度一般不应超过500℃。
单铸试棒的形状和尺寸见图和图。
单铸试棒的形状和尺寸也可由供需双方商定。
单铸试棒应与它所代表的铸件用同一批次的铁液浇注,并在该批次铁液的后期浇注。
图3 单铸试棒试样附铸试样当铸件重量等于或超过2000,而且壁厚大于200时,优先采用附铸试块,……。
附铸试块的尺寸和位置由供需双方商定。
附铸试块在铸件上的位置应考虑到铸件形状和浇注系统的结构形式,以避免对邻近部位的各项性能产生不良影响,并以不影响铸件的结构性能、铸件外观质量以及试块致密性为原则。
如铸件需热处理,附铸试样应在铸件热处理后再从铸件上切开。
除非供需双方另有特殊规定,附铸试样的形状和尺寸如图和。
本体试样若需方对铸件本体取样位置、试样尺寸和抗拉强度值有明确规定时,应按需方图样、技术要求执行。
需方应向供方指明铸件本体取样位置,如果需方没有指明铸件本体取样位置,供方应依据铸件的重要截面厚度自行选择本体试样的直径。
本体试样的直径可以等于或小于1/3壁厚且大于1/5壁厚。
本体取样的位置、铸件本体力学性能、检测频次和数量,由供需双方商定。
本体取样的位置也可以是铸件的平均壁厚处。
硬度试块硬度试块一般取自单铸试棒试样上。
硬度也可以在供需双方商定的铸件某位置上测试。
如果铸件需要热处理,硬度试块应在铸件热处理后切取。
光谱化学分析试样光谱化学分析试样形状和尺寸见图5。
冲击试块球墨铸铁件需要做冲击试样时,冲击试块的形状和尺寸见图6所示。
取样批次的构成和检验数量取样批次的构成由同一包处理过的铁液浇注的铸件作为一个批量,构成一个取样批次。
连续浇注时,2小时浇注的铸件作为一个批次。
经供需双方同意,取样的批次可以变动。
在某一时间间隔内,如发生炉料的改变、工艺条件的变化或要求的化学成分有变化时,在此期间连续熔化的铁液浇注的所有铸件,无论时间间隔有多短,都作为一个取样批次。
取样次数每个取样批次应至少取一次拉伸试样。