传动轴发展.
汽车底盘发展史讲解

汽车行驶过程中,需要经常改变行驶方向, 即所谓的转向,这就需要有一套能够按照司机意 志使汽车转向的机构,它将司机转动方向盘的动 作转变为车轮(通常是前轮)的偏转动作。
汽车转向系的发展
内燃汽车发明者本次在他发明的三轮汽车上首次采用 了所谓的齿轮齿条式转向器,但是靠一根操纵杆控制,类 似舵柄;
汽车轮胎的发展
1895年,法国人米其林把1888年发明的自行车充气轮胎经 过改良后安装在汽车上,参加巴黎至波尔多的比赛,才出 现首辆使用这种轮胎的汽车。 1911年,美国哈德门轮胎和橡胶制品公司的财务管 理员菲利普,在亚利山大·施特劳斯的文件中发现了施特 劳斯于1894年的一次发明,即可织物在一个方向上拉伸 而在另一个方向上却不变。于是他们公司利用这一发明, 推出了成套的内外胎,即用橡胶和织物织成外胎,里面装 上橡胶内胎。至此,充气轮胎取得了完全的成功,汽车才 真正穿上了现代化的"鞋子"。
自从汽车发明以来,工程师们就一直在研究如何将汽 车的悬架系统设计得更好。最初的汽车悬架系统是采用马 车的弹性钢板,效果当然不会很好。因此,汽车最早采用 的应是钢板弹簧非独立悬架。
1900年美国人哈德福特制成了第一个汽车减振器, 并将它装在奥兹莫比尔轿车上。
1921年英国得利兰德汽车公司生产第一个使用扭杆 弹簧悬架的汽车。
汽车底盘发展史
汽车传动系的发展
汽车传动系的发展
汽车刚刚问世时,人们大多采用后置发动机、 后轮驱动的方式,从发动机到后轮之间分散地采 用链轮和齿轮传递动力。
1893年美国的杜里埃兄弟在汽车上首次使用 了干式单片离合器,同时采用了差速器后桥;
1894年法国的本哈特和拉瓦索发明了齿轮变 速器;
1898年法国雷诺汽车公司首次使用了传动轴; 1902年皮尔里斯发明了汽车万向节; 1913年美国派克特汽车推广应用了螺旋锥齿 轮主减速器后桥。
传动轴行业现状及未来发展思路-概述说明以及解释

传动轴行业现状及未来发展思路-概述说明以及解释1.引言1.1 概述概述部分的内容可以包括以下内容:传动轴作为机械传动系统的核心元件之一,扮演着将引擎动力传递到车轮的关键角色。
传动轴行业作为汽车行业的重要组成部分,一直以来都在不断发展演变。
本文将通过对传动轴行业现状及未来发展思路的研究,旨在探讨该行业的市场规模、增长趋势、主要竞争对手和市场份额,并提出相应的技术创新、产品升级、市场拓展和合作发展的思路,以期为传动轴行业的可持续发展寻找更多机遇和契机。
目前传动轴行业的市场规模逐渐扩大,随着汽车市场的不断增长,对于传动轴的需求也在逐年上升。
同时,随着技术的不断进步和创新,传动轴的性能、质量和可靠性也在不断提升,满足了消费者对于汽车驾驶的安全性和舒适性的要求。
然而,传动轴行业仍面临一些挑战。
首先,市场竞争激烈,主要竞争对手众多,各家企业之间的市场份额竞争激烈。
其次,技术创新的速度仍然不够快,产品升级和改进的空间有限。
此外,市场拓展和合作发展也是制约传动轴行业进一步发展的重要因素。
因此,为了推动传动轴行业的持续发展,我们需要加强技术创新,积极推动产品升级,提高产品质量和性能。
同时,我们还需要加强市场拓展和合作发展,寻找更多的合作伙伴,拓宽销售渠道,提高市场份额。
综上所述,传动轴行业具有广阔的市场前景和潜力,但也面临着一系列的挑战。
通过不断的技术创新和市场拓展,相信传动轴行业在未来会取得更大的发展,为整个汽车行业的发展做出更大贡献。
1.2文章结构文章结构部分的内容可以包括以下内容:文章结构部分主要介绍了本文的大致框架和内容安排,下面将对各个部分进行简要介绍。
1. 引言部分:在引言中,我们将对传动轴行业的背景和重要性进行概述,介绍传动轴在各个领域的应用和发展现状。
同时,我们也会说明本文的结构和目的,从而引导读者对文章内容的理解和阅读。
2. 正文部分:本文的主要内容将分为两部分。
2.1 传动轴行业现状:在本节中,我们将详细分析传动轴行业的市场规模和增长趋势。
汽车传动轴研究报告

汽车传动轴研究报告概述汽车传动轴作为汽车的重要部件之一,在汽车运动中起着关键的作用。
本文将通过对汽车传动轴的研究,深入探讨其结构、原理、功能以及发展趋势。
传动轴的定义传动轴是汽车动力传动系统中的一个关键组成部分,用于将发动机的动力传递到驱动轮上,从而实现车辆的运动。
传动轴一般由金属材料制成,承受着转矩和扭转力的作用。
传动轴的结构传动轴一般包括轴心线、轴承支撑点、连接部件和平衡装置等组成部分。
轴心线是传动轴的基准线,通过轴心线的位置确定传动轴的安装方式。
轴承支撑点是传动轴的固定点,用于支撑传动轴的运动。
连接部件通常是通过与传动轴相连接的方式,将传动轴与其他动力元件连接在一起。
平衡装置则是为了降低传动轴的振动和噪音,提高汽车的稳定性和舒适性。
传动轴的原理传动轴通过发动机产生的动力,将扭矩传递到驱动轮上。
传动轴的工作原理可以简单分为以下几个步骤: 1. 发动机产生动力; 2. 动力通过传动装置传递至传动轴;3. 传动轴将动力传递到驱动轮。
传动轴的功能传动轴作为汽车动力传递的核心部分,具有以下几个功能: - 承受动力和扭转力;- 传递动力至驱动轮; - 保持转速稳定; - 减少振动和噪音。
传动轴的发展趋势随着汽车技术的不断进步和发展,传动轴也在不断改进和演进。
未来传动轴的发展趋势主要有以下几个方向: 1. 轻量化:采用更先进的材料和制造工艺,减轻传动轴的重量,提高车辆的燃油经济性和性能。
2. 高效化:通过改进传动轴的结构和传动装置,提高动力传递的效率,减少能量损耗。
3. 智能化:引入电动传动轴和智能控制系统,提高传动轴的响应速度和精确性,优化车辆的驾驶性能和舒适性。
结论通过对汽车传动轴的研究,我们深入了解了它的结构、原理、功能以及发展趋势。
传动轴作为汽车动力传递的重要组成部分,对于车辆的性能和安全起着至关重要的作用。
随着技术的发展,我们可以期待传动轴在未来的应用上有更大的突破和创新。
参考文献1.张三, “汽车传动轴的研究进展”,《汽车工程学报》,2020.2.李四, “传动轴轴承优化设计”,《机械制造与自动化》,2019.。
传动轴国内外发展现状

传动轴国内外发展现状在国内市场发展方面,中国汽车市场规模不断扩大,汽车销量稳步增长。
这为传动轴行业提供了广阔的市场需求和发展空间。
据中国汽车工业协会数据显示,2019年中国汽车产销量达到了2571.11万辆,同比增长0.8%。
汽车销量增长的背后,对传动轴的需求也在不断增加。
传动轴生产企业积极扩大产能,提高生产效率,以满足市场需求。
传动轴技术不断创新和提升。
随着汽车动力系统的不断发展,传动轴在结构设计、材料选用、制造工艺等方面都有了重大改进。
传动轴的结构形式从传统的实心轴、中空轴发展到可以调节长度的伸缩式传动轴。
这种结构设计可以有效适应车辆在运动过程中的变化,提高传动效率和稳定性。
同时,传动轴采用了更轻量化的材料,如高强度合金钢、铝合金等,以减轻整车质量,提高燃油经济性。
在制造工艺方面,采用了更先进的电子控制技术和自动化生产设备,提高了传动轴的加工精度和质量稳定性。
环保和节能要求的提高也推动了传动轴行业的发展。
随着全球对环境保护和能源消耗的关注度不断提高,对于汽车动力系统的要求也越来越严格。
传动轴作为汽车动力系统的重要组成部分,对其节能减排性能有着更高的要求。
因此,传动轴生产企业积极研发和应用新型技术,如双离合器传动系统、纯电动汽车传动系统等,以提高传动效率和减少能量损失。
此外,传动轴制造过程中也采用了更环保的工艺和材料,以减少对环境的污染。
国际市场的开拓是中国传动轴行业发展的重要方向。
随着中国汽车制造业的崛起,中国传动轴产品的质量和技术水平得到了国际市场的认可。
许多中国传动轴生产企业开始向海外市场拓展,并与国外企业进行技术合作和品牌合作。
这些举措有助于中国传动轴企业树立国际形象,提高产品的竞争力和市场份额。
同时,也促进了国际市场上传动轴行业的发展。
传动轴行业在国内外都取得了重要的进展和发展。
随着汽车市场的不断扩大和升级,传动轴的需求与日俱增。
传动轴技术的创新和环保要求的提高为行业发展提供了新机遇和挑战。
国内外轴承钢的现状与发展趋势
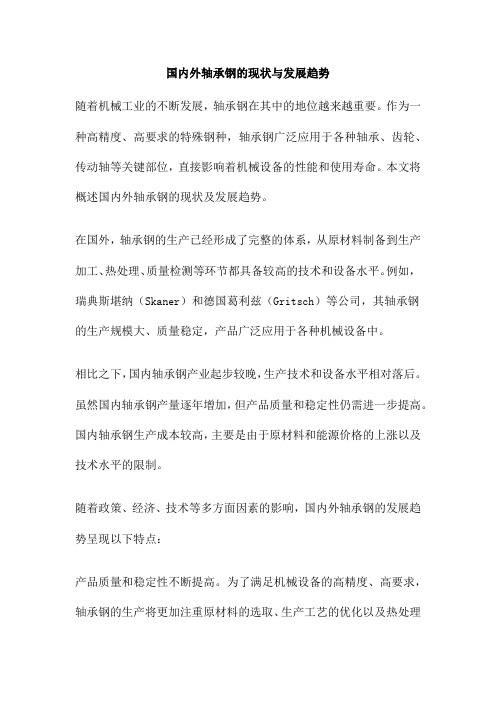
国内外轴承钢的现状与发展趋势随着机械工业的不断发展,轴承钢在其中的地位越来越重要。
作为一种高精度、高要求的特殊钢种,轴承钢广泛应用于各种轴承、齿轮、传动轴等关键部位,直接影响着机械设备的性能和使用寿命。
本文将概述国内外轴承钢的现状及发展趋势。
在国外,轴承钢的生产已经形成了完整的体系,从原材料制备到生产加工、热处理、质量检测等环节都具备较高的技术和设备水平。
例如,瑞典斯堪纳(Skaner)和德国葛利兹(Gritsch)等公司,其轴承钢的生产规模大、质量稳定,产品广泛应用于各种机械设备中。
相比之下,国内轴承钢产业起步较晚,生产技术和设备水平相对落后。
虽然国内轴承钢产量逐年增加,但产品质量和稳定性仍需进一步提高。
国内轴承钢生产成本较高,主要是由于原材料和能源价格的上涨以及技术水平的限制。
随着政策、经济、技术等多方面因素的影响,国内外轴承钢的发展趋势呈现以下特点:产品质量和稳定性不断提高。
为了满足机械设备的高精度、高要求,轴承钢的生产将更加注重原材料的选取、生产工艺的优化以及热处理技术的提升。
通过引进先进的生产设备和工艺技术,提高轴承钢产品的质量和稳定性。
生产成本降低。
为了提高轴承钢的市场竞争力,降低生产成本成为关键。
通过提高生产设备的利用率、优化原材料的采购渠道以及强化生产管理等措施,降低轴承钢的生产成本。
多元化的应用领域。
随着机械工业的发展,轴承钢的应用领域将越来越广泛。
除了传统的轴承、齿轮、传动轴等部位,轴承钢还将应用于航空航天、高速列车、石油化工等领域。
这些领域对轴承钢的性能和质量要求更高,将进一步促进轴承钢技术的发展。
环保和节能。
随着全球环保意识的提高,轴承钢的生产将更加注重环保和节能。
采用绿色生产工艺、降低能源消耗、减少废弃物排放等措施,实现轴承钢生产的可持续发展。
轴承钢作为机械工业的关键材料,其生产技术和产品质量直接关系到机械设备的性能和使用寿命。
目前,国外轴承钢的生产已经具备较高的技术和设备水平,而国内轴承钢产业仍有较大的发展空间。
传动轴发展

传动轴发展传动轴发展一背景汽车是最普通的代步、运输工具,许多国家均将汽车工业作为其重要的支柱产业。
面对资源和环境的严峻挑战,推进汽车轻量化以降低油耗,一直是汽车工业发展的主题。
复合材料因具有加工能耗低, 轻质高强, 可设计性强, 耐锈蚀, 成型工艺性好等优点, 成为汽车工业以塑代钢的理想材料。
汽车用材料在经历了通用塑料、工程塑料时代之后, 20世纪九十年代进人复合材料时期。
通用汽车公司1953年生产的世界上第一辆复合材料汽车车身汽车Chevrolet Corvette,敲开了复合材料在汽车领域的应用,自推出此款车型以来通用汽车公司目前已销售130余万辆,此款车型采用的是玻璃纤维增强树脂复合材料。
汽车复合材料的应用主要经历了两个时期:在20世纪70年代开始,由于SMC材料的成功开发和机械化模压技术以及模内涂层技术的应用,促使玻璃钢/复合材料在汽车应用的年增长速度达到25%,形成汽车玻璃钢制品发展的第一个快速发展时期;到20年代90年代初,随着环保和轻量化、节能等呼声越来越高,以GMT(玻璃纤维毡增强热塑性复合材料)、LFT(长纤维增强热塑性复合材料)为代表的复合材料得到了迅猛发展,主要用于汽车结构部件的制造,年增长速度达到10~15%,掀起第二个快速发展时期。
作为新材料前沿的复合材料逐步替代汽车零部件中的金属产品和其它传统材料,并取得更加经济和安全的效果。
据统计,汽车用复合材料已占全球复合材料总量的23%以上,并且成逐步上升的趋势。
美国、日本、欧洲的德国,意大利等发达国家是车用复合材料的主要国家,全球汽车用增强塑料制品的市场规模为每年454万吨,其中美国达到172 万吨,欧洲达到136万吨。
目前,德国每辆汽车平均使用的纤维增强塑料制品近300kg,占汽车总消费材料的22%左右,日本每辆汽车平均使用的纤维增强塑料制品达100kg,约占汽车材料消费总量的7.5%。
其汽车用复合材料部件制造的整体技术水平高,大量采用SMC/BMC材料,采用流水线作业方式,机械化、自动化程度高,产品质量好,经济效益高。
石宝枢:开创汽车传动轴新时代

石宝枢:开创汽车传动轴新时代创新是企业生存和发展的灵魂,也是企业快速发展的核心价值。
现任浙江众达传动股份有限公司董事、总工程师石宝枢,站在整车、汽车零部件行业发展的高度,经不断探索、潜心钻研、奋力攻关、努力实践,对各种汽车等速万向节及等速万向节传动轴总成等产品和技术,进行了一系列革命性的创新与突破,获得了累累硕果。
标签:等速万向节;传动轴;创新等速万向节及等速万向节传动轴总成是各种汽车,特别是轿车传动系统中至关重要、高科技含量的零部件。
其主要功能是:当主、从动轴同时有一定角位移(或轴向位移)等复杂工况下,仍能平稳、可靠、灵活、精确地传递运动和转矩。
等速万向节传动轴总成多用于汽车的前(或后)桥,通过它的机械传动,实现汽车的驱动、行走及转向等功能。
随着汽车产业的快速发展,等速万向节及等速万向节传动轴总成产品,国内外市场需求量巨大。
在我国,等速万向节、等速万向节传动轴总成及相关(或相近)产品和产业,呈高速发展的态势。
但是,由于等速万向节及等速万向节传动轴总成产品的研发、设计、制造、检测和试验等,几乎所有的厂家都是拿来主义的盲目照搬国外样品和技术,产品设计的主要模式是测绘国外样品的逆向设计,制造工艺亦是盲目的仿制。
基本上是处在无研发能力、无核心技术、无自主知识产权、无创新的原始阶段。
以传统的六沟道和三球销式等速万向节等为主体结构的汽车传动轴总成,在长时间的使用中,大范围出现了承载能力不足、不耐冲击、体积大、结构不紧凑、噪声大、温升快等结构性的不足和缺陷,始终难以得到根本的解决。
严重制约了我国该类产品的科技进步、产品质量的提高和产业发展。
为彻底解决上述问题,国内外著名的汽车传动轴专家,现任浙江众达传动股份有限公司董事、总工程师石宝枢,站在整车、汽车零部件行业发展的高度上,经不断探索、潜心钻研、奋力攻关、努力实践,对各种汽车等速万向节及等速万向节传动轴总成等产品和技术,进行了一系列革命性的创新与突破,获得了累累硕果。
2012-2016年中国汽车传动轴产业市场专题调研及投资方向分析报告

2012-2016年中国汽车传动轴产业市场专题调研及投资方向分析报告51报告在线2012年11月目录第一章汽车传动轴产业概述 (8)第一节汽车传动轴产业定义 (8)第二节汽车传动轴产业发展历程 (8)第三节汽车传动轴分类情况 (12)第四节汽车传动轴产业链分析 (13)一、产业链模型介绍 (13)二、汽车传动轴产业链模型分析 (13)第二章中国汽车传动轴产业发展环境分析 (15)第一节中国经济环境分析 (15)一、宏观经济 (15)二、工业形势 (16)三、固定资产投资 (17)第二节汽车传动轴产业相关政策 (18)一、国家“十二五”产业政策 (18)二、其他相关政策 (19)第三节中国汽车传动轴产业发展社会环境分析 (21)一、居民消费水平分析 (21)二、工业发展形势分析 (23)第三章全球汽车传动轴市场分析 (26)第一节美国 (26)第二节西欧 (27)第三节日本 (28)第四节新兴市场 (28)第五节重点厂商分析 (30)第四章中国汽车传动轴产业供需现状分析 (31)第一节汽车传动轴产业总体规模 (31)第二节汽车传动轴产能概况 (31)一、2009-2011年产能分析 (31)二、2012-2016年产能预测 (32)第三节汽车传动轴产量概况 (32)第四节汽车传动轴市场需求概况 (33)一、2009-2011年市场需求量分析 (33)二、2012-2016年市场需求量预测 (33)第五节进出口分析 (34)第五章中国汽车传动轴产业总体发展状况 (35)第一节中国汽车传动轴产业规模情况分析 (35)一、产业单位规模情况分析 (35)二、产业人员规模状况分析 (35)三、产业资产规模状况分析 (36)四、产业市场规模状况分析 (36)第二节中国汽车传动轴产业财务能力分析 (37)一、行业盈利能力分析与预测 (37)二、行业偿债能力分析与预测 (37)三、行业营运能力分析与预测 (37)四、行业发展能力分析与预测 (37)第三节产业竞争结构分析 (38)一、现有企业间竞争 (38)二、潜在进入者分析 (38)三、替代品威胁分析 (39)第四节国际竞争力比较 (39)第五节汽车传动轴企业竞争策略分析 (40)第六章2011年我国汽车传动轴产业重点区域分析 (42)第一节华北 (42)第二节东北 (42)第三节华东 (43)第四节西南 (44)第五节西北 (45)第七章汽车传动轴产业市场分析 (46)第一节重点产品 (46)一、市场占有率 (46)二、市场应用及特点 (47)三、供应商分析 (47)第二节技术分析 (47)一、技术现状 (47)二、创新技术研发及方向 (48)第三节产品细分 (49)第四节市场价格分析 (49)第八章汽车传动轴国内重点生产厂家分析 (50)第一节许昌远东传动轴有限公司 (50)一、企业基本概况 (50)二、企业经营与财务状况分析 (50)三、企业竞争优势分析 (51)四、企业未来发展战略与规划 (51)第二节上海纳铁福传动轴有限公司 (52)一、企业基本概况 (52)二、企业经营与财务状况分析 (52)三、企业竞争优势分析 (53)四、企业未来发展战略与规划 (53)第三节东风汽车传动轴有限公司 (54)一、企业基本概况 (54)二、企业经营与财务状况分析 (54)三、企业竞争优势分析 (55)四、企业未来发展战略与规划 (56)第四节江苏宇山万向传动轴制造有限公司 (56)一、企业基本概况 (56)二、企业经营与财务状况分析 (57)三、企业竞争优势分析 (57)四、企业未来发展战略与规划 (58)第五节北京北汽远东传动部件有限公司 (58)一、企业基本概况 (58)二、企业经营与财务状况分析 (58)三、企业竞争优势分析 (59)四、企业未来发展战略与规划 (59)第九章2012-2016年汽车传动轴产业发展趋势及投资风险分析 (61)第一节当前汽车传动轴市场存在的问题 (61)第二节汽车传动轴未来发展预测分析 (61)一、2012-2016年中国汽车传动轴产业发展规模 (61)二、2012-2016年中国汽车传动轴产业技术趋势预测 (62)三、总体产业“十二五”整体规划及预测 (62)第三节2012-2016年中国汽车传动轴产业投资风险分析 (66)一、市场竞争风险 (66)二、原材料压力风险分析 (66)三、技术风险分析 (66)四、政策和体制风险 (67)五、外资进入现状及对未来市场的威胁 (68)第四节专家建议 (69)图目录图1-碳纤维传动轴使用进展 (10)图2-传动轴长度与临界转速的关系 (11)图3-金属传动轴和CFRP传动轴对比示意图 (12)图4-产业链模型分析 (13)图5-汽车传动轴产业链模型分析 (13)图6-2011-2012年国内生产总值同比增长速度 (16)图7-2011-2012年规模以上工业增加值增速(月度同比) (17)图8-固定资产投资(不含农户)同比增速 (18)图9-居民消费价格同比变化情况 (23)图10-2011年我国城镇居民收入差距 (24)图11-2012年前三季度城镇居民人均可支配收入实际增长速度 (25)图12-2012年前三季度农村居民人均收入实际增长速度 (25)图13-2012年1-8月美国汽车生产情况 (26)图14-1-7月西欧汽车生产情况 (27)图15-2012年1-7月巴西汽车销售情况 (28)图16-2012年1-7月俄罗斯汽车销售情况 (29)图17-2012年7月印度汽车生产情况 (29)图18-2009-2011年中国传动轴市场规模 (31)图19-2009-2011年中国传动轴行业产能分析 (31)图20-2012-2016年传动轴行业市场容量 (32)图21-2009-2011年中国传动轴行业产量分析 (32)图22-2009-2011年中国传动轴市场需求量 (33)图23-2012-2016年中国传动轴市场需求量预测 (33)图24-2009-2011年中国传动轴产品进出口规模 (34)图25-2009-2011年中国传动轴行业企业数 (35)图26-2009-2011年中国传动轴行业从业人员规模 (35)图27-2009-2011年中国传动轴行业资产规模 (36)图28-2009-2011年中国传动轴行业市场规模 (36)图29-2011年远东传动销售收入及同比增长 (51)图30-2009-2011年上海纳铁福销售收入及同比增长 (52)图31-2009-2011年东传公司销售收入及同比增长 (54)图32-2009-2011年江苏宇山万向销售收入及同比增长 (57)图33-2009-2011年北汽远东销售收入及同比增长 (59)图34-2012-2016年传动轴行业市场容量 (61)表目录表1-2011-2012年我国国民经济(GDP)运行情况 (15)表2-2011-2012年我国居民消费价格指数CPI情况 (21)表3- 2012年1-7月日本汽车生产情况 (28)表4-传动轴行业盈利能力指标 (37)表5-传动轴行业偿债能力指标 (37)表6-传动轴行业营运能力指标 (37)表7-传动轴行业发展能力指标 (37)表8-汽车零部件及配件制造登记注册类型 (68)表9-汽车零部件及配件制造控股类型 (69)第一章汽车传动轴产业概述第一节汽车传动轴产业定义传动轴是由轴管、伸缩套和万向节组成。
汽车传动系统ppt
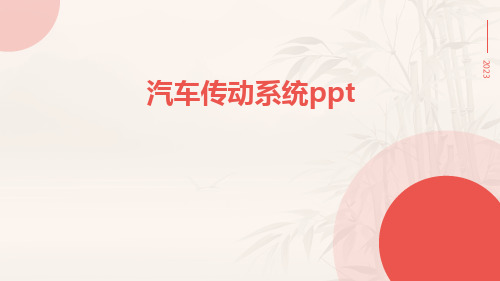
02
汽车发动机系统
发动机的基本构造及工作原理
发动机的基本构造
发动机是汽车的动力源,由曲柄连杆机构、配气机构、燃油供给系统、润滑系统 、冷却系统和点火系统等组成。
工作原理
发动机通过将燃料燃烧产生的热能转化为机械能,推动活塞运动,从而产生动力 。
发动机的性能指标及影响因素
性能指标
主要包括功率、扭矩、油耗、排放等。
调整间隙
定期调整离合器间隙,以 保证其正常工作。
06
汽车传动系统的发展趋势与挑战
新能源汽车对传统汽车传动系统的挑战
01
驱动方式的改变
新能源汽车采用电力驱动方式,改变了传统汽车燃油发动机的传动方
式,对汽车传动系统带来挑战。
02
电池技术的瓶颈
新能源汽车的电池技术尚未完全成熟,电池的续航里程、充电速度和
2023
汽车传动系统ppt
目录
• 汽车传动系统概述 • 汽车发动机系统 • 汽车变速器系统 • 汽车传动轴系统 • 汽车离合器系统 • 汽车传动系统的发展趋势与挑战
01
汽车传动系统概述
汽车传动系统的定义与组成
汽车传动系统的定义
汽车传动系统是车辆的动力传输系统,它负责将发动机产生 的动力传递到车轮,从而驱动车辆行驶。
定期检查
定期检查传动轴的连接处是否 松动、轴承是否损坏等。
更换润滑油
定期更换传动轴的润滑油,保持 传动轴的润滑。
避免超载
避免长时间超载行驶,防止对传动 轴造成过大的负荷。
05
汽车离合器系统
离合器的分类及工作原理
离合器的分类
机械式离合器、液压式离合器、电磁式离合器等。
工作原理
通过机械、液压或电磁方式传递发动机动力,控制传动系统的接合和分离,以保 证车辆的平稳起步和换挡。
传动轴国内外发展现状

传动轴国内外发展现状
(最新版)
目录
1.传动轴的定义和作用
2.传动轴的分类
3.传动轴在国内外的发展现状
4.传动轴行业面临的挑战和未来发展趋势
正文
一、传动轴的定义和作用
传动轴是汽车传动系统中的关键部件,负责将发动机产生的动力传递给驱动轮,使汽车前进或后退。
根据传动轴的连接方式和结构特点,传动轴可分为多种类型,如实心轴、空心轴、万向节轴等。
二、传动轴的分类
1.根据轴体的结构特点,传动轴可分为实心轴、空心轴和复合轴等。
2.根据连接方式,传动轴可分为固定式传动轴和万向节传动轴。
3.根据驱动方式,传动轴可分为前置引擎前轮驱动、前置引擎后轮驱动和后置引擎后轮驱动等。
三、传动轴在国内外的发展现状
1.在我国,随着汽车产业的迅速发展,传动轴行业市场需求不断扩大。
国内企业不断加大研发投入,提高产品性能和质量,逐步突破国际市场的竞争压力。
2.在国际市场,欧美等发达国家凭借先进的技术和丰富的经验,在传动轴领域占据主导地位。
随着全球汽车产业的逐步融合,国际市场竞争日益激烈。
四、传动轴行业面临的挑战和未来发展趋势
1.面临挑战:随着汽车保有量的持续提升,市场对汽车传动轴的需求逐渐扩大,企业需不断提高产能,满足市场需求;同时,国际市场竞争激烈,企业需要提高产品性能和质量,提升竞争力。
2.未来发展趋势:传动轴行业将朝着轻量化、高性能、智能化的方向发展。
机械齿轮传动装置的制造技术与发展趋势

机械齿轮传动装置的制造技术与发展趋势摘要:机械齿轮传动装置是一种被广泛使用的机器设备,它具有体积小、重量轻、结构紧凑等特点,在现代工业生产中起着重要作用。
随着社会经济和科学技术水平不断发展提高,人们对产品质量要求越来越高,对零件的精度提出了更高标准的要求,所需的技术水平也就更高。
所以就需要我们去研究机械齿轮传动系统来满足其性能需求及工作环境条件下更深层次的加工设计与制造,从而更好地改善机器设备的工作情况,降低工人劳动强度并达到提升生产效率等目的。
关键词:机械;齿轮;传动装置;技术在机械制造业的发展过程中,国外很多国家对于机械齿轮传动装置进行了大量研究,并且取得了一定成果。
例如:日本、法国等发达国家已经将行星轮系作为一种重要结构来使用;美国是最早开始将该技术应用到工业方面的国家之一。
在国内虽然有许多学者对大型传动轴及大转矩器展开过深入分析和实验工作,但是由于我国国情以及相关设备制造厂家与国外先进水平相比存在较大差距,所以还需要进一步完善改进,同时也要采取加强研究力度、加大研发资金投入等措施。
一、机械传动装置技术研究1.1机械传动装置制造技术特点(1)生产效率高,产品质量稳定。
由于加工工艺和方法不同,在相同条件下的零件之间可以相互转换。
因此可以实现高速度、大扭矩等特殊性能要求,也可以具有一定的承载能力。
同时也能满足各种复杂工件对加工精度及表面粗糙度和尺寸公差的需求,而不与其他设备相矛盾。
(2)生产周期短,产品质量稳定且易于调整,可降低成本并提高生产效率。
(3)装置质量要求高。
在机械零件加工过程中需要对其进行严格的控制和检测。
由于齿轮齿面是通过热处理之后才被传递到下一个部位上,所以要求其具有较好的耐磨性、抗磨损性能等特点,对于齿轮来说就需要其有一定硬度以便能达到相应标准,从而可以保证传动装置工作时不会出现卡刀等现象,这也有利于提高生产效率并降低成本。
1.2传动装置制造技术对齿轮传动的影响传动装置的制造技术对齿轮和轴都有着非常重要的影响,主要是通过其本身的结构来决定。
纳铁福 等速万向节传动轴产品技术参数

纳铁福等速万向节传动轴产品技术参数一、产品概述1. 纳铁福等速万向节传动轴是一种用于车辆传动系统的重要零部件,具有传输动力和扭矩的功能。
其主要特点是能够在传动过程中保持传动轴的同心性和等速性,从而保证车辆行驶时的稳定性和平顺性。
2. 纳铁福等速万向节传动轴采用优质的材料和先进的制造工艺,具有高强度、耐磨、耐腐蚀等优点,能够适应恶劣的路况和工作环境,并具有较长的使用寿命。
3. 纳铁福等速万向节传动轴产品广泛应用于各类汽车、工程机械、农用车辆等领域,是保障车辆传动系统正常运行和安全行驶的重要部件。
二、主要技术参数1. 扭矩传输范围:纳铁福等速万向节传动轴产品能够承受的最大扭矩为XXXX Nm,最小扭矩为XXXX Nm。
2. 同心度:在正常工作状态下,纳铁福等速万向节传动轴能够保持的同心度误差小于XXXX mm。
3. 等速性:在各种工作条件下,纳铁福等速万向节传动轴能够保持的等速性误差小于XXXX rad/s。
4. 耐磨性:纳铁福等速万向节传动轴的摩擦副部件经过特殊处理,能够保证在恶劣路况下的耐磨性,使用寿命长。
5. 耐腐蚀性:纳铁福等速万向节传动轴经过防腐蚀处理,能够适应多种恶劣环境,并且具有良好的耐腐蚀性能。
6. 工作温度范围:纳铁福等速万向节传动轴能够在-40℃至+80℃的温度范围内正常工作。
7. 安装尺寸:根据不同车辆型号和传动系统的要求,纳铁福等速万向节传动轴具有多种安装尺寸可供选择,能够满足不同需求。
三、产品优势1. 高可靠性:纳铁福等速万向节传动轴经过严格的质量控制和性能测试,具有高可靠性和稳定的性能。
2. 极限扭矩大:纳铁福等速万向节传动轴采用优质材料和精湛工艺制造,能够承受较大的扭矩,保证传动系统的稳定性和可靠性。
3. 使用寿命长:纳铁福等速万向节传动轴经过耐磨处理和防腐蚀处理,具有较长的使用寿命,能够降低维护成本。
4. 安装方便:纳铁福等速万向节传动轴具有多种安装尺寸可供选择,安装方便,能够快速替换。
轴系 标准术语-概述说明以及解释

轴系标准术语-概述说明以及解释1.引言1.1 概述概述轴系作为机械工程领域中的重要概念,是指用于传递运动和力的一系列相互平行的轴线所组成的系统。
在机械设计和制造中,轴系起着至关重要的作用,它不仅决定了机械装置的结构和性能,还直接关系到运动的平稳性和传递效率。
轴系承载着传递力和扭矩的任务,同时也承受着各种外部力和负载的作用。
为了满足不同的工作条件和需求,轴系的设计和制造需要考虑材料的选择、结构的合理性以及表面处理等因素。
从传统的机械设备到现代的高精度机械系统,轴系一直在不断发展和演变,以适应不同行业和领域的需求。
本文将首先对轴系的定义进行详细解释,并介绍轴系的分类方式。
通过对轴系的概述,读者将能够全面了解轴系的基本概念和作用。
接下来,我们将总结轴系在机械工程中的重要性,并展望轴系在未来的发展趋势。
希望通过本文的内容能够帮助读者更加深入地理解轴系的概念和应用,为机械工程领域的设计与制造提供参考和指导。
同时,也希望本文能够引起读者对于轴系研究领域的兴趣,促进相关领域的进一步发展和创新。
1.2 文章结构文章结构部分的内容可以包括以下内容:文章结构的目的是为了使读者能够清晰地了解整个文章的组织和内容,从而更好地理解和掌握主题。
本文的结构分为引言、正文和结论三个部分。
引言部分主要介绍了整篇文章的背景和意义。
在概述中,将简要描述轴系的定义和其在各个领域的应用重要性。
文章结构部分的目的是为了让读者对整篇文章的组织和内容有初步的了解。
正文部分是整篇文章的主体部分,详细介绍了轴系的定义和分类。
在2.1轴系的定义部分,将对轴系进行准确定义,包括轴系的基本概念、特点以及它在各个领域的具体应用。
在2.2轴系的分类部分,将详细介绍轴系的分类方法,比如按照结构特性、工作原理、用途等方面进行分类,并举例说明各种不同类型的轴系的特点和应用领域。
结论部分对整篇文章进行总结,并展望轴系在未来的发展。
在3.1总结轴系的重要性部分,将再次强调轴系在各个领域的重要性,并总结轴系的特点和应用优势。
传动轴发展

传动轴发展传动轴发展一背景汽车是最普通的代步、运输工具,许多国家均将汽车工业作为其重要的支柱产业。
面对资源和环境的严峻挑战,推进汽车轻量化以降低油耗,一直是汽车工业发展的主题。
复合材料因具有加工能耗低, 轻质高强 , 可设计性强 , 耐锈蚀 , 成型工艺性好等优点 , 成为汽车工业以塑代钢的理想材料。
汽车用材料在经历了通用塑料、工程塑料时代之后 , 20 世纪九十年代进人复合材料时期。
通用汽车公司 1953 年生产的世界上第一辆复合材料汽车车身汽车Chevrolet Corvette ,敲开了复合材料在汽车领域的应用,自推出此款车型以来通用汽车公司目前已销售130 余万辆,此款车型采用的是玻璃纤维增强树脂复合材料。
汽车复合材料的应用主要经历了两个时期:在20 世纪70 年代开始,由于SMC 材料的成功开发和机械化模压技术以及模内涂层技术的应用,促使玻璃钢/复合材料在汽车应用的年增长速度达到 25%,形成汽车玻璃钢制品发展的第一个快速发展时期;到 20 年代 90 年代初,随着环保和轻量化、节能等呼声越来越高,以 GMT (玻璃纤维毡增强热塑性复合材料)、 LFT (长纤维增强热塑性复合材料)为代表的复合材料得到了迅猛发展,主要用于汽车结构部件的制造,年增长速度达到 10~ 15%,掀起第二个快速发展时期。
作为新材料前沿的复合材料逐步替代汽车零部件中的金属产品和其它传统材料,并取得更加经济和安全的效果。
据统计,汽车用复合材料已占全球复合材料总量的 23% 以上,并且成逐步上升的趋势。
美国、日本、欧洲的德国,意大利等发达国家是车用复合材料的主要国家,全球汽车用增强塑料制品的市场规模为每年454 万吨,其中美国达到 172 万吨,欧洲达到 136 万吨。
目前,德国每辆汽车平均使用的纤维增强塑料制品近 300kg,占汽车总消费材料的 22% 左右,日本每辆汽车平均使用的纤维增强塑料制品达 100kg,约占汽车材料消费总量的 7.5% 。
2024年万向节传动轴市场发展现状

2024年万向节传动轴市场发展现状引言万向节传动轴是一种重要的机械传动元件,广泛应用于汽车、机械设备、船舶等领域。
在不同的市场中,万向节传动轴具有不同的应用需求和发展现状。
本文将介绍万向节传动轴市场的总体发展现状,并分析其中的关键驱动因素和发展趋势。
万向节传动轴市场概况万向节传动轴作为一种重要的传动元件,具有承受大扭矩、抗扭转、自适应角偏差等特点,因此得到了广泛的应用。
目前,万向节传动轴市场呈现出以下几个特点:1.市场规模不断扩大:随着汽车、机械设备等行业的不断发展,万向节传动轴的市场需求不断增加。
根据统计数据显示,全球万向节传动轴市场规模从2015年的X亿美元增长到2020年的X亿美元,年均增长率约为X%。
2.应用领域持续多样化:万向节传动轴在汽车、机械设备、船舶等领域中得到广泛应用。
其中,汽车行业是万向节传动轴最主要的应用领域,占据全球市场的大部分份额。
未来随着新能源汽车和智能汽车的发展,对万向节传动轴的需求将进一步增加。
3.技术创新成为市场竞争的关键:万向节传动轴市场竞争激烈,各家企业通过不断的技术创新来提升产品性能和竞争力。
例如,一些企业推出了具有更高扭矩传递能力和更低噪音的新型万向节传动轴产品,得到了市场的认可和好评。
万向节传动轴市场的关键驱动因素万向节传动轴市场的发展受到多种因素的影响。
以下是一些关键的驱动因素:1.经济增长:经济的快速增长将带动汽车和机械设备等行业的需求增加,进而推动万向节传动轴市场的发展。
2.技术进步:随着科技的不断进步,万向节传动轴的设计和制造技术也在不断提升。
新材料、新工艺和新技术的应用,使得万向节传动轴的性能不断得到改善。
3.政策环境:政府对于环保和节能的要求不断提高,推动了新能源汽车的发展。
新能源汽车对于万向节传动轴的需求增加,也为万向节传动轴市场提供了新的发展机遇。
万向节传动轴市场的发展趋势基于对目前万向节传动轴市场的分析,我们可以预见以下几个发展趋势:1.智能化:随着汽车行业的数字化和智能化发展,万向节传动轴也将朝着智能化方向进行升级。
重型直升机及其传动系统的发展分析

重型直升机及其传动系统的发展分析摘要:本文通过整理国内外关于重型直升机发展情况的资料文献,通过对重型直升机目前的发展现状及动力情况的分析与比较,归纳了重型直升机的传动系统的技术特点,总结了重型直升机未来性能需求的发展方向,并分析我国发展重型直升机的重要性。
关键词:重型直升机、传动系统、发展0前言重型直升机通常是指最大起飞质量超过20t的直升机。
重型直升机有很大的内部和外部载荷,因此有高运输效率和许多其他优点,可以完成比较特殊的任务。
在军事领域,重型直升机战术运输融入了整个航天作战系统的深度重要环节。
首要担任战略输送任务,尤其是带领作战队伍,去执行机动和空中作战任务。
在民用范畴,重型直升机在基础设施和救援方面的应用更加重要,它可用于医疗救援、紧急救援、抢险救灾、森林火灾和基础设施建设[1]。
重型直升机是用于国家防护和人民经济开发的战略设施,是一个国家综合实力必不可少的象征,在使用中可以创造庞大的军事和社会效果。
1重型直升机的发展现状目前,世界上只有俄罗斯和美国这两个国家为重型直升机的主要生产国,占领着中心位置,并指导着重型直升机的发展。
最早开始使用重型直升机的国家苏联,该国在20世纪50年代进行了重型直升机技术范畴的大胆试验,并将其改造成一系列几吨重的产品。
美国的重型直升机发展比苏联稍微晚些,但发展更快。
与苏联相比较,美国重型直升机的研发保持了稳定的发展,并逐渐获得了技术研究的地位。
在20世纪50年代至60年代,美国和苏联凭借各自强盛的技术优势研究出了多个型号的重型直升机[2]。
目前,由于俄罗斯对直升机研究的科学研究投资较少,国家级设计公司和企业的资金不足。
在这种情况下,只有对现有的重型直升机进行升级和改进,以满足基本需求。
2009年,基于米-26 T为基础进行了研究制造了米-26T2,首次飞行于2011年4月完成。
2016年4月1日米-26T2直升机的制造开始有效的实行。
在改进和升级现有重型直升机的同时,美国还在加强研制新的重型直升机。
- 1、下载文档前请自行甄别文档内容的完整性,平台不提供额外的编辑、内容补充、找答案等附加服务。
- 2、"仅部分预览"的文档,不可在线预览部分如存在完整性等问题,可反馈申请退款(可完整预览的文档不适用该条件!)。
- 3、如文档侵犯您的权益,请联系客服反馈,我们会尽快为您处理(人工客服工作时间:9:00-18:30)。
传动轴发展一背景汽车是最普通的代步、运输工具,许多国家均将汽车工业作为其重要的支柱产业。
面对资源和环境的严峻挑战,推进汽车轻量化以降低油耗,一直是汽车工业发展的主题。
复合材料因具有加工能耗低, 轻质高强, 可设计性强, 耐锈蚀, 成型工艺性好等优点, 成为汽车工业以塑代钢的理想材料。
汽车用材料在经历了通用塑料、工程塑料时代之后, 20世纪九十年代进人复合材料时期。
通用汽车公司1953年生产的世界上第一辆复合材料汽车车身汽车Chevrolet Corvette,敲开了复合材料在汽车领域的应用,自推出此款车型以来通用汽车公司目前已销售130余万辆,此款车型采用的是玻璃纤维增强树脂复合材料。
汽车复合材料的应用主要经历了两个时期:在20世纪70年代开始,由于SMC材料的成功开发和机械化模压技术以及模内涂层技术的应用,促使玻璃钢/复合材料在汽车应用的年增长速度达到25%,形成汽车玻璃钢制品发展的第一个快速发展时期;到20年代90年代初,随着环保和轻量化、节能等呼声越来越高,以GMT(玻璃纤维毡增强热塑性复合材料)、LFT(长纤维增强热塑性复合材料)为代表的复合材料得到了迅猛发展,主要用于汽车结构部件的制造,年增长速度达到10~15%,掀起第二个快速发展时期。
作为新材料前沿的复合材料逐步替代汽车零部件中的金属产品和其它传统材料,并取得更加经济和安全的效果。
据统计,汽车用复合材料已占全球复合材料总量的23%以上,并且成逐步上升的趋势。
美国、日本、欧洲的德国,意大利等发达国家是车用复合材料的主要国家,全球汽车用增强塑料制品的市场规模为每年454万吨,其中美国达到172 万吨,欧洲达到136万吨。
目前,德国每辆汽车平均使用的纤维增强塑料制品近300kg,占汽车总消费材料的22%左右,日本每辆汽车平均使用的纤维增强塑料制品达100kg,约占汽车材料消费总量的7.5%。
其汽车用复合材料部件制造的整体技术水平高,大量采用SMC/BMC材料,采用流水线作业方式,机械化、自动化程度高,产品质量好,经济效益高。
涉及到轿车、客车、火车、拖拉机、摩托车以及运动车、农用车等所有车种,个别车型的单车平均用量已超过200kg。
采用复合材料制造的汽车零部件种类繁多,主要包括以下几类[图1.]:纤维增强树脂复合材料已被广泛应用于桥车、客车、卡车等的各种覆盖件和结构件上。
主要包括以下应用,车身及车身部件:车身壳体、地板、车门、前端板、阻流板等;悬挂部件:前后保险杠、仪表板等;动力部件:传动轴、导流罩、发动机外壳等;车内装饰:门内饰板、车门把手、仪表盘等。
图1. 碳纤维复合材料在汽车上的应用图2.复合材料在汽车上的应用碳纤维复合材料,具有高强度、高刚性, 有良好的耐蠕变和耐腐蚀性, 与其他纤维增强复合材料相比较更具有前途成为汽车轻量化材料。
用碳纤维取代钢材制造车身和底盘构件, 可减轻质量, 从而节约汽油消耗。
碳纤维复合材料在汽车上的应用, 美国开展的最好, 美国福特公司早已采用制造汽车传动轴、发动机罩、上下悬架臂等零部件,主要应用在结构件和受力件上。
2003年,碳纤维的SMC 复合材料首先成功批量应用于2003款的Dodge Viper车型和mercedes Maybach 车型的系列化生产中。
二汽车传动轴发展历程汽车传动轴作为汽车的一个重要的运动部件,传动轴在不同轴心的两轴间甚至在工作过程中相对位置不断变化的两轴间传递动力,工作环境都比较恶劣。
对传动轴材料性能有着较高的要求,传统的汽车传动轴是金属件。
包括传动轴体(一根或者多根)、万向节(两个或者多个)、滑动花键副、中间支承结构。
对于金属传动轴而言,当两个万向节的中心距离不大于1.5m时,一般采用单根传动轴管。
当距离较远传动轴长度超过1.5m时,通常就要采用两根或者两根以上传动轴管、由三个或者三个以上的万向节连接而成,并且要增设中间结构件。
金属传动轴在使用过程中要定期给其注入润滑油,以保养传动轴,而且注润滑油又脏又累,给驾驶人员增加负担还浪费时间。
并且金属传动轴在使用过程中容易磨损,引起传动轴噪音和发动机能量损失、缩短使用寿命。
为了解决磨损、润滑等缺点,美国最先进行了传动轴涂覆层的研发。
1966年成功申请专利。
此种工艺将尼龙11、尼龙12、尼龙1010粉末结合粘结剂涂覆在金属传动轴的表面。
此种方法对传动轴的性能及其应用有一定的改进,但在部件简化及性能强度上的改善不大。
纤维增强树脂复合材料传动轴的问世及发展正在逐渐解决传统金属传动轴的缺点和完善其性能。
国内传动轴涂敷尼龙的研究已很成熟了,河南许昌传动轴总厂年产尼龙涂敷汽车传动轴总成90万套,其中:轻型汽车传动轴28万套,中型汽车传动轴34万套,重型汽车传动轴28万套。
最早生产碳纤维复合材料的公司是美国摩里逊公司(Morrison Molded Fiber Glass)生产的碳纤维复合材料汽车传动轴。
其生产的传动轴供通用汽车公司载重汽车应用。
采用的碳纤维复合材料可以使原来的两件合并为一件,与钢材相比较质量可以减轻60%,每个传动轴减轻9Kg。
该传动轴采用卓尔泰克公司(ZOLTKE)公司的工业级48K碳纤维,年生产量为60万根传动轴,每根传动轴消耗碳纤维0.68Kg。
福特公司1984年将玻璃纤维复合材料传动轴应用到汽车领域。
此种材料的抗扭曲强度是传统金属材料的两倍以上,扭矩力测试结果为17 793N远大于安全设计值10 000N,作为受力材料玻璃纤维还要逊色于碳纤维复合材料。
考虑到碳纤维使用的成本,早期传动轴主要采用的时玻璃纤维纤维增强树脂或者是玻璃纤维和碳纤维混合的使用,其中碳纤维作为结构层。
GKN公司在1988年开始着手于碳纤维复合材料传动轴的研究,传动轴在Renault Espace Quadra 上的使用开导了碳纤维复合材料汽车传动轴的先驱。
1992年推出的Renault Safrane Quadra 的传动轴由原始的金属三段式发展到了金属和复合材料相连的两节式,减重高达40%,此种传动轴销量较小,仅年产500套。
在Toyota Mark II使用的碳纤维传动轴减重大50%,性能上大大改善了N•V•H。
Audi 80/90 Quattro 首次使用碳纤维传动轴是在1989年,并且使用汽车汽车型号一直延续到了1998年的Audi A4/A8 Quattro,此种型号传动轴年产已达30 000套。
此外碳纤维汽车传动轴在以下车型上均有使用:阿斯顿•马丁DB9,阿斯顿·马丁V8 Vantage Coupe,阿斯顿马丁V12 Vantage,马自达RX-8。
即将上市的2011款奔驰SLS AMG欧翼,碳纤维传动轴的使用也将成为此款车型的标配。
图2.碳纤维传动轴使用进展汽车传动轴的诸多性能参数但中,临界转速是其很重要的一个参数,当传动轴的转速与它的弯曲振动的固有频率相同时,传动轴就会发生共振使传动轴有折断的危险。
常用的计算汽车传动轴临界转速的公式如下:N c = (C / L2)·(E/ñ·I/A)0.5上式中,N c为汽车传动轴的临界转速,C为常数,L为传动轴的长度,I为轴管连接部位力矩,A为万向十字节的连接面积。
对这些限制因素进行分析可以发现,传动轴长度及连接万向节确定的情况下,要提高传动轴的临界转速只能提高E/ñ模量系数,对复合材料而言有高强,高模,弯曲模量可高达100Gpa。
简化的临界转速的计算公式:上式中:l为传动轴的长度,E al、E co为铝和碳纤维/环氧树脂的弹性模量;q al,q co为铝管和碳纤维铺层的单位长度质量。
与金属材料相比较,碳纤维复合材料有着高弹性模量,并且有较小的单位长度质量。
碳纤维复合材料传动轴具有优异力学性能并且具有位移补偿能力,单根轴体管就能达到使用上的要求。
研究表明:轴体直径一致的情况下,汽车传动轴的临界转速为8000 rev/min时传统金属传动轴的长度为1250mm,而碳纤维增强树脂复合材料传动轴的长度可以达到1650mm。
碳纤维复合材料有望实现传动轴的一体化。
图3.传动轴长度与临界转速的关系碳纤维复合材料具有很高的比强度、比模量,实现汽车轻量化的同时可以达到节能省油的目的。
资料表明:碳纤维复合材料传动轴与传统金属传动轴相比较可以至少减轻40%的质量如示意图4,其中包括传动轴两段的金属链接部件。
汽车普通部件质量每减轻1%,可节油1%,类似传动轴等运动部件则可以节油2%。
纤维增强树脂复合材料传动轴已经广泛应用到汽车领域,并且成功的改善了传统金属汽车传动轴的N•V•H(Noise, Vibration, and Harshness)性能,为汽车驾驶者提供了安静怡人的环境。
图4.金属传动轴和CFRP传动轴对比示意图三 成型工艺纤维增强树脂复合材料汽车传动轴成型技术已趋于成熟,常见的成型工艺有拉挤成型,缠绕成型,空心管轧碾成型,压模注塑成型等成型工艺。
3.1缠绕成型图5.缠绕工艺示意图金属传动轴CFRP 传动轴缠绕成型是生产复合材料传动轴最常用的成型工艺。
缠绕成型可以精度的控制纤维的方向和轴体直径,此成型工艺具有高度的自动化生产能力。
GKN公司所提供的复合材料传动轴均由缠绕工艺制备而成。
缠绕成型过程中主要控制的参数有缠绕线型和缠绕角度对传动轴性能的影响,复合材料传动轴轴体与金属连接部件连接的方式。
针对具体的的缠绕成型工艺选举典型的几个实例予以说明。
3.1.1缠绕线型对传动轴体的影响:早期的复合材料传动轴考虑增强纤维的加工成本,增强纤维主要采用玻璃纤维(弹性模量552-827GPa,E-glass、S-glass),基体采用双酚A型环氧树脂:Epi-Rez508,Epi-Rez 510(Celanese Coatings),Epon 828(Shell),固化剂采用酸酐类固化剂(邻苯二甲酸酸酐,)或者胺类固化剂(间本二胺,N,N-二甲基苯胺)。
其中纤维体积含量为55-70%(60%)。
传动轴长度69.5 英寸(176.53cm,1 英寸=2.54 cm),内径:4英寸(10.16cm),由四个缠绕层组成如图6所示,考虑缠绕角度及每层的厚度对传动轴的影响,US 4171626专利考察了轻微改变每缠绕层的厚度和缠绕角,采用了四种方案进行缠绕,并对比了传动轴的基本性能指标。
图5 轴体示意图方案一:Layer No. Thickness/ inch(cm) Fiber reinforcement Fiber angle1 0.02 (0.051) E-glass fiber ±45°2 0.074 (0.188) E-glass fiber 0°3 0.014 (0.036) Carbon fiber0°(2206GPa)4 0.012 (0.030) E-glass fiber 90°Layer No. Thickness/ inch(cm) Fiber reinforcement Fiber angle1 0.020 (0.051) E-glass fiber ±45°2 0.070 (0.178) E-glass fiber ±10°3 0.017 (0.043) Carbon fiber±10°(2206GPa)4 0.012 (0.030) E-glass fiber ±80°方案三:Layer No. Thickness/ inch(cm) Fiber reinforcement Fiber angle1 0.02 (0.051) E-glass fiber ±45°2 0.082 (0.208) E-glass fiber 0°0°3 0.008 (0.020) Carbon fiber(3792GPa)4 0.010 (0.025) E-glass fiber 90°方案四:1 0.020 (0.051) E-glass fiber ±45°2 0.080 (0.203) E-glass fiber ±10°±10°3 0.010 (0.025) Carbon fiber(3792GPa)4 0.010 (0.025) E-glass fiber ±80°四种方案传动轴参数:小角度纤维缠绕层主要为传动轴提供静态弯曲强度,大角度纤维缠绕层为了保障静传动轴态扭曲强度。