炼钢工艺学
炼钢工艺简介(1)
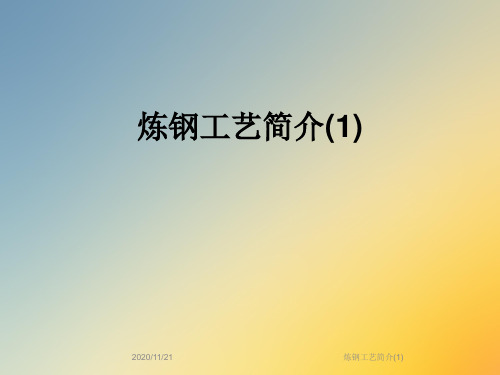
氧气顶吹转炉炼钢法的特点
• 利于自动化生产和开展综合利用 • 氧气顶吹转炉炼钢冶炼时间短,生产率高
,其机械化程度较高,有利于实现生产过程 的自动化,也有利于开展综合利用,如回收 煤气、炉尘(做烧结矿原料)等。
炼钢工艺简介(1)
四、炼钢基本原理
炼钢基本原理
一、什么叫钢
一般把碳小于2.11%的铁碳合金称为钢。 二、什么叫炼钢
炼钢工艺简介(1)
氧气顶吹转炉炼钢法的特点
• 原料消耗少,热效率高、成本低 • 氧气顶吹转炉炼钢的金属消耗一般为1100~1140
公斤/吨钢,稍高于平炉(但在良好燥作情况下 ,金属消耗与平炉接近)。但由于顶吹转炉的热 源是利用铁水本身的物理热和化学热,热效率高 ,不需外加热源,因此在燃料和动力消耗方面均 较平炉、电炉低。由于氧气顶吹转炉炼钢法具有 高的生产率和低的消耗,所以钢的成本也较低。
四、一炼钢技术经济指标
一炼钢在今年前几个月与国内部分同类生产厂指标相比, 在钢铁料消耗、日历作业率上差别较大.而与全国平均水平相 比各项指标均好于同时期的全国平均水平。 ➢ 钢铁料消耗比莱钢高21kg/t,比全国平均低了7.4 kg/t ➢ 日历作业率上比南京低15.56%,比全国平均高2.64% ➢ 氧气消耗比莱钢高3.78m3/t,比全国平均低3.85m3/t。 ➢ 转炉冶炼周期比安阳多1.56min,比全国平均低6.9min。 ➢ 炉衬寿命比莱钢略低。 ➢ 具体对比数据见附表。
➢音频化渣技术:2000年转炉与上海工业大学合作开发的音 频化渣技术,该项技术能根据炉内反应的声音,分析炉渣 的性质,及时指导氧枪枪位控制,促进化渣
炼钢工艺简介(1)
➢ 转炉数据静态模拟控制:2001年,转炉与上海阿塞克自动 化公司合作,开发出转炉数据静态模拟控制系统,使小转炉 炼钢局部实现自动化,降低了劳动强度,改善了生产环境, 提高了转炉作业率及生产效率。
转炉炼钢炼钢工艺学

2023-11-06contents •炼钢的基本原理•转炉炼钢技术•钢的分类与特性•炼钢设备与工艺技术改进•炼钢过程中的质量控制•转炉炼钢技术的发展趋势与挑战•转炉炼钢工艺的前景展望目录01炼钢的基本原理转炉炼钢的氧化反应是通过向熔融的铁水中注入氧气,将铁水中的碳、硅、锰等元素氧化成气体,形成氧化物。
炼钢的物理化学原理氧化反应为了去除铁水中的杂质,需要向熔融的铁水中加入石灰石、萤石等造渣材料,形成炉渣。
造渣为了防止钢水在凝固过程中产生气泡,需要向熔融的钢水中加入脱氧剂,如锰铁、硅铁等,以减少钢水中的氧含量。
脱氧在钢的凝固过程中,固态相变包括铁素体和奥氏体的形成和转变。
这些相变过程受到温度、成分和其他因素的影响。
固态相变在钢的熔炼过程中,液态相变包括碳和其他合金元素的溶解和扩散。
这些相变过程受到温度、成分和其他因素的影响。
液态相变钢的相变原理去除杂质为了提高钢的纯度,需要去除铁水中的杂质,如硫、磷、氮等。
这些杂质可以通过造渣或添加脱氧剂等方式去除。
合金化为了调整钢的成分和性能,需要向熔融的钢水中加入合金元素,如碳、硅、锰等。
这些元素可以通过合金铁块或废钢等方式添加。
钢的纯净化原理02转炉炼钢技术装炉将铁水、废钢等原材料装入炉内,形成铁水包和废钢包。
熔化通过高温加热铁水包和废钢包,将铁水和废钢熔化为液态。
氧化向熔化的铁水中吹入氧气,使其中的碳、硅、锰等元素氧化生成气体,去除杂质。
脱碳继续向熔化的铁水中吹入氧气,降低铁水中的碳含量,使铁的含量增加。
调整成分根据需要加入合金元素,调整铁水的成分以满足产品要求。
出钢将符合要求的铁水倒入钢包中,进行浇铸成钢坯。
转炉炼钢的工艺流程由高炉或直接还原铁熔化而成,是转炉炼钢的主要原料。
铁水由报废的钢铁制品和加工过程中的余料组成,作为添加元素加入到铁水中。
废钢用于氧化反应,将铁水中的杂质氧化成气体,提高铁水的纯度。
氧气根据产品要求,向铁水中加入不同的合金元素,调整成分以满足产品要求。
炼钢8步工艺流程

炼钢8步工艺流程炼钢是将生铁或铸铁中的杂质除去,达到要求的成分和性能的一种冶金工艺。
下面将介绍一种典型的炼钢8步工艺流程。
首先是原料的准备。
在炼钢之前,需要准备适当的原料。
常见的原料包括生铁、铸铁、废钢等。
这些原料需要进行检验和分选,确保其质量符合要求。
第二步是装炉。
将准备好的原料放入炉中,同时加入适量的石灰石和燃料。
石灰石可以吸收硫、磷等有害元素,燃料则提供炉内所需的高温。
第三步是预热。
将炉内的原料进行预热,使其达到较高的温度,以便更好地进行下一步的冶炼过程。
第四步是冶炼。
利用高温和还原剂作用,使炉内的原料发生化学反应,除去其中的杂质,逐步提高钢的成分和性能。
第五步是调温。
在冶炼过程中,需要不断调整炉温和气氛,以确保冶金反应的顺利进行。
调温工作需要根据具体情况进行,通常由冶炼工进行控制。
第六步是出钢。
当炉内的炼钢反应完成后,需要将炼得的钢水从炉中取出。
这一步需要非常谨慎,以防止钢水温度过高或过低,造成不必要的损失或安全事故。
第七步是调质。
出钢后,钢水需要经过进一步的调质处理。
这包括温室冷却、脱硫、脱氧等工艺,以提高钢的硬度、强度和耐腐蚀性能。
最后一步是出炉。
经过上述工艺处理后,钢水变为钢坯。
钢坯需要进行冷却和加工,最终成为制品。
出炉后,还需要对炉内进行清洁和维护,为下一次炼钢作准备。
总的来说,炼钢是一个复杂而严谨的工艺流程,需要专业的设备和技术支持。
通过上述八个步骤的操作,可以获得质量良好的钢材,在冶金行业中起到重要的作用。
钢的冶炼工艺
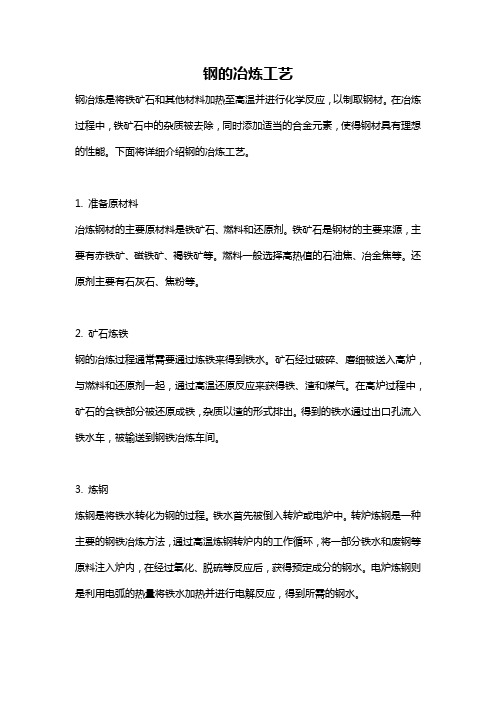
钢的冶炼工艺钢冶炼是将铁矿石和其他材料加热至高温并进行化学反应,以制取钢材。
在冶炼过程中,铁矿石中的杂质被去除,同时添加适当的合金元素,使得钢材具有理想的性能。
下面将详细介绍钢的冶炼工艺。
1. 准备原材料冶炼钢材的主要原材料是铁矿石、燃料和还原剂。
铁矿石是钢材的主要来源,主要有赤铁矿、磁铁矿、褐铁矿等。
燃料一般选择高热值的石油焦、冶金焦等。
还原剂主要有石灰石、焦粉等。
2. 矿石炼铁钢的冶炼过程通常需要通过炼铁来得到铁水。
矿石经过破碎、磨细被送入高炉,与燃料和还原剂一起,通过高温还原反应来获得铁、渣和煤气。
在高炉过程中,矿石的含铁部分被还原成铁,杂质以渣的形式排出。
得到的铁水通过出口孔流入铁水车,被输送到钢铁冶炼车间。
3. 炼钢炼钢是将铁水转化为钢的过程。
铁水首先被倒入转炉或电炉中。
转炉炼钢是一种主要的钢铁冶炼方法,通过高温炼钢转炉内的工作循环,将一部分铁水和废钢等原料注入炉内,在经过氧化、脱硫等反应后,获得预定成分的钢水。
电炉炼钢则是利用电弧的热量将铁水加热并进行电解反应,得到所需的钢水。
4. 精炼炼钢后的钢水还需要进行精炼工艺,以进一步提高钢的纯净度和性能。
常见的精炼方法包括氧气顶吹、真空脱气和脱磷等。
氧气顶吹是通过向钢水中吹入高纯度的氧气,利用氧气与杂质发生的反应将其氧化而去除。
真空脱气则是将钢水置于真空环境下进行处理,以脱除钢水中的氧、氮、氢等元素。
除杂的同时,精炼工艺还可以添加调合剂和合金元素,以调整钢材的性能。
5. 结晶精炼后的钢水被注入连铸机进行结晶过程。
连铸是将熔化的钢水通过结晶器冷却成坯料的过程。
结晶器内部有一套冷却水系统,可以通过冷却水的注入使钢水迅速冷却并结晶。
冷却的钢水成为钢坯,经过切割、定尺等工序,成为标准规格的钢坯。
6. 轧制经过连铸成坯后,钢坯需要进行轧制,以获得所需的钢材产品。
轧制分为粗轧和精轧两个过程。
粗轧是将钢坯经过一系列的轧制机械设备进行压制,使其形状和尺寸逐渐得到调整。
炼钢的工艺流程
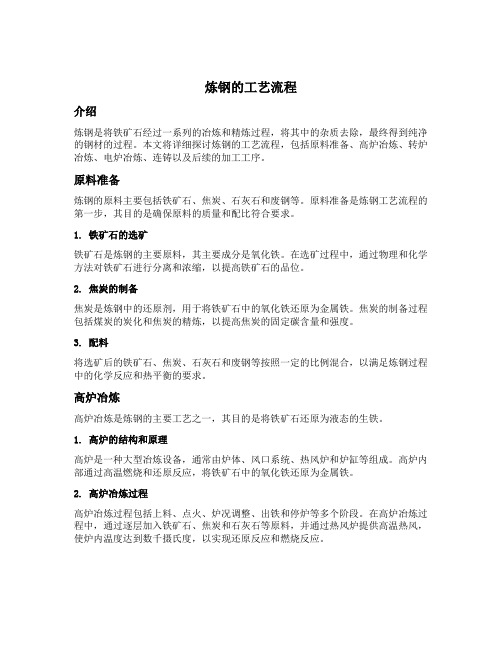
炼钢的工艺流程介绍炼钢是将铁矿石经过一系列的冶炼和精炼过程,将其中的杂质去除,最终得到纯净的钢材的过程。
本文将详细探讨炼钢的工艺流程,包括原料准备、高炉冶炼、转炉冶炼、电炉冶炼、连铸以及后续的加工工序。
原料准备炼钢的原料主要包括铁矿石、焦炭、石灰石和废钢等。
原料准备是炼钢工艺流程的第一步,其目的是确保原料的质量和配比符合要求。
1. 铁矿石的选矿铁矿石是炼钢的主要原料,其主要成分是氧化铁。
在选矿过程中,通过物理和化学方法对铁矿石进行分离和浓缩,以提高铁矿石的品位。
2. 焦炭的制备焦炭是炼钢中的还原剂,用于将铁矿石中的氧化铁还原为金属铁。
焦炭的制备过程包括煤炭的炭化和焦炭的精炼,以提高焦炭的固定碳含量和强度。
3. 配料将选矿后的铁矿石、焦炭、石灰石和废钢等按照一定的比例混合,以满足炼钢过程中的化学反应和热平衡的要求。
高炉冶炼高炉冶炼是炼钢的主要工艺之一,其目的是将铁矿石还原为液态的生铁。
1. 高炉的结构和原理高炉是一种大型冶炼设备,通常由炉体、风口系统、热风炉和炉缸等组成。
高炉内部通过高温燃烧和还原反应,将铁矿石中的氧化铁还原为金属铁。
2. 高炉冶炼过程高炉冶炼过程包括上料、点火、炉况调整、出铁和停炉等多个阶段。
在高炉冶炼过程中,通过逐层加入铁矿石、焦炭和石灰石等原料,并通过热风炉提供高温热风,使炉内温度达到数千摄氏度,以实现还原反应和燃烧反应。
转炉冶炼是炼钢的另一种常用工艺,其主要特点是采用氧气吹炼,将生铁转化为钢水。
1. 转炉的结构和原理转炉是一种承压容器,通常由炉体、氧气吹炼系统和倾炉机构等组成。
转炉内部通过氧气吹炼和搅拌,将生铁中的碳和其他杂质氧化除去,从而得到低碳钢水。
2. 转炉冶炼过程转炉冶炼过程包括预热、装料、吹炼、倾炉和取样等多个阶段。
在转炉冶炼过程中,通过预热转炉、加入生铁和废钢等原料,并通过氧气吹炼和搅拌,使炉内温度升高并实现氧化还原反应,最终得到符合要求的钢水。
电炉冶炼电炉冶炼是一种利用电能将废钢和生铁等原料进行冶炼的工艺,其主要特点是能够灵活调整炉温和合金成分。
炼钢8步工艺流程

炼钢8步工艺流程
《炼钢8步工艺流程》
炼钢是一项重要的冶金工艺,用于生产高质量的钢材。
它需要经过一系列复杂的步骤才能完成。
以下是炼钢的典型8步工艺流程:
1. 预处理:原料是铁矿石和废钢,它们需要进行预处理,去除杂质和控制化学成分。
2. 熔炼:预处理后的原料被放入大型高炉中,通过高温熔炼达到融化状态。
3. 脱硫:在熔炼过程中,加入脱硫剂,以去除铁水中的硫和磷等杂质。
4. 脱氧:通过加入脱氧剂,去除铁水中的氧化物,提高钢的质量。
5. 合金化:根据生产需求,加入合金元素,如铬、镍和钛等,来调整钢的化学成分。
6. 精炼:在精炼炉中,对合金成分进行精密调整,以确保钢的质量和性能。
7. 结晶器:通过冷却处理,控制钢材的晶粒结构,使其获得理想的物理性能。
8. 成型:将高纯度的钢水倒入模具中,冷却后得到成品。
以上8步工艺流程是炼钢的基本工艺,每一步都至关重要,需要高度的技术和经验支持。
通过严格执行这些步骤,可以生产出高品质的钢材,满足各种工业领域的需求。
精选炼钢工艺学
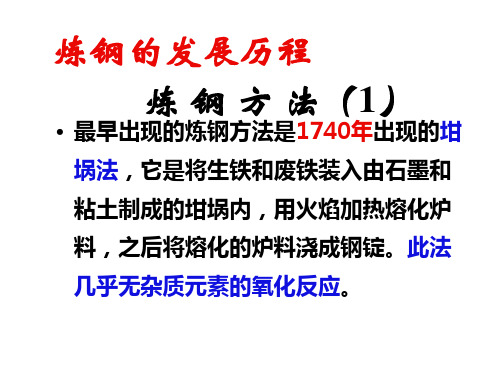
LD/ BOF/ BOP
OBM/ Q-BOP
LD- Q- BOP
2.2 电炉炼钢及其发展
2.2.1 前言
电炉是采用电能作为热源进行炼钢的炉子 的统称。 按电能转换热能方式的差异,电炉可 分为: – 电渣重熔炉—利用电阻热; – 感应熔炼炉—利用电磁感应; – 电 子 束 炉—依靠电子碰撞; – 等 离 子 炉—利用等离子弧; – 电 弧 炉—利用高温电弧,不包括加热炉、
★ 吹炼
前期 温度低于1400-1500℃, [Si], [Mn],
[Fe], [C]开始氧化。
中期 温度高于1500℃,碳氧化速度高。 后期 超过1600℃,碳氧化速度比中期低。
★ 测温、取样化验
★ 脱氧出钢与合金化
★ 溅渣护炉
氧枪位置的确定
◆ 开吹时氧枪枪位采用高枪位,目前是为了早化渣, 多去磷,保护炉衬; ◆在吹炼过程中适当降低枪位的保证炉渣不“返干”, 不喷溅,快速脱碳与脱硫,熔池均匀升温为原则; ◆在吹炼末期要降枪,主要目的是熔池钢水成分和温 度均匀,加强熔池搅拌,稳定火焰,便于判断终点, 同时使降低渣中Fe含量,减少铁损,达到溅渣的要求。
近年电炉短流程的发展及电炉钢产量 的高速增长,也正是由于电炉短流程的经 济效益与环境优势。
我国电炉钢成本高的原因:
◆ 之一废钢暂时短缺,北科大黄务涤指出:印度、 韩国废钢存储量远不如中国,他们采取部分进口 弥补不足,以发展电炉,即废钢不足不是理由;
◆ 之二是中国电价高的不合理,宝钢周渝生指出: 美国电炉用电价格合0.25元/kWh,韩国从中国内 地运煤去发电,电炉用电价格却比我们低,这才 是问题的症结所在。还有不少国家对电炉用电出 于环保原因,还有优惠政策等。
炼钢工艺流程
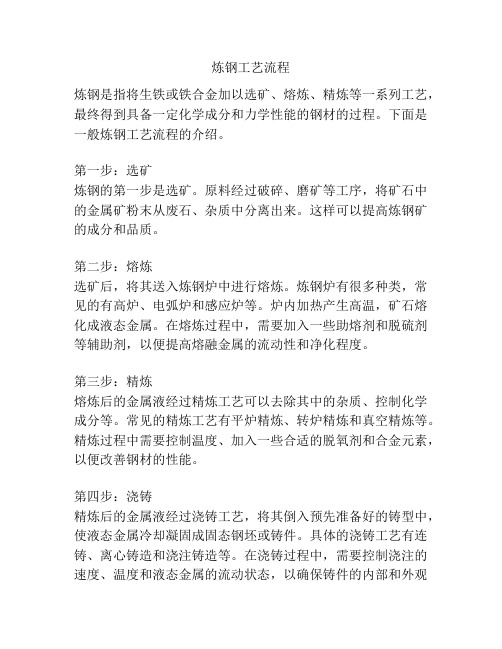
炼钢工艺流程炼钢是指将生铁或铁合金加以选矿、熔炼、精炼等一系列工艺,最终得到具备一定化学成分和力学性能的钢材的过程。
下面是一般炼钢工艺流程的介绍。
第一步:选矿炼钢的第一步是选矿。
原料经过破碎、磨矿等工序,将矿石中的金属矿粉末从废石、杂质中分离出来。
这样可以提高炼钢矿的成分和品质。
第二步:熔炼选矿后,将其送入炼钢炉中进行熔炼。
炼钢炉有很多种类,常见的有高炉、电弧炉和感应炉等。
炉内加热产生高温,矿石熔化成液态金属。
在熔炼过程中,需要加入一些助熔剂和脱硫剂等辅助剂,以便提高熔融金属的流动性和净化程度。
第三步:精炼熔炼后的金属液经过精炼工艺可以去除其中的杂质、控制化学成分等。
常见的精炼工艺有平炉精炼、转炉精炼和真空精炼等。
精炼过程中需要控制温度、加入一些合适的脱氧剂和合金元素,以便改善钢材的性能。
第四步:浇铸精炼后的金属液经过浇铸工艺,将其倒入预先准备好的铸型中,使液态金属冷却凝固成固态钢坯或铸件。
具体的浇铸工艺有连铸、离心铸造和浇注铸造等。
在浇铸过程中,需要控制浇注的速度、温度和液态金属的流动状态,以确保铸件的内部和外观质量。
第五步:热处理浇铸后的钢坯或铸件经过热处理工艺可以改善其组织和性能。
常见的热处理工艺有淬火、回火和正火等。
在热处理过程中,通过控制温度和时间,使钢材达到理想的组织结构和性能。
第六步:终轧经过热处理的钢材需要进一步进行成形和加工,这个过程称为终轧。
终轧可以通过轧制、拉拔、挤压等方式将钢材制成所需的形状和尺寸。
在终轧过程中,钢材需要经过多道工序的轧制和调整,以达到精度和表面质量的要求。
第七步:质量检测最后一步是对成品钢材进行质量检测。
通过对成品钢材的化学成分、力学性能、表面质量和尺寸精度等进行检测,以确保钢材符合标准和客户要求的质量标准。
总的来说,炼钢工艺流程是一个复杂的过程,需要经过多个环节的操作和控制,以确保最终得到具备一定化学成分和力学性能的钢材。
这些工艺流程的运行需要专业知识和技术,以保证钢材的质量和性能。
炼钢的基本工艺流程

炼钢的基本工艺流程
炼钢是一种重要的金属冶炼工艺,通过控制合金元素的含量和结晶形态,使金属获得特定的力学性能和物理性能。
下面将介绍炼钢的基本工艺流程。
原料准备
炼钢的第一步是原料准备,包括铁矿石、焦炭、石灰石等原料。
这些原料需要经过破碎、粉碎、篦筛等预处理工序,确保原料的化学成分和颗粒大小符合生产要求。
炼铁炉炉料装入
原料准备完成后,将各种原料按照一定的比例装入炼钢炉中。
通常,在炼钢炉中装入铁矿石、焦炭和石灰石等原料,熔化后得到炼钢渣。
同时,需要控制炉内氧气含量和燃烧温度,以确保炉料充分燃烧和炼化。
炉内溶解和合金化
随着炉料的加热,炼钢炉中的原料逐渐熔化,并形成炼钢液态金属。
在此过程中,还需要加入合金元素,如铬、钼等,以调控炼钢的成分和性能。
脱气和脱硫
炼钢过程中,金属液态状态下会溶解一定量的氧气和其他气体,因此需要进行脱气处理,通过加入脱气剂去除金属液态中的气体。
同时,炼钢炉中也会生成硫化物,需进行脱硫处理,提高炼钢的质量。
流化床冶炼
流化床是一种特殊的炼钢工艺,通过在炼钢炉中加入流体化砂和空气,使原料在床层中流动,利于传热和物质反应。
流化床冶炼技术具有炼钢速度快、能耗低的特点,逐渐成为炼钢领域的重要发展方向。
以上是炼钢的基本工艺流程,通过控制各项工序,可以获得具有一定性能和质量的炼钢产品。
炼钢工艺的不断改进和创新,将有助于提高炼钢质量和生产效率,推动炼钢工业的发展和进步。
炼钢精炼工艺介绍课件
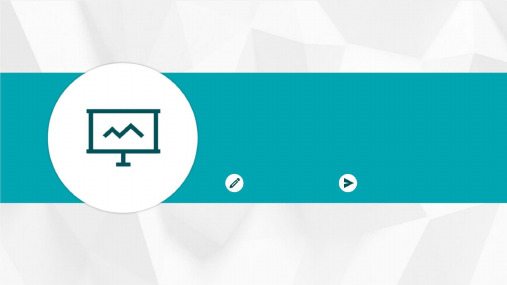
熔化与氧化期
使用电能加热,将生 铁和废钢等材料熔化 为钢水,并使用氧气 吹入钢水,去除杂质, 形成初期钢水。
还原期
使用电能、化学能和 辐射能加热,调整钢 水成分,控制钢水温 度,形成中期钢水。
精炼期
使用不同的精炼剂和 合金元素调整钢水成 分和温度,控制钢水 中气体和夹杂物含量, 形成末期钢水。
浇注期
影响因素
主要因素包括温度、压力、合金元素含量、熔渣 组成等。这些因素会影响化学反应的速度和程度, 进而影响最终产品的性能和质量。
炼钢精炼工艺的选择及优化
不同炼钢精炼工艺的比较及选择
转炉炼钢法
适合大型钢厂,生产效率高,但不适合生 产高精度、高合金钢。
连铸法
提高钢水凝固效率,降低能耗,提高生产 效率。
炉外精炼的主要设备和工艺流程
主要设备
包括钢水罐、真空脱气装置、合金添 加装置、喷粉装置等。
工艺流程
首先将钢水从转炉或电炉转移到钢水 罐中,然后进行真空脱气、合金添加、 喷粉等工序,最后将处理后的钢水返 回转炉或电炉进行二次处理。
炉外精炼过程中的化学反应及影响因素
主要化学反应
包括碳氧反应、脱硫反应、脱氧反应等。
炉外精炼工艺在某钢厂的应用实例
总结词
灵活性、高精度控制、适应性强
VS
详细描述
某钢厂采用炉外精炼工艺,通过使用各种 合金料和脱氧剂等辅助材料,实现了对钢 水成分和温度的精确控制。该工艺具有灵 活性高、适应性强等优点,可根据不同产 品需求进行灵活调整。
还原反应
使用焦炭、石灰等材料与氧化 物反应,生成铁、硅、锰等元 素,调整钢水成分。
合金化反应
添加合金元素与钢水反应,形 成合金元素化合物,调整钢水 成分和温度。
土法炼钢工艺流程

土法炼钢工艺流程土法炼钢是一种古老的炼钢工艺,起源于中国古代。
它是一种以土炉为炼钢设备,以生铁和生铁渣为原料,通过高温熔炼、氧化还原等化学反应,将生铁转化为钢的工艺。
土法炼钢工艺流程复杂,需要严格控制各个环节,下面我们来详细介绍土法炼钢的工艺流程。
1. 原料准备。
土法炼钢的原料主要包括生铁、生铁渣、石灰石、木炭等。
生铁是主要原料,生铁渣是副原料,石灰石用于脱硫,木炭用于提供燃料和还原剂。
这些原料需要经过精确的配比,以确保炼钢过程中的化学反应能够顺利进行。
2. 炉料装入。
炉料装入是土法炼钢的第一步,将原料按一定的配比装入土炉中。
生铁和生铁渣是主要的炉料,石灰石和木炭作为辅助炉料也需要一同装入。
在装入过程中需要注意炉料的均匀分布,以便于后续的加热和化学反应。
3. 加热熔化。
炉料装入后,需要进行加热熔化。
这个过程需要耗费大量的木炭,以提供足够的热量。
在加热的过程中,炉料中的生铁和生铁渣开始熔化,石灰石开始脱硫,产生大量的气体。
这个过程需要持续数小时,直到炉料完全熔化。
4. 氧化还原反应。
炉料完全熔化后,开始进行氧化还原反应。
这个过程是土法炼钢的关键,通过控制氧化还原反应的条件,可以使炉料中的碳、硅、锰等元素发生化学变化,从而将生铁转化为钢。
这个过程需要严格控制炉内氧气的含量和炉温的分布,以确保反应能够顺利进行。
5. 钢水浇铸。
当炉料中的生铁完全转化为钢后,需要进行钢水浇铸。
这个过程需要将炉料中的钢水倒入浇铸模具中,进行冷却凝固,形成钢锭。
在浇铸过程中需要注意控制浇注速度和冷却速度,以确保钢锭的质量。
6. 钢锭处理。
钢锭冷却后,需要进行钢锭处理。
这个过程主要包括除渣、除气、除杂质等工序,以提高钢锭的质量。
除渣是将浇铸过程中产生的氧化物和其他杂质从钢水中去除,除气是将钢水中的气体去除,除杂质是将钢水中的杂质去除。
这些工序需要使用一些特殊的设备和工具,以确保钢锭的质量符合要求。
土法炼钢是一种古老的炼钢工艺,虽然在现代工业中已经被淘汰,但是它仍然具有一定的历史意义和文化价值。
炼钢工艺流程简介
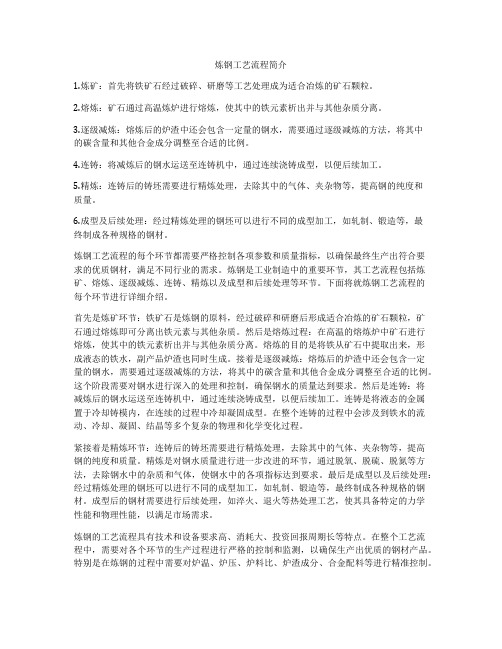
炼钢工艺流程简介1.炼矿:首先将铁矿石经过破碎、研磨等工艺处理成为适合冶炼的矿石颗粒。
2.熔炼:矿石通过高温炼炉进行熔炼,使其中的铁元素析出并与其他杂质分离。
3.逐级减炼:熔炼后的炉渣中还会包含一定量的钢水,需要通过逐级减炼的方法,将其中的碳含量和其他合金成分调整至合适的比例。
4.连铸:将减炼后的钢水运送至连铸机中,通过连续浇铸成型,以便后续加工。
5.精炼:连铸后的铸坯需要进行精炼处理,去除其中的气体、夹杂物等,提高钢的纯度和质量。
6.成型及后续处理:经过精炼处理的钢坯可以进行不同的成型加工,如轧制、锻造等,最终制成各种规格的钢材。
炼钢工艺流程的每个环节都需要严格控制各项参数和质量指标,以确保最终生产出符合要求的优质钢材,满足不同行业的需求。
炼钢是工业制造中的重要环节,其工艺流程包括炼矿、熔炼、逐级减炼、连铸、精炼以及成型和后续处理等环节。
下面将就炼钢工艺流程的每个环节进行详细介绍。
首先是炼矿环节:铁矿石是炼钢的原料,经过破碎和研磨后形成适合冶炼的矿石颗粒,矿石通过熔炼即可分离出铁元素与其他杂质。
然后是熔炼过程:在高温的熔炼炉中矿石进行熔炼,使其中的铁元素析出并与其他杂质分离。
熔炼的目的是将铁从矿石中提取出来,形成液态的铁水,副产品炉渣也同时生成。
接着是逐级减炼:熔炼后的炉渣中还会包含一定量的钢水,需要通过逐级减炼的方法,将其中的碳含量和其他合金成分调整至合适的比例。
这个阶段需要对钢水进行深入的处理和控制,确保钢水的质量达到要求。
然后是连铸:将减炼后的钢水运送至连铸机中,通过连续浇铸成型,以便后续加工。
连铸是将液态的金属置于冷却铸模内,在连续的过程中冷却凝固成型。
在整个连铸的过程中会涉及到铁水的流动、冷却、凝固、结晶等多个复杂的物理和化学变化过程。
紧接着是精炼环节:连铸后的铸坯需要进行精炼处理,去除其中的气体、夹杂物等,提高钢的纯度和质量。
精炼是对钢水质量进行进一步改进的环节,通过脱氧、脱硫、脱氮等方法,去除钢水中的杂质和气体,使钢水中的各项指标达到要求。
转炉炼钢原理及工艺介绍

转炉炼钢原理及工艺介绍引言转炉炼钢是一种常用的钢铁生产工艺,具有高效、灵活、环保等特点。
本文将介绍转炉炼钢的原理及工艺流程。
一、转炉炼钢原理转炉炼钢是通过在高温下将生铁与废钢等原料进行反应,去除杂质,调整合金成分来生产钢铁。
其原理基于以下几个重要的化学反应步骤:1.氧化反应:在高温下,将生铁中的杂质氧化为气体或溶于渣中。
主要的氧化反应有:Fe+C+O2=FeO+CO、Mn+C+O2=MnO+CO等。
2.还原反应:在氧化反应的基础上,通过还原剂(如脱氧剂)来还原产生的氧化物。
主要还原反应有:FeO+CO=Fe+CO2、MnO+CO=Mn+CO2等。
3.合金化反应:在还原反应的基础上,通过加入适量合金元素来调整合金成分。
合金化反应可以通过添加合金块、废钢等方式实现。
通过以上化学反应的组合,转炉炼钢可以控制合金成分、去除杂质、调整温度等,从而得到符合要求的钢铁产品。
二、转炉炼钢工艺介绍转炉炼钢的工艺可以分为以下几个主要步骤:1.预处理:生铁、废钢等原料经过破碎、除尘等处理后,进入转炉炉前料斗。
2.加料:原料从炉前料斗通过螺旋输送机被输送至转炉炉缸中。
3.预热:将炉缸中的原料进行预热,以提高反应效果。
4.吹炼:将炉底引入的高纯氧吹入炉缸中,通过氧化反应和还原反应去除杂质、调整合金成分。
5.加料:在吹炼过程中,适量添加合金块、废钢等调整合金成分。
6.测温:通过测温仪器监测和调节炉内温度。
7.出渣:通过倾炉装置将产生的渣浆从转炉中排出。
8.抽炉:将炉内得到的钢液通过倾炉装置倾出,并进行钢液处理(如脱氧、出气、精炼等)9.浇铸:将经过处理的钢液进行浇铸,得到需要的钢铁产品。
三、转炉炼钢的优势转炉炼钢工艺具有以下几个优势:1.高效:转炉炼钢的操作灵活,能够快速调整合金成分和生产规格,生产效率高。
2.资源利用:转炉炼钢可以利用废钢等再生资源,减少资源浪费。
3.环保:转炉炼钢排放的烟尘、废气等污染物可以通过环保设施进行处理,达到环保要求。
炼钢原理与工艺
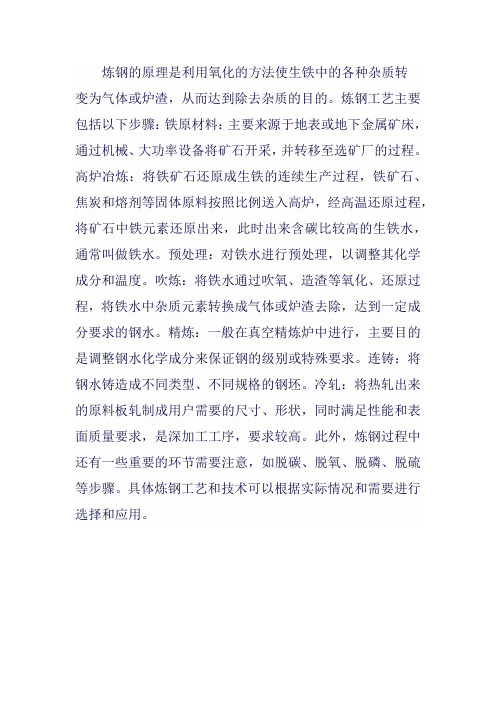
炼钢的原理是利用氧化的方法使生铁中的各种杂质转
变为气体或炉渣,从而达到除去杂质的目的。
炼钢工艺主要包括以下步骤:铁原材料:主要来源于地表或地下金属矿床,通过机械、大功率设备将矿石开采,并转移至选矿厂的过程。
高炉冶炼:将铁矿石还原成生铁的连续生产过程,铁矿石、焦炭和熔剂等固体原料按照比例送入高炉,经高温还原过程,将矿石中铁元素还原出来,此时出来含碳比较高的生铁水,通常叫做铁水。
预处理:对铁水进行预处理,以调整其化学成分和温度。
吹炼:将铁水通过吹氧、造渣等氧化、还原过程,将铁水中杂质元素转换成气体或炉渣去除,达到一定成分要求的钢水。
精炼:一般在真空精炼炉中进行,主要目的是调整钢水化学成分来保证钢的级别或特殊要求。
连铸:将钢水铸造成不同类型、不同规格的钢坯。
冷轧:将热轧出来的原料板轧制成用户需要的尺寸、形状,同时满足性能和表面质量要求,是深加工工序,要求较高。
此外,炼钢过程中还有一些重要的环节需要注意,如脱碳、脱氧、脱磷、脱硫等步骤。
具体炼钢工艺和技术可以根据实际情况和需要进行选择和应用。
精选炼钢工艺学
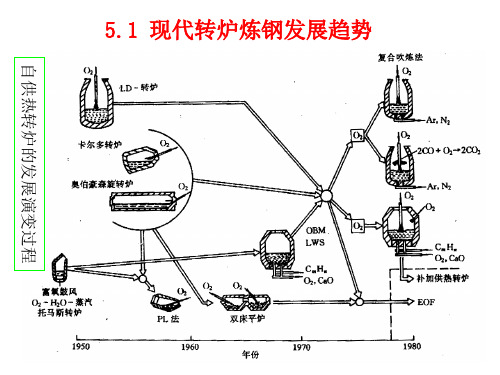
2) 指挥吊废钢的吊车工开吊车至炉口正中位 置。
3) 指挥吊车移动大、小车将废钢斗口伸进转 炉炉口。
4) 指挥吊车提升副钩,将废钢倒入炉内。如 有废钢搭桥,轧死等,可指挥吊车将副钩稍稍下 降,再提起,让废钢松动一下,再倒入炉内。
5) 加完废钢后即指挥吊车离开,指挥转炉摇 正,至此加废钢毕。
转炉兑铁水操作程序
兑铁水 A 准备工作
转炉具备兑铁水条件或等待兑铁水时,将铁水包吊至 转炉正前方,吊车放下副钩,炉前指挥人员将两只铁水 包底环分别挂好钩。
B 兑铁水操作
1)炉前指挥人员站于转炉和转炉操作室中间近转炉的侧 旁(如图所示)。指挥人员的站位必须能同时被摇炉工和 吊车驾驶员看到,又不会被烫伤的位置。 2)指挥吊车驾驶员开动大车和主、副钩将铁水包运至炉 口正中和高度恰当的位置。 3)指挥吊车驾驶员开小车将铁水包移近炉口位置,必要 时指挥吊车对铁水包位置进行微调。 4)指挥吊车上升副钩,开始兑铁水。 5)随着铁水不断兑入炉内,要同时指挥炉口不断下降和 吊车副钩的不断上升,使铁水流逐步加大,并使铁水流 全部进入炉内,而铁水包和炉口互不相碰,铁水不溅在 炉外。 6)兑完铁水指挥吊车离开,至此兑铁水完。
氧气顶吹转炉设备
➢ 废气处理系统 ✓ 转炉烟气净化及回收处理的意义 ——防止环境污染、回收能源。 ✓ 烟气的处理方式有燃烧法与未燃法两种 ✓ 烟尘的净化方式也有两种,即湿式净化与干式净化。 o 目前绝大多数顶吹转炉的烟气是采用未燃法(氮幕法)、湿
法净化回收系统,称OG系统; o 有的也采用未燃、干式净化回收系统,又称LT系统。 o 烟气除尘设备——洗涤除尘器(文氏管)、静电除尘器、布
电除尘器(除细尘)→风机(I D)→切换站
精选炼钢用原材料炼钢工艺学

造渣材料—白云石
白云石的主要成分CaCO3.MgCO3。经焙烧可成为轻烧白云石, 其主要成分为CaO.MgO。 加入一定量白云石代替部分石灰,增加渣料中MgO含量,可 以减少炉衬中的MgO向炉渣中转移,而且还能促进前期化渣, 减少萤石用量和稠化终渣,减轻炉渣对炉衬的浸蚀,延长 炉衬寿命。 溅渣护炉操作时,通过加入适量的生白云石或轻烧白云石 保持渣中的MgO含量达到饱和或过饱和,使终渣能够做黏, 出钢后达到溅渣的要求。
造渣材料—萤石
萤石是普遍应用的熔剂,其主要成分为CaF2。熔点很低(约 930℃)。 能使CaO和阻碍石灰熔解的2CaO·SiO2外壳的熔点显著降 低,而且作用迅速。因而能加速石灰的熔解,迅速改善碱 性炉渣的流动性。 转炉炼钢要求快速化渣,萤石成为必备的材料。但大量使 用萤石会增加喷溅,加剧对炉衬的浸蚀。 电炉炼钢用的萤石,使用前应经过烘烤。 萤石供应不足和价格贵,寻求其代用品的研究很活跃。 我国许多转炉钢厂使用铁矾土和氧化铁皮作为萤石的代用 品。但它们的助熔速度比萤石慢,而且消耗的热量比萤石 多。也有个别工厂采用锰矿作辅助熔剂,但因来源有限, 应用不普遍。
的石灰
度大的应石能灰力高的石灰
石灰石煅烧 生烧石灰 硬烧石灰 软烧石灰
石灰石煅烧
石灰石在煅烧过程中的分解反应为:
CaCO3→CaO+C02 CaCO3的分解温度为880~910℃。石灰石煅烧温度高于其 分解温度越多,石灰石分解越快,生产率越高。 煅烧温度越高,烧成的CaO的晶粒长大也越快,难以获得 细晶石灰。同样,分解出的CaO在煅烧的高温区停留的时 间越长,晶粒也长得越大。因此,要获得细晶石灰,CaO 在高温区停留的时间应该短。 相反,煅烧温度过低,石灰块核心部分的CaCO3来不及分 解而使生烧率增大。因此,煅烧温度一般控制在1050~ 1150℃的范围。 烧成石灰的晶粒大小也决定着石灰的气孔率和体积密度, 随着细小晶粒的合并长大,细小孔隙也随着减少。
炼钢工艺学
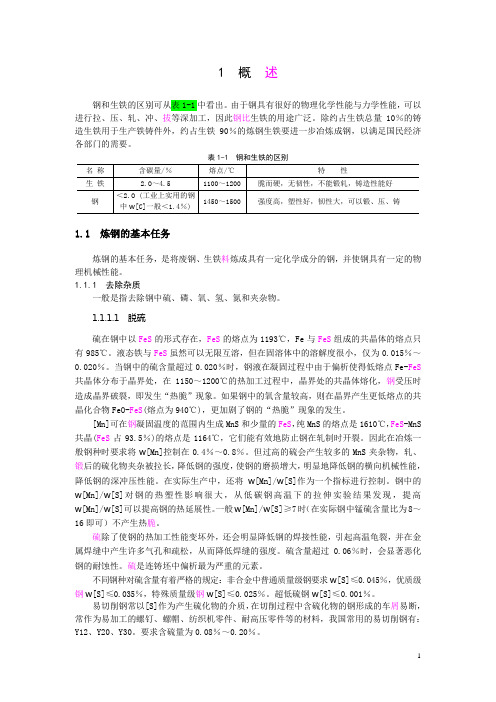
1 概述钢和生铁的区别可从表1-1中看出。
由于钢具有很好的物理化学性能与力学性能,可以进行拉、压、轧、冲、拔等深加工,因此钢比生铁的用途广泛。
除约占生铁总量10%的铸造生铁用于生产铁铸件外,约占生铁90%的炼钢生铁要进一步冶炼成钢,以满足国民经济各部门的需要。
表1-1 钢和生铁的区别1.1 炼钢的基本任务炼钢的基本任务,是将废钢、生铁料炼成具有一定化学成分的钢,并使钢具有一定的物理机械性能。
1.1.1 去除杂质一般是指去除钢中硫、磷、氧、氢、氮和夹杂物。
1.1.1.1 脱硫硫在钢中以FeS的形式存在,FeS的熔点为1193℃,Fe与FeS组成的共晶体的熔点只有985℃。
液态铁与FeS虽然可以无限互溶,但在固溶体中的溶解度很小,仅为0.015%~0.020%。
当钢中的硫含量超过0.020%时,钢液在凝固过程中由于偏析使得低熔点Fe-FeS 共晶体分布于晶界处,在1150~1200℃的热加工过程中,晶界处的共晶体熔化,钢受压时造成晶界破裂,即发生“热脆”现象。
如果钢中的氧含量较高,则在晶界产生更低熔点的共晶化合物FeO-FeS(熔点为940℃),更加剧了钢的“热脆”现象的发生。
[Mn]可在钢凝固温度的范围内生成MnS和少量的FeS,纯MnS的熔点是1610℃,FeS-MnS 共晶(FeS占93.5%)的熔点是1164℃,它们能有效地防止钢在轧制时开裂。
因此在冶炼一般钢种时要求将w[Mn]控制在0.4%~0.8%。
但过高的硫会产生较多的MnS夹杂物,轧、锻后的硫化物夹杂被拉长,降低钢的强度,使钢的磨损增大,明显地降低钢的横向机械性能,降低钢的深冲压性能。
在实际生产中,还将w[Mn]/w[S]作为一个指标进行控制。
钢中的w[Mn]/w[S]对钢的热塑性影响很大,从低碳钢高温下的拉伸实验结果发现,提高w[Mn]/w[S]可以提高钢的热延展性。
一般w[Mn]/w[S]≥7时(在实际钢中锰硫含量比为8~16即可)不产生热脆。
- 1、下载文档前请自行甄别文档内容的完整性,平台不提供额外的编辑、内容补充、找答案等附加服务。
- 2、"仅部分预览"的文档,不可在线预览部分如存在完整性等问题,可反馈申请退款(可完整预览的文档不适用该条件!)。
- 3、如文档侵犯您的权益,请联系客服反馈,我们会尽快为您处理(人工客服工作时间:9:00-18:30)。
冶2007-1、2班《炼钢工艺学》复习题(详见课本和笔记)2010.7.8(授课教师:刘宇雁)1.铁水预处理的“三脱”是指脱硅、脱磷、脱硫。
2.铁水预处理指铁水在兑入炼钢炉之前,为除去某种有害成分( 如S、P、Si等)或提取/回收某种有益成分(如V、Nb 等)的处理过程。
或铁水在兑入转炉之前进行的脱硫、脱磷或脱硅操作。
3.铁水预处理目的及意义:主要是使其中硫、硅、磷含量降低到所要求范围,以简化炼钢过程,提高钢的质量。
⑪有效提高铁水质量;⑫减轻炼钢负担;⑬为优化炼钢工艺,提高钢材质量创造良好条件;⑭对特殊铁水预处理而言,可有效回收利用有益元素,实现综合利用。
4.铁水预脱硅技术的目的:⑪减少转炉石灰耗量(硅氧化形成的SiO2大大降低渣的碱度),减少渣量和铁损,改善操作和提高炼钢经济技术指标。
⑫铁水预脱P的需要,可减少脱磷剂用量、提高脱磷、脱S效率。
当铁水[Si]>0.15%时,脱磷剂用量急剧增大。
因此,脱磷处理前需将铁水含[Si]脱至<0.15%,这个值远远低于高炉铁水的硅含量,也就是说,只有当铁水中的硅大部分氧化后,磷才能被迅速氧化去除。
所以脱磷前必须先脱硅。
铁水预脱P的最佳[Si]:初始①苏打脱P:[Si]初始<0.1%②石灰熔剂脱P:[Si]初始0.10~0.15%⑬对含V或Nb等特殊铁水,预脱Si可为富集V2O5和Nb2O5等创造条件。
5.铁水预脱硫技术迅速发展的原因:⑪用户对钢的品种和质量要求提高。
⑫连铸技术的发展要求钢中硫含量进一步降低,否则连铸坯容易产生内裂,铁水脱硫可满足冶炼低硫钢和超低硫钢种的要求。
⑬铁水中碳、硅、磷等元素的含量高,可提高硫在铁水中的活度系数,而有利于脱硫,同时铁水中的氧含量低,没有强烈的氧化性气氛,有利于直接使用一些强脱硫剂,如电石(CaC2)、金属镁等;故铁水脱硫效率高。
⑭铁水脱硫费用低于高炉、转炉和炉外精炼的脱硫费用。
其费用比值为:高炉脱硫:铁水预处理脱硫:转炉:炉外精炼=2.6:1:16.9:6.10 ⑮降低炼铁和炼钢炉脱硫负担; 有利于降低消耗和成本,并增加产量。
⑯提高炼铁和炼钢经济技术指标;有效提高钢铁企业铁、钢、材的综合经济效益。
全程脱硫:高炉-铁水炉外-炼钢炉(-精炼炉)→实现铁水深度脱硫,经济有效生产超低S高级优质钢;⑰提高钢质、扩大品种、优化工艺(改善转炉炼钢操作);6.铁水预脱硫优点(铁水脱硫条件比钢水脱硫优越的主要原因)用优质铁水炼钢,是提高产品质量、扩大品种、增加效益和增强产品市场竞争力的重要条件之一,也是生产低硫洁净钢的基础。
铁水炉外脱硫有利于提高炼铁、炼钢技术经济指标。
通过比较各种脱硫工艺,铁水脱硫预处理工艺有如下优点:⑪铁水中[C]、[Si]较高,fs↑,提高硫的反应能力;⑫铁水中[O]较低,提高渣铁之间的硫分配比(Ls↑),脱硫效率高;⑬搅拌充分,脱硫剂利用率高,脱硫速度快;⑭铁水脱硫可提高炼铁炼钢的生产能力、节约工序能源、降低成本。
⑮故铁水脱硫费用费用比其他工序低。
7.铁水预脱硫技术的发展:铁水炉外脱硫技术在20世纪60年代氧气顶吹转炉炼钢工艺发展后得到迅速推广,在国外已趋成熟,在实际生产中大量应用,处理工艺方法约数十种之多。
先后发明的工艺大致可分为分批处理法和连续处理法两大类,其中分批处理法又可分为铺撒法/投入法(含倒包法)、机械搅拌法、吹气搅拌法、喷射法、镁脱硫法等。
目前常用的方法有喷吹法和KR机械搅拌法。
8.铁水脱硫预处理的工艺方法:⑪投掷(入)法:将脱硫剂投入铁水中。
⑫喷吹法:将脱硫剂喷入铁水中。
⑬搅拌法(KR法):将通过中空机械搅拌器向铁水内加入脱硫剂,搅拌脱硫。
9.常用铁水预脱硫剂有石灰、碳化钙、苏打、金属镁及复合脱硫剂等。
10.提高铁水脱硫效果的措施:1)热力学条件。
⑪fs↑([C]↑、[Si]↑);⑫降低氧位,即[O]↓、(O2-)↓(加入铝)⑬脱硫剂用量↑(同时生产费用↑);⑭控制好温度。
2)动力学条件。
⑪根据铁水条件及钢种要求,选择适当主脱硫剂。
即要满足脱硫要求,又要尽量降低脱硫成本且操作方便。
脱硫要求一般时(轻脱硫),脱硫剂组成以石灰粉为主;生产低硫生铁时,以电石粉为主(深脱硫)。
⑫添加适当促进剂。
⑬适当减小脱硫剂粒度,增大反应界面,加快脱硫速度;⑭强化熔池搅拌,增加逗留时间,减小扩散边界层厚度,提高混匀搅拌效率,均可加快脱硫反应速度;⑮控制好温度。
提高铁水温度,增大硫的传质系数;⑯选择适当的喷吹参数,以取得最佳喷吹效果。
11.选择脱硫方法的原则(铁水脱硫方案的选择)⑪铁水条件供应条件;⑫冶炼钢种要求;⑬处理规模(处理能力,作业率)、工艺流程(铁水运输方式)及总图布置(布置位置);⑭脱硫效率及脱硫剂消耗;⑮处理成本(设备和基建费用);⑯铁水温降;⑰预留铁水三脱的可能性;⑱环境污染12.转炉的内衬由绝热层/隔热层、永久层、工作层组成。
13.转炉炉衬损坏原因主要为机械作用、高温作用、化学侵蚀、炉衬剥落。
或机械冲击和磨损、耐材的高温溶解、高温溶液渗透、高温下气体挥发。
14.炼钢的基本任务:“四脱”(脱碳、脱氧、脱磷和脱硫),“二去(去气和去夹杂)”,“两调整”(调整温度和成分)。
15.炼钢生产中熔渣的主要作用(有利作用):⑪通过调整熔渣成分氧化还原钢液,使钢液中硅、锰、铬等元素氧化或还原的硫、磷、氧等元素;⑫吸收钢液中的非金属夹杂物;⑬防止炉衬的过分侵蚀;⑭覆盖钢液,减少散热和防止二次氧化和吸氢。
其他作用:在不同炼钢方法中,熔渣还有其独特的作用。
如:①氧气顶吹转炉炼钢过程→熔渣-钢液滴-气泡形成高度的乳化相→钢渣接触面积↑→加速吹炼过程。
②电弧炉炼钢时→稳弧(稳定电弧燃烧)和传热→良好的泡沫渣能包围住弧光→弧光对炉衬的辐射侵蚀↓③电渣重熔时→作电阻发热体→可重熔和精炼金属(电渣炉)④出钢时→钢液的二次氧化↓⑤浇注时→作保护渣,可减少氧化,防止散热,并改善铸坯表面质量等。
不利作用:①侵蚀耐火材料,降低炉衬寿命,特别是低碱度熔渣对炉衬的侵蚀更为严重。
②熔渣中夹带小颗粒金属及未被还原的金属氧化物,降低了金属的回收率。
③严重泡沫化熔渣会引起喷溅。
(转炉)16.熔渣的氧化性(熔渣的氧化能力):是指在一定的温度下,单位时间内熔渣向钢液供氧的数量(在单位时间内从渣相向金属相供氧的数量);通常用渣中氧化铁含量的多少表示熔渣氧化能力的强弱。
生产中常用渣中∑(%FeO)表示渣的氧化性。
17.熔渣氧化性对操作过程有何影响?如①杂质的去除程度;②钢水含氧量;③石灰溶化速度;④熔渣的泡沫程度;⑤喷溅;⑥炉衬寿命;⑦金属和铁合金的收得率。
18.熔渣与熔融金属之间应有足够大的表面张力,以有助于渣壳分离,防止熔渣卷入金属内;而熔渣与非金属夹杂物之间的表面张力越小越好,以利于熔渣对非金属夹杂物的浸润、吸附和溶解。
19.氧化脱磷的有利条件:⑪较高的炉渣碱度(3~4);⑫氧化铁较高(15%~20%);⑬良好流动性熔渣;⑭充分的熔池搅拌;⑮适当的温度(1450~1550℃);⑯渣量要大,可利用多次放渣和造新渣去磷。
20.炼钢脱磷、脱硫的有利条件有哪些?答:1)脱磷反应:2[P]+5(FeO)+4(CaO)=(4CaO·P2O5)+5[Fe]脱磷有利条件:高碱度、高(FeO)/氧化性、良好流动性熔渣、充分的熔池搅拌、适当的温度和大渣量。
2)脱硫的有利条件:高温、高碱度、低氧化铁(FeO),良好流动性熔渣、充分的熔池搅拌和大渣量。
21.回磷:就是磷从熔渣中又返回到钢中,也是脱磷的逆向反应;或成品钢中磷含量高于终点磷含量也属回磷现象。
22.减少回磷的措施:⑪冶炼中期,保持∑(FeO)>10%,防止因炉渣“返干”而产生的回磷;控制终点温度不要过高,并调整好炉渣成分,使炉渣碱度保持在较高水平。
⑫出钢时,①适当提高脱氧前的炉渣碱度;②挡渣出钢,尽量避免下渣;⑬出钢后,向钢包渣面加一定量石灰,增加炉渣碱度;脱氧合金化时,尽可能采取钢包脱氧,而不采取炉内脱氧。
23.碳氧浓度积:在一定的温度和压力下钢液中的碳氧反应达到平衡时,碳和氧的质量百分浓度之积是一个常数。
24.脱碳反应对炼钢过程的作用/碳氧化在炼钢中的作用:①脱碳,将熔池中的碳氧化脱除至所炼钢种的终点要求;②放热升温,加速传质传热;③均匀熔池成分、温度;④加大钢-渣界面,加速反应的进行,也有利于熔渣的形成;⑤去气去夹杂(有利于非金属夹杂的上浮和有害气体的排出)。
⑥爆发性的脱碳反应会造成喷溅。
25.碳氧反应发生的必要条件是:必须存在过剩氧,即[O]实际>[O]平衡。
26.钢中氧的危害性主要表现在以下方面(1)产生夹杂;(2)形成气泡;(3)加剧硫的危害。
27.脱氧任务:⑪按钢种要求降低钢液中溶解的氧;⑫排除脱氧产物;⑬控制残留夹杂的形态和分布。
28.沉淀脱氧:将块状脱氧剂沉入钢液中,熔化、溶解后与钢中氧反应生成稳定的氧化物并上浮进入炉渣,以降低钢中氧的脱氧方法。
29.促使脱氧产物上浮的措施:⑪上浮速度↑;⑫形成液态的脱氧产物。
⑬形成与钢液间界面张力大的脱氧产物。
30.合金元素加入一般的原则:⑪脱氧元素先加,合金化元素后加;⑫脱氧能力较强、且比较贵重的合金,应在钢水脱氧良好的情况下加入,以提高合金的收得率。
⑬熔点高,不易氧化的元素,可加在炉内。
31.氧气顶吹转炉设备除转炉外还包括供氧、供料、废气处理及回收系统等附属系统。
32.按金属熔池(炉底)形状转炉炉型可分为:筒球型、锥球型、截锥型。
33.烟气净化回收装置:目前主要有湿法(OG法)和干法(LT法)两种除尘方式。
(原始含尘量100~150g/Nm3降至<100mg/Nm3,排放标准)34.转炉的烟尘排放浓度环保要求:随着工业和科学技术的发展,环境保护问题越来越引起人们的重视,根据《工业三废排放标准》规定,大于12吨的转炉的烟尘排放浓度≯150mg/Nm3(烟气),小于12吨转炉的烟尘排放浓度<200mg/Nm3(烟气)。
而烟气的实际烟尘浓度为80~150g/Nm3(烟气),高出国家规定排放标准的上千倍,所以转炉烟气必须进行净化处理后方可排放。
35.采用炉烟气净化回收系统条件:CO:50~70%,O2:<1~2%,≥100t转炉,要求实现负能炼钢。
36.对铁水温度的要求:高(≥1250℃)且稳定。
37.炼钢对废钢的基本要求:(1)废钢表面应清洁干燥(清洁、少锈、无混杂)。
(2)废钢中不得混有铁合金(有害的残余金属元素如铜、锌、铅、锡、锑、砷等;部分合金结构钢中五害元素为Pb、As、Sb、Bi、Sn,对优质合金结构钢,五害元素含量应分别控制在≯0.02%。
)。
(3)废钢中不得混有封闭器皿、爆炸物和易燃易爆品以及有毒物品。
以保证安全生产。
(4)废钢要有明确的化学成分;废钢中有用的合金元素应尽可能在冶炼过程中回收利用;对有害元素含量应限制在一定范围以内。