高炉炉身下部及炉缸_炉底冷却系统的传热学计算
高炉计算方法
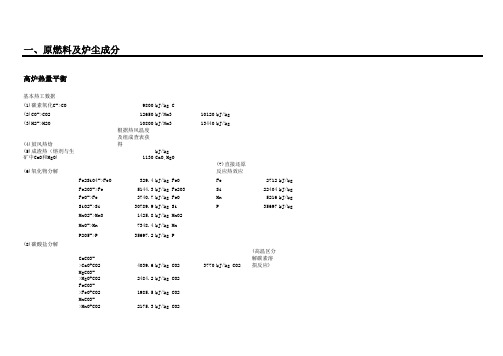
一、原燃料及炉尘成分高炉热量平衡基本热工数据(1)碳素氧化C->CO9800kJ/kg C(2)CO->CO212650kJ/Nm310120kJ/kg(3)H2->H2O10800kJ/Nm313440kJ/kg(4)鼓风热焓根据热风温度及组成查表获得(5)成渣热(熔剂与生矿中CaO和MgO)1130kJ/kg CaO,MgO(6)氧化物分解(7)直接还原反应热效应Fe2SiO4->FeO329.4kJ/kg FeO Fe2712kJ/kgFe2O3->Fe5144.3kJ/kg Fe2O3Si22404kJ/kgFeO->Fe3740.7kJ/kg FeO Mn5216kJ/kgSiO2->Si30789.9kJ/kg Si P35697kJ/kgMnO2->MnO1425.8kJ/kg MnO2MnO->Mn7348.4kJ/kg MnP2O5->P35697.2kJ/kg P(8)碳酸盐分解CaCO3->CaO+CO24039.6kJ/kg CO23770kJ/kg CO2(高温区分解碳素溶损反应)MgCO3->MgO+CO22484.2kJ/kg CO2FeCO3->FeO+CO21985.5kJ/kg CO2MnCO3->MnO+CO22175.3kJ/kg CO2(9)脱硫耗热第一总热平衡8300kJ/kg S第二总热平衡4650kJ/kg S(10)炉渣铁水热焓炉渣比热(1720-181780kJ/kg 渣铁水比热(1130-121240kJ/kg 铁(11)水蒸气相变热2257.2kJ/kg H2O(12)水蒸气的比焓100℃150.9kJ/Nm3200℃305.6kJ/Nm3380.30222kJ/kg(13)结晶水析出331kJ/Kg(14)水煤气反应吸热6150kJ/kg H2O(15)炉尘热容0.8kJ/kg℃(16)煤粉分解热(17)中温区炉料比焓无烟煤1005kJ/kg q脉石860烟煤1172kJ/kg q铁630重油1675kJ/kg q焦氧化物分解Fe2O3-FeO#REF!FeO-Fe#REF!MnO-Mn#REF!MnO2-Mn#REF!Si#REF!P#REF!直接还原Fe#REF!Si#REF!Mn#REF!P#REF!能量利用系数和碳素热能利用系数计算1)能量利用系数#REF!GJ/tηt#REF!#REF!GJ/tηt#REF!它更真实地反应了高炉内能量利用情况。
高炉技术之燃烧与热交换相关知识点

则燃烧1kg碳素所需风量V风 为:
V风
1
0.933
f 0.5 f
0.933 0.21 0.29
f
m3 /kgC
当f=0时,V风 =4.44 m3/kg, f=1% 时,V风 =4.39m3/kg .
8
燃烧1kg碳素所生成的炉缸煤气体积(即生成的CO、
N2、H2体积之和)。
V煤 = V风 (VCO+ VN2+ V H2 )
=(1.21+0.79f)×
0.933
当f=0时,V煤 =5.38 m3/k0g.21,f0.2=9 f1%时, V煤=5.32
m3/kg
由此可知:炉缸煤气量约为风量的1.21倍, 即 V 煤 =1.21V 风 。
9
1.3炉缸煤气成分沿半径方向的变化
二、炉缸煤气成分、温度和压力的变化
从风口向炉缸中心插人取样管,可以得知沿炉缸半径 煤气成分、温度和压力的变化规律。 (一)炉缸煤气成分变化 1.炉缸煤气成分变化
1.理论燃烧温度 风口前焦炭燃烧所能达到的最高温度,即假定风口前焦炭 燃烧放出的热量全部用来加热燃烧产物时所能达到的最高 温度叫作风口前理论燃烧温度。 理论燃烧温度是燃烧带(炉缸内燃料燃烧成C02的区域)在 理论上能达到的最高温度,在生产中一般是指燃烧带燃烧 焦点的温度。而炉缸温度一般是指炉缸渣铁的温度两者有 本质上的区别。理论燃烧温度一般可达1800~2400℃, 而炉缸温度一般在1500℃左右。
H =2
2 100% 1.63% 122.58
N =2
77.42 100% 63.16% 122.58
6
2.影响炉缸煤气成分和数量因素
• 增加鼓风湿度(加湿鼓风)时,炉缸煤气中H 2和CO含量 增加,N2 含量减少。
长寿高炉冷却器布置方式的计算传热学分析

壁安全工作温度 ) 甚至在一些 部位超过其 融化 温度. 计算结 果表明通 过提高水速或者 改进凸
台内部冷却水管布置难 以改变 凸台温度 分布 , 其原因主要是 凸台部位的下 端及前端 同时遭受 炙热 的煤气流 冲刷. 这说 明当炉气 温度较 高时
2 帅2年 2月
长寿高炉冷却器布置方式的计算传热学分析
程素 森 ” 杨天钧 薛庆 国 全 强
1 京科技大学冶金学院, HE 北京 118 HE 003 2 京钢铁设计研究总院. ) 北京 1 0 0 5 0
摘 要
应用 计算 传热 学研究 了 目前 常用 的一些 高炉冷却 器 的温度 场. 通过摸 拟在 高炉 内部
改善 凸台冷 却壁的结 构参数 , 以提高 其冷却 难
强度 对 凸台 内部 温度场 的影 响. 当炉 内 煤气 流温度 90℃时 , 为 0 即使 凸台裸 露时 , 凸
-
维普资讯
・ 6 1・
北
京
科
技
大
学
学
报
2O 年 第 1 O2 期
砖及在 凸台前 端和上部 凝 固渣铁 , 过炉衬砖 通 及凝固的渣铁壳保护凸 台冷却壁率身. 但是 , 很 多高炉在开炉后的二三年 内便发 现凸台大量烧 毁, 继而导致砖村失去支撑 而垮蹋 , 使高炉炉役
维普资讯
第2 4卷 第 1 期
北 京 科 技 大 学 学 报
J u n l f ies yo s e c n eb oo B te o r a o Unvri f d - e dT c . t ̄ e| g t a t
高炉冷却壁的传热学分析

钢铁IRON & STEEL1999年 第34卷 第5期 No.5 Vol.34 1999高炉冷却壁的传热学分析*程素森 薛庆国 苍大强 杨天钧 摘 要 应用传热学理论计算分析了高炉冷却水的稳定性、冷却水的水速、冷却水管与冷却壁本体的间隙及冷却壁的高度对长寿高效高炉冷却壁寿命的影响。
关键词 高炉 冷却系统HEAT TRANSFER ANALYSIS OF BLAST FURNACE STAVECHENG Susen XUE Qingguo CANG Daqiang YANG Tianjun(University of Science and Technology Beijing) ABSTRACT In this paper, effect of the cooling water stability, cooling water velocity, gap between cooling water pipe and stave and height of stave on the stave life is analyzed by heat transfer theory. KEY WORDS blast furnace, cooling system1 前言 在1994年国际炼铁会议上,霍戈文公司(Hoogven)的专家提出了下一个世纪钢铁联合企业生存的条件之一是高炉寿命达到15年。
日本千叶6号高炉(容积为4500m3)到1997年底已经连续生产20年6个月,创高炉长寿的世界记录。
80年代以来国外新设计的高炉寿命一般在15年以上,而我国1000m3以上高炉的中修周期目前一般为4~5年,大修周期一般为9年左右。
因此,就整体而言我国高炉寿命与国外相比仍有很大差距。
高炉是一个巨大的反应器,其寿命与许多因素有关,依据我国对高炉寿命的调查结果,冷却系统的设计和制造质量是影响高炉长寿的重要因素之一。
高炉炉体冷却的传热计算及其推论

高炉炉体冷却的传热计算及其推论
王长霖
【期刊名称】《安徽冶金》
【年(卷),期】2001(000)001
【摘要】本文根据炉墙复合体传热理论,列举实例计算了炉墙复合体在不同情况
下的传热结果,并对如何强化冷却及可否用控制水量的方法进行“中部调剂”等问题进行了探讨,设计了冷却水的水量与水速。
指出“中部调剂”的主要作用是节能,而对处理炉墙结厚的作用不明显。
【总页数】6页(P34-39)
【作者】王长霖
【作者单位】合肥钢铁集团有限公司
【正文语种】中文
【中图分类】TF549
【相关文献】
1.高炉冷却壁的稳态传热计算 [J], 温宏权;李山青;冯莲芹;孙大乐;向顺华
2.从首钢高炉汽化冷却的实践探讨提高炉体寿命的途径 [J], 陈欣田
3.八钢1~#高炉采用铜冷却棒恢复炉体冷却技术的设计及实施 [J], 廖文新;梁振斌;杨世俊
4.马钢A高炉炉体冷却水管道在线改造实践 [J], 张全一;杭桂生;曹兵;孙薄涛;孙树
峰
5.高炉炉体冷却壁安全维护实践与应用 [J], 张永刚
因版权原因,仅展示原文概要,查看原文内容请购买。
高炉耐材侵蚀简易计算
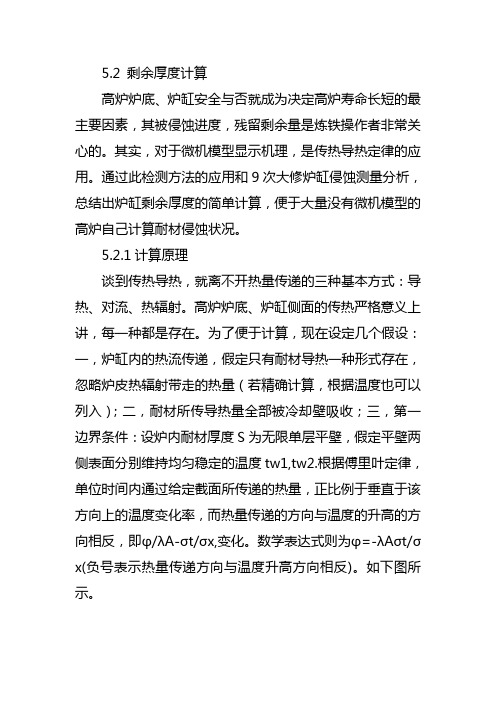
5.2 剩余厚度计算高炉炉底、炉缸安全与否就成为决定高炉寿命长短的最主要因素,其被侵蚀进度,残留剩余量是炼铁操作者非常关心的。
其实,对于微机模型显示机理,是传热导热定律的应用。
通过此检测方法的应用和9次大修炉缸侵蚀测量分析,总结出炉缸剩余厚度的简单计算,便于大量没有微机模型的高炉自己计算耐材侵蚀状况。
5.2.1计算原理谈到传热导热,就离不开热量传递的三种基本方式:导热、对流、热辐射。
高炉炉底、炉缸侧面的传热严格意义上讲,每一种都是存在。
为了便于计算,现在设定几个假设:一,炉缸内的热流传递,假定只有耐材导热一种形式存在,忽略炉皮热辐射带走的热量(若精确计算,根据温度也可以列入);二,耐材所传导热量全部被冷却壁吸收;三,第一边界条件:设炉内耐材厚度S为无限单层平壁,假定平壁两侧表面分别维持均匀稳定的温度tw1,tw2.根据傅里叶定律,单位时间内通过给定截面所传递的热量,正比例于垂直于该方向上的温度变化率,而热量传递的方向与温度的升高的方向相反,即φ/λA-σt/σx,变化。
数学表达式则为φ=-λA σt/σx(负号表示热量传递方向与温度升高方向相反)。
如下图所示。
图1 通过平壁的导热其中φ---热流密度w/m2(单位时间内通过单位面积的热流量)σt/σx----物体温度沿x轴方向的变化率若物体温度分布满足:t=f(x,y,z)时,则三个方向上单位矢量与该方向上的热流密度分量乘积合成一个热流密度矢量写出的,其形式为q=-λgradt。
其中gradt---空间某点的温度梯度;q---为该点的热量密度矢量。
经过简化和汇总整理,则单位时间通过平壁传导的热量公式可以简化为:Q=λFΔT/S式中Q:热流量,Wλ:比例系数,称为导热系数或者热导率W/(m. ℃)F:面积,m2ΔT:温度差,℃S:厚度,m4.2.2 推导简单计算侵蚀公式有了上面的导热公式,就可以反推导侵蚀公式了,以冷却设备的面积为基础,根据传热公式Q=λFΔT/S推演出:S=λΔTF/Mδt A式中S:耐材侵蚀剩余长度,mλ:比例系数,耐材的导热系数或者热导率,W/(m, ℃)ΔT:耐材热端温度为T1,冷端温度为T2,则ΔT=T1-T2,F:冷却设备面积,m2M:单位时间通过冷却设备的冷却水量,m3/hA:水的比热容,J/(g. ℃)δt:冷却设备进出水的温差,℃根据以上公式,需要至少6种参数。
高炉各部位用耐火材料要求
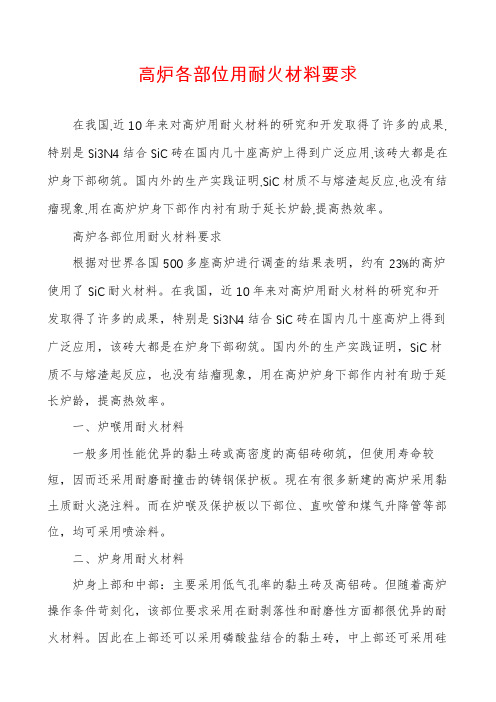
高炉各部位用耐火材料要求在我国,近10年来对高炉用耐火材料的研究和开发取得了许多的成果,特别是Si3N4结合SiC砖在国内几十座高炉上得到广泛应用,该砖大都是在炉身下部砌筑。
国内外的生产实践证明,SiC材质不与熔渣起反应,也没有结瘤现象,用在高炉炉身下部作内衬有助于延长炉龄,提高热效率。
高炉各部位用耐火材料要求根据对世界各国500多座高炉进行调查的结果表明,约有23%的高炉使用了SiC耐火材料。
在我国,近10年来对高炉用耐火材料的研究和开发取得了许多的成果,特别是Si3N4结合SiC砖在国内几十座高炉上得到广泛应用,该砖大都是在炉身下部砌筑。
国内外的生产实践证明,SiC材质不与熔渣起反应,也没有结瘤现象,用在高炉炉身下部作内衬有助于延长炉龄,提高热效率。
一、炉喉用耐火材料一般多用性能优异的黏土砖或高密度的高铝砖砌筑,但使用寿命较短,因而还采用耐磨耐撞击的铸钢保护板。
现在有很多新建的高炉采用黏土质耐火浇注料。
而在炉喉及保护板以下部位、直吹管和煤气升降管等部位,均可采用喷涂料。
二、炉身用耐火材料炉身上部和中部:主要采用低气孔率的黏土砖及高铝砖。
但随着高炉操作条件苛刻化,该部位要求采用在耐剥落性和耐磨性方面都很优异的耐火材料。
因此在上部还可以采用磷酸盐结合的黏土砖,中上部还可采用硅线石砖炉身下部:一般使用要求有良好的抗渣性、抗碱性、耐磨的黏土砖、高铝砖、刚玉砖及碳化硅砖。
经过在炉身下部试用各类耐火砖,从抗强碱试验结果看,在1400 ℃时普通刚玉砖并不比黏土砖好多少,而莫来石结合的刚玉砖和直接结合或Si3N4结合SiC砖仍保持有足够的强度。
使用结果表明,直接结合或Si3N4结合SiC砖对碱蒸气不发生反应,对碳裂解沉淀物不敏感,导热性能优良,因而是一种有前途的制品,在近几年的高炉建设中,尤其是在大高炉上得到了广泛的应用。
但该砖易氧化,也不耐铁水侵蚀,故只能在不接触铁水的部位使用三、炉腰用耐火材料炉腰环境条件,一般选择抗渣侵蚀性强、耐冲刷的耐火材料。
2022年注册安全工程师《金属冶炼安全》模拟卷( A )
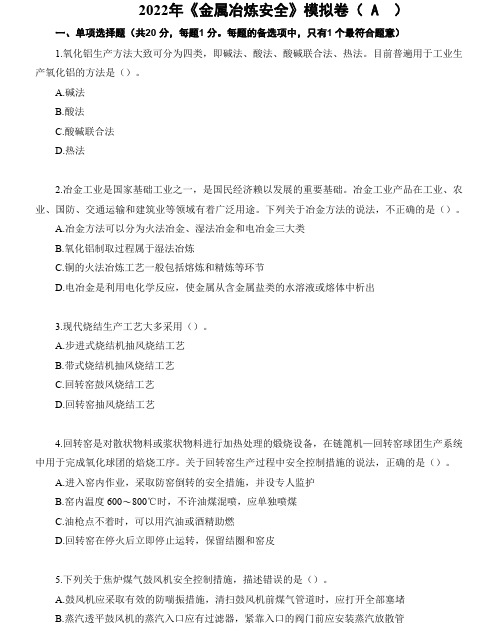
2022年《金属冶炼安全》模拟卷( A )一、单项选择题(共20分,每题1分。
每题的备选项中,只有1个最符合题意)1.氧化铝生产方法大致可分为四类,即碱法、酸法、酸碱联合法、热法。
目前普遍用于工业生产氧化铝的方法是()。
A.碱法B.酸法C.酸碱联合法D.热法2.冶金工业是国家基础工业之一,是国民经济赖以发展的重要基础。
冶金工业产品在工业、农业、国防、交通运输和建筑业等领域有着广泛用途。
下列关于冶金方法的说法,不正确的是()。
A.冶金方法可以分为火法冶金、湿法冶金和电冶金三大类B.氧化铝制取过程属于湿法冶炼C.铜的火法冶炼工艺一般包括熔炼和精炼等环节D.电冶金是利用电化学反应,使金属从含金属盐类的水溶液或熔体中析出3.现代烧结生产工艺大多采用()。
A.步进式烧结机抽风烧结工艺B.带式烧结机抽风烧结工艺C.回转窑鼓风烧结工艺D.回转窑抽风烧结工艺4.回转窑是对散状物料或浆状物料进行加热处理的煅烧设备,在链篦机—回转窑球团生产系统中用于完成氧化球团的焙烧工序。
关于回转窑生产过程中安全控制措施的说法,正确的是()。
A.进入窑内作业,采取防窑倒转的安全措施,并设专人监护B.窑内温度600〜800℃时,不许油煤混喷,应单独喷煤C.油枪点不着时,可以用汽油或酒精助燃D.回转窑在停火后立即停止运转,保留结圈和窑皮5.下列关于焦炉煤气鼓风机安全控制措施,描述错误的是()。
A.鼓风机应采取有效的防喘振措施,清扫鼓风机前煤气管道时,应打开全部塞堵B.蒸汽透平鼓风机的蒸汽入口应有过滤器,紧靠入口的阀门前应安装蒸汽放散管C.鼓风机前煤气系统着火,应立即停机,通蒸汽(或氮气)灭火D.鼓风机后煤气系统着火严禁停机,应立即降低机后压力,通蒸汽(或氮气)灭火6.某钢铁公司焦化厂现有2×50孔TJL4350型复热式捣固型机焦炉及相应配套设施,设计年生产能力60×l04t。
下列情形,焦炉生产过程中不需要立即停止焦炉加热的是()。
炉膛传热计算的基本步骤

炉膛传热计算的基本步骤
•已知:炉膛结构尺寸。
•求:炉膛的出口烟温
•计算过程:
1.由燃料计算求得烟气特性表和焓温表,由热平衡计算得到计算燃料量B ca l和保热系数ϕ。
2.求炉膛受热面积F、炉膛的有效容积V f、燃烧器的相对高度x B和有效辐射层厚度S。
3.根据水冷壁的结构、燃料性质、燃烧方式求热有效系数ψav。
4.根据燃烧器结构特性求x b[方法一],或根据燃料特性和燃烧器结构求炉内介质的温度分布系数M[方法二、三]。
5.求随同1kg燃料带入炉内的有效热量Q f ef和理论燃烧温度T th.。
6.假设炉膛出口烟温T f〃,由焓温表查的烟气焓。
7.求平均热容。
8.求三原子气体的辐射减弱系数k g r、灰粒辐射减弱系数k ashμash、焦炭颗粒辐射减弱系数k cokμcok。
9.求炉内介质的辐射减弱系数k a。
10.求火焰黑度ε1[方法二]或综合火焰黑度ε1[方法一、三]。
11.求炉膛黑度εf[方法二]或εf syn[方法一、三]。
12.计算炉膛出口烟温T f〃。
13.若计算与假定值之差小于100℃,则计算结果符合要求,否则从第6步重新假设计算。
高炉冷却壁的稳态传热计算_温宏权
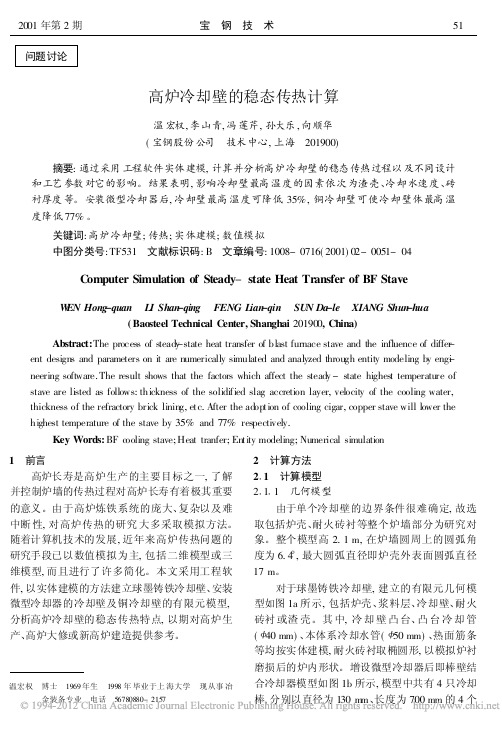
问题讨论高炉冷却壁的稳态传热计算温宏权,李山青,冯莲芹,孙大乐,向顺华(宝钢股份公司技术中心,上海201900)摘要:通过采用工程软件实体建模,计算并分析高炉冷却壁的稳态传热过程以及不同设计和工艺参数对它的影响。
结果表明,影响冷却壁最高温度的因素依次为渣壳、冷却水速度、砖衬厚度等。
安装微型冷却器后,冷却壁最高温度可降低35%,铜冷却壁可使冷却壁体最高温度降低77%。
关键词:高炉冷却壁;传热;实体建模;数值模拟中图分类号:TF531文献标识码:B文章编号:1008-0716(2001)02-0051-04C omputer Simulation of Steady-state Heat Transfer of BF StaveW EN Hong-quan L I Shan-qing FENG L ian-qin SU N Da-le XIANG Shun-hua(Baosteel Technical C enter,Shanghai201900,China)Abstract:The process of steady-state heat transfer of blast furnace stave and the influence of differ-ent designs and parameters on it are numerically simulated and analyzed through entity modeling by eng-i neering software.The result shows that the factors which affect the steady-state highest temperature of stave are listed as follows:thickness of the solidified slag accretion layer,velocity of the cooling water, thickness of the refractory brick lining,etc.After the adoption of cooling cigar,copper stave will lower the highest temperature of the stave by35%and77%respectively.Key Words:BF c ooling stave;Heat tranfer;Entity modeling;Numerical simulation1前言高炉长寿是高炉生产的主要目标之一,了解并控制炉墙的传热过程对高炉长寿有着极其重要的意义。
第14章炉膛传热计算

三、过热蒸汽的溶盐规律
1、饱和蒸汽易于溶解的盐类在过热器中溶解度也较大; 2、压力越高,溶解度越大; 3、压力一定,溶解度不同的盐有增有减,过热汽温很高 时,接近理想气体,盐分受温度影响大;
16
第四节 汽水分离装置 一、汽水分离过程的组织 二、立式旋风分离器 三、涡轮式旋风分离器:(轴流式)
22
一、蒸汽清洗工作原理
分配系数: Sqsi2oa1s0i2oS0gsis2o,mg/kg
蒸汽的含硅酸量取决于锅水的含硅酸量; (1)凝结蒸汽率: d1x00(100p)(i'ism), %
i"i'
(2)总平衡方程:( 10 p ) 0Sg s2 io 1S 0 q s2 i0 opg sS 2 iso
S'qsio2 Sqsio2
S'qsio2
asio2 (Sgsio2 100
Ssio2 qx
2
)
β:清洗不完全系数;
S q s2 io (1 )K 1 q s2 ix 0 ( oS g s0 2 i 2 oS q s2 ix)o K 1 g s2 is 0 S og s2 0 iso
26
影响蒸汽清洗效果的因素:
力; ② 局部区域汽流流速不要太高; ③ 进行重力分离;
④采用二次分离元件;
19
二、立式旋风分离器:
1、工作过程:(见《锅炉原理》多媒体教学软件) 2、结构型式及允许负荷:φ290,φ315,φ350
20
三、涡轮式旋风分离器:(轴流式) 多用于强制循环锅炉
21
第五节 蒸汽清洗装置
一、蒸汽清洗工作原理 二、蒸汽清洗装置 三、提高蒸汽清洗效果措施
四、ψ、Χ、ζ关系
高炉炉底炉缸温度场计算及排铅槽影响的分析

高 炉 炉 底 炉 缸 进 行 物 理 建 模 和传 热 等数 值模 拟 , 分 析 了 有 无 排 铅 槽 对 炉 底 炉 缸 不 同侵 蚀 阶段 的 温 度 场
分布影 响, 研 究 了该 高 炉 的侵 蚀 演 变 规 律 , 从 而 确 定 了 排 铅 槽 的合 理 设 置 位 置 。 同 时指 出 应 根 据 高 炉 铅
Do ng Ho n g wa ng‘ , Zh a o Ho n g bo
( 1 . Ta n g s h a n I n t e r n a t i o n a l I r o n a n d S t e e l E n g i n e e r i n g T e c h n i q u e Co . ,Lt d .,T a n g s h a n,He b e i ,0 6 3 0 0 9;
f r o m t he b ot t om o f bl a s t f u r na c e t o a d a p t t he c ha ng e i n b u r de n. Ba s e d o n t h e ph ys i c a l mo de l i ng f o r bo t t o m a n d h e a r t h o f bl a s t f u r na c e a nd n um e r i c a l s i m ul a t i o n o f he a t c on d uc t i o n,i t i s a na l y z e d t h e i nf l u e nc e o f l e a d d r a i n a g e t r o u gh on t h e t e m pe r a t u r e f ie l ds o f b o t t om a n d he a r t h o f bl a s t f u r n a c e d u r i n g di f f e r e n t e t c hi ng s t a — g es ,r e s ea r c h e d t he e t c h i n g e v o l u t i o n l a w o f t h i s b l a s t f u r na c e,a n d S O t h e r ea s o na bl e s e t t i ng l o c a t i o n of t he t r o u gh c a n b e d e t e r mi n e d. A t t h e s a me t i me i t i s po i nt e d o ut t ha t t h e l e a d d r a i na g e s ys t e m s ho ul d b e ma de
高炉热平衡计算方法

高炉热平衡计算方法4.3热平衡计算过程需要补充的原始条件:鼓风温度1100℃;炉顶温度200℃;入炉矿石温度为80℃。
4.3.1 热量收入(1)碳素氧化热由C 氧化1m³ 成CO 2放热1222.433410.66⨯=17898.43 KJ/m³由C 氧化成1m³ 的CO 放热1222.49797.11⨯=5250.50 KJ/m ³碳素氧化热=288.45×19878.43+(435.04-2.22)×5250.50=8006454.54 KJ(2)热风带入热1100 ℃时干空气的比热容为1.429kJ / m 3·℃ ,水蒸气的比热为1.753 kJ / m 3·℃,热风带入热=[(1238.89-18.58)×1.429+18.58×1.753]×1100=1954033.10 KJ(3)成渣热炉料中以碳酸盐形式存在的CaO 和MgO ,在高炉内生成钙铝酸盐时,1kg 放出热量1130.49 kJ混合矿的CaO=1666.82×0.0154×4456=32.67 KJ 成渣热=32.67×1130.49=36933.10 kJ (4)混合矿带入的物理热80 ℃时混合矿的比热容为1.0 KJ/Kg·℃混合矿带入的物理热=1666.82×1.0×80=133345.60 kJ (5)H 2氧化放热1m³ H 2氧化成H 2O 放热10806.65 KJ H 2氧化放热=51.81×10806.65=559892.53 kJ (6)CH 4生成热1Kg CH 4生成热=1677874.4=4865.29 KJCH 4的生成热=10.78×22.416×4865.29=37462.73 KJ冶炼1t 生铁总热为以上各热量的总和Q总收=8006454.54+1954033.10+36933.10+133345.60+559892.53+37462.7 3=10728121.6KJ4.3.2 热量支出(1) 氧化物分解与脱硫耗热1)铁氧化物分解热:设焦炭和煤粉中FeO 以硅酸铁形态存在,烧结矿中FeO 有20%以硅酸铁形态存在其余以Fe 3O 4,铁氧化物分解热由FeO 、Fe 3O 4和 Fe 2O 3三部分组成。
《炼铁工艺》复习题及答案

1-1高炉炼铁工艺由哪几部分组成?答案(1):在高炉炼铁生产在中,高炉是工艺流程的主体,从其上部装入的铁矿石燃料和溶剂向下运动,下部鼓入空气燃烧燃料,产生大量的还原性气体向上运动。
炉料经过加热、还原、熔化、造渣、渗碳、脱硫等一系列物理化学过程,最后生成液态炉渣和生铁。
组成除高炉本体外,还有原料系统、上料系统、装料系统、送风系统、冷却系统、、回收煤气与除尘系统、喷吹系统等辅助系统。
1-2高炉炼铁有哪些技术经济指标?答案:有效容积利用率、焦比、冶炼强度、焦炭负荷、生铁合格率、休风率、生铁成本、炉龄。
答案:各个系统相互配合,互相制约大规模、高温、连续性、多工种1-4高炉送风系统的主要作用是什么?答:保证连续可靠地供给高炉冶炼所需数量和足够温度的热风。
1-5高炉生产有哪些产品和副产品,各有何用途?答案:高炉冶炼主要产品是生铁,炉渣和高炉煤气是副产品。
(1)生铁。
按其成分和用途可分为三类:炼钢铁,铸造铁,铁合金。
(2)炉渣。
炉渣是高炉生产的副产品,在工业上用途很广泛。
按其处理方法分为:1)水渣:水渣是良好的水泥原料和建筑材料。
2)渣棉:作绝热材料,用于建筑业和生产中。
3)干渣块:代替天然矿石做建筑材料或铺路用。
(3)高炉煤气。
高炉煤气可作燃料用。
除高炉热风炉消耗一部分外,其余可供动力、烧结、炼钢、炼焦、轧钢均热炉等使用。
1-6影响高炉寿命因素,如何长寿?答:从工作区域看,有两个限制性环节:一是炉缸底的寿命;二是炉腹炉腰及炉身下部寿命。
实现长寿,需具备:(1)高炉内型合理;(2)耐火材料质量优质;(3)先进的冷却系统和冷却设备;(4)完善的自动化检测与控制手段;(5)高水平检测维护手段。
2-1高炉常用的铁矿石有哪几种,各有什么特点?答:高炉炼铁使用的铁矿石分为赤铁矿(红矿)Fe2O3、磁铁矿(黑矿)Fe3O4、褐铁矿Fe2O3•nH2O和菱铁矿FeCO3。
赤铁矿又称红铁矿,其颜色为赤褐色到暗红色,硫、磷含量低,其在常温下无磁性,但在一定温度下,当α—Fe2O3转变为γ—Fe2O3时便具有磁性。
氧气高炉冷态模型的设计计算

氧气高炉冷态模型的设计计算
氧气高炉是一种先进的冶炼设备,其冷态模型的设计计算是确定炉身温度分布和炉身
结构的关键。
本文将介绍氧气高炉冷态模型的设计计算方法。
1. 炉身温度分布的计算:根据高炉的结构、材料和冷却方式,利用传热学计算方法,确定炉身各部位的温度分布。
需要建立炉身的数学模型,包括高炉炉身的几何形状和热物
性参数。
然后,利用传热学的理论和方法,根据高炉内部的热源和热传导条件,计算各部
位的温度分布。
对计算结果进行验证和调整,确保计算的准确性和可靠性。
2. 炉身结构的设计:根据炉身温度分布的计算结果,确定炉身的结构设计参数。
高
炉的炉身结构需要满足强度和稳定性的要求,同时能够适应高炉内部温度分布的变化和热
膨胀的影响。
炉身结构的设计包括材料的选择、特殊部位的加固和防护措施等。
4. 炉身热应力的计算:根据炉身温度分布和炉身结构的设计,利用热应力学的理论
和方法,计算炉身的热应力。
高炉的炉身在冷热循环过程中会受到热膨胀和热应力的影响,可能导致炉身的损坏和破裂。
炉身热应力的计算可以用来评估炉身的可靠性和安全性,为
炉身结构的优化设计提供依据。
以上就是氧气高炉冷态模型的设计计算方法的基本介绍。
在实际的工程应用中,还需
要考虑其他因素,如煤质、炉渣、热风温度等对高炉运行的影响,以及高炉的升温、卸渣、装料等操作过程的控制和优化。
氧气高炉冷态模型的设计计算是一个复杂而重要的工作,
需要结合实际情况进行综合分析和研究。
高炉炉缸炉底内衬的等效冷却条件计算方法
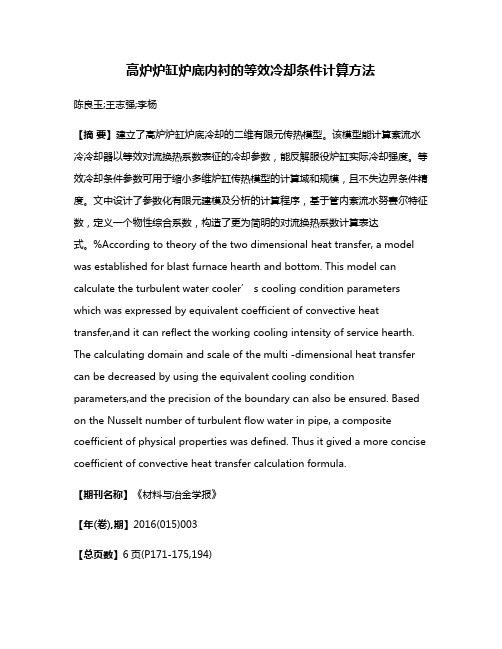
高炉炉缸炉底内衬的等效冷却条件计算方法陈良玉;王志强;李杨【摘要】建立了高炉炉缸炉底冷却的二维有限元传热模型。
该模型能计算紊流水冷冷却器以等效对流换热系数表征的冷却参数,能反解服役炉缸实际冷却强度。
等效冷却条件参数可用于缩小多维炉缸传热模型的计算域和规模,且不失边界条件精度。
文中设计了参数化有限元建模及分析的计算程序,基于管内紊流水努赛尔特征数,定义一个物性综合系数,构造了更为简明的对流换热系数计算表达式。
%According to theory of the two dimensional heat transfer, a model was established for blast furnace hearth and bottom. This model can calculate the turbulent water cooler’ s cooling condition parameters which was expressed by equivalent coefficient of convective heat transfer,and it can reflect the working cooling intensity of service hearth. The calculating domain and scale of the multi -dimensional heat transfer can be decreased by using the equivalent cooling condition parameters,and the precision of the boundary can also be ensured. Based on the Nusselt number of turbulent flow water in pipe, a composite coefficient of physical properties was defined. Thus it gived a more concise coefficient of convective heat transfer calculation formula.【期刊名称】《材料与冶金学报》【年(卷),期】2016(015)003【总页数】6页(P171-175,194)【关键词】高炉缸炉;传热;等效对流换热系数【作者】陈良玉;王志强;李杨【作者单位】东北大学机械工程与自动化学院,沈阳 110819;东北大学机械工程与自动化学院,沈阳 110819;东北大学机械工程与自动化学院,沈阳 110819【正文语种】中文【中图分类】TF572冷却是高炉炉缸结构安全和长寿的重要的必要条件[1].目前高炉炉缸多采用水冷光面铸铁冷却壁,炉底采用直排水冷管,使用大水量、较高流速紊流通水冷却.数值传热学是高炉炉缸传热分析的重要手段,冷却条件参数是数值传热模型的必要条件[2],尽管管内水的对流换热系数可由准数关联式确定[3],但它作用在相对于整个炉缸结构属于小尺寸的水管壁面上,而处理小尺寸会使计算模型规模过大.还有,冷却壁本体与水管间存在防渗碳涂料和铸造间隙的热阻、炉底水管与不定型材料之间的接触热阻,若在整体模型包含这些热阻又会进一步增大模型规模及复杂程度.水冷管内的换热系数经管壁、冷却器本体的热阻、间隙或接触热阻衰减后作用在炉缸炉底内衬上,若能确定炉缸炉底内衬冷面上的冷却参数并以此为传热外边界,则可把模型的冷却边界内移,缩小计算域、减小模型规模,另外内衬冷面冷却参数对评估炉缸炉底的冷却情况尤其是服役中的冷却情况更为直接.本文根据二维传热理论,建立炉缸冷却壁和炉底水冷管冷却的有限元传热模型,研究计算作用在内衬冷面的等效对流换热系数,以期缩小炉缸整体传热模型计算域、规模,并提供不失精确性的热边界条件.在模型研究的基础上,通过设计的基于ANSYS有限元分析系统的参数化计算程序,计算分析并讨论炉缸内衬等效条件参数,还作了服役高炉炉底实际冷却强度实例分析.管内水的紊流换热的准数关联式和对流换热系数可由下列计算式确定:由式(1)、式(2),管内壁的对流换热系数hG有式中, fw为水的综合物性系数其值随温度tw变化(表1,图1),温度(tw= 10~100 ℃)拟合式为2.1 传热模型高炉炉缸冷却壁中水管的蛇形、U型排布,其横截面呈等距圆孔形式,埋设在不定型耐火材料中的炉底水冷,其纵剖面也成等距圆孔形式.炉内热量经水冷管导出为单侧冷却方式,可建立图2所示的单根水冷管传热模型.图2中,s为水管间距;b为炉缸冷却壁或炉底水管填料的厚度;a为内衬厚度;c为内衬与冷却器间的辅助材料厚度,通常为填料,下置水冷管的炉底还有钢质封板; D、δ为水管内径、壁厚;δQ为铸造冷却壁-水管间隙或水管填料接触热阻的等效间隙.传热边界条件:内衬热面温度tn;冷却水温度tw;水管内水对流换热系数hG,由水速、管径按式(3)确定.相比水冷管的换热,炉缸炉壳、炉基的散热很小,可略去.因单侧冷却且管内换热系数大,水管周围的传热呈显著的二维特征,需用数值传热计算,本文采用有限单元法.2.2 模型离散与参数处理(1)考虑到水管周围传热的复杂性,数值离散时水管内壁单元尺寸应作细化,一般沿管周长分30~50单元.(2)小尺寸的间隙按其热阻等效到相邻材料上,相应地计算等效导热系数.按一维圆筒传热理论,包含水管外壁间隙热阻的水管导热系数为式中, kG、kGeqv分别为水管的导热系数、等效导热系数, kQ为间隙的导热系数.对于炉底下置水管系统,炉底封板与水管填料接触热阻等效进封板,封板等效导热系数为式中, kB、 kBeqv分别为封板导热系数、等效导热系数, e为封板厚度,δBQ为水管填料-封板接触热阻的等效间隙厚度.2.3 等效对流换热系数的计算作模型的有限元传热分析后,可提取平均热流密度q和冷却器热面平均温度tb或内衬冷面平均温度te,根据一维平壁定常传热理论,冷却水温度不变时,按牛顿冷却式冷却器热面、内衬冷面的冷却强度——对流换热系数hb、 he为两者满足热阻平衡式[4],即式中, Rc为冷却器热面、内衬冷面间的材料热阻.对流换热系数hb、 he的大小与内衬热阻和内衬热面温度无关.本文使用ANSYS系统作模型的传热分析,并设计了APDL语言的参数化计算程序[6,7].给定模型尺寸、材料导热系数、热边界条件参数,程序可完成模型离散、边界条件施加、传热分析和冷却壁热面对流换热系数计算.3.1 炉缸冷却壁计算例尺寸和参数如下:钢质水管内径为 D=33, 48, 64 mm,壁厚δ=6 mm,导热系数50 W/(m·K);铸铁冷却壁厚对应水管内径的厚度为120, 140, 160 mm,导热系数40 W/(m·K);冷却壁本体-水管间隙δQ= 0.1 mm,导热系数0.023W/(m·K);内衬碳砖与冷却壁顶砌,c= 0 mm. 水管间距s=180, 200, 220,240 mm;管内水速v=1.0~4.0 m/s;冷却水平均温度tw=30 ℃.内衬厚度a=800 mm,导热系数10 W/(m·K),热面温度tn=1 150 ℃.图3为冷却壁热面等效对流传热hb随管径D、间距s、水速v变化情况.随v增大,hb呈非线性增大,水速由低到高hb增大变缓;水速相同时水管间距s减小,hb增大.3.2 炉底水冷管计算模型的尺寸和参数如下:钢质水管内径D为64, 80, 96 mm,壁厚δ=6 mm,导热系数50 W/(m·K);水管填料厚b=200 mm;水管与填料等效接触间隙δQ= 0.1 mm,导热系数0.023 W/(m·K);内衬碳砖、水管填料间找平填料(厚度100 mm)和钢质炉底封板(厚度25 mm);水管填料与炉底封板接触热阻的等效间隙δBQ=0.1 mm.水管间距s=300 mm;管内水速v=0.5~2.0 m/s;冷却水平均温度tw=30 ℃.内衬厚度a=800 mm,导热系数10 W/(m·K),热面温度500 ℃. 取找平层、水管的填料导热系数k=7, 10, 13 W/(m·K).图4为炉底内衬底面等效换热传热he随管径D、填料导热系数k、水速v变化情况.可见随v增大,he呈非线性增大,水速由低到高he增大变缓;水速相同时k增大(热阻减小),he增大.3.3 分析与讨论在计算参数范围内时,尽管管内紊流水的换热系数hG(=2 000~1 2000W/(m2·K))高,但经过多个热阻的衰减,炉缸冷却壁热面的对流换热系数降低到97~183 W/(m2·K),衰减大,炉底内衬底面的降低到24~42 W/(m2·K),衰减更大.hb、he为作用在炉缸冷却器热面、内衬冷面上的等效对流换热系数,用于炉缸多维尤其是三维整体传热学建模与分析,可避免对小尺寸冷却器水管处理,进而实现缩小计算域和模型规模而不降低边界条件的精度.4.1 实例的计算某炉容1 080 m3高炉,服役3年.炉底为炉封板下置水冷管冷却,水管内径6 mm,壁厚6 mm,间距300 mm.找平层厚96 mm;炉底封板25 mm;水管填料层170 mm,水冷管位于中点.单根水管水流量20.8 m3/h,冷却水温度27.5 ℃.高炉砌筑时实测内衬碳砖导热系数(见表2),找平层填料导热系数12W/(m·K),水管填料上层、下层导热系数分别为10 W/(m·K)、3 W/(m·K).内衬找平层中点、第2层砖(砖厚400 mm)的中心有实测温度t1=140 ℃、t2=307 ℃.利用图2所示的模型,给定尺寸、参数,使用设计的有限元数值传热分析程序,按水管-填料间隙、封板-填料间隙相同即δQ=δB Q作反解计算,因内衬导热系数随温度变化,设定非线性求解模式.给定第2层碳砖热面实测温度t2(= 307 ℃),施加水管内壁面对流换热条件,以间隙δQ为待定值并调整,以找平层实测温度t1为核定值,以t1的计算值与实测值(140 ℃)的相对差≤0.5%为终止计算条件,作逼近计算.计算中忽略了炉缸侧壁冷却、炉底内衬工作形貌等两个影响较小的因素.计算结果见表3,炉底中心部位温度云图见图5.由表3,当前水速为v=1.796 m/s,中心热流密度q=1 702.2 W/m2,炉底内衬底面实际对流换热系数he=14.22 W/(m2·K),水管填料热面对流换热系数hb= 24.41 W/(m2·K),水管-填料、封板-填料的等效间隙各为0.48 mm.按当前水速、水温,取水管-填料、封板-填料间无接触热阻(δQ=δBQ=0)计算,得理论值he=53.92 W/(m2·K),hb=99.55 W/(m2·K).炉底实际冷却强度为理论值的26.37%,存在附加热阻性的冷却缺陷.4.2 实例的分析与讨论当结构和水量、温度一定时,无接触热阻的冷却器热面的等效对流换热系数是理论值.考虑建筑施工质量和生产实际的影响,引入一定量的间隙热阻确定的对流换热系数为设计值.根据服役高炉炉缸炉底的实测热工参数(内衬温度、冷却器热负荷等),由文中所建模型和计算方法可判断以对流换热系数表征的实际冷却强度.若实际冷却强度比理论值、设计值低过多,则可判定存在间隙热阻和冷却缺陷.本文作者对国内100多座炉容400~2 500 m3服役高炉炉底内衬温度、冷却情况和散热量作了实际调查和计算,炉底封板下置水冷管的炉底内衬底面的实际换热系数高不过30~35W/(m2·K),低的不足5 W/(m2·K),10~15 W/(m2·K)的占比约70%,表明存在正常热阻之外的接触、间隙等附加热阻,基本现象为炉底内衬温度高而水冷管热流量小.因填料厚度减小尤其是消除了封板、填料间的接触热阻,封板上置水冷管的炉底内衬底面对流换热系数大多在35~55 W/(m2·K),高的达到65 W/(m2·K),封板上置水冷管在发挥冷却能力上好于下置的.服役炉缸炉底常出现炉缸炉底窜入热煤气的情况.当冷却器、内衬间窜入热煤气时,内衬温度升高、冷却器热负荷增大;当炉缸炉壳、冷却壁间窜煤气,冷却壁热负荷增大、炉壳温度升高[5].文中的模型和计算方法用于服役高炉时似应注意窜煤气的影响.(1)提出并建立了计算冷却壁热面、炉底内衬底面的以等效对流换热系数表征冷却强度的炉缸炉底冷却传热的二维有限元模型.计算表明,该模型及方法能计算冷却强度的理论值、设计值,能反解评估服役炉缸的实际冷却强度、识别冷却缺陷. (2)把冷却器热面等效冷却条件参数用于炉缸多维整体传热建模及分析可避免冷却器水管、接触热阻等小尺寸建模、增加建模复杂性,进而缩小计算区域和模型规模而又保证边界条件精度.(3)定义了一个水物性综合系数fw并给出其温度拟合式,进而给出了一个简明的管内紊流对流换热系数计算表达式.【相关文献】[1]周传典. 高炉炼铁生产技术手册[M]. 北京: 冶金工业出版社, 2003. (Zhou Chuandian. Blast furnace ironmaking production technical manuals[M]. Beijing: Metallurgical Industry Press, 2003.)[2]沈熙身, 李保卫, 吴懋林. 冶金传输原理基础[M]. 北京:冶金工业出版社, 2003. (Shen Xishen, Li Baowei, Wu maolin. Principles of transfer in metallurgy[M]. Beijing: Metallurgical Industry press, 2003.)[3]Elsaadawy E, Lu W-K. 3D mathematical modeling of flows in the deadman/hearth region of a blast furnace[C]// Iron and Steel Technology Conference Proceedings. 2006:471-480.[4]陈良玉, 李玉. 冷却壁对流换热边界的等效置换与导热模型化简[J]. 钢铁研究, 2007, 36(6): 26-29. (Chen Liangyu, Li Yu. Convective heat transfer boundary equivalent replacement and model simplification of cooling stave of blase furnace hearth[J]. Research on Iron and Steel, 2007, 36(6): 26-29.)[5]Chen Liangyu, Li Yu, Lu Chao-yang. Judgment method for the gas gap of BF hearth lining[C]// Proceeging of 5th Inter. Congress on the Science and Technology of Ironmaking (ICSTI’09): 864-868, 2009, Shanghai, China.[6]张朝晖. ANSYS 8. 0热分析教程与实例解析[M] . 北京: 中国铁道出版社, 2005. (Zhang Chaohui. ANSYS 8. 0 thermal analysis course and case analyze[M]. Beijing: China Railway Publishing House. 2005.)[7]ANSYS User’s manual[M]. Swanson Analysis Systems, Inc, 2003.[8] Holman J P. Heat transfer[M]. McGraw-Hill Companies Inc, 2005.。
炉内传热及其计算

西 安 交 通 大 学 锅 炉 研 究 所
西 安 交 通 大 学 锅 炉 研 究 所
西 安 交 通 大 学 锅 炉 研 究 所
西 安 交 通 大 学 锅 炉 研 究 所
1.特点 ①炉膛内的传热过程与燃料的燃烧过程同时进行,参 与燃烧与传热过程的各因素相互影响。例如,燃料种 类不同燃烧过程不尽相同,形成的火焰成分及温度场 不同,炉膛的吸热量就会不同,即传热过程不同。反 之,传热过程不同就会导致温度场发生变化,影响燃 烧及燃尽。 ②炉膛传热以辐射为主,对流所占比例很小。 原因: 炉膛内火焰温度较高,例如1000℃左右,而四周水冷 壁管的温度较低,例如≤400℃ 炉膛内烟气流速较低,因此,对流传热量占总换热量 的份额很小,一般≤5%。
al
西 安 交 通 大 学 锅 炉 研 究 所
1 1 a hy 1
a hy 1 a hy
1
其中 为炉排面积R与炉膛总壁面积 F l 之比 (不包括R)
R Fl
§4火焰黑度
在炉膛黑度的计算式中,除 外,还须知道 a , 即火焰黑度,那么怎样计算 a 呢?
4 4
m
均为 和 的函数,联立后消去α和β,
得到:
hy f l , X
m
此函数关系画在图上
西 安 交 通 大 学 锅 炉 研 究 所
可以看出,Xm不变时, lg 与 lg l 呈线性关系. 因此有 n hy 4 m l
hy
m和n均是Xm的函数
lg 截距近似为0,
q5
''
q5
西 安 交 通 大 学 锅 炉 研 究 所
B j—计算燃料消耗量
2高炉保温理论依据测算
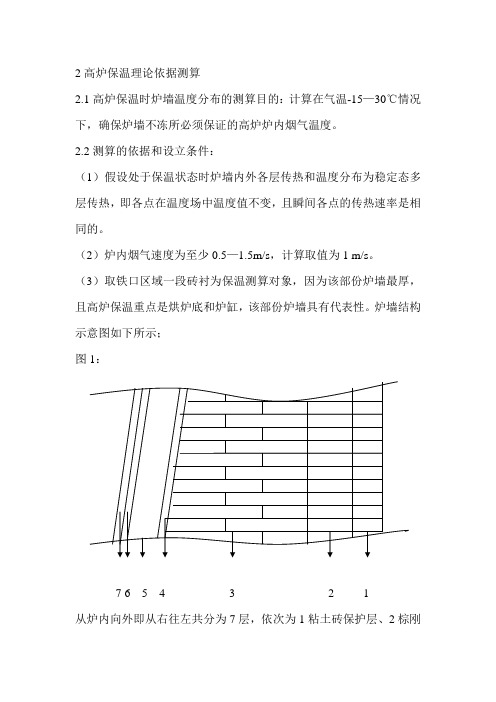
2高炉保温理论依据测算2.1高炉保温时炉墙温度分布的测算目的:计算在气温-15—30℃情况下,确保炉墙不冻所必须保证的高炉炉内烟气温度。
2.2测算的依据和设立条件:(1)假设处于保温状态时炉墙内外各层传热和温度分布为稳定态多层传热,即各点在温度场中温度值不变,且瞬间各点的传热速率是相同的。
(2)炉内烟气速度为至少0.5—1.5m/s,计算取值为1 m/s。
(3)取铁口区域一段砖衬为保温测算对象,因为该部份炉墙最厚,且高炉保温重点是烘炉底和炉缸,该部份炉墙具有代表性。
炉墙结构示意图如下所示;图1:7 6 5 4 3 2 1从炉内向外即从右往左共分为7层,依次为1粘土砖保护层、2棕刚玉砖、3微孔炭砖、4炭捣层、5冷却壁、6灌浆层(尚未灌浆)、7炉壳。
(4)灌浆层现尚未灌浆,里面主要是空气,此外还有施工中落在里面的物料和烘炉过程中有可能渗入的水;传热方式有对流传热,还有通过各冷却壁、冷却板、冷却水箱管道的传导传热,由于不清楚落在里面的物料的填充率及传导传热所占比例,按全部为空气层和全部为粘土质耐火泥料层计算,并按该段平均直径和最大直径分别进行计算。
(5)炉内烟气与粘土砖的传热设为强制对流传热,按相似准数定律确定对流给热系数。
2.3计算方法与公式按炉墙平均直径计算时假定炉壳外表面温度为-15—30℃,按炉墙最大直径计算时设为-10℃,采取多次逼近的计算方法。
计算所得数据经验算后与设定值接近或在误差范围内,即可视为设定条件成立,否则将所得数据设为条件再代入计算,如此循环,多次逼近,直到取得合格数据。
高炉炉墙从内到外可视为多层圆筒传热,按单位长度稳定态多层传热公式进行计算:Q=K(t内-t气)Q—单位时间内传输的热量,即传热速率,W/m;t内—炉内烟气温度,℃;t气—气温,℃;K —综合传热系数,w/℃。
K=123456712345671234567111F F F F F F F F F s s s s s s s a a λλλλλλλ++++++++内内均均均均均均均外外其中:S —各层的厚度,S 1、 S 2 、S 3 、S 4、S 5、S 6 S 7分别对应粘土砖、棕刚玉砖、炭砖、炭捣层、冷却壁、灌浆层、炉壳的厚度, m ;λ—各层的传热系数,λ1~λ7分别对应上述各层,w/(m ·℃); F —各层的单位长度的平均传热面积,F 1~F 7分别对应上述粘土砖、棕刚玉砖、炭砖、炭捣层、冷却壁、灌浆层、炉壳各层单位长度平均传热面积,m 2;F 内—炉内即粘土砖内表面单位长度的面积,m 2/m ; F 外—炉壳外表面单位长度的面积,m 2/m ;α内—炉内烟气对炉墙内壁的对流给热系数,W/(m 2·℃); α外—大气对炉壳的对流给热系数,W/(m 2·℃)按炉墙平均直径计算时,各层半径尺寸及对应温度如下图所示: 图2:半径: R 8R 7 R 6 R 5 R 4 R 3 R 2 R 1 温度: t 8t 7 t 6 t 5 t 4 t 3 t 2 t 1 2.4计算结果表3:按铁口区域炉墙平均直径计算F=πD,m2/m经计算得各环层面积,且F2/F1、F3/F2……F8/F7<2,所以F1均=(F1+F2)/2、F2均=(F2+F3)/2……F7均=(F7+F8)/2表4:经计算得各环层面积α内按强制对流给热计算,按烟气速度1m/s得出Re(雷诺准数)>10000,即假设成立。
氧气高炉冷态模型的设计计算
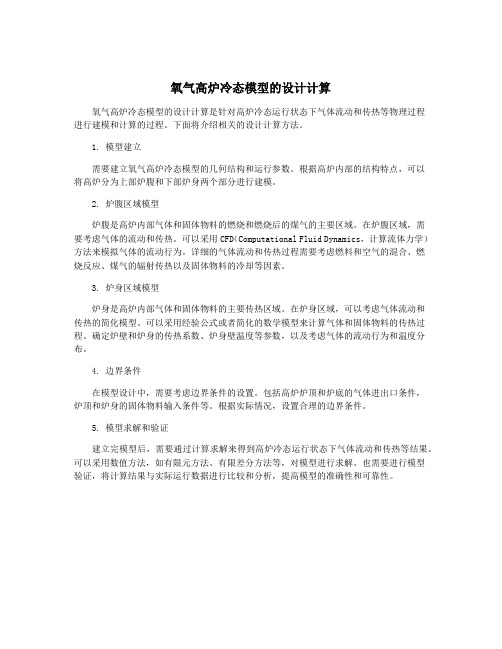
氧气高炉冷态模型的设计计算氧气高炉冷态模型的设计计算是针对高炉冷态运行状态下气体流动和传热等物理过程进行建模和计算的过程。
下面将介绍相关的设计计算方法。
1. 模型建立需要建立氧气高炉冷态模型的几何结构和运行参数。
根据高炉内部的结构特点,可以将高炉分为上部炉腹和下部炉身两个部分进行建模。
2. 炉腹区域模型炉腹是高炉内部气体和固体物料的燃烧和燃烧后的煤气的主要区域。
在炉腹区域,需要考虑气体的流动和传热。
可以采用CFD(Computational Fluid Dynamics,计算流体力学)方法来模拟气体的流动行为。
详细的气体流动和传热过程需要考虑燃料和空气的混合、燃烧反应、煤气的辐射传热以及固体物料的冷却等因素。
3. 炉身区域模型炉身是高炉内部气体和固体物料的主要传热区域。
在炉身区域,可以考虑气体流动和传热的简化模型。
可以采用经验公式或者简化的数学模型来计算气体和固体物料的传热过程。
确定炉壁和炉身的传热系数、炉身壁温度等参数,以及考虑气体的流动行为和温度分布。
4. 边界条件在模型设计中,需要考虑边界条件的设置。
包括高炉炉顶和炉底的气体进出口条件,炉顶和炉身的固体物料输入条件等。
根据实际情况,设置合理的边界条件。
5. 模型求解和验证建立完模型后,需要通过计算求解来得到高炉冷态运行状态下气体流动和传热等结果。
可以采用数值方法,如有限元方法、有限差分方法等,对模型进行求解。
也需要进行模型验证,将计算结果与实际运行数据进行比较和分析,提高模型的准确性和可靠性。
02炉膛传热计算02

" l
Ta
3 o l pj FT l a M B V C j y pj 0.6
273 1
Q (Ql Il" )
计算过程: 1、假定θl’’ 2、计算 M、 、Vcpj、al、Ta 2、用该公式计算θl’’ 3、检验假设
对流换热面计算
ahy 1 e s 3.6 Vl Fl
kps
k 火焰辐射减弱系数 p 炉膛压力 s 炉膛的有效辐射层厚度 Vl 炉膛容积 Fl 炉壁面积
关键是求k
k h 火焰中悬浮灰粒辐射减 弱系数 kh 55900
3 2 Tl"d h
h 飞灰浓度
k j 火焰中焦炭颗粒的辐射 减弱系数 x1 , x2 影响系数
Ql VC p 0
该如何求绝热燃烧温度呢?根据Ql查炉膛处烟气焓温表,找出温度对应值。 示例! ((F10-24195.29)*100)/‘烟气焓温表(炉膛、 屏式过热器、高温过热器)’!F36:F37+1900)
1.炉膛传热原理
热平衡方程: 未知
4 xt Fb0 (Thy Tb4 ) BjVc pj (Ta Tl" )
1.假设炉膛出口温度 2.某些物理量的定义 其它炉型及公式看看书即可,求解方法大同小异!
3.炉膛黑度计算
一、炉膛黑度计算 说明:炉膛黑度是进行炉膛热力计算时引进对应于火焰有效辐射的 假想黑度。其与火焰黑度和炉壁黑度有一定关系。
q yx1 q yx2 q yx1
q yx1 火焰对炉壁的有效辐射 热负荷 q yx2 炉壁对火焰的有效反辐 射热负荷
2.对流受热面的传热计算
针对过热器再热器具体公式为:
- 1、下载文档前请自行甄别文档内容的完整性,平台不提供额外的编辑、内容补充、找答案等附加服务。
- 2、"仅部分预览"的文档,不可在线预览部分如存在完整性等问题,可反馈申请退款(可完整预览的文档不适用该条件!)。
- 3、如文档侵犯您的权益,请联系客服反馈,我们会尽快为您处理(人工客服工作时间:9:00-18:30)。
第16卷第5期2004年10月 钢铁研究学报JOURNAL OF IRON AND STEEL RESEARCHVol.16,No.5 Oct.2004基金项目:国家自然科学基金资助项目作者简介:程树森(19642),男,博士,教授; 收稿日期:2003201210; 修订日期:2004201210・冶金与金属加工・高炉炉身下部及炉缸、炉底冷却系统的传热学计算程树森1, 杨天钧1, 左海滨1, 孙 磊1, 杨为国2, 潘奉贤3(1.北京科技大学冶金学院,北京100083; 2.北京钢铁设计研究总院炼铁室,北京100053;3.韩国顺天国立大学工科学院,顺天)摘 要:在高炉冷却器及炉缸、炉底热面凝结一层渣铁壳有利于防止炉衬侵蚀,延长高炉寿命。
为了达到这一目的,需要设计无过热的铸铁冷却壁、铜冷却壁和板2壁结合冷却器以及无过热的炉缸和炉底。
为此建立了高炉炉身下部冷却器及炉缸、炉底温度场的数学模型,应用C ++语言在VC++集成环境下开发了高炉炉身下部冷却器及炉缸、炉底温度场计算软件。
计算结果表明,通过优化炉身下部冷却器及炉缸、炉底的设计参数,能够确保在冷却器热面及炉缸、炉底热面凝结一层渣铁壳。
目前,国内一些大型高炉的设计中已采用该软件。
关键词:高炉;冷却系统;温度场;数学模型中图分类号:TF57311 文献标识码:A 文章编号:100120963(2004)0520010205Design of Low er Shaft and H earth Bottom forLong C ampaign B last FurnaceCHEN G Shu 2sen 1, YAN G Tian 2jun 1, ZUO Hai 2bin 1, SUN Lei 1,YAN G Wei 2guo 2, PAN Feng 2xian 3(1.University of Science and Technology Beijing ,Beijing 100083,China ; 2.Central Eengineering and Incorporation of Beijing ,Beijing 100053,China ; 3.Sunchon National University ,Sunchon City ,S outh K orea )Abstract :A model for calculating the temperature distribution of the stave and the hearth bottom and a mathematical model of tem perature distribution of lower shaft cooler and hearth bottom of blast furnace were built.The computational software of the tem perature field was developed by using C ++language in VC ++integrated environment.The calculation results show that the formation of the protection shell can be achieved by optimizing the parameters for designing the stave and the hearth bottom.The software has been used to design blast furnace of some large companies in China.K ey w ords :blast furnace ;cooling system ;temperature field ;mathematical model符 号 总 表 c p ———定压比热容,J/(kg ・℃); D ———冷却水管直径,mm ; d ———冷却板中冷却通道的等效直径,m ; grad ———梯度算符; H ———铁水热焓; h ———铁水的凝固潜热,J/kg ; L ———冷却壁1/2肋与1/2镶砖高度之和,mm ; l ———冷却水管间距,mm ; r ———炉缸、炉底半径,m ; S ———凝固率; s———冷却水管中心线与冷却壁热面的距离,mm; T———温度,℃; T壳———炉壳表面温度,℃; T煤———炉内煤气温度,℃; t———时间,s; V———铁水体积,m3; v———冷却水流速,m/s; x,y,z———空间坐标; α壳2气———炉壳与大气的综合对流换热系数,W/(m2・℃); α壁2水———冷却壁本体与冷却水之间的综合对流换热系数,W/(m2・℃); α煤2墙———炉内煤气热流与炉墙之间的综合对流换热系数,W/(m2・℃); α板2水———冷却板与冷却水之间的综合对流换热系数, W/(m2・℃); λ———导热系数,W/(m・℃); λ水———冷却水的导热系数,W/(m・℃); λ砖———碳砖的导热系数,W/(m・℃); ρ———密度,kg/m3; Re———雷诺数; N u———努塞尔数; Pr———普郎特数。
现代大型高炉长寿有两个限制性环节:一个是炉缸、炉底容易烧穿;另一个是炉腹、炉腰及炉身下部寿命短。
高炉生产实践证明,随着冶炼强度不断提高,因炉腹、炉腰及炉身下部冷却器的烧毁或炉缸、炉底的烧穿而导致的高炉停炉事故屡见不鲜。
炉身下部冷却器及炉缸、炉底烧毁的机理主要是铁水的冲刷、氧化和化学侵蚀。
只要将铁水与冷却器及炉缸、炉底隔离,便可阻止渣铁的侵蚀。
目前,用于高炉的耐火炉衬都不能长期经受高温铁水的侵蚀,只有在炉身下部冷却器及炉缸、炉底凝结一层渣铁壳作为耐火炉衬的保护层。
为此尝试了根据传热学理论建立炉身下部冷却器及炉缸、炉底温度场数学模型,应用数值分析结果指导设计,将铸铁冷却壁及铜冷却壁损坏的临界温度(760℃[1]及200℃[2])推离冷却器热面,并将1150℃[3]及870℃[4]等温线推离炉缸、炉底碳砖热面,使炉身下部冷却器及炉缸、炉底热面凝结一层渣铁壳,将侵蚀物与其隔离开,从而阻止侵蚀发生,以保证高炉长寿。
1 炉身下部冷却器的设计 炉身下部的冷却器有各种类型。
按结构划分,有冷却壁式、冷却板式及板2壁结合式等;按材质划分,有铸铁质、铜质等。
笔者应用经实验验证的冷却器温度场计算软件计算了炉衬内表面温度和热流通量的分布,分析了冷却器结构参数(包括本体厚度、肋间距、镶砖面积、水管直径及中心间距和水管位置等)、操作参数、冷却介质、炉衬厚度和炉衬材质、渣铁壳厚度等因素对冷却器温度分布的影响。
111 冷却器温度场的数学模型 根据热力学第一定律,三维导热微分方程[1~4]为: ρc p5T5t+ [λ(T)grad T(x,y,z)]=0 该方程的定解条件为: ①对称面上的边界条件均为第二类边界条件,一般设定热流通量为零; ②炉壳与大气之间为对流换热,属于第三类边界条件,其综合对流换热系数为: α壳2气=913+01058T壳 ③冷却板与冷却水之间为对流换热,属于第三类边界条件。
依据泰托斯公式,其综合对流换热系数为: α板2水=(λ/d)N u N u=01023Re018Pr014 ④冷却壁本体与冷却水之间的综合对流换热系数为: α壁2水=208+4715v ⑤炉衬内侧的边界条件为第三类边界条件,炉内煤气流与炉墙的综合对流换热系数为: α煤2墙=232 W/(m2・℃) 炉内煤气流温度设定为T煤=1200℃。
112 计算结果及分析11211 铸铁冷却壁结构对温度场的影响 图1示出冷却壁结构参数不同时其内部的等温线分布情况。
改变冷却壁结构参数可降低冷却壁热面温度。
具体来说,增加冷却水管直径或缩短冷却水管间距和冷却水管至冷却壁热面的距离或者减小镶砖厚度和镶砖面积都将减小冷却壁本体的热阻,增强其冷却能力,降低冷却壁热面温度,减小冷却壁内部的温差和热应力,使冷却壁热面易形成渣铁壳。
第5期 程树森等:高炉炉身下部及炉缸、炉底冷却系统的传热学计算 10月(a )D =70mm ,l =254mm ,s =160mm ;(b )D =80mm ,l =200mm ,s =140mm图1 冷却壁结构参数不同时冷却壁内等温线的分布Fig 11 T emperature distribution of stave11212 铜冷却板结构对温度场的影响 冷却器中使用铜冷却板时,冷却板的垂直间距对温度场有显著影响。
图2示出采用六通道铜冷却板且炉衬为半石墨碳砖时,炉衬热面最高温度、冷却板最高温度和炉壳最高温度随冷却板垂直间距的变化。
可见:①冷却板最高温度受垂直间距的影响不大,维持在80~90℃之间;②炉衬热面最高温度随着冷却板垂直间距的增大而升高。
当冷却板的垂直间距为0145m 时,其最高温度未超过800℃,离图2 冷却板垂直间距对温度分布的影响Fig 12 Influence of vertical distance betw een coolingplates on temperature distribution870℃等温线相差甚远,足以保证在炉衬热面凝结一层渣铁壳;③随着冷却板垂直间距的增大,炉壳最高温度有所提高,但提高的幅度很小。
图3给出冷却板导热系数及炉衬导热系数对温度分布的影响。
从图3(a )可见,当冷却板的导热系数从400W/(m ・℃)降低到50W/(m ・℃)时,冷却板的最高温度从150℃升高到350℃,升温较快(此时冷却板垂直间距为700mm );炉衬热面最高温度基本维持在700~710℃;炉壳最高温度基本不变。
当炉身下部采用冷却板或冷却器时,在选择碳质炉衬时,应把炉衬的870℃等温线推向炉内,以减小炉衬的侵蚀和破坏,从而获得良好的操作炉型。
若炉衬热面温度超过1150~1200℃,则难以形成渣铁壳,炉衬将承受炉内铁水直接的化学侵蚀和热侵蚀。
温度超过870℃时还有可能出现因碱金属及碳沉积而形成的脆化。
从图3(b )可以看出,随着炉衬导热系数的降低[从100W/(m ・℃)降到20W/(m ・℃)],炉衬热面最高温度从550℃升高到900℃。
特别是炉衬的导热系数小于30W/(m ・℃)时,炉衬的热面最高温度将超过870℃。
11213 渣铁壳厚度对钻孔铜冷却壁温度场的影响 图4示出渣铁壳厚度对铜冷却壁热面温度和热图3 冷却板导热系数(a)及炉衬导热系数(b)对温度分布的影响Fig 13 Influence of conductivity of cooling plates (a)andbrick lining (b)on temperature distribution2004年 钢 铁 研 究 学 报 第16卷图4 渣铁壳厚度对温度分布的影响Fig 14 Influence of accretion thickness on temperaturedistribution流通量的影响。