轴承零件硝盐淬火性能分析
热处理中的轴承热处理技术

热处理中的轴承热处理技术轴承是机械工业中不可或缺的部分,它的质量直接影响到机器的性能和使用寿命。
轴承的热处理技术是制造高品质轴承的重要一环。
本文将讨论热处理中的轴承热处理技术。
1. 热处理的定义和目的热处理是指将金属制品加热到一定温度,保持一定时间,然后冷却至室温的工艺。
热处理的目的是改变金属材料的组织结构、性质和形状,以获得满足设计要求的性能指标。
在轴承的热处理中,应用最为广泛的是淬火、回火、正火和表面强化等方法。
而这些方法选择的依据则是轴承所要求的性能和工作条件。
2. 淬火技术淬火是一种将金属加热至高温,然后在水或油中迅速冷却的热处理方法。
淬火的目的是将钢的组织变为马氏体,增加硬度和强度。
在轴承的热处理中,淬火主要应用于内、外圈和滚子等零件的加工。
淬火后的零件硬度高、耐磨性好、抗疲劳性能强。
但另一方面,淬火的缺点是易产生裂纹和变形,从而影响轴承的使用效果。
因此,在轴承淬火的过程中,需经过多次淬火和回火操作,以减少材料的内部应力和变形,从而保证轴承的品质。
3. 回火技术回火是指在淬火后,将零件再次加热到中低温度,并保温一定时间,然后迅速冷却的热处理方法。
回火的目的是消除淬火后产生的内应力和提高零件的韧度和韧性。
在轴承的热处理中,回火主要应用于内、外圈及滚子等零件,以消除淬火过程中产生的内应力和提高零件的韧性。
回火的加热温度和保温时间的选择应根据不同材料的工作条件和性能要求来决定。
4. 正火技术正火是指将零件加热至一定温度,然后进行持续保温,最后冷却的热处理方法。
正火的目的是使零件的组织达到均匀化,提高零件的强度和韧性。
在轴承的热处理中,正火通常应用于轴承外壳零件的加工。
正火的加热温度和保温时间的选择应根据材料的性能进行确定,以达到设计要求。
5. 表面强化技术表面强化是指在材料表面形成一层用于提高材料表面耐磨性和抗疲劳性的物理、化学、热力学或机械层。
表面强化一般分为热处理、渗碳、硝化、电火花加工和喷涂等。
一种轴承零件淬火用硝盐含水量控制方法[发明专利]
![一种轴承零件淬火用硝盐含水量控制方法[发明专利]](https://img.taocdn.com/s3/m/a3b0fdfb59eef8c75ebfb3be.png)
专利名称:一种轴承零件淬火用硝盐含水量控制方法专利类型:发明专利
发明人:陈云,张春宝,曹海军,汪凤文,张宁
申请号:CN201911070737.X
申请日:20191105
公开号:CN110760649A
公开日:
20200207
专利内容由知识产权出版社提供
摘要:本发明的一种轴承零件淬火用硝盐含水量控制方法,涉及轴承生产加工领域,包括如下步骤:S1、通过试验测量淬火硝盐槽内水的消耗速度,所述消耗速度记为D;S2、根据所述消耗速度乘以一个工步周期的时长计算得到每个工步周期内向所述淬火硝盐槽补水的补水量,所述一个工步周期的时长记为△T,所述补水量记为M1,M1=D*△T;S3、实际淬火加工中,每个工步周期内按所述补水量向所述淬火硝盐槽内加水,并搅拌所述淬火硝盐槽内的硝盐和水使它们均匀混合。
本发明能够减少轴承零件淬火过程中硝盐含水量的波动,提高轴承零件的淬火质量。
申请人:浙江辛子精工机械有限公司,浙江为尚机械有限公司
地址:313000 浙江省湖州市湖州经济技术开发区方家山路298号
国籍:CN
代理机构:浙江千克知识产权代理有限公司
代理人:裴金华
更多信息请下载全文后查看。
轴承零件硝盐淬火性能分析

为检 验样 本 。均 采 用 辊底 式 淬 回火 生 产 线 , 内 炉
用于贝氏体等温淬火及轧机轴承等厚壁轴承 的热 处理 _ 。2 纪 9 1 0世 J 0年 代 末 , 典 S F 德 国 F G 瑞 K、 A 在轴承零件热处理 中开始批量使用硝盐替代淬火 油 J 0 6年 国内轴 承生 产厂 家开 始用 硝盐 替 代 。2 0 淬火油做为冷却介质应用并逐 步推广 , 浴淬火 盐 在轴承行业有迅速普及 的趋势 。
! Q 二Z 墨
轴承
2 1 年 1期 01 1
CN41 — 1 48/ 1 TH Be rn 011, aig2 No. 11
轴 承零件硝 盐淬火性能分析
关力 , 陈卉珍
( 洛阳 L C轴承有 限公司, 南 洛 阳 4 13 ) Y 河 7 09
摘要: 分别从硬度梯度 、 变形控制 、 冷却性能调节 、 碎载荷等方面对硝盐淬火后的零件性 能与油基淬火后 的零 压 件性 能进行试验对 比分析 。结果表 明 : 与油基淬火相 比 , 盐熔液 化学性 质稳定 , 硝 淬火 冷却能 力强 , 畸变小 ; 淬
着一定的局限性 , 由于冷却性能的局 限, 壁厚较大 的零件 出现表 面软 点 、 部 硬 度偏 低 、 硬 层 较 浅 心 淬 等问题 ; 对于薄壁零件 又存在变形大影 响后序加 工等缺陷。同时 , 淬火 油在长期 的使用 过程 中还 存在老化变质 、 冷却性能 不够稳定等现象 。熔化 的硝盐 (0 5 %硝 酸钾 +5 %亚 硝 酸钠 ) 为淬 火 介 0 作
铬轴承钢轴承零件退火、淬回火组织评级

铬轴承钢轴承零件退火、淬回火组织评级说明(JB1255-1991、JB1255-2001评级依据)1.关于退火组织的评级依据和说明,在JB1255-1991的起草宣贯材料之二中,对第一级别图-退火组织,有详细的评级说明、评级原则和组织特征,具体内容如下:1.1评级图说明:该评级图采用JB1255-2001标准中第一级别图评定。
视场直径:78mm,放大倍率:500倍。
腐蚀剂:2%硝酸酒精溶液。
1.2评级原则:理想的退火组织是铁素体基体上均匀分布着细小的球状或粒状碳化物。
①碳化物的颗粒大小;②碳化物的分布均匀性;③碳化物的形态(球化程度)。
说明:1)细小的粒状或点状珠光体有利于淬火后获得含量均匀分布的马氏体。
单碳化物过细往往伴随着高的硬度,不利于随后的切削加工,且淬火加热工艺要求严格;碳化物颗粒过粗,硬度过低,同样不利于切削加工,且由于碳化物间距增大,使随后的淬火组织碳浓度分布不均匀,影响使用性能。
2)碳化物分布的均匀性直接影响淬火后能否得到均匀的马氏体,碳化物分布过度不均,除退火硬度不均匀而影响切削性能外,还影响淬火后马氏体的含量及尺寸不均,甚至产生局部过热组织。
1.3组织特征:1级:细点状+细粒状珠光体+局部细片状珠光体组织特征:碳化物颗粒细小呈点状和细粒状,分布弥散,局部有细片状,为不合格组织。
形成原因是加热不足,部分锻造组织被保留下来。
2级:点状珠光体+细粒状珠光体组织特征:碳化物颗粒细小呈点状和细点状,圆度好,分布较均匀,为优良的合格组织。
3级:球状珠光体组织组织特征:碳化物颗粒大于2级,球化完全,分布较均匀,为良好的合格组织4级:球状珠光体组织组织特征:碳化物颗粒较粗,均匀性较差,碳化物分布不均,有的区域密集,有的区域稀少,为合格组织。
上述2、3、4级退火组织均属正常工艺形成。
GCr15,ZGCr15钢的硬度应在HB179~207范围内,GCrSiMn,ZGCr15SiMn钢硬度应在HB179~217范围内。
我国轴承零件热处理现状及对策

我国轴承零件热处理现状及对策随着主机的高速化、轻量化,轴承的工作条件更加苛刻,对轴承的性能要求越来越高,如更小的体积、更轻的质量、更大的承载容量、更高的寿命和可靠性等。
其中,国产轴承的寿命和可靠性成为近年来越来越突出的问题,开发热处理新技术、提高热处理质量一直是国内外轴承生产企业及相关企事业单位关注的课题。
本文对近年来来年热处理技术的进展进行综述,以期对我国的轴承行业相关人员有所借鉴。
1. 高碳铬轴承钢的退火高碳铬轴承钢的理想退火组织是铁素体基体上分布着细、小、匀、圆的碳化物颗粒的组织,为以后的冷加工及最终的淬回火作组织准备。
目前,除少数企业使用周期式设备外,普遍使用的是无保护气氛的单通道推杆式等温退火炉。
退火的组织和硬度控制已比较成熟可靠,可较容易地把退火组织控制在JB1255标准中的2~3级或细点组织。
存在的问题是能耗偏高、退火后氧化脱碳严重。
近年来,从节能的角度出发,开发了油电复合加热等温退火炉、双室首尾并置(水平或上下)的等温退火炉,节能效果显著,应大力推广;同时,随着毛坯精密成形工艺和设备的出现,开始采用氮基保护气氛等温退火炉,以减少退火过程中的氧化脱碳,降低原材料的消耗和机加工成本。
2. 高碳铬轴承钢的马氏体淬回火常规的高碳铬轴承钢马氏体淬回火工艺的发展主要分3个方面:一是开展淬回火工艺参数对组织和性能影响的基础性研究,如淬回火过程中的组织转变、残余奥氏体的分解、淬回火后的韧性与疲劳性能等;二是淬回火的工艺性能的研究,如淬火条件对尺寸和变形的影响、尺寸稳定性等;三是取缔氧化或保护气氛加热,推广可控气氛加热。
2.1 组织与性能常规马氏体淬火后的组织为马氏体、残余奥氏体和未溶(残留)碳化物组成。
轴承钢淬火后马氏体基体含碳量为0.55%左右,组织形态一般为板条和片状马氏体的混合组织,或称介于二者之间的中间形态—枣核状马氏体,轴承行业上所谓的隐晶马氏体、结晶马氏体;其亚结构主要为位错缠结以及少量的孪晶。
轴承圈淬火脱碳和变形分析

造成零件报废 的 原 因 有 两 种 情 况:一 是 脱 碳,二 是 变 形 超差。脱碳产生的原因有:第一,由于煤油作为保护气氛,在 B"$F下裂解的效果很差,产生的活性碳原子很少,而且易生 成大量的碳黑,所 以 造 成 零 件 的 脱 碳。第 二,采 用 箱 式 炉 加 热,零件每 次 出 炉 时 都 要 打 开 炉 门,用 钩 子 将 零 件 挑 出 来。 每炉零件在操作过程中要开启五次炉门,而炉门口没有火帘 装置,很容易使炉内形成负压,从而使空气进入炉内造成零 件的脱碳。第三,采用的淬火介质是上海!"油,该淬火介质 使用时间长,冷却能力也降低,致使工件局部冷却速度低于 临界淬火速度而产生屈氏体转变,有可能造成部分轴承套圈 淬火后局 部 硬 度 不 合 格。第 四,零 件 出 炉 采 用 的 是 手 工 操
图" 轴承圈挂装示意图
$ 问题的解决
根据零件的脱碳分析和生产厂的实际情况,选用小贝力 克保护气氛箱式炉,保护气氛采用吸热式保护气氛,即丙烷 加空气混合裂解产生活性碳原子。炉体为双炉门结构,分前 后两室,可保证 炉 膛 的 密 封 性 很 好,维 持 正 压。零 件 的 装 炉 和出炉由电机带动链条自动完成,这样不仅很好地解决了零 件的脱碳问题,而且降低了工人的劳动强度。
西安航空技术高等专科学校学报 JOURNAL OF XI'AN AEROTECHNICAL COLLEGE 2006,24(1)
参考文献(2条) 1.王广生 金属热处理缺陷分析及案例 2002 2.李泉华 热处理实用技术 2002
本文链接:/Periodical_xahkjsgdzkxxxb200601006.aspx
硝盐淬火(下)

( )心部硬度对 比 心部硬度油淬火 比盐淬火高约 3
1 HR ( ~2 C 见表 5 。 )
2 1 0l 年第 3期
热 处 锻 铸 造
WW W . et l or i 9 co m aw k ng7 50 m
奄 如  ̄n :r j t -
一
…
L_ 丝处 . 里圈
现 无 排 放 清洗 是 可 能 的。
是检测冷却速度 ,使用镍合金 探头 ,将 探头加热
—
到 5 &C左右,然后放 人硝 盐 中,检 测冷却 到 4 0C的 5 0 ̄ 时间 ,如小于规定时间 ,则 自动补充 水 ,这 种检测方法
的优 点是 检测速 度 快 ,能 自动控 制 ,问题 是 使用 频次
槽补充 ,低浓度槽补充 自来水 的方法 补水 ,一般工件淬 火后 带 出 的 盐 量 为 5 0~10/ 0 gm ,根 据 试 验 ,单 重
3 0 5
层深 / mm
图 1 齿轮渗碳后分别经硝盐和油淬火后 硬度梯度对 比 1
15 g左右 的齿轮硝 盐淬火 时,平 均每吨工件 带 出量 约 .k
^
盐 齿面 2
起 ,造成传动困难 ,可通过加水溶解解决 凝固 ,但 不能 影响工件 。 为减少排放 ,按将清洗机高浓度 的盐水 泵人淬火槽
蚕5 6 0 壶5 5 0
4 0 5
一 督, 誊
弋 1
{
■
、 △
补充淬火蒸发和 自然蒸发 ,将低浓度水槽 的水 向高浓度
对齿轮渗碳盐淬和油淬后的公法线内花键内花键和齿顶圆的尺寸进行检测硝盐淬火的公法线变化略大于油淬内花键的变化量和变化范围硝盐淬火均优于油淬火齿顶圆的变化量和变化范围硝盐淬火均优于油淬火且硝盐淬火的变化趋势为收缩变化油淬火为膨胀变化见表
硝盐淬火(上)

5 5 ℃ 油 0
7 .6 H 0 —4 2 % ,
50C冷 却速 度 0 ̄
/℃ ・s
30 冷却 速 度 0℃
3
最 高冷 却 速 度
/ ・ 。 银探头 ) ℃ s 。(
1O 5
3l O
1O l
4 最 高 冷速 温 度 段/ ℃
5
70 5
4 0
7 0~60 5 0
10 5
70 0
9 0
4 % H 0通压缩 空气 — ,
6 3 9 % H 0通压 缩空 气 — .3 ,
工 件 带 出 率/ /。 g・3 " 1
5 O~lo o
固态 B=1 5 E一 K .9 3
来 回收盐等措施 ,克服了硝盐淬火介质 的缺点 ,重新 发
挥 了硝盐淬火介质的优点。
一
熔 盐 口=1 1 E一 K .2 2
二、冷 却特性
1 .添加水对硝盐的冷却特性曲线的影响
无水硝 盐 ( 5 N ,+ 5 N N 5 %K O 4 % a O )的 冷却 特性 曲线如 图 2中的 曲线 3所示 。在 10 2 7  ̄ 使用 时,无水硝
以上 有
蒸汽膜阶段
冷却 速 度 / ・  ̄ S C
2 最 高 冷速 起 始 温度 /
70 5 70 5 70 0
图 2 &0 m银球冷却速度的变化与水含量 ( 2m 质量分数)的
关系 ( 浴温 10 7 ̄ C)
l J6 % H2 — . 8 O 2 9 % H2 3 _ % H2 3 0 _0 O
当,30C以下硝 盐 由于 温 差减 小 ,冷 速 将 明 显 降低 ; 0 ̄
硝 盐 的物 理 性 能 见 表 1 。
如何提高硝盐浴的淬火冷却能力?(转)
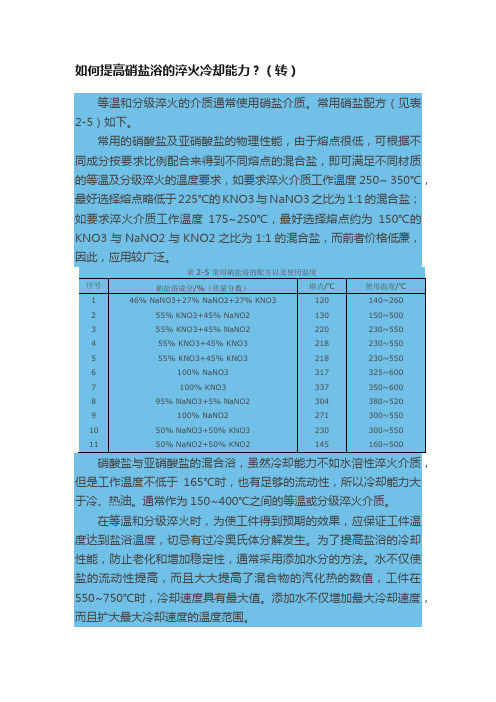
如何提高硝盐浴的淬火冷却能力?(转)熔盐浴温度不同,水的含量也不同,当熔盐浴的温度超过250℃时,含水量<1%。
在55%KNO3+45%NaNO2熔盐浴中加入水,将显著提高冷却性能,无水熔盐浴的温度对散热系数影响甚小;而有水熔盐浴,当浴温超过300℃时,散热系数却明显下降。
对于熔盐为145℃的50%KNO3+50%NaNO2硝盐浴,在250℃和300℃时分别添加1%和0.5%的水,从而可以使淬透性差的碳素工具钢和碳素钢有效地冷却。
减少熔盐浴的含水量,将显著地影响冷却性能,随时间的延长,逐渐接近无添加水的冷却性能,因此必须使含量保持相对稳定。
静止时熔盐浴水分的小事比搅拌时快,故生产中用搅拌器进行连续搅拌,或采用专用设备使水的损耗量不断地给以补充。
在连续淬火等温时,必须采用这些方法维持淬火硝盐浴中的水分,等温的硝盐槽与淬火硝盐槽分离。
添加0.12%水,与未加入者相比,冷却能力可提高1倍。
每班工作后要捞渣,硝盐老化渣多,捞渣就是把不熔物除掉。
捞渣是保持硝盐浴冷却能力的一个有效手段。
捞渣方法:其方法一般是“先高后低”,即把硝盐浴温度升至比正常工作温度高30~50℃以上,然后温度自然下降,比正常工作温度稍低,此时可进行捞渣操作。
若渣多且块大,表明老化严重,视情况确定是否更新。
生产中,在淬火工件前进行一次捞渣工作,对保证硝盐浴冷却能力起到一定作用。
根据实际生产量来确定硝盐浴的过滤周期,过滤使用120目的铜丝网,将沉淀在槽底的高熔点盐渣以及氧化物过滤掉,并按比例同时每周进行一次化验,根据化验结果,调整熔盐浴成分,这样熔盐浴可长期使用,使工件的淬火质量稳定。
熔盐浴在使用过程中,浴温应严格控制,不宜波动过打。
当生产批量大时,会使熔盐浴温度升高,因此,浴槽要设有冷却装置。
由于熔融的硝酸盐容易着火和飞溅伤人,因此在操作过程中,应备防护用具,注意安全。
在停止使用时要注意密封,以防氧化。
浴槽在重新加热时,特别是在浴槽底部加热的炉子应缓慢进行,否则会因浴槽底部迅速熔化,体积激烈膨胀,顶部不熔而爆炸。
轴承套圈盐浴淬火

轴承套圈盐浴淬火引言:轴承套圈是一种常见的机械零件,广泛应用于各种机械设备中。
为了提高轴承套圈的硬度和耐磨性,常采用盐浴淬火工艺。
本文将对轴承套圈盐浴淬火进行介绍,包括其原理、工艺流程以及优点。
一、原理:盐浴淬火是一种通过将工件浸入熔盐中进行淬火的热处理方法。
在盐浴中,由于盐的导热性能较好,能够迅速吸热并传递给工件,从而使工件迅速冷却。
盐浴淬火不仅能够提高工件的硬度,还能够改善其组织结构,提高工件的耐磨性和使用寿命。
二、工艺流程:1. 准备工作:首先需要准备好盐浴淬火设备,包括加热炉、盐浴槽和升降装置等。
同时,还需要准备好合适的盐浴液和工件。
2. 加热:将盐浴液加热至适当的温度,通常在300℃到400℃之间。
加热过程中需要控制好温度,确保盐浴液达到预定的淬火温度。
3. 清洗:将待淬火的轴承套圈进行清洗,去除表面的油污和杂质,以保证淬火效果。
4. 浸入盐浴:将清洗后的轴承套圈缓慢地浸入预热好的盐浴液中,确保工件完全浸没在盐浴中,并且要注意不要产生剧烈的气泡。
5. 淬火保持时间:根据不同的工件材料和要求,设定合适的淬火保持时间,使工件充分吸收热量并达到所需的硬度。
6. 从盐浴中取出:淬火时间结束后,将轴承套圈从盐浴中取出,同时要注意避免盐浴液残留在工件表面。
7. 冷却:将取出的轴承套圈进行冷却处理,通常采用自然冷却或水冷却的方式。
8. 清洗与处理:淬火后的轴承套圈还需要进行清洗和处理,以去除盐浴残留和表面的氧化物,保证工件质量。
三、优点:1. 高硬度:盐浴淬火能够使轴承套圈获得较高的硬度,提高其抗磨性和使用寿命。
2. 均匀淬火:盐浴液具有良好的导热性能,可以使工件均匀受热,并且能够迅速吸热,保证工件在短时间内达到所需的淬火温度。
3. 组织结构改善:盐浴淬火可以改善轴承套圈的组织结构,细化晶粒,提高其耐磨性和强度。
4. 生产效率高:盐浴淬火工艺简单,操作方便,能够快速完成淬火过程,提高生产效率。
结论:轴承套圈盐浴淬火是一种常用的热处理方法,能够提高轴承套圈的硬度和耐磨性。
轴承钢淬火工艺

轴承钢淬火工艺轴承钢淬火是一种重要的热处理工艺,通过对轴承钢进行淬火处理,可以显著提高其硬度和耐磨性,从而增强轴承的使用寿命和性能。
在实际生产中,轴承钢淬火工艺的控制和优化对于确保轴承质量和性能至关重要。
本文将就轴承钢淬火工艺的原理、工艺参数控制和优化等方面进行探讨。
一、轴承钢淬火工艺原理轴承钢淬火是通过将轴承钢加热至适当温度后迅速冷却的热处理过程。
在加热阶段,轴承钢的晶粒逐渐长大,晶界变得清晰,同时也会出现一些溶解的碳化物。
在快速冷却的过程中,晶粒会被锁定,并形成新的组织结构,从而提高轴承钢的硬度和强度。
此外,淬火还可以使碳化物重新析出,进一步提高硬度和耐磨性。
二、轴承钢淬火工艺参数控制在进行轴承钢淬火时,需要控制多个工艺参数,包括加热温度、保温时间、淬火介质和冷却速度等。
首先是加热温度,加热温度的选择应根据轴承钢的成分和组织结构来确定,一般应控制在临界温度以上50~100℃。
保温时间一般取决于轴承钢的尺寸和要求的淬火效果,通常为15~30分钟。
淬火介质通常采用水、油或气体,不同的介质会对淬火效果产生影响。
冷却速度的选择也很重要,过快的冷却速度可能导致内部应力过大,从而影响轴承钢的性能。
三、轴承钢淬火工艺优化为了获得更好的淬火效果,可以对轴承钢淬火工艺进行优化。
首先是选择合适的淬火介质,不同的介质对淬火效果有显著影响。
其次是控制冷却速度,可以通过调整冷却速度来控制淬火组织的形成,进而影响轴承钢的硬度和强度。
此外,还可以通过改变加热温度和保温时间来优化淬火工艺,以获得更好的淬火效果。
总的来说,轴承钢淬火工艺是一项重要的热处理工艺,对于提高轴承钢的硬度和耐磨性至关重要。
在实际生产中,合理控制和优化轴承钢淬火工艺可以有效提高轴承的使用寿命和性能。
希望本文对轴承钢淬火工艺有所帮助,谢谢阅读。
淬火方式对薄壁轴承套圈变形的影响
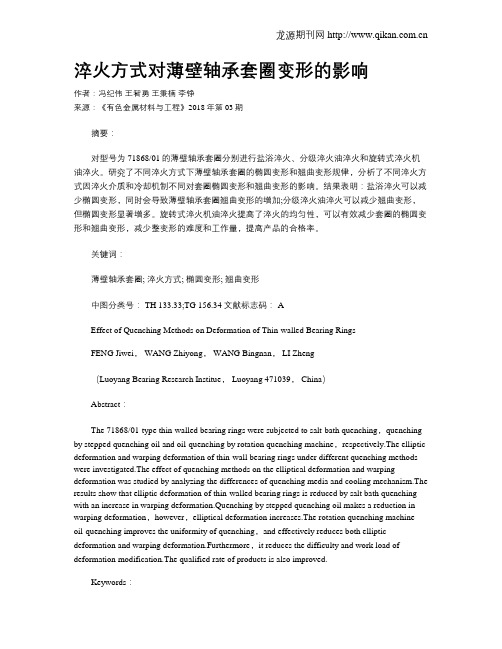
淬火方式对薄壁轴承套圈变形的影响作者:冯纪伟王智勇王秉楠李铮来源:《有色金属材料与工程》2018年第03期摘要:对型号为71868/01的薄壁轴承套圈分别进行盐浴淬火、分级淬火油淬火和旋转式淬火机油淬火。
研究了不同淬火方式下薄壁轴承套圈的椭圆变形和翘曲变形规律,分析了不同淬火方式因淬火介质和冷却机制不同对套圈椭圆变形和翘曲变形的影响。
结果表明:盐浴淬火可以减少椭圆变形,同时会导致薄壁轴承套圈翘曲变形的增加;分级淬火油淬火可以减少翘曲变形,但椭圆变形显著增多。
旋转式淬火机油淬火提高了淬火的均匀性,可以有效减少套圈的椭圆变形和翘曲变形,减少整变形的难度和工作量,提高产品的合格率。
关键词:薄壁轴承套圈; 淬火方式; 椭圆变形; 翘曲变形中图分类号: TH 133.33;TG 156.34 文献标志码: AEffect of Quenching Methods on Deformation of Thin-walled Bearing RingsFENG Jiwei, WANG Zhiyong, WANG Bingnan, LI Zheng(Luoyang Bearing Research Institue, Luoyang 471039, China)Abstract:The 71868/01-type thin-walled bearing rings were subjected to salt-bath quenching,quenching by stepped quenching oil and oil-quenching by rotation quenching machine,respectively.The elliptic deformation and warping deformation of thin-wall bearing rings under different quenching methods were investigated.The effect of quenching methods on the elliptical deformation and warping deformation was studied by analyzing the differences of quenching media and cooling mechanism.The results show that elliptic deformation of thin-walled bearing rings is reduced by salt bath quenching with an increase in warping deformation.Quenching by stepped quenching oil makes a reduction in warping deformation,however,elliptical deformation increases.The rotation quenching machineoil-quenching improves the uniformity of quenching,and effectively reduces both elliptic deformation and warping deformation.Furthermore,it reduces the difficulty and work load of deformation modification.The qualified rate of products is also improved.Keywords:thin-walled bearing rings; quenching method; elliptical deformation; warping deformation随着科学技术的发展,轴承的工作环境越来越复杂,对轴承的性能提出了更高的要求。
轴承钢的热处理

轴承钢的热处理
轴承钢是用于制造轴承零件的一种特殊钢材,具有高强度、高硬度和良好的耐磨性能。
对于工艺,是非常重要的工艺环节,直接影响到轴承零件的性能和使用寿命。
轴承钢的热处理主要包括回火、淬火、正火等工艺。
在制造轴承零件时,必须根据不同的要求和工件的结构,选择适当的热处理工艺。
下面介绍一下轴承钢的热处理工艺及其影响。
回火是热处理工艺的一种,主要是通过加热和保温,使材料内部的应力得以释放,晶粒尺寸适当调整,提高材料的韧性和耐磨性。
回火工艺中,需要根据具体情况选择适当的回火温度和时间,以及冷却方式,以保证材料的性能。
淬火是轴承钢热处理工艺中的一种重要工艺,通过将材料加热至适当的温度后急冷,使其快速冷却,使组织变质,提高硬度和强度。
淬火工艺对材料性能的影响很大,需要根据具体要求选择适当的淬火温度和时间,以及冷却介质。
正火是轴承钢热处理中的另一种重要工艺,通过加热材料至适当的温度后保温,使组织发生调整,提高材料的韧性和强度。
正火工艺也需根据要求选择适当的温度和时间,以及冷却方式。
除了以上几种热处理工艺外,还有一些特殊的热处理方法,如表面强化热处理、渗碳热处理等,这些方法可以进一步提高轴承钢的性能,延长使用寿命。
总的来说,轴承钢的热处理对于提高材料的性能和使用寿命至关重要。
在制造轴承零件时,必须根据具体要求和工件的结构选择适当的热处理工艺,确保材料具有理想的性能,满足使用要求。
同时,在热处理过程中,需要严格控制各项参数,确保热处理效果达到最佳。
只有这样,才能保证轴承钢的质量和可靠性,真正发挥轴承零件的作用。
大模数重载人字齿轮轴硝盐淬火工艺研究
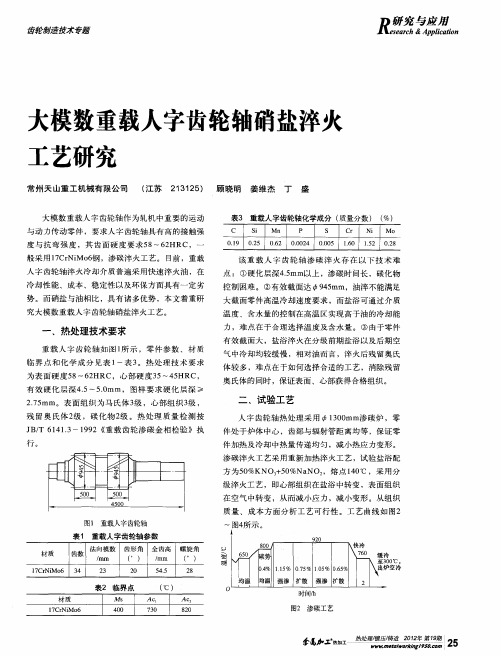
M0
O2 .8
般 采 用 1C N Mo 钢 ,渗 碳 淬 火 工艺 。 目前 ,重 载 7 ri 6 人 字 齿轮 轴 淬 火 冷 却 介 质普 遍 采 用 快 速淬 火 油 ,在
该 重 载 人 字 齿 轮 轴 渗 碳 淬 火 存 在 以 下 技 术 难 点 :①硬 化 层 深 4 mm以上 ,渗 碳 时 间长 ,碳 化 物 . 5
时 间/ n mi
赠
O
速 度 ,导 致 冷 却 时析 出条状 铁 素 体 。② 含水 量05 .% 的 10 9 ℃硝盐 淬 火冷 却介 质的 高温 区冷 却能 力不 足 。 硝 盐含 水 量 对于 盐 浴 的冷 却 性 能十 分 关 键 ,未 加 水 的 盐浴 其 冷 却性 能 较 差 ,通 过 向 硝盐 中加水 可 以 大 幅 提 高其 高 温冷 却 性 能 。随 着 硝盐 浴 温 度 度提 高 ,
力 ,难 点 在 于 合 理选 择 温 度 及 含水 量 。 ③ 由于零 件 有 效 截 面 大 ,盐 浴 淬 火 在 分 级 前期 盐 浴 以 及后 期 空
、
热处理技术要求
重 载 人 字 齿 轮 轴 如 图 1 示 ,零 件 参 数 、 材 质 所
气中冷却均较缓慢 ,相对油而 言 ,淬火后残留奥 氏
1 Cr M 06 7 Ni
( ) ℃
Ac 1
70 3
Ms
40 0
Ac 3
80 2
图2 渗碳工艺
参 … 謦 磊
蓦
2 G
s 直甩
& Ap iain pl to c
齿轮翩造技术专题
p
由于合金元素贫乏 ,导致淬透性下降 ,淬火冷却时
由于 冷 却 能 力达 不 到偏 析 区 马 氏体 形 成 的临 界 冷 却
轴承零件热处理的常见缺陷

成表面脱碳。
表面脱碳层的深度超过最后加工的留量就会使零件报废。
表面脱碳层深度的测定在金相检验中可用金相法和显微硬度法。
以表面层显微硬度分布曲线测量法为准,可做仲裁判据。
6.软点由于加热不足,冷却不良,淬火操作不当等原因造成的轴承零件表面局部硬度不够的现象称为淬火软点。
它象表面脱碳一样可以造成表面耐磨性和疲劳强度的严重下降。
若本文对您有所帮助,同时为了让更多人能看到此文章,请多宣传一下本站,支持本站发展;多谢!目录一、滚动轴承材料 (1)1.1滚动轴承用钢的基本性能要求 (1)1.2 轴承用钢冶金质量的基本要求 (3)1.3 滚动轴承常用材料 (4)1.4 轴承用钢的发展 (12)二、轴承热处理 (15)2.1 轴承热处理新技术 (15)2.2 产品设计时应考虑的几个问题 (16)PDF created with pdfFactory Pro trial version 1一、滚动轴承材料1.1滚动轴承用钢的基本性能要求滚动轴承零件在实际使用过程中,往往要在拉伸、压缩、弯曲、剪切、交变等复杂应力状态和高应力值条件下,高速长时间工作。
选择制造滚动轴承的材料是否合适,对其使用性能和寿命将有很大影响。
而选择材料的基本方法是根据轴承的破坏(失效)形式来决定的。
一般情况下,滚动轴承的主要破坏形式是在交变应力作用下的疲劳剥落,以及由于摩擦磨损而使轴承的精度丧失,此外,还有裂纹、压坑、锈蚀等原因造成轴承的非正常破坏。
因此,总体而言,滚动轴承应具有高的抗塑性变形能力,少的摩擦磨损,良好的旋转精度,高的尺寸精度,良好的尺寸稳定性,以及长的接触疲劳寿命。
而且其中很多性能是由材料和热处理工艺所共同决定的。
因而要求制造滚动轴承的材料经过后工序的一定热处理后具备以下的性能。
1.1.1高的接触疲劳性能滚动轴承运转时,滚动体在轴承内、外圈的滚道间滚动时,其接触部分承受周期性交变负荷,多者每分钟达数万次或数十万次。
在周期性交变应力的反复作用下,接触表面出现疲劳剥落。
轴承套圈盐浴淬火

轴承套圈盐浴淬火一、引言轴承是机械设备中重要的零部件之一,其质量直接影响到整个机械设备的性能和寿命。
而轴承套圈是轴承组件中的关键部分,需要经过一系列的加工和处理工艺来提升其硬度和耐磨性。
其中,盐浴淬火作为一种常用的热处理工艺,被广泛应用于轴承套圈的制造过程中。
本文将详细介绍轴承套圈盐浴淬火的原理、工艺过程以及优点。
二、盐浴淬火原理盐浴淬火是通过将轴承套圈放置在高温盐浴中加热,使其达到适当的温度后迅速冷却,以改变材料的组织结构和性能。
具体来说,盐浴淬火的原理可以归结为以下几个方面:1. 盐浴的导热性能好:盐浴是一种优质的导热介质,可以快速将热量传递给轴承套圈表面,使其均匀受热。
2. 盐浴的冷却效果好:盐浴具有较高的冷却速度,可以迅速将轴承套圈表面的热量带走,使其迅速冷却。
3. 盐浴的化学成分可调:通过控制盐浴的化学成分和温度,可以实现对轴承套圈的组织结构和性能的调控,以满足不同要求。
三、盐浴淬火工艺过程盐浴淬火的工艺过程可以分为预处理、加热、保温、冷却和清洗等环节。
1. 预处理:在进行盐浴淬火前,需要对轴承套圈进行表面清洁和除锈处理,以确保盐浴淬火的效果。
2. 加热:将清洁后的轴承套圈放置在盐浴中进行加热,通常采用电阻加热或燃气加热方式。
加热温度根据不同材料和要求而定,一般在500-900摄氏度之间。
3. 保温:在加热到适当温度后,需要将轴承套圈保持在该温度下一段时间,以保证其达到均匀加热和组织结构的转变。
4. 冷却:将保温后的轴承套圈迅速浸入冷却介质中,通常采用盐水或水作为冷却介质。
冷却过程需要控制冷却速度,以确保轴承套圈获得所需的硬度和性能。
5. 清洗:冷却后的轴承套圈需要进行清洗,以去除附着在表面的盐渍和杂质,以免影响轴承的使用寿命。
四、盐浴淬火的优点盐浴淬火作为一种热处理工艺,在轴承套圈制造中具有以下几个优点:1. 高硬度:盐浴淬火可以使轴承套圈表面获得较高的硬度,提高其抗磨性和耐用性。
2. 均匀性好:盐浴淬火能够实现对轴承套圈的均匀加热和冷却,避免了不均匀变形和应力集中等问题。
滚动轴承零件常见的淬火裂纹分析与预防
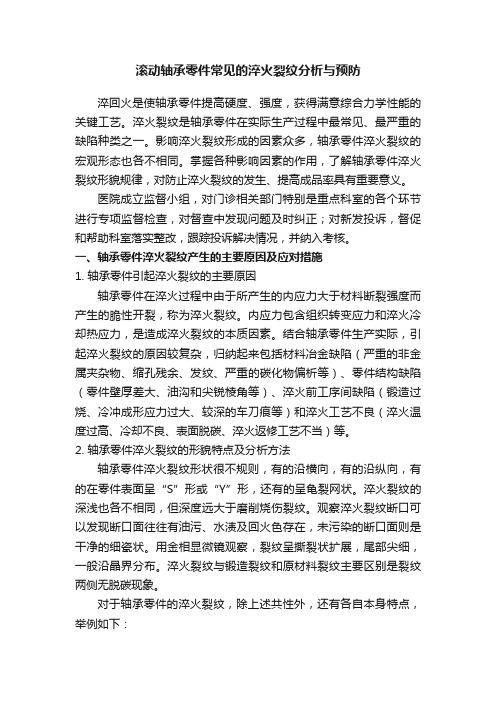
滚动轴承零件常见的淬火裂纹分析与预防淬回火是使轴承零件提高硬度、强度,获得满意综合力学性能的关键工艺。
淬火裂纹是轴承零件在实际生产过程中最常见、最严重的缺陷种类之一。
影响淬火裂纹形成的因素众多,轴承零件淬火裂纹的宏观形态也各不相同。
掌握各种影响因素的作用,了解轴承零件淬火裂纹形貌规律,对防止淬火裂纹的发生、提高成品率具有重要意义。
医院成立监督小组,对门诊相关部门特别是重点科室的各个环节进行专项监督检查,对督查中发现问题及时纠正;对新发投诉,督促和帮助科室落实整改,跟踪投诉解决情况,并纳入考核。
一、轴承零件淬火裂纹产生的主要原因及应对措施1. 轴承零件引起淬火裂纹的主要原因轴承零件在淬火过程中由于所产生的内应力大于材料断裂强度而产生的脆性开裂,称为淬火裂纹。
内应力包含组织转变应力和淬火冷却热应力,是造成淬火裂纹的本质因素。
结合轴承零件生产实际,引起淬火裂纹的原因较复杂,归纳起来包括材料冶金缺陷(严重的非金属夹杂物、缩孔残余、发纹、严重的碳化物偏析等)、零件结构缺陷(零件壁厚差大、油沟和尖锐棱角等)、淬火前工序间缺陷(锻造过烧、冷冲成形应力过大、较深的车刀痕等)和淬火工艺不良(淬火温度过高、冷却不良、表面脱碳、淬火返修工艺不当)等。
2. 轴承零件淬火裂纹的形貌特点及分析方法轴承零件淬火裂纹形状很不规则,有的沿横向,有的沿纵向,有的在零件表面呈“S”形或“Y”形,还有的呈龟裂网状。
淬火裂纹的深浅也各不相同,但深度远大于磨削烧伤裂纹。
观察淬火裂纹断口可以发现断口面往往有油污、水渍及回火色存在,未污染的断口面则是干净的细瓷状。
用金相显微镜观察,裂纹呈撕裂状扩展,尾部尖细,一般沿晶界分布。
淬火裂纹与锻造裂纹和原材料裂纹主要区别是裂纹两侧无脱碳现象。
对于轴承零件的淬火裂纹,除上述共性外,还有各自本身特点,举例如下:(1)材料冶金缺陷沿轧制方向分布,因此,由于组织疏松和显微孔隙造成的淬火裂纹热酸洗后在套圈、滚子端面和钢球两级呈点状或短线状分布,发纹和严重的碳化物偏析多在零件表面沿轴向分布。
gcr15simn淬火硬度 -回复

gcr15simn淬火硬度-回复gcr15simn淬火硬度是一个关键性能指标,用于评估材料的硬度和耐磨性。
在工程领域中,gcr15simn是一种常见的合金钢材料,被广泛应用于制造轴承、齿轮和其他机械零件。
淬火是一种常见的热处理工艺,通过快速冷却使钢材达到理想的硬度。
本文将逐步解释gcr15simn淬火硬度的相关概念、影响因素和测试方法。
第一部分:介绍gcr15simnGcr15simn是一种含有铬、钼、锰和硅等元素的合金钢材料。
这种材料具有优良的抗磨性、硬度和韧性,使其成为机械零件制造业中重要的材料选择之一。
该材料通常经过热处理才能达到所需的性能,其中淬火是最常见的热处理方法之一。
第二部分:淬火硬度的概念和影响因素淬火硬度是衡量钢材硬度的重要指标之一,它通常是通过测量材料在淬火后达到的硬度来衡量的。
淬火过程会使钢材中的奥氏体转变为马氏体,从而显著增加钢材的硬度。
淬火硬度受到多个因素的影响,包括淬火温度、淬火介质、淬火时间和淬火冷却速度等。
较高的淬火温度和冷却介质可能会导致较低的淬火硬度,而较短的淬火时间和更快的冷却速度则有助于提高淬火硬度。
第三部分:gcr15simn淬火硬度测试方法测试gcr15simn的淬火硬度通常使用洛氏硬度试验。
这种试验方法通过使用一个钢球或钻石锥对材料进行压痕硬度测量来确定其硬度。
洛氏硬度试验结果以一个数字表示,该数字越高表示材料的硬度越大。
在测试过程中,先将gcr15simn样品进行淬火处理,然后在淬火后的材料表面选择一定的测试区域进行测量。
然后使用洛氏硬度计装置施加一定的负荷,并观察压痕的尺寸。
根据压痕尺寸和试验参数,计算出样品的洛氏硬度值。
第四部分:gcr15simn淬火硬度的应用和意义gcr15simn淬火硬度的准确测量对于确定材料的性能和适用范围至关重要。
硬度是影响材料抗磨性、耐冲击性和强度的重要因素之一。
了解gcr15simn的淬火硬度有助于制造商选择适当的工艺参数和淬火条件,从而使所制造的零件具备所需的硬度和耐磨性。
轴承钢淬火

国内铁路轴承等温淬火现状3.1.材料GCr15GCr18Mo (SKF-24)0.90~1.05%C、1.65~1.95%Cr、0.15~0.25%Mo、0.20~0.40%Mn 3.2.HT工艺230~240℃×3.5h 100%B L等温淬火未采用B L+M原因:↑αk、防止套圈脆断↑表层压应力防止过盈装配崩裂↓淬火变形工艺简单(不回火)3.3.设备自动生产线转底、推盘、输送带式周期式淬火冷却槽+等温槽+清洗槽硝盐等温(50%KNO3+50%NaNo3+少量水)清洗 60~80℃水3.3.1.南京浦镇车辆厂 B等温淬火生产线X1轴承套圈 GCr18Mo奥地利爱协林同一工件硬度≤1HRC同一批工件硬度≤2HRC60~61.5HRC 235~240℃×5h HRC↓≤1组织:B L+M变形:涨大量稳定、椭圆变形↓3.3.2.瓦房店轴承集团 B等温淬火生产线NJP3226X轴承外圈 GCr18Mo北京爱协林 REDS270-CN 转底式工艺流程:上料台上料→保护气氛转底炉加热→淬火槽升降送料机械手→淬火平台→淬火槽淬火→等温槽升降送料机械手→等温淬火槽→风冷却台风冷→热水浸洗→漂洗→烘干机→卸料台卸料工艺曲线:材料:GCr18Mo HRC60~60.5 金相组织 3级3.3.3.宁波华海轴承 B等温淬火简易生产线轴承:FC202870、6488240 轧机轴承HRC59.5~61变形:FC405819 椭圆度 0.06~0.20mm径向涨大 0.55~0.70mm高度涨大 0.15~0.20mmM轴承4.1.影响轴承寿命的因素及其控制影响轴承寿命的材料因素滚动轴承的早期失效形式,主要有:破裂、塑性变形、磨损、腐蚀、疲劳在正常条件下主要是接触疲劳主要内在影响因素:硬度、强度、韧性、耐磨性、抗蚀性、内应力状态(服役条件之外)4.1.1. 淬火钢中的马氏体高碳铬钢原始组织:粒状珠光体淬火+低温回火:淬火马氏体 M中含碳量,明显影响钢的力学性能GCr15钢淬火M含碳量为0.5%~0.56%可获得抗失效能力最强的综合力学性能。
硝盐浴淬火烈度的计算及分析

硝盐浴淬火烈度的计算及分析摘要:硝盐浴淬火烈度是衡量金属材料淬火性能的一种方法,本文介绍了硝盐浴淬火烈度的计算方法及其在金属材料淬火性能评价中的应用。
首先,根据淬火前后的材料性能参数计算得到硝盐浴淬火烈度值。
然后,通过对比不同烈度值下的材料性能变化情况,评价金属材料的淬火性能。
最后,本文还介绍了硝盐浴淬火烈度的限制因素和未来发展方向。
关键词:硝盐浴淬火烈度;金属材料;淬火性能;计算方法;评价方法正文:一、硝盐浴淬火烈度的定义硝盐浴淬火烈度是一种用于评价金属材料淬火性能的方法,它表示在硝盐浴中淬火的强度大小。
硝盐浴淬火烈度主要包括两个指标:淬火烈度值和淬火时间。
淬火烈度值越大,淬火强度越大,金属材料的淬火性能越好。
二、硝盐浴淬火烈度的计算方法硝盐浴淬火烈度的计算方法主要包括以下步骤:1、根据金属材料的成分、硬度和淬火前的温度,选择相应的硝盐浴浓度和淬火时间。
2、将金属材料放入预热好的硝盐浴中,经过一段时间后取出。
3、测量淬火前后材料的性能变化参数,例如硬度、韧性、冲击强度等。
4、根据淬火前后的材料性能参数计算得到淬火烈度值。
其中,淬火烈度值的计算公式为:硝盐浴淬火烈度值=(淬火后的材料硬度-淬火前的材料硬度)/淬火后的时间三、硝盐浴淬火烈度在金属材料淬火性能评价中的应用通过比较不同淬火烈度值下的材料性能变化情况,可以评价金属材料的淬火性能。
在实际应用中,可以根据所需淬火性能要求,选择合适的淬火烈度值和淬火时间。
例如,在制造汽车零件时,需要将钢材淬火至一定硬度,以满足零件使用时的强度要求。
通过硝盐浴淬火烈度的计算和评价,可以选择出最适合的淬火强度和时间,以获取最佳的淬火效果。
四、硝盐浴淬火烈度的限制因素和未来发展方向硝盐浴淬火烈度的应用面较广,但同时也存在一些限制因素。
首先,硝盐浴浓度和淬火时间的选择需要大量的实验验证和经验积累。
其次,硝盐浴淬火烈度的计算结果只是对淬火性能的一个定性评价,无法给出淬火效果的具体数值化描述。