集中润滑系统的原理和维护
集中润滑系统的原理及维护审批稿
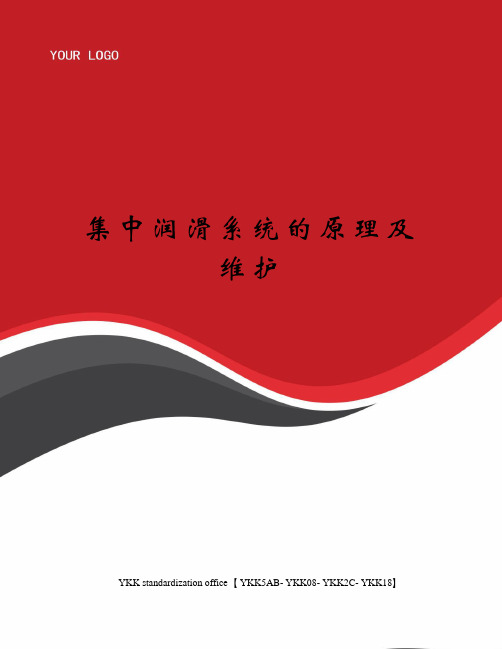
集中润滑系统的原理及维护YKK standardization office【 YKK5AB- YKK08- YKK2C- YKK18】集中润滑系统的原理及维护前言:什么是润滑?•理想状态下的润滑:在相互运动的接触表面之间形成一层油膜,使得两表面之间的直接摩擦(干摩擦)转变为油液内部分子间的摩擦(液体摩擦)•边界润滑:在两个滑动摩擦表面之间,由于润滑剂供应不充足,无法建立液体摩擦,只能依靠润滑剂中的极性分子在摩擦表面上形成一层极薄的(~μm)“绒毛”状油膜润滑。
这层油膜能很牢固地吸附在金属的摩擦表面上。
这时,相互接触的不是摩擦表面本身(或有个别点直接接触),而是表面的油膜•润滑的定义:在相互运动的接触表面之间形成一层油膜,使得两表面之间的直接摩擦(干摩擦)转变为油液内部分子间的摩擦(液体摩擦)或油膜之间的摩擦润滑的主要作用•减磨抗磨:使运动零件表面之间形成油膜接触,以减少磨损和功率损失•冷却降温:通过润滑油的循环带走热量,防止烧结•清洗清洁:利用循环润滑油冲洗零件表面,带走磨损剥落下来的金属细屑•密封作用:依靠油膜提高零件的密封效果。
•防锈防蚀:能吸附在零件表面,防止水、空气、酸性物质及有害气体与零件的接触。
设备润滑的重要意义•设备上几乎所有相对运动的接触表面都需要润滑,设备润滑是防止和延缓零件磨损和其他形式失效的重要手段之一•60%以上的设备故障是由润滑不良和油变质引起的引言:润滑工作一直是设备管理的重中之重,现代设备的机械故障大部分是由于润滑引起。
集中润滑的基本概念是从一个配有润滑剂的油泵装置给各个摩擦副集中提供适量的润滑剂。
由于现代机械制造技术的高速发展,人工加油已不能满足各种机械的需要,越来越多的集中润滑系统被运用到机械设备中并在提高设备可靠性、降低润滑劳动强度、减少润滑油量消耗方面起到关键作用;集中润滑系统分类:集中润滑系统总体可分为全损耗型系统、循环系统;循环系统属于专用系统,要求高,润滑点少;全损耗系统涵盖了机床润滑点的绝大部分。
自动润滑系统的原理及维护
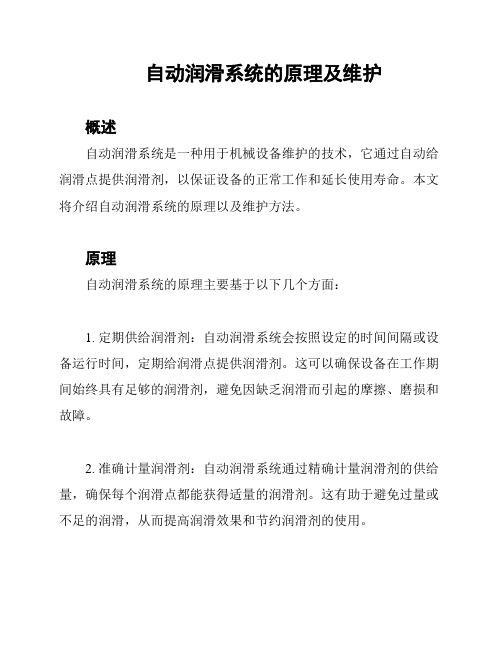
自动润滑系统的原理及维护概述自动润滑系统是一种用于机械设备维护的技术,它通过自动给润滑点提供润滑剂,以保证设备的正常工作和延长使用寿命。
本文将介绍自动润滑系统的原理以及维护方法。
原理自动润滑系统的原理主要基于以下几个方面:1. 定期供给润滑剂:自动润滑系统会按照设定的时间间隔或设备运行时间,定期给润滑点提供润滑剂。
这可以确保设备在工作期间始终具有足够的润滑剂,避免因缺乏润滑而引起的摩擦、磨损和故障。
2. 准确计量润滑剂:自动润滑系统通过精确计量润滑剂的供给量,确保每个润滑点都能获得适量的润滑剂。
这有助于避免过量或不足的润滑,从而提高润滑效果和节约润滑剂的使用。
3. 合理分配润滑剂:自动润滑系统可以根据设备不同部位的需求,将润滑剂分配到各个润滑点。
这样可以确保每个部位都能得到适量的润滑剂,提高设备的整体润滑效果。
维护方法为了确保自动润滑系统的正常运行,以下是一些维护方法的建议:1. 定期检查润滑剂供给量:定期检查自动润滑系统的润滑剂供给量,确保供给量的准确性和稳定性。
如有发现异常,应及时修复或更换润滑系统的零部件。
2. 清洁和保养润滑系统:定期清洁和保养自动润滑系统的零部件,以确保其正常工作。
清除灰尘、杂质等可以防止堵塞和损坏润滑系统的零部件。
3. 检查润滑效果:定期检查设备的润滑效果,如有异常或润滑不足的情况,应及时调整或修复润滑系统,以确保设备的正常运行。
总结自动润滑系统是一种可靠和高效的设备维护技术,它通过定期供给润滑剂,准确计量和合理分配润滑剂来确保设备的正常工作。
为了保证自动润滑系统的可靠性,我们需要定期进行维护和检查。
这些简单的维护方法可以帮助我们延长设备的使用寿命并减少故障的发生。
(完整版)干油集中润滑系统工作原理
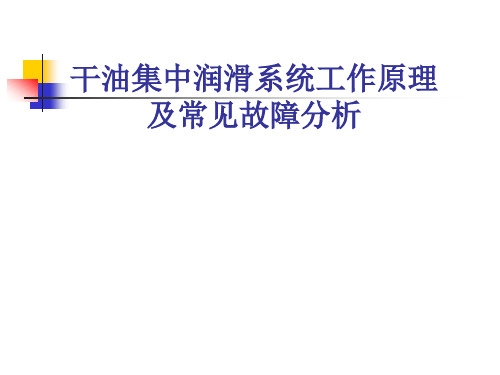
泵的工作原理
设位置1为初始位置,柱塞 B向下运动,柱塞A滞后B先 向上运动后向下运动;由于
出口设有单向阀,当运动到 位置2时A腔内被抽成真空; 到达位置3时,A、B两腔间 的通路被开启,油脂在真空 的作用下被吸入A腔;柱塞 继续运动到位置4时通路被 关闭,位置4到6为压油过 程;转过位置6后,柱塞继 续运动回到初始位置1,为 下一次压油循环做好准备,
DRB—L系列电动润滑泵
该系列电动润滑泵采用双柱塞机构,运转可靠, 减速机构置于泵体内,结构紧凑,体积小,配 以相应的电控箱可以实现自动控制。
型号说明:
DRB—L系列电动润滑泵使用说明
1.该系列电动润滑泵应安装在环境温度合适、灰尘少、 振动小,便于调整、检查、维护保养及补脂方便的地 方,并且尽可能地布置在系统的中心位置,缩短系统 配管长度,保持最低压力降,使泵能产生足以克服润 滑点背压的压力。
双线式集中润滑系统的工作原理 及特点
供油管内的压力达到分配器动作所需的压力, 分配器就能动作。而分配器动作完成又使供油 管内压力继续上升,当供油管内各处的压力都 超过分配器动作所需的压力,分配器全部动作, 系统完成了一次给油运行。因此,双线式集中 润滑系统通过控制供油管内的压力保障分配器 动作,完成系统的给油运行。
当左侧电磁铁得电时, 阀芯在电磁力作用下被 推向右侧,此时,进油 腔P与工作腔A相连,另 一腔B与回油腔相连,实 现向Байду номын сангаас管路供油,B管路 卸压;当右侧电磁铁得 电时,阀芯在电磁力作 用下被推向左侧,此时, 进油腔P与工作腔B相连, 另一腔A与回油腔相连, 实现向B管路供油,A管 路卸压,实现换向。
干油过滤器
如此往复实现向外部供应压 力油脂。
2
3
润滑脂(干油)集中润滑系统

润滑脂(干油)集中润滑系统一、润滑脂(干油)集中润滑系统的结构原理所谓“干油”,就是润滑脂;目前常用的干油集中润滑系统都是开式的,即润滑脂在润滑点消耗掉,不返回油桶。
典型的智能式干油集中润滑系统由电动油脂泵、加油泵、过滤器、分配器、控制柜、管路附件组成(见下图),其油路采用一个电磁换向阀控制一个润滑点的方式,管路布置和工作原理简单,故障判断和处理相对于使用单线或双线分配器容易;缺点是分配器体积较大。
该系统的突出特点是将传统的集中润滑与现代高新技术相结合,采用PLC对系统进行自动控制,并可实现计算机远程监控。
控制柜中的PLC是该系统的核心,它控制系统实现:按设定的循环间隔时间,启动系统,各电磁换向阀依次得电动作,逐点给油;通过设定各电磁换向阀得电时间,控制各点给油量;电磁换向阀得电时,流量传感器检测油流信号并反馈,通过指示灯或在监控电脑画面上显示;系统高、低压、油位低自动保护及报警;系统运行和故障记录功能。
采用计算机远程监控,则更可凸显系统控制和维护方便的高科技特点。
系统适用于上百个给油点的大型机械设备或生产线的集中润滑,并可与单线式集中润滑系统相结合使用。
与这些优点对应的是:系统的维护对电气人员、系统的使用对系统管理人员素质要求较高;系统的价格较高。
二、润滑脂(干油)集中润滑系统的优点智能干油集中润滑系统可根据设备工作状态,现场环境温度不同条件及设备润滑部位的不同要求,准确、定时、定量、可靠的满足各种润滑要求。
以维克森VICSEN-MX型集中润滑系统为例,该系统采用递进式工作方式,泵设计成可间歇或持续工作,这样可以按照不同的需要来编辑运行程序,一个直联的减速电机驱动泵内凸轮工作,可以同时驱动3个外置泵单元。
每个泵单元都配有溢流过压保护阀防止超压损坏。
可设置1-200个润滑点,能够准确及时地推送油脂到各个润滑点,还可以显著提高设备寿命,更加节省润滑脂的用量,多个润滑点可以采用统一的一个集中润滑系统,不仅可以大幅度的降低运营成本,而且维护起来也更加简单。
机床润滑系统的特点和工作原理
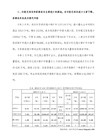
2 递进式润滑系统:主要由泵站、递进片式分流器组成,并可附有控制装置加以监控。特点是能对任一润滑点的堵塞进行报警并终止运行,以保护设备;定量准确、压力高,不但可以使用稀润滑油,而且还适用于使用润滑脂润滑的情况。润滑点可达100个,压力可达21MPa。
工作原理:是由中间板中的柱塞从一定位置起依次动作供油,若某一点产生堵塞,则下一个出油口就不会动作,因而整个分流器停止供油。堵塞指示器可以指示堵塞位置,便于维修。
机床润滑系统在机床整机中占有十分重要的位置,其设计、调试和维修保养,对于提高机床加工精度、延长机床使用寿命等都有着十分重要的作用。现代机床导轨、丝杆等滑动副的润滑,基本上都是采用集中润滑系统。
集中润滑系统是由一个液压泵提供一定排量、一定压力的润滑油,为系统中所有的主、次油路上的分流器供油,而由分流器将油按所需油量分配到各润滑点:同时,由控制器完成润滑时间、次数的监控和故障报警以及停机等功能,以实现自动润滑的目的。集中润滑系统的特点是定时、定量、准确、效率高,使用方便可靠,有利于提高机器寿命,保障使用性能。集中润滑系统按使用的润滑元件可分为单线阻尼式润滑系统、递进式润滑系统和容积式润滑系统。
3 容积式润滑系统:以定量阀为分配器向润滑点供油,在系统中配有压力继电器,使得系统油压达到预定值后发讯,使电动机延时停止,润滑油从定量分配器供给,系统通过换向阀卸荷,并保持一个最低压力,使定量阀分配器补充润滑油,电动机再次起动,重复这一过程,直至达到规定润滑时间。该系统压力一般在50MPa以下,润滑点可达几百个,其应用范围广、性能可靠,但不能作为连续润滑系统。
Hale Waihona Puke 1 单线阻尼式润滑系统:适合于机床润滑点需油量相对较少,并需周期供油的场合。此润滑系统是利用阻尼式分配器,把泵打出的油按一定比例分配到润滑点。一般用于循环系统,也可以用于开放系统,可通过时间的控制,以控制润滑点的油量。独特的优点是非常灵活,多一个润滑点或少一个都可以,并可由用户安装,且当某一点发生阻塞时,不影响其他点的使用,因此应用十分广泛。
集中润滑系统工作原理

集中润滑系统工作原理
集中润滑系统是一种用于在多个润滑点上提供润滑剂的系统。
它主要由润滑泵、管路、配油器和润滑点组成。
工作原理如下:
1. 润滑泵:集中润滑系统通常使用电动润滑泵。
润滑泵将润滑剂从润滑剂储罐或油箱中抽取,通过压力来驱动润滑剂流动。
2. 管路:润滑泵通过一系列管道将润滑剂输送到各个润滑点。
管路通常会使用钢管或高压软管。
3. 配油器:在润滑系统中,配油器用来控制润滑剂的流量和压力。
配油器通常包括减压阀、分配器和测量装置。
减压阀用来将高压润滑剂降压到合适的工作压力,分配器将润滑剂分配到各个润滑点,测量装置用来监测润滑剂的流量和压力。
4. 润滑点:润滑点是机械设备上需要润滑的部位,包括轴承、齿轮、滑动面等。
润滑剂通过润滑点进入机械设备,起到润滑、降低摩擦和冷却的作用。
集中润滑系统的工作原理是通过润滑泵将润滑剂压力送到润滑点,确保各个润滑部位得到足够的润滑剂,从而提高设备的使用寿命和可靠性。
润滑系统工作原理

润滑系统工作原理
润滑系统的工作原理是通过给机械设备提供合适的润滑剂,在摩擦表面形成一层润滑膜,减少摩擦力和磨损,以保证设备正常运转。
具体工作原理包括以下几个方面:
1. 润滑剂供给:润滑系统通过泵或其他方式将润滑剂从润滑油箱中供给到润滑点,形成润滑膜。
通常润滑剂会经过滤器过滤,确保润滑剂的清洁度。
2. 润滑膜形成:润滑剂在润滑点形成一层润滑膜,填充耦合间隙和表面凹陷,以减少金属间的直接接触。
这层润滑膜能够减少摩擦和磨损,并且具有较高的抗压性。
3. 摩擦力减小:润滑剂的润滑膜能够在机械设备工作时减小接触表面的摩擦力。
当设备运转时,润滑剂在润滑膜的作用下形成润滑沟槽,减少金属表面接触,有效减小摩擦力。
4. 磨损减少:润滑系统的润滑膜能够保护机械设备的表面,防止金属间的磨损。
润滑剂中的添加剂,如抗氧化剂、防锈剂和减摩添加剂,能够延长设备的使用寿命,并降低维修和更换成本。
5. 热量分散:润滑剂在润滑过程中还承担着散热的作用,将摩擦产生的热量带走,保持设备的温度在适宜范围内,防止过热损坏。
总之,润滑系统的工作原理是通过正确选择润滑剂、合理供给润滑剂,形成润滑膜,减少摩擦和磨损,保护机械设备的正常运行,延长使用寿命。
车辆集中润滑系统介绍

车辆集中润滑(AG)系统概况对于车辆来说,保证良好的润滑是极其重要的。
在油田,有很多重要的大型车辆:如吊车、压裂车、水泥车、修井机、重型运输车、工程机械等。
这些设备的使用率高,工作中不容抛锚。
而油田的使用工况又都比较恶劣,坑洼不平的油区道路、尘土、泥坑、水坑等,这就对车辆的润滑提出了更高的要求。
设备管理部门为此建立了完善的管理制度,其中就包括润滑的管理,常常还进行设备大检查等。
但由于种种原因,润滑还是得不到保证,由此而引起的设备损坏时有发生。
常见的因润滑不好造成的磨损部位有:钢板弹簧销及吊耳销(严重后将引起钢板断裂)、横直拉杆和尚头、吊车平衡梁中间铜套及两端的关节轴承、吊车的刹车凸轮轴滑动轴承等。
磨损后必然要修理换零件,少则几小时,多则数日。
既耽误了生产,又付出了修理费用。
目前车辆打黄油情况大型车辆的黄油润滑点非常多,一般3桥卡车有20多个点,轮式装载机30多点,而25-50吨的(加腾)吊车等可多达40-60多点。
这些点的润滑全靠司机逐点用黄油枪加注。
由此产生一系列问题:◆即便有严格的设备润滑制度,也难保证司机会定时、定量的加油。
◆很难保证将所有的润滑点都打上黄油。
有时是遗忘,几十个点全记住较难。
有时则是条件所限,如没有地沟、没有时间(出勤率太高)、黄油嘴被油泥糊住等。
◆有的润滑点长时间未加油后,老油脂老化变硬后将油道堵塞,再想加油就加不进去了,除非及时发现检修,否则运动付磨损是很快的事情。
◆由于黄油嘴外露,打油时常常将泥沙等一同挤入,反而加速了磨损。
◆由于黄油嘴外露,水容易进入运动付,造成油脂变质而实效。
◆司机加油的劳动强度大,麻烦,工作条件差。
集中润滑系统的特点车辆的自动润滑系统是将底盘上的各个黄油润滑点(旋转部分除外)连接起来,通过电动润滑泵、控制器、分配器、高压树脂软管等,准确的向各润滑点定时、定量的供给油脂。
具有以下特点:◆定时润滑:每个供油周期(可调)由控制器设定后自动执行。
(也可手动控制)◆定量润滑:每个润滑点的供油量事先设计好,由分配器精确供给,每次相同。
第三节 集中润滑系统的构造与维护

第三节集中润滑系统的构造与维护一、集中润滑系统的构造盾构机的集中润滑装置一般采用双线式消耗型集中润滑系统。
双线式集中润滑系统主要由电动润滑泵、换向阀(通常设置在润滑泵上)、双线分配器、控制装置、压力控制阀类和2条供油管路组成,通常情况下还需要油脂转运泵,自动补充电动润滑泵的油脂供给,电动润滑泵和换向阀一般布置在盾构机后配套台车上,油脂经电动润滑泵输出后经过后配套台车和操作平台上主油脂管路达到各个润滑设备,再经过润滑设备附近的双线分配器,被输送到各个润滑点,其原理简图见图3-4。
1、双线式集中润滑系统的原理双线式集中润滑系统使用2条供油管路交替供油,当其中一条由润滑泵供油,另一条则向贮油器开放,双线分配器有2个进油口,分别与2根供油管连接。
双线式集中润滑系统的原理是,润滑泵从贮油器吸入润滑脂,经过换向阀由供油管输送到分配器,进入分配器后加压于先导活塞,先导活塞下腔与供油管连通,经换向阀向贮油器开放。
先导活塞在供油压力的作用下,移动到下端,使主活塞上腔连通,主活塞下腔与出油口连通,供送的润滑脂进入主活塞上腔,推动主活塞下移,将其下腔的润滑脂经给油管压送到润滑点,给油量由主活塞的直径和行程确定。
切换供油管,分配器活塞按相同的顺序反向进行前述动作,分配器得以循环工作。
图3-4 双线式集中润滑系统原理图2、双线式集中润滑系统的结构特点(1)给油定量准确,且可以对其进行手动调节分配器采用容积计量,给油量不受外界因素影响并且分配器有行程微调装置,可以在一定范围内对给油量进行定点手动调节,准确地调整给油量,确保各润滑点的油脂量稳定充足。
(3)给油可靠润滑泵输出的高压润滑脂直接推动分配器主活塞向润滑点压送润滑脂,压力高,在需要润滑密封的部位确保给油可靠,确保各润滑部位的润滑和密封作用。
3、集中润滑系统润滑油脂的性能指标(1)通用润滑油脂工业锂基润滑脂并加有极压、防锈和抗氧化添加剂。
型号为NLGI O#;滴点不低于170℃;25℃工作锥入度为35~38.5 mm;适宜温度为-20~+120℃。
稀油集中润滑系统原理及其故障处理

稀油集中润滑系统组成
稀油集中润滑系统组成 1、储存油液的装置---油箱
作用: ①:贮油 ②:沉淀杂质 ③:消除泡沫,发散气体 ④:散热、冷却 ⑤:支撑作用
稀油集中润滑系统组成
2、供油装置---油泵
稀油集中润滑系统工作压力在0.3~0.6Mpa,属 于低压范围,多采用齿轮泵。对于高低压润滑系统 的高压部分会采用柱塞泵来供油。 2.1齿轮泵的工作原理 原理图见图2-1-1 常见型号CB-*的含义:CB是“齿”、“泵”汉字的 首拼 *代表该泵的公称流量L/min
2-2 齿轮泵常见故障处理
分析原因 处理方法
①:装配时盖板与轴不同心, ①:根据查出的情况逐一 滚针质量差,滚针轴承不干净,处理 齿轮上有毛刺,轴上的螺栓紧 ②:修复有关零件及调整 固脚太长 间隙 ②:轴向及径向间隙过小 ③:严防污物进入油池, ③:油液中的污物吸入泵内 加强过滤,保持油液清洁 ①:压盖堵塞了前后盖板的回 油通道,造成回油不畅,压力 升高 ②:骨架油封与泵的前盖配合 过松 ③:泄漏通道被污物堵塞 ①:重新装配压盖,使回 油通道畅通。 ②:更换骨架油封 ③:清除污物,消除堵塞
稀油集中润滑系统概述
6、油箱加热控制
为了发挥润滑油润滑的最好效果,润滑油温度一 般要保持在40℃,所以要给油箱加热,通常采用 的方法①蒸汽加热法:比较缓和。②电热元加热: 比较剧烈,有时局部加热会使油产生裂化反应,降 低黏度并产生胶质沉淀。 加热会有温度自动调节装置,一般会在油箱安装 电接触点温度计,控制加热器操作电气回路。
稀油集中润滑系统概述
7、过滤器报警系统
当油流进出过滤器压差大于0.15Mpa时,过滤 器被阻塞,系统就会发出报警信号,当压差减小或 恢复到允许压差范围后,报警信号解除。 控制连锁由接在过滤器上的压差发讯器控制系统 电气回路。
集中润滑
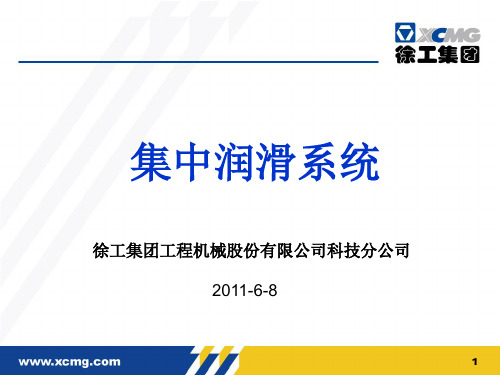
推荐采用下述加油方式加油。 加油时应注意保持清洁。
20
3. 集中润滑系统维护及保养
3.2 日常维护及保养
用油品牌:-35℃至80℃采用NLGI 2#锂基润滑脂,-35℃以下采用NLGI
00#锂基润滑脂。 警告:加入油箱内的油脂必须保证洁净,并且必须采用锂基润滑脂。
(推荐使用美孚NLGI 2号锂基润滑脂。)
15
2. 集中润滑系统原理
2.5 S-EP4电控器
S-EP4电控器可以对集中润滑系统进行时间控制。 时间编程控制: (润滑时间,间隔时间)启动后,黄色的LED指 示灯将被点亮2.5秒,表示可以进行操作了。
16
2. 集中润滑系统原理
2.5 S-EP4电控器
当按下电机外壳或操作仪表板上的启动 键进行操作时,润滑周期开始。当润滑周期 完成后,润滑泵电机被关闭,间隔时间开始。 所有后续润滑作业将按照预先设定的时间程 序进行。
更换泵单元; 连续使泵运转,排气; 向油箱加注油脂。
检查系统; 清洗或更换分配器; 更换安全阀
安全阀喷油
23
4. 集中润滑系统故障及维修
4.1 故障及维修
故障现象 原因 维修方法 1、检查电线是否损坏; 2、检查电线连接是否紧密; 3、检查接线是否正确; 4、检查电源电压; 5、检查保险丝是否熔断。 更换电控器 更换新泵 检查系统; 清洗或更换分配器; 更换安全阀
5
2. 集中润滑系统原理
2.1 集中润滑系统的组成
1. EP-S电动泵 2. S-EP4电控器 3. PE-120F泵单元 4. MX-F分配器 5. 管线及管接头
6
2. 集中润滑系统原理
2.2 EP-S电动泵工作原理
集中润滑是什么原理的应用

集中润滑是什么原理的应用1. 什么是集中润滑集中润滑是一种润滑系统,它利用专用设备将润滑脂或润滑油从中央润滑泵通过管路输送到多个润滑点,实现对多个设备零部件的同时润滑。
集中润滑系统的核心是中央润滑泵和分配器,通过这两个设备实现润滑脂的供给和分配。
2. 集中润滑的原理集中润滑系统的原理是通过中央润滑泵抽取润滑脂或润滑油,将其输送到分配器,再由分配器将润滑脂或润滑油分配到各个润滑点。
中央润滑泵可以根据设备的润滑需要,以一定的频率和压力抽取润滑脂或润滑油,同时通过管路输送到分配器。
分配器则根据设备的要求,将润滑脂或润滑油平均分配到各个润滑点,确保设备的零部件得到充分的润滑。
3. 集中润滑的应用集中润滑系统广泛应用于各种设备和机械中,以提高设备的润滑效果和工作效率。
以下是集中润滑的一些应用场景:3.1 机械设备集中润滑系统在各种机械设备中都有广泛的应用,如工业机械、冶金设备、挖掘机、装载机等。
通过集中润滑系统,可以同时润滑设备的多个润滑点,减少润滑时间和工作量,提高设备的工作效率和寿命。
3.2 汽车行业在汽车行业中,集中润滑系统被广泛应用于汽车发动机和底盘润滑。
通过集中润滑系统,可以确保发动机和底盘的各个润滑点得到充分的润滑,减少摩擦和磨损,提高汽车的性能和耐久性。
3.3 轴承润滑轴承是各种机械设备中常见的零部件,其正常润滑对于设备的正常运行至关重要。
集中润滑系统可以实现对轴承的集中润滑,通过精确的润滑量控制和分配,确保轴承得到适量的润滑,减少磨损和故障发生的可能性。
3.4 铁路和航空设备在铁路和航空设备中,由于工作环境的特殊性和设备的复杂性,对润滑的要求更加严格。
集中润滑系统可以满足这些要求,通过自动化的控制系统,实现对设备的精确润滑,减少维修和故障率,提高设备的可靠性和安全性。
3.5 食品加工设备在食品加工设备中,由于对润滑油或润滑脂的要求更高,需要确保润滑剂不会对食品产生污染。
集中润滑系统可以通过使用特殊的润滑剂和密封材料,满足食品工业的卫生要求,同时实现对设备的可靠润滑。
双线式集中润滑系统原理

一、双线式集中润滑系统原理双线集中润滑系统是集中润滑的一种主要方式,双线式集中润滑系统主要由润滑泵、换向阀、压力操纵阀(或压差开关)、双线分配器、电控箱和两条供油管道组成,润滑泵输出的润滑脂,经换向阀交替由两条供油管输送到双线分配器,经过双线分配器定量地分配到各润滑点。
供油管内的压力达到分配器所需动作压力,分配器进行动作,而分配器动作完成又使油管内压力继续上升,当供油管各次压力都使分配器完成动作(系统完成一次给油运行)后,系统压力升到换向阀换向压力,换向阀换向进行二次给油。
二、双线式集中润滑系统常见几种方式:1、手动式手动润滑泵上装有手动换向阀,当供油管路压力急剧上升,判断系统给油工作已完成,进行手动换向。
原理图:该系统由人工控制换向,设备简单、费用低,适用于给油间隔时间长,润滑点少的场合。
2、电动式A、电动终端式该系统由终端压力操纵阀(或压差开关)发出压力(差)信号(终端分配器动作压力),由电气控制换向阀进行换向。
原理图:该系统采用终端压力作为系统给油工作的控制参数,故适用于润滑点散布较广的场合。
特点:配管费用较低。
B、液压换向终端式该系统由换向阀出口压力直接控制换向,换向不需终端压力(差)信号和电气控制。
原理图:该系统采用换向阀出口压力作为系统给油工作的控制参数,因而液压换向的换向压力需根据系统润滑点多少进行现场设定。
特点:配管费用较低、控制环节简化。
C、液压换向环式该系统由进入液压换向阀的环式回路末端压力控制换向,换向不需终端压力(差)信号和电气控制,但需接环式回路。
原理图:该系统采用环式末端压力作为系统给油工作的控制参数。
特点:配管费用相对较高,适用于润滑点比较集中的场合。
三、双线润滑系统设备元件驱动方式配管方式换向方式润滑泵公称压力Mpa换向阀电控箱型号流量ml/min贮油器容积L电极功率kw标准型号引进型号手动式终端式手动式SGZ-8 / 8ml/循环 3.5/6.3手动换向/ SRB-J7Z-2 FB-4A7ml/循环210SRB-J7Z-5 FB-6A 5SRB-L3.5Z-2 FB-62A 3.5ml/循环220SRB-L3.5Z-5 FB-62A 5电动式终端式电动式DRB-L60Z-Z U-25AE 60 20 0.372034DF-L2型电磁换向器YZF-L压力操R1904 DRB-L19.5Z-Z U-4AE 195 35 0.75DRB-L58.5Z-2 U-5AE 585 90 1.5。
轮斗设备集中润滑系统工作原理和常见及疑难故障排除
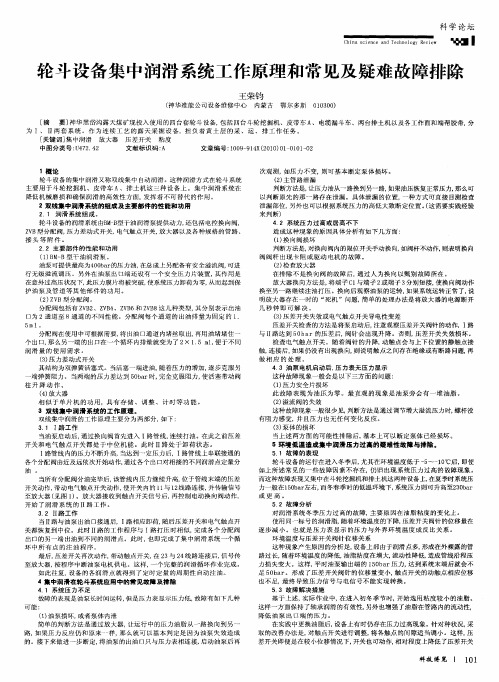
分 配 阀在 使用 中可 根据 需要, 出油 口通道 内堵丝取 出, 将 再用 油堵 堵住 一 个 出 口, 那么 另 一端 的出 口在一 个循 环 内排量 就变 为 了 2 15 m , 于不 同 × . l 便
润滑 量 的使 用 需求 。
() 力差动 式 开关 3压 其 结构 为双 弹簧活 塞式 。当活塞 一端 进油 , 随着 压力 的增 加, 步克 服另 逐
5m1 。
次观 测, 压 力不 变, 可 基本 断定 泵 体 损坏 。 如 则 () 管路 泄漏 2主 判 断方法 是, 让压力 油从一路 换到 另一路, 如果油 压恢复 正常压 力, 么可 那 以判 断原 先 的那 一路 存在 泄漏 。具 体 泄漏 的位 置, 一种 方 式可直 接 目测 检查 泄漏 部位, 另外 也 可 以根 据 系统 压力 的 高低 大致 断 定位置 。这 需要 实践 经验 ( 来判 断) 4 2 系统 压 力过 高或居 高 不下 造 成这 种现 象 的原 因具 体分析 有 如下 几方 面 : ( ) 向阀损 坏 1换 判 断方法是, 换向 阀内的限位 开关手 动换 向, 阀杆不动 作, 对 如 则表 明换 向 阀 阀杆 出现 卡 阻 或 驱动 电机 的 故 障 。 () 2 检查 放大 器 在排 除 不 是换 向阀 的故 障后 , 过 人 为换 向 以甄 别故 障 所在 。 通 放大 器 换 向方 法是 , 将端 子 c 与端 子 2 端子 3 别短 接, l 或 分 使换 向阀动作 换 至 另一路 继续注 油 打压 。换 向后观察 油泵 的运 转 , 果系 统运 转正常 了, 如 说 明放大 器存 在 一时 的 “ 死机 ”问题, 简单 的 处理办 法 是将 放大 器 的 电源 断 开 几 秒 钟 即可 解 决 。 () 3 压差 开关 失效 或 电气触 点开 关导 电性 变差 压差 开关 检查 的方法 是将 泵启 动后, 意观 察压差 开关 阀针 的动作,I 注 路 与 I路 达 到 5 b r的压 差 后, I 08 阀针 会 出现升 降 。否则, 压差 开 关失 效损 坏 。 检查 电气 触 点开 关 。随着 阀针 的升 降, 动触 点会 与上 下 位置 的静 触点接 触, 接后 , 连 如果仍 没有 出现 换 向, 说 明触 点 之 间存 在绝 缘或有 断 路 问题, 则 再 做相应 的处理 。 4 3 油 泵 电机 启 动后 . 压力 表无 压力 显示 这种 故障 现象 一般 会是 以下三方 面 的 问题 : () 力安 全 片损坏 1压 此故 障 表 现 为 油压 为 零 。最 直 观 的 现 象是 油泵 旁 会有 一堆 油 脂 。 () 2 溢流 阀的失效 这种故 障现 象 般很少 见, 一 判断 方法 是通 过调 节增大 溢流 压力 时, 螺杆没 有 阻力 感觉 , 且压 力 也 无任 何 变化 反 应 。 并 () 体 的损坏 3泵 当上 述两 方 面 的可 能性 排 除后 , 本 上可 以 断定 泵体 已经损 坏 。 基
集中润滑系统的原理及维护
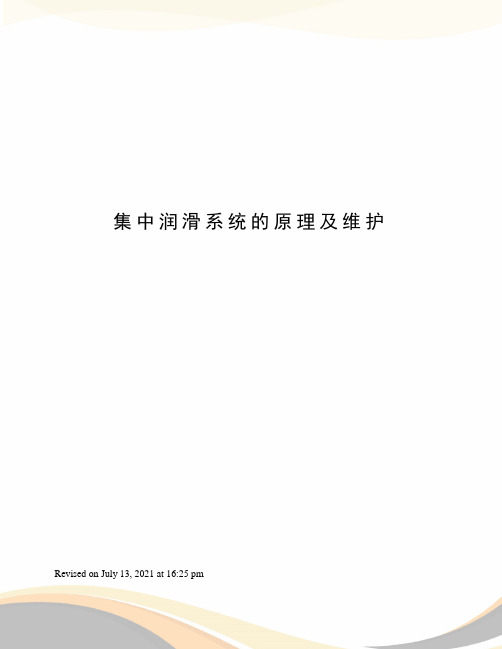
集中润滑系统的原理及维护Revised on July 13, 2021 at 16:25 pm集中润滑系统的原理及维护前言:什么是润滑•理想状态下的润滑:在相互运动的接触表面之间形成一层油膜;使得两表面之间的直接摩擦干摩擦转变为油液内部分子间的摩擦液体摩擦•边界润滑:在两个滑动摩擦表面之间;由于润滑剂供应不充足;无法建立液体摩擦;只能依靠润滑剂中的极性分子在摩擦表面上形成一层极薄的0.1~0.2μm“绒毛”状油膜润滑..这层油膜能很牢固地吸附在金属的摩擦表面上..这时;相互接触的不是摩擦表面本身或有个别点直接接触;而是表面的油膜•润滑的定义:在相互运动的接触表面之间形成一层油膜;使得两表面之间的直接摩擦干摩擦转变为油液内部分子间的摩擦液体摩擦或油膜之间的摩擦润滑的主要作用•减磨抗磨:使运动零件表面之间形成油膜接触;以减少磨损和功率损失•冷却降温:通过润滑油的循环带走热量;防止烧结•清洗清洁:利用循环润滑油冲洗零件表面;带走磨损剥落下来的金属细屑•密封作用:依靠油膜提高零件的密封效果..•防锈防蚀:能吸附在零件表面;防止水、空气、酸性物质及有害气体与零件的接触..设备润滑的重要意义•设备上几乎所有相对运动的接触表面都需要润滑;设备润滑是防止和延缓零件磨损和其他形式失效的重要手段之一•60%以上的设备故障是由润滑不良和油变质引起的引言:润滑工作一直是设备管理的重中之重;现代设备的机械故障大部分是由于润滑引起..集中润滑的基本概念是从一个配有润滑剂的油泵装置给各个摩擦副集中提供适量的润滑剂..由于现代机械制造技术的高速发展;人工加油已不能满足各种机械的需要;越来越多的集中润滑系统被运用到机械设备中并在提高设备可靠性、降低润滑劳动强度、减少润滑油量消耗方面起到关键作用;集中润滑系统分类:集中润滑系统总体可分为全损耗型系统、循环系统;循环系统属于专用系统;要求高;润滑点少;全损耗系统涵盖了机床润滑点的绝大部分..全损耗系统按供油方式分为单线阻尼系统、容积式系统、递进式润滑系统单线阻尼系统特点:• 1 节流式供油利用流体阻力分配润滑剂• 2 系统工作压力低1bar 到 10bar• 3 结构简单、造价低• 4 油量误差较大• 5 润滑点数小于30点容积式润滑系统特点:• 1 定量式供油• 2 系统工作压力15bar - 25bar• 3 排油准确• 4 造价适中应用广泛•5润滑点数300点以下•6适用于中小型设备递进式润滑系统特点:•递进定量式供油•系统工作压力10bar - 60 bar•排油准确•造价较高安装复杂•一般用于大型设备润滑系统的组成•润滑泵 - 提供定量清洁的润滑油..分为:手动、机动、电动、气动润滑泵;•油量分配器 - 将润滑油定量或按比例分配到各个润滑点..分为:计量件、定量注油件、递进式分配器•分配系统 - 由管道接头、硬管或软管、分配接头等各种附件组成;按要求向润滑点输送润滑油•滤油器 - 过滤杂质;保证提供清洁的油•电子程控器和压力开关、感应开关、液位开关等 - 控制润滑泵按预定要求周期工作;具有对系统压力、液位进行监控和报警以及对系统工作状态进行显示等功能容积式润滑系统工作原理定量注油件工作原理系统加压润滑系统卸荷;补液回到原始状态参考上面示意图;定量注油件的工作步骤如下:1.润滑泵将压力油打入分配器底腔8;随着底腔8压力升高;润滑剂被压进进油腔7;压力继续升高;密封阀6的唇型密封变形;润滑剂流入分配器下腔5;密封阀6同时封住活塞4连接上腔3与下腔5的通道..由于底腔8油压大于复位弹簧2的压力及系统背压;活塞4上升;强迫上腔3内的润滑剂通过出口1注入润滑点..2.电气控制润滑泵停止;底腔8卸荷; 复位弹簧将活塞往下压;下腔5压力上升;迫使密封阀向下;由于密封阀的截面直径小于活塞的截面直径;密封阀6的返回速度大于活塞4;密封阀的运动导致活塞4通孔打开同时底腔8 关闭;随着活塞4继续下移;下腔的润滑剂通过活塞4的通道进入上腔..3.完成了第二步的油液补充循环后;密封阀6关闭底腔8、下腔5、上腔3相互间的通道;分配器充满油液等待下一次润滑过程;容积式分配器剖视图容积系统泵源要求•工作压力15—25公斤•间歇供油;每次供油持续一段时间管路保压时间•供油结束系统卸荷•系统卸荷后低压保持典型电动润滑泵原理图工作过程:1.润滑泵打油——压力油打开液控换向阀——压力油进入主润滑管路——溢流阀限定系统最高压力;2.泵停止——液控换向阀在弹簧力作用下回位——主油路油液通过单向阀回油箱——单向阀弹簧保持主油路一定低压;容积式系统通常配备的电气开关及功能如下:•液位开关——油箱低液位报警•高压压力开关——系统达到设定值开关发信号;泵延时后停止;•低压压力开关——系统压力低于此开关设定值时报警;表明管路或单向阀有泄漏综上所述;容积式系统工作步骤如下:•油泵启动管路压力上升•压力油推动注油件活塞•分配器排出定量润滑油•分配器出油口封闭•所有分配器完成一次排油•油压达到高压开关设定压力•油泵继续工作电气设定的时间5秒— 20秒•多余油液通过溢流阀回油箱•油泵停止系统自动卸荷•管路油压达到系统设定低压•注油件活塞靠弹簧力返回•注油件上腔补充油液;等待下一润滑循环容积式系统故障诊断根据容积式系统工作原理;现场常见故障及可能原因总结如下:•现象:泵连续运转可能原因:管路、分配器或润滑油箱内部泄漏压力达不到高压开关设定值;高压开关故障;导致电气没有压力到达信号;•现象:润滑点不出油•可能原因:分配器堵塞;系统压力不够;不能推动分配器弹簧;泵源不卸压;分配器活塞不能复位;无法补充油液;•现象:润滑点连续油液流出可能原因:分配器密封件坏;有泄漏•现象:润滑站油量消耗急剧增大可能原因:管路或分配器有泄漏;高压开关或其它电气控制元件故障导致频繁打油递进式润滑系统工作原理MSP模块式分配器阀组Lubriquip•上图为MSP递进式分配器阀组;类似于液压叠加阀;每个工作阀片均有一个活塞;类似于液压阀的阀芯.. 系统供油时;分配器中一系列活塞按一定的顺序做差动往复运动;各出油口按一定顺序依次出油;一旦某点堵塞;将引起整个系统堵塞..1 工作阀块;2 阀块底板 3首片 4 尾片 5备用片分配器阀组工作原理位置1; 1口出油位置2; 2口出油位置3;3口出油位置4;4口出油位置5;5口出油位置6;6口出油图中;红色通道表示压力进油、蓝色通道表示润滑剂出口、浅红色为封闭的油路;压力油进油通道红色总是与所有分配器相通;但每次只有一个活塞能够移动;润滑按图1到图6顺序循环进行..•如上图所示;各个工作片的柱塞副在紧跟着上一片循环之后;各自工作完成自己的柱塞行程;把定量的润滑剂输送到润滑点..只要有压力油供给首片;分配器的工作片就以递进式方式连续循环运行..递进式润滑泵源要求•工作压力10公斤— 60公斤•间歇或连续供油;管路系统不需保压•不需要卸荷装置•需要电气或机械高压保险装置..•油液清洁度要求较容积式高递进式润滑系统连接见第二页系统连接示意图;泵的出油口只能接一组分配器;其它的必须在第一组的出油口连接;称为母-子-孙接法;由以上原理可知;分配器的任意出油口不能堵死使用;否则将引起递进循环中断;进而所有润滑中断..常见递进式系统开关/报警器及其功能•电气循环指示器——监控润滑剂在系统中流动情况;异常报警•机械式堵塞指示器——系统压力超过额定值时;伸出指示杆以示报警..故障排除后;需采用手动将压力报警器的指示杆复位..•液位开关——油箱低液位时报警递进式系统工作步骤•油泵启动;压力油进入主分配器•压力油推动与之相通的某一活塞运动直至该活塞到终点•与此活塞对应出油口排出定量油;进入相应的子分配器•活塞位置变化导致另一阀块活塞压力油接通;此活塞开始运动到终点..定量的油液排到相应子分配器进油管路•只要压力油存在;主分配器各个阀块活塞依次循环运动..相应出油口依次排出定量油液;进入对应子分配器..•各子分配器由主分配器排出的油驱动;各出油口循环定量排油..•泵停止供油;各分配器活塞停在当前的位置..•下一供油周期开始;泵打油;各活塞由上次停止的位置开始运动打油..递进式系统故障诊断根据递进式系统工作原理;现场常见故障及可能原因总结如下:•现象:供油时系统无压力可能原因:主管路泄漏 / 膜片式保险破裂 / 泵源内泄漏;引起系统泄压•现象:系统压力偏高;但所有润滑点不出油可能原因:某点分配器或某出油口或某油路堵塞;导致整个系统堵塞;•现象某子分配器不出油;其它正常可能原因:该分配器对应支路/接头漏油;该分配器进油压力不足两种系统预防性维护检查步骤在现场的维修实践中;我总结了这两种系统的标准预防性维护检查步骤;指导维修工进行设备集中润滑系统周期性检查;在降低故障率;避免灾难性的润滑事故方面起到很好的作用..容积式润滑系统标准检查步骤•启动润滑;检查润滑过程是否正常;主管路压力是否为 20bar 左右•外观检查各分配器及润滑点接头有无漏油现象•检查各分配器工作是否正常• A 松开润滑部位前接头;擦干油液• B 启动润滑泵;检查接头处无油液滴出;确认后拧紧接头;• C 接头不滴油及连续滴油均为不正常;需清洗或更换分配器递进式润滑系统标准检查步骤•启动油泵;检查泵出口压力是否正常 10-60bar•外观检查各分配器及润滑点接头有无漏油现象•首先处理漏油的阀块;接头;•检查各分配器是否功能正常• A 任选一末端润滑部位前接头;擦干油液•B启动润滑泵;检查接头处有无周期性油液滴出• C 如果有周期性油液冒出;表明整个系统无堵塞;• D 如果无油液滴出;表明系统堵塞;执行以下操作•松开润滑泵后第一级分配器所有出口接头;启动油泵;观察各出口有无出油;a.如果没有出油;拆下此分配器清洗;疏通或更换备件;b如果周期性出油;接上一个出口;按A;B步骤检查该出口下一级分配器;•依次接上主分配器出口;按上一步骤检查;直到找出堵点;两种润滑系统在DCEC西区的分布容积式润滑系统• B 缸体所有生产线线、B 缸盖所有机加线、C缸体YNC各生产线、C 缸体清洗机递进式润滑系统•EQX 各生产线、COUMA 线、B 缸盖清洗机。
稀油集中润滑系统原理及其故障处理

稀油集中润滑系统组成
稀油集中润滑系统组成
5、增加油温的装置---加热器
电气加热元件 蒸汽加热
稀油集中润滑系统组成
6、油路限制元件---阀
6.1 平安阀——在润滑系统中油压设计最 大压力为0.6Mpa,多余的压力就会通过 平安阀泄回油箱,从而起到爱护润滑系统 的作用。
平安阀分法兰式和螺纹接管式。
整体式结构
分散式结构
稀油集中润滑系统组成
稀油集中润滑系统组成 1、储存油液的装置---油箱
作用: ①:贮油 ②:沉淀杂质 ③:消退泡沫,发散气体 ④:散热、冷却 ⑤:支撑作用
稀油集中润滑系统组成
2、供油装置---油泵 稀油集中润滑系统工作压力在
0.3~0.6Mpa,属于低压范围,多接受齿 轮泵。对于凹凸压润滑系统的高压部分会 接受柱塞泵来供油。 2.1齿轮泵的工作原理 原理图见图2-1-1 常见型号CB-*的含义:CB是“齿”、“泵” 汉字的首拼 *代表该泵的公称流量L/min
稀油集中润滑系统概述
7、过滤器报警系统 当油流进出过滤器压差大于
0.15Mpa时,过滤器被堵塞,系统就会发 出报警信号,当压差减小或复原到允许压 差范围后,报警信号解除。 限制连锁由接在过滤器上的压差发讯 器限制系统电气回路。
稀油集中润滑系统组成
稀油集中润滑系统依据润滑元件布置形 式不同分两种
稀油集中润滑系统概述
3、强迫主机停止运行 当备用泵启动后,系统压力仍接着下
降低于工作压力0.12Mpa,则油泵停止并 发出信号,强迫主机停止运行,同时发出 报警跳停信号。 限制连锁由电接触点压力计;压力继 电器限制主机操作电气回路。
稀油集中润滑系统概述
4、高压信号 当系统压力超过正常工作压力一般为
集中润滑系统的原理及维护
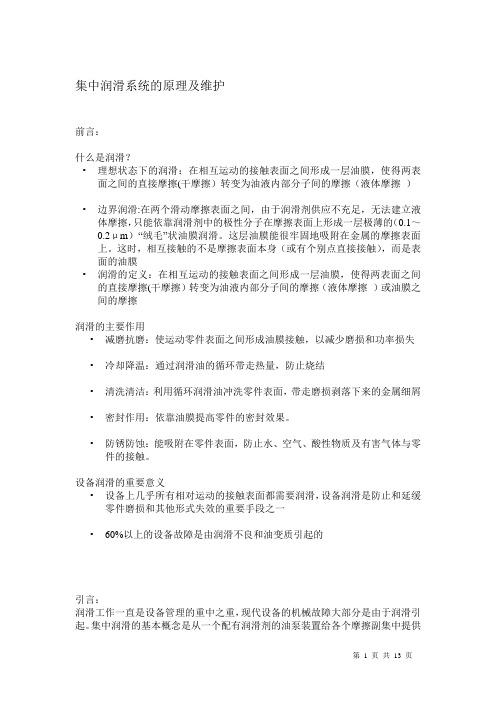
集中润滑系统的原理及维护前言:什么是润滑?•理想状态下的润滑:在相互运动的接触表面之间形成一层油膜,使得两表面之间的直接摩擦(干摩擦)转变为油液内部分子间的摩擦(液体摩擦)•边界润滑:在两个滑动摩擦表面之间,由于润滑剂供应不充足,无法建立液体摩擦,只能依靠润滑剂中的极性分子在摩擦表面上形成一层极薄的(0.1~0.2μm)“绒毛”状油膜润滑。
这层油膜能很牢固地吸附在金属的摩擦表面上。
这时,相互接触的不是摩擦表面本身(或有个别点直接接触),而是表面的油膜•润滑的定义:在相互运动的接触表面之间形成一层油膜,使得两表面之间的直接摩擦(干摩擦)转变为油液内部分子间的摩擦(液体摩擦)或油膜之间的摩擦润滑的主要作用•减磨抗磨:使运动零件表面之间形成油膜接触,以减少磨损和功率损失•冷却降温:通过润滑油的循环带走热量,防止烧结•清洗清洁:利用循环润滑油冲洗零件表面,带走磨损剥落下来的金属细屑•密封作用:依靠油膜提高零件的密封效果。
•防锈防蚀:能吸附在零件表面,防止水、空气、酸性物质及有害气体与零件的接触。
设备润滑的重要意义•设备上几乎所有相对运动的接触表面都需要润滑,设备润滑是防止和延缓零件磨损和其他形式失效的重要手段之一•60%以上的设备故障是由润滑不良和油变质引起的引言:润滑工作一直是设备管理的重中之重,现代设备的机械故障大部分是由于润滑引起。
集中润滑的基本概念是从一个配有润滑剂的油泵装置给各个摩擦副集中提供适量的润滑剂。
由于现代机械制造技术的高速发展,人工加油已不能满足各种机械的需要,越来越多的集中润滑系统被运用到机械设备中并在提高设备可靠性、降低润滑劳动强度、减少润滑油量消耗方面起到关键作用;集中润滑系统分类:集中润滑系统总体可分为全损耗型系统、循环系统;循环系统属于专用系统,要求高,润滑点少;全损耗系统涵盖了机床润滑点的绝大部分。
全损耗系统按供油方式分为单线阻尼系统、容积式系统、递进式润滑系统单线阻尼系统特点:• 1 节流式供油(利用流体阻力分配润滑剂)• 2 系统工作压力低(1bar 到10bar)• 3 结构简单、造价低• 4 油量误差较大• 5 润滑点数小于30点容积式润滑系统特点:• 1 定量式供油• 2 系统工作压力(15bar - 25bar)• 3 排油准确• 4 造价适中应用广泛•5润滑点数300点以下•6适用于中小型设备递进式润滑系统特点:•递进定量式供油•系统工作压力(10bar - 60 bar)•排油准确•造价较高安装复杂•一般用于大型设备润滑系统的组成•润滑泵- 提供定量清洁的润滑油。
一文看懂稀油集中润滑系统原理及组成,附故障处理方案
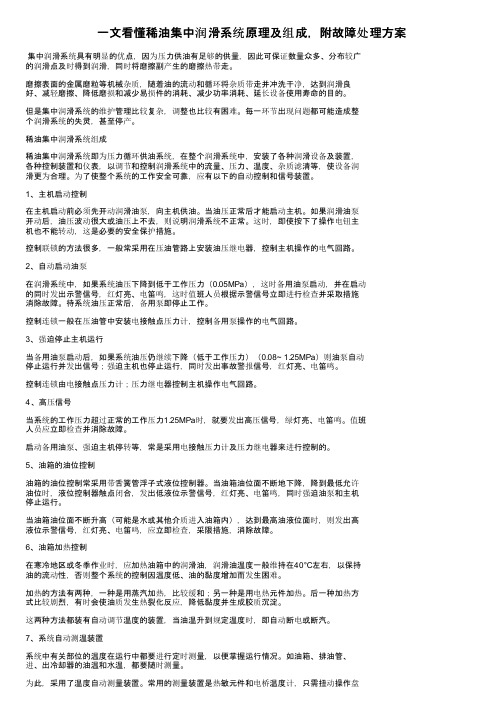
一文看懂稀油集中润滑系统原理及组成,附故障处理方案集中润滑系统具有明显的优点,因为压力供油有足够的供量,因此可保证数量众多、分布较广的润滑点及时得到润滑,同时将磨擦副产生的磨擦热带走。
磨擦表面的金属磨粒等机械杂质,随着油的流动和循环将杂质带走并冲洗干净,达到润滑良好、减轻磨擦、降低磨损和减少易损件的消耗、减少功率消耗、延长设备使用寿命的目的。
但是集中润滑系统的维护管理比较复杂,调整也比较有困难。
每一环节出现问题都可能造成整个润滑系统的失灵,甚至停产。
稀油集中润滑系统组成稀油集中润滑系统即为压力循环供油系统,在整个润滑系统中,安装了各种润滑设备及装置,各种控制装置和仪表,以调节和控制润滑系统中的流量、压力、温度、杂质滤清等,使设备润滑更为合理。
为了使整个系统的工作安全可靠,应有以下的自动控制和信号装置。
1、主机启动控制在主机启动前必须先开动润滑油泵,向主机供油。
当油压正常后才能启动主机。
如果润滑油泵开动后,油压波动很大或油压上不去,则说明润滑系统不正常。
这时,即使按下了操作电钮主机也不能转动,这是必要的安全保护措施。
控制联锁的方法很多,一般常采用在压油管路上安装油压继电器,控制主机操作的电气回路。
2、自动启动油泵在润滑系统中,如果系统油压下降到低于工作压力(0.05MPa),这时备用油泵启动,并在启动的同时发出示警信号,红灯亮、电笛鸣,这时值班人员根据示警信号立即进行检查并采取措施消除故障。
待系统油压正常后,备用泵即停止工作。
控制连锁一般在压油管中安装电接触点压力计,控制备用泵操作的电气回路。
3、强迫停止主机运行当备用油泵启动后,如果系统油压仍继续下降(低于工作压力)(0.08~ 1.25MPa)则油泵自动停止运行并发出信号;强迫主机也停止运行,同时发出事故警报信号,红灯亮、电笛鸣。
控制连锁由电接触点压力计;压力继电器控制主机操作电气回路。
4、高压信号当系统的工作压力超过正常的工作压力1.25MPa时,就要发出高压信号,绿灯亮、电笛鸣。
- 1、下载文档前请自行甄别文档内容的完整性,平台不提供额外的编辑、内容补充、找答案等附加服务。
- 2、"仅部分预览"的文档,不可在线预览部分如存在完整性等问题,可反馈申请退款(可完整预览的文档不适用该条件!)。
- 3、如文档侵犯您的权益,请联系客服反馈,我们会尽快为您处理(人工客服工作时间:9:00-18:30)。
集中润滑系统的原理及维护前言:什么是润滑?•理想状态下的润滑:在相互运动的接触表面之间形成一层油膜,使得两表面之间的直接摩擦(干摩擦)转变为油液内部分子间的摩擦(液体摩擦)•边界润滑:在两个滑动摩擦表面之间,由于润滑剂供应不充足,无法建立液体摩擦,只能依靠润滑剂中的极性分子在摩擦表面上形成一层极薄的(0.1~0.2μm)“绒毛”状油膜润滑。
这层油膜能很牢固地吸附在金属的摩擦表面上。
这时,相互接触的不是摩擦表面本身(或有个别点直接接触),而是表面的油膜•润滑的定义:在相互运动的接触表面之间形成一层油膜,使得两表面之间的直接摩擦(干摩擦)转变为油液内部分子间的摩擦(液体摩擦)或油膜之间的摩擦润滑的主要作用•减磨抗磨:使运动零件表面之间形成油膜接触,以减少磨损和功率损失•冷却降温:通过润滑油的循环带走热量,防止烧结•清洗清洁:利用循环润滑油冲洗零件表面,带走磨损剥落下来的金属细屑•密封作用:依靠油膜提高零件的密封效果。
•防锈防蚀:能吸附在零件表面,防止水、空气、酸性物质及有害气体与零件的接触。
设备润滑的重要意义•设备上几乎所有相对运动的接触表面都需要润滑,设备润滑是防止和延缓零件磨损和其他形式失效的重要手段之一•60%以上的设备故障是由润滑不良和油变质引起的引言:润滑工作一直是设备管理的重中之重,现代设备的机械故障大部分是由于润滑引起。
集中润滑的基本概念是从一个配有润滑剂的油泵装置给各个摩擦副集中提供适量的润滑剂。
由于现代机械制造技术的高速发展,人工加油已不能满足各种机械的需要,越来越多的集中润滑系统被运用到机械设备中并在提高设备可靠性、降低润滑劳动强度、减少润滑油量消耗方面起到关键作用;集中润滑系统分类:集中润滑系统总体可分为全损耗型系统、循环系统;循环系统属于专用系统,要求高,润滑点少;全损耗系统涵盖了机床润滑点的绝大部分。
全损耗系统按供油方式分为单线阻尼系统、容积式系统、递进式润滑系统单线阻尼系统特点:• 1 节流式供油(利用流体阻力分配润滑剂)• 2 系统工作压力低(1bar 到10bar)• 3 结构简单、造价低• 4 油量误差较大• 5 润滑点数小于30点容积式润滑系统特点:• 1 定量式供油• 2 系统工作压力(15bar - 25bar)• 3 排油准确• 4 造价适中应用广泛•5润滑点数300点以下•6适用于中小型设备递进式润滑系统特点:•递进定量式供油•系统工作压力(10bar - 60 bar)•排油准确•造价较高安装复杂•一般用于大型设备润滑系统的组成•润滑泵- 提供定量清洁的润滑油。
分为:手动、机动、电动、气动润滑泵;•油量分配器- 将润滑油定量或按比例分配到各个润滑点。
分为:计量件、定量注油件、递进式分配器•分配系统- 由管道接头、硬管或软管、分配接头等各种附件组成;按要求向润滑点输送润滑油•滤油器- 过滤杂质,保证提供清洁的油•电子程控器和压力开关、感应开关、液位开关等- 控制润滑泵按预定要求周期工作,具有对系统压力、液位进行监控和报警以及对系统工作状态进行显示等功能容积式润滑系统工作原理定量注油件工作原理系统加压润滑系统卸荷,补液回到原始状态参考上面示意图,定量注油件的工作步骤如下:1.润滑泵将压力油打入分配器底腔8,随着底腔8压力升高,润滑剂被压进进油腔7;压力继续升高,密封阀6的唇型密封变形,润滑剂流入分配器下腔5;密封阀6同时封住活塞4连接上腔3与下腔5的通道。
由于底腔8油压大于复位弹簧2的压力及系统背压,活塞4上升,强迫上腔3内的润滑剂通过出口1注入润滑点。
2.电气控制润滑泵停止,底腔8卸荷; 复位弹簧将活塞往下压,下腔5压力上升,迫使密封阀向下;由于密封阀的截面直径小于活塞的截面直径,密封阀6的返回速度大于活塞4,密封阀的运动导致活塞4通孔打开同时底腔8 关闭;随着活塞4继续下移,下腔的润滑剂通过活塞4的通道进入上腔。
3.完成了第二步的油液补充循环后,密封阀6关闭底腔8、下腔5、上腔3相互间的通道,分配器充满油液等待下一次润滑过程;容积式分配器剖视图容积系统泵源要求•工作压力15—25公斤•间歇供油,每次供油持续一段时间(管路保压时间)•供油结束系统卸荷•系统卸荷后低压保持典型电动润滑泵原理图工作过程:1.润滑泵打油——压力油打开液控换向阀——压力油进入主润滑管路——溢流阀限定系统最高压力;2.泵停止——液控换向阀在弹簧力作用下回位——主油路油液通过单向阀回油箱——单向阀弹簧保持主油路一定低压;容积式系统通常配备的电气开关及功能如下:•液位开关——油箱低液位报警•高压压力开关——系统达到设定值开关发信号;泵延时后停止;•低压压力开关——系统压力低于此开关设定值时报警;表明管路或单向阀有泄漏综上所述,容积式系统工作步骤如下:•油泵启动管路压力上升•压力油推动注油件活塞•分配器排出定量润滑油•分配器出油口封闭•所有分配器完成一次排油•油压达到高压开关设定压力•油泵继续工作电气设定的时间(5秒— 20秒)•多余油液通过溢流阀回油箱•油泵停止系统自动卸荷•管路油压达到系统设定低压•注油件活塞靠弹簧力返回•注油件上腔补充油液,等待下一润滑循环容积式系统故障诊断根据容积式系统工作原理,现场常见故障及可能原因总结如下:•现象:泵连续运转可能原因:管路、分配器或润滑油箱内部泄漏压力达不到高压开关设定值;高压开关故障,导致电气没有压力到达信号;•现象:润滑点不出油•可能原因:分配器堵塞;系统压力不够,不能推动分配器弹簧;泵源不卸压,分配器活塞不能复位,无法补充油液;•现象:润滑点连续油液流出可能原因:分配器密封件坏,有泄漏•现象:润滑站油量消耗急剧增大可能原因:管路或分配器有泄漏;高压开关或其它电气控制元件故障导致频繁打油递进式润滑系统工作原理MSP模块式分配器阀组(Lubriquip)•上图为MSP递进式分配器阀组,类似于液压叠加阀;每个工作阀片均有一个活塞,类似于液压阀的阀芯。
系统供油时,分配器中一系列活塞按一定的顺序做差动往复运动,各出油口按一定顺序依次出油;一旦某点堵塞,将引起整个系统堵塞。
1 工作阀块;2 阀块底板3首片 4 尾片5备用片分配器阀组工作原理位置1,1口出油位置2,2口出油位置3,3口出油位置4,4口出油位置5,5口出油位置6,6口出油图中,红色通道表示压力进油、蓝色通道表示润滑剂出口、浅红色为封闭的油路;压力油进油通道(红色)总是与所有分配器相通,但每次只有一个活塞能够移动,润滑按图1到图6顺序循环进行。
•如上图所示,各个工作片的柱塞副在紧跟着上一片循环之后,各自工作完成自己的柱塞行程,把定量的润滑剂输送到润滑点。
只要有压力油供给首片,分配器的工作片就以递进式方式连续循环运行。
递进式润滑泵源要求•工作压力10公斤— 60公斤•间歇或连续供油,管路系统不需保压•不需要卸荷装置•需要电气或机械高压保险装置。
•油液清洁度要求较容积式高递进式润滑系统连接见第二页系统连接示意图,泵的出油口只能接一组分配器,其它的必须在第一组的出油口连接,称为母-子-孙接法;由以上原理可知,分配器的任意出油口不能堵死使用,否则将引起递进循环中断,进而所有润滑中断。
常见递进式系统开关/报警器及其功能•电气循环指示器——监控润滑剂在系统中流动情况;异常报警•机械式堵塞指示器——系统压力超过额定值时,伸出指示杆以示报警。
故障排除后,需采用手动将压力报警器的指示杆复位。
•液位开关——油箱低液位时报警递进式系统工作步骤•油泵启动,压力油进入主分配器•压力油推动与之相通的某一活塞运动直至该活塞到终点•与此活塞对应出油口排出定量油,进入相应的子分配器•活塞位置变化导致另一阀块活塞压力油接通,此活塞开始运动到终点。
定量的油液排到相应子分配器进油管路•只要压力油存在,主分配器各个阀块活塞依次循环运动。
相应出油口依次排出定量油液,进入对应子分配器。
•各子分配器由主分配器排出的油驱动,各出油口循环定量排油。
•泵停止供油,各分配器活塞停在当前的位置。
•下一供油周期开始,泵打油,各活塞由上次停止的位置开始运动打油。
递进式系统故障诊断根据递进式系统工作原理,现场常见故障及可能原因总结如下:•现象:供油时系统无压力可能原因:主管路泄漏/ 膜片式保险破裂/ 泵源内泄漏,引起系统泄压•现象:系统压力偏高,但所有润滑点不出油可能原因:某点分配器或某出油口或某油路堵塞,导致整个系统堵塞;•现象某子分配器不出油,其它正常可能原因:该分配器对应支路/接头漏油,该分配器进油压力不足两种系统预防性维护检查步骤在现场的维修实践中,我总结了这两种系统的标准预防性维护检查步骤,指导维修工进行设备集中润滑系统周期性检查,在降低故障率,避免灾难性的润滑事故方面起到很好的作用。
容积式润滑系统标准检查步骤•启动润滑,检查润滑过程是否正常,主管路压力是否为20bar 左右•外观检查各分配器及润滑点接头有无漏油现象•检查各分配器工作是否正常• A 松开润滑部位前接头,擦干油液• B 启动润滑泵,检查接头处无油液滴出;确认后拧紧接头;• C 接头不滴油及连续滴油均为不正常;需清洗或更换分配器递进式润滑系统标准检查步骤•启动油泵,检查泵出口压力是否正常(10-60bar)•外观检查各分配器及润滑点接头有无漏油现象•首先处理漏油的阀块,接头;•检查各分配器是否功能正常• A 任选一末端润滑部位前接头,擦干油液•B启动润滑泵,检查接头处有无周期性油液滴出• C 如果有周期性油液冒出,表明整个系统无堵塞;• D 如果无油液滴出,表明系统堵塞,执行以下操作•松开润滑泵后第一级分配器所有出口接头,启动油泵,观察各出口有无出油;a.如果没有出油,拆下此分配器清洗,疏通或更换备件;b如果周期性出油,接上一个出口,按A,B步骤检查该出口下一级分配器;•依次接上主分配器出口,按上一步骤检查,直到找出堵点;两种润滑系统在DCEC西区的分布容积式润滑系统• B 缸体所有生产线线、B 缸盖所有机加线、C缸体YNC各生产线、C 缸体清洗机递进式润滑系统•EQX 各生产线、COUMA 线、B 缸盖清洗机。