汽车车轮弯曲疲劳试验机国内外研究现状综述
疲劳试验机调研报告

疲劳试验机调研报告疲劳试验机调研报告疲劳试验机是一种用于测试材料在重复或持续加载下的疲劳强度和寿命的设备。
目前,随着工业化进程的不断推进和新材料的开发,对疲劳试验机的需求逐渐增加。
为了解疲劳试验机的市场现状和发展趋势,我们进行了一次调研。
调研结果显示,疲劳试验机市场主要分为国内市场和国际市场两部分。
国内市场主要由几家大型试验机生产厂商垄断,产品种类齐全,价格相对较低。
而国际市场则受到一些国际大公司的控制,产品质量和技术水平较高。
由于国内市场需求日益增长,国内厂商正积极拓展国际市场。
在产品种类方面,疲劳试验机主要分为高周疲劳试验机和低周疲劳试验机两大类。
高周疲劳试验机适用于对金属材料进行疲劳试验,具有高频振动和较小振幅的特点;低周疲劳试验机适用于对复杂载荷下的材料进行疲劳试验,具有低频振动和较大振幅的特点。
随着新材料的出现和应用范围的扩大,对疲劳试验机的需求也不断增加。
在技术水平方面,目前疲劳试验机行业主要面临的问题是设备精度和自动化程度较低。
传统的疲劳试验机多采用液压控制系统,操作繁琐,精度不高。
而现代化的疲劳试验机则采用电子控制系统,操作简便,精度高。
但是,由于技术和成本等方面的限制,电子控制系统的普及程度较低。
随着科技的发展和需求的增加,疲劳试验机行业将加大对自动化技术的研发和应用。
综上所述,疲劳试验机市场前景广阔,但仍然存在一些问题需要解决。
为了提高产品质量和竞争力,厂商需要加大科技研发力度,推动疲劳试验机技术的创新和进步。
同时,政府应加大对疲劳试验机行业的政策支持和扶持力度,为行业的快速发展提供保障。
相信在各方的共同努力下,疲劳试验机行业将迎来更加美好的明天。
疲劳试验机的发展研究
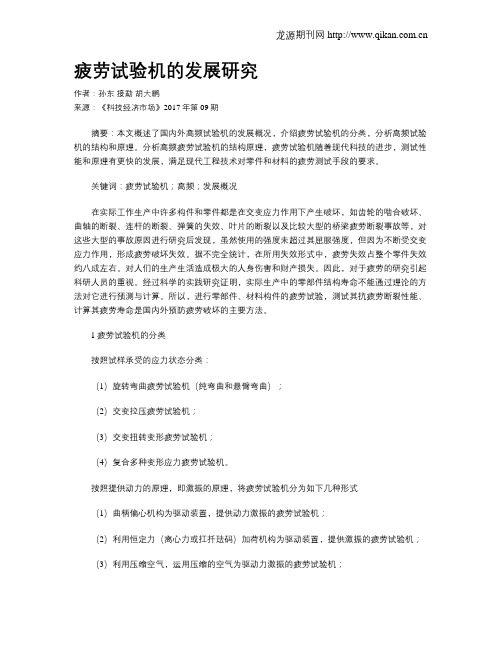
疲劳试验机的发展研究作者:孙东接勐胡大鹏来源:《科技经济市场》2017年第09期摘要:本文概述了国内外高频试验机的发展概况,介绍疲劳试验机的分类,分析高频试验机的结构和原理。
分析高频疲劳试验机的结构原理,疲劳试验机随着现代科技的进步,测试性能和原理有更快的发展,满足现代工程技术对零件和材料的疲劳测试手段的要求。
关键词:疲劳试验机;高频;发展概况在实际工作生产中许多构件和零件都是在交变应力作用下产生破坏,如齿轮的啮合破坏、曲轴的断裂、连杆的断裂、弹簧的失效、叶片的断裂以及比较大型的桥梁疲劳断裂事故等,对这些大型的事故原因进行研究后发现,虽然使用的强度未超过其屈服强度,但因为不断受交变应力作用,形成疲劳破坏失效。
据不完全统计,在所用失效形式中,疲劳失效占整个零件失效约八成左右。
对人们的生产生活造成极大的人身伤害和财产损失。
因此,对于疲劳的研究引起科研人员的重视。
经过科学的实践研究证明,实际生产中的零部件结构寿命不能通过理论的方法对它进行预测与计算。
所以,进行零部件、材料构件的疲劳试验,测试其抗疲劳断裂性能、计算其疲劳寿命是国内外预防疲劳破坏的主要方法。
1疲劳试验机的分类按照试样承受的应力状态分类:(1)旋转弯曲疲劳试验机(纯弯曲和悬臂弯曲);(2)交变拉压疲劳试验机;(3)交变扭转变形疲劳试验机;(4)复合多种变形应力疲劳试验机。
按照提供动力的原理,即激振的原理,将疲劳试验机分为如下几种形式(1)曲柄偏心机构为驱动装置,提供动力激振的疲劳试验机;(2)利用恒定力(离心力或扛扦珐码)加荷机构为驱动装置,提供激振的疲劳试验机;(3)利用压缩空气,运用压缩的空气为驱动力激振的疲劳试验机;(4)利用电磁、电动和磁致伸缩为驱动提供激振动力的疲劳试验机;(5)利用电气液压为驱动装置,为激振提供动力的疲劳试验机。
通过疲劳试验,求得测试件的S-N曲线,试验时间漫长。
特别是当试验机单位时间内的交变应力往复次数(即频率)较低时,试验周期更长。
汽车车轮弯曲疲劳试验机国内外研究现状综述

汽车车轮弯曲疲劳试验机国内外研究现状综述文章对汽车车轮弯曲疲劳试验机研究的国内外现状进行了综述,力求为汽车车轮弯曲疲劳试验机的研制提供技术参考。
标签:汽车车轮;弯曲疲劳试验机;现状1 汽车车轮弯曲疲劳试验机国内研究现状我国的汽车车轮弯曲疲劳试验机新设备开发起步较晚,直到20世纪70年代前后才刚刚开始。
长春天水红山试验机厂家开发出的液压伺服试验机和其他企业的相关领域的研究,才使中国的动态试验机研究水平是迈出了一大步。
近年来国内车轮弯曲疲劳试验机行业正在加快步伐,广泛采用计算机控制、电液伺服、高精度测力和测变形技术,研制出各种金属和非金属的疲劳试验仪器和工况动态力学试验设备,填补了国内的空白,部分设备还达到了国际先进水平;同时,也使我国的试验领域得到了进一步扩展。
但是与国际先进水平相比,我国的车轮弯曲疲劳试验机水平还相差较远,又由于相关领域如电液伺服阀、伺服液压缸、电子技术、计算机技术等领域相对比较薄弱,在一定程度上影响了我国车轮弯曲疲劳试验机行业的发展,部分产品和零件仍需进口。
因此,我国车轮弯曲疲劳试验机要赶超世界先进水平,实现全部产品和零件的国产化,仍是我国车轮弯曲疲劳试验机行业今后的奋斗目标和发展方向。
当今,主要有两种车轮弯曲疲劳试验方法:一种方法是让车轮进行旋转,而载荷固定不动,即车轮随着加载臂的旋转而旋转,在加载臂一端施加一个固定的弯矩,对车轮产生旋转弯矩。
把车轮与疲劳试验机的工作台固定在一起,用电机来驱动疲劳试验机的工作台及与其固定在一起的车轮进行旋转运动,在加载臂的一侧连接上车轮的轮毂,而在加载臂的另一侧则施加一个固定不变的力,用来实现对加载臂即车轮轮轴产生一个旋转弯矩的效果,以便真实反映汽车车轮在行驶过程中承受旋转弯矩的实际状况。
在模拟试验条件下,要求汽车车轮在经历了若干次循环载荷之后,不能产生由于疲劳所致的破坏。
另一种方法是让车轮静止不动,而载荷进行旋转,即车轮跟加载轴固定,在加载臂一端施加一个相当于旋转弯矩效果的离心力。
汽车轮胎试验研究现状与发展趋势
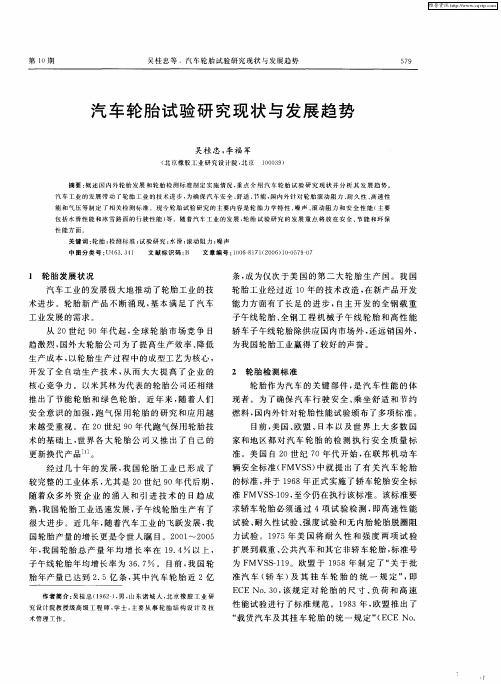
摘 要 : 述 国 内 外 轮 胎 发展 和轮 胎 检 测 标 准 制 定 实 施情 况 , 点介 绍 汽 车 轮 胎 试 验 研 究 现 状 并 分 析 其 发展 趋 势 。 概 重 汽车 工 业 的 发 展带 动 了 轮胎 工业 的技 术 进 步 , 确 保 汽 车 安 全 、 适 、 能 , 内 外 针 对 轮胎 滚 动 阻 力 、 久 性 、 速性 为 舒 节 国 耐 高 能 和 气 压 等 制 定 了 相 关检 测标 准 。现 今 轮 胎 试 验 研 究 的 主 要 内容 是 轮 胎 力学 特 性 、 声 、 动 阻 力 和 安 全 性 能 ( 要 噪 滚 主 包 括 水 滑 性 能 和 冰 雪 路 面 的 行驶 性 能 ) 。随 着 汽 车 工 业 的 发展 , 胎 试 验 研 究 的 发 展 重 点 将 放 在 安 全 、 能 和环 保 等 轮 节
扩展到 载重 、 公共 汽车 和其它 非轿 车轮 胎 , 准号 标
子 午线 轮胎年 均增 长率 为 3 . 。 目前 , 国轮 67 我 胎年产量 已达到 2 5亿 条 , 中汽 车 轮胎 近 2亿 . 其
作 者 简 介 : 桂 忠 ( 9 2) 男 , 吴 16 一 , 山东 诸 城 人 , 京 橡 胶 工 业 研 北
维普资讯
第 1 0期
吴 桂 忠 等 .汽 车 轮 胎 试 验 研 究 现 状 与 发 展 趋 势
汽 车 轮胎 试 验 研 究现 状 与发 展 趋 势
吴桂 忠 , 李福 军
( 京 橡 胶 工 业 研 究 设计 院 , 京 l0 3 ) 北 北 0 0 9
究设 计 院教 授 级 高 级 工 程 师 , 士 , 要 从 事 轮 胎 结 构 设 计 及 技 学 主
术 管理 工 作 。
疲劳试验机发展现状

疲劳试验机发展现状
近年来,疲劳试验机在工程材料、航空航天、机械制造等领域得到了广泛应用。
疲劳试验机的发展趋势主要体现在以下几个方面:
1. 多功能化:传统的疲劳试验机仅能进行单一的疲劳试验,而现代疲劳试验机通过改进设计和增加功能,可以同时进行多种疲劳试验,如拉伸、压缩、弯曲、扭转等。
这种多功能化设计大大提高了试验机的实用性和效率。
2. 自动化控制:随着自动化技术的快速发展,自动化控制在疲劳试验机中得到广泛应用。
通过采用电动伺服控制系统和先进的传感器,对试验过程进行精确的控制。
自动化控制不仅提高了疲劳试验的可靠性和准确性,还减少了人为因素对试验结果的影响。
3. 多参数监测:疲劳试验机不仅可以对材料的疲劳性能进行评估,还可以对其它相关参数进行监测,如载荷、位移、应变等。
这些参数的监测可以提供全面的试验数据,为进一步分析和研究提供基础。
4. 高频疲劳试验:传统的疲劳试验机主要用于低频疲劳试验,而随着科技的进步,对于高频疲劳试验的需求也日益增加。
现代疲劳试验机通过结构优化和先进的控制算法,可以进行更高频率的疲劳试验,满足复杂材料的需求。
5. 多轴联动试验:在一些特殊领域,如航空航天和汽车工程中,
材料同时受到多个方向的载荷作用。
因此,多轴联动试验成为了疲劳试验机发展的新方向。
通过多个试验机的联动控制,可以模拟出真实工况下的复杂载荷情况,提高试验的可靠性和真实性。
总的来说,疲劳试验机的发展不仅体现在试验机的功能和控制方式上,还涉及到试验范围的拓展和试验数据的全面性。
随着科技的不断进步,预计疲劳试验机的发展还会继续推动工程材料和相关领域的进步和创新。
汽车专业毕业论文国内外速度检测设备的发展现状与研究
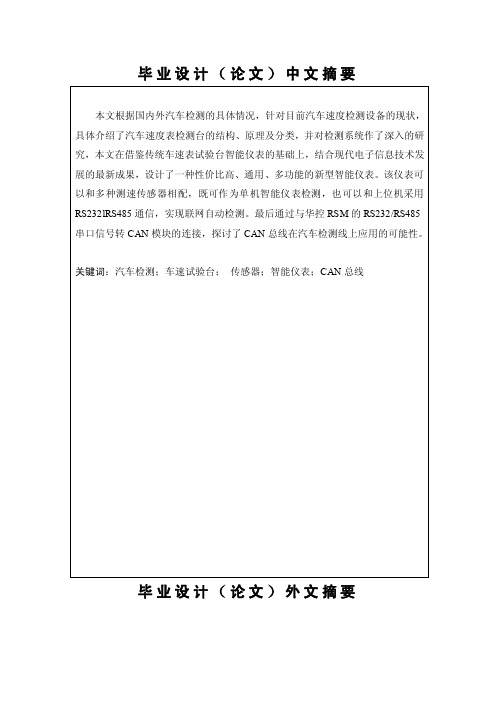
毕业设计(论文)中文摘要毕业设计(论文)外文摘要目录1 绪论 (5)1.1 汽车性能检测的意义 (5)1.2 国外汽车性能检测的发展状况 (5)1.3 国内汽车性能检测的发展状况 (6)2 车速表试验台的结构及工作原理 (8)2.1 车速表试验台的结构 (8)2.1.1 标准型车速表试验台 (9)2.1.2 驱动型车速表试验台 (9)2.1.3 车速表试验台的检测方法和工作过程 (10)2.2 传感器和步进电机的工作原理 (10)2.2.1 磁电式传感器 (10)2.2.2 光电式传感器 (11)2.2.3 步进电机 (11)2.2.4 车速测量的方法 (12)2.2.5 车速台智能仪表的主要功能及技术参数 (12)3 智能仪表的硬件与软件系统设计 (13)3.1 硬件系统设计 (13)3.1.1 单片机系统 (14)3.1.2 LED动态扫描显示电路 (14)3.1.3 信号调理电路 (15)3.1.4 电源模块 (16)3.2 操作面板及接线端子示意图 (16)3.3 软件系统设计 (17)3.3.1 系统主程序 (18)3.3.2 中断服务程序 (18)3.3.3 系统的菜单实现 (19)3.3.4 智能仪表功能分析 (21)4 智能仪表的CAN总线设计 (21)4.1 华控RSM智能模块的系统组成及工作方式 (22)4.2 智能仪表与RSM模块接口 (23)4.2.1 RSM-20智能模块及其组态 (23)4.2.2 系统软件设计 (24)结论 (25)致谢 (26)参考文献 (27)1 绪论随着现代汽车工业的飞速发展和人民生活水平的不断提高,汽车已成为人们工作、生活中不可缺少的一种交通工具。
汽车在为人们造福的同时,也带来了大气污染、噪声和交通安全等一系列问题。
因此,我们一方面要不断研制性能优良的汽车;另一方面也要不断的发展我国汽车检测事业。
只有开发研制多功能、智能化的检测设备,才能促进我国汽车行业的迅猛发展。
基于Wohler_曲线的车轮弯曲疲劳试验机关联性研究

Mechanical Engineering and Technology 机械工程与技术, 2023, 12(4), 325-335 Published Online August 2023 in Hans. https:///journal/met https:///10.12677/met.2023.124037基于Wohler 曲线的车轮弯曲疲劳试验机关联性研究魏晓辰,王乔穆,张志鹏,杨清淞中汽研汽车检验中心(天津)有限公司,天津收稿日期:2023年5月22日;录用日期:2023年7月28日;发布日期:2023年8月4日摘 要因为两台不同生产厂家的汽车车轮弯曲试验机的控制系统和设备结构不同,即使设备的力传感器和转速传感器都校正一致,那么输出到车轮的弯矩值也会产生差异,从而对试验结果造成影响,这是车轮行业普遍存在的现象。
那么为了验证两台不同生产厂家的汽车车轮弯曲试验机之间的差异到底有多大,并且找到设备之间的关联性尤为重要。
首先在两台设备上分别测试10件车轮,通过设置相同的停机条件,得到两台设备停机时车轮的循环次数和裂纹位置,从而得出两台设备车轮循环次数的差异大小。
然后使用同一批次的新车轮在裂纹容易产生的位置贴应变片,用同一个应变轮分别在两台设备上采集应变数据,从而得到两台设备之间的应变差异大小。
最后引入伪损伤理论,基于雨流循环计数的概念,使用nCode 软件计算出两台动态弯曲疲劳试验机的累积损伤结果,得到两台设备贴片位置的累积损伤差异大小,两台设备之间累积损伤的差异验证了车轮循环次数差异大小的准确性,并通过Wohler 曲线公式推导出两台设备之间的关联转化关系。
关键词车轮试验,设备比对,动态弯曲疲劳,伪损伤,Wohler 曲线Research on Correlation of Wheel Bending Fatigue Testing Machine Based on Wohler CurveXiaochen Wei, Qiaomu Wang, Zhipeng Zhang, Qingsong YangChina Automotive Research Center (Tianjin) Co., Ltd., TianjinReceived: May 22nd , 2023; accepted: Jul. 28th , 2023; published: Aug. 4th, 2023魏晓辰 等AbstractBecause the control systems and equipment structures of two automobile wheel bending testing machines from different manufacturers are different, even if the force sensors and speed sensors of the equipment are calibrated consistently, the bending moment values output to the wheels will be different, thus affecting the test results, which is a common phenomenon in the wheel industry. So in order to verify the difference between two automobile wheel bending testing machines from different manufacturers, it is particularly important to find the correlation between the equip-ment. Firstly, 10 wheels were tested on two equipments, and the cycle times and crack positions of the wheels when the two equipments stopped were obtained by setting the same shutdown condi-tions, thus the difference of the cycle times between the two equipments was obtained. Then, strain gauges are attached to the crack-prone positions with new wheels of the same batch, and strain data are collected on two devices with the same strain wheel, so as to obtain the strain dif-ference between the two devices. At last, based on the concept of rain flow cycle counting, the cu-mulative damage results of two dynamic bending fatigue testing machines were calculated by us-ing nCode software, and the cumulative damage difference between the two devices was obtained. The cumulative damage difference between the two devices verified the accuracy of the difference in wheel cycle times, and the relationship between the two devices was deduced by Wohler curve formula.KeywordsWheel Test, Equipment Comparison, Dynamic Bending Fatigue, Pseudo Damage, Wohler CurveCopyright © 2023 by author(s) and Hans Publishers Inc.This work is licensed under the Creative Commons Attribution International License (CC BY 4.0). /licenses/by/4.0/1. 引言车轮是汽车的重要零部件,承受着汽车行驶过程中的各种力和力矩,起着承载、转向、驱动、制动等作用,因此车轮直接影响汽车的安全性和可靠性[1]。
钢制车轮弯曲试验多轴疲劳寿命预测研究
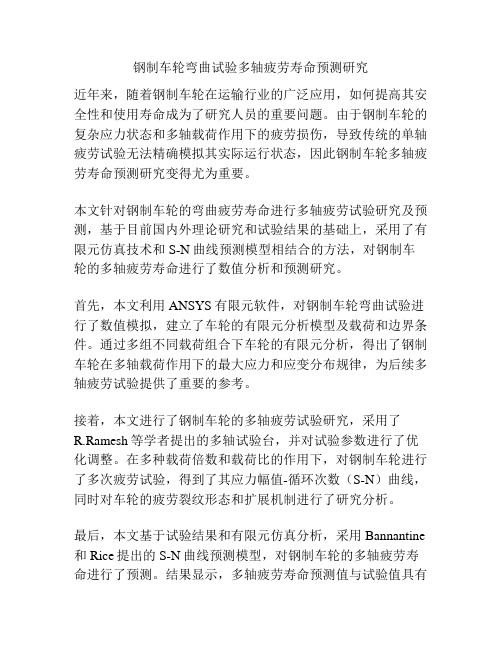
钢制车轮弯曲试验多轴疲劳寿命预测研究近年来,随着钢制车轮在运输行业的广泛应用,如何提高其安全性和使用寿命成为了研究人员的重要问题。
由于钢制车轮的复杂应力状态和多轴载荷作用下的疲劳损伤,导致传统的单轴疲劳试验无法精确模拟其实际运行状态,因此钢制车轮多轴疲劳寿命预测研究变得尤为重要。
本文针对钢制车轮的弯曲疲劳寿命进行多轴疲劳试验研究及预测,基于目前国内外理论研究和试验结果的基础上,采用了有限元仿真技术和S-N曲线预测模型相结合的方法,对钢制车轮的多轴疲劳寿命进行了数值分析和预测研究。
首先,本文利用ANSYS有限元软件,对钢制车轮弯曲试验进行了数值模拟,建立了车轮的有限元分析模型及载荷和边界条件。
通过多组不同载荷组合下车轮的有限元分析,得出了钢制车轮在多轴载荷作用下的最大应力和应变分布规律,为后续多轴疲劳试验提供了重要的参考。
接着,本文进行了钢制车轮的多轴疲劳试验研究,采用了R.Ramesh等学者提出的多轴试验台,并对试验参数进行了优化调整。
在多种载荷倍数和载荷比的作用下,对钢制车轮进行了多次疲劳试验,得到了其应力幅值-循环次数(S-N)曲线,同时对车轮的疲劳裂纹形态和扩展机制进行了研究分析。
最后,本文基于试验结果和有限元仿真分析,采用Bannantine 和Rice提出的S-N曲线预测模型,对钢制车轮的多轴疲劳寿命进行了预测。
结果显示,多轴疲劳寿命预测值与试验值具有较高的一致性和准确性,能够为钢制车轮的材料选择和设计提供重要的参考依据。
总之,本文对钢制车轮弯曲试验多轴疲劳寿命预测研究进行了深入分析和探讨,通过有限元仿真和多轴试验研究相结合的方法,可以更加精确地预测钢制车轮的多轴疲劳寿命,为运输行业的安全和可靠性提供了保障。
钢制车轮作为运输行业的重要组成部分,在使用过程中会遇到复杂的多轴载荷作用,常常出现疲劳裂纹和损伤,严重影响车辆的稳定性和安全性。
传统的单轴疲劳试验往往无法精确模拟实际的复杂应力状态和多轴载荷作用,因此多轴疲劳试验和寿命预测成为了钢制车轮疲劳研究的重要内容。
2023年弯曲机行业市场分析现状

2023年弯曲机行业市场分析现状弯曲机是一种用于金属材料弯曲的机械设备。
它广泛应用于金属加工、建筑、汽车制造等行业。
市场需求的增加和技术的进步推动了弯曲机行业的发展。
本文将对弯曲机行业的市场分析进行现状的探讨。
弯曲机行业市场的规模不断扩大。
随着全球经济的快速发展和产业结构的升级换代,对弯曲机设备的需求不断增长。
尤其是在建筑和汽车制造领域,弯曲机的应用越来越广泛。
根据市场研究报告,全球弯曲机市场规模在过去几年中增长迅速,预计未来几年仍将保持稳定增长。
弯曲机行业市场竞争激烈。
随着需求的增加,越来越多的公司进入到这个行业中,市场竞争激烈。
大型制造商和小型企业都在争夺市场份额,并通过不断创新提高产品质量和技术水平来吸引客户。
同时,国内外企业的竞争也在增加,国际品牌和本地制造商之间的竞争加剧。
弯曲机行业市场的技术进步推动了产品升级。
随着科技的不断进步,弯曲机的技术也在不断改进。
新型材料、数字化控制系统和自动化技术的应用,使得弯曲机的精度和效率得到了显著提高。
同时,随着用户需求的变化,弯曲机的功能也在不断扩展,比如多轴控制、自动化生产线等。
弯曲机行业市场的发展面临一些挑战。
首先,市场价格竞争激烈,利润空间较小。
其次,技术研发和创新需要投入大量成本和人力资源,对企业来说是一项巨大的挑战。
此外,市场需求的波动也会对行业带来一定的不确定性。
为了应对这些挑战,弯曲机行业需要继续加强产品创新和研发投入,提高产品质量和技术水平。
同时,通过产品差异化和市场定位来拓展市场份额,并加强与用户的合作和沟通,了解并满足用户需求。
此外,加强行业协会和研究机构的合作,加强行业标准的制定和推广,也是行业发展的重要途径。
总结来说,弯曲机行业市场规模不断扩大,竞争激烈,技术不断进步,同时也面临一些挑战。
随着需求的增加和技术的进步,弯曲机行业有望在未来继续保持稳定增长。
汽车车轮弯曲疲劳试验机的研究与开发
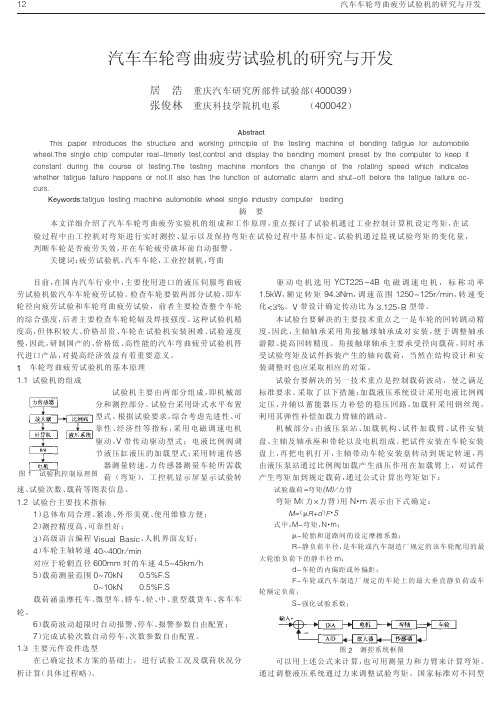
汽车车轮弯曲疲劳试验机的研究与开发居浩重庆汽车研究所部件试验部(400039)张俊林重庆科技学院机电系(400042)目前,在国内汽车行业中,主要使用进口的液压伺服弯曲疲劳试验机做汽车车轮疲劳试验。
检查车轮要做两部分试验,即车轮径向疲劳试验和车轮弯曲疲劳试验,前者主要检查整个车轮的综合强度,后者主要检查车轮轮辐及焊接强度。
这种试验机精度高,但体积较大、价格昂贵、车轮在试验机安装困难、试验速度慢,因此,研制国产的、价格低、高性能的汽车弯曲疲劳试验机替代进口产品,对提高经济效益有着重要意义。
1车轮弯曲疲劳试验机的基本原理1.1试验机的组成试验机主要由两部分组成,即机械部分和测控部分。
试验台采用卧式水平布置型式。
根据试验要求,综合考虑先进性、可靠性、经济性等指标,采用电磁调速电机驱动,V 带传动驱动型式;电液比例阀调节液压缸液压的加载型式;采用转速传感器测量转速,力传感器测量车轮所需载荷(弯矩),工控机显示屏显示试验转速、试验次数、载荷等图表信息。
1.2试验台主要技术指标1)总体布局合理、紧凑、外形美观、使用维修方便;2)测控精度高、可靠性好;3)高级语言编程Visual Basic 、人机界面友好;4)车轮主轴转速40~400r /min 对应于轮辋直径600mm 时的车速4.5~45km /h 5)载荷测量范围0~70kN 0.5%F.S0~10kN 0.5%F.S载荷涵盖摩托车、微型车、轿车、轻、中、重型载货车、客车车轮。
6)载荷波动超限时自动报警、停车、报警参数自由配置;7)完成试验次数自动停车,次数参数自由配置。
1.3主要元件设件选型在已确定技术方案的基础上,进行试验工况及载荷状况分析计算(具体过程略)。
驱动电机选用YCT225-4B 电磁调速电机,标称功率1.5kW ,额定转矩94.3Nm ,调速范围1250~125r /min ,转速变化<3%。
V 带设计确定传动比为3.125,B 型带。
轮辋动态弯曲疲劳试验国际先进的数据指标

轮辋动态弯曲疲劳试验国际先进的数据指标轮辋动态弯曲疲劳试验国际先进的数据指标1.引言轮辋是列车行驶的关键部件,其安全性和可靠性直接关系到列车的运行安全。
在轮辋的设计和制造过程中,动态弯曲疲劳试验是不可或缺的一环,它能够评估轮辋在列车运行过程中承受动态负荷的能力,为轮辋的设计和制造提供重要的参考依据。
而国际先进的数据指标对于轮辋动态弯曲疲劳试验具有重要的指导意义,本文将全面评估轮辋动态弯曲疲劳试验国际先进的数据指标,并且针对其意义进行深入探讨。
2.轮辋动态弯曲疲劳试验的重要性轮辋作为列车的重要部件,承受着巨大的动态负荷,因此其动态弯曲疲劳特性成为了制约其安全可靠性的关键。
而动态弯曲疲劳试验正是以模拟列车实际运行过程中的动态载荷作用下的状态,来评估轮辋的疲劳特性和寿命,因此具有不可替代的重要性。
3.国际先进的数据指标在轮辋动态弯曲疲劳试验中,国际先进的数据指标是评估轮辋性能的重要依据。
这些数据指标主要包括疲劳极限、应力幅值、载荷频率、载荷比等。
其中,疲劳极限是指在特定载荷下轮辋能够承受的最大循环次数,是评估轮辋疲劳寿命的重要参数;应力幅值则是表示轮辋在动态载荷作用下的实际应力范围,直接影响着轮辋的疲劳破坏;载荷频率和载荷比则是评估轮辋受载荷循环变化情况的重要参数。
4.国际先进的数据指标意义的深入探讨国际先进的数据指标对于轮辋动态弯曲疲劳试验具有重要的指导意义,其重要性主要体现在以下几个方面:这些数据指标能够全面、客观地评估轮辋的实际工作状态和疲劳特性,为轮辋的设计和制造提供重要的参考依据;国际先进的数据指标能够对轮辋的寿命进行准确评估,有助于延长轮辋的使用寿命和提高其可靠性;这些数据指标还能够为轮辋的性能改进和优化提供重要依据,有助于提高轮辋的安全性和稳定性。
5.个人观点和理解在我看来,国际先进的数据指标对于轮辋动态弯曲疲劳试验具有非常重要的意义。
它不仅可以全面客观地评估轮辋的疲劳特性,为轮辋的设计和制造提供重要依据,同时还能够对轮辋的寿命进行准确评估,为轮辋的使用和维护提供重要参考,有助于延长轮辋的使用寿命和提高其可靠性。
轮机材料疲劳性能的实验与分析与研究

轮机材料疲劳性能的实验与分析与研究在现代航运业中,轮机作为船舶的核心动力系统,其可靠性和安全性至关重要。
而轮机材料的疲劳性能则是影响轮机长期稳定运行的关键因素之一。
为了深入了解轮机材料的疲劳特性,提高轮机的使用寿命和可靠性,进行相关的实验、分析与研究具有重要的现实意义。
一、轮机材料疲劳性能的重要性轮机在运行过程中,其零部件会不断承受循环载荷的作用。
长时间的循环载荷可能导致材料内部出现微小裂纹,并逐渐扩展,最终引发零部件的失效。
这种由于疲劳导致的失效往往具有突发性,难以提前预测,一旦发生可能会造成严重的后果,如船舶失去动力、发生事故等。
因此,了解轮机材料的疲劳性能,对于保障船舶的安全航行和降低运营成本具有极其重要的意义。
二、实验方法与设备为了准确评估轮机材料的疲劳性能,需要采用一系列科学的实验方法和先进的实验设备。
(一)疲劳实验方法常见的疲劳实验方法包括旋转弯曲疲劳实验、拉压疲劳实验和扭转疲劳实验等。
其中,旋转弯曲疲劳实验因其简单易行且能够较好地模拟实际工况,被广泛应用于轮机材料的疲劳性能研究。
(二)实验设备实验通常在专门的疲劳试验机上进行。
这些试验机能够精确控制加载的应力幅、频率和循环次数等参数,并实时监测试样的应变和位移等数据。
三、实验过程与结果(一)试样制备首先,需要根据相关标准制备疲劳试样。
试样的形状、尺寸和表面质量都会对实验结果产生影响。
通常,试样会被加工成圆柱形或矩形,表面经过精细的打磨和抛光处理,以减少表面缺陷对实验结果的干扰。
(二)加载条件设置根据实际工况和研究目的,确定加载的应力幅、平均应力、频率和环境温度等参数。
不同的加载条件会导致材料表现出不同的疲劳性能。
(三)实验结果在实验过程中,通过试验机记录试样的疲劳寿命(即试样在特定加载条件下发生断裂所经历的循环次数)。
同时,还可以观察试样断口的形貌特征,分析裂纹的起始位置、扩展路径和断裂方式等。
四、实验结果分析(一)疲劳寿命曲线通过对大量实验数据的整理和分析,可以绘制出材料的疲劳寿命曲线(SN 曲线)。
轿车轮毂疲劳寿命试验研究

轿车轮毂疲劳寿命试验研究申富强;石胜文【摘要】轮毂影响着车辆的形式,是其重要的组成部分。
轮毂的疲劳寿命与汽车的安全质量有着千丝万缕的关系,其担负着汽车的重量,又与外形息息相关。
轮毂对其性能和外形要求较高,进行制作的过程难度很大。
现在的汽车在很多方面追求高速行驶,时速在不断提高,高速行驶的汽车最容易发生损坏的是轮毂,高速行驶中的轮毂疲劳破坏不仅对轿车本身有严重的影响,更影响着驾乘者安全。
【期刊名称】《企业技术开发:下旬刊》【年(卷),期】2016(035)006【总页数】2页(P56-57)【关键词】轿车轮;疲劳寿命;试验【作者】申富强;石胜文【作者单位】东风柳州汽车有限公司,广西柳州545005【正文语种】中文【中图分类】TH133.33汽车轮毂长时间行驶之后会产生疲劳状态,并且在行驶中所发生的碰撞,都让其成为工程设计人员在进行设计时候所需要考虑的重要因素。
疲劳寿命是衡量轮毂质量的一个非常重要的汽车使用的频率,以及人们对汽车的要求都让其寿命试验成为非常重要的产品检验途径。
疲劳试验的过程需要耗费的人力、物力较为严重,并且需要占用很长的时间,对于一些复杂实验则还需要增加相应的支出,并且该实验目前尚无法在试验机上实现。
当前阶段,在轮毂实验方面所使用的方法主要包括以下几种,即:有限元法、边界元法、离散单元法和有限差分法。
有限元法相对于实际情况来说,应用较为广泛。
可以说,有限元法的试验已经开始呈现出越来越广泛的取代之势,其代替了大量的实物试验,具有“虚拟实验”的代表性。
并且,依据相关资料显示,一个产品的应用只有在设计阶段进行有效实验,大部分问题都可以予以解决。
因此,通过大量的数据统计,计算方法的应用,以及典型的验证性,能够让试验的成本呈现出下降的趋势,并提高其相应的试验效率。
轮毂的台架试验主要包括疲劳强度的测试(弯曲疲劳和径向疲劳试验)和冲击强度的测试(冲击试验)。
轮毂是汽车的重要组成部分,其对于企业的安全驾驶,平稳形式,以及相关的牵引作用都具有重要影响,与能源消耗,驾驶员的劳动强度等等方面关系密切。
轮胎疲劳测试器细分市场深度研究报告
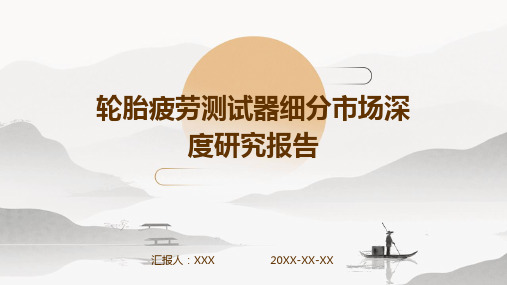
轮胎疲劳测试器市场面临技术更新换代、市场竞 争加剧等问题。
研究目的
1
分析轮胎疲劳测试器市场的现状和未来发展趋势 。
2
探讨轮胎疲劳测试器细分市场的需求和竞争格局 。
3
提出针对不同细分市场的营销策略和产品优化建 议。
02
轮胎疲劳测试器市场概述
客户需求多样化
不同客户对轮胎疲劳测试器的性能、功能和价格有不同的需求,因此 ,提供多样化、定制化的产品和服务是市场发展的重要趋势。
对企业的建议
加强技术创新
企业应加大研发投入,不断推动轮胎疲劳测试技 术的创新,提高产品的智能化、高精度、高效率 水平,以满足市场的不断变化和客户的需求。
提高服务质量
企业应重视客户的需求和反馈,不断提高服务质 量,提供专业、高效的售前、售中和售后服务, 提升客户满意度和忠诚度。
市场挑战与限制
高成本
尽管轮胎疲劳测试器的技术不断进步,但其制造成本仍然较高,限 制了市场的进一步拓展。
技术壁垒
由于涉及复杂的机械和电子技术,轮胎疲劳测试器的研发和生产存 在较高的技术壁垒,对新进入者构成了挑战。
标准不一
由于缺乏统一的国际标准,不同地区和国家对轮胎疲劳测试器的性 能要求存在差异,增加了市场的不确定性。
增长趋势
随着汽车工业的发展和消费者对轮胎 性能要求的提高,轮胎疲劳测试器的 需求将进一步增加。同时,新技术和 新材料的出现也将推动轮胎疲劳测试 器市场的创新和发展。
主要参与者分析
国际知名品牌
包括德国的HBM、美国的MTS和 意大利的CEIA等,这些企业在轮 胎疲劳测试器领域拥有较高的知 名度和市场份额。
- 1、下载文档前请自行甄别文档内容的完整性,平台不提供额外的编辑、内容补充、找答案等附加服务。
- 2、"仅部分预览"的文档,不可在线预览部分如存在完整性等问题,可反馈申请退款(可完整预览的文档不适用该条件!)。
- 3、如文档侵犯您的权益,请联系客服反馈,我们会尽快为您处理(人工客服工作时间:9:00-18:30)。
汽车车轮弯曲疲劳试验机国内外研究现状综述
作者:徐恒斌顾佳超孟凡荣
来源:《科技创新与应用》2014年第34期
摘要:文章对汽车车轮弯曲疲劳试验机研究的国内外现状进行了综述,力求为汽车车轮弯曲疲劳试验机的研制提供技术参考。
关键词:汽车车轮;弯曲疲劳试验机;现状
1 汽车车轮弯曲疲劳试验机国内研究现状
我国的汽车车轮弯曲疲劳试验机新设备开发起步较晚,直到20世纪70年代前后才刚刚开始。
长春天水红山试验机厂家开发出的液压伺服试验机和其他企业的相关领域的研究,才使中国的动态试验机研究水平是迈出了一大步。
近年来国内车轮弯曲疲劳试验机行业正在加快步伐,广泛采用计算机控制、电液伺服、高精度测力和测变形技术,研制出各种金属和非金属的疲劳试验仪器和工况动态力学试验设备,填补了国内的空白,部分设备还达到了国际先进水平;同时,也使我国的试验领域得到了进一步扩展。
但是与国际先进水平相比,我国的车轮弯曲疲劳试验机水平还相差较远,又由于相关领域如电液伺服阀、伺服液压缸、电子技术、计算机技术等领域相对比较薄弱,在一定程度上影响了我国车轮弯曲疲劳试验机行业的发展,部分产品和零件仍需进口。
因此,我国车轮弯曲疲劳试验机要赶超世界先进水平,实现全部产品和零件的国产化,仍是我国车轮弯曲疲劳试验机行业今后的奋斗目标和发展方向。
当今,主要有两种车轮弯曲疲劳试验方法:
一种方法是让车轮进行旋转,而载荷固定不动,即车轮随着加载臂的旋转而旋转,在加载臂一端施加一个固定的弯矩,对车轮产生旋转弯矩。
把车轮与疲劳试验机的工作台固定在一起,用电机来驱动疲劳试验机的工作台及与其固定在一起的车轮进行旋转运动,在加载臂的一侧连接上车轮的轮毂,而在加载臂的另一侧则施加一个固定不变的力,用来实现对加载臂即车轮轮轴产生一个旋转弯矩的效果,以便真实反映汽车车轮在行驶过程中承受旋转弯矩的实际状况。
在模拟试验条件下,要求汽车车轮在经历了若干次循环载荷之后,不能产生由于疲劳所致的破坏。
另一种方法是让车轮静止不动,而载荷进行旋转,即车轮跟加载轴固定,在加载臂一端施加一个相当于旋转弯矩效果的离心力。
把车轮与疲劳试验机的工作台台面进行绑定,与第一种方法一样,在加载臂的一侧连接上车轮的轮毂。
与第一种方法不一样的是,在加载臂的另一侧则装载一个不平衡的质量块,通过电机带动装载的不平衡质量块进行转动,用来产生一个离心力,进而实现对加载臂即车轮轮轴产生一个旋转弯矩作用在汽车的车轮上。
随着国内汽车工业水平的不断发展,国内涌现出了一大批汽车车轮弯曲疲劳试验机生产厂家,其中最具代表性的是天津久荣车轮有限公司研制的用于轿车车轮弯曲疲劳性能试验的CFT-2型和CFT-3型车轮弯曲疲劳试验机,其中CFT-2型车轮弯曲疲劳试验机采用的是让车轮进行旋转,而载荷固定不动的试验方式。
CFT-3型车轮弯曲疲劳试验机采用的是让车轮固定不动,而载荷进行旋转的试验方式。
除了天津久荣车轮有限公司,国内还有其他一些资质雄厚的车轮弯曲疲劳试验机的生产厂家研究的车轮弯曲疲劳试验机,例如,东风汽车有限公司研究的采用让车轮进行旋转,而载荷固定不动的试验方式的RF30K型车轮弯曲疲劳试验机。
2 汽车车轮弯曲疲劳试验机国外研究现状
要对车轮进行弯曲疲劳研究,汽车车轮弯曲疲劳试验机是不可或缺的弯曲疲劳研究工具。
从最早的模拟轴旋转弯曲疲劳试验机开始至今,车轮弯曲疲劳试验机已有超过一个世纪的历史。
汽车车轮弯曲疲劳试验机是一种技术密集型的测试设备,现已涉及机械,液压,电气,材料,测量,自动控制,数字显示等众多技术领域,其相关技术被广泛应用在机械,造船,航空航天等许多工业部门。
目前国内许多大型和弯曲疲劳试验机都可进行低周疲劳试验,这些设备一般采用静态测试微电子伺服术,通过改变电机的运行参数可自动完成进行必要的测试。
测试结果和测试数据可实现自动采集,处理,显示和打印记录,大大降低了试验人员的劳动强度,提高测试效率。
由于试验机具有闭环伺服机电控制系统,又因它的负载范围广,因此能够成完低频往复拉伸和压缩循环试验。
另一种是动态疲劳试验机,它是由机械,液压和电子系统三者组合而成的新型伺服机构。
电液伺服疲劳试验机变开环控制为闭环控制,与此同时也大大的提高了测试动态精度。
电液伺服疲劳试验机除了可采用正弦波载荷外,还可以也施加方波,三角波,锯齿波,梯形波等载荷谱。
因此,试验结果更逼近于实际的工作状态,可为最佳优化设计提供更可靠的依据。
任何一个大型现代化的项目都必须经过动态力学测试,否则就不能保证其设计的安全性。
目前,随着科学技术的进步和现实需求,电液伺服疲劳试验机正朝着全微机化、智能化,节能化的方向发展,进一步提高了电液伺服疲劳试验机的测试效率,改善了准确度,并且降低了电液伺服液压伺服疲劳试验机以及疲劳试验机[2-3]的能量消耗。
从上个世纪80年代末到现在,汽车车轮弯曲疲劳试验机行业的规模,品种,先进程度取得长足发展,美国,德国,日本等国家的相关技术在这一领域处于领先水平。
比较知名的厂家有:美国MTS公司,公司奥尔森(OLSEN),总部设在美国英斯特朗(INSTRON)公司;德国MFL公司申克(SCHENCK)公司,沃尔玛伯特(WOLPERT)公司和茨维柯(ZWICK)公司;日本的岛津公司,东京衡机公司,东洋精机公司和松泽公司等等。
目前,随着大规模集成电路、电脑系统和数字控制技术的应用,车轮弯曲疲劳试验机的加载臂产品已经普遍采用计算机和微机进行设计,并应用现代化的通讯系统使弯曲疲劳试验机产品趋于自动化和智能化,
其技术结构方面是模拟式逐渐被数字化和全数字化所取代,由提供数据向提供方法和结果的方向发展;产品结构方面,从技术密集型逐步转向高技术密集型,达到产品结构的最佳化。
总之,现代车轮弯曲疲劳试验机产品已实现了计算机化、智能化、数字化、自动化、节能化、微型化和超大型化。
试验机今后的主要发展趋势是对现有的这些高技术密集型产品的开发和发展,充分利用新材料,广泛应用机械手和机器人技术以及最现代化的通讯技术。
参考文献
[1]Kay S.M.Marple, S.L.Jr.Spectrum analysis-a modern perspective[J].Proceedings of the IEEE. Nov.1981,69(11).
[2]M.A. Mariscotti. A method for automatic identification of peaks in the presence of background and its application to spectrum analysis[J]. Nuclear Instruments and Methods, 1967-Elsevier. Volume 50, Issue 2, 1 May 1967, Pages 309-320.
[3]Bendat, J. S. Piersol, A. G. Engineering applications of correlation and spectral
analysis[M].
[4]刘岩.基于分形的往复机械振动信号分析技术[D].大庆:大庆石油学院,2006.
作者简介:徐恒斌(1986-),男,助教,硕士,主要从事机械设计制造方面的教学科研工作。