铝合金半固态压铸成形过程的模拟
A380铝合金压铸温度场模拟

A380铝合金压铸温度场模拟如图所示汽车传动轴,用A380铝合金半固态触变压铸成型工艺可获得重量轻、强度高、综合力学性能优越的零件,能够满足未来汽车工业轻量化、节能环保的要求。
查相关资料,A380铝合金半固态触变压铸成型工艺的浆料温度为570℃,模具预热温度为200℃,冷却水对流换热系数为450W/(m2·℃), A380铝合金密度为2730㎏/m3, 模具材料密度为7800㎏/m3,导热系数为21W/(m·℃),比热为110J/(㎏·℃)。
A380铝合金热性能参数相关尺寸在建模时提及,不赘述。
为简化建模,只取冷却水包络面以内的模具和铸件建模。
操作步骤1.定义工作标题和文件名(1)指定工作文件名:执行Utinity Menu/File/Change Jobname命令,在【Enter new Name】文本框中输入“WBA.file”,单击OK按钮。
(2)指定工作标题:执行Utinity Menu/File/Change Title命令,输入“Casting Solidification”, 单击OK按钮。
2.定义单元类型和材料属性(1)定义单元类型:执行Main Menu/Preprocessor/Element Type/Add、Edit、Delete命令,单击Add按钮,选择如下图选项,单击OK按钮。
(2)定义材料特性:执行Main Menu/Preprocessor/Material Props/ Material Models命令,双击【Material Models Available】列表框中的“Thermal/Conductivity/Isotropic”选项,定义模具导热系数(KXX)为“21”,接着双击“Thermal/Specific heat”选项, 定义模具比热(C)为“110”,单击OK按钮。
接着双击“Thermal/Density”选项, 定义模具密度(DENS)为“7800”,单击OK按钮。
半固态金属成形过程的数值模拟技术概况

d v lpn le l,a d a b c me o e o h h tg t n h ils o t il rs a c ig e eo ig f t e y n h s e o n ft e o l hs i te f d f maer s e e r hn i e a
Ab ta t s r c:W i t e t h ma u i o h c h t ry f t e omp tt n l t u a i a maer l ce c a d h elv t o t e o t is a s in e n t e e a i on f h
s i c .1 h ril t e c m p t g me h d o u e ia i ua in f rm e a 0 m ig p o e sa d cen e n te a ce。h o t u i t o fn m r l m lt o t l r n r c s n n c s o f
维普资讯
De .2 0 c 0 6 VO .5 No1 I5 .2
铸
造
・2 1 21・
F OUNDR Y
●
^ ●
■●
●^
‘ '
‘
{ 专题综述 {
’'^ - 、●- 、 ●●、‘r●~‘ 一 ■
Hale Waihona Puke 半 固态金 属成 形过程 的数值模拟 技术概 况
自从 2 世纪 6 年代 开始 凝 固过 程数 值 模拟 ,8年 0 0 0 代 初开 始成形 过 程数值 模 拟 和成形 件应 力应 变 数值 模 拟 ,到9 年代 兴起 成形 件微 观组 织 数值 模拟 的研 究 以 O 来 ,数值 模拟技 术 已应用 到金 属成形 过程 的各个方 面 , 使成 形件 从设 计 到完 成制 作 的周 期越来 越 短 。作 为铸
铝合金半固态压铸成形过程的模拟

成明显的温度梯度。
凝固过程
随着温度的下降,铝合金逐渐凝固, 凝固顺序与温度分布密切相关。
热节与冷隔
在温度场模拟中,可以发现热节 (局部高温区域)和冷隔(局部低 温区域)现象,这些区域对铸件质 量有重要影响。
流场模拟结果分析
充填过程
流动前沿与流动末端
本研究成果有助于推动铝合金半固态压铸技术的发展,提 高其在工业生产中的应用水平,促进相关产业的进步。
未来研究方向与展望
01
完善模拟方法,提高 模拟精度
未来可以进一步完善铝合金半固态压 铸成形过程的模拟方法,提高模拟精 度和效率,以更好地指导实际生产。
02
拓展应用领域,探索 新工艺
可以探索将铝合金半固态压铸技术应 用于更多领域,如航空航天、汽车制 造等,并研究新工艺,以满足不同领 域的需求。
成形精度高
半固态铝合金具有良好的流动性和触 变性,能够精确填充模具型腔,减少 飞边和毛刺等缺陷,提高零件的成形 精度。
组织性能好
半固态铝合金在成形过程中经历了固 液共存状态,有利于晶粒细化和均匀 化,提高材料的力学性能和耐蚀性。
铝合金半固态压铸成形技术原理及特点
生产效率高
铝合金半固态压铸成形技术具有 高效、自动化的特点,可大幅缩 短生产周期和降低成本,适用于 大规模生产。
优化后工艺参数的确定
1 2
综合评估
根据正交试验、数值模拟和人工智能算法的分析 结果,综合评估各工艺参数对成形质量的影响, 确定最优工艺参数组合。
实验验证
通过实际压铸实验对优化后的工艺参数进行验证, 确保优化结果的准确性和可靠性。
3
参数调整
在实际生产过程中,根据设备状况、原材料批次 等因素对工艺参数进行适当调整,以保证生产稳 定性和产品质量的稳定性。
ZL201合金半固态压铸成形过程数值模拟
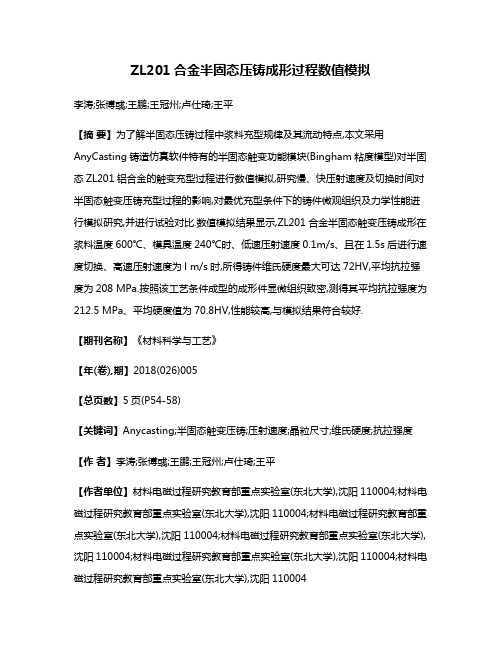
ZL201合金半固态压铸成形过程数值模拟李涛;张博彧;王鹏;王冠州;卢仕琦;王平【摘要】为了解半固态压铸过程中浆料充型规律及其流动特点,本文采用AnyCasting铸造仿真软件特有的半固态触变功能模块(Bingham粘度模型)对半固态ZL201铝合金的触变充型过程进行数值模拟,研究慢、快压射速度及切换时间对半固态触变压铸充型过程的影响,对最优充型条件下的铸件微观组织及力学性能进行模拟研究,并进行试验对比.数值模拟结果显示,ZL201合金半固态触变压铸成形在浆料温度600℃、模具温度240℃时、低速压射速度0.1m/s、且在1.5s后进行速度切换、高速压射速度为l m/s时,所得铸件维氏硬度最大可达72HV,平均抗拉强度为208 MPa.按照该工艺条件成型的成形件显微组织致密,测得其平均抗拉强度为212.5 MPa、平均硬度值为70.8HV,性能较高,与模拟结果符合较好.【期刊名称】《材料科学与工艺》【年(卷),期】2018(026)005【总页数】5页(P54-58)【关键词】Anycasting;半固态触变压铸;压射速度;晶粒尺寸;维氏硬度;抗拉强度【作者】李涛;张博彧;王鹏;王冠州;卢仕琦;王平【作者单位】材料电磁过程研究教育部重点实验室(东北大学),沈阳110004;材料电磁过程研究教育部重点实验室(东北大学),沈阳110004;材料电磁过程研究教育部重点实验室(东北大学),沈阳110004;材料电磁过程研究教育部重点实验室(东北大学),沈阳110004;材料电磁过程研究教育部重点实验室(东北大学),沈阳110004;材料电磁过程研究教育部重点实验室(东北大学),沈阳110004【正文语种】中文【中图分类】TG249铝合金的触变压铸是目前研究和应用最多的触变压铸工艺,早在20世纪70年代初期,就进行了半固态铝合金触变压铸实验[1-3].经过半固态触变压铸成形,成型件中的缩孔、气孔等显微孔洞很少,零件可进行热处理强化[4];零件的成分、组织和性能很均匀,可实现近终化成形和大幅度减少机加工量.因此,铝合金触变压铸在汽车及其他工业得到较大规模的实际应用[4-5].目前,人们对半固态成型技术已进行了大量研究[6-8],并取得了许多卓有成效的成果[9-12],但对于半固态压铸过程中浆料充型规律、流动特点等尚缺乏系统深入的了解.为此,本文采用AnyCasting铸造仿真软件特有的半固态触变功能模块(Bingham粘度模型)对半固态ZL201铝合金的触变充型过程进行数值模拟[13-14],研究慢、快压射速度及切换时间对半固态触变压铸充型过程的影响,对最优充型条件下的铸件微观组织及力学性能进行模拟研究,并进行试验对比,以期为半固态成型技术的深入研究奠定实验基础.1 模拟研究模拟研究采用AnyCasting软件,在半固态金属浆料充型过程中,由于充型几乎在瞬间完成,可以忽略时间对半固态浆料粘度的影响,并假设半固态金属浆料所受剪切力超过屈服应力时开始流动,且表观粘度为常值,因此,在模拟过程中流体模型采用Bingham模型.半固态金属浆料的表观粘度是与温度、固相分数、剪切速率等有关的多元函数,比纯液态金属约高2~3个数量级,本模拟过程取表观粘度10 Pa·s[15].若铸件的内浇口直径为4.5 mm,半固态坯料充型速度为4 m/s,两相区的平均密度为2 780 kg/m3,则其雷诺数远小于临界雷诺数2 300,是层流流动.式中:v为流体的流速;ρ为流体密度;η为流体的黏性系数;d为内浇口直径.利用三维绘图软件Pro/E进行实体造型,如图1所示.造型结束后将实体模型导入AnyCasting中,而后进行网格划分、初始条件设置,最后进行流场数值模拟.半固态触变压铸实验材料为ZL201合金,其液相线温度为650 ℃,固相线温度为547 ℃.模拟过程中半固态浆料温度设定为600 ℃,模具温度为240 ℃.压铸过程中速度主要有以下两种阶段.1)慢速阶段.当半固态浆料注入压室的充满度在70%以下时,压室内的空气含量仍很多,此时需要慢速压射,使金属液流动平稳,空气能顺利排出.通常慢速射出速度为0.1~0.5 m/s.本文设定慢速阶段压射速度分别为0.35、0.25、0.15、0.1m/s,确定最优慢速阶段压射速度.2)快速阶段.金属液到达内浇口时,可进行高速切换,使金属液在高压高速下填充.通常高速压射速度在0.2~4.5 m/s以上.本文在确定最优低速阶段压射速度后,选择不同时间进行高速切换,高速压射速度分别设定为1、2、3、4 m/s.图1 模拟模型Fig.1 Simulation model2 分析与讨论2.1 慢速阶段不同压射速度对充型过程的影响不同慢速阶段压射速度过程如图2所示.图2 不同慢速阶段压射速度过程图Fig.2 Rate plan of filling process of different low shot speed: (a) 0.35 m/s;(b) 0.25 m/s;(c) 0.15 m/s;(d) 0.1 m/s 由图2看见,当压射速度分别为0.35、0.25、0.15 m/s时,金属浆料通过狭窄的内浇口后流动速度变快,此时随着浆料注入,填充型腔,流动特征发生了改变,由层流流动变成了紊流流动,如图2(a)、(b)、(c)所示,这种紊流的添充形式容易使大量气体被裹挟进型腔,使得成型件内部包裹大量气体,造成成型件内部组织疏松,力学性能严重下降.当慢速阶段压射速度较小时,如为0.1 m/s时,此时由于压射速度不高,半固态浆料通过内浇口后并没有快速射入型腔,而是在内浇口附近堆积,逐渐向型腔里流动,流动平稳,呈层流特征,这种压射形式非常利于气体的逐渐溢出,成型件裹气的可能性大幅降低,成型件内部组织致密,具有较高的力学性能,如图2(d)所示,因此,慢速阶段最优的压射速度为0.1 m/s.2.2 快速阶段压射速度与慢快速切换时间点对充型的影响快速压射速度分别设定为1、2、3、4 m/s,金属浆料的填充过程将如图3所示.图3(a)为高速压射速度为1 m/s时的填充图,可以看到,浆料平稳的填充到型腔内,并无卷气现象,浆料呈现层流流动;而随着切换速度的增大,出现卷气现象并愈加明显,如图3(b)、(c)、(d)所示,由于充填速度很快,金属浆料获得很高的动能,充型过程会产生明显的卷气现象,严重影响铸件的质量.因此,高速阶段最优压射速度为1 m/s.压铸的基本特点之一是快速充型,在整个快速压射阶段,即从快速点开始一直到浆料充型结束,金属浆料以30~60 m/s的速度,以射流的形式进入型腔,金属液会包卷气体,因此,第2阶段快速压射点的时间转换节点至关重要.转换太慢影响效率,转换太快浆料容易容易发生喷溅.根据前期的工作[9],本文选取4个时间点进行高速切换,分别为低速阶段压射时间0.6、1.1、1.3、1.5 s后,从低速到高速的切换时间为0.01 s,高速压射速度选取较优的1.0 m/s.图3 不同快速压射阶段速度填充图Fig.3 Rate plan of filling process of different high shot speed: (a) 1 m/s;(b) 2 m/s;(c) 3 m/s;(d) 4 m/s图4为不同高速切换点的压铸过程图.当低速阶段充型时间较短时进行速度切换,即在内浇口附近进行高速切换,由于内浇口的限制,浆料充型速度很快,在充型刚开始时,在内浇口附近直接产生气囊,在浆料充型过程中,气囊中的气体逐渐被浆料包裹带到型腔的各个位置,如果气体不能排出,将在铸件内部形成气孔缺陷,严重影响铸件的质量,如图4(a)、(b)、(c)所示.随着低速阶段充型时间的延长,过了内浇口后再进行速度切换,这是因为型腔的下部在高速切换前已经填充了部分金属,因此,在高速切换后并无裹气现象,也没有发生回流,浆料平稳的充满整个型腔.铸件内部不会有气孔产生,使得组织致密,性能高,如图4(d)所示.因此,最优的压射速度是慢速阶段压射速度为0.1 m/s,在1.5 s时进行快速压射,快速阶段压射速度为1 m/s.图4 不同快速切换点充型过程图Fig.4 Rate plan of filling process of different high speed switch图5是压铸件的凝固过程,可以看出,压铸件的凝固是先从零件周围开始,向中心处延伸,最后凝固部位为浇口中心处和零件尺寸较大的部位.图5 压铸件的凝固过程Fig.5 Solidification process of die-casting workpiece图6是模拟的铸件硬度分布图,可以看出,ZL201合金半固态触变压铸件上不同部位维氏硬度分布,其最小维氏硬度为68HV,最大维氏硬度为72HV,整个铸件平均硬度为70HV,分布均匀.图6 维氏硬度Fig.6 Vickers hardness由图7的模拟抗拉强度分布图可见,在内浇口附近抗拉强度最高可达238 MPa,而在其内部平均值约为208 MPa.这是由于金属液流动时对周围的不断冲刷和搅拌作用,在这一区域形成一细晶区,晶粒尺寸较小,密度较大的原因.图7 抗拉强度Fig.7 Tensile strength图8为联合缺陷系数分布图.由图8可知,由于宏观补缩容易形成管筒形的一次缩孔,因此,在铸件浇口处由于补缩的原因造成联合缺陷系数较大.另外,由于冷却强度较大浆料来不及补缩,在零件曲率较大的地方也会造成缺陷系数较大.图8 联合缺陷系数分布Fig.8 Distribution of combined defect parameter图9是按照低速阶段压射速度是0.1 m/s,在1.5 s时进行快速压射,快速阶段压射速度是1 m/s工艺条件下的成型件显微组织照片.表1为其力学性能,可以看出,成型件内部组织致密,性能较高,与模拟结果符合较好.图9 压铸件的显微组织Fig.9 Microstructures of die casting parts表1 ZL201合金压铸件性能Table 1 The rigidity values of ZL201 alloy平均抗拉强度/MPa平均硬度值(HV)212.570.83 结论1)通过Anycasting模拟,压射速度为慢速阶段压射速度0.1 m/s,在1.5 s时进行快速压射,快速阶段压射速度1 m/s,此时压铸效果最好且浆料以层流方式填充.2)模拟成型件的平均硬度为70HV,平均抗拉强度为208 MPa,与实际符合较好. 参考文献:【相关文献】[1] 朱鸣芳,苏华钦. 半固态铸造技术的研究现状[J].特种铸造及有色合金,1996(2):29-32. ZHU Mingfang,SU Huaqin. The present study status of semi-solid castingtechniques[J].Special Casting & Nonferrous Alloy,1996(2):29-32.DOI: 10.15980/j.tzzz.1996.02.009[2] 苏华钦,朱鸣芳,高志强. 半固态铸造的现状及发展前景[J].特种铸造及有色合金,1998(5):1-6.SU Huaqin,ZHU Mingfang,GAO Zhiqiang. Overview and prospect of semi-solid casting[J]. Special Casting & Nonferrous Alloy,1998(5):1-6.DOI: 10.15980/j.tzzz.2002.s1.099[3] FLEMINGS M C. Behavior of metal alloys in the semi-solid state[J]. Metallurgical Transactions , 1991, 21A(5): 975-981.[4] 杜平,李双寿,唐靖林,等.半固态铝合金触变压铸技术中关键问题的讨论[J].铸造技术,2006(6):545-549.DU Ping,LI Shuangshou,TANG Jinglin,et al. Discussion of key problems on thixotropic die casting in semi-solid aluminum alloys[J].Foundry Technology,2006(6):545-549.[5] 张志峰,田战峰,杨必成,等.汽车用铝合金半固态零件触变压铸工艺研究[J].铸造技术,2005(9):770-773.ZHANG Zhifeng,TIAN Zhanfeng,YANG Bicheng,et al. Investigation on semi-solid thixo diecasting processing of automobile aluminum alloy part[J]. FoundryTechnology,2005(9):770-773.[6] 田战峰,杨必成,张志峰,等.铝合金半固态触变压铸试验研究[J].轻金属,2005(9):42-46.TIAN Zhanfeng, YANG Bicheng, ZHANG Zhifeng,et al.Study on semi-solid thixo-diecasting processing of aluminium alloys[J].Light Metals,2005(9):42-46.DOI:10.13662/ki.qjs.2005.09.013.[7] 杨明波,代兵,伍光凤,等.铝合金半固态压铸触变成形技术的研究进展[J].铸造,2003(8):533-537. YANG Mingbo, DAI Bing, WU Guangfeng, et al. Research and development of semi-solid dieing casting thixo forming technology about aluminum alloys[J]. Foundry,2003(8):533-537.[8] CHEN Song, LI Daquan, ZHANG Fan,et al. Development of semi-solid die casting process technology for aluminium alloy clamp[J]. Materials Science Forum,2016,4328(850).[9] 熊守美等.铸造过程模拟仿真技术[M].北京:机械工业出版社,2004.[10] 柳百成,荆涛主编. 铸造工程的模拟仿真与质量控制[M].北京:机械工业出版社,2001.[11] YOUNG K P, RIEK R G, BOYLAN J E, et al. Machine casting of copper base alloys by thixocasting[J]. AFS Transaction, 1973(84): 169-174.[12] 张恒华. 铝合金半固态触变成形技术及其仿真研究[D].上海:上海大学,2003.[13] 王平,康浩,史立峰,等. ZL201合金半固态成形的AnyCasting模拟与验证[J].稀有金属材料与工程,2003(3):44-46.WANG Ping,KANG Hao,SHI Lifeng.The anycasting simulation and verification of ZL201 alloy semisolid forming[J]. Rare Metal Materials and Engineering,2003(3):44-46.[14] 崔成林,毛卫民,赵爱民,等.半固态触变压射成形过程模拟及验证[J]. 北京科技大学学报,2001,23(3):237-239.CUI Chenglin,MAO Weimin,ZHAO Aimin,et al. Verification and numerical simulation for semi-sold modeling the thixoforming process[J].The Journal of University of Science and Technology Beijing[J]. 2001,23(3):237-239.[15] MEHRABIAN R, FLEMINGS M C. Die casting of partially solidified alloys [J]. AFS Trans,1972, 80: 173-182.。
铝合金液相线半连续铸造过程模拟的开题报告

铝合金液相线半连续铸造过程模拟的开题报告一、研究背景随着航空、汽车、船舶等重点行业的不断发展,对铝合金材料的需求量越来越大。
而半连续铸造技术作为一种高效、低成本的生产方法,被广泛应用于铝合金材料的生产过程中。
在半连续铸造过程中,液相线的形态和位置对铸件的质量和成形性能有着重要的影响。
因此,开展铝合金液相线半连续铸造过程的模拟研究具有重要的实际意义和科学价值。
二、研究内容及目标本文将利用数值模拟方法,对铝合金液相线半连续铸造过程进行模拟研究。
具体包括以下研究内容:1. 建立铝合金液相线半连续铸造过程的数学模型,包括热传导方程、流体力学方程、相变方程等。
2. 采用计算流体力学(CFD)软件,对液相线的形态和位置进行模拟计算。
3. 通过对模拟结果进行分析,探究液相线形态和位置对铝合金铸件质量和成形性能的影响机理。
4. 为进一步优化铝合金半连续铸造工艺提供理论支持。
本文的研究目标是深入了解铝合金液相线半连续铸造过程的物理现象,探究液相线形态和位置对铸件质量和成形性能的影响机理,为铝合金半连续铸造工艺的优化提供科学依据。
三、研究方法和步骤1. 收集相关文献,了解半连续铸造技术的基本原理和铝合金液相线形态的研究现状。
2. 建立铝合金液相线半连续铸造过程的数学模型,包括热传导方程、流体力学方程、相变方程等。
3. 选取适当的计算流体力学(CFD)软件,对液相线的形态和位置进行模拟计算,并分析计算结果。
4. 分析液相线形态和位置对铸件质量和成形性能的影响机理。
5. 结合实际铸造工艺,对模拟结果进行验证,并进一步优化半连续铸造工艺。
四、论文预期成果1. 建立了铝合金液相线半连续铸造过程的数学模型,包括热传导方程、流体力学方程、相变方程等。
2. 采用计算流体力学(CFD)软件,模拟计算液相线的形态和位置,并分析计算结果。
3. 探究液相线形态和位置对铸件质量和成形性能的影响机理,并为铝合金半连续铸造工艺的优化提供理论支持。
半固态A356铝合金流变压铸充填过程的数值模拟

[ 10]
张环月 , 张兴国 , 房灿 峰 . 大板 坯连铸 结晶器 内熔体 流动的 DPIV
( 编辑: 张正贺 )
428
半固态 A356 铝合金流变压铸充填过程的数值模拟 态 A 356 铝合金浆料的表观粘度比液态 A356 铝合金高 3~ 4 个数量级, 可将半固态 A356 铝合金浆料的充填流 动看作是层流流动。因此半固态 A356 铝合金浆料的 充填流动仍然遵循质量守恒定律、 动量守恒定律 , 与之 相对应的数学方程则为连续性方程和 N S 方程。在三 维直角坐标系下 , 半固态 A356 铝合金浆料流变压铸时 的连续性方程和 N S 方程可表示为: 连续性方程 U+ x 动量方程 V+ U V+ V V+ W V = t x y y 1 P + gy + y
i [ 12]
:
= exp [- ( 3. 20 - 1. 301 4 10
4 - 1. 93
。但实际
-
e e
) ! t]
( 1)
上半固态金属浆料在压铸型腔中会发生强烈的剪切, 且 充填过程中的浆料温度会发生变化 , 因此浆料的表观粘 度肯定会发生变化, 充填行为也会发生变化。为了准确 的模拟半固态金属的充填过程 , 模拟时必须考虑浆料温 度和剪切时间的变化对其充填行为的影响[ 12, 13] 。 基于上述原因, 本课题在基础试验数据的基础上 , 建立了半固态 A356 铝合金浆料的表观粘度数学模型,
V+ y
W= 0 z
( 2)
式中 , U, V , W 为 x , y , z 方向的速度分量
V+ 2 x
2
V + 2 y
2
铝合金半固态压铸成形过程的模拟
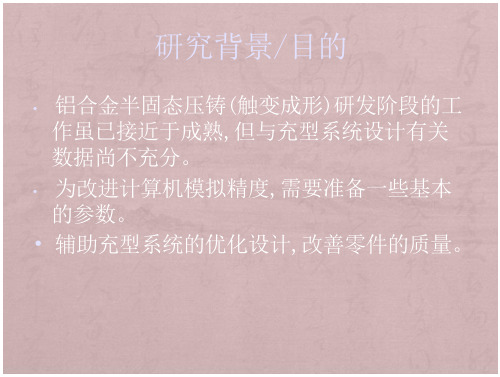
To optimize design of gating sysytem
The shape and size of gate are optimized
X-ray inspection(1)
X-ray inspection(2)
结 论(一)
• 系统地比较了压铸过程不同主要因素(溶体/型壁 的摩擦系数,模具型腔的背压,溶体/型壁的换热系 数和压铸机的推杆速度)对充型状态的影响,为确 定后续模拟的主要使用条件打下了基础。
• 分析和验证典型试样充型流场与铸造缺陷 的关系,优化模具设计
• 实际应用于汽车零件的研发过程,预测缺陷 和对策
研究方法
实验方法
• 实验材料 A356铝合金 • 主要实验工艺过程(制坯-二次加热-压铸)
制造坯料的水平连铸装置
电磁搅拌
多工位旋转式坯料感应二次加热设备
感应圈 控制面板
500吨压铸机
kg/m3 kJ/(kg K) W/(m K) KJ/kg m2/s
K
K
2700
0.96
155
389
*
887
850
* Function of solid fraction
Relationship between kinematic viscosity and solid fraction
Solid fraction, % Kinematic Viscosity
模具型腔的局部形状
模拟结果
gate的形状与大小
模 拟 结 果
局部中空的设计
模 拟 结 果
综合改进(1)
模拟结果
综合改进(2)
模 拟 结 果
该处的充满较方 案11明显加快
_筒壳_铸件半固态压铸过程数值模拟_王广太

··“筒壳”铸件半固态压铸过程数值模拟收稿日期:2012-09-25收到初稿,2012-12-10收到修订稿。
作者简介:王广太(1968-),男,讲师,主要从事金属成形的教学和研究工作。
E-mail:gt@yahoo.com.cn王广太(沈阳理工大学材料科学与工程学院,辽宁沈阳110159)摘要:采用铸造模拟软件ProCAST对腔深、壁薄的A356合金的“筒壳”铸件进行模拟分析。
通过对其压铸过程中的温度场进行数值模拟、分析,预测缩孔缩松所在的位置及大小。
优化出最佳工艺参数:浇注温度为590℃,压射速度为5m/s,模具温度为220℃。
在此工艺条件下A356半固态浆料充型平稳,温度场分布均匀,无飞溅卷气和浇注不足等缺陷,在实际生产中获得了质量完好的铸件,验证了该工艺参数。
关键词:模具温度;浇注温度;压射速度;半固态压铸中图分类号:TG249.2文献标识码:A文章编号:1001-4977(2013)03-0218-04Numerical Simulation of Semi-Solid Die Casting of Barrel ShellWANGGuang-tai(SchoolofMaterialsScienceandEngineering,ShenyangLigongUniversity,Shenyang110159,Liaoning,China)Abstract:Thediecast“barrelshell”castingwithdeepcavityandthinwallwassimulatedbycastingsimulationsoftwareProCAST.Bymakingcastingsimulationoncastingprocessandtemperaturefield,thelocationandsizesofshrinkageanddispersedshrinkagewereforecasted.Theoptimizedparametersare:pouringtemperature590℃,injectionspeed5m/s,moldtemperature220℃.Underthisprocess,semi-solidslurrymoldfillingisstable,temperaturefieldisuniformandtherewerenocastingdefectssuchassplashairentrapmentsandmisrun.Theprocessparameterswereprovedbyobtainingperfectpartqualityinactualproduction.Keywords:moldtemperature;pouringtemperature;injectionspeed;semi-soliddiecastingMar.2013Vol.62No.3铸造FOUNDRY半固态成形是一种近终成形工艺,具有成形温度低、模具寿命长、成形件内部组织致密、表面平整光滑、缺陷少、力学性能好等优点。
铝合金半固态流变压铸过程数值模拟及试验验证_唐景

··1971年,Flemings 和Spencers 在用Couette 黏度计测定Sn-15%Pb 的黏度的试验中,发现了半固态金属组织[1]。
于是,Flemings 依据试验结果提出了半固态金属成形的概念,并对其做了系统的开拓性研究[2-4]。
半固态金属成形的优点在于,它可以采用较低的成形温度,提高模具寿命,减少铸件凝固收缩率,减少压铸过程中的卷气和氧化,提高铸件性能[5]。
因此,人们开始将半固态金属成形技术应用于工业领域,并取得了一定的成果[6-8]。
在半固态金属成形技术中,铝合金半固态流变压铸由于越来越明显的经济性,逐渐成为重要的研究方向[9]。
然而,半固态流变压铸的产品由于工艺设计的问题,往往容易产生卷气和缩孔缩松缺陷。
于是,Jae 等人开始采用数值模拟的方法来对半固态浆料的充型和凝固过程进行分析,从而预测铸件可能产生的缺陷[10-12]。
本课题采用铸造仿真软件对Al-Si 合金半固态流变压铸的充型及凝固过程进行数值模拟,准确预测了铸件卷气以及缩孔缺陷,并对工艺参数和模具的设计进行了优化,减少了卷气及缩凹缺陷。
同时解释了铸件不同部位不同显微组织的形成原因,为Al-Si 合金半固态流变压铸的模具设计和工艺试验提供借鉴。
1模拟过程1.1数学模型在几何型腔中,带有自由表面的高温半固态金属连续流动,且向周围传递热量。
Al-Si 合金半固态浆料可以看做均匀的、连续的、不可压缩的流体。
它遵循质量守恒、动量守恒、能量守恒定律[13]:其黏度模型采用幂律模型进行描述[14]。
唐景,董选普,张磊,潘璋,王文俊,樊自田(华中科技大学材料成形及模具技术国家重点实验室,湖北武汉430074)摘要:采用模拟软件对Al-Si 合金半固态流变压铸的充型和凝固过程进行模拟,并与试验进行了对比。
结果表明,浇注温度为610℃、压射速度为90mm/s 、料柄及内浇口直径为40mm 时,半固态压铸的卷气以及缩凹缺陷明显减少。
高硅铝合金的半固态压铸成形技术
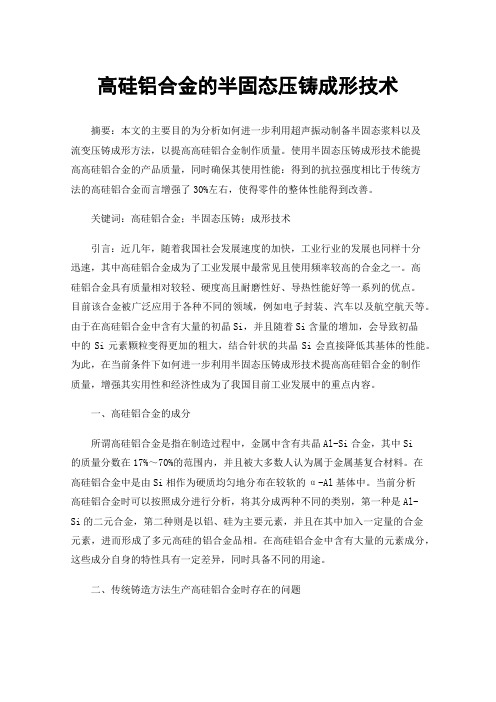
高硅铝合金的半固态压铸成形技术摘要:本文的主要目的为分析如何进一步利用超声振动制备半固态浆料以及流变压铸成形方法,以提高高硅铝合金制作质量。
使用半固态压铸成形技术能提高高硅铝合金的产品质量,同时确保其使用性能:得到的抗拉强度相比于传统方法的高硅铝合金而言增强了30%左右,使得零件的整体性能得到改善。
关键词:高硅铝合金;半固态压铸;成形技术引言:近几年,随着我国社会发展速度的加快,工业行业的发展也同样十分迅速,其中高硅铝合金成为了工业发展中最常见且使用频率较高的合金之一。
高硅铝合金具有质量相对较轻、硬度高且耐磨性好、导热性能好等一系列的优点。
目前该合金被广泛应用于各种不同的领域,例如电子封装、汽车以及航空航天等。
由于在高硅铝合金中含有大量的初晶Si,并且随着Si含量的增加,会导致初晶中的Si元素颗粒变得更加的粗大,结合针状的共晶Si会直接降低其基体的性能。
为此,在当前条件下如何进一步利用半固态压铸成形技术提高高硅铝合金的制作质量,增强其实用性和经济性成为了我国目前工业发展中的重点内容。
一、高硅铝合金的成分所谓高硅铝合金是指在制造过程中,金属中含有共晶Al-Si合金,其中Si的质量分数在17%~70%的范围内,并且被大多数人认为属于金属基复合材料。
在高硅铝合金中是由Si相作为硬质均匀地分布在较软的α-Al基体中。
当前分析高硅铝合金时可以按照成分进行分析,将其分成两种不同的类别,第一种是Al-Si的二元合金,第二种则是以铝、硅为主要元素,并且在其中加入一定量的合金元素,进而形成了多元高硅的铝合金品相。
在高硅铝合金中含有大量的元素成分,这些成分自身的特性具有一定差异,同时具备不同的用途。
二、传统铸造方法生产高硅铝合金时存在的问题在利用传统的方式生产高硅铝合金过程中,存在以下几点问题:第一,在进行初晶硅的细化过程时其难度较高:尝试增加高硅铝合金中含有的Si含量,会导致合金中含有的初晶硅体积率增大,致使高硅铝合金的抗拉强度、屈服强度以及塑性都会在这一阶段明显的降低。
铝合金半固态压铸成形过程的模拟

铝合金半固态压铸成形过程的模拟铝合金半固态压铸成形是一种先将铝合金预热至半固态,然后以压铸的方式将其注入模具中。
这种成形过程常用于制造复杂形状的铝合金零件,具有高精度、高韧性和高耐热性的特点。
采用数值模拟方法可以有效地研究和优化这一成形过程。
本文将对铝合金半固态压铸成形过程的模拟方法、影响因素以及应用进行综述,总结目前这一领域的研究现状。
铝合金半固态压铸成形的模拟方法主要分为两个方面:固相区域的模拟和液相区域的模拟。
固相区域的模拟主要是通过有限元方法来研究铝合金的形变过程,包括应力分布、应变速率和细晶度等。
而液相区域的模拟则是通过计算流体力学方法来研究熔融铝合金的流动行为,包括注射压力、液相填充和凝固过程等。
影响铝合金半固态压铸成形的因素有很多,其中包括合金的成分、半固态温度、模具温度以及注射速度等。
合金的成分决定了其流动性和凝固性,而半固态温度和模具温度则影响铝合金的半固态行为和凝固过程。
注射速度对铝合金的充填性能和表面质量有重要影响。
研究这些因素的变化规律,可以为铝合金半固态压铸成形提供指导和优化方案。
铝合金半固态压铸成形广泛应用于航空航天、汽车制造和电子工业等领域。
通过数值模拟方法,可以提高产品的质量和制造效率。
例如,可以通过优化半固态温度和模具温度的组合,来控制铝合金的凝固过程,从而获得理想的微观组织和力学性能。
此外,模拟还可以研究注射速度对充填性能的影响,优化产品的表面质量和密度分布。
总之,铝合金半固态压铸成形的数值模拟是一种研究和优化这一成形过程的有效方法。
通过模拟,可以深入理解铝合金的变形和凝固行为,并优化工艺参数,从而提高铝合金零件的质量和性能。
随着数值模拟方法的不断发展,铝合金半固态压铸成形的模拟研究将迎来更广阔的发展空间。
铝合金半固态压铸成形过程的模拟讲解共62页文档

16、业余生活要有意义,不要越轨。——华盛顿 17、一个人即使已登上顶峰,也仍要自强不息。——罗素·贝克 18、最大的挑战和突破在于用人,而用人最大的突破在于信任人。——马云 19、自己活着,就是为了使别人过得更美好。——雷锋 20、要掌握书,莫被书掌握;要为生否则对不起自己。
2、要冒一次险!整个生命就是一场冒险。走得最远的人,常是愿意 去做,并愿意去冒险的人。“稳妥”之船,从未能从岸边走远。-戴尔.卡耐基。
梦 境
3、人生就像一杯没有加糖的咖啡,喝起来是苦涩的,回味起来却有 久久不会退去的余香。
铝合金半固态压铸成形过程的模拟讲解 4、守业的最好办法就是不断的发展。 5、当爱不能完美,我宁愿选择无悔,不管来生多么美丽,我不愿失 去今生对你的记忆,我不求天长地久的美景,我只要生生世世的轮 回里有你。
铝合金半固态金属触变成形过程的数值模拟
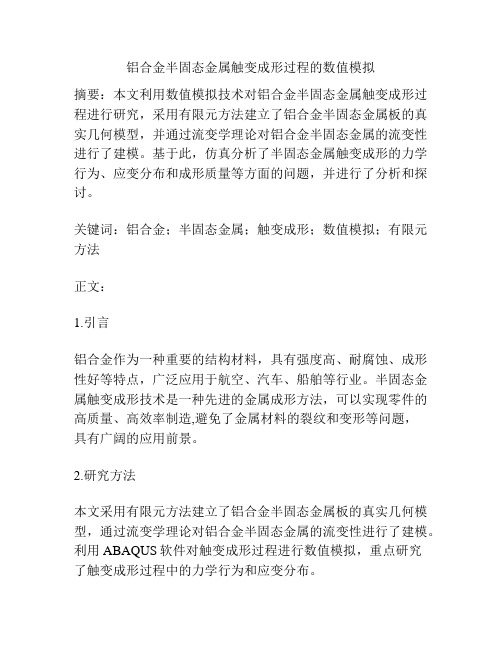
铝合金半固态金属触变成形过程的数值模拟摘要:本文利用数值模拟技术对铝合金半固态金属触变成形过程进行研究,采用有限元方法建立了铝合金半固态金属板的真实几何模型,并通过流变学理论对铝合金半固态金属的流变性进行了建模。
基于此,仿真分析了半固态金属触变成形的力学行为、应变分布和成形质量等方面的问题,并进行了分析和探讨。
关键词:铝合金;半固态金属;触变成形;数值模拟;有限元方法正文:1.引言铝合金作为一种重要的结构材料,具有强度高、耐腐蚀、成形性好等特点,广泛应用于航空、汽车、船舶等行业。
半固态金属触变成形技术是一种先进的金属成形方法,可以实现零件的高质量、高效率制造,避免了金属材料的裂纹和变形等问题,具有广阔的应用前景。
2.研究方法本文采用有限元方法建立了铝合金半固态金属板的真实几何模型,通过流变学理论对铝合金半固态金属的流变性进行了建模。
利用ABAQUS软件对触变成形过程进行数值模拟,重点研究了触变成形过程中的力学行为和应变分布。
3.结果与分析本文将不同成形速度下铝合金半固态金属板的应变分布进行了仿真分析,得到了不同成形速度下的最大应变和变形区域。
同时,还对触变成形过程中的力学行为和成形质量进行了分析和探讨。
结果表明,在成形速度为0.1 mm/s时,铝合金半固态金属的形变量最小、形状最好,成形质量最高。
4.结论本文利用数值模拟技术对铝合金半固态金属触变成形过程进行了深入研究,得到了不同成形速度下铝合金半固态金属板的应变分布和成形质量。
研究结果表明,在成形速度为0.1 mm/s 时的成形质量最佳。
此外,研究成果也可为铝合金半固态金属触变成形工艺提供理论依据和参考。
5.讨论本文中采用的有限元方法可用于真实材料的坯料建模和半固态金属材料的触变成形仿真分析。
在本文的仿真实验中,铝合金半固态金属的触变行为经过流变学建模,得到了较为准确的应变-应力曲线,进而获得铝合金半固态金属的流变参数。
本文研究结果表明,在成形速度为0.1 mm/s时铝合金半固态金属的成形质量最佳。
材料加工原理之半固态铸造成形(ppt 32页)

铝合金 铝基复合材料
SIMA加工过程组织变化
a 原始组织 b 挤压预变形后 C 挤压预变形后再加热 至半固态
ZL101A合金不同成型方式显微组织对比
半固态铸造
重力铸造
液态成形
半固态成形
ZL101A合金力学性能对比
合金
ZL101 A
状态 抗拉强度(MPa)
下直接送往成形设备进行成形加工,通常称为半固态金属 的流变成形(Rheoforming) 触变成形是将半固态金属浆料进一步凝固成坯料后,再按 需要将坯料分切成一定大小,把这种切分的半固态坯料重 新加热到半固态温度,然后将半固态坯料送往成形设备进 行成形加工 (Thixoforming)
高温合金半固态组织
设备投资大,工艺较复杂,成本高。
电磁搅拌示意图
3、应力诱发熔化激活工艺:S.I.M.A.(Strain Induced Metl Activated) 常铸锭经过20%左右的预形变,然后加热至 半固态。
加热过程组织变化:
首先发生再结晶,然后部分熔化,使固相晶粒分散 在液相基体中,得到半固态金属成型所需的原材 料。
着剪切速率的增加而降低的特性。
非常小的流动阻力和良好的成形性能。
技术核心: 固-液混合浆料获得非枝晶组织,固
相必须球化和细化,
近球形晶或等轴晶
枝晶
球形晶或 等轴晶
工艺如何实现?
半固态金属坯料制备方式
1、机械搅拌法: 是最早用于制备非枝晶组织金属的方法。
一种是由两个同心带齿的圆筒组成,内筒保持静 止,外筒旋转;另一种是在熔融的金属中利用搅 拌棒进行搅动。 存在问题:
半固态成形定义?
利用金属从固态向液态或从液态向固态两相转变过 程中的半固态区的金属具有良好的流变特性而进行的金 属成形。
铝合金半固态压铸与液态压铸充型过程的模拟

・
造
Ma 0 2 y2 1
44・ 9
F OUND Y R
VO . 1 NO. I6 5
铝合金半 固态压铸与液态压铸充型过程的模拟
史立峰 ,赵 大志 ,王 平s ,崔建忠
(. 1 辽宁装备制造职业技术学院塑性 成形 系,辽宁沈阳 10 6 ;2 11 1 .东北大学材料与冶金 学院 ,辽 宁沈 阳 10 0 ; 10 4 3 东北大学材料 电磁 过程研 究教 育部重点 实验室 ,辽 宁沈阳 10 0 ) . 10 4
摘 要 :利用A y a i 软件模拟TZ 21 nC sn tg L 0合金半固态压铸和液态压铸充型的流动过程 , 并进行了试验验证。模拟及试
验结果 显示 :合理的控制速 度转换位置 ,能够保证半固态浆料以层 流方式的产生 。在相 同的速度条件下进 行液态压铸 ,金属液以湍流方式充填 型腔 ,容易形 成喷溅和
Po es go Mae a , ote s r ies y S e y n 1 0 4 L a nn , hn ) r c si f t il N r at n n r s h e Unv r t, h n a g1 0 0 , io i C ia i g
Ab tat Th o c aa tr t so e i oi l n n iud f l g wee c mp r d a d a ay e y src : e f w h r cei i fsm . l f l g a d l i ln r o ae n n lz d b l sc s di i q i i
Thesmu a i nr s t r l a r e n t x e i n a n s i l to e ulsa eweli g e me twi e p rme tlo e . n h
下壳体半固态压铸件数值模拟的开题报告

下壳体半固态压铸件数值模拟的开题报告一、选题背景下壳体是航空发动机中一个关键的部件,起着支撑、过滤、导流、密封等多种作用。
而下壳体的制造工艺对其质量和性能有直接的影响,传统的下壳体生产采用铸造技术,但由于该工艺需要较长的时间进行冷却,导致生产效率低下,成本高昂。
因此,半固态压铸成为了一种广泛应用于下壳体制造的工艺。
半固态压铸是一种集铸造和挤压于一体的新型材料成形技术,在快速结晶下,可以得到具有高密度、细小均匀组织的零件,特别适用于高强度铝合金、镁合金及铜合金零件的制造。
针对下壳体半固态压铸件的形成过程及性能研究,本课题旨在针对下壳体半固态压铸组织演变和变形行为进行模拟及分析,为相关工程领域提供技术支持。
二、研究目的和内容目的:通过建立下壳体半固态压铸件的数值模拟模型,对其组织演变和变形行为进行模拟和分析,探究下壳体半固态压铸件制造工艺的优化及其在航空发动机设计中的应用。
内容:1. 建立下壳体半固态压铸件的数值模拟模型,包括模具和铸件几何模型及工艺参数模型。
2. 通过有限元分析方法,探究下壳体半固态压铸件组织演变和变形行为,并对其性能进行分析。
3. 针对下壳体半固态压铸件制造工艺的问题,提出解决方案,探究其对零件性能和质量的影响。
4. 设置不同参数条件,对下壳体半固态压铸件数值模拟模型进行优化和验证。
三、研究意义1. 为下壳体半固态压铸件制造工艺提供技术支持和理论指导。
2. 探究下壳体半固态压铸件组织演变和变形行为,对优化工艺参数、提高零件性能和质量具有重要意义。
3. 建立下壳体半固态压铸件数值模拟模型,为类似零件的制造提供科学参考,方便快捷。
四、研究方法1. 借助有限元分析软件,建立下壳体半固态压铸件的数值模拟模型,模拟其组织演变和变形行为。
2. 通过本研究中提出的优化方案,尝试解决下壳体半固态压铸件制造工艺的问题,进一步提高其制造效率。
3. 通过参数优化和验证,对下壳体半固态压铸件数值模拟模型进行调整和测试,以达到最佳效果,保证零件质量和性能。
半固态铝合金压铸充型凝固过程数值模拟研究
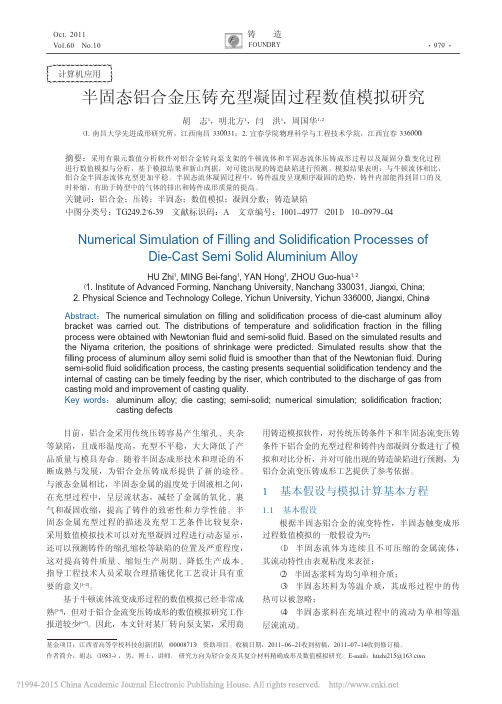
··目前,铝合金采用传统压铸容易产生缩孔、夹杂等缺陷,且成形温度高,充型不平稳,大大降低了产品质量与模具寿命。
随着半固态成形技术和理论的不断成熟与发展,为铝合金压铸成形提供了新的途径。
与液态金属相比,半固态金属的温度处于固液相之间,在充型过程中,呈层流状态,减轻了金属的氧化、裹气和凝固收缩,提高了铸件的致密性和力学性能。
半固态金属充型过程的描述及充型工艺条件比较复杂,采用数值模拟技术可以对充型凝固过程进行动态显示,还可以预测铸件的缩孔缩松等缺陷的位置及严重程度,这对提高铸件质量、缩短生产周期、降低生产成本、指导工程技术人员采取合理措施优化工艺设计具有重要的意义[1-2]。
基于牛顿流体流变成形过程的数值模拟已经非常成熟[3-5],但对于铝合金流变压铸成形的数值模拟研究工作报道较少[6-7]。
因此,本文针对某厂转向泵支架,采用商用铸造模拟软件,对传统压铸条件下和半固态流变压铸条件下铝合金的充型过程和铸件内部凝固分数进行了模拟和对比分析,并对可能出现的铸造缺陷进行预测,为铝合金流变压铸成形工艺提供了参考依据。
1基本假设与模拟计算基本方程1.1基本假设根据半固态铝合金的流变特性,半固态触变成形过程数值模拟的一般假设为[8]:(1)半固态流体为连续且不可压缩的金属流体,其流动特性由表观粘度来表征;(2)半固态浆料为均匀单相介质;(3)半固态坯料为等温介质,其成形过程中的传热可以被忽略;(4)半固态浆料在充填过程中的流动为单相等温层流流动。
------------------计算机应用胡志1,明北方1,闫洪1,周国华1,2(1.南昌大学先进成形研究所,江西南昌330031;2.宜春学院物理科学与工程技术学院,江西宜春336000)摘要:采用有限元数值分析软件对铝合金转向泵支架的牛顿流体和半固态流体压铸成形过程以及凝固分数变化过程进行数值模拟与分析,基于模拟结果和新山判据,对可能出现的铸造缺陷进行预测。
铝合金标准试样半固态压铸模设计研究
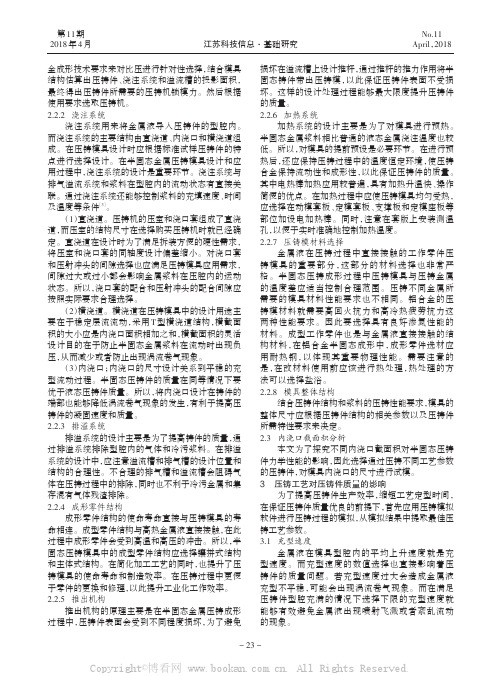
金成形技术要求来对比压进行针对性选择,结合模具结构估算出压铸件、浇注系统和溢流槽的投影面积,最终得出压铸件所需要的压铸机锁模力。
然后根据使用要求选取压铸机。
2.2.2浇注系统浇注系统用来将金属液导入压铸件的型腔内。
而浇注系统的主要结构由直浇道、内浇口和横浇道组成。
在压铸模具设计时应根据标准试样压铸件的特点进行选择设计。
在半固态金属压铸模具设计和应用过程中,浇注系统的设计是重要环节。
浇注系统与排气溢流系统和浆料在型腔内的流动状态有直接关联。
通过浇注系统还能够控制浆料的充填速度、时间及温度等条件[3]。
(1)直浇道。
压铸机的压室和浇口套组成了直浇道,而压室的结构尺寸在选择购买压铸机时就已经确定。
直浇道在设计时为了满足拆装方便的硬性需求,将压室和浇口套的同轴度设计偏差缩小。
对浇口套和压射冲头的间隙选择也应满足压铸模具应用需求,间隙过大或过小都会影响金属浆料在压腔内的运动状态。
所以,浇口套的配合和压射冲头的配合间隙应按照实际要求合理选择。
(2)横浇道。
横浇道在压铸模具中的设计用途主要在于稳定层流流动,采用T型横浇道结构,横截面积的大小应是内浇口面积相加之和,横截面积的灵活设计目的在于防止半固态金属浆料在流动时出现负压,从而减少或者防止出现涡流卷气现象。
(3)内浇口;内浇口的尺寸设计关系到平稳的充型流动过程。
半固态压铸件的质量在同等情况下要优于液态压铸件质量。
所以,将内浇口设计在铸件的端部也能够降低涡流卷气现象的发生,有利于提高压铸件的凝固速度和质量。
2.2.3排溢系统排溢系统的设计主要是为了提高铸件的质量,通过排溢系统排除型腔内的气体和冷污浆料。
在排溢系统的设计中,应注意溢流槽和排气槽的设计位置和结构的合理性。
不合理的排气槽和溢流槽会阻碍气体在压铸过程中的排除,同时也不利于冷污金属和集存混有气体残渣排除。
2.2.4成形零件结构成形零件结构的使命寿命直接与压铸模具的寿命相连。
成型零件结构与高热金属液直接接触,在此过程中成形零件会受到高温和高压的冲击。
- 1、下载文档前请自行甄别文档内容的完整性,平台不提供额外的编辑、内容补充、找答案等附加服务。
- 2、"仅部分预览"的文档,不可在线预览部分如存在完整性等问题,可反馈申请退款(可完整预览的文档不适用该条件!)。
- 3、如文档侵犯您的权益,请联系客服反馈,我们会尽快为您处理(人工客服工作时间:9:00-18:30)。
位移曲线测试结果小结
• (1)慢压式和快压式各具有明显不同的位移曲线,各次测试 的结果均反映出相似的曲线特征,说明压铸机系统可以保 证相对稳定的充型状态; • (2)慢压条件下两种方法得到的位移曲线非常相似,虽然压 铸初期的推杆空走和后期的保压阶段存在少许位移的差别, 但模具型腔充填时的位移变化斜率(即速度)基本一致,涉 及充型的部分包括充型主要阶段和充型末期,由位移曲线 的斜率变化可以推算出这两个阶段的推杆速度分别约为 0.25 m/s(按70%计)和0.06 m/s(按30%计),这将作为后续 模拟的初始条件; • (3)快压条件下的位移曲线按前图所示同样可分为充型主 要和充型末期两个阶段,从曲线的斜率可以推算出推杆速 度分别为0.79 m/s(按70%计)和0.09 m/s(按30%计); • (4)压铸机测试记录系统和高速摄像机测试的结果虽存在 差异,但反映的趋势是一致的,也说明了测试记录系统的准 确与可靠。
型内流动的测试
0.4
Experiment(slow filling) Simulation(slow filling) Experiment(rapid filling) Simulation(rapid filling)
Relative filling time (reaction timing), s
Density kg/m3 2700 Specific heat kJ/(kg K) 0.96 Thermal conductivity W/(m K) 155 Latent heat KJ/kg 389 Kinematic Liquids Solidus viscosity m2/s K K
*
887
初始方案的凝固模拟
凝固特征的比较
改进方案的凝固模拟
模具温度分布的求解
半固态压铸的成形周期
稳 定 状 态 下 的 模 具 温 度 分 布
在30个压铸循环周期中模具型腔表面的温度变化 (模具初始预热至250℃)
在30个压铸循环周期中模具型腔表面的温度变化 (模具不预热)
模具优化结果的验证
0.3 0.2 0.1 0
1
2
3
4
5
6
7
8
9
10
Position of thremocouple(10 points)
坯料加热后的组织形貌
中心位置
边缘位置
充型过程的Short shot实验 (快压式)
充型模拟(温度场显示)
模拟与实验的对比
50μm
Combination photo with low magnification Distribution image
铸型/铸件之间换热系数的影响
5000W/m2・K
9500W/m2・K
14000W/m2・K
压铸机的推杆速度的影响
0.1m/s
0.5m/s
0.8m/s
压铸机冲头的位移曲线
400
machine video
400
充型末期和保压阶段
displacement,mm
displacement,mm
machine video
The shape and size of gate are optimized
X-ray inspection(1)
X-ray inspection(2)
结 论(一)
• 系统地比较了压铸过程不同主要因素(溶体/型壁 的摩擦系数,模具型腔的背压,溶体/型壁的换热系 数和压铸机的推杆速度)对充型状态的影响,为确 定后续模拟的主要使用条件打下了基础。 • 通过测试并验证压铸过程的位移曲线较为准确地 推测压铸速度,有益于提高模拟的精度;通过型内 充型轨迹实测和模拟的对比以及引入独特的Short shot实验法为模拟提供了有力的支持和旁证手段。
Short-shot
Simulation
defects analysis
模拟与实验的对比
X-ray inspection Simulated cross-section
充型过程的Short shot实验 (慢压式)
充型模拟(温度场显示)
辅助模具优化
• 因现行模具在快压式的成形条件下,存在着 如上所述的铸造缺陷,通过观察模拟和实验 结果,本研究拟从修改模具型腔局部形状,浇 口(gate)大小和形状等方面寻求优化的工艺 方案,在模拟计算时固定通常的模具预热温 度(523K)和压铸机的推杆速度(0.8m/s)。
结 论(二)
• 试样铸造缺陷的分析与模拟以及Short shot结果 的反复对比表明,流场与缺陷形成有紧密的相关 性,通过流场的模拟可以预测可能产生缺陷的位置 和程度,从而提出改进的方向。 • 利用计算机模拟可以从流场,凝固场的角度优化模 具型腔的设计,准确把握成形的模具条件,在对板 形试样模具实施优化设计后的实践结果充分证明 了计算机模拟在辅助模具设计优化上的有效性和 实用性。 • 在实际复杂汽车零件的试制中有效地使用计算机 模拟法取得了良好的效果,并被作为一种通用的技 术手法得以进一步的验证和确立。
In testing machine
Crack position in diecasting
Analyzing reason by computer simulation
animation
Un-filling area in the front of gate
To optimize design of gating sysytem
模具型腔的局部形状
模拟结果
gate的形状与大小
模 拟 结 果
局部中空的设计
模 拟 结 果
综合改进(1)
模拟结果
综合改进(2)
模 拟 结 果
该处的充满较方 案11明显加快
试样上部大致呈 逐层充填特征
凸台作为局部的最 终充填之处,可望实 现排渣集气的目的
试样上部大致呈 逐层充填特征
凸台作为局部的最 终充填之处,可望实 现排渣集气的目的
缺陷分析
慢压式
快压式
凸台内组织分布
慢压式
快压式
力学性能的对比
模具的 不同 原模具
慢压 221 7.99 平均值
压铸方式 抗拉强度 MPa 207 快压
延伸率 % 4.43
备注
快压
优化后的 模具 慢压
238
265
7.65
10.3
汽车零件的研制 (后桥支撑座)
• A severe demand for desk frame fatigue experiment (all samples>450000 cycles) • A trouble example
充型末期和保压阶段
300 200 100 0 0 500 1000 1500 Time, ms 2000 2500
充型主要阶段
300 200 100 0 0 500
充型主要阶段
预备充 型 ( 含 将料 缸 中的坯料推至模具入 口的预备期)
此前为 推杆空走
1000 Time, ms
1500
慢压式
快压式
850
* Function of solid fraction
Relationship between kinematic viscosity and solid fraction
Solid fraction, % Kinematic Viscosity m2/s 0 1E-06 0-60 Linear inserting value >60 1E-05
研究方法
实验方法
• 实验材料 A356铝合金 • 主要实验工艺过程(制坯-二次加热-压铸)
制造坯料的水平连铸装置
电磁搅拌
多工位旋转式坯料感机
压铸条件
• 模具温度: 523K(250℃) • 坯料温度: 858-863K(585-590℃) • 试样的三维CAD模型, 10个 测试点
铝合金半固态压铸成形过程的模拟
研究背景/目的
• 铝合金半固态压铸(触变成形)研发阶段的工 作虽已接近于成熟,但与充型系统设计有关 数据尚不充分。 • 为改进计算机模拟精度,需要准备一些基本 的参数。 • 辅助充型系统的优化设计,改善零件的质量。
主要内容
• 通过对压铸过程的实验测试和模拟相结合 的方法,确认模拟的初始参数,奠定模拟的 准确性 • 分析和验证典型试样充型流场与铸造缺陷 的关系,优化模具设计 • 实际应用于汽车零件的研发过程,预测缺陷 和对策
半固态流体充型时背压(排气)的影响
物理模型
网格长度单位为1cm
排出的空气
V=A・(c3/L)・(P-P0)・Δt・ΔS
V为空气的体积; A为空气的流动系数; L和c分别是排气口的长度和宽度; P 和P0分别为型内外的空气压力; Δ t和Δ S分别是时间步长和排气面积
有无背压的对比
未考虑背压
考虑背压
力学性能测试
100mm
研究(实验与模拟)结果
半固态流体与型壁之间摩擦系数的影响
f=0
f=0.5
f=1
半固态流体与型壁之间摩擦系数的影响 • 摩擦系数虽然几乎不影响总的充型时间以 及最终汇流的位置,但对流体的表面充型状 态,汇流方式和充型模样存在一定的影响。 因实际摩擦系数的准确测定是十分困难的, 本研究根据反复计算的经验在该阶梯形板 状试样以及其他零件模具的模拟计算中选 择了0.5的摩擦系数。
试制零件的三维CAD模型
Rear bridge support
Forward control arm
Rear bridge support (typeⅠ)
Rear bridge support (typeⅡ)
计算条件
(模拟软件: ADSTEFAN)
Physical properties of Aluminum alloy A356