数控车床的对刀原理及对刀方法
数控机床对刀的方式及其对刀步骤

在进行加工之前,数控车床要进行对刀操作,以便确保产品加工的精度以及准度,在实际进行生产的过程中,数控车床对刀的操作有试切对刀和机外对刀仪这两种对刀方法,但是在进行对刀操作的时候也会出现一些问题,下面我们就来具体介绍一下数控车床对刀的操作步骤。
1、试切对刀试切对刀主要用在建立加工坐标系。
在安装好工件后,为了可以加工出需要的加工件,要将编程原点设定为加工原点,建立加工坐标系,用来确定刀具和工件的相对位置,使刀具按照编程轨迹进行运动,最终加工出所需零件。
试切对刀的步骤主要有:(1)选择机床的手动操作模式;(2)启动主轴,试切工件外圆,保持X方向不移动;(3)停主轴,测量出工件的外径值;(4)选择机床的MDI操作模式;(5)按下“off set sitting”按钮;(6)按下屏幕下方的“坐标系”软键;(7)光标移至“G54”;(8)输入X及测量的直径值;(9)按下屏幕下方的“测量”软键;(10)启动主轴,试切工件端面,保持Z方向不移动;2、机外对刀仪对刀机外对刀仪对刀需要将显微对刀仪固定于车床上,用于建立刀具之间的补偿值。
但是因为刀具尺寸会有一定差别,机床中刀位点的坐标值也会因此而出现不同。
如果不设立刀具之间的补偿值,运行相同的程序时就不可能加工出相同的尺寸,想要保证运行相同的程序时,运用不同的刀具得出相同的尺寸,则需要建立刀具间的补偿。
机外对刀仪对刀的步骤主要有:(1)移动基准刀,让刀位点对准显微镜的十字线中心;(2)将基准刀在该点的相对位置清零,具体操作是选择相对位置显示;(3)将其刀具补偿值清零,具体操作是按下“off set sitting”按钮,按下屏幕下方的“补正”软键,选择“形状”,在基准刀相对应的刀具补偿号上输入Xo、Zo;(4)选择机床的手动操作模式,移出刀架,换刀;(5)使其刀位点对准显微镜的十字线中心;(6)选择机床的MDI操作模式;(7)设置刀具补偿值,具体操作是按下“offset sitting”按钮,按下屏幕下方的“补正”软键,选择“形状”,在相对应的刀补号上输入X、Z;(8)移出刀架,执行自动换刀指令即可。
数控机床的对刀原理及常用的对刀方法

万方数据万方数据2.6百分表(或千分表)对刀法(一般用于圆形工件的对刀)1)并,Y向对刀。
将百分表的安装杆装在刀柄上,或将百分表的磁性座吸在主轴套筒上,移动工作台使主轴中心线(即刀具中心)大约移到工件中心,调节磁性座上伸缩杆的长度和角度,使百分表的触头接触工件的圆周面,(指针转动约0.1mill)用手慢慢转动主轴,使百分表的触头沿着工件的圆周面转动,观察百分表指针的便移情况,慢慢移动工作台的轴和轴,多次反复后,待转动主轴时百分表的指针基本在同一位置(表头转动一周时,其指针的跳动量在允许的对刀误差内,如0.02mm),这时可认为主轴的中心就是轴和轴的原点。
2)卸下百分表装上铣刀,用其他对刀方法如试切法、塞尺法等得到z轴坐标值。
2.6专用对刀器对刀法易撞坏)占用机时多(如试切需反复切量几次),人为带来的随机性误差大等缺点,已经适应不了数控加工的节奏,更不利于发挥数控机床的功能。
用专用对刀器对刀有对刀精度高、效率高、安全性好等优点,把繁琐的靠经验保证的对刀工作简单化了,保证了数控机床的高效高精度特点的发挥,已成为数控加工机上解决刀具对刀不可或缺的一种专用工具。
参考文献:[1]陈志雄.数控机床与数控编程技术[M].北京:电子工业出版社,2007.[2]华中数才全一操作说明书[z].武汉华中数控股份有限公司.[3]任国兴主编.数控铣床华中系统编程与操作实训[M].北京:中国劳动社会保障出版社,2007.传统对刀方法有安全性差(如塞尺对刀,硬碰硬刀尖收稿日期:2009一10—14(上接第38页)通过机床附带的后处理程序后即可得到控制机床运行的代码程序。
创建刀轨选择的加工参数及其他加工信息汇总列在表l中。
表I加工参数及其他加工信息加工设备加工工具直径/mm板料毛坯尺寸/mm3切削连接方式固定好板料,对好刀具后,将加工代码程序输入机床,既可实现壁板零件的自动加工成形。
2.2.4成形零件机床加工完成后,得到的实际零件如图5所示。
数控车床对刀的原理及方法

数控车床对刀的原理及方法一、数控车床对刀的原理:对刀是数控加工中的主要操作和重要技能。
在一定条件下,对刀的精度可以决定零件的加工精度。
同时,对刀效事还直接影响数控加工效丰。
仅仅知道对刀方法是不够的。
还要知道数控系统的各种对刀设置方式,。
以及这些方式在加工程序中的调用方法,同时要知道各种对刀方式的优缺点。
使用条件等。
一股来说,数控加工零件的编程和加工是分开进行的。
数控编程员根据零件的设计图纸,速定一个方便编程的工件坐标系,工件坐标系-般与零件的工艺基准或设计基准重合。
在工件坐标系下进行零件加工程序的编制,对刀时,应使指刀位点与对刀点重合,所谓刀位点是指刀具的定位基准点,对于车刀来说,其刀位点是刀失。
对刀的目的是确定对刀点。
在机床坐标系中的绝对坐标值,测量刀具的刀位偏基值。
对刀点找正的准确度直接影响加工精度。
在实际加工工件时。
使用一把刀具一般不能满足工件的加工要求,通常要使用多把刀具进行加工。
在使用多把车刀加工时,在换刀位置不变的情况下,换刀后刀失点的几何位置将出现差异,这就要求不同的刀具在不同的起始位置开始加工时。
都能保证程序正常运行。
为了解决这个问题。
机床数控系統配备了刀具几何位置补能的功能,利用刀其几何位置补偿功能,只要事先把每把刀相对于某一预先选定的基准刀的位置偏差测量出来,输入到数控系统的刀具梦数补正栏指定组号里,在加工程序中利用T指令,即可在刀具轨述中自动补偿刀具位置偏差。
刀具位置值差的利量同样也需通过对刀操作来实现。
生产厂家在制造数控车床,必须建立位置测量,控制、显示的统基准点。
该基准点就是机床坐标系原点,也就是机床机械目零后所处的位置。
操作方法01数控车床对刀是车床加工技术中比较复杂的工艺之一,它的精度将会直接影响到所加工零部件的精度,所以不能马虎。
02数控车床对刀的基本原理就是将零件的坐标系与数控机床的坐标系整合起来,然后依据这个坐标系来确定对刀位置。
03目前数控车床大部分采用的是对刀器主动对刀,对刀器会自动向零件确定一个原点位置,这是十分方便快捷的对刀方法。
数控机床对刀

(7)将光标移动至欲设定的偏置号处。
(8)输入Zβ(或0)。
(9)按软键[MESURE]。
(10)在手动方式中用一把实际刀具切削外圆。
(11)仅仅在Z方向上退刀,不要移动X,停止主轴。
(12)测量被车削部分的直径D。
(13)按功能键OFFSET/SETING。
(14)按软键[OFFSET]。
实习总结:
用试切法确定起刀点的位置对刀的步骤:
(1)在MDI或手动方式下,用基准刀切削工件端面;
(2)用点动移动X轴使刀具试切该端面,然后刀具沿X轴方向退出,停主轴。
记录该Z轴坐标值并输入系统。
(3)用基准刀切量工件外径。
(4)用点动移动Z轴使刀具切该工件的外圆表面,然后刀具沿Z方向退出,停主轴。用游表卡尺测量工件的直径,记录该X坐标值并输入系统。
(3)对刀点与对刀:对刀点是用来确定刀具与工件的相对位置关系的点,是确定工件坐标系与机床坐标系的关系的点。
对刀就是将刀具的刀位点置于对刀点上,以便建立工件坐标系。
(4)对刀基准(点):对刀时为确定对刀点的位置所依据的基准,该基可以是点、线、面,它可以设在工件上或夹具上或机床上。
(5)对刀参考点:是用来代表刀架、刀台或刀盘在机床坐标系内的位置的参考点,也称刀架中心或刀具参考点。
(5)对第二把刀,让刀架退离工件足够的地方,选择刀具号,重复(1)—(4)步骤。
法拉克车床对刀:
基准刀的对法:
(1)在手动方式中用一把实际刀具切削端面。
(2)仅仅在X轴方向上退刀,不要移动Z轴,停止主轴。
(3)测量工件坐标系的零点至端面的距离β(或0)。
(4)按功能键OFFSET/SETING。
(5)按软键[OFFSET]。
数控车床对刀的原理与方法

数控车床对刀的原理与方法数控车床的刀具对刀是确保机床工作精度的关键步骤之一、对刀准确度影响着工件的加工精度和质量。
数控车床的对刀一般采用刀具测量、感应式对刀、比较式对刀等方式。
下面将介绍数控车床对刀的原理和方法。
1.刀具测量:数控车床通常提供一个专门的测量装置,用来测量刀具的长度和半径。
通过刀具测量装置的读数,可以计算出刀具的几何参数,以便在数控系统中设置正确的刀具补偿值。
2.感应式对刀:数控车床使用感应式传感器,通过与刀具接触或靠近刀具来感应刀具的位置信息。
传感器可以测量到刀具的长度和半径,并将这些信息传递给数控系统。
3.比较式对刀:比较式对刀是通过测量工件上已加工的特征来确定刀具的位置。
例如,在数控车床上面加工一个规定尺寸的槽后,可以使用传感器测量槽的尺寸,然后根据预定的槽尺寸,调整刀具的位置。
根据数控车床对刀的原理,可以采用以下方法进行对刀:1.感应式对刀:数控车床上通常有一个专用的感应式对刀装置。
在对刀过程中,需要选取一把已知长度的刀具,并使用感应式传感器测量其长度。
将测量到的刀具长度输入数控系统,系统会自动计算并设置刀具长度补偿值。
然后,将正确长度的刀具安装到车刀刀架上,依次对各个刀具进行对刀。
2.刀具测量:刀具测量是比较常见的对刀方式。
使用专用的刀具测量设备可以测量刀具的长度和半径。
在对刀过程中,首先选取一把已知长度和半径的刀具,将其放入测量设备中测量。
然后,将测量到的数值输入数控系统,系统会自动计算出刀具的补偿值。
最后,将已校准好的刀具安装到车刀刀架上。
3.比较式对刀:在比较式对刀中,首先需要加工一个已知尺寸的特征,例如一条槽或一组孔。
然后,使用专用的测量仪器测量加工后的特征尺寸。
将测量到的尺寸和预定的尺寸进行比较,计算出相应的补偿值。
最后,根据计算结果调整刀具的位置。
除了上述方法外,还可以使用图形化的数控系统来辅助进行对刀。
通过在数控系统中显示工件轮廓的模拟图像,可以直观地观察刀具的位置与工件轮廓之间的关系,从而调整刀具的位置。
数控车床对刀的原理及方法

数控车床对刀的原理及方法数控车床对刀是指在进行数控加工前,通过调整工具与工件之间的相对位置,使其达到最佳的加工状态,从而确保加工精度和质量。
在进行数控车床对刀时,需要掌握一定的原理和方法。
一、数控车床对刀的原理:数控车床对刀是以工具为基准,通过调整工具与工件之间的相对位置,使其达到预定的加工要求。
数控车床对刀的原理包括工具长度补偿和半径补偿。
工具长度补偿:数控车床对刀时,要考虑工具长度的影响。
在机床的编程中,以工件参考点统一参考工具长度,通过编程输入工具长度补偿值,使操作者无需考虑具体工具长度,直接参照工件参考点与加工长度编程。
半径补偿:数控车床对刀时,还要考虑工具半径的影响。
在机床的编程中,通过编程输入刀具半径补偿值,使操作者无需考虑具体工具半径,直接参照工件轮廓绘制加工轮廓。
二、数控车床对刀的方法:1. 机械对刀法:数控车床对刀时,一般先采用机械对刀法进行初步调整。
具体步骤如下:(1) 选择合适的切削工具,将其装夹到主轴上;(2) 将工件装夹在工作台上,固定好;(3) 调整工具的位置,使其与工件接触;(4) 缓慢移动工具,观察工具与工件的接触情况;(5) 调整对刀量,使工具的刀尖与工件表面轻微接触;(6) 用毛刷或布将切屑清除干净;(7) 检查工具与工件的接触情况,如需调整,继续进行机械对刀。
2. 触发器对刀法:在数控车床上,一般配备有触发器对刀装置。
该装置可以根据工具与工件的相对位置变化,给出相应的触发信号。
具体步骤如下:(1) 在数控系统中,选择相应的对刀程序和参数;(2) 将工具装夹到主轴上;(3) 将工件装夹在工作台上,固定好;(4) 运行对刀程序,使切削工具逐渐接近工件;(5) 当工具与工件发生接触时,触发器将给出触发信号,停止继续靠近;(6) 根据触发信号调整工具位置,以使其与工件的接触减小到最小值;(7) 检查工具与工件的接触情况,如果需要调整,可再次进行触发器对刀。
3. 光电对刀法:光电对刀法是一种非接触式的对刀方法,通过使用光电开关检测刀具的位置与工件的位置关系,以确定最佳的对刀位置。
数控车床对刀
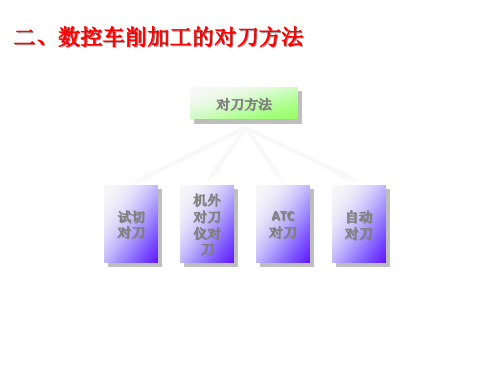
第二步:试切工件端面,把端面在工件坐标系中Z的坐标值,保持Z轴方向不动, 刀具退出。进入形状补偿参数设定界面,将光标移到相应的位置,输入Z0,按 [测量]软键对应的刀具偏移量自动输入 ;
第三步:按照第一、二步对刀方法,对其余2把刀具进行对刀及设置
928TC数控系统 对刀步骤:
第一步:在手动方式下移动刀具在工件上切出一个小台阶。测量所切出的 台阶的直径,按 I 键,屏幕显示 刀偏 X ,输入测量出的直径值,按 Enter 键
3.ATC对刀 它是在机床上利用对刀显微镜自动地计算出车刀长度的简称,
对刀镜与支架不用时取下,需要对刀时才装到主轴箱上。对刀时, 用手动方式将刀尖移到对刀镜的视野内,再用手动脉冲发生器微量 移动使假象刀尖点与对刀镜内的中心点重合(如图所示),再将光 标移到相应刀具补偿号,按“自动计算(对刀)”按键,这把刀具 在两个方向的长度就被自动计算出来,并自动存入它的刀具补偿号 中。
(2) 对刀原理
1
2
X
Z刀补
ZZxx xx
3
φD
X刀补
Xxx
试切一段外圆
Z
FANUC数控系统 对刀步骤:
第一步:用所选刀具试切工件外圆,测量试切后的工件直径,比如记为α,
保持X轴方向不动,刀具退出。点击MDI键盘上
的键,进入形状补偿参
数设定界面,将光标移到与刀位号相对应的位置,输入Xα,按菜单软键[测 量],对应的刀具偏移量自动输入 ;
谢谢观看/欢迎下载
BY FAITH I MEAN A VISION OF GOOD ONE CHERISHES AND THE ENTHUSIASM THAT PUSHES ONE TO SEEK ITS FULFILLMENT REGARDLESS OF OBSTACLES. BY FAITH I BY FAITH
对刀竟然有七种方法

对刀竟然有七种方法导读:数控车床对刀是加工中的重要技能,对刀的准确性决定了零件的加工精度,对刀效率直接影响零件的加工效率,对刀对机床加工操作非常重要。
数控车床开机后,必须进行回零(参考点)操作,其目的是建立数控车床进行位置测量、控制、显示的统一基准,也就是刀具回到机床原点,机床原点通常在刀具的最大正行程处,它的位置由机床位置传感器决定。
机床回零后,刀具(刀尖)的位置与机床原点的距离是固定不变的,因此,为便于对刀和加工,可将机床回零后刀尖的位置看作机床原点。
对刀就是在数控机床的机床坐标系中建立工件坐标系,并使工件坐标系原点与编程原点重合的操作过程。
通过试切或非接触方法测量出机床坐标系中的刀尖编程点距加工原点X和Z 方向的距离,并把数值设置到机床参数中,通过程序调用,建立工件坐标系,程序中基点的绝对坐标值就是以建立的工件坐标系的原点为原点的,加工出零件的轮廓。
一、对刀原理对刀的目的是为了建立工件坐标系,直观的说法是,对刀是确立工件在机床工作台中的位置,实际上就是求对刀点在机床坐标系中的坐标。
对于数控车床来说,在加工前首先要选择对刀点,对刀点是指用数控机床加工工件时,刀具相对于工件运动的起点。
对刀点既可以设在工件上(如工件上的设计基准或定位基准),也可以设在夹具或机床上,若设在夹具或机床上的某一点,则该点必须与工件的定位基准保持一定精度的尺寸关系。
对刀时,应使指刀位点与对刀点重合,所谓刀位点是指刀具的定位基准点,对于车刀来说,其刀位点是刀尖。
对刀的目的是确定对刀点(或工件原点)在机床坐标系中的绝对坐标值,测量刀具的刀位偏差值。
对刀点找正的准确度直接影响加工精度。
在实际加工工件时,使用一把刀具一般不能满足工件的加工要求,通常要使用多把刀具进行加工。
在使用多把车刀加工时,在换刀位置不变的情况下,换刀后刀尖点的几何位置将出现差异,这就要求不同的刀具在不同的起始位置开始加工时,都能保证程序正常运行。
为了解决这个问题,机床数控系统配备了刀具几何位置补偿的功能,利用刀具几何位置补偿功能,只要事先把每把刀相对于某一预先选定的基准刀的位置偏差测量出来,输入到数控系统的刀具参数补正栏指定组号里,在加工程序中利用T指令,即可在刀具轨迹中自动补偿刀具位置偏差。
数控车床对刀原理及对刀方法分析

中图分 类号 :T G5 1 9 . 1
一
文献标 识码 :A 文章编号 :1 0 0 3 — 9 0 8 2( 2 0 1 3 )0 6 — 0 0 1 7 — 0 1
动 的起点 。 当前数 控车床编 程坐标 系的确定 方法通过 G指令完成 ,不 同标 准 中的指令 略有不 同。在编程 坐标 系建立后 ,其本 身 与机 床 的坐 标系 没有联 系 ,两 者仍 然处 于相互 独立 的状 态 。此 时 , 数控 车床 的数控 系统 不能识 别零件在 机床 中 的位 置 ,同时也不 能识 别 刀具 刀尖 A的位置 。只 有确 定 了 A点 和机 床原 点 0的 关系 ,才能 实现零件 的加工 。机床坐 标系 和零件 坐标 系之 间的 p ,z =L0 +L+zp 关系为 :X=X 3 . 对 刀参考 点和对刀 过程 T点 是对 刀具进 行调 校 的一 个重要 参考 点 ,数控 车床 通过 对 T点 的控制 ,来完 成刀具 的运行 。对刀过程 其实是 刀具 偏值
二 、 数控 车床 对 刀原 理
数 控车 床的对 刀问题 已经成 为数 控车床 加工 和设 备调整 的 难点 ,阻碍 了加 工的精 确度 和效 率 。其实 ,对刀 就是 确定刀 具 位置 的坐标 系 ,也 就是求偏 差值 。 因此 对刀 原理 围绕着 求偏 差 值展 开 。 1 . 车床坐 标系 和参考点 的确定 数控 车床 的坐标 系 以机床 原点 为坐 标原 点建立 ,如 图 1 所 示 ,其 中 0为 机床 的原 点 ,0。 为零件 的原 点 ,B点 为起 刀点 , T为 对刀 参考点 ,L 0 是卡盘 的厚 度 ,L为所 加工 零件 伸 出卡盘 的长度 ,d为零 件 的直径 ,从 机床 原点 出发作 x, z两个方 向与 对 刀 的参 考点 T形成 动态 坐标值 ,另外 ,R为车床参 考点 。
数控车床对刀方法

数控车床对刀方法一、对刀对刀的目的是确定程序原点在机床坐标系中的位置,对刀点能够设在零件上、夹具上或机床上,对刀时应使对刀点与刀位点重合。
数控车床常用的对刀方法有三种:试切对刀、机械对刀仪对刀〔接触式〕、光学对刀仪对刀〔非接触式〕,如图3-9 所示。
1、试切对刀1 〕外径刀的对刀方法如图3-10 所示。
Z 向对刀如(a) 所示。
先用外径刀将工件端面( 基准面) 车削出来;车削端面后,刀具能够沿X 方向移动远离工件,但不可Z 方向移动。
Z 轴对刀输入:〝Z0 测量〞。
X 向对刀如(b) 所示。
车削任一外径后,使刀具Z 向移动远离工件,待主轴停止转动后,测量刚刚车削出来的外径尺寸。
例如,测量值为Φ50.78mm, 那么X 轴对刀输入:〝X50.78 测量〞。
2 〕内孔刀的对刀方法类似外径刀的对刀方法。
Z 向对刀内孔车刀轻微接触到己加工好的基准面〔端面〕后,就不可再作Z 向移动。
Z 轴对刀输入:〝Z0 测量〞。
X 向对刀任意车削一内孔直径后,Z 向移动刀具远离工件,停止主轴转动,然后测量已车削好的内径尺寸。
例如,测量值为Φ45.56mm, 那么X 轴对刀输入:〝X45.56 测量〞。
3 〕钻头、中心钻的对刀方法如图3-11 所示。
Z 向对刀如〔a 〕所示。
钻头( 或中心钻) 轻微接触到基准面后,就不可再作Z 向移动。
Z 轴对刀输入:〝Z0 测量〞。
X 向对刀如〔b 〕所示。
主轴不必转动,以手动方式将钻头沿X 轴移动到钻孔中心,即看屏幕显示的机械坐标到〝X0.0 ”为止。
X 轴对刀输入:〝X0 测量〞。
2、机械对刀仪对刀将刀具的刀尖与对刀仪的百分表测头接触,得到两个方向的刀偏量。
有的机床具有刀具探测功能,即通过机床上的对刀仪测头测量刀偏量。
3、光学对刀仪对刀将刀具刀尖对准刀镜的十字线中心,以十字线中心为基准,得到各把刀的刀偏量。
二、刀具补偿值的输入和修改依照刀具的实际参数和位置,将刀尖圆弧半径补偿值和刀具几何磨损补偿值输入到与程序对应的储备位置。
数车的对刀方法

• Z 向对刀如 ( a )所示。钻头 ( 或中心钻 ) 轻微接触到基准面后, 就不可再作 Z 向移动。 Z 轴对刀输入: “ Z0 测量”。 X 向对刀 如( b )所 示。主轴不必转动,以手动方式将钻头沿 X 轴移动到钻 孔中心,即看屏幕显示的机械坐标到“ X0.0 ”为止。X 轴对刀输入: “ X0 测量 ”。 2、机械对刀仪对刀 将刀具的刀尖与对刀仪的百分 表测头接触,得到两个方向的刀偏量。有的机床具有刀具探测功能, 即通过机床上的对刀仪测头测量刀偏量。 3、光学对刀仪对刀 将刀 具刀尖对准刀镜的十字线中心,以十字线中心为基准,得到各把刀的 刀偏量。二、 刀具补偿值的输入和修改 根据刀具的实际参数和位 置,将刀尖圆弧半径补偿值和刀具几何磨损补偿值输入到与程序对应 的存储位置。如试切加工后发现工件尺寸不符合要求时,可根据零件 实测尺寸进行刀偏量的修改。例如测得工件外圆尺寸偏大 0.5mm , 可在刀偏量修改状态下,将该刀具的 X 方向刀偏量改小 0.25mm。
数车
• 数控车的对刀方法
• 一、对刀 对刀的目的是确定程序原点在 机床坐标系中的位置,对刀点可以设在零 件上、夹具上或机床上,对刀时应使对刀 点与刀位点重合。 数控车床常用的对刀 方法有三种:试切对刀、机械对刀仪对刀 (接触式)、光学对刀仪、 试切对刀1 )外径刀的对刀方法 如图 3-10 所 示。 Z 向对刀如 (a) 所示。先用外径刀将工件端面 ( 基 准面 ) 车削出来;车削端面后,刀具可以沿 X 方向移动远 离工件,但不可 Z 方向移动。 Z 轴对刀输入:“ Z0 测 量”。 X 向对刀如 (b) 所示。车削任一外径后,使刀具 Z 向移动远离工件,待主轴停止转动后,测量刚刚车削出 来的外径尺寸。例如,测量值为 Φ 50.78mm, 则 X 轴对 刀输入:“ X50.78 测量 ”。 2 )内孔刀的对刀方 法 类似外径刀的对刀方法。 Z 向对刀内孔车刀轻微 接触到己加工好的基准面(端面)后,就不可再作 Z 向移 动。Z 轴对刀输入:“ Z0 测量 ”。 X 向对刀任意车削 一内孔直径后,Z 向移动刀具远离工件,停止主轴转动, 然后测量已车削好的内径尺寸。例如,测量值为 Φ 45.56mm, 则 X 轴对刀输入:“ X45.56 测量 ” 。 3 ) 钻头、中心钻的对刀方法 如图 3-11 所示。
数控车对刀操作

本课学习对刀过程中是先对的X轴坐标, 然后对Z轴坐标。可以不可以先对Z轴坐标, 然后对X轴坐标?
1、试切对刀的几个步骤
2、退刀的时候坐标轴一定原路退回 2、测量一定要准确 3、输入坐标数据的时候不要输错
通过学习对刀的操作结合对刀的几个 步骤。自己归纳并总结对刀的方法,后在 数控机床上进行实际对刀操作。
返回
上页
下页
图库
看一看数控加工产品
返回
上页
下页
图库
目录
一、对刀的几种方式 二、试切 对刀法 详细讲解
返回
上页
下页
图库
一、对刀的几种方式
1、试切 对刀法 2、定点对刀法 3、自动对刀法(自动对刀仪器)
返回
上页
下页
图库
二、试切对刀法
试切对刀法的步骤:
1、在机床上装夹好试切工件,选择一把刀具安装在刀架 上(一般习惯把刀按在第一个刀位号上)。
Hale Waihona Puke 2、选择合适的 主轴转速(一般在S600~S800),启动 主轴,在手动或手脉的方式下移动(进给倍率在2%~ 10%)刀具向Z负方向移动在工件上切出一个小的台阶。
3、在X轴不移动的情况下沿Z正方向将刀具移到安全位置 停止主轴(按原路退出刀具)。
返回
上页
下页
图库
4、 测量所切出台阶的直径,在操作面板上按刀补 刀具偏 置磨损界面 在X轴的对话框内输入测量的值(直径) 确认。
数控车对刀操作
一、引入
在数控加工零件中,数控车床为了默认我们 编写程序加工我们需要的零件,所以我们就需要 在工件上人为的找一个基准坐标点,只有找准了 一个基准点,在加工中数控车床就以找到基准坐 标来进行加工,所以我们就需要对刀,对刀是数控 加工中的主要操作方法和重要技能,对刀的准确性 决定零件加工精度。
数控车床对刀方法

数控车床对刀方法数控车床是一种高精度、高稳定性的机械设备,广泛应用于制造、加工、雕刻等各个方面。
但是在使用数控车床进行加工时,对于刀具的刀具、工件的工件必须进行正确的调整和校准,以确保加工的精度和效率。
本文将介绍数控车床对刀的方法,包括刀具对刀、辅助装置调整等方面。
一、数控车床对刀前的准备在进行数控车床对刀前,需要进行一些准备工作,以确保切削工具和工件位置准确,保证工作效率和准确性。
对刀前的准备包括以下几个方面:1. 确认刀具几何参数。
根据加工任务选择不同类型的刀具,并确认数控车床上的刀具几何参数,包括半径、长度、角度等。
2. 清洁工件表面。
工件表面必须干净无杂物,以确保切削齿能够充分接触工件表面,以达到更好的切削效果。
3. 机械调整。
数控车床必须先进行机械调整,包括机床导轨的润滑、机床组件的紧固、丝杆的调整等。
4. 确认刀具和工件位置。
确认数控车床上刀具和工件的安装位置,切削刀具必须与工件表面平行,刀具运动方向与切削方向垂直。
二、数控车床对刀方法1. 刀具对刀法刀具对刀是数控车床最常用的对刀方式,实现方式为将要使用的刀具与一根对比长度相同的比较条对齐,进行校准。
刀具对刀法需要的材料包括:切削刀具、比较条、扳手等。
(1)确定比较条。
比较条是一根长度与要对刀的切削刀具相等的条形物,可以是一根判断曲线的铁条或是一根可以摆动的比钢板,其作用是通过与要对刀的刀具进行比较,以确定刀具的位置和角度。
(2)摆放比较条。
将比较条放在工件表面平行的位置上,并用卡盘或夹具固定好,确认比较条与工件表面平齐,并将比较条从左至右图4.6-1。
(3)调整刀具。
将切削刀具固定在刀架上,并使用扳手调整刀具位置和角度,使之与比较条平行,并且与工件表面垂直,保证刀具切削齿与工件表面接触充分。
(4)测量刀具位置。
使用卡尺或其它测量工具,测量刀具的位置和长度,与比较条长度相同或偏差很小的范围内,说明刀具位置已调整正确,并可以进行下一步工序。
数控车床对刀方法

对刀操作加工一个零件常需要几把不同的刀具,由于刀具安装及刀具偏差,每把刀具在切削位置时,其刀尖所处位置并不完全相同。
为此,根据零件图纸及加工工艺编写工件程序,只需要在编写程序的换刀指令中调用相应的刀具补偿。
<一>.定点对刀(1)将基准刀具的刀尖定位到标准点(2)复位相对坐标(U,W),使其坐标值为零(3)选择基准刀对应的偏置号(按刀偏键)(4)按X0,按IN,按Z0,按IN,使基准刀对应的偏置量为零(5)移动实际加工用的刀具并定位到基准点在选择偏置号后,按X或U,和Z或W,IN,则相对坐(6)标值被置到相应的偏置号中。
相应地,标准刀具和实际刀具的差别被指示出来重复步骤(6),可找出其它刀偏<二>.试切对刀(1)用基准刀试切工件设定基准坐标系a.按【刀补】设基准刀偏置号(如:001),X,Z值清零b.主轴旋转,用手动方式,沿X轴切削c.主轴停止,进入录入方式,按【程序】,输入G50,Z0,按启动键(此时相对坐标Z显示为0)d.主轴旋转,用手动方式,沿Z轴切削e.主轴停止,测量直径值(比如:φ25)进入录入方式,按【程序】,输入G50,X25,按启动键(此时相对坐标X显示为25)(2)非基准刀偏置设置a.设对刀偏置号(如:003),X,Z值清零b.轴旋转,用手动方式,沿X轴切削c. 主轴停止,按【刀补】输入Z0,按输入键,刀补值自动计算并输入d.主轴旋转,用手动方式,沿Z轴切削e.主轴停止,按【刀补】,测量直径值(比如:φ25),输入X25,按输入键,刀补值自动计算并输入三、刀补(偏)设置工作方式本系统设置了T1~T9共9组刀偏值,每组刀偏有Z轴、X轴方向两个数据。
其中的可通过手动对刀操作自动生成的刀偏组数量是使用的刀具总数相同,其余的刀偏数据只能通过键盘输入。
1、刀偏数值的检索在刀偏工作方式中可以查看每个刀偏值的具体内容。
按“向上”、“向下”光标移动键可以检索前一个或后一个刀偏值。
数控车床对刀培训课件.ppt

精品课件
二、刀具补偿指令
刀具补偿指令由刀具功能 T 设定。
T 指令后跟四位数,前两位是刀具号,后两位是刀具补偿号。刀具补偿 号实际上是刀具补偿器的地址号。该寄存器存有刀具补偿量。数控车床 试切对刀主要是设置刀具几何补偿。
设定偏置号处。F10→F4→F2 3、在试切长度下输入0,则自动显示该把刀在Z方向刀补。
精品课件
数控车床对刀
三、试切法对刀步骤
精品课件
数控车床对刀
三、试切法对刀步骤
4、用第一把刀试切工件外圆,仅仅在Z轴方向退刀,停止主轴。 5、测量直径,按MDI子菜单下的刀偏表,显示刀具补偿画面,移
动光标至欲设定偏置号处。在试切直径下输入测量值,
三、试切法对刀步骤
精品课件
数控车床对刀
数控车床对刀
江苏大学无锡机电学院
精品课件
一、对刀定义和原理
1、定义 所谓对刀,其实质就是侧量程序原点与机床原点之间的偏移距离
并设置程序原点在以刀尖为参照的机床坐标系里的坐标。 对刀是数控加工中的主要操作和重要技能。对刀的准确性决定
了零件的加工精度,同时,对刀效率还直接影响数控加工效率。
2、原理 编程员按程序坐标系中的坐标数据编制刀具(刀尖)的运行轨迹
T指令代码说明如下: T XX XX
刀具号 刀具补偿号
如: T 01 01 1号刀 1号刀具补偿
精品课件
数控车床对刀
三、试切法对刀步骤
精品课件
数控车床对刀
三、试切法对刀步骤
数控机床对刀的原理分析以及常用对刀方法

数控机床对刀的原理分析以及常用对刀方法进行数控加工时,数控程序所走的路径均是主轴上刀具的刀尖的运动轨迹。
刀具刀位点的运动轨迹自始至终需要在机床坐标系下进行精确控制,这是因为机床坐标系是机床唯一的基准。
编程人员在进行程序编制时不可能知道各种规格刀具的具体尺寸,为了简化编程,这就需要在进行程序编制时采用统一的基准,然后在使用刀具进行加工时,将刀具准确的长度和半径尺寸相对于该基准进行相应的偏置,从而得到刀具刀尖的准确位置。
所以对刀的目的就是确定刀具长度和半径值,从而在加工时确定刀尖在工件坐标系中的准确位置。
对刀仪演示视频(时长1分10秒,建议wifi下观看)一、对刀的原理和对刀中出现的问题1、刀位点刀位点是刀具上的一个基准点,刀位点相对运动的轨迹即加工路线,也称编程轨迹。
2、对刀和对刀点对刀是指操作员在启动数控程序之前,通过一定的测量手段,使刀位点与对刀点重合。
可以用对刀仪对刀,其操作比较简单,测量数据也比较准确。
还可以在数控机床上定位好夹具和安装好零件之后,使用量块、塞尺、千分表等,利用数控机床上的坐标对刀。
对于操作者来说,确定对刀点将是非常重要的,会直接影响零件的加工精度和程序控制的准确性。
在批生产过程中,更要考虑到对刀点的重复精度,操作者有必要加深对数控设备的了解,掌握更多的对刀技巧。
(1)对刀点的选择原则在机床上容易找正,在加工中便于检查,编程时便于计算,而且对刀误差小。
对刀点可以选择零件上的某个点(如零件的定位孔中心),也可以选择零件外的某一点(如夹具或机床上的某一点),但必须与零件的定位基准有一定的坐标关系。
提高对刀的准确性和精度,即便零件要求精度不高或者程序要求不严格,所选对刀部位的加工精度也应高于其他位置的加工精度。
选择接触面大、容易监测、加工过程稳定的部位作为对刀点。
对刀点尽可能与设计基准或工艺基准统一,避免由于尺寸换算导致对刀精度甚至加工精度降低,增加数控程序或零件数控加工的难度。
数控车床的对刀原理及对刀方法

系。
点 0 的位置 ,即刀具相对于工件运动的起始点。如图 l B点,图 l 中 B点与 A点重合。工件坐标系的建立实 际上是确定刀具起刀点相对于工件原点 的坐标值 的过
程。 ③工件坐标 系建 立。 目前数控车床上建立工件 坐 标系 的 方 法 一般 用 相 应 的 G指 令 来 设 定 ( 如 , 例 FN C G0 A U 用 5 指令 ,I S O标准中为 C 2 。 9) _
标系。 ②起刀点 B ( 又称程 序起点)—— 即刀具刀位点 A( 如图 l 中车刀 的刀位点为 刀尖 A点)相对工件愿
所建立的坐标系。数控车床的机床 原点通常取在卡盘 前端面与主轴 中心线交点处 ( 图 l 如 中O点) 。一般机 床原点在数控车床 出厂前 由生产厂家 已经调 整好,一
() 工件 坐标 系与 起 刀点 2
当工件坐标系建 立以后 .并未与机床坐标 系发 生 任何联系 ,此时,两者仍然相互 独立,数 控系绕既不 知道工件在机床中的位置 ,也不知道刀具刀位点 A在 机床 中的位置 ,即无 法按所编程序正确加工 ,因此加 工之前 ,还必须确定刀具刀位点 A与机 床坐标 原点 O
《 机床 与液压)20 .03 0 2 H
—19 ・ 7
数控 车床 的对 刀原理 及 对刀 方法
陈 光 明 , 吴 洪彬
( 南京农业大学农业工程学院,江苏南京 203 ) 1 2 0
摘要 :本 文分析 了数控车床 的对刀原 理,并从 实用角度分析介绍 了几 种常用的对刀方法。 关 建词:数控车床 ;坐标系 ;参考点 ;对 刀法 中田分类号 :嘶 1 9 文献标识码 :B 文章编号 :1 1 3 8 2 0 】3 7 3 0 — 8 1 f02 —1 0 9—
- 1、下载文档前请自行甄别文档内容的完整性,平台不提供额外的编辑、内容补充、找答案等附加服务。
- 2、"仅部分预览"的文档,不可在线预览部分如存在完整性等问题,可反馈申请退款(可完整预览的文档不适用该条件!)。
- 3、如文档侵犯您的权益,请联系客服反馈,我们会尽快为您处理(人工客服工作时间:9:00-18:30)。
{万方数据《机床与液压》!##!J B8J$数控车床的对刀原理及对刀方法陈光明,吴洪彬(南京农业大学农业工程学院,江苏南京 !"##$!)摘要:本文分析了数控车床的对刀原理,并从实用角度分析介绍了几种常用的对刀方法。
关键词:数控车床;坐标系;参考点;对刀法・ =<; ・中图分类号:%&’"(文献标识码:)文章编号:"##" * $++"(!##!)$ * ",( * $!"#$%#&’() *$+ ,(-./+) /0 !"()(--#$1 23--(" #$ * 42 5*-.(-./01 &23014501,62 7801950(:;.88< 8= >1?5;2<@2?/ A010//?501,B30C501 >1?5;2<@2?/ D05E/?F5@G ,B30C501 !"##$!,-.503)67)-"*%-:%./ H?50;5H</F 8= H?/F/@@501 ;2@@/? 50 3 B- <3@./ 3?/ 303<GF/I ,30I F/E/?3< 2F/=2< 4/@.8IF 8= H?/F/@@501 ;2@@/? 3?/ 3<F8 H?/F/0@/I 50 @.5F H3H/?J8(9:/"+):B- <3@./;-88?I503@/ FGF@/4;K/=/?/0;/ H850@;L?/F/@@501 ;2@@/? 4/@.8I数控车床的对刀问题一直是一个难题,这一问题 已成为数控加工中的“瓶颈”,阻碍了数控加工效率和 质量的提高。
为此,本文分析了数控车床的对刀原理, 并从实用角度介绍了几种常用的对刀方法。
!工件坐标系(又称为编程坐标系)———是指以 工件原点(或称编程原点)为坐标原点所建立的坐标 系。
编程坐标系,供编程用,是人为设置的。
工件原点可以是工件上任意点,但为了编程,方便数值计算, !数控车床的对刀原理一般数控车床编程原点选工件右端面或左端面与中心 所谓对刀,就是在数控车床进行切削加工之前需 要确定每一把刀具的刀位点在工件坐标系和数控车床 坐标系中的位置,也就是求刀偏值。
(")数控车床坐标系与数控车床参考点数控车床坐标系———是指以机床原点为坐标原点 所建立的坐标系。
数控车床的机床原点通常取在卡盘 前端面与主轴中心线交点处(如图 " 中 M 点)。
一般机 床原点在数控车床出厂前由生产厂家已经调整好,一 般不允许用户随意变动。
如图 " 中 NMO 为机床坐标 系。
数控车床参考点———是指刀架上某一固定点,即 对刀参考点 %(如图 " 中 % 点)退离距机床原点 M 最 远的一个固定点 K 点(如图 " 中 K 点)。
该 K 点在机 床出厂时也由生产厂家调试好,并将数据输入到数控 系统中。
因此机床参考点 K 对机床原点 M 的坐标是一 线交点作为工件原点(如图 " 中 M H 点)。
如图 " 中 N L M L O L 为工件坐标系。
数控编程时应首先确定工件坐 标系。
"起刀点 )(又称程序起点)———即刀具刀位点 >(如图 " 中车刀的刀位点为刀尖 > 点)相对工件原 点 M L 的位置,即刀具相对于工件运动的起始点。
如图 " 中 ) 点,图 ") 点与 > 点重合。
工件坐标系的建立实 际上是确定刀具起刀点相对于工件原点的坐标值的过 程。
#工件坐标系建立。
目前数控车床上建立工件坐 标系 的 方 法 一 般 用 相 应 的 & 指 令 来 设 定(例 如, P>BD- 用 &’# 指令,Q:M 标准中为 &(!)。
如图 " 所示,假设刀具起点相对于工件坐标系的 坐标值为( !#、"# )则执行该程序段后,即建立了工 件坐标系 N L M L O L 。
个已知数,一个固定值。
一般对刀之前,必先使数控 例如:B#"#&’#! !# " "#;车床进行“回零”操作(即使刀架返回参考点操作), 就是使刀架上对刀参考点 % 与机床参考点 K 重合。
此 时 -K% 屏幕上显示值 !、" 即为机床参考点 K 相对于机 床原点 M 点在 N 方向和 O 方向的值。
此时,若再次对 机床进行手动操作时,例如,使刀架向工件靠近时, 此时 -K% 屏幕上显示值为刀架上对刀参考点 % 相对于 机床原点 M 点在 N 向、O 向上的值(即对刀参考点 % 当工件坐标系建立以后,并未与机床坐标系发生任何联系,此时,两者仍然相互独立,数控系统既不 知道工件在机床中的位置,也不知道刀具刀位点 > 在 机床中的位置,即无法按所编程序正确加工,因此加 工之前,还必须确定刀具刀位点 > 与机床坐标原点 M 之间的关系,即一般加工之前通过对刀方法来实现。
如图 " 所示数控车床的二种坐标系即机床坐标系 NMO 在机床坐标系中的坐标值 !、" )。
数控车床参考点 K 点的位置由设置在机床 O 向和 N 向滑板上的机械挡块通过行程开关来确定,刀架返 与工件坐标系 N L M L O L 之间关系如下:! # !$" # 卡盘厚度 %& ’ 工作外伸长度 % ’ ($(")回参考点时由挡块压下相应行程开关向数控系统发出 信号,即停止滑板运动,完成返回参考点操作。
(!)工件坐标系与起刀点($)对刀参考点及对刀过程!对刀参考点 %———是指数控机床加工时,校准 刀具相对工件运动起点的一个刀具参考点,数控车床・#"!・《机床与液压》%##%8 *981 上常取刀架上某一固定点作为车刀的对刀参考点(如! 对刀方法图!中"点)。
数控系统通过控制该点运动,间接地控制每把刀的刀尖运动。
!对刀过程:刀偏值的设置过程称为对刀操作。
数控车床加工时,首先应按编程所确定的刀具刀位点相对工件原点的尺寸值(!#、"#)来校准刀位点起始位置。
对于多刀作业数控车床,由于每把刀的刀尖就其各自安装位置相对于对刀参考点“"”点在两个坐标方向的位置均不同,即每一把刀具的刀位点不可能调整到同一坐标点上,为此这就需要确定各刀具刀位点$相对于对刀参考点"的刀偏值(如图!中#!、#%)并输入到相应刀偏寄存器中,这一过程就称为对刀过程。
在加工程序中调用刀具时,数控系统会自动补偿两个方向&、’的刀偏值(刀具位置补偿量)从而准确地控制每把刀的刀尖轨迹———即使各把不同位号上的不同刀具的刀尖在加工零件执行程序时,处于同一个位置上,这样给加工与编程带来很大的方便。
(()刀具位置补偿及刀偏值的设定原理"刀具位置补偿。
刀具位置补偿又称为刀具位置偏置补偿。
下列三种情况下,均须进行刀具位置的偏置补偿:一是在实际加工中,通常是各把不同位置的若干把刀具(即各把刀具的刀尖在刀架上相对于某固定点的位置各不相同)加工同一轮廓尺寸的工件,而编程时,往往都建立统一的坐标系,要求使所有的刀尖都移到坐标系中的一个基准点上,或者以一把刀为基准设定工件坐标系,因此须将其余刀具的刀尖都偏移到此基准刀尖位置上。
利用刀具位置补偿即可完成;二是对同一把刀具而言,当刀具重磨或更换新刀后,再把它准确地安装到程序所设定的原位置,是非常困难的,总是存在位置误差,这个位置误差,在实际加工后,即成为加工误差,此时,需通过刀具位置补偿功能来修正刀具安装位置误差;三是每把刀具在使用过程中都有不同程度的磨损,而磨损后的刀尖位置与编程位置存在差值,同样会造成加工误差,这种误差,也可通过刀具位置补偿功能来纠正。
!刀偏值的设定原理。
各类数控机床的对刀方法各异,但其原理与目的一致:即通过对刀操作,将刀偏值人工算出后输入)*)系统;或把对刀时屏幕显示的有关数据直接输入)*)系统,由系统自动换算出刀偏值存入刀具数据库。
如图%为数控车床试切对刀原理图。
图中&+’为机床坐标系,&,+,’,为工件坐标系。
在手动、对刀状态下,)-"动态坐标为刀具参考点“"”在机床坐标系内的坐标值(!,")。
刀偏值(#!、#%)可通过下式目前数控车床常用对刀的方法有试切对刀法和对刀仪自动对刀法等。
(!)试切对刀法对刀前,应先进行手动机床回参考点操作。
然后按图1所示,将一工件毛坯夹持于卡盘上,测出$、#,启动机床,以手动方式进行对刀(以2#3外圆车刀为例)。
"将车刀刀尖与棒料端面轻轻接触对刀,然后’向不动,&向退出车刀,记下)-"动态坐标值"。
!将车刀刀尖与棒料外圆轻轻接触对刀,然后&向不动,’向退出车刀,记下)-"动态坐标值!。
#计算刀偏值(#!,#%)。
由于!、"、$、##、#已知,代入公式(%)式计算即可计算出#%、#!的值。
$将刀偏值(#!、#%)输入)*)系统中。
刀具补偿值输入到数控系统后,刀具的运动轨迹便会自动校正。
对于多刀加工时,其它各刀的对刀过程一样,将各刀的刀偏值分别输入相应刀偏寄存器中供数控系统补偿使用。
也可以以第一把刀的刀位点作为基点,将其余各刀的刀位点相对第一把刀的偏差值作为补偿值。
用上述方法对刀,实质上是使每把刀的刀尖与工件外圆母线与端面的交点接触,利用这一交点为基准,算出各把刀的刀偏量。
采用试切法对刀时,精确对刀的方法是:手动对刀时,将工件试件端面、外圆车一刀,并仔细测量试件伸出卡盘长度#、试切外圆直径$,并降低进给速度,并使每把刀对刀接触工件的程度尽可能统一,可有效提高试切对刀的精度。
采用试切法对刀优点是无需特殊对刀工具,操作者只需按常规操作,简便快速,有时! 4 %567就能对出一把刀,而且较为正确有效。
(%)对刀仪自动对刀法在数控车床某固定位置上(如车床主轴箱)固定一显微对刀镜支架,上装显微镜,显微镜的十字线交点位于机床坐标系的一固定点上(即与机床参考点或机床原点位置固定并已知)。
测量时只需将刀架上各刀具的刀位点(车刀刀尖)分别对准显微对刀镜的十字线交点,数控系统便能自动算出刀位点相对机床原点的距离,并把这些数据寄存起来,在加工时自动把刀尖相对于机床原点的距离加进去。
采用对刀仪自动对刀系统,对一把刀一般只需一分钟左右,对刀速度快,而且对刀精度高,大大减少计算:#% . ! / $#!万方数据# 0 #)(%)了数控车削加工的辅助时间,有效提高了劳动生产率和车削加工质量。