FFX成型技术的先进性分析
电火花成形加工技术的研究现状和发展趋势

电火花成形加工技术的研究现状和发展趋势电火花成形加工技术是一种利用电火花在工件表面放电形成微小孔洞的加工方法,广泛应用于制造业的精密加工领域。
本文将对电火花成形加工技术的研究现状和发展趋势进行分析。
电火花成形加工技术最早于19世纪末提出,并在20世纪50年代进行了实践应用。
随着电气放电技术的不断发展,此技术得以推动,并在精密模具、航空航天零部件、汽车制造和生物医疗器械等领域得到广泛应用。
电火花成形加工技术的研究现状主要集中在以下几个方面:第一,放电参数研究。
通过调整电压、电流、脉冲宽度和频率等参数,可以控制电火花放电的能量和形态,从而实现对工件表面的精细加工。
研究者通过实验和仿真等方法,探索最优的放电参数组合,以提高加工效率和加工质量。
第二,电极材料研究。
电极是电火花成形加工中的重要组成部分,其材料的选择直接影响到放电效果和加工质量。
研究者通过对不同材料的电极进行比较试验,确定最适合不同工件材料和加工需求的电极材料,并研究其表面处理技术,以提高耐磨性和放电稳定性。
第三,放电脉冲控制技术研究。
电火花成形加工中,放电脉冲的控制对于形成精细的加工效果至关重要。
研究者通过改变脉冲参数的波形、幅值和频率等,可以实现微细加工和纳米加工,进一步提高加工的精度和表面质量。
第四,放电液的优化研究。
电火花成形加工中常常使用放电液来冷却工件和电极,并清除放电过程中产生的氧化物和熔融物。
研究者通过改变放电液的成分和性能,可以改善放电的稳定性和加工质量。
电火花成形加工技术的未来发展趋势主要体现在以下几个方面:第一,提高加工效率和精度。
随着工件精度要求的不断提高,电火花成形加工技术需要进一步改进,以实现更高的加工效率和更好的加工精度。
研究者将继续优化放电参数和脉冲控制技术,以提高加工速度和形成更精细的加工效果。
第二,拓展加工材料范围。
目前电火花成形加工主要应用于金属和合金材料,但随着复合材料、陶瓷材料和高性能材料的不断发展,对于电火花成形加工技术的要求也越来越高。
快速成形技术发展状况与趋势

快速成形技术发展状况与趋势快速成形技术,又称为三维打印、增材制造等,是近年来新兴的一种制造技术,它可以将数字化的设计文件转化为实体物体,而且速度快、成本低,能够满足个性化定制的需求。
该技术的发展已经引起海内外制造业的广泛关注和研究,下面介绍快速成形技术的发展状况和趋势。
快速成形技术最早出现在20世纪80年代,最初被用于快速制作模型,其发展始于CAD 设计技术、计算机组成技术以及材料工程技术的发展。
20世纪90年代以后,该技术经过不断的改良和完善,应用范围逐渐扩大,主要涉及到汽车、航空、医疗、建筑等领域。
目前,全球主要的快速成形技术公司有美国Stratasys、德国EOS、瑞典Arcam和中国沃特玛等。
近年来,随着材料科技、智能制造和数字工厂的发展,快速成形技术呈现出以下几个趋势:1. 多材料、多工艺:不同快速成形技术采用不同材料和工艺,未来发展方向是多材料、多工艺的结合。
例如,增材制造可以利用多种材料打印出复杂的组件,立体光绘可以通过多重叠加实现更高的可塑性和更精细的表面质量。
2. 智能化、网络化:快速成形技术已经与计算机、互联网和智能化制造相结合,实现了数字化和智能化的设计与制造,未来将趋向于更加智能化和网络化,实现生产和流程的自动化。
例如,智能打印机具有自我诊断和自动修复的功能,可以自主管理并调节打印参数,提高设备利用率和打印效率。
3. 个性化、定制化:快速成形技术具有快速、便捷、低成本的特点,可以实现个性化和定制化的生产,未来将趋向于更加个性化和高效化。
例如,医疗领域可以利用该技术制作个性化的医疗器械、假体和植入物,满足患者的特殊需求;商品领域可以利用该技术实现全球化生产和本地化供应,提高响应速度和市场竞争力。
4. 生态可持续、绿色制造:快速成形技术采用增材制造和材料回收等技术,可以实现生态可持续和绿色制造,未来将趋向于更加环保和节能。
例如,采用生物降解材料可以实现零污染和资源循环利用,采用能源节约技术可以减少能源消耗和碳排放。
快速成型技术的现状和发展趋势
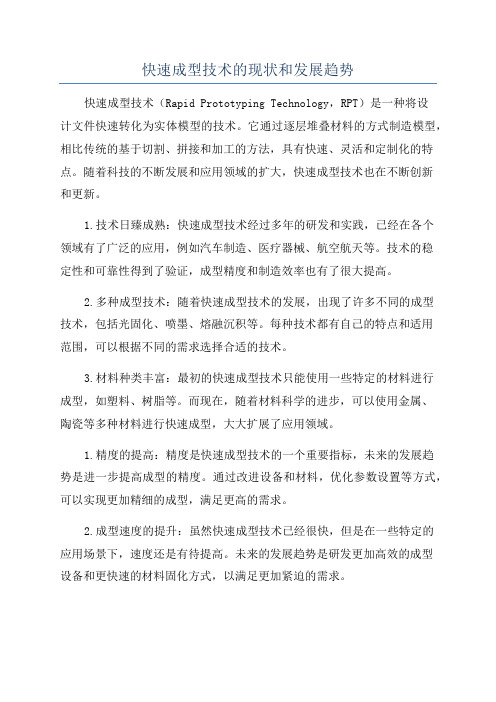
快速成型技术的现状和发展趋势快速成型技术(Rapid Prototyping Technology,RPT)是一种将设计文件快速转化为实体模型的技术。
它通过逐层堆叠材料的方式制造模型,相比传统的基于切割、拼接和加工的方法,具有快速、灵活和定制化的特点。
随着科技的不断发展和应用领域的扩大,快速成型技术也在不断创新和更新。
1.技术日臻成熟:快速成型技术经过多年的研发和实践,已经在各个领域有了广泛的应用,例如汽车制造、医疗器械、航空航天等。
技术的稳定性和可靠性得到了验证,成型精度和制造效率也有了很大提高。
2.多种成型技术:随着快速成型技术的发展,出现了许多不同的成型技术,包括光固化、喷墨、熔融沉积等。
每种技术都有自己的特点和适用范围,可以根据不同的需求选择合适的技术。
3.材料种类丰富:最初的快速成型技术只能使用一些特定的材料进行成型,如塑料、树脂等。
而现在,随着材料科学的进步,可以使用金属、陶瓷等多种材料进行快速成型,大大扩展了应用领域。
1.精度的提高:精度是快速成型技术的一个重要指标,未来的发展趋势是进一步提高成型的精度。
通过改进设备和材料,优化参数设置等方式,可以实现更加精细的成型,满足更高的需求。
2.成型速度的提升:虽然快速成型技术已经很快,但是在一些特定的应用场景下,速度还是有待提高。
未来的发展趋势是研发更加高效的成型设备和更快速的材料固化方式,以满足更加紧迫的需求。
3.结构复杂性的增加:快速成型技术的优势之一就是可以制造复杂结构的模型。
未来的发展趋势是进一步发展可以制造更加复杂的结构,如组织结构、微观结构等,以满足更多领域的需求。
4.材料种类的扩展:材料的种类对快速成型技术的应用范围有很大的影响。
未来的发展趋势是不断扩展可用材料的范围,如增加金属、陶瓷、生物材料等,以满足更广泛的应用需求。
总之,快速成型技术是一项具有广阔应用前景的技术,随着科技的不断发展和创新,将会在制造业、医疗、航空等领域发挥更为重要的作用。
felss轴向成形工艺

felss轴向成形工艺Felss轴向成形工艺是一种高效、精确的金属加工方法,广泛应用于汽车制造、航空航天、机械制造等领域。
本文将对Felss轴向成形工艺进行详细介绍。
Felss轴向成形工艺是一种通过轴向压缩和塑性变形来加工金属材料的方法。
与传统的切削加工相比,Felss轴向成形工艺具有高效、节能、精确的特点。
该工艺主要通过利用旋转的模具和挤压力将金属材料塑性变形成所需的形状。
与其他成形工艺相比,Felss轴向成形工艺可以在短时间内完成复杂零件的加工,提高生产效率。
Felss轴向成形工艺的主要步骤包括料材准备、夹紧、预制成形、精密成形和后处理。
首先,需要对金属料材进行准备,确保其尺寸和质量符合要求。
然后,将料材夹紧在加工设备上,以确保其稳定性。
接下来,通过旋转模具和挤压力对料材进行预制成形,以便后续精密成形。
在精密成形阶段,通过调整模具和挤压力,将料材逐渐变形成所需的形状。
最后,进行后处理工序,如清洁、退火等,以提高零件的性能和表面质量。
Felss轴向成形工艺具有许多优点。
首先,该工艺可以实现高度精确的成形,能够满足对形状和尺寸要求较高的零件加工。
其次,Felss 轴向成形工艺可以减少材料的浪费,因为该工艺是通过压缩和变形而不是切削来加工材料,因此可以节约材料成本。
此外,该工艺还可以提高零件的强度和硬度,改善其机械性能。
Felss轴向成形工艺在汽车制造领域得到了广泛应用。
在汽车制造过程中,需要大量的金属零件,如发动机曲轴、减震器杆等。
传统的加工方法往往需要多道工序和复杂的切削工具,而Felss轴向成形工艺可以在一道工序中完成复杂零件的成形,大大提高了生产效率。
此外,由于该工艺能够减少材料的浪费,因此可以降低汽车制造的成本。
除了汽车制造领域,Felss轴向成形工艺还在航空航天、机械制造等领域得到了广泛应用。
在航空航天领域,航空发动机零件的制造要求极高,需要具备高度精确的形状和尺寸。
Felss轴向成形工艺可以满足这些要求,同时还可以提高零件的强度和硬度,提高发动机的性能。
快速成型技术的心得心得:从零到一的技术细节
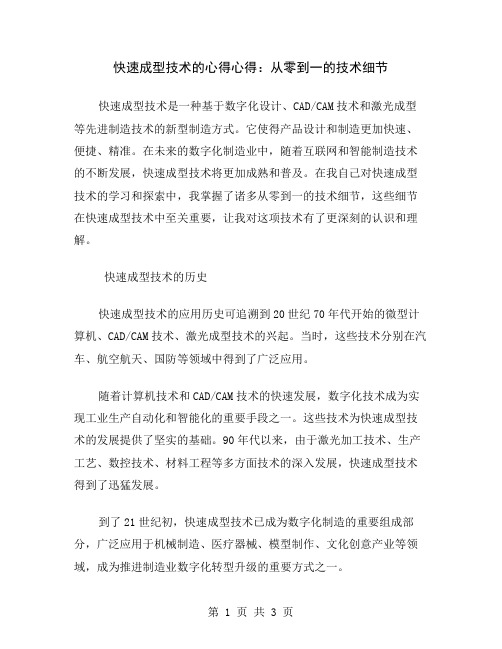
快速成型技术的心得心得:从零到一的技术细节快速成型技术是一种基于数字化设计、CAD/CAM技术和激光成型等先进制造技术的新型制造方式。
它使得产品设计和制造更加快速、便捷、精准。
在未来的数字化制造业中,随着互联网和智能制造技术的不断发展,快速成型技术将更加成熟和普及。
在我自己对快速成型技术的学习和探索中,我掌握了诸多从零到一的技术细节,这些细节在快速成型技术中至关重要,让我对这项技术有了更深刻的认识和理解。
快速成型技术的历史快速成型技术的应用历史可追溯到20世纪70年代开始的微型计算机、CAD/CAM技术、激光成型技术的兴起。
当时,这些技术分别在汽车、航空航天、国防等领域中得到了广泛应用。
随着计算机技术和CAD/CAM技术的快速发展,数字化技术成为实现工业生产自动化和智能化的重要手段之一。
这些技术为快速成型技术的发展提供了坚实的基础。
90年代以来,由于激光加工技术、生产工艺、数控技术、材料工程等多方面技术的深入发展,快速成型技术得到了迅猛发展。
到了21世纪初,快速成型技术已成为数字化制造的重要组成部分,广泛应用于机械制造、医疗器械、模型制作、文化创意产业等领域,成为推进制造业数字化转型升级的重要方式之一。
快速成型技术的工艺流程快速成型技术的工艺流程包括设计、成型设备、材料组合等多个环节,其中最突出的是数字化设计和3D打印技术。
数字化设计是快速成型技术的基础。
设计人员需要通过计算机制图软件进行3D数字化建模,将设计方案完整地记录在计算机中,成为可供工艺制造的CAD文件。
这个过程需要设计人员对产品尺寸、形状、材料、结构等多方面进行详细考虑。
成型设备包括SLA光固化成型、SLS激光烧结成型、FDM熔丝沉积成型、LMD激光建模熔化成型等多种。
其中,SLA光固化成型是使用激光将固态光聚合树脂或光敏聚合物成型的一种方法,主要适用于小型零件或精密零件生产。
SLS激光烧结成型是一种利用高能量密度激光束,使得粉末材料熔融、结成三维零件的方法。
电火花成形加工技术的现状与发展趋势

电火花成形加工技术的现状与发展趋势电火花成形加工技术是一种高精度、高效率、高灵活性的加工方法,广泛应用于模具制造、航空航天、汽车、电子等领域。
该技术通过形成电火花放电腐蚀、切割工件表面,将固体工件形成所需形状。
随着制造行业的发展和技术的不断升级,电火花成形加工技术在应用范围、加工精度、成型效率等方面也有所提升。
本文将详细介绍电火花成形加工技术的现状和发展趋势。
一、电火花成形加工技术的现状1. 应用范围扩大电火花成形加工技术广泛应用于钢铁、航空、汽车、电子、医疗、航天等行业。
特别是在模具加工领域,电火花成形加工技术已成为最常见的成形加工方法。
除此之外,电火花成形加工技术在加工高强材料、微细零部件等方面也有广泛应用。
2. 加工精度提高电火花成形加工技术具有高精度的优势,其加工精度可达到亚微米级别。
由于电火花加工时,电极与工件之间的间隙可以控制在微米级,因此可以保证加工出的模具和零部件的精度和表面质量的高度一致性。
3. 加工效率提高传统的电火花成形加工技术通常采用单电极加工方式,加工效率较低。
如今,优化后的多电极电火花成形加工技术可以同时加工多个工件,从而提高了加工效率。
此外,电极与工件間隙的控制技术也不断完善,使得加工效率得到快速提升。
4. 自动化程度提高随着工业4.0时代的到来,电火花成形加工技术的自动化程度逐渐提高。
目前,许多厂家已经研发出自动化程度高的电火花成形加工机床。
这样可以大幅提高电火花加工的生产效率和稳定性,减少加工错误和损失,节约生产成本。
二、电火花成形加工技术的发展趋势1. 精密化和高速化电火花成形加工技术目前的发展方向是提高加工精度和加工速度。
因此,更加精密化的切削工具和更高速的电火花腐蚀液将成为电火花成形加工技术发展的重点。
这将有助于提高产品质量和加工效率。
2. 智能化和自动化随着科技的进步,电火花成形加工技术将越来越智能化和自动化。
这将会使得机器人、机器视觉和自主化控制系统的应用变得更加常见,从而提高电火花成形加工技术的高效性和可靠性。
电火花成形加工技术的现状与发展趋势
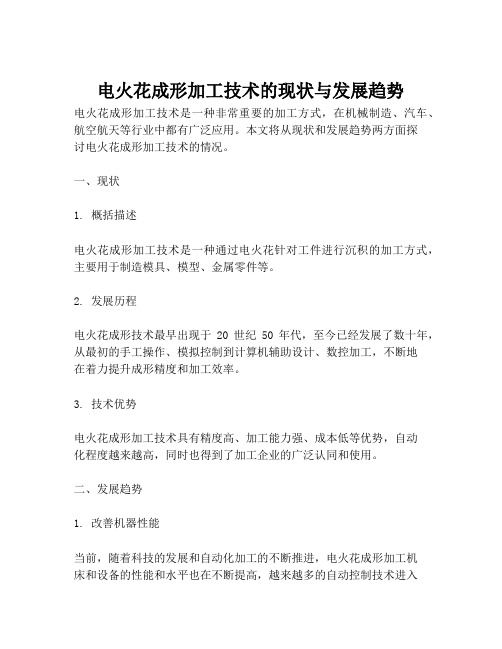
电火花成形加工技术的现状与发展趋势电火花成形加工技术是一种非常重要的加工方式,在机械制造、汽车、航空航天等行业中都有广泛应用。
本文将从现状和发展趋势两方面探讨电火花成形加工技术的情况。
一、现状1. 概括描述电火花成形加工技术是一种通过电火花针对工件进行沉积的加工方式,主要用于制造模具、模型、金属零件等。
2. 发展历程电火花成形技术最早出现于20世纪50年代,至今已经发展了数十年,从最初的手工操作、模拟控制到计算机辅助设计、数控加工,不断地在着力提升成形精度和加工效率。
3. 技术优势电火花成形加工技术具有精度高、加工能力强、成本低等优势,自动化程度越来越高,同时也得到了加工企业的广泛认同和使用。
二、发展趋势1. 改善机器性能当前,随着科技的发展和自动化加工的不断推进,电火花成形加工机床和设备的性能和水平也在不断提高,越来越多的自动控制技术进入到该行业中。
2. 提升加工质量近年来,随着电火花成形技术的不断发展,加工质量已经达到了较为稳定的水平,未来会通过不断地技术改进和提升,以更好的方式满足市场需求。
3. 减少人工操作在未来,电火花成形工程师将更多地关注如何在自动化系统中通过编程、模拟加工等方式减少人工操作,以提升加工效率和精度。
4. 强化数据管理在不断的技术革新中,与之相关的信息和数据处理也变得越来越重要,将会有越来越多的信息管理人员参与到电火花成形行业中,涉及到的数据管理技术也将越来越先进和复杂。
总体来看,电火花成形加工技术的发展前景非常广阔。
未来,电火花成形加工技术将会更加精密化、自动化,不断地为制造行业提供优质的加工解决方案。
电火花成形加工技术的研究现状和发展趋势

电火花成形加工技术的研究现状和发展趋势电火花成形加工技术是一种利用电火花放电进行材料加工的先进工艺。
它在自动化、高效率、高精度方面具有明显的优势和广泛的应用前景。
本文将对电火花成形加工技术的研究现状和发展趋势进行详细探讨。
电火花加工技术最早是在20世纪50年代初期由苏联工程师、科学家等人发明的,起初主要应用于修复机械零件表面的磨损、修复损伤、修复变形等工作。
随着科技的进步和工艺的不断改进,电火花成形加工技术在机械制造、模具制造和微细工艺加工等领域得到了广泛应用。
目前,电火花成形加工技术已经在各个领域取得了显著的进展。
首先,在机械制造领域,电火花成形加工技术广泛应用于制造高精度复杂曲面零件、机械模具以及各类高精度刀具等。
其次,在航空航天领域,电火花成形加工技术可用于制造高温合金材料的复杂结构件,提高其耐高温、高压和高速等工作环境的适应能力。
再次,在微细加工领域,电火花成形加工技术被广泛应用于微型零件、精密模具以及各类微细孔、微细纹等微细结构的加工。
与传统加工技术相比,电火花成形加工技术具有以下优势。
首先,电火花成形加工技术可以实现高精度加工,其加工精度可达到亚微米甚至纳米级别。
其次,电火花成形加工技术可以加工各种材料,包括热处理钢、不锈钢、铁素体不锈钢、高温合金、硬质合金等,广泛适用于各种行业的加工需求。
再次,电火花成形加工技术可以实现复杂曲面的加工,无论是二维曲面还是三维曲面,都可以实现高效率、高质量的加工。
然而,电火花成形加工技术也存在一些问题和挑战。
首先,电火花成形加工技术的重复性和稳定性有待提高,特别是在加工复杂结构和微细结构时,容易出现放电不稳定、电极损耗严重等问题。
其次,由于放电过程中产生的热量和应力,容易导致工件表面产生热裂纹和变形等问题,需要进一步研究改进。
再次,电火花成形加工技术的加工效率有待提高,尤其是在大批量生产和高效率加工领域中,需要进一步提高加工速度和加工效率。
为了克服这些问题和挑战,电火花成形加工技术的研究者正在开展一系列的研究工作。
CAE管道成型技术

直缝焊管由于具有生产效率高、能源消耗低、成型质量好等优点,在液体输送、气体输送及结构用管中的应用越来越广泛。
其成型工艺主要有辊式弯板法(RBE)、排辊法(CFE)、FFX柔性成型法、JCOE法和UOE法,前三种采用高频直缝焊接(ERW)技术,后两种采用直缝埋弧焊接(LSAW)技术。
辊式弯板成型机组的构造是平、立辊+立辊组的形式,主要用于生产中、小直径焊管,所生产的钢管较短、生产率低、质量较差,由于其设备少且易制造,在多品种、小批量生产中具有较好的灵活性,仍被一些制管企业采用。
排辊成型法是辊式成型法的一种改进,主要特点是在水平成型辊之间连续配置许多小辊,即所谓的排辊,使带钢边缘能够沿着一条平滑的自然变形路径进行,减小了带钢边缘褶皱,这种工艺产品成型性好,质量较高,调整小辊的空间位置可适应焊管规格的变换,但是排辊调整十分复杂。
FFX成型技术是由中田制造所开发的一种柔性辊弯成型技术,水平机架和立辊机架的轧辊完全可以共用,相比排辊成型方式,FFX成型少了精成型机和定径机,降低了用户的轧辊和设备费用,节省了换辊时间,提高了生产率。
JCOE法和UOE法是生产大口径、大壁厚直缝焊管的有效方法,前者主要成型过程为板边预弯成型→C成型→O成型→扩径,后者依次经过板边预弯→U成型→O成型→扩径。
JCOE法在成为O形后,仍然存在着各次“折弯”处的“转折点”,并且成为O 形后在对缝处开口度很大,并且没有减径的“压缩”过程,所以残余应力较大,扩径工序依然不能完全消除残存的应力。
而U-O成型是连续应变,其屈服强度的增加量要多一些,工艺优于JCOE,成品管的质量更好。
从全球石油天然气管道建设项目的规划来看,采用UOE 工艺生产的长输管道用直缝焊管的需求量迅速增加。
对比发达国家直缝焊管生产技术,我国直缝焊管成型工艺设计水平还有较大差距。
国内先进的焊管成型机组基本以进口为主,机组引进方对成型工艺设计技术严格保密,所以国内工程技术人员仍利用“试凑”法来解决工程问题。
JCO成型技术
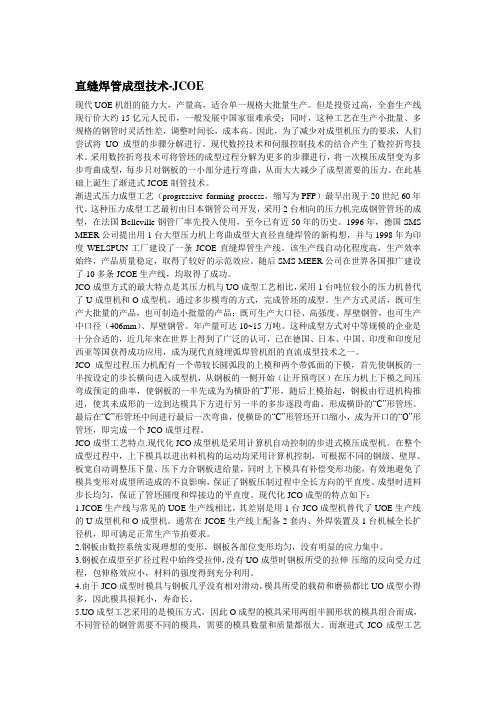
直缝焊管成型技术-JCOE现代UOE机组的能力大,产量高,适合单一规格大批量生产。
但是投资过高,全套生产线现行价大约15亿元人民币,一般发展中国家很难承受;同时,这种工艺在生产小批量、多规格的钢管时灵活性差,调整时间长,成本高。
因此,为了减少对成型机压力的要求,人们尝试将UO成型的步骤分解进行。
现代数控技术和伺服控制技术的结合产生了数控折弯技术。
采用数控折弯技术可将管坯的成型过程分解为更多的步骤进行,将一次模压成型变为多步弯曲成型,每步只对钢板的一小部分进行弯曲,从而大大减少了成型需要的压力。
在此基础上诞生了渐进式JCOE制管技术。
渐进式压力成型工艺(progressive forming process,缩写为PFP)最早出现于20世纪60年代。
这种压力成型工艺最初由日本钢管公司开发,采用2台相向的压力机完成钢管管坯的成型,在法国Belleville钢管厂率先投入使用,至今已有近50年的历史。
1996年,德国SMS MEER公司提出用1台大型压力机上弯曲成型大直径直缝焊管的新构想,并与1998年为印度WELSPUN工厂建设了一条JCOE直缝焊管生产线。
该生产线自动化程度高,生产效率始终,产品质量稳定,取得了较好的示范效应。
随后SMS-MEER公司在世界各国推广建设了10多条JCOE生产线,均取得了成功。
JCO成型方式的最大特点是其压力机与UO成型工艺相比,采用1台吨位较小的压力机替代了U成型机和O成型机,通过多步模弯的方式,完成管坯的成型。
生产方式灵活,既可生产大批量的产品,也可制造小批量的产品;既可生产大口径、高强度、厚壁钢管,也可生产中口径(406mm)、厚壁钢管。
年产量可达10~15万吨。
这种成型方式对中等规模的企业是十分合适的,近几年来在世界上得到了广泛的认可,已在德国、日本、中国、印度和印度尼西亚等国获得成功应用,成为现代直缝埋弧焊管机组的直流成型技术之一。
JCO成型过程.压力机配有一个带较长圆弧段的上模和两个带弧面的下模,首先使钢板的一半按设定的步长横向进入成型机,从钢板的一侧开始(让开预弯区)在压力机上下模之间压弯成预定的曲率,使钢板的一半先成为为横卧的“J”形,随后上模抬起,钢板由行进机构推进,使其未成形的一边到达模具下方进行另一半的多步逐段弯曲,形成横卧的“C”形管坯。
电火花成形加工技术的现状与发展趋势

电火花成形加工技术的现状与发展趋势电火花成形加工技术是一种重要的金属材料加工技术,具有高精度、高效率、可靠性强等优势,被广泛应用于航天、航空、医疗器械、汽车、家电等各个领域。
然而,随着市场竞争日益激烈和技术的不断进步,电火花成形加工技术的现状与发展趋势也逐渐受到关注。
本文将从电火花成形加工技术的现状和发展趋势两个方面进行解读。
一、电火花成形加工技术的现状目前,电火花成形加工技术在我国的应用已经逐渐成熟。
检测数据表明,其加工精度可以达到0.001mm以上,而粗加工时,加工效率可以高达每小时500mm³。
此外,电火花成形加工技术还具有以下优点:1、可加工高硬度材料电火花成形加工技术采用电脉冲放电进行加工,可以对金属、合金等高硬度材料进行加工,大大拓展了加工材料的选择范围。
2、形状复杂的成品电火花成形加工技术可以制作出头发丝般细的细微形状,同时也可以加工出复杂的三维异形零部件,为大型零件的制造提供了方便。
3、内部孔加工通过电极管的穿透和内部电极扫描的方式,电火花成形加工技术可以对材料进行内部孔的加工,生产更小巧、更精细的零件。
二、电火花成形加工技术的发展趋势1、智能化随着人工智能技术的广泛运用,电火花成形加工技术也正在朝着智能化方向不断发展。
新一代智能式电火花成形加工机将拥有更加智能的控制系统、更高效的自适应控制系统和更严格的质量控制系统,使其在精度和效率上更上一层楼。
2、先进技术的应用电火花成形加工技术和其他先进技术的结合,将有助于取得更加令人瞩目的成果。
例如,采用异步高速电机、低噪音螺杆空气压缩机、高效能量回收系统、智能化机器人操作系统等技术,可以使电火花成形加工机的效率和稳定性更高。
3、环保节能在保证加工效果的前提下,电火花成形加工技术还应当加强节能环保方面的建设。
研发新型绿色电火花成形加工剂、采用清洁能源替代传统燃料、开发废气、废水资源、减少环境污染等措施,是电火花成形加工技术未来发展的必然趋势。
双射线束流成型技术

双射线束流成型技术
双射线束流成型技术是一种高精度、高效率的材料成型技术,通过利用两条射线束将熔融金属或塑料材料加热至熔点并形成特定形状的工件。
这种技术具有以下特点:
1. 高精度:双射线束可以在三维空间内精确控制加热区域的大小和形状,可以制造出非常复杂的结构和细节。
2. 高效率:双射线束可以同时加热多个点,从而提高生产效率。
此外,由于只有加热区域受热,实现了能量的局部利用,节约能源。
3. 无接触加热:双射线束采用无接触方式加热材料,不会对工件表面造成破坏或留下痕迹。
4. 材料适应性强:双射线束可以对多种材料进行成型,包括金属、陶瓷、塑料等。
5. 环保节能:由于采用了局部加热方式,减少了材料的浪费和环境污染。
双射线束流成型技术在航空航天、汽车制造、电子设备等领域具有广泛的应用前景。
它可以制造出高精度的零部件和复杂的结构件,提高产品的质量和性能。
同时,该技术还能节约材料和能源,减少环境污染,符合可持续发展的要求。
FFX成型技术在不锈钢焊管生产中的应用
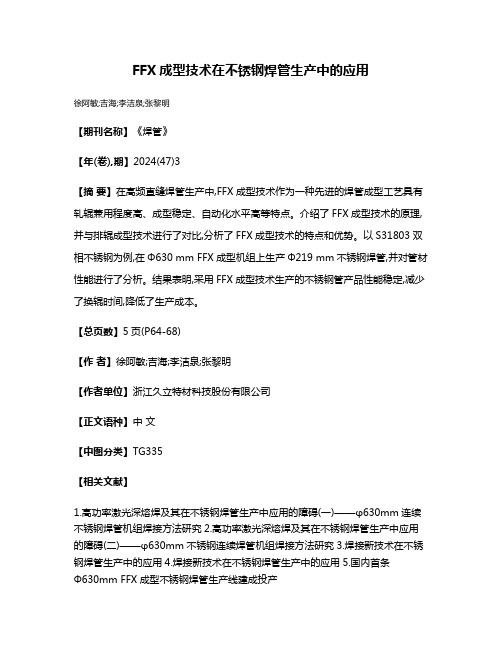
FFX成型技术在不锈钢焊管生产中的应用
徐阿敏;吉海;李洁泉;张黎明
【期刊名称】《焊管》
【年(卷),期】2024(47)3
【摘要】在高频直缝焊管生产中,FFX成型技术作为一种先进的焊管成型工艺具有轧辊兼用程度高、成型稳定、自动化水平高等特点。
介绍了FFX成型技术的原理,并与排辊成型技术进行了对比,分析了FFX成型技术的特点和优势。
以S31803双相不锈钢为例,在Φ630 mm FFX成型机组上生产Φ219 mm不锈钢焊管,并对管材性能进行了分析。
结果表明,采用FFX成型技术生产的不锈钢管产品性能稳定,减少了换辊时间,降低了生产成本。
【总页数】5页(P64-68)
【作者】徐阿敏;吉海;李洁泉;张黎明
【作者单位】浙江久立特材科技股份有限公司
【正文语种】中文
【中图分类】TG335
【相关文献】
1.高功率激光深熔焊及其在不锈钢焊管生产中应用的障碍(一)——φ630mm连续不锈钢焊管机组焊接方法研究
2.高功率激光深熔焊及其在不锈钢焊管生产中应用的障碍(二)——φ630mm不锈钢连续焊管机组焊接方法研究
3.焊接新技术在不锈钢焊管生产中的应用
4.焊接新技术在不锈钢焊管生产中的应用
5.国内首条
Φ630mm FFX成型不锈钢焊管生产线建成投产
因版权原因,仅展示原文概要,查看原文内容请购买。
DEFORM粉末冶金成形工艺数值模拟技术应用-安世亚太

DEFORM粉末冶金成形工艺数值模拟技术应用安世亚太公司晏建军1 前言金属粉末冶金成形已应用于多种工业机械零部件的成形工艺,包括齿轮、轮盘、汽车连杆等。
粉末冶金成形是将松散的粉末体加工成具有一定尺寸、形状以及一定密度和强度的坯块。
传统的成形方法有模压成形、等静压成形、挤压成形、轧制成形、注浆成形和热压铸成形等。
DEFORM金属粉末成形技术可实现粉末成形工艺过程的计算机数值模拟,预测粉末成形缺陷,优化加工工艺参数。
2 粉末冶金成形工艺优势及面临问题从制作机械零部件方面来看,粉末冶金法制作机械零部件是一种少切削、无切削工艺,可以大量减少切削加工量而节省机床,节约金属材料,提高劳动生产率。
用金属粉末冶金法制作机械结构零件时,比用其他加工方法的材料利用率高、能耗低。
粉末成形工艺过程的实现,涉及到工艺参数及模具结构设计等种种因素,粉末的初始装填密度、压机的锻压速度、压制力等对粉末冶金零件的成形形状、压实密度分布、成形应力应变等具有难以预测的影响,而成形零件的锻压质量又影响到产品的机械性能和使用寿命,因此如何更科学更准确地评估压实成形质量,是汽车齿轮、连杆等金属粉末加工产品的重要方面。
DEFORM塑性成形分析程度的金属粉末成形功能可预测成形过程中产品可能出现的缺陷、分析成形尺寸精度、各部位密度分布等现象,优化成形工艺参数,缩短研发周期。
3 DEFORM粉末冶金成形工艺方案的工业应用粉末冶金成形工艺模拟软件用于精确预测产品最终形状及机械加工件的密度分布,DEFORM数值模拟技术已成为产品及加工工艺设计和优化的有力工具。
在数值模拟计算系统中,可通过快速仿真分析,获得粉末成形模具粉料填充、材料流动、成形吨位、温度场分布、应力应变、能量及裂纹等信息,同时,该数值仿真系统可对粉末成形后的产品进行烧结工艺分析,预测烧结后的产品体积变化及内应力、密度,指导成形模具和工艺参数的优化设计。
在粉末冶金成形领域已获得良好的工业化应用。
高频直缝焊管FFX成型板边质量控制方法

高频直缝焊管FFX成型板边质量控制方法
孙文奎;张慧明
【期刊名称】《焊管》
【年(卷),期】2024(47)4
【摘要】为了改善FFX成型方式下高频直缝焊管的板边质量,针对小直径大壁厚钢管存在的板边成型不充分以及大直径薄壁管存在的板边成型波浪边的问题,提出了相应的调整措施。
通过对粗成型辊(BD1)上辊的压下调整、BD1的成形曲率调整、精成型辊(FP)的减径量调整,以及焊接挤压辊(SQ)上辊的压下调整,能够有效实现板边端面的“I”形对接;通过增加FP的减径量,合理调整BD、RVS和CL机架轧辊位置,减小材料在FFX成型过程产生的长度方向的伸长量,均匀分配整条生产线的拉力等措施,能够避免波浪边的产生。
【总页数】6页(P63-68)
【作者】孙文奎;张慧明
【作者单位】胜利油田孚瑞特石油装备有限责任公司华锐石油钢管公司;石家庄铁能机电设备有限公司
【正文语种】中文
【中图分类】TG335
【相关文献】
1.高频直缝焊管成型过程仿真分析
2.F.F.成型法在φ340 mm高频直缝焊管机组中的应用
3.高频直缝电阻焊钢管成型过程仿真
4.浅析高频直缝焊管用坯料及成型要求
5.高频直缝焊管上山成型底线的再认识
因版权原因,仅展示原文概要,查看原文内容请购买。
- 1、下载文档前请自行甄别文档内容的完整性,平台不提供额外的编辑、内容补充、找答案等附加服务。
- 2、"仅部分预览"的文档,不可在线预览部分如存在完整性等问题,可反馈申请退款(可完整预览的文档不适用该条件!)。
- 3、如文档侵犯您的权益,请联系客服反馈,我们会尽快为您处理(人工客服工作时间:9:00-18:30)。
Ab t a t s r c :Ov rt e p s i ed c d s d v l p n f h l i e F X r n e h o o yh se p re c d e a t v e a e , e e o me t ewe d p p F f mi g t c n l g a x e i n e h f ot o
Z o h jn u h a j o h uS uu ,L oC u ni ,WuX u u i u z e g a iy ,Q oh n G ( a e OiSe l ieC . a gh uB a c f o a P t lu Hu b i l te Pp o,Y n z o rn ho h i er e m B o E up e t n fcueC r. a gh u 2 5 ,C ia) q im n ua tr op,Y n zo 2 8 hn Ma 1 2
Ba e n t e a t a p l a i n r s l o a e lS e l i e Co , Ya g h u Br n h o o a to e m q i — s d o h c u la p i to e u t fHu b i t e p . c Oi P n z o a c fB h i Pe r l u E u p
中图分类号 :T 4 文献标识码 :B 文章编号:10 — 3 2 1 ) 10 5 — 3 G4 0 1 2 1 ( 0 0 0 — 0 3 0 1
An ls s o v n a s o X Or i g Te h ol g a y i f Ad a t ge f FF F m n c n o y
tv n s . ie es
Ke r s HF l i e F X o mi g Ro ld a - u p s s ; Hi h a t ma i n l v l Ad a t g y wo d : W wed p p ; F f r n ; l u lp r o e u e g u o to e e ; v n a e; Co te e tv n s s f C i e e s
渤海石油装备华 油钢管公司扬州分公 司的实际应用情况 ,重 点分析 了 F X成型技术在其粗成型轧辊兼用和结构合 F 理 、控制系统高度 的 自动化水平 、钢管易调型、设备运行全过程监控等方面的先进性以及运行 的经济性 。 关键词 :HF 焊管 ;F X成型 ;轧辊兼用 ;自动化水平 ;先进性 ;经济性 W F
e s i e t p h n e a d f l・ r c s u e v s o f h q i me to e a i n a l a h p r t n c s・ fe - a y p p y e c a g n u lp o e ss p r ii n o e e u p n p r to swe l st e o e a i o t ef e - t o ・
笈
5 3
F X成型技术的先进性分析 F
周 淑 军 ,骆 传教 ,吴 秀 宇 ,齐 国政
(渤海石油装备华油钢管公司扬州分公 司,江苏 扬州 2 5 2 2 1 8)
摘
要 :近 5 年来 , F 焊管成型技术 经历 了 3 O HW 个阶段 的技术进步 :传统成型一 排辊成型一 F F X成型 。结合
3 s a e , i . t e c n e to a t g s . , h o v n i n l ̄r n r c s , t e c g o l f r n r c s n h F f r n r c s . e mi g p o e s h a e r l o mi g p o e s a d t e F X o mi g p o e s
油套管、油气输送管等使用高钢级 、高质量无缝钢 伴随着我国国民经济建设的飞速发展和人民生 管的领域 。正在大规模采用直缝焊管取代大量耗能 F 活水平 的不断提高,对更为清洁高效的天然气资源 的无缝钢管。H W 焊管以其高效率 、低成本的优 F 的需求大大增加 。加快了我国天然气支线——城市 势获得 了市场的青睐。为适应市场对 H W 焊管越 O年来 ,HF 焊管成 型 技术经 W 管网的建设步伐 ,加大了对建设用材——钢管的需 来越 高 的要求 ,近 5 个 排辊成型一 求。钢铁冶炼技术 、热带钢卷轧制技术、自动控制 历 了 3 阶段 的技术进步 :传统成型一 F 技术 、无损探 伤技 术 的飞 速发展 为 生产 高 品质 F X成 型 。在 此背 景下 ,渤 海石 油装备 华油钢 管公
me tMa u a t r r . t e a v n a e ft e F X o mi g p o e s i n l z d, f c s n n s c s e t s n n f c u e Co p , h d a t g s o h F f r n r c s s n o ld a u p s s n h e s n b e sr c u e h g u o t n l v lo h o to y t m , og mi g r l u lp r o e u e a d t e r a o a l tu t r , i h a t ma i e e ft e c n r ls s e o