汽车轻量化技术的研究与进展
汽车车身轻量化文献评述

汽车车身轻量化是当前汽车工业的一个重要研究方向。下面是一篇关于汽车车身轻量化的 文献评述:
标题:汽车车身轻量化技术的研究进ห้องสมุดไป่ตู้与挑战
摘要:汽车车身轻量化是一种有效的方法,可以提高汽车的燃油经济性和减少尾气排放。 本文对汽车车身轻量化的研究进展和挑战进行了综述。首先,介绍了汽车车身轻量化的重要 性和背景。然后,对当前常用的轻量化材料进行了概述,包括高强度钢、铝合金、碳纤维复 合材料等。接着,探讨了不同的轻量化技术,如结构优化设计、材料组合和制造工艺改进。 最后,讨论了汽车车身轻量化面临的挑战,如成本、安全性和可持续性等方面的问题。综合 分析了当前研究的热点和趋势,并提出了未来研究的方向和发展前景。
汽车车身轻量化文献评述
关键词:汽车车身轻量化,轻量化材料,轻量化技术,挑战,发展前景
这篇文献评述综合了汽车车身轻量化的重要性、常用材料和技术、以及面临的挑战。它提 供了对该领域研究的概述和综合分析,为进一步的研究和发展提供了指导和展望。
面向汽车轻量化设计的关键技术研究

面向汽车轻量化设计的关键技术研究摘要:经济的发展也带来了资源匮乏等问题,如何实现经济发展、环境保护以及资源节约之间的平衡成为关注的焦点。
在内需驱动下,实现碳中和,进行产业结构调整和能源转型势在必行。
在此次研究中主要对汽车设计的关键技术、轻量化焊接工艺、设计保障等进行了研究,以达到提高汽车的整体质量和使用效果,为汽车轻量化设计提供帮助。
同时,也希望本文的分析能为探索轻量化发展的同行提供参考经验。
关键词:汽车、轻量化、焊接工艺引言当前随着汽车工业的持续发展,很多新技术开始应用到了车辆设计以及生产领域中,轻量化设计成为必然的发展趋势,更是推动汽车工业实现节能减排的重要手段。
在轻量化设计方面总体可以划分为工艺、材料以及结构轻量化三个方面,为了实现轻量化的目标,必须在材料以及结构上进行更多的研究,致力于对关键技术进行突破。
在汽车以及航天等领域中广泛使用了基于塑性以及断裂等方式吸收或者或耗散碰撞能量的材料,此类材料显示出广阔的应用前景。
1汽车轻量化工艺简介汽车轻量化主要是通过降低车身整体质量来提高动态性能,在保证汽车安全性的同时降低对于外部环境的不利影响,节约资源,减少污染。
当前针对轻量化的研究非常多,形成了不同类型的材料,常用的主要划分为金属、非金属材料两大类,前者一般指的是铝合金以及其他的金属材料;后者则以塑料等材料为主。
如何实现轻量化,提高整车质量和性价比,是车企的关键指标之一,随着新材料、新技术、新工艺的推广,将会有更多新型轻量化材料应用于整车生产。
大量的车企重视在此领域的研究,将这些新材料以及新工艺逐步能够到了车辆生产中,改善了车辆的安全性,降低了重量,取得了一定的突破。
近年来,广泛使用的典型轻量化连接工艺主要包括以下几个方面。
自冲铆接:该技术实际上属于一种冷连接技术,具备了较高的适用性,可以实现多种材料的连接,包括金属和非金属材料。
该板被致动器刺穿,首先穿过上部,然后穿过下部。
下板成功穿透后,铆钉的尾部会继续向外延伸,从而获得更稳定的接头。
汽车轻量化材料及相关技术的研究进展
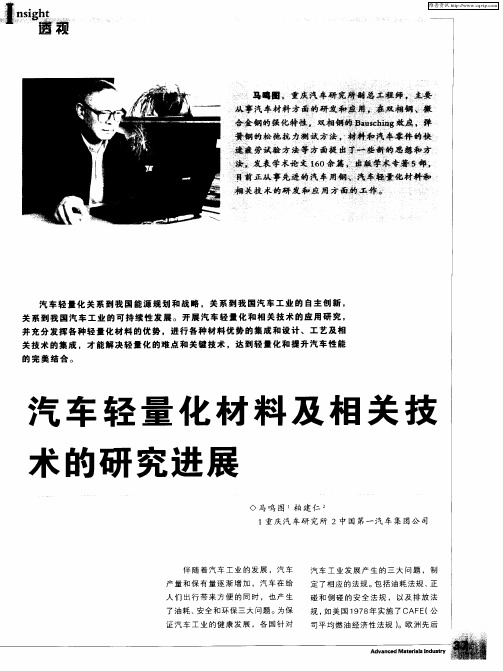
影 响 我 国轿 车 产量 增长 的首 要 因素 。
提 高 燃 油 经 济 性 和 能 源 多 元 化 是 保 证 汽 车 工 业 可 持 续 发 展 的 当 务 之 急 。 国 家 汽 车 产 业 发 展 政 策 中 第 1 规 定 “ 车 产 业 及 相 关 产 业 要 0条 汽 注 重 发 展 和 应 用 新 技 术 。 提 高 汽 车 燃油 经 济性 。2 1 0 0年 前 ,乘 用 车 新 车平 均 油 耗 比 2 0 0 3年 降 低 1 % 以 5
上 。 ”
为 91 k g。与福 特 的 T u u 轿 车相 0 a s r
比 轻 了 4 %。 0 商用车 的 自质量 也在 逐年 减少 ,
意 味 着 二氧 化碳 、氮 氧 化 物 等 有 害 气体 排 放量 的下 降。据报 道 。 国汽 美 车质 量 如果 减 少 2 % 。燃 油 消耗 按 5
维普资讯
维普资讯
nsg i ht
廛 透 颖
实 施 欧 l、 l、欧 ¨和 欧 l 放 法 欧 l l V排
汽 车 中 实 现 轻 量 化 。 不 但 可 以 减 少 油耗 。还可 以降低 制造 费 用 。
1 2 k ; 0 代 初 下 降至 1 7 k ; 50g 9 年 4 5 g 9 0年 代 末 下 降 至 1 3 k 0 g; 1 8 — 2 5 9
规 。 对碰 撞 对人 体 伤害 。 国制 定 针 美
了正 碰 法规 F MUS 2 8和 侧 碰 法 规 S 0 F MOS 21 S 4等 。 我 国 亦 有 类 似 的 法 规 公 布 和 实 施 。各 国 汽 车 工 业 认 为 :
进 汽车业提 高燃油经济 性;8 0年代 中
期 以后 。保 护 地 球 环 境 又 一 次 推 动 汽 车 业 提 高 燃 油 经 济 性 、降 低 排 放 。研 究 表 明 。约 7 % 的 油 耗 与 整 车 质 量 有 5
工程伦理结课论文

目录第1章汽车轻量化工程伦理问题综述 (1)第1.1节汽车轻量化工程简介 (1)第1.2节汽车轻量化工程带来的伦理问题 (1)第2章汽车轻量化带来的安全风险伦理问题 (2)第2.1节安全风险伦理问题的产生 (2)第2.2节利用人道主义原则处理安全风险伦理问题 (2)第3章汽车轻量化的受益者及公正伦理问题 (3)第3.1节汽车轻量化的受益者 (3)第3.2节利用社会公正原则处理公正伦理问题 (4)第4章汽车轻量化带来的环境伦理问题 (5)第4.1节环境伦理问题的产生 (5)第4.2节利用人与自然和谐发展原则处理环境伦理问题 (5)第5章汽车工程师应承担的伦理责任 (6)参考文献 (7)第1章汽车轻量化工程伦理问题综述第1.1节汽车轻量化工程简介随着汽车工业的持续快速发展,汽车保有量大幅增长,全球汽车已超10亿辆。
汽车已成为世界能源消耗和污染物排放的主要来源。
各发达国家均制订了严格的法规来限制汽车燃油消耗和温室气体的排放,我国也发布了油耗强制性国家标准——《乘用车燃料消耗量限值》(GB19578-2004)。
研究表明,汽车轻量化是降低能耗、减少排放的最有效措施之一。
例如汽车每减少100kg,可节省燃油0.3~0.5 L/ (100 km),可减少CO2排放8~11 g/ (100 km)。
因此,自20世纪90年代以来,国内外许多大型研究计划积极推动了汽车轻量化技术的研究,以之作为节省行车成本和应对石油资源短缺问题的一项关键技术。
汽车轻量化技术主要包括结构优化设计和轻量化材料的应用。
塑料及纤维复合材料在汽车工业中的应用日趋广泛,使用量持续增长。
从1977年到2001年,单车塑料用量由76 kg提高到115 kg,增幅达50%,2013年更是已经超过了150kg。
第1.2节汽车轻量化工程带来的伦理问题10多年前,《纽约时报》刊登了一篇题为“研究表明轻型汽车将危及到车内人员生命”的文章,里面提到了小型汽车的死亡率最高,而中型车比小型车更安全。
汽车轻量化技术的研究与进展

汽车轻量化技术的研究与进展作者:范子杰, 桂良进, 苏瑞意, FAN Zijie, GUI Liangjin, SU Ruiyi作者单位:清华大学汽车安全与节能国家重点实验室,北京100084,中国刊名:汽车安全与节能学报英文刊名:JOURNAL OF AUTOMOTIVE SAFETY AND ENGERGY年,卷(期):2014,5(1) Government Printing Office Partnership for a New Generation of Vehicles (PNGV):assessment of programgoals,activities,and priorities 19962.American Iron and Steel Institute UltraLight steel auto body final report 20143.American Iron and Steel Institute ULSAB-AVC overview report 20024.EAA (European Aluminium Association),Aluminium in Cars 20085.杨阳;周谊;桂良进双扭杆双横臂悬架有限元建模与分析 2006(11)6.桂良进;范子杰;陈宗渝“长安之星”微型客车白车身刚度研究 2004(09)7.周长路;范子杰;陈宗渝微型客车白车身模态分析 2004(01)8.郝春鹏;范子杰;桂良进微型客车车身结构正面碰撞特性的数值模拟 2004(05)9.Gobbi M;Haque I;Papalambros P P Y A critical review of optimization methods for road vehicles design 200610.郝琪;张继伟车门结构优化设计的灵敏度分析研究 2010(05)11.桂良进;范子杰;周长路某型载重车车架结构轻量化设计研究 2003(04)12.苏瑞意;桂良进;王旭燃料电池城市客车结构有限元分析与轻量化设计 2008(12)13.刘江;桂良进;王青春全承载式大客车车身结构多目标优化 2008(02)14.丁炜琦;苏瑞意;桂良进基于应力优化的大客车结构多目标优化 2010(04)15.Botkin M E Structural Optimization of Automotive Body Components Based on Parametric Solid Modeling 2002(02)16.Shin J K;Lee K H;Song S I Automotive door design with the ULSAB concept using structural optimization 2002(04)17.XIANG Yujiang;WANG Qian;FAN Zijie Optimal crashworthiness design of a spot-welded thin-walled hat section 2006(10)18.Su Ruiyi;Gui Liangjin;Fan Zijie Multi-objective optimization for bus body with strength and rollover safety constraints based on surrogate models 2011(03)19.朱茂桃;钱洋;顾娅欣基于Kriging模型的车门刚度和模态优化 2013(11)20.Choi W S;Park G J Structural optimization using equivalent static loads at all time intervals 2002(19-20)21.Jeong S;Yi S;Kan C Structural optimization of an automobile roof structure using equivalent static loads 2008(11)22.Shimoda M;Tsuji J Shape optimization for weight reduction of automotive shell structures subject to a strength constraint.SAE Technical Paper,2007-01-372023.方剑光;高云凯;王婧人基于网格变形技术的白车身多目标形状优化 2012(24)24.Bendsφe M P Optimal shape design as a material distribution problem 1989(04)25.Yang R J;Chahande A I Automotive applications of topology optimization 1995(3-4)26.Yang R J;Chuang C;Che X New applications of topology optimization in automotive industry 2000(01)27.Baskin D M;Reed D B;Seel T N A case study in structural optimization of an automotive body-in-white design.SAE Tech Paper,2008-01-088028.SU Ruiyi;GUI Liangjin;FAN Zijie Truss Topology Optimization Using Genetic Algorithm with Individual Identification 200929.SU Ruiyi;GUI Liangjin;FAN Zijie Topology and sizing optimization of truss structures using adaptive genetic algorithm with node matrix encoding 200930.SU Ruiyi;WANG Xu;GUI Liangjin Multi-objective topology and sizing optimization of truss structures based on adaptive multi-island search strategy 2011(02)31.Sobieski J Optimization by decomposition:a step from hierarchic to non-hierarchic systems 198832.Kroo I;Altus S;Braun R Multidisciplinary optimization methods for aircraft preliminary design 199433.Kim H M;Michelena N F;Papalambros P Y Target cascading in optimal system design 2003(03)34.De Weck O;Agte J;Sobieski J State-of-the-art and future trends in multidisciplinary design opti-mization 200735.苏瑞意;桂良进;吴章斌大客车车身骨架多学科协同优化设计 2010(018)36.Michelena N;Louca L;Kokkolaras M Design of an advanced heavy tactical trucks:A target cascading case study.SAE Tech Paper,2001-01-279337.Kim H M;Rideout D G;Papalambros P Y Analytical target cascading in automotive vehicle design 2003(03)38.赵迁;陈潇凯;林逸解析目标分流法在汽车多学科设计优化中的应用 2010(06)39.冯美斌汽车轻量化技术中新材料的发展及应用 2006(03)40.马鸣图;柏建仁汽车轻量化材料及相关技术的研究进展 2006(06)41.王利;陆匠心汽车轻量化及其材料的经济选用 2013(01)42.王广勇;王刚高强度钢在汽车轻量化中的应用 2011(01)43.桂良进;高付海;范子杰双相钢板料的单向拉伸断裂失效研究(Ⅰ)一数字图像相关技术试验 2010(02)44.高付海;桂良进;范子杰双相钢板料的单向拉伸断裂失效研究(Ⅱ)一弧长法非线性有限元分析 2010(03)45.GAO F;GUI L;Fan Z Experimental and Numerical Analysis of an In-Plane Shear Specimen Designed for Ductile Fracture Studies 2011(06)46.桂良进;高付海;范子杰先进高强度钢的断裂失效准则研究 2012(33)47.Sadagopan S Formability characterization of advanced high-strength steels48.Pickett AK;Pyttel T;Payen F Failure prediction for advanced crashworthiness of transportation vehicles 2004(07)49.Ducker Worldwide EAA Aluminium penetration in cars 201250.Hirsch Ju¨ rgen Aluminum in Innovative Light-Weight Car Design 2011(05)51.马鸣图;游江海;路洪洲汽车轻量化以及铝合金汽车板的应用 200952.詹志强铝合金汽车车身板应用现状及需求前景 201253.王丹铝合金汽车板应用及生产现状 2013(03)54.桂良进;范子杰;王青春泡沫填充圆管的轴向压缩能量吸收特性 2003(11)55.桂良进;范子杰;王青春泡沫填充圆管的动态轴向压缩吸能特性 2004(05)56.王青春;范子杰;桂良进泡沫铝填充帽型结构轴向冲击吸能特性的试验研究 2006(04)57.王青春;范子杰;桂良进中等应变率下泡沫铝的吸能特性 2005(06)58.WANG Q;FAN Z;SONG H Experimental and numerical analyses of the axial crushing behaviour of hat sections partially filled with aluminum foam 2005(05)59.WANG Q;FAN Z;GUI L A theoretical analysis for the dynamic axial crushing behaviour of aluminium foamfilled hat sections 2006(7-8)60.WANG Q;FAN Z;GUI L Theoretical analysis for axial crushing behaviour of aluminium foam-filled hat sections2007(04)61.Waurzyniak P Advanced materials in automotive:Newer steels,aluminum,magnesium,and other materials lead to more lightweight,economical vehicles 2009(03)62.Kulekci M K Magnesium and its alloys applications in automotive industry 2008(09)63.吴章斌;桂良进;范子杰AZ31B镁合金挤压板材力学性能的各向异性 2012(02)64.许江菱;钟晓萍;殷荣忠2011-2012年世界塑料工业 进展 2013(03)65.杨挺汽车工业中塑料材料应用的现状及展望 2013(05)66.ZHANG Ping;GUI Liangjin;FAN Zijie Finite element modeling of the quasi-static axial crushing of braided composite tubes 2013(01)67.ZHANG Ping;GUI Liangjin;FAN Zijie Crash energy absorption of braided composite tubes and its application in vehicle passive safety 201368.GUI Liangjin;ZHANG Ping;FAN Zijie Energy absorption properties of braided glass/epoxy tubes subjected to quasi-static axial crushing 2009(01)69.ZHANG Ping;GUI Liangjin;FAN Zijie An analytical model for predicting the elastic properties of triaxially braided composites 2009(15)70.张平;桂良进;范子杰三向编织复合材料弹性性能研究 2009(01)71.康万平;王宇;康蕾管件液压成型技术简述 2010(01)72.王习文;宗长富;郭立书管件液压成形技术及其在汽车零部件制造中的应用 2013(04)73.杨勇;徐峰;苏海波管件液压成形技术及其在副车架上的应用 2010(03) Hydroforming achieves vehicle weight and cost reduction says study 201275.Koca f da A;Sadtowska H Automotive component development by means of hydroforming 2008(03)ngerak N;Rout D K;Verma R Tube hydroforming in automotive applications 201477.陈杰管材内高压成形数值模拟与工艺研究 201378.李泷杲金属薄壁管液压成形应用基础研究 200779.任芝兰汽车用高强度钢的激光焊焊接性研究 2006(01)80.朱久发激光拼焊汽车板的应用现状与发展前景 2011(03)81.ROFIN Lasers in Automotive Industry 201482.Klaus L Laser Applications in the Automotive Industry 201183.Chen H C;Pinkerton J A Mistry,Gap-free fibre laser welding of Zn-coated steel on A1 alloy for light-weight automotive applications 2011(02)84.HYRCZA-MICHALSKA M;GROSMAN F The evaluate of laser welded tailor and tubular blanks formability for automotive vehicle elements stamping 2009(01)85.Sieben M;Brunnecker F Laser-Hybrid welding,an innovative technology to join automotive body parts 201086.Schimek M;Springer A;Kaierle S Laser-welded dissimilar steel-aluminum seams for automotive lightweight construction 201287.Vasilash G S VW Is Hot On Lasers 200488.Bea M;Brockmann R;Havrilla D Remote laser welding in automotive production 2011引用本文格式:范子杰.桂良进.苏瑞意.FAN Zijie.GUI Liangjin.SU Ruiyi汽车轻量化技术的研究与进展[期刊论文]-汽车安全与节能学报 2014(1)。
汽车轻量化技术
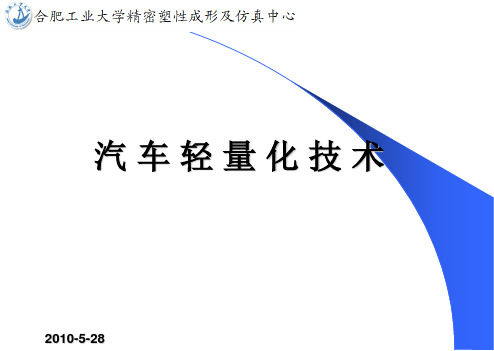
车重与燃油利用率的关系
油耗与CO2排放关系
6-294
汽车轻量化具有重要意义
一、节能减排是汽车工业发展的必然趋势 20世纪 70年代的两次石油危机 ,促进汽车工业提高了燃油经济性。
80年代中期以后,保护人类居住和赖以生存的环境又一次推动汽车工业
提高燃油经济性和排放。
《BP世界能源统计2008》的数据 , 2007年全球石油产量为 8 150万桶 , 按照这一数字 ,全球石油储量可满足 40年的需求;目前美国53 %依赖进
2-294
汽车轻量化的意义及概念
国内外汽车轻量化技术发展现状
汽车轻量化的主要途径 汽车轻量化技术应用的成功案例
3-294
汽车轻量化之
第一章 汽车轻量化意义及概念
伴随着我国现代化进程,汽车工 业的发展势头强劲,已成为我国国民经 济的支柱产业之一。 据中国汽车工业协会的统计显示, 2009年我国汽车产量达到1379万辆,首
13-294
汽车轻量化的概念
汽车轻量化不能以简单的减重多少来衡量,必须与所设计车身的尺寸和
功能相关
对于已有的功能可满足要求的汽车,轻量化的设计是降低重量而保持原功能 不变,其轻量化的效果是直接的减重;
现有功能尚不能全部满足要求或需要提升的汽车,轻量化设计是完善功能而
保持质量不变; 既要提高改进性能,同时也使汽车减重。 汽车轻量化设计实际上是功能改进,质量降低,结构优化和合理价格的
新技术项目和国家科技攻关重大项目。 促进了汽车轻量化技术的进步。
九五“期间,我国进行了铝合金材料和铸件生产成套工艺技术的开 发研究,开发出了多种铸造合金和高性能轴瓦材料:耐热铝合金、高强 高韧铝合金、铝基复合材料等新材料的研究取得了较大进展。 半固态 成型、快速凝固等先进成型技术研究与应用也取得了突破。一汽等几大 汽车生产厂家都有自己的铝合金铸造生产线; 湖南大学也正在进行汽 车大型铝合金结构件整体铸造成形技术和关键设备的研究; 重庆汽车
汽车发动机连杆轻量化设计研究

汽车发动机连杆轻量化设计研究汽车发动机连杆轻量化设计研究引言汽车发动机作为汽车的心脏,承担着转换能量和驱动汽车运行的重要功能。
在发动机的设计中,连杆作为一个关键部件,在发动机的运转过程中承担着极其重要的作用。
本文将从汽车发动机连杆的轻量化设计入手,探讨其对汽车发动机性能和效率的影响。
一、轻量化设计的定义和意义1. 轻量化设计的概念轻量化设计是指在满足产品性能、寿命、安全和成本等综合要求的前提下,以减轻产品自重为目的,采用新的材料、新的结构和新的工艺等手段,达到减轻产品质量的目的。
2. 轻量化设计的意义轻量化设计可以显著减少汽车部件的质量,降低汽车自身的重量,提高汽车的燃油经济性和动力性能,减少对环境的影响,同时也符合节能和减排的国家政策。
轻量化设计对于汽车的性能改进和环境保护具有重要的意义。
二、发动机连杆轻量化设计的技术要点1. 材料的选择发动机连杆的轻量化设计首先要选择合适的材料。
一般来说,铝合金、镁合金和钛合金都是常用的轻量化材料。
这些材料具有优异的比强度和比刚度,可以在减轻连杆质量的同时保证其强度和刚度。
2. 结构的优化发动机连杆的轻量化设计还需要对其结构进行优化。
通过采用空心结构、椭圆形截面等设计手段,可以在保证连杆强度的前提下减少其质量,达到轻量化的效果。
3. 工艺的改进传统的连杆制造工艺一般采用锻造和机加工,这种方式存在浪费材料和能源的问题。
而采用先进的成型工艺,如压铸、粉末冶金等,可以有效降低原材料的消耗,实现连杆的轻量化设计。
三、发动机连杆轻量化设计的影响1. 性能提升轻量化设计可以显著减少连杆的质量,降低发动机的整体质量,提高发动机的功率重量比,从而提升汽车的加速性能和燃油经济性。
2. 热效率改善减轻连杆质量可以减少发动机的惯性负荷,降低摩擦损失和热损失,提高发动机的热效率,减少燃油的消耗,降低尾气排放。
3. 减少振动和噪音轻量化设计可以改善发动机的平衡性和稳定性,减少发动机的振动和噪音,提高汽车的乘坐舒适性。
汽车轻量化前沿制造技术的研究进展

在大量 采用 高强 度钢 板 的 同 时 , 了适 合 于这 种 轻量 为 化材料 并获 得最 佳 的力 学性 能 , 些 先进 的轻 量 化 制 一 造 技术 如 : 压成形 、 冲压 成 形 、 光 拼焊 和 管 材 内 液 热 激 高压成 形等 不断 开发 , 并逐步 广泛 应用 于车身制 造 中。
② Sa e a oa r o d acdD s nadMa u c r rV hc oy t eK yL brty f vn e ei n n f t ef e i eB d , t o A g au o l
H u a ie st n n Un v riy,Cha g h 0 2, n s a41 08 CHN ;
L O R i■ U u
WA G Y n N a 。WUQI i 1
( D p.o c a i l nier g u a n ut o t h i,C a gh 12 8 C N; et f Meh n a E g ei ,H n nId s yP l e nc hn sa4 0 0 , H c n n r yc
1 1 液压 成 形技术 .
面尺寸是 减轻 汽车 自重 的最 有 效 手 段 。 目前 , 高强 度
1 1 1 液压成 形技 术原理 .. 板 材液压 成形 如 图 1所 示 , 的原 理是 采 用 液态 它
p i so tt e c m p trsmu a in a h e r s n a ie o h n t lme tn me ia i l t n t e — ont u h o u e i l t s t e r p e e t t ft e f ie ee n u rc lsmu ai e h o v i o n lg n t e s p e in,o tmiain o r c s a a t r oo y i h ha e d sg p i z to fp o e sp r mee s,p o e sc nto p lc to sa d a c r— r c s o r la p ia in n o n
汽车轻量化的发展
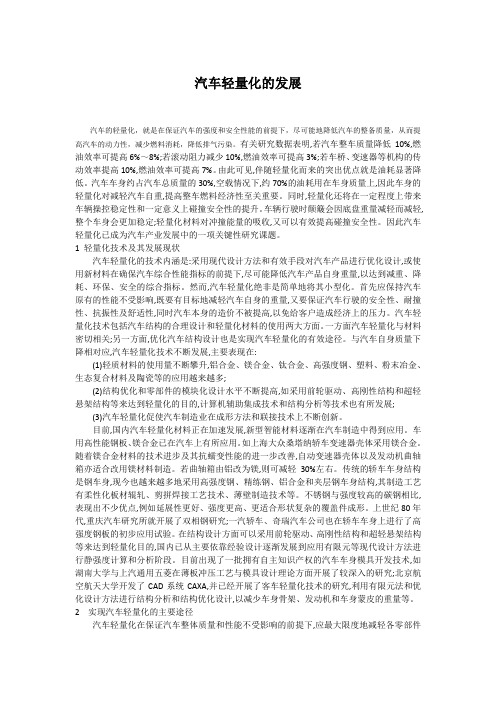
汽车轻量化的发展汽车的轻量化,就是在保证汽车的强度和安全性能的前提下,尽可能地降低汽车的整备质量,从而提高汽车的动力性,减少燃料消耗,降低排气污染。
有关研究数据表明,若汽车整车质量降低10%,燃油效率可提高6%~8%;若滚动阻力减少10%,燃油效率可提高3%;若车桥、变速器等机构的传动效率提高10%,燃油效率可提高7%。
由此可见,伴随轻量化而来的突出优点就是油耗显著降低。
汽车车身约占汽车总质量的30%,空载情况下,约70%的油耗用在车身质量上,因此车身的轻量化对减轻汽车自重,提高整车燃料经济性至关重要。
同时,轻量化还将在一定程度上带来车辆操控稳定性和一定意义上碰撞安全性的提升。
车辆行驶时颠簸会因底盘重量减轻而减轻,整个车身会更加稳定;轻量化材料对冲撞能量的吸收,又可以有效提高碰撞安全性。
因此汽车轻量化已成为汽车产业发展中的一项关键性研究课题。
1 轻量化技术及其发展现状汽车轻量化的技术内涵是:采用现代设计方法和有效手段对汽车产品进行优化设计,或使用新材料在确保汽车综合性能指标的前提下,尽可能降低汽车产品自身重量,以达到减重、降耗、环保、安全的综合指标。
然而,汽车轻量化绝非是简单地将其小型化。
首先应保持汽车原有的性能不受影响,既要有目标地减轻汽车自身的重量,又要保证汽车行驶的安全性、耐撞性、抗振性及舒适性,同时汽车本身的造价不被提高,以免给客户造成经济上的压力。
汽车轻量化技术包括汽车结构的合理设计和轻量化材料的使用两大方面。
一方面汽车轻量化与材料密切相关;另一方面,优化汽车结构设计也是实现汽车轻量化的有效途径。
与汽车自身质量下降相对应,汽车轻量化技术不断发展,主要表现在:(1)轻质材料的使用量不断攀升,铝合金、镁合金、钛合金、高强度钢、塑料、粉末冶金、生态复合材料及陶瓷等的应用越来越多;(2)结构优化和零部件的模块化设计水平不断提高,如采用前轮驱动、高刚性结构和超轻悬架结构等来达到轻量化的目的,计算机辅助集成技术和结构分析等技术也有所发展;(3)汽车轻量化促使汽车制造业在成形方法和联接技术上不断创新。
重型载重汽车车架轻量化设计研究
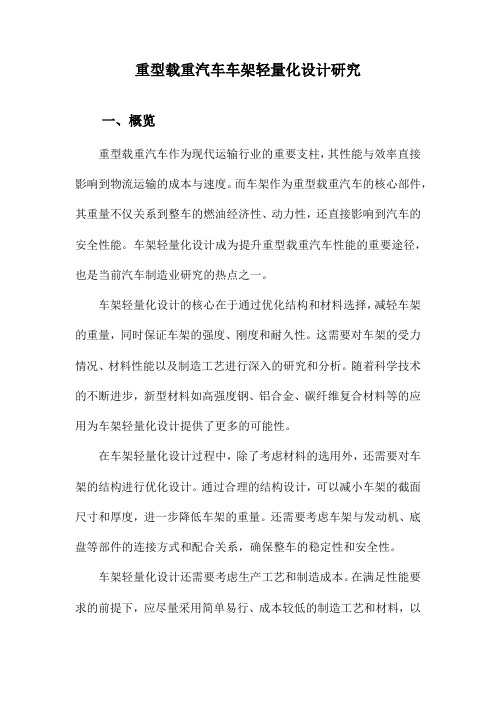
重型载重汽车车架轻量化设计研究一、概览重型载重汽车作为现代运输行业的重要支柱,其性能与效率直接影响到物流运输的成本与速度。
而车架作为重型载重汽车的核心部件,其重量不仅关系到整车的燃油经济性、动力性,还直接影响到汽车的安全性能。
车架轻量化设计成为提升重型载重汽车性能的重要途径,也是当前汽车制造业研究的热点之一。
车架轻量化设计的核心在于通过优化结构和材料选择,减轻车架的重量,同时保证车架的强度、刚度和耐久性。
这需要对车架的受力情况、材料性能以及制造工艺进行深入的研究和分析。
随着科学技术的不断进步,新型材料如高强度钢、铝合金、碳纤维复合材料等的应用为车架轻量化设计提供了更多的可能性。
在车架轻量化设计过程中,除了考虑材料的选用外,还需要对车架的结构进行优化设计。
通过合理的结构设计,可以减小车架的截面尺寸和厚度,进一步降低车架的重量。
还需要考虑车架与发动机、底盘等部件的连接方式和配合关系,确保整车的稳定性和安全性。
车架轻量化设计还需要考虑生产工艺和制造成本。
在满足性能要求的前提下,应尽量采用简单易行、成本较低的制造工艺和材料,以降低整车的生产成本,提高市场竞争力。
重型载重汽车车架轻量化设计是一个涉及材料、结构、工艺等多方面的复杂问题。
通过深入研究和分析,采用合理的设计方法和手段,可以实现车架的轻量化,提高重型载重汽车的性能和效率,为物流运输行业的发展做出贡献。
1. 重型载重汽车在社会经济中的地位与作用重型载重汽车作为道路交通的重要载体,在社会经济发展中占据着举足轻重的地位。
它们不仅是货物运输的主要工具,还是基础设施建设、物流运输、农业生产等领域不可或缺的力量。
随着全球经济一体化的加速推进,重型载重汽车的需求日益增长,对社会经济的发展起着重要的支撑作用。
重型载重汽车在货物运输中发挥着关键作用。
无论是长途运输还是短途配送,重型载重汽车都能以其强大的承载能力和稳定的性能,确保货物安全、高效地到达目的地。
在国际贸易中,重型载重汽车更是扮演着重要角色,它们穿梭于世界各地的港口、仓库和物流中心,将货物运送到各个角落,为国际贸易的繁荣做出了巨大贡献。
电动汽车的轻量化技术研究

目录页
Contents Page
1. 电动汽车轻量化技术概述 2. 材料选择与优化 3. 结构设计与优化 4. 制造工艺与技术 5. 轻量化对性能的影响 6. 轻量化对成本的影响 7. 国内外研究进展 8. 未来发展趋势
电动汽车的轻量化技术研究
电动汽车轻量化技术概述
电动汽车轻量化技术概述
▪ 模块化设计
1.模块化设计是电动汽车轻量化技术的重要手段,通过模块化设计可以将车辆的各个部分拆分 成独立的模块,便于生产和维护。 2.模块化设计可以提高车辆的生产效率和质量,同时也可以降低车辆的重量和成本。 3.模块化设计需要考虑模块的连接方式、接口设计等因素,以保证模块的稳定性和可靠性。
结构设计与优化
轻量化材料的优化
1.材料的组合:通过将不同的材料组合在一起,可以实现轻量化和性能的优化。例如,将铝合金和 碳纤维复合材料组合在一起,可以实现轻量化和强度的优化。 2.材料的加工:通过优化材料的加工工艺,可以提高材料的性能和降低制造成本。例如,通过热处 理和表面处理,可以提高铝合金和镁合金的性能。 3.材料的回收:通过优化材料的回收工艺,可以实现材料的循环利用,降低环境污染。例如,通过 化学回收和物理回收,可以回收和再利用铝合金和镁合金。
电动汽车的轻量化技术研究
国内外研究进展
国内外研究进展
▪ 国内研究进展
1.国内电动汽车轻量化技术研究起步较晚,但近年来发展迅速 ,已取得一些重要成果。 2.国内研究主要集中在材料、结构和工艺等方面,如高强度钢 、铝合金、镁合金等轻质材料的应用,以及车身结构优化、制 造工艺改进等。 3.国内企业如比亚迪、特斯拉等在电动汽车轻量化技术方面投 入大量研发资源,取得了一定的市场优势。
奇瑞汽车轻量化技术新进展

发 ( 图6 ,显著 降低 了零部件 的重量 ( 见 ) 见附表 ) 。 同时 奇瑞公司掌握 了S MC ̄IMT I : G 复合材料 的零 部件设
计 、产 品试制和试验验证的综合开发能力 。
()S a MC后 备 门
l
()G 防 护罩 b MT
图 6
材料变化前后零 件重 量对 比表
成形 、热压 成形和滚 压成形等 材料 成形应 用技术将 成为
首选。
汽车轻量化材料应用现状
轻 量 化 材料 是 指 可用 来减 轻 汽车 自重 的材 料 ,它
有两大 类 :一类 是低密度 的轻质材料 ,如铝合 金、镁合 金 、钛 合金 、塑料 和 复合 材 料等 ;另一 类是 高 强 度材 料 ,如 高强度钢 等。 目前 ,已得到实 际工业化应 用的轻 量化材料主要有 高强度钢 、铝合金 、镁 合金和塑料等。
此 外 ,奇 瑞 公司瑞麒 G5 开发 了镁 合金仪表 板 骨架
成本 与普 通 点焊设 计 基本持 平 ,但 能显 著提 高正 碰性
( 见图5 ),已完成各种试验验证 ,实现批量装车。仪
表板 骨架采用镁 合金 整体压铸 ,绿色环保的 同时单 件减
能,在奇瑞A 的前纵梁上已有批量应用 ( 3 见图7 ),并
轻量化 系数的定义为 :
M L =-- -— -- - — - -- C
2铝合金 .
铝 合金在奇瑞 公司的 产品上 已得 到广泛应用 ,铝合
式中:
L —— 轻量化 系数 ;
金零部件 以铸件 为主 ,还有 少量的型材 和板材 ,已 占到 整车备 重的 1%左右 。典 型应用 为变速 器壳体 、发 动机 0 缸 体 、缸盖 、油底 壳 、底盘转 向节 、控制 臂 、隔热板 和 散热器等零 件 ( 见图3 )。另外 ,在 国家 “6 ”项 目的 83 支持下 ,奇瑞完 成了铝合金板 材的应用开发 工作 ,使A 5
汽车轻量化背景及趋势

图 2020年乘用车节能标准技术选项
图片来自乘用车燃料消耗量第四阶段标准解读,中国汽车燃料消耗量网站
14
2)法规和标准驱动的汽车行业发展态势
新能源汽车的发展
随着关于汽车燃料经济性、节能减排方面的法规和标准愈发严 格,汽车行业着力于开发研究新的能源汽车,可以预见,新能 源汽车会成为汽车行业未来一段时间内发展的重点。 新能源汽车发展趋势
2012
2016
轿车和轻型卡车达到35.5英里/加仑的平均油耗标准 比现行每加仑25英里的标准提高了42% 每车每英里尾气排放降低45克
6
1)汽车行业能耗法规和标准
美国
美国政府于 2012 年 8月1日颁布了针对 2017-2025 (第二阶段)的轻型 汽车燃料经济性及温室气体排放规定,要求2025年美国轻型汽车的平 均燃料经济性达到56.2mpg。
26
3)轻量化与整车性能及生产成本的关系
轻量化与燃油经济性的关系
重型货车: 牵引车/拖车减重50%,整体重量降低23% 货物重量无法降低,运输效率可以提升
27
3)轻量化与整车性能及生产成本的关系
轻量化与动力性的关系
美国颁布的汽车总质量与加速时间关系图(U.S.EPA,2009a data)
13
2)法规和标准驱动的汽车行业发展态势
节能技术发展
针对2020年我国乘用车产品平均燃料消耗量达到 5L/100km的目 标,汽标委从整车、发动机、变速器、车轮 /轮胎等几个方面, 组织开展较大规模的节能技术发展及应用状态调查,对特定技 术的成本、节能效果进行调查,组织开展验证试验。
从减少车辆行驶所需阻力、 提高热动能量转换效率、减 少能量传输过程损失、减少 辅助能量消耗、优化车辆能 量管理等5个方面,提出应 对2020年节能标准的技术选 项
轻量化设计在汽车制造中的研究进展

轻量化设计在汽车制造中的研究进展在当今的汽车制造领域,轻量化设计已成为一项关键的技术发展趋势。
随着环保要求的日益严格以及消费者对燃油经济性和车辆性能的不断追求,汽车制造商们纷纷将目光聚焦于轻量化设计,试图通过减轻车辆重量来实现节能减排、提升性能和增加续航里程等目标。
轻量化设计的重要性不言而喻。
首先,减轻车辆重量能够显著降低燃油消耗和尾气排放。
研究表明,汽车每减重 10%,燃油效率可提高 6%至8%。
这对于应对全球能源危机和环境污染问题具有重要意义。
其次,轻量化有助于提升车辆的加速、制动和操控性能,使驾驶体验更加出色。
此外,对于电动汽车来说,轻量化能够延长电池续航里程,缓解消费者的里程焦虑。
目前,汽车轻量化设计主要通过材料创新、结构优化和制造工艺改进等途径来实现。
在材料方面,高强度钢、铝合金、镁合金和碳纤维复合材料等轻质材料的应用越来越广泛。
高强度钢具有较高的强度和良好的成形性,能够在保证车身强度的前提下减轻重量。
铝合金具有密度小、耐腐蚀等优点,常用于车身覆盖件和发动机部件。
镁合金的密度比铝合金更低,但强度稍逊,适用于一些对重量要求极为苛刻的零部件。
碳纤维复合材料则具有极高的强度和轻量化优势,但由于成本较高,目前主要应用于高端车型和赛车领域。
结构优化是轻量化设计的另一个重要手段。
通过采用先进的计算机辅助设计和模拟技术,工程师们能够对汽车的结构进行精确分析和优化。
例如,采用空心结构、薄壁结构和一体化设计等方法,可以在不影响结构强度的情况下减轻零部件的重量。
此外,合理的车架和车身结构设计能够有效分散载荷,减少材料的使用量。
制造工艺的改进也为轻量化设计提供了有力支持。
激光焊接、液压成型和热成型等先进工艺能够制造出更加复杂和精确的零部件,提高材料的利用率和零部件的强度。
增材制造(3D 打印)技术的出现为汽车轻量化设计带来了新的机遇,通过逐层堆积材料,可以制造出具有复杂内部结构的轻量化零部件。
然而,轻量化设计在汽车制造中也面临着一些挑战。
汽车车身材料轻量化的应用现状及研究进展

汽车车身材料轻量化的应用现状及研究进展【摘要】汽车车身的轻量化是一个复杂的系统工程,也是汽车行业发展的趋势之一,实现车身的轻量化,可以有效的节约能源,减少废气排放。
本文综述了车身材料轻量化的应用现状及最新研究进展。
【关键词】汽车车身轻量化新材料据最新数据显示,截至2012年底,中国机动车保有量达到2.38亿辆。
其中,汽车保有量首次突破1亿辆大关,跃居全球第二,预计到2020年中国汽车保有量将超过2亿辆。
到2015年,全球汽车保有量将从2007年的近9.2亿辆增至11.2亿辆左右。
汽车保有量的增加在给人们出行带来方便的同时也带来了能耗,安全和环保问题。
为了治理环境污染,各国相继对大气中各种排放污染源提出控制要求,制定强制性排放标准,以控制汽车污染物的排放量。
按照世界铝业协会的统计标准,汽车总重减轻10%,百公里油耗减少6%-8%,排放降低5%-6%,而燃油消耗降低1L,CO2排放量将降低2.45Kg。
可见汽车轻量化是实现节能减排的重要手段,且能同时满足安全、油耗和排放三项法规要求。
轻量化,即是在满足碰撞要求且保证汽车整体性能不受影响的前提下,最大限度地减轻各零部件的质量,达到质量-性能-成本三者的最优结合。
实现汽车轻量化主要有3种途径:一是改进汽车结构,使部件薄壁化、中空化、小型化及复合化;二是开发新型轻质材料,如使用铝、镁合金等有色金属、塑料及非金属复合材料,或者截面厚度较薄的高强钢度钢;三是采用先进的制造工艺,如激光拼焊、液压成型、辊压成型等。
汽车车身质量占整车自重的30%-40%[1],对于整车的轻量化具有重要的意义,因此轻量化新材料的开发与应用是汽车轻量化的最有效途径之一。
1 高强度钢板材料钢铁材料由于其高强度,成本低的特点,相对于高分子材料和镁、铝合金材料而言仍是车身材料最广泛的应用材料。
钢铁材料的结构已发生很大变化,高强度钢的用量越来越大。
目前已经先后开发出高强度钢(屈服强度大于210Mpa)和超高强度钢(屈服强度大于550Mpa)。
汽车轻量化技术的研究与进展
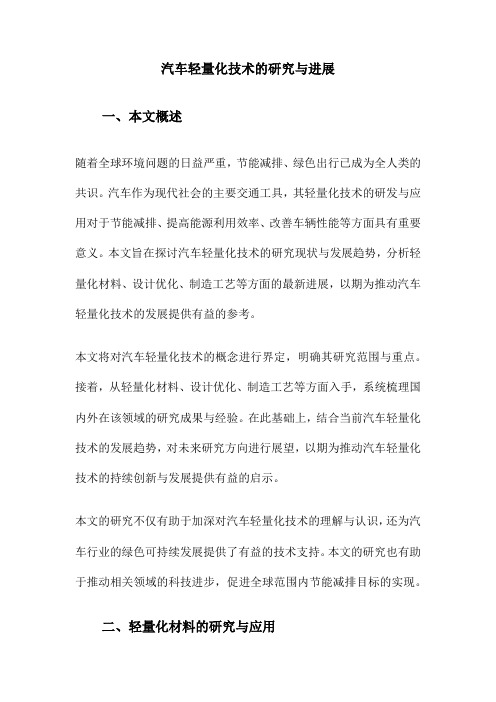
汽车轻量化技术的研究与进展一、本文概述随着全球环境问题的日益严重,节能减排、绿色出行已成为全人类的共识。
汽车作为现代社会的主要交通工具,其轻量化技术的研发与应用对于节能减排、提高能源利用效率、改善车辆性能等方面具有重要意义。
本文旨在探讨汽车轻量化技术的研究现状与发展趋势,分析轻量化材料、设计优化、制造工艺等方面的最新进展,以期为推动汽车轻量化技术的发展提供有益的参考。
本文将对汽车轻量化技术的概念进行界定,明确其研究范围与重点。
接着,从轻量化材料、设计优化、制造工艺等方面入手,系统梳理国内外在该领域的研究成果与经验。
在此基础上,结合当前汽车轻量化技术的发展趋势,对未来研究方向进行展望,以期为推动汽车轻量化技术的持续创新与发展提供有益的启示。
本文的研究不仅有助于加深对汽车轻量化技术的理解与认识,还为汽车行业的绿色可持续发展提供了有益的技术支持。
本文的研究也有助于推动相关领域的科技进步,促进全球范围内节能减排目标的实现。
二、轻量化材料的研究与应用随着全球环保意识的增强和能源危机的日益严峻,汽车轻量化已成为汽车工业发展的重要趋势。
轻量化材料的研究与应用是实现这一目标的关键。
轻量化材料主要包括高强度钢、铝合金、镁合金、塑料及复合材料等。
高强度钢以其优良的力学性能和相对较低的成本,在汽车制造中得到了广泛应用。
通过优化钢材成分、改进热处理工艺和微观结构设计,高强度钢不仅具有更高的强度,而且具有更好的塑性和韧性,能够满足汽车结构件对材料性能的要求。
铝合金以其低密度、高比强度、良好的加工性能和耐腐蚀性等特点,在汽车轻量化中发挥着重要作用。
尤其是铝合金铸件和锻件,因其结构紧凑、重量轻,被广泛应用于发动机、底盘和车身等部件的制造中。
镁合金作为一种轻质、高强度的金属材料,在汽车轻量化领域也备受关注。
镁合金具有良好的电磁屏蔽性能、高的阻尼性能和低的热膨胀系数,特别适用于制造汽车仪表板、座椅框架等部件。
然而,镁合金的耐腐蚀性较差,限制了其在汽车领域的应用。
电动汽车车身轻量化技术研究

NEW ENERGY AUTOMOBILE | 新能源汽车电动汽车车身轻量化技术研究翟慧颖 胡新河南职业技术学院汽车与交通学院 河南省郑州市 450046摘 要: 与传统燃油车相比,纯电动车在取消发动机及部分附件的同时,增加了“三电系统”,按行业统计数据,其质量较传统车增加一般为15%~40%。
因其质量明显增加,对车辆电耗、续驶里程、动力性、制动性、被动安全、车辆可靠和耐久均带来不利影响,而轻量化则是消除这些影响的重要应对手段之一。
着重对如何实现电动汽车车身的轻量化的问题探讨,以轻量化意义、轻量化发展现状及趋势为切入点,提出电动汽车车身轻量化的技术路线。
关键词:电动汽车 车身轻量化 技术路线1 车身轻量化内涵及意义在2020年发布的《节能与新能源汽车技术路线图2.0》(下文简称路线图2.0)中确认了全球汽车技术“低碳化、信息化、智能化”的发展方向,节能汽车仍是市场主力,呈现出一体化、轻量化、高压化发展趋势。
路线图2.0中形成了总体技术路线图+节能汽车、纯电动和插电式混合动力汽车、氢燃料电池汽车、智能网联汽车、汽车智能制造与关键装备、汽车动力电池、新能源汽车电驱动总成系统、充电基础设施、汽车轻量化的1+9研究布局[1]。
如图1所示。
由此可见,汽车轻量化作为共性指标,贯穿在国家新能源汽车进步发展的全过程中。
汽车轻量化是一项复杂的系统工程,它是在成本控制与性能改进条件下,通过轻量化结构设计与轻量化材料和制造技术在整车产品上的集成应用而实现的产品减重。
面对日益严峻的油耗法规,世界各国汽车企业都在采取积极的措施以推动汽车产品的节能减排,轻量化是一种有效的手段。
因此,推动汽车轻量化的进步,能够快速提高自主品牌汽车的开发能力。
研究表明,电动汽车整车质量每降低100kg,续航里程可增加17km(约提升3.6%),相当于增加2.5kwh电量,节约电池成本约3000元。
路线图2.0中制定了2020-2035期间,整车轻量化系数降低目标,见下表1。
- 1、下载文档前请自行甄别文档内容的完整性,平台不提供额外的编辑、内容补充、找答案等附加服务。
- 2、"仅部分预览"的文档,不可在线预览部分如存在完整性等问题,可反馈申请退款(可完整预览的文档不适用该条件!)。
- 3、如文档侵犯您的权益,请联系客服反馈,我们会尽快为您处理(人工客服工作时间:9:00-18:30)。
c u r r e n t r e s e a r c h a n d f u t u r e t r e n d s o f a u t o m o t i v e l i g h t w e i g h t t e c h n o l o g y i n C h i n a a n d i n t h e wo r l d f r o m t h r e e a s p e c t s : t h e s t r u c t u r a l o p t i mi z a t i o n , t h e l i g h t w e i g h t m a t e r i a l s , a n d t h e a d v a n c e d ma n u f a c t u r i n g t e c h n o l o g y . T h e r e v i e w i n c l u d e s t h e b a s i c p r i n c i p l e s a n d r e s e a r c h d e v e l o p me n t s o f s t r u c t u r a l s i z e o p t i mi z a t i o n , s h a p e o p t i mi z a t i o n , t o p o l o g i c a l o p t i mi z a t i o n , a n d mu l t i d i s c i p l i n a r y d e s i g n o p t i mi z a t i o n . A n d i t i n t r o d u c e s t h e a p p l i c a t i o n s o f h i g h - s t r e n g t h s t e e l , a l u mi n u m a l l o y , ma g n e s i u m a l l o y , p l a s t i c ma t e r i a l , c o mp o s i t e ma t e r i a l ;
1 / 1 3
1 —1 6
CN 1 1 - 5 9 0 4 / U
汽车轻量化技术的研究与进展
范子杰,桂 良进 ,苏瑞意
( 清华大学 汽车安全与节能国家重点实验室 ,北京 1 0 0 0 8 4 ,中国 )
摘 要:汽车轻量化是实现节能减排的重要措施之 _,对汽车工业的可持续发展具有重要意义。本 文从结构优化设计、轻量化材料的 应用和先进制造工艺这三个方面对汽车轻量化技术的国内 外研究 现状和发展趋势进行了 综述。这包括: 汽车结构的 尺寸优化、形状优化、拓扑优化和多学科设计优化 的基本原理和研究进展;高强度钢、铝合金、镁合金、塑料和复合材料;以及液压成型和激光焊接 工艺在汽车中的使用现状。作者认为: 汽车轻量化技术的未来研究方向是: 汽车结构优化设计理论的 完善、多 材料一体化、零部件的轻量化和轻量化技术的系统化与 集成化。 关键词:汽车轻量化技术; 多学科设计优化; 高强度钢; 液压成型; 激光焊接
F AN Z i j i e , GU I L i a n g j i n , S U R u i y
( T s i n g h u a U n i v e r s i t y , S t a t e K e y L a b o r a t o r y o f A u t o m o t i v e S a f e t y a n d E n e r g y , B e i j i n g 1 0 0 0 8 4 , C h i n a )
I SSN 1 6 7 4 - 8 4 8 4
—
—
汽 车安全与 节能 学报 , 2 0 1 4年 ,第 5卷 第 1 期
J Au t o mo t i v e S a f e t y a n d En e r g y , 2 0 1 4 . Vo 1 . 5 No . 1
Ab s t r a c t : L i g h t w e i g h t i n g o f a u t o m o t it me a s u r e f o r e n e r g y c o n s e r v a t i o n a n d e mi s s i o n s
r e d u c t i o n w i t h s i g n i i f c a n c e f o r s u s t a i n a b l e d e v e l o p me n t o f a u t o mo t i v e i n d u s t r y . T h i s p a p e r s u mma r i z e s t h e
a s w e l l a s t h e a p p l i c a t i o n s o f h y d r o f o r m a n d l a s e r w e l d i n g i n a u t o mo t i v e i n d u s t r y . T h e a u t h o r s t h i n k t h a t t h e
中图分类号 :U 6 4 3 . 0 2 文献 标识码 :A D OI :1 0 . 3 9 6 9 / j . i s s n . 1 6 7 4 — 8 4 8 4 . 2 0 1 4 . 0 1 . 0 0 1
Re s e a r c h a n d de v e l o pm e n t o f a ut o mo t i v e l i g h t we i g ht t e c hno l o g y