从SCR废催化剂中回收重金属的处理工艺
湿法工艺回收板式SCR废弃催化剂中的钛、钒、钼
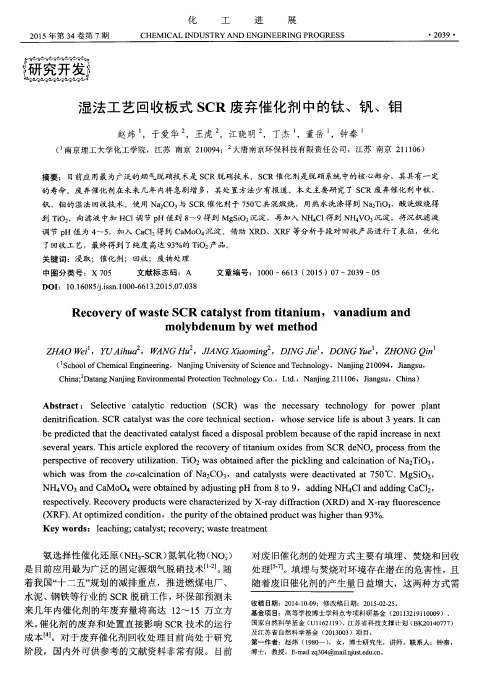
D oI :1 0 . 1 6 0 8 5  ̄ . i s s n . 1 0 0 0 - 6 6 1 3 . 2 0 1 5 0 7 . 0 3 8
( 南 京 理 工 大 学 化 工 学 院 ,江 苏 南 京 2 1 0 0 9 4 ; 大 唐 南 京 环 保 科 技 有 限 责任 公 司 , 江 苏 南 京 2 1 1 1 0 6 )
摘要 : 目前应用最 为广泛的烟气脱硝技术是 S C R脱硝技术 。S C R催化 剂是脱硝 系统 中的核 心部 分,其具有 一定
p e r s p e c t i v e o f r e c o v e y r u t i l i z a t i o n . T i O2 wa s o b t a i n e d a f t e r t h e p i c k l i n g a n d c a l c i n a t i o n o f Na 2 T i O3 ,
的寿命。废弃催化 剂在 未来几年 内将急剧增 多,其处置方法少有报道 。本 丈主要研 究 了 S C R废 弃催化 剂 中钛 、
钒 、钼 的湿法回收技 术。使用 Na 2 C O 3 与 S C R催化 剂于 7 5 0  ̄ C共混煅烧 ,用 热水洗涤得到 Na 2 T i O3 ,酸洗煅烧得 到T i O 2 。向滤液 中加 HC 1 调节p H值到 8 ~9得到 Mg S i O3 沉淀 ,再加入 NH 4 C 1 得到 N/ - / 4 VO 3 沉淀。将沉钒滤液
( S c h o o l o f C h e mi c a l E n g i n e e r i n g ,Na n j i n g U n i v e r s i t y o f S c i e n c e a n d T e c h n o l o g y ,Na n j i n g 2 1 0 0 9 4 ,J i a n g s u , C h i n a ; D a t a n g Na n j i n g E n v i r o n me n t a l P r o t e c t i o n T e c h n o l o y g C o . ,L t d . ,Na n j i n g 2 1 1 1 0 6 ,J i a n g s u , v e r y o f wa s t e SCR c a t a l y s t f r o m t i t a ni um , va na di um a nd mo l y bde num b y we t me t ho d
SCR脱硝催化剂再生工艺浅析

SCR脱硝催化剂再生工艺浅析SCR脱硝催化剂再生工艺浅析摘要:脱硝系统已成为燃煤电厂的重要组成部分,脱硝催化剂占脱硝工程投资比例较高,加大对失效催化剂的再生力度,成为降低燃煤电厂脱硝运行费用的重要突破口。
同时脱硝催化剂再生具有显著的社会效益和环保效益。
本文将结合本公司再生生产简单介绍脱硝催化剂的工厂再生工艺以及如何选择合适的化学清洗液。
关键词:SCR;催化剂;再生;清洗液引言催化剂是SCR系统的核心部件,一般催化剂使用3年左右就会出现失活现象。
造成失活的原因主要有催化剂的烧结、砷中毒、钙中毒、碱金属中毒、SO3 中毒以及催化剂空隙积灰堵塞等。
对失活催化剂更换或是再生将直接影响SCR系统的运行成本[1-3]。
因此,研究SCR催化剂的失活与再生,具有很重要的现实意义。
我国催化剂研究已有好多年,目前比较成熟的有V2O5-WO3/TiO2、V2O5-MoO3/TiO2 及V2O5-WO3-MoO3/TiO2,它们都是以TiO2为载体,V2O5、WO3、、MoO3、为活性物质负载在其上。
具有较好的活性、高选择性以及强抗中毒性,在商业上已经投入生产。
据统计,2012年新投运火电厂烟气脱硝机组容量约为9000kW,其中,采用SCR工艺的脱硝机组容量占当年投运脱硝机组总容量的98%。
一、失活SCR催化剂的再生技术在实际应用领域,脱硝催化剂失效后主要采用现场再生及工厂再生两种方式。
由于现场再生易对现场环境和水质造成污染,且现场再生的催化剂的质量和性能较差,所以工厂再生是发展方向。
经过再生后的SCR催化剂,活性和使用寿命等能够达到运行要求,可以实现再利用,达到节省火电厂环保投入和运行成本的目的[4-6]。
SCR催化剂工厂再生工艺首先使用超声水洗清除废旧催化剂表面的溶解性碱金属物质和堵塞在SCR催化剂孔道中的灰尘颗粒沉积物,超声水洗过程中使用渗透促进剂、表面活性剂等有机高分子清洗剂提高清洗能力,特别是对硫酸盐等污垢的去除,为了进一步提高SCR催化剂的活性,应用超声浸渍法在催化剂表面负载钒、钨、钼等活性组分,以满足提高脱硝催化活性的要求。
SCR废催化剂回收生产中重金属物的治理
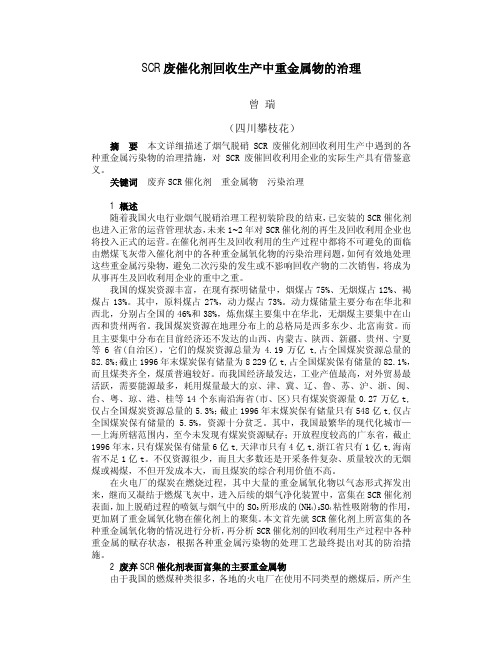
中(因为温度呈逐渐降低的状态),最终随烟气直接排入大气的汞(形态为元素
汞 HgO,具有相对比较稳定的形态,难以被污染控制设备收集)不到气化汞总量
的 10%。 废弃 SCR 催化剂中富集的气态二价汞(Hg2+),具有水溶性的特点,在回
收工艺的除灰清洗工序基本就会被清除掉大部分,通过碱浸出工序进入浸出液的
部分仅占总汞量的 4%~18%。
2.3 铅(Pb)
煤中的铅是大气铅污染的来源之一,煤燃烧后产生 20%~25%的灰份,煤中的
大部分铅在燃烧过程汽化后凝结于飞灰中形成铅尘。我国煤中铅含量的平均值为
15.55mg/kg,其燃烧产物中铅的分布情况如表 2 所示。
表 2 铅在煤燃烧产物中的分配(%)
项目
底渣
3 废弃 SCR 催化剂回收利用生产过程中重金属物的赋存情况
3.1 典型的 SCR 废催化剂回收工艺
典型的 SCR 废催化剂回收工艺如下图 1 所示:
废 SCR 催化剂 浸出渣
浸出液
净化液
吹扫、洗 涤除灰
粉碎
高温碱 液浸出
积尘
危废填埋厂填埋
浸出渣
制备富钛料
浸出液
沉淀钒钨
盐酸脱钠
洗涤干燥
富钛料成品
工艺废水
4.1 各种重金属物的处理技术
4.1.1 砷化合物的处理技术
砷化合物的常规处理方法包括化学沉淀法、共沉淀法、生化法、吸附法、离
子交换法、离子浮选法等。
①化学沉淀法
砷能够与许多金属离子形成难溶化合物,例如砷酸根或亚砷酸根与钙、三价
铁、三价铝等离子均可形成难溶盐,经过滤后即可除去液相中的砷。由于亚砷酸
盐的溶解度一般都比砷酸盐的高很多,不利于沉淀反应的进行,因此在许多实际
浅谈SCR废催化剂的回收再利用
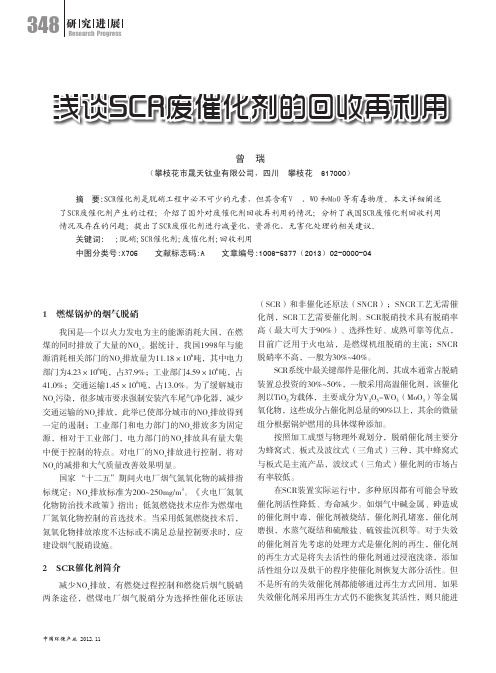
曾 瑞(攀枝花市晟天钛业有限公司,四川 攀枝花 617000)摘 要:SCR催化剂是脱硝工程中必不可少的元素,但其含有V 2O 5、WO 3和MoO 3等有毒物质。
本文详细阐述了SCR废催化剂产生的过程;介绍了国外对废催化剂回收再利用的情况;分析了我国SCR废催化剂回收利用情况及存在的问题;提出了SCR废催化剂进行减量化、资源化、无害化处理的相关建议。
关键词:NO x ;脱硝;SCR催化剂;废催化剂;回收利用中图分类号:X705 文献标志码:A 文章编号:1006-5377(2013)02-0000-04浅谈SCR废催化剂的回收再利用1 燃煤锅炉的烟气脱硝我国是一个以火力发电为主的能源消耗大国,在燃煤的同时排放了大量的NO x 。
据统计,我国1998年与能源消耗相关部门的NO x 排放量为11.18×106吨,其中电力部门为4.23×106吨,占37.9%;工业部门4.59×106吨,占41.0%;交通运输1.45×106吨,占13.0%。
为了缓解城市NO x 污染,很多城市要求强制安装汽车尾气净化器,减少交通运输的NO x 排放,此举已使部分城市的NO x 排放得到一定的遏制;工业部门和电力部门的NO x 排放多为固定源,相对于工业部门,电力部门的NO x 排放具有量大集中便于控制的特点。
对电厂的NO x 排放进行控制,将对NO x 的减排和大气质量改善效果明显。
国家 “十二五”期间火电厂烟气氮氧化物的减排指标规定:NO x 排放标准为200~250mg/m 3。
《火电厂氮氧化物防治技术政策》指出:低氮燃烧技术应作为燃煤电厂氮氧化物控制的首选技术。
当采用低氮燃烧技术后,氮氧化物排放浓度不达标或不满足总量控制要求时,应建设烟气脱硝设施。
2 SCR催化剂简介减少NO x 排放,有燃烧过程控制和燃烧后烟气脱硝两条途径,燃煤电厂烟气脱硝分为选择性催化还原法(SCR)和非催化还原法(SNCR);SNCR工艺无需催化剂,SCR工艺需要催化剂。
SCR催化剂再生与回收

SCR催化剂再生与回收一:硫酸处理再生比单纯的水洗再生更有效,酸洗再生后K2O得以完全清除,同时在催化剂表面引入了硫酸根离子,使其再生后的脱销活性在350℃-500℃内,稀硫酸的浓度最佳为0.5mol/L,催化剂的脱销活性能够达到中毒前的92%。
这主要是因为硫酸根离子在催化剂表面的出现,增加了酸性位的数量,提高了酸性位的强度。
钒的溶解量随再生溶液的PH值变化,PH值越低,被溶解的钒越多。
钨的浸出量相对于其在催化剂中的担载量并不明显。
研究采用0.5mol/L的稀硫酸对KCl中毒的催化剂进行再生,当反应温度超过300℃后,再生后的催化剂表现出比新鲜催化剂更高的脱销活性。
这可能是由于表面硫酸物种的促进作用,钾被稀硫酸洗去,以及V-OH基团得到恢复。
酸液再生对Ca中毒的SCR 催化剂恢复效果也较好。
二:①还原浸出-氧化沉钒法。
该法将废钒催化剂加水加热煮沸,并加入二氧化硫或亚硫酸钠还原,使五氧化二钒还原成四价钒呈硫酸钒酰形态进入溶液,然后加入氧化剂氯酸钾氧化沉钒。
②酸性浸出-氧化沉钒法。
用盐酸或硫酸溶液升温浸出,同时加入氧化剂氯酸钾氧化四价钒为五价钒,五氧化二钒的浸出率可达95%-98%,再用碱溶液调节PH值,煮沸溶液得到五氧化二钒沉淀。
③碱性浸出-沉钒法。
由于五氧化二钒为两性氧化物,可采用酸液浸取液,采用碱液加以浸取回收。
用NaOH或者碳酸钠溶液在90℃下浸出,溶液过滤后调整PH值1.6-1.8,煮沸得到五氧化二钒沉淀。
碱浸法五氧化二钒的回收率与酸法相当,但碱法回收五氧化二钒的纯度不如酸法。
④高温活化法。
将废钒催化剂直接进行高温活化,焙烧时不加任何添加剂,然后用碳酸氢钠浸出,同时加入少量氯酸钾氧化溶液,通过过滤、浓缩浸出液,再加入氯化铵使钒以偏钒酸铵形式沉淀,干燥、煅烧得到五氧化二钒产品。
三:再生技术联用在实际的操作中,由于催化剂的中毒因素很多,所以再生方法也不限于一种,往往由多种方法组合,最常用的工艺:去灰→水洗→超声波化学清洗→活性物质负载→干燥。
废弃SCR脱硝催化剂中二氧化钛的回收和提纯研究
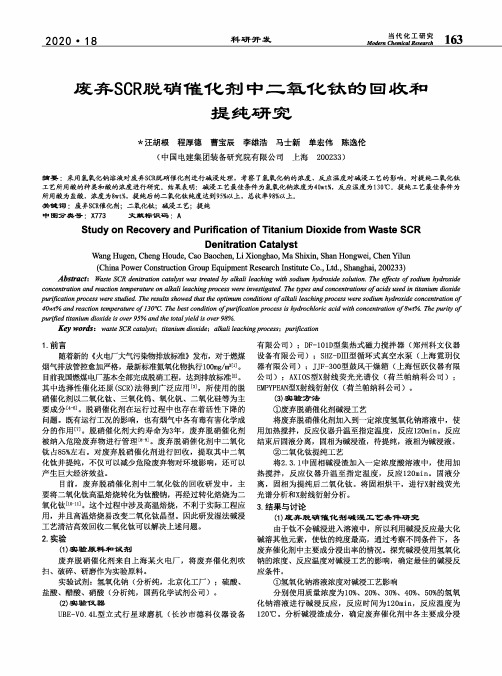
当代化工研究Modern Chemical Research163 2020•18科研开发废弃SCR脱硝催化剂中二氧化钛的回收和提纯研究*汪胡根程厚德曹宝辰李雄浩马士新单宏伟陈逸伦(中国电建集团装备研究院有限公司上海200233)摘耍:采用氢氧化钠溶液对废弃SCR脱硝催化剂进行碱浸处理,考察了氢氧化钠的浓度、反应温度对碱浸工艺餉影响.对提纯二氧化钛工艺所用酸的种类和酸餉浓度进行研究.结果表明:碱浸工艺最佳条件为氢氧化钠浓度为40wt%,反应温度为130r.提纯工艺最佳条件为所用酸为盐酸,浓度为8wt%,提纯后的二氧化钛纯度达到95%以上,总收率98%以上.关键词:废弃SCR催化剂;二氧化钛;碱浸工艺;提纯中图分类号:X773文献标识码:AStudy on Recovery and Purification of Titanium Dioxide from Waste SCRDenitration CatalystWang Hugen,Cheng Houde,Cao Baochen,Li Xionghao,Ma Shixin,Shan Hongwei,Chen Yilun(China Power Construction Group Equipment Research Institute Co.,Ltd.,Shanghai,200233) Abstracts Waste SCR denitration catalyst was treated by alkali leaching with sodium hydroxide solution.The effects of sodium hydroxide concentration and reaction temperature on alkali leaching p rocess were investigated.The types and concentrations of a cids used in titanium dioxide purification process were studied.The results showed that the optimum conditions of a lkali leaching p rocess were sodium hydroxide concentration of 40wt%and reaction temperature of130°C.The best condition of p urification process is hydrochloric acid with concentration of8wf%.The purity of purified titanium dioxide is over95%and the total y ield is over98%.Key words:waste SCR catalyst;titanium dioxide^alkali leaching p rocess purification1.前言随着新的《火电厂大气污染物排放标准》发布,对于燃煤烟气排放管控愈加严格,最新标准氮氧化物执行lOOmg/mMU。
一种从废旧SCR脱硝催化剂中回收钛、钒、钨的方法
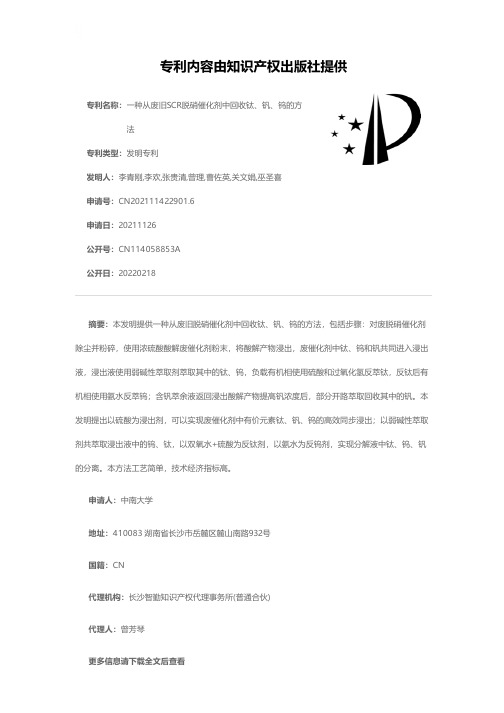
专利名称:一种从废旧SCR脱硝催化剂中回收钛、钒、钨的方法
专利类型:发明专利
发明人:李青刚,李欢,张贵清,曾理,曹佐英,关文娟,巫圣喜
申请号:CN202111422901.6
申请日:20211126
公开号:CN114058853A
公开日:
20220218
专利内容由知识产权出版社提供
摘要:本发明提供一种从废旧脱硝催化剂中回收钛、钒、钨的方法,包括步骤:对废脱硝催化剂除尘并粉碎,使用浓硫酸酸解废催化剂粉末,将酸解产物浸出,废催化剂中钛、钨和钒共同进入浸出液,浸出液使用弱碱性萃取剂萃取其中的钛、钨,负载有机相使用硫酸和过氧化氢反萃钛,反钛后有机相使用氨水反萃钨;含钒萃余液返回浸出酸解产物提高钒浓度后,部分开路萃取回收其中的钒。
本发明提出以硫酸为浸出剂,可以实现废催化剂中有价元素钛、钒、钨的高效同步浸出;以弱碱性萃取剂共萃取浸出液中的钨、钛,以双氧水+硫酸为反钛剂,以氨水为反钨剂,实现分解液中钛、钨、钒的分离。
本方法工艺简单,技术经济指标高。
申请人:中南大学
地址:410083 湖南省长沙市岳麓区麓山南路932号
国籍:CN
代理机构:长沙智勤知识产权代理事务所(普通合伙)
代理人:曾芳琴
更多信息请下载全文后查看。
干湿法结合工艺回收废弃CR脱硝催化剂中的钛、钒和钨
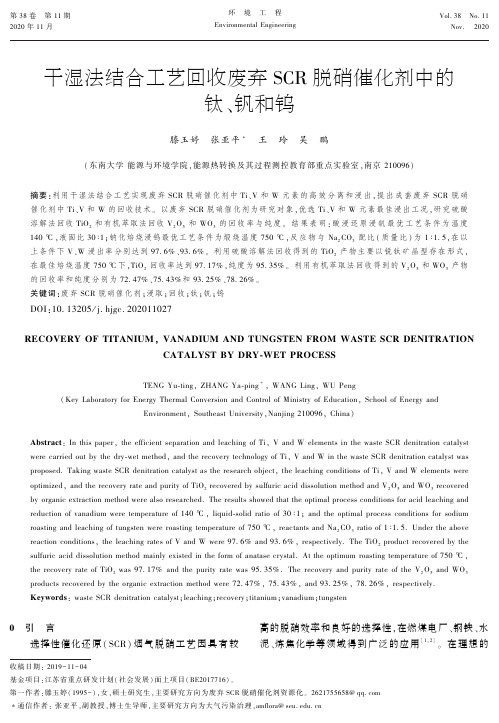
第38卷㊀第11期2020年11月环㊀境㊀工㊀程Environmental EngineeringVol.38㊀No.11Nov.㊀2020干湿法结合工艺回收废弃SCR 脱硝催化剂中的钛、钒和钨滕玉婷㊀张亚平∗㊀王㊀玲㊀吴㊀鹏(东南大学能源与环境学院,能源热转换及其过程测控教育部重点实验室,南京210096)摘要:利用干湿法结合工艺实现废弃SCR 脱硝催化剂中Ti ㊁V 和W 元素的高效分离和浸出,提出成套废弃SCR 脱硝催化剂中Ti ㊁V 和W 的回收技术㊂以废弃SCR 脱硝催化剂为研究对象,优选Ti ㊁V 和W 元素最佳浸出工况,研究硫酸溶解法回收TiO 2和有机萃取法回收V 2O 5和WO 3的回收率与纯度㊂结果表明:酸浸还原浸钒最优工艺条件为温度140ħ,液固比30ʒ1;钠化焙烧浸钨最优工艺条件为煅烧温度750ħ,反应物与Na 2CO 3配比(质量比)为1ʒ1.5,在以上条件下V ㊁W 浸出率分别达到97.6%㊁93.6%㊂利用硫酸溶解法回收得到的TiO 2产物主要以锐钛矿晶型存在形式,在最佳焙烧温度750ħ下,TiO 2回收率达到97.17%,纯度为95.35%㊂利用有机萃取法回收得到的V 2O 5和WO 3产物的回收率和纯度分别为72.47%㊁75.43%和93.25%㊁78.26%㊂关键词:废弃SCR 脱硝催化剂;浸取;回收;钛;钒;钨DOI:10.13205/j.hjgc.202011027RECOVERY OF TITANIUM ,VANADIUM AND TUNGSTEN FROM WASTE SCR DENITRATIONCATALYST BY DRY-WET PROCESSTENG Yu-ting,ZHANG Ya-ping ∗,WANG Ling,WU Peng(Key Laboratory for Energy Thermal Conversion and Control of Ministry of Education,School of Energy andEnvironment,Southeast University,Nanjing 210096,China)Abstract :In this paper,the efficient separation and leaching of Ti,V and W elements in the waste SCR denitration catalystwere carried out by the dry-wet method,and the recovery technology of Ti,V and W in the waste SCR denitration catalyst wasproposed.Taking waste SCR denitration catalyst as the research object,the leaching conditions of Ti,V and W elements wereoptimized,and the recovery rate and purity of TiO 2recovered by sulfuric acid dissolution method and V 2O 5and WO 3recoveredby organic extraction method were also researched.The results showed that the optimal process conditions for acid leaching andreduction of vanadium were temperature of 140ħ,liquid-solid ratio of 30ʒ1;and the optimal process conditions for sodiumroasting and leaching of tungsten were roasting temperature of 750ħ,reactants and Na 2CO 3ratio of 1ʒ1.5.Under the above reaction conditions,the leaching rates of V and W were 97.6%and 93.6%,respectively.The TiO 2product recovered by thesulfuric acid dissolution method mainly existed in the form of anatase crystal.At the optimum roasting temperature of 750ħ,the recovery rate of TiO 2was 97.17%and the purity rate was 95.35%.The recovery and purity rate of the V 2O 5and WO 3products recovered by the organic extraction method were 72.47%,75.43%,and 93.25%,78.26%,respectively.Keywords :waste SCR denitration catalyst;leaching;recovery;titanium;vanadium;tungsten㊀㊀㊀㊀㊀㊀㊀㊀收稿日期:2019-11-04基金项目:江苏省重点研发计划(社会发展)面上项目(BE2017716)㊂第一作者:滕玉婷(1995-),女,硕士研究生,主要研究方向为废弃SCR 脱硝催化剂资源化㊂2621755658@ ∗通信作者:张亚平,副教授,博士生导师,主要研究方向为大气污染治理,amflora@0㊀引㊀言选择性催化还原(SCR)烟气脱硝工艺因具有较高的脱硝效率和良好的选择性,在燃煤电厂㊁钢铁㊁水泥㊁炼焦化学等领域得到广泛的应用[1,2]㊂在理想的环㊀境㊀工㊀程第38卷情况下,SCR脱硝催化剂可以长期使用,但由于长期暴露在没有经过除尘脱硫的有毒烟气中,烟气中的粉煤灰会堵塞催化剂微孔,有毒烟化合物会导致催化剂在运行时失活,使用寿命缩短[3]㊂随着我国 十三五 规划推进燃煤电厂㊁水泥㊁钢铁等行业的SCR脱硝工作,环保部发布了‘全面实施燃煤电厂超低排放和节能改造工作方案“,要求2020年前基本完成所有燃煤电厂的超低排放改造,SCR脱硝催化剂需求量也随之飞速增加[4]㊂以火电行业为例,据中国环保产业协会脱硫脱硝委员会公布的数据,截至2016年底,国内已投运火电厂烟气脱硝机组容量约86400万kW,占全国火电机组容量的82%,占全国煤电机组容量的91.7%㊂另外,从2013年开始,国内火电机组大规模采用SCR脱硝工程,约80%使用进口催化剂,使用寿命一般约为5年,因此2019年将迎来催化剂报废的峰值,预计仅火电行业,每年废弃的催化剂将高达5000万m3[5]㊂2014年8月,国家环保部正式发布‘关于加强废烟气脱硝催化剂监管工作的通知“,将废烟气脱硝催化剂(钒钛系)纳入危险废物进行管理,在2016版‘国家危险废物名录“中已将废脱硝催化剂(钒钛系)归为 HW50废催化剂 [6]门类㊂目前针对废弃SCR脱硝催化剂的处理,对于可逆性中毒或者活性降低的催化剂可再生利用,而不可再生的废催化剂主要采用填埋㊁焚烧和回收处理[7,8],不仅产生大量土地资源需求,且不能彻底解决其环境污染风险,此外SCR脱硝催化剂本身含有的TiO2㊁V2O5和WO3随着丢弃也会浪费[9]㊂已有研究通过物理㊁化学方法将有价重金属或者是对环境造成严重污染的物质从催化剂中提取并循环利用[10,11]㊂当前的废SCR脱硝催化剂有价金属提取技术研究已有部分环保公司完成了中试,但具有参考价值的文献资料较少,目前主要工艺有2种,即干法回收和湿法回收工艺[12]㊂干法回收工艺研究方面:KIM等[13]采用钠化焙烧 水浸出法,对SCR催化剂进行回收,最佳W浸出率和钒浸出率分别为92%㊁46%㊂Zhao等[14]研究了在高压釜中通过钠化焙烧法以Na2WO4的形式回收钨,但此法存在一些缺陷,废催化剂中含有SiO2㊁Al2O3等杂质,在焙烧过程中,钒可与其发生反应转化为含钒硅酸盐,导致钒浸出率的降低㊂湿法回收工艺研究方面:李力成等[15]通过对比4种常规酸在不同工况条件对废催化剂中V2O5的提取效果,结果表明,钒浸出率最佳可达72.9%㊂张兵兵等[16]以稀硫酸浸出研究为基础,在常规酸浸的同时向催化剂中加入还原剂Na2SO3,钒的回收率为87%,样品纯度可达95%以上㊂但通过酸法湿法工艺浸出废催化剂中的W元素效率较低㊂针对目前废弃SCR脱硝催化剂回收技术存在有价金属Ti㊁V㊁W不能同时达到高浸出率的缺陷,本文利用干湿法结合工艺实现废弃SCR脱硝催化剂中钒㊁钨和钛元素的高效分离和浸出,回收二氧化钛(TiO2)作为生产钛白粉的原料,同时利用有机萃取法从钒㊁钨浸出液中回收五氧化二钒(V2O5)和三氧化钨(WO3),以期实现SCR废脱硝催化剂的资源化利用㊂1㊀实验部分1.1㊀实验原料原料:SCR废弃V2O5-WO3/TiO2脱硝催化剂㊂试剂:浓硫酸㊁无水碳酸钠㊁亚硫酸钠㊁氢氧化钠㊁二(2-乙基己基)磷酸酯(P204)㊁磷酸三丁脂(TBP)㊁磺化煤油(AR)㊁氯酸钾(KClO3)㊁氨水(NH3㊃H2O)㊁三辛烷胺基铵(N235),以上均为分析纯㊂1.2㊀实验方法1)钒㊁钨和钛元素的分离:首先对废弃SCR脱硝催化剂进行预处理,利用高压水进行冲洗,除去灰尘及其他杂质,置于行星式球磨机球磨8h,过200目筛制得回收料;然后通过酸浸还原法分离出V元素;最后将滤渣通过钠化焙烧法分离出W元素㊂2)TiO2的回收:将经过钠化焙烧法的滤渣于120ħ下干燥6h,再用0.1mol/L H2SO4调节pH至5以下,恒温25ħ下水浴振荡5h,再进行水洗㊁干燥,然后在马弗炉中550ħ煅烧3h,最终得到TiO2产品㊂3)V2O5的回收:调节钒浸出液pH为1.7后,进行4级逆流萃取V元素,其中萃取剂为P204,并添加适量调节剂TBP和磺化煤油㊂以H2SO4溶液作为反萃取剂,将经过错流萃取后负载4价钒的有机相在常温下进行3级逆流反萃取,在经反萃取后水相中加入KClO3溶液,煮沸至溶液变为黄色,再用氨水沉淀出多钒酸铵,再进行过滤㊁水洗,然后在马弗炉中以500ħ下煅烧2h,制得V2O5㊂4)WO3的回收:调节钨浸出液pH为2.5后,进行四级逆流萃取W元素,其中萃取剂为N235,并添加适量调节剂TBP和磺化煤油㊂以NH3㊃H2O溶液作为反萃取剂,将经过萃取后负载有机相在常温下进行三级逆流反萃取,再进行蒸发结晶㊁煅烧,最终制得WO3㊂461第11期滕玉婷,等:干湿法结合工艺回收废弃SCR 脱硝催化剂中的钛㊁钒和钨废弃脱硝SCR 催化剂中Ti㊁V㊁W 回收工艺如图1所示㊂图1㊀废弃脱硝SCR 催化剂中Ti㊁V㊁W 回收工艺流程Figure 1㊀Process flow for recovery of titanium,vanadium andtungsten from waste denitrification SCR catalyst2㊀结果与讨论2.1㊀V 、W 元素的分离2.1.1㊀反应温度㊁液固比对V 浸出率的影响为从废弃SCR 脱硝催化剂中选择性回收V 元素,通过酸浸还原法浸出V,其原理为将废弃SCR 脱硝催化剂中难溶于水的活性成分V 2O 5还原为低价钒盐(VOSO 4),因低价钒盐(VOSO 4)易溶于酸而难溶于碱,故可利用酸性还原环境浸出V 元素[17,18]㊂V 2O 5+2H 2SO 4+Na 2SO 3ң2VOSO 4+Na 2SO 4+2H 2O(1)㊀㊀将废弃SCR 脱硝催化剂进行预处理后,与Na 2SO 3按质量比为10ʒ1充分混合,分别以液固比以10ʒ1㊁20ʒ1㊁30ʒ1㊁40ʒ1㊁50ʒ1加入质量分数为8%硫酸,放入反应釜中,并分别在100,120,140,160,180ħ下反应10h㊂液固比㊁反应温度对钒浸出率的影响如图2所示㊂ʏ 100ħ; Ә 120ħ; һ 140ħ;▼ 160ħ; Ң 180ħ㊂图2㊀反应温度和液固比对钒浸出率的影响Figure 2㊀Effect of reaction temperature and liquid /solid ratio onrecovery of vanadium由图2可知:反应温度由100ħ增至140ħ过程中,钒浸出率增加较快,反应温度超过140ħ后,钒浸出率变化趋于缓慢㊂由分子热运动可知:其他条件保持不变,随着温度的升高,分子及离子的运动速度相应提高,同时使溶液黏度降低,加快VOSO 4溶解过程,但温度持续升高,溶液中将出现结块现象[16],同时能耗越大,综合考虑最佳反应温度选为140ħ㊂另外,随着液固比由10ʒ1增至30ʒ1过程中,钒浸出率随着液固比增加而增加,在液固比超过30ʒ1后,钒浸出率呈下降趋势㊂液固比在一定范围内增加可提高钒浸出率,因液固比太低,则形成的溶液黏度大,不利于低钒盐VOSO 4的溶解过程,并可能增加矿浆团聚情况㊂但液固比过高时,钒浸出率反而下降,可能由于过量酸溶液与反应釜底层固相反应不均匀,导致V 2O 5向VOSO 4转化不彻底,并且液固比过高则浸出液中钒浓度降低,不利于后续处理,因此最佳液固比为30ʒ1㊂在最佳反应温度和液固比条件下,钒浸出率为97.6%㊂2.1.2㊀煅烧温度㊁Na 2CO 3配比对W 浸出率的影响为选择性回收W 元素,在经过酸浸还原法V 元素后通过钠化焙烧法浸出W㊂原理为将废弃SCR 脱硝催化剂中难溶于水的活性成分WO 3在高温碱性环境下煅烧成易溶于水的Na 2WO 4㊂WO 3+Na 2CO 3ңNa 2WO 4+CO 2ʏ(2)TiO 2+Na 2CO 3ңNa 2TiO 3+CO 2ʏ(3)㊀㊀浸出V 元素后,将滤渣与Na 2CO 3按质量比1ʒ0.5㊁1ʒ1㊁1ʒ1.5㊁1ʒ2㊁1ʒ2.5充分混合,混合时加入少量的水使固体搅拌成泥状,以加强固体颗粒间的接触[19]㊂再将混合物分别在650,700,750,800,850ħ下煅烧8h,煅烧温度㊁Na 2CO 3配比对W 浸出率的影响如图3所示㊂由图3可知:煅烧温度由650ħ增至800ħ时,W 浸出率随着温度升高而增加,煅烧温度超过800ħ后,W 浸出率呈下降趋势,在煅烧温度为800ħ条件下,钒浸出率达到最大为93.2%,该结果与刘子林等[20]的研究一致㊂但通常纯锐钛型TiO 2转化为金红石型TiO 2的温度为610~915ħ[21]㊂虽煅烧温度为800ħ时,W 浸出率达到最高,但不利于后续高品质TiO 2的回收,且温度为750ħ时,钒浸出率也可达到91.6%,故最佳煅烧温度设为750ħ㊂另外,反应物与Na 2CO 3质量比在1ʒ0.5~1ʒ1.5时,Na 2CO 3含量增加促进W 元素的浸出效果明561环㊀境㊀工㊀程第38卷ʏ 650ħ; Ә 700ħ; һ 750ħ;▼ 800ħ; Ң 850ħ㊂图3㊀煅烧温度和Na2CO3配比对W浸出率的影响Figure3㊀Effect of calcination temperature and Na2CO3contenton recovery of tungsten显,在质量比>1ʒ1.5时,W浸出率逐渐趋于稳定㊂陈晨[19]认为Na2CO3含量过高则焙烧后容易形成玻璃相,抑制了W的浸出,综合考虑材料成本问题,最佳反应物与Na2CO3配比选为1ʒ1.5㊂在最佳煅烧温度㊁Na2CO3配比条件下,W浸出率为93.6%㊂2.2㊀TiO2的回收图4为不同焙烧温度下回收产物TiO2的XRD 谱图㊂可知:随着钠化焙烧温度的升高,锐钛矿TiO2衍射峰逐渐减弱(JCPDS No.21-1272)㊂当焙烧温度低于650ħ时,TiO2产物主要呈锐钛矿相且结晶度较好,当焙烧温度升高至700,750ħ时,锐钛矿的衍射峰强度呈减弱趋势,转化为金红石衍射峰,且温度越高,金红石的峰强越大㊂当焙烧温度超过750ħ时,锐钛矿的衍射峰逐渐消失,出现了钛酸盐的衍射峰,并随着温度升高,锐钛矿衍射峰消失现象越明显㊂图4㊀不同焙烧温度下回收产物TiO2的XRD谱图Figure4㊀XRD spectra of TiO2recovered at differentcalcination temperatures利用XRF对不同焙烧温度下回收产物成分进行分析,结果如表1所示㊂可知:随着焙烧温度的升高,回收产物中Ti元素含量逐渐增多,而Na㊁Si㊁W元素含量逐渐减少,V元素含量低至未被检测出,说明经酸浸还原后V元素基本全部被浸出㊂由以上方法回收TiO2,在不同焙烧温度下,TiO2回收率均可达到82%以上,于750ħ焙烧温度下TiO2的回收率达到最高97.17%,结合XRD表征结果,在焙烧温度为750ħ时,回收产物主要以TiO2晶型存在且晶粒较好,主要特征峰为锐钛矿,故最佳焙烧温度为750ħ,所得TiO2的纯度为95.35%,完全满足回收需求㊂表1㊀不同焙烧温度下回收产物的XRF分析结果Table1㊀XRF analysis results of the recovered products at different calcination temperatures 焙烧温度/ħ质量分数/%V Na Si Ti WTiO2回收率/%未煅烧0.850.260.8451.47 3.48/ 6000.000.950.5156.70 1.2082.29 6500.00 1.250.4856.800.9091.12 7000.00 2.210.2857.080.3295.47 7500.00 1.380.2057.300.1797.17 8000.00 1.890.2157.300.2295.29 8500.000.150.2358.310.00095.24 2.3㊀V2O5的回收在反应温度25ħ,水相pH=1.7,以P204-TBP-磺化煤油为萃取剂,硫酸为反萃取剂,进行4次逆流萃取和3级反萃取,重复3次试验,结果如表2所示㊂可知:V元素的萃取效果较好,萃取率在98%以上,反萃取出V2O5较完全,反萃取率在99%以上㊂表2㊀V元素萃取率及反萃取率试验结果Table2㊀Test results of vanadium element extractionrate and back extraction rate序号萃原液V元素浓度/(g/L)V元素萃取率/%V元素反萃取率/%1 2.4998.4799.292 2.5199.3499.373 2.4898.4199.23㊀㊀图5为经过有机萃取法从钒浸出液中回收V2O5的XRD谱图㊂可知:煅烧后的回收产物在衍射角分别为15.34ʎ㊁20.26ʎ㊁25.56ʎ㊁31.00ʎ等处出现V2O5的衍射峰,该衍射峰与X射线衍射标准(JCPDS No. 41-1426)的衍射峰基本一致,且衍射峰强度大,杂峰较少,说明V2O5结晶纯度较高㊂利用XRF对该回收产物成分进行分析,结果如表3所示㊂结合XRD表征结果,经过酸浸还原法浸出㊁萃取㊁沉钒等工序后,获得回收产物V2O5的纯度达到93.25%,经计算V2O5回收率为72.47%㊂661第11期滕玉婷,等:干湿法结合工艺回收废弃SCR脱硝催化剂中的钛㊁钒和钨图5㊀钒回收产物的XRD谱Figure5㊀XRD pattern of vanadium recovery products表3㊀钒回收产物的XRF分析结果Table3㊀XRF analysis results of vanadium recoveryproducts% V2O5Na2O K2O SO3SiO2Cl2O Al2O3ZnO 93.25 2.040.270.56 1.250.43 1.260.09 2.4㊀WO3的回收在反应温度25ħ,水相pH=2.5,以N235-TBP-磺化煤油为萃取剂,氨水为反萃取剂进行4次逆流萃取和3级逆流反萃取,并重复3次试验,结果如表4所示㊂可知:3次试验W元素的萃取及反萃取均较完全,W元素萃取率可达97%以上,反萃取率达到99%以上,能够满足深度提纯W元素的需要㊂表4㊀W元素萃取率及反萃取率试验结果Table4㊀Test results of tungsten extraction rate andback extraction rate萃原液W元素浓度/(g/L)W元素萃取率/%W元素反萃取率/%10.1697.2799.3610.2898.4199.4510.2998.5199.21㊀㊀图6为经过有机萃取法从钨浸出液中回收WO3的XRD谱图㊂可知:经500ħ温度下煅烧2h后的回收产物在衍射角分别为23.08ʎ㊁23.71ʎ㊁24.10ʎ㊁28.76ʎ等处出现WO3的衍射峰,该衍射峰与X射线衍射标准(JCPDS No.20-1324)的衍射峰高度一致㊂采用XRF对该回收产物成分进行分析,结果如表5所示㊂结合XRD表征结果,经过钠化焙烧法浸出㊁萃取㊁蒸发结晶等工序后,获得回收产物WO3的纯度达到78.26%,经计算WO3回收率为75.43%㊂表5㊀钨回收产物的XRF分析结果Table5㊀XRF analysis results of tungsten recovery products% WO3Na2O Al2O3SO3SiO2ZnO MgO Fe2O3 78.26 4.35 3.27 4.86 1.050.130.060.04图6㊀钨回收产物的XRD谱Figure6㊀XRD patterns of tungsten recovery products3㊀结㊀论通过高压水洗㊁粉碎㊁湿法酸浸还原㊁干法钠化焙烧处理方法实现了对废弃SCR脱硝催化剂中Ti㊁V㊁W元素的高效分离与浸出,再结合硫酸溶解法和有机萃取法资源化回收TiO2㊁V2O5和WO3,解决了有毒物质存在的环境污染风险,并避免造成有价金属资源的浪费,主要得出以下结论:1)利用酸浸还原法浸出废弃SCR脱硝催化剂中V元素的最佳工况条件:反应温度为140ħ,液固比为30ʒ1,在该反应条件下钒浸出率达到97.6%㊂采用钠化焙烧法浸出W元素的最佳工况条件为煅烧温度为750ħ,反应物与Na2CO3配比为1ʒ1.5,在该条件下W浸出率达到93.6%㊂2)利用硫酸溶解法回收得到的TiO2产物主要以锐钛矿晶型存在形式,在最佳焙烧温度750ħ下, TiO2的回收率达到97.17%,纯度为95.35%㊂3)利用有机萃取法回收得到的V2O5和WO3产物的结晶纯度均较高,V2O5和WO3产物回收率和纯度分别为72.47%㊁75.43%和93.25%㊁78.26%㊂参考文献[1]㊀曾瑞.浅谈SCR废催化剂的回收再利用[J].中国环保产业,2013(2):39-42.[2]㊀喻小伟,周瑜,刘帅,等.SCR脱硝催化剂失活原因分析及再生处理[J].热力发电,2014,43(2):109-113.[3]㊀LEE J B,EOM Y S,KIM J H,et al.Regeneration of waste SCRcatalyst by air lift loop reactor[J].Journal of Central SouthUniversity,2013,20(5):1314-1318.[4]㊀赵炜,于爱华,王虎,等.湿法工艺回收板式SCR废弃催化剂中的钛㊁钒㊁钼[J].化工进展,2015,34(7):2039-2042. [5]㊀火电厂脱硝催化剂报废高峰将至回收再利用势在必行[J].技术与市场,2018,25(10):4.[6]㊀余岳溪,廖永进,李娟,等.废弃SCR脱硝催化剂无害化处理的研究进展[J].环境工程,2016,34(6):136-139.(下转第174页)761。
- 1、下载文档前请自行甄别文档内容的完整性,平台不提供额外的编辑、内容补充、找答案等附加服务。
- 2、"仅部分预览"的文档,不可在线预览部分如存在完整性等问题,可反馈申请退款(可完整预览的文档不适用该条件!)。
- 3、如文档侵犯您的权益,请联系客服反馈,我们会尽快为您处理(人工客服工作时间:9:00-18:30)。
H g O、H g S O  ̄ I H g ( N O 3 ) 2 ・ 2 H 2 0 。颗粒态 的固相汞容易被 飞灰 吸附 ,经 过脱 硝装置时被截 留在催化剂表面和孑 L 洞 置的运行温度 为2 8 0  ̄ C ~ 4 1 0 ℃,附着 在飞灰上 的汞在此
2 废弃s c R催化剂表 面富集 的主要重 金属污染物
由于我 国的燃煤种类很多 ,各地 的火 电厂在使用不
炭资源总量为4 . 1 9 万亿 吨 ,占全 国煤炭资源总量 的8 2 . 8 % 同类型的燃煤后 ,所产生的废弃s c R 催化剂中含有的重金 ;截至1 9 9 6 年末 ,煤炭 的保有储量 为8 2 2 9 亿 吨 ,占全国 属污染 物情况差别也较大 ,主要含有铅 、铬 、铍 、铊 、 煤 炭保有储量 的8 2 . 1 %,而且煤种类 齐全 ,煤质普遍较 砷和汞等重金 属。据 中国环境科学研究 院对我 国部分燃
采条件复杂 、质量较次 的无烟煤或褐煤 ,不但开发成本 火 电厂的煤炭在燃烧过程 中,其 中大量的重金属氧
避 免二次污染 的发生或 不影 响 回收产 物的二次销售 ,将 大 ,而且煤炭 的综合利用价值也 不高。 我 国的煤炭 资 源丰 富 ,在现探 明 的储量 中 ,烟煤 化物 以气态形式挥发 出来 ,继而又凝结于燃煤飞灰 中, 占7 5 %、无烟煤 占1 2 %、褐煤 占1 3 %。其 中 ,原料煤 占 进 入后 续的烟气净化装置 ,富集在 S C R 催 化剂表面 ,加 2 7 %,动力煤 占7 3 %。动力 煤储量 主要分 布在华北和西 上脱 硝过程 的喷氨与烟气 中的s 0 所 形成 的( N H ) , s 0 黏 北 地 区,分别 占全 国总量 的4 6 %和3 8 %,炼焦煤主要集 性 吸附物的作用 ,更加剧 了重金属氧化物在催化剂上 的 中在华北 地区 ,无烟煤 主要集 中在 山西和贵州两省 。我 聚集 。 国煤炭资 源在地理分布上 的总格局是 西多东少 、北 富南 贫。而且 主要集 中分布在 目前 经济还 不发达 的山西 、内 蒙古 、陕 西 、新疆 、贵州 、宁夏 等6 省 ( 自治区 ),煤
关键词 : 废 弃S C R 催化剂;重金 属;污染治理 中图分类号 : X 7 0 5
1 概 述
国煤炭资源总量的5 . 3 %;截至 1 9 9 6 年末 ,煤炭的保有储 十分贫乏 。其 中,上海所辖范围内 ,至今未发 现有煤 炭
随着我 国火 电行业烟气脱硝治理工程初装 阶段 的结 量 只有 5 4 8 亿 吨 ,仅 占全 国煤炭保有储 量的5 . 5 %,资源 束 ,已安 装的S C R 催 化剂 已进入正 常的运 营管理状态 , 未来 1 ~ 2 年s c R 催化剂的再生及 回收利用企业也将投入正 资源赋存 ;截至 1 9 9 6 年末 ,开放程度较高的广东省 ,煤 式 的运 营。在催化剂再生及 回收利用 的生产过程 中 ,都 炭保有储量 只有6 1 乙 吨,天津市为4 亿吨 ,浙江省1 亿吨 , 将 面临由燃煤飞灰带入催化剂 中的各种重金属氧化物 的 海南省 不足 1 亿 吨。不仅资源 很少 ,而且 大多数还是 开 污染 治理 问题 。因此如何有效处理这些重金属污染物 , 会成为从事再生及 回收利用企业的重中之 重。
好 。而我国经 济最发达 、工业产值最 高 、对外 贸易最 活 煤 电厂产生 的废烟气脱硝催化剂 的危险特性分析结果表 跃 、需要 能源 最多 、耗 用煤量最大的京 、津 、冀 、辽 、 明 ,废 烟气脱 硝催化剂 的主要危险特性为浸 出毒性 ,其
鲁 、苏 、沪 、浙 、闽 、台 、粤 、琼 、港 、桂等 1 4 个 东南 中铍 、铜 、砷 的浸出浓度普遍 高于新脱硝催化剂 的浸 出
沿海省 ( 市 、区 ) 煤炭 资源量只有0 . 2 7 万亿 吨 ,仅 占全 浓度 ;部分废 烟气脱 硝催化剂 中铍 、砷 、汞 的浸 出浓度
I
中 国环保 产 业
2 0 1 5 年 第8 期
嚣 释 瀚 瀚辅 黼缴l 嚣 张 甏鼗 嘲醚露 i 霸 酶
j 交 流 与探 讨
超过 《 危险废 物鉴别标准 浸 出毒性鉴别 》 ( G B 5 0 8 5 . 3 — 究 应 以烟气 中汞 的形态 转化规律 为重点 。 燃烧烟气 中汞
2 0 0 7 )的有关要求 ,超标 的主要原 因是 由于脱硝催化剂 在烟气脱硝过程 中附着 了烟气 中的各种有害重金属 。因 的形态 主要有气态元 素态汞 ( H g O ) 、 气态二价汞 ( H g ) 和颗 粒态汞 ( Hg P ) 三种 形态存在 。 不
攀 枝花 6 1 7 0 0 0 )
鬻
摘
要: 分析 了烟气脱 ̄ g S C R 废催化剂在回收利用生产 中,各种 重金属 污染物 的处理工艺。
文献标志码 : A 文章编号 : 1 0 0 6 - 5 3 7 7( 2 0 1 5 )0 8 - 0 0 3 8 - 0 6
此 ,本文选取具有代表性 的重金属进行分析 ,其他未涉 中的物理 和化 学性质有很 大差异 。 在锅 炉燃烧过 程 中 , g O 的形式进入 烟气 中,部分 H g O 及的重金属或有毒金属氧化物在本文 的处理工艺下均能 煤 中的汞几乎全 部以H g C 1 , 为主 ,另外还有 附带去除 ,不会形成 “ 意料之外 ”的二次污染和影 响回 在烟气冷却过程中被 氧化 ,其 中以H 收产品质量的情况 。
煤 炭是一种复杂的天然矿物 ,各种煤 中砷 的含量变 内 ,其余则 随飞灰进 入后续的除尘和脱硫装置 ;脱硝装 化很大 ,一般为每公斤3 ~ 4 5 m g 。煤 中的砷多数 以硫化砷