浅析“零缺陷抽样检验方案”_如风的小世界
零缺陷(C=0)抽样方案

零缺陷概念的产生:被誉为“全球质量管理大师”、“零缺陷之父”和“伟大的管理思想家”的菲利浦·克劳士比(Philip B. Crosby)在20世纪60年代初提出“零缺陷”思想,并在美国推行零缺陷运动。
后来,零缺陷的思想传至日本,在日本制造业中得到了全面推广,使日本制造业的产品质量得到迅速提高,并且领先于世界水平,继而进一步扩大到工商业所有领域。
零缺陷理论核心是:“第一次就把事情做对”。
所谓"零缺陷"抽样方案,简单的说,就是不管你的批量和样本大小如何,其抽样检验的接收数Ac=0,即"0收1退"。
举例:某客户在其《供应商质量手册》中规定成品验收采用 C=0 抽样方案。
所谓 C=0 抽样方案通常又被大家称为零缺陷抽样方案,即只有抽样产品全部经检验全部合格,整批产品才能够被接收;而只要在验收过程中发现有一个不良品,整批产品将被判为不合格。
客户的这一要求在公司内部引起了一些同事的担心,认为这样的要求是不是过于严格了?公司根本做不到,甚至有同事认为客户这样的要求是“霸王”条款。
事实上,C=0 抽样方案目前在国内已经被广泛使用。
它和我们中国应用较多的GB/T2828.1-2012抽样方案一样,就方案本身来讲不存在严格不严格的概念。
在应用GB/T2828.1-2012时,一个抽样计划严格与否取决于我们对于 AQL 的选择。
AQL 值小,抽样计划就严格;AQL 值大,抽样计划就宽松。
同样的,C=0 抽样方案也规定了一系列与GB/T2828.1-2012 相同的 AQL值,选择哪个AQL 值完全在于我们自己的选择以及与客户的协商来决定。
所以有关“C=0 抽样方案过于严格”的论断完全不成立,出现这种认识仅仅是因为大家不了解C=0 抽样方案。
需要说明的是,该客户的《供应商质量手册》是根据IATF16949:2016 建立的,而IATF16949 :2016标准条款8.6.6中明确要求接收水平必须是零缺陷。
零缺陷活动实施方案

零缺陷活动实施方案一、背景介绍。
随着市场竞争的日益激烈,产品质量已成为企业竞争的关键因素之一。
为了提高产品质量,降低生产成本,我公司决定开展零缺陷活动,以实现产品质量的全面提升。
二、目标设定。
1. 提高产品质量,降低次品率;2. 提高员工工作积极性和责任感;3. 降低生产成本,提高企业竞争力。
三、活动内容。
1. 制定零缺陷活动实施方案,明确活动的具体内容、时间节点和责任人;2. 设立零缺陷活动小组,明确小组成员及各自职责;3. 开展质量管理培训,提高员工的质量意识和技能水平;4. 建立零缺陷检查机制,对生产过程中的每一个环节进行严格把控;5. 定期召开零缺陷活动总结会议,及时发现问题,改进工艺。
四、实施步骤。
1. 制定零缺陷活动实施方案。
明确零缺陷活动的时间安排、目标要求、责任人及具体工作内容,确保活动的顺利实施。
2. 设立零缺陷活动小组。
成立零缺陷活动小组,明确小组成员的职责分工,确保各项工作有序进行。
3. 开展质量管理培训。
组织员工参加质量管理培训,提高员工的质量意识和技能水平,使其能够更好地参与到零缺陷活动中来。
4. 建立零缺陷检查机制。
建立零缺陷检查机制,对生产过程中的每一个环节进行严格把控,及时发现并解决存在的质量问题。
5. 定期召开总结会议。
定期召开零缺陷活动总结会议,分析问题产生的原因,制定改进措施,确保活动的持续推进。
五、预期效果。
1. 产品质量得到提升,次品率明显降低;2. 员工工作积极性和责任感得到提高;3. 生产成本得到有效控制,企业竞争力得到提升。
六、总结。
零缺陷活动的实施对于提升产品质量、降低生产成本具有重要意义。
通过全员参与,严格把控,不断改进,我们相信一定能够取得显著的成效,为企业的可持续发展打下坚实的基础。
C=0-抽样方案介绍

C=0-抽样方案介绍1965年,零缺陷抽样检验方案(c=0)首次发表在国际刊物上,虽然零缺陷抽样检验方案目前还是不是国际和国家标准。
但由于“零缺陷”的品质理念已经深入人心,在加上ISO/TS16949:2002中有明确的条文要求。
所以欧美很多的企业,特别是汽车供应链相关企业普遍采用的都是零缺陷抽样检验方案。
零缺陷抽样检验方案简单的说,就是不管你的批量和样本大小如何,其抽样检验的接收数Ac=0,即“0收1退”。
在抽样检验过程中,一旦发现一个缺陷或不合格,就要实施100%的全检或退货处置。
零缺陷抽样检验方案的优点就是不存在加严、放宽与正常检验之间的转移规定。
在ISO/TS16949:2002里面的7.1.2条款里面有明确规定“7.1.2接收准则必须由组织定义,要求时,必须由顾客批准。
对于计数型数据抽样,接收水平必须是零缺陷”。
标准条文明确规定的,也就是我们要恪守的。
其实我们也一直在实用C=O的抽样检验方案。
但对其认识上可能存在一定的误区。
导致其真正的效率发挥的不够充分。
所以希望通过本文,能起抛砖引玉作用,为公司后续检验和试验活动更加顺畅的开展起到积极作用。
首先,零缺陷抽样检验方案的准则就是我们通常说的C=0,0收1退。
但其要和GB/T2828.1-2003按接收质量限(AQL)检索逐批检验抽样计划结合使用,要使用GB/T2828.1来确定其“零缺陷抽样检验方案”的样本大小。
按我们以前的经验,采用GB/T2828.1的时候,首先是确定批量大小、确定检验水平、那么它的样本大小就确定,再定义我们的接收质量限(AQL)就可以得出我们的接收准则,而现在采用零缺陷抽样检验方案的接收准则是已知的,意味着AQL值在零缺陷抽样检验方案中就失去了作用。
这就是我们认识上的一个明显误区。
试想,如果采用零缺陷抽样检验方案与AQL值无关的话,那么假设采用GB/T2828.1里面的正常检验一次抽样方案II级检验水平的话,意味着样本量是统一的。
什么是“零缺陷”抽样?与正常抽样有何不同?

什么是“零缺陷”抽样?与正常抽样有何不同?所谓“零缺陷”抽样方案,简单的说,就是不管你的批量和样本大小如何,其抽样检验的接收数Ac=0,即“0收1退”。
很多人会有疑问,这样会不会太理想、太严格了,供应商根本不可能做到?本文将通过对正常抽样和“零缺陷”抽样的介绍和比较为你详解“零缺陷”抽样的理念与做法。
抽样检验概述抽样检验是指从交验的一批产品中,随机抽取若干单位产品组成样本进行检验,通过对样本的检验结果对整批产品做出质量判定的过程。
抽样检验又分为统计抽检检验和非统计抽样检验。
非统计抽样(已淘汰):按照固定的百分比例来抽样。
存在两个方面的问题:大批宽、小批严;总体数量多的时候,抽样数很大,不具经济性。
统计抽样:是美国贝尔实验室的道奇和罗米格于1929年创立的,它和1924年休哈特提出的统计过程控制(SPC)一起被视为质量管理从质量检验阶段进入统计质量控制阶段的两个标志性成果。
其标准在美国是MIL-STD-105E(已被MIL-STD-1916取代),国标是GB2828。
第一部分:正常抽样正常抽样的标准1,检验水平的选择原则1)没有特殊规定时,首先采取一般检验水平II2)比较检查费用,若每个样品的检查费用为a,处理一个判批不合格样品的费用为b,检查水平应遵循:a) a>b,选择检验水平Ib) a<b,选择检验水平III3)另外4 个特殊检验水平S-1、S-2、S-3 和S-4,可用于样本量必须相对地小而且能容许较大抽样风险的情形,例如检验费用极高或者破坏性检验的情形。
4)辨别能力:Ⅰ<Ⅱ<Ⅲ;S-1<S-2<S-3<S42,确定抽样方案根据此前已确定的检验水平与AQL水准制定抽样方案。
在了解如何确定AQL水准之前,需要知道抽样风险的概念。
采用抽样检验时,生产方和使用方都要冒一定的风险。
因为抽样检验是按照一定的抽样方案从批中抽取样本进行检验,根据检验结果及接收准则来判断该批是否接收。
由于样本的随机性,同时它仅是批的一部分,通常还是很少的一部分,所以有可能做出错的判断。
浅谈“零缺陷”(C=0)抽样方案
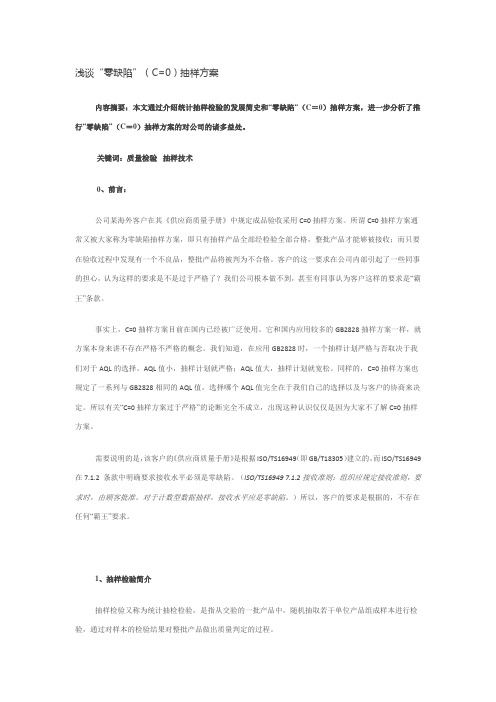
浅谈“零缺陷”(C=0)抽样方案内容摘要:本文通过介绍统计抽样检验的发展简史和“零缺陷”(C=0)抽样方案,进一步分析了推行“零缺陷”(C=0)抽样方案的对公司的诸多益处。
关键词:质量检验抽样技术0、前言:公司某海外客户在其《供应商质量手册》中规定成品验收采用C=0抽样方案。
所谓C=0抽样方案通常又被大家称为零缺陷抽样方案,即只有抽样产品全部经检验全部合格,整批产品才能够被接收;而只要在验收过程中发现有一个不良品,整批产品将被判为不合格。
客户的这一要求在公司内部引起了一些同事的担心,认为这样的要求是不是过于严格了?我们公司根本做不到,甚至有同事认为客户这样的要求是“霸王”条款。
事实上,C=0抽样方案目前在国内已经被广泛使用。
它和国内应用较多的GB2828抽样方案一样,就方案本身来讲不存在严格不严格的概念。
我们知道,在应用GB2828时,一个抽样计划严格与否取决于我们对于AQL的选择。
AQL值小,抽样计划就严格;AQL值大,抽样计划就宽松。
同样的,C=0抽样方案也规定了一系列与GB2828相同的AQL值,选择哪个AQL值完全在于我们自己的选择以及与客户的协商来决定。
所以有关“C=0抽样方案过于严格”的论断完全不成立,出现这种认识仅仅是因为大家不了解C=0抽样方案。
需要说明的是,该客户的《供应商质量手册》是根据ISO/TS16949(即GB/T18305)建立的,而ISO/TS16949在7.1.2条款中明确要求接收水平必须是零缺陷。
(ISO/TS16949 7.1.2接收准则:组织应规定接收准则,要求时,由顾客批准。
对于计数型数据抽样,接收水平应是零缺陷。
)所以,客户的要求是根据的,不存在任何“霸王”要求。
1、抽样检验简介抽样检验又称为统计抽检检验,是指从交验的一批产品中,随机抽取若干单位产品组成样本进行检验,通过对样本的检验结果对整批产品做出质量判定的过程。
我们知道,检验是不产生价值的工作,因此如何更经济、快捷的进行检验就直接关系到生产的成本和效率。
C= 抽样方案介绍

1965年,零缺陷抽样检验方案(c=0)首次发表在国际刊物上,虽然零缺陷抽样检验方案目前还是不是国际和国家标准。
但由于“零缺陷”的品质理念已经深入人心,在加上ISO/TS16949:2002中有明确的条文要求。
所以欧美很多的企业,特别是汽车供应链相关企业普遍采用的都是零缺陷抽样检验方案。
零缺陷抽样检验方案简单的说,就是不管你的批量和样本大小如何,其抽样检验的接收数Ac=0,即“0收1退”。
在抽样检验过程中,一旦发现一个缺陷或不合格,就要实施100%的全检或退货处置。
零缺陷抽样检验方案的优点就是不存在加严、放宽与正常检验之间的转移规定。
在ISO/TS16949:2002里面的7.1.2 条款里面有明确规定“7.1.2 接收准则必须由组织定义,要求时,必须由顾客批准。
对于计数型数据抽样,接收水平必须是零缺陷”。
标准条文明确规定的,也就是我们要恪守的。
其实我们也一直在实用C=O的抽样检验方案。
但对其认识上可能存在一定的误区。
导致其真正的效率发挥的不够充分。
所以希望通过本文,能起抛砖引玉作用,为公司后续检验和试验活动更加顺畅的开展起到积极作用。
首先,零缺陷抽样检验方案的准则就是我们通常说的C=0,0收1退。
但其要和GB/T2828.1-2003按接收质量限(AQL)检索逐批检验抽样计划结合使用,要使用GB/T 2828.1来确定其“零缺陷抽样检验方案”的样本大小。
按我们以前的经验,采用GB/T 2828.1的时候,首先是确定批量大小、确定检验水平、那么它的样本大小就确定,再定义我们的接收质量限(AQL)就可以得出我们的接收准则,而现在采用零缺陷抽样检验方案的接收准则是已知的,意味着AQL值在零缺陷抽样检验方案中就失去了作用。
这就是我们认识上的一个明显误区。
试想,如果采用零缺陷抽样检验方案与AQL值无关的话,那么假设采用GB/T2828.1里面的正常检验一次抽样方案II级检验水平的话,意味着样本量是统一的。
零缺陷管理实施方案
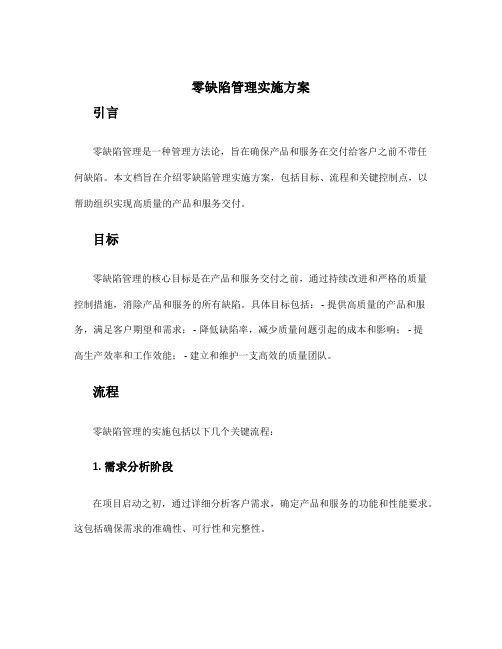
零缺陷管理实施方案引言零缺陷管理是一种管理方法论,旨在确保产品和服务在交付给客户之前不带任何缺陷。
本文档旨在介绍零缺陷管理实施方案,包括目标、流程和关键控制点,以帮助组织实现高质量的产品和服务交付。
目标零缺陷管理的核心目标是在产品和服务交付之前,通过持续改进和严格的质量控制措施,消除产品和服务的所有缺陷。
具体目标包括: - 提供高质量的产品和服务,满足客户期望和需求; - 降低缺陷率,减少质量问题引起的成本和影响; - 提高生产效率和工作效能; - 建立和维护一支高效的质量团队。
流程零缺陷管理的实施包括以下几个关键流程:1. 需求分析阶段在项目启动之初,通过详细分析客户需求,确定产品和服务的功能和性能要求。
这包括确保需求的准确性、可行性和完整性。
2. 设计和开发阶段在设计和开发阶段,重点关注以下方面: - 详细设计:设计符合需求规范的产品和服务; - 单元测试:在开发过程中,进行模块和组件的单元测试,确保每个单元的功能和性能满足要求; - 集成测试:将各个模块和组件进行集成,测试系统的功能和性能。
3. 验证和验证阶段在产品和服务开发完成后,进行验证和验证以确保其质量和可靠性: - 验证测试:确认产品和服务是否满足需求规范; - 验证规范:与客户一起确认需求分析阶段定义的规范; - 验证报告:生成验证报告以记录验证结果。
4. 生产和交付阶段在产品和服务交付之前,进行以下工作: - 生产准备:建立生产环境并进行必要的培训; - 系统测试:进行全面的系统测试,确保整个系统的功能和性能符合规范; - 交付:将产品和服务交付给客户,并记录交付证明。
5. 持续改进阶段零缺陷管理不仅仅是一个阶段性的过程,而是一个持续改进的过程。
持续改进阶段包括: - 定期评估:定期评估产品和服务的质量,并与客户和利益相关者沟通反馈; - 分析问题:对质量问题进行分析和根本原因分析,以推动问题解决; - 改进措施:制定改进计划,包括培训、流程优化等; - 实施改进:按计划实施改进措施,并进行监控和评估。
质量零缺陷活动方案

质量零缺陷活动方案一、活动主题。
“追求零缺陷,质量大过天”二、活动目的。
咱们搞这个活动啊,就是想让咱的产品或者服务没有一丁点儿毛病。
让客户拿到手就忍不住竖起大拇指,说“这玩意儿,真绝了,一点毛病挑不出来!”而且呢,这样还能给咱公司省钱,减少那些因为质量问题产生的返工啊、售后啊之类的烦心事。
三、活动时间。
[具体开始时间]-[具体结束时间],就像一场质量的马拉松比赛,这期间大家可得鼓足了劲儿。
四、参与人员。
全体员工,不管你是在前线冲锋陷阵的销售,还是在后方默默支持的后勤,都得参与进来。
因为质量这事儿,就像一根绳子上的蚂蚱,缺了谁都不行。
五、活动内容。
1. 质量意识培训。
首先呢,咱得让大家知道为啥质量零缺陷这么重要。
请公司里那些经验丰富的老师傅或者外面的专家来给大家上课。
讲讲那些因为质量问题闹出来的大笑话,还有那些因为质量过硬而大获成功的牛事儿。
比如说,曾经有个公司啊,就因为产品一个小零件老出问题,结果客户全跑光了,最后只能关门大吉;而另外一个公司呢,对质量要求超级严格,产品那叫一个完美,现在都成行业老大了。
通过这些故事,让大家心里有个底儿。
培训完了,咱还得来个小测试。
就像上学时候的考试一样,不过别担心,题目不会太难,就是考考大家对质量零缺陷的理解。
答对的呢,有小奖品,像小零食啊或者公司定制的小徽章之类的。
答错的也别灰心,咱们再补补课就好啦。
2. 质量问题大排查。
全体员工分成小组,就像侦探小分队一样,对咱们的工作流程、产品或者服务进行全面的排查。
从原材料的采购开始,到最后的成品交付或者服务完成,每个环节都不能放过。
大家要像挑刺儿一样,找出那些可能存在质量隐患的地方。
比如说,生产线上某个机器的螺丝是不是拧紧了,客服人员回答客户问题是不是够专业、够耐心。
每个小组把发现的问题都写下来,然后咱们汇总起来。
对于排查出来的问题,咱们再一起讨论怎么解决。
能当场解决的,绝不拖延;要是比较复杂的,那就制定一个详细的解决方案,规定好谁负责、什么时候完成。
零缺陷抽样检验计划

转入间接检查不充分时; 抽样检查与全检相比,受检单位产品数少,检查项可
多些,但是同一质量的产品批有可能判合格,也有可 能判不合格。而且,当不合格品率很小时,很难抽出 不合格品。
何时无需抽样检验?
生产稳定,对后续生产无影响,质量控制图无异常的有限批。 国家批准的免检产品,质量认证产品入厂检查时。 长期检查质量优良,使用信誉高的产品的接收检查和认可生
更换或修复。
合格批入库或转入下道工序。这时,要求
附上合格证或检查记录,按规定办法处理。
不合格批的处理
经检查不合格的批,除记录何处不合格外,作 出不合格批的标志,存放地点切勿与合格批混 淆,不合格批可据具体情況作如下处理,且要 事先做出规定:
退货或返工; 全检更换不合格品或修复不合格品; 检查部门或产品接收方对产品全检,挑出不合格品; 整批报废; 让步接收。
x!
其中u=np,e=2.71828
注意事项:
卜氏分布的应用是假定群体N相当大,而不合格品
的发现很少时(即批中的不合格品数量很少,或不合格
品率很低时),因为在此种情形下,其分配曲线将呈右
偏形态,故不能以正态分布或二项分布来计算。
卜氏分布例题
设有一检验批,其批量为100,000个,其不合格品
53单次抽样示意图nnac随机抽取n件检验出d件不合格品若dac则判定该批合格若dac则判定该批不合格54双次抽样示意图nn1n2ac1re1ac2re2在n件中随机抽n1件设检验出d1件不合格若d1re1判定不合格若d1ac1判定合格若ac1d1re1則再抽取n2件设检验出d2件不合格若d1d2ac2判定合格若d1d2re2判定不合格55多次抽样使用说明抽样次数样本大小累积n大小50505010050150502005025050300503501056抽样方案的选择项目多次对产品质量的影响几乎相同对供方心理上的影响最差中间最好总检验费用最多中间最少行政费训练人员记录最少中间最多检验负荷的变异性不变变动变动对每批产品质量估计准确性最好中间最差对制程平均数估计的速度最快较慢最慢检验人员及设备使用率最佳较差较差57检查严格度的意义计数调整型抽样检查规定抽样检查与抽样方案调整同时进行旨在保证批质量在aql附近或优于aql
零缺陷抽样方案

2
简介及说明
组织
IQC
STEP1 STEP2 STEP3
OQC
IPQC
3
各项检验的趋势(IQC)
供货商 OQC
组织 IQC
IQC目前的趋势倾向由供货商负责,进来时免 检方式,但前提是你能相信供货商的制造能力 以及供货商OQC的情形,这样可以避免供货商 和组织的重复检验以及人员的投资
4
各项检验的趋势(IPQC)
e 2.71828
期望值:E( X )
變異數:Var( X )
表示式:X ~ P.D()
18
泊松分布例题
设有一检验批,其批量为100,000个,其不良率已知为 3%,试问从其中随机抽取100个样品检验,其中含有0 个以及1个不良品的概率分别为多少?
N 100,000, n 100,則n / N 0.001 0.1
8
P5
(8
8! 5)!
8! 3!
6720
因为有8篇文可用但却仅能容纳5篇,第一篇时有8种选择,第二 篇时有7种选择,第三篇有6种选择,第四篇有5种选择,第五篇 有4种选择,共有8*7*6*5*4=6720种不同的可能安排,但 8*7*6*5*4恰为8!/3!。一般上,从n件可用事物中取出r件,即共 有n!/(n-r)!种不同的可能安排数,这即排列法则。
28
分层随机抽样
++++++++ ++++++++ *********** *********** ######## ######## $$$$$$$$$$$ $$$$$$$$$$$
+++ *** ### $$$
零缺陷抽样方案

P0
=
30 0!
e -3
=
0 .04979
d =1
P1
=
31 1!
e -3
=
0 .14937
一般应用上的检验,使 用卜氏分布求近似值时, 除了与二项分布相同 n/N要小于0.1外,样本 数n要大于16以上,以 及不良率要小于10%, 方可求得正确结果.
计数分布汇总:
N<10n 不归还法
计数值分配
N 10n
品数为0、1个的概率分別为多少
d=0
P0
30 970 ( )( ) = 01010000=
()
03!30!0!1•1 00 0 9!!0 0 8 7!7 0!0=8970!1 0 !0 9070!0 !0 =0.04036
100
10!0 90!0
d =1
30 970
( )(
)
30 !
970 !
P1 =
组合法则
从n个可用事物中取出r件组合数为如下式子:(式 中n=可用事物总数,r=取出事物数.利用上述组合法则, 须有n个事物,且由n个中取出r个做组合,另应考虑相同 事物重新安排是相同的.)
C
r n
=
(n
n! - r)!r!
组合例题
纽约发行彩券,设头奖一名,由1至54中选出6
种不同组合数,恰好与头奖号码完全一样则贏得头
例如一批产品有1000件,分四层放置,每层有 250件,现准备选择样本20件,可从每层的250件 中随机抽取5件,合计为20件样本.
区域抽样
区域抽样时,要求每个区域內部的差异大些,区域之间 的差异要小些,这样的效果才会比较好.
例如有一批螺丝共100盒,每盒中有100个螺丝,准备抽 取500个样本,可从100盒中随机抽取5盒,检查5盒中的 全部螺丝.
- 1、下载文档前请自行甄别文档内容的完整性,平台不提供额外的编辑、内容补充、找答案等附加服务。
- 2、"仅部分预览"的文档,不可在线预览部分如存在完整性等问题,可反馈申请退款(可完整预览的文档不适用该条件!)。
- 3、如文档侵犯您的权益,请联系客服反馈,我们会尽快为您处理(人工客服工作时间:9:00-18:30)。
浅析“零缺陷抽样检验方案”_如风的小世界百度空间 | 百度首页 | 登录如风的小世界宝宝的个人空间主页博客相册|个人档案 |好友查看文章
浅析“零缺陷抽样检验方案”2008年11月11日星期二 13:09浅析“零缺陷抽样检验方案”
1965年,零缺陷抽样检验方案(c=0)首次发表在国际刊物上,虽然零缺陷抽样检验方案目前还是不是国际和国家标准。
但由于“零缺陷”的品质理念已经深入人心,在加上ISO/TS16949:2002中有明确的条文要求。
所以欧美很多的企业,特别是汽车供应链相关企业普遍采用的都是零缺陷抽样检验方案。
零缺陷抽样检验方案简单的说,就是不管你的批量和样本大小如何,其抽样检验的接收数Ac=0,即“0收1退”。
在抽样检验过程中,一旦发现一个缺陷或不合格,就要实施100%的全检或退货处置。
零缺陷抽样检验方案的优点就是不存在加严、放宽与正常检验之间的转移规定。
在ISO/TS16949:2002里面的7.1.2 条款里面有明确规定“7.1.2 接收准则必须由组织定义,要求时,必须由顾客批准。
对于计数型数据抽样,接收水平必须是零缺陷”。
标准条文明确规定的,也就是我们要恪守的。
其实我们也一直在实用C=O的抽样检验方案。
但对其认识上可能存在一定的误区。
导致其真正的效率发挥的不够充分。
所以希望通过本文,能起抛砖引玉作用,为公司后续检验和试验活动更加顺畅的开展起到积极作用。
首先,零缺陷抽样检验方案的准则就是我们通常说的C=0,0收1退。
但其要和GB/T2828.1-2003按接收质量限(AQL)检索逐批检验抽样计划结合使用,要使用GB/T
2828.1来确定其“零缺陷抽样检验方案”的样本大小。
按我们以前的经验,采用GB/T 2828.1的时候,首先是确定批量大小、确定检验水平、那么它的样本大小就确定,再定义我们的接收质量限(AQL)就可以得出我们的接收准则,而现在采用零缺陷抽样检验方案的接收准则是已知的,意味着AQL值在零缺陷抽样检验方案中就失去了作用。
这就是我们认识上的一个明显误区。
试想,如果采用零缺陷抽样检验方案与AQL值无关的话,那么假设采用GB/T2828.1里面的正常检验一次抽样方案II级检验水平的话,意味着样本量是统一的。
我们可以举个实际的例子,如果某批量为1000pcs
产品。
按GB/T2828.1的正常检验一次抽样方案II级检验水平抽取样本大小n=80pcs,也就是说不管这个产品的那个质量特性,都需要对其80个样本进行逐一的检验,而且还是C=0的接收准则。
那么这种做法无论从理论上还是实践中都是不经济的。
而我们公司目前就恰恰走入的就是这个误区。
针对上述的问题,国内外比较优秀的公司大都采用针对同一产品的不同的质量特性分别指定不同的AQL值,针对A类质量特性(关键项目)选择AQL一般为0.1,B类质量特性(重点项目)选择AQL一般为1.5,C类质量特性(一般项目)选择AQL一般为6.5,这样在进行了质量特性划分以后,针对不同的质量特性可以抽取不同的样本数。
我们还是继续上面的例子,如果上面提到的1000pcs
产品有2个质量特性项目需要检测,一个是A类的,一个是C类的。
按照我们以往的做法,有下面两种情况:
1)按GB/T2828.1的正常检验一次抽样方案II级检验水平的抽样方案为第一个质量特性(A类),n=125,(Ac,Re=0,1)
第二个质量特性(C类),n=80,(Ac,Re=10,11)。
2)按我们公司现有C=0抽样方案,并结合GB/T2828.1的相关要求。
第一个质量特性(A类),n=80,(Ac,Re=0,1)
第二个质量特性(C类),n=80,(Ac,Re=0,1)。
上面的第一中抽样方案对于一般的企业可能是适用的,但对于通过了ISO/TS16949的汽车零部件制造性企业肯定是不允许的。
同样我们公司也不能采用。
我们仔细分析下上面的第二种情形,是粗略的理解了零缺陷抽样检验方案中有关AQL所带来的作用。
我们试想对于一个C类的项目如果不考虑AQL值也简单抽取那么大的样本而按零缺陷接收的,无疑将增加生产方(供应商)的风险,浪费我们使用方的资源。
过多的抽取样本。
适用零缺陷抽样检验方案的其中一个好处就是节省检验和试验的成本。
那么我们就应该要考虑AQL值的作用。
我们的实际的抽样方案应该这样制订。
3)按零缺陷抽样检验方案(C=0),并结合GB/T2828.1的相关要求。
第一个质量特性(A类),n=125,(Ac,Re=0,1)
第二个质量特性(C类),n=11,(Ac,Re=0,1)。
这样以来,总体样本量在下降,当质量特性较多时,更加明显,可见采用零缺陷抽样检验方案不当不会增加我们日常的工作量,还会简化我们的工作程序和方法。
当然我们在学习抽样方案零缺陷的同时,我们也应该要力求工作效能的“零缺陷“,因为毕竟第一次就把事情作对,对每个人每个公司都显得尤为重要。
类别:质量管理 | 添加到搜藏 | 浏览(528) | 评论 (1) 上一篇:品质管理的几个苦恼感受下一篇:探讨如何加强与提高产品质量管理
最近读者:登录后,您就出现在这里。
lookathere
网友评论:1网友:czl2009年03月23日星期一 15:23 | 回复 LZ举的例子B类是0.15 C 类是0.65吧?
还有取数值的时候眼睛好象跳行了吧
发表评论:姓名:注册 | 登录 *姓名最长为50字节
网址或邮箱: (选填)
内容:插入表情▼闪光字
验证码:请点击后输入四位验证码,字母不区分大小写
看不清?
取消回复
©2009 Baidu。