C=0抽样方案
【干货】零缺陷(C=0)抽样方案
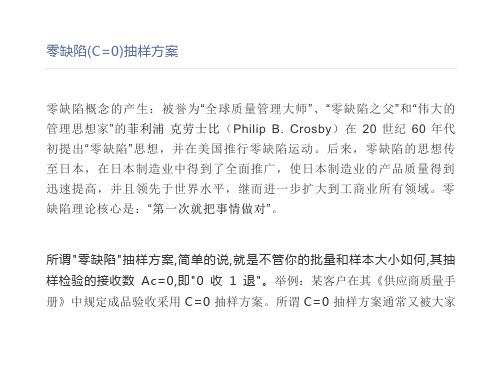
零缺陷(C=0)抽样方案零缺陷概念的产生:被誉为“全球质量管理大师”、“零缺陷之父”和“伟大的管理思想家”的菲利浦·克劳士比(Philip B. Crosby)在20世纪60年代初提出“零缺陷”思想,并在美国推行零缺陷运动。
后来,零缺陷的思想传至日本,在日本制造业中得到了全面推广,使日本制造业的产品质量得到迅速提高,并且领先于世界水平,继而进一步扩大到工商业所有领域。
零缺陷理论核心是:“第一次就把事情做对”。
所谓"零缺陷"抽样方案,简单的说,就是不管你的批量和样本大小如何,其抽样检验的接收数Ac=0,即"0收1退"。
举例:某客户在其《供应商质量手册》中规定成品验收采用C=0抽样方案。
所谓C=0抽样方案通常又被大家称为零缺陷抽样方案,即只有抽样产品全部经检验全部合格,整批产品才能够被接收;而只要在验收过程中发现有一个不良品,整批产品将被判为不合格。
客户的这一要求在公司内部引起了一些同事的担心,认为这样的要求是不是过于严格了?公司根本做不到,甚至有同事认为客户这样的要求是“霸王”条款。
事实上,C=0 抽样方案目前在国内已经被广泛使用。
它和我们中国应用较多的 GB/T2828.1-2012抽样方案一样,就方案本身来讲不存在严格不严格的概念。
在应用 GB/T2828.1-2012时,一个抽样计划严格与否取决于我们对于 AQL 的选择。
AQL 值小,抽样计划就严格;AQL 值大,抽样计划就宽松。
同样的,C=0 抽样方案也规定了一系列与GB/T2828.1-2012相同的AQL值,选择哪个AQL值完全在于我们自己的选择以及与客户的协商来决定。
所以有关“C=0抽样方案过于严格”的论断完全不成立,出现这种认识仅仅是因为大家不了解C=0 抽样方案。
需要说明的是,该客户的《供应商质量手册》是根据 IATF16949:2016建立的,而IATF16949:2016标准条款8.6.6中明确要求接收水平必须是零缺陷。
C=0抽样方案

1﹑目的
明确品管部各单位的抽样标准,并提供文件支持。
2﹑范围
适用于本公司所生产的汽车工业链上的相关产品。
适用于进料、制程、成品检验时,计数型数值允收水准的确定。
3﹑权责
3.1品管经理:确定各阶段的AQL值。
3.2品检人员:C=0 抽样标准的实施。
4﹑定义
4.1 C=0抽样计划:零缺陷抽样计划,即0收1退,Acc=0,Rej=1。
5﹑作业内容
5.1使用方法
5.1.1确定检验项目、判定标准。
5.1.1.1抽检数量:样品全检(性能除外)。
量产抽检。
5.1.1.2检验项目:尺寸、外观、性能、装配等。
根据客户要求及产品特性确定。
5.1.2确定允收水准AQL值。
外观:AQL:0.65 Ac=0 Re=1
尺寸:AQL:6.5 Ac=0 Re=1
性能:AQL:6.5 Ac=0 Re=1
5.1.3根据实际批量及规定的AQL值从“附件一”中查出应抽取的样本数量。
5.1.4从批量中随机抽取规定的样本数。
5.1.5检验
根据Acc=0 Rej=1判定。
5.2如遇特殊情况,品管部可根据客户要求更改允收品质水准AQL,只需书面通知相关部门,而
无需更改本规定及相关检验标准。
6﹑参考文件
无
7﹑使用表单
无
8﹑附件
8.1 C=0抽样计划表
附件一:
C=0抽样计划表
注:* 表示整批须百分之百检验。
C=0抽样方案

内容摘要:本文经由过程介绍统计抽样磨练的成长简史和“零缺点”(C=0)抽样筹划,进一步剖析了履行“零缺点”(C =0)抽样筹划的对公司的诸多益处.0.媒介:客户在其《供给商质量手册》中划定成品验收采取C=0抽样筹划.所谓C=0抽样筹划平日又被大家称为零缺点抽样筹划,即只有抽样产品全体经磨练全体及格,整批产品才干够被吸收;而只要在验收进程中发明有一个不良品,整批产品将被判为不及格.客户的这一请求在公司内部引起了一些同事的放心,以为如许的请求是不是过于严厉了?我们公司基本做不到,甚至有同事以为客户如许的请求是“霸王”条目.事实上,C=0抽样筹划今朝在国内已经被普遍运用.它和国内运用较多的GB2828抽样筹划一样,就筹划本身来讲不消失严厉不严厉的概念.我们知道,在运用GB2828时,一个抽样筹划严厉与否取决于我们对于AQL的选择.AQL值小,抽样筹划就严厉;AQL值大,抽样筹划就宽松.同样的,C=0抽样筹划也划定了一系列与GB2828雷同的AQL值,选择哪个AQL值完整在于我们本身的选择以及与客户的协商来决议.所以有关“C=0抽样筹划过于严厉”的论断完整不成立,消失这种熟悉仅仅是因为大家不懂得C=0抽样筹划.须要解释的是,该客户的《供给商质量手册》是依据ISO/TS16949(即GB/T18305)建立的,而ISO/TS16949在条目中明白请求吸收程度必须是零缺点.(吸收准则:组织应划定吸收准则,请求时,由顾客同意.对于计数型数据抽样,吸收程度应是零缺点.)所以,客户的请求是依据的,不消失任何“霸王”请求.1.抽样磨练简介抽样磨练又称为统计抽检磨练,是指从交验的一批产品中,随机抽取若干单位产品构成样本进行磨练,经由过程对样本的磨练成果对整批产品做出质量剖断的进程.我们知道,磨练是不产生价值的工作,是以若何更经济.快捷的进行磨练就直接关系到临盆的成本和效力.统计抽样磨练理论是美国贝尔试验室的道奇和罗米格于1929年创立的,它和1924年休哈特提出的统计进程掌握(掌握图)一路被视为质量治理从质量磨练阶段进入统计质量掌握阶段的两个标记性成果.统计抽样磨练理论的消失转变了以往那种依附大批量磨练来包管产品德量的工作方法.从1950年美军宣布MIL-STD-105抽样尺度起,统计抽样磨练在全世界慢慢推广开来.MIL-STD-105的进级.延长版本被国际尺度化组织以及很多国度的国度尺度采取.美军MIL-STD-105尺度共阅历A~E五个版本,该尺度今朝已经被美军废除.2.两种“零缺点”抽样筹划1965年,美国的一位大学传授尼古拉斯•斯托格力亚揭橥C=0抽样筹划,几经改版,今朝最新的版本为第四版.C=0抽样筹划是依据MIL-STD105 修正而成,吸收准则限制为“0收1退”,因而又被人们称为“零缺点”抽样筹划.固然到今朝为止,C=0抽样筹划还不是国际以及任何国度的国度尺度,但因为“零缺点”的质量理念已经深刻人心,在加上ISO/TS16949:2002中有明白的条则请求,在企业界已经得到了普遍的运用.1994年,美国三大汽车厂商(通用.福特.克来斯勒)宣布了QS9000质量体系尺度,QS9000中的条目就明白请求:吸收准则必须是零缺点.QS9000的这一请求,促进了C=0抽样筹划的被敏捷推广运用.在QS9000被国际尺度化组织采取为国际尺度ISO/TS16949之后,使得C=0抽样筹划的运用又进一步扩展.2005年,为了表扬尼古拉斯•斯托格力亚传授创制C=0抽样筹划的凸起进献,美国质量学会把当年的谢宁奖章颁给已经退休的尼古拉斯•斯托格力亚传授.美国质量学会在表扬词中说:他最巨大的进献是开辟了一套实用.便于运用.经济的零缺点的数字抽样筹划.他的办法在军事和商用上,节俭了数以百万计的美元.因为他的办法被证实实用.简略单纯并且经济,因而被普遍接收.1996年,美军推出新版的抽样尺度MIL-STD-1916.和C=0抽样筹划一样,MIL-STD-1916也限制它的吸收准则为“0收1退”,所以MIL-STD-1916也可以称为零缺点抽样筹划.MIL-STD-1916不再像MIL-STD-105那样强调抽样的技巧,而是转为请求供给商建立预防性的质量体系和有效的进程质量掌握体系.MIL-STD-1916强调以事先的预防代替过后的磨练.因为ISO/TS16949只请求了“吸收程度应是零缺点”,并没有明白划定应采取C=0抽样筹划照样MIL-STD-1916.对于企业来说,运用哪一种“零缺点”抽样筹划可以联合企业自身以及客户的具体请求来决议.3.国内抽样尺度的运用情形1981年我国开端参照ISO2859(即MIL-STD-105D)制定中国的统计抽样尺度GB2828.GB2828经由1987年和2003年两次修订,今朝在国内运用最为普遍.固然MIL-STD-105在美国已经被废除,但是该尺度今朝在我国仍有很多企业在运用,甚至还有少数企业在运用早期的版本MIL-STD-105D.今朝,C=0抽样筹划已经在我国浩瀚的汽车行业企业和其它自愿采取ISO/TS16949尺度的企业中被普遍的运用.4.“零缺点”的概念“零缺点”(C=0)抽样筹划是依据MIL-STD-105修正而来,有关统计抽样的概念与GB2828出自同源,GB2828相干的术语界说在“零缺点”(C=0)抽样筹划都可以运用.为了凸起“零缺点”这一重要概念,“零缺点”(C=0)抽样筹划把GB2828中“不及格”.“不及格品”两个术语修正为“缺点”.“缺点品”.因为“零缺点”(C=0)抽样筹划的剖断准则限制为“0收1退”,只要消失一个缺点品,不管批量大小.样本若干,都可以判整批不及格.凸起“零缺点”不雅念,可以促进大家质量意识晋升.“零缺点”(C=0)抽样筹划的别的斟酌是:假如你的质量相当差,大于0的允收数并没有多大的帮忙;当你的抽样筹划允收数大于零,你在授权你的磨练人员接收一些可能没有效的产品;零缺点强迫对任何不及格采纳措施;假如你正在尽力迈向零缺点,那你怎能许可你的抽样筹划许可出缺点数呢?我们看到很多公司经常运用“零缺点”的概念来进行质量宣扬,但“零缺点”的精力要怎么去贯彻落实呢?假如我们一方面宣扬着“零缺点”,另一方面仍然在运用GB2828的抽样筹划来吸收不良品,那本身就是一个自相抵触的笑话.5.“零缺点”(C=0)抽样筹划的轻便性与GB2828比拟“零缺点”(C=0)抽样筹划不消失加严.放宽与正常磨练之间的转移划定,也没有二次及多次抽样筹划.“零缺点”(C=0)抽样筹划仅运用一张主抽样表,相对GB2828的几十张抽样表大大简化,即便利进修,也便于运用治理.同时,“零缺点”(C=0)抽样筹划不但实用于逐批磨练,也实用于孤立批次磨练.6.履行“零缺点”(C=0)抽样筹划的益处有助于形成严谨务实的工作风格固然三星电气品德治理部分在现行的成品磨练尺度中,把产品功效参数类磨练项目标抽样筹划划定为不及格品GB2828ⅡAQL=0.65%;而外不雅类磨练项目则划定为不及格品GB2828ⅡAQL=1.0% .但是否严厉按抽样筹划进行了抽检照样一个问题.磨练员们在被问题按何种尺度磨练产品时,经常会答复:按GB2828磨练.但是我们是按GB2828的哪一级磨练水准?各类质量特征分离拔取何种AQL值呢?大家答不上来.事实上,一批产品在抽检时应当抽取若干样本?以及若何剖断及格与否?往往都是主管人员凭感到.凭小我经验的指导.如许做的问题是:抽检工作缺乏合理性,抽检剖断缺乏公正性,对出厂产品的质量风险把控也不具有科学性.不管我们选用GB2828或是“零缺点”(C=0)抽样筹划,尺度一旦确立,就必定要包管按尺度进行磨练.必须转变那种靠人的主不雅经验剖断的不良习惯,促使工作严谨性.而因为“零缺点”(C=0)抽样筹划的易学易用性,更有助于帮忙我们形成严谨.务实的工作风格.选用“零缺点”(C=0)抽样筹划更经济在拔取雷同AQL值的情形下,“零缺点”(C=0)抽样筹划的抽检风险概率与GB2828相似,同时抽检量大大削减.与GB2828一样,运用“零缺点”(C=0)抽样筹划时同样须要为不合类此外质量特征划定不合的AQL(吸收质量限).“零缺点”(C=0)抽样筹划实用于:期望是临盆的产品完整达到规范请求.对一些非症结的特征愿望用比较少的磨练.比方三星电气公司的电能表产品,对于表计功效.机能等重要质量特征是客户重点存眷的,并且也必须知足“零缺点”;而对于外不雅等次要质量特征,客户平日其实不会像看待工艺品一样深究,就不须要保持大量的抽检,那样显著是不经济的.将帮忙我们建立“零缺点”的质量意识并晋升产品德量程度因为“零缺点”(C=0)抽样筹划的剖断准则限制为“0收1退”,只要消失一个不良品,就可以判整批不及格,就必须采纳全检返措施.在履行的初期无疑将会加大效力和成本的压力,从而促使全部公司真正建立“零缺点”的不雅念,不容忍一个不良品.当我们每小我都形成了不克不及够容忍不良品和不克不及够容忍工作错误之后,信任我们的产品德量程度也必定会响应的晋升.有助于晋升客户信念,并帮忙拓展海外市场.今朝,“零缺点”的质量不雅念已经风靡全球,假如期望打入欧美日等成熟的高端市场,我们必须运用顾客可以或许听懂的“零缺点”质量说话来跟顾客接轨.“零缺点”(C=0)抽样筹划契合公司的经营理念公司建议准确.高效.务实.简略的工作文化,而“零缺点”(C=0)抽样筹划正好相符这四个词的请求.总之,“零缺点”是今朝企业质量治理的潮流所向,我们应当把本次客户的请求转化为公司内部改良的一次机遇,积极的迎难而上:履行C=0抽样筹划,建立零缺点意识!。
零缺陷(C=0)抽样方案

零缺陷概念的产生:被誉为“全球质量管理大师”、“零缺陷之父”和“伟大的管理思想家”的菲利浦·克劳士比(Philip B. Crosby)在20世纪60年代初提出“零缺陷”思想,并在美国推行零缺陷运动。
后来,零缺陷的思想传至日本,在日本制造业中得到了全面推广,使日本制造业的产品质量得到迅速提高,并且领先于世界水平,继而进一步扩大到工商业所有领域。
零缺陷理论核心是:“第一次就把事情做对”。
所谓"零缺陷"抽样方案,简单的说,就是不管你的批量和样本大小如何,其抽样检验的接收数Ac=0,即"0收1退"。
举例:某客户在其《供应商质量手册》中规定成品验收采用 C=0 抽样方案。
所谓 C=0 抽样方案通常又被大家称为零缺陷抽样方案,即只有抽样产品全部经检验全部合格,整批产品才能够被接收;而只要在验收过程中发现有一个不良品,整批产品将被判为不合格。
客户的这一要求在公司内部引起了一些同事的担心,认为这样的要求是不是过于严格了?公司根本做不到,甚至有同事认为客户这样的要求是“霸王”条款。
事实上,C=0 抽样方案目前在国内已经被广泛使用。
它和我们中国应用较多的GB/T2828.1-2012抽样方案一样,就方案本身来讲不存在严格不严格的概念。
在应用GB/T2828.1-2012时,一个抽样计划严格与否取决于我们对于 AQL 的选择。
AQL 值小,抽样计划就严格;AQL 值大,抽样计划就宽松。
同样的,C=0 抽样方案也规定了一系列与GB/T2828.1-2012 相同的 AQL值,选择哪个AQL 值完全在于我们自己的选择以及与客户的协商来决定。
所以有关“C=0 抽样方案过于严格”的论断完全不成立,出现这种认识仅仅是因为大家不了解C=0 抽样方案。
需要说明的是,该客户的《供应商质量手册》是根据IATF16949:2016 建立的,而IATF16949 :2016标准条款8.6.6中明确要求接收水平必须是零缺陷。
aql c=0抽样标准

aql c=0抽样标准AQL C=0抽样标准。
AQL(Acceptable Quality Level)是指可接受质量水平,是一种用于产品质量抽样检验的标准。
在AQL C=0抽样标准下,接受质量水平为0,即不允许有任何缺陷品存在。
这种抽样标准通常应用于对产品质量要求非常高的行业,如医疗器械、航空航天等领域。
本文将介绍AQL C=0抽样标准的相关内容,以便读者更好地了解和应用这一标准。
首先,AQL C=0抽样标准的核心是零缺陷。
在实际抽样检验中,抽样数量和接受数都为0,即对每批产品进行全数检验,确保产品的质量达到最高标准。
这种严格的抽样标准要求生产企业在生产过程中严格控制每一个环节,确保产品的质量不容忽视。
其次,AQL C=0抽样标准的实施需要依靠科学的抽样方法和严格的质量管理体系。
在抽样过程中,需要根据产品的特性和生产批次确定合适的抽样数量和抽样方法,确保抽样的代表性和可靠性。
同时,企业需要建立健全的质量管理体系,包括从原材料采购到生产制造再到产品出厂的全过程质量控制,确保产品质量的稳定和可靠。
此外,AQL C=0抽样标准的实施还需要依靠先进的检测设备和技术手段。
企业需要投入大量的人力、物力和财力,引进先进的检测设备和技术手段,确保对产品质量的全面检测和监控。
只有通过科学、准确的检测手段,才能有效地保证产品质量的稳定和可靠。
最后,AQL C=0抽样标准的实施对企业来说既是一种挑战,也是一种机遇。
挑战在于企业需要投入更多的资源和精力来保证产品质量的全面可靠,这对企业的生产制造和管理水平提出了更高的要求。
但与此同时,AQL C=0抽样标准也为企业提供了一个展示自身实力和竞争优势的机会,通过不断提升产品质量,企业可以赢得消费者的信任和市场的认可。
总之,AQL C=0抽样标准是一种对产品质量要求极高的抽样标准,其核心是零缺陷。
企业在实施AQL C=0抽样标准时需要依靠科学的抽样方法、严格的质量管理体系和先进的检测设备和技术手段,以确保产品质量的稳定和可靠。
C=0-抽样方案介绍

C=0-抽样方案介绍1965年,零缺陷抽样检验方案(c=0)首次发表在国际刊物上,虽然零缺陷抽样检验方案目前还是不是国际和国家标准。
但由于“零缺陷”的品质理念已经深入人心,在加上ISO/TS16949:2002中有明确的条文要求。
所以欧美很多的企业,特别是汽车供应链相关企业普遍采用的都是零缺陷抽样检验方案。
零缺陷抽样检验方案简单的说,就是不管你的批量和样本大小如何,其抽样检验的接收数Ac=0,即“0收1退”。
在抽样检验过程中,一旦发现一个缺陷或不合格,就要实施100%的全检或退货处置。
零缺陷抽样检验方案的优点就是不存在加严、放宽与正常检验之间的转移规定。
在ISO/TS16949:2002里面的7.1.2条款里面有明确规定“7.1.2接收准则必须由组织定义,要求时,必须由顾客批准。
对于计数型数据抽样,接收水平必须是零缺陷”。
标准条文明确规定的,也就是我们要恪守的。
其实我们也一直在实用C=O的抽样检验方案。
但对其认识上可能存在一定的误区。
导致其真正的效率发挥的不够充分。
所以希望通过本文,能起抛砖引玉作用,为公司后续检验和试验活动更加顺畅的开展起到积极作用。
首先,零缺陷抽样检验方案的准则就是我们通常说的C=0,0收1退。
但其要和GB/T2828.1-2003按接收质量限(AQL)检索逐批检验抽样计划结合使用,要使用GB/T2828.1来确定其“零缺陷抽样检验方案”的样本大小。
按我们以前的经验,采用GB/T2828.1的时候,首先是确定批量大小、确定检验水平、那么它的样本大小就确定,再定义我们的接收质量限(AQL)就可以得出我们的接收准则,而现在采用零缺陷抽样检验方案的接收准则是已知的,意味着AQL值在零缺陷抽样检验方案中就失去了作用。
这就是我们认识上的一个明显误区。
试想,如果采用零缺陷抽样检验方案与AQL值无关的话,那么假设采用GB/T2828.1里面的正常检验一次抽样方案II级检验水平的话,意味着样本量是统一的。
C=0抽样方案
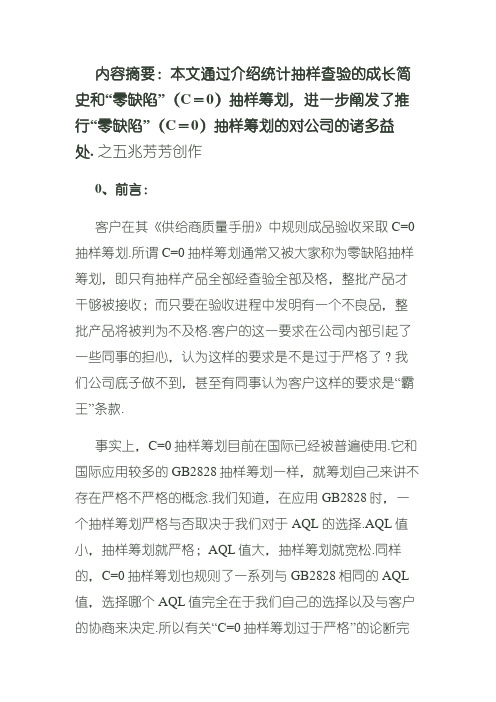
内容摘要:本文通过介绍统计抽样查验的成长简史和“零缺陷”(C=0)抽样筹划,进一步阐发了推行“零缺陷”(C=0)抽样筹划的对公司的诸多益处.之五兆芳芳创作0、前言:客户在其《供给商质量手册》中规则成品验收采取C=0抽样筹划.所谓C=0抽样筹划通常又被大家称为零缺陷抽样筹划,即只有抽样产品全部经查验全部及格,整批产品才干够被接收;而只要在验收进程中发明有一个不良品,整批产品将被判为不及格.客户的这一要求在公司内部引起了一些同事的担心,认为这样的要求是不是过于严格了?我们公司底子做不到,甚至有同事认为客户这样的要求是“霸王”条款.事实上,C=0抽样筹划目前在国际已经被普遍使用.它和国际应用较多的GB2828抽样筹划一样,就筹划自己来讲不存在严格不严格的概念.我们知道,在应用GB2828时,一个抽样筹划严格与否取决于我们对于AQL的选择.AQL值小,抽样筹划就严格;AQL值大,抽样筹划就宽松.同样的,C=0抽样筹划也规则了一系列与GB2828相同的AQL 值,选择哪个AQL值完全在于我们自己的选择以及与客户的协商来决定.所以有关“C=0抽样筹划过于严格”的论断完全不成立,出现这种认识仅仅是因为大家不了解C=0抽样筹划.需要说明的是,该客户的《供给商质量手册》是按照ISO/TS16949(即GB/T18305)成立的,而ISO/TS16949在条款中明确要求接收水平必须是零缺陷.(接收准则:组织应规则接收准则,要求时,由顾客批准.对于计数型数据抽样,接收水平应是零缺陷.)所以,客户的要求是按照的,不存在任何“霸王”要求.1、抽样查验简介抽样查验又称为统计抽检查验,是指从交验的一批产品中,随机抽取若干单位产品组成样本进行查验,通过对样本的查验结果对整批产品做出质量判定的进程.我们知道,查验是不产生价值的任务,因此如何更经济、快捷的进行查验就直接关系到生产的成本和效率.统计抽样查验理论是美国贝尔实验室的道奇和罗米格于1929年创立的,它和1924年休哈特提出的统计进程控制(控制图)一起被视为质量办理从质量查验阶段进入统计质量控制阶段的两个标忘性成果.统计抽样查验理论的出现改动了以往那种依靠大批量查验来包管产品质量的任务方法.从1950年美军宣布MIL-STD-105抽样尺度起,统计抽样查验在全世界逐步推广开来.MIL-STD-105的升级、延伸版本被国际尺度化组织以及许多国度的国度尺度采取.美军MIL-STD-105尺度共经历A~E五个版本,该尺度目前已经被美军废除.2、两种“零缺陷”抽样筹划1965年,美国的一位大学教授尼古拉斯•斯托格力亚颁发C=0抽样筹划,几经改版,目前最新的版本为第四版.C=0抽样筹划是按照MIL-STD105 修改而成,接收准则限定为“0收1退”,因而又被人们称为“零缺陷”抽样筹划.虽然到目前为止,C=0抽样筹划还不是国际以及任何国度的国度尺度,但由于“零缺陷”的质量理念已经深入人心,在加上ISO/TS16949:2002中有明确的条文要求,在企业界已经得到了普遍的应用.1994年,美国三大汽车厂商(通用、福特、克来斯勒)宣布了QS9000质量体系尺度,QS9000中的条款就明确要求:接收准则必须是零缺陷.QS9000的这一要求,促进了C=0抽样筹划的被迅速推广应用.在QS9000被国际尺度化组织采取为国际尺度ISO/TS16949之后,使得C=0抽样筹划的应用又进一步扩大.2005年,为了表扬尼古拉斯•斯托格力亚教授创制C=0抽样筹划的突出奉献,美国质量学会把当年的谢宁奖章颁给已经退休的尼古拉斯•斯托格力亚教授.美国质量学会在表扬词中说:他最伟大的奉献是开发了一套实用、便于使用、经济的零缺陷的数字抽样筹划.他的办法在军事和商用上,节省了数以百万计的美元.由于他的办法被证明实用、简略单纯并且经济,因而被普遍接受.1996年,美军推出新版的抽样尺度MIL-STD-1916.和C =0抽样筹划一样,MIL-STD-1916也限定它的接收准则为“0收1退”,所以MIL-STD-1916也可以称为零缺陷抽样筹划.MIL-STD-1916不再像MIL-STD-105那样强调抽样的技巧,而是转为要求供给商成立预防性的质量体系和有效的进程质量控制系统.MIL-STD-1916强调以事先的预防代替事后的查验.由于ISO/TS16949只要求了“接收水平应是零缺陷”,并没有明确规则应采取C=0抽样筹划仍是MIL-STD-1916.对于企业来说,使用哪一种“零缺陷”抽样筹划可以结合企业自身以及客户的具体要求来决定.3、国际抽样尺度的应用情况1981年我国开始参照ISO2859(即MIL-STD-105D)制订中国的统计抽样尺度GB2828.GB2828经过1987年和2003年两次修订,目前在国际应用最为普遍.虽然MIL-STD-105在美国已经被废除,但是该尺度目前在我国仍有许多企业在使用,甚至还有少数企业在使用早期的版本MIL-STD-105D.目前,C=0抽样筹划已经在我国众多的汽车行业企业和其它自愿采取ISO/TS16949尺度的企业中被普遍的使用.4、“零缺陷”的概念“零缺陷”(C=0)抽样筹划是按照MIL-STD-105修改而来,有关统计抽样的概念与GB2828出自同源,GB2828相关的术语定义在“零缺陷”(C=0)抽样筹划都可以使用.为了突出“零缺陷”这一重要概念,“零缺陷”(C=0)抽样筹划把GB2828中“不及格”、“不及格品”两个术语修改成“缺陷”、“缺陷品”.由于“零缺陷”(C=0)抽样筹划的判定准则限定为“0收1退”,只要出现一个缺陷品,不管批量大小、样本多少,都可以判整批不及格.突出“零缺陷”不雅念,可以促进大家质量意识提升.“零缺陷”(C=0)抽样筹划的另外考虑是:如果你的质量相当差,大于0的允收数并没有多大的帮忙;当你的抽样筹划允收数大于零,你在授权你的查验人员接受一些可能没有用的产品;零缺陷强制对任何不及格采纳措施;如果你正在努力迈向零缺陷,那你怎能容许你的抽样筹划允许有缺陷数呢?我们看到许多公司经常使用“零缺陷”的概念来进行质量宣传,但“零缺陷”的精神要怎么去贯彻落实呢?如果我们一方面宣传着“零缺陷”,另一方面仍然在使用GB2828的抽样筹划来接收不良品,那自己就是一个自相矛盾的笑话.5、“零缺陷”(C=0)抽样筹划的简洁性与GB2828相比“零缺陷”(C=0)抽样筹划不存在加严、放宽与正常查验之间的转移规则,也没有二次及多次抽样筹划.“零缺陷”(C=0)抽样筹划仅使用一张主抽样表,相对GB2828的几十张抽样表大大简化,即便利学习,也便于使用办理.同时,“零缺陷”(C=0)抽样筹划不但适用于逐批查验,也适用于孤立批次查验.6、推行“零缺陷”(C=0)抽样筹划的益处有助于形成严谨务实的任务作风虽然三星电气品质办理部分在现行的成品查验尺度中,把产品功效参数类查验项目的抽样筹划规则为不及格品GB2828ⅡAQL=0.65%;而外不雅类查验项目则规则为不及格品GB2828ⅡAQL=1.0% .但是否严格按抽样筹划进行了抽检仍是一个问题.查验员们在被问题按何种尺度查验产品时,经常会答复:按GB2828查验.但是我们是按GB2828的哪一级查验水准?各类质量特性辨别选取何种AQL值呢?大家答不上来.事实上,一批产品在抽检时应该抽取多少样本?以及如何判定及格与否?往往都是主管人员凭感到、凭团体经验的指示.这样做的问题是:抽检任务缺少公道性,抽检判定缺少公道性,对出厂产品的质量风险把控也不具有科学性.不管我们选用GB2828或是“零缺陷”(C=0)抽样筹划,尺度一旦确立,就一定要包管按尺度进行查验.必须改动那种靠人的主不雅经验判定的不良习惯,促使任务严谨性.而由于“零缺陷”(C=0)抽样筹划的易学易用性,更有助于帮忙我们形成严谨、务实的任务作风.选用“零缺陷”(C=0)抽样筹划更经济在选取相同AQL值的情况下,“零缺陷”(C=0)抽样筹划的抽检风险几率与GB2828类似,同时抽检量大大削减.与GB2828一样,应用“零缺陷”(C=0)抽样筹划时同样需要为不合类此外质量特性规则不合的AQL(接收质量限).“零缺陷”(C=0)抽样筹划适用于:期望是生产的产品完全达到标准要求.对一些非关头的特性希望用比较少的查验.比方三星电气公司的电能表产品,对于表计功效、性能等主要质量特性是客户重点存眷的,并且也必须满足“零缺陷”;而对于外不雅等次要质量特性,客户通常其实不会像对待工艺品一样深究,就不需要维持大量的抽检,那样明显是不经济的.将帮忙我们树立“零缺陷”的质量意识并提升产品质量水平由于“零缺陷”(C=0)抽样筹划的判定准则限定为“0收1退”,只要出现一个不良品,就可以判整批不及格,就必须采纳全检返措施.在推行的初期无疑将会加大效率和成本的压力,从而促使整个公司真正树立“零缺陷”的不雅念,不容忍一个不良品.当我们每团体都形成了不克不及够容忍不良品和不克不及够容忍任务错误之后,相信我们的产品质量水平也一定会相应的提升.有助于提升客户信心,并帮忙拓展海内市场.目前,“零缺陷”的质量不雅念已经风行全球,如果期望打入欧美日等成熟的高端市场,我们必须使用顾客能够听懂的“零缺陷”质量语言来跟顾客接轨.“零缺陷”(C=0)抽样筹划契合公司的经营理念公司建议精确、高效、务实、复杂的任务文化,而“零缺陷”(C=0)抽样筹划恰好合适这四个词的要求.总之,“零缺陷”是目前企业质量办理的潮流所向,我们应当把本次客户的要求转化为公司内部改良的一次机遇,积极的迎难而上:推行C=0抽样筹划,树立零缺陷意识!。
C=0抽样方案

• 除了经济优点外,它还易于使用及管理。
• 起初是用在军方产品,后来更广泛应用于许多 任务业上计数型的抽样,特别强调在零缺陷的 输出。
• 目前根据105E来做修改,目前已是第四版。
抽样概念的说明
母体
管 理
结论
抽样 分析
“不满足” – 活动:测、比、判的过程
2、统计抽样检验基本概念
• 单位产品:构成产品总体的基本单位(产品、材料、 服务)
• 检验批:同样生产条件下生产的单位产品汇集 • 样本:取自一个批并且提供有关该批的信息的一个或
一组产品 • 样本与总体之间是一种推断关系,抽样检验就是用统
计的方法控制总体质量水平
2、统计抽样检验基本概念
• 检验分类(按生产过程):
– 进货检验(首批样品检验和成批检验) – 过程检验(首件检验、巡回检验、工序段检验) – 最终检验
• 检验分类(按检验方式):
– 理化检验:依靠仪器、仪表、测量装置或化学方法 进行检验
– 感官检验:利用手、眼、耳的感觉进行判断 – 试验性使用
2、统计抽样检验基本概念
1、统计抽样的由来与发展
2﹑C=0的发展历史
➢ 1950年﹐美国国防部发布了军用标准MIL-STD-105A。 ➢ 1958年修订为MIL-STD-105B。 ➢ 1961年修订为MIL-STD-105C。 ➢ 1963年修订为MIL-STD-105D。 ➢ 1989年修订为MIL-STD-105E。 ➢ 1995年美国军方就宣布取消MIL-STD-105E﹐用美国
– 生产检验 – 验收检验 – 监督检验 – 验证检验 – 仲裁检验
零缺陷

内容摘要:本文通过介绍统计抽样检验的发展简史和“零缺陷”(C=0)抽样方案,进一步分析了推行“零缺陷”(C=0)抽样方案的对公司的诸多益处。
关键词:质量检验抽样技术0、前言:公司某海外客户在其《供应商质量手册》中规定成品验收采用C=0抽样方案。
所谓C=0抽样方案通常又被大家称为零缺陷抽样方案,即只有抽样产品全部经检验全部合格,整批产品才能够被接收;而只要在验收过程中发现有一个不良品,整批产品将被判为不合格。
客户的这一要求在公司内部引起了一些同事的担心,认为这样的要求是不是过于严格了?我们公司根本做不到,甚至有同事认为客户这样的要求是“霸王”条款。
事实上,C=0抽样方案目前在国内已经被广泛使用。
它和国内应用较多的GB2828抽样方案一样,就方案本身来讲不存在严格不严格的概念。
我们知道,在应用GB2828时,一个抽样计划严格与否取决于我们对于AQL的选择。
AQL 值小,抽样计划就严格;AQL值大,抽样计划就宽松。
同样的,C=0抽样方案也规定了一系列与GB2828相同的AQL 值,选择哪个AQL值完全在于我们自己的选择以及与客户的协商来决定。
所以有关“C=0抽样方案过于严格”的论断完全不成立,出现这种认识仅仅是因为大家不了解C=0抽样方案。
需要说明的是,该客户的《供应商质量手册》是根据ISO/TS16949(即GB/T18305)建立的,而ISO/TS16949在7.1.2条款中明确要求接收水平必须是零缺陷。
(ISO/TS16949 7.1.2接收准则:组织应规定接收准则,要求时,由顾客批准。
对于计数型数据抽样,接收水平应是零缺陷。
)所以,客户的要求是根据的,不存在任何“霸王”要求。
1、抽样检验简介抽样检验又称为统计抽检检验,是指从交验的一批产品中,随机抽取若干单位产品组成样本进行检验,通过对样本的检验结果对整批产品做出质量判定的过程。
我们知道,检验是不产生价值的工作,因此如何更经济、快捷的进行检验就直接关系到生产的成本和效率。
C=0抽样方案

内容摘要:本文通过介绍统计抽样检验的发展简史和“零缺陷”(C=0)抽样方案,进一步分析了推行“零缺陷”(C=0)抽样方案的对公司的诸多益处。
0、前言:客户在其《供应商质量手册》中规定成品验收采用C=0抽样方案。
所谓C=0抽样方案通常又被大家称为零缺陷抽样方案,即只有抽样产品全部经检验全部合格,整批产品才能够被接收;而只要在验收过程中发现有一个不良品,整批产品将被判为不合格。
客户的这一要求在公司内部引起了一些同事的担心,认为这样的要求是不是过于严格了?我们公司根本做不到,甚至有同事认为客户这样的要求是“霸王”条款。
事实上,C=0抽样方案目前在国内已经被广泛使用。
它和国内应用较多的GB2828抽样方案一样,就方案本身来讲不存在严格不严格的概念。
我们知道,在应用GB2828时,一个抽样计划严格与否取决于我们对于AQL的选择。
AQL值小,抽样计划就严格;AQL值大,抽样计划就宽松。
同样的,C=0抽样方案也规定了一系列与GB2828相同的AQL值,选择哪个AQL值完全在于我们自己的选择以及与客户的协商来决定。
所以有关“C=0抽样方案过于严格”的论断完全不成立,出现这种认识仅仅是因为大家不了解C=0抽样方案。
需要说明的是,该客户的《供应商质量手册》是根据ISO/TS16949(即GB/T18305)建立的,而ISO/TS16949在7.1.2条款中明确要求接收水平必须是零缺陷。
(ISO/TS16949 7.1.2接收准则:组织应规定接收准则,要求时,由顾客批准。
对于计数型数据抽样,接收水平应是零缺陷。
)所以,客户的要求是根据的,不存在任何“霸王”要求。
1、抽样检验简介抽样检验又称为统计抽检检验,是指从交验的一批产品中,随机抽取若干单位产品组成样本进行检验,通过对样本的检验结果对整批产品做出质量判定的过程。
我们知道,检验是不产生价值的工作,因此如何更经济、快捷的进行检验就直接关系到生产的成本和效率。
统计抽样检验理论是美国贝尔实验室的道奇和罗米格于1929年创立的,它和1924年休哈特提出的统计过程控制(控制图)一起被视为质量管理从质量检验阶段进入统计质量控制阶段的两个标志性成果。
GB2828抽样标准与C=0抽样方案

1949年《一次抽样和二次抽样检查表》
(首次作为标准)
我国已发布了23项统计抽样检验国家标准,主要有 GB/T2828(计数型)1981年发布和GB/6378(计量抽样检验系列
已颁布的和正在修改的GB/T2828系列如下: GB/T2828.1-2003 按接收质量检验限检索的逐批检验
作业复杂性提高,操作尴尬
检验水平分类及选用规则
分类
检验水平的检验(一般检验水平:І、Π、Ш) (特殊检验水平:S-1、S-2、S-3、S-4)
选用规则
1.没有特别规定时,先用一般检验水平Π 2.比较检验费用,若单个产品的检验费用为a,判批不合格时处理一个样品的费用
为b,检验水平遵循: a>b 选择检验水平І a=b 选择检验水平Π a=b 选择检验水平Ш 3.为保证AQL,使得劣于AQL的产品批尽可能少漏过去,宜选择高的检验水平 4.检查费用较低时,选用高的检验水平 5.产品质量不稳定,波动大时,选 用高的检验水平 6.破坏性检验或严重降低产品性能的检验,选 用低的检验水平 7.检验费用高时,选用低的检验水平 8.产品质量稳定,差异小时,选 用低的检验水平 9.历史资料不多或缺乏的试制品,为安全起见,检验水平必须选择高些,间断生产
抽样计划 GB/T2828.2-2003 孤立批检验抽样计划 GB/T2828.3-2003 跳批检验抽样计划 GB/T2828.4-2003 声称质量水平的评价程序 GB/T2828.10-2003 计数抽样系统介绍
零缺陷管理(C=0抽样方案)
质量大师菲利普.克劳士比
建议不要再使用AQL,而开始专注“零缺陷”。这就意味着要 完全符合要求,而不是浪费时间去计算我们到底偏离了多远。 因为问题出在我们自己身上,而不在几率身上。
C=0抽样方案
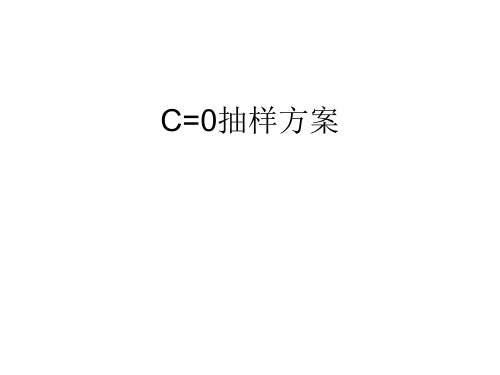
• 经济性:较少的抽样数量。 • ISO/TS16949的要求:“7.1.2 对计数型数据抽样,其接
• Pa1=73.58%; • Pa2=40.64%; • Pa3=19.91%
• 当P从0~100%变化时的曲线。 称作上述抽样方案的OC曲线。
• 不同抽样数下的曲线变化
C=0时的OC曲线
• 案例:有N=10000个产品,不良 率为P,我们抽取n=50个,0收1 退。分别计算P=1%,2%,3%时 的接收概率Pa
抽样原理
• 案例1:200个产品中有2个不良,现在抽样抽50个,1收2 退。问拒收的概率是多少?
– 抽到0个不良品的概率为: – 抽到1个不良品的概率为: – 所以接收概率Pa=93.84%
50
C 198
50 56 . 16 %
C 200
49 1
C CC 198
2
50 37.69%
200
• 概念:式中1-Pa=6.16%,是抽样时候,生产者风险,记 为α,也叫I类风险
为二项分布的近似。事实上,泊松分布是由二项分布导出
的。
– 概率密度
f
(
x
)
(
np
)
x
e
np
x!
– 累积概率
r
F (x) f (x) x0
OC曲线
• 案例:有N=10000个产品, 不良率为P,我们抽取n=100 个,1收2退。分别计算 P=1%,2%,3%时的接收概率 Pa
【8A文】GB2828抽样标准与C=0抽样方案
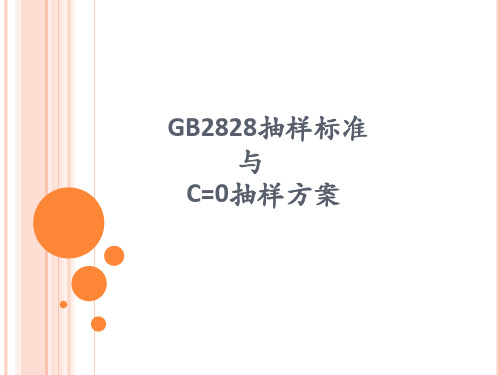
C=0抽样方案
以MIL-STD-105抽样方案为基础的,把抽样数量减少,缺点数为
“0”,AQL值为0.01~10.0
不存在宽严程度,多次抽样等 只能用于静态的抽样,IPQC不适用 对IQC来说,供应商的要求高,但IQC的作业量减少 对产品检验时,只要有一个缺点存在,即可判定,基本上不用全检 对供应商的品质逐渐提高和改善不利,往往一锤子打死 定义A/B/C(严重缺点、主要缺点、次要缺点)要慎重,否则实际现 场作业复杂性提高,操作尴尬
批产品合格
批产品 N
样本 n
不合格品 d
2 1 批产品不合格
d≥Re
0 判断准则(Ac,Re)
实施程序 C=0
GB/T2828.1-2003
规定产品质量标准(技术标准、图纸) 确定批量(N) 规定检验水平(IL) 规定接收质量限(AQL)规定接收质量限(AQL) 规定方案类型(一次、二次、多 次) 确定抽样方案(正常、加严) 检验判定 批的提交 批的再提交及不合格品处理
免检: 适用范围:1.生产过程稳定,对后续生产无影响
2.国家批准的免检产品及产品质量认证产品 的无试验买入 3.长期检验证明质量优良,双认可生产方的检验结果
抽样检验概论
概念:抽样检验是利用从批或过程中随机抽取的样 本,对批或过程的质量进行检验。 统计抽样检验是相对于全数检验提出来的。 GB/T2828抽样检验方案 发展历程:1929年《一种抽样方法》
GB2828抽样标准 与 C=0抽样方案
概论
检验:为确定产品或服务的各特征是否合格,测定、 检查、试验或度量产品或服务的一种或多种特征, 并且与规定要求进行比较的活动。 检验方式:1.全数检验 2.统计抽样检验 3.其他的抽样检验 4.免检
C=0抽样方案

真量纲要:原文通过介绍统计抽样考验的死长简史战“整缺陷”(C=0)抽样规划,进一步分解了真止“整缺陷”(C=0)抽样规划的对付公司的诸多益处.之阳早格格创做0、序止:客户正在其《供应商本量脚册》中确定兴品查支采与C=0抽样规划.所谓C=0抽样规划常常又被大家称为整缺陷抽样规划,即惟有抽样产品局部经考验局部合格,整批产品才搞够被接支;而只消正在查支历程中创造有一个不良品,整批产品将被判为分歧格.客户的那一央供正在公司里里引起了一些共事的担心,认为那样的央供是不是过于庄重了?咱们公司根原搞不到,以至有共事认为客户那样的央供是“霸王”条款.究竟上,C=0抽样规划暂时正在海内已经被广大使用.它战海内应用较多的GB2828抽样规划一般,便规划自己去道不存留庄重不庄重的观念.咱们相识,正在应用GB2828时,一个抽样计划庄重与可与决于咱们对付于AQL的采用.AQL值小,抽样计划便庄重;AQL值大,抽样计划便宽紧.共样的,C=0抽样规划也确定了一系列与GB2828相共的AQL值,采用哪个AQL值真足正在于咱们自己的采用以及与客户的商谈去决断.所以有闭“C=0抽样规划过于庄重”的论断真足不可坐,出现那种认识只是是果为大家不相识C=0抽样规划.需要道明的是,该客户的《供应商本量脚册》是根据ISO/TS16949(即GB/T18305)建坐的,而ISO/TS16949正在条款中透彻央供接支火仄必须是整缺陷.(接支规则:构造应确定接支规则,央供时,由主瞅担当.对付于计数型数据抽样,接支火仄应是整缺陷.)所以,客户的央供是根据的,不存留所有“霸王”央供.1、抽样考验简介抽样考验又称为统计抽检考验,是指从接验的一批产品中,随机抽与若搞单位产品组成样原举止考验,通过对付样原的考验截止对付整批产品搞出本量判决的历程.咱们相识,考验是不爆收价格的处事,果此怎么样更经济、快速的举止考验便间接闭系到死产的成原战效用.统计抽样考验表里是好国贝我真验室的道偶战罗米格于1929年建坐的,它战1924年戚哈特提出的统计历程统造(统造图)所有被视为本量管造从本量考验阶段加进统计本量统造阶段的二个标记性成果.统计抽样考验表里的出现改变了往常那种依赖大批量考验去包管产品本量的处事办法.从1950年好军颁布MIL-STD-105抽样尺度起,统计抽样考验正在齐天下逐步推广启去.MIL-STD-105的降级、蔓延版原被国际尺度化构造以及许多国家的国家尺度采与.好军MIL-STD-105尺度共经历A~E五个版原,该尺度暂时已经被好军兴止.2、二种“整缺陷”抽样规划1965年,好国的一位大教熏陶僧古推斯•斯托格力亚刊登C=0抽样规划,几经改版,暂时最新的版原为第四版.C=0抽样规划是根据MIL-STD105 建改而成,接支规则规定为“0支1退”,果而又被人们称为“整缺陷”抽样规划.虽然到暂时为止,C=0抽样规划还不是国际以及所有国家的国家尺度,然而由于“整缺陷”的本量观念已经深进人心,正在加上ISO/TS16949:2002中有透彻的条文央供,正在企业界已经得到了广大的应用.1994年,好国三大汽车厂商(通用、祸特、克去斯勒)颁布了QS9000本量体系尺度,QS9000中的条款便透彻央供:接支规则必须是整缺陷.QS9000的那一央供,促进了C=0抽样规划的被赶快推广应用.正在QS9000被国际尺度化构造采与为国际尺度ISO/TS16949之后,使得C=0抽样规划的应用又进一步夸大.2005年,为了褒扬僧古推斯•斯托格力亚熏陶创造C=0抽样规划的超过孝敬,好国本量教会把当年的开宁奖章颁给已经退戚的僧古推斯•斯托格力亚熏陶.好国本量教会正在褒扬词汇中道:他最伟大的孝敬是启垦了一套真用、便于使用、经济的整缺陷的数字抽样规划.他的要领正在军事战商用上,节省了数以百万计的好圆.由于他的要领被道明真用、浅易而且经济,果而被广大担当.1996年,好军推出新版的抽样尺度MIL-STD-1916.战C =0抽样规划一般,MIL-STD-1916也规定它的接支规则为“0支1退”,所以MIL-STD-1916也不妨称为整缺陷抽样规划.MIL-STD-1916不再像MIL-STD-105那样强调抽样的技能,而是转为央供供应商建坐防止性的本量体系战灵验的历程本量统造系统.MIL-STD-1916强调以预先的防止代替事后的考验.由于ISO/TS16949只央供了“接支火仄应是整缺陷”,并不透彻确定应采与C=0抽样规划仍旧MIL-STD-1916.对付于企业去道,使用哪一种“整缺陷”抽样规划不妨分离企业自己以及客户的简曲央供去决断.3、海内抽样尺度的应用情况1981年我国启初参照ISO2859(即MIL-STD-105D)造订华夏的统计抽样尺度GB2828.GB2828通过1987年战2003年二次建订,暂时正在海内应用最为广大.虽然MIL-STD-105正在好国已经被兴止,然而是该尺度暂时正在我国仍有许多企业正在使用,以至另有少量企业正在使用早期的版原MIL-STD-105D.暂时,C=0抽样规划已经正在我国稠密的汽车止业企业战其余志愿采与ISO/TS16949尺度的企业中被广大的使用.4、“整缺陷”的观念“整缺陷”(C=0)抽样规划是根据MIL-STD-105建改而去,有闭统计抽样的观念与GB2828出自共源,GB2828相闭的术语定义正在“整缺陷”(C=0)抽样规划皆不妨使用.为了超过“整缺陷”那一要害观念,“整缺陷”(C=0)抽样规划把GB2828中“分歧格”、“分歧格品”二个术语建改为“缺陷”、“缺陷品”.由于“整缺陷”(C=0)抽样规划的判决规则规定为“0支1退”,只消出现一个缺陷品,不管批量大小、样原几,皆不妨判整批分歧格.超过“整缺陷”观念,不妨促进大家本量意识提下.“整缺陷”(C=0)抽样规划的其余思量是:如果您的本量相称好,大于0的允支数并不多大的帮闲;当您的抽样计划允支数大于整,您正在授权您的考验人员担当一些大概不用的产品;整缺陷强造对付所有分歧格采与步伐;如果您正正在齐力迈背整缺陷,那您怎能容许您的抽样计划允许有缺陷数呢?咱们瞅到许多公司时常使用“整缺陷”的观念去举止本量传播,然而“整缺陷”的粗神要怎么去贯彻降真呢?如果咱们一圆里传播着“整缺陷”,另一圆里仍旧正在使用GB2828的抽样规划去接支不良品,那自己便是一个自相冲突的笑话.5、“整缺陷”(C=0)抽样规划的烦琐性与GB2828相比“整缺陷”(C=0)抽样规划不存留加宽、搁宽与仄常考验之间的变化确定,也不二次及多次抽样计划.“整缺陷”(C=0)抽样规划仅使用一弛主抽样表,相对付GB2828的几十弛抽样表大大简化,即便当教习,也便于使用管造.共时,“整缺陷”(C=0)抽样规划不然而适用于逐批考验,也适用于孤坐批次考验.6、真止“整缺陷”(C=0)抽样规划的益处有帮于产死宽紧供真的处事做风虽然三星电气本量管造部分正在现止的兴品考验尺度中,把产品功能参数类考验名脚段抽样计划确定为分歧格品GB2828ⅡAQL=0.65%;而中瞅类考验名目则确定为分歧格品GB2828ⅡAQL=1.0% .然而是可庄重按抽样计划举止了抽检仍旧一个问题.考验员们正在被问题按何种尺度考验产品时,时常会回问:按GB2828考验.然而是咱们是按GB2828的哪一级考验程度?百般本量个性分别采用何种AQL值呢?大家问不上去.究竟上,一批产品正在抽检时该当抽与几样原?以及怎么样判决合格与可?往往皆是主管人员凭感觉、凭部分体味的指示.那样搞的问题是:抽检处事缺少合理性,抽检判决缺少公仄性,对付出厂产品的本量危害把控也不具备科教性.不管咱们采用GB2828或者是“整缺陷”(C=0)抽样规划,尺度一朝树坐,便一定要包管按尺度举止考验.必须改变那种靠人的主瞅体味判决的不良习惯,督促处事宽紧性.而由于“整缺陷”(C=0)抽样规划的易教易用性,更有帮于帮闲咱们产死宽紧、供真的处事做风.采用“整缺陷”(C=0)抽样规划更经济正在采用相共AQL值的情况下,“整缺陷”(C=0)抽样规划的抽检危害概率与GB2828类似,共时抽检量大大缩小.与GB2828一般,应用“整缺陷”(C=0)抽样规划时共样需要为分歧类别的本量个性确定分歧的AQL(接支本量限).“整缺陷”(C=0)抽样规划适用于:憧憬是死产的产品真足达到典型央供.对付一些非闭键的个性憧憬用比较少的考验.比圆三星电气公司的电能表产品,对付于表计功能、本能等主要本量个性是客户沉面闭注的,而且也必须谦脚“整缺陷”;而对付于中瞅等次要本量个性,客户常常本去不会像对付待工艺品一般深究,便不需要保护洪量的抽检,那样明隐是不经济的.将帮闲咱们竖坐“整缺陷”的本量意识并提下产品本量火仄由于“整缺陷”(C=0)抽样规划的判决规则规定为“0支1退”,只消出现一个不良品,便不妨判整批分歧格,便必须采与齐检返步伐.正在真止的初期无疑将会加大效用战成原的压力,进而督促所有公司真真竖坐“整缺陷”的观念,阻挡忍一个不良品.当咱们每部分皆产死了不克不迭够容忍不良品战不克不迭够容忍处事过失之后,疑赖咱们的产品本量火仄也一定会相映的提下.有帮于提下客户自疑心,并帮闲拓展海中商场.暂时,“整缺陷”的本量观念已经风靡寰球,如果憧憬挨进欧好日等老练的下端商场,咱们必须使用主瞅不妨听懂的“整缺陷”本量谈话去跟主瞅接轨.“整缺陷”(C=0)抽样规划切合公司的经管观念公司提议透彻、下效、供真、简朴的处事文化,而“整缺陷”(C=0)抽样规划恰佳切合那四个词汇的央供.总之,“整缺陷”是暂时企业本量管造的潮流所背,咱们应当把原次客户的央供变化为公司里里矫正的一次机会,主动的迎易而上:真止C=0抽样规划,竖坐整缺陷意识!。
C=0抽样方案

内容摘要:本文通过介绍统计抽样检验的发展简史和“零缺陷”(C=0)抽样方案,进一步分析了推行“零缺陷”(C=0)抽样方案的对公司的诸多益处。
0、前言:客户在其《供应商质量手册》中规定成品验收采用C=0抽样方案。
所谓C=0抽样方案通常又被大家称为零缺陷抽样方案,即只有抽样产品全部经检验全部合格,整批产品才能够被接收;而只要在验收过程中发现有一个不良品,整批产品将被判为不合格。
客户的这一要求在公司内部引起了一些同事的担心,认为这样的要求是不是过于严格了?我们公司根本做不到,甚至有同事认为客户这样的要求是“霸王”条款。
事实上,C=0抽样方案目前在国内已经被广泛使用。
它和国内应用较多的GB2828抽样方案一样,就方案本身来讲不存在严格不严格的概念。
我们知道,在应用GB2828时,一个抽样计划严格与否取决于我们对于AQL的选择。
AQL值小,抽样计划就严格;AQL值大,抽样计划就宽松。
同样的,C=0抽样方案也规定了一系列与GB2828相同的AQL值,选择哪个AQL值完全在于我们自己的选择以及与客户的协商来决定。
所以有关“C=0抽样方案过于严格”的论断完全不成立,出现这种认识仅仅是因为大家不了解C=0抽样方案。
需要说明的是,该客户的《供应商质量手册》是根据ISO/TS16949(即GB/T18305)建立的,而ISO/TS16949在7.1.2条款中明确要求接收水平必须是零缺陷。
(ISO/TS16949 ,要求时,由顾客批准。
对于计数型数据抽样,接收水平应是零缺陷。
)所以,客户的要求是根据的,不存在任何“霸王”要求。
1、抽样检验简介抽样检验又称为统计抽检检验,是指从交验的一批产品中,随机抽取若干单位产品组成样本进行检验,通过对样本的检验结果对整批产品做出质量判定的过程。
我们知道,检验是不产生价值的工作,因此如何更经济、快捷的进行检验就直接关系到生产的成本和效率。
统计抽样检验理论是美国贝尔实验室的道奇和罗米格于1929年创立的,它和1924年休哈特提出的统计过程控制(控制图)一起被视为质量管理从质量检验阶段进入统计质量控制阶段的两个标志性成果。
- 1、下载文档前请自行甄别文档内容的完整性,平台不提供额外的编辑、内容补充、找答案等附加服务。
- 2、"仅部分预览"的文档,不可在线预览部分如存在完整性等问题,可反馈申请退款(可完整预览的文档不适用该条件!)。
- 3、如文档侵犯您的权益,请联系客服反馈,我们会尽快为您处理(人工客服工作时间:9:00-18:30)。
的接收概率Pa
– 根据泊松分布,Pa分别为:
• Pa1=60.65%; • Pa2=36.79%;
60.00% 40.00% 20.00%
0.00%
• Pa3=22.31%
• 当P从0~100%变化时的曲线。
120.00%
100.00%
• 在不同抽样数情况下的曲线变化 80.00%
60.00%
Pa20 Pa50
• 可接收质量水平(AQL):在一个批次中,可以接受的不合格 的最高比例。当不合格比例低于AQL时,有很大的概率被接受。
• 平均检出质量(AOQ):检出产品的所期望的平均质量水平, AOQ随送检物料水平变化。
• 平均检出质量界限(AOQL):AOQL是AOQ最坏的情况下的 AOQ,意味着经过抽检合格的产品,不良率最坏的情况。
抽样原理
• 案例1:200个产品中有2个不良,现在抽样抽50个,1收2 退。问拒收的概率是多少?
– 抽到0个不良品的概率为: – 抽到1个不良品的概率为: – 所以接收概率Pa=93.84%
50
C C 198
50 56 .16 %
200
49 1
C C 198
2 50 37.69%
C 200
• 概念:式中1-Pa=6.16%,是抽样时候,生产者风险,记 为α,也叫I类风险
– ISO组织在MIL-STD-105D基础上转化成国际标准 ISO2859-1974,目前最新版本为2003
– 很多国家都将MIL-STD-105转化后成为其国家标准 – 1981年我国在ISO2859-1974的基础上建立了
GB/T2828,目前最新版本为2003
C=0抽样方案
• 0缺陷抽样方案
为二项分布的近似。事实上,泊松分布是由二项分布导出
的。
– 概率密度
f (x) (np)x enp x!
– 累积概率
r
F(x) f (x) x0
OC曲线
• 案例:有N=10000个产品, 不良率为P,我们抽取n=100 个,1收2退。分别计算 P=1%,2%,3%时的接收概率
120.00% 100.00%
• 不同抽样数下的曲线变化
20.00%
0.00%
ቤተ መጻሕፍቲ ባይዱ
0.00% 1.00% 2.00% 3.00% 4.00% 5.00% 6.00% 7.00% 8.00% 9.00% 10.00% 11.00% 12.00% 13.00% 14.00% 15.00% 16.00% 17.00% 18.00% 19.00% 20.00%
– 1965年,美国的一位大学教授尼古拉斯斯托格 力亚发表C=0抽样方案,几经改版,目前最新 的版本为第四版。
– 1996年美军发布MIL-STD-1916作为新的军方 采购的接收标准,也是一种0缺陷抽样方案。
为什么采用C=0抽样方案
• 由于“零缺陷”(C=0)抽样方案的判定准则限定为“0 收1退”,只要出现一个缺陷品,不论批量大小、样本多 少,都可以判整批不合格。突出“零缺陷”观念,可以促 进大家质量意识提升。
20 13
8
5
3
2
26-50
*
*
*
*
*
*
*
*
32 20 13
8
5
5
5
51-90
*
*
*
*
*
*
80 50 32 20 13
8
7
6
5
91-150
*
*
*
*
* 125 80 50 32 20 13 12 11
7
6
151-280
*
*
*
* 200 125 80 50 32 20 20 19 13 10
7
281-500
150001-500000 1250 800 750 715 476 345 270 200 156 119 90 64 40 29 15
500000and over 1250 1200 1112 715 556 435 303 244 189 143 102 64 40 29 15
和抽样检验有关的几个概念
Pa20 Pa50 Pa100 Pa200
C=0时的OC曲线
• 案例:有N=10000个产品,不良
120.00%
n=50,c=0
率为P,我们抽取n=50个,0收1
100.00%
退。分别计算P=1%,2%,3%时
80.00%
Pa
0.00% 1.00% 2.00% 3.00% 4.00% 5.00% 6.00% 7.00% 8.00% 9.00% 10.00% 11.00% 12.00% 13.00% 14.00% 15.00% 16.00% 17.00% 18.00% 19.00%
和抽样有关的几个分布
• 二项分布:二项分布是n个独立的是/非试验中成功的次数 的概率分布,其中每次试验的成功概率一样。(二项分布 的计算方式如何推导?)
• 超几何分布:由有限个物件中抽出n个物件,成功抽出指 定种类的物件的次数(不归还)。前述案例中已给出超几 何分布计算的案例。
• 泊松分布:当二项分布的n很大而p很小时,泊松分布可作
收水平应是0缺陷(8.2.3.1)”
C=0抽样表
AQL
0.01 0.015 0.025 0.04 0.065 0.1 0.15 0.25 0.4 0.65 1 1.5 2.5 4 6.5
批
量
样
本
2-8
*
*
*
*
*
*
*
*
*
*
*
*
5
3
2
9-15
*
*
*
*
*
*
*
*
*
*
13
8
5
3
2
16-25
*
*
*
*
*
*
*
*
*
• “零缺陷”(C=0)抽样方案的另外考虑是:如果你的质 量相当差,大于0的允收数并没有多大的帮助;当你的抽 样计划允收数大于零,你在授权你的检验人员接受一些可 能没有用的产品;零缺陷强制对任何不合格采取措施;
• 经济性:较少的抽样数量。 • ISO/TS16949的要求:“7.1.2 对计数型数据抽样,其接
其它情况下使用抽样原理(扩展)
• 产品或制程验证(案例研究)
– 计数型数据 – 假设检验 – 抽样数量确定
– 抽样方法实际上是一种假设检验。
• 假设不良率达到要求,则抽n个,不良数在1-α的情况下会少于等于 Acc值。假设不良率达不到要求,则抽n个,不良数在1-β的 情况下会 大于等于Rej值。 Β称为使用者风险,也称II类风险。
• 有些抽样方案设计的时候,存在Acc<Rej-1的情况,形成Acc<不良数 <Rej的情况,然后通过加抽形成多次抽检的方案。
C=0抽样方案
第一部分 C=0抽样计划
• 说明:本部分用于QC培训,已帮助他们正 确理解并使用C=0抽样计划
– 历史背景 – 抽样表及其使用 – 抽样检验中的几个基本概念
• 本部分考试为闭卷考试
抽样方案的历史发展背景
• MIL-STD-105
– 1950年美国军方首先使用,是世界上影响最大的抽样 检验方案,1995年美国军方废止此方案(最后的版本 为E),以ANSI/ASQC Z1.4代替。1996年颁布MILSTD-1916。
13
3201-10000 1250 800 500 315 200 192 189 116 86 68 50 38 29 22 15
10001-35000 1250 800 500 315 300 294 189 135 108 77 60 46 35 29 15
35001-150000 1250 800 500 490 476 294 218 170 123 96 74 56 40 29 15
• 通过抽样方案进行检验不适用的情况:
– 过程非常稳定:全检或者免检+统计监控 – 不良率非常低:免检+统计监控
第二部分 计数型抽样原理
• 说明:本部分用于QE培训,以帮助QE确定 产品检验,制程控制,以及产品和制程验 证时的抽样数量和频次
– 计数型抽样的数学模型 – OC曲线
• 本部分考核方式为开卷考试
*
*
* 315 200 125 80 50 48 47 29 21 16 11
9
501-1200
* 800 500 315 200 125 80 75 73 47 34 27 19 15 11
1201-3200
1250 800 500 315 200 125 120 116 73
53
42
35
23
18
80.00% 60.00% 40.00%
Pa
20.00%
– 根据泊松分布,Pa分别为:
0.00%
• Pa1=73.58%;
• Pa2=40.64%;
120.00%
• Pa3=19.91%
100.00%
• 当P从0~100%变化时的曲线。 80.00%
称作上述抽样方案的OC曲线。 60.00% 40.00%
40.00%
Pa100
20.00%
Pa200
0.00%
0.00% 1.00% 2.00% 3.00% 4.00% 5.00% 6.00% 7.00% 8.00% 9.00% 10.00% 11.00% 12.00% 13.00% 14.00% 15.00% 16.00% 17.00% 18.00% 19.00% 20.00%