石油脱硫技术
石油加工中的脱硫技术

石油加工中的脱硫技术脱硫技术在石油加工中起着重要的作用。
随着环境保护意识的增强,减少二氧化硫排放已成为石油行业的重要任务。
本文将探讨石油加工中常用的脱硫技术,并分析其原理和应用。
一、湿法脱硫技术湿法脱硫技术是目前石油加工中广泛应用的一种方法。
在湿法脱硫中,通过将石油中含有的硫化物与一种溶剂反应,使硫化物转化为可溶性的形式并从石油中移除。
这种技术可以同时去除硫和氮等杂质。
湿法脱硫技术中最常用的方法是氧化脱硫。
在这种方法中,石油经过一系列的处理,使其酸性增加,然后通过与空气中的氧气反应,将硫化物氧化为硫酸盐。
最后,硫酸盐与水反应形成硫酸,从而实现脱硫的目的。
二、干法脱硫技术干法脱硫技术是另一种在石油加工中使用的脱硫方法。
与湿法脱硫不同,干法脱硫不需要使用溶剂,而是通过物理化学反应直接去除石油中的硫化物。
干法脱硫技术中,最常用的方法是选择性吸附。
在这种方法中,石油经过特殊的吸附剂,硫化物会被吸附剂选择性地吸附,从而实现脱硫的目的。
这种方法能够高效地去除硫化物,并且不会引入额外的溶剂,因此在石油加工中得到了广泛应用。
三、生物脱硫技术生物脱硫技术是一种新兴的脱硫方法,其原理是利用特定微生物对硫化物进行降解。
这种方法具有环保、经济和高效的特点,在石油加工中越来越受到关注。
生物脱硫技术中,最常用的方法是利用硫氧化细菌进行脱硫。
这些细菌能够通过代谢过程将硫化物转化为硫酸盐,并从石油中除去。
利用生物脱硫技术不仅可以减少二氧化硫的排放,还可以降低工艺过程中的能耗和废物产生。
四、新兴脱硫技术除了传统的湿法脱硫、干法脱硫和生物脱硫技术,还有一些新兴的脱硫技术在石油加工中逐渐兴起。
这些技术包括离子液体脱硫、高温煤气脱硫以及催化剂脱硫等。
离子液体脱硫技术是利用特殊的离子液体作为溶剂,将硫化物溶解并从石油中去除。
这种方法具有高效率和可再生性的特点,被认为是一种可持续发展的脱硫技术。
高温煤气脱硫技术是将石油加工中产生的高温煤气与一种脱硫剂反应,使硫化物转化为硫酸盐并从煤气中去除。
石油脱硫技术

石油生物催化脱硫石油及其产品的燃烧产生大量的有毒气体SO进入大气,造成严重的空气污染,同时也2是产生酸雨的主要原因,因此需要对含硫量高的石油燃料进行脱硫处理.化学脱硫方法——S气体,反应在加氢脱硫hydrodesulfurizationHDS法通过催化过程将有机硫化物转化成H2高温高压下进行,费用较高,而且难以脱除石油燃料中的噻吩类物质,而生物催化脱硫biodesulfurizationBDS在常温常压就可以进行,并且具有高度专一性,因此发展石油生物催化脱硫方法是十分必要的.由于世界范围内可开发的低硫原油日益减少,人们不得不重视对高硫石油的利用.因此对石油中含硫化合物的化学分析也随之越来越被重视起来.石油中的硫是以有机硫和无机S、FeS等溶解或悬浮在油中.硫两种形式存在的,其中主要是有机硫,也存在少量元素硫、H2有人对4种不同产地的原油进行了化学分析,分离出13类包括176种不同化学结构的有机硫化合物,如图1-1.原油中的硫醇大部分是低分子量,在石油的炼制过程中易被除去,200℃以上沸点的石油产品中几乎很少存在.脂肪族硫化物是沸点200℃以上石油产品如柴油中硫化物的主要成分,芳香族硫化物在较重的馏分中含量较低.虽然喳吩在原油中很少见,但唾吩的衍生物很多,苯唾吩、二苯唆吩、蔡唾吩是高硫原油的重要组成.而且这些含硫化合物在原油加工过程中不同程度地分布于各馏分油中.在流化床催化裂化Fluldeaatlyti..arkce,Fcc汽油中,唆吩和各种取代唆吩是主要的含硫化合物,其中苯并唾吩BeZnohtiophene,BTH占30%.催化柴油馏分中的含硫化合物主要是BHT和二苯并唆吩Dibenzothi0Phene,DBT及各种烷基取代物.随着唾吩类含硫化合物的环数的增加,多环唾吩因空间位阻效应使加氢脱硫催化剂反应活性迅速降低.从炼油角度来看,非活性硫的化合物一般比活性硫的化合物更难脱除,而原油中的硫大部分都是以硫醚类和噻吩类硫的形态存在于沸点较高的石油馏分中,这是含硫原油加工过程中所面临的主要问题.1石油脱硫技术概述碱洗法长期以来,炼油厂大多采用碱洗的办法来去除原油中的硫化物,这一方法较为简单,通过碱洗,可以除去原油中的绝大部分硫化物,但它却产生大量的含硫废水,如果不加以妥善处理,对环境的危害是相当严重的.此外,由于碱洗对有机硫化物的脱除率不高,致使成品油中还含有不同程度的有机硫化物,如果不进一步对成品油进行精制处理,会严重的影响成品油的使用价值.萃取法成品油中的有机硫化物可通过萃取法来去除,常用的萃取剂是碱液,但有机硫化物在碱液和成品油中的分配系数并不高,为了提高萃取效率,可在碱液中加入极性有机溶剂,如DMF、DMSOD等,这样可以大大提高萃取的脱硫效率1.夏道宏、苏贻勋2等提出了MDS-H2O-KOH 化学萃取法.用3种萃取剂对胜利炼油厂催化裂化FCC汽油进行萃取率及回收率的考察.结果表明,该方法既能将油品中的硫醇萃取出来,达到脱硫目的,又可高效回收萃取液中的单一硫醇以及混合硫醇,得到硫醇浓缩液.在同一套脱硫装置中既可高效脱硫又可得到高纯度的硫醇副产品,增加炼厂经济效益和社会效益.福建炼油化工公司3把萃取与碱洗两种工艺结合起来,采用甲醇-碱洗复合溶剂萃取法显着提高了催化裂化FCC柴油的储存安定性,色度由18号降到8号,萃取溶剂经蒸馏回收甲醇后可循环使用.此方法投资不高,脱硫效率较高,对一般炼油厂是可行的.1.3络合法用金属氯化物的DMF溶液处理含硫的石油产品4,可使有机硫化物与金属氯化物作用,生成水溶性的络合物而加以去除.能与有机硫化物生成络合物的金属离子很多,而其中以CdCl2的效果最佳,但由于Cd2+的毒性较大,也可用CoCl2或NiCl2来代替.不同金属氯化物与有机硫化物的络合反应活性依次为5:Cd2+>Co2+>Ni2+>Mn2+>Cr3+>Cu2+>Zn2+>Li+>Fe3+.络合法脱硫无法脱除油品中的酸性组分,而剩余的氮化物、硫化物可在酸性物质的催化作用下聚合、氧化.因此工业上采用络合萃取与碱洗精制相结合的办法,可使油品的安定性最好.在经济上,与萃取法同样具有较好经济效益.1.4吸附法KonyukhovaT.P.6把一些天然沸石如丝光沸石、钙十字石、斜发沸石等经酸性活化后,可用于吸附去除成品油中的乙基硫醇和二甲基硫,而ZSM-5和NaX沸石则分别适用于对硫醚和硫醇的去除.徐志达、陈冰7等用聚丙烯腈基活性炭纤维NACF吸附汽油中的硫醇,但只能把汽油中一部分硫醇脱除,不能把硫醇硫的含量降到10 g/g以下.吸附法脱硫效率不高,而且若吸附剂上吸附了胶质等物质,其脱硫效率更低,所以大多炼油厂不采用此种方法.1.5催化法催化法去除有机硫化合物的方法主要有以下三种:1用沉积在碳纤维或石墨纤维上的酞菁催化剂,在碱性水溶液中对石油馏分进行氧化处理,可以去除其中的硫醇8.在这一体系中,如果不加碱性溶液,而改用碱性多孔性固体催化剂9由碱性硅酸铝、活性碳、金属螯合剂、有机或矿物粘合剂等物质组成,也能有效地去除成品油中的有机硫化物.2用一个固体碱固定床和一个载体于非碱性固体上的金属螯合剂组成的处理系统10对含硫成品油进行处理,在处理时,使含有硫醇且酸性中等的烃类馏分首先与固体碱接触,然后在氧气和极性化合物的存在下,硫醇与载体上的金属螯合剂接触,发生催化氧化反应,可有效地去除成品油中的有机硫化物.3在没有外加氢的条件下,含硫成品油与酸性催化剂ZSM系列、MCM系列、沸石Y、沸石及其混合物在流动床中接触,可使有机硫化物转化为HS,从而可以较容易地从成品油2中去除硫化物10.1.6加氢脱硫hydrodesulfurization,HDS图1-2苯并噻吩的HDS反应机理Cat=催化剂图1-3二苯并噻吩的HDS反应机理Cat=催化剂加氢脱硫从广义上讲也是催化脱硫的方法之一,它是在金属催化剂的作用下,进行高温高压并加氢的脱硫处理,将有机硫化合物转化为硫化氢HS,再从系统中分离出来的方法.该2方法已在工业生产中得到普遍的应用.但是,这种方法本身也存在许多的问题:1加氢脱硫反应的操作温度通常为270~420℃,较高的操作温度可降低产品中的硫含量,但是会缩短催化剂寿命,提高成本费用.2加氢脱硫的操作压力为以下均为表压 2.0~3.45MPa,粗柴油为2.8~12.4MPa:而对重组分如渣油,操作压力需要高达20.7MPa.加氢脱硫的程度随氢气分压的增加而增加,但当氢气分压超过10.3MPa后,压力变化对加氢脱硫反应速率的影响已不太明,而烷基类DBT化合物中芳环的加氢较为显着.此外,裂解汽油反应生成的链烃也会发生加的消耗.3这种方法对石油氢反应,链烃加氢不仅会降低FCC汽油的辛烷值,而且也增加了H2中某些含硫分子无影响,特别是对重组分中的聚芳烃硫杂环PASHs不起作用11;4HS存在会2S的排放会污染大气.毒害脱硫系统的催化剂,使得高含硫石油的HDS变得复杂化;5H21.7生物脱硫石油炼厂的废水、焦油污染的土壤里的硫化合物在自然条件下,其中的一部分会发生生物降解,这是自然界中存在着细菌的作用.细菌脱硫MDS是在温和的条件下,利用适宜的细菌代谢过程使石油脱硫,在生化过程中,脱硫剂可以再生或自身补充.这种脱硫操作中,有机硫分子的代谢仍要以烃作碳源,而不是选择性或专一性地代谢硫,有机硫化合物只是从非水溶性转变成水溶性,随后从石油中被分离出来,但有价值的烃也被部分地损失掉了.MDS对诸如硫醇、硫醚等分子量较小的有机硫化合物较为有效.对于带有硫杂环的芳香族化合物,据报导12,13迄今只有少数几个细菌菌株能够将其代谢为水溶性的化合物,如亚臭假单胞菌和P.alcaligens等,这样就大大地限制了MDS法的商业利用价值.在细菌脱硫法基础上90年代国外迅速发展起来了石油的生物催化脱Biodesulfurization,BDS技术.BDS技术是利用微生物所产生的酶催化特定的C-S断键反应,释放出可溶性硫,而留下碳氢化合物,也就是酶催化反应基本不破坏石油的骨架烃链.BDS与HDS相比较,具有如下优点:1可在低温低压下操作;2成本较低BDS比HDS投资少50%、操作费用少10%~15%;3灵活性好,可用于处理各种油品,如原油、石脑油、中馏分油、FCC汽排放量,对环境保护极为有利;5能有油、残渣燃料油等;4不需要氢气,节省能源,减少CO2效脱除HDS装置难于处理的含硫杂环化合物,而这是传统的脱硫技术HDS很难解决.因此,酶催化反应脱硫法是一种很有前途的脱硫方法.2生物催化脱硫代谢途径2.1以二苯并噻吩表征的生物脱硫代谢途径由于加氢脱硫难以除去二苯并噻吩DBT及其衍生物,而DBT又广泛存在于化石颜料中,所以生物脱硫多以DBT作为模型化合物来进行研究.目前公认的BDS脱硫的有效性是以二苯并噻吩DBT为模型化合物来表征的,并且搞清楚了它们的作用机制是由于微生物酶的作用,因此,对于酶脱硫路线,研究者进行了深入的研究确定了其脱硫路线,并且发现此路线与其它脱硫路线相比,最具有商业化应用价值.酶脱硫路线主要有两种,一种是还原路线,另一种是氧化路线.在还原路线脱硫过程中, S,然后进一步被氧化成为单质硫.此过程由于没有氧的存在,可以防止烃有机硫被转化成H2类物质的氧化,减少油品热值的损失.但是这种方法脱硫能力比较差,很难把它应用于工业化生产.因此,常常采用氧化路线脱硫.在氧化路线中其代谢途径有以下几种:1以碳代谢为中心的Kodama途径14如图2-1所示.图2-1Kodama途径这一路线是在从土壤中分离出的假单胞菌Pseudomonas15,拜叶林克氏菌beijerinckia16及不动杆菌acintobacter和根瘤菌rhizobium17的混合培养中发现的.Kadama路线是在两相油/水生物反应器中通过酶选择性地DBT分子中的C-C键断裂而C-S键保留下来,脱去3个或4个碳的碎片,生成溶于水的小分子有机硫化合物,并不破坏含硫化合物基体.由于是整个含硫化物转入水相,虽可从石油中分离出去,但也损失了有机烃,故油品的液体收率有所下降.若油中含硫化合物以DBT计算,则其质量约为硫原子的5.3倍,即硫质量分数为0.2%的油品脱硫后收率约损失1.0%18,因此,工业化价值小.2以硫代谢为中心的4S途径1989年Kilbane在研究IGTS8细菌脱除煤中有机硫时,从理论上提出了生物降解DBT 的“4S”途径.在该途径中,二苯并噻吩中的硫经过4步氧化,反应的硫中间体分别是DBT-亚砜,DBT-砜,DBT-羟基磺酸,最终生成SO42-和2-羟基联苯2-HBP.硫是以SO42-的形式从有机物中除去的,对烃不发生降解.对不同的菌株,4S途径并不完全相同,被认为有两种脱硫途径19如图2-2所示,但共同的特点都是对C-S键作用.图2-24S途径根据4S脱硫路线Monticello20提出了生物催化脱硫代谢机理,在Cx-DBT代谢过程中,第一步有时起速率控制作用是Cx-DB从油相进入细胞,然后发生一系列氧化反应,最后脱掉含硫的2-羟基联苯2-HBP,移出细胞回到油相中去,保持了油的燃烧值.在此过程中,有两个问题目前还不清楚:1憎水性的Cx-DBT分子从油相到第一个酶的传递过程中,究竟有多少步骤发生还不清楚.研究发现,传质过程并没有受到中间步骤油-水,水-细胞的限制.2Cx-HBP 或Cx-HBPS如何移出细胞也不清楚.微生物氧化有机硫化合物的生化机理也有两种21:①有机化合物的同系化,随后转移至细胞内;②有机化合物在细胞外解离,转化为可溶性产物进入细胞内.前一途径是微生物与典型的不溶性基质如苯并噻吩或二苯并噻吩相互作用;后一途径则要求微生物必须具有所需要的胞外酶.苯并噻吩在细胞内主要沉积在细胞中,而在酵母中主要沉积在线粒体中.同样,二苯并噻吩降解及进入细胞与细胞脂质和脂蛋白有关,二苯并噻吩的氧化可发生在膜结构上.芳环在细菌细胞中的解离可能通过酶的作用发生羟基化,起诱导作用的加氧酶可能是细胞素P450或依赖性黄素.2.2其它含硫化合物的代谢过程2.2.1苯并噻吩的代谢过程苯并噻吩是FCC汽油中的主要含硫化合物.早在198年就有人对苯并噻吩中硫的去除进行了研究22,1994年,Kropp经过实验发现一些假单胞菌属细菌可以把苯并噻吩代谢为苯并噻吩亚砜、苯并噻吩砜和苯甲酸萘噻吩23.这些隔离种群从在苯环上含有甲基取代物的甲基苯并噻吩中生成了类甲基取代苯甲酸萘噻吩,该反应是一个Diels-Alder二分子的亚砜缩合反应,反应同时失去了二原子的氢、氧和一原子的硫,其中,亚砜分子来自于被细菌分解的苯并噻吩、当亚砜分子被带有细胞色素c和氢过氧化物的苯并噻吩酶化合成时,也可得到上述缩和产物.2.2.2噻吩的代谢过程噻吩是最简单的硫杂环化合物,目前没有多少微生物能够对噻吩进行分解.Amphlett24和Cripps25研究发现只有一种自发的反应可以对噻吩完全降解,该反应可以把噻吩中的碳和硫分别转化成二氧化碳和硫酸盐,因此反应由于损失了部分碳而损失了部分热量.对噻吩的生物脱硫技术还在继续研究之中.2.2.3硫醇和烷基硫醇的代谢过程某些需氧和厌氧微生物可以对硫醇和其它的有机硫化物进行代谢,例如:噬硫杆菌thiobacillusthioparus生丝微菌hyphomicrobium都可以通过甲基硫醇氧化酶把甲基硫醇氧化为甲醛、硫单质和氢过氧化物26.3生物脱硫技术的实际应用3.1生化反应器的设计3.1.1搅拌式反应器1953年和1979年的两个专利提出当硫还原菌SRB存在时加氢脱硫,前者只给出了过程与方法,后者处理Romaschlino原油,经2~3d厌氧培养后,40%的有机硫被还原.1974年,前东德VEB公司用未定性混合菌在间歇式发酵罐中与不同的油作用,结果是既脱除了硫,但也引起了油品中碳氢化合物的大量损失27.1978年,加拿大Alberta大学微生物系利用三种不同的海洋环境水样处理PrudhoeBay原油,油中有机硫化合物被降解28.1982年,澳大利亚申请专利使用Bacillus菌脱除原油中的硫,提出此过程为C-S键断裂过程29.1987年Unocal公司在加入表面活性剂使油水相充分接触条件下,用Pseudomonas菌使杂环硫羟基化,生成水溶性产品30,该过程引起杂环馏分在水相中的损失且作用前水相的处理费用较高.从以上实例可以看出,生物催化脱硫大都处于实验室研究阶段,尚未投入工业化使用.要使生物脱硫技术得以在工业应用中扩大,还必须设计适用于生物过程的反应器,目前研究较多的主要有搅拌釜反应器、气升式反应器、流化床反应器、固定床反应器和膜反应器,这些反应器各有优缺点.生物催化脱硫反应受底物和产物抑制,pH值也会影响反应,所以反应器和控制系统的设计必须相适应.由于生物脱硫研究大多处在基础研究阶段,仅有几个反应器的研究.美国EBS公司31设计了使用搅拌槽的生物反应流程如图3-1,过程中生物催化剂、进料油、空气及少量水一起被加入搅拌反应器中,在其中高硫油被氧化,硫被沉积在水相,离开反应器时,油、水、生物催化剂及硫副产品被分离、精制、再利用.这个流程现在仍在不断发展图3-1生物脱硫流程图Eric32等在生物脱硫过程中使用电喷射反应器,通过静电乳化技术减少样品混合能耗,该系统可产生大的表面积却不产生抑制传质的表面活性还原物质,从而节省很大的费用.由此可以看出生物脱硫的反应器有待进一步研究.3.1.2乳化液相接触器BDS过程的产物一般由高纯度的油相、溶有生物催化剂的水相以及油、水、生物催化剂乳化液等三相组成,能否从乳化液相中回收高纯度的油、使生物催化剂循环利用和分离副产品对BDS技术的经济可行性有重要影响.为了提高脱硫反应速率和脱硫效率,一般脱硫反应要求在高催化剂浓度和高油水比条件下运行,这进一步增加了乳化液分离难度.YuLi一Qun等1998开发了一种很有效的油/水/生物催化剂三相分离方法和设备,采用水力旋流器来进行多相分离.该水力旋流器是一种高lm直径5-10cm的圆锥形管.流体加入旋流管中开始旋转,由于油和水的密度不同,密度轻的油相会从管的顶部或者宽的一端溢出,密度大的将会从管的底部或窄的一端溢出.主要步骤有:①将来自乳化液罐中以水为连续相的油/水/生物催化剂乳化液送入第一水力旋流器,②转化来自第一水力旋流器顶部的富油乳化液,形成以油为连续相的乳化液,③使以油为连续相的乳化液通过一个或多个串联的水力旋流器;④收集水相和油相.步骤②中的相转化可采用静态在线搅拌器或在乳化液进入水力旋流器前用泵加压形成压降来实现.在加压条件下可以得到体积百分数为9.999%~100%的高纯度的油,采用静态在线搅拌器也可回收体积百分数为90%的油.也可将以水为连续相的乳化液儿次通过旋流器,得到含油1%-3%的生物催化剂水溶液.该分离方法能回收高纯度的油,生物催化剂可以循环使用,系统效率高,泵是唯一的传动设备,操作简单,运行费用低,很有工业化应用前景.对于高催化剂的系统,利用反应器中乳化现象的优势,还可以加入化学试剂使乳化液暂时失稳,来实现高催化剂浓度下的乳化液相分离.乳化液相接触器能产生很小的水/油/生物催化剂的液滴,从而减少水进入油相,然而这种系统的脱硫效率很低MFcarlnad等,1998.图3-2EPC结构示意图Erie等1998采用一种电力驱动的乳化液相接触器emulsionphaseeonatcter,EPC作为反应器进行生物脱硫过程研究,有机油相为连续相,含催化剂的水相为分散相.该反应器采用两个不同的电极区提高处理能力,结构如图2一8所示.上面是喷嘴区,在喷口处产生分散液滴进入连续油相;下面部分是操作管道,通过平行金属板间的水平振荡电场控制分散相的停留时间,并不断连续的分散液滴,使液滴在反应器中曲折流动.这样就为两相之间的接触提供了足够的表面积.以这种方式,液滴又不断结合,在相界面的分离能力也得到提高.该装置与搅拌反应器相比,能耗减小,形成直径为5μm的液滴,能耗为3W/l.但由于实验中生物催化剂的活性不够高,虽然有足够的反应表面,脱硫率没有明显增加.如果生物催化剂的活性不断得到提高,在传质成为脱硫反应限制因素的条件下,EPC将是一种操作费用低,传质效果好的很有应用前景的生物脱硫反应器.如果采用固定化细胞为催化剂,则反应器为流化床.催化剂固定化的结构优势是操作连续化和产物容易分离,但是固定化的催化剂脱硫性能需要进一步改进.对于一个有效的生物脱硫过程来说,流化床中生物催化剂的反应时间和寿命分别是1和400小时Pacheco 等,1999.3.1.3气升式反应器气升式反应器ALR是用于气一液两相或气一液一固三相过程的接触反应装置.它通过压缩空气膨胀提供能量,依靠含气泡液体与纯液体的密度差造成的升力使流体沿特定的流道循环流动,属于气力搅拌反应器.己工业应用的ALR有外循环式和内循环式两种类型.在低通气量下,仅仅是液相循环;高通气量下则有气泡跟随液相循环.这两类ALR还有其它结构形式,例如气体分布器有的采用喷嘴等;但作用原理基本上相同.可以看出,与传统的鼓泡塔相比,气升式反应器增加了流体循环的流动结构,从而大大改善了相间混合与接触条件,有利于传质和反应过程.其可操作的气体和液体流速范围也大得多.由于其独特的流体力学特性,反应器具有下列突出优点:l热、质传递速率高.2供气效率高,与输入能量关系不大.3结构简单,内部没有运动部件.4通气量高,在有气体循环的条件下,上升室中通气量可大于反应器进气量.5流化效果极佳,可以使固体颗粒甚至较重的颗粒完全保持悬浮状态,这对许多气一液一固三相反应体系具有重要意义.近年来,内循环ALR通过在环隙中增加旋流,这一特性己得到大幅度提高.6能量耗散很均匀,与通气搅拌式反应器形成鲜明的对照.这一优点对剪切力敏感物料例如细胞养殖等反应过程具有特别重要的意义.当然,气升式反应器也存在某些缺点.一是用于高粘性液体效果不够理想,主要是相间混合接触较差.相比之下,通气搅拌反应器依靠机械搅拌作用帮助分散气体.能适应高粘度液体操作.另一缺点是混合与通气是祸合问题.换言之,很难在不改变通气的条件下改善混合状况;反之亦然.3.2生物脱硫工艺近年来,国外生物催化处理工艺发展得很快,下面是几个由EBC公司研制运行的处理工艺Pahcec.,1999,从中可以看出生物脱硫技术的一些优点.lHDS顺流连接BDS图3-3为HDS顺流连接BDS脱硫工艺.在处理含20%轻质催化循环油LCCO的进料混合物时,通过在HDS装置后串接BDS装置不仅大大减少了深度脱硫所需的氢气、避免了过饱和芳香族化合物同加氢脱硫后产生的沸腾燃料混合物相结合,而且减少了燃料的损耗和COZ的排放量.该工艺可使柴油脱硫率达到65一70%,硫排放含量低于50μg/ml.图3-3HDS顺流连接BDS工艺2BDS代替HDs图3-4为BDS代替HDS直接脱硫工艺.使用该工艺处理中度含硫燃料,其脱硫率在40-70%之间.该工艺不仅节省了氢气、减少了燃料的损耗和CO:的排放量.而且不需要二段脱硫和尾气处理装置,大大降低了成本,适用于小型炼油厂使用.图3-4BDS单独脱硫工艺3BDs去除高含硫裂化原料中的硫图3-5为高含硫裂化原料的BDS脱硫工艺.在此工艺中进料多为高含硫轻质催化循环油Hs一Lcco,若BDs顺流连接HDs,不仅节省了大量的氢气、改善了加氢脱硫和脱氮率以及芳香族化合物的饱和度ASAT,而且与l相比还减少BDs装置的规模.产物主要为可在表面活性剂和其它化学产品中作为化学中间体的亚磺酸盐,该工艺的总脱硫效率可达到75-90%.图3-5BDS高含硫裂化原料脱硫上述的3种工艺代表了国外BDS_J几艺目前研究发展的基本情况,对BDS在炼油厂的工艺组合及最优化的设计研究还在进行之中.4生物脱硫实现工业化的关键技术4.1生物催化剂性能的改善生物脱硫技术至今还没有广泛应用的原因之一,是在原生菌中的脱硫酶浓度太低以至影响了反应速度和活性,即脱硫酶的寿命、选择性都还不能满足工业化催化反应所需的基本要求.为此EBC公司从1990年开始对催化剂的活性、寿命及选择性进行了研究并取得了长足的进步:1990年优化了红球菌生长条件,将活性提高到自然菌株的5倍;1992一1993年通过基因工程技术提高了DszA,B,C的表达量;19%年用四种酶优化催化剂设计;1997年通过敲除dszB,将脱硫活性提高200倍,进而开辟了利用携带不完整Dsz酶生物催化剂的新领域,。
石油脱硫工艺流程

石油脱硫工艺流程概述石油脱硫是一项重要的工艺,旨在降低石油中含硫化合物的浓度,以提高石油的质量和环境可接受性。
本文将详细介绍石油脱硫的工艺流程以及相关的技术细节。
工艺流程石油脱硫通常包括以下几个主要步骤:1. 预处理在石油脱硫之前,通常需要对原油进行预处理。
这一步骤的目的是去除石油中的杂质和水分,以减少对后续脱硫工艺的影响。
•原油在进入预处理阶段时,首先通过沉淀和过滤来去除悬浮颗粒物和固体杂质。
•接下来,原油需要被加热以分离其中的水分。
常用的方法是在加热过程中注入蒸汽或使用加热器。
•最后,通过第三次沉淀将油中的水分进一步去除。
2. 硫化物转化在预处理之后,石油进入硫化物转化阶段。
这一步骤旨在将硫化物转化为易于去除的形式。
•首先,将催化剂注入到石油中,以加速硫化物的转化过程。
常用的催化剂包括氢化铝和钠。
•在加热的条件下,硫化物会与催化剂发生反应,生成硫化物的易于去除的形式,如硫化钠。
•这一转化过程需要在高压和高温环境下进行,以提高反应速率和转化效率。
3. 吸收剂处理硫化物转化后,石油进入吸收剂处理阶段。
这一步骤旨在去除石油中的硫化物。
•吸收剂通常选择具有高选择性和吸附能力的物质,如碱性溶液、氨水或酸性氧化物。
•石油与吸收剂接触,硫化物以化学反应的形式被吸附到吸收剂表面。
•重新加热吸收剂,使其继续可用于后续的硫化物吸附。
4. 再生吸收剂处理后,石油中的硫化物被成功去除。
然而,吸收剂中的硫化物达到一定浓度后,需要进行再生。
•再生通常通过多级加热和蒸馏来实现。
首先,将吸收剂加热至高温,以驱除其中的硫化物。
•接下来,通过蒸馏将硫化物从冷却的吸收剂中分离出来。
•结果是得到一种含高浓度硫化物的流体,常被称为“硫化剂废液”。
技术细节石油脱硫工艺中的一些关键技术细节包括以下几点:1. 选择适当的催化剂催化剂的选择对于脱硫工艺的效果至关重要。
不同类型的原油和硫化物需要使用不同的催化剂。
2. 控制温度和压力温度和压力对于脱硫工艺的效果有着重要影响。
石油催化裂化烟气脱硫技术

石油催化裂化烟气脱硫技术石油是我国经济发展的支柱性产业之一,能够为社会经济发展提供助力,而在石油生产环节,产生的烟气含有大量会对大气环境和生态环境造成严重污染的硫氧化物,需要石油生产企业做好烟气脱硫工作,在保证石油质量和产量的同时,对硫氧化物的排放进行控制,促进经济的可持续发展。
标签:石油;催化裂化;烟气;脱硫前言:催化裂化是石油生产中一个非常关键的过程,这个过程产生的烟气含有大量硫氧化物和氮氧化物,容易引发严重的环境污染问题。
可持续发展理念不断深化背景下,要求石油化工企业做好烟气脱硫工作,减少烟气中硫氧化物的含量,对空气污染问题进行有效控制,实现经济效益与环境效益的共同提高。
1 技术发展现状科学技术的进步,带动了石油催化裂化烟气脱硫技术的发展,也取得了较为显著的成果,就目前而言,石油催化裂化脱硫技术大致可以分为两种,一是资源脱硫技术,其主要工艺包括了CANSOLV工艺以及LABSORB工艺,强调借助部分可再生能源实现烟气脱硫,借助无机缓冲液来保证烟气脱硫过程的温度恒定,搭配相应的过滤装置,将缓冲液中的杂质去除;二是非资源脱硫技术,以EDV 工艺为基础,借助碱性洗涤剂,开展烟气脱硫操作,不过实践中发现,这种烟气脱硫技术需要消耗大量水资源,而且产生的废水难以进行二次利用。
我国在对石油催化裂化烟气脱硫技术进行研究的过程中,强调以国外先进技术理念为支撑,开发出更加符合石油化工企业生产特点的烟气脱硫技术,提升技术的针对性和实用性,减少烟气中的有害物质,实现对于自然生态环境的有效保护。
2 烟气脱硫技术石油生产中,催化裂化设备在得到汽油、柴油等目标产品的同时,也会产生大量的烟气,包括再生器烧焦时的再生烟气和燃料燃烧烟气,这些烟气中含有一些会对大气环境造成影响的物质,如氮氧化物、二氧化硫以及催化剂粉尘等,在得不到有效处理的情况下,会引发严重的环境污染问题。
对此,石化企业应该做好石油催化裂化烟气脱硫技术的研究,做好烟气脱硫处理。
工艺方法——催化裂化烟气脱硫技术

工艺方法——催化裂化烟气脱硫技术工艺简介催化裂化是石油炼制的重要过程之一,在催化剂的作用下,通过加热的方式促使重油发生裂化反应生产裂化气、汽油和柴油。
催化裂化工艺流程中产生的烟气含有大量的硫化物,对设备造成了腐蚀,同时对环境产生了很大的影响。
1、干法、半干法脱硫技术干法脱硫技术主要使用干粉作为吸收剂,半干法脱硫一般使用润湿的干粉吸收剂进行硫化物的吸收,两种方法的吸收剂都是通过颗粒回收系统进行吸收剂的回收。
干法和半干法脱硫的主要优点是可以在不降低烟气温度的基础上完成硫化物吸附,避免了硫化物扩散和脱硫作业的水污染问题。
缺点是硫化物的吸附只在脱硫剂的表面进行,内部反应时间长,需要大型的吸附塔和大量的吸附剂才能完成脱硫作业。
干法脱硫比较有代表性的公司,比如Engelhard公司开发的SO2干法脱硫工艺(ESR)是一种比较先进的干法脱硫技术,该工艺采用干燥脱硫剂固体流化床,硫化物脱除率达到95%以上,脱硫剂可以全部再生,并且投资少,操作费用较低。
2、EDV湿法烟气脱硫技术EDV湿法洗涤脱硫技术由Belco公司开发,20世纪90年代中期开始工业应用,问世以来显示出了较为优异的操作性和可靠性。
EDV 烟气脱硫技术主要由氧化镁制浆系统、烟气洗涤系统和废水处理系统组成,利用对烟气喷射的方法,通过烟气的急冷降温处理,在烟气温度恢复正常后,在温度变化过程中脱除烟气中的有害物质,使得烟气中的硫化物凝结最后采用系统过滤烟气,完成烟气的气液分离。
氢氧化镁溶液放置到卸料机上以后,倒入适量的水进行搅拌,制成脱硫溶液,在配置过程中需要控制好水的加入量。
3、加氢预处理技术原油的加氢预处理可以有效处理原油中的硫化物,通过加氢预处理,对于减少原油中硫化物、重金属等杂质具有良好的效果。
加氢预处理技术在对原油进行有害物质处理的过程中,可以进一步提高原油中轻质产品的回收率和回收质量,从而改善催化裂化工艺产品的质量,满足现代炼油企业催化裂化技术发展的需求,从而满足炼化企业快速发展的需求。
石油加工中的脱硫脱氮工艺技术

石油加工中的脱硫脱氮工艺技术在石油加工中,脱硫脱氮工艺技术扮演着至关重要的角色。
随着环境保护意识的增强,对燃料的污染物排放要求也越来越严格,特别是对硫和氮的排放控制。
为了满足这些要求,石油加工行业积极探索和应用各种脱硫脱氮工艺技术,以减少环境污染,改善空气质量。
一、脱硫技术1.吸收法吸收法是最常见的脱硫技术之一。
其原理是利用吸收剂,如氨水、碱溶液等,在气相和液相之间进行气体吸收和气液反应。
这种方法能有效地从燃料中去除硫化物,减少二氧化硫的排放。
常用的吸收法脱硫工艺有胺法和碱吸收法。
2.氧化法氧化法是通过氧化剂氧化硫化物,使其转化为更易于去除的氧化产物。
常用的氧化法包括氧化吸附法和氧化催化法。
其中,氧化吸附法利用氧化剂将硫化物氧化成二氧化硫,并通过吸附剂吸附去除。
氧化催化法则是在催化剂的作用下,将硫化物氧化成二氧化硫,然后通过吸附剂进行去除。
二、脱氮技术1.选择性催化还原法选择性催化还原法是目前最常用的脱氮技术。
该技术利用催化剂将氮氧化物还原成氮气,从而达到脱氮的目的。
常用的催化剂有铈铁、钴钼等。
选择性催化还原法具有脱氮效率高、能耗低等优点。
2.吸附法吸附法是利用吸附剂从燃料中吸附氮氧化物,然后再进行再生或者处理。
吸附剂通常选择活性炭、分子筛等材料。
该方法具有简单易行、处理效果稳定等优点,但需要定期更换吸附剂。
三、脱硫脱氮技术的应用脱硫脱氮技术已广泛应用于石油加工领域,特别是在石油炼制、天然气加工和燃煤电厂等领域。
这些技术的应用不仅可以降低环境污染,减少大气二氧化硫和氮氧化物的排放,还能够改善空气质量,保护生态环境。
在石油炼制过程中,通过脱硫脱氮技术可以有效地去除原油中的硫和氮杂质,提高燃油质量,减少污染物排放。
在天然气加工过程中,脱硫脱氮技术可以提高天然气质量,保护管道设备的使用寿命。
在燃煤电厂中,使用脱硫脱氮技术可以降低燃料中的硫和氮含量,减少燃煤产生的大气污染物。
综上所述,脱硫脱氮工艺技术在石油加工中的重要性不言而喻。
石油油品脱硫技术综述

存 在 着 催 化 剂投 资 大 、 制 备 条 件 苛 刻 、 常 压 下利 用需 氧菌 、厌 氧 菌 除去 石 油含
硫 杂 环化 合 物 中 结 合 硫 。早 在 1 4 8年 资较 少 , 催 化 加氢 难 以脱 除 的苯 并噻 9 对
美 国就 有 了生 物脱 硫 的专 利 ,但 一 直没 吩 类化 合 物有 较 高 的脱 硫 效 率 , 一 项 是
进 行 处 理 ,可 除 去 硫 醇 。金 属 螯 合 剂 是 对重 组分 中的聚芳烃 硫杂 环不起作 用 法 和 酸 性 催 化 剂 法 都 能 使 有 机 硫 化 物 () s存在会 毒害脱 硫系统 的催化 剂 。 4
料 油深 度 脱 硫 的 有效 方 法 。 氧 化脱 硫
氧 化 脱 硫 (O ) 为 近 年 来 发 展 O S 作
存 在 的 问 题 :()加 氢 脱 硫 反 应 热 量 。美 国 E C公 司不 仅 成 功 多放 术 生 产 的 由于 柴 油 中 的 二 甲基 二 苯
并 噻 吩 结 构 稳 定 不 易 加 氢 脱 硫 .为 了 的 操 作 温 度 通 常 为 2 0~ 4 0。 7 2 C.较 再 生 了生 物 脱硫 催 化 剂 并 在 降低 催 化 使 油 品 中的硫 含 量 降 到 1 9 9.需 要 0 / 高 的 操 作 温 度 可 降 低 产 品 中 的 硫 含 剂 生产 成 本 的 同 时也 延 长 了催 化 剂 的寿 更 高 的反 应 压 力 和 更 低 的 空 速 这 无 量 , 但 是 会 缩 短 催 化 剂 寿 命 , 提 高 命 。此 外 该 公 司 又 分 离 得 到 了玫 鸿 球 疑 增 加 了 加 氢 技 术 的 投 资 费 用 和 生 产 成 本 费 用 。 () 汽 油 加 氢 脱 硫 的 操 菌 的 细 菌 ,该 细 菌 能 够 使 C 2 -S键 断裂 成 本 。 而 氧 化 脱 硫 技 术 不 仅 可 以 满 足
石油化工脱硫方法

石油化工脱硫方法随着环保和市场对石化产品中硫含量要求越来越苛刻,石油化工中硫化物脱除,尤其是较难脱除的有机硫化物脱除方法已成为各石化企业和研究者关注的热点。
本文就近年来有机硫化物脱除方法的研究进展进行综述,介绍了加氢转化、生物脱除技术、超生婆脱硫、沸石脱硫、液相吸附脱硫、离子液脱硫等,展望了有机硫脱除技术发展远景。
关键词:有机硫;脱除;石油化工随着世界范围环保要求日益严格,人们对石油产品质量要求也越来越苛刻,尤其是对燃烧后形成SO2、SO3继而与大气中水结合形成酸雾、酸雨严重影响生态环境和人们日常生活的硫化物含量限制。
世界各国对燃油中的硫提出了越来越严格的限制,以汽油为例,2005年欧美要求含硫质量分数降低到30×10-6~50×10-6,至2006年,欧洲、德国、日本、美国等国家和地区要求汽油中硫含量低于10~50µg/g,甚至提出生产含硫质量分数为5×10-6~10×10-6的“无硫汽油;”自2005年起,我国供应北京、上海的汽油招待相当于欧洲Ⅲ排放标准的汽油规格,即含硫质量分数低于150×10-6。
为了满足人们对石油产品高质量的要求和维护生产安全稳定进行,石油化工各生产企业不断改进生产过程中的脱硫工气。
石油化工生产过程中涉及到的硫化物可分为无机硫化物和有机硫化物,无机硫化物较容易脱除,本文就比较难脱除的有机硫脱除技术新进展进行综述。
1 加氢转化脱硫天然气、液化气、炼厂气、石脑油及重油中常含有二硫化碳、硫醇、硫醚、羰基硫和噻吩等有机硫化物,热分解温度较高,且不易脱除。
加氢转化脱硫技术是最有效的脱除手段之一。
有机硫在加氢转化催化剂作用下加氢分解生成硫化氢(H2S)和相应的烷烃或芳烃,生成的H2S可由氧化锌等脱硫剂脱除达到很好的脱除效果。
近年来,国外开发出几种典型的催化裂化(FCC)汽油脱硫新工艺,如ExxonMobil公司的SCANFining工艺和OCTGAIN工艺、LFP公司的Prime-G+工艺和UOP公司的ISAL工艺;在中内,中国石化抚顺石油化工研究院(FRIPP)针对我国FCC汽油的不同特点,开发出了OCT-M、FRS和催化裂化(FCC)汽油加氢脱硫/降烯烃技术并在国内石化企业得到成功应用;还开发了FH-DS柴油深度加氢脱硫催化剂,成功应用于福建炼油化工有限公司柴油加氢装置[1,2],此外洛阳石油化工工程公司工程研究院开发出催化裂化汽油加氢脱硫及芳构化工气技术Hydro-GAP[3]。
原油脱硫的原理

原油脱硫的原理原油脱硫是指通过一系列化学和物理处理方法,将原油中的硫化物去除的过程。
硫化物是原油中的一种不纯物质,它们对环境和人体健康都具有一定的危害性。
因此,对原油进行脱硫处理可以降低燃料和石油产品中硫化物的含量,减少对环境和人体的污染。
原油脱硫的主要原理是利用不同化学反应和物理分离方法来去除硫化物。
下面将详细介绍一些常用的原油脱硫原理及相应的工艺。
1. 催化剂脱硫催化剂脱硫是一种常用的原油脱硫技术。
该技术利用催化剂在一定温度和压力下加速硫化物的化学反应,将其转化为较为稳定的无机物质。
常用的脱硫催化剂有氧化铝、氧化锌等。
催化剂脱硫的过程包括催化剂的选择与制备、反应条件的优化以及催化剂的再生。
催化剂的选择主要考虑其活性和稳定性,优化反应条件包括温度、压力和粒度等,以提高反应的效率和选择性。
而催化剂的再生则是指通过热解、蒸汽氧化等方法将饱和的催化剂中的残留硫化物还原为较为活性的状态,以保证催化剂的持续使用。
2. 溶剂抽提脱硫溶剂抽提脱硫是一种采用有机溶剂将硫化物从原油中萃取出的方法。
该技术适用于硫化物与溶剂之间的选择性较差而硫化物与原油之间的选择性较好的情况。
溶剂抽提脱硫的过程包括溶剂的选择、萃取工艺的确定以及溶剂的再生。
溶剂的选择主要考虑其溶解度、萃取性能以及经济性等因素。
确定萃取工艺则是考虑溶剂与原油的相容性、溶剂的浓度、温度和压力等参数。
而溶剂的再生则包括对含硫萃取物的蒸馏、洗涤和蒸发等步骤,以回收溶剂和清除硫化物。
3. 水洗脱硫水洗脱硫是一种常用的原油脱硫技术,其原理是利用水与硫化物的亲和性将硫化物从原油中洗出。
水洗脱硫适用于含硫油中硫化物饱和度较低且硫化物与水之间的亲和性较强的情况。
水洗脱硫的过程主要包括水与原油的混合、分离和再生。
混合过程中通过搅拌或喷淋等方式将水与原油充分接触,使硫化物溶解在水中。
而分离过程则通过重力沉淀、离心分离和分析等手段将含硫水与原油分离。
再生过程则通常采用气体吹扫或蒸发浓缩等方法将含硫水中的硫化物还原为元素硫,以实现水的再利用。
石油炼制废气净化改造及脱硫脱硝工程技术方案

石油炼制废气净化改造及脱硫脱硝工程技术方案介绍本文档旨在提供一种对石油炼制废气进行净化改造以及脱硫脱硝的工程技术方案。
通过采用简单且无法引起法律风险的策略,我们将重点解决废气处理中的主要问题,并提出相应的解决方案。
废气净化改造方案废气净化改造是为了减少石油炼制过程中产生的有害气体排放。
我们建议采用以下几个步骤来实施废气净化改造:1. 废气监测与分析:首先,对石油炼制过程中产生的废气进行监测和分析,以确定主要的污染物和排放浓度。
废气监测与分析:首先,对石油炼制过程中产生的废气进行监测和分析,以确定主要的污染物和排放浓度。
2. 废气收集与处理:将废气有效地收集起来,并通过适当的处理设备进行处理,如采用活性炭吸附、湿式洗涤等方法来去除有害物质。
废气收集与处理:将废气有效地收集起来,并通过适当的处理设备进行处理,如采用活性炭吸附、湿式洗涤等方法来去除有害物质。
3. 废气排放监控:在废气净化改造后,建立废气排放监控系统,以确保排放符合相关的环境标准和法规要求。
废气排放监控:在废气净化改造后,建立废气排放监控系统,以确保排放符合相关的环境标准和法规要求。
脱硫脱硝工程技术方案脱硫和脱硝是减少石油炼制废气中二氧化硫和氮氧化物排放的重要措施。
以下是我们的工程技术方案:1. 脱硫工艺选择:根据炼厂的具体情况,选择适合的脱硫工艺,如湿法脱硫或干法脱硫,并确保该工艺符合环境标准。
脱硫工艺选择:根据炼厂的具体情况,选择适合的脱硫工艺,如湿法脱硫或干法脱硫,并确保该工艺符合环境标准。
2. 脱硝工艺选择:针对石油炼制废气中的氮氧化物排放,选择适当的脱硝工艺,如选择选择选择选择选择选择,以降低氮氧化物的排放浓度。
脱硝工艺选择:针对石油炼制废气中的氮氧化物排放,选择适当的脱硝工艺,如选择选择选择选择选择选择,以降低氮氧化物的排放浓度。
3. 脱硫脱硝设备安装与调试:安装并调试脱硫脱硝设备,确保其正常运行并达到预期的脱硫脱硝效果。
脱硫脱硝设备安装与调试:安装并调试脱硫脱硝设备,确保其正常运行并达到预期的脱硫脱硝效果。
石油脱硫知识点

石油脱硫知识点石油脱硫是指通过一系列化学和物理方法去除石油中的硫化物,以降低石油中的硫含量。
这是一项重要的工艺,因为硫在燃烧过程中会产生污染物,如二氧化硫,对环境和人类健康有害。
下面将介绍石油脱硫的一些基本知识点。
1.脱硫方法:石油脱硫的主要方法包括物理吸附、化学吸收和催化脱硫。
物理吸附是通过吸附剂将硫化物吸附到其表面,例如使用活性炭进行脱硫。
化学吸收是通过溶剂将硫化物溶解,如使用苯胺溶液进行脱硫。
催化脱硫是通过催化剂催化硫化物的反应,例如使用氢气和催化剂进行脱硫。
2.常见脱硫剂:常见的物理吸附脱硫剂包括活性炭、沸石等。
化学吸收脱硫剂包括苯胺、二乙胺等。
催化脱硫剂包括氢气和不同的催化剂,如钴钼催化剂、镍钼催化剂等。
3.脱硫工艺流程:石油脱硫的工艺流程通常包括前处理、主处理和后处理三个步骤。
前处理主要是通过沉淀、过滤等方法去除石油中的固体杂质。
主处理是将石油与脱硫剂接触,去除其中的硫化物。
后处理则是对脱硫后的产物进行处理,如去除脱硫剂残留物等。
4.脱硫效率:脱硫效率是评价脱硫工艺性能的重要指标,它表示脱硫后石油中硫的含量。
脱硫效率越高,表示脱硫工艺越好。
脱硫效率可以通过实验室测试或工业生产中的监测来确定。
5.脱硫催化剂的选择:选择合适的催化剂对于脱硫工艺的成功至关重要。
催化剂的选择应考虑催化剂的活性、稳定性、成本等因素。
不同的石油组分可能需要不同的催化剂,因此在选择催化剂时需要考虑到石油的特性。
6.脱硫工艺的优化:为了提高脱硫效率和降低成本,脱硫工艺经常需要进行优化。
优化的目标包括提高脱硫效率、降低能耗、减少催化剂的消耗等。
通过调整操作条件、改进催化剂、优化催化剂的使用等方式可以实现脱硫工艺的优化。
总结:石油脱硫是一项重要的工艺,可以降低石油中的硫含量,减少环境污染。
脱硫方法包括物理吸附、化学吸收和催化脱硫。
选择合适的脱硫剂和催化剂,并优化脱硫工艺,可以提高脱硫效率和降低成本。
这些知识点对于理解石油脱硫工艺的原理和应用具有重要意义。
石油脱硫工艺流程

石油脱硫工艺流程一、前言石油是一种重要的能源资源,但其含有的硫化物会对环境和人体健康造成危害,因此需要进行脱硫处理。
本文将介绍石油脱硫的工艺流程。
二、石油脱硫的原理石油中含有硫化物,主要为硫酸盐、有机硫和元素硫等。
脱除这些硫化物的方法主要有吸收法、催化氧化法和生物降解法等。
其中,吸收法是最常用的方法。
吸收法是指将含有硫化物的石油与一种具有亲硫性质的溶液接触,使得溶液中的亲硫剂与石油中的硫化物发生反应,形成可溶性或不可溶性产物,并从中分离出含有亲硫剂和产物的混合物。
常用亲硫剂包括三氧化钼、三氧化铬、二氧化钛等。
三、工艺流程1. 前处理石油在进行脱硫前需要进行前处理,以去除其中的杂质和水分。
该步骤通常包括以下几个步骤:(1)沉淀:将石油放置一段时间,使其中的杂质和水分沉淀到底部。
(2)过滤:将沉淀后的石油通过滤网过滤,去除其中的杂质。
(3)脱水:将过滤后的石油通过加热或其他方法脱去其中的水分。
2. 吸收吸收是脱硫工艺中最关键的步骤,其主要流程包括以下几个步骤:(1)选择亲硫剂:根据不同石油中硫化物含量和种类的不同,选择适合的亲硫剂。
(2)溶液制备:将亲硫剂与溶剂按一定比例混合,并加入少量助剂,制成吸收剂。
(3)接触反应:将含有硫化物的石油与吸收剂进行接触反应,使得硫化物与亲硫剂发生反应,并形成可溶性或不可溶性产物。
(4)分离产物:对接触反应后得到的混合物进行分离处理,以得到含有亲硫剂和产物的两个单独体系。
3. 再生再生是指对已经用过并且失去活性的吸收剂进行再生处理,以使其重新获得活性。
常用的再生方法包括以下几种:(1)加热再生:将失活的吸收剂加热至一定温度,使得其中的产物发生分解反应,从而使亲硫剂重新获得活性。
(2)洗涤再生:将失活的吸收剂放入洗涤槽中,并用洗涤液进行冲洗,以去除其中的产物和杂质。
(3)气体再生:将失活的吸收剂放入反应器中,并通过注入气体等方式进行再生处理。
4. 产品处理经过以上步骤后,最终得到含有较少硫化物的石油产品。
石油脱硫知识点总结

石油脱硫知识点总结石油脱硫技术是一项非常复杂的工程,涉及物理、化学、工程等多个领域的知识。
为了全面了解石油脱硫技术,下面将从原理、方法、工艺流程、应用等多个方面进行详细介绍。
一、石油脱硫的原理石油脱硫的原理主要是依靠物理或化学手段来去除石油中的硫化物。
根据原理的不同,石油脱硫可以分为热解脱硫、溶剂抽提脱硫、氧化脱硫等多种方法。
1. 热解脱硫热解脱硫是一种物理方法,利用热能将硫化物分解出来。
石油中的硫化物在高温条件下会分解成硫磺和其他化合物,然后通过冷凝和分离的方法将硫磺去除。
这种方法通常适用于高温炼油过程中,需要配合其他设备一起使用。
2. 溶剂抽提脱硫溶剂抽提脱硫是一种化学方法,通过在石油中加入特定的溶剂,将硫化物吸附到溶剂中,然后把溶剂与硫化物分离出来。
这种方法相对比较温和,不会对石油本身产生太大的影响。
3. 氧化脱硫氧化脱硫是一种常用的脱硫方法,通过加入氧化剂将硫化物氧化成易于分离的物质。
常用的氧化剂包括过氧化物、双氧水等,可以选择适当的氧化剂根据硫化物的特性来进行脱硫。
以上这些原理只是石油脱硫的几种方法,实际应用中需要根据石油的成分、硫化物的类型和含量等多方面考虑,选择合适的脱硫方法。
二、石油脱硫的方法根据不同的原理,石油脱硫的方法也多种多样,主要包括物理方法、化学方法和生物方法等。
1. 物理方法物理方法是指利用物理性质来进行脱硫,如温度、压力、相态等。
常见的物理方法包括蒸馏、吸附、结晶等。
蒸馏是一种通过升高温度将硫化物分离出来的方法,常用于高温精制过程中。
吸附是一种利用吸附剂将硫化物吸附出来的方法,常用于溶剂抽提脱硫。
结晶是一种通过溶剂的相变来将硫化物从石油中分离出来的方法,也是一种常见的物理方法。
2. 化学方法化学方法是指利用化学反应来进行脱硫,如氧化、还原、配位等。
常见的化学方法包括氧化脱硫、还原脱硫、络合脱硫等。
氧化脱硫是通过加入氧化剂将硫化物氧化成易于分离的物质,如过氧化物、双氧水等。
石油化工中的脱硫脱硝技术

石油化工中的脱硫脱硝技术石油化工行业是世界上最重要的工业部门之一,然而,其生产过程会产生大量的二氧化硫(SO2)和氮氧化物(NOx),这些气体对环境和人类健康造成严重威胁。
因此,在石油化工过程中,脱硫脱硝技术的应用变得非常重要。
本文将讨论石油化工中常见的脱硫脱硝技术及其应用。
一、脱硫技术1. 燃烧方式脱硫燃烧方式脱硫是一种常见的脱硫技术,在石油化工中广泛应用。
该技术通过在燃烧过程中添加脱硫剂,如石灰石、石膏等,来降低燃料中的硫含量。
在燃烧过程中,硫与脱硫剂发生化学反应,生成无害的硫酸钙(CaSO4)沉淀物。
这种方法既可以减少SO2的排放,又可以回收硫。
2. 湿法烟气脱硫湿法烟气脱硫是一种高效脱硫技术,其原理是通过将烟气与含有碱金属离子的吸收剂接触,将SO2吸收到吸收剂中。
常用的吸收剂包括氢氧化钙(Ca(OH)2)和氨水(NH3)。
其中,氨水法是目前最常用的湿法脱硫技术,具有高效、灵活性强等优点。
3. 干法烟气脱硫干法烟气脱硫是一种将石灰石作为脱硫剂进行固定床吸收的技术。
通过将烟气与石灰石直接接触,SO2会与石灰石中的氧化钙(CaO)发生化学反应,生成无害的硫酸钙。
该技术可以同时去除烟气中的SO2和微粒物质。
二、脱硝技术1. 选择性催化还原(SCR)选择性催化还原(SCR)是一种常用的脱硝技术,通过在合适的温度下将氨(NH3)或尿素(CO(NH2)2)注入烟气中,通过催化剂的作用将NOx转化为无害的氮气(N2)和水(H2O)。
SCR技术具有高效、能耗低、适应性强等优点,已广泛应用于石油化工中。
2. 活性炭吸附法活性炭吸附法是一种将烟气中的NOx吸附到活性炭表面的方法。
这种技术通过在活性炭上形成一层氮氧化物吸附剂,使NOx在表面被吸附并转化为无害物质。
活性炭吸附法具有操作简单、投资成本低和损耗小等优点。
3. SDNR技术SDNR(Selective Direct Noncatalytic Reduction)技术是一种新型的非催化还原技术,其原理是通过在烟气中注入适量的还原剂(如氨或尿素)来直接还原NOx为N2和H2O。
石油炼化企业烟气脱硫技术研究综述
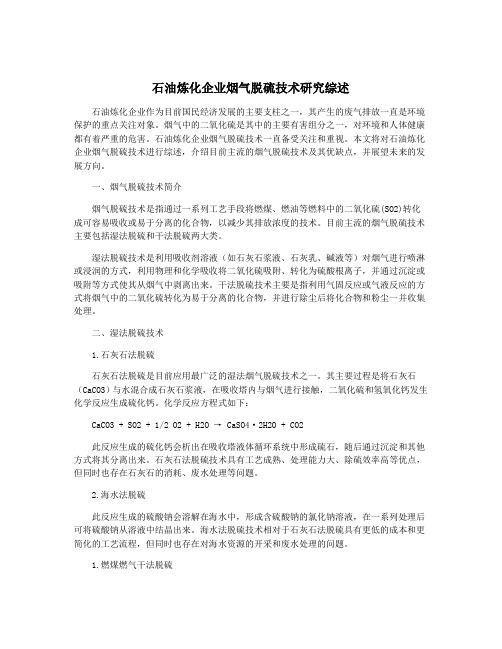
石油炼化企业烟气脱硫技术研究综述石油炼化企业作为目前国民经济发展的主要支柱之一,其产生的废气排放一直是环境保护的重点关注对象。
烟气中的二氧化硫是其中的主要有害组分之一,对环境和人体健康都有着严重的危害。
石油炼化企业烟气脱硫技术一直备受关注和重视。
本文将对石油炼化企业烟气脱硫技术进行综述,介绍目前主流的烟气脱硫技术及其优缺点,并展望未来的发展方向。
一、烟气脱硫技术简介烟气脱硫技术是指通过一系列工艺手段将燃煤、燃油等燃料中的二氧化硫(SO2)转化成可容易吸收或易于分离的化合物,以减少其排放浓度的技术。
目前主流的烟气脱硫技术主要包括湿法脱硫和干法脱硫两大类。
湿法脱硫技术是利用吸收剂溶液(如石灰石浆液、石灰乳、碱液等)对烟气进行喷淋或浸润的方式,利用物理和化学吸收将二氧化硫吸附、转化为硫酸根离子,并通过沉淀或吸附等方式使其从烟气中剥离出来。
干法脱硫技术主要是指利用气固反应或气液反应的方式将烟气中的二氧化硫转化为易于分离的化合物,并进行除尘后将化合物和粉尘一并收集处理。
二、湿法脱硫技术1.石灰石法脱硫石灰石法脱硫是目前应用最广泛的湿法烟气脱硫技术之一。
其主要过程是将石灰石(CaCO3)与水混合成石灰石浆液,在吸收塔内与烟气进行接触,二氧化硫和氢氧化钙发生化学反应生成硫化钙。
化学反应方程式如下:CaCO3 + SO2 + 1/2 O2 + H2O → CaSO4·2H2O + CO2此反应生成的硫化钙会析出在吸收塔液体循环系统中形成硫石,随后通过沉淀和其他方式将其分离出来。
石灰石法脱硫技术具有工艺成熟、处理能力大、除硫效率高等优点,但同时也存在石灰石的消耗、废水处理等问题。
2.海水法脱硫此反应生成的硫酸钠会溶解在海水中,形成含硫酸钠的氯化钠溶液,在一系列处理后可将硫酸钠从溶液中结晶出来。
海水法脱硫技术相对于石灰石法脱硫具有更低的成本和更简化的工艺流程,但同时也存在对海水资源的开采和废水处理的问题。
石油化工脱硫方法

石油化工脱硫方法随着环保和市场对石化产品中硫含量要求越来越苛刻,石油化工中硫化物脱除,尤其是较难脱除的有机硫化物脱除方法已成为各石化企业和研究者关注的热点。
本文就近年来有机硫化物脱除方法的研究进展进行综述,介绍了加氢转化、生物脱除技术、超生婆脱硫、沸石脱硫、液相吸附脱硫、离子液脱硫等,展望了有机硫脱除技术发展远景。
关键词:有机硫;脱除;石油化工随着世界范围环保要求日益严格,人们对石油产品质量要求也越来越苛刻,尤其是对燃烧后形成SO2、SO3继而与大气中水结合形成酸雾、酸雨严重影响生态环境和人们日常生活的硫化物含量限制。
世界各国对燃油中的硫提出了越来越严格的限制,以汽油为例,2005年欧美要求含硫质量分数降低到30×10-6~50×10-6,至2006年,欧洲、德国、日本、美国等国家和地区要求汽油中硫含量低于10~50µg/g,甚至提出生产含硫质量分数为5×10-6~10×10-6的“无硫汽油;”自2005年起,我国供应北京、上海的汽油招待相当于欧洲Ⅲ排放标准的汽油规格,即含硫质量分数低于150×10-6。
为了满足人们对石油产品高质量的要求和维护生产安全稳定进行,石油化工各生产企业不断改进生产过程中的脱硫工气。
石油化工生产过程中涉及到的硫化物可分为无机硫化物和有机硫化物,无机硫化物较容易脱除,本文就比较难脱除的有机硫脱除技术新进展进行综述。
1 加氢转化脱硫天然气、液化气、炼厂气、石脑油及重油中常含有二硫化碳、硫醇、硫醚、羰基硫和噻吩等有机硫化物,热分解温度较高,且不易脱除。
加氢转化脱硫技术是最有效的脱除手段之一。
有机硫在加氢转化催化剂作用下加氢分解生成硫化氢(H2S)和相应的烷烃或芳烃,生成的H2S可由氧化锌等脱硫剂脱除达到很好的脱除效果。
近年来,国外开发出几种典型的催化裂化(FCC)汽油脱硫新工艺,如ExxonMobil公司的SCANFining工艺和OCTGAIN工艺、LFP公司的Prime-G+工艺和UOP公司的ISAL工艺;在中内,中国石化抚顺石油化工研究院(FRIPP)针对我国FCC汽油的不同特点,开发出了OCT-M、FRS和催化裂化(FCC)汽油加氢脱硫/降烯烃技术并在国内石化企业得到成功应用;还开发了FH-DS柴油深度加氢脱硫催化剂,成功应用于福建炼油化工有限公司柴油加氢装置[1,2],此外洛阳石油化工工程公司工程研究院开发出催化裂化汽油加氢脱硫及芳构化工气技术Hydro-GAP[3]。
石油焦脱硫技术
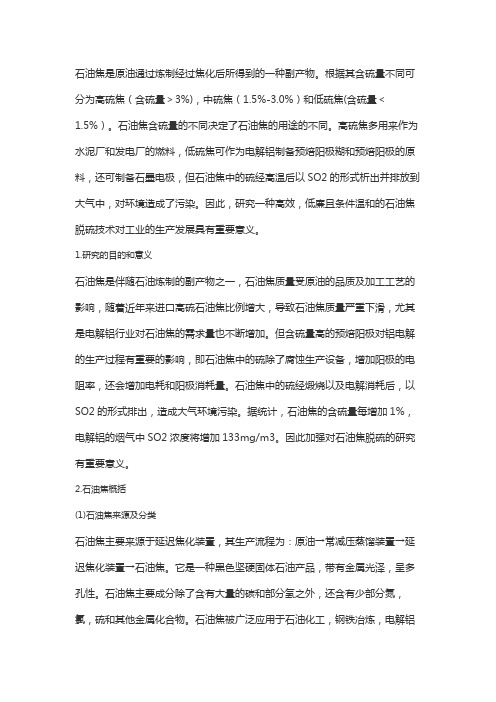
石油焦是原油通过炼制经过焦化后所得到的一种副产物。
根据其含硫量不同可分为高硫焦(含硫量>3%),中硫焦(1.5%-3.0%)和低硫焦(含硫量<1.5%)。
石油焦含硫量的不同决定了石油焦的用途的不同。
高硫焦多用来作为水泥厂和发电厂的燃料,低硫焦可作为电解铝制备预焙阳极糊和预焙阳极的原料,还可制备石墨电极,但石油焦中的硫经高温后以SO2的形式析出并排放到大气中,对环境造成了污染。
因此,研究一种高效,低廉且条件温和的石油焦脱硫技术对工业的生产发展具有重要意义。
1.研究的目的和意义石油焦是伴随石油炼制的副产物之一,石油焦质量受原油的品质及加工工艺的影响,随着近年来进口高硫石油焦比例增大,导致石油焦质量严重下滑,尤其是电解铝行业对石油焦的需求量也不断增加。
但含硫量高的预焙阳极对铝电解的生产过程有重要的影响,即石油焦中的硫除了腐蚀生产设备,增加阳极的电阻率,还会增加电耗和阳极消耗量。
石油焦中的硫经煅烧以及电解消耗后,以SO2的形式排出,造成大气环境污染。
据统计,石油焦的含硫量每增加1%,电解铝的烟气中SO2浓度将增加133mg/m3。
因此加强对石油焦脱硫的研究有重要意义。
2.石油焦概括(1)石油焦来源及分类石油焦主要来源于延迟焦化装置,其生产流程为:原油→常减压蒸馏装置→延迟焦化装置→石油焦。
它是一种黑色坚硬固体石油产品,带有金属光泽,呈多孔性。
石油焦主要成分除了含有大量的碳和部分氢之外,还含有少部分氮,氯,硫和其他金属化合物。
石油焦被广泛应用于石油化工,钢铁冶炼,电解铝等各个领域。
根据石油焦的结构和外观,石油焦又可被分为针状焦,海绵焦,弹丸焦和粉焦。
(2)石油焦现状和发展趋势近年来我国石油焦的产量不断增加。
截至2019年末,国内石油焦总产量高达2766.75万吨,同比增长了2.47%。
由于工业上对石油焦的需求量大幅度上升,我国每年生产的石油焦供不应求,每年都需进口大量的石油焦。
进口的石油焦大部分是高硫焦,燃烧后危害较多。
石油脱硫技术的进展研究

定根 据 , 以更好 地发展石油脱硫 技术 。 关键词 : 加氢 脱硫 非加氢脱 硫 生物 脱硫技术
1 引 言
2 1 1 复合氧化物载体 ..
众所周 知 , 石油 中的硫 化物 不仅使 石 油品 质变 坏 , 而且对炼 厂设 备有 严重 腐 蚀作 用 。因此 , 油 炼制 过 石 程 中的脱硫 问题 已成为石油化 工行业 的 主要技 术攻 关 课题 , 近年来 , 世界 各 国对 环保 要 求 日益 提高 , 国从 我
实现 深度加氢脱硫 , 中无定形 硅酸铝 ( S )、 其 AA 分子 筛 和新 型 介孔 材 料 作 为载 体 备受 关 注.章 健 等利 用 S M、 :一 物理吸 附和联 碱滴定 法等 表征手 段系统 比 E N 较 了竹 质活性炭 和普 通竹炭与其他 材质 活性炭在 物化
2 石 油加氢脱硫技术的论述 当前 , 深度加 氢脱硫 或 超深 度加 氢脱 硫 的 主要 问 题是催化剂 的开发 问题 。迄 今对催 化剂 的主 活性 组分 和金属助剂 的 比例 、 体 制备 、 化剂 制备 方 法 、 载 催 干燥
研究价值 。
现在 , 一个是 未来 。我们 以科 学发 展 观 的思 想进 行科
学研究 , 当立足 当前 , 放眼未来 。在现 在石脱 硫技
术。
2 13 酸性载体及炭载体 .. 酸性载 体较 大 的 比表 面积及 较 高的 有序 度 , 够 能
在 单一 的氧化 物载体 中最传 统的 当是 A: ,特别 IO ,
是在石 油化工和环境保 护领域 , 有报道说 明, 也 现在 的
A , 体已经无 法满 足当前工业 的催化 剂的要求 , hO 载 同
时 , 二十年来人 们 已经 不 断 的研究 和开 发 出多 种新 近
原油脱硫剂

原油脱硫剂简介原油脱硫剂是一种广泛用于工业领域的化学物质,用于去除原油中的硫化物。
硫化物是一种常见的污染物,对环境和人类健康带来威胁。
原油脱硫剂通过特定的化学反应,将硫化物转化为无害物质,从而降低原油中的硫含量。
工作原理原油脱硫剂的工作原理基于化学反应。
主要有以下几个步骤:1.吸附:原油脱硫剂吸附硫化物分子到其表面。
2.反应:吸附在原油脱硫剂上的硫化物分子与原油脱硫剂中的活性基团发生反应,形成新的化合物。
3.脱附:脱硫剂上形成的新化合物分离出来,原油中的硫化物被转化为无害物质。
原油脱硫剂通常是特制的化学配方,具有高效去除硫化物的能力。
它们可以根据原油中的硫含量和其他条件进行调整,以达到最佳的脱硫效果。
应用领域原油脱硫剂主要用于石油炼制和天然气加工过程中。
以下是一些常见的应用领域:炼油厂炼油厂是主要的原油脱硫剂使用地点之一。
原油中的硫化物会对炼油过程中的催化剂和设备产生腐蚀作用,降低炼油效率。
通过使用原油脱硫剂,可以降低原油中的硫含量,减少对催化剂的腐蚀,提高炼油效率。
石油储运石油储运过程中,原油中的硫化物会与金属管道和设备中的水分反应,形成腐蚀性物质,从而对管道和设备造成损坏。
使用原油脱硫剂可以去除原油中的硫化物,减少对管道和设备的腐蚀,延长其使用寿命。
天然气加工天然气中的硫化物会对天然气加工设备产生腐蚀作用,并在存储和运输过程中产生硫化氢气体,对环境和人类健康造成威胁。
原油脱硫剂可以用于去除天然气中的硫化物,减少对设备和环境的腐蚀,提高天然气的质量。
使用注意事项在使用原油脱硫剂时,需要注意以下几点:1.安全操作:原油脱硫剂可能会对人体产生刺激性和有害性。
在使用时,应佩戴适当的防护设备,避免直接接触皮肤和眼睛。
2.使用指导:根据不同的应用领域和硫含量,使用合适的原油脱硫剂型号和用量。
遵循生产商提供的使用指南和安全操作手册。
3.废物处理:处理用过的原油脱硫剂和产生的废物时,需遵循相关法规和规定。
通常废物需交由专业机构进行处理。
- 1、下载文档前请自行甄别文档内容的完整性,平台不提供额外的编辑、内容补充、找答案等附加服务。
- 2、"仅部分预览"的文档,不可在线预览部分如存在完整性等问题,可反馈申请退款(可完整预览的文档不适用该条件!)。
- 3、如文档侵犯您的权益,请联系客服反馈,我们会尽快为您处理(人工客服工作时间:9:00-18:30)。
石油生物催化脱硫石油及其产品的燃烧产生大量的有毒气体SO2进入大气,造成严重的空气污染,同时也是产生酸雨的主要原因,因此需要对含硫量高的石油燃料进行脱硫处理。
化学脱硫方法——加氢脱硫(hydrodesulfurization HDS)法通过催化过程将有机硫化物转化成H2S气体,反应在高温高压下进行,费用较高,而且难以脱除石油燃料中的噻吩类物质,而生物催化脱硫(biodesulfurization BDS)在常温常压就可以进行,并且具有高度专一性,因此发展石油生物催化脱硫方法是十分必要的。
由于世界范围内可开发的低硫原油日益减少,人们不得不重视对高硫石油的利用。
因此对石油中含硫化合物的化学分析也随之越来越被重视起来。
石油中的硫是以有机硫和无机硫两种形式存在的,其中主要是有机硫,也存在少量元素硫、H2S、FeS等溶解或悬浮在油中。
有人对4 种不同产地的原油进行了化学分析,分离出13 类包括176 种不同化学结构的有机硫化合物,如图1-1。
原油中的硫醇大部分是低分子量,在石油的炼制过程中易被除去,200℃以上沸点的石油产品中几乎很少存在。
脂肪族硫化物是沸点200℃以上石油产品如柴油中硫化物的主要成分,芳香族硫化物在较重的馏分中含量较低。
虽然喳吩在原油中很少见,但唾吩的衍生物很多,苯唾吩、二苯唆吩、蔡唾吩是高硫原油的重要组成。
而且这些含硫化合物在原油加工过程中不同程度地分布于各馏分油中。
在流化床催化裂化(Fluldeaatlyti。
arkce,Fcc)汽油中,唆吩和各种取代唆吩是主要的含硫化合物,其中苯并唾吩(BeZnohtiophene,BTH)占30%。
催化柴油馏分中的含硫化合物主要是BHT和二苯并唆吩(Dibenzothi0Phene,DBT)及各种烷基取代物。
随着唾吩类含硫化合物的环数的增加,多环唾吩因空间位阻效应使加氢脱硫催化剂反应活性迅速降低。
从炼油角度来看,非活性硫的化合物一般比活性硫的化合物更难脱除,而原油中的硫大部分都是以硫醚类和噻吩类硫的形态存在于沸点较高的石油馏分中,这是含硫原油加工过程中所面临的主要问题。
1石油脱硫技术概述碱洗法长期以来,炼油厂大多采用碱洗的办法来去除原油中的硫化物,这一方法较为简单,通过碱洗,可以除去原油中的绝大部分硫化物,但它却产生大量的含硫废水,如果不加以妥善处理,对环境的危害是相当严重的。
此外,由于碱洗对有机硫化物的脱除率不高,致使成品油中还含有不同程度的有机硫化物,如果不进一步对成品油进行精制处理,会严重的影响成品油的使用价值。
萃取法成品油中的有机硫化物可通过萃取法来去除,常用的萃取剂是碱液,但有机硫化物在碱液和成品油中的分配系数并不高,为了提高萃取效率,可在碱液中加入极性有机溶剂,如DMF、DMSOD等,这样可以大大提高萃取的脱硫效率[1]。
夏道宏、苏贻勋[2]等提出了MDS-H2O -KOH 化学萃取法。
用 3 种萃取剂对胜利炼油厂催化裂化(FCC)汽油进行萃取率及回收率的考察。
结果表明,该方法既能将油品中的硫醇萃取出来,达到脱硫目的,又可高效回收萃取液中的单一硫醇以及混合硫醇,得到硫醇浓缩液。
在同一套脱硫装置中既可高效脱硫又可得到高纯度的硫醇副产品,增加炼厂经济效益和社会效益。
福建炼油化工公司[3]把萃取与碱洗两种工艺结合起来,采用甲醇-碱洗复合溶剂萃取法显著提高了催化裂化(FCC)柴油的储存安定性,色度由18 号降到8 号,萃取溶剂经蒸馏回收甲醇后可循环使用。
此方法投资不高,脱硫效率较高,对一般炼油厂是可行的。
1.3 络合法用金属氯化物的DMF溶液处理含硫的石油产品[4],可使有机硫化物与金属氯化物作用,生成水溶性的络合物而加以去除。
能与有机硫化物生成络合物的金属离子很多,而其中以CdCl2的效果最佳,但由于Cd2+的毒性较大,也可用CoCl2或NiCl2来代替。
不同金属氯化物与有机硫化物的络合反应活性依次为[5]:Cd2+>Co2+>Ni2+>Mn2+>Cr3+>Cu2+>Zn2+>Li+>Fe3+。
络合法脱硫无法脱除油品中的酸性组分,而剩余的氮化物、硫化物可在酸性物质的催化作用下聚合、氧化。
因此工业上采用络合萃取与碱洗精制相结合的办法,可使油品的安定性最好。
在经济上,与萃取法同样具有较好经济效益。
1.4 吸附法Konyukhova T. P.[6]把一些天然沸石(如丝光沸石、钙十字石、斜发沸石等)经酸性活化后,可用于吸附去除成品油中的乙基硫醇和二甲基硫,而ZSM-5和NaX沸石则分别适用于对硫醚和硫醇的去除。
徐志达、陈冰[7]等用聚丙烯腈基活性炭纤维(NACF)吸附汽油中的硫醇,但只能把汽油中一部分硫醇脱除,不能把硫醇硫的含量降到10 g/g以下。
吸附法脱硫效率不高,而且若吸附剂上吸附了胶质等物质,其脱硫效率更低,所以大多炼油厂不采用此种方法。
1.5 催化法催化法去除有机硫化合物的方法主要有以下三种:(1)用沉积在碳纤维或石墨纤维上的酞菁催化剂,在碱性水溶液中对石油馏分进行氧化处理,可以去除其中的硫醇[8]。
在这一体系中,如果不加碱性溶液,而改用碱性多孔性固体催化剂[9](由碱性硅酸铝、活性碳、金属螯合剂、有机或矿物粘合剂等物质组成),也能有效地去除成品油中的有机硫化物。
(2)用一个固体碱固定床和一个载体于非碱性固体上的金属螯合剂组成的处理系统[10]对含硫成品油进行处理,在处理时,使含有硫醇且酸性中等的烃类馏分首先与固体碱接触,然后在氧气和极性化合物的存在下,硫醇与载体上的金属螯合剂接触,发生催化氧化反应,可有效地去除成品油中的有机硫化物。
(3)在没有外加氢的条件下,含硫成品油与酸性催化剂(ZSM系列、MCM系列、沸石Y 、沸石及其混合物)在流动床中接触,可使有机硫化物转化为H2S,从而可以较容易地从成品油中去除硫化物[10]。
1.6加氢脱硫(hydrodesulfurization,HDS)图1-2 苯并噻吩的HDS反应机理(Cat=催化剂)图1-3 二苯并噻吩的HDS反应机理(Cat=催化剂)加氢脱硫从广义上讲也是催化脱硫的方法之一,它是在金属催化剂的作用下,进行高温高压并加氢的脱硫处理,将有机硫化合物转化为硫化氢(H2S),再从系统中分离出来的方法。
该方法已在工业生产中得到普遍的应用。
但是,这种方法本身也存在许多的问题:(1)加氢脱硫反应的操作温度通常为270~420℃,较高的操作温度可降低产品中的硫含量,但是会缩短催化剂寿命,提高成本费用。
(2)加氢脱硫的操作压力为(以下均为表压)2.0~3.45MPa,粗柴油为2.8~12.4MPa:而对重组分如渣油,操作压力需要高达20.7MPa。
加氢脱硫的程度随氢气分压的增加而增加,但当氢气分压超过10.3MPa后,压力变化对加氢脱硫反应速率的影响已不太明,而烷基类DBT化合物中芳环的加氢较为显著。
此外,裂解汽油反应生成的链烃也会发生加氢反应,链烃加氢不仅会降低FCC汽油的辛烷值,而且也增加了H2的消耗。
(3)这种方法对石油中某些含硫分子无影响,特别是对重组分中的聚芳烃硫杂环(PASHs)不起作用[11];(4)H2S存在会毒害脱硫系统的催化剂,使得高含硫石油的HDS变得复杂化;(5)H2S的排放会污染大气。
1.7 生物脱硫石油炼厂的废水、焦油污染的土壤里的硫化合物在自然条件下,其中的一部分会发生生物降解,这是自然界中存在着细菌的作用。
细菌脱硫(MDS)是在温和的条件下,利用适宜的细菌代谢过程使石油脱硫,在生化过程中,脱硫剂可以再生或自身补充。
这种脱硫操作中,有机硫分子的代谢仍要以烃作碳源,而不是选择性或专一性地代谢硫,有机硫化合物只是从非水溶性转变成水溶性,随后从石油中被分离出来,但有价值的烃也被部分地损失掉了。
MDS对诸如硫醇、硫醚等分子量较小的有机硫化合物较为有效。
对于带有硫杂环的芳香族化合物,据报导[12,13]迄今只有少数几个细菌菌株能够将其代谢为水溶性的化合物,如亚臭假单胞菌和P.alcaligens等,这样就大大地限制了MDS法的商业利用价值。
在细菌脱硫法基础上90年代国外迅速发展起来了石油的生物催化脱(Biodesulfurization,BDS)技术。
BDS技术是利用微生物所产生的酶催化特定的C-S断键反应,释放出可溶性硫,而留下碳氢化合物,也就是酶催化反应基本不破坏石油的骨架烃链。
BDS与HDS相比较,具有如下优点:(1)可在低温低压下操作;(2)成本较低BDS比HDS投资少50%、操作费用少10%~15%;(3)灵活性好,可用于处理各种油品,如原油、石脑油、中馏分油、FCC汽油、残渣燃料油等;(4)不需要氢气,节省能源,减少CO2排放量,对环境保护极为有利;(5)能有效脱除HDS装置难于处理的含硫杂环化合物,而这是传统的脱硫技术HDS很难解决。
因此,酶催化反应脱硫法是一种很有前途的脱硫方法。
2生物催化脱硫代谢途径2.1 以二苯并噻吩表征的生物脱硫代谢途径由于加氢脱硫难以除去二苯并噻吩(DBT)及其衍生物,而DBT又广泛存在于化石颜料中,所以生物脱硫多以DBT作为模型化合物来进行研究。
目前公认的BDS 脱硫的有效性是以二苯并噻吩(DBT)为模型化合物来表征的,并且搞清楚了它们的作用机制是由于微生物酶的作用,因此,对于酶脱硫路线,研究者进行了深入的研究确定了其脱硫路线,并且发现此路线与其它脱硫路线相比,最具有商业化应用价值。
酶脱硫路线主要有两种,一种是还原路线,另一种是氧化路线。
在还原路线脱硫过程中,有机硫被转化成H2S,然后进一步被氧化成为单质硫。
此过程由于没有氧的存在,可以防止烃类物质的氧化,减少油品热值的损失。
但是这种方法脱硫能力比较差,很难把它应用于工业化生产。
因此,常常采用氧化路线脱硫。
在氧化路线中其代谢途径有以下几种:(1)以碳代谢为中心的Kodama途径[14]如图2-1所示。
图2-1 Kodama 途径这一路线是在从土壤中分离出的假单胞菌(Pseudomonas)[15],拜叶林克氏菌(beijerinckia)[16]及不动杆菌(acintobacter)和根瘤菌(rhizobium)[17]的混合培养中发现的。
Kadama路线是在两相(油/水)生物反应器中通过酶选择性地DBT分子中的C-C键断裂而C-S键保留下来,脱去3个或4个碳的碎片,生成溶于水的小分子有机硫化合物,并不破坏含硫化合物基体。
由于是整个含硫化物转入水相,虽可从石油中分离出去,但也损失了有机烃,故油品的液体收率有所下降。
若油中含硫化合物以DBT计算,则其质量约为硫原子的5.3倍,即硫质量分数为0.2%的油品脱硫后收率约损失1.0%[18],因此,工业化价值小。
(2 )以硫代谢为中心的4S途径1989年Kilbane在研究IGTS8细菌脱除煤中有机硫时,从理论上提出了生物降解DBT的“4S”途径。