学习锻造技术的参考文献
从_锻造工艺过程及模具设计_教材看锻造工艺发展的新进展

主动 实际生产中去发现问题和解决问题, 而是积极、 引导学生从理论的高度去考察和分析问题。教材除 广泛吸收中外专家的理论论述以外,主要介绍富于 创造性的研究成果,例如净形和近似净形加工方面 的内容。 作者在科研和生产实践中总结出减少锻压负载 的一般规律: “在外在条件相同,金属流动情况也相 同的情况下, 比较两种锻造工艺, 如减少模具 (或工 具 ) 与坯料的接触面积, 负载一定减少” 。 教材中精密 模锻章在“减少精密模锻负载的工艺过程措施中强 调不仅分流面分流减压、预流补偿空间等是减少精 如图 密模锻负载的一种形式, 而且引用了不少例证。 3、 图 4 所示。图 5 的穿孔挤压能保证凹模内六方型 腔的成形精密成形。图 6 所示的三种形式由左向右 模具与坯料的接触面积越来越小,因而其变形力必 定越来越小。
年 《第二届全国设计与过程集成技术研讨会》 上大力 宣传 “过程技术” 。 该教材从内容、 结构体系和书名上 都紧紧把握了这一大的趋势,并结合近年来的新工 艺、 新方法和新成果进行介绍。 是 “锻造过程” 技术的核心部分, “锻 “锻造工艺” 造工艺” 不能代表全部 “锻造过程” 技术。 “过程” 技术 不仅仅是制造工艺, 还包括制造过程中所用的装备、 工具、仪表和组织管理技术以及整个生产过程的构 思、 变化和设计。 作者在撰写过程中对传统的经典内容加以精 选, 重点反映当代锻造技术方面的最新成就。 使学生 学习后能对具体产品锻造方法的选择迅速做出可行 性和局限性的评价, 为锻造工艺参数的典型化、 系统 化打下基础,也能为现代信息技术在锻件设计和制 造中的应用开辟新的道路。 作者在坯料的准备一章中以一定的篇幅简单介 绍了带锯。带锯如同数控机床一样获得迅速发展和 广泛应用。 美国在 20 多年前的带锯机就占机拥有量 的 10%。成为与车床、 铣床、 刨床、 磨床 、 镗床 、 钻床 并肩媲美的第七种基本加工机床。金属带锯由变速 机构、 锯带张紧装置 、 无级变速液压控制系统 、 冷却 系统、 锯刷、 床身等六个部分构成。在以往的教科书 中一点也没有提到过。而坯料的准备是一个非常重 要的环节。 特别是对精密锻造来讲, 它对模具的寿命 和产品的质量的影响关系极大。 教材中介绍开式模锻时,引用了清华大学叶庆 荣教授的观点,叶教授论述锤锻模上开式模锻的成 形过程分为镦粗阶段、充满模膛阶段几个阶段的论 述符全实际情况, 非常精辟、 深刻。 教材中介绍了流动控制成形、 板料锻造、 模具型 腔的挤压成形等新技术。
锻造的原理及应用方法论文

锻造的原理及应用方法论文引言锻造是一种通过施加压力和热量的方式对金属材料进行变形加工的方法。
这种加工方法在制造业中得到广泛应用,可以用于生产各种复杂形状的金属制品。
本文将介绍锻造的原理、应用领域和方法论,以帮助读者更好地了解和运用这一加工技术。
锻造的原理锻造的原理基于金属材料在高温下具有可塑性的特性。
通过施加压力和热量,原始金属材料可以被塑造成所需的形状。
锻造可以分为冷锻和热锻两种方式。
冷锻冷锻是在室温下进行的金属锻造过程。
这种方法适用于某些金属材料,比如铝和铜,因为它们在室温下具有较好的可塑性。
冷锻可以用于制造一些细小和高精度的零件,例如螺栓和钉子。
热锻热锻是在高温下进行的金属锻造过程。
通过加热金属材料,使其达到较高的塑性,从而可以更容易地进行形状变化。
热锻适用于大多数金属材料,包括钢、铁和合金。
热锻广泛应用于汽车、航空航天和能源行业,可以制造大型零件和复杂结构。
锻造的应用领域锻造在许多行业中都得到了广泛应用。
以下是一些常见的应用领域:•汽车工业:锻造用于制造汽车发动机零件、传动系统和悬挂部件等。
通过锻造,这些零件可以具有更高的强度和耐久性。
•航空航天工业:锻造用于制造飞机发动机零件、飞行器结构和涡轮机叶片等。
这些零件需要具备优异的性能,以确保航空航天系统的安全性和可靠性。
•能源行业:锻造用于制造石油和天然气开采设备、核电站部件和风力发电设备等。
这些设备需要承受极端条件下的高压和高温,因此对材料的强度和耐腐蚀性要求较高。
•建筑业:锻造用于制造建筑结构和桥梁等。
通过锻造,可以制造出更坚固和耐久的金属构件,以确保建筑物的结构稳定性和安全性。
锻造的应用方法论在进行锻造加工时,需要遵循一定的应用方法论。
以下是一些常用的锻造方法论:1.设计合理的模具:根据所需的零件形状和尺寸,设计适合的模具。
模具的设计应考虑到材料的流动性和纹理。
2.控制合适的工艺参数:确定合适的锻造温度、压力和速度等工艺参数。
这些参数的选择影响着材料的塑性和最终产品的质量。
精密锻造文献小综述讲解

一,总述类1.1.加工技术展望:塑性加工既是材料制备的主要手段,又是装备制造的重要环节,它正随着新材料的出现及对装备性能的不断完善而提出的新要求面临很多挑战与机遇,其发展总的趋是:(1)构件轻量化成形有两个主要途径,一是从材料角度,采用高强钢、铝合金和镁合金;二是从结构角度,采用管件液压成形和拼焊板成形。
前一成形方法是“按需配料,物尽其用”;后一成形方法是“以空代实”,在减轻重量的同时保持构件有很高的刚度。
应当指出,构件轻量化成形不仅仅是为了减轻产品的重量,而且还为其带来运行过程中显著的节能效果。
(2)柔性化成形柔性化是制造业的总趋势,即是一种迅速适应产品与构件多变性的制造方式。
这不仅是市场竞争的需求,也应是成形技术发展的趋势,不应再指望一套模具长期用下去的“几十年一贯制”。
减少装备(包括模具)的数量无疑会增加制造的柔性,软模成形(含液压成形、聚氨酯成形及气压成形)可省去凸模或凹模,甚至不用模具的无模胀形已经得到应用,利用可调节的离散化模具成形将会越来越受到重视。
(3)低载荷、节能化成形塑性加工往往需要很大的动力,成形过程中浪费很多的能量。
因此,如何省力与节能是塑性加工界备受关注的问题。
降低变形力的主要途径有三个,一是降低流动应力,如固-液态成形;二是减少接触面积,如单点成形;三是减少摩擦,如液压成形。
(4)复合成形技术例如热冲压与淬火结合、激光加热与成形结合及成形与焊接结合等复合成形技术正得到重视。
作为后者的实例,可以提到搅拌摩擦焊,它是将两块金属板沿界面用高速旋转棒产生高温大塑性变形而焊合在一起。
1.2现状:航空、航天和汽车等高技术领域与高端产业的发展,不断要求零件的高性能、轻量化、高可靠性和功能高效化,由此导致零件的形状复杂化、大型整体化、薄壁化、大小几何尺寸极端结合。
而零件在锻造过程中对工艺参数及其耦合作用极为敏感,并要经历复杂的不均匀变形和组织演化历程,这使得其锻造过程的优化设计与稳健控制极其困难。
精密锻造文献小综述
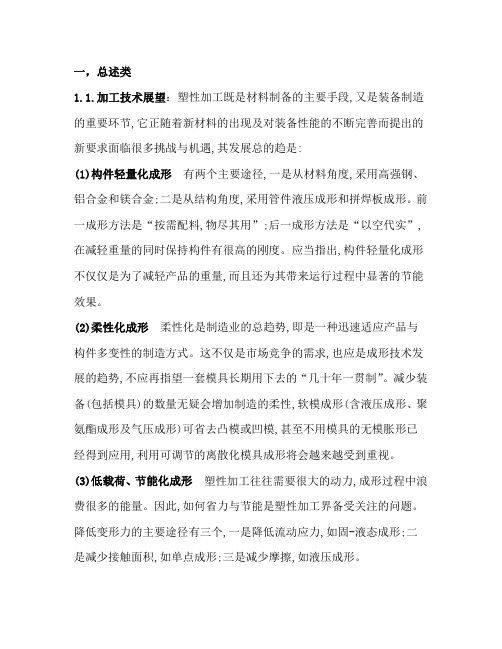
(4)复合成形技术 例如热冲压与淬火结合、激光加热与成形结合及成 形与焊接结合等复合成形技术正得到重视。作为后者的实例,可以提到 搅拌摩擦焊,它是将两块金属板沿界面用高速旋转棒产生高温大塑性变 形而焊合在一起。 1.2 现状:航空、航天和汽车等高技术领域与高端产业的发展,不断要 求零件的高性能、轻量化、高可靠性和功能高效化,由此导致零件的形 状复杂化、大型整体化、薄壁化、大小几何尺寸极端结合。而零件在锻 造过程中对工艺参数及其耦合作用极为敏感,并要经历复杂的不均匀变 形和组织演化历程,这使得其锻造过程的优化设计与稳健控制极其困 难。因此,从多场耦合、多尺度与全过程的角度深入研究并深刻认识大 型复杂锻件高性能精密锻造过程中的变形机理与规律,发展 形性一体化调控的理论与方法,进而发展数字化高性能热精密锻造技 术,是解决我国大型复杂锻件成形制造问题的技术途径,具有带动国家 制造技术和工业技术水平整体提升的关键作用。 习惯将精密锻造成形技术分为:冷精锻成形、热精锻成形、温精锻成形、 复合成形、复动锻造(闭塞锻造)、等温锻造以及分流锻造等。 我国未来热精密锻造技术的重点发展方向包括: 1) 更加关注材料锻造过程中的微观组织协调变形机制,与理论分析相 结合,建立高精度、高效率、多尺度、全过程的模型,为实现多场和多 尺度模拟的整体优化设计奠定基础。
类.锻造时一般根据锻件材料和性能要求以及经济性和可行性分析选择 合适的等温锻造工艺。 2.2.2 等温模锻的工艺设备 (1)设备。等温模锻要求缓慢成型,因此变形设备通常采用液压机。 液压机的规格,可根据等温模锻的变形力选定。大体上等温模锻的压力 为普通模锻的 1/5~1/10。 (2)模具。由于等温模锻需将模具加热到毛坯的锻造温度,这就必须 相应解决一些问题。铝镁合金的变形温度低,用 5CrNiMo、3Cr3Mo3VNb 等 一般的模具钢作为等温锻模具材料就能满足要求。钛合金和高温合金的 等温锻,则需寻找高温下能够长期稳定可靠工作而且不氧化的模具材 料。一般应选择耐热性良好的合金作模具材料,目的是使其在等温锻造 温度下的力学性能高于模锻材料的相应性能。尤其是模具材料的屈服强 度,至少应为模锻材料屈服强度的三倍。 英、美等国在锻造钛合金时,用得较多的模具材料为::Inconel-713C、 INl00、MAR-M200、Udimet700 等,前苏联则用铸造镍基高温合金强Ж C6-K,ЖC6-Y,J1114。我国目前根据材料资源的情况,较多地选用 K3 铸 造高温合金作为等温模锻钛合金用的模具材料。模锻材料是根据等温锻 造的合金牌号和锻件的产量决定,选用高级的高温合金在经济上需要要 做具体分析,在锻造小批量锻件时,一般可选用较低级的合金。
我国精密锻造成型技术及应用
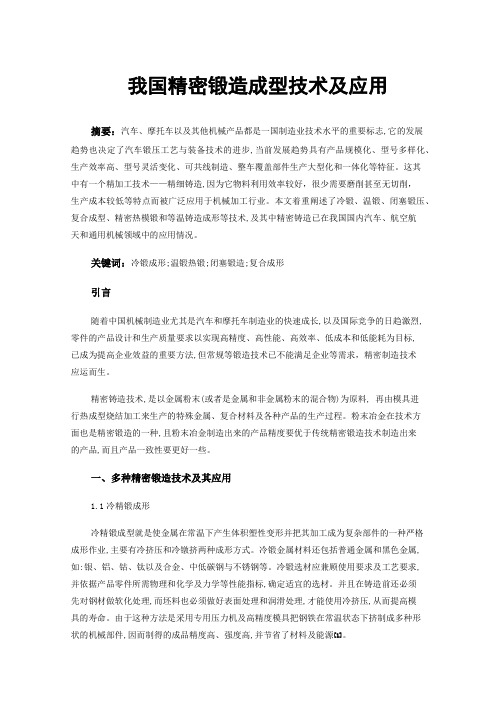
我国精密锻造成型技术及应用摘要:汽车、摩托车以及其他机械产品都是一国制造业技术水平的重要标志,它的发展趋势也决定了汽车锻压工艺与装备技术的进步,当前发展趋势具有产品规模化、型号多样化、生产效率高、型号灵活变化、可共线制造、整车覆盖部件生产大型化和一体化等特征。
这其中有一个精加工技术——精细铸造,因为它物料利用效率较好,很少需要磨削甚至无切削,生产成本较低等特点而被广泛应用于机械加工行业。
本文着重阐述了冷锻、温锻、闭塞锻压、复合成型、精密热模锻和等温铸造成形等技术,及其中精密铸造已在我国国内汽车、航空航天和通用机械领域中的应用情况。
关键词:冷锻成形;温锻热锻;闭塞锻造;复合成形引言随着中国机械制造业尤其是汽车和摩托车制造业的快速成长,以及国际竞争的日趋激烈,零件的产品设计和生产质量要求以实现高精度、高性能、高效率、低成本和低能耗为目标,已成为提高企业效益的重要方法,但常规等锻造技术已不能满足企业等需求,精密制造技术应运而生。
精密铸造技术,是以金属粉末(或者是金属和非金属粉末的混合物)为原料, 再由模具进行热成型烧结加工来生产的特殊金属、复合材料及各种产品的生产过程。
粉末冶金在技术方面也是精密锻造的一种,且粉末冶金制造出来的产品精度要优于传统精密锻造技术制造出来的产品,而且产品一致性要更好一些。
一、多种精密锻造技术及其应用1.1冷精锻成形冷精锻成型就是使金属在常温下产生体积塑性变形并把其加工成为复杂部件的一种严格成形作业,主要有冷挤压和冷镦挤两种成形方式。
冷锻金属材料还包括普通金属和黑色金属,如:银、铝、钴、钛以及合金、中低碳钢与不锈钢等。
冷锻选材应兼顾使用要求及工艺要求,并依据产品零件所需物理和化学及力学等性能指标,确定适宜的选材。
并且在铸造前还必须先对钢材做软化处理,而坯料也必须做好表面处理和润滑处理,才能使用冷挤压,从而提高模具的寿命。
由于这种方法是采用专用压力机及高精度模具把钢铁在常温状态下挤制成多种形状的机械部件,因而制得的成品精度高、强度高,并节省了材料及能源[1]。
大型锻件的锻造工艺研究进展

大型锻件的锻造工艺研究进展发布时间:2021-08-26T11:39:59.990Z 来源:《工程管理前沿》2021年7卷4月第12期作者:刘威李新宇[导读] 镦粗和拔长是大型锻件锻造的基本工序,随着数值模拟技术的进步,对二者的研究也逐渐深入。
刘威1 李新宇2中国一重铸锻钢事业部水压机锻造厂,黑龙江省齐齐哈尔市, 161041中国一重铸锻钢事业部工艺技术部,黑龙江省齐齐哈尔市,161041摘要:镦粗和拔长是大型锻件锻造的基本工序,随着数值模拟技术的进步,对二者的研究也逐渐深入。
扭转镦粗将锻件与模具的摩擦力转化成利于锻件变形的剪切应力,从而提高锻件的等效应变值,提升锻件的力学性能。
随着对扭转镦粗各工艺参数的优化和扭转镦粗设备的研发,扭转镦粗将在改善锻件质量上发挥更大的作用。
关键词:大型锻件;锻造工艺;镦粗;拔长;研究进展大型锻件广泛应用于能源、交通、国防、钢铁、石化等工业,通常是机械设备的核心部件,例如:重型压力容器、水轮机大轴、汽轮机主轴、齿轮轴、发电机转子、船用大型曲轴、大型模块等,所以对大型锻件的晶粒组织和力学性能要求都比较高。
在某种意义上,大型锻件的制造技术是衡量国家重工业发展水平的一个重要标志。
随着相关工业的快速发展,大型锻件的尺寸越来越大,对质量的要求也日益提高。
因此,提高大型锻件的锻造水平,规范其生产工艺,具有非常重要的意义。
1大型锻件的锻造工艺大型锻件主要特点是体形大、质量要求高、批量小、生产费用高、周期长,其生产过程包括:冶炼、铸造、锻造、热处理等多道工序。
钢锭在铸造过程中,不可避免的会有一些偏析、缩孔、疏松等缺陷,并且钢锭体形越大,钢锭内部的缺陷就越明显,钢锭内部缺陷对大锻件的性能有着重要影响。
锻造消除或改善钢锭内部缺陷的主要目的有两个:“成形”和“改性”,前者将坯料变形到锻件所需要的形状,后者通过改变坯料的微观组织使锻件的力学性能达到要求。
大型锻件所用到的基本锻造工序是镦粗和拔长。
精密锻造技术的研究现状及发展趋势分析

—289—《装备维修技术》2021年第1期引言:现代设备、汽车、工具类产品,在新时期被提出了更高的要求,尤其是部分精密仪器,汽车类产品对组成零部件的要求极高,我国现阶段的精密锻造技术依然达不到高精密零件的加工要求,一般需要从国外进口,且价格高昂。
基于这种状况,很多企业的研究人员开始着力于研究精密锻造技术,并且已经取得了一定的成绩,不但提升了零件的加工质量与效率,还可减少原材料的使用,提升企业的生产能力,促进企业的长远发展。
1、精密锻造技术的研究现状经过长时间的研究发展,我国的精密锻造技术已经取得了初步的发展,大致分为以下几种:1.1.冷精锻工艺冷精锻工艺所需的锻造温度低于热精锻,在室温下进行即可。
其主要的特点是工件尺寸与工件形状易于控制,能够降低因高温造成误差的概率,工件表面质量好、精度高与强度高。
但是在冷锻过程中,会存在变形抗力大与工件塑性差等缺陷,这设备与模具的质量要求较高,难以完成复杂零件的锻造工作。
为解决冷精锻填充效果差与变形抗力大等问题,相关研究者陆续开发出一系列新型的锻造工艺,比如预制分流锻造、浮动凹模锻造与闭塞锻造等。
预制分流锻造指的是在锻件的恰当位置增开溢流口,让材料充填型腔时不至于卡涩,有持续流动的空间,以此来满足加工载荷、降低变形阻力与提高型腔填充性;浮动凹模锻造在应用过程中,由于其凹模没有进行固定,在零件锻造过程中会发生浮动,通过这种调整,能够有效降低金属变形体与凹模的相对速度,减小两者接触位置的摩擦影响,提高锻造零件充填性能的同时,降低其变形抗力;闭塞锻造指的是在封闭凹模内通过单向或者对向、一个或者两个冲头对金属进行挤压,使其能够一次成形,在闭塞锻造过程中,使用的加工模具属于上下结合的组合模具,由上凹模、下凹模、上冲头与下冲头组成。
在进行锻造的过程中,首先将上下凹模进行严密闭合,形成较高封闭性的模腔,在施加压力的同时,用上下冲头挤压模膛内的材料,使其逐渐成形。
模腔中的材料受到三个方向的压力,塑性较好,可直接生成质量较好的复杂零件,保障其生产效率的同时,亦能确保其力学性能。
锻造车间绿色制造技术应用研究
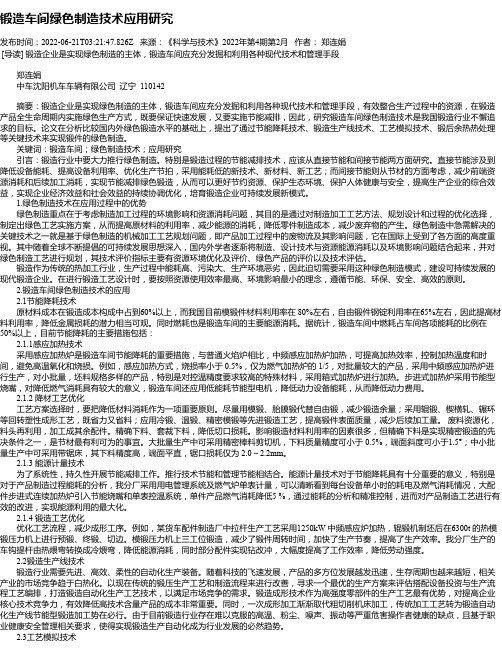
锻造车间绿色制造技术应用研究发布时间:2022-06-21T03:21:47.826Z 来源:《科学与技术》2022年第4期第2月作者:郑连娟[导读] 锻造企业是实现绿色制造的主体,锻造车间应充分发掘和利用各种现代技术和管理手段郑连娟中车沈阳机车车辆有限公司辽宁 110142 摘要:锻造企业是实现绿色制造的主体,锻造车间应充分发掘和利用各种现代技术和管理手段,有效整合生产过程中的资源,在锻造产品全生命周期内实施绿色生产方式,既要保证快速发展,又要实施节能减排,因此,研究锻造车间绿色制造技术是我国锻造行业不懈追求的目标。
论文在分析比较国内外绿色锻造水平的基础上,提出了通过节能降耗技术、锻造生产线技术、工艺模拟技术、锻后余热热处理等关键技术来实现锻件的绿色制造。
关键词:锻造车间;绿色制造技术;应用研究引言:锻造行业中要大力推行绿色制造。
特别是锻造过程的节能减排技术,应该从直接节能和间接节能两方面研究。
直接节能涉及到降低设备能耗、提高设备利用率、优化生产节拍,采用能耗低的新技术、新材料、新工艺;而间接节能则从节材的方面考虑,减少前端资源消耗和后续加工消耗,实现节能减排绿色锻造,从而可以更好节约资源、保护生态环境、保护人体健康与安全,提高生产企业的综合效益,实现企业经济效益和社会效益的持续协调优化,培育锻造企业可持续发展新模式。
1.绿色制造技术在应用过程中的优势绿色制造重点在于考虑制造加工过程的环境影响和资源消耗问题,其目的是通过对制造加工工艺方法、规划设计和过程的优化选择,制定出绿色工艺实施方案,从而提高原材料的利用率,减少能源的消耗,降低零件制造成本,减少废弃物的产生。
绿色制造中急需解决的关键技术之一就是基于绿色制造的机械加工工艺规划问题,即产品加工过程中的废物流及其影响问题,它在国际上受到了各方面的高度重视。
其中随着全球不断提倡的可持续发展思想深入,国内外学者逐渐将制造、设计技术与资源能源消耗以及环境影响问题结合起来,并对绿色制造工艺进行规划,其技术评价指标主要有资源环境优化及评价、绿色产品的评价以及技术评估。
略议现代锻造技术的发展及应用

关 键 词 :现 代锻 造 技 术 ; 用 途 ; 发展 方 向
锻造技 术的发展与进步 ,极大的推动了机械制造业 的发展。近年 来 ,我 国的经济持 续发展 ,人们的生活水平不断改 善 ,给 机械 制造到 来 了极大 的发展空间。因此 ,一定要重视锻造技术 的应 用与完善 ,开 展培训活动 ,增强技术人 员的专业技 能,引进新工艺 ,借鉴发达 国家 的相关经验 ,为锻造技术 的发展提供有力的保障。
[精品]锻造论文
![[精品]锻造论文](https://img.taocdn.com/s3/m/a52e78741fb91a37f111f18583d049649b660ed5.png)
铸造技术基础及设备0专业:车辆工程00班级:09级车辆工程00姓名:任强00学号:086711123900摘要:铸造生产是用液态合金形成产品的方法,将液态合金注入造型中使之冷却,凝固。
绝大多数铸件用作毛坯,需要经机械加工后能成为各种机械零件;少数铸件当达到使用的尺寸精度和表面粗糙度要求时,可作为成品或零件而直接使用。
00关键词:型砂,型芯,浇道,冒口,砂箱,合箱。
002铸造设备002.1砂型的结构00在造型的过程中,型砂在外力作用下成型并达到一定的紧实度而成为砂型。
它是由原砂和黏结剂组成的一种具有一定强度的微孔—多孔系,原砂是骨干材料,占型砂总质量的82%—99%;黏结剂起粘结沙粒的作用,以粘结薄膜形式包覆砂粒,使型砂具有必要的强度和韧性。
002.2原砂的主要作用00用原砂作为型砂的主要骨干材料,更重要是它能为砂型提供必要的耐高温性能和热物理性能,有助高温金属液顺利充型,以及是金属液在铸型中冷却,凝固并得到所要求形状和性能的铸件。
另一方面,原砂砂粒能为砂型提供孔隙,保证型芯的透气性,在浇注过程中,使金属液在型腔内受热急剧膨胀形成的气体和铸型本身产生的大量气体能顺利逸出。
002.3型(芯)砂应具备的性能要求00根据液态金属和铸型的相互作用可见,用于制造砂型(芯)的型砂和芯砂的性能优劣直接影响到铸件的质量。
型芯砂的性能主要有强度、透气性、耐火度和化学稳定性、退让性和工艺性能等。
砂芯处于金属液体的包围之中,其工作条件较型砂更恶劣,因此对芯砂的性能要求比型砂高。
001、强度00型(芯)砂应具有一定的强度,以保证在浇注时铸型在液体金属的冲刷和压力作用下不掉砂、不变形以及在造型、合箱和搬运过程中不损坏。
型(芯)砂强度的大小与水分、黏结剂含量以及紧砂程度有关。
水分过多或过少,都使强度降低。
黏结剂含量越多,砂的粒度越细和紧实度越大,则强度越高。
但是型(芯)砂的强度太高,又会使铸(芯)型太硬,透气性变差,阻碍铸件收缩而使铸件形成气孔和裂纹等缺陷。
探讨锻造技术与应用进展

探讨锻造技术与应用进展前言随着科技的不断进步,锻造技术在生产制造中的作用也越来越明显。
在工业生产中,锻造工艺的重要性不言而喻。
下面将就锻造技术与应用进展进行探讨。
基本概念锻造,就是在锻造压力作用下,对金属材料进行塑性变形,以达到所需形状和性能的目的。
锤击、压制、滚压和弯曲等方法都可以用于锻造。
传统锻造工艺中,通过将金属材料置于高温下进行加工,以使材料变得更加柔韧,便于修改形状。
但是,这种方法有其局限性,如无法处理反复变形的工件和复杂的三维结构等。
近年来,新型的锻造技术得到了广泛应用,通过新型工艺的应用,使锻造更加完美。
新型锻造技术等径挤压成形在等径挤压成形中,加工件通过轴向漏斗型模具保持其周径尺寸未变,在模具的轴向受到压力的作用下,使得加工件在较短的时间内沿轴向挤压成形。
这种工艺可实现无缝管的加工,并带有部分变形、弯曲和扭曲。
等径挤压成形具有低成本、高效率、高精度等特点。
因此,该方法在航空航天、汽车、石油化工等生产领域扮演着重要的角色。
相变式锻造相变式锻造是一种新型的金属成形工艺,其将热机械变形和相变耦合起来,通过对材料进行恒温加热和连续锻造,达到对材料的再次结晶和再配制。
相变式锻造主要用于形状记忆合金和高温合金的制备,其所制备的合金具有高性能、高强度、耐高温等特点。
相变式锻造具有高精度、高效率、无需后续加工等特点。
因此,该方法被广泛应用在高端制造领域,如高铁制造、汽车制造、航空航天等。
模锻成形模锻成形也是一种新型的金属成形技术,其将高温时期的工件放置到合适的模具中进行压制和拉伸,以达到期望形状。
这种方法具有高效率、高精度和材料省去等特点,尤其适用于生产大尺寸、形状复杂、球形等规则体工件。
模锻成形可以以精确的方式加工工件,并且可以使工件具有连续性和统一性。
因此,这种方法在生产各种机械零部件、制造大型直接型转子和轮毂、模型制造等领域上得到了广泛的应用。
锻造技术的另类应用除了在传统的工业制造领域,锻造技术也被应用在其他的场合中,为生活带来便利。
锻造课程设计论文.
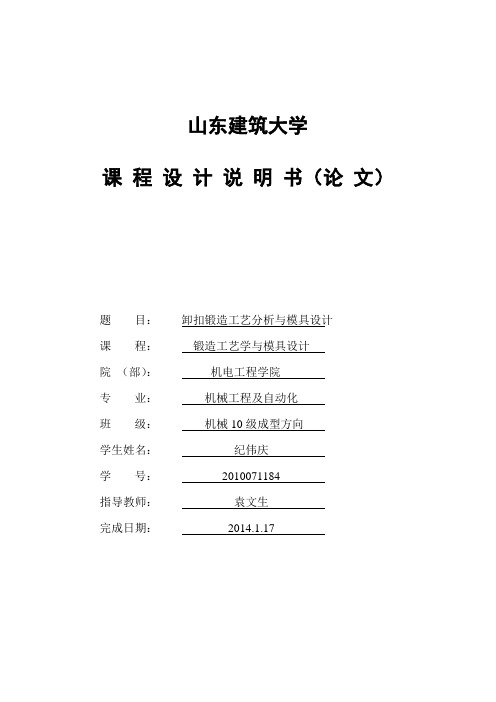
山东建筑大学课程设计说明书(论文)题目:卸扣锻造工艺分析与模具设计课程:锻造工艺学与模具设计院(部):机电工程学院专业:机械工程及自动化班级:机械10级成型方向学生姓名:纪伟庆学号:2010071184指导教师:袁文生完成日期:2014.1.17摘要锻造是一种借助工具或模具在冲击或压力作用下加工金属机械零件或零件毛坯的方法。
与其它方法相比,锻造加工生产的生产率最高,锻件的尺寸形状稳定,并有最佳的综合力学性能。
锻件的最大优势是韧性高,纤维组织合理,件与件之间的性能变化小,并且其内部质量与加工历史有关,不会被任何一种金属加工工艺超过。
锻造是模具三大行业之一,并且随着国内以及国外的机械化加工的越来越被重视,锻造正在发挥着不可替代的作用。
卸扣因体积小承载重量大而广泛适用于电力、冶金、石油、机械、铁路、化工、港口、矿山、建筑等各行各业。
关键字:锻造工艺学;锻造模具;CAD制图;目录摘要 (I)正文 ................................................................................................................................................................... - 1 - 1、零件分析及工艺方案确定 ............................................................................................................................. - 1 -1.1零件分析 ................................................................................................................................................. - 1 -1.2工艺方案的确定 ..................................................................................................................................... - 1 -2、绘制锻件图 ..................................................................................................................................................... - 2 -2.1确定分模位置 ......................................................................................................................................... - 2 -2.2确定模锻件加工余量及公差 ................................................................................................................. - 2 -2.3模锻斜度 ................................................................................................................................................. - 2 -2.4确定锻件圆角半径 ................................................................................................................................. - 2 -2.5技术条件: ............................................................................................................................................. - 3 -3、计算锻件的主要参数 ..................................................................................................................................... - 3 -4、确定锻锤吨位 ................................................................................................................................................. - 3 -5、确定毛边槽形式和尺寸 ................................................................................................................................. - 4 -6、确定终锻型槽 ................................................................................................................................................. - 4 -7、设计预锻型槽 ................................................................................................................................................. - 5 -8、绘制计算毛坯图 ............................................................................................................................................. - 5 -9、制坯工步选择 ................................................................................................................................................. - 7 -10、确定坯料尺寸 ............................................................................................................................................... - 7 -11、制坯型槽设计 ............................................................................................................................................... - 8 -12、锻模结构设计 ............................................................................................................................................... - 9 -13、锻前加热、锻后冷却及热处理要求的确定 ............................................................................................. - 10 -13.1确定加热方式,及锻造温度范围 ..................................................................................................... - 10 -13.2确定加热时间 ..................................................................................................................................... - 11 -13.3确定冷却方式及规范 ......................................................................................................................... - 11 -13.4确定锻后热处理方式及要求 ............................................................................................................. - 11 -14、卸扣件的模锻工艺流程 ............................................................................................................................. - 11 -15、课程设计感悟 ............................................................................................................................................. - 12 -16、参考资料 ..................................................................................................................................................... - 12 -正文1、零件分析及工艺方案确定1.1零件分析卸扣,索具的一种。
铸造工技师论文参考文献范例
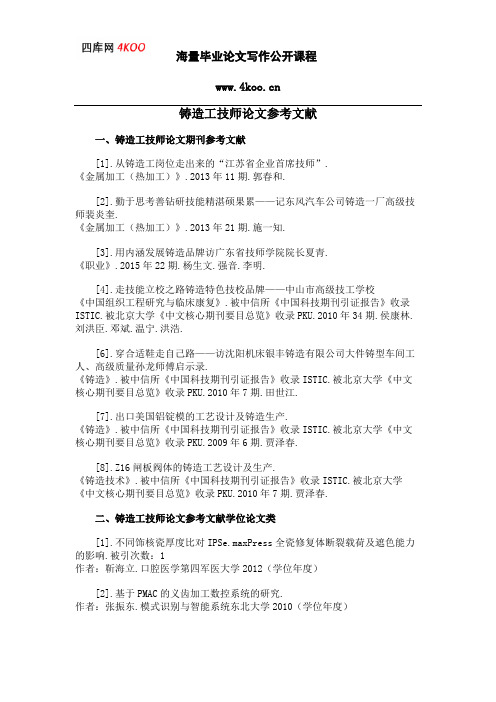
铸造工技师论文参考文献一、铸造工技师论文期刊参考文献[1].从铸造工岗位走出来的“江苏省企业首席技师”.《金属加工(热加工)》.2013年11期.郭春和.[2].勤于思考善钻研技能精湛硕果累——记东风汽车公司铸造一厂高级技师裴炎奎.《金属加工(热加工)》.2013年21期.施一知.[3].用内涵发展铸造品牌访广东省技师学院院长夏青.《职业》.2015年22期.杨生文.强音.李明.[4].走技能立校之路铸造特色技校品牌——中山市高级技工学校《中国组织工程研究与临床康复》.被中信所《中国科技期刊引证报告》收录ISTIC.被北京大学《中文核心期刊要目总览》收录PKU.2010年34期.侯康林.刘洪臣.邓斌.温宁.洪浩.[6].穿合适鞋走自己路——访沈阳机床银丰铸造有限公司大件铸型车间工人、高级质量孙龙师傅启示录.《铸造》.被中信所《中国科技期刊引证报告》收录ISTIC.被北京大学《中文核心期刊要目总览》收录PKU.2010年7期.田世江.[7].出口美国铝锭模的工艺设计及铸造生产.《铸造》.被中信所《中国科技期刊引证报告》收录ISTIC.被北京大学《中文核心期刊要目总览》收录PKU.2009年6期.贾泽春.[8].Z16闸板阀体的铸造工艺设计及生产.《铸造技术》.被中信所《中国科技期刊引证报告》收录ISTIC.被北京大学《中文核心期刊要目总览》收录PKU.2010年7期.贾泽春.二、铸造工技师论文参考文献学位论文类[1].不同饰核瓷厚度比对IPSe.maxPress全瓷修复体断裂载荷及遮色能力的影响.被引次数:1作者:靳海立.口腔医学第四军医大学2012(学位年度)[2].基于PMAC的义齿加工数控系统的研究.作者:张振东.模式识别与智能系统东北大学2010(学位年度)[3].纯钛金属全冠微渗漏及密合度的研究.作者:任晓娟.口腔临床医学河北联合大学2014(学位年度)三、铸造工技师论文专著参考文献[1]上海船厂青铜艺术铸造概述.陈林才,1999中国艺术铸造第一届年会[2]稀土元素Gd对Zr基块体非晶合金形成能力的影响.梁顺星.宗海涛.宋爱君.张卫国.马明臻,2008第十二届全国特种铸造及有色合金学术年会、第六届全国铸造复合材料学术年会暨2008年福建省铸造学术年会[3]120t吊架铸件造型模具的设计.贾泽春,20122012年中国铸造活动周[4]原位自生TiCpLD7复合材料高温蠕变应力指数及激活能.嵇峰.宋爱君.张卫国.宗海涛.梁顺星.马明臻,2008第十二届全国特种铸造及有色合金学术年会、第六届全国铸造复合材料学术年会暨2008年福建省铸造学术年会[5]SHS法合成TiCP/2A12基复合材料的组织与性能.马明臻.韦娜.张卫国,2006第十一届全国特种铸造及有色合金学术年会、第五届全国铸造复合材料学术年会、第十二届全国铸钢及熔炼学术年会暨中国有色金属加工工业协会重有色分会技术交流会[6]TiCP/2024复合材料蠕变性能.张卫国.宋爱君.稽峰.马明臻,20072007年中国压铸、挤压铸造、半固态加工学术年会[7]添加Al<,2>O<,3>对重力分离SHS法制备Al<,2>O<,3>/Fe复合管组织的影响.张卫国.王煦.邢剑申.马明臻,20052005年中国压铸、挤压铸造、半固态加工学术年会[8]SiC泡沫/Al双连续相复合材料连续性的研究.赵龙志.何向明.赵明娟.熊光耀.何柏林.张劲松,2007第六届中国功能材料及其应用学术会议。
锻造毕业论文汇总
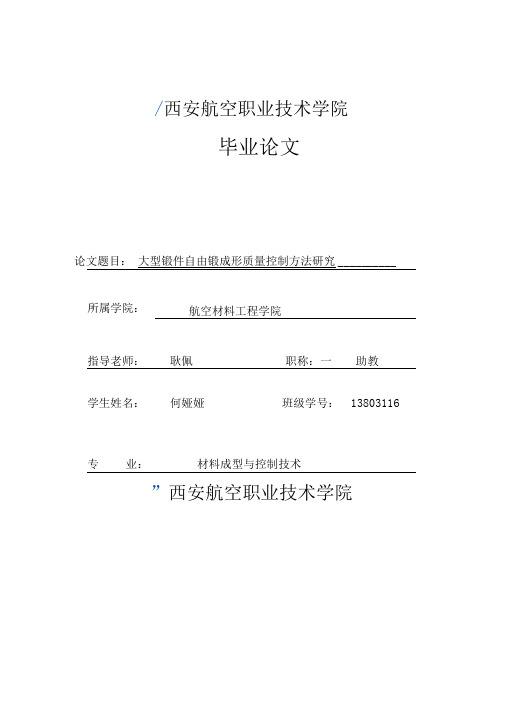
/西安航空职业技术学院毕业论文”西安航空职业技术学院毕业论文任务书题目:大型锻件自由锻成形质量控制方法研究任务与要求:1.查阅大量文献与书籍资料先了解什么是大型锻件自由锻成形;毕业设计(论文)进度计划表()成后交系(部)保存,作为计算教师指导工作量的主要依据之一。
大型锻件自由锻成形质量控制方法研究【摘要】大型锻件是国家重大技术装备和重大工程建设所需要的重要基础部件,比如电力、石化、造船、交通、军工、重矿机械、航空航天工业设备生产都离不开大型锻件,其成形质量直接决定着重大技术装备的制造能力和水平。
因此,大型锻件产业的发展是衡量一个国家工业水平和国防实力的标志之一。
本论文主要阐述了大型自由锻件的成形过程中缺陷种类,以及关键影响因素,并归纳了提高大型自由锻件成形的有效方法,最后基于现有技术水平,总结出了最新用于提高大型锻件自由锻成形质量控制方法。
关键词:大型自由锻件,缺陷,质量控制Abstract: The large casti ngs and forgi ngs are coun tries of majortech ni cal equipme nt and major project con struct ion importa nt comp onent, such as electric power, ir on and steel, petrochemical, shipbuildi ng, tran sportati on, military, heavy mi ning mach in ery, aerospace and in dustrial equipme nt product ion are in separable from it, its manu facturi ng capacity and the level directly determ ines the major tech no logy and equipme nt manu facturi ng capacity and the level. Therefore, the development of large casting and forging industry is one of the marks of a coun try's in dustrial level and n ati onal defe nse stre ngth.This paper mainly expounds the kinds of defects in the forming process of large forgin gs, and key in flue ncing factors, and summarizes the effective method to improve the formi ng of large forgi ngs, fin ally, based on prese nt tech no logy, summed up the latest to improve large forgings forgi ng into morphological qua ntity con trol method.第1章大型锻件自由锻1.1XXXXX (1)1.1.1XXXX ......................................................................... 错误!未定义书签。
第1章 锻造工艺概述

模锻锤
滚挤、弯曲、成形、 预锻、终锻。
长 轴 类 锻 件
短 轴 类 锻 件
第五章 锻造工艺与模具设计
曲柄压力机
行程不能调节; 不能拔长和滚挤; 每个变形工步在 一次行程中完成。
第五章 锻造工艺与模具设计
摩擦压锻机
螺杆与滑块非刚性连接, 承受偏心能力差; 滑块行程、打击能量 可自动调节。
第五章 锻造工艺与模具设计
较高
较低
第1章 绪论
锻造工艺概述
六、锻造工艺的主要生产工序
(1)下料:将原材料切割成所需尺寸的坯料 (2)加热:提高金属的塑性,降低变形抗力,便于模锻成形。 (3)模锻:得到所需锻件的形状和尺寸。 (4)切边或冲孔:切去飞边或冲掉连皮 (5)热校正或热精压:使锻件形状和尺寸更准确 (6)在砂轮上磨毛刺:切边所剩下的毛刺 (7)热处理:保证合适的硬度和力学性能,常用正火和调质。 (8)清除氧化皮:常用喷砂、喷丸、滚筒抛光、酸洗等方法。 (9)冷校正和冷精压:进一步提高锻件精度,降低表面粗糙度 (10)检查锻件
适应于小型锻件,中、小批量生产。
第1章 绪论
锻造工艺概述
三、锻造加工特点
优点: 1、能改善金属的组织,提高金属的机械性能; 2、提高材料的利用率和经济效益(节省材料和切削加工工时); 3、具有较高的劳动生产率。 缺点: 1、不能获得形状复杂的锻件; 2、初次投资费用高(设备、工模具、厂房); 3、生产现场劳动条件差。
第1章 绪论
锻造工艺概述
四、锻造设备
1.自由锻设备:锻锤、空气锤、蒸汽-空气锻锤 水压机、油压机
2.模锻设备:锤上模锻 压力机模锻 摩擦压力机模锻
第1章 绪论
模锻设备
模锻设备 模锻锤
精密锻造技术现状以及发展探析
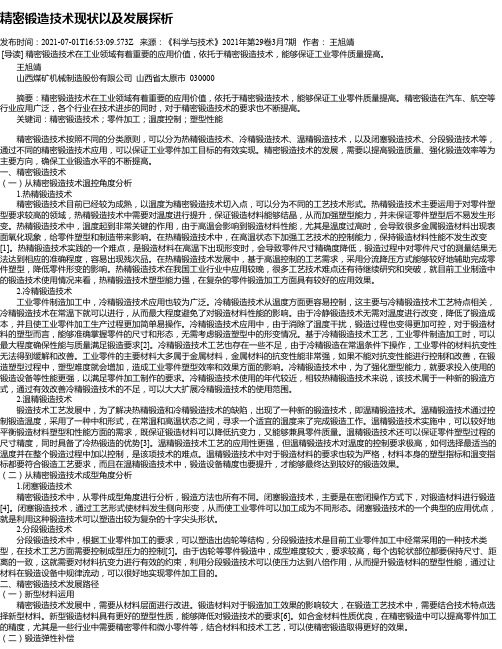
精密锻造技术现状以及发展探析发布时间:2021-07-01T16:53:09.573Z 来源:《科学与技术》2021年第29卷3月7期作者:王旭靖[导读] 精密锻造技术在工业领域有着重要的应用价值,依托于精密锻造技术,能够保证工业零件质量提高。
王旭靖山西煤矿机械制造股份有限公司山西省太原市 030000摘要:精密锻造技术在工业领域有着重要的应用价值,依托于精密锻造技术,能够保证工业零件质量提高。
精密锻造在汽车、航空等行业应用广泛,各个行业在技术进步的同时,对于精密锻造技术的要求也不断提高。
关键词:精密锻造技术;零件加工;温度控制;塑型性能精密锻造技术按照不同的分类原则,可以分为热精锻造技术、冷精锻造技术、温精锻造技术,以及闭塞锻造技术、分段锻造技术等,通过不同的精密锻造技术应用,可以保证工业零件加工目标的有效实现。
精密锻造技术的发展,需要以提高锻造质量、强化锻造效率等为主要方向,确保工业锻造水平的不断提高。
一、精密锻造技术(一)从精密锻造技术温控角度分析 1.热精锻造技术精密锻造技术目前已经较为成熟,以温度为精密锻造技术切入点,可以分为不同的工艺技术形式。
热精锻造技术主要运用于对零件塑型要求较高的领域,热精锻造技术中需要对温度进行提升,保证锻造材料能够结晶,从而加强塑型能力,并未保证零件塑型后不易发生形变。
热精锻造技术中,温度起到非常关键的作用,由于高温会影响到锻造材料性能,尤其是温度过高时,会导致很多金属锻造材料出现表面氧化现象,给零件塑型和制造带来影响。
在热精锻造技术中,在高温状态下加强工艺技术的控制能力,保持锻造材料性能不发生改变[1]。
热精锻造技术实践的一个难点,是锻造材料在高温下出现形变时,会导致零件尺寸精确度降低,锻造过程中对零件尺寸的测量结果无法达到相应的准确程度,容易出现残次品。
在热精锻造技术发展中,基于高温控制的工艺需求,采用分流降压方式能够较好地辅助完成零件塑型,降低零件形变的影响。