数控加工中的误差来源分析
数控机床加工尺寸不稳定原因及解决方法
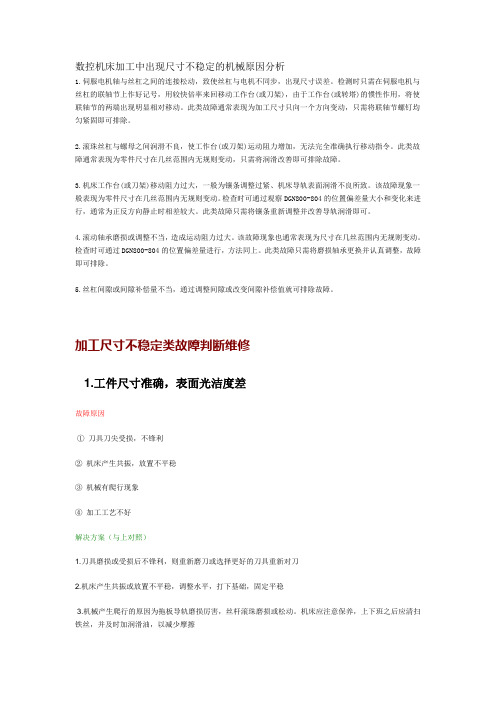
数控机床加工中出现尺寸不稳定的机械原因分析1.伺服电机轴与丝杠之间的连接松动,致使丝杠与电机不同步,出现尺寸误差。
检测时只需在伺服电机与丝杠的联轴节上作好记号,用较快倍率来回移动工作台(或刀架),由于工作台(或转塔)的惯性作用,将使联轴节的两端出现明显相对移动。
此类故障通常表现为加工尺寸只向一个方向变动,只需将联轴节螺钉均匀紧固即可排除。
2.滚珠丝杠与螺母之间润滑不良,使工作台(或刀架)运动阻力增加,无法完全准确执行移动指令。
此类故障通常表现为零件尺寸在几丝范围内无规则变动,只需将润滑改善即可排除故障。
3.机床工作台(或刀架)移动阻力过大,一般为镶条调整过紧、机床导轨表面润滑不良所致。
该故障现象一般表现为零件尺寸在几丝范围内无规则变动。
检查时可通过观察DGN800-804的位置偏差量大小和变化来进行,通常为正反方向静止时相差较大。
此类故障只需将镶条重新调整并改善导轨润滑即可。
4.滚动轴承磨损或调整不当,造成运动阻力过大。
该故障现象也通常表现为尺寸在几丝范围内无规则变动。
检查时可通过DGN800-804的位置偏差量进行,方法同上。
此类故障只需将磨损轴承更换并认真调整,故障即可排除。
5.丝杠间隙或间隙补偿量不当,通过调整间隙或改变间隙补偿值就可排除故障。
加工尺寸不稳定类故障判断维修1.工件尺寸准确,表面光洁度差故障原因①刀具刀尖受损,不锋利②机床产生共振,放置不平稳③机械有爬行现象④加工工艺不好解决方案(与上对照)1.刀具磨损或受损后不锋利,则重新磨刀或选择更好的刀具重新对刀2.机床产生共振或放置不平稳,调整水平,打下基础,固定平稳3.机械产生爬行的原因为拖板导轨磨损厉害,丝杆滚珠磨损或松动。
机床应注意保养,上下班之后应清扫铁丝,并及时加润滑油,以减少摩擦4. 选择适合工件加工的冷却液;在能达到其它工序加工要求的情况下,尽量选用较高的主轴转速2.工件产生锥度大小头现象故障原因①机床放置的水平没调整好,一高一低,产生放置不平稳②车削长轴时,工件材料比较硬,刀具吃刀比较深,造成让刀现象③尾座顶针与主轴不同心解决方案1.使用水平仪调整机床的水平度,打下扎实的地基,把机床固定好提高其韧性2.选择合理的工艺和适当的切削进给量避免刀具受力让刀3. 调整尾座3.驱动器相位灯正常,而加工出来的工件尺寸时大时小故障原因①机床拖板长期高速运行,导致丝杆和轴承磨损②刀架的重复定位精度在长期使用中产生偏差③拖板每次都能准确回到加工起点,但加工工件尺寸仍然变化。
数控机床加工误差原因及对策分析

数控机床加工误差原因及对策分析数控车床为零件加工的主要方式,对于零件加工具有较高的自动化水平,但是就实际情况来看,零件加工经常会因为设备自身或者操作不当等因素限制,而造成工件精度达不到专业要求,存在一定误差。
零件加工精度最终由机床刀具与零件间相对位移误差决定,因此需要确定加工误差存在的原因,以降低误差为面对,采取措施进行优化。
本文选择经济性数控机床为对象,就其加工误差与优化对策进行了简要分析。
标签:数控机床;加工误差;补偿0 引言数控机床零件加工经常会因为各项因素的影响而出现误差,即加工后零件实际几何参数与设计几何参数间存在一定偏差,导致零件精确度不能满足设计要求,最终只能作为不合格或者废品处理。
以提高数控机床加工精确度为的目的,需要对各类加工误差原因进行分析,有针对性的采取措施进行处理,对存在的误差进行有效补偿。
1 数控机床加工误差分析经济性数控车床对零件的加工,应用为步进电机开环伺服系统或者半闭环伺服系统来驱动刀具,在这个过程中就会因为受各项因素的影响而存在加工误差。
一方面,数控机床自身因素。
主要是因为数控机床所用构件精确度较低,以及机床装配过程中存在误差,导致零件加工后精确度达不到设计要求。
针对此种误差原因,一般可以就高精度零部件进行更换,以及在装配环节做好控制,争取提高机床自身精确度。
另外,对于部分技术能力可以达到要求的企业,还可以选择对步进电机构成的开环伺服系统进行适当的改造,使其成为闭环伺服系统,来提高零件加工精度[1]。
另一方面,工艺操作因素。
部分零件在加工过程中,会因为机床以及零件本身的热变形,造成切削、振动、装夹、磨损等细节存在误差。
想要对此类误差进行补偿,需要建立补偿模型在CNC系统内补偿,实施难度比较大,对提高数控机床零件加工精确度需要重点研究。
2 数控机床加工误差原因与对策分析2.1 数控机床自身原因2.1.1 控制系统误差(1)开环控制系统。
开环控制系统并未设置反馈装置,数控信号为单向流程,并不能对移动部件实际位移量进行测量与反馈,进而会影响对加工过程中所存误差的调整。
加工中心圆度出现误差的原因是什么?怎么调整?
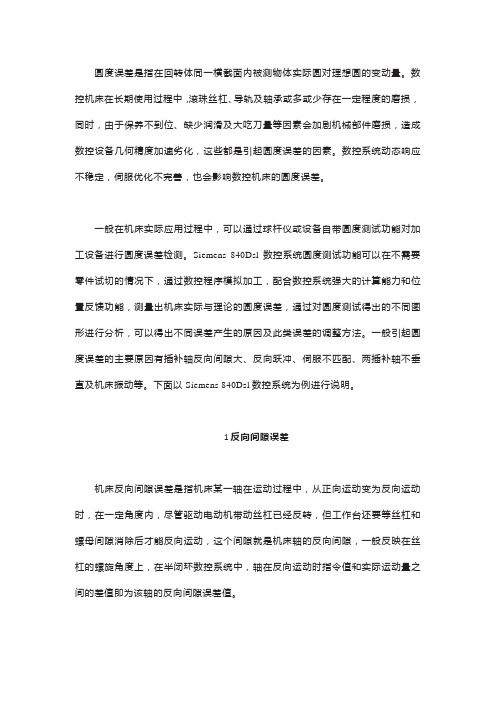
圆度误差是指在回转体同一横截面内被测物体实际圆对理想圆的变动量。
数控机床在长期使用过程中,滚珠丝杠、导轨及轴承或多或少存在一定程度的磨损,同时,由于保养不到位、缺少润滑及大吃刀量等因素会加剧机械部件磨损,造成数控设备几何精度加速劣化,这些都是引起圆度误差的因素。
数控系统动态响应不稳定,伺服优化不完善,也会影响数控机床的圆度误差。
一般在机床实际应用过程中,可以通过球杆仪或设备自带圆度测试功能对加工设备进行圆度误差检测。
Siemens 840Dsl数控系统圆度测试功能可以在不需要零件试切的情况下,通过数控程序模拟加工,配合数控系统强大的计算能力和位置反馈功能,测量出机床实际与理论的圆度误差,通过对圆度测试得出的不同图形进行分析,可以得出不同误差产生的原因及此类误差的调整方法。
一般引起圆度误差的主要原因有插补轴反向间隙大、反向跃冲、伺服不匹配、两插补轴不垂直及机床振动等。
下面以Siemens 840Dsl数控系统为例进行说明。
1反向间隙误差机床反向间隙误差是指机床某一轴在运动过程中,从正向运动变为反向运动时,在一定角度内,尽管驱动电动机带动丝杠已经反转,但工作台还要等丝杠和螺母间隙消除后才能反向运动,这个间隙就是机床轴的反向间隙,一般反映在丝杠的螺旋角度上,在半闭环数控系统中,轴在反向运动时指令值和实际运动量之间的差值即为该轴的反向间隙误差值。
(1)反向间隙对圆度误差的影响反向间隙的存在会影响机床的定位精度和重复定位精度,降低数控机床加工精度,在加工中心铣圆过程中会造成圆度误差。
当Y轴在反向运动过程中,由于反向间隙的存在,会造成Y轴反向后滞后于X 轴进行插补运动,铣圆加工会出现如图1所示结果。
图1反向间隙造成的圆度误差(2 )反向间隙测量与调整影响机床轴反向间隙误差的因素多种多样,从驱动电动机到运动部件之间所有的机械联接件都会存在间隙,电动机对丝杠的联轴结是否松动、滚珠丝杠制造误差、丝杠预紧是否过紧或过松、丝母与运动部件联接是否紧固,都是造成机床轴反向间隙的原因。
数控机床加工误差原因及对策分析

数控机床加工误差原因及对策分析数控机床是当今制造业的主要设备之一。
数控机床生产效率高,运行速度快,加工精度高,成品质量好,成本相对较低。
但是,在实际生产过程中,经常会出现加工误差,影响生产效率和成品质量。
因此,分析数控机床加工误差原因并寻找对策是很必要的。
本文将探讨数控机床加工误差的原因,以及如何通过改进措施来减少误差的发生。
一、误差的种类数控机床加工误差通常包括以下几种:1.轨迹误差。
轨迹误差是指数控机床加工时导致实际加工轨迹与期望轨迹之间的误差。
2.定位误差。
定位误差是指数控机床在加工中出现的位置偏差。
定位误差可能由机床本身、工件、刀具等方面的原因引起。
3.回转误差。
回转误差是指数控机床在进行旋转加工时出现的偏差。
回转误差通常由转台本身、传动系统和工件等原因引起。
4.表面误差。
表面误差是指数控机床加工表面的粗糙度、平整度、垂直度和平行度等参数上的误差。
二、误差产生的原因1.机床本身的精度。
数控机床的精度与质量直接相关,是影响加工质量的最重要因素。
如果机床本身的精度不高,则会直接导致加工误差的发生。
2.工具刃磨质量。
如果刀具的刃磨质量不好,切屑排出不畅等问题,也容易引起加工误差。
3.刀具稳定性。
刀具的稳定性是指在加工过程中刀具的稳定性,如果刀具不稳定,则极易引起加工误差的发生。
4.机床几何精度调整。
机床几何精度调整直接影响加工误差发生的概率,如果机床几何精度调整不当,则会引起加工误差的出现。
5.机床零部件磨损。
随着机床的使用,部件常会出现磨损,进而影响加工精度。
三、解决方案1.提高加工前的加工过程控制。
在加工前加强对加工过程的控制,可通过模具设计等预处理阶段减少误差出现的可能性。
2.注意刀具选择。
选择质量高的刀具,并保持刀具在加工过程中的稳定性。
3.指导及培训操作人员。
操作人员要具备相应的知识和技能,遵循正确的加工流程,熟练使用数控机床,能够及时发现和解决数控机床加工过程中的问题。
4.定期机床保养。
数控机床的加工精度误差分析与精度校正技巧
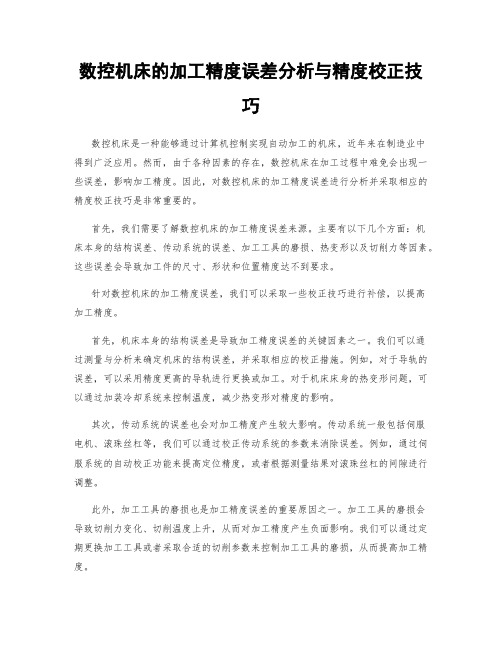
数控机床的加工精度误差分析与精度校正技巧数控机床是一种能够通过计算机控制实现自动加工的机床,近年来在制造业中得到广泛应用。
然而,由于各种因素的存在,数控机床在加工过程中难免会出现一些误差,影响加工精度。
因此,对数控机床的加工精度误差进行分析并采取相应的精度校正技巧是非常重要的。
首先,我们需要了解数控机床的加工精度误差来源。
主要有以下几个方面:机床本身的结构误差、传动系统的误差、加工工具的磨损、热变形以及切削力等因素。
这些误差会导致加工件的尺寸、形状和位置精度达不到要求。
针对数控机床的加工精度误差,我们可以采取一些校正技巧进行补偿,以提高加工精度。
首先,机床本身的结构误差是导致加工精度误差的关键因素之一。
我们可以通过测量与分析来确定机床的结构误差,并采取相应的校正措施。
例如,对于导轨的误差,可以采用精度更高的导轨进行更换或加工。
对于机床床身的热变形问题,可以通过加装冷却系统来控制温度,减少热变形对精度的影响。
其次,传动系统的误差也会对加工精度产生较大影响。
传动系统一般包括伺服电机、滚珠丝杠等,我们可以通过校正传动系统的参数来消除误差。
例如,通过伺服系统的自动校正功能来提高定位精度,或者根据测量结果对滚珠丝杠的间隙进行调整。
此外,加工工具的磨损也是加工精度误差的重要原因之一。
加工工具的磨损会导致切削力变化、切削温度上升,从而对加工精度产生负面影响。
我们可以通过定期更换加工工具或者采取合适的切削参数来控制加工工具的磨损,从而提高加工精度。
另外,热变形也是影响加工精度的重要因素。
随着机床的连续工作,温度会逐渐升高,导致机床的热变形。
我们可以通过在机床上安装温度传感器,监测温度的变化,然后根据变化的温度对加工精度进行校正。
此外,通过改进机床的散热系统,减少热量的积聚,也可以有效地降低热变形对加工精度的影响。
最后,我们还可以通过控制切削力来提高加工精度。
切削力对加工精度具有较大的影响,对切削力的控制可以通过调整切削参数(如切削速度、进给量等)来实现。
数控加工产生误差的根源及解决方案

数控加工产生误差的根源及解决方案数控加工是利用数控技术通过控制机床和刀具相对运动的方式,对工件进行加工的一种工艺。
虽然数控加工相对手工加工来说具有高精度、高效率、高一致性等优点,但是由于一些原因还是会在实际应用中产生一些误差,下面我们对数控加工误差的根源及解决方案进行详细介绍。
一、误差产生的根源1.机床本身问题机床是数控加工的基础,如果机床本身精度不高,则会直接影响到加工的精度。
例如机床的重复定位精度、圆度等问题都会导致数控加工中的误差。
2.编程和操作问题编程和操作的问题也是数控加工中产生误差的重要原因。
编写的程序是否符合实际加工的要求、操作人员能否正确的操作数控设备、调整数控设备的参数等都会影响加工的精度。
3.工件材料和加工工艺工件的材料和加工工艺也是数控加工中产生误差的原因之一。
因为不同的材料及加工工艺的选用,需要有不同的加工参数设置,否则加工出来的零件尺寸不稳定,而且不同的材料具有不同的热膨胀系数,会使得加工出来的工件产生偏差。
二、误差的解决方案1.提高机床精度如何提高机床精度呢?首先我们要选用性能稳定、精度高的数控机床。
同时,在加工过程中要注意定期检查机床的重复定位精度、圆形度等指标,及时进行维护和保养。
2.优化编程和操作流程软件程序的编写和操作过程是决定加工精度的重要环节之一,因此编写程序时要结合实际加工要求,同时要对操作流程进行规范化和标准化,让操作流程尽量简单,便于操作人员进行操作。
3.优化材料和加工工艺合理选用材料及加工工艺,是提高精度的重要环节之一,因此选择合适的加工工艺的同时,要注意材料的热膨胀系数等性质,以此来保证加工出来的工件符合设计要求。
总之,数控加工误差的根源较多,但只要我们能够从机器、人员和程序三个方面入手,针对性的进行优化,加工精度是能够得到不断提高的。
数控机床的加工精度误差分析与校正方法
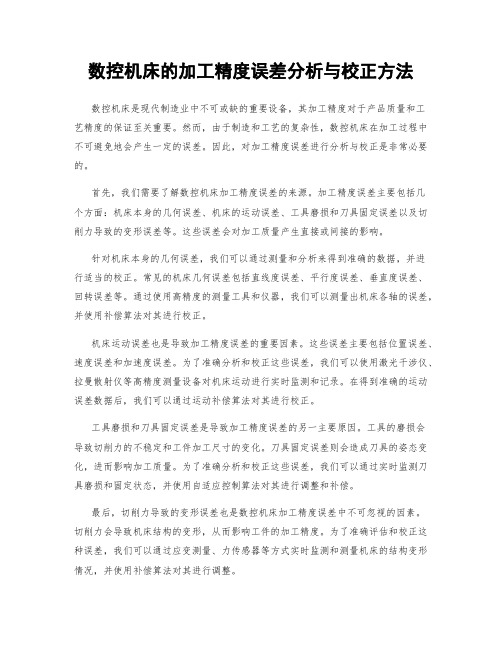
数控机床的加工精度误差分析与校正方法数控机床是现代制造业中不可或缺的重要设备,其加工精度对于产品质量和工艺精度的保证至关重要。
然而,由于制造和工艺的复杂性,数控机床在加工过程中不可避免地会产生一定的误差。
因此,对加工精度误差进行分析与校正是非常必要的。
首先,我们需要了解数控机床加工精度误差的来源。
加工精度误差主要包括几个方面:机床本身的几何误差、机床的运动误差、工具磨损和刀具固定误差以及切削力导致的变形误差等。
这些误差会对加工质量产生直接或间接的影响。
针对机床本身的几何误差,我们可以通过测量和分析来得到准确的数据,并进行适当的校正。
常见的机床几何误差包括直线度误差、平行度误差、垂直度误差、回转误差等。
通过使用高精度的测量工具和仪器,我们可以测量出机床各轴的误差,并使用补偿算法对其进行校正。
机床运动误差也是导致加工精度误差的重要因素。
这些误差主要包括位置误差、速度误差和加速度误差。
为了准确分析和校正这些误差,我们可以使用激光干涉仪、拉曼散射仪等高精度测量设备对机床运动进行实时监测和记录。
在得到准确的运动误差数据后,我们可以通过运动补偿算法对其进行校正。
工具磨损和刀具固定误差是导致加工精度误差的另一主要原因。
工具的磨损会导致切削力的不稳定和工件加工尺寸的变化。
刀具固定误差则会造成刀具的姿态变化,进而影响加工质量。
为了准确分析和校正这些误差,我们可以通过实时监测刀具磨损和固定状态,并使用自适应控制算法对其进行调整和补偿。
最后,切削力导致的变形误差也是数控机床加工精度误差中不可忽视的因素。
切削力会导致机床结构的变形,从而影响工件的加工精度。
为了准确评估和校正这种误差,我们可以通过应变测量、力传感器等方式实时监测和测量机床的结构变形情况,并使用补偿算法对其进行调整。
总结来说,数控机床的加工精度误差分析与校正是确保产品质量和工艺精度的关键步骤。
在这个过程中,我们需要准确地识别和分析加工精度误差的来源,并采取相应的校正措施。
数控机加工常见问题及分析
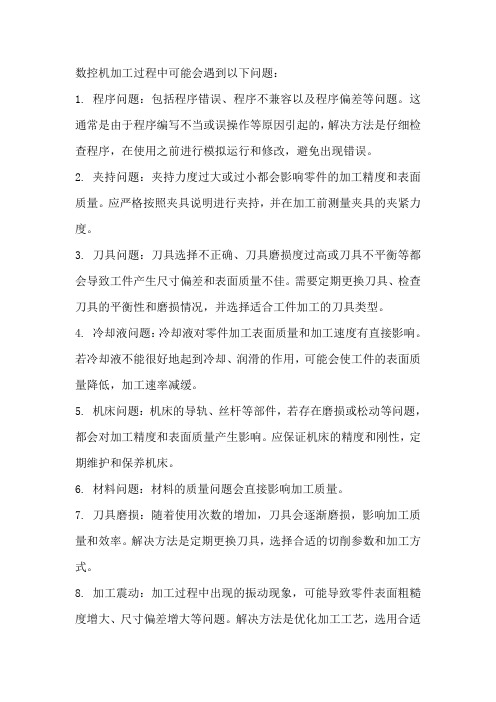
数控机加工过程中可能会遇到以下问题:1. 程序问题:包括程序错误、程序不兼容以及程序偏差等问题。
这通常是由于程序编写不当或误操作等原因引起的,解决方法是仔细检查程序,在使用之前进行模拟运行和修改,避免出现错误。
2. 夹持问题:夹持力度过大或过小都会影响零件的加工精度和表面质量。
应严格按照夹具说明进行夹持,并在加工前测量夹具的夹紧力度。
3. 刀具问题:刀具选择不正确、刀具磨损度过高或刀具不平衡等都会导致工件产生尺寸偏差和表面质量不佳。
需要定期更换刀具、检查刀具的平衡性和磨损情况,并选择适合工件加工的刀具类型。
4. 冷却液问题:冷却液对零件加工表面质量和加工速度有直接影响。
若冷却液不能很好地起到冷却、润滑的作用,可能会使工件的表面质量降低,加工速率减缓。
5. 机床问题:机床的导轨、丝杆等部件,若存在磨损或松动等问题,都会对加工精度和表面质量产生影响。
应保证机床的精度和刚性,定期维护和保养机床。
6. 材料问题:材料的质量问题会直接影响加工质量。
7. 刀具磨损:随着使用次数的增加,刀具会逐渐磨损,影响加工质量和效率。
解决方法是定期更换刀具,选择合适的切削参数和加工方式。
8. 加工震动:加工过程中出现的振动现象,可能导致零件表面粗糙度增大、尺寸偏差增大等问题。
解决方法是优化加工工艺,选用合适的夹持方式和刀具,并设置合适的进给量和转速。
9. 运动平稳性差:机床的运动平稳性差,容易导致轮廓不光滑、表面粗糙度高等问题。
解决方法是保证机床的精度和刚性,定期维护和保养机床。
10. 温度变化:温度变化会导致机床和工件的尺寸发生变化,从而影响加工质量。
解决方法是控制车间温度,使用稳定的进给系统和刀具以及优化加工策略。
11. 夹紧力不足:夹紧力不足可能导致工件位置偏差或者变形等问题。
12. 切削参数不合适:切削速度、进给量和切削深度等参数设置不合理,会导致刀具磨损加剧,加工效率低下,甚至可能损坏刀具或机床。
解决方法是根据工件材料、加工要求和刀具特性,合理选择切削参数。
浅谈数控机床加工精度误差原因分析及改进措施

中, 虽然数控机床上 能实现对几何误差的软件补偿, 但还是不能解 决根本问题 , 还是容 易出现插补误差 。 因为倾斜 直线主要 是沿平 面 上两个坐标轴方向刀具走折线而形成 , 而插补误差主要是 由脉冲均 匀程度 、 机 床分辨率 、 控制系统的动态特性 四个方面构成, 然后会造 成工件表面呈锯齿状 , 最终形成插补误差。 与此同时, 在插补运算 的 时候 , 整个加工过程 都以某 一固定点为基准 , 每执行一个过程都 以 前一个点作为基 础 , 这样连续执行多段程 序必然导致方 式编程增 量, 最后产生累积误差 , 对加工精度造成影响。 编程 的过程 中机 床产 生移动和定位误差都是 因为误差累积到一定程度的时候造成的 , 因 此我们要想让 机床回到插入参考点 的时侯把各坐标清零就应该采 取一定减小累积误差和预防堆积 的措施。 然而要想消除对 数控系统 运算的累积误差 , 就必须在操作过程 中多植入 回参考点指令 , 这样 加工精度才能得到保证 。 编程误差对机 床加工精度 的影响, 一般可 以通过减小插补间隙或增加机床分辨率的方法。 不需要进行专 门软 件的补偿 , 但是在必要的时候 , 还是可 以进行软件 补偿 的。
随着 社会的进 步 , 我 国的科学技术也 随着飞速发展 , 人们现代 化的生活 中, 机械化 已在人们的生活 中得到广泛使 用。 机械化使用 让人们从繁忙的体力劳动 中解脱 了出来 , 同时机械加工技术也得到 了飞速的发展 。 如果使用机械化 , 那么数控机床上生产的产 品, 都只 是依赖于机床 自身加工精 度。 然而在数控机加工中仍然存在许多影 响, 影响数控 机床的加工精度有很多 , 使用过程 中也会 出现很多 的 不确定因素对加工精度造成 影响。 在此本文就数控机床加工精度的 影 响 因 素 进 及 改 进 措 施 进 行 以下 探 讨 。
数控加工的误差补偿在生产中的运用分析
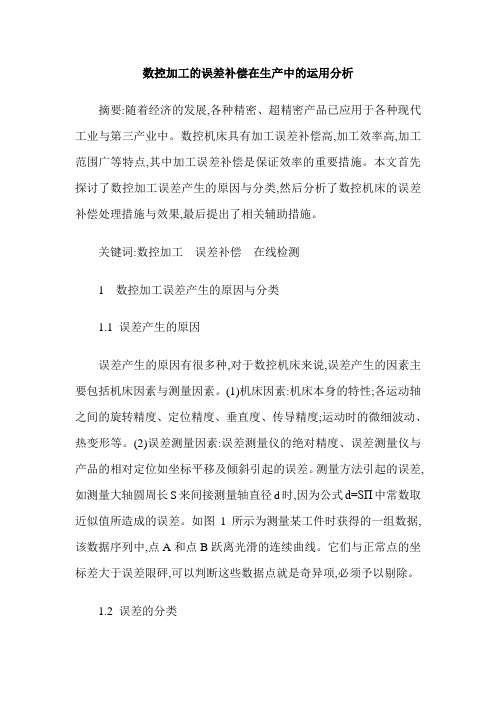
数控加工的误差补偿在生产中的运用分析摘要:随着经济的发展,各种精密、超精密产品已应用于各种现代工业与第三产业中。
数控机床具有加工误差补偿高,加工效率高,加工范围广等特点,其中加工误差补偿是保证效率的重要措施。
本文首先探讨了数控加工误差产生的原因与分类,然后分析了数控机床的误差补偿处理措施与效果,最后提出了相关辅助措施。
关键词:数控加工误差补偿在线检测1 数控加工误差产生的原因与分类1.1 误差产生的原因误差产生的原因有很多种,对于数控机床来说,误差产生的因素主要包括机床因素与测量因素。
(1)机床因素:机床本身的特性;各运动轴之间的旋转精度、定位精度、垂直度、传导精度;运动时的微细波动、热变形等。
(2)误差测量因素:误差测量仪的绝对精度、误差测量仪与产品的相对定位如坐标平移及倾斜引起的误差。
测量方法引起的误差,如测量大轴圆周长S来间接测量轴直径d时,因为公式d=SΠ中常数取近似值所造成的误差。
如图1所示为测量某工件时获得的一组数据,该数据序列中,点A和点B跃离光滑的连续曲线。
它们与正常点的坐标差大于误差限砰,可以判断这些数据点就是奇异项,必须予以剔除。
1.2 误差的分类1.2.1 几何误差包括机床、夹具、刀具的制造和磨损,尺寸链误差,机床传动链的静态和动态调整误差,产品、夹具、刀具的安装误差。
1.2.2 粗大误差粗大误差是指在一系列测量所得的数据中,经修正系统误差后如有个别数据与其他数据有明显差异,则这些数值很可能含有粗大误差。
粗大误差产生主要是由于在测量过程中系统受外界干扰不可避免会出现偶然性、突发性的测试不稳定状况。
1.2.3 系统误差系统误差是指在相同测量条件下重复测量某一被测量时,误差的大小和符号不变或按一定的规律变化,这样的测量误差称为系统误差。
系统误差对测量结果的影响较大。
因此,应认真分析,设法发现系统误差并予以消除或减小其对测量结果的影响。
对于数控机床在线检测系统来说,系统误差可以分为两类:一类是传感器系统误差,一类是机床系统误差。
两轴联动数控系统轮廓误差分析与补偿

两轴联动数控系统轮廓误差分析与补偿两轴联动数控系统在工业生产中得到了广泛应用,能够实现高精度、高效率的加工。
然而,由于各种因素的影响,轮廓误差是不可避免的。
因此,对于轮廓误差的分析与补偿显得非常重要。
本文将从两个方面进行阐述,分别是轮廓误差的分析和补偿方法。
一、轮廓误差的分析轮廓误差是指工件的实际加工轮廓与期望轮廓之间的差异。
其主要原因可以归结为以下几点。
1.机床误差:机床的几何误差和运动误差是导致轮廓误差的主要原因之一、几何误差包括机床结构的刚度、直线度、垂直度等方面的误差;运动误差包括机床运动系统的滑台间隙、伺服系统的迟滞等。
2.切削力误差:在切削过程中,刀具与工件之间的切削力会产生弯曲变形,从而导致轮廓误差的产生。
而切削力的大小与刀具的刃磨状况、切削参数等有关。
3.热变形误差:机床在工作过程中会产生热变形,导致加工轮廓的偏差。
尤其在高速切削加工中,机床热变形误差更加显著。
4.加工参数误差:加工参数的选择不合理也会导致轮廓误差的增加。
例如,切削速度过高、进给速度不合理、冷却液用量不足等。
针对以上因素,我们可以通过以下方法进行轮廓误差的分析。
1.实测法:通过使用测量仪器来对加工后的工件进行测量,对比实际加工轮廓与期望轮廓,得出轮廓误差的大小和分布情况。
2.数学建模法:通过建立机床系统的数学模型,考虑诸如机床刚度、系统的滞后等因素,对轮廓误差进行模拟与分析。
可以通过有限元法、正交多项式法等方法进行。
二、轮廓误差的补偿方法轮廓误差的补偿方法主要包括硬补偿和软补偿。
1.硬补偿:硬补偿是通过对机床进行结构调整、精度提升或者更换零部件等方式来消除或减小轮廓误差。
它的核心思想是通过调整机床本身的刚度和精度,来提高机床的加工精度和稳定性。
例如,优化机床的机械结构、改进导轨设计、提高伺服系统的动态性能等。
2.软补偿:软补偿是通过数控系统的参数设置和补偿算法来消除轮廓误差。
软补偿的优点是可以在不改变机床结构的情况下,改善加工精度。
数控机床的进给误差检测与修正方法

数控机床的进给误差检测与修正方法数控机床是现代制造业中关键的加工设备之一,具有高效、精确、灵活等优点。
然而,在加工过程中,由于复杂的机械结构和运动控制系统的限制,难免会产生进给误差。
进给误差会对零件的精度和表面质量产生直接影响,因此准确检测和修正进给误差显得尤为重要。
本文将介绍数控机床的进给误差检测与修正方法。
一、进给误差的分类及原因数控机床的进给误差主要包括常值误差和变化型误差两种。
常值误差是指在整个加工过程中,机床进给轴的位移偏差始终保持不变,主要由机床结构刚度、传动系统误差等因素引起。
变化型误差是指在加工过程中,机床进给轴的位移偏差呈周期性或随机性变化,主要由传动系统、机床导轨等因素引起。
进给误差的主要原因包括机床结构的刚度不足、传动系统的误差、机床导轨的磨损以及热变形等。
这些因素的存在导致了机床进给轴的位移偏差,进而产生加工误差。
二、进给误差的检测方法1. 静态检测方法静态检测是通过测量机床进给轴的位移偏差来判断进给误差的大小。
常用的静态检测方法包括光栅尺、激光干涉仪以及红外线测量等。
光栅尺是利用一对光学栅尺和测量头将机床进给轴的位移转化为电信号进行测量的方法。
它具有测量范围大、分辨率高、抗干扰性能强等优点,成为目前最常用的进给误差检测方法之一。
激光干涉仪则利用激光干涉现象测量进给轴的静态位移误差,它具有高精度、无接触、测量速度快等优点,适用于高要求的进给误差检测。
红外线测量方法是利用红外线光栅和接收器进行测量,通过红外光栅发射器发射的光束到达接收器时,测量红外光栅的位移,从而获得进给轴的位移误差。
这种方法具有测量范围大、精度高、适用于恶劣环境等特点。
2. 动态检测方法动态检测是通过分析工件在加工过程中的轨迹和加工力信息来判断进给误差的变化特性。
常用的动态检测方法包括切削力测量、加工轨迹分析等。
切削力测量是通过测量工件在加工过程中的切削力大小和方向来间接推算进给误差的变化规律。
这种方法适用于加工过程中切削力变化显著的情况,但要求测量设备精度高且能承受大的切削力。
数控机床操作中的误差分析与修正

数控机床操作中的误差分析与修正数控机床是当今工业生产过程中必不可少的一种高精度加工设备,它通过电子控制系统实现了对工件的精确加工。
然而,由于各种因素的影响,数控机床在实际操作中存在着一定的误差。
为了保证产品质量,提高加工效率,操作人员需要对误差进行分析,并及时进行修正。
本文将对数控机床操作中的误差进行分析,并提供修正的方法。
误差来源分析数控机床操作中的误差来源主要包括机床自身误差、刀具误差、工件装夹误差和运动控制误差等。
首先是机床自身误差。
机床自身的几何精度、运动传动系统、定位系统等方面存在一定误差,例如导轨的平行度、直线度、回转度等。
这些误差会直接影响到加工的精度和稳定性。
刀具误差是指刀具在使用过程中由于磨损而产生的误差。
刀具磨损会导致切削力的变化,从而影响到加工质量。
此外,刀具的安装和夹持也会引起误差。
工件装夹误差是指在夹持工件时产生的装夹偏差。
工件装夹不稳定会导致工件在加工过程中产生振动和位移,进而影响到加工质量。
运动控制误差包括机床伺服系统的误差和数控系统的误差。
伺服系统的误差主要来自于位置反馈误差、传动误差和非线性误差等。
数控系统的误差主要包括插补误差、指令误差和输出误差等。
误差修正方法对于数控机床操作中的误差,我们可以采取以下几种修正方法:首先是机床自身误差的修正。
在使用数控机床之前,可以通过校正设备对机床进行定期检测和校准,以确保机床的几何精度和运动传动系统的精度。
此外,在加工过程中也可以通过优化切削参数来减小机床自身误差对加工质量的影响。
其次是刀具误差的修正。
刀具的磨损是一个不可避免的过程,为了减小刀具磨损对加工质量的影响,操作人员可以根据加工情况定期更换刀具,并确保刀具的正确安装和夹持。
对于工件装夹误差,操作人员需要在夹持工件时严格按照操作规程进行操作,确保工件的稳定夹持。
如有条件,可以使用更加稳定可靠的夹具,以减小装夹误差对加工质量的影响。
运动控制误差的修正需要依靠数控系统和伺服系统的调试。
数控加工产生误差的根源及解决方案(二篇)

数控加工产生误差的根源及解决方案本文从数控机床加工过程中误差产生的根源入手,分析了各类误差产生的原因并找出了减少误差的解决方案。
数控机床是机电一体化的高科技产品,用数控加工程序控制数控机床自动加工零件,不必使用复杂、特制的工装夹具,就能够较好地解决中、小批量,多品种复杂曲面零件的自动化加工问题。
但在零件加工过程中,由于种种原因,会造成零件不合格,甚至于产生废品。
本文从加工中误差产生的原因入手,分析并找出减少误差的解决办法。
零件在数控机床上加工过程中,误差主要四个方面:一、误差是制造工艺不合理造成的;二、误差是程序编制不科学造成的;三、是工装使用不当造成的;四、是机床系统自身误差产生的。
制造工艺不合理造成的加工误差在现实生产中,由于工艺设计不合理而造成的误差一般有以下几种形式。
2.1.加工路线不合理而产生的误差由于孔的位置精度要求较高,因此安排镗孔路线问题就显得比较重要,安排不当就有可能把坐标轴的反向间隙带入,直接影响孔的位置精度。
2.2.刀具切入切出安排不当产生的误差铣削整圆时,要安排刀具从切向进入圆周进行铣削加工,当整圆加工完毕之后,不要在切点处取消刀补或退刀,要安排一段沿切线方向继续运动的距离,这样可以避免在取消刀补时,刀具与工件相撞而造成工件和刀具报废。
当铣切内圆时也应该遵循此种切入切出的方法,最好安排从圆弧过渡到圆弧的加工路线,切出时也应多安排一段过渡圆弧再退刀,这样可以降低接刀处的接痕,从而可以降低孔加工的粗糙度和提高孔加工的精度。
2.3.工艺分析不足而造成的误差普遍性的零件结构工艺性并不完全适用于数控加工中,但以下几点的特别注意:2.3.1.采用统一的定位基准,数控加工中若没有统一的定位基准,会因零件的重新___而引起加工后两个面上的轮廓位置及尺寸不协调,造成较大的误差。
2.3.2.避免造成欠切削或过切削现象,在数控车床上加工圆弧与直线或圆弧与圆弧连接的内外轮廓时,应充分考虑其过渡圆弧半径的大小,因为刀具刀尖半径的大小可能会造成欠切削或过切削现象。
数控加工中的误差及补偿方法
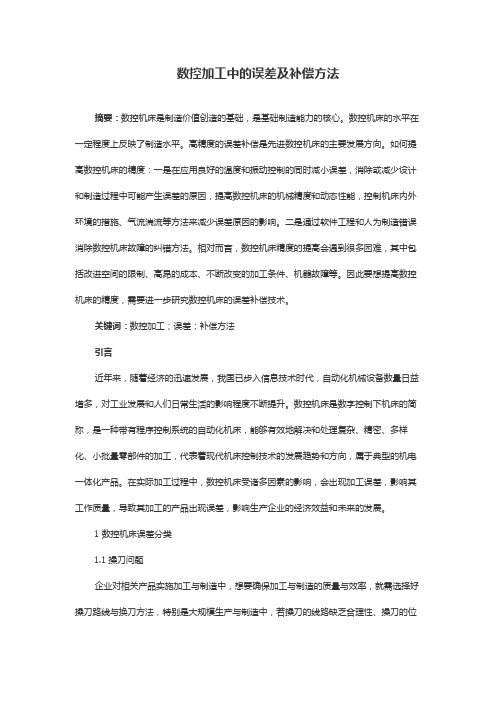
数控加工中的误差及补偿方法摘要:数控机床是制造价值创造的基础,是基础制造能力的核心。
数控机床的水平在一定程度上反映了制造水平。
高精度的误差补偿是先进数控机床的主要发展方向。
如何提高数控机床的精度:一是在应用良好的温度和振动控制的同时减小误差,消除或减少设计和制造过程中可能产生误差的原因,提高数控机床的机械精度和动态性能,控制机床内外环境的措施、气流湍流等方法来减少误差原因的影响。
二是通过软件工程和人为制造错误消除数控机床故障的纠错方法。
相对而言,数控机床精度的提高会遇到很多困难,其中包括改进空间的限制、高昂的成本、不断改变的加工条件、机器故障等。
因此要想提高数控机床的精度,需要进一步研究数控机床的误差补偿技术。
关键词:数控加工;误差;补偿方法引言近年来,随着经济的迅速发展,我国已步入信息技术时代,自动化机械设备数量日益增多,对工业发展和人们日常生活的影响程度不断提升。
数控机床是数字控制下机床的简称,是一种带有程序控制系统的自动化机床,能够有效地解决和处理复杂、精密、多样化、小批量零部件的加工,代表着现代机床控制技术的发展趋势和方向,属于典型的机电一体化产品。
在实际加工过程中,数控机床受诸多因素的影响,会出现加工误差,影响其工作质量,导致其加工的产品出现误差,影响生产企业的经济效益和未来的发展。
1数控机床误差分类1.1操刀问题企业对相关产品实施加工与制造中,想要确保加工与制造的质量与效率,就需选择好操刀路线与换刀方法,特别是大规模生产与制造中,若操刀的线路缺乏合理性、操刀的位置不够准确,就会导致换刀的时间延长,影响到生产的效率提高。
鉴于此,在操作中,需确保操作的熟练度,做好操刀线路的控制,对刀具与换刀的顺序进行合理选择,以确保机械加工的效率,并实现企业的生产效益提升。
1.2设备运行产生的误差①传统轴反转误差。
数控机床在运转的过程中,坐标轴移动或静止都会使机床驱动轴经过加速或者是减速的流程,在此过程中受设备运行的惯性作用以及驱动加、减速度的影响,容易产生加工误差。
数控加工中误差产生原因分析及解决办法

工 业 技 术随着科学技术的飞速发展,数控加工技术在机械制造业也越来越重要。
在提高生产率、降低成本、实现对各种复杂精密零件的自动化加工、保证加工质量及改善劳动条件等方面均体现出优越性。
有利于加快产品的开发和更新换代,提高企业对市场的适应能力并提高企业综合经济效益。
1 数控加工中常见误差的产生原因1.1操作人员的原因(1)程序不准确。
数控加工中有些操作工人文化水平并不高,编程的时候由于马虎不认真导致的输入错误,往往会产生巨大加工误差。
如数控车加工中,圆弧输入时G02和G03的方向搞混了,导致整个工件外形毁掉。
(2)工艺不可靠。
安排工艺不合理,也会导致加工误差甚至发生事故。
如调头螺纹件加工时,先加工了螺纹,导致调头后下道工序无法装夹进行或者装夹后影响螺纹质量,这都是工艺安排不合理造成的。
(3)对刀不认真。
数控加工质量很大程度上取决于对刀的准确程度,如果对刀不准确,加工出来的工件是不会准确的。
但是由于操作工人的责任心不够,还是经常出现对刀失误导致加工误差。
(4)装夹不牢固。
装夹的时候工件没有放平、放稳、放正都会影响加工质量,产生加工误差。
1.2机床本身的原因1.2.1滚珠丝杠副误差(1)过载问题滚珠丝杠副进给传动的润滑状态不良、轴向预加载荷太大、丝杠与导轨不平行、螺母轴线与导轨不平行、丝杠弯曲变形时,都会引起过载报警。
一般会在CRT上显示伺服电动机过载、过热或过流的报警,或在电柜的进给驱动单元上,用指示灯或数码管提示驱动单元过载、过流信息。
(2)窜动问题窜动问题是滚珠丝杠副进给传动的润滑状态不良、丝杠支承轴承的压盖压合情况不好、滚珠丝杠副滚珠有破损、丝杠支承轴承可能破裂、轴向预加载荷太小,使进给传动链的传动间隙过大,引起丝杠传动时的轴向窜动。
(3)爬行问题爬行问题一般发生在启动加速段或低速进给时,多因进给传动链的润滑状态不良、外加负载过大等因素所致。
尤其要注意的是,伺服电动机和滚珠丝杠连接用的联轴器,如连接松动或联轴器本身缺陷,如裂纹等,会造成滚珠丝杠转动和伺服电动机的转动不同步,从而使进给运动忽快忽慢,产生爬行现象。
- 1、下载文档前请自行甄别文档内容的完整性,平台不提供额外的编辑、内容补充、找答案等附加服务。
- 2、"仅部分预览"的文档,不可在线预览部分如存在完整性等问题,可反馈申请退款(可完整预览的文档不适用该条件!)。
- 3、如文档侵犯您的权益,请联系客服反馈,我们会尽快为您处理(人工客服工作时间:9:00-18:30)。
8槲 为采用插补段逼近零件轮廓 曲线时产生的 误差 , 称为 插补误 差 ; 8圆 为进行数据处理时,将小数脉冲圆整为整 整 数脉冲时产生的误差。 分析产生原因:
1 . 近误差 8 逼 1逼 近
如果零件的原始轮廓形状用列表 曲线表示 , 那
么 当采 用 近似 方程 式 去逼 近 列表 曲线 时 ,则方 程 式
i o tn o r s l e p o lm fa c r y h s p p r a ay e e man s u c fe r r o me c lC n r l mp r tt e o v r b e o u a .T i a e a c c n lz s t i o r e o ro n Nu r a o to h i P o e sn dp vd sb s s o r vn n f trn c r c f NC ma h n l. r c si ga r i e a i f r mp i g ma u a u iga u a yo n o i o c c C c i et s o Ke o d : NC ma h et l , r r P o e sn c u a y y W r s C c i s Ero , rc s i ga c r c n o
关键 词: 数控机床 误差
加工精度
An lsso o r eo r ro m e ia n r l o e s g ay i nS u c f Er o nNu rc l Co to c i Pr s n
S UN n i g Ha yn
( . e at n o c iey 1 pr D me t f Ma h r &A tm b e n ier g Z b o a o a C l g , io 2 5 1 ) n uo o i g e n , i V c t n l o e e Zb , 5 0 3 lE n i o i l
c ua f u r a yC nr e c ieT o i eo e i r n i rT o t l r  ̄g i a acr yo N me cl ot ldMahn ol sbcm shg e adhg e. ocn o errm i c i l o h h r o n sn
8逼 为所采用的近似计算方法逼近零件轮廓 曲 近 线时产生的误差 , 称为逼近误差 ;
圆整误差 8圆 是把零件几何尺寸参数计算 时 整
圆整到一个脉冲当量而引起的误差 ,它一般不会超
维普资讯
过脉冲当量的一半 。 程编误差 8程 允许 占有工件数控 加工误差 8数 编 加
维普资讯
数控加工 中的误差来 源分析
孙翰 英
( 淄博职业学院机械与汽车工程系 , 淄博 2 5 1 ) 5 0 3
摘 要: 随着数控技术 的发展 , 对数控 机床加工精度 的要 求越 来越高 , 控制误差是解决精度 的重要问 题。本文分析 了数控机床加工 中的主要误差来源 , 为提 高数控机床加工精度 , 提供 了依据。
Ab t a t sr c :Aln i e d v lp n f te Nu rc l Co t l tc n lg ,rq i me t o r c si g o g w t t e eo me t o me a nr e h oo y e u r hh h i o e n n p o e制 8定 , 给 8对 即 加 ( 编 8控 , 位 8进 , 刀 8换 , 刀……) 可见 , 。 每一项误差都会直接影响总的 误差值 , 以下分别讨论几项主要误差的产生原因。
1 程序 编制 中产 生 的误差 6程 缩 程序 编制 中的误差 8程 是有 三部分组成 的 : 编 8程 编=f 8逼 8插 8 N ) ( 近, 补, I 。
在机械制造业 中, 提高加工效率 、 降低成 本 、 提 高加工质量是竞争和发展的基础。提高数控机床的 加工精度尤为重要 ,因此必须仔细分析数控加工过 程 中的各种误差来源 , 以便采取相应措施 , 对误差进 行补偿。在数控加工过程 中, 从零件图纸到成品工件 的全过程中的各种误差都会影响到工件的精度。 在 数控 加 工 工件 的过 程 中 ,误 差 来 源 可分 两 大 类 。第一类误差是程序编制过程 中产生的误差 , 记为 8程 。 编 第二类是参与加工的整个工艺系统( 包括数控
所表示 的形状与零 件的原始 轮廓形状之 间必有差 值, 即为逼近误差。此误差 的出现发生在用列表曲线 表示 零 件轮廓 形状 的情 况之 下 。
1 . 补误 差 8 槲 2插
在 数控 系 统 中 , 用 的插 补 方法 是 有 所不 同 的。 所 当数 控 加工 零件 时 ,可 以用直 线 或 圆弧 逼 近零 件 轮
机床 、 刀具 、 具 和毛 坯 ) 夹 中引起 的 , 主要 有 控制 系统 误 差 8洲 、 工件定位误 差 8定 、 给系统 位进 对刀误 差 8对 、 刀 自动换 刀误 差 8 换 等 。 刀 数控 加 工 工 件 的误 差 8 数 应 为 上述 各 项 误 差 加 8进 、 给
廓 。当用直线或圆弧逼近零件轮廓 曲线时 , 逼近曲线 与实际原始轮廓 曲线之间的最大差值 ,即为插补误 差。此误差 出现在构成零件轮廓 曲线 的几何要素或 列表 曲线的逼近方程式 曲线与数控装 置的插补功能
不 同的情 况之 下 。 1 圆整误 差 8 圆 - 3 整
式 中:
.