数控车削加工案例分析
《数控车削加工——控制尺寸精度》——将党史教育融于课程思政教学案例
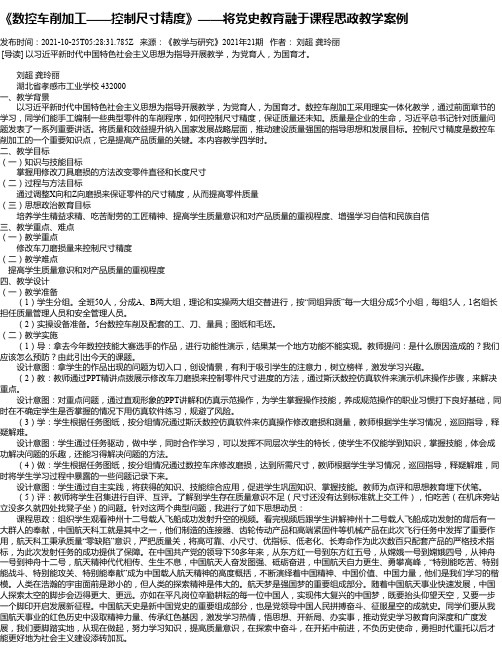
《数控车削加工——控制尺寸精度》——将党史教育融于课程思政教学案例发布时间:2021-10-25T05:28:31.785Z 来源:《教学与研究》2021年21期作者:刘超龚玲丽[导读] 以习近平新时代中国特色社会主义思想为指导开展教学,为党育人,为国育才。
刘超龚玲丽湖北省孝感市工业学校 432000一、教学背景以习近平新时代中国特色社会主义思想为指导开展教学,为党育人,为国育才。
数控车削加工采用理实一体化教学,通过前面章节的学习,同学们能手工编制一些典型零件的车削程序,如何控制尺寸精度,保证质量还未知。
质量是企业的生命,习近平总书记针对质量问题发表了一系列重要讲话。
将质量和效益提升纳入国家发展战略层面,推动建设质量强国的指导思想和发展目标。
控制尺寸精度是数控车削加工的一个重要知识点,它是提高产品质量的关键。
本内容教学四学时。
二、教学目标(一)知识与技能目标掌握用修改刀具磨损的方法改变零件直径和长度尺寸(二)过程与方法目标通过调整X向和Z向磨损来保证零件的尺寸精度,从而提高零件质量(三)思想政治教育目标培养学生精益求精、吃苦耐劳的工匠精神、提高学生质量意识和对产品质量的重视程度、增强学习自信和民族自信三、教学重点、难点(一)教学重点修改车刀磨损量来控制尺寸精度(二)教学难点提高学生质量意识和对产品质量的重视程度四、教学设计(一)教学准备(1)学生分组。
全班50人,分成A、B两大组,理论和实操两大组交替进行,按“同组异质”每一大组分成5个小组,每组5人,1名组长担任质量管理人员和安全管理人员。
(2)实操设备准备。
5台数控车削及配套的工、刀、量具;图纸和毛坯。
(二)教学实施(1)导:拿去今年数控技能大赛选手的作品,进行功能性演示,结果某一个地方功能不能实现。
教师提问:是什么原因造成的?我们应该怎么预防?由此引出今天的课题。
设计意图:拿学生的作品出现的问题为切入口,创设情景,有利于吸引学生的注意力,树立榜样,激发学习兴趣。
数控车床零件的工艺分析及编程典型实例

数控车床零件的工艺分析及编程典型实例更新日期:来源:数控工作室根据下图所示的待车削零件,材料为45号钢,其中Ф85圆柱面不加工。
在数控车床上需要进行的工序为:切削Ф80mm 和Ф62mm 外圆;R70mm 弧面、锥面、退刀槽、螺纹及倒角。
要求分析工艺过程与工艺路线,编写加工程序。
图1 车削零件图1.零件加工工艺分析(1)设定工件坐标系按基准重合原则,将工件坐标系的原点设定在零件右端面与回转轴线的交点上,如图中Op点,并通过G50指令设定换刀点相对工件坐标系原点Op的坐标位置(200,100)(2)选择刀具根据零件图的加工要求,需要加工零件的端面、圆柱面、圆锥面、圆弧面、倒角以及切割螺纹退刀槽和螺纹,共需用三把刀具。
1号刀,外圆左偏刀,刀具型号为:CL-MTGNR-2020/R/1608 ISO30。
安装在1号刀位上。
3号刀,螺纹车刀,刀具型号为:TL-LHTR-2020/R/60/1.5 ISO30。
安装在3号刀位上。
5号刀,割槽刀,刀具型号为:ER-SGTFR-2012/R/3.0-0 IS030。
安装在5号刀位上。
(3)加工方案使用1号外圆左偏刀,先粗加工后精加工零件的端面和零件各段的外表面,粗加工时留0.5mm的精车余量;使用5号割槽刀切割螺纹退刀槽;然后使用3号螺纹车刀加工螺纹。
(4)确定切削用量切削深度:粗加工设定切削深度为3mm,精加工为0.5mm。
主轴转速:根据45号钢的切削性能,加工端面和各段外表面时设定切削速度为90m/min;车螺纹时设定主轴转速为250r/min。
进给速度:粗加工时设定进给速度为200mm/min,精加工时设定进给速度为50mm/min。
车削螺纹时设定进给速度为1.5mm/r。
2.编程与操作(1)编制程序(2)程序输入数控系统将程序在数控车床MDI方式下直接输入数控系统,或通过计算机通信接口将程序输入数控机床的数控系统。
然后在CRT 屏幕上模拟切削加工,检验程序的正确性。
对数控车床上的成型刀具的车削加工工艺分析

1引言
的手 段 。下 面 就 对 4 。分 型 面 橡 胶 模具 的 5
上模 上 的 一 个腔 面 R1 5 . 8± 0 0 mm 的加 .l
工 进 行 重 点论 述 。
T0 2 M 0 S1 0 20 3 0 0;
G0 X 1 Z1. 0 . ; G71 U O. R l; 5
这样 就 可 以保 证 尺 寸和 保 持 尖边 的 要 求 了 。
3具体工艺设计
零 件 的 A面 一 端 较 易 加 工 , 再 赘述 。 不 下面就零件关键 的锥面进行详 细的分析。 3 1 确定工 艺路 线 . 由于该 部位加 工精度 要求 比较高 , 需 要 采 用 多把 刀具 才 能 完 成加 工 。 根 据 先 粗 后 精 、 先 近 后 远 、 内 外 交 叉 、 路 线 最短 等 确 定 原 则 , 艺 路 线 确 定如 下 : 工 ( ) 车 锥 面 及 小 台 阶 面 , 用 固 定 粗 1粗 采 车 循环一次成形 ; ( ) 车 锥面 及 小 台阶 面 ; 2精 , () 3精车 腔 面 R15 .8± 0 0 mm, .l 采用 成 型刀具车削 ; ( ) 削 内孔 5 m。 4钻 a r 3 2 选择 刀具及 参数 . 根 据 加 工 要 求 和 各 工 步 加 工 表 面 形 状 选 择 刀具 和 主 轴 转 数 和 进 给 量 。 () 车 锥面 及小 台 阶面 。选 用 8 的 1粗 O 菱 形 刀片 外 圆车 刀 , 刀片 型号 C MT 9 3 4 C 0T 0 UR。主轴转速 n 0 0 r mi , =10 / n 进给量 f 0 - .
R1 5 t 0 rm 处 , . 8- -0. 1 a 对此 处一 般 的 圆弧 插 补 就 不 一 定 能保 证 , 可采 用 成 型 刀 具 车 削 ,
油箱端盖零件的数控车削加工工艺分析

Q: !
Sc en a Tech i ce nd nOl Ogy n I nova on ti Her d al
工 程 技 术
油 箱 端 盖 零 件 的数 控 车 削加 工 工 艺 分 析 ①
张 鑫 宋云艳 ( 长春职 业技术学 院 吉林 长春 1 0 3 ) 0 3 3
纹 配 合 的 螺 纹 套 , 后 把 已加 工 的 零 件 旋 然 入 螺纹 套 中 , 位 、 紧 、 刀 , 精 加 工 其 定 旋 对 粗 余 未 加 工表 面 。 夹 以 及 精 加 工 走 刀 路 批量
3/ 2 其 余
施 : ①零 件 图样 上 带 公 差 的 尺 寸 , 由于 公 差 带大小不一致 , 编程 时取 中偏 差 值 。 因为 后 续 加 工 时 要 通 过 调 整 刀具 磨 损 补 偿 来 获 得 零 件 的 尺 寸 精 度 。 零 件 毛坯 为铸 件 , 工 ② 加 余 量 不 大 。 为 了 防 止 “ 差 复 映 ” 象 出 但 误 现 现 , 响 加 工 尺 寸 精 度 , 用 两 次 精 车 车 影 采 削 。 因为 零 件 加 工性 能 比较 好 , 具 磨 损 ③ 刀 也 较 小 , 时 为 了提 高加 工效 率 , 精 加 工 同 粗 采 用 同 一把 刀具 。 ( ) 定 零 件 装 夹 方案 。 零 件 为 批 量 2确 该 生 产 , 坯 为 铸 件 , 一 有 拔 模 斜 度 , 用 毛 ~般 采 普 通 的 三 爪 卡 盘 装 夹 很 难 完 成 。 虑 零 件 考 左 端 面 和 右 端 面 在 轴 向有 尺 寸 精 度 要 求 , 采 取 如 下装 夹 方 案 在 第 一 台 数 控 车 床 上 , 据 零 件 正 六 根 边 形 表 面 大 小 把 三 爪 P 三个 卡 爪 铣 成 三 - 盘
数控加工零件误差产生原因的实例分析1

数控加工零件误差产生原因的实例分析摘要:数控加工零件经常出现尺寸、精度误差,本文从机床特性、夹具设计、工艺参数、刀具及装夹以及测量过程等诸多方面入手,藉由自己的工作经验,通过实例分析了数控车削、铣削加工中常见误差的原因,以供同行交流参考。
关键词:数控加工;实例;误差分析1.引言数控加工以高效率、高精度、高度的自动化等无可比拟的技术优势,引领着机械加工制造业的潮流,然而,并非拥有了先进的数控设备就可以一劳永逸的进行高精度高效率的加工。
在加工现场经常会有零件加工下来尺寸、精度不合乎技术要求的情况。
这是因为数控机床实质上毕竟只是高度自动化、智能化的机床,要想真正发挥数控加工技术的优势,除了购置数控设备之外,还必须由技能精湛的数控操作工进行加工,此外,和传统的机械加工一样,数控加工依然离不开合理、优化的数控工艺,离不开精准科学的装夹、装配,离不开合理选用刀具材料、角度以及切削用量等等这些必备的数控技术基础。
本文通过对两个数控加工零件进行误差分析,总结了生产加工中常见的问题和误差分析技巧。
2.实例加工误差分析下面的图A为零件图,图B为加工后实测的零件图纸。
通过对比A、B两份图纸,找出尺寸、精度误差产生的原因。
2.1数控车削零件误差分析通过仔细核对上面两张车削图纸,发现以下几个方面有以下几个方面的加工误差:长度60mm 超差;Ф18孔造成锥度;Ф18孔与Ф36外圆同轴度超差;内台阶深度4mm超差;内孔表面粗糙度超差。
2.1.1 长度60mm超差的原因:(1) 长度尺寸链控制出错。
(2) 测量方面问题:图1 原零件图纸A图2数控加工后实测零件图纸B●量具选择错:按公差要求用千分尺测量,但是选用了游标卡尺。
●用游标卡尺时,测量力太大: 用游标卡尺时,引起自己测量时是对的,但是工件检验后尺寸变长了。
●读数出错了:粗心大意读错数值。
●量具存在误差:零位误差导致测量产生误差(3) 粗心大意(粗大误差)将公差看错。
(4) 刀具问题:安装时主偏角小于90°;刀具主切削刃刃磨倾斜了。
数控——教学案例三车槽和车断

令了解沟槽的种类和作用。
令掌握矩形槽和圆弧形槽的车削方法和测量方法。
令理解车沟槽时可能产生的问题和防止方法。
令掌握切断的方法。
令掌握车削沟槽零件加工的方法。
令掌握车削沟槽零件的检测。
令掌握切断时的注意事项。
槽轴,如图3- 1 所示,毛坯尺寸 50 150 mm,材料为45 号钢,分析零件加工工艺。
图3- 1 槽轴1.本任务车削矩形槽和圆形槽,并切断(4mm 处),毛坯材料为45 钢。
2.掉头,用一夹一顶加工。
3.根据尺寸公差.表面粗糙度的要求,采用先粗后精的加工方法。
切断与车槽是车工的基本操作技能之一,能否掌握好,关键在于刀具的刃磨。
⑴刃磨左侧副后刀面:两手握刀,车刀前刀面向上,同时磨出左侧副后角和副偏角。
⑵刃磨右侧副后刀面:两手握刀,车刀前刀面向上,同时磨出右侧副后角和副偏角。
⑶刃磨主后刀面:同时磨出主后角。
⑷刃磨前刀面和前角:车刀前刀面对着砂轮磨削表面。
⑴切断刀的卷屑槽不宜磨得太深,普通为0.75-1.5mm。
⑵刃磨切断刀和车槽刀的两侧副后角时,应以车刀的底面为基准,用钢尺或者直角尺检查。
⑶刃磨切断刀和车槽刀的副偏角时,要防止下列情况产生:副偏角太大,刀头强度变差,容易折断;副偏角为负值,不能用直进法切削;副切削刃不平直,不能用直进法切削;车刀左侧磨去太多,不能切割有高台阶的工件。
在零件上加工各种形状的槽的操作,叫做切沟槽。
常用的外沟槽有外圆沟槽.45 外沟槽.外圆端面沟槽和圆弧沟槽等。
车槽刀装夹是否正确,对车槽的质量有直接影响。
如矩形车槽刀的装夹,要求垂直工件轴心线,否则车出的槽壁不会平直。
⑴车精度不高.宽度较窄的矩形沟槽,可以用刀宽等于槽宽的车槽刀,采用直进法一次进给车出。
精度要求较高的沟槽,普通采用二次进给车成。
即第一次进给车沟槽时,槽壁两侧留精车余量,第二次进给时用等宽刀修整。
⑵车较宽的沟槽,可以采用多次直进法切割。
并在槽壁两侧留一定的精车余量,然后根据槽深. 槽宽精车至尺寸。
⑶车较小的圆弧形槽,普通用成型刀车削。
数控车床——教学案例五车成形面
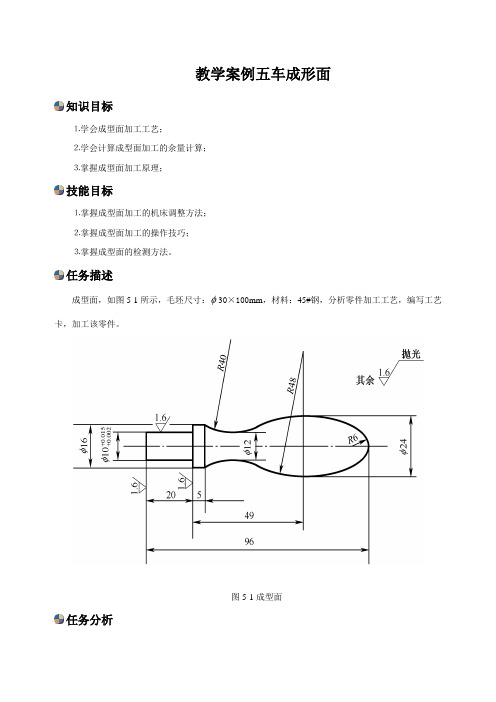
教学案例五车成形面知识目标⒈学会成型面加工工艺;⒉学会计算成型面加工的余量计算;⒊掌握成型面加工原理;技能目标⒈掌握成型面加工的机床调整方法;⒉掌握成型面加工的操作技巧;⒊掌握成型面的检测方法。
任务描述成型面,如图5-1所示,毛坯尺寸: 30×100mm,材料:45#钢,分析零件加工工艺,编写工艺卡,加工该零件。
图5-1成型面任务分析如图5-1所示,成型面材料为45钢,毛坯尺寸为 30×100mm,通过分析零件图尺寸,计算粗加工及精加工余量。
加工时,注意保证零件的同轴度。
知识准备⒈、基本原理双手控制法车成形面是成形面车削的基本方法。
1、双手控制法车成形面使用双手控制中、小滑板或者是控制中滑板与床鞍的合成运动,使刀尖的运动轨迹与零件表面素线(曲线)重合,已达到车成形面的目的。
在实际生产中由于用双手控制中、小滑板合成运动的劳动强度大,而且操作也不方便,故常采用的是用右手操纵中滑板实现刀具的横向运动(应由外向内进给);左手操纵床鞍实现刀具的纵向运动(应由工件高处向低处进给),通过这两个方向运动的合成来车削成形面。
图5-2双手控制法注意事项:⑴、本案例加工零件加工时成型面加工需要两手同时动作,控制机床实现不同方向的合成运动。
⑵、需要二次装夹,并且分为粗精加工工序,加工时要留出足够的余量。
车削成形面时要分工步进行,。
⑶、摇手柄一般用操纵中滑板(横向运动)和床鞍(纵向运动)控制实现车削。
⑷、砂布抛光。
2.成型面的车削方法成型面的车削方法,见表5-1,成型面车刀刃口是圆弧形,刀尖角α=180°。
表17-2成型面的车削方法车削方法具体要求粗车时,保证φ24、φ16、φ10及槽的尺寸,并留有精车余量。
定出R48mm和R40mm的圆弧中心位置,尺寸为49mm与17.5mm。
用小圆头车刀车φ12.5mm的定位槽。
φ16mm外圆的右端面量起,长等于5mm处并在,φ12.5mm定位槽处左右方向车出R40mm圆弧面。
铝合金薄壁套数控车削加工分析

切 削三要 素,切削速度 低 。 、进给 量慢些 、背吃刀量 小 。 些
一
些 ,完成 其余尺寸 精度制 作。力I 时的几 点注 意事项 : f 工
工件 要加紧 , 以防车 削时打滑 和扎 刀;在车削 时使用适 当 的冷却液 ;安全文 明生产 。
关键词 : 薄壁零件 ;解 决方案 ;加 工 步骤
D I 1 .9 9 J8n1 7 —6 9 .0 . 70 0 O : 5 6 / .s. 6 1 3 62 1 2 . 2 O i 1
l 引言
薄壁零件 已日益 , 泛地应 用在各 工业 部门 ,具 有重量 轻 ,节约材料 ,结 构紧凑等特 点 。但 由于溥 壁零件 的刚性 差 ,强度 弱 ,在 加 工 中极 易 变形 ,使零 件 的 形位 误 差增
形 、重 复定位精度 与增 加壁厚 。辅助夹具加 工步骤 :① 先 加 工 5外 圆 。②用 三爪 臼定心 卡盘夹住 5外 圆 ,加工 5 5 内螺纹 :先用 中心 钻定心 保证螺纹 中心与主轴 中心 同轴 , 用 中2 麻花 钻钻通 ,之后用镗 7加 工到 内螺纹 小径值 ,以 4 J 保 证M 7 圆柱度 ,再用 丝锥攻 出M 7 内螺纹 ,用 丝锥 2 x2 2 ×2
大 , 不 易 保 证 零 件 的 加 工 质 量 。在 加 工 时 , 应 充 分 考 虑 加 工工 艺 ,保 证 加 工 精 度 。
具 ,具有较好 的刚性 ,能减 少振动变形 和防止产 生振纹 。
( )外 圆粗 、精 车刀选 用6 。机 夹刀 。 ( )螺 纹刀选用 2 O 3 机夹刀 ,刀尖角度标准 ,磨损时易于更换。 5 具体操作步骤 ( )装 夹毛坯,平端面至加工要求 ,加工 ①4外 圆留 1 5 余量 。 ( )加工M 7 螺纹,加工到规定 的尺寸 值,由于 2 2 ×2
一种薄壁零件数控车削加工工艺分析与编程加工

( 工程 图 a )
( )走 刀 路 线 的选 择 4
为了保证两 内孔有 同轴 度要 求 , 这里 选择 一 次装 夹 , 所
以走 刀 路 线 的选 择 为先 加 工 内孔 , 后 利 用 芯 轴 加 工 外 圆 。 最 ( )加 工 方 案 的制 定 5 工 步 1夹 持 外 圆精 车 左 端 面 ; : 工 步 2 掉 头 夹持 外 圆 定 总 长 ; : 工 步 3 钻 3 : O通 孔 ; 工步 4 粗镗 0的内孔 留 1 m的精加工余量 ; : m f) 体 图 b实
具 , 用 芯 轴 ( 图 3 右 侧 的 台 阶实 现 零 件 的 轴 向 夹 紧 , 利 如 ) 同时 在零 件 右 侧 内壁 预 置 圆周 面 积 相 当的 厚 度 为 2 m 的 橡胶 垫 , m
N G 1 O. 1 F 0 3 0 X4 0 3 4
M O3 oo s8
N4Z 一2l
HUANG i Je
( afn stt o n ut e nl y, aj g2 0 4 ,C ia N n g I tue fId sy Tc o g N n n 1 0 6 hn ) i ni r h o i
Ab ta t h a e n lz st eNC t r ig p o e s go i — alp r , e in p ca xu e rt ep r,a d d aswi ep o . sr c :T ep p ra ay e h u n n r c s i f h n w l a t d sg ss e i f t r sf a t n e l t t rb n t li o h hh 1m ft i — le o k ic e omain,whc a r d c h u l e rd c si e o n wald w r pe e d f r t h o ih c n p o u e t e q ai d p o u t HUA HONG HN 2 i f n Z C- 1 CNC s se a d a h e e T y t m n c iv
数控车削圆弧和圆锥的加工路线分析

1 )车 圆弧 的阶梯 切 削路 线 ( 图 1 , 先粗 见 )即 车戚阶梯 , 最后 一 次走刀精 车 出圆弧 种方 法在 这 确定 了每次 走刀 的切削 深 度 a 后 , 精确 地计 算 须
定 多 次走 刀 时 的 加 工 路 线 .
图 】 阶梯 切 削 路 线 车 圆 弧
在 数 控 加工 中, 刀具 ( 格地 讲 是 刀位 点 ) 严 相
对 于 被 加 工 零 件 的 运 动 轨 迹 称 为 加 工 路 线 。 它 包
2 )车 圆 弧 的 同 心 圆 弧 切 削 路 线 ( 图 2 , 见 ) 即
先用 不同 的半 径 来 车 削 , 最后 一 刀将 所 需 圆 弧加 工出来 。此 法 在确 定 每次 的 切 削深度 a . 于 后 对 圆心角 为 9 0 的圆弧起 点和 终点 坐标较 易 确定 , 数
括 切 削加 工 的路 径 、 具 的 引人 、 出、 回 等非 刀 引 返
切削空行 程 。
3 )车 圆 弧 的 车 锥 法 坍 削 路 线 L 图 3 , 先 见 )即
车一个 圆锥 , 车圆弧 , 要 注意 车锥 时起 点 和终 再 但 点 的确 定 , 若确 定 不 好 , 可 能损 坏 圆弧表 面 , 则 也
可 能 使 加 工 余 量 留 的 过 大
车的 终刀 距s要进行 计算 。 由相似 三角形计 算 : 可
加 工路径 短 。
螭 a h Fra bibliotek围 5 车 圆 锥 的 儿种 加 L路线 图 3 车锥 { 削 路线 车 蹬 孤 击切
《数控车削加工编程与操作》思政教育案例

数控车削加工编程与操作一、概述随着现代工业技术的不断发展,数控车床已经成为工业生产中不可或缺的重要设备。
数控车床通过计算机程序控制刀具在工件上的运动,可以精确高效地完成各种复杂的加工任务。
掌握数控车床的编程与操作技能对于现代制造业的从业人员来说至关重要。
本文将以数控车削加工编程与操作为主题,结合实际案例进行深入探讨。
二、数控车削加工的基本原理1. 数控车床的结构与工作原理数控车床是一种利用数字信号控制机床自动化加工的设备。
其基本结构包括床身、主轴与主轴箱、进给系统、刀架、夹具等部件。
通过数控系统的指令控制,数控车床可以实现不同类型的加工,包括车削、镗削、钻削等工艺。
2. 数控编程的基本概念数控编程是指根据工件的加工要求,编写相应的数控程序,将工件的几何形状、尺寸和加工工艺等信息转化为机床能够识别和执行的指令。
数控编程的核心是确定刀具的运动路径和工件的加工轨迹,以实现精确的加工。
三、数控车削加工编程与操作的实际案例以某机械零件的数控车削加工为例,介绍数控编程与操作的具体步骤和注意事项。
1. 工件加工要求与工艺分析某机械零件是一种轴类零件,需要进行外圆车削、端面车削和螺纹加工。
根据零件的实际尺寸和加工要求,需要编写相应的数控加工程序。
2. 数控车削加工程序编写根据工件的加工要求,编写数控车削加工程序。
首先确定加工工艺,包括选用合适的刀具、切削参数和进给速度等;然后根据工件的几何形状,编写加工路径和刀具运动轨迹的数控指令;最后进行程序调试和优化,确保加工精度和效率。
3. 数控车床操作将编写好的数控加工程序加载到数控车床的控制系统中,进行加工前的设备调试和检查工作。
操作工人需要熟悉数控车床的操作界面和各项功能按钮,按照程序要求对机床进行设置和调整,保证加工过程的顺利进行。
4. 加工过程的监控与调整在数控车床进行加工过程中,操作工人需要及时监控加工状态,并根据实际情况做出必要的调整。
包括刀具的磨损情况、加工质量的检查、加工参数的调整等。
不规则零件数控车削加工工艺分析
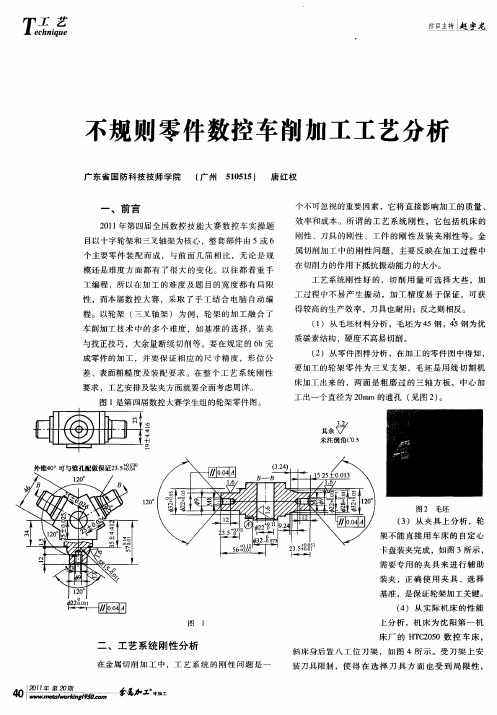
还涉 及 到轴 套 配 合 即 机座 与转轴配 合 。
( ) 从 刀具 上 分 6
析 ,为了 提 高 加 工 效 率 ,保 证 加 工 质 量 ,
后 刀 面 的磨损 高度 ,指 刀 具
后 角等 于或 小 于零 度 时 的 磨
损 量 。通常 ,在 一 定 的加 工
使 用 的 刀 具 刚 性 良
好 ,尽量 选 用 标 准 机 夹刀具 。 提供 的 刀 具 清单如 附表所 示 。
刀 具清 单
序 号 名 称 说 明
条 件下 ,都 有 一个 合 理 的 刀
具磨损限度 或叫磨钝 标准。
图 5
图 6
若 超过 些此 磨 钝 标 准 ,则 会加 快 刀具 磨 损 ,降低 加
8
9 1 0 l l 1 2 l 3 1 4
1 5
切槽 刀 外 螺 绞 车 刀 中 心钻 6 . mm钻 头 68
M 8丝 锥
1 宽外 圆切 槽 刀 mm 端 面 切 槽 刀 A . 25
切 屑 形 状 发 生 明 显 改 变 ,如 从 原 来 较 长 的 或 片 状 的 切 屑 变 为 短 碎 或 碎 粒 切 屑 ;切 屑 的 颜 色 发 生 明 显 改
试验 出每一 种刀具加_ 丁的极限参数 ,然 后下降 1% ~ 5 2 %使 用 ,确保 安全 以及效率 。 0
装夹 ,需要 使 用 全 国数控 大赛 指 定 专
用 的夹 具 进 行 辅 助 装 夹 ,夹 具 如 图 7
所示 。
2 .切 削 用量 的选择
要 能 承 受 断 续 切 削 ,才 能 使 切 削 顺 畅 , 所 以 在 刀 具
数控车削加工实例
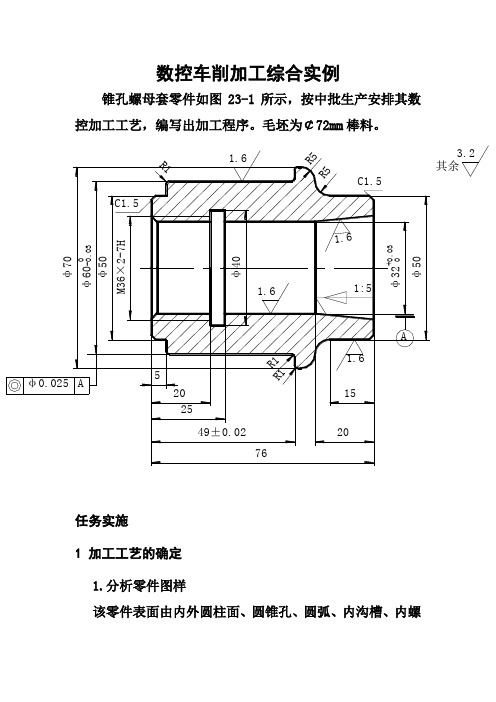
数控车削加工综合实例锥孔螺母套零件如图23-1所示,按中批生产安排其数控加工工艺,编写出加工程序。
毛坯为¢72mm 棒料。
任务实施1 加工工艺的确定 1.分析零件图样该零件表面由内外圆柱面、圆锥孔、圆弧、内沟槽、内螺其余3.2纹等表面组成。
其中多个径向尺寸和轴向尺寸有较高的尺寸精度、表面质量和位置公差要求。
2.工艺分析1)加工方案的确定根据零件的加工要求,各表面的加工方案确定为粗车→精车。
2)装夹方案的确定加工内孔时以外圆定位,用三爪自定心卡盘装夹。
加工外轮廓时,为了保证同轴度要求和便于装夹,以工件左端面和¢32孔轴线作为定位基准,为此需要设计一心轴装置(图23-2中双点划线部分),用三爪卡盘夹持心轴左端,心轴右端留有中心孔并用顶尖顶紧以提高工艺系统的刚性。
外轮廓车削心轴定位装夹方案3)加工工艺的确定(1)加工路线的确定加工路线见表23-1。
数控加工工艺路线单(2)工序30①工序卡工序卡见表。
数控加工工序卡②进给路线的确定(略)③刀具及切削参数的确定刀具及切削参数的确定见表。
数控加工刀具卡(3)工序40①工序卡工序卡见表。
数控加工工序卡②进给路线的确定(略)③刀具及切削参数的确定刀具及切削参数的确定见表。
数控加工刀具卡(3)工序50①工序卡工序卡见表。
数控加工工序卡②进给路线的确定精加工外轮廓的走刀路线如图所示,粗加工外轮廓的走刀路线略。
外轮廓车削进给路线③刀具及切削参数的确定刀具及切削参数的确定见表。
数控加工刀具卡2 参考程序编制1.工序301)工件坐标系的建立以工件左端面与轴线的交点为编程原点建立工件坐标系。
2)基点坐标计算(略)3)参考程序参考程序见表工序30参考程序2.工序401)工件坐标系的建立以工件右端面与轴线的交点为编程原点建立工件坐标系。
2)基点坐标计算(略)3)参考程序参考程序见表工序40参考程序3.工序501)工件坐标系的建立以工件右端面与轴线的交点为编程原点建立工件坐标系。
数控车床车削典型零件工艺分析

数控车床车削典型零件工艺分析数控车床是一种利用数控技术进行自动化车削加工的机床,广泛应用于制造业的各个领域。
下面将以数控车床车削典型零件为例进行工艺分析。
以加工一台螺杆为例,工艺分析如下:1.零件材质选择:根据螺杆的使用要求,选择适当的材料,常见的有碳钢、不锈钢等。
2.设计图纸:根据产品需求,在CAD软件中绘制螺杆的设计图纸,包括尺寸、形状等。
3.工艺规程编制:根据零件的设计要求,编制螺杆的工艺规程,包括车削工序、工艺参数、刀具选择等。
4.刀具选择:根据工艺规程选择适合的刀具,考虑切削力、刀具寿命等因素。
5.数控编程:根据工艺规程,利用CAM软件编写数控程序,确定刀具路径、切削深度、进给速度等参数。
6.夹紧装夹:将材料切割到合适的长度后,将工件固定在数控车床的主轴上,使用合适的夹具夹紧。
7.车削加工:根据数控程序进行车削加工,包括外径车削、内径车削、螺纹加工等工序。
8.检测与修正:每一道工序完成后,需要进行质量检测,确保零件尺寸、表面粗糙度等符合要求。
若发现问题,及时进行修正。
9.表面处理:根据产品要求,对螺杆表面进行处理,如抛光、镀层等。
10.质量检验:经过表面处理后,对零件进行再次质量检验,确保各项指标符合要求。
11.包装运输:将加工好的螺杆进行包装和标识,便于运输和使用。
以上是加工一台螺杆的工艺流程,数控车床的精度高、重复性好,能够高效、精确地进行复杂零件的加工。
在实际应用中,根据不同的零部件要求,工艺流程可能会有所不同,但总的来说,工艺分析包括材料选择、工艺规程编制、刀具选择、数控编程、夹紧装夹、车削加工、检测与修正、表面处理、质量检验、包装运输等环节。
通过合理的工艺分析和流程设计,可以实现零件的高效、精确加工,提高生产效率和产品质量。
数控车床加工程序的编制及实例分析

数控车床加工程序的编制及实例分析[内容摘要] 本文通过对数控车床加工程序的分类,掌握合适的编程方法,并对零件图样进行合理的分析,确定合理的走刀路线,合理调用G命令和安排“回零”路线,合理选择切削用量。
并通过实例分析掌握常见零件加工程序的编制。
学会编程中细节问题的处理。
[关键词] 数控车床程序精加工刀补数控车床是一种技术密集度及自动化程度很高的机电一体化加工设备,是综合应用计算机、自动控制、自动检测及精密机械等高新技术的产物。
随着数控车床的发展与普及,利用数控车床来加工零件变得越来越普遍。
在数控车削中,程序贯穿整个零件的加工过程。
由于每个人的加工方法不同,编制加工程序也各不相同,但最终的目的是为了提高数控车床的生产效率,因此对于选择最合理的加工路线显得尤为重要。
一、编程方法分类数控编程方法有手工编程和自动编程两种。
手工编程是指从零件图样分析工艺处理、数据计算、编写程序单、输入程序到程序校验等各步骤主要有人工完成的编程过程。
它适用于点位加工或几何形状不太复杂的零件的加工,以及计算较简单,程序段不多,编程易于实现的场合等。
但对于几何形状复杂的零件(尤其是空间曲面组成的零件),以及几何元素不复杂但需编制程序量很大的零件,由于编程时计算数值的工作相当繁琐,工作量大,容易出错,程序校验也较困难,用手工编程难以完成,因此要采用自动编程。
所谓自动编程即程序编制工作的大部分或全部有计算机完成,可以有效解决复杂零件的加工问题,也是数控编程未来的发展趋势。
同时,也要看到手工编程是自动编程的基础,自动编程中许多核心经验都来源于手工编程,二者相辅相成。
二、零件图样分析零件图样分析是工艺准备中的首要工作,直接影响零件的编制及加工结果。
主要包括以下几项内容:(1)分析加工轮廓的几何条件:主要目的是针对图样上不清楚尺寸及封闭的尺寸链进行处理。
(2)分析零件图样上的尺寸公差要求,以确定控制其尺寸精度的加工工艺,如刀具的选择及切削用量的确定等。
数控车削网螺纹的编程方法及案例分析

滚花是用滚花刀将工件表面滚压出直纹或网纹的方法称为滚花。
想采用螺纹刀在数控车床上完成网纹状滚花的加工,加工的思路就是多线(多头)螺纹+左右旋螺纹加工!在编制程序之前,首先要搞清楚到底要加工多少头螺纹及圆分度?还要搞清楚螺纹的导程是多少?以及左右旋螺纹的加工方法?关于头数的求解,不想向滚花刀一样,通过直径除以模数求解。
这里就灵活一点,假设想要的节距也就是网纹间距为1mm,那么头数就应该等于工件的周长除以节距。
例如直径为30时,头数为94。
关于螺纹的导程,应该拿头数乘以节距,反正就是螺纹而已,其实呢?大概就是工件的周长94.23,这样比较简单一些好计算!这样加工出来的应该是倾斜45°的网纹!关于左右旋螺纹的加工方法如下如所示,简单的一把刀就是从右往左为右旋,反之左旋!在明白以上的讲解之后,回头再想一下,关于多条螺纹的加工方法,不同的系统有不同的指令或方法。
参考程序如下:1.广数M3S300T0101G0X32Z6X30G92X29.9Z-120F94L94X29.8X29.7X29.6G0X32Z-120G92X29.9Z60F94L94X29.8X29.7X29.6G0X32Z100M302.FANUCM3S300T0101G0X32Z6#1=0WHILE[#1LT360000]DO1#3=#3-0.1X#3G32Z-120F94Q#1G32Z6F94Q#1#2=FUP[360000/94];或#2=4#1=#1+#2;每次Q的角度增量END1G0X32Z100M303.其它FANCU,又不会宏程序,可以采用调用子程序的方式来进行,编程思路或主要参考程序如下主程序:M98P1L94子程序:G32X29.9F94G0X32W1M99以上针对网螺纹或滚花如何在数控车床进行加工的一点个人思路,并不是说可取代滚花,只是探讨一种加工思路或方法而已。
比如薄壁或圆弧手柄等,是不是就要采用这中近似的方法呢?。
调节盘分析

案例10 数控车削加工调节盘一、案例内容数控车削加工调节盘。
调节盘外形图如图2—10—1所示。
二、案例要求调节盘为某模具上的产品零件,属于典型的盘类零件,生产规模为小批量加工,零件如图2—10—2所示。
零件的轨迹曲线复杂,所以加工的难度大,而且轨迹精度要求高,必须保证调节盘零件的尺寸精度、几何精度。
其它要求同与案例1。
三、案例加工使用的设备、辅具与材料1.此案例在FANUC数控系统的卧式数控车床上进行实际调试和加工。
2.配备零件锻造毛坯1件。
材料:45钢。
3.配备三爪自动定心卡盘等相关装夹辅具。
4.配备:外圆精车车刀(主偏角Kr=93°,刀尖圆弧半径R1.5)1把;内孔精车车刀(主偏角Kr=93°,刀尖圆弧半径R1)1把;切槽车刀(刀刃宽B=3mm)1把。
四、案例解析1.零件加工工艺分析(1)结构分析。
零件成型轮廓的形状结构复杂,所以不仅加工的难度大,而且轨迹精度要求高,该零件既要求准确的加工精度,而且要求保证正确的几何精度。
(2)精度分析。
在数控车削加工中,零件重要的径向加工部位有:φ187-0.015 -0.044圆柱段,二零件φ600 -0.019球体部,上述各部径向尺寸均有几何形位公差要求。
零件重要的轴向加工部位有:φ187圆柱段左端面,距球体中心的轴向长度为14±0.135mm。
零件两端的中心孔倒是实现加工上述部位的基准,必须予以保证。
具体要求参见图2—10—2。
图2—10—2 调节盘零件图(3)加工刀具分析。
由图2—10—2可知,零件空刀槽加工使用刃宽B=3内孔切槽车刀,其它刀具选择同案例6。
零件的右端面使用主偏角Kr=93°的内孔精车车刀进行切削加工,既可以保证加工基准的重合,又可以避免零件重新装夹造成不应有的误差,还节省加工中的辅助时间。
(4)毛坯余量分析。
毛坯零件为锻造成形,所以工件轮廓外的切削余量不均匀,在切削过程中会产生变形。
考虑到锻造毛坯余量的不均匀性,因此应该在数控车削前先进行常规的粗车加工,然后再进行数控车削加工。
- 1、下载文档前请自行甄别文档内容的完整性,平台不提供额外的编辑、内容补充、找答案等附加服务。
- 2、"仅部分预览"的文档,不可在线预览部分如存在完整性等问题,可反馈申请退款(可完整预览的文档不适用该条件!)。
- 3、如文档侵犯您的权益,请联系客服反馈,我们会尽快为您处理(人工客服工作时间:9:00-18:30)。
数控车削加工案例分析(二)
一图样分析:
1 材料与毛坯:材料的属性和毛坯的大小直接影响编程时的切削用量的选择和坐标尺寸的计算,因此,我们要给与足够的重视。
2 练习加工的项目:①外轮廓加工(包括圆弧的加工);
②沟槽的加工
③螺纹的加工
3 加工所用的刀具:1#刀外轮廓粗车刀
2#刀外轮廓精车刀
3#刀4mm宽切槽刀
4#刀600螺纹车刀
4 技术要求:注意未注倒角、未注公差、未注表面粗糙度的要求
5 加工工序卡
二手工编写程序:
要求:1 外轮廓的粗精加工使用G71\G70指令;
2 编制倒角程序;
3 计算牙型高度并使用G92螺纹固定循环指令
三程序的输入与修改:
把编写好的程序输入到机床中,熟练掌握用操作面板输入程序。
四程序的校验:
利用机床上的图形模拟功能校验程序,掌握定义毛坯、判断图形。
五对刀操作:
对刀操作是数控机床学习中的重点,将重点讲述。
六零件的加工:
1 空运行、
2 单段运行、
3 自动运行
七工件的检验:。