QMW00511(CHPD-S-009)OE计划的意外情况
OEE 计划停机和异常停机定义及代码
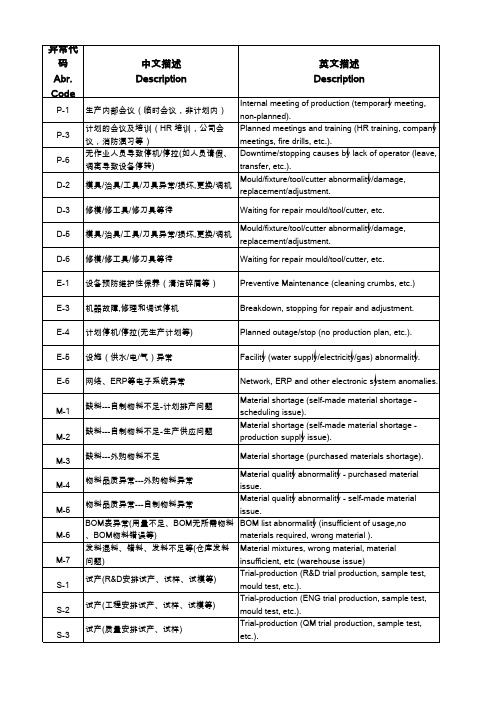
C-4 换模-按计划换模(设备)
Change of die - scheduled (equipment)
设备/生产线损失工
计划停机/停线工时
时
Planned downtime
Unplanned
downtime
●
●
●
●
●
●
●
●
●
●
●
ห้องสมุดไป่ตู้
●
●
●
●
●
●
●
●
●
●
●
● ● ● ● ● ● ●
试产(工程安排试产、试样、试模等) S-2
Trial-production (ENG trial production, sample test, mould test, etc.).
S-3 试产(质量安排试产、试样)
Trial-production (QM trial production, sample test, etc.).
replacement/adjustment.
D-3 修模/修工具/修刀具等待
Waiting for repair mould/tool/cutter, etc.
Mould/fixture/tool/cutter abnormality/damage, D-5 模具/治具/工具/刀具异常/损坏,更换/调机
M-3 缺料---外购物料不足
Material shortage (purchased materials shortage).
M-4 物料品质异常---外购物料异常
Material quality abnormality - purchased material issue.
OEE管理

生产汇总表生成
要痘疑贾罢皆瞧吃居淌趟今府稽老恭祸涡幂塞裂具设门吗炳忆惹谓冲道队OEE管理OEE管理
公式说明: 1.人员操作周期=(3600/((合格品数+废品数)/(生产时间-换产时间-异常时 间)))*模腔数 2.人员操作实际工时=(合格品数+废品数)*人员操作周期 3.额定工时=(合格品数+废品数)*额定生产周期 4.实际工时=(合格品数+废品数)*实际生产周期 5.理论工时=合格品数*额定周期/一模几腔 6.废品损失工时=废品数*额定周期 7.产出工时=合格品数/(3600/额定生产周期)*标准定员/模腔数 8.节拍达标率(单个产品)=额定周期/实际周期 9.节拍达标率(合计)=∑额定工时/ ∑实际工时
计划利用率=运行时间/设备负荷时间
时间开动率率=净运行时间/运行时间
计算负荷时间需要做的基础工作,应对所有时间做出明确的规定, 并在生产计划中有所安排。 在负荷时间确定后,计算净运行时间的关键是要求准确记录各种原始 计划外停机时间和小故障停机时间。计划外停机时间可分为五大类, 主要是为便于查找停机原因和考核部门工作。
突发故障引起之停止时间
模具、工具之交换、调整、试加工之时间。
运转时间-(加工数× C.T)
基准加工速度与实际加工速度之差。加工数×(实际C.T-基准C.T)
正常生产时作出不良品之时间。选别、修理不良品而致设备停止有效稼动之时间
生产开始时,自故障小停止至回复运转时,条件之设定、试加工等制作不良品之时间
现 场 管 理 与 改 善
合格品率
填阳庶陵馋纶奠尖橙寓晰请淄淖公郁今咯玖貌堤况骨凡寺世哆畦功影吗霹OEE管理OEE管理
设备损失结构
正 常 出 勤 时 间
OEE(设备综合效率)分析与管理ppt课件

故障是冰山的一角
“如果我们问一问为什么会发生这样的情况——为什么、为什么、—— 我们通常能找出问题,以及解决问题的方法。
灰尘、污垢、原料粘附 磨损、偏斜、松动、泄露 腐蚀、变形、伤痕、裂纹 温度、震动、声音等异常
故障
灰尘、污垢、原料粘附 磨损、偏斜、松动、泄露 腐蚀、变形、伤痕、裂纹 温度、震动、声音等异常
OEE衡量的是礁石的大小,说明应该先从哪块暗礁着手处理。
8.OEE可带来的管理效益
1.企业规划: A、可以为企业规划提供客观科學的決策依据。 B、可以为企业提供很多的增值意見和建议。
2.生产管理: A、现场实时数据的收集,建立监控管理系统。 B、对OEE数据分析,规避潜在风险,降低设备六大损失,挖掘设备最大潜能。 C、为企业精益生产管理提供可视化的生产報告。
您是不是正在制造一个不合格产品
早晨机器的启动需要花去一定的时间
二、OEE的定义及开展目的
1.OEE是什么?
OEE代表整体设备效能; 这是一种严格的机器总体性能的衡量手段,揭示时间浪费存在于哪里,统计各种时间浪费,目的在于实现改进。
总时间损失
生产转换
故障停机
传统效率衡量方式只计算了部分时间损失
计划外停机
速度缓慢
设备损坏
OEE介绍ppt课件

设备的六大损失和设备的综合效率的关系
设备
六大损失
设备综合效率的计算
负荷时间
故障 流程更换、调整
负荷时间-停止时间
利用时间
真正利用时间
创造价值的 运转时间
不 良 损 失
停
空转、间歇停顿
止 速度慢
损
失
速
度 损
废品、返工
失 启动、开机
时间利用率=
*
100
负荷时间
理论循环时间*加工数量
性能利用率=
*
100
--- 故障 --- 小停机 --- 速度降低
--- 质量返工
--- 有效的时间 = 价值产出时间
停机损 失
负
性能利用率损 荷
失
时 可间
缺陷损 失
间
利 用
时
什么是六大损失
你不可能在设备故障停机时生产出产品
设置和调整占用了太多的时间
一个微小的问题就会造成设备的停机
设备运转过快容易造成故障
您是不是正在制造一个不合格产品
停
空转、间歇停顿
止 速度慢
损
失
速
度 损
废品、返工
失 启动、开机
负荷时间-停止时间
时间利用率=
*
100
负荷时间
理论循环时间*加工数量
性能利用率=
*
100
利用时间
加工数量 - 不合格数量 合格率=
加工数量
* 100
设备综合效率的计算与解释
A:1班的实际工作时间=工厂规定的上班和下班时间
B:1班的计划休息时间=如吃饭、午休、开会等
C:1班的负荷时间=A-B(实际用于工作的时间)
QA-MWI-001异常反馈处理流程A1

《质量异常反馈处理流程》
006
确认方案
质量工程师
《品质异常分析报告》
质量工程师对临时处理方案风险及可行性进行确认,必要时升级确认。
A类不良1PCS及以上签核到经理;3PCS及以上签核到总监,10PCS及以上签核到副总
B类不良50pcs以下由工程师/主管处理,50PCS及以上签核到经理;100PCS及以上签核到总监
3.定义
3.15M1E:人Man(岗位资质)、机Machine(工装设备)、料Material(成分性能)、法Method(工艺&规程)、环Environment(温湿度&洁净度)、测Measurement(测量仪器&方法)等生产过程6要素合称5M1E,常用于根因分类。
3.25W2H:时间When、地点Where、人物Who、事件What、原因Why、结果How、程度How Much等7步法思维合称5W2H,常用于事件的详细描述。
《品质异常分析报告》
《质量异常反馈处理流程》
003
采取应急措施
分析小组
《品质异常分析报告》
分析小组责任人在接到生产或质检反馈质量异常时,15min内需到达或派人到达异常发现地点进行处理分析,确认影响范围,追溯隔离所有涉及风险批次或待确认产品进行风险评估确认,并判定是否有交期影响,如存在影响由生产知会计划进行计划调整
《品质异常分析报告》
《质量异常反馈处理流程》
005
制定临时处理方案
分析小组
《品质异常分析报告》
研发或工艺工程师对不良进行风险评估,并给出临时处理方案或计划写在分析报告内,必要时出具文件支持。如4H内未给出临时处理方案则升级到责任经理处理;1个工作日内未给出升级到总监处理,依次升级直至到总经理或异常解决。
TPM的理论与实例

TPM的理论与实例什么是TPM?TPM(Total Productive Maintenance,全面生产维护)是一种通过全员参与,实现设备全寿命周期管理的维护方法。
TPM着重于预防性维护,目标是通过减少故障和停机时间来提高设备的利用率和生产效率。
TPM的理论基础主要包括以下几个方面:1. 6大损失TPM将生产中的损失分为6大类,包括设备停机损失、设备速度损失、次品品率损失、调整和调试损失、物料更换损失以及员工安全和环境损失。
通过对这些损失的分析和解决,可以提高设备的生产效率。
2. OEE(Overall Equipment Efficiency)OEE是衡量设备绩效的指标,它是设备利用率、生产效率和产品质量的综合指标。
OEE的计算包括设备的稼动时间、产量以及良品率等因素。
TPM的目标是提高设备的OEE,以实现更高的生产效率。
3. 自律性维护自律性维护是指将维护的责任下放到操作工人,并鼓励工人进行日常设备维护和保养。
自律性维护的目的是提高设备的可靠性,并培养工人对设备维护的责任心和自我管理能力。
TPM的实例以下是两个TPM实例,分别涉及设备保养和故障预防。
实例一:设备保养在一个制造企业中,管理层决定引入TPM来提高设备的可靠性和生产效率。
首先,他们成立了一个跨职能的团队,包括生产、工程和维护等部门的代表。
这个团队开始对设备进行全面的评估和保养计划的制定。
团队首先分析设备产生的故障原因,并根据故障的频率和影响程度排序。
然后,他们制定了设备的保养计划,包括日常巡检、定期保养和维护计划。
这些计划由设备操作人员和设备维修人员共同执行。
此外,团队还组织了培训课程,培训设备操作人员进行日常设备保养和故障排除。
通过培训,工人们学会了如何进行设备的基础保养,并及时发现和解决设备故障。
这不仅提高了设备的可靠性,还培养了工人的技能和责任心。
在实施TPM后,该企业的设备的生产效率显著提高,设备故障率降低,生产线的停机时间减少,从而大大提高了生产效率和产品质量。
oo现场IE(精益)
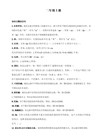
9
放 于 栈 板
10
用 叉 车 运
平均活性指数=
0+3+4+0+3+4+3+4+2+4 10
= 2.7
工程分析
流动数分析
入库累计从月初的保有量开始记录,出库累计从原始点开始 记录,从图中可以看出出库累差距计线和入库累计线的纵向 差距为停滞数量,横向差距为停滞时间 流动数分析图表
数 量 千
8 7 6 5 4 3 2 1
1)发现并消除作业性能底下的损耗时间和非运转损耗时间; 2)测试各种作业方法的优劣后,改善作业方法、工器具、设备等等; 3)评价设计及制造方式的改善程度; 4)作业人员培训的基础水平及评价 5)测试作业人员、监督人员的成果,并进行评价。 6)作好流水线作业等的作业量平衡.
标准时间的应用-计划
1)作为生产计划的基础(制造能力) 2)作为日程计划的基础(制造日程) 3)作为人员计划、加班计划、设备计划的基础 4)作为设定标准成本、成本报价等 5)外协单价的决定
工程分析
工程 着眼点
工程改善着眼点
工程 全部
1)纵观整个工程所需时间,搬运距离及人数 和各工序所需时间,搬运距离与人数时, 将改善的重点放在何处 2) 可省略的工序是哪个 3)有没有可同时进行的工序 4)有没有将工序顺序交换,来减少工序数,时 间,人员的可能性 5)是不是认为现在的工序是最好的工序
抽样检验与可靠性试验

抽样检验与可靠性试验抽样检验课程內容简介:质量管理的基础思想抽样检验OC曲线说明GB2828抽样表零缺陷抽样计划表如何将GB2828、105E表转换成零缺陷抽样计划计量值抽样检验可靠性实验质量管理的基础思想1质量是生产出来的,检验只是后盾。
2选择合格的供应商、控制生产过程的稳定性,保证供应链的整体水平,让检验工作成为质量水平的验证。
3运用统一的测量语言/术语建立质量标准(举例)。
4测量仪器应与产品的公差要求对应。
何时需要采用全检?生产过程不能保证达到预先规定的质量水平,不合格品率大时。
不合格品漏检有可能造成人身事故或对下道工序或消费者带来重大损失时。
检查效果比检查费用大时,多采用全检,例如能用效率高、精度稳定的“过─止〞量规检查时。
全检花费的时间和费用高并限制在非破坏性检查项目的检查。
全检时,很少有产品的性能指标全部检查,一般只对特定检查项目进行检查,所以即使全检,也不一定确保一个不合格品也没有。
全检是在有限期间內检查大量产品,难免误检,因此尽量使用样板和自动检验,完善管理和使作业合理化。
何时需要使用抽样检验?产量大、批量大、并且连续生产时无法进行全数检验;允许一定数量的不合格存在;希望减少检验时间和检验费用时;刺激生产者注意改进质量时;破坏性检查全检不允许时。
何时需要采用抽样检验?间断交易,以往批质量情报不充分时;质量水平达不到,全检又没有必要,只对坏批进行全检,希望改善平均质量时;根据检查结果选择供方时,批间质量不稳定或批数不多,转入间接检查不充分时;抽样检查与全检相比,受检单位产品数少,检查项可多些,但是同一质量的产品批有可能判合格,也有可能判不合格。
而且,当不合格品率很小时,很难抽出不合格品。
检验一般的工作程序:准备阶段决定检查单位决定检查项目决定试验方法决定质量判定标准决定在生产过程那个阶段检查决定全检、抽检还是无试验检查决定质量指标选择抽样表(计数、计量和抽样类型)实施阶段决定批的构成决定抽样方法决定批处理方法整理阶段决定检查结果的记录方法。
WCM-OEE

-2-
OEE - 设备综合效率
衡量范畴
OEE是衡量计划时间段内生产线/设备的生产效率的指标
不包括
OEE不衡量计划外的理论潜在时间的利用能力,例如,设备无生产计划的时间,不包 括在计算之内。
1.0 oee
EFESO © 1999 - 2016
-3-
OEE - 设备综合效率
用于
衡量生产线/设备效率 识别并量化损失
了解损失是OEE真正的威力
典型的损失指切换、故障、短停、速度损失、缺陷(随后详细定义损失) 了解这些损失,能够帮助我们抓住重点,进而改进OEE
100% 90% 80% 70% 60% 50% 40% 30% 20% 10% 0%
1.0 oee
37.5 62.5
100%
90%
80%
70%
60%
50%
EFESO © 1999 - 2016
时间
-6-
OEE计算简便
OEE =
合格品产量 理论产量
1.0 oee
EFESO © 1999 - 2016
-7-
例如...
...计算某周的OEE
计划生产时间 = 120 小时 最大生产速度 = 100 件/小时 理论最大产量 = (100 x 120) = 12000 件 实际产量 (无缺陷) = 7500 件
EFESO © 1999 - 2016
- 15 -
别忘记定义操作工 短停 速度损失 缺陷
定义
从一种产品切换到另一种产品所需的时间 计划外停机,需要维护人员进行修理 由于物料供给不及时造成的计划外停机 由于操作员缺席造成的停机 划外停机,可通过操作员重启设备解决 由于设备运转达不到最大速度造成的损失 生产出的产品不符合规格要求
潜在的失效模式及后果分析

很高
20个 每1000件
10个 每1000件 2个 每1000件
8
7 6 5 4 3
中等
0.5个 每1000件 0.1个 每1000件 0.01个 每1000件
低
2019/4/10
0.001个 每1000件
通过预防控制消除了失效
2
1
22
很低
探测度(D)推荐评价准则表
探测性 评价准则 绝对不可能 不能找出潜在原因及后续的失效模式 很极少 极少 很少 很极少找出潜在原因及后续的失效模式 极少找出潜在原因及后续的失效模式 很少找出潜在原因及后续的失效模式 探测 度数(D) 10
关键日期 产品图纸发布日期
2019/4/10
33
FMEA日期
填入編制FMEA原始稿的日期及最新修訂的日期。
原始稿日期
第一版
第二版 第三版 最新修訂日期
2019/4/10 34
核心小組:
列出有权限参与或执行這 項工作負責人姓名和单位 (建义將所有小組成員名字、 单位、电话号码、地址等 另行列表)。
9 8 7
少
中等 中上 多 很多 几乎肯定
2019/4/10
少找出潜在原因及后续的失效模式
中等找出潜在原因及后续的失效模式 中上找出潜在原因及后续的失效模式 多找出潜在原因及后续的失效模式 很多找出潜在原因及后续的失效模式 几乎肯定找出潜在原因及后续的失效模式
6
5 4 3 2 1
23
对FMEA的几点要求:
填入負責编制FMEA工作的工程師姓名、电话及 所在公司名称。
姓名:XXX 部门:XXX 电话:XXX 公司名称:XXX
2019/4/10
OEE计算及损失分析

某产线计划每班生产8小时 (480分钟).其中计划用餐 时间为40分钟
生产时间 = 480分钟 − 40分钟 = 440分钟
8. 清洁消毒ቤተ መጻሕፍቲ ባይዱ失
生
清
产
洁
计
时
消
划
间
毒
停
损
机
失
损
失
7.
8.
9.
非 计 划 停 机
运 行 时 间
损
失
10. 11.
• 是指从一种产品至另一种产品 换产导致的停机损失
• 包括:
损
失
10. 11.
• 包括:
➢ 生产准备
– 退仓,5S,会议,交接班,清场,卫生 – 工艺要求的准备工作 –换标签,换缸,更换辅助物料(油墨,色带) – 在生产时间内的计划维护保养
➢ 轮岗 ➢ 培训
10. 非计划停机损失
生
清
产
洁
计
时
消
划
间
毒
停
损
机
失
损
失
7.
8.
9.
非 计 划 停 机
运 行 时 间
损
负 荷 时
用 餐
间
生 产 时 间
1. 2. 3. 4.
5.
6. 7.
设备综合效率=价值运行时间/生产时间
清
洁 消 毒 损 失
计 划 停 机 损
失
8.
9.
非 计 划 停 机 损 失
运 行 时 间
速 度 损 失
有 效 运 行
质 量 损
时失
间
价 值 运 行 时
间
10. 11. 12. 13. 14. 15.
综合设备效率OEE

主要内容
为什么引进OEE 如何计算OEE
八大损失及改进措施
主要内容
为什么引进OEE 如何计算OEE
八大损失及改进措施
为什么引进OEE
OEE的概念
OEE(Overall Equipment Effectiveness),即设备 综合效率,最早由日本能率协会顾问公司提出,OEE是用 来考察设备在时间上的利用情况,也考察由于操作和工艺 造成的性能降低和合格品率的问题,更全面地体现了全员 参与关注设备的思想。
1、设备利用率:(计算TEEP时用)
在整个日历时间中去除休止时间后的可利用时间所占的比例。
设备利用率=
日历时间-休止时间
日历时间
×100% =
负荷时间
日历时间 ×100%
总日历时间
计划停机时间(年修、定修、节假日) 非设备因素停机时间(停电、待料)
休止时间
负荷时间(总的可用生产时间)
如何计算OEE
如何计算OEE
OEE计算困惑:性能开动率为何会大于1
1、原则上,理论加工时间不大于实际加工周期,即速 度开动率是不会大于100%的;
2、国内企业经过不断升级改造或为超产拼速度,许 多设备当前加工运转速度超出了设计速度;
3、这样如果仍使用原有数据为基准,则使速度开动 率超过100%,进而使性能开动率超过100%。
为什么引进OEE
OEE和TEEP的总体水平
世界先进企业的OEE水平 80-85%
世界先进企业的TEEP水平 70-75%
74.6-%-77.4% 59.7%-63.5%
69.3%-72.4% 57.2%-60.3%
考察主要设备的 OEE值和TEEP值, 有利于企业对当前 设备管理情况有一 个总体认识。
DFMEA失效模式分析

手冊。
B. FMEA概要介绍
FMEA的应用:
设计FMEA: 针对产品本身,产品设计、开发时期的分析技术。 主要是设计工程师和其小组应用。
系统FMEA:针对产品系统,考虑系统和系统间交互作用。 过程FMEA:
针对产品的实现过程,过程开发设计的分析技术。 主要是过程(制造)工程师和其小组应用。 程序/项目 FMEA: 针对程序/项目,程序 /项目开发设计的分析技术。
会有效地运用 FMEA;
FMEA概要介绍
FMEA是一组系统化的工作,其目的是:
发现、评价产品/过程中潜在的失效及后果; 找到能够避免或减少这些潜在失效的控制措施;
将以上过程文件化,作为过程控制计划的输入。
FMEA的发展历史:
FMEA起始于60年代航空航天工业项目。 1974年美海军用于舰艇装备的标准《舰艇装备的失效模式和后果分析实施程》,首先 将它用于军事项目合约。 1970年晚期,汽车工业将FMEA作为在对其零件设计和生产制造的会审项目的一部分。
D-FMEA:
零件功能单
零件功能单
零件编号: 零件功能: 设想哪些是零件要起的作用? 哪些是零件不必须的作用? 列出所有作用,并与限制因素相区别。 确定当零件的某个功能不工作时的影响并初步给出严重度数。 列出所有功能 功能:动词+名词 1 2 3 保持清洁 保护顾客 规范 程度?时间? 0.06mm 与相邻零件 顾客可接触处无毛边 6 9 严重度 零件名称:
2
灯泡 总成 D
3 4
灯罩 A
1 5
电池 B
4 5
极板 E +
设计FMEA
__系统 X 子系统 __ 零部件
D-FMEA表头(1-10)
《TPM全员生产维护》试题 - 副本答案

《TPM全员生产维护》试题-副本答案姓名:考分:精益管理试题(考试时间:90分钟满分:100分)一、单项选择题1.全员生产维护英文缩写为()。
A.TQMB.TPSC.TPMD.QFD2.制作自主维护临时基准属于自主保全的第()阶段。
A.二B.三C.四D.五E.六3.下列哪项不是强制劣化()。
A.汽车强制报废B.超负荷工作C.电脑强行关机D.中国足球的假球黑哨4.零故障对策中确定基本条件,遵守使用条件在TPM八大支柱中哪一个支柱中进行()。
A.自主维护 B.专业维护 C.个别改善 D.设备初期管理E.事务改善5.一台设备每天的可用时间是24小时,计划停机时间是4小时,设备故障停机损失2小时,性能损失时间2小时,当天生产良品率为98%,则该设备当天OEE为()。
A.68.6%B.78.4%C、76.8%D.80.3%6.下列哪一项反映设备的时间利用情况,度量了设备的故障、调整等项停机损失()。
A.时间稼动率B.性能稼动率C.设备稼动率D.设备故障时间7.设备从启动到正常工作所需要的时间属于哪一种损失()。
A.速度低下损失B.空转损失C.启动稳定损失D.换型损失8.75%的设备瘫痪是由()两大因素造成的。
A.操作不当B.设计不合理C.污染物D.缺少润滑油9.()反映了设备的性能发挥情况、度量了设备的短暂停机、空转、速度降低等性能损失。
A.时间稼动率B.性能稼动率C.设备稼动率D.设备故障时间10.培养防止劣化的能力处于自主维护中哪一阶段()。
A.初期清扫B.发生源、困难部位对策C.制作自主维护临时基准D.自主点检E、总点检二、多项选择题1.TPM特点包括()。
A.全员B.全系统C.全效率D.持续改善2.TPM三大管理思想()。
A.预防哲学B.“零”目标C.PDCA循环D.全员参与小组活动E.目视化3.TPM活动两大基石是()。
A.持续改善B.六西格玛活动C.领导作用D.5SE.小组活动4.零故障对策中改善设计上的弱点与哪些支柱关系最为密切()。
OEE的定义

OEE的定义一般,每一个生产设备都有自己的最大理论产能,要实现这一产能必须保证没有任何干扰和质量损耗。
当然,实际生产中是不可能达到这一要求,由于许许多多的因素,车间设备存在着大量的失效: 例如除过设备的故障,调整以及设备的完全更换之外,当设备的表现非常低时,可能会影响生产率,产生次品,返工等。
OEE是一个独立的测量工具,它用来表现实际的生产能力相对于理论产能的比率。
国际上对OEE的定义为:OEE是Overall Equipment Effectiveness(全局设备效率)的缩写,它由可用率,表现性以及质量指数三个关键要素组成,即:OEE=可用率X 表现性X质量指数。
其中:可用率=操作时间/ 计划工作时间它是用来考虑停工所带来的损失,包括引起计划生产发生停工的任何事件,例如设备故障,原料短缺以及生产方法的改变等。
表现性=理想周期时间/ (操作时间/ 总产量)=(总产量/ 操作时间)/ 生产速率表现性考虑生产速度上的损失。
包括任何导致生产不能以最大速度运行的因素,例如设备的磨损,材料的不合格以及操作人员的失误等。
质量指数=良品/总产量质量指数考虑质量的损失,它用来反映没有满足质量要求的产品(包括返工的产品)。
利用OEE的一个最重要目的就是减少一般制造业所存在的六大损失:停机损失、换装调试损失、暂停机损失、减速损失、启动过程次品损失和生产正常运行时产生的次品损失。
下面表格是六大损失的说明及其与OEE的关系:六大损失类别OEE损失类别事件原因注释停机损失有效率刀具损坏设备突发故障原料短缺等表示设备因为一些大的故障,或者突发事件所引起的停工。
换装调试损失有效率改变工具设备预热等因改换工具,生产线调试等准备工作而造成的损失,一般位于工位安排,生产布置这一阶段暂停机损失表现性不通畅的生产流导轨阻塞清洁,检查一般指停工5分钟以下,并不需要维护人员介入的停工减速损失表现性低于设计产能运行设备磨损员工技术因素等任何阻止设备达到设计产能的因素启动过程次品损失质量指数报废、重工等设备预热,调节等生产正式运行之前产生的次品生产过程次品损失质量指数报废、重工等生产稳定进行时产生的次品表一六大损失与OEE的关系OEE计算实例我们举一个例子来说明OEE的计算方法:设某设备某天工作时间为8h, 班前计划停机15min, 故障停机30min,设备调整25min, 产品的理论加工周期为0.6 min/件, 一天共加工产品450件, 有20件废品, 求这台设备的OEE。
QHS4009-2002 电器设备挂牌锁定制度

2
Q/HS 4009—2002
i) 作业负责人不在现场时,可以指定代理人,但不得将职责分解; j) 如果在一个班内的有关电器设备挂牌锁定的作业活动还没有结束,作业个人或负责人在交班时
应向接班人员对电器设备挂牌锁定进行交接。 5.2 电气人员的职责
主要包括: a) 应仔细检查电气设备的电力控制和连接部分,确保所有可能存在电力源的地方都被辨识出; b) 作业之前,应准备好适用的个人防护设备并检测是否合格,如需监护人员,则应确认监护人员
的到位; c) 应将控制电器设备主电源闸门断开,切断电源; d) 应将容量大的电容器、电感器彻底放电; e) 应通知操作或维修人员做现场启动试验,确认设备已不能启动后,则断开断路装置,进行挂牌
接给设施的管理人员; e) 应完成电器设备挂牌锁定的表格。 6.2 电气人员的职责 主要包括: a) 应检查电器设备和维修现场,确认设备的电力部分的连接、绝缘、接地的安全; b) 应向操作和维修作业人员确认是否可以取消电器设备挂牌锁定; c) 作业之前,应准备好适用的个人防护设备并检测是否合格,如需监护人员,则应确认监护人员
3 总则
3.1 单位在购买、引进电器设备时,应确保该电器设备能够适用于挂牌锁定制度。 3.2 在对以空气开关、闸刀、断路器、漏电开关等电器设备作为电力连接装置的电气设备进行检查或维 修作业之前,均应实施挂牌锁定措施。
4 组织和管理
1
Q/HS 4009—2002
4.1 一般电器设备 一般电器设备的挂牌锁定由检查或维修作业人员申请和参与,设施的电气人员负责实施电器设备的
失效模式效应分析

EEMS Suzhou Co Ltd
2.1
设计FMEA
◆ D-FMEA: ◇ 针对产品本身,产品设计、开发 时期的分析技术。 ◇ 主要是设计工程师和其小组应用。
16
Property of EEMS Suzhou. Shall not be copied or reproduced to any other format without prior permission from EEMS Suzhou
EEMS Suzhou Co Ltd
1.4
系统与子系统
接口和交互作用
系统
子系统A
环境
子系统B
子系统C
子系统D
整机\部件\零件的展开
14
Property of EEMS Suzhou. Shall not be copied or reproduced to any other format without prior permission from EEMS Suzhou
EEMS Suzhou Co Ltd
FMEA
失效模式效应分析 Failure Mode & Effects Analysis
1
Property of EEMS Suzhou. Shall not be copied or reproduced to any other format without prior permission from EEMS Suzhou
9
Property of EEMS Suzhou. Shall not be copied or reproduced to any other format without prior permission from EEMS Suzhou
史上最全的全局设备效率(OEE)介绍!

史上最全的全局设备效率(OEE)介绍!全局设备效率是Overall Equipment Effectiveness,简称OEE。
一般,每一个生产设备都有自己的理论产能,要实现这一理论产能必须保证没有任何干扰和质量损耗。
OEE就是用来表现实际的生产能力相对于理论产能的比率,它是一个独立的测量工具。
OEE是由可用率,表现性以及质量指数三个关键要素组成:OEE = 可用率X 表现指数X 质量指数可用率:可用率=操作时间/计划工作时间它是用来评价停工所带来的损失,包括引起计划生产发生停工的任何事件,例如设备故障,原材料短缺以及生产方法的改变等。
计划工作时间一般是:总时间- 法定假日- 双休日+ 加班时间overtime - 计划非工作时间planned stoppages注:计划非工作时间,如公司成立纪念日休息,所在城市准备举办重大赛事要求固定时间停产,这些大多数都是不可抗拒,不可改善的因素。
操作时间就是计划工作时间再减去生产上的停顿stoppages (比如机器突然坏了,突然电断了,没有原料供应,没有好用的刀具可换,换模,设备由于上游缺料或者下游满料停下line constraints 等原因,这些大多都是可改善的因素)注:可用率这项是大家产生不同理解,解释最多的项。
强烈建议一个公司内部统一这一项的定义,否则无法测量,分析,管理。
很多情况下,为了使OEE提高,现场会把生产上的停顿归为计划非工作时间。
且理由很充分。
比如,小A今天一大早就计划了今天要换3次模,一次一小时。
小A说,这段时间不生产是计划中的,所以应该是计划非工作时间。
听起来似乎没有什么不妥,但是这个换模时间是可以缩短的,改善的。
不能就简单算作计划非工作时间。
如果我们像小A说的那样做,那么换模时间哪怕长到4小时、8小时一次,OEE 都不会影响。
换模时间长这个问题大家也不会去关注。
表现指数:表现指数=理想周期时间/(操作时间/总产量)=(总产量/操作时间)/生产速率表现性是用来评价生产速度上的损失。
- 1、下载文档前请自行甄别文档内容的完整性,平台不提供额外的编辑、内容补充、找答案等附加服务。
- 2、"仅部分预览"的文档,不可在线预览部分如存在完整性等问题,可反馈申请退款(可完整预览的文档不适用该条件!)。
- 3、如文档侵犯您的权益,请联系客服反馈,我们会尽快为您处理(人工客服工作时间:9:00-18:30)。
操作类型Operation
文档类型Type of document 生效期Valid from
计划Scheduling
作业指导书Work instruction
Author: Telephone:
Release-No.: LILI 779
QMW00-511(CHPD-
1. 目的
OE 计划流程描述
1. Purpose
Description of schedule Process for OE.
2. 适用范围
计划,生产和生产运营部
2. Area of application
Scheduling, Production & P.O. department.
3. 责任
计划,生产和生产运营部的员工
3. Responsibilities
Employees from Scheduling, Production & P.O. Department.
操作类型Operation
文档类型Type of document 生效期Valid from
计划Scheduling
作业指导书Work instruction
Author: Telephone:
Release-No.: LILI 779
QMW00-511(CHPD-
* -可用能力优先OE 于替换市场
注释 : 意外情况要通知质量经理和生产经理
操作类型Operation
文档类型Type of document 生效期Valid from
计划Scheduling
作业指导书Work instruction
Author: Telephone:
Release-No.: LILI 779
QMW00-511(CHPD-
A B
C
D
E
F
G
H
I
J
K
L
* 可能生产数量 表示有可用的的材料和设备来生产 (**)
** 这些可用的材料和设备优先用于OE
操作类型Operation
文档类型Type of document 生效期Valid from
计划Scheduling
作业指导书Work instruction
Author: Telephone:
Release-No.: LILI 779
QMW00-511(CHPD-
* - available capacity will be allocated with priority to OE in stead replacement Note : in case of contingency QM and Production Manager will be announced
操作类型Operation
文档类型Type of document 生效期Valid from
计划Scheduling
作业指导书Work instruction
Author: Telephone:
Release-No.: LILI 779
QMW00-511(CHPD-
A
B
C
D
E
F
G
H
I
J
K
L
* Possible production represents all that can be done with available materials, machines (**)
** These materials will go with priority to the OE tires
操作类型Operation
文档类型Type of document 生效期Valid from
计划Scheduling
作业指导书Work instruction
Author: Telephone:
Release-No.: LILI 779
QMW00-511(CHPD-
相关文件Related documents:
Emergency Concepts from Plant Operation, Engineering & Maintenance Dept PO,工程&维修 部的紧急流程.。