浅析油井杆管防偏磨措施及应用
影响抽油井管杆偏磨的原因分析及治理措施

影响抽油井管杆偏磨的原因分析及治理措施随着石油工业的不断发展,抽油井已经成为了石油生产的重要设备之一。
抽油井管杆作为抽油井的主要组成部分,其运行状态直接关系到油井的生产效率和安全稳定性。
抽油井管杆偏磨问题一直是困扰产油公司的一个难题。
本文将对影响抽油井管杆偏磨的原因进行分析,并针对这些原因提出相应的治理措施,以期能够更好地解决这一难题。
1.1 技术方面原因影响抽油井管杆偏磨的一个重要原因是油井技术设计不合理。
在油井设计过程中,如果未能充分考虑到地质条件、油井结构和油井作业环境等因素,就容易导致管杆的偏磨。
如果油井地质条件复杂,设计时未考虑到地层变化对管杆的影响,就容易导致油井管杆的偏磨。
技术设计方面的不合理性是导致抽油井管杆偏磨的一个重要原因。
抽油井管杆的材料及加工质量问题也是导致管杆偏磨的原因之一。
抽油井管杆通常是由钢材制成,如果管杆的材料质量不合格或者加工过程中存在问题,就容易导致管杆的偏磨。
管杆表面存在缺陷、夹杂等问题,就容易引起管杆的偏磨,从而影响抽油井的正常运行。
抽油井管杆的润滑问题也是导致管杆偏磨的一个重要原因。
由于抽油井的特殊工作环境,管杆在运行过程中常常会受到高温、高压、高速等因素的影响,容易导致管杆表面润滑不足,从而造成管杆的偏磨。
在抽油井的作业过程中,合理选择润滑剂、加强对润滑状况的监控和管理,对于减少管杆的偏磨是非常重要的。
抽油井作业工艺不当也是导致管杆偏磨的一个重要原因。
抽油井在进行抽取作业时,如果未能严格控制抽取速度和频率,就容易导致管杆的过度磨损,从而影响抽油井的正常运行。
在抽油井作业过程中,合理控制抽取速度和频率,对减少管杆的偏磨非常重要。
二、治理措施分析对于油井技术设计不合理导致的管杆偏磨问题,可以通过改进设计方案来加以解决。
在设计油井时,充分考虑地质条件、油井结构和油井作业环境等因素,采用适当的技术手段来解决管杆偏磨的问题。
2.2 材料方面的治理措施针对管杆材料及加工质量问题,可以通过加强对材料质量的监控和管理,严格执行相关标准,采用优质的原材料,严格控制加工工艺,避免管杆表面存在缺陷、夹杂等问题,从而提高管杆的使用寿命。
抽油机井杆管偏磨原因分析及防治措施

抽油机井杆管偏磨原因分析及防治措施抽油机井杆管是油田开采中的重要设备,其主要作用是将下面的油液抽到地面。
然而,在使用过程中,井杆管常常会出现偏磨现象,这种现象会严重影响设备的正常运行,甚至带来安全隐患。
因此,为了保障油田的正常生产,必须对抽油机井杆管偏磨进行分析和防治。
1、普遍磨损在抽油机井杆管工作的过程中,其表面会产生一定的磨损,这是一种正常的现象。
由于油泥中含有微小颗粒,抽油机井杆管在长时间使用后,其表面会逐渐被磨损。
这类现象普遍存在于使用时间较长的井杆管上。
2、轴向载荷不均轴向载荷不均是导致井杆管偏磨的主要原因之一。
在抽油机运转的过程中,由于油田地质条件和地面装备的差异等原因,井杆管所承受的载荷不是完全均匀的,而是存在一定的偏差。
这种偏差会导致井杆管产生一定的倾斜,从而出现偏磨。
3、水平运动不稳定抽油机井杆管在工作中,其水平方向的运动也很容易产生不稳定的情况。
当井杆管在水平方向上发生偏差时,其表面与钻井孔壁摩擦会增大,这种情况会加速井杆管的磨损,进而导致偏磨的产生。
1、优化井口设备井口设备是导致抽油机井杆管偏磨的重要因素之一。
为了降低其不稳定的运动状态,可以在井口区域安装合适的导向器和限位器,并合理安排布置井口设备。
2、控制水平动态控制抽油机井杆管的水平动态也很有必要。
可以通过在井口区域增加一定的支撑装置来达到控制井杆管垂直度的目的。
3、选择合适的材料为了延长抽油机井杆管的使用寿命,可以选择一些耐磨性能极佳的材料进行制造。
这样能够有效减缓井杆管表面的磨损速度,从而有效防止偏磨的发生。
4、及时维护保养为了保证抽油机井杆管的正常运转,应定期对设备进行维护、保养。
在进行维修时,要及时更换磨损严重的部件,避免设备使用过程中出现安全隐患。
总之,抽油机井杆管偏磨现象的发生对油田开采非常不利,应对该问题进行严肃认真的对待和解决。
利用一些科学的治理措施,能够在一定程度上延长设备的使用寿命,提高工作效率,为油田的生产带来更多的福利。
抽油机井杆管偏磨原因分析及防治措施

抽油机井杆管偏磨原因分析及防治措施一、引言抽油机是油田生产中的重要设备之一,它通过上下运动的井杆管从井下将油液送到地面。
由于井杆管在使用过程中会出现偏磨,导致其使用寿命减少,甚至影响正常的生产运行。
对于抽油机井杆管的偏磨原因进行分析,并提出相应的防治措施是非常重要的。
本文将对抽油机井杆管偏磨原因进行分析,并提出相对应的防治措施。
二、抽油机井杆管偏磨原因分析1. 润滑不良抽油机在运行时,井杆管会不断的上下运动,如果润滑不良,摩擦会增大,从而导致井杆管表面的磨损加剧,造成偏磨。
如果使用的润滑油质量不好,也会加速井杆管的磨损速度。
2. 杂质侵入在油田生产中,井下环境恶劣,很容易有杂质进入井杆管内部,这些杂质会在井杆管与其搭扣的接触部位造成磨损,导致偏磨的发生。
3. 井杆管使用寿命井杆管属于易损耗部件,长时间的使用和摩擦会导致其表面出现磨损,从而形成偏磨。
4. 操作不当在使用抽油机的过程中,如果操作不当,如过度加速或减速,会导致井杆管的磨损速度增加,从而形成偏磨。
5. 环境因素井下环境非常恶劣,地质条件复杂,可能存在地震、岩层崩塌等环境因素,这些都是导致井杆管偏磨的重要原因。
三、抽油机井杆管偏磨的防治措施1. 加强润滑管理针对润滑不良导致的井杆管偏磨问题,可以加强润滑管理,选择优质的润滑油,确保井杆管的良好润滑,减少摩擦,延长井杆管的使用寿命。
2. 定期清理井杆管内部为了防止杂质侵入导致的磨损,应该定期对井杆管内部进行清理,检查井杆管的磨损情况,并及时清除杂质,减少磨损。
3. 规范操作对于抽油机的操作人员,应该接受专业的培训,掌握正确的操作技巧,避免操作不当导致的井杆管磨损。
4. 加强检测定期对井杆管进行检测,发现磨损情况及时进行维修或更换,避免因井杆管磨损加剧导致偏磨。
5. 使用优质材料在制造井杆管时,选择优质的材料,提高井杆管的抗磨性能,延长其使用寿命。
6. 加强环境监测加强井下环境的监测,避免地震、岩层崩塌等环境因素对井杆管的磨损影响。
影响抽油井管杆偏磨的原因分析及治理措施

影响抽油井管杆偏磨的原因分析及治理措施抽油井管杆偏磨是指在油田采油生产过程中,由于管杆与配套设备、井筒等部件接触摩擦产生物理磨损,导致管杆表面出现不同程度的磨损现象。
管杆偏磨会严重影响井下设备的正常运行,甚至造成安全事故,也会导致油田生产受阻,给油田开发和生产带来不良影响。
及时分析管杆偏磨的原因,并采取有效的治理措施,对于确保油田生产安全和持续生产至关重要。
1.井下环境恶劣抽油井作业环境复杂,常常受到高温、高压、酸碱腐蚀等因素的影响,这些因素会加剧管杆表面的磨损。
井下含硫化氢气体的腐蚀作用、井下流体的酸碱腐蚀作用等都会导致管杆表面磨损加剧。
2.管杆质量不合格部分抽油井管杆质量不合格,表面处理不良,表面硬度不足等情况也会导致管杆表面易于磨损。
3.运输和安装过程中的损伤在管杆的运输和安装过程中,如果操作不慎或者设备不当,就有可能导致管杆表面受损,从而增加磨损的可能性。
4.井下设备运行不稳定抽油井井下设备运行时,如果发生振动、冲击等异常情况,也会导致管杆表面出现偏磨现象。
二、治理措施1. 加强管杆表面处理针对管杆表面易受腐蚀的问题,可以采用表面处理技术,如喷涂耐腐蚀涂层、电镀硬铬等方法,提高管杆表面的硬度和耐腐蚀能力,减少管杆表面的磨损。
2. 优化运输和安装流程在管杆的运输和安装过程中,加强对操作人员的培训,确保操作人员熟练掌握操作技能,减少在运输和安装过程中对管杆表面的损害。
3. 定期维护保养对井下设备进行定期维护保养,包括检查设备是否运行正常、是否有异常振动和冲击等情况,及时发现问题并进行维修,减少管杆表面的偏磨情况。
4. 优化井下生产工艺对井下生产工艺进行优化,减少井下流体对管杆的腐蚀作用,采取相应的措施降低井下环境对管杆的影响,减少管杆的磨损情况。
5. 强化管杆质量管理对抽油井管杆的质量进行严格管理,确保管杆的质量符合标准要求,提高管杆的硬度和耐腐蚀性能,减少管杆表面的磨损。
管杆偏磨对抽油井生产安全和稳定运行都会带来不利影响,针对管杆偏磨的原因,采取相应的治理措施至关重要。
抽油机井杆管偏磨原因分析及防治措施

抽油机井杆管偏磨原因分析及防治措施一、引言抽油机井杆管在油田开采过程中扮演着非常重要的作用,它负责输送油气和水等物质,并承受着各种压力和磨损。
随着开采深度的增加和油田设备的老化,井杆管的偏磨现象也逐渐增多,严重影响了油田的生产效率和安全。
针对井杆管的偏磨问题,进行原因分析并提出防治措施,对于保障油田的正常开采具有重要意义。
本文将就抽油机井杆管偏磨的原因进行分析,并提出相应的防治措施。
二、抽油机井杆管偏磨原因分析1. 设备老化抽油机井杆管作为油田开采设备的重要组成部分,经过长期使用后,其表面会出现磨损和腐蚀,从而降低了其耐磨性能。
在这种情况下,井杆管容易出现偏磨现象,影响其使用寿命和运行效率。
2. 弯曲载荷在油田开采过程中,井杆管在输送油气和水的过程中会承受各种弯曲载荷,从而导致其表面受到不均匀的力量作用。
当井杆管承受过大的弯曲载荷时,容易引起局部磨损,最终导致偏磨现象的产生。
3. 润滑不良井杆管的运行会产生大量的摩擦热和磨损颗粒,而润滑不良会加剧磨损进而引发偏磨。
尤其是在重载工况下,井杆管容易出现润滑不良,从而加速了偏磨的发生。
4. 环境因素在油田的工作环境中,会受到各种环境因素的影响,例如沙尘、高温、潮湿等。
这些因素会导致井杆管表面受到腐蚀、磨损等影响,进而导致偏磨现象的产生。
5. 操作不当油田设备的操作不当也是造成井杆管偏磨的一个重要原因。
在操作过程中如果未及时发现和处理异常情况,就会导致井杆管磨损加剧,从而产生偏磨现象。
为了延长抽油机井杆管的使用寿命,必须加强设备维护工作。
定期对井杆管进行清洗和润滑,及时更换磨损严重的部件,保持井杆管的良好状态。
2. 提高材料耐磨性针对设备老化导致的偏磨现象,可以在材料选择上做出改进。
选择更耐磨的材料制作井杆管,提高其抗磨性能,从根本上减轻偏磨的发生。
改进润滑系统设计,加强对井杆管表面的润滑,降低摩擦系数,减少磨损,有利于减轻井杆管的偏磨现象。
4. 加强操作培训提高操作人员的技能水平,加强对设备操作和维护的培训,使其能够及时发现异常情况并采取有效措施,减少人为因素对井杆管偏磨的影响。
影响抽油井管杆偏磨的原因分析及治理措施

影响抽油井管杆偏磨的原因分析及治理措施1. 引言1.1 背景介绍抽油井是油田开发中常见的设备,使用抽油机将地下的原油抽送到地面。
而抽油井管杆作为连接地面和井底的重要部件,承受着巨大的工况压力和摩擦力。
在实际运行中,抽油井管杆常常出现偏磨现象,给井下作业带来了诸多问题。
抽油井管杆偏磨的背后隐藏着许多复杂的原因,包括润滑不足、井底砂粒对管杆的刮擦、井内腐蚀以及管杆过长等。
这些原因导致了管杆表面的磨损加剧,从而影响了抽油井的正常运行。
为了有效解决抽油井管杆偏磨问题,需要采取科学有效的治理措施。
提高润滑效果、使用抗磨涂层、加强管杆的检测和维护、优化管杆长度设计等方法都能在一定程度上减轻管杆偏磨的情况。
通过对影响抽油井管杆偏磨的原因进行分析和治理措施的研究,可以为抽油井的正常运行和维护提供重要的参考,也有助于提高油田开发的效率和生产水平。
【字数:239】1.2 问题提出抽油井管杆偏磨是油田生产过程中常见的问题,其严重影响着抽油井的正常运行。
管杆偏磨不仅会导致生产效率降低,还可能造成设备损坏,增加维护成本。
及时有效地控制管杆偏磨问题对于提高油田生产效率具有重要意义。
抽油井管杆偏磨的问题主要源于多种原因,包括润滑不足、井底砂粒对管杆的刮擦、井内腐蚀、管杆过长等因素。
这些原因相互作用,加剧了管杆的磨损程度,增加了管杆偏磨的风险。
针对这些原因进行深入分析并采取有效的治理措施显得尤为重要。
本文将从影响抽油井管杆偏磨的原因进行分析,结合润滑不足、井底砂粒刮擦、井内腐蚀和管杆过长等因素,探讨管杆偏磨问题的成因及其影响。
将提出相应的治理措施,包括提高润滑效果、使用抗磨涂层、加强管杆的检测和维护以及优化管杆长度设计等方法,以期降低管杆偏磨的风险,保障抽油井的正常运行。
1.3 研究意义抽油井是石油工业中至关重要的设备,管杆偏磨是抽油井在运行中常见的问题,会影响抽油效率并增加维护成本。
对影响抽油井管杆偏磨的原因进行深入分析并提出有效的治理措施具有重要的研究意义。
抽油机井杆管偏磨原因分析及治理措施探讨

抽油机井杆管偏磨原因分析及治理措施探讨1. 杆管质量不合格:井杆管的原材料或制造工艺不达标,导致杆管的表面硬度不均匀、抗磨性较差。
此时,可通过加强杆管质量的检验和监控,确保杆管质量合格,并及时更换不合格的杆管。
2. 杆管与井筒之间的摩擦:杆管与井筒之间存在摩擦,加上长时间的运转,会导致杆管的偏磨现象。
治理措施包括:- 加大润滑剂的使用量:在井杆管与井筒的接触处增加合适的润滑剂,以减少摩擦力,并提高润滑效果。
- 优化操作技术:合理控制抽油机的运转速度和工作负荷,避免过大的负荷导致摩擦增大。
- 定期巡检维修:定期进行井下设备的巡检和维修,及时发现并处理存在的问题,以保证设备的正常运转。
3. 井下沙砾堵塞:井底存在大量的沙砾或杂质,容易造成井杆与井筒的摩擦增大,引起杆管的偏磨。
此时,适当采取以下治理措施:- 清洗井筒:定期清洗井筒,清理井底的沙砾和杂质,以减少摩擦。
- 井下过滤器的使用:在抽油机的井下位置设置过滤器,过滤掉大颗粒的杂质,减少其对杆管的磨损。
4. 抽油机安装不规范:抽油机的安装位置不准确或固定不牢固,会导致杆管与井筒之间有较大的摩擦力,引起偏磨。
应采取以下措施进行治理:- 定期检查抽油机的安装情况:确保其位置准确且固定牢固,避免出现倾斜或摇动的情况。
- 加强固定措施:增加安装固定的紧固件,加强抽油机的固定力度,并定期检查其是否松动。
5. 工作环境条件恶劣:井下环境条件差,如温度、湿度较大、粉尘多等,也可能会导致杆管的偏磨现象。
在此类环境下,应采取以下措施:- 加强设备维护:定期检查设备的工作状态和维护情况,确保其正常运转。
- 防护设备的使用:增加防护设备,如防尘罩、防潮罩等,保护设备不受恶劣环境的影响。
针对抽油机井杆管偏磨的原因分析及治理措施,应根据具体的情况进行综合考虑和选择合适的措施进行治理。
定期的巡检和维护工作也是确保设备正常运转和延长使用寿命的重要措施。
抽油机井杆管偏磨原因分析及防治措施

抽油机井杆管偏磨原因分析及防治措施
抽油机井杆管是油田开采过程中使用的重要设备之一。
由于井杆管的长期使用,其表
面会因为各种原因而磨损,从而影响油井的生产效率。
本文将分析抽油机井杆管偏磨的原因,并提出相应的防治措施。
1. 吊卡调整不当:井杆管安装在油井中是需要吊卡协助的,如果吊卡调整不当,会
导致井杆管直线度不够,产生摩擦,从而使井杆管表面磨损。
2. 载荷不均:油井生产过程中由于液体比气体密度大,常常会受到油液的重压,这
种载荷极不均匀,导致井杆管不均匀磨损。
3. 井深过浅:由于油井井深和井杆管直径关系密切,如果井深过浅,就会导致井杆
管的受力不均匀,表面易产生磨损。
4. 氧化:井杆管在油井内长时间暴露在高温高压的环境下,会发生氧化反应,导致
表面变硬,表面松散物质和垃圾附着等情况,从而使井杆管表面磨损加剧。
2. 控制载荷:在油井生产过程中,需要控制载荷均匀性,采取一些措施,比如调整
油液流量,使油液与气体的比例适当,保证混合物的均匀性,从而减少井杆管的磨耗。
3. 选用适当井深:根据井杆管的直径,选择适当的井深,从而保证井杆管受力均匀,避免表面磨损加剧。
4. 做好防腐保护:涂上先进的防腐护理漆或涂覆亚铁氧化物,从而有效抗氧化,可
延长井杆管使用寿命,减少表面磨损。
总之,抽油机井杆管偏磨是油井生产过程中常见问题之一,可对照以上原因和防治措
施进行排查和改进,从而保证井杆管的正常使用和生产效率。
抽油机井杆管偏磨原因分析及防治措施

抽油机井杆管偏磨原因分析及防治措施
抽油机井杆管在使用过程中可能出现偏磨的问题,其原因可能有以下几方面:
1. 选材不当:井杆管选用的材质不符合工作环境的要求,或者材质质量不合格,容易导致井杆管的偏磨现象。
解决方法:在选材时要根据具体工作环境和需要承受的压力、温度等因素来选材,确保材质符合要求并且质量合格。
2. 润滑不良:在井杆管与其他金属部件摩擦的接触面上,如果润滑不良,长时间运行会导致井杆管偏磨。
解决方法:选择适合的润滑剂,进行定期的润滑维护,确保接触面的光滑度和润滑性。
3. 使用不当:操作人员在使用抽油机井杆管时,如果不按照正确的使用方法进行操作,也会导致井杆管的偏磨。
解决方法:操作人员应该接受专业培训,熟悉抽油机的工作原理和操作流程,按照正确的操作方法进行使用。
防治措施:
2. 加强润滑维护:定期检查润滑剂的情况,保证润滑剂的充足和正常使用,避免干摩擦导致的偏磨问题。
4. 定期检修:定期对抽油机井杆管进行检修和维护,及时发现问题并进行修复,避免小问题演变成大问题。
5. 定期更换:根据使用情况和经验,合理安排井杆管的更换周期,避免过度磨损或老化材料带来的偏磨问题。
通过以上的分析和防治措施,可以有效减少抽油机井杆管的偏磨现象,并保证其正常运行和使用寿命。
抽油机井杆管偏磨原因分析及防治措施

抽油机井杆管偏磨原因分析及防治措施在油田开发中,抽油机井杆管是连接地表和地下油井的重要设备,其主要作用是将井口与地下油层连接起来,实现油井的抽油作业。
在使用过程中,井杆管常常会出现偏磨现象,导致井杆的寿命减少、生产效率下降,甚至引发事故,因此需要对该问题进行分析和防治措施的研究。
分析抽油机井杆管偏磨的原因。
主要原因可以归纳为以下几点:1. 油井工艺问题:油井开发中,井杆管在井口与地下油层之间会受到巨大的拉力和扭矩,同时水的冲刷和携带垂直向下运动的砂粒对井杆管也会产生冲击和磨损。
如果井口设计不合理,或者井底油层存在砂粒较多的情况,都会加剧井杆管的磨损。
2. 井杆材料问题:抽油机井杆管通常采用碳钢或者合金钢制造,这些材料在使用过程中会受到腐蚀和磨损的影响。
特别是在油水界面处,会产生电化学反应,使得井杆管受到腐蚀。
井杆管在使用过程中还会承受不同程度的冲击和摩擦,导致材料表面的磨损和松动,从而加剧偏磨现象。
3. 润滑不良:井杆管在使用过程中需要润滑剂的保护,以减少磨损和摩擦。
在实际操作中,由于时间限制或者人为疏忽,往往会导致润滑不及时或者不足,从而使井杆管无法得到有效的保护,进而出现偏磨现象。
针对抽油机井杆管偏磨现象,可以采取以下的防治措施:1. 定期检查和维修井口:井口是油井与地表连接的关键部位,其设计是否合理对井杆管的偏磨具有重要影响。
需要定期检查和维修井口,确保井口的结构完整和符合要求,减少井口对井杆管的冲击和磨损。
2. 选择合适的井杆材料:在制造井杆管时,应根据油井的工况和环境条件选择适合的材料,尽量采用抗腐蚀能力较强的合金钢,以减少井杆管的腐蚀和磨损。
3. 合理使用润滑剂:井杆管在使用前应进行润滑处理,选择适当的润滑剂,确保其能够在使用过程中提供足够的润滑效果,减少井杆管的摩擦和磨损。
并且,需要注意及时更换和补充润滑剂,以保证井杆管的持续润滑效果。
4. 加强培训和管理:在油田开发过程中,需要加强对操作人员的培训,增强其对抽油机井杆管偏磨问题的认识和理解,在操作过程中严格按照操作规程进行操作。
抽油机井杆管偏磨原因分析及防治措施
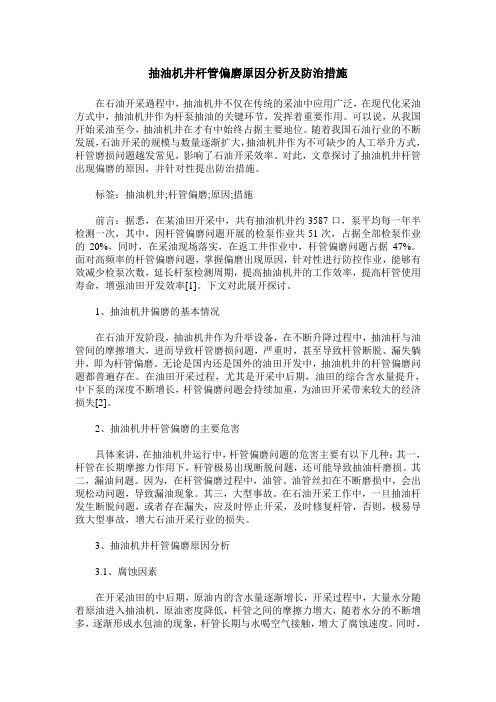
抽油机井杆管偏磨原因分析及防治措施在石油开采過程中,抽油机井不仅在传统的采油中应用广泛,在现代化采油方式中,抽油机井作为杆泵抽油的关键环节,发挥着重要作用。
可以说,从我国开始采油至今,抽油机井在才有中始终占据主要地位。
随着我国石油行业的不断发展,石油开采的规模与数量逐渐扩大,抽油机井作为不可缺少的人工举升方式,杆管磨损问题越发常见,影响了石油开采效率。
对此,文章探讨了抽油机井杆管出现偏磨的原因,并针对性提出防治措施。
标签:抽油机井;杆管偏磨;原因;措施前言:据悉,在某油田开采中,共有抽油机井约3587口,泵平均每一年半检测一次,其中,因杆管偏磨问题开展的检泵作业共51次,占据全部检泵作业的20%,同时,在采油现场落实,在返工井作业中,杆管偏磨问题占据47%。
面对高频率的杆管偏磨问题,掌握偏磨出现原因,针对性进行防控作业,能够有效减少检泵次数,延长杆泵检测周期,提高抽油机井的工作效率,提高杆管使用寿命,增强油田开发效率[1]。
下文对此展开探讨。
1、抽油机井偏磨的基本情况在石油开发阶段,抽油机井作为升举设备,在不断升降过程中,抽油杆与油管间的摩擦增大,进而导致杆管磨损问题,严重时,甚至导致杆管断脱、漏失躺井,即为杆管偏磨。
无论是国内还是国外的油田开发中,抽油机井的杆管偏磨问题都普遍存在。
在油田开采过程,尤其是开采中后期,油田的综合含水量提升,中下泵的深度不断增长,杆管偏磨问题会持续加重,为油田开采带来较大的经济损失[2]。
2、抽油机井杆管偏磨的主要危害具体来讲,在抽油机井运行中,杆管偏磨问题的危害主要有以下几种:其一,杆管在长期摩擦力作用下,杆管极易出现断脱问题,还可能导致抽油杆磨损。
其二,漏油问题。
因为,在杆管偏磨过程中,油管、油管丝扣在不断磨损中,会出现松动问题,导致漏油现象。
其三,大型事故。
在石油开采工作中,一旦抽油杆发生断脱问题,或者存在漏失,应及时停止开采,及时修复杆管,否则,极易导致大型事故,增大石油开采行业的损失。
导致抽油井杆管偏磨的因素分析与治理对策

导致抽油井杆管偏磨的因素分析与治理对策抽油井杆管的偏磨问题是油田开发过程中常见的一种问题,主要是由于以下因素引起的:1. 原油中含有砂粒和杂质:油井中的原油中往往含有一定的固体颗粒物质,如砂粒和硫酸盐等。
这些固体颗粒物质会随着原油一起进入抽油井杆管,其中的颗粒物质与杆管内壁发生摩擦,导致杆管表面磨损。
2. 抽油井杆管长期运行:抽油井的开采周期一般较长,油井杆管长时间在高温和高压的工况下运行,而杆管在此条件下容易产生塑性变形,失去原有的圆形,杆管表面与泥浆或其他杂质摩擦,从而导致偏磨。
3. 不良的维护保养:不良的维护保养也是导致抽油井杆管偏磨的一个重要因素。
如果对抽油井设备和管道进行不规范的维护保养,如长时间不清洗管道、不及时更换磨损的部件等,会使杆管表面积聚很多杂物,增加了杆管表面的摩擦,导致杆管偏磨加剧。
针对抽油井杆管偏磨问题,可以采取以下治理对策:1. 选择合适的井下抽油设备:选择性能可靠、品质上乘的抽油设备,提高设备使用寿命和工作效率。
应根据原油的性质选择合适的抽油设备,如可采用离心式抽油泵等,减少固体颗粒物质进入抽油井杆管的机会。
2. 定期清洗管道:定期对抽油井杆管进行清洗,将杆管表面的污物、固体颗粒和沉积物清除干净,使杆管表面保持光滑,降低摩擦,减少偏磨的可能性。
3. 加强油井维护管理:建立完善的设备维护管理制度,定期检查抽油设备的运行情况,并及时更换磨损的部件,保障设备正常工作。
还应加强对油井环境的管理,避免油井周围的杂物进入井下设备和管道中。
4. 检测和监控杆管磨损情况:通过采用声波测量、超声波测量等技术手段,对抽油井杆管的磨损情况进行实时检测和监控,及时发现异常情况进行处理,以避免因杆管磨损导致的故障和事故。
抽油井杆管偏磨是油田开发中常见的问题,可以通过选择合适的抽油设备、定期清洗管道、加强维护管理和监控磨损情况等措施来减少和避免杆管偏磨问题的发生,保障抽油井的正常运行。
抽油机井杆管偏磨原因分析及治理措施探讨

抽油机井杆管偏磨原因分析及治理措施探讨抽油机井杆管偏磨是指油井开采过程中,油井杆管在运动过程中出现偏磨现象,从而导致油井的正常运行受到影响。
以下是对抽油机井杆管偏磨原因分析以及治理措施的探讨。
抽油机井杆管偏磨的原因主要有以下几点:1.工作负荷不均衡:抽油机在运行过程中,如果井下油层压力的变化过大或者是井口装置的设计出现问题,会导致工作负荷不均衡,从而引起杆管的偏磨。
2.油井杆管制造质量问题:油井杆管的制造质量如果不符合要求,表面硬度不均匀或者是表面质量较差,容易出现偏磨现象。
3.运动过程中润滑不良:抽油机井杆管在运行过程中,如果润滑条件不良,例如润滑油的种类选择不合适、使用时间过长或者是润滑油污染,会导致摩擦增大,进而引起偏磨现象。
针对抽油机井杆管偏磨问题,可以采取以下治理措施:1.加强井下油层压力监测:及时了解井下油层压力变化,对于压力变化较大的油井要进行及时的调整,避免工作负荷不均衡。
2.加强油井杆管制造质量管理:对于油井杆管的制造过程进行严格把关,确保杆管表面硬度均匀、质量较好,降低偏磨现象的产生。
3.改善润滑条件:选择适合的润滑油,按照规定的时间和方式对润滑油进行更换和补充。
定期对润滑油进行检测,确保其质量达到要求。
4.定期检查杆管磨损情况:抽油机运行一段时间后,定期检查井口和井下杆管磨损情况,对于已偏磨的部位,及时采取修复措施,避免进一步扩大磨损。
5.加强现场操作培训:提高抽油机操作人员的技能水平,让其了解抽油机的运行原理,掌握正确的操作方法,避免不正确的操作导致杆管偏磨。
通过以上的治理措施,可以有效地预防和解决抽油机井杆管偏磨问题,提高油井的运行效率和延长杆管的使用寿命,对于油田的正常开采起到重要的作用。
导致抽油井杆管偏磨的因素分析与治理对策

导致抽油井杆管偏磨的因素分析与治理对策抽油井是非常重要的石油开采设备,其正常运行对于石油生产具有重要意义。
在日常生产中,我们经常会发现抽油井杆管出现偏磨现象,这不仅会影响井下设备的寿命,还会导致生产能力下降,甚至停产,给整个油田的生产造成严重影响。
对于抽油井杆管偏磨的原因进行深入分析,并提出相应的治理对策,是非常必要的。
本文将对导致抽油井杆管偏磨的因素进行分析,并提出相应的治理对策。
一、导致抽油井杆管偏磨的因素分析1. 抽油井杆管质量问题抽油井杆管是承受地层压力和机械运动力的关键部件,材料的质量直接影响到其抗压性能和耐磨性。
如果材料质量不达标,会导致杆管表面易发生磨损,甚至出现裂纹,从而影响整个井下设备的正常运行。
2. 抽油井杆管运行状态问题抽油井杆管在运行过程中,受到地层压力和机械运动力的作用,很容易出现疲劳破坏,尤其是在井口和井下弯头处,更容易发生偏磨。
如果抽油井杆管在运行过程中出现振动、摆动等异常情况,也会加剧其表面磨损。
3. 润滑不良在抽油井的运行过程中,润滑是非常关键的一环,好的润滑可以降低杆管的磨损。
否则,会导致摩擦增加、磨损加剧,进而导致杆管偏磨。
4. 环境因素抽油井在不同的地质环境中运行,地层的硬度、地质条件、油田开采方式等都会对抽油井杆管的磨损产生影响。
例如在产量较大的地层中运行,地层对杆管的磨损会更加明显。
二、抽油井杆管偏磨的治理对策1. 严格抽油井杆管的质量管理在使用抽油井杆管前,需要严格进行质量检查,选用质量可靠的杆管,并在正常生产中进行定期检测,及时发现问题,进行更换和维修。
2. 加强抽油井杆管的运行状态监测定期对抽油井杆管的运行状态进行监测,一旦发现异常情况,及时采取措施,避免杆管出现过多磨损。
3. 合理选用润滑材料在抽油井杆管的运行中,使用质量可靠的润滑材料,合理注滑,能有效降低杆管磨损程度。
4. 优化抽油井运行环境通过优化井口设计和加强管道支撑,减小抽油井杆管的振动和摩擦力,减少杆管磨损。
抽油井管杆偏磨的原因分析与对策探讨

抽油井管杆偏磨的原因分析与对策探讨一、引言抽油井是石油开采过程中的重要设备之一,而抽油井管杆偏磨则是抽油井常见的问题之一。
管杆偏磨会严重影响井口设备的使用寿命,甚至可能引发事故,因此在石油开采过程中,抽油井管杆的偏磨问题必须引起足够重视。
二、抽油井管杆偏磨的原因分析1. 油井内部环境导致管杆受损抽油井的工作环境相对恶劣,地下的高温、高压、腐蚀性介质等因素会对管杆造成损坏。
特别是在海洋油田,海水的腐蚀性更加严重,容易导致管杆的偏磨。
2. 操作不当造成管杆受损在抽油井的操作过程中,如果操作不当,例如使用过大的拉力、过高的冲击力等,都有可能导致管杆的偏磨。
操作人员疏忽大意、技术水平低下等也会导致管杆受损的风险增加。
3. 材料质量和加工工艺问题抽油井管杆的材料质量、加工工艺等均会直接影响其使用性能。
如果材料质量不达标或者加工工艺存在问题,都有可能导致管杆出现偏磨现象。
4. 设备老化和磨损随着设备的使用时间的增长,设备自身的老化和磨损现象不可避免。
设备老化和磨损可能导致管杆的受损,从而引发偏磨问题。
5. 其他因素除上述原因外,还有一些其他因素可能会导致抽油井管杆偏磨的问题,比如设计缺陷、材料疲劳等。
三、对策探讨1. 优化抽油井的设计和选材在抽油井的设计阶段就要考虑管杆的耐磨性能,选用耐磨性能好的材料,并采用合理的工艺来加工制造。
根据油井运行环境的特点,优化设计,减少外部因素对管杆的影响。
2. 加强抽油井的维护与管理定期对抽油井设备进行检查、维护和保养,及时发现设备存在的问题并进行修理和更换,有效减少设备的老化和损坏,从根本上减少管杆偏磨的风险。
3. 提高操作人员的技术水平加强操作人员的培训和管理,提高其技术水平,使其具备良好的操作技能和丰富的操作经验,减少操作不当导致的管杆偏磨问题。
4. 使用合适的润滑和冷却技术在抽油井的运行过程中,采用合适的润滑和冷却技术,有效的降低管杆的磨损和热损,减少管杆的偏磨现象。
浅谈抽油机井杆管偏磨主要原因及预防
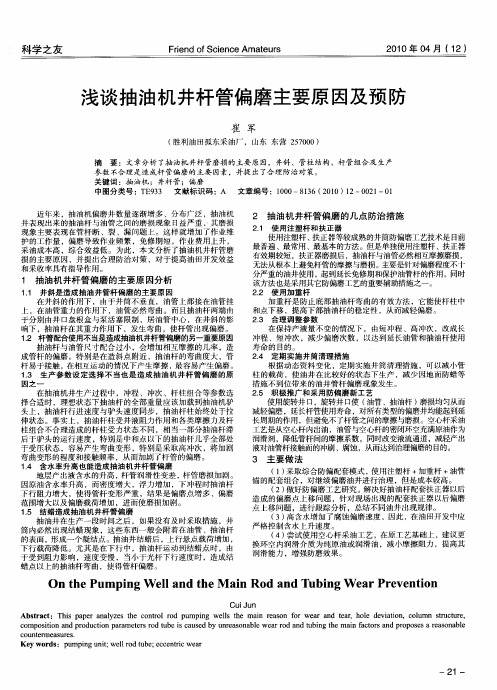
3 主 要做 法
( ) 1 采取综合 防偏 配套模式 , 使用注塑杆 +加重杆 +油管 锚 的配套组合 ,对继续偏磨油井进行治理 ,但是成本较高。 ( 做好 防偏磨工艺研究 。解决好抽油杆配套扶 正器 以后 2) 造 成的偏磨点上移问题 ,针对现场 出现 的配套扶正器 以后偏磨 点上移 问题 ,进行跟踪分析 ,总结不 同油井 出现规律 。 ( ) 3 高含水增加 了腐蚀偏磨速度 ,因此 ,在油田开发 中应 严格控制含水上 升速度 。 ( 尝试使用空心杆采油工艺 ,在原工艺基 础上 , 4) 建议更 换 环空内润滑介质为纯原油或润滑油 ,减小摩擦 阻力 ,提高其 施井筒清理措施 ,可 以减小管 柱的载荷 ,使油井在 比较好 的状态下生产 ,减少 因地 面防蜡等 措施不 到位带来 的油井管杆偏磨现象发生 。 25 积极推广和采用防偏磨新工艺 . 使用旋转井 口,旋转井 口使 ( 油管 、抽油杆 ) 磨损均匀从而 减轻偏磨 ,延长杆管使用寿命 ,对所有类型的偏磨井均能起到延 长周期的作用 ,但避免不了杆管之间的摩擦与磨损。空心杆采油 工艺是从空心杆内出油 ,油管与空心杆的密闭环空充满原油作为 润滑剂 ,降低管杆间的摩擦 系数 ,同时改变液流通道 ,减轻产出 液对油管杆接触面的冲刷 、腐蚀 ,从而达到治理偏磨的 目的。
科 学 之友
Fi do S i c m tus r n f c ne ae r e e A
21 0 0 0年 4月 (2) 1
浅谈抽 油机 井杆 管偏磨主 要原 因及预 防
崔 军
( 胜利油 田孤东采油厂 ,山东 东营 2 70 5 0 0)
摘 要 :文章分析 了抽油机井杆管磨损的主要原 因,井斜、管柱结构、杆管组合及 生产 参数不合理是造成杆管偏磨的主要 因素 ,并提 出了合理 防治对策。 关键词 :抽油机 ;井杆管 ;偏磨 中图分类号 :T 9 3 文献标识码 :A 文章编号 :10 E 3 0 0—8 3 2 1 1 0 2 —0 16( 0 0) 2— 0 1 1
抽油机井杆管偏磨原因分析及防治措施

抽油机井杆管偏磨原因分析及防治措施抽油机井杆管是油田采油工程中的重要设备,经常会出现杆管磨损严重的情况。
杆管的磨损会导致泵的工作效率下降,耗能增加,甚至会引发泵杆断裂等严重后果。
因此,对抽油机井杆管的偏磨原因进行分析,并采取相应的防治措施对于油田生产具有重要意义。
一、偏磨原因分析1.1 杆管内部接触磨损抽油杆在工作过程中,会在杆管内部不断向上下运动。
由于摩擦力的存在,在运动过程中,杆管内部接触面处容易发生磨损。
这种磨损在下行时最为明显,其原因是由于井液的黏度随温度升高而下降,而下行过程中,液体上移导致井口液体温度升高,黏度下降,杆管受到井液下压力的影响被向下拉动,从而产生强烈的磨损。
1.2 杆管外部机械磨损由于地形起伏,抽油杆在井筒内不断横向摆动,杆管与井筒之间产生摩擦力,导致杆管外部产生机械磨损。
1.3 杆管与泥浆接触磨损在井筒施工过程中,井壁腐蚀不良,泥浆不充分等原因,会导致泥浆中的细沙、碎石等硬颗粒物料与杆管接触,产生摩擦力,从而导致杆管与泥浆接触部位产生磨损。
1.4 泵口负压磨损当泵口内网目滤芯粘满或泥浆中杂物较多,导致泵口出现明显的噪声,说明抽油杆已被负压拉直而与井筒接触。
此时,抽油杆随泥浆流动运行,容易发生磨损。
二、防治措施2.1 加强井口液体温度调控为了减少下行时杆管内部接触磨损的产生,可采用调整井口液体温度的方法。
根据井口实际温度,通过适时调整泵入口和出口的附加装置,可控制井口液温,降低井下磨损。
2.2 防止杆管外部机械磨损为了防止杆管外部机械磨损,可采用加固井眼的方法。
通过对井眼进行加固,减少地形起伏和杆管摆动的程度,可以有效减少机械磨损。
2.3 采用合适强度的杆管选择合适强度、硬度较高的杆管可有效减少杆管与泥浆接触磨损的程度。
常用的防磨损材料包括金属涂层、碳化硅、氮化硅等。
2.4 如实测量井深度和泵位置在井斜段,由于抽油杆的重量引起呈锯齿形状的橡胶垫圈变形和运动,因此应准确测量井深度和泵位置,以防止泵口于杆管接触后产生磨损。
导致抽油井杆管偏磨的因素分析与治理对策

导致抽油井杆管偏磨的因素分析与治理对策抽油井杆管的偏磨问题是油田开发中常见的问题,其主要原因包括以下几方面:1. 地层原因:地层中可能存在坚硬物质,如砾石、沙粒等,当井筒通过地层时,井杆管容易与这些坚硬物质发生摩擦和碰撞,导致偏磨。
2. 技术操作不当:抽油井的日常操作中,如果井杆下降或提升速度过快,同时没有保持足够的润滑,容易引起井杆与井筒之间的摩擦,增加偏磨的风险。
3. 井筒直径不合理:井筒直径过小,无法容纳井杆的运动,使井杆在运动过程中容易受到摩擦,导致偏磨。
4. 井杆质量不良:井杆的制造质量不合格,如表面硬度不够、粗糙度过大等,容易加速偏磨的发生。
针对抽油井杆管偏磨问题,可以采取以下治理对策:1. 提高井杆材质质量:选择质量可靠、表面光滑度高的材质制作井杆,提高其抗磨损能力。
2. 合理调整井杆的下降和提升速度:通过减缓井杆的下降和提升速度,减少井杆与井筒之间的摩擦和碰撞,降低偏磨的风险。
3. 增加润滑剂的使用量:在井杆与井筒之间增加适量的润滑剂,可以减少摩擦,降低偏磨的发生。
4. 定期检查和维修井筒:定期对井筒进行检查和维修,清除地层中的坚硬物质,保持井筒内部光滑,减少摩擦和碰撞的发生。
5. 合理设计井筒直径:根据井杆的尺寸和运动特点,合理设计井筒的直径,确保井杆运动时充分的空间,避免与井筒产生过多的摩擦。
6. 加强技术培训:加强操作人员的技术培训,提高其对抽油井操作规程的理解和掌握,减少操作失误引起的偏磨问题。
7. 定期检查井杆管的磨损情况:定期检查抽油井的井杆管的磨损情况,及时发现和处理,避免磨损程度加剧。
抽油井杆管偏磨的原因分析有多方面,治理对策就是针对不同的原因采取相应的措施,以减少偏磨的发生,提高抽油井的开采效率和安全性。
浅析油井防偏磨技术的应用

浅析油井防偏磨技术的应用有杆抽油举升方式由于具有多种优点而广泛使用,它成本低廉、管理维修简便、适应范围广.。
但有杆抽油也有缺点,比如随着工作幅度的增大、泵挂的加深、油田含水的增高,有杆泵抽油的困难愈来愈大.。
此外侧钻井、定向井等大斜度井不断增加,更容易出现杆管偏磨问题.。
本文探讨了防偏磨技术,分析了防偏磨工艺的现场应用,最后总结了其效果.。
关键词:防偏磨;扶正器;加重杆;有杆泵采油;偏磨一、防偏磨技术研究目前防偏磨主要技术措施主要有:扶正器、加重杆、杆柱组合、内衬油管、旋转、柔性杆、无油管采油技术、井下油水分离油润滑防偏磨技术、防腐蚀、防结垢、防结蜡、防砂配套技术等.。
每种方法都各有千秋,为解决管、杆偏磨问题都起到了一定的积极作用.。
安徽油田为解决管杆偏磨问题也采取了很多办法,在实践中,积累了丰富的经验并取得了一定的成效.。
抽油杆柱防偏磨措施的主要目的是降低抽油杆柱与接触油管之间的摩擦力.。
从摩擦力公式可以看出:降低摩擦力的主要方法是降低正压力和摩擦系数.。
因此可这两方面着手.。
要降低正压力,应减少抽油杆柱与油管之间的点接触或减小面积接触,尽可能避免抽油杆柱的受压变形,可通过抽油杆加重来实现,在加重时,要确定的两个要素是:加重量和力的作用点,亦即计算中和点位置和选择合理的加重方式.。
(一)抽油杆加重方式的研究改进在有杆泵运行过程中,上行时抽油杆在液柱负荷、杆柱重量等作用下,承受拉力作用使整个杆柱呈伸直状态;下行时抽油杆受到浮力、液流阻力、柱塞和泵筒之间的摩擦力等多种因素影响,抽油杆柱常常会受到一个阻止柱塞向下运动的上顶力.。
由于这个上顶力的存在,使得柱塞以上的一段抽油杆发生螺旋弯曲、造成管杆偏磨.。
据最新大量的现场实际测量资料表明,该阻力大约在350-700公斤,左右,造成深井泵柱塞以上大约500米的抽油杆受压,容易使抽油杆磨损、断脱.。
为了解决这个问题,常常在柱塞以上采用直径40毫米的特殊抽油杆加重,该特殊抽油杆是空心杆灌铅或实心杆,由于直径粗、重量大,从某种程度上讲可以增加钢度、抵消柱塞的下行阻力,但中和点仍然存在,且随加重的重量增加,中和点逐渐上移,从理论上讲,无法彻底改善底部抽油杆柱的受力状况.。
- 1、下载文档前请自行甄别文档内容的完整性,平台不提供额外的编辑、内容补充、找答案等附加服务。
- 2、"仅部分预览"的文档,不可在线预览部分如存在完整性等问题,可反馈申请退款(可完整预览的文档不适用该条件!)。
- 3、如文档侵犯您的权益,请联系客服反馈,我们会尽快为您处理(人工客服工作时间:9:00-18:30)。
3551 在井筒和管柱上采取的措施套管变形是一种必然现象,为清楚反映油井拐点位置,采油厂应适时跟踪从油井中起出的油管、抽油杆,针对弯曲变形状况和偏磨部位,可初步判断出井筒拐点位置,必要时借助测试井筒数据,结合前期修井作业记录,一定要准确判定井筒存在的变形位置,定期组织分析井筒的变化趋势,便于在设计修井作业方案时,有针对性地采取措施。
(1)根据井筒拐点位置,在生产管柱上适量加装油管扶正器,扶正器的结构型式有两种。
一种钢制弹性油管扶正器,安装在油管接箍位置;另一种是强化尼龙油管扶正器,直接套在油管的管体上,可自由在单根管体上轴向窜动。
氮化防腐油管主要性能:表面硬度:650~800Hv,耐磨性比普通油管提高3倍以上,耐腐蚀性比普通油管提高5倍以上。
(2)在井筒变形位置使用一定数量的氮化防腐油管,氮化处理后的油管其防腐耐磨性能大副提高,特别是和喷焊的抽油杆接箍组合使用,效果最佳。
(3)为防止杆管偏磨,可在井口上加装使用油管旋转器;也可安装旋转旋绳器,利用抽油机在带动抽油杆作上下往复运动的过程中,每一个周期均会出现负荷交变,利用负荷产生的能量推动抽油杆旋转,使井下泵杆均匀磨损,延长泵杆使用寿命。
该装置优点:增加泵杆偏磨角度、防脱扣、减震、转速具有可调性、无须人工旋转。
(4)对于泵挂>1200米的油井,由于管柱承拉应力增加,为防止管柱变形,作业方案要考虑在管柱上使用油管锚。
2 在杆柱上采取的措施(1)根据前期修井起出的抽油杆,确定杆柱磨损部位,并在实施方案中考虑使用抽油杆扶正器。
目前扶正器的种类有:a、钢制和尼龙滚轮径向交错分布结构的扶正器,其连接在杆接箍部位;b、直接套在杆体上的扶正器,分为固定和活动两种结构型式;c、在杆体上直接压注成型固定的扶正器。
实际选用时,要根据井筒杆管偏磨位置、管柱组合或单一口径、泵排量等因素综合考虑,科学确定杆体扶正器加装位置和数量,依据经验,在井筒拐点处要求每根抽油杆上应均布2~3个扶正器;在拐点交界处上下25~35米位置每根杆上1~2个扶正器,加装遵循远离拐点顺次递减。
(2)在油井的偏磨位置,杆柱上考虑使用新开发的防偏磨抽油杆。
该装置是由高强度、高柔性和耐磨的扶正体,以及经过镀铬处理的(长度约为4~5米)抽油杆组成。
其工作原理为:当油井中管杆发生挠性弯曲时,扶正体自动找到偏磨点,卡在偏磨点部位,使抽油杆在扶正体内运动,避免了杆体与管壁的接触。
另外,高强度镀铬杆和扶正体之间因选用特种材料和处理强化方式,二者间的磨损程度很低(按照6次/分钟的模拟实验,结果表明磨损量≤0.4mm/年),从而有效避免了管、杆柱间偏磨现象的发生。
(3)在井筒杆、管偏磨段,除在杆柱上使用扶正器外,杆柱上可采用经过表面强化处理的接箍,再配以耐磨的氮化防腐油管组合使用。
所以,在防偏磨措施配套设计时,作为目前杆管偏磨措施的首选。
(4)为避免杆柱下行时产生的弯曲变形,杆柱设计时应酌情考虑使用一定数量的加重杆,根据泵挂深度和抽油机额定载荷、原油物性等实际情况合理确定。
依据理论计算,杆柱下行主要克服抽油泵游动凡尔开启的反向作用力。
因此,对于Φ57泵以下规格采油系统,杆柱上应使用700~1500Kg的加重杆,对于Φ70泵以上规格的采油系统,杆柱上应使用1600~2500Kg的加重杆。
(5)为提高杆柱在管柱内的抗弯强度,在进行杆柱设计方案时,除使用正常长度的对应规格抽油杆外,应在井筒拐点处特别考虑使用一定数量的专用定尺抽油杆,定尺杆长度要和抽油机冲程长度相匹配(一般为实际冲程长度+0.5米为宜)。
同时,在每根定尺抽油杆上加装一套扶正器(具体结构类型从前述中选取),在拐点部位应使用喷焊耐磨接箍。
此外,为避免在拐点处实施防偏磨措施后出现新的偏磨位置更迭移动,方案设计时应该考虑有意延长防偏磨措施配套长度,一般在拐点的上下位置各延长80米左右即可。
3 在抽油泵上采取的举措针对国内各油田生产油井大多进入中后期开采,以及水平井、侧钻井、分支井等钻采新工艺的实际运用。
另外,新投入的油井超深、高压、高含气和伴有腐蚀性介质等,多变的工况条件,无疑给机械采油系统带来较大难度。
因此,在抽油泵的选用上采取以下措施。
(1)抽油泵结构类型的选择和确定根据不同的井况,合理选用抽油泵的类型,抽油泵的类型按照功用不同可以分为:常规管式泵、杆式泵、防砂泵、抽稠泵、防气泵、斜井泵等,合理选择抽油泵是延长检泵周期,提高泵效的方法之一。
浅析油井杆管防偏磨措施及应用廖凯 徐佳 李永钢冀东油田南堡作业区 河北 唐山 063200摘要:有杆抽油举升方式在油田内广泛使用,油井杆管的防偏磨措施将直接影响抽油机工作的安全性与可靠性。
石油企业必须对油井防偏磨技术给予足够的重视,加大对油井情况的研究力度,努力寻找造成防偏磨的措施方法,只有这样才能促进石油有杆举升工艺的发展,提升石油企业的经济效益和社会效益关键词:油井 防偏磨 杆管356(2)抽油泵配套应用环阀,环阀安装在抽油泵上部,下冲程时,管柱内液柱作用在环阀上,柱塞游动阀不承受液柱重力,很容易打开。
4 合理确定抽油机工作制度对于杆管偏磨问题,抽油机的工作制度也是造成偏磨加剧的关键因素之一,由于受各油田抽油机类型的限制,以及选择工作制度的传统习惯,短冲程、高冲次将会直接导致杆管偏磨加剧。
因此,不论为何种类型抽油机,应首选使用其最大冲程和低冲次相组合。
建议抽油机冲程<4.2米时,冲次应选择为4~6次/min为好;冲程在4.2~5.1米之间时,冲次应选择为2~4次/min为宜,冲程>5.1时,冲次选择在1~2次/min为佳。
根据优化方案,每日跟踪抽油机示工图分析,载荷和电流变化超出设定预警值进行热洗井,避免了盲目设定热洗周期,2018年1-11月份累计减少热洗井7井次。
5 结束语以上是从井筒、抽油机、油管、抽油杆、抽油泵等各方面,采取的措施设计,但对于具体一口井或是一个区块,要如何选择确定配套机具或防偏磨措施,应根据具体情况而定。
作业区近几年老井因偏磨作业频繁,检泵周期期平均在500天左右,而应用系统防偏磨技术后效果明显,检泵周期期均延长至600天;新井投产后到目前最长检泵周期期已达700天。
根据实际应用总结适应我区的防偏磨工艺:一是防偏磨接箍与扶正器在造斜点,狗腿度大井段应用,该技术适用于泵深在2000m左右的中深井、最大井斜<25°、使用井段<600m;二是防偏磨接箍与加重杆配合技术,该技术适用于泵深在1500m以内的直井;三是内衬油管技术,该技术适用于中深井,该技术适用于最大井斜大于25°井。
有杆抽油井的偏磨问题治理是一项长期工作,是不断认识与再认识的过程。
参考文献 [1]王莉萍,化学清防蜡技术在陆梁油田的研究与应用[J].新疆化工.2010(1):15-17. [2]聂翠平,张家明,李文彬,油井清防蜡技术及其应用分析[J].内蒙古石油化工,2008.18:67—68.分蒸氨汽冷凝成浓氨水,补充入脱硫循环液中,剩余部分则送入氨催化分解炉分解成氢气和氮气,回兑入煤气。
经上述洗氨处理以后,挥发氨塔中将会产生蒸馏残液,残液中氨质量分数小于0.01%,部分返回洗氨塔作为末端洗氨水,剩余部分则送入固定铵分解塔中进行处理。
固定铵塔中产生的残液氨氮质量分数小于0.01%,这部分残液将直接被送往生物污水处理系统。
通过这一洗氨工艺的作用,净化工艺系统中将不会产生外排废气,所有残液都能得到有效的利用和处理,净化效果较好。
2.2 新工艺脱硫及水洗氨组合工艺应用的特点和优势结合上文中的内容,催化氧化法脱硫和水洗氨组合工艺在焦炉煤气净化中的应用能达到无硫泡废渣、无外排废液等净化要求,同时,在废液提盐技术的支持之下,实际生产过程中的各类资源都将能得到更为彻底的应用,在焦炉煤气净化过程中实现变废为宝。
从工业标准上来说,洗氨水的氨质量浓度可以从0.1g/L增加到7g/L~8g/L,脱硫后煤气中残余的H 2S将能得到有效吸收,确保H 2S质量浓度降低到20mg/m 3以下。
同时,脱硫工艺煤气中氨含量以及脱硫液循环液中氨含量的指标要求都能得到很好的满足。
从系统建设成本上来说,催化氧化法脱硫与水洗氨工艺的组合使用能有效降低系统建设成本,系统运行过程中所产生的动力消耗也能原有基础之上得到更好的控制,降低运行成本,避免因为新工艺的引进耗费大量人力物力。
2.3 废液提盐技术这一工艺中所使用的废液提盐技术主要是利用了脱硫废液中各种副盐的热稳定性、热分解程度、结晶点以及杂质产生阶段等方面的差异,进而通过脱杂质来去除废液中包含的金属杂质、硫磺等,在此基础上对处理后的废液进行蒸发浓缩,经过冷却、结晶、过滤等步骤,初步提出(NH 4)2S 2O 3粗产品。
最后,对滤液再次进行蒸发、浓缩、冷却、结晶等处理,得到工业上可以使用的NH 4SCN。
在这一工艺的作用之下,焦炉煤气净化的经济效益将能得到有效提升,保障生产厂家能在短时间内实现成本回收。
同时,从环保层面来说,这一废液处理技术也能在原有基础上更好的实现零外排,避免废气的产生,保障环保效益。
3 结束语综上所述,在针对现有焦炉煤气净化工艺实际应用过程中存在的缺陷进行简单论述的基础之上,本文主要针对催化氧化脱硫及水洗氨组合工艺进行介绍,并对这一工艺实际应用过程中所涉及到的废液提盐技术做了研究。
在这一工艺的作用之下,焦炉煤气净化效果将能很好的满足工业指标标准,同时能实现零外排、无硫泡废渣等要求,且整体系统的建设成本、运行成本相对较低,能很好的满足生产厂家需求。
参考文献 [1]张鑫.焦炉煤气制合成气的脱硫及净化工艺技术[J].山西化工,2018,38(3).[2]郭晓林.焦炉煤气净化工艺的有关思考[J].中国化工贸易,2018,10(20).[3]祁永程,高攀.焦炉煤气净化工艺节能技术探讨[J].当代化工研究,2018,(5).[4]中冶焦耐(大连)工程技术有限公司.一种用于焦炉煤气净化工艺的脱硫液加药系统及方法:中国,CN201810153378.3[P].2018-06-29.(上接第345页)。