液化气液膜脱硫醇组合工艺及其应用
液化气脱硫技术及应用.doc

液化紗脱硫技术及其应用莫娅南(中**辽阳钉分公司,**辽阳,111003)摘要:阐述了液化**脱硫技术的进展,以及各种技术在国内实际应用过程中存在的问题和改进的措施。
关键词:液化**脱硫技术The desulfuratcd technology of LPG and applicationMoyanan Wangbo(PetroChina Liaoyang Petrochemistry Company, Liaoning Liaoyang, 111003? Abstract: The article summarizes the development of LPG desulfurated technology, the problems of domestic application of the desulfurated technology and the improved methods are also be summarized ・Keywords: LPG. desulfurated technology1.液化材脱硫技术液化桂脱硫技术一般根据其硫含量及净化要求而定,对于硫含量低或处理量小的液化材采用干法,如用氧化锌、氧化铝、活性炭吸附或者用简单的碱法吸收。
对于硫含量高、处理量大的液化材的处理分成两步:第一步利用碱液脱除液化衬中的硫化氢,或将cos水解后一并脱除,常用的碱液为醇胺溶液及相应的复配溶液;第二步则是采用含磺化酥菁钻催化剂的碱液碱洗,碱洗的方式可以为抽提,也可以采用纤维膜技术。
1.1无碱催化氧化脱臭技术液化衬无碱催化氧化脱臭技术是以复合金属氧化物为催化剂,利用液化林中所溶解的微量氧将硫醇氧化成二硫化物,在总硫超标的情况下可通过精憎除去二硫化物,同时预碱洗过程使用固定床脱硫剂脱硫化氢,使整个工艺过程不存在碱渣排放问题。
中**齐鲁分公司研究院开发了QTM-01硫醇催化氧化催化剂,该催化剂经工业侧流试验结果表明,在液相及常温条件下可有效地把液化材中的硫醇氧化成二硫化物,无碱液排放加。
液化气深度脱硫醇技术的应用与分析
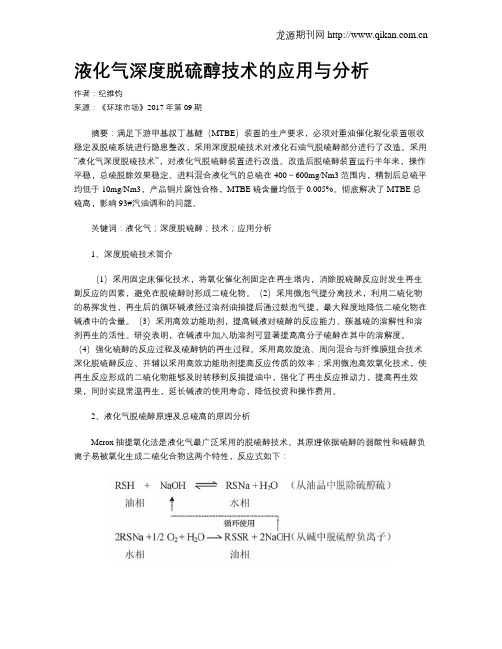
液化气深度脱硫醇技术的应用与分析作者:纪维钧来源:《环球市场》2017年第09期摘要:满足下游甲基叔丁基醚(MTBE)装置的生产要求,必须对重油催化裂化装置吸收稳定及脱硫系统进行隐患整改,采用深度脱硫技术对液化石油气脱硫醇部分进行了改造。
采用“液化气深度脱硫技术”,对液化气脱硫醇装置进行改造。
改造后脱硫醇装置运行半年来,操作平稳,总硫脱除效果稳定。
进料混合液化气的总硫在400~600mg/Nm3范围内,精制后总硫平均低于10mg/Nm3,产品铜片腐蚀合格,MTBE硫含量均低于0.005%。
彻底解决了MTBE总硫高,影响93#汽油调和的问题。
关键词:液化气;深度脱硫醇;技术;应用分析1、深度脱硫技术简介(1)采用固定床催化技术,将氧化催化剂固定在再生塔内,消除脱硫醇反应时发生再生副反应的因素,避免在脱硫醇时形成二硫化物。
(2)采用微泡气提分离技术,利用二硫化物的易挥发性,再生后的循环碱液经过溶剂油抽提后通过鼓泡气提,最大程度地降低二硫化物在碱液中的含量。
(3)采用高效功能助剂,提高碱液对硫醇的反应能力、羰基硫的溶解性和溶剂再生的活性。
研究表明,在碱液中加入助溶剂可显著提高高分子硫醇在其中的溶解度。
(4)强化硫醇的反应过程及硫醇钠的再生过程。
采用高效旋流、周向混合与纤维膜组合技术深化脱硫醇反应、并辅以采用高效功能助剂提高反应传质的效率;采用微泡高效氧化技术,使再生反应形成的二硫化物能够及时转移到反抽提油中,强化了再生反应推动力,提高再生效果,同时实现常温再生,延长碱液的使用寿命,降低投资和操作费用。
2、液化气脱硫醇原理及总硫高的原因分析Merox抽提氧化法是液化气最广泛采用的脱硫醇技术。
其原理依据硫醇的弱酸性和硫醇负离子易被氧化生成二硫化合物这两个特性,反应式如下:首先由强碱(NaOH)与硫醇反应生成硫醇钠,硫醇钠溶于碱液中,从而从液化气中脱除;抽提有硫醇钠的碱液在催化剂作用下通入空气将硫醇钠氧化为二硫化物脱除再生,脱除了硫醇后的再生碱液循环使用,可以避免大量碱渣的产生。
液化气深度脱硫技术原理及其应用

(1)采用深度脱硫技术对液化气脱硫醇装置进行了技术改 造,该技术为传统 Merox 抽提-氧化脱硫醇的改进,采用固定床 催化剂再生塔及功能助剂,实现对剂碱的高效再生及脱硫醇。 工业装置运行结果表明,该工艺完全满足当前对液化气硫含量 的指标要求,脱后液化气总硫含量不大于 20mg/m3。
从表 3-1 可以看到,脱硫醇后液化气硫醇硫≯3 mg/m3、总硫 含量 ≯20mg/m3,均满足产品指标要求。由上表计算可得总硫脱 除率均在 95% 以上。
4 存在问题建议
氧化再生塔为固定床,塔内介质自下而上流动,催化剂填
有效地降低了液化气的总硫。
2 脱硫醇技术改造
改造后工艺流程见图 1。从图中可以看出,深度脱硫技术 对梅洛克斯脱硫醇工艺进行了创新改进,取消了一、二级剂碱
3
49. 2
276
2
40. 31. 89 Nhomakorabea3
68. 8
227
2
55. 4
1. 3
4
5
58. 3
210
3
46. 8
2. 2
8
料顶层丝网如有破损,则会出现跑剂,在日常操作中应注意混 合器、过滤器前后管路压降情况,出现升高时应及时拆卸疏通, 另一方面,应在停工检修期间注意格栅丝网是否破损,如有破 损应及时更换。
自循环流程,简化了流程与控制回路,节省了建设投资与操作
费用;停用了碱液再生中换热设备,实现抽提剂常温再生。
3 改造后效果
2015 年 12 月改造完成投用至今,运行平稳,表 3-1 为部分 运行分析数据。
表 3-1 液化气脱硫醇分析数据
日期
20170616 20170616 20170616 20170615 20170615 20170615 20170614 20170614 20170614
液化气深度脱硫技术原理及其应用

液化气深度脱硫技术原理及其应用作者:杜轲来源:《中国化工贸易·上旬刊》2020年第06期摘要:通过对液化气深度脱硫技术进行简介,详细说明与分析液化气脱硫技术的原理,了解该项技术在工业生产中的广泛应用。
为满足下游MTBE装置的生产要求,重油催化分解装置吸收稳定,脱硫系统安全隐患得到改善。
并且LPG脱硫酒精装置采用LPG深度脱硫技术改造,脱硫醇装置运行稳定,总脱硫效果稳定。
关键词:液化气;深度脱硫原理;技术应用随着各炼化企业挖潜增效的迫切要求,液化气的深度应用受到广泛重视。
同时,随着环保工作加强,国家有关部门相继出台了石油石化产品新标准,如我国提高油品质量的强制性要求,也对液化气质量提出更高要求。
总硫和硫化氢含量是液化石油气(LPG)质量指标中的重要指标之一。
例如,在液化石油气(LPG)标准中,总硫含量是强制性的。
在车用液化石油气标准中,对深加工过程中总硫含量和硫化氢含量要求较高。
液化石油气脱硫醇装置的原料是催化裂化装置和延迟焦化装置生产的液态烃。
硫化氢用碱洗脱,液态烃、干气脱硫化氢一般采用MDEA胺洗抽提工艺,硫醇用碱脱除。
目前液化石油气脱硫醇工艺不能满足加工高硫液化气的产品质量要求。
在实施深脱硫技术改造后,投入使用至今,各项指标均达到了改造的预期目的。
1 深度脱硫技术简介①再生催化剂固定在再生塔上,以消除催化剂的副作用,防止脱硫醇的生成;②采用小型泡沫机分离技术,对不同物料进行挥发再生后,从循环碱液中提取溶剂,再通过泡沫装置进行萃取,最大限度降低碱液中不同商品的含量;③使用高效率的功能添加剂,提高了碱性溶液对酒精的反应能力、碳素基硫的溶解度和溶剂再生活性,结果在碱性液中添加辅助溶剂,显著提高高分子硫醇的溶解度;④强化醇反应过程和钠醇再生工艺,通过有效管线深化脱臭反应,整合复合纤维组合技术和高效添加剂使用,提高反应质量,高效利用微效氧化技术,形成再生反应的二级产物,迅速转移到采油中,增强再生反应的驱动力,提高再生效果。
液化气深度脱硫醇技术的应用与分析

液化气深度脱硫醇技术的应用与分析付连祥;王洪春【期刊名称】《山东化工》【年(卷),期】2011(040)011【摘要】The LPG desulfurization unit was improved by adopting the LPG deep desulfurization technology. After improvement, the LPG desulfurization unit has been running smoothly for half a year with a steady total sulfur removal effect. Total sulfur of the feeding mixed LPG isin the range of 400 -600 mg/Nm3. After refining, the average total sulfur is below 10 mg/Nm3; the product copper strip corrosion tests are up to the standard; the average sulfur content of MTBE is lower than 0. 005%. Thus, problem for the high total sulfur of MTBE and affection on 93# gasoline blending are completely solved.%采用“液化气深度脱硫技术”,对液化气脱硫醇装置进行改造。
改造后脱硫醇装置运行半年来,操作平稳,总硫脱除效果稳定。
进料混合液化气的总硫在400~600mg/Nm3范围内,精制后总硫平均低于10mg/Nm3,产品铜片腐蚀合格,MTBE硫含量均低于0.005%。
彻底解决了MTBE总硫高,影响93。
汽油调和的问题。
【总页数】3页(P64-66)【作者】付连祥;王洪春【作者单位】利华益集团,山东东营257400;利华益集团,山东东营257400【正文语种】中文【中图分类】TE624.55【相关文献】1.液化气Merox脱硫醇精制中脱硫深度和催化剂稳定性研究 [J], 王玉海;田永亮;刘瑞婷;项玉芝;夏道宏2.探究液化气脱硫醇碱渣减排技术工业化运用 [J], 邵兆鹏3.近零废碱排放的液化气深度脱硫醇成套技术 [J],4.液化气脱硫醇技术方案研究 [J], 张宝龙;刘春阳;张岩5.焦化液化气脱硫醇装置深度脱硫技术应用 [J], 淳于声雯因版权原因,仅展示原文概要,查看原文内容请购买。
炼油厂适用的液化气脱总硫及深度脱硫技术
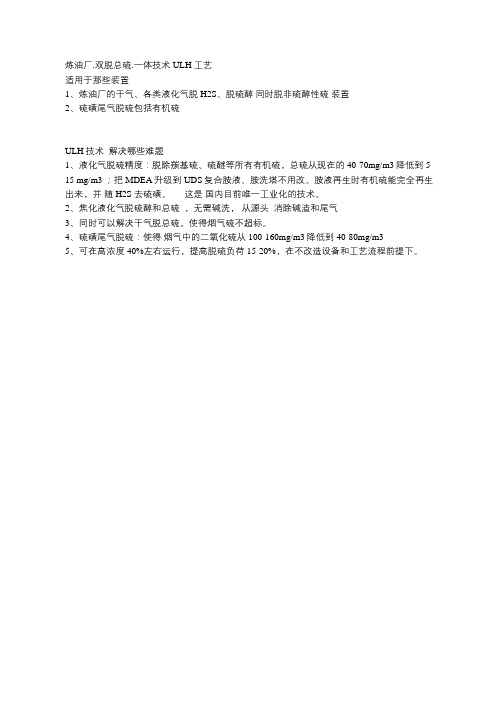
炼油厂.双脱总硫.一体技术 ULH 工艺
适用于那些装置
1、炼油厂的干气、各类液化气脱H2S、脱硫醇同时脱非硫醇性硫装置
2、硫磺尾气脱硫包括有机硫
ULH技术解决哪些难题
1、液化气脱硫精度:脱除羰基硫、硫醚等所有有机硫,总硫从现在的40-70mg/m3降低到 5-15 mg/m3 ;把MDEA升级到UDS复合胺液、胺洗塔不用改。
胺液再生时有机硫能完全再生出来,并随 H2S 去硫磺。
这是国内目前唯一工业化的技术。
2、焦化液化气脱硫醇和总硫,无需碱洗,从源头消除碱渣和尾气
3、同时可以解决干气脱总硫,使得烟气硫不超标。
4、硫磺尾气脱硫:使得烟气中的二氧化硫从100-160mg/m3降低到40-80mg/m3
5、可在高浓度40%左右运行,提高脱硫负荷15-20%,在不改造设备和工艺流程前提下。
干气液化气脱硫脱硫醇工艺讲解

干气液化气脱硫脱硫醇工艺讲解干气、液化气-脱硫、脱硫醇操作讲义 2.4.1. 脱硫岗位的任务(1) 利用化学吸收原理将干气及液化气中的硫化氢吸收下来,使干气及液化气中硫化氢含量达到质量要求。
(2) 采用预碱洗脱硫化氢及催化剂碱液抽提催化氧化脱硫醇工艺,将液化气中的硫化氢及硫醇脱除。
(3) 负责维护本岗位所属设备、仪表、电气可靠好用,保证安全生产。
(4) 严格遵守巡回检查制度,定时、定点对室内、外仪表进行对照,保证平稳生产。
(5) 优化操作,努力降低能耗及剂耗。
2.4.2. 脱硫岗位操作要点(1) 操作中发生超温、超压以及停水、电、汽、风等不正常现象,岗位要根据具体情况果断及时地进行处理,严防事故扩大。
(2) 严格按照工艺卡片规定控制好各塔压力、温度以及液、界位。
(3) 正常生产运行时,严防设备受憋、超压,串压,做到安全第一。
2.4.3. 净化干气硫化氢含量的控制控制目标:指令值范围内控制范围:?3,(V/V)相关参数:原料温度;原料量;脱硫塔压力;贫液量;溶剂贫液中硫化氢含量;贫液入塔温度控制方式:正常情况下,净化后的干气及液化气硫化氢含量由溶剂量的大小来控制。
正常调整:影响因素调整方法 1.贫液浓度的变化联系硫磺装置提高溶剂浓度 2.溶剂贫液量的变化加大贫液量 3.溶剂再生效果差,溶剂贫液中硫化氢联系降低贫液中的硫化氢含量含量高4.贫液入塔温度的变化联系控制好贫液温度5.原料温度的变化适当降低原料温度6.原料中的硫化氢含量的变化原料中硫化氢含量增加,可以提高溶剂量或联系厂调度提高溶液浓度 7.原料量的变化原料量增加,相应增加溶剂量 8.脱硫塔压力的变化提高脱硫塔压力The innovative city plan a: innovative city of City, comprehensively promote the implementation of national innovation pilot city, according to the Ministry of science and technology, on the sea of province "agreed as a national innovation pilot city of the little letter2.4.4. 干气脱硫塔压力的控制控制范围: 0.85-0.95MPa控制目标:正常操作中干气脱硫塔顶压力应控制在上述范围内,保证干气质量合格相关参数:高压瓦斯管网压力控制方式:干气脱硫塔压力由压控阀控制,通过控制干气出装置流量来控制干气脱硫塔压力正常调整:影响因素调整方法干气量的变化联系稳定岗位控制干气来量平稳高压瓦斯管网压力的变化联系调度瓦斯管网撤压仪表失灵仪表失灵,及时改手动或副线控制,联系仪表工处理异常处理:现象影响因素处理方法及时联系厂调度撤瓦斯管网压力,紧急时可以通瓦斯管网憋压过安全阀付线临时泄压塔压力升高,压力处理量突然大幅平稳处理量上限报警度增加仪表失灵,及时改手动或副线控制,联系仪表工压控阀失灵全关处理若原料干气中断,停止接受原料,及时关闭净化焦化部分故障或干气出装置阀,当稳定系统压力低于本系统时,干气中断,塔压力气压机故障,引起及时关闭稳定干气来的手阀,以保证系统内压力,下降干气中断维持溶剂循环和催化剂碱液循环,随时准备接受原料 2.4.5. 干气脱硫塔液位的控制控制范围: 45%?5%控制目标:正常操作中干气脱硫塔底液位应控制在上述范围内,保证平稳操作相关参数:干气脱硫塔压力,贫液循环量,富液闪蒸控制方式:干气脱硫塔底液位由液控阀控制,通过控制富液流量来控制干气脱硫塔液位正常调整:影响因素调整方法液面指示失灵联系仪表处理,加强现场液位指示的检查富液进料量突然增大,后稳定贫液量,加大富液到闪蒸罐量路不十分畅通干气脱硫塔压力波动稳定压力2etterto the Ministry of science and technology, on the sea of province "agreed as a national innovation pilot city of the little lity plan a: innovative city of City, comprehensively promote theimplementation of national innovation pilot city, according The innovative c异常处理:现象影响因素处理方法前路压力迅速上升,干气胺液回收干气脱硫塔液位器液位迅速上升甚过高,或没过干气通知厂调度并及时将干气切出脱硫装置至干气分液罐液位进口迅速上升2.4.6. 液化气脱硫抽提塔压力的控制控制范围: 1.40-1.50MPa控制目标:正常操作中液化气脱硫塔顶压力应控制在上述范围内,保证液化气硫醇含量合格相关参数:液化气流量,液化气与碱洗沉降罐压力,贫液进塔温度控制方式:干气脱硫塔压力由压控阀控制,通过控制干气出装置流量来控制干气脱硫塔压力正常调整:影响因素调整方法液化气量的变化联系稳定岗位控制液化气来量平稳液化气罐区系统故障憋压联系调度泄压仪表失灵仪表失灵,及时改手动或副线控制,联系仪表工处理液化气温度、溶剂温度的控制好液化气入脱硫温度和溶剂温度变化异常处理:现象影响因素处理方法后部憋压及时联系后部撤压,如果是脱硫醇系统问题紧急时可以通过安全阀付线临时泄压塔压力升高,压力处理量突然大幅平稳处理量上限报警度增加压控阀失灵全关仪表失灵,及时改手动或副线控制,联系仪表工处理3city of the little letter city, according to the Ministry ofscience and technology, on the sea of province "agreed as a national innovation pilotThe innovative city plan a: innovative city of City, comprehensively promote the implementation of national innovation pilot2.4.7. 液化气脱硫塔液位的控制控制范围: 45%?5%控制目标:正常操作中液化气脱硫塔液位应控制在上述范围内,保证平稳操作相关参数:液化气脱硫塔压力,贫液循环量,富液闪蒸罐压力控制方式:液化气脱硫塔液位由液控阀控制,通过控制富液流量来控制液化气脱硫塔液位正常调整:影响因素调整方法液面指示失灵联系仪表处理,加强现场液位指示的检查贫液进料量突然增大,后稳定贫液量,加大富液到闪蒸罐量路不十分畅通液化气脱硫塔压力的变化查找原因稳定液化气脱硫塔压力液化气预碱洗沉降罐界面的控制控制范围:45?5,控制方式:补充碱液和现场底部排碱渣正常调整:影响因素调整方法液化气带水严重,界面上升发现V1312界面上升快,应及时联系稳定岗位解决液化气带水问题碱液循环线堵塞,造成界面下降发现碱液循环线堵塞,一是进行蒸汽吹扫,启用伴热线,二是联系维修处理循环线2.4.8. 净化液化气硫醇含量的控制控制目标:指令值范围内控制范围:?3,(V/V)相关参数:碱液循环量,碱液浓度控制方式:正常情况下,净化后液化气硫醇含量由碱液量的大小来控制。
液化气脱硫醇工艺操作培训
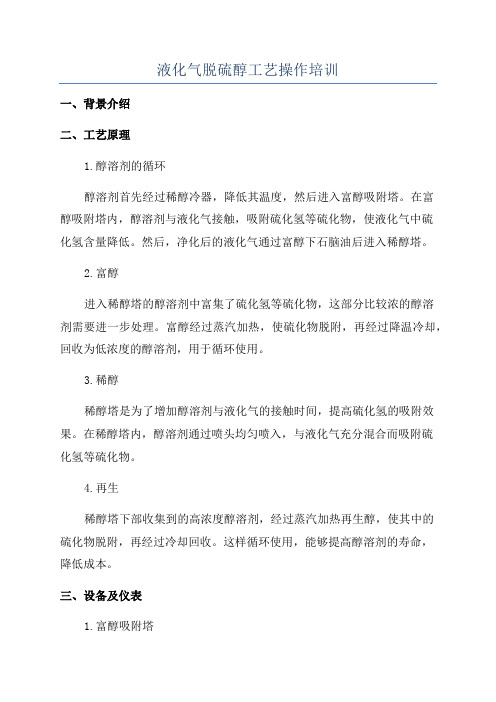
液化气脱硫醇工艺操作培训一、背景介绍二、工艺原理1.醇溶剂的循环醇溶剂首先经过稀醇冷器,降低其温度,然后进入富醇吸附塔。
在富醇吸附塔内,醇溶剂与液化气接触,吸附硫化氢等硫化物,使液化气中硫化氢含量降低。
然后,净化后的液化气通过富醇下石脑油后进入稀醇塔。
2.富醇进入稀醇塔的醇溶剂中富集了硫化氢等硫化物,这部分比较浓的醇溶剂需要进一步处理。
富醇经过蒸汽加热,使硫化物脱附,再经过降温冷却,回收为低浓度的醇溶剂,用于循环使用。
3.稀醇稀醇塔是为了增加醇溶剂与液化气的接触时间,提高硫化氢的吸附效果。
在稀醇塔内,醇溶剂通过喷头均匀喷入,与液化气充分混合而吸附硫化氢等硫化物。
4.再生稀醇塔下部收集到的高浓度醇溶剂,经过蒸汽加热再生醇,使其中的硫化物脱附,再经过冷却回收。
这样循环使用,能够提高醇溶剂的寿命,降低成本。
三、设备及仪表1.富醇吸附塔用于让液化气与醇溶剂接触,吸附硫化氢等硫化物。
塔体内部需要填充合适的填料,提高接触面积,增强吸附效果。
2.稀醇塔用于增加醇溶剂与液化气的接触时间,提高硫化氢的吸附效果。
稀醇塔内部需要装有喷头,使醇溶剂均匀喷入。
3.冷却器、加热器用于对醇溶剂进行冷却和加热的设备,保证循环醇溶剂的温度符合要求。
4.净化塔用于净化后的液化气排放。
净化塔内部需要装有填料,提高液化气与醇溶剂的接触,进一步净化液化气中的硫化氢。
5.仪表包括温度计、压力计、流量计等,用于实时监测和控制工艺中的温度、压力、流量等参数。
四、操作注意事项1.液化气的准备操作人员需要提前检查液化气的质量和含硫化氢等硫化物的浓度,确保液化气符合工艺要求。
2.设备的运行情况操作人员需要定期检查设备的运行情况,包括塔底硫化物浓度、吸附塔压差、冷却器和加热器的温度等。
3.醇溶剂的检测定期对醇溶剂进行检测,包括浓度、温度和流量等参数,确保醇溶剂的质量符合要求。
4.仪表的检修与校准定期对各项仪表进行检修与校准,确保仪表的准确性和可靠性。
崔化液化气纤维液膜脱硫醇LiFT—HR工艺工业应用研究

目的就 是 将 脱 硫 生 成 的硫 化 钠 和 硫 醇 钠 氧 化 , 化钠 氧化 为硫 代 硫 酸 硫 钠 和硫 酸钠 , 醇 钠 氧 化 为 氢 氧 化 钠 和 二 硫 化 物 。其 目的一 方 面 是 降 硫
1 纤 维 液 膜 脱硫 醇 技 术 分 析
醇 钠 含 量 持 续 累 积 升 高 。 该 碱 液 循 环 用 于 液 化 气 脱 硫 时 , 据 相 似 相 根 溶 原 理 , 硫 化 物 和 液 化 气 均 为 油相 , 液 中二 硫 化 物 将 被 萃 取 到 液 二 碱
【 关键词 】 催化液化气; 脱硫 醇; 氧化再 生; 纤维液膜 ; 渣 ; 碱 减排
0 前 言
随着 原油的劣质化 、 杂化 , 复 以及 对 液 化 气 产 品质 量 要 求 的 不 断 低 系统 碱 液 中硫 化 钠 和 硫 醇 钠 浓 度 . 一 方 面 通 过 硫 醇钠 氧 化 转 化 为 另 提 高 , 油 厂 各 类 装 置 生 产 的 液 化 气 均 面 临 着 总 硫 不 断 升 高 、 品液 炼 产 氢 氧化 钠 使 系 统 碱 液 中氢 氧 化 钠 浓 度 维 持 在 足 够 高 的水 平 , 保证 系 以 化 气 总 硫 指 标 更 为 苛 刻 的 趋 势 。 用 传 统 的 液 化 气 脱 硫 醇 工 艺 已经 很 采 统碱液有 足够高 的脱硫能力 。 难 保 证 总 硫 和 硫 醇 含 量 合 格 。 且 传 统 的 液 化 气 脱 硫 醇 工艺 不仅 消耗 而 碱 液氧化再生传统工艺 大都是将含催化剂 碱液加热至 5—0 , 57 ℃ 和浪 费 大 量 的碱 液 . 且 产 生 大 量 的 废 碱 渣 。 随 着 炼 油 化 工 生 产 环 保 压 缩 空 气 与催 化 剂 碱 液 在 填 料 塔 内 剧 烈 剪 切 扰 动 以 增 加 两 相 接 触 面 而 考 核 标 准 的提 高 , 统 的 碱 洗 脱硫 醇 技术 越 来 越 受 限制 。 我公 司 D C 传 C 积 , 气 中氧 气 与 碱 液 中硫 化 钠 、 醇 钠 接 触 时 发 生 反 应 并 生 成 硫 代 空 硫 装 置产品精制 部分 2 8万 吨/ 催 化 液 化 气 脱 硫 醇 及 碱 液 氧 化 再 生 装 硫 酸钠 、 氧化 钠 和 二 硫 化 物 。理 论 上 可 以利 用 二 硫 化 物 与 碱 液 的 极 年 氢 置 采 用 宁 波 中 ~ 石 化 科 技 有 限 公 司 开 发 的 液 膜 脱 硫 醇 专 利 技 术 性 不 同及 密度 差 分 离 二 硫 化 — R 工 艺 及 专 有设 备 , 于 2 1 JT H i 0 0年 8月 7 日至 8月 9日进 行 了标 的二 硫 化 物极 易 乳 化 及 随 尾 气 挥 发 , 液 与 空 气 扰 动 剧 烈 引起 二 硫 化 碱 定 。标 定 结 果 表 明 , 置运 行 良好 , 硫 效 果 达 到 合 同 要 求 的 指 标 , 装 脱 精 物 在 碱 液 中严 重 乳 化 , 此 工 业 装 置 几 乎 没 有 一 套 装 置 能 够 定 期 分 离 因 制后液化气总硫平均为 4p p m。远 低 于 产 品 总硫 2 p m 的 设 计 指 标 要 排 放 二 硫 化 物 。 统 工艺 中碱 液 氧 化 生 成 的二 硫 化 物 一 部 分 随 尾气 挥 0p 传 求 , 硫 效 果 明 显 脱 发 带 走 , 一 部 分 乳 化 夹 带 在 碱 液 中 , 此 再 生 碱 液 中 二 硫 化 物 及 硫 另 因
焦化液化气纤维液膜脱硫醇应用.

焦化液化气纤维液膜脱硫技术在焦化装置的应用中石化武汉分公司技术处肖翔文摘:本文介绍了纤维膜脱硫技术原理,结合我公司2#焦化装置液态烃脱硫醇系统改造前后运行效果的比较,证明改造效果明显,运行平稳,同时提出了下步改造的建议。
关键词:纤维膜脱硫改造运行比较1 纤维液膜技术基础1.1 化学基础和传质过程分析用碱洗脱除轻质油品中的硫化氢、二氧化碳、环烷酸、苯酚和硫醇等杂质是典型的炼厂工艺。
此工艺的化学基础是氢氧化钠和以上各种杂质之间发生的酸碱中和反应。
在水溶液中上述反应几乎可在瞬间完成,反应速度极快而且反应效率极高。
但是,当氢氧化钠和上述杂质分别溶解在水和烃中时,上述的反应速度急剧下降,难以实现工业应用。
因为两种互不相溶的液相主体之间的阻力以及杂质在两相之间分布的阻力,都促使原来以化学反应为主要控制因素的过程转变为以质量传递(杂质的质量从烃相向水溶液相的传递)为主要控制因素的过程。
质量传递的速率是三个独立变量的乘积:⨯⨯=(式1-1)CAKM∆式中:M——传质反应速率;K——烃水相体系的传质常数;A——烃/水两相接触的有效面积;∆——杂质从烃相转移到水相的浓度差推动力。
C∆主要受烃物式1-1中K与温度有关,大小随烃相和水相性质的不同而略有差异,C料中杂质含量的影响,但是杂质含量的绝对值最大也不过百分之几,而且非设计人员可调节的。
只有烃/水两相的有效接触面积A,是一个可以随接触装置结构设计的不同而大小迥异的变量。
许许多多技术前辈在这方面作了不懈的努力,并成功设计出各式各样的塔填料、精馏塔盘、静态混和等传质界面拓展组件和设备。
传统混合器-沉降器系统中所产生的夹带源于其制造的液滴的形状(即传质界面)、数量及其尺寸。
如果把一个液滴放置到纤维丝上,在静态条件下很容易观察到它会倾向于变长,如果有第二种流体与它并行,那么还能观察到第二种流体还能推动第一种流体沿着纤维丝流动,这是两种流体之间的表面曳力的作用,而两种液体之间的表面张力会倾向于使它裹在丝上。
液化气液膜脱硫醇组合工艺及其应用

提起液化气,很多人都是有所了解的,而这种了解大多是局限于家庭用液化气,但是从实际应用角度上看,液化气的使用范围要广得多,在本公司液化气可作为气体分馏原料,通过精馏原理可以分出丙烷、丙烯等产品。
而且碳四原料里面的异丁烯可作为生产MTBE的原料。
随着人们对生活质量、生产效率的要求越来越高,如何完善液化气液膜脱硫醇工艺,实现高质量液化气生产成为很多专家学者关注的事情。
液化气液膜脱硫醇组合工艺在行业内是比较受欢迎的,在研究中也发现了其优势所在,这种工艺生产出来的液化气含硫量较低,碱渣及污水排放较小,尾气排放量也在一定的合理范围之内。
1 液化气液膜脱硫醇组合工艺的特点本公司采用宁波中一石化公司工艺技术,采用纤维液膜反应器及碱洗工艺对液化气进行脱硫醇处理,脱除其中的硫醇,使其符合气分装置使用的标准。
脱硫醇的基本原理为:利用氢氧化钠水溶液脱除液化气中的有机硫,将其中的硫醇转化硫醇钠,溶于碱液中。
相关反应如下:RSH + NaOH → NaSR + H2O液化气夹带的微量胺液中所含的H2S可以与碱液发生如下反应:H2S + 2NaOH → Na2S+ 2H2O碱液再生的基本原理为:脱硫醇后碱液中硫醇钠在催化剂作用下与氧反应生成氢氧化钠和二硫化物,二者沉降分离,二硫化物去储罐,再生碱液循环利用。
反应式如下:2NaSR + 1/2 O2 + H2O → 2NaOH + RSSR碱液中可能存在的硫化钠能进行如下氧化反应:2Na2S + 2O2 + H2O → Na2S2O3 + 2NaOHNa2S2O3 + 2O2 + 2NaOH → 2Na2SO4 + H2O(Na2S2O3继续缓慢被氧化)液化气液膜脱硫醇组合工艺在液化气生产中的使用越来越广,这和工艺自身所具有的特点是分不开的。
1.1 脱硫醇对于液化气而言,碱洗脱硫醇的效率是由碱液与液化气的接触面积及碱液的有效浓度决定的,任何一点的改变都会给工作效率带来直接影响[1]。
液化气脱硫醇工艺模拟

液化气脱硫醇工艺模拟液化气脱硫醇工艺模拟一、引言液化气是一种广泛应用于工业和民用领域的燃料,但其中含有硫化氢等有害物质,对环境和人体健康造成潜在危害。
液化气脱硫醇工艺的研究和应用具有重要意义。
本文将介绍一种常用的液化气脱硫醇工艺模拟方法。
二、工艺流程1. 原料准备液化气主要成分为丙烷、丁烷等烷烃混合物,其中含有硫化氢。
为了进行脱硫处理,需要准备适量的脱硫剂(如醇类)。
2. 压缩与冷却将原料液化气进行压缩,使其达到适宜的操作压力,并通过冷却装置降低温度,以便更好地进行后续处理。
3. 脱硫剂注入在压缩冷却后的液化气中注入适量的脱硫剂。
脱硫剂可以选择乙二醇、丙二醇等醇类物质,其具有良好的脱硫效果。
4. 反应器处理将含有脱硫剂的液化气送入反应器进行处理。
反应器中通常设置有催化剂床层,以增加反应速率和效果。
在反应过程中,硫化氢与脱硫剂发生化学反应生成不同的产物。
5. 分离与回收经过反应后的液化气含有产物和未反应的物质。
通过分离装置将产物与未反应物分离开来,并对产物进行回收利用。
6. 净化处理分离后的液化气还可能残留少量杂质,需要进行净化处理。
常见的净化方法包括吸附、膜分离等,以提高液化气的纯度和质量。
7. 储存与输送经过脱硫和净化处理后的液化气可以进行储存和输送。
储存设备一般采用压力容器或罐车等形式,输送方式可选择管道输送或罐车运输等。
三、工艺优势1. 高效性采用催化剂床层和适当的反应条件,可以提高脱硫效率和反应速率,实现高效处理。
2. 环保性脱硫剂醇类物质在反应过程中与硫化氢发生化学反应,生成的产物相对环境友好,减少了对环境的污染。
3. 经济性脱硫剂醇类物质价格相对较低,且可以进行回收利用,降低了生产成本。
四、工艺模拟方法1. 建立反应动力学模型通过实验和数据分析,建立液化气脱硫醇工艺的反应动力学模型。
该模型可以描述反应速率、转化率等关键参数随时间变化的规律。
2. 模拟软件选择选择合适的工艺模拟软件进行液化气脱硫醇工艺的数值模拟。
液膜脱硫醇与碱液富氧再生组合工艺的应用

液膜脱硫醇与碱液富氧再生组合工艺的应用西安石化分公司50万吨/年的催化裂化装置于2006年4月经过技术改造后,液化气的产量从10t/h增加到15t/h,同时经过总部批复新建12万吨/年气体分离装置一套,精制后的液化气将作为气分装置的原料,分离得到高附加值的[wiki]化工[/wiki]原料-丙烯,余下的轻烃作为民用液化气出厂。
在进行技术改造前精制后液化气总硫偏高(基本上在80-240 mg/m3范围内);铜片[wiki]腐蚀[/wiki]不合格。
本次改造后精制液化气的处理量增加50%;同时对精制后液化气质量如总硫和铜片腐蚀等提出了更高要求,要求总硫不大于46 mg/m3,铜片腐蚀不大于1级。
因此公司经过充分的技术调查和论证,决定对液化气精制装置实施原地改造,脱硫醇部分采用宁波中一石化科技有限公司的液膜脱硫技术和成套[wiki]设备[/wiki]。
装置设计目标:1) 液化气处理量15t/h2) 原料液化气总硫含量最高为1500mg/m33) 产品液化气总硫含量不超过46mg/m34) 产品液化气铜片腐蚀合格率100%液膜脱硫塔等主要设备2006年3月25日开始安装,2006年4月15日投用。
其中碱液富氧常温氧化再生部分于6月2日投用。
自4月15日催化装置开工至今,液膜脱硫系统运行平稳,达到了设计要求。
1. 改造基本情况改造前采用常规碱洗流程,即“预碱洗+筛板抽提塔+砂滤沉降+碱液空气加温氧化再生”流程。
由于铜片腐蚀不合格,在砂滤沉降后,串联了一座精脱硫塔,需要定期更换精脱硫剂,增加了操作成本。
改造后采用宁波中一石化科技有限公司设计的“预碱洗+1级液膜脱硫+碱液富氧常温氧化再生+碱液反萃取脱二硫化物”流程。
取消了筛板抽提塔、砂滤沉降罐、精脱硫塔。
部分设备利旧,其中碱液氧化再生塔原地原位改造。
1.1拆除的设备有:1) 液化气抽提塔2) 液化气水洗罐3) 液化气沉降罐4) 液化气精脱硫塔5) 碱液换热器(2台一组)1.2利旧的设备主要有:1) 液化气原料缓冲罐2) 预碱洗罐3) 二硫化物分离罐4) 二硫化物储罐5) 碱液储罐1.3原地改造利用的设备主要有:1) 碱液氧化再生塔1.4增加的设备有:1) 液化气胺液聚结分离罐(1台)2) 液膜脱硫塔(1座)3) 碱液反萃取脱二硫化物塔(1台)4) 防爆型富氧发生机(1台)控制箱:防爆等级ExdⅡBT6电磁阀:型号DF10-0.6 矿用浇封型防爆等级ExmⅠ空气干燥机:防爆等级EXdΠ BT55) 碱液预过滤器(1个,待安装)6) 碱液精细过滤器(2个一组并联)7) 液化气精细过滤器(2个一组并联)1.5装置布局通过本次改造,在液化气处理量增大后,装置布局更加合理,精制装置占地面积减少。
探究液化气脱硫醇碱渣减排技术工业化运用

探究液化气脱硫醇碱渣减排技术工业化运用摘要:某石化企业购进了液化气脱硫醇装置,具体是应用了“液化气纤维液膜脱硫醇及碱液再生工艺”,该工艺是本石化企业自主研发的,并以此为基础上研制了工业化配套技术与设施,可以将该工艺看成是二级碱洗一级水洗液膜传质手段,设定的技术目标是保证产品液化气含硫总量≤20ppm,碱液历经再生处理后,氧化生成的部分二硫化物自行聚集形成大液滴,同时大液体会和碱液维持互为分离状态。
鉴于此,本文对液化气脱硫醇碱渣减排技术工业化运用进行分析,以供参考。
关键词:液化气;脱硫醇;碱渣减排;工业化分析引言传统液脱装置使用期间暴露出的问题有脱硫处理后产品总硫含量偏高。
设备构件腐蚀较明显及排渣量较多等,对其本质进行分析主要是由于抽提和再生效率偏低,其中后者是问题的关键。
为解除以上现实问题,本文设计了LiFT-HR工艺,结果表明经本工艺处理后,液化气产品含硫碱渣年排放量≤125t/年,和国内外同种产品相比较,降低幅度高达70%;经系统测算后发现将该装置用于工业领域中,每年均能减少数百吨碱渣排放量,环保处理费也会相应降低,进而节省碱液采购成本。
液化气脱硫醇尾气的性质及特点在实际生产中,从二硫化物分离罐中分出液相二硫化物的难度较大。
二硫化物与碱液的密度相近,前者密度为1.06×103kg/m3,后者密度在(1.02~1.08)×103kg/m3,生成的二硫化物小油滴在黏度较大的碱液中难以聚集成大油滴,不容易分离出去。
二硫化物主要成分为二甲基二硫和二乙基二硫,其沸点在109~120℃,且极性很小,在大风量、较高温(45~65℃)时挥发性较强。
因此,碱液再生单元二硫化物分离罐排放尾气中的主要成分是氮气、未反应的氧气、挥发出来的二硫化物以及携带的碱液和烃类,典型组成见表1。
2工艺技术方案对比2.1专利商一专有技术(1)采用纤维液膜反应器及碱洗工艺脱除液化气中的硫醇。
该技术利用其表面张力和重力场的作用,使得碱液在亲水纤维上面形成碱液液膜,液化气则被纤维丝分散成烃相膜,在重力、密度差和亲水纤维聚结,以及流体推动力的作用下,碱液沿着纤维丝的表面向下流动,流至分离罐和液化气进行快速地分离。
液膜技术在液化石油气脱硫中的工业应用
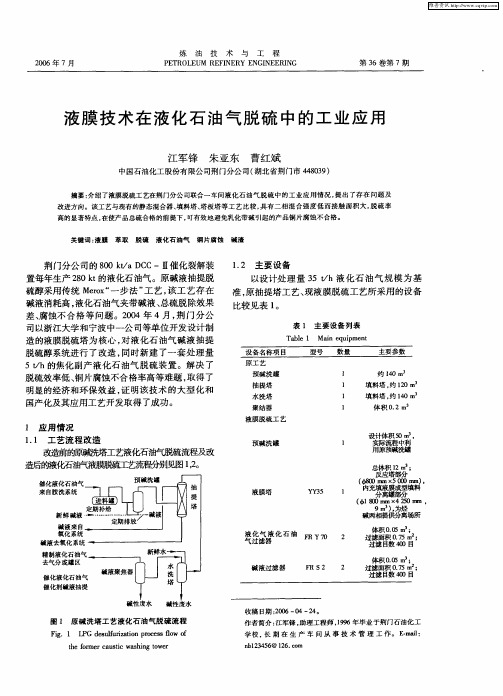
荆 门分公 司 的 80k/ C 0 taD C—I催化 裂解 装 I 置 每年 生产 20k 的液化石 油气 。原 碱液 抽提脱 8 t 硫 醇采用 传统 Meo“ 步 法 ” 艺 , rx 一 工 该工 艺存 在
1 2 主要 设备 . 以设 计处 理 量 3 / 5 th液 化 石 油 气 规 模 为 基
中国石油化工股份有 限公司荆 门分公司 ( 湖北省荆 门市 4 83 ) 4 09
摘要 : 介绍 了液膜脱硫工 艺在荆 门分公司联合 一车间液化石 油气脱硫 中的工业应 用情况 , 提出 了存 在问题 及 改进方 向。该工艺与现有 的静态混合器、 填料 塔、 塔板 塔等工 艺比较 , 具有二 相混合强 度低而接 触 面积大 , 脱硫率 高的显著特点 , 在使产 品总硫合格的前提下 , 可有效地避 免乳化带碱引起的产 品铜片腐蚀不合 格。 关键词 : 液膜 萃取 脱硫 液化石油气 铜 片腐蚀 碱渣
硫 塔 , 计 二相 接触 面积 约 为 同体 积 传统 填 料 塔 设
的9 0倍左 右 。 2 2 脱硫 情 况 . 2 2 1 铜 片腐蚀 合格 率 ..
液化 石油气 总硫 的分 析方 法 为 库 仑法 ( 见标 准 S / 2 2- )铜 片腐蚀 的分析方 法见标 准 H T02 - 02 ;
用 ) 液膜塔 进 碱 量/ 化 石 油气 进 料 量 2 5 ~ ; 液 .%
液 化石油 气 中硫 化物 、 硫含 量 达 标 的 目的 。 同 总 时 由于是 同相 层 流 接 触 而 非 湍流 接 触 , 免 了碱 避 液 的乳化 夹带 , 证 了产 品 液 化 石 油气 铜 片 腐 蚀 保 的合格 。
3 / 催 化 裂化 液化 石油气 处 理 量 的液 膜脱 5th
液膜脱硫技术的工程应用
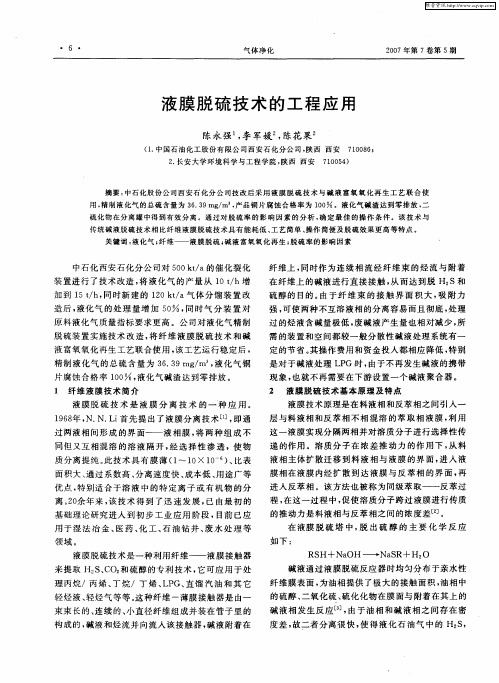
程, 在这一过 程 中 , 促使 溶质分 子跨 过液 膜进行 传质
的推 动力是 料液 相与反 萃相之 间的浓度 差L 。 2 ] 在液膜 脱 硫 塔 中, 出硫 醇 的 主 要 化 学 反 应 脱
如下 :
RSH + Na OH — Na R+ H2 S O
造后 , 液化 气 的 处 理 量增 加 5 , 时气 分 装 置 对 0 同 原 料液化 气质 量指标要 求更 高 。公 司对 液化气 精 制 脱硫 装置 实施 技术 改 造 , 将纤 维 液膜 脱 硫 技 术 和 碱 液 富氧氧 化再 生工艺 联合使 用 , 工艺运 行稳 定后 , 该
1 纤维 液膜技 术简 介
现 象 , 就不再 需要 在下游设 置一 个碱 液聚合 器 。 也
2 液 膜脱硫 技术 基本原 理及 分 离 技 术 的 一 种 应 用 。 1 6 年 , N. i 先 提 出了液 膜分 离技 术 [ , 9 8 N. L 首 1 即通 ] 过 两液 相 间形成 的界 面—— 液 相膜 , 将两 种 组 成 不 同但 又互相 混溶 的溶 液 隔 开 , 选 择性 渗 透 ,使 物 经 质分离 提纯 。 技术 具有 膜 薄 ( ~ 1 ×l 一 ) 比表 此 1 0 O6、 面 积大 、 通过 系数 高 、 离速度 快 、 分 成本低 、 用途 广等 优点 , 特别适 合 于溶 液 中 的特 定离 子 或 有 机物 的分
来提取 I: 、 O 和硫 醇 的专利 技术 , 可应 用 于处 -S C I 它
理丙烷 /丙 烯 、 烷/丁 烯 、 P 直 馏 汽 油 和 其 它 丁 L G、 轻烃液 、 轻烃 气 等等 。 种纤维 一 薄膜 接触 器是 由一 这
液化气脱硫醇工艺提高碱液利用率研究

液化气脱硫醇工艺提高碱液利用率研究摘要本公司生产的催化裂化液化气是生产MTBE产品的主要原料,如果液化气脱硫不彻底,MTBE产品的硫含量就会非常高。
液化气脱硫醇目前基本上采用Merox碱洗抽提和碱液空气氧化再生循环利用工艺。
随着高含硫原油加工比例的上升以及液化气产量和综合利用率提高,液化气脱硫醇碱渣排放量大幅增加,对环保压力很大且增加了操作成本。
按照液化气中所含硫化物性质和含硫分布的特点,理论上经过脱硫醇后的液化气中的硫含量能降10μg/g,本论文的研究方向为,在保证液化气脱硫醇效果的前提下,减少碱渣排放量,提高碱液的利用率。
关键词:液化气、脱硫醇、碱液、改造、利用率前言高含硫液化气作为化工原料,将对下游装置的加工过程产生较大影响,因此液化气脱硫显得尤为重要。
当前,国内外的液化气脱硫醇工艺主要有Merox抽提-氧化再生技术[1]、催化氧化脱硫醇技术[2]、吸附法[3]和催化氧化-吸附法[4]等。
Merox抽提-氧化再生技术是目前液化气脱硫醇应用最为广泛的技术。
该技术是在催化剂的作用下,硫醇与碱反应生成硫醇钠,而碱液可以再生,循环使用。
一、装置现状本公司目前有一套催化液化气碱洗脱硫醇单元,脱硫醇装置精制后液化气硫含量较低。
同时,脱硫醇装置排渣碱浓度为15%,每年需消耗4589t新鲜碱液,碱耗量大,碱液利用率低。
初始注碱液浓度20%,排渣碱浓度15%。
总耗碱量为4589t/a。
而目前公司总碱液再生量为5t/h。
再生总碱液量不足脱硫醇总循环碱液量的5%。
经分析,可通过改变工艺流程及采用新技术等措施减少碱渣排放量,提高碱液利用率二、工艺分析1 预碱洗部分在催化裂化液化气脱硫醇精制过程中,预碱洗的目的主要是脱除来自醇胺脱硫后液化气中残留的微量硫化氢,以防止碱氧化再生过程中被氧化成元素硫带入精制后的液化气或者影响脱硫醇过程的催化剂。
目前多采用7%~10%的氢氧化钠溶液进行预碱洗,但产生的废碱液处理起来相当困难,不能进入氧化再生塔C-9007进行再生,需排至莱特进行后续处理。
纤维膜脱硫组合技术在液化石油气脱硫脱硫醇中的应用

纤维膜脱硫组合技术在液化石油气脱硫脱硫醇中的应用孙守华【摘要】介绍了纤维膜脱硫组合技术在某石化公司液化石油气脱硫脱硫醇装置上的工业应用情况。
结果表明,纤维膜脱硫组合技术具有适用性强、开工过程简单等优点。
脱硫脱硫醇后催化裂化装置液化石油气中总硫质量浓度降至16.3~16.8 mg/m3,铜片腐蚀等级为1a ,延迟焦化装置液化石油气中总硫质量浓度降至50.8~77.8 m g/m3,铜片腐蚀等级为1a ,均满足产品质量要求。
经过水洗后,两装置循环碱性洗水中硫化物质量浓度分别为17.91 m g/L和73.83 m g/L ,回收大量副产物二硫化物;废碱液经过碱液再生后,碱液质量分数均大于15%,满足纤维膜脱硫醇的需要。
碱渣经过湿法氧化处理后,满足排放标准。
%The industrial application of the fiber film desulfurization combination technology in liq‐uefied petroleum gas sweetening unit in a petrochemical company was introduced .The result indicated that the fiber film desulfurization combination technology had the advantages of great applicable activ‐ity and simple starting‐up .The total sulfur content in liquefied petroleum gas in fluid catalytic crack‐ing unit may reduce to16 .3-16 .8 mg/m3 after sweetening ;and the corrosion grade of copper sheet was 1a .The total sulfur concentration of liquefied petroleum gas in delayed coking unit may reduce to 50 .8-77 .8 mg/m3 ,and the corrosion grade of copper sheet was 1a ,meeting the p roduct quality re‐quirement .After water washing ,the sulfide concentrations in alkaline washing water of two sets of u‐nits were 17 .91 mg/L and 73 .83mg/L ,respectively ,recovering the disulfides as by‐products .The massfraction of regenerated lye was above 15% ,meeting the sweetening requirment of fiber film . The alkaline sludge could meet the discharge requirements after treated by wet oxidation .【期刊名称】《石油与天然气化工》【年(卷),期】2015(000)004【总页数】5页(P19-23)【关键词】纤维膜;液化石油气;脱硫;脱硫醇;应用【作者】孙守华【作者单位】中化泉州石化有限公司【正文语种】中文【中图分类】TE868液化石油气是炼油厂在深加工过程中产生的重要高附加值产品,可应用于民用燃气,也可用于合成聚丙烯、甲乙酮及甲基叔丁基醚等化工品。
- 1、下载文档前请自行甄别文档内容的完整性,平台不提供额外的编辑、内容补充、找答案等附加服务。
- 2、"仅部分预览"的文档,不可在线预览部分如存在完整性等问题,可反馈申请退款(可完整预览的文档不适用该条件!)。
- 3、如文档侵犯您的权益,请联系客服反馈,我们会尽快为您处理(人工客服工作时间:9:00-18:30)。
第25卷 第6期2007年11月 石化技术与应用Pe troche m i ca lT echno l ogy&A pp licati onV o.l25 N o.6N ov.2007工业技术(520~523)液化气液膜脱硫醇组合工艺及其应用李锋,申明,田波(中国石化西安石化分公司联合车间,陕西西安710086)摘要:采用液膜脱硫醇组合工艺,对中国石化西安石化分公司的液化气脱硫醇装置进行了技术改造。
工业应用表明,精制液化气的含硫总量由改造前的170m g/m3下降到60m g/m3以下,产品铜片腐蚀合格率由30%~40%提高到100%,液化气碱渣达到零排放。
改造后单元操作成本每年下降约58万元。
关键词:液化气;脱硫醇;液膜;铜片腐蚀;碱渣中图分类号:TE26.7;T E624.5+5 文献标识码:B 文章编号:1009-0045(2007)06-0520-04中国石化西安石化分公司液化气脱硫醇装置处理量为10t/h。
2006年采用宁波中一石化科技有限公司开发的液膜脱硫醇组合工艺,对装置进行了改造。
改造后,液化气处理量增加了50%,装置运行正常,脱硫醇后液化气总硫含量小于60mg/m3,碱渣、污水达到零排放,恶臭尾气排放量也大幅度降低,取得了一定经济效益和环保效益。
1 原工艺存在的问题原工艺存在的主要问题是:(1)脱硫醇后液化气含硫总量偏高,脱硫率为40%~80%;(2)液化气铜片腐蚀合格率低(30%~40%),需要在砂滤塔后串联1台精脱硫塔,但精脱硫剂使用寿命较短,通常需12~18个月更换1次,且废脱硫剂需要进行环保处理;(3)碱渣排放量大,每年排放约350;t(4)二硫化物随尾气进入辐射炉焚烧,经常造成恶臭;(5)在气温低于0 时,尾气管线容易被二硫化物冷凝液堵塞,影响装置正常运行。
2 液膜脱硫醇组合工艺特点2.1 脱硫醇在液化气中,碱洗脱硫醇效率的高低取决于碱液与液化气的接触面积及碱液的有效浓度。
在液膜脱硫醇组合新工艺中,碱液进入液膜脱硫醇反应器后,均匀分布于亲水性纤维表面,形成极大的接触面积,液化气中的H2S,RS H等与N a OH充分接触并进行反应,提高了脱硫醇效率。
同时,由于是同相层流接触,可有效减少碱液乳化夹带,保证产品液化气铜片腐蚀合格。
液膜脱硫醇反应器比常规的填料塔传质效率提高约50倍。
2.2 碱液氧化再生采用富氧常温氧化法及结构气体分布器等专利技术[1]对原氧化塔进行技术改造,使之达到将碱液中硫醇钠深度氧化、提高再生碱液质量的目的。
采用富氧常温氧化再生技术后,硫醇钠氧化速度比原工艺提高3倍以上,氧化深度加深,碱液中的二硫化物浓度可以控制在200010-6以下,低于常规填料型氧化塔。
因此再生碱液质量得到提高,碱液能够长周期循环使用而不影响脱硫率。
3 装置改造液化气脱硫醇装置改造后的流程见图1。
对原碱液氧化塔进行改造:拆除内部填料,塔内件改为宁波中一石化科技有限公司的专利结构气体分布器。
将原工艺抽提塔改为新工艺二硫化物分离罐。
增设胺液聚结分离器,对胺洗脱H2S 后液化气进行聚结分离,脱除夹带胺液,有效减轻夹带胺液对脱硫醇的影响。
增设液膜脱硫醇反应器,用于碱洗脱硫醇。
增设PSA(Pressure*收稿日期:2007-05-11;修回日期:2007-08-24作者简介:李锋(1976!),男,河南漯河人,学士。
Sw ing Adso r b i o n ,变压吸附)富氧发生机,为氧化再生提供质量分数为30%~45%的富氧。
图1 改造后的液化气液膜脱硫醇组合工艺流程4 工业应用4.1 装置原料改造后液化气脱硫醇装置处理来自胺洗脱H 2S 后液化气,处理量为15t/h ,总硫含量小于400m g /m 3。
4.2 操作条件采用新工艺后,装置的主要操作条件见表1。
碱液采用间歇式氧化再生工艺,根据生产实际,再生系统为3~4个月运行1次,每次运行3~5d 。
表1 组合工艺操作条件项目指标项目指标液膜脱硫醇单元碱液富氧再生单元(间歇式氧化)压力/M Pa 1.0~1.2 压力/M Pa 0.1~0.3 温度/25~35 温度/25~35 碱液质量分数/%18~25 富氧体积分数/%30~45 预碱洗碱/液化气 (质量比)0.10~0.15富氧风量/(m 3∀h -1)3~5 液膜脱硫醇反应器碱/液化气(质量比)0.06~0.08 催化剂浓度 106150注:催化剂采用磺化酞菁钴。
4.3 分析方法分别根据SH /T 0222!92,S H /T 0232!92测定液化气总硫含量及铜片腐蚀状况。
4.4 产品液化气总硫情况4.4.1 改造前后产品含硫对比改造前,产品液化气平均总硫含量为170m g /m 3;改造后,碱液富氧再生单元未运行时,试样总硫含量为5~60mg /m 3,平均值为35m g /m 3。
当该单元运行时,在再生碱液中夹带微量氧化生成的二硫化物,当再生碱液循环进行脱硫醇时,夹带的二硫化物进入液化气,导致产品液化气总硫含量短时间升高,这种现象被称为#再生碱加硫效应∃。
实际运行中,在确保循环碱液脱硫醇效率的前提下,采用间歇式运行碱液氧化再生单元的方式,以此来抑制产品液化气总硫含量升高。
4.4.2 碱液再生质量对产品液化气总硫含量的影响表2显示,改造后随再生碱液中氢氧化钠质量分数增加,产品液化气总硫含量降低,同时再生碱液中硫醇钠质量分数越低,产品液化气总硫含量亦越低。
表2 改造后再生碱液质量与产品液化气总硫含量的关系NaO H 质量分数/%18.720.121.6硫醇钠质量分数/% 3.42.00.6产品总硫含量/(m g ∀m -3)473119采用碱液富氧常温氧化再生工艺后,系统再生碱液温度为25~35 ,碱液质量分数可以提高到30%,不会对碳钢设备产生腐蚀。
碱浓度提高,有利于提高硫醇的脱除深度。
改造后再生碱液中,二硫化物对产品液化气仍具有加硫效应,但比改造前小得多(见表3)。
∀521∀ 第6期 李锋等 液化气液膜脱硫醇组合工艺及其应用表3 改造后再生碱液中二硫化物对液化气总硫含量的影响再生碱液二硫化物含量106液化气总硫含量/(m g∀m-3)备 注46043碱液氧化再生前数据127086碱液氧化再生后1d的数据113582碱液氧化再生后2d的数据96076碱液氧化再生后3d的数据液化气总硫含量与再生碱液中二硫化物含量有直接的关系[2]。
改造前,装置更换再生碱液10d后,液化气二硫化物含量即逐步上升到250010-6,最高可达到900010-6,导致产品液化气硫含量超过170m g/m3。
由此可见,改造前产品液化气总硫含量超标,主要是由于再生碱液中二硫化物对液化气的加硫效应所致。
比较改造前后产品液化气进行硫形态分析结果(见表4)可知,产品液化气中硫醇含量通常小于20m g/m3;总硫含量高时,二硫化物比例一般占到总硫含量的80%以上。
由生产可知,采用富氧常温氧化再生工艺后,可明显降低再生碱液中的二硫化物含量,降低二硫化物对液化气的加硫效应。
表4 改造前后产品液化气硫成分分析产品液化气试样A试样B试样C总硫含量/(m g∀m-3)4657163硫醇含量/(m g∀m-3)121425二硫化物含量/(m g∀m-3)3443未检测注:试样A和B为改造后的数据。
试样C为改造前数据,未作二硫化物分析。
4.5 产品液化气铜片腐蚀情况研究表明[3]:碱洗脱硫醇后的液化气,夹带H2S的可能性非常小,引起铜片腐蚀不合格的主要原因是夹带微量乳化碱液,而传统脱硫醇工艺很难避免。
改造前,碱洗脱硫醇后的液化气经过水洗、砂滤后,液化气碱液夹带质量分数为0.1%~ 1.0%,铜片腐蚀合格率只有30%~40%;将砂滤后液化气经过精脱硫后,铜片腐蚀合格率可达99%以上。
但随着时间的推移,铜片腐蚀合格率又会逐渐下降,需更换脱硫剂,否则无法保证铜片腐蚀合格率。
这不仅影响到产品质量,增加脱硫成本,而且废脱硫剂也需要进行环保处理。
改造后,对液膜脱硫醇反应器出口液化气进行残留物分析,检测不到碱液,同时对产品液化气进行铜片腐蚀分析,合格率为100%。
4.6 液化气胺液聚结分离情况新增胺液聚结器后,需定期排放聚结器底部的胺液,一般10d排放1次,每次约120L,频繁时2d排放1次。
胺液聚结分离器对液化气中夹带胺液有较好的脱除效果,有效控制了夹带胺液对碱液的污染。
4.7 碱液氧化再生由表5可知,在相同处理量条件下,富氧氧化再生工艺的硫转化速率高于常规工艺;前者的氧气利用率高于后者,前者碱液和尾气中二硫化物含量降低幅度很大,说明新工艺二硫化物的分离效果得到显著提高,有利于从源头上消除恶臭污染。
新工艺运行1年多来,碱液没有更换,脱硫效果稳定,碱渣排放量降为零。
表5 改造前后碱液再生系统主要技术参数对比工艺类别反应温度/硫醇钠质量分数/%硫转化速率/(kg∀m-3∀h-1)氧气利用率/%碱液中二硫化物含量106尾气中二硫化物含量/(mg∀m-3)碱渣排放量/(t∀a-1)常规氧化50~65 1.3~1.80.6~0.815~304700~900030000~120000350富氧氧化25~35 1.2~1.71.8~2.5921000~25005000~65000 25~350.8~1.20.9~1.8651000~25005000~650005 经济与环保效益改造后,液化气总硫含量可稳定在60m g/m3以下,保证了气分装置丙烯硫含量达标和球罐区民用液化气的总硫含量合格。
改造前后液化气精制系统物耗和能耗成本分别约为84,26万元/a,每年可节约运行成本58万元。
采用新工艺后,碱渣排放每年减少约350,t 且二硫化物从分离罐得以有效分离,仅有少部分随尾气到焚烧炉燃烧,减轻了污水处理和恶臭气体处理的压力。
6 结论a.采用液膜脱硫醇组合工艺后,在碱液氧∀522∀石 化 技 术 与 应 用 第25卷化单元不运行时,产品液化气总硫含量可稳定在60m g/m3以下;运行时,产品液化气总硫含量稳定在100m g/m3以下;无论是否运行碱液氧化再生单元,产品液化气铜片腐蚀合格率均达到100%。
b.采用胺液聚结分离技术及碱液富氧常温氧化新技术后,脱硫效果稳定,碱液可以长期循环使用。
c.改造后,工艺流程简单,单元操作成本下降约58万元/a。
污水、碱渣均达到零排放。
参考文献:[1]宁波中一石化科技有限公司.一种再生含有硫醇钠碱液的方法[P].中国专利,200610050894.0.2006.[2]陈泽坚.液化气脱硫质量的瓶颈[J].广石化科技,2002,12(3):10-12.[3]聂通元.液化石油气铜片腐蚀不合格原因及后精制工艺研究[J].炼油设计,2000,30(11):43-45.相关文献链接:[1]江军锋,朱亚东,曹红斌.液膜技术在液化石油气脱硫中的工业应用[J].炼油技术与工程,2006,36(7):31-34.[2]李广庆.催化氧化法在液化气脱硫醇装置上的应用[J].化学工业与工程技术,2006,27(2):47-48.[3]潘光成,李涛,陶志平,等.催化裂化汽油轻馏分碱液抽提脱硫醇的实验室研究[J].石油炼制与化工,2005,36(10):24-27.[4]万一.液态烃脱硫醇装置的工艺改造[J].河南化工,2001(6):36-37.Integral process and application of re m ovi ng m ercaptan fro m li quefi ed petroleu m gas by li quid fil mL i Feng,Shen M i n g,T ian Bo(X i%an P etroche m ical Co m pany,SI NOPEC,X i%an710086,China)Abstract:Lique fied petro l e u m gas(LPG)re m o ving m ercaptan unit i n X i%an Petr oche m ica lCo m pa ny w as reva m ped by usi n g li q u i d fil m process.The resu lts sho w ed t h at the content o f tota l su l p hur i n re fi n ed LPG decli n ed fro m170m g/m3to60m g/m3, pass precent o f t h e product corr osion resistance o f copper p iece w as i m pr oved fro m30%-40%to 100%,and the dischar ge o f a l k aline residue w as ze ro.A fter reva m ping,the un it operati o n cost w as de creased by580thousands yuan per year.K ey w ords:li q ueified petroleum gas;re m oval o f m ercaptan;liquid fil m;corrosion resistance o f cop per p iece;al k aline resi d ue&简讯&植物油加氢脱氧异构化制备#绿色∃柴油工艺美国UOP公司和意大利埃尼公司开发出从植物油生产#绿色∃柴油的工艺,可将这种#绿色∃柴油与石油基柴油调和使用。