液化气脱硫醇装置运行情况总结
燃气脱硫系统的改造及运行总结
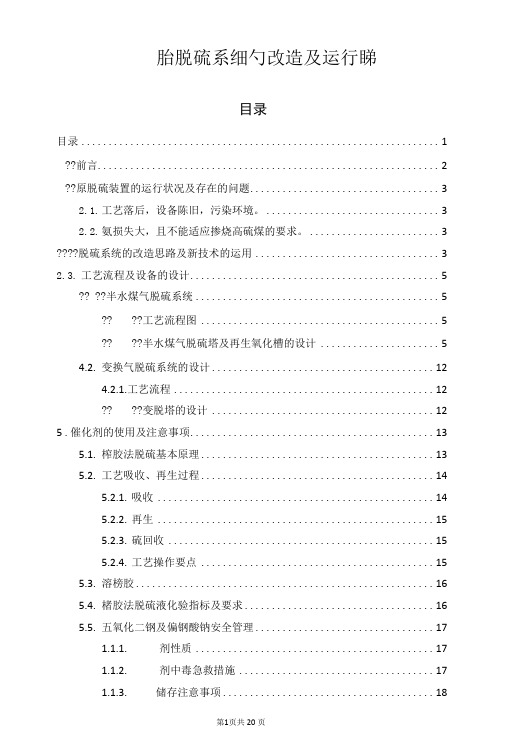
胎脱硫系细勺改造及运行睇目录目录 (1)前言 (2)原脱硫装置的运行状况及存在的问题 (3)2.1.工艺落后,设备陈旧,污染环境。
(3)2.2.氨损失大,且不能适应掺烧高硫煤的要求。
(3)脱硫系统的改造思路及新技术的运用 (3)2.3.工艺流程及设备的设计 (5)半水煤气脱硫系统 (5)??工艺流程图 (5)??半水煤气脱硫塔及再生氧化槽的设计 (5)4.2.变换气脱硫系统的设计 (12)4.2.1.工艺流程 (12)??变脱塔的设计 (12)5 .催化剂的使用及注意事项 (13)5.1.榨胶法脱硫基本原理 (13)5.2.工艺吸收、再生过程 (14)5.2.1.吸收 (14)5.2.2.再生 (15)5.2.3.硫回收 (15)5.2.4.工艺操作要点 (15)5.3.溶榜胶 (16)5.4.楮胶法脱硫液化验指标及要求 (16)5.5.五氧化二钢及偏钢酸钠安全管理 (17)1.1.1.剂性质 (17)1.1.2.剂中毒急救措施 (17)1.1.3.储存注意事项 (18)1.1.4.操作注意事项 (18)1.1.5.劳保穿戴要求 (18)1.1.6.泄漏应急处理措施 (18)1.1.7.管理规定 (18)6.新建的楮胶法脱硫系统的生产运行状况 (19)____________ 1-刖百众所周知,脱硫是合成氨生产中原料气净化的重要工艺环节。
目前我国大多数合成氨厂均以无烟煤为原料。
一方面随着优质低硫无烟煤的价格不断上涨,供应紧张。
而另一方面,碳镂市场又日渐萎缩,效益下滑,举步维坚。
为了适应市场竞争及追求较佳的经济效益,众多小氮肥企业纷纷对原料路线进行适当的调整。
不断地扩能改造开发新产品使其产品多样化,才不至于在市场竞争中遭到淘汰。
鉴于此,安微某公司,在3000吨合成氨装置的基础上,合成氨生产装置经过了扩能及联产甲醇的改造。
经过不断地发展,目前已具备了年产6万吨氨醇的生产能力。
产品由单一的生产碳镂走向了生产碳镂、甲醇、液氨并举之路。
脱硫运行管理总结汇报

脱硫运行管理总结汇报脱硫运行是煤炭、石油等工业领域中常见的处理过程,目的是去除燃料中的硫化物污染物,降低排放浓度,改善环境质量。
我在过去的一段时间里负责脱硫运行管理工作,现就此进行总结汇报,包括脱硫设备的运行状况、操作管理的经验教训以及改进措施等方面的内容。
首先,我对脱硫设备的运行状况进行了详细的分析和总结。
通过监控脱硫设备的运行参数和排放浓度,我发现设备的稳定性非常好,在规定的运行条件下,能够达到预期的脱硫效果。
然而,我也注意到在高负荷运行情况下,脱硫效果可能会有所下降,需要进行相应的调整和优化。
其次,我总结了在脱硫运行管理过程中的一些经验教训。
首先,定期检查设备的运行状况和维护情况非常重要,可以及时发现并解决问题,避免设备故障对生产造成不利影响。
其次,加强操作人员培训和技术指导,提高其操作水平和专业素质,减少操作错误和事故发生的可能性。
另外,密切监测和控制脱硫剂的投加量、浓度和pH值等参数,保证脱硫效果稳定可靠。
最后,及时准确地记录和汇报脱硫运行数据,有利于进行后续的分析和决策。
然后,我针对脱硫运行中存在的一些问题,提出了改进措施。
首先,可以考虑引入先进的自动化控制系统,提高脱硫设备的自动化程度,减少人为因素的影响。
其次,优化脱硫剂的选择和投加方式,提高脱硫效率,降低运行成本。
另外,加强与相关部门的沟通和合作,在运行管理方面形成有效的协同机制,共同解决脱硫运行过程中的问题。
最后,我总结了脱硫运行管理工作中取得的成绩和经验,同时也认识到了存在的不足之处。
在今后的工作中,我将继续努力,加强学习和实践,提高我在脱硫运行管理方面的专业能力和管理水平,为企业的可持续发展做出更大的贡献。
通过这段时间的脱硫运行管理工作,我不仅对脱硫设备的运行情况有了更深入的了解,也提升了自己的业务能力和管理水平。
希望在未来的工作中,能够继续发挥自己的优势,为脱硫运行管理工作做出更大的贡献,为保护环境、改善空气质量做出应有的努力。
脱硫设备运行报告模板

脱硫设备运行报告模板
一、报告概述
本报告旨在总结脱硫设备的运行情况,对设备的运行效率、稳定性进行评估,
提出相关的改进措施和建议。
二、设备概况
脱硫设备是用于烟气脱硫的关键设备,主要由吸收塔、循环泵、喷淋系统、反
应器、烟气处理系统、除湿系统等部分组成。
目前,本单位使用的脱硫设备型号为XXX,安装于XXX号机组,使用时间为XX年。
三、设备运行情况
1. 设备运行效率
本次脱硫设备的运行效率评估主要从两个方面进行:
•脱硫效率:在实际运行过程中,对脱硫效率进行取样分析,结果表明脱硫效率保持在XX%以上,符合国家标准。
•运行稳定性:对设备运行过程中的数据进行分析发现,设备运行维持稳定,未出现过多的异常情况,说明设备稳定性较好。
2. 设备运行故障及处理
在本次脱硫设备的运行中,主要发生了以下几种故障:
•故障1:XXX
•故障2:XXX
针对以上的设备故障,我们尽快采取了以下的处理措施:
•解决措施1:XXX
•解决措施2:XXX
经过对设备故障的处理,设备运行效率得到了提升。
四、设备改进建议
根据以上的设备运行情况和故障及处理情况,本次对脱硫设备的改进建议如下:•建议1:XXX
•建议2:XXX
以上的改进建议,我们将会积极采纳和实施,以不断提升脱硫设备的运行效率和稳定性。
五、总结
综上所述,本报告对脱硫设备运行情况进行了全面的评估和总结,并提出了相应的改进建议,相信这些建议的贯彻和落实必将进一步提升脱硫设备的运行效率和稳定性,为保护环境和保障生产做出应有的贡献。
脱硫系统连续熔硫装置生产运行总结

脱硫系统连续熔硫装置生产运行总结1 工艺流程来自脱硫系统的硫泡沫,进入硫泡沫浓缩槽中,经静止沉降与浓缩的硫泡沫分离后自流返回脱硫系统。
浓缩后得到的硫膏,用泵送人熔硫釜。
硫膏在熔硫釜的换热段内与加热熔硫后返回的清液换热升温,然后硫膏下降进入加热段。
加热段由间接蒸汽供热,硫膏在加热段内经加热、分离、熔融、沉降等过程,熔融硫与脱硫清液分离,呈液态硫磺继续下降进入贮硫段。
在贮硫段内,熔融硫经排硫装置断续排出后冷却装袋入库。
加热段分离出的高温清液,向上进入熔硫器换热段并同下降的硫膏间接逆流换热降温后,从换热段返回脱硫系统。
连续熔硫工艺流程简图2 工艺装置及特点硫泡沫在加热段中以相对较快的速度连续强制对流,其液固两相间传热效果好,熔硫操作温度相对较低,熔硫效率高。
熔融了的硫磺以重力沉降的形式自流入贮硫段后被断续排出。
当硫泡沫的处理量相同时,该熔硫设备具有体积小、重量轻、管道化、连续操作、熔硫效率高、操作弹性大等优点。
2.1 工艺装置技术参数主要生产工艺参数如下:熔硫釜下部温度:140℃熔硫釜内部压力:0.3~0.4MPa外排清液温度:70~85℃加热蒸汽压力:0.6MPa2.2 工艺装置特点(1)该熔硫工艺实现了生产操作的连续化,该工艺从熔硫设备的进料到外排清液均实现了连续生产。
熔硫釜的供热根据操作温度需要控制,控制进口蒸汽阀以满足熔硫过程的正常运行。
(2)采用深度换热工艺。
并分别在以下三个阶段分离出温度不等的脱硫清液。
一是在硫泡沫槽中加热沉降分离出的清液,二是重复向熔硫釜中添加硫膏阶段断续排出的分离清液,三是熔硫结束放硫排渣后排出的分离清液。
这三个阶段所排脱硫清液的温度分别为80℃、95℃、135℃左右,其加权平均温度约90℃。
连续熔硫工艺的硫泡沫浓缩槽对全部熔硫装置的节能降耗作用显著。
其次,熔硫过程中分离出的高温清液,经连续熔硫釜的换热段与待加热硫膏换热降温后再外排,其外排清液温度低于75℃,远小于传统工艺在硫泡沫槽中分离清液80℃的操作温度,故熔硫釜中待外排清液的热量得到了较为充分地利用。
焦化液化气脱硫醇装置存在问题分析及技术改造

焦化液化气脱硫醇装置存在问题分析及技术改造摘要:脱硫废液综合利用带来的环境风险不明,并且缺乏相关的污染控制标准或技术规范,致使综合利用受阻,脱硫废液的综合利用和安全处置已成为我国钢铁和炼焦行业面临的客观难题。
基于对脱硫废液产生和利用处置现状的分析,可对脱硫废液进行精准管控从而防范环境风险,也对提高脱硫废液的综合利用率有一定的指导作用,还可促进钢铁和炼焦行业的健康发展。
基于此,本文章对焦化液化气脱硫醇装置存在问题分析及技术改造进行探讨,以供参考。
关键词:焦化液化气脱硫醇装置;问题分析;技术改造引言近几年,随着我国经济的发展和科学技术的发展,化学工业得到了较好的发展。
在此过程中,炼油工艺日趋成熟,生产效率提高,炼油设备的更新换代,设备的功能也逐步完善。
在这种大环境下,炼油装备管理工作要进行管理变革、技术革新、合理运用现代管理技术,才能更好地提高炼油设备的管理水平,推动炼油产业高速发展。
一、脱硫废液产生节点目前,我国炼焦行业广泛采用以对苯二酚、双核酞菁钴磺酸铵及硫酸亚铁组成的醌钴铁类复合型催化剂为催化剂、以氨为碱源的HPF法,对焦炉煤气进行脱硫脱氰。
具体工艺流程为:经过冷凝冷却的煤气经预冷塔冷却后进入脱硫塔,与塔顶喷淋下来的含氨脱硫液逆流接触进行脱硫,脱除硫的煤气自脱硫塔上部排出引入硫铵工序。
在脱硫过程中,吸收了煤气中硫化氢、氰化氢的脱硫液中不断生成硫代硫酸盐、硫氰酸盐、硫酸盐等无机盐,当脱硫液中含盐量超过250g/L时,脱硫效率会明显降低,为了保证脱硫效率的稳定、煤气下游工序的正常生产和产品质量,脱硫液须进入反应槽,大部分用泵送入再生塔,再生后经液位调节器返回脱硫塔循环使用;部分进入硫泡沫槽后返回反应槽循环使用。
为了避免脱硫液黏度增加堵塞脱硫塔和再生塔、腐蚀设备和管道,部分企业将剩余部分脱硫液排出成为脱硫废液;另一部分企业将剩余部分脱硫液送至提盐工序或制酸工序进行资源化利用,提出盐分的脱硫液返回反应槽循环使用。
脱硫维护工作总结
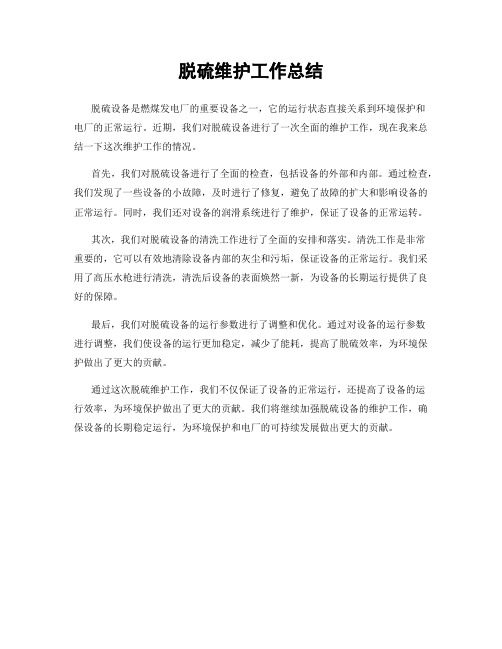
脱硫维护工作总结
脱硫设备是燃煤发电厂的重要设备之一,它的运行状态直接关系到环境保护和
电厂的正常运行。
近期,我们对脱硫设备进行了一次全面的维护工作,现在我来总结一下这次维护工作的情况。
首先,我们对脱硫设备进行了全面的检查,包括设备的外部和内部。
通过检查,我们发现了一些设备的小故障,及时进行了修复,避免了故障的扩大和影响设备的正常运行。
同时,我们还对设备的润滑系统进行了维护,保证了设备的正常运转。
其次,我们对脱硫设备的清洗工作进行了全面的安排和落实。
清洗工作是非常
重要的,它可以有效地清除设备内部的灰尘和污垢,保证设备的正常运行。
我们采用了高压水枪进行清洗,清洗后设备的表面焕然一新,为设备的长期运行提供了良好的保障。
最后,我们对脱硫设备的运行参数进行了调整和优化。
通过对设备的运行参数
进行调整,我们使设备的运行更加稳定,减少了能耗,提高了脱硫效率,为环境保护做出了更大的贡献。
通过这次脱硫维护工作,我们不仅保证了设备的正常运行,还提高了设备的运
行效率,为环境保护做出了更大的贡献。
我们将继续加强脱硫设备的维护工作,确保设备的长期稳定运行,为环境保护和电厂的可持续发展做出更大的贡献。
脱硫运行年终个人工作总结
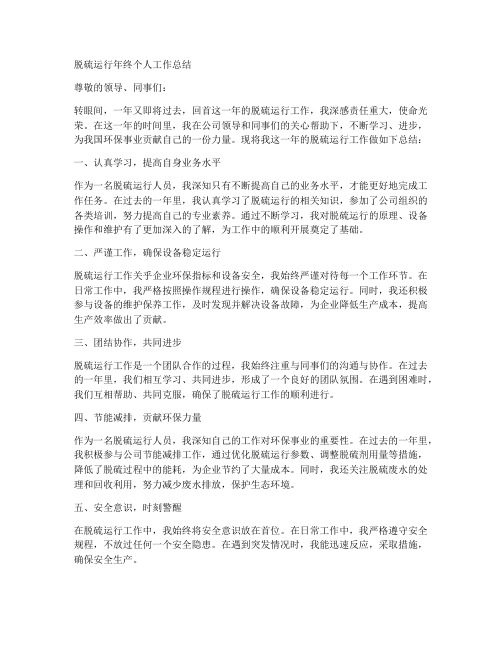
脱硫运行年终个人工作总结尊敬的领导、同事们:转眼间,一年又即将过去,回首这一年的脱硫运行工作,我深感责任重大,使命光荣。
在这一年的时间里,我在公司领导和同事们的关心帮助下,不断学习、进步,为我国环保事业贡献自己的一份力量。
现将我这一年的脱硫运行工作做如下总结:一、认真学习,提高自身业务水平作为一名脱硫运行人员,我深知只有不断提高自己的业务水平,才能更好地完成工作任务。
在过去的一年里,我认真学习了脱硫运行的相关知识,参加了公司组织的各类培训,努力提高自己的专业素养。
通过不断学习,我对脱硫运行的原理、设备操作和维护有了更加深入的了解,为工作中的顺利开展奠定了基础。
二、严谨工作,确保设备稳定运行脱硫运行工作关乎企业环保指标和设备安全,我始终严谨对待每一个工作环节。
在日常工作中,我严格按照操作规程进行操作,确保设备稳定运行。
同时,我还积极参与设备的维护保养工作,及时发现并解决设备故障,为企业降低生产成本,提高生产效率做出了贡献。
三、团结协作,共同进步脱硫运行工作是一个团队合作的过程,我始终注重与同事们的沟通与协作。
在过去的一年里,我们相互学习、共同进步,形成了一个良好的团队氛围。
在遇到困难时,我们互相帮助、共同克服,确保了脱硫运行工作的顺利进行。
四、节能减排,贡献环保力量作为一名脱硫运行人员,我深知自己的工作对环保事业的重要性。
在过去的一年里,我积极参与公司节能减排工作,通过优化脱硫运行参数、调整脱硫剂用量等措施,降低了脱硫过程中的能耗,为企业节约了大量成本。
同时,我还关注脱硫废水的处理和回收利用,努力减少废水排放,保护生态环境。
五、安全意识,时刻警醒在脱硫运行工作中,我始终将安全意识放在首位。
在日常工作中,我严格遵守安全规程,不放过任何一个安全隐患。
在遇到突发情况时,我能迅速反应,采取措施,确保安全生产。
总之,在过去的一年里,我在公司领导和同事们的帮助下,取得了一定的成绩。
然而,我也深知自己还存在诸多不足,需要在今后的工作中不断努力,提高自己的业务能力和综合素质。
液化石油气深度脱硫工业应用总结

液化石油气深度脱硫工业应用总结于宏【摘要】为满足下游甲基叔丁基醚(MTBE)装置的生产要求,2011年7月,锦西石化分公司对重油催化裂化装置吸收稳定及脱硫系统进行隐患整改,采用深度脱硫技术对液化石油气脱硫醇部分进行了改造.介绍深度脱硫技术在重油催化裂化装置液化石油气脱硫醇系统的应用情况.对过去两年装置运行数据的统计和系统分析结果表明,液化石油气深度脱硫技术在装置运行中操作简便、稳定可靠;液化石油气脱后总硫质量浓度低于10 mg/m3,液化石油气除臭精制液单耗为0.05 kg/t,新鲜碱液单耗为0.05 kg/t,软化水单耗为30 kg/t.单位液化气处理成本累计降低2.95 RMB ¥/t,上述指标均大大低于传统的液化石油气脱硫醇工艺,产生了良好的经济和社会效益.【期刊名称】《炼油技术与工程》【年(卷),期】2014(044)003【总页数】4页(P6-9)【关键词】重油催化;液化石油气;脱硫;脱硫醇;减排【作者】于宏【作者单位】中国石油天然气股份有限公司锦西石化分公司,辽宁省葫芦岛市125000【正文语种】中文产自催化裂化装置和延迟焦化装置的液化石油气(简称液化气)是聚丙烯和甲基叔丁基醚(MTBE)生产的重要原料,要求其总硫质量浓度小于50 mg/m3,铜片腐蚀不超过1级[1]。
近年来,汽油质量升级要求降低MTBE的硫含量,进而要求液化气的硫质量浓度降低到10 mg/m3以下。
传统的液化气脱硫醇工艺因脱硫率低,能耗、物耗高,环境污染大,无法满足新的生产要求。
在这种情况下,各种新型脱硫醇催化剂、设备和工艺应运而生。
锦西石化分公司液化气脱硫醇装置于1998年8月投产,设计规模168 kt/a,采用MEROX液-液抽提工艺。
投用后装置存在着铜片腐蚀经常不合格、脱后总硫质量浓度偏高(120 mg/m3左右)的问题,影响了液化气产品出厂及下游MTBE、聚丙烯装置的生产。
2005年该公司对重油催化裂化(简称重催)装置进行MIP扩能改造,液化气脱硫醇装置维持原工艺,对部分设备进行了改造,但脱后液化气铜片腐蚀经常不合格和脱后总硫质量浓度偏高(100 mg/m3左右)的问题仍然没有解决。
焦化液化石油气脱硫醇装置运行状况分析及其优化
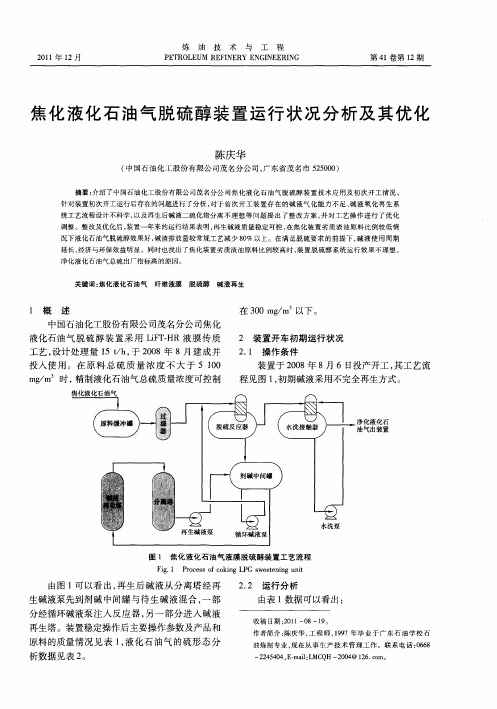
1 概
述
在 3 0rg m 0 / 。以下 。 a
中 国石 油化 工股份 有 限公司 茂名 分公 司焦化
液化石油气脱硫醇装 置采 用 L TH i . R液膜传质 F
工艺 , 设计 处理 量 1 / , 20 5th 于 0 8年 8月建 成 并 投 入使 用 。在 原 料 总 硫 质 量 浓 度 不 大 于 510 0 mgm / 时 , 精制 液化 石油气 总硫 质量 浓度 可控制
况下液化石油气脱硫醇效果好 , 碱渣排放量较常规工艺减少 8 % 以上 。在满足脱硫要 求的前提 下, 0 碱液使用周 期 延长 , 经济与环保效益明显。同时也找 出了焦化装置劣质渣油原料 比例较高时 , 置脱硫 醇系统运行效果不理想 , 装
净 化液化石油气总硫出厂指标 高的原 因。 关键词 : 焦化液化石油气 纤维液膜 脱硫醇 碱液再生
21 0 1年 1 2月
炼 油 技 术 与 工 程 P T 0 E M R FN R N I E RN E R L U E IE Y E GN E I G
第4 1卷第 1 2期
焦 化 液化 石 油 气 脱 硫 醇 装 置运 行 状 况 分 析及 其优 化
陈庆华
( 中国石油化工股份有 限公 司茂名分公 司, 东省茂名 市 5 50 ) 广 2 00
炼
油
技
术
与
工
程
2 1 年第 4 01 1卷
() 1 装置 工 艺 操 作 平 稳 , 精 制 液化 石 油 气 但 总硫未 能达 标 , 总 硫 波 动较 大 且 碱 液再 生 效 果 且 差 。20 08年 9月 1日起 通 过 加 大 氧 化 风量 后 碱
低 流量 。氧化风 量调低后直接导致再 生效果下 降。 ( )循 环碱 液质 量 的好 坏直 接影 响到精 制液 2 化石 油气 总硫 高低 , 环碱液 质量好 ( N O 循 即 a H浓
催化裂化干气和液化气脱硫装置设计生产总结
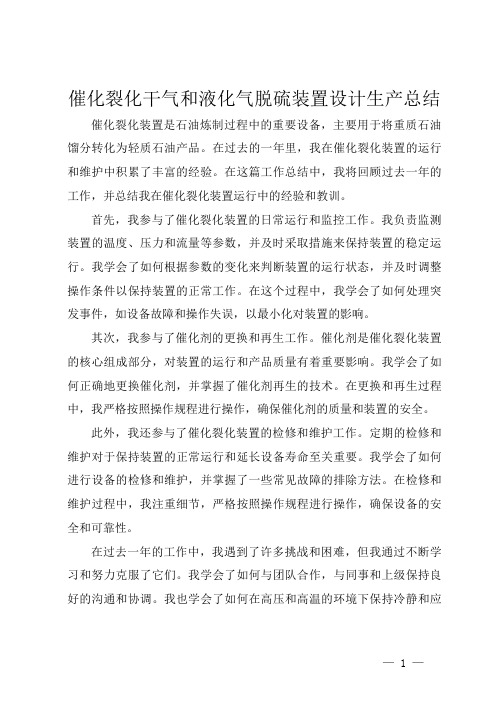
催化裂化干气和液化气脱硫装置设计生产总结催化裂化装置是石油炼制过程中的重要设备,主要用于将重质石油馏分转化为轻质石油产品。
在过去的一年里,我在催化裂化装置的运行和维护中积累了丰富的经验。
在这篇工作总结中,我将回顾过去一年的工作,并总结我在催化裂化装置运行中的经验和教训。
首先,我参与了催化裂化装置的日常运行和监控工作。
我负责监测装置的温度、压力和流量等参数,并及时采取措施来保持装置的稳定运行。
我学会了如何根据参数的变化来判断装置的运行状态,并及时调整操作条件以保持装置的正常工作。
在这个过程中,我学会了如何处理突发事件,如设备故障和操作失误,以最小化对装置的影响。
其次,我参与了催化剂的更换和再生工作。
催化剂是催化裂化装置的核心组成部分,对装置的运行和产品质量有着重要影响。
我学会了如何正确地更换催化剂,并掌握了催化剂再生的技术。
在更换和再生过程中,我严格按照操作规程进行操作,确保催化剂的质量和装置的安全。
此外,我还参与了催化裂化装置的检修和维护工作。
定期的检修和维护对于保持装置的正常运行和延长设备寿命至关重要。
我学会了如何进行设备的检修和维护,并掌握了一些常见故障的排除方法。
在检修和维护过程中,我注重细节,严格按照操作规程进行操作,确保设备的安全和可靠性。
在过去一年的工作中,我遇到了许多挑战和困难,但我通过不断学习和努力克服了它们。
我学会了如何与团队合作,与同事和上级保持良好的沟通和协调。
我也学会了如何在高压和高温的环境下保持冷静和应— 1 —对突发事件。
这些经验和技能对于我未来的工作和职业发展都将非常有帮助。
总的来说,过去一年的催化裂化装置工作经历让我受益匪浅。
我不仅学到了专业知识和技能,还培养了团队合作和应对压力的能力。
我将继续努力学习和提升自己,在未来的工作中发挥更大的作用。
— 2 —。
液化气脱硫装置近期问题和调整情况

液化气脱硫装置近期问题及调整情况一、近期问题1、MTBE装置脱硫含硫不合格:6月10日16点MTBE脱后硫含量8.7ppm,岗位将防胶剂注入泵行程调至50%并联系调度高硫外送,进行操作调整后20点加样11.3ppm,依旧不合格,初步判断高硫外送量以及防胶剂注入量过小,防胶剂行程调至80%,高硫外送量调至146kg/h,调整操作后11日零点采样6.6ppm,脱后样合格,岗位恢复正常操作,高硫外送量降至30kg/h,防胶剂行程调至50%。
16日零点脱后样10.5ppm,岗位联系调度高硫外送,4点加样5.9ppm。
17日8点再次出现不合格样10.0ppm,岗位在调整操作后加样合格6.7ppm。
18日MTBE脱后含硫样连续不合格,硫含量大于8ppm,岗位在调整防胶剂注入量和高硫外送量后,产品质量依然不合格,在和兄弟单位以及防胶剂厂家交流后初步判断为原料中带硫醇,联系化验对脱后样品进行博士实验定性分析,分析结果为MTBE脱后含有硫醇。
即催化液化气脱硫装置液化气中的硫醇没有完全脱去,微量的硫醇随液化气在经过气分装置分离和MTBE装置反应分离后,由于MTBE比醚后碳四对硫化物有更高的溶解性,这些微量的硫醇富集于MTBE中,防胶剂对重组分硫有很好的脱除效果,但对轻组分硫没有显著的脱除效果,从而导致MTBE脱后硫含量超标。
2、罐区丙烷腐蚀不合格二、双脱装置调整情况1、催化双脱装置:在分析MTBE脱后不合格为液化气中含有硫醇后,双脱岗位及时采取相应措施:6月18日,将双脱D-701,D-702液位各退掉10%,退到D-809碱渣罐中,将D-707新鲜碱液补充在D-701,D-702中。
置换后D-701,D-702液位由55%升至65 %。
6月19日,将D-703水洗罐液位退掉5%,用除盐水置换。
将D-701,D-702中的碱液各退掉5%至D-809为加入GL除臭精致液做准备。
6月20日,中午12时,安排岗位人员开始加入GL除臭精致液,白班加入10桶精致液,中夜班加入精致液11桶,21日加入精致液20桶,22日加入精致液9桶,共加入精致液50桶,共计10吨。
脱硫年终工作总结范文(3篇)
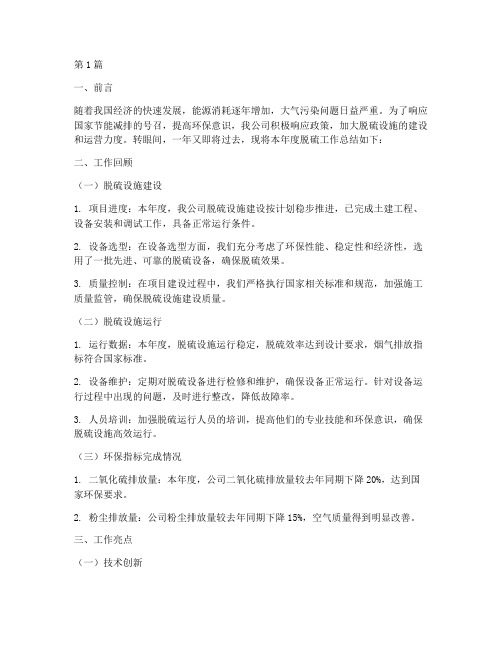
第1篇一、前言随着我国经济的快速发展,能源消耗逐年增加,大气污染问题日益严重。
为了响应国家节能减排的号召,提高环保意识,我公司积极响应政策,加大脱硫设施的建设和运营力度。
转眼间,一年又即将过去,现将本年度脱硫工作总结如下:二、工作回顾(一)脱硫设施建设1. 项目进度:本年度,我公司脱硫设施建设按计划稳步推进,已完成土建工程、设备安装和调试工作,具备正常运行条件。
2. 设备选型:在设备选型方面,我们充分考虑了环保性能、稳定性和经济性,选用了一批先进、可靠的脱硫设备,确保脱硫效果。
3. 质量控制:在项目建设过程中,我们严格执行国家相关标准和规范,加强施工质量监管,确保脱硫设施建设质量。
(二)脱硫设施运行1. 运行数据:本年度,脱硫设施运行稳定,脱硫效率达到设计要求,烟气排放指标符合国家标准。
2. 设备维护:定期对脱硫设备进行检修和维护,确保设备正常运行。
针对设备运行过程中出现的问题,及时进行整改,降低故障率。
3. 人员培训:加强脱硫运行人员的培训,提高他们的专业技能和环保意识,确保脱硫设施高效运行。
(三)环保指标完成情况1. 二氧化硫排放量:本年度,公司二氧化硫排放量较去年同期下降20%,达到国家环保要求。
2. 粉尘排放量:公司粉尘排放量较去年同期下降15%,空气质量得到明显改善。
三、工作亮点(一)技术创新1. 引进先进的脱硫技术,提高脱硫效率。
2. 对脱硫设备进行技术改造,降低能耗和运行成本。
(二)节能减排1. 通过脱硫设施运行,减少二氧化硫和粉尘排放,降低环境污染。
2. 优化能源结构,提高能源利用效率。
(三)团队建设1. 加强脱硫运行团队建设,提高团队凝聚力和战斗力。
2. 定期开展员工培训,提高员工专业技能和环保意识。
四、不足与改进(一)不足1. 脱硫设施运行过程中,部分设备存在故障,影响脱硫效率。
2. 部分员工环保意识不强,对脱硫设施运行维护不够重视。
(二)改进措施1. 加强设备维护,提高设备运行稳定性。
烟气脱硫运行年度总结(3篇)

第1篇一、前言随着我国环保政策的日益严格,燃煤电厂烟气脱硫成为降低大气污染、改善环境质量的重要手段。
本年度,我单位烟气脱硫系统运行稳定,取得了显著成效。
现将本年度烟气脱硫运行情况进行总结,以期为今后工作提供参考。
二、主要工作及成效1. 系统运行稳定:本年度,我单位烟气脱硫系统运行稳定,未发生重大故障,保证了烟气排放达标。
2. 脱硫效率提升:通过优化运行参数,提高脱硫效率,本年度脱硫效率达到95%以上,优于设计要求。
3. 运行成本降低:通过优化运行方案,降低能耗和物耗,本年度烟气脱硫运行成本较上年降低5%。
4. 环保效益显著:本年度,烟气脱硫系统有效降低了二氧化硫排放量,对改善区域环境质量起到了积极作用。
三、存在问题及改进措施1. 设备腐蚀问题:部分设备存在腐蚀现象,影响了系统稳定运行。
针对此问题,我们将加强设备防腐措施,提高设备使用寿命。
2. 运行参数波动:运行过程中,部分参数波动较大,影响了脱硫效率。
我们将进一步优化运行参数,提高系统稳定性。
3. 培训力度不足:部分员工对烟气脱硫系统的操作和维护知识掌握不足。
我们将加强员工培训,提高员工技能水平。
针对上述问题,我们将采取以下措施:1. 加强设备维护保养:定期对设备进行检查、维修,及时消除设备隐患。
2. 优化运行参数:根据实际情况,调整运行参数,确保系统稳定运行。
3. 加强员工培训:定期组织员工进行技能培训,提高员工操作和维护水平。
四、展望未来,我单位将继续加强烟气脱硫系统的运行管理,不断提高脱硫效率,降低运行成本,为我国环保事业贡献力量。
1. 技术创新:关注烟气脱硫领域的新技术、新工艺,提高系统运行效率。
2. 节能减排:进一步降低能耗和物耗,实现绿色发展。
3. 环保达标:确保烟气排放达标,为改善环境质量作出贡献。
总之,本年度烟气脱硫系统运行取得了显著成效,但也存在一些问题。
我们将以此次总结为契机,不断改进工作,为我国环保事业做出更大贡献。
第2篇一、引言随着我国经济的快速发展和能源需求的不断增长,燃煤电厂作为主要的能源生产者,对环境的影响日益凸显。
脱硫装置运行总结
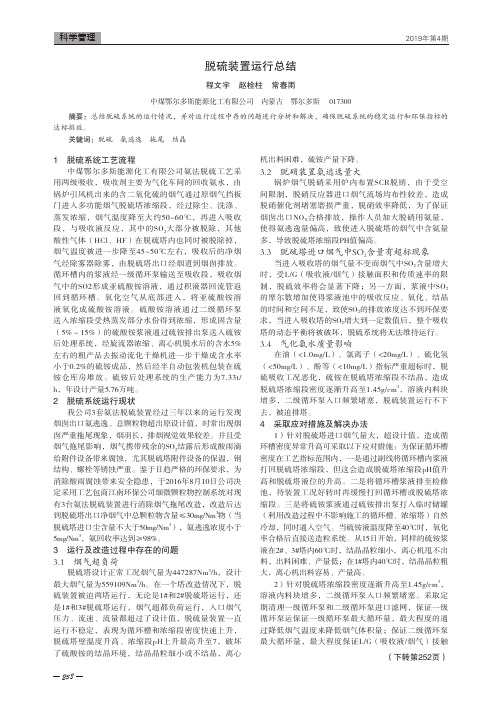
2381 脱硫系统工艺流程中煤鄂尔多斯能源化工有限公司氨法脱硫工艺采用两级吸收,吸收剂主要为气化车间的回收氨水,由锅炉引风机出来的含二氧化硫的烟气通过原烟气挡板门进入多功能烟气脱硫塔浓缩段,经过除尘、洗涤、蒸发浓缩,烟气温度降至大约50~60℃,再进入吸收段,与吸收液反应,其中的SO 2大部分被脱除,其他酸性气体(HCl、HF)在脱硫塔内也同时被脱除掉,烟气温度被进一步降至45~50℃左右,吸收后的净烟气经除雾器除雾,由脱硫塔出口经烟道到烟囱排放。
循环槽内的浆液经一级循环泵输送至吸收段,吸收烟气中的SO2形成亚硫酸铵溶液,通过积液器回流管返回到循环槽。
氧化空气从底部进入,将亚硫酸铵溶液氧化成硫酸铵溶液。
硫酸铵溶液通过二级循环泵送入浓缩段受热蒸发部分水份得到浓缩,形成固含量(5%~15%)的硫酸铵浆液通过硫铵排出泵送入硫铵后处理系统,经旋流器浓缩、离心机脱水后的含水5%左右的粗产品去振动流化干燥机进一步干燥成含水率小于0.2%的硫铵成品,然后经半自动包装机包装在硫铵仓库房堆放。
硫铵后处理系统的生产能力为7.33t/h,年设计产量5.76万吨。
2 脱硫系统运行现状我公司3套氨法脱硫装置经过三年以来的运行发现烟囱出口氨逃逸、总颗粒物超出原设计值,时常出现烟囱严重拖尾现象,烟羽长,排烟视觉效果较差。
并且受烟气拖尾影响,烟气携带残余的SO 2结露后形成酸雨滴给附件设备带来腐蚀,尤其脱硫塔附件设备的保温,钢结构、螺栓等锈蚀严重。
鉴于日趋严格的环保要求,为消除酸雨腐蚀带来安全隐患,于2016年8月10日公司决定采用工艺包商江南环保公司细微颗粒物控制系统对现有3台氨法脱硫装置进行消除烟气拖尾改造,改造后达到脱硫塔出口净烟气中总颗粒物含量≤30mg/Nm 3物(当脱硫塔进口尘含量不大于50mg/Nm 3),氨逃逸浓度小于5mg/Nm 3,氨回收率达到≥98%。
3 运行及改造过程中存在的问题3.1 烟气超负荷脱硫塔设计正常工况烟气量为447287Nm 3/h,设计最大烟气量为559109Nm 3/h。
脱硫工作总结范文(3篇)

第1篇一、前言随着我国经济的快速发展,工业生产规模不断扩大,大气污染问题日益严重。
为了改善环境质量,我国政府高度重视环保工作,大力推进节能减排和大气污染防治。
脱硫技术作为防治大气污染的重要手段,在电力、化工、钢铁等行业得到广泛应用。
本人在脱硫岗位上工作多年,现将工作总结如下:一、脱硫工作概述1. 脱硫技术简介脱硫技术是指通过物理、化学或生物方法,将烟气中的二氧化硫(SO2)转化为无害物质,从而减少大气污染的技术。
目前,我国主要采用湿法脱硫技术,即利用石灰石、石膏等脱硫剂与烟气中的SO2反应,生成石膏等固体废弃物。
2. 脱硫工作职责作为一名脱硫工作人员,我的主要职责包括:(1)负责脱硫系统的运行、维护和检修工作;(2)对脱硫设备进行定期检查,确保设备正常运行;(3)对脱硫运行数据进行监测和分析,及时发现和解决问题;(4)参与脱硫项目的建设和改造工作;(5)对脱硫技术进行研究和创新,提高脱硫效率。
二、脱硫工作总结1. 脱硫系统运行情况(1)脱硫系统运行稳定,SO2排放浓度低于国家规定标准;(2)脱硫设备运行良好,故障率低;(3)脱硫运行数据监测准确,为环保部门提供可靠数据。
2. 脱硫系统维护与检修(1)定期对脱硫设备进行清洁、润滑和紧固;(2)对脱硫系统进行定期检查,发现故障及时处理;(3)对脱硫设备进行定期更换,确保设备性能;(4)对脱硫系统进行技术改造,提高脱硫效率。
3. 脱硫运行数据分析(1)对脱硫运行数据进行实时监测,分析脱硫系统运行状态;(2)根据运行数据,优化脱硫运行参数,提高脱硫效率;(3)对脱硫系统运行数据进行统计和分析,为环保部门提供数据支持。
4. 脱硫项目建设和改造(1)参与脱硫项目的可行性研究、设计、施工和验收工作;(2)根据脱硫项目需求,提供技术支持和服务;(3)对脱硫项目进行跟踪管理,确保项目顺利实施。
5. 脱硫技术研究和创新(1)关注国内外脱硫技术发展趋势,不断学习新技术;(2)结合实际工作,开展脱硫技术研究和创新;(3)撰写脱硫技术论文,分享工作经验。
脱硫工段运行情况分析总结报告

脱硫工段运行情况报告一、系统状态化工公司脱硫系统分常脱和变脱两个脱硫,均属净化车间,满量下处理水煤气气量约38000NnI3∕h,水煤气4S含500-600mg∕m∖工艺流程简述如下:1、常脱气体流程:由造气气柜送来的水煤气经罗茨鼓风机加压至约35KPa,经冷却塔降温至40℃以下进入常脱脱硫塔下部,与塔上部喷淋下来的脱硫溶液逆流接触,脱除气体中的AS(50-150mg∕m3),气体由脱硫塔顶部出来,经干式除尘器后去压缩岗位。
脱硫溶液流程:脱硫贫液经贫液泵加压打入水煤气脱硫塔上部,溶液自上而下,由水煤气脱硫塔底部出来,吸收了HzS的富液,进入富液槽,用富液泵加压经再生槽喷射器和再生槽,浮选出来的硫泡沫溢流到硫泡沫槽,经泡沫泵加压送到熔硫工段,再生后的贫液溢流入贫液槽,贫液由贫液泵加压送入水煤气脱硫塔上部循环使用;贫富液泵循环量约470m3∕h o主要设备:水煤气脱硫塔Φ4800X36000X14富液槽Φ7000×12052×10常脱再生槽Φ6500×8∕Φ5600×10×7878常脱贫液槽Φ4500X5660×102、变脱气体流程:由变换过来的压力为2.05MPa,温度40°C以下的变换气由脱硫塔下部进入,由气体分布器均匀分布后与塔顶喷淋下来的脱硫溶液逆流接触后,吸收气体中的AS(IOPPn1以下),经塔后分离器到脱碳岗位。
脱硫溶液流程:脱硫贫液由贫液泵打入变脱塔上部,自上而下,吸收4S后,溶液从脱硫塔底部通过系统压力的作用进入再生槽喷射器,溶液得到再生,再生后的溶液溢流至贫液槽,经贫液泵加压再次打入变脱塔,进行循环使用;贫液泵循环量约32(W∕h°主要设备:变换气脱硫塔Φ2800×41520×20变脱再生槽Φ5700X8/①4800X1OX7878变脱贫液槽Φ3600X5560X12二、存在问题化工公司当前因限电轻负荷生产(约70%负荷),根据车间介绍情况,同时查看以前记录报表,目前对生产造成严重影响,总结主要存在以下几个问题。
脱硫设备运行报告范文模板

脱硫设备运行报告范文模板
一、背景介绍
脱硫设备是燃煤电厂的重要组成部分之一,目的是将燃煤产生的二氧化硫排放
量降到国家规定的标准以内,达到环境保护的要求。
二、设备运行情况
1. 设备运行时间和累计运行时间
本次脱硫设备的运行时间为XXX,累计运行时间为XXX,符合预定的运行时间
范围。
2. 设备工作状态
脱硫设备工作状态良好,操作记录表中无任何异常记录。
经检查,各设备连接
管路未发现渗漏,设备内部压力、温度稳定,运行过程中无噪音和振动。
3. 设备运行能力
根据监测数据,脱硫设备能够有效地将二氧化硫的排放浓度控制在国家规定标
准以内。
三、运行故障及处理情况
在本次运行中,脱硫设备未发生任何故障,未进行任何维修和保养。
四、存在的问题及建议
本次脱硫设备运行情况良好,但在平时的维护过程中,我们发现了一些存在的
问题:
1.设备的防腐保护需要加强,以减少设备在酸雨等恶劣环境中的腐蚀。
2.某些设备部件的使用寿命已经接近或超过了使用寿命,需要进行更换
或维护。
为了保障设备的长期稳定运行,我们建议在日常使用中,注意设备的维护保养,并定期对设备进行检修,以保证设备完好无损。
五、总结
本次脱硫设备的运行情况良好,没有发生任何故障,运行效率稳定,符合环保法规要求。
我们将继续关注设备的日常维护和管理,以保证设备的长期稳定运行和有效地减少污染物排放。
谢谢。
脱硫工作年终总结
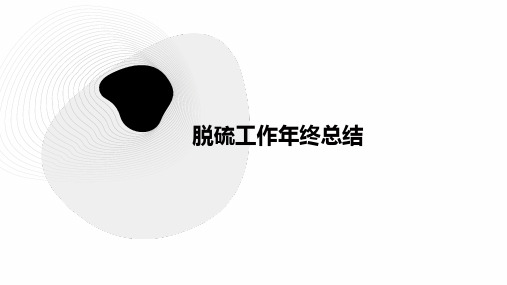
其他低硫化合物,实现脱硫目的。
超声波脱硫技术
03
利用超声波的空化效应、机械效应和化学效应,强化脱硫过程
,提高脱硫效率。
现有技术优化改进举措
石灰石-石膏法脱硫优化
改进石灰石研磨系统、优化石膏脱水方式,提高脱硫效率和石膏 品质。
氨法脱硫技术改进
优化氨逃逸控制技术、开发高效氨回收系统,降低运行成本和环境 污染。
智能化运维系统建设
推进了脱硫系统智能化运维系统建设,提高了设备管理水平和运维 效率。
Part
02
技术创新与应用实践
新技术、新工艺探索
活性焦干法脱硫技术
01
研究活性焦的制备、改性及脱硫性能,开发高效、低成本的活
性焦干法脱硫工艺。
微生物脱硫技术
02
利用特定微生物或酶催化作用,将含硫化合物转化为硫单质或
加大安全培训和演练的力度,提高员工应 对突发事件的能力,确保脱硫装置的安全 运行。
推进环保技术创新
加强与相关部门的沟通和协作
积极研究和推广先进的脱硫技术和设备, 进一步提高污染物排放控制水平,降低对 环境的影响。
加强与环保、安监等相关部门的沟通和协 作,及时了解政策动态和监管要求,确保 脱硫工作的顺利开展。
确保资源投入,保障计划顺利推进
资金保障
对明年脱硫工作计划所 需资金进行充分预算和 筹备,确保资金及时到 位,保障计划的顺利推 进。
人员保障
加强脱硫专业队伍建设 ,引进高素质人才,提 高员工技能水平和工作 效率,为计划的实施提 供有力保障。
物资保障
对脱硫系统所需物资进 行充分储备和采购,确 保物资供应及时、质量 可靠,满足系统运行和 改造需求。
循环流化床脱硫技术提升
- 1、下载文档前请自行甄别文档内容的完整性,平台不提供额外的编辑、内容补充、找答案等附加服务。
- 2、"仅部分预览"的文档,不可在线预览部分如存在完整性等问题,可反馈申请退款(可完整预览的文档不适用该条件!)。
- 3、如文档侵犯您的权益,请联系客服反馈,我们会尽快为您处理(人工客服工作时间:9:00-18:30)。
液化气脱硫醇装置运行情况总结
一、装置情况简介:
液化气脱硫醇装置由南京金炼科技有限公司设计,2009年4月份建成,12月份随1000万吨/年炼油装置同时开车,开车初期运行平稳,产品质量合格。
装置将纤维膜分离技术和Merox工艺很好的结合到一起,提高了液化气脱硫醇的效率。
基本流程如下:
脱硫后的混合焦化液化气经焦化液化气过滤器(SR-301A/B)后,从一级液化气脱硫醇罐(D-301)上部进入一级脱硫醇纤维膜接触器(FFC-301),在纤维膜的表面液化气与自二级碱洗沉降罐(D-302)来的碱液接触,使含有的少量硫化氢以及硫醇被碱液抽提出来进入碱液。
之后液化气和碱液依靠重力在一级液化气脱硫醇罐(D-301)沉降分离。
为保证液化气中的硫醇脱除至满意的效果,串级设置两台液化气脱硫醇纤维膜接触器。
脱除了硫化氢及硫醇的焦化液化气从一级液化气脱硫醇罐(D-301)的顶部流出,从上部进入二级脱硫醇纤维膜接触器(FFC-302),在纤维膜的表面液化气与再生后的碱液接触,进一步脱除硫醇,经二级液化气脱硫醇罐(D-302)沉降聚结分离,进入水洗纤维膜接触器(FFC-303)与除盐水接触,使液化气中的溶解性杂质溶于水中。
从液化气水洗罐(D-303)顶出来的精制液化气至产品罐区。
除盐水经除盐水过滤器(SR-303A/B) 过滤后,由除盐水注入泵(P-305)间断加入,含油污水间断排出。
从一级液化气脱硫醇罐(D-301)底出来的碱液经碱液加热器(E-301)加热至60℃并与一定量的空气混合后进入氧化塔(C-301),在塔内被空气氧化为二硫化物,碱液得到再生。
再生后的碱液依次经过二硫化物沉降分离罐(D-304)、碱液冷却器(E-302)冷却至40℃后,从碱液再生沉降罐(D-305)上部进入碱液再生接触器(FFC-304),在纤维膜表面,碱液和轻石脑
油接触,使碱液中的少量的二硫化物被轻石脑油抽提出来。
轻石脑油作为抽提溶剂经汽油循环泵(P-304A/B)循环使用,部分含轻硫石脑油外甩出装置,同时补充少了新鲜的轻石脑油,以控制抽提的总硫含量。
再生后的碱液进碱液循环泵(P-303A/B)送回二级碱液接触器(FFC-302)循环使用。
流程图见附图.一
二、运行情况介绍:
装置从开工到2010年2月25日,液化气总硫一直保持合格,在此期间,原油硫含量一直维持在0.5%左右,液化气进脱硫醇前总硫维持在不大于4000mg/Nm3。
自2月26日后,炼油部开始调整原油硫含量至1.2%,液化气总硫出现不合格,经车间多次调整工艺参数,液化气总硫仍不能合格(数据见附表二),为此,炼油部聘请石油大学专家和设计公司来到现场研究解决方案。
在此过程中,先后提出了以下解决方案:
1、提高石脑油外送量至2t/h(原1t/h),降低石脑油停留时间。
2、降低二硫化物分离罐D-304压力至 0.23Mpa,降低碱液中氧含量。
3、提高E-302循环水流量,尽量降低碱液温度,降低碱液中氧含量。
4、提高催化剂浓度至225-250PPm。
5、改用液态磺化态箐钴,提高催化剂溶解度。
6、委托石油大学对液化气做形态分析,另外增加分析位置及项目,由原5个采样点增加到
9个,分别为胺洗后、水洗后硫醇和总硫,一级、二级脱后总硫,再生前、萃取前、萃取后碱液硫醇钠、硫化钠、碱浓度,石脑油进的总硫、硫醇,石脑油出的硫醇,帮助分析确认原因。
7、采裂化重石脑油和萃取后碱液,按1:1比例充分混合静置后,分析前后重石硫含量,评
价萃取后碱液效果,为评价萃取效果提供数据。
三、调整分析结果及解决方案
1、原料性质变化对装置造成一定的影响,但不是根本原因。
2、石脑油萃取试验发现再生后碱液二硫化物仍达到4000ppm以上,分离不合格。
3、通过对比发现,美国Merox工艺和南京金炼科技有限公司的工艺存在一定区别,美国
Merox工艺采用了两级二硫化物萃取分离工艺,而后者只是一级萃取,分离效果相对较差,导致一部分二硫化物分离不完全,带入二级碱洗系统后融入液化气,造成液化气总硫不合格。
解决方案:
1、增加石脑油循环量至12t/h,提高石脑油进装置量不小于2t/h,提高萃取效果。
2、委托设计单位改造
附图一
附表二。