液化气脱硫醇不同工艺技术及设备比较110322
液化气脱硫技术及应用.doc

液化紗脱硫技术及其应用莫娅南(中**辽阳钉分公司,**辽阳,111003)摘要:阐述了液化**脱硫技术的进展,以及各种技术在国内实际应用过程中存在的问题和改进的措施。
关键词:液化**脱硫技术The desulfuratcd technology of LPG and applicationMoyanan Wangbo(PetroChina Liaoyang Petrochemistry Company, Liaoning Liaoyang, 111003? Abstract: The article summarizes the development of LPG desulfurated technology, the problems of domestic application of the desulfurated technology and the improved methods are also be summarized ・Keywords: LPG. desulfurated technology1.液化材脱硫技术液化桂脱硫技术一般根据其硫含量及净化要求而定,对于硫含量低或处理量小的液化材采用干法,如用氧化锌、氧化铝、活性炭吸附或者用简单的碱法吸收。
对于硫含量高、处理量大的液化材的处理分成两步:第一步利用碱液脱除液化衬中的硫化氢,或将cos水解后一并脱除,常用的碱液为醇胺溶液及相应的复配溶液;第二步则是采用含磺化酥菁钻催化剂的碱液碱洗,碱洗的方式可以为抽提,也可以采用纤维膜技术。
1.1无碱催化氧化脱臭技术液化衬无碱催化氧化脱臭技术是以复合金属氧化物为催化剂,利用液化林中所溶解的微量氧将硫醇氧化成二硫化物,在总硫超标的情况下可通过精憎除去二硫化物,同时预碱洗过程使用固定床脱硫剂脱硫化氢,使整个工艺过程不存在碱渣排放问题。
中**齐鲁分公司研究院开发了QTM-01硫醇催化氧化催化剂,该催化剂经工业侧流试验结果表明,在液相及常温条件下可有效地把液化材中的硫醇氧化成二硫化物,无碱液排放加。
液化气脱硫工艺技术分析

液化气脱硫工艺技术分析作者:才涛来源:《科学与财富》2019年第16期摘要:在液化气石油化工生产中,脱硫工艺是一项重要技术应用,对于提高液化气生产质量及降低液化气使用环境污染问题具有重要意义。
本文对液化气脱硫工艺技术进行了探讨,旨在促进液化气脱硫工艺技术的发展,降低液化气含硫量,是现实社会经济与环境保护效益的共同发展。
关键词:液化气;脱硫工艺;脱硫醇液化石油气生产在社会经济发展中有着重要作用,但其在促进经济发展的同时,也带来较为严重的空气污染问题,尤其是液化石油气中硫物质的存在,如果不加以处理对环境带来的影响是非常大的。
随着社会环保意识的不断增强,国家对液化气中含硫量也有了更高要求,在这种形势下,液化气脱硫工艺技术应用受到进一步重视,如何不断优化脱硫工艺技术以在确保液化石油气质量的基础上降低含硫量成为了社会高度关注和不断探究的一个重要课题。
一、液化气脱硫必要性分析液化石油气中含有一定量的硫化氢、硫醇、羰基硫等成分,这些成分的存在不仅给液化气加工造成影响,而且在环境污染方面危害也较大。
液化气中硫化物超标就会出现产品异味、催化剂中毒等问题,因此为确保液化气加工过程安全性及降低化工生产对环境造成的影响,加强脱硫工艺技术应用具有非常大的必要性和重要性。
二、液化气脱硫工艺技术(一)液化气脱硫化氢工艺液化石油气中硫化氢是硫存在的一种主要形式,也是液化气脱硫工艺技术应用目的的一个重要方面。
目前液化气脱硫化氢主要有干法脱硫与湿法脱硫两种工艺。
干法脱硫主要是通过利用固体吸附剂的媳妇作用来达到脱出硫化氢的目的,氧化铁、氧化锌及活性炭等是常用的固体吸附剂。
这种工艺虽然操作比较简单,但是只能应用于含有少量硫化氢气体处理中,对于硫化氢含量较大的砌体并不适用,脱硫效果也并不理想。
湿法脱硫工艺是与干法相对的一种脱硫化氢技术,主要利用液体吸收剂对液化气气中硫化氢进行洗涤脱出,包括物理吸收法、直接氧化法及胺溶剂化学吸收法,其中胺法占据主要地位。
脱硫工艺技术对比

脱硫工艺技术对比脱硫工艺技术是指将燃煤电厂或锅炉排放的硫化物进行减排的技术方法。
目前常见的脱硫工艺技术包括湿法脱硫和干法脱硫两种。
下面将对这两种脱硫工艺技术进行对比。
湿法脱硫是一种利用化学反应将SO2转化为硫酸盐的方法。
这种技术主要包括石灰石石膏法、石灰浆喷雾吸收法和海水脱硫法等。
其中石灰石石膏法是最常用的湿法脱硫技术。
这种方法是将石灰石与SO2气体反应生成硫酸钙,然后再通过过滤的方式分离出硫酸盐。
湿法脱硫技术具有脱硫效率高、操作稳定等优点,但是其缺点是投资大、设备体积大、能耗高。
干法脱硫是一种通过化学吸附或物理吸附的方式将SO2气体去除的技术。
这种技术主要包括活性炭吸附法、电吸附法和干式法等。
其中活性炭吸附法是最常用的干法脱硫技术。
这种方法是将煤炭燃烧产生的SO2经过活性炭吸附,使其转化为硫酸盐。
干法脱硫技术具有投资小、装置简单等优点,但是其缺点是脱硫效率低、处理能力有限。
对比来看,湿法脱硫技术相较于干法脱硫技术在脱硫效率和稳定性上更有优势。
湿法脱硫技术通过化学反应将SO2转化为硫酸盐,脱硫效率可以达到90%以上,而干法脱硫技术的脱硫效率一般在70%左右。
此外,湿法脱硫技术操作相对稳定,适用范围广,可以适应不同燃煤电厂或锅炉的需求。
然而,湿法脱硫技术也存在一些问题。
首先是投资成本高,设备体积大,需要占用较多的空间。
其次是能耗高,需要大量的能源来进行操作。
另外,湿法脱硫技术还会产生大量的废水和废渣,对环境造成一定的污染。
干法脱硫技术相较于湿法脱硫技术在投资成本和能耗方面具有优势。
干法脱硫技术投资成本相对较低,适用于一些投资有限的企业。
同时,干法脱硫技术使用的能源相对较少,节省了能源成本。
然而,干法脱硫技术的脱硫效率相对较低,不能达到湿法脱硫技术的脱硫效果。
此外,干法脱硫技术对煤种的适应性较差,处理能力有限。
因此,在选择脱硫工艺技术时,需要综合考虑各种因素,选择最合适的技术方案。
综上所述,在湿法脱硫技术和干法脱硫技术之间进行对比,可以发现每种技术都有自己的优势和劣势。
脱硫工艺的比较

几种脱硫工艺的比较烟气脱硫经过了近30年的发展已经成为一种成熟稳定的技术,在世界各国的燃煤电厂中各种类型的烟气脱硫装置已经得到了广泛的应用。
烟气脱硫技术是控制SO2和酸雨的有效手段之一,根据脱硫工艺脱硫率的高低,可以分为高脱硫率工艺、中等脱硫率工艺和低脱硫率工艺;最常用是按照吸收剂和脱硫产物的状态进行分类可以分为三种:湿法烟气脱硫、半干法烟气脱硫和干法烟气脱硫。
1) 干法烟气脱硫工艺是采用吸收剂进入吸收塔,脱硫后所产生的脱硫副产品是干态的工艺流程,干法脱硫技术与湿法相比具有投资少、占地面积小、运行费用低、设备简单、维修方便、烟气无需再热等优点,但存在着钙硫比高、脱硫反应速度慢,设备庞大,脱硫效率低、副产物不能商品化等缺点。
干法烟气脱硫技术中,炉内喷钙优点同样有无污水和废酸排放,设备腐蚀小,净化后烟气烟温高,利于烟囱排放扩散,投资省占地少易于国产化等。
但是也有比较明显的缺点,它只适合煤种含硫量《2%,脱硫率低,脱硫率大概只有70%-90%,不能适应目前对SO2的排放限制越来越严的环保要求。
与常规煤粉炉相比,由于脱硫剂的加入和增湿活化的使用,会对锅炉的运行产生一定影响,比如结灰结渣,对锅炉受热面的磨损加重,也使锅炉效率降低。
该技术还需要改动锅炉,这些都会影响锅炉的运行。
对现有的除尘器也产生了响,由于灰量增加,除尘器效率应提高。
2) 半干法烟气脱硫工艺是采用吸收剂以浆液状态进入吸收塔(洗涤塔),脱硫后所产生的脱硫副产品是干态的工艺流程。
常见的半干法烟气脱硫技术主要包括循环悬浮式半干法、喷雾干燥法、炉内喷钙尾部增湿脱硫工艺等。
其中循环悬浮式半干法烟气脱硫技术较为成熟,应用也较为广泛。
3) 湿法烟气脱硫(FGD)的基本原理是碱性物质吸收并固定酸性的二氧化硫。
主要有两种方法,一种是石灰石(碳酸钙),即钙法;一种是氨,即氨法。
钙法烟气脱硫工艺是采用石灰石(碳酸钙)洗涤SO2烟气以脱除SO2。
钙法烟气脱硫技术以其脱硫效率较高、适应范围广、钙硫比低、技术成熟、副产物石膏可做商品出售等优点成为世界上占统治地位的烟气脱硫方法。
液化气脱硫工艺现状分析

液化气脱硫工艺现状分析液化气脱硫工艺是指对液化石油气中的硫化氢进行脱除的工艺。
随着环保意识的增强和对环境污染的重视,液化气脱硫工艺在化工领域中变得越来越重要。
本文将对液化气脱硫工艺的现状进行分析,并对其发展趋势进行展望。
一、液化气脱硫工艺的主要方法液化气中的硫化氢是一种有害的气体,不但对人体健康造成危害,而且还会对大气环境造成污染。
对液化气脱硫的要求越来越高。
目前,液化气脱硫主要采用以下几种工艺方法:1. 化学吸收法:化学吸收法是通过将液化气通入含有分散在其中的化学吸收剂的吸收器中,利用吸收剂与气体中的硫化氢发生化学反应,从而将硫化氢从气体中脱除。
常用的吸收剂有醇胺、乙二胺等。
化学吸收法能够将硫化氢脱除率达到较高水平,但是需要消耗大量的吸收剂,并且在后续的再生过程中也需要投入大量的能源,造成了一定的能源浪费。
2. 生物脱硫法:生物脱硫法是指利用一些特定微生物对液化气中的硫化氢进行生物氧化反应,从而将硫化氢转化为硫酸盐或者硫,达到脱硫的目的。
生物脱硫法具有脱硫效率高、耗能低、对环境友好等优点,但是存在微生物生长慢、对气体成分要求高、操作复杂等缺点。
3. 传质脱硫法:传质脱硫法是指利用气液两相之间的传质作用,将液化气中的硫化氢传送到液相中去。
传质脱硫法的工艺简单、操作方便、成本较低,但是脱硫效率和适用范围相对较窄。
上述方法各有优缺点,并且适用于不同的工艺条件和需要。
在实际工程中,常常会根据具体情况选择合适的液化气脱硫工艺方法,或者进行工艺的组合应用。
随着对环境保护的要求日益提高,液化气脱硫工艺在制气、天然气液化、LPG储罐、地下储罐以及分装装置等领域中得到了广泛应用。
在我国,液化气脱硫工艺的现状包括以下几个方面:1. 技术水平不断提高:近年来,我国在液化气脱硫工艺方面的技术水平不断提高,大量技术装备和工艺设备逐步更新升级。
在传质脱硫、化学吸收脱硫、生物脱硫等方面都取得了一定的突破和进展。
2. 成本不断降低:随着液化气脱硫工艺技术的进步和成熟,其成本不断降低。
各种脱硫技术方法的比较
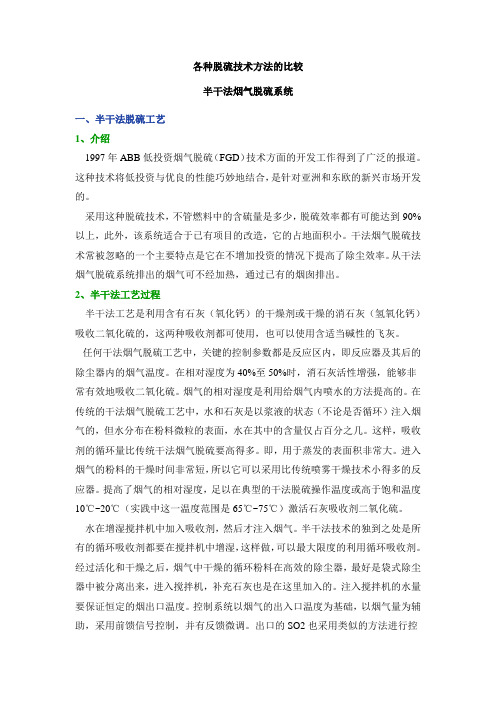
各种脱硫技术方法的比较半干法烟气脱硫系统一、半干法脱硫工艺1、介绍1997年ABB低投资烟气脱硫(FGD)技术方面的开发工作得到了广泛的报道。
这种技术将低投资与优良的性能巧妙地结合,是针对亚洲和东欧的新兴市场开发的。
采用这种脱硫技术,不管燃料中的含硫量是多少,脱硫效率都有可能达到90%以上,此外,该系统适合于已有项目的改造,它的占地面积小。
干法烟气脱硫技术常被忽略的一个主要特点是它在不增加投资的情况下提高了除尘效率。
从干法烟气脱硫系统排出的烟气可不经加热,通过已有的烟囱排出。
2、半干法工艺过程半干法工艺是利用含有石灰(氧化钙)的干燥剂或干燥的消石灰(氢氧化钙)吸收二氧化硫的,这两种吸收剂都可使用,也可以使用含适当碱性的飞灰。
任何干法烟气脱硫工艺中,关键的控制参数都是反应区内,即反应器及其后的除尘器内的烟气温度。
在相对湿度为40%至50%时,消石灰活性增强,能够非常有效地吸收二氧化硫。
烟气的相对湿度是利用给烟气内喷水的方法提高的。
在传统的干法烟气脱硫工艺中,水和石灰是以浆液的状态(不论是否循环)注入烟气的,但水分布在粉料微粒的表面,水在其中的含量仅占百分之几。
这样,吸收剂的循环量比传统干法烟气脱硫要高得多。
即,用于蒸发的表面积非常大。
进入烟气的粉料的干燥时间非常短,所以它可以采用比传统喷雾干燥技术小得多的反应器。
提高了烟气的相对湿度,足以在典型的干法脱硫操作温度或高于饱和温度10℃~20℃(实践中这一温度范围是65℃~75℃)激活石灰吸收剂二氧化硫。
水在增湿搅拌机中加入吸收剂,然后才注入烟气。
半干法技术的独到之处是所有的循环吸收剂都要在搅拌机中增湿,这样做,可以最大限度的利用循环吸收剂。
经过活化和干燥之后,烟气中干燥的循环粉料在高效的除尘器,最好是袋式除尘器中被分离出来,进入搅拌机,补充石灰也是在这里加入的。
注入搅拌机的水量要保证恒定的烟出口温度。
控制系统以烟气的出入口温度为基础,以烟气量为辅助,采用前馈信号控制,并有反馈微调。
炼油厂适用的液化气脱总硫及深度脱硫技术
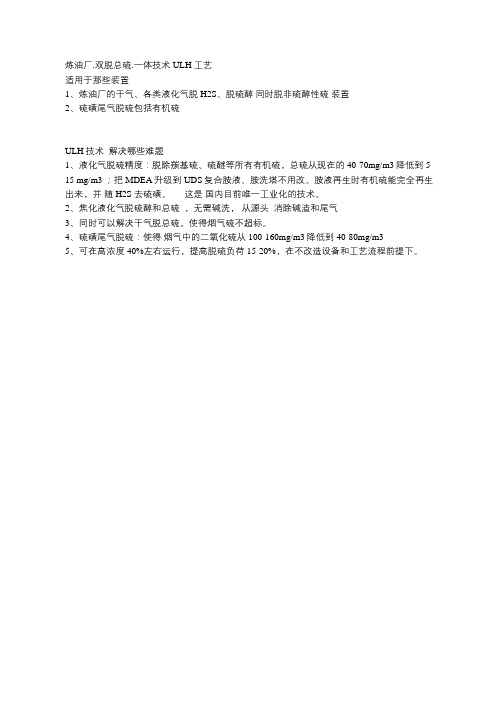
炼油厂.双脱总硫.一体技术 ULH 工艺
适用于那些装置
1、炼油厂的干气、各类液化气脱H2S、脱硫醇同时脱非硫醇性硫装置
2、硫磺尾气脱硫包括有机硫
ULH技术解决哪些难题
1、液化气脱硫精度:脱除羰基硫、硫醚等所有有机硫,总硫从现在的40-70mg/m3降低到 5-15 mg/m3 ;把MDEA升级到UDS复合胺液、胺洗塔不用改。
胺液再生时有机硫能完全再生出来,并随 H2S 去硫磺。
这是国内目前唯一工业化的技术。
2、焦化液化气脱硫醇和总硫,无需碱洗,从源头消除碱渣和尾气
3、同时可以解决干气脱总硫,使得烟气硫不超标。
4、硫磺尾气脱硫:使得烟气中的二氧化硫从100-160mg/m3降低到40-80mg/m3
5、可在高浓度40%左右运行,提高脱硫负荷15-20%,在不改造设备和工艺流程前提下。
干气液化气脱硫脱硫醇工艺讲解

干气液化气脱硫脱硫醇工艺讲解干气、液化气-脱硫、脱硫醇操作讲义 2.4.1. 脱硫岗位的任务(1) 利用化学吸收原理将干气及液化气中的硫化氢吸收下来,使干气及液化气中硫化氢含量达到质量要求。
(2) 采用预碱洗脱硫化氢及催化剂碱液抽提催化氧化脱硫醇工艺,将液化气中的硫化氢及硫醇脱除。
(3) 负责维护本岗位所属设备、仪表、电气可靠好用,保证安全生产。
(4) 严格遵守巡回检查制度,定时、定点对室内、外仪表进行对照,保证平稳生产。
(5) 优化操作,努力降低能耗及剂耗。
2.4.2. 脱硫岗位操作要点(1) 操作中发生超温、超压以及停水、电、汽、风等不正常现象,岗位要根据具体情况果断及时地进行处理,严防事故扩大。
(2) 严格按照工艺卡片规定控制好各塔压力、温度以及液、界位。
(3) 正常生产运行时,严防设备受憋、超压,串压,做到安全第一。
2.4.3. 净化干气硫化氢含量的控制控制目标:指令值范围内控制范围:?3,(V/V)相关参数:原料温度;原料量;脱硫塔压力;贫液量;溶剂贫液中硫化氢含量;贫液入塔温度控制方式:正常情况下,净化后的干气及液化气硫化氢含量由溶剂量的大小来控制。
正常调整:影响因素调整方法 1.贫液浓度的变化联系硫磺装置提高溶剂浓度 2.溶剂贫液量的变化加大贫液量 3.溶剂再生效果差,溶剂贫液中硫化氢联系降低贫液中的硫化氢含量含量高4.贫液入塔温度的变化联系控制好贫液温度5.原料温度的变化适当降低原料温度6.原料中的硫化氢含量的变化原料中硫化氢含量增加,可以提高溶剂量或联系厂调度提高溶液浓度 7.原料量的变化原料量增加,相应增加溶剂量 8.脱硫塔压力的变化提高脱硫塔压力The innovative city plan a: innovative city of City, comprehensively promote the implementation of national innovation pilot city, according to the Ministry of science and technology, on the sea of province "agreed as a national innovation pilot city of the little letter2.4.4. 干气脱硫塔压力的控制控制范围: 0.85-0.95MPa控制目标:正常操作中干气脱硫塔顶压力应控制在上述范围内,保证干气质量合格相关参数:高压瓦斯管网压力控制方式:干气脱硫塔压力由压控阀控制,通过控制干气出装置流量来控制干气脱硫塔压力正常调整:影响因素调整方法干气量的变化联系稳定岗位控制干气来量平稳高压瓦斯管网压力的变化联系调度瓦斯管网撤压仪表失灵仪表失灵,及时改手动或副线控制,联系仪表工处理异常处理:现象影响因素处理方法及时联系厂调度撤瓦斯管网压力,紧急时可以通瓦斯管网憋压过安全阀付线临时泄压塔压力升高,压力处理量突然大幅平稳处理量上限报警度增加仪表失灵,及时改手动或副线控制,联系仪表工压控阀失灵全关处理若原料干气中断,停止接受原料,及时关闭净化焦化部分故障或干气出装置阀,当稳定系统压力低于本系统时,干气中断,塔压力气压机故障,引起及时关闭稳定干气来的手阀,以保证系统内压力,下降干气中断维持溶剂循环和催化剂碱液循环,随时准备接受原料 2.4.5. 干气脱硫塔液位的控制控制范围: 45%?5%控制目标:正常操作中干气脱硫塔底液位应控制在上述范围内,保证平稳操作相关参数:干气脱硫塔压力,贫液循环量,富液闪蒸控制方式:干气脱硫塔底液位由液控阀控制,通过控制富液流量来控制干气脱硫塔液位正常调整:影响因素调整方法液面指示失灵联系仪表处理,加强现场液位指示的检查富液进料量突然增大,后稳定贫液量,加大富液到闪蒸罐量路不十分畅通干气脱硫塔压力波动稳定压力2etterto the Ministry of science and technology, on the sea of province "agreed as a national innovation pilot city of the little lity plan a: innovative city of City, comprehensively promote theimplementation of national innovation pilot city, according The innovative c异常处理:现象影响因素处理方法前路压力迅速上升,干气胺液回收干气脱硫塔液位器液位迅速上升甚过高,或没过干气通知厂调度并及时将干气切出脱硫装置至干气分液罐液位进口迅速上升2.4.6. 液化气脱硫抽提塔压力的控制控制范围: 1.40-1.50MPa控制目标:正常操作中液化气脱硫塔顶压力应控制在上述范围内,保证液化气硫醇含量合格相关参数:液化气流量,液化气与碱洗沉降罐压力,贫液进塔温度控制方式:干气脱硫塔压力由压控阀控制,通过控制干气出装置流量来控制干气脱硫塔压力正常调整:影响因素调整方法液化气量的变化联系稳定岗位控制液化气来量平稳液化气罐区系统故障憋压联系调度泄压仪表失灵仪表失灵,及时改手动或副线控制,联系仪表工处理液化气温度、溶剂温度的控制好液化气入脱硫温度和溶剂温度变化异常处理:现象影响因素处理方法后部憋压及时联系后部撤压,如果是脱硫醇系统问题紧急时可以通过安全阀付线临时泄压塔压力升高,压力处理量突然大幅平稳处理量上限报警度增加压控阀失灵全关仪表失灵,及时改手动或副线控制,联系仪表工处理3city of the little letter city, according to the Ministry ofscience and technology, on the sea of province "agreed as a national innovation pilotThe innovative city plan a: innovative city of City, comprehensively promote the implementation of national innovation pilot2.4.7. 液化气脱硫塔液位的控制控制范围: 45%?5%控制目标:正常操作中液化气脱硫塔液位应控制在上述范围内,保证平稳操作相关参数:液化气脱硫塔压力,贫液循环量,富液闪蒸罐压力控制方式:液化气脱硫塔液位由液控阀控制,通过控制富液流量来控制液化气脱硫塔液位正常调整:影响因素调整方法液面指示失灵联系仪表处理,加强现场液位指示的检查贫液进料量突然增大,后稳定贫液量,加大富液到闪蒸罐量路不十分畅通液化气脱硫塔压力的变化查找原因稳定液化气脱硫塔压力液化气预碱洗沉降罐界面的控制控制范围:45?5,控制方式:补充碱液和现场底部排碱渣正常调整:影响因素调整方法液化气带水严重,界面上升发现V1312界面上升快,应及时联系稳定岗位解决液化气带水问题碱液循环线堵塞,造成界面下降发现碱液循环线堵塞,一是进行蒸汽吹扫,启用伴热线,二是联系维修处理循环线2.4.8. 净化液化气硫醇含量的控制控制目标:指令值范围内控制范围:?3,(V/V)相关参数:碱液循环量,碱液浓度控制方式:正常情况下,净化后液化气硫醇含量由碱液量的大小来控制。
各脱硫工艺简介及对比

(2)SO2吸收系统 锅炉烟气通过静电除尘器,除去99.5%左右的烟尘,然后 进入引风机,在引风机出口进入FGD吸收塔,烟气从底部进 入喷雾吸收塔,与喷淋液逆流接触。烟气中的SO2经过FGD吸 收塔的吸收,其烟气二氧化硫脱除率在95%以上。净烟气在塔 体上段通过高效组合式除雾装置(有二级除雾设施,机械去除 雾滴效率在99.8%以上)除去烟气中的雾滴,净化后的烟气经 塔后烟道进入烟囱排放。吸收塔采用耐高温玻璃钢制作。 脱硫液在吸收塔内与烟气充分接触、反应后,经塔体底部 排灰水沟回流入混合池,流入混合池的脱硫液与石灰浆液进行 再生反应。
4、脱硫设计原则 (1)确保烟气(烟尘、二氧化硫)达标排放并达到总 量控制要求; (2)确保烟气治理系统的安全、稳定运行; (3)因地制宜,优化组合,制定具有针对性的技术实 施方案; (4)可利用废碱(液)脱硫,实现以废治废; (5)采用先进、成熟的脱硫工艺技术和设备,在确保达 到设计指标的前提下,结合厂方的实际情况,尽可能降低工 程投资和运行费用。
双碱法喷淋空塔具有以下优点: (1)系统简便,投资省; (2)脱硫效率高; (3)不易结垢; (4)液气比低,电耗省,运行成本低; (5)吸收塔采用喷淋空塔,阻力小,运行可靠。 (6)克服了旋流板塔易结垢、阻力大的缺点。 (7)以钠碱液为塔内主脱硫剂,以石灰或电石渣为 脱硫液塔外再生剂,可以达到设备和管道不结垢。 (8)本脱硫装置同时也是二级除尘设备。
3、脱硫系统说明
脱硫系统的工艺流程图见下页图。 整套系统由六大部分组成: (1)烟气系统;(2)SO2吸收系统;(3)吸收剂 制备及供给系统;(4)石膏脱水系统;(5)工艺水 系统;(6)电控系统。
(1)烟气系统 烟气从锅炉引风机后的烟道上引出,进入吸收塔。 在吸收塔内脱硫净化,经除雾器除去水雾,送入锅炉引 风机后的总烟道,经然后烟囱排入大气。在烟道上设一 段旁路烟道,并设置旁路挡板门,当锅炉启动、进入 FGD的烟气超温和FGD装置故障停运时,烟气由旁路挡 板经烟囱排放。 烟气系统主要包括FGD进出口烟道,进出口挡板门, 旁路挡板门以及与挡板门配套的执行机构。
煤化工技术专业《16种脱硫工艺技术以及实际应用情况详解》
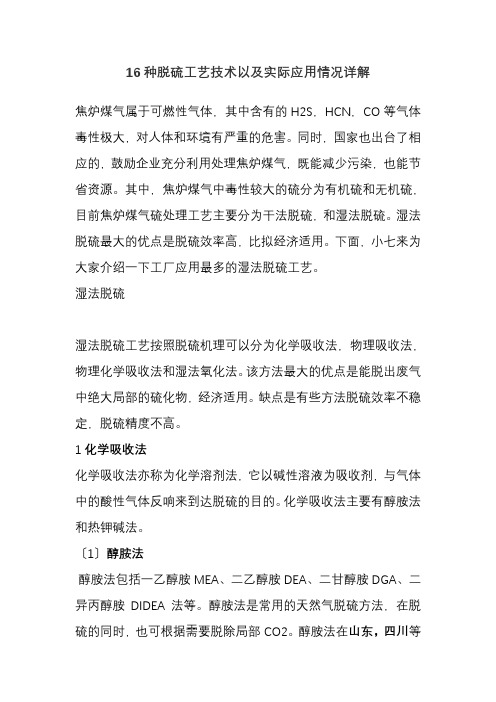
16种脱硫工艺技术以及实际应用情况详解焦炉煤气属于可燃性气体,其中含有的H2S,HCN,CO等气体毒性极大,对人体和环境有严重的危害。
同时,国家也出台了相应的,鼓励企业充分利用处理焦炉煤气,既能减少污染,也能节省资源。
其中,焦炉煤气中毒性较大的硫分为有机硫和无机硫,目前焦炉煤气硫处理工艺主要分为干法脱硫,和湿法脱硫。
湿法脱硫最大的优点是脱硫效率高,比拟经济适用。
下面,小七来为大家介绍一下工厂应用最多的湿法脱硫工艺。
湿法脱硫湿法脱硫工艺按照脱硫机理可以分为化学吸收法,物理吸收法,物理化学吸收法和湿法氧化法。
该方法最大的优点是能脱出废气中绝大局部的硫化物,经济适用。
缺点是有些方法脱硫效率不稳定,脱硫精度不高。
1化学吸收法化学吸收法亦称为化学溶剂法,它以碱性溶液为吸收剂,与气体中的酸性气体反响来到达脱硫的目的。
化学吸收法主要有醇胺法和热钾碱法。
〔1〕醇胺法醇胺法包括一乙醇胺MEA、二乙醇胺DEA、二甘醇胺DGA、二异丙醇胺DIDEA法等。
醇胺法是常用的天然气脱硫方法,在脱硫的同时,也可根据需要脱除局部CO2。
醇胺法在山东,四川等工厂有广泛的应用。
2021年,永坪炼油厂改用醇胺法脱硫,脱硫效果及产品质量均得到提高。
〔2〕热钾碱法催化热钾碱法工艺图热碱钾法采用的是较高浓度的碳酸钾水溶液做吸收剂,可以直接吸收煤气中的硫化氢和氰化氢。
该方法吸收酸气速率慢,效率低,已逐渐被催化热钾碱法取代。
催化热钾碱法就是在碳酸钾溶液里参加一定量的催化剂,加快反响速率。
真空碳酸钾法工艺流程真空碳酸钾法是利用碳酸钾溶液直接吸收酸性气体,脱硫装置在粗苯回收后面,位于焦炉煤气工艺流程末端。
该工艺开始是由德国引进而来的,使用该方法脱硫脱氰后的酸性气体,既可以采用克劳斯法生产元素硫,也可以使用接触法生产硫酸。
之后,中野焦耐公司在吸收国内外真空碳酸钾先进技术及生产实践的根底上,与高等院校合作开发了具有自主产权的新工艺,已在宝钢股份化工公司梅山分公司,陕西焦化,邯郸新区焦化厂等工厂得到应用。
浅析液化石油天然气脱硫技术

浅析液化石油天然气脱硫技术作者:游海兵来源:《科技资讯》 2011年第30期游海兵(陕西延长石油(集团)公司油气勘探公司陕西延安 716000)摘要:近年来,我国的石油天然气等化工行业发展速度加快,液化石油天然气在化工生产应用的过程中必须要先进行脱硫处理,因此液化石油天然气脱硫技术的发展与改进正成为我国化工行业生产的关键。
未处理过的液化石油天然气中存在许多的杂质,这些杂质中除了含有H2S和CO2等酸性成分外,还包含硫醇等有机硫成分,这些硫成分会对石油天然气的提炼产品的加工和生产环境保护工作造成不利的影响。
液化石油天然气的脱硫以及对其所含的硫化物的检验成为液化石油天然气生产过程中的重要环节。
目前,国内外脱硫和硫化物检验方法正在不断的发展,对液化石油天然气进行脱硫的方法日益增多,本文将简单分析目前较常用的几种石油天然气脱硫方法。
关键词:石油天然气脱硫技术硫化物中图分类号:TE62 文献标识码:A 文章编号:1672-3791(2011)10(c)-0064-011 干法脱硫液化石油天然气的干法脱硫技术是目前在生产过程较为常用的脱硫方法之一,其主要的脱硫原理是利用特殊的固体吸附剂与液化气体中所包含的H2S、CO2等硫化物进行吸附并与之发生化学反应,以此完成脱硫。
较为常见的固体吸附剂有铁系、锌系、锰系氧化物较为活泼氧化物。
干法脱硫方法有许多优点,主要表现在液化石油天然气脱化后的气体硫含量较低;但是,干法脱硫还是存在一些缺陷,一般进行干法脱硫所需的设备一般较为庞大,而且所应用的脱硫剂不能再生或再次利用,只能直接废弃,在这就会降低生产环境质量并且增加脱硫技术的成本,因此这种干法脱硫技术目前主要应用于含硫成分较低的气体的精细脱硫生产环节中。
近年来,液化石油天然气干法脱硫技术由于其简单的操作工业和成熟的技术得到了广泛的应用,最为常用的脱硫剂就是氢氧化铁,也就是多种结晶形态的水和氧化铁。
但是,干法脱硫方法所采用的脱硫剂一般是非再生的,因此他的应用受到了一定的限制。
液化气脱硫工艺现状分析

液化气脱硫工艺现状分析液化气脱硫工艺是液化气生产过程中必不可少的环节,它能够有效地去除液化气中的硫化氢、二硫化碳等硫化物,提高液化气的质量,减少对环境的污染,保护人们的健康。
目前,液化气脱硫工艺在国内外已经得到了广泛的应用,各种脱硫工艺也在不断发展和改进。
本文将对当前液化气脱硫工艺的现状进行分析,以期为液化气脱硫工艺的改进和发展提供一些参考。
一、传统的液化气脱硫工艺传统的液化气脱硫工艺主要采用化学吸收法和物理吸附法两种方式。
化学吸收法主要以氧化钠溶液、氧化钙溶液、氨水溶液等作为吸收剂,通过化学反应将液化气中的硫化氢等硫化物吸收下来,从而达到脱硫的目的。
这种方法具有脱硫效率高、操作简单的优点,但同时也存在着吸收剂的损耗大、废液处理麻烦等问题。
物理吸附法主要采用活性炭、分子筛等吸附剂对液化气中的硫化氢等硫化物进行吸附,然后再通过脱附或再生的方式将硫化物从吸附剂上去除。
这种方法具有吸附剂的再生利用率高、操作成本低的优点,但是脱硫效率低、吸附剂的选择和再生等方面也存在一定的难题。
随着科学技术的不断进步,现代液化气脱硫工艺也在不断发展和改进。
现代液化气脱硫工艺主要包括吸收法、氧化法、膜法、催化法等多种方式,每种方式都有其独特的优点和适用范围。
吸收法中的新型吸收剂、吸收设备和脱硫反应器等的研发应用,已经极大地提高了液化气脱硫的效率和稳定性。
氧化法中的新型氧化剂、氧化反应器等的应用,也使得对硫化氢等硫化物的氧化过程更加高效和精确。
膜法和催化法等新型工艺的引入,更是为液化气脱硫工艺的进步带来了新的希望。
三、现状分析目前国内外液化气脱硫工艺的现状是多种多样的,传统工艺和现代工艺并存,各种工艺都在不断地向高效、低成本、环保等方面发展。
但与此也存在一些问题和挑战。
传统工艺中存在吸收剂损耗大、废液处理麻烦等问题,需要进一步提高吸收剂的再生利用率和废液的资源化处理技术。
现代工艺中存在着设备成本高、运行稳定性差等问题,需要加大对新型设备和工艺的研发和应用力度。
液化气脱硫工艺现状分析

液化气脱硫工艺现状分析1. 引言1.1 引言液化气脱硫工艺是一种有效的净化空气质量的手段,其主要作用是去除液化气中的硫化氢等硫化物,保障液化气的清洁和安全。
随着环保意识的增强和大气污染治理的加强,液化气脱硫工艺的研究和应用也越来越受到人们的重视。
在传统的工艺中,液化气脱硫主要通过化学吸收、物理吸附、化学氧化等方法实现硫化氢的去除。
这些方法各有优缺点,需要根据实际情况选择合适的工艺。
近年来,随着技术的不断发展,液化气脱硫工艺也得到了不断改进和完善,新型的脱硫技术不断涌现。
本文将对液化气脱硫工艺现状进行深入分析,包括脱硫工艺的分类、常见脱硫工艺的优缺点分析、液化气脱硫技术研究的最新进展以及影响液化气脱硫效果的因素进行探讨。
通过对这些内容的研究,可以更好地了解液化气脱硫工艺的发展现状,为今后的工程应用提供参考。
2. 正文2.1 液化气脱硫工艺现状分析液化气脱硫工艺是一种广泛应用于工业生产中的脱硫技术。
目前,液化气脱硫工艺在市场上具有较高的发展潜力和应用前景。
在液化气脱硫工艺中,常用的方法包括化学吸收法、物理吸附法、生物脱硫法等。
化学吸收法是一种较为成熟的液化气脱硫工艺,通过将气体通入吸收液中,利用吸收剂中的化学物质与硫化氢发生反应,从而达到脱硫的目的。
物理吸附法则是通过将气体通入具有吸附剂的吸附剂层中,利用吸附剂对硫化氢的吸附作用进行脱硫。
生物脱硫法则是利用微生物对硫化氢进行降解,也是一种节能环保的脱硫技术。
在液化气脱硫工艺中,各种方法都有其优缺点。
化学吸收法虽然效果显著,但存在耗能大、设备成本高等问题。
物理吸附法则对硫化氢的吸附效果较好,但吸附剂的再生成本较高。
生物脱硫法虽然环保,但其技术较为复杂,难以实现规模化应用。
针对不同的生产需求和环境要求,选择合适的液化气脱硫工艺至关重要。
液化气脱硫工艺在目前具有较高的应用前景,但在实际应用中还需要进一步的技术研究和改进,以提高脱硫效率和降低成本。
应该在工艺选择和优化上注重环保和节能,促进液化气脱硫工艺的可持续发展。
液化气液膜脱硫醇组合工艺及其应用

提起液化气,很多人都是有所了解的,而这种了解大多是局限于家庭用液化气,但是从实际应用角度上看,液化气的使用范围要广得多,在本公司液化气可作为气体分馏原料,通过精馏原理可以分出丙烷、丙烯等产品。
而且碳四原料里面的异丁烯可作为生产MTBE的原料。
随着人们对生活质量、生产效率的要求越来越高,如何完善液化气液膜脱硫醇工艺,实现高质量液化气生产成为很多专家学者关注的事情。
液化气液膜脱硫醇组合工艺在行业内是比较受欢迎的,在研究中也发现了其优势所在,这种工艺生产出来的液化气含硫量较低,碱渣及污水排放较小,尾气排放量也在一定的合理范围之内。
1 液化气液膜脱硫醇组合工艺的特点本公司采用宁波中一石化公司工艺技术,采用纤维液膜反应器及碱洗工艺对液化气进行脱硫醇处理,脱除其中的硫醇,使其符合气分装置使用的标准。
脱硫醇的基本原理为:利用氢氧化钠水溶液脱除液化气中的有机硫,将其中的硫醇转化硫醇钠,溶于碱液中。
相关反应如下:RSH + NaOH → NaSR + H2O液化气夹带的微量胺液中所含的H2S可以与碱液发生如下反应:H2S + 2NaOH → Na2S+ 2H2O碱液再生的基本原理为:脱硫醇后碱液中硫醇钠在催化剂作用下与氧反应生成氢氧化钠和二硫化物,二者沉降分离,二硫化物去储罐,再生碱液循环利用。
反应式如下:2NaSR + 1/2 O2 + H2O → 2NaOH + RSSR碱液中可能存在的硫化钠能进行如下氧化反应:2Na2S + 2O2 + H2O → Na2S2O3 + 2NaOHNa2S2O3 + 2O2 + 2NaOH → 2Na2SO4 + H2O(Na2S2O3继续缓慢被氧化)液化气液膜脱硫醇组合工艺在液化气生产中的使用越来越广,这和工艺自身所具有的特点是分不开的。
1.1 脱硫醇对于液化气而言,碱洗脱硫醇的效率是由碱液与液化气的接触面积及碱液的有效浓度决定的,任何一点的改变都会给工作效率带来直接影响[1]。
液化气脱硫醇工艺模拟

液化气脱硫醇工艺模拟液化气脱硫醇工艺模拟一、引言液化气是一种广泛应用于工业和民用领域的燃料,但其中含有硫化氢等有害物质,对环境和人体健康造成潜在危害。
液化气脱硫醇工艺的研究和应用具有重要意义。
本文将介绍一种常用的液化气脱硫醇工艺模拟方法。
二、工艺流程1. 原料准备液化气主要成分为丙烷、丁烷等烷烃混合物,其中含有硫化氢。
为了进行脱硫处理,需要准备适量的脱硫剂(如醇类)。
2. 压缩与冷却将原料液化气进行压缩,使其达到适宜的操作压力,并通过冷却装置降低温度,以便更好地进行后续处理。
3. 脱硫剂注入在压缩冷却后的液化气中注入适量的脱硫剂。
脱硫剂可以选择乙二醇、丙二醇等醇类物质,其具有良好的脱硫效果。
4. 反应器处理将含有脱硫剂的液化气送入反应器进行处理。
反应器中通常设置有催化剂床层,以增加反应速率和效果。
在反应过程中,硫化氢与脱硫剂发生化学反应生成不同的产物。
5. 分离与回收经过反应后的液化气含有产物和未反应的物质。
通过分离装置将产物与未反应物分离开来,并对产物进行回收利用。
6. 净化处理分离后的液化气还可能残留少量杂质,需要进行净化处理。
常见的净化方法包括吸附、膜分离等,以提高液化气的纯度和质量。
7. 储存与输送经过脱硫和净化处理后的液化气可以进行储存和输送。
储存设备一般采用压力容器或罐车等形式,输送方式可选择管道输送或罐车运输等。
三、工艺优势1. 高效性采用催化剂床层和适当的反应条件,可以提高脱硫效率和反应速率,实现高效处理。
2. 环保性脱硫剂醇类物质在反应过程中与硫化氢发生化学反应,生成的产物相对环境友好,减少了对环境的污染。
3. 经济性脱硫剂醇类物质价格相对较低,且可以进行回收利用,降低了生产成本。
四、工艺模拟方法1. 建立反应动力学模型通过实验和数据分析,建立液化气脱硫醇工艺的反应动力学模型。
该模型可以描述反应速率、转化率等关键参数随时间变化的规律。
2. 模拟软件选择选择合适的工艺模拟软件进行液化气脱硫醇工艺的数值模拟。
催化裂化液化气脱硫工艺对比分析
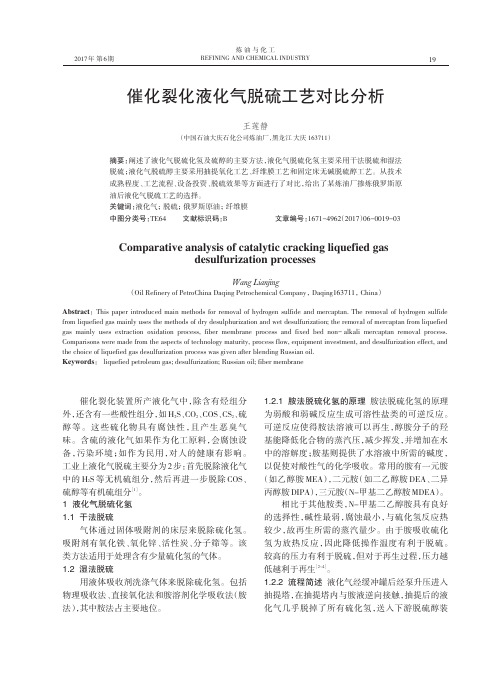
摘要:阐述了液化气脱硫化氢及硫醇的主要方法,液化气脱硫化氢主要采用干法脱硫和湿法脱硫;液化气脱硫醇主要采用抽提氧化工艺、纤维膜工艺和固定床无碱脱硫醇工艺。
从技术成熟程度、工艺流程、设备投资、脱硫效果等方面进行了对比,给出了某炼油厂掺炼俄罗斯原油后液化气脱硫工艺的选择。
关键词:液化气;脱硫;俄罗斯原油;纤维膜中图分类号:TE64文献标识码:B文章编号:1671-4962(2017)06-0019-03催化裂化液化气脱硫工艺对比分析王莲静(中国石油大庆石化公司炼油厂,黑龙江大庆163711)Comparative analysis of catalytic cracking liquefied gas desulfurization processesWang Lianjing(Oil Refinery of PetroChina Daqing Petrochemical Company ,Daqing163711,China )Abstract :This paper introduced main methods for removal of hydrogen sulfide and mercaptan.The removal of hydrogen sulfidefrom liquefied gas mainly uses the methods of dry desulphurization and wet desulfurization;the removal of mercaptan from liquefied gas mainly uses extraction oxidation process,fiber membrane process and fixed bed non-alkali mercaptan removal parisons were made from the aspects of technology maturity,process flow,equipment investment,and desulfurization effect,and the choice of liquefied gas desulfurization process was given after blending Russian oil.Keywords :liquefied petroleum gas;desulfurization;Russian oil;fiber membrane催化裂化装置所产液化气中,除含有烃组分外,还含有一些酸性组分,如H 2S、CO 2、COS、CS 2、硫醇等。
各种脱硫工艺比较
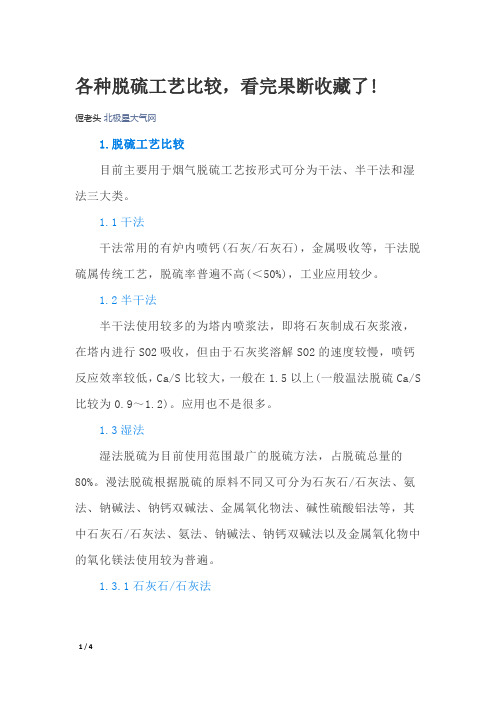
各种脱硫工艺比较,看完果断收藏了!倔老头北极星大气网1.脱硫工艺比较目前主要用于烟气脱硫工艺按形式可分为干法、半干法和湿法三大类。
1.1干法干法常用的有炉内喷钙(石灰/石灰石),金属吸收等,干法脱硫属传统工艺,脱硫率普遍不高(<50%),工业应用较少。
1.2半干法半干法使用较多的为塔内喷浆法,即将石灰制成石灰浆液,在塔内进行SO2吸收,但由于石灰奖溶解SO2的速度较慢,喷钙反应效率较低,Ca/S比较大,一般在1.5以上(一般温法脱硫Ca/S 比较为0.9~1.2)。
应用也不是很多。
1.3湿法湿法脱硫为目前使用范围最广的脱硫方法,占脱硫总量的80%。
漫法脱硫根据脱硫的原料不同又可分为石灰石/石灰法、氨法、钠碱法、钠钙双碱法、金属氧化物法、碱性硫酸铝法等,其中石灰石/石灰法、氨法、钠碱法、钠钙双碱法以及金属氧化物中的氧化镁法使用较为普遍。
1.3.1石灰石/石灰法石灰石法采用将石灰石粉碎成200~300目大小的石灰粉,将其制成石灰浆液,在吸收塔内通过喷淋雾化使其与烟气接触,从而达到脱硫的目的。
该工艺需配备石灰石粉碎系统与石灰石粉化浆系统,由于石灰石活性较低,需通过增大吸收液的喷淋量,提高液气比,来保证足够的脱硫效率,因此运行费用较高。
石灰法是用石灰粉代替石灰石,石灰活性大大高于石灰石,可提高脱硫效率,石灰法主要存在的问题是塔内容易结垢,引起气液接触器(喷头或塔板)的堵塞。
1.3.2钠碱法钠碱法采用碳酸钠或氢氧化钠等碱性物质吸收烟气中的SO2,并可副产高浓度SO2气体或Na2SO3,它具有吸收剂不挥发、溶解度大、活性高、吸收系统不堵塞等优点,适合于烟气SO2浓度比较高的废气SO2吸收处理。
但也存在副产回收困难、投资较高、运行费用高等缺点。
1.3.3氨法氨法采用氨水作为SO2的吸收剂,SO2与NH3反应可产生亚硫酸氨、亚硫酸氢氨与部分因氧化而产生的硫酸氨。
根据吸收液再生方法的不同,氨法可分为氨—酸法、氨—亚硫酸氨法和氨——硫酸氨法。
液化气脱硫醇工艺提高碱液利用率研究

液化气脱硫醇工艺提高碱液利用率研究摘要本公司生产的催化裂化液化气是生产MTBE产品的主要原料,如果液化气脱硫不彻底,MTBE产品的硫含量就会非常高。
液化气脱硫醇目前基本上采用Merox碱洗抽提和碱液空气氧化再生循环利用工艺。
随着高含硫原油加工比例的上升以及液化气产量和综合利用率提高,液化气脱硫醇碱渣排放量大幅增加,对环保压力很大且增加了操作成本。
按照液化气中所含硫化物性质和含硫分布的特点,理论上经过脱硫醇后的液化气中的硫含量能降10μg/g,本论文的研究方向为,在保证液化气脱硫醇效果的前提下,减少碱渣排放量,提高碱液的利用率。
关键词:液化气、脱硫醇、碱液、改造、利用率前言高含硫液化气作为化工原料,将对下游装置的加工过程产生较大影响,因此液化气脱硫显得尤为重要。
当前,国内外的液化气脱硫醇工艺主要有Merox抽提-氧化再生技术[1]、催化氧化脱硫醇技术[2]、吸附法[3]和催化氧化-吸附法[4]等。
Merox抽提-氧化再生技术是目前液化气脱硫醇应用最为广泛的技术。
该技术是在催化剂的作用下,硫醇与碱反应生成硫醇钠,而碱液可以再生,循环使用。
一、装置现状本公司目前有一套催化液化气碱洗脱硫醇单元,脱硫醇装置精制后液化气硫含量较低。
同时,脱硫醇装置排渣碱浓度为15%,每年需消耗4589t新鲜碱液,碱耗量大,碱液利用率低。
初始注碱液浓度20%,排渣碱浓度15%。
总耗碱量为4589t/a。
而目前公司总碱液再生量为5t/h。
再生总碱液量不足脱硫醇总循环碱液量的5%。
经分析,可通过改变工艺流程及采用新技术等措施减少碱渣排放量,提高碱液利用率二、工艺分析1 预碱洗部分在催化裂化液化气脱硫醇精制过程中,预碱洗的目的主要是脱除来自醇胺脱硫后液化气中残留的微量硫化氢,以防止碱氧化再生过程中被氧化成元素硫带入精制后的液化气或者影响脱硫醇过程的催化剂。
目前多采用7%~10%的氢氧化钠溶液进行预碱洗,但产生的废碱液处理起来相当困难,不能进入氧化再生塔C-9007进行再生,需排至莱特进行后续处理。
- 1、下载文档前请自行甄别文档内容的完整性,平台不提供额外的编辑、内容补充、找答案等附加服务。
- 2、"仅部分预览"的文档,不可在线预览部分如存在完整性等问题,可反馈申请退款(可完整预览的文档不适用该条件!)。
- 3、如文档侵犯您的权益,请联系客服反馈,我们会尽快为您处理(人工客服工作时间:9:00-18:30)。
液化气纤维(液)膜脱硫醇及碱液氧化再生不同工艺技术比较
(以40吨/小时催化液化气脱硫醇装置为例)
一. 工艺流程及技术特点比较
1.宁波中一石化LiFT-HR工艺(工艺流程图见附图1)
(1) 纤维式聚结器脱除胺液预处理,降低胺洗后液化气中的硫化氢,从源头控制碱渣排放;
(2) 两级纤维液膜反应器碱洗脱硫醇,硫醇脱除率可达到95-99%,同时可保证无碱液夹带,有利于降低除盐水消耗;
(3) 一级纤维液膜接触器水洗脱碱,除盐水消耗低于传统工艺的1/2,产品钠离子可保证低于0.1ppm;
(4) 脱硫醇碱液采用高效氧化、二硫化物聚结分离及气提工艺精脱二硫化物,可保证再生碱液中硫醇钠浓度低于0.5%wt、二硫化物含量不超过200ppm(提供企标分析方法),系统碱液可长周期使用,催化装置半年以上不用更换碱液、焦化装置1-2个月更换一次碱液,碱渣排放率较其它工艺降低50-80%;
(5) 碱液再生尾气经过脱硫系统处理后,可达到国家《恶臭污染物排放标准GB14554-1993》排放标准,直排烟囱。
(6) 碱液、除盐水循环流量为传统工艺的1/5-1/3,为其它纤维膜同类工艺的1/3-1/2,同时碱液氧化在常温条件下进行,显著降低了碱液氧化再生加热和冷却用的能耗;机泵电耗也大幅降低;
(7) 回收的二硫化物精制后可作为加氢装置催化剂预硫化剂,替代目前广泛使用的二硫化碳,二硫化物也是目前使用较多的化工原料,二硫化物的回收利用为企业增加了一个利润创效点。
2.MERICHEM公司工艺(工艺流程图见附图2)
(1) 两级纤维膜反应器碱洗脱硫醇,脱硫醇效果较传统填料塔有明显提高;
(2) 一级纤维膜接触器水洗脱碱;
(3) 脱硫醇碱液氧化再生采用填料氧化塔、二硫化物分离罐及纤维膜反抽提脱二硫化物工艺:碱液氧化塔在传统填料塔基础上有些改进,但仍无法分离二硫化物,碱液中二硫化物主要通过纤维膜反抽提溶剂油带走及尾气、碱渣排放带走;(根据对齐鲁石化一套焦化装置的了解,采用两级纤维膜反抽提后碱液中二硫化物含量仍较LiFT-HR工艺略高)
(4) 反抽提技术要避免溶剂油夹带碱液,会导致溶剂油加氢催化剂中毒,因此需要增设配套的溶剂油脱碱设施,工艺流程较复杂;(5) 碱液氧化前需要加热至55-70℃,再生后需要冷却至40℃,增加了液化气精制成本。
二. 设备及规格比较
- - 宁波中一石化LiFT-HR工艺MERICHEM公司纤维膜脱硫醇及再生碱液
反抽提工艺
备注
序号设备名称数量
(台)
设备规格
数量
(台)
设备规格 -
1 纤维(液)膜脱硫醇接触器
2 Φ950×4500 2 Φ900×4500 -
2 纤维(液)膜水洗接触器 1 Φ950×4500 1 Φ900×4500 -
3 纤维(液)膜反抽提接触器 - 无 1 Φ600×4500 -
4 碱液氧化塔 1 30
m3 1 20
m3-
5 二硫化物分离塔 1 9
m3- 无塔式有利于二硫化物排放
6 脱硫醇分离罐 2 34
m3 2 70-80
m3LiFT-HR工艺液化气夹带碱
7 水洗分离罐 1 34
m3 1 70 -80 m3液极少,分离罐小得多。
8 反抽提分离罐 - 无 1 40-60
m3-
16 反抽提溶剂沉降罐 - 无 1 10-20
m3-
11 二硫化物分离罐 - 无 1 30
m3-
12 尾气水洗罐/尾气分液罐 1 3
m3 1 3
m3-
13 二硫化物罐 1 7
m3 1 2
m3-
14 液化气过滤器 1
可蒸汽吹扫再生重复使用 2 一次性,半年换一次滤芯 -
15 碱液过滤器 2
可蒸汽吹扫再生重复使用 2 一次性,半年换一次滤芯 -
16 空气过滤器 2 常规过滤器 2 常规过滤器 -
17 碱液预热器 1
碱液流量4.0 m3/h 1 碱液流量6-10 m3/h
18 碱液冷却器 - 无 1
碱液流量6-10 m3/h
19 一级循环碱液泵 2 碱液流量4.0 m3/h 2 碱液流量6-10 m3/h
20 二级循环碱液泵 - 无 2
碱液流量6-10 m3/h 21 催化剂碱液泵 2
碱液流量4.0 m3/h 2 碱液流量6-10 m3/h 22 循环水洗泵 2
除盐水流量9m3/h 2 除盐水流量12-16 m3/h 23 除盐水泵 1
除盐水流量9 m3/h 1 除盐水流量12-16 m3/h LiFT-HR工艺所需要的碱液循环量为MERICHEM工艺的1/3左右,大幅降低了电机
能耗。
24 反抽提溶剂循环泵 - 无 2
溶剂流量15-20 m3/h - 其它可选配设备
1 胺液聚结分离器 1 Φ1200×3350-
2 尾气氧化罐 1 5.4
m3- 3 尾气膜分离罐 1 2.2
m3- 4 碱液预过滤器 1 0.3
m3- 无
LiFT-HR工艺选配,减排环
保辅助设施。
附图1 LiFT-HR工艺流程图
附图2 MERICHEM公司纤维膜脱硫醇及再生碱液反抽提工艺流程图。