液化气脱硫醇培训资料
液化气脱硫醇工艺操作培训共29页文档

液化气脱硫醇工艺操作培训
56、极端的法规,就是极端的不公。 ——西 塞罗 57、法律一旦成为人们的需要,人们 就不再 配享受 自由了 。—— 毕达哥 拉斯 58、法律规定的惩罚不是为了私人的 利益, 而是为 了公共 的利益 ;一部 分靠有 害的强 制,一 部分靠 榜样的 效力。 ——格 老秀斯 59、假如没有法律他们会更快乐的话 ,那么 法律作 为一件 无用之 物自己 就会消 灭。— —洛克
60、人民的幸福是至高无个的法。— 就越加自命不凡。——邓拓 12、越是无能的人,越喜欢挑剔别人的错儿。——爱尔兰 13、知人者智,自知者明。胜人者有力,自胜者强。——老子 14、意志坚强的人能把世界放在手中像泥块一样任意揉捏。——歌德 15、最具挑战性的挑战莫过于提升自我。——迈克尔·F·斯特利
脱硫系统教材培训

• 框架 Q235-A Q235-A包钢包 净烟气侧碳钢包
• 密封材料 DIN 1.4529 DIN1.4529或相当 DIN1.4529或相当
•
或相当 Alloy C276或相当 Alloy C276或相当
•
• • •
• 吸收塔系统 SO 2吸收系统流程: 在吸收塔内加入石灰石 浆液,吸收塔循环泵将反应 槽中浆液至喷淋层,并通 过浆液喷嘴均匀喷淋出,浆 液中的碳酸钙与烟气中SO2 反应,生成亚硫酸钙,脱硫 后的净烟气通过除雾器除去 夹带的雾滴后排出吸收塔 在吸收塔反应槽中喷入 空气,将亚硫酸钙氧化为硫 酸钙,并生成石膏晶体
耐腐蚀能力 在腐蚀
烟囱出现腐蚀
• 布置
复杂
简单
• 可靠性 故障点增加,可靠性差
好
• 维护 机械设备较多,维护工作量大维护 工作量较少
• • •
挡板门
通常采用百叶窗式: • 原烟气挡板门:一般采用电动执行机构 • 净烟气挡板门:一般采用电动执行机构 • 旁路挡板门:电动、气动均可,快开时间一般为15~20s
吸收塔反应器类型
A).喷淋空塔 B).液体分布环型塔 C).带托盘的喷淋塔 D)脉冲悬浮/池分离器型 E)液柱塔 F).喷射鼓泡吸收塔 / 反应器CT121
A).喷淋空塔
液体分布环 (LDR) 作用:将靠近塔壁上的浆液和烟气向塔中 心导向 以改善使气液接触更为均匀
•
液体分布环的好处
• n CFD 模型显示逆流吸收塔内的气体流速 40
脱硫系统培训 ——北京国电龙源环保工程有限公司承德分公司
脱硫系统组成及描述
1.1 - 吸收剂制备系统 - 烟气系统 - SO 2吸收系统 - 石膏脱水系统 - 浆液排空系统 - 工艺水系统 - 压缩空气系统
液化气安全培训教材(PPT 44页)
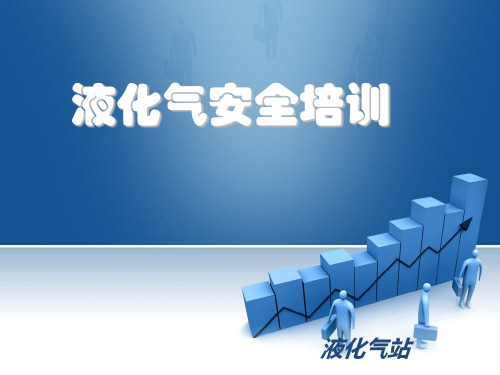
力作用下处于常闭状态,当设备或管道内的介质压 力升高,超过规定值时自动开启,通过向系统外排 放介质来防止管道或设备内介质压力超过规定数值 。安全阀属于自动阀类,主要用于锅炉、压力容器 和管道上,控制压力不超过规定值,对人身安全和 设备运行起重要保护作用。
LPG的出生地
炼油厂
油气田
液化气的特性
1. 颜色与气味:
– 原本无色、无味,基本上不含硫 – 液化气加臭有助于液化气气体泄漏的检测
– 所用的加臭剂, 乙基硫醇, 也是臭鼬所有的!
第二章
液化石油气常用设备简介
压力表 减压阀
气化器
球阀
胶管
调压器:
又称减压器,它是液化石油气安全燃烧 的一个重要部件,连通在钢瓶和炉具之间,调 压器不仅能把瓶内的高压石油气变为低压石 油气,还能把低压气,稳定在适合炉具安全燃 烧的压力范围之内,因此调压器是一种自动 稳压装置.人们习惯地把它称为减压器、减 压阀 。
燃气胶管: 是连接燃气管道和燃气用具的专用耐油胶管,
国家燃气规范明确规定,一般普通燃气胶管的安全 使用期为24个月,过期会老化或漏气。要想家中的 燃气安全,要注意下面6方面:
1.注意使用期限,过期的一定要更换。 2.燃气胶管长度不得超过2米。如果管子太长, 气体压力会降低,火会点不着,还容易脱落
3.胶管中间不能有接头。否则,胶管所承受的压 力不均等,容易造成泄漏。
3、扑救一般场所石油液化气钢瓶火灾的措施: (1)立于地的钢瓶燃烧时,应先检查其角阀
是否完好。如角阀完好,应先关闭阀门,火焰将 自行熄灭;倘火势猛烈,无法先关闭阀门时,可 采用开花水流或干粉、卤代烷、二氧化碳等灭火 剂灭火,然后再关阀断气。在灭火前应先冷却钢 瓶瓶体。
焦化液化气脱硫技术交流材料PPT液化气脱硫醇清洁生产新工艺交流稿

脱硫系统的硫平衡
脱硫醇系统中的硫平衡: 硫醇转化平衡。 总的硫平衡。 二硫化物移除平衡。
脱硫醇
碱氧化再生
应用效果
硫醇脱除率99.2%以上。硫醇一般在10 mg/m3 二硫化物脱除率70%左右,从1000 mg/m3降低到300-400 mg/m3(茂名石化焦化液化气的特例,需要25%的高浓度碱液) 二硫化物反加硫率:没有。 但这一结论目前还不能推广到催化液化气。
应用效果
二硫化物液化回收。回收率70%左右。运行2个月已经分离了20多吨液体二硫化物。其余尾气夹带+产品液化气夹带(由于尾气温度为40℃左右,尾气量小,可以经过水洗再回收其中的80%左右) 传统工艺液化回收率为零,大部分为尾气和碱渣夹带。 如果采用反萃取,回收率一般占到原料总硫的15-20%。但设备投资和加氢处理高硫油的成本增加。
碱循环
原料带入硫
产品带硫
尾气带硫
碱渣带硫
二硫化物液体回收
环保性差的原因分析
碱渣排放的核心原因: 硫(硫醇钠、二硫化物)在碱液中富集。 再生碱液中各类硫形态影响因子从大到小依次为: 二硫化物浓度——与硫化物的回收率有关 硫醇钠浓度——与脱硫醇设备传质效率、氧化塔的效率有关 有效氢氧化钠浓度——与碱液起始浓度、循环过程中的吸水、硫化氢消耗碱有关 硫醚、羰基硫——与原料有关,部分可随二硫化物排出 解决之道:在脱硫醇前杜绝胺液夹带。 在脱硫醇单元保证硫醇脱除率。 在碱液氧化单元保证硫醇钠转化率。 在二硫化物分离单元保证二硫化物分离率。
碱渣量排放大的原因
1) 再生碱液中二硫化物分离度差。 二硫化物在碱液中的微乳化或溶解,静止沉降作用不大,如经过8小时,仍高达7000ppm 如何改进?改变二硫化物的生产方式、采用多级分离。 2) 氧化塔效率低,硫醇钠转化不平衡,逐步累积。 如何改进?气液分布效果、催化剂稳定性、反应温度
液化气脱硫醇工艺操作培训讲课稿
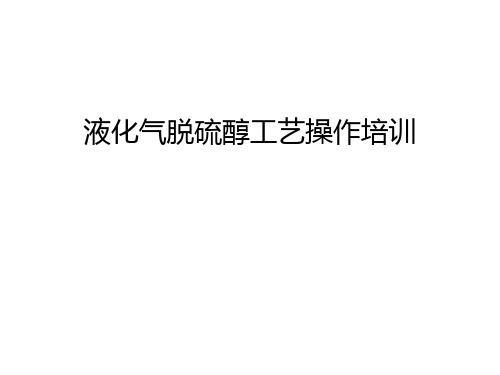
Ⅰ、首先检查工艺流程是否正确,预碱洗文丘里管混合器离预碱洗罐越近越 好,降低压降,并且安装时要低于脱水包位置。
Ⅱ、系统开停工能否正常补碱和退碱。
Ⅲ、助剂能否打入系统。配剂罐有没有自循环线。反抽提油接口位置,能否 保证进脱硫醇系统压力,反抽提油有没有循环线。
Ⅳ、检查氧化塔是否有再生循环线,正常开工前氧化塔需清洗,生产非正常 (再生)时是否能够切出。
安全阀
安全阀的定压是否合适。
开工前试运行 吹扫、试压
河北精致科技有限公司
设备就位管道仪表安装完成后,应按照工艺流程先后,风吹扫清理管路 中的焊渣,并对设备、管路试压,检查漏点等。检查各现场仪表按装情况是 否到位,电力系统,中控控制系统调试完成后,检查调试各压力、液位、流 量的变送信号是否正常。
RSSR +2NaOH (从碱中脱硫醇负离子) ⑵ 油相
首先由强碱(NaOH)与硫醇反应生成硫醇钠,硫醇钠溶于碱液中,从而 从液化气中脱除;抽提有硫醇后的碱液(即富溶剂),在催化剂作用下通入 空气将硫醇氧化为二硫化物脱除再生,再生脱除了硫醇后的碱液(即贫溶剂) 循环使用,可以避免大量碱渣的产生。
液化气脱硫醇工艺流程简图
Ⅱ、防止催化剂富集造成的中毒,稳定了催化活性,确保硫醇钠向二硫化物 的转变活性。
Ⅲ、实现再生催化剂和抽提碱剂的分离,防止抽提时有催化剂存在造成的副 反应发生。
反抽提部分
河北精致科技有限公司
再生工艺采用剂、风、油三相混合接触反应技术,油剂接触时间长,使 再生反应形成的二硫化物能够及时转移到反抽提油中,强化了再生反应推动 力,大大提高了再生和反抽提效果。
除臭精制液
河北精致科技有限公司
Ⅰ、除臭精制液主要由天然植物酸鞣花酸和烷基醇反应制得的水性溶剂。
液化气脱硫醇培训资料
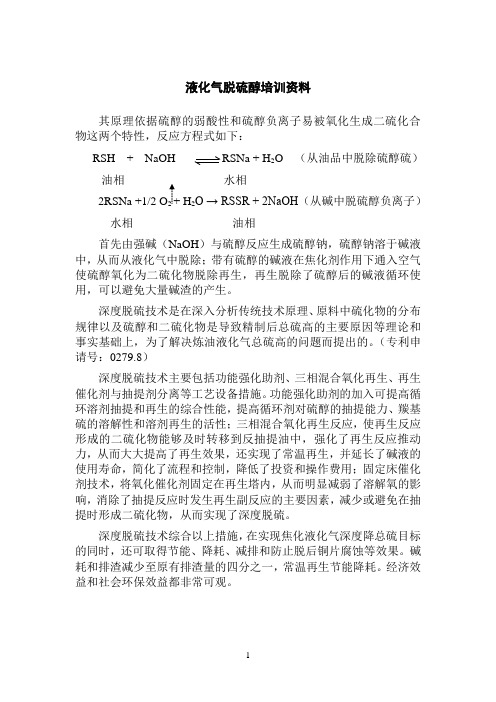
液化气脱硫醇培训资料其原理依据硫醇的弱酸性和硫醇负离子易被氧化生成二硫化合物这两个特性,反应方程式如下:RSH + NaOH RSNa + H2O (从油品中脱除硫醇硫)油相水相2RSNa +1/2 O2 + H2O → RSSR + 2NaOH(从碱中脱硫醇负离子)水相油相首先由强碱(NaOH)与硫醇反应生成硫醇钠,硫醇钠溶于碱液中,从而从液化气中脱除;带有硫醇的碱液在焦化剂作用下通入空气使硫醇氧化为二硫化物脱除再生,再生脱除了硫醇后的碱液循环使用,可以避免大量碱渣的产生。
深度脱硫技术是在深入分析传统技术原理、原料中硫化物的分布规律以及硫醇和二硫化物是导致精制后总硫高的主要原因等理论和事实基础上,为了解决炼油液化气总硫高的问题而提出的。
(专利申请号:0279.8)深度脱硫技术主要包括功能强化助剂、三相混合氧化再生、再生催化剂与抽提剂分离等工艺设备措施。
功能强化助剂的加入可提高循环溶剂抽提和再生的综合性能,提高循环剂对硫醇的抽提能力、羰基硫的溶解性和溶剂再生的活性;三相混合氧化再生反应,使再生反应形成的二硫化物能够及时转移到反抽提油中,强化了再生反应推动力,从而大大提高了再生效果,还实现了常温再生,并延长了碱液的使用寿命,简化了流程和控制,降低了投资和操作费用;固定床催化剂技术,将氧化催化剂固定在再生塔内,从而明显减弱了溶解氧的影响,消除了抽提反应时发生再生副反应的主要因素,减少或避免在抽提时形成二硫化物,从而实现了深度脱硫。
深度脱硫技术综合以上措施,在实现焦化液化气深度降总硫目标的同时,还可取得节能、降耗、减排和防止脱后铜片腐蚀等效果。
碱耗和排渣减少至原有排渣量的四分之一,常温再生节能降耗。
经济效益和社会环保效益都非常可观。
2.2 主要工艺操作条件2.2.1 预碱洗操作参数表2.1 预碱洗部分操作参数2.2.2 硫醇抽提部分操作参数表2.2 硫醇抽提部分操作参数2.2.3 碱液再生部分操作参数表2.3 剂碱再生部分操作参数2.3 工艺流程说明本工艺包括液化气预碱洗、抽提脱硫醇、剂碱再生及反抽提油水洗三部分。
干气液化气脱硫脱硫醇工艺讲解

干气液化气脱硫脱硫醇工艺讲解干气、液化气-脱硫、脱硫醇操作讲义 2.4.1. 脱硫岗位的任务(1) 利用化学吸收原理将干气及液化气中的硫化氢吸收下来,使干气及液化气中硫化氢含量达到质量要求。
(2) 采用预碱洗脱硫化氢及催化剂碱液抽提催化氧化脱硫醇工艺,将液化气中的硫化氢及硫醇脱除。
(3) 负责维护本岗位所属设备、仪表、电气可靠好用,保证安全生产。
(4) 严格遵守巡回检查制度,定时、定点对室内、外仪表进行对照,保证平稳生产。
(5) 优化操作,努力降低能耗及剂耗。
2.4.2. 脱硫岗位操作要点(1) 操作中发生超温、超压以及停水、电、汽、风等不正常现象,岗位要根据具体情况果断及时地进行处理,严防事故扩大。
(2) 严格按照工艺卡片规定控制好各塔压力、温度以及液、界位。
(3) 正常生产运行时,严防设备受憋、超压,串压,做到安全第一。
2.4.3. 净化干气硫化氢含量的控制控制目标:指令值范围内控制范围:?3,(V/V)相关参数:原料温度;原料量;脱硫塔压力;贫液量;溶剂贫液中硫化氢含量;贫液入塔温度控制方式:正常情况下,净化后的干气及液化气硫化氢含量由溶剂量的大小来控制。
正常调整:影响因素调整方法 1.贫液浓度的变化联系硫磺装置提高溶剂浓度 2.溶剂贫液量的变化加大贫液量 3.溶剂再生效果差,溶剂贫液中硫化氢联系降低贫液中的硫化氢含量含量高4.贫液入塔温度的变化联系控制好贫液温度5.原料温度的变化适当降低原料温度6.原料中的硫化氢含量的变化原料中硫化氢含量增加,可以提高溶剂量或联系厂调度提高溶液浓度 7.原料量的变化原料量增加,相应增加溶剂量 8.脱硫塔压力的变化提高脱硫塔压力The innovative city plan a: innovative city of City, comprehensively promote the implementation of national innovation pilot city, according to the Ministry of science and technology, on the sea of province "agreed as a national innovation pilot city of the little letter2.4.4. 干气脱硫塔压力的控制控制范围: 0.85-0.95MPa控制目标:正常操作中干气脱硫塔顶压力应控制在上述范围内,保证干气质量合格相关参数:高压瓦斯管网压力控制方式:干气脱硫塔压力由压控阀控制,通过控制干气出装置流量来控制干气脱硫塔压力正常调整:影响因素调整方法干气量的变化联系稳定岗位控制干气来量平稳高压瓦斯管网压力的变化联系调度瓦斯管网撤压仪表失灵仪表失灵,及时改手动或副线控制,联系仪表工处理异常处理:现象影响因素处理方法及时联系厂调度撤瓦斯管网压力,紧急时可以通瓦斯管网憋压过安全阀付线临时泄压塔压力升高,压力处理量突然大幅平稳处理量上限报警度增加仪表失灵,及时改手动或副线控制,联系仪表工压控阀失灵全关处理若原料干气中断,停止接受原料,及时关闭净化焦化部分故障或干气出装置阀,当稳定系统压力低于本系统时,干气中断,塔压力气压机故障,引起及时关闭稳定干气来的手阀,以保证系统内压力,下降干气中断维持溶剂循环和催化剂碱液循环,随时准备接受原料 2.4.5. 干气脱硫塔液位的控制控制范围: 45%?5%控制目标:正常操作中干气脱硫塔底液位应控制在上述范围内,保证平稳操作相关参数:干气脱硫塔压力,贫液循环量,富液闪蒸控制方式:干气脱硫塔底液位由液控阀控制,通过控制富液流量来控制干气脱硫塔液位正常调整:影响因素调整方法液面指示失灵联系仪表处理,加强现场液位指示的检查富液进料量突然增大,后稳定贫液量,加大富液到闪蒸罐量路不十分畅通干气脱硫塔压力波动稳定压力2etterto the Ministry of science and technology, on the sea of province "agreed as a national innovation pilot city of the little lity plan a: innovative city of City, comprehensively promote theimplementation of national innovation pilot city, according The innovative c异常处理:现象影响因素处理方法前路压力迅速上升,干气胺液回收干气脱硫塔液位器液位迅速上升甚过高,或没过干气通知厂调度并及时将干气切出脱硫装置至干气分液罐液位进口迅速上升2.4.6. 液化气脱硫抽提塔压力的控制控制范围: 1.40-1.50MPa控制目标:正常操作中液化气脱硫塔顶压力应控制在上述范围内,保证液化气硫醇含量合格相关参数:液化气流量,液化气与碱洗沉降罐压力,贫液进塔温度控制方式:干气脱硫塔压力由压控阀控制,通过控制干气出装置流量来控制干气脱硫塔压力正常调整:影响因素调整方法液化气量的变化联系稳定岗位控制液化气来量平稳液化气罐区系统故障憋压联系调度泄压仪表失灵仪表失灵,及时改手动或副线控制,联系仪表工处理液化气温度、溶剂温度的控制好液化气入脱硫温度和溶剂温度变化异常处理:现象影响因素处理方法后部憋压及时联系后部撤压,如果是脱硫醇系统问题紧急时可以通过安全阀付线临时泄压塔压力升高,压力处理量突然大幅平稳处理量上限报警度增加压控阀失灵全关仪表失灵,及时改手动或副线控制,联系仪表工处理3city of the little letter city, according to the Ministry ofscience and technology, on the sea of province "agreed as a national innovation pilotThe innovative city plan a: innovative city of City, comprehensively promote the implementation of national innovation pilot2.4.7. 液化气脱硫塔液位的控制控制范围: 45%?5%控制目标:正常操作中液化气脱硫塔液位应控制在上述范围内,保证平稳操作相关参数:液化气脱硫塔压力,贫液循环量,富液闪蒸罐压力控制方式:液化气脱硫塔液位由液控阀控制,通过控制富液流量来控制液化气脱硫塔液位正常调整:影响因素调整方法液面指示失灵联系仪表处理,加强现场液位指示的检查贫液进料量突然增大,后稳定贫液量,加大富液到闪蒸罐量路不十分畅通液化气脱硫塔压力的变化查找原因稳定液化气脱硫塔压力液化气预碱洗沉降罐界面的控制控制范围:45?5,控制方式:补充碱液和现场底部排碱渣正常调整:影响因素调整方法液化气带水严重,界面上升发现V1312界面上升快,应及时联系稳定岗位解决液化气带水问题碱液循环线堵塞,造成界面下降发现碱液循环线堵塞,一是进行蒸汽吹扫,启用伴热线,二是联系维修处理循环线2.4.8. 净化液化气硫醇含量的控制控制目标:指令值范围内控制范围:?3,(V/V)相关参数:碱液循环量,碱液浓度控制方式:正常情况下,净化后液化气硫醇含量由碱液量的大小来控制。
液化气脱硫醇工艺操作培训
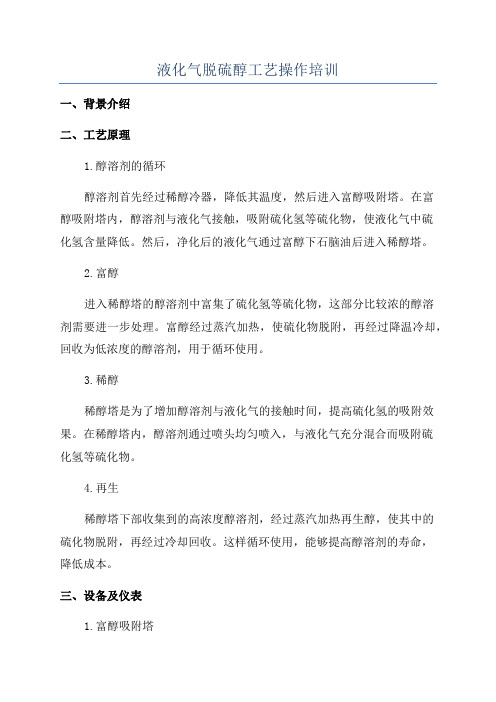
液化气脱硫醇工艺操作培训一、背景介绍二、工艺原理1.醇溶剂的循环醇溶剂首先经过稀醇冷器,降低其温度,然后进入富醇吸附塔。
在富醇吸附塔内,醇溶剂与液化气接触,吸附硫化氢等硫化物,使液化气中硫化氢含量降低。
然后,净化后的液化气通过富醇下石脑油后进入稀醇塔。
2.富醇进入稀醇塔的醇溶剂中富集了硫化氢等硫化物,这部分比较浓的醇溶剂需要进一步处理。
富醇经过蒸汽加热,使硫化物脱附,再经过降温冷却,回收为低浓度的醇溶剂,用于循环使用。
3.稀醇稀醇塔是为了增加醇溶剂与液化气的接触时间,提高硫化氢的吸附效果。
在稀醇塔内,醇溶剂通过喷头均匀喷入,与液化气充分混合而吸附硫化氢等硫化物。
4.再生稀醇塔下部收集到的高浓度醇溶剂,经过蒸汽加热再生醇,使其中的硫化物脱附,再经过冷却回收。
这样循环使用,能够提高醇溶剂的寿命,降低成本。
三、设备及仪表1.富醇吸附塔用于让液化气与醇溶剂接触,吸附硫化氢等硫化物。
塔体内部需要填充合适的填料,提高接触面积,增强吸附效果。
2.稀醇塔用于增加醇溶剂与液化气的接触时间,提高硫化氢的吸附效果。
稀醇塔内部需要装有喷头,使醇溶剂均匀喷入。
3.冷却器、加热器用于对醇溶剂进行冷却和加热的设备,保证循环醇溶剂的温度符合要求。
4.净化塔用于净化后的液化气排放。
净化塔内部需要装有填料,提高液化气与醇溶剂的接触,进一步净化液化气中的硫化氢。
5.仪表包括温度计、压力计、流量计等,用于实时监测和控制工艺中的温度、压力、流量等参数。
四、操作注意事项1.液化气的准备操作人员需要提前检查液化气的质量和含硫化氢等硫化物的浓度,确保液化气符合工艺要求。
2.设备的运行情况操作人员需要定期检查设备的运行情况,包括塔底硫化物浓度、吸附塔压差、冷却器和加热器的温度等。
3.醇溶剂的检测定期对醇溶剂进行检测,包括浓度、温度和流量等参数,确保醇溶剂的质量符合要求。
4.仪表的检修与校准定期对各项仪表进行检修与校准,确保仪表的准确性和可靠性。
脱硫系统专业培训材料

石灰石-石膏湿法脱硫工艺系统及主要 设备
❖ 一、石灰石脱硫工艺系统简介 ❖ 二、烟气系统 ❖ 三、吸收塔系统 ❖ 四、石灰石浆液制备系统 ❖ 五、石膏脱水系统 ❖ 六、 废水处理系统
脱硫系统专业培训材料
一、石灰石脱硫工艺系统简介
❖ 锅炉排出的烟气经引风机送入烟道,再从烟道引出经增压风机升压进入 烟气换热器(GGH),烟气被冷却后进入吸收塔。吸收塔内浆液经浆液 循环泵送到喷淋装置喷淋。烟气在吸收塔内上升与喷淋下来的石灰石浆 液 排相出接后触经G发G生H吸升收温反后应由,净除烟去道烟通气入中烟的囱S排O入2。大洗气涤。后吸的收净塔烟内气吸从收吸S收O2塔后 生成的亚硫酸钙,喷淋到吸收塔底部经过氧化空气的强制氧化生成硫酸 钙,经石膏排出泵从吸收塔排出,由脱水系统处理后,生成的石膏被再 次利用。
❖ 振动给料机为非封闭式,上方配有用于分离大金属的永磁除 铁器。
❖ 筒仓仓顶设有雷达连续测量料位计,料位指示器可防止石灰 石筒仓加料过满和/或完脱硫全系排统专空业培。训材料
石灰石浆液制备系统
❖ 石灰石湿磨制浆时,石灰石从石灰石筒仓经秤重皮 带给料机喂入湿式球磨机进行研磨制浆,球磨机总 的物料(新的石灰石、水力旋流器底流的浆液和水) 在球磨机筒体内被粉碎;浆液通过磨球止回螺旋及 滚动筛拦截下大块的石灰石,浆液通过装在球磨机 出口的浆液卸料筛进入湿磨排浆罐,根据系统浆液 浓度按一定比例加入稀释水后,由调速型湿磨浆液 泵将石灰石浆液输入水力旋流分离器。
脱硫基础知识培训课件
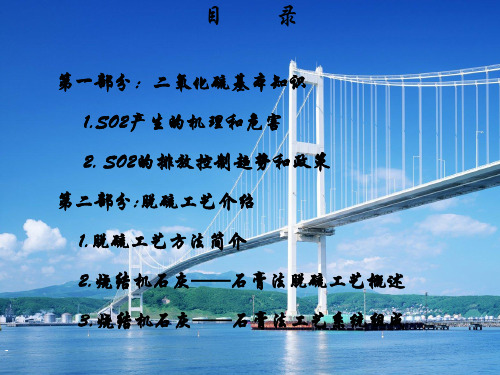
第二部分 脱硫工艺介绍
2. 石灰-石膏湿法脱硫工艺原理 脱硫剂采用石灰粉(150目以上,含钙率≥80%,筛余量≤5%),脱硫浆液吸收烟气中的S02后,经氧化生成石膏,
其反应方程式如下: (1)烟气中SO2及SO3的溶解; 烟气中所含的SO2与吸收剂浆液发生充分的气/液接触,在气—液界面上发生传质过程,烟气中气态的SO2及SO3溶 解转变为相应的酸性化合物: SO2+H2O ←→ H2SO3 SO3+H2O ←→ HSO4 烟气中的一些其他酸性化合物(如:HF、HCl等),在烟气与喷淋下来的浆液接触时也溶于浆液中形成氢氟酸、盐 酸等。 (2)酸的离解 SO2溶解后形成的亚硫酸迅速按下式进行离解: H2SO3 ←→ H++HSO3- (较低PH值) HSO3- ←→ H+ +SO32- (较高PH值) HSO4以及溶解的HF、HCl也进行了相应的离解,由于离解反应中产生了H+,因而造成PH值的下降。离解反应中 产生的H+必须被移除,方可使浆液能重新吸收烟气中的二氧化硫,H+通过与吸收剂发生中和反应被移除。
第二部分脱硫工艺介绍13吸收塔设备图净烟气出口喷淋层烟气进口浆液搅拌器循环泵循环管第二部分脱硫工艺介绍吸收塔外形实物图第二部分脱硫工艺介绍浆液循环泵图片第二部分脱硫工艺介绍循环泵现场照片第二部分脱硫工艺介绍循环泵喷嘴第二部分脱硫工艺介绍氧化风机吸收塔搅拌器氧化风机吸收塔搅拌器氧化风机吸收塔搅拌器第二部分脱硫工艺介绍侧搅拌器现场图片第二部分脱硫工艺介绍吸收塔除雾器第二部分脱硫工艺介绍除雾器现场图片第二部分脱硫工艺介绍除雾器喷嘴第二部分脱硫工艺介绍石灰浆液制备系统脱硫剂采用石灰粉由业主用罐车运至现场粉仓
第一部分 二氧化硫基本知识
二.二氧化硫的排放控制趋势 及政策 1.二氧化硫排放量趋势 1995年,我国SO2排放量达到2370万吨,比1990年增加了870万吨,已超过欧洲 和美国,居世界第一位。从1995年以来,由于国家对S02等主要污染物排放实施总 量控制和经济结构调整,SO2排放总量已有所减少。但随着经济快速发展,特别是 煤炭的消耗持续增长,SO2排放量又有增加趋势,2004年达到2254.9万吨,2005年 达到2549万吨。按现在的能源政策到2020年我国的SO2排放量将达到3500万吨,据 估算,我国大气中SO2浓度达到国家空气二级标准的环境容量是1200万吨,而现在 每年排放的SO2总量都远超过这个值。
最新脱硫培训教材(技术、维护)
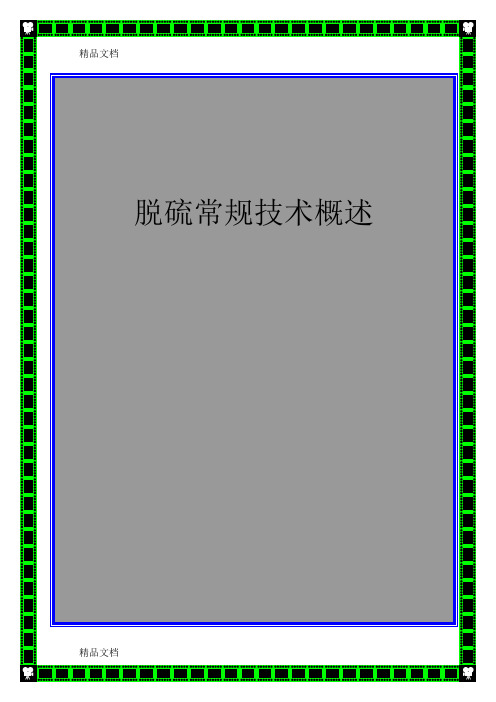
脱硫常规技术概述中国能源资源以煤炭为主。
在电源结构方面,今后相当长的时间内以燃煤发电机组为主的基本格局不会改变,由此造成了严重的环境污染,特别是SO2即酸雨的污染。
火电厂的SO2排放量在全国SO2总排放量中占有相当的比例,1995年全国工业燃煤排放的SO2超过2000万t,排在世界第一位,其中电力行业排放SO2为630万t,到2000年电力行业的SO2年排放量约占到全国SO2总排放量的44%,是SO2污染大户。
近年来,随着国民经济的发展和人民生活水平的提高,我国开始加速对环境污染的治理。
SO2是大气的重要污染物之一,已对农作物、森林、建筑物和人体健康等方面造成了巨大的经济损失,排放的控制十分重要。
因此,采取必要的措施,控制燃煤电厂的SO2排放,对于推行电力洁净生产和改善我国的大气环境质量有着十分重要的意义。
1.脱硫技术通过对国内外脱硫技术以及国内电力行业引进脱硫工艺试点厂情况的分析研究,目前脱硫方法一般可划分为燃烧前脱硫、燃烧中脱硫和燃烧后脱硫等3类。
其中燃烧后脱硫,又称烟气脱硫(Flue gas desulfurization,简称FGD),在FGD技术中,按脱硫剂的种类划分,可分为以下五种方法:以CaCO3(石灰石)为基础的钙法,以MgO 为基础的镁法,以Na2SO3为基础的钠法,以NH3为基础的氨法,以有机碱为基础的有机碱法。
世界上普遍使用的商业化技术是钙法,所占比例在90%以上。
按吸收剂及脱硫产物在脱硫过程中的干湿状态又可将脱硫技术分为湿法、干法和半干(半湿)法。
湿法FGD技术是用含有吸收剂的溶液或浆液在湿状态下脱硫和处理脱硫产物,该法具有脱硫反应速度快、设备简单、脱硫效率高等优点,但普遍存在腐蚀严重、运行维护费用高及易造成二次污染等问题。
干法FGD技术的脱硫吸收和产物处理均在干状态下进行,该法具有无污水废酸排出、设备腐蚀程度较轻,烟气在净化过程中无明显降温、净化后烟温高、利于烟囱排气扩散、二次污染少等优点,但存在脱硫效率低,反应速度较慢、设备庞大等问题。
- 1、下载文档前请自行甄别文档内容的完整性,平台不提供额外的编辑、内容补充、找答案等附加服务。
- 2、"仅部分预览"的文档,不可在线预览部分如存在完整性等问题,可反馈申请退款(可完整预览的文档不适用该条件!)。
- 3、如文档侵犯您的权益,请联系客服反馈,我们会尽快为您处理(人工客服工作时间:9:00-18:30)。
液化气脱硫醇培训资料
1.1.1脱硫醇技术原理
其原理依据硫醇的弱酸性和硫醇负离子易被氧化生成二硫化合物这两个特性,反应方程式如下:
RSH + NaOH RSNa + H2O (从油品中脱除硫醇硫)油相
(从碱中脱硫醇负离子)水相油相
首先由强碱(NaOH)与硫醇反应生成硫醇钠,硫醇钠溶于碱液中,从而从液化气中脱除;带有硫醇的碱液在焦化剂作用下通入空气使硫醇氧化为二硫化物脱除再生,再生脱除了硫醇后的碱液循环使用,可以避免大量碱渣的产生。
1.1.2深度脱硫的原理、措施及效果
深度脱硫技术是在深入分析传统技术原理、原料中硫化物的分布规律以及硫醇和二硫化物是导致精制后总硫高的主要原因等理论和事实基础上,为了解决炼油液化气总硫高的问题而提出的。
(专利申请号:200910250279.8)
深度脱硫技术主要包括功能强化助剂、三相混合氧化再生、再生催化剂与抽提剂分离等工艺设备措施。
功能强化助剂的加入可提高循环溶剂抽提和再生的综合性能,提高循环剂对硫醇的抽提能力、羰基硫的溶解性和溶剂再生的活性;三相混合氧化再生反应,使再生反应形成的二硫化物能够及时转移到反抽提油中,强化了再生反应推动力,从而大大提高了再生效果,还实现了常温再生,并延长了碱液的使用寿命,简化了流程和控制,降低了投资和操作费用;固定床催化剂技术,将氧化催化剂固定在再生塔内,从而明显减弱了溶解氧的影响,消除了抽提反应时发生再生副反应的主要因素,减少或避免在抽提时形成二硫化物,从而实现了深度脱硫。
深度脱硫技术综合以上措施,在实现焦化液化气深度降总硫目标
的同时,还可取得节能、降耗、减排和防止脱后铜片腐蚀等效果。
碱耗和排渣减少至原有排渣量的四分之一,常温再生节能降耗。
经济效益和社会环保效益都非常可观。
2.2 主要工艺操作条件
2.2.1 预碱洗操作参数
表2.1 预碱洗部分操作参数
2.2.2 硫醇抽提部分操作参数
表2.2 硫醇抽提部分操作参数
2.2.3 碱液再生部分操作参数
表2.3 剂碱再生部分操作参数
2.3 工艺流程说明
本工艺包括液化气预碱洗、抽提脱硫醇、剂碱再生及反抽提油水洗三部分。
2.3.1原料要求
认真控制胺脱后液化气硫化氢含量及夹带的富胺液的量,控制液化气稳定进料,是装置稳定操作的基础。
脱硫醇反应与胺脱硫化氢一样,都是化学吸附和解吸过程。
低温有利吸收,加温有利解吸再生。
采用助溶法强化脱硫醇技术后,虽然可以实现常温再生,但再生温度不得低于30℃。
采用稳定汽油作为反抽提油时,为了提高油剂的分离效果,减少反抽提油带碱,尤其是冬季要求合理控制液化气来料温度,使再生温度控制在40℃左右。
或者保留循环剂的加热措施;采用改质柴油作为反抽提油时,再生温度不高于50℃。
2.3.2 焦化液化气预碱洗部分
预碱洗的主要目的,是为了脱除液化气中的硫化氢和夹带的富胺液,防止抽提剂过早失活的同时,避免精制液化气铜片腐蚀不合格现象发生。
硫化氢和碱液之间的反应:
H2S + 2NaOH → Na2S + 2H2O (1)
原料液化气与D-1318底部来的碱液在文丘里管M-1305内混合,再经静态混合器M-1301充分接触反应,进预碱洗罐D-1318沉降分离,液化气中的硫化氢被脱除。
预碱洗后的液化气从罐D-1318顶压出,去脱硫醇。
控制D-1318界位,防止预减洗后液化气带碱。
预碱洗液化气出口管线上设采样口,定期进行硫化氢含量测定,以确定是否更换碱液;预碱洗碱液设采样口,定期分析碱浓度。
2.3.3 脱硫醇部分
抽提脱硫醇的原理是利用硫醇的弱酸性与强碱反应形成硫醇钠,硫醇钠溶于碱液中,使硫醇从液化气中脱除。
反应方程式如下:
RSH + NaOH → RSNa + H2O (2)
在抽提脱硫醇的同时,抽提剂中的COS水解焦化剂促进液化气中COS的水解反应。
COS+H2O OH-→H2S+CO2
H2S + 2NaOH → Na2S + 2H2O
溶剂抽提脱硫醇采用两级逆流抽提,都采用静态混合器组作为反应设备,确保油剂接触传质效果的同时降低设备投资;液化气自二级抽提罐沉降罐D-1319压出,进入水洗罐D-1311水洗后出装置。
预碱洗合格的液化气与泵P-1308A/B来的半贫溶剂经静态混合器M-1302A/B充分混合,完成一级抽提反应后,进罐D-1310沉降分离,富含硫醇钠的抽提溶剂由罐D-1310底部压出,经界位控制去再生部分。
液化气自D-1310顶压出,与P-1306A/B来的再生贫溶剂,进二级反应静态混合器M-1306A/B充分接触,进行二级抽提脱硫醇反应后,进罐D-1319沉降分离。
脱硫醇合格的液化气从D-1319顶部去水洗罐D-1311后出装置。
D-1319底部的半贫溶剂被泵P-1308A/B 抽出,经界位控制送至一级反应混合器M-1302A/B前。
由于一二级抽提过程都采用强混合,所以D-1310和D-1319要有足够的沉降分离时间。
设计剂油混合物停留时间要大于45分钟。
精制后液化气出装置管路上设采样口,采样分析脱硫醇和总硫效果,作为抽提操作调整的依据。
循环剂管路上设采样口,采样分析循环抽提剂碱浓度。
2.3.4 溶剂再生部分工艺
这部分包括两个过程:抽提剂氧化再生过程和溶剂反抽提脱二硫化物过程
含有硫醇钠的抽提溶剂,在氧化焦化剂的存在下,硫醇钠被溶剂中的溶解氧氧化形成二硫化物,抽提剂得以再生。
催化剂RSSR + 2NaOH
2RSNa + 1/2 O2 + H2O −−−−−→
−
二硫化物为油溶性物质,利用此特性,用反抽提溶剂将二硫化物从脱硫醇抽提剂中萃取脱除。
自D-1310来的富溶剂与系统来的非净化风、反抽提油经静态混合器M-1307预混合,进入溶剂再生塔T-1304下部。
经过塔内填料段进行再生反应。
抽提剂溶解的硫醇钠被氧化成二硫化物,并溶解于反
抽提油中。
抽提剂、反抽提油自塔顶压出进三相分离罐D-1312进行分离,尾气经塔顶压控送去焦化烟囱。
再生好的贫溶剂经泵P-1306A/B循环使用;反抽提油越过罐内隔板,自罐底由反抽提油泵P-1307A/B抽出,部分由流量控制去再生塔静态混合器M-1307前循环使用,部分经反抽提油液位控制去塔顶粗汽油罐。
氧化风、反抽提油进装置设流量控制、单向阀;混合器前后设压力表,D-1312设界位指示及高低报警、压力指示和反抽提油液位控制。
溶剂系统管路、玻璃板液位计、容器底部及脱液包需伴热。
根据季节合理控制液化气进料温度,如冬季温度低,循环剂管路上要考虑设加热措施,以保证溶剂不低于30℃。
根据脱硫醇效果,脱硫醇循环剂需定期置换;换剂操作时注意先停反抽提油进入和循环,防止退补剂过快至反抽提油泵抽空或液位超高。
装置内设配剂储剂罐,故障时也可作为系统溶剂的退剂罐。
从再生注风到尾气排放,设备管线均需设置静电接地消除静电措施。
循环溶剂各段,如贫溶剂、半贫溶剂、富溶剂管线上均设采样口,用于碱浓度和硫化物的分析,作为换补溶剂的参考。