步进式加热炉汽化冷却系统设计说明-设计院
步进炉汽冷操作说明

精品线材生产线步进梁加热炉汽化冷却系统操作说明1 加热炉汽化冷却系统1.1 设计依据根据工艺专业所提委托任务书1.2 设计内容本专业的设计内容为加热炉汽化冷却及蒸汽、软水供应。
1.3 加热炉汽化冷却系统1.3.1设计条件蒸汽设计参数:蒸汽设计压力: 1.47MPa蒸汽设计温度:201︒C蒸汽工作参数:蒸汽工作压力: 1.27MPa蒸汽工作温度:194︒C1.3.2系统描述加热炉汽化冷却系统由汽化冷却水循环系统、给水系统、加药系统等组成。
1.3.3加热炉汽化冷却水循环系统由于加热炉为步进式,汽化冷却需采用强制循环系统。
系统组成为由汽包引出2条下降管(DN200),接至循环水泵进口母管(DN300),经循环水泵加压后,由出口母管(DN300)分两路(DN200);一路接至固定梁进水母管(DN200),经固定梁各冷却回路至出水母管(DN250),由一根集中上升管(DN250)送入汽包;另一路接至步进梁旋转接头(固定给水联箱(DN250),经步进梁各冷却回路至旋转接头(固定)回水联箱(DN250),由一根集中上升管(DN250)送入汽包。
返回汽包的汽水混合物经汽水分离后,汽送入蒸汽管网,水重新循环。
炉子支撑梁为9排,4排步进梁和5排固定梁。
每排步进梁分2段,每排固定梁分2段。
步进梁冷却系统的分组以每排步进梁的前段和后段的纵梁及其立柱管组成,由连接管串联成一个冷却回路。
4组冷却回路进出水管相应地连接到给水与回水联箱上,给水与回水联箱各通过3组柔性组件和固定的给水和回水联箱连接。
其中一组柔性组件可做备用,正常运行时两组柔性组件同时流通,当一组柔性组件发生故障时,其余两组柔性组件仍能保证由足够的流通能力进行冷却,不需要停炉。
每套柔性组件由3个球形旋转接头、1个恒力弹簧支架、1个防震导向装置及2个阀门组成,以保证步进活动灵活、平稳。
前后两段步进梁共需6套柔性组件。
每组固定梁的各段也基本由一根纵梁及其立柱管组成,由连接管将固定梁的两段或三段串联成一个冷却回路。
加热炉汽化冷却系统简介

基本参数
数量
1台
出力
15 t/h
工ቤተ መጻሕፍቲ ባይዱ压力
0.02 MPa
除氧水箱
软水经过除氧装置除氧后,进入除氧水 箱,再由给水泵升压经给水调节阀送入汽 包。给水泵共3台,1台运行2台备用,其 中一台备用蒸汽泵是在停电的情况下紧急 启动,向汽包内供水。
基本参数 数量 1个 体积 10M3
循环水泵
汽包下降管接至循环水泵的进水 联箱,供给3台循环水泵。其中2 台循环水泵是电机驱动,另1台是 柴油机驱动。柴油机循环水泵作 为停电、事故备用泵。
流量 扬程 转速 功率
25 m3/h 0.5 MPa 2900 r/min 7.5 kW
除氧器
汽化冷却系统的循环水要在200℃左 右的温度下通过水梁, 因此,除要求 其给水采用软化水外,还要对给水进 行除氧,以减轻水中溶解氧对支撑梁 的腐蚀。 除氧器规格如下:
从汽包出口接出一路蒸汽经减压阀和 调节阀进入除氧器,在除氧器中软水 和蒸汽充分混合,达到除氧器额定压 力下的饱和温度。从水中分离出的空 气由除氧器顶部排入大气,除氧后的 水进入除氧水箱。除氧水箱的水位和 除氧器的压力均采用自动调节控制。
软水箱
基本参数
数量:
1台
软水箱容积: V=20 m3
给水路径
1、正常运行时,通过自动调节阀给 水,阀坏时走旁通;
2、紧急情况下直接将软水或净环水 加入。
软水泵
软水泵的作用是将水箱内的软 水送到除氧器进行除氧
本汽化站设置2台电动软泵,1 台柴油软水泵。其中1台运行 , 2台备用。 柴油泵是在紧急 情况下,将软水不经过除氧直 接加入到汽包内。
业锅炉给水泵,该泵为单吸、多
级、节段式离心水泵。水泵规格 如下:
步进梁式加热炉汽化冷却的应用研究
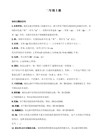
步进梁式加热炉的冷却构件主要是固定梁与活动梁 对固定粱来讲,就我厂目前的技术与实际运行经验,安全可以借鉴推钢式汽化冷却技术来代替水冷却系统。但对步进活动梁来说.由于它要求上升、前进、下降、后退这四个动作为一个活动周期,并周而复始,不断重复运动。这就要求管道的联接必须能承受一定的温度,一定的压力并作长期旋转活动而不渗漏的柔性组件联接。这是步进梁式加热炉汽化冷却技术成功与否的关键所在。其次.步进炉冷却构件的联接管的数量与汽包的高差等因素,较推钢式有极大的不同.其汽化冷却的计算、水量合理分配,特别是安全运行问题亦必须在设计中给予足够的重视。
三、步进式加热炉汽化冷却技术的现实性与可行性
推钢式加热炉采用汽化冷却技术.实践证明可达到省能、省电、省水,能够将回收的热量有效地予以利用.可以延长炉内冷却构件的寿命,减少被加热钢坯上的黑印,减少加热炉生产事故,使加热炉运行更加安全可靠若步进式加热炉的冷却系统也能改为汽化冷却系统,则其现实意义将比推钢式加热炉更加显著。
2、步进加热炉冷却系统.根据其结构形式不同.由原来的工业水冷却系统改造成汽化冷却系统、软水密闭循环系统、工业水冷却系统等三个部分,用于上钢二厂步进梁式加热炉上。实践证明,采用联合冷却装置,保证了不同结构的冷却构件得到合理冷却,设计技术合理,运行安全可靠,可为同类型设计提供有益的借鉴。
3、本项目中的柔性组件的关键设备活动接头,经实践证明运行时转动灵活可靠,密封性能好。在高压、高温(1.6MPa、200℃)下长期使用不渗漏,安全能替代进口专利产品满足步进梁式加热炉汽化冷却装置正常运行的需要,该设备结构简单,造价低廉,开创了我国转动阀门的新品种。具有广阔推广应用价值。
步进式加热炉汽化冷却系统设计说明-设计院

首钢迁钢2#热轧工程步进梁式加热炉汽化冷却系统设计说明1、汽化冷却系统的设计概述1.1汽化冷却系统的冷却效果取决于汽化水的热量吸收。
对于步进梁式加热炉,汽化冷却系统设计为强制循环系统。
系统产生的饱和蒸汽进入车间蒸汽管网,或者在紧急情况下排入大气。
1.2循环系统的主要设备如下:——炉底水梁及立柱——汽包——循环水泵(共3台)——旋转接头组给水供应系统主要设备如下:——电动给水泵——除氧器——除盐水箱——电动除盐水泵——柴油机给水泵——加药装置加热炉炉底水梁,其外表面包扎有耐高温的保温层。
活动梁:4根;固定梁:4根;每根固定梁分为3段;每根活动梁分为3段;另外,在均热段设两根单独固定梁,各自并联进相邻的固定梁;梁的编号为:活动梁(串联结构):2#、4#、5#、7#;固定梁(串联结构):1#、8#;固定梁(串并联结构):3#、6#。
每段梁均由一根双水平管和若干立柱组成,其中一根立柱为双管立柱,是支撑梁冷却水进水和出水的接管;其它为采用带有芯管的单管立柱。
1.3主要运行参数汽包设计工作压力:0.8—1.3MPa(g)工作温度:对应压力下的饱和温度蒸发量:13.0t/h(保温完好,10%排污率时)对应给水量:14.3 m3/h蒸发量:16t/h(10%保温脱落,10%排污率时)对应给水量:17.6 m3/h蒸发量:25t/h(40%保温脱落,10%排污率时)对应给水量:27.5m3/h给水温度:102~104℃系统总循环水量:700—600 m3/h以上参数参见X5212R1以及X5212ZK5。
2、汽化冷却系统的工作原理2.1.循环冷却回路内部冷却回路是指如下的回路:在正常工作时,汽包中的水位保持在汽包中心线以上100mm;由于本工程汽化冷却产汽送入厂区蒸汽管网,因此汽包运行压力根据管网压力确定,目前汽包工作压力确定为1.0—1.1MPa(g)。
冷却水通过汽包下降管、循环水泵、冷却水管总管,分配联箱,进入加热炉支撑水梁。
步进梁式加热炉汽化冷却步进装置立式结构 (1)__tr

步进梁式加热炉汽化冷却步进装置立式结构程 链(中冶赛迪公司动力设计部, 重庆 400013)[摘 要] 介绍了步进梁式加热炉汽化冷却系统中的步进装置采用立式结构的技术方案,论述了立式结构的具体形式、旋转式球形接头的运行轨迹和受力分析,并通过试验对理论研究进行了验证,为在国内冶金行业大型步进梁式加热炉汽化冷却系统步进装置采用立式结构提供了理论上的保证,和实际经验。
[关键词] 汽冷装置 强制循环 水梁及立柱 立式结构1 概述1971年德国波鸿厂300 t/h 板坯步进梁式加热炉(下称步进炉)汽化冷却装置(下称汽冷装置)投运后,各国竞相采用,至1998年国外已有60余座。
从70多座。
1993年1月上钢二厂140 t/h 迪公司)设计,年获冶金部科技进步三等奖,重庆院申报了发明专利[1],1999年41997年9月列为“九五”划项目。
计或建设中的8座。
全部设备国产化的坯步进炉汽冷装置于2000年7见表1。
2 步进炉冷却方式及比较步进炉冷却方式及比较详见表3 汽冷装置循环冷却原理头和循环回路下降管中欠饱和水与上升管中汽水混合物的密度差产生的流动压头克服回路总阻力而形成的。
立柱管由带芯管的套管组成,外管受热,芯管不受热,立柱管是靠芯管内外介质的密度差产生的流动压头克服芯管内外阻力形成自然循环。
循环流动中利用水变为蒸汽吸收大量的热而冷却水梁及立柱。
循环冷却原理图如图1所示。
示:())1(0098.0/=∆+∆+∆=∆=−+=∑s ld x qs sh P P P P H Hp S γγ表1 国内在用和在建的步进炉汽冷装置加热炉 汽冷装置用户名称能力(t/h) 数量座 压力(MPa) 蒸发量(t/h.台)循环方式设计单位 投产时间 上钢二厂 140 1 0.8 3 强制 重庆院 1993年 新沪钢厂 80 1 0.8 4 强制 重庆院 1996年 西安轧钢厂 70 1 0.8 3.5 强制 重庆院 1998年 鞍钢热轧厂 270 2 1.3 12 强制 德国莱林公司 1999年 石钢热轧厂 80 1 0.8 4 强制 法国斯坦因 1999年 本钢4号炉 250 1 1.3 11 强制 重庆院 2000年 宣钢热轧厂 100 1 1.3 4.5 强制 重庆院、首钢院 2001年 武钢二热轧 300 2 1.3 15 强制 日本中外炉 2002年 梅钢2号炉 210 1 1.3 10 强制 重庆院 2001年 梅钢3号炉 210 1 1.3 10 强制 重庆院 建设中 武钢中板厂 110 1 1.27 8.5 强制 重庆院 2002年 上钢一钢 300 3 1.6 20 强制 重庆院 2003年 本钢5号炉 250 1 1.3 11 强制 中冶赛迪 2004年 太钢热轧厂 300 3 1.4 15 强制 中冶赛迪 2006年 八钢热轧厂 250 1 1.3 11 强制 中冶赛迪 2006年 宝钢三热轧 250 4 1.6 11 强制 中冶赛迪 2007年 安阳炉卷加热炉 250 1 1.0 11 强制 中冶赛迪 2005年 安阳1780 250 1 1.0 11 强制 中冶赛迪 2006年 武钢1580热轧厂 300 1 1.3 10.7 强制 中冶赛迪 建设中 本钢3号加热炉 250 1 1.3 11 强制 中冶赛迪 设计中 本钢三热轧 300 4 1.3 9.2 强制 中冶赛迪 设计中 太钢4号加热炉 260 1 1.6 17.9 强制 中冶赛迪 设计中 承德热轧厂加热炉 290 2 1.3 12.8 强制 中冶赛迪 设计中 泰钢加热炉 180 1 1.3 11.5 强制 中冶赛迪 设计中 八钢2号炉 250 1 1.3 11 强制 中冶赛迪 设计中 宝钢条钢厂 240 1 1.9 7.2 强制 中冶赛迪 设计中 安钢3号炉 250 1 1.0 11 强制 中冶赛迪 设计中∆4 汽冷装置系统组成、主要设备及功能汽冷装置由循环水、软水制备、给水及除氧、排污和取样系统组成。
加热炉汽化冷却系统简介
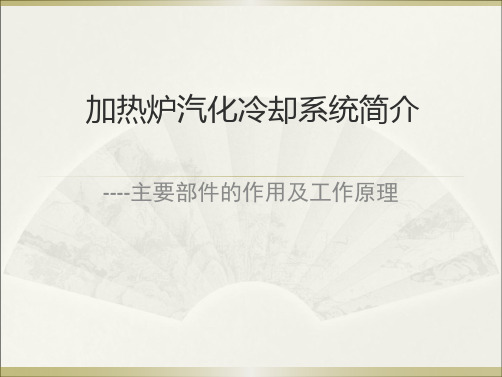
柴油机循环水泵
当全厂事故停电时,炉内 钢坯与炉墙的蓄热量很大, 支撑梁和立柱仍需要冷却, 因此,加热炉的汽化冷却 系统设有柴油机带动的循 环水泵,可以在停电的10 秒钟内自动启动,保证水 循环正常运行从而使炉子 的支撑梁及其立柱不被烧 坏。
给水泵
给水系统设置2台电动给水泵, 1台蒸汽泵。正常生产时, 1台 运行, 2台备用。水泵采用中低 压锅炉上广泛采用的DG型工业
软水箱
基本参数
数量:
1台
软水箱容积: V=20 m3
给水路径
1、正常运行时,通过自动调节阀给 水,阀坏时走旁通;
2、紧急情况下直接将软水或净环水 加入。
软水泵
软水泵的作用是将水箱内的软 水送到除氧器进行除氧
本汽化站设置2台电动软泵,1 台柴油软水泵。其中1台运行, 2台备用。 柴油泵是在紧急情 况下,将软水不经过除氧直接 加入到汽包内。
基本参数
数量
1台
出力
15 t/h
工作压力
0.02 MPa
除氧水箱
软水经过除氧装置除氧后,进入除氧水 箱,再由给水泵升压经给水调节阀送入汽 包。给水泵共3台,1台运行2台备用,其 中一台备用蒸汽泵是在停电的情况下紧急 启动,向汽包内供水。
基本参数 数量 1个 体积 10M3
循环水泵
汽包下降管接至循环水泵的进水 联箱,供给3台循环水泵。其中2 台循环水泵是电机驱动,另1台是 柴油机驱动。柴油机循环水泵作 为停电、事故备用泵。
加热炉汽化冷却系统简介
----主要部件的作用及工作原理
汽化冷却系统原理图
汽化冷却系统冷却回路原理简介
内部冷却回路是指如下的回路: 在正常工作时,汽包中的水位保持在汽包中心线以上250mm,汽包工作压
步进梁式加热炉汽化冷却系统设计研究

【 e od】w l n- em fr c; vprtn con; nr ai K y w rs a i b a n e eao i ol g ee sv g kg ua ao i y g n 1 引言 ‘
水梁 1 J 4 0 k 的热量 , 而汽化冷却方式是利用汽化潜 热来带走水梁热量 , 以国内汽化冷却主流设计压力 0 P 为 例 ,这种 压 力 条 件下 的汽化潜 热 为 .Ma 8 2 00 k/g饱 和水 焓 为 7 2k/g这样 采用 汽 化 3 J , k 4 J , k 冷却 l 水能带走 27 2k 热量 , 7 J 也就是说, 一般 条件下汽化冷却方式 的用水量是水冷方式用水量的
【 要】 摘 从节 能和安全生产两方面出发 , 阐述了步进粱式加热炉采用汽化冷却的优势。介绍 了我 国两种
炉型采用加热炉汽化冷却的发展过程 。说 明了保 障整个系统安全稳定运行的关键设计工艺和技术。
【 关键词 】 步进梁式加热炉 ; 化冷却 ; 汽 节能
【 中图分类号】T 0 1 Q 5. 5
删 E gn eig& T cn l yC roai ,MC ,Manhn n u 4 05 hn) ∽ nier n eh oo o rtn g p o C a sa,A ai n a t oeao, t dat e o vprtn A s at ae nee y s n ads e pr i r g vg fy t n h avn gs f ao i e a e ao
其次 是 节 能 。因为 5 c 0 c左右 的热水 是不 能二
次利用的低档热源 , 而饱和蒸汽能够满足生产和生 活用汽的要求 , 随着各大钢铁企业综合管线改造的 完成和我 国低参数蒸汽利用技术的逐步完善 , 汽化 冷却相对水 冷的优势将会更加显现 . 也将改变我国 南 方多水 地 区钢铁 厂还 在采 用水冷方 式 的局 面 。 另外还能保证安全 、 高效 、 高质量生产。最主要 点是防止结垢 , 因为水冷方式是通过温差传热, 温
过程控制系统课程设计--步进式加热炉控制系统设计

步进式加热炉控制系统设计一、步进式加热炉工艺流程⒈步进式加热炉简介⑴步进式加热炉步进式加热炉是一种靠炉底或水冷金属梁的上升、前进、下降、后退的动作把料坯一步一步地移送前进的连续加热炉。
炉子有固定炉底和步进炉底,或者有固定梁和步进梁。
前者叫做步进底式炉,后者叫做步进梁式炉。
轧钢用加热炉的步进梁通常由水冷管组成。
步进梁式炉可对料坯实现上下双面加热。
(2)步进式炉的几种类型步进式炉从炉子构造上分目前有:单面供热步进式炉、两面供热步进式炉、钢料可以翻转的步进式炉、交替步进式炉、炉底分段的步进式炉等等。
单面供热步进式炉也称步进底式炉,钢料放置在耐火材料炉底或铺设在炉底上的钢枕上。
钢坯吸热主要来自上部炉膛,由于一面受热,这种炉子的炉底强度较低。
它适用于加热薄板坯、小断面方坯或有特殊要求的场合。
两面供热步进式炉也称步进梁式炉,活动梁和固定梁上都安设有能将钢坏架空的炉底水管。
在钢坯的上部炉膛和下部炉膛都设置烧嘴,因此炉底强度较高,适用于产量很高的板坯或带钢轧前加热。
钢坯可以翻转的步进式炉是每走一步炉内钢料可以翻转某一角度,步进梁和固定梁都带有锯齿形耐热钢钢枕,这是加热钢管的步进式炉,每走一步钢管可以在锯齿形钢枕上滚动一小段距离,使受热条件较差的底面逐步翻转到上面,以求加热均匀。
交替步进式炉则有两套步进机构交替动作。
运送过程中,钢坯不必上升和下降,振动较小,底面不会被划伤,表面质量较好。
炉底分段的步进式炉的加热段和预热段可以分开动作。
例如预热段每走一步,加热段可以走两步或两步以上。
这种构造是专门为易脱碳钢的加热而设计的。
钢坯在预热段放置较密,可以得到正常的预热作用,在加热段钢坯前进较快,达到快速加热,以减少脱碳。
(3)步进式炉的优缺点步进式炉是借机械将炉内钢坯托着一步一步前进,因此钢坯与钢坯还不必紧挨着,其间距可根据需要加以改变。
原始的步进式炉只用于加热推钢机无法推进的落板坯或异形坯,随着轧机的大型化和连续化,推钢式炉已不能满足轧机产量和质量的要求。
加热炉汽化冷却控制系统优化设计
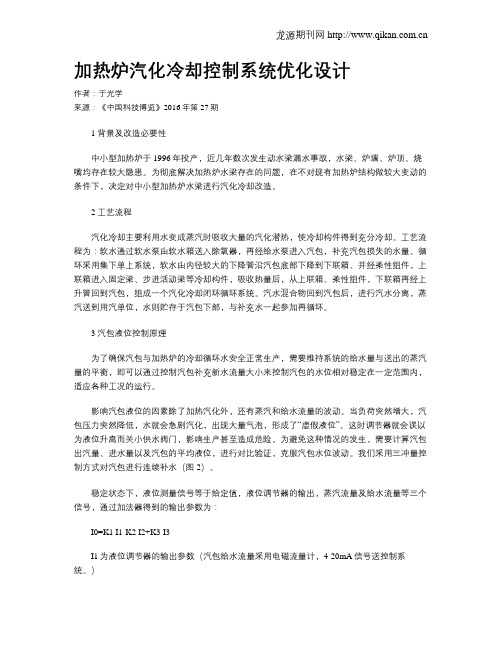
加热炉汽化冷却控制系统优化设计作者:于光学来源:《中国科技博览》2016年第27期1 背景及改造必要性中小型加热炉于1996年投产,近几年数次发生动水梁漏水事故,水梁、炉墙、炉顶、烧嘴均存在较大隐患。
为彻底解决加热炉水梁存在的问题,在不对现有加热炉结构做较大变动的条件下,决定对中小型加热炉水梁进行汽化冷却改造。
2 工艺流程汽化冷却主要利用水变成蒸汽时吸收大量的汽化潜热,使冷却构件得到充分冷却。
工艺流程为:软水通过软水泵由软水箱送入除氧器,再经给水泵进入汽包,补充汽包损失的水量。
循环采用集下单上系统,软水由内径较大的下降管沿汽包底部下降到下联箱、并经柔性组件,上联箱进入固定梁、步进活动梁等冷却构件,吸收热量后,从上联箱、柔性组件,下联箱再经上升管回到汽包,组成一个汽化冷却闭环循环系统。
汽水混合物回到汽包后,进行汽水分离,蒸汽送到用汽单位,水则贮存于汽包下部,与补充水一起参加再循环。
3 汽包液位控制原理为了确保汽包与加热炉的冷却循环水安全正常生产,需要维持系统的给水量与送出的蒸汽量的平衡,即可以通过控制汽包补充新水流量大小来控制汽包的水位相对稳定在一定范围内,适应各种工况的运行。
影响汽包液位的因素除了加热汽化外,还有蒸汽和给水流量的波动。
当负荷突然增大,汽包压力突然降低,水就会急剧汽化,出现大量气泡,形成了“虚假液位”。
这时调节器就会误以为液位升高而关小供水阀门,影响生产甚至造成危险。
为避免这种情况的发生,需要计算汽包出汽量、进水量以及汽包的平均液位,进行对比验证,克服汽包水位波动。
我们采用三冲量控制方式对汽包进行连续补水(图2)。
稳定状态下,液位测量信号等于给定值,液位调节器的输出,蒸汽流量及给水流量等三个信号,通过加法器得到的输出参数为:I0=K1 I1-K2 I2+K3 I3I1为液位调节器的输出参数(汽包给水流量采用电磁流量计,4-20mA信号送控制系统。
)I2为蒸汽流量变送器的参数(汽包送出蒸汽流量采用孔板测量,流量信号送控制系统。
步进梁式加热炉汽化冷却系统的设计及应用
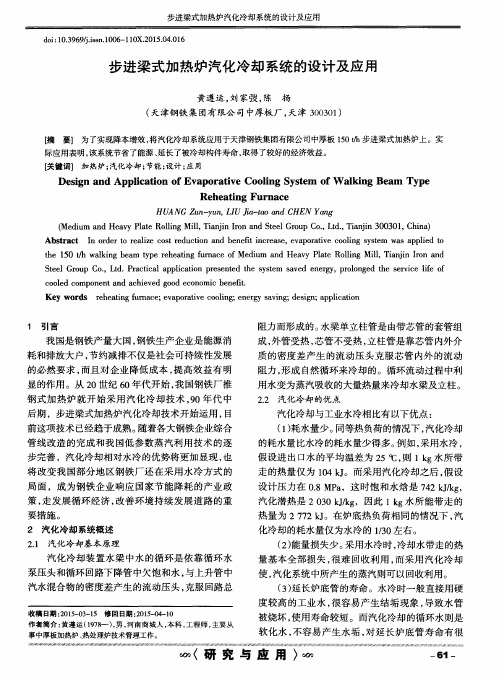
汽化冷却与工业水冷相 比有以下优点 :
( 1 ) 耗水 量少 。 同等 热负 荷 的情 况 下 , 汽 化冷 却 的耗 水量 比水 冷 的耗水 量少 得多 。 例如 , 采用 水冷 ,
假设 进 出 口水 的平均 温 差 为 2 5℃ , 则 1 k g 水 所 带
走的热量仅为 1 0 4 k J 。而采用汽化冷却之后 , 假设
设 计压 力 在 0 . 8 MP a ,这 时饱 和 水焓 是 7 4 2 k J , k g , 汽 化潜 热 是 2 0 3 0 k J / k g ,因此 1 k g水 所 能带 走 的 热量为 2 7 7 2 k J 。在 炉底 热 负 荷相 同 的情 况下 , 汽
1 引言
阻力而 形成 的。 水 梁单 立柱 管是 由带 芯管 的套 管组
我 国是 钢铁 产量 大 国 , 钢 铁 生产 企业 是 能源 消
成, 外管受热 , 芯管不受热 , 立柱管是靠芯管 内外介 质的密度差产生 的流动压头克服芯管 内外的流动
阻力 , 形成 自然循 环来 冷却 的 。循 环 流动 过程 中利
S t e e l Gr o u p Co . ,L t d .Pr a c t i c a l a p p l i c a t i o n p r e s e n t e d t h e s y s t e m s a v e d e n e r g y ,p r o l o ng e d t h e s e r v i c e l i f e o f c o o l e d c o mp o n e n t a n d a c h i e v e d g o o d e c o n o mi c b e ne i f t . Ke y wo r ds r e h e  ̄i n g f u r n a c e ; e v a p o r a t i v e c o o l i ng ;e n e r g y s a v i ng ;d e s i g n ;a p p l i c a t i o n
步进式加热炉控制系统设计
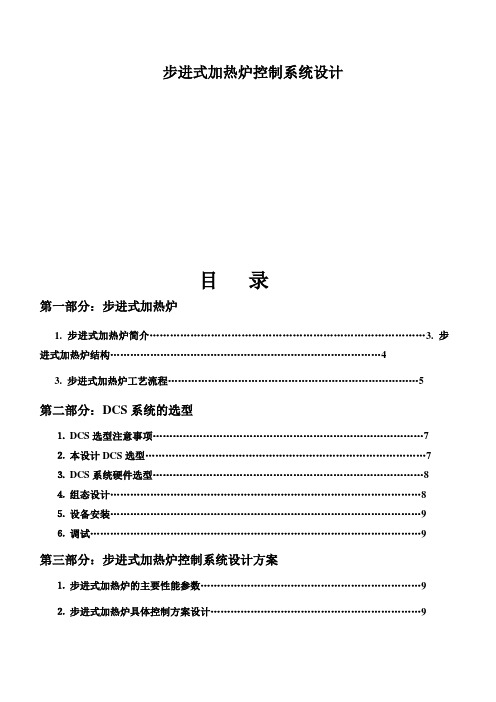
步进式加热炉控制系统设计目录第一部分:步进式加热炉1. 步进式加热炉简介.................................................................................3. 步进式加热炉结构 (4)3. 步进式加热炉工艺流程 (5)第二部分:DCS系统的选型⒈DCS选型注意事项 (7)⒉本设计DCS选型 (7)⒊DCS系统硬件选型 (8)⒋组态设计 (8)⒌设备安装 (9)⒍调试 (9)第三部分:步进式加热炉控制系统设计方案⒈步进式加热炉的主要性能参数 (9)⒉步进式加热炉具体控制方案设计 (9)第四部分:DCS组态图⒈JX-300组态 (13)⒉加热炉控制系统演示工程 (14)⒊温度报警显示 (15)⒋温度和炉膛压力监控 (16)第五部分:心得体会第六部分:参考资料一、步进式加热炉工艺流程⒈步进式加热炉简介⑴步进式加热炉步进式加热炉是一种靠炉底或水冷金属梁的上升、前进、下降、后退的动作把料坯一步一步地移送前进的连续加热炉。
炉子有固定炉底和步进炉底,或者有固定梁和步进梁。
前者叫做步进底式炉,后者叫做步进梁式炉。
轧钢用加热炉的步进梁通常由水冷管组成。
步进梁式炉可对料坯实现上下双面加热。
⑵步进式加热炉特点⒉步进式加热炉的结构⑴步进式加热炉结构图图(1)⒊步进式加热炉工艺流程一般情况下,加热炉沿炉膛长度方向分为预热段、加热段和均热段。
进料端为预热段,炉气温度较低,其作用在于充分利用炉气热量,给进炉板坯预热到一定温度,以提高炉子的热效率。
加热段为主要供热段,炉气温度较高,以利于实现板坯的快速加热,保证板坯加热到要求的目标温度。
均热段位于出料端,炉气温度与金属料温度差别很小,保证出炉料坯的断面温度均匀。
一般用于加热小断面料坯的炉子只有预热段和加热段。
钢坯加热是热轧生产工艺过程中的重要工序。
其生产过程如下:对于步进式加热炉,钢坯的移动是通过固定梁和移动梁的周期运动来实现的。
步进梁式加热炉汽化冷却装置的设计探讨

步进梁式加热炉汽化冷却装置的设计探讨摘要:重点介绍了南钢新中棒180t/h步进梁式加热炉汽化冷却装置的组成、基本原理、结构及使用效果。
对同类加热炉的设计具有一定的指导作用。
关键词:步进梁式;加热炉;汽化冷却;中图分类号:tg155.1+21引言步进梁式加热炉具有加热速度快、加热均匀、烧损少,可调节装钢量、减少和防止钢坯脱碳、可防止拱钢和粘钢,易出空炉料、可缩短凉炉检修和开炉升温周期、易于采用计算机对钢坯跟踪等优点。
轧钢加热炉冷却构件的冷却有工业水冷却和汽化冷却两种方式。
工业水冷却存在以下问题:水中含钙镁离子、溶解氧和杂物、影响轧机生产;为防结垢,水温控制在小于等于55度,致使循环水量大,能耗高;有室外冷却水系统,占地大;水温低致使钢坯黑印加重。
余热不回收,不能直接回收投资。
步进梁式加热炉的水梁和立柱采用汽化冷却的优点:1.在水梁和立柱中循环流动的水是软水,能延长水梁和立柱的使用寿命,减少停炉维修时间,增加了轧制产量。
2.由于在水梁和立柱中的循环水温度比较高,能减轻钢坯的黑印,提高了待轧坯料的加热质量。
3.汽化冷却装置能产蒸汽,回收热能,降低能耗,节能效益显著。
4.较之水冷却,布置紧凑,补充水量少,有效回收热能。
5.汽化冷却装置的一次性投资虽然比较大,但能回收蒸汽,节约用水,投资回收约需2年~2年6个月。
目前国内大部分轧钢加热炉已采取汽化冷却技术。
2.南钢步进梁加热炉汽化冷却装置2.1、加热炉主要参数以南京钢铁厂新中棒180t/h步进梁式加热炉工程为例,本工程设步进梁式加热炉一座,加热炉额定生产能力为180t/h(冷坯),有效炉长为42.96m、炉宽13.1m、炉底有效面积600m2;加热钢种为优质碳结钢、合金结构钢、冷镦钢、齿轮钢、弹簧钢、轴承钢、易切钢和锚链钢等。
加热炉设两套液压步进机构、两套提升和平移框架;按其功能分:均热段炉温:1200~1220℃,加热段炉温:1240~1260℃;预热段炉温:1000~1150℃。
汽化冷却系统在步进梁式加热炉上的节能改造

汽化冷却系统在步进梁式加热炉上的节能改造轧钢学术交流会论文专辑2009年中南·泛珠三角地区第五届1前言汽化冷却是国内加热炉上普遍采用的一种冷却工艺技术,它不仅可以提高炉内水冷件的使用寿命,而且产生的蒸汽也可以回收利用,是轧钢工序能耗中的一项“负能耗”指标。
安阳钢铁集团责任有限公司1780热连轧生产线上的3座步进梁式加热炉内的水梁和立柱全部采用汽化冷却。
我们对该系统在生产使用过程中暴露出的一些问题,采取了相关的措施,优化了这套冷却系统,达到了节能减排的目的。
2汽化冷却系统的构成及工艺流程汽化冷却系统由汽水循环回路系统、给水除氧系统、蒸汽系统、排汽系统、排污系统、加药系统、取样冷却系统组成,其中给水除氧系统为3座加热炉共用。
冷却介质是公司动力厂供应的软水。
冷却工艺流程为:软水→软水箱→软水泵→除氧器→给水泵→汽包→下降管→热力循环泵→分配联箱→(固定梁)→进口步进装置→活动梁→出口步进装置→上升管→汽包→蒸汽分离送入厂区管网。
3汽化冷却系统在运行中存在的一些问题3.1蒸汽流量负荷变化时,汽包水位三冲量控制不易实现汽包是汽化冷却系统中的核心设备,主要作用是对进入其内部的汽水混合物进行汽水分离,产生大量的蒸汽,维持炉内水梁、立柱的软水使用量。
可见汽包的水位控制是关键问题。
为了有效防止汽包虚假水位的产生,我们采用了以汽包产生的蒸汽流量为前馈信号,以汽包水位为主参数、给水流量为副参数的前馈加串级反馈的三冲量自动控制。
在汽包的放散管路上原先设计有一个蒸汽压力调节阀T,如图1所示,该阀的开闭只和汽包设定的压力值有关,汽化冷却系统在步进梁式加热炉上的节能改造李敬(安阳钢铁股份有限公司)摘要介绍了安钢1780热连轧步进梁式加热炉汽化冷却系统的进一步优化情况和在生产中的节能降耗措施。
关键词步进梁式加热炉汽化冷却装置节能降耗Energy-saving Reformation of Vaporization Cooling System inWalking-beam Reheating FurnaceLI Jing(Anyang Iron and Steel Stock Company Limited)Abstract The further optimized situation of vaporization cooling system in walking-beam reheating furnace of1780hot continuous rolled mill and its energy-saving and consumption-reducing measures in production were introduced.Key Words Walking-beam Reheating Furnace Vaporization Cooling Device Energy-saving and consumption-reducing 柳钢科技217柳钢科技轧钢学术交流会论文专辑2009年中南·泛珠三角地区第五届在打开后容易造成虚假水位的产生,并且放散量也无法得知。
- 1、下载文档前请自行甄别文档内容的完整性,平台不提供额外的编辑、内容补充、找答案等附加服务。
- 2、"仅部分预览"的文档,不可在线预览部分如存在完整性等问题,可反馈申请退款(可完整预览的文档不适用该条件!)。
- 3、如文档侵犯您的权益,请联系客服反馈,我们会尽快为您处理(人工客服工作时间:9:00-18:30)。
首钢迁钢2#热轧工程步进梁式加热炉汽化冷却系统设计说明1、汽化冷却系统的设计概述1.1汽化冷却系统的冷却效果取决于汽化水的热量吸收。
对于步进梁式加热炉,汽化冷却系统设计为强制循环系统。
系统产生的饱和蒸汽进入车间蒸汽管网,或者在紧急情况下排入大气。
1.2循环系统的主要设备如下:——炉底水梁及立柱——汽包——循环水泵(共3台)——旋转接头组给水供应系统主要设备如下:——电动给水泵——除氧器1——除盐水箱——电动除盐水泵——柴油机给水泵——加药装置加热炉炉底水梁,其外表面包扎有耐高温的保温层。
活动梁:4根;固定梁:4根;每根固定梁分为3段;每根活动梁分为3段;另外,在均热段设两根单独固定梁,各自并联进相邻的固定梁;梁的编号为:活动梁(串联结构):2#、4#、5#、7#;固定梁(串联结构):1#、8#;固定梁(串并联结构):3#、6#。
2每段梁均由一根双水平管和若干立柱组成,其中一根立柱为双管立柱,是支撑梁冷却水进水和出水的接管;其它为采用带有芯管的单管立柱。
1.3主要运行参数汽包设计工作压力:0.8—1.3MPa(g)工作温度:对应压力下的饱和温度蒸发量: 13.0t/h(保温完好,10%排污率时)对应给水量: 14.3 m3/h蒸发量: 16t/h(10%保温脱落,10%排污率时)对应给水量: 17.6 m3/h蒸发量: 25t/h(40%保温脱落,10%排污率时)对应给水量: 27.5m3/h给水温度: 102~104℃系统总循环水量: 700—600 m3/h3以上参数参见X5212R1以及X5212ZK5。
2、汽化冷却系统的工作原理2.1.循环冷却回路内部冷却回路是指如下的回路:在正常工作时,汽包中的水位保持在汽包中心线以上100mm;由于本工程汽化冷却产汽送入厂区蒸汽管网,因此汽包运行压力根据管网压力确定,目前汽包工作压力确定为1.0—1.1MPa(g)。
冷却水通过汽包下降管、循环水泵、冷却水管总管,分配联箱,进入加热炉支撑水梁。
冷却水从分配联箱接出的进水支管,经过流量调节后,流经各冷却部件。
各段炉底梁构成8个冷却回路,在进水联箱和回水联箱之间这些4回路为并联工作方式。
在炉底水梁中,冷却水吸收热量,并将热量通过循环水经上升管送至汽包。
2.1.1汽包系统产生的汽水混合物在汽包中被分离成蒸汽和水,水流回内部冷却回路,而蒸汽通过蒸汽引出管排出。
为保证系统运行安全,汽包的容积能够保证在停止向汽包给水后,加热炉仍能运行约1小时。
汽包的正常水位在汽包中心线以上100mm。
正常工作时,汽包的蒸汽压力和水位分别通过蒸汽压力调节阀、蒸汽放散阀及汽包液位调节阀进行自动控制。
这三个控制阀均可通过闸阀与系统隔离,此时汽包的水位和工作压力分别可通过手动旁路控制阀来手动控制。
汽包压力和水位在就地和控制室均有指示,汽包上装设了远传压力表和两个远传水位计(平衡容器),汽包超高低压及高低水位报警在控制室发出。
为系统排空,在汽包上装设放散管,并设放散调节阀,在紧急情况下,可以用该放散阀控制汽包压力。
为保证放散调节阀在事故状态下失电失气时全开放散,在放散管道上设手动阀。
汽包上装有两个安全阀,每个安全阀能够排放系统产生蒸汽量的一半。
为控制锅炉水水质,汽包排污设定期排污阀,排除汽包底部杂质,同时设连续排污阀以排出汽水表面杂质,根5据汽包内的水质来调节排污率,可以通过取样冷却器的控制阀每天取样。
2.1.2循环水泵循环冷却回路的冷却水是靠循环水泵产生动力,进行循环,两台循环水泵为电动机驱动,一台循环水泵为柴油机驱动。
正常工作时,一台电动循环水泵运行,当(1)运行水泵故障,(2)或者循环水泵进出口联箱之间的压差小于0.2MPa,(3)或者循环泵出口流量小于530m3/h时,备用电动循环水泵自动启动。
启动顺序为:1)备用电动循环水泵2)柴油机循环水泵此后由操作人员根据现场水泵及电源的实际工况判断是否保证双泵或多泵运行。
柴油机循环水泵的另外一个启动信号是两台电动热水循环泵电源失电或两台电动泵故障。
每台电动泵可通过泵出口处的电动切断蝶阀以及止回阀与系统隔离。
电动热水循环泵以及泵出口电动蝶阀的启动、停止顺序控制是:启动热水循环水泵,启动后延时10s再打开泵出口电动蝶阀。
电动蝶阀开到位;热水循环泵停泵顺序控制是:6关闭热水循环泵电动蝶阀,延时10s再停泵。
电动蝶阀关到位。
参见X5212ZK5。
2.1.3旋转接头组为连接步进梁炉底管冷却系统,在加热炉底部设有旋转接头组件装置,这些旋转接头组件能够满足步进梁垂直和水平运行的需要。
进水旋转接头组件装置有两套,回水旋转接头组件装置两套。
在不用停止加热炉运行的情况下,通过装设的手动蝶阀可将一组旋转接头组与系统隔离,更换泄露的旋转接头。
2.1.4单个冷却回路炉底水梁共有8个冷却回路。
每一冷却回路的冷却水流量是根据该回路的最大计算热负荷以及介质在水梁中的流速来确定的,每个回路的流量可以通过设置在回路上的手动阀进行调节。
在每个冷却回路上均装有流量计,包括指示和低流量报警,报警信号送入控制室并记录。
当出现某一冷却回路流量过低报警时,说明该回路流量低于最小值,通过调节相应回路进水管上的手动控制阀,使该回路的进水流量回到正常值。
每个冷却回路以及总管的正常运行流量、报警流量参见下表7表一82.2给水供应2.2.1汽包排出蒸汽及排污等要通过连续的给水来补充,以保持汽包水位的恒定。
给水管道上设给水调节阀,通过汽包上的液位信号连续调整给水量,控制液位。
2.2.2给水泵房9两座加热炉汽化冷却设一座给水泵房,给水系统的主要设备有:除盐水箱、除盐水泵、给水泵和磷酸盐加药装置。
2.2.2.1除盐水箱及水泵除盐水从厂区综合管网进入加热炉汽化冷却水泵房内的除盐水箱,通过除盐水泵将除盐水箱中的除盐水送至1#、2#除氧器的除氧头,系统设3台除盐水泵,工作制度为两用一备。
除盐水泵共有三台,其中1#除盐水泵对应于1#炉汽化冷却;2#除盐水泵对应于2#炉汽化冷却,放在1#炉汽化冷却系统进行控制;而3#除盐水泵为1#除盐水泵及2#除盐水泵的备用泵,放在1#炉汽化冷却系统进行控制。
除盐水泵启停控制:除氧器液位高于+700mm时,除盐水泵停止运行;除氧器液位低于-250mm时,启动除盐水泵。
经除氧后的除盐水从1#、2#除氧器的支管汇入总管,之后通过电动给水泵将除氧后的除盐水送至1#、2#汽包。
2.2.2.2给水泵系统中给水泵共有5台,其中1#、2#电动给水泵用于1#汽化冷却系统,一备一用;3#、4#电动给水泵用于2#10汽化冷却系统,一备一用;此外还有一台柴油给水泵,当电动给水泵同时发生故障时,或电动给水泵电源故障时,柴油机给水泵启动,柴油机给水泵既可从除氧水箱吸水又可从除盐水箱吸水,保证汽化冷却系统继续运行。
电动给水泵启停控制:汽包液位高于+300mm时,给水泵停止运行;汽包液位低于-100mm时,启动给水泵。
电动给水泵启动顺序:启动给水泵,启动后延时10s再打开给水泵出口电动阀。
电动给水泵停泵顺序:关闭给水泵出口电动阀,延时10s再停泵。
汽包给水管上装有压力和流量仪表以及液位控制阀。
参见X5212ZK52.2.2.3加药装置给水泵房中设有一套磷酸盐加药装置,磷酸盐药液通过加药泵加到汽包中。
112.3蒸汽送出通过蒸汽输送管道,加热炉汽化冷却系统产生的饱和蒸汽送入车间蒸汽母管。
蒸汽送出管上装有流量计,可在汽化冷却控制室指示蒸汽产量。
当蒸汽流量超过最大允许蒸汽产量时,炉底管的保温需要更新。
蒸汽流量过大报警值为20t/h,报警信号在加热炉控制室发出。
汽包的压力通过蒸汽送出管上的压力阀控制。
3、各个调节阀的控制说明3.1 汽包出口蒸汽管压力调节阀(V1 )根据汽包出口蒸汽压力(汽包本体压力),对汽包出口蒸汽压力调节阀V1进行调节。
控制汽包压力范围为1.0—1.1MPa。
3.2 汽包补水管流量调节阀(V2)根据汽包液位,对汽包补水流量调节阀V2进行调节。
以汽包水平中心线为0.0mm,中心线以上为正,中心线以下为负。
汽包极限高水位为+500mm,极限低水位为-100,控制汽包液位范围为+50mm~+150mm。
3.3 除氧器压力调节阀(V3a/V3b)根据除氧器本体压力,对除氧器入口蒸汽压力调节阀V3a/V3b进行调节。
除氧器为大气式热力除氧器,正常工12作压力变化范围为0.015MPa~0.03MPa,正常值为0.02MPa。
3.4 除氧器入口除盐水流量调节阀(V4a/V4b)根据除氧器液位高低,对除氧器入口除盐水流量调节阀V4a/V4b进行调节。
以除氧器水平中心线为中心线,中心线以上为正,中心线以下为负。
除氧器极限高水位为+700mm,极限低水位为-200mm,正常液位控制范围为+500mm~+350mm。
3.5 除氧器温度调节阀V5a/V5b根据除氧器水空间的温度,对流入除氧器的蒸汽调节阀V5a/V5b进行调节。
水温控制在102℃—104℃。
3.6 汽包蒸汽放散调节阀(V6)根据汽包出口蒸汽压力(即汽包本体压力),对汽包出口蒸汽压力调节阀V6进行控制。
当汽包压力大于1.2MPa 时,压力调节阀开启,放散卸压;当汽包压力低于1.0MPa时,调节阀关闭。
3.7 除盐水补水管切断阀(V7)根据除盐水箱液位高低,对除盐水补水管切断阀(V7)进行控制。
以水箱底面为0.0位,控制除盐水箱液位范围+2700—+1000mm,+1000mm时打开切断阀,+2700mm时关闭切断阀。
13参见X5212ZK514151617。