RAMS及LCC控制程序
RAMS管理程序
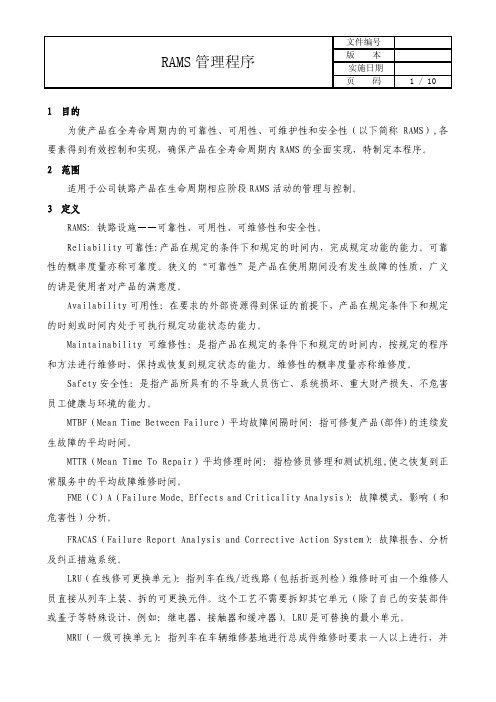
划并实施,保证其处于完好状态。ຫໍສະໝຸດ 4.8.2 负责产品交付中的防护。
4.9 办公室负责 RAMS 知识的教育和培训并做好相关记录。
5 过程乌龟图
使用资源 1、计算机/网路资源 2、传 真机 3、资料库及相关文献 4、打印机等
由谁进行: 过程所有者:技术部(经理、RAMS 工程师、设计工程师) 过程协助者:总经理;管理者代表; 顾客代表;营销部;采购部;质管 部;生产部;办公室
项目组 RAMS 专题会讨论评审同意,经管理者代表批
准后实施。
6.1.4 项目组 RAMS 专题会由项目负责人主持,RAMS
工程师和项目组相关人员共同参加。必要时邀请顾客
RAMS 管理程序
文件编号 版本 实施日期 页码
5 / 10
工作流程 A
建立危害记 录 制定 RAMS 工作 计划
实施 RAMS 设计 B
FRACAS(Failure Report Analysis and Corrective Action System):故障报告、分析 及纠正措施系统。
LRU(在线修可更换单元):指列车在线/近线路(包括折返列检)维修时可由一个维修人 员直接从列车上装、拆的可更换元件。这个工艺不需要拆卸其它单元(除了自己的安装部件 或盖子等特殊设计,例如:继电器、接触器和缓冲器)。LRU 是可替换的最小单元。
RAMS 信息至少应包括以下内容:
●产品功能、性能要求、与其它产品的相互关系和接
RAMS 目标 《 RAMS 工 作策划表》
口;
●有关法律法规和行业要求,如产品标准、行业安全 政策等;
●产品工作的环境条件、地理条件、以及产品的运行
策略;
●产品维护条件、后勤保障条件、维护策略(如维护
ramslcc控制程序
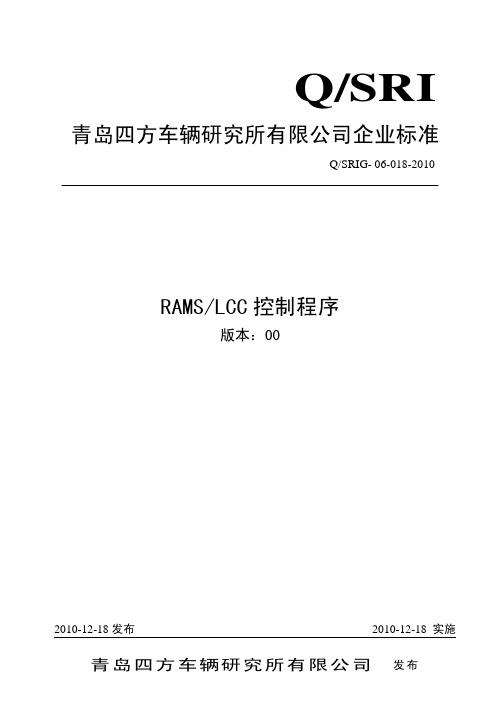
文件控制程序青岛四方车辆研究所有限公司企业标准Q/SRIQ/SRIG- 06-018-2010RAMS/LCC 控制程序版本:00RAMS/LCC控制程序1目的与适用范围1.1 为规范产品的RAMS/LCC实施步骤和控制要求,特制定本程序。
1.2 本程序适用于公司轨道车辆产品RAMS/LCC工作。
2 规范性引用文件Q/SRIG-06-001-2010《经营管理手册》GB/T21562《轨道交通可靠性、可用性、可维修性和安全性规范及示例》(idt EN 50 126)GB/T19001-2008《质量管理体系要求》(idt ISO9001:2008)国际铁路行业标准(IRIS)3 术语3.1 RAMS:指(铁路)产品的可靠性、可用性、可维护性和安全性。
3.2 可靠性:产品在规定条件下和规定的时间区间内完成规定功能的能力。
3.3 可用性:可修复产品在某一特定瞬间维持其功能的概率,或在某一期间内维持其功能的时间比率。
可用性是产品可靠性、可维护性的综合指标。
3.4 可维护性:产品在规定的使用条件下并按规定的程序和手段实施维修时,为保持产品处于正常使用状态或为修复产品故障、缺陷,使之恢复执行功能状态的能力。
3.5 安全性:保证行车和人身以及设备安全的能力,以在给定时刻系统维持安全功能完善的概率指标。
3.6 LCC:是指生命周期成本。
3.7 其它术语:本程序中标准术语采用GB/T 19000-2008 《质量管理体系基础和术语》(idt ISO9000:2005)中的有关术语和定义。
铁路行业的术语和定义采用国际铁路行业标准(IRIS)附录5的内容。
4 管理职责4.1 发展计划部负责RAMS归口管理。
4.2财务部负责公司成本核算的归口管理及汇总。
Q/SRIG- 06-018-20104.3 事业部负责识别顾客RAMS要求,负责产品的RAMS相关的试验及数据分析,并提供相应的分析报告。
负责LCC成本的分析。
4.4 市场部负责收集产品运用阶段的RAMS的数据资料。
RAMS管理程序

企业标准RAMS管理程序发布1.前言基于顾客、产品与自身发展要求,根据本公司的企业特征和产品特点,提出了轨道交通产品的RAMS/LCC的实施手册。
2 定义2.1 RAMS可靠性、可用性、可维护性和安全性的英文缩写。
2.2 可靠性(Reliability)产品在规定条件下和规定时间内,完成(或保持)规定功能的能力。
2.3 可用性(Availability)在要求的外部条件得到保证的前提条件下,产品在规定的条件下和规定时刻或规定区间内,处于可执行规定功能状态的能力。
2.4 可维护性(Maintainability)在规定的条件下,使用规定的程序和资源进行维护时,对于给定使用条件下的使用产品,在规定的时间区间内,能完成指定的实际维护工作的能力。
2.5 安全性(Safty)免除不可接受的风险影响的特性。
3 职责3.1 研发部RAMS职责a)评估和制定产品RAMS指标;b)按要求进行RAMS分析与设计;c)产品RAMS试验方案制定;d)在产品的研制和使用阶段,进行产品RAMS评估与验证,进行产品可靠性增长管理;e)负责产品研制过程中的故障分析与解决方案;f)负责产品使用过程中的疑难故障分析和制定纠正、预防措施;g)进行RAMS数据的收集。
3.2 制造部RAMS职责a)负责配合制作相关的样品、产品等;b)产品使用过程中的问题和故障组织解决,当原因不明确时,提交质管部进行故障分析和解决;c)制造过程RAMS数据收集。
3.3 质管部RAMS职责a)对各部门提交的故障信息进行规范性审查,组织落实疑难问题的分析,跟踪重大故障的闭环解决;b)负责产品RAMS相关的检验、测试、试验分析,并提供相应的报告;c)定期进行故障汇总、统计与分析;d)组织进行RAMS阶段性评审。
3.4 采购部RAMS职责a)参与各供应商RAMS要求的制定;b)向各产品供应商发布RAMS要求;供应商产品RAMS跟踪管理与符合性确认;c)供应商管理和评价。
RAMS与LCC控制程序
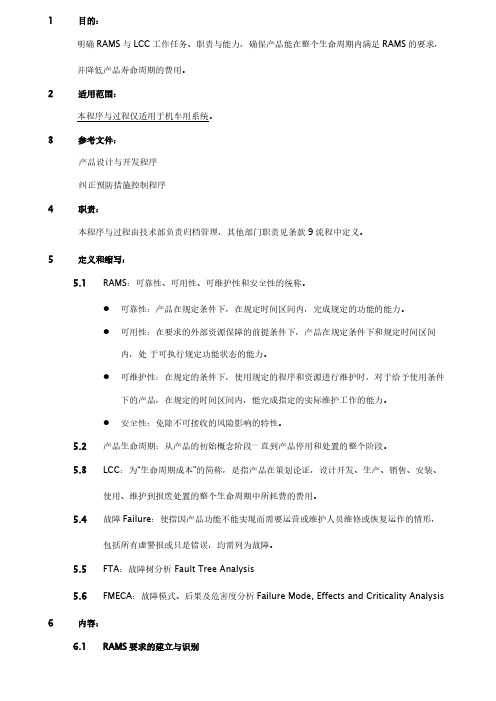
1目的:明确RAMS与LCC工作任务、职责与能力,确保产品能在整个生命周期内满足RAMS的要求,并降低产品寿命周期的费用。
2适用范围:本程序与过程仅适用于机车用系统。
3参考文件:产品设计与开发程序纠正预防措施控制程序4职责:本程序与过程由技术部负责归档管理,其他部门职责见条款9流程中定义。
5定义和缩写:5.1RAMS:可靠性、可用性、可维护性和安全性的统称。
⚫可靠性:产品在规定条件下,在规定时间区间内,完成规定的功能的能力。
⚫可用性:在要求的外部资源保障的前提条件下,产品在规定条件下和规定时间区间内,处于可执行规定功能状态的能力。
⚫可维护性:在规定的条件下,使用规定的程序和资源进行维护时,对于给予使用条件下的产品,在规定的时间区间内,能完成指定的实际维护工作的能力。
⚫安全性:免除不可接收的风险影响的特性。
5.2产品生命周期:从产品的初始概念阶段一直到产品停用和处置的整个阶段。
5.3LCC:为“生命周期成本”的简称,是指产品在策划论证,设计开发、生产、销售、安装、使用、维护到报废处置的整个生命周期中所耗费的费用。
5.4故障Failure:使指因产品功能不能实现而需要运营或维护人员维修或恢复运作的情形,包括所有虚警报或只是错误,均需列为故障。
5.5FTA:故障树分析 Fault Tree Analysis5.6FMECA:故障模式、后果及危害度分析Failure Mode, Effects and Criticality Analysis 6内容:6.1RAMS要求的建立与识别6.1.1如果是顾客设计的产品,应由技术部与顾客联系,获取产品周期和产品规格等信息以及RAMS的要求。
6.1.2如果是公司设计的产品,由技术部与顾客联系,以确认是否有RAMS的要求。
6.1.3对于行业标准产品,则按电线电缆产品标准执行,同时考虑顾客对RAMS的要求。
一般来说,标准电线电缆的电气性能、机械与物理性能可作为RAMS的输入。
RAMS控制程序(含表格)
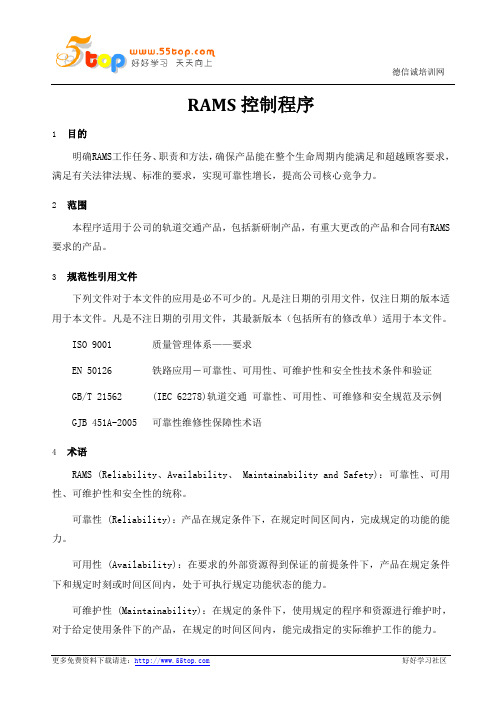
RAMS控制程序1目的明确RAMS工作任务、职责和方法,确保产品能在整个生命周期内能满足和超越顾客要求,满足有关法律法规、标准的要求,实现可靠性增长,提高公司核心竞争力。
2范围本程序适用于公司的轨道交通产品,包括新研制产品,有重大更改的产品和合同有RAMS 要求的产品。
3规范性引用文件下列文件对于本文件的应用是必不可少的。
凡是注日期的引用文件,仅注日期的版本适用于本文件。
凡是不注日期的引用文件,其最新版本(包括所有的修改单)适用于本文件。
ISO 9001 质量管理体系——要求EN 50126 铁路应用-可靠性、可用性、可维护性和安全性技术条件和验证GB/T 21562 (IEC 62278)轨道交通可靠性、可用性、可维修和安全规范及示例GJB 451A-2005 可靠性维修性保障性术语4术语RAMS (Reliability、Availability、 Maintainability and Safety):可靠性、可用性、可维护性和安全性的统称。
可靠性 (Reliability):产品在规定条件下,在规定时间区间内,完成规定的功能的能力。
可用性 (Availability):在要求的外部资源得到保证的前提条件下,产品在规定条件下和规定时刻或时间区间内,处于可执行规定功能状态的能力。
可维护性 (Maintainability):在规定的条件下,使用规定的程序和资源进行维护时,对于给定使用条件下的产品,在规定的时间区间内,能完成指定的实际维护工作的能力。
安全性 (Safety):免除不可接受的风险影响的特性。
寿命周期(Life Cycle):系统从论证开始到退役为止的全部时期。
故障(Failure):是指因产品功能不能实现而需要运营或维护人员维修或恢复运作的情形,包括所有虚警报或指示错误,均需列为故障。
FTA:故障树分析 Fault Tree AnalysisFMECA:故障模式、影响及危害性分析 Failure Mode, Effects and Criticality Analysis SAP:系统保证计划System Assurance PlanRBD:可靠性框图Reliability Block DiagramQRA:定量风险评估Quantitative Risk AssessmentPHA:初步危险分析Preliminary Hazard AnalysisO&SHA:使用和保障危害分析Operating & Support Hazard AnalysisHL:危险登记簿Hazard LogRCM:以可靠性为中心的维修Reliability Centered MaintenanceFRACAS:故障报告、分析和纠正措施系统Failure Report Analysis and Corrective Action SystemSSR:系统安全报告System Safety Report技术部门:本程序中的“技术部门”是具有技术研发职能的部门。
(PEONY)RAMS控制程序

(PEONY)RAMS控制程序1. 简介本文档旨在介绍和解释(PEONY)RAMS控制程序的相关细节和功能。
该控制程序是为了提高系统的可靠性、可用性、维护性和安全性而开发的。
2. 功能和特点- (PEONY)RAMS控制程序包含以下几个主要功能:- 可靠性(Reliability):通过监测系统的故障和故障率,提供系统的可靠性评估和预测。
- 可用性(Availability):监测和评估系统的可用性,包括系统的运行时间、可操作性和故障恢复时间。
- 维护性(Maintainability):提供系统的维护计划和预防性维护建议,以提高系统的可维护性和可修复性。
- 安全性(Safety):评估系统的安全性和风险,提供安全控制措施和建议,确保系统的安全性。
- (PEONY)RAMS控制程序的特点包括:- 可定制性:根据具体系统的需求和特点,可以定制化设置和调整控制程序的功能和参数。
- 实时监测和反馈:控制程序能够实时监测系统的状态和指标,并提供及时的反馈和报警信息。
- 数据分析和可视化:控制程序能够对系统的数据进行分析和可视化展示,帮助用户理解系统的性能和问题。
- 故障诊断和预测:通过分析系统的历史数据和趋势,控制程序可以进行故障诊断和预测,帮助用户提前采取措施避免故障的发生。
3. 使用指南在使用(PEONY)RAMS控制程序时,用户应注意以下几个方面:- 安装和配置:按照控制程序的安装和配置指南进行操作,确保正确安装和设置控制程序。
- 数据输入和采集:提供系统的数据输入,确保控制程序可以获取准确的系统数据。
- 监测和分析:监测控制程序的反馈和报警信息,及时了解系统的状态和性能。
- 故障处理和维护:根据控制程序的故障诊断和预测结果,采取相应的故障处理和维护措施。
4. 总结(PEONY)RAMS控制程序是一款强大而实用的工具,可帮助用户提高系统的可靠性、可用性、维护性和安全性。
通过实时监测、故障诊断和预测等功能,帮助用户及时发现和解决系统问题,确保系统的正常运行和安全性。
22.GTE-MSPD-TE03- 2018 RAMS、LCC控制程序 B0918

3引用标准或文件
GTE-MSPD-TE01-2018设计与开发控制程序
4职责
4.1技术部
负责产品设计开发和制造过程的RAMS控制,确保产品满足规定RAMS/LCC的要求;归口管理公司RAMS/LCC工作。
■项目管理部
□
10
■质量部
■
文件修订记录
N0.
版本
修订人
修订内容摘要
批准人
生效日期
1
A0
初版发行。
2018-06-01
2
B0
重新梳理过程各要素。
2018-09-01
3
4
5
1适用范围及目的
本文件定义了公司RAMS/LCC工作的过程,以确保产品满足RAMS/LCC的要求。适用于产品的设计与开发。
2术语和定义
3)如客户没有要求可用性目标,则可不定可用性目标。
7.3.3.4.2可用性的统计
服务部收集OT和TCM数据,提交给RAMS/LCC负责人分析计算Ai值。
7.3.3.4.3提高可用性的方法
1)提高可靠性
2)适时增加维修间隔时间。
3)使用优秀维修人员,加强技术培训,优化维修程序,减少不可用时间。
4)提高标准化、模块化、互换性,完善防错措施和识别标记,使维修良好的可达性。
5)保证维修安全
设计时考虑维修作业不会引起机械损伤、有害气体等伤害。
6)检测诊断准确、迅速、简便
配备检测仪表、软件;选择检测方式;合理安排传感器的位置。
7)重视贵重部件的可维修性
应具备恢复原形的性能以节约成本。
RAMS与LCC培训资料

生命周期成本LCC1、生命周期成本(IEC300-3,IEC60300-3-3 ):根据LCC 模型,一个产品在其生命周期内累计的模型成本。
2、生命周期成本过程:根据LCC模型,对购买和使用一个产品的总成本进行经济分析的过程。
这个分析为决定产品的设计、开发和使用提供了重要的输入。
产品供应商可以通过评估不同方案和进行比较分析研究,优化产品的设计。
也可以评估不同的运行和维修策略以优化LCC。
3、LCC由若干方面组成:-投资列车的购置成本需要的专用工具备品备件(LRU:Line Replaceable Unit)培训文件化……页脚内容1-维修预防性维修(PM:Preventive maintenance)纠正性维修(CM:Corrective maintenance)-运行成本能源(电或燃料)轨道的使用(*)运行人员(*)-生命结束成本处置成本(*)注:(*)- 这些项目一般不包括在LCC的合同中。
页脚内容23、LCC的作用:-投标-比较不同的方案-项目控制页脚内容3-成本预测-……页脚内容4可靠性Reliability1、定义(IEC50 191-02-06)可靠性指的是一个部件履行要求的功能的能力:-在给定的条件下和-在给定的时间内。
2、测量方法1)R(t), 可靠性概率: 一个部件在给定条件下、在给定的时间间隔内能够履行要求的功能的概率。
当= 常数时,t 可以是以下任何一种参数:-时间(日历时间, 车辆运行时间, 部件运行时间, 旅行时间) -运行的距离页脚内容5-工作循环或类似的.2) 故障概率F(t) = 1-R(t)3) 故障概率密度f(t) = d F(t) / d t4) 故障率= f(t) / R(t)当故障率为常数时, 即不随时间和行程变化时,= 1/MTTF, 对于不可修复部件;= 1/MTBF, 对于可修复部件;= 1/MDBF, 通常是对车辆.这里, MTTF: Mean Time To Failure到故障的平均时间MTBF: Mean Time Between Failures故障间的平均时间(指运行时间) MDBF: Mean Distance Between Failures故障间的平均行程页脚内容6注意: 一般情况下, 是随时间变化的, 譬如在运行初期和末期故障率都会比较高(浴盆曲线).MDBF是经常被作为规范使用的.MDBF = 在一段时间里的运行行程/ 这段时间总的故障次数3、故障分类(EN 50 126)1)特大故障(Significant, Immobilizing Failure)具有下列特征的故障:-产生危害和/或-列车无法移动或者导致服务延迟大于某一规定时间和/或引起成本高于某一规定水平.2)大故障(Major, Service Failure)具有下列特征的故障:-系统必须调整以达到规定的性能, 并且-不满足特大故障的条件.3)小故障(Minor)具有下列特征的故障:页脚内容7-不阻止系统达到规定的性能, 并且-不满足大故障或特大故障的条件.页脚内容8可靠性确定的例题:5辆机车在24个月内的故障情况如下表. 所有机车每月的行程为20 Tkm. 故障之后立即被修理好并返回到运行. 要求确定机车的MDBF.(24个月平均; 前12个月平均; 后12个月平均)页脚内容9页脚内容101. 用全部24个月数据: MDBF = 5*480 / 20 = 120 Tkm故障率= 1/MDBF = 0.83 次/ 100 Tkm2. 用前12个月数据:MDBF = 5*240 / 14 = 85.7 Tkm故障率= 1/MDBF = 1.17 次/ 100 Tkm3. 用后12个月数据:MDBF = 5*240 / 6 = 200 Tkm故障率= 1/MDBF = 0.5 次/ 100 Tkm4. 每辆机车的MDBF, 故障率= ?5. 行程-累计故障次数曲线页脚内容116. M(d)程序页脚内容12有效性Availability1. 定义(IEC50 191-02-05)一个部件在履行要求功能的状态的能力-在给定的条件下-在给定的时间内或在给定的时间间隔内-假定要求的外部资源已被提供.2. 有效性的测量A = 有效时间up time / (有效时间up time +无效时间down time) = up time / 总的时间total time= 1 - down time / total time有效时间up time: 部件在有效状态的时间间隔无效时间down time: 部件在无效状态的时间间隔1)固有有效性inherent availability (Ai)Ai = 纠正性维修时间/ 总的时间页脚内容13= MTBF / (MTBF + MTTR)MTBF: Mean Time Between Failure平均故障时间MTTR: Mean Time To Restoration 平均恢复时间纠正性维修时间corrective maintenance time (主动维修时间active maintenance time): -故障定位时间-零件更换时间(包括进入到更换位置)-修完后的复查时间但不包括: 服务时间, 路途时间, 休息时间和作决定的时间.2)技术有效性technical availability (At)At = (纠正性维修时间+ 预防性维修时间) / 总的时间预防性维修时间Preventive maintenance time:-维修计划中包括的安全措施和工作准备时间-纯维修时间-修完后的复查时间页脚内容14但不包括: 服务时间, 路途时间, 休息时间和作决定的时间.作为一个规则, 预防性和纠正性维修时间不包括在维修工场中修理, 大修或重新调试被更换零件的时间, 因为这不会影响到车辆的有效性. 但是如果被换下的零件修好后要被重新安装在原车辆中, 这个时间要被计入作为计算有效性.4)运行有效性Operational availability (Ao)除纠正性, 预防性维修时间之外, 还将物流和管理性延迟时间也计入无效时间.5)车辆有效性Fleet availability (Afleet)Afleet = 可运行的车辆数/ (可运行的车辆数+ 现在维修的车辆数)=可运行的车辆数/ 总的车辆数专用非有效性(special unavailability):由于纠正性维修而不有效的车辆数/ 总的车辆数一般, Ai, At, 专用非有效性会在合同中用到.页脚内容15例题:车辆每天运行18h (一年按365天计). 每年纠正性维修的时间为100h, 预防性维修的时间是200h. 请计算Ai, At.1.时间按h计算.2. 时间按天计算, 每天按24小时计.3. 时间按天计算, 每天按8小时工作时间计.页脚内容161. Ai = (18*365-100)/(18*365)=0.9848At = (18*365 -100 -200) / (18*365) = 0.95432. Ai = 1-100/24/365=0.9886At = 1- (100+200)/24/365 = 0.96573. Ai = 1-100/8/365=0.9658At = 1- (100+200)/8/365 = 0.8973页脚内容174. 如何改进车辆的有效性-改进可靠性-在合适时加大维修间隔-减少维修时间(用尽可能多的有用的工人人数, 用优化的程序)-改善可维修性(maintainability): 快速故障探测, 易进入, 很好诊断, 对更换频繁的部件很容易进入, 更换时不需重工或调整等)-将维修活动放在运行不太繁忙的时间里-将维修时间换到车辆不运行时.页脚内容18可维修性Maintainability1.定义(IEC50 191-02-07)一个部件的能力:-在给定的使用条件下-被维持在-或被恢复到-一个它能履行要求的功能的状态-当在给定的条件和使用规定的程序和资源执行维修时.2.可维修性的量测MTTR: Mean Time To Restoration平均恢复时间恢复时间具有统计分布特性, 一般用对数正态分布来表示.页脚内容19恢复Restoration: 通过更换缺陷件(LRU: Line Replaceable Unit在线可更换件)将车辆恢复到正常运行状态. 缺陷件随后在维修工场被修理.3. 恢复时间Restoration time, 主动维修时间Active maintenance time, 可维修性Maintainability可维修性可以被描述为在规定的维修和运行条件下易于服务程度和易修理程度的特性.其主要特点是:-可进入性(accessibility)-可测试性(testability)-可更换性(exchangeability)可进入性(accessibility): 要测量部件的特性或进行维修, 部件必须容易进入(人员和工具的空间, 尽可能页脚内容20少地移出其它部件).可测试性(testability): 故障之后要进行的检查要使用简单的, 不相互矛盾的测试(故障识别和定位, 即诊断的准确性).可更换性(exchangeability):故障发生后, 有缺陷的部件要用储存的备件去更换, 要没有调整和其它形式的重工.可测试性(testability): 更换缺陷部件后, 需要用另一个简单的测试去检查故障是否已被消除.因此, 可以用3个时间之和(故障定位, 更换, 复核)来表示检查和修理过程, 称为”主动维修时间” (Active maintenance time). 服务时间(可进入性)也被计入主动维修时间.主动维修时间:-故障定位时间, 包括进入-缺陷部件更换时间-复核时间页脚内容21主动维修时间也就是恢复时间, 具有统计分布特性, 一般用对数正态分布来表示. 其平均值就是MTTR(平均恢复时间) –可维修性的量测方法.4. 可维修性和维修(Maintainability & Maintenance)维修Maintenance: 所有技术性和行政性措施的组合, 包括管理措施, 其目的是维持部件在或将其恢复到能够履行要求的功能的状态.可维修性是一个部件的内在特性, 这个特性是部件制造商的职责.维修是由维修团队应用技能和资源来实施的一种活动, 这是维修者的职责.理想状况: 可维修性和维修应该彼此和谐.不理想: -差的可维修性可以被好的维修补偿掉(但有一定限度)-好的可维修性可以被差的维修所毁掉-内装式零件的好的可维修性可以被差的系统集成所毁掉页脚内容225. 可维修性的验证5.1 Sample analysis样本分析5.2 Test Restoration恢复测试可从FMEA分析中的故障里随即选取一些做试验.页脚内容23安全性Safety1.定义(IEC 50 126)Freedom from unacceptable risk. 安全性指的是免于不可接受的风险.风险: 故障后果的严重性和故障发生概率的组合.Combination of the severity of a failure consequence and the probability of occurrence of the failure.2.风险水平根据有害事件发生的严重性和其频率, 风险的水平可以分为: (IEC 50 126)-不可接受的Unacceptable-不希望的Undesirable-可忍受的Tolerable-可忽略的Negligible页脚内容24有害事件发生的频率风险水平有害事件发生的严重度低---------------------------------------------------------高风险会与下列因素相关:-乘客-运行和管理人员-铁路系统之外的人员(行人, 汽车司机)页脚内容25-维修人员-环境-铁路系统或子系统本身最基本的安全特性:-出轨-刹车和牵引力的控制-门的控制-结构损坏-碰撞(同其它车辆或铁路系统之外的东西)-防火-触电安全性不仅是一个技术问题, 也是一个运行和维修的安全程序问题. 实际上, 大部分安全问题是由于人员的错误或失误引起的.铁路系统的安全性目标是聚焦在事故预防(Error proof), 而不是减轻事故的后果.页脚内容263. 安全性的量测有害故障率(Hazarduous Failure Rate)页脚内容27预防性和纠正性维修Preventive & Corrective Maintenance1.定义(IEC50)维修: 所有技术性和行政性措施的组合, 包括管理措施, 其目的是维持部件在或将其恢复到能够履行要求的功能的状态.纠正性维修: 故障之后所实施的维修, 目的是将部件恢复到其能履行要求的功能的状态.预防性维修: 按照预先确定的间隔或根据预先定义的准则实施维修, 其目的是降低故障发生或部件功能降低的概率.2. 按照VOV6.7的维修流程图页脚内容283.维修的量测页脚内容29维修费用. 可以有多种形式:-每车每年的维修成本-每车每km的维修成本-每座每km的维修成本维修费用可分为人员成本(或man.hours)和设备成本. 维修成本是LCC的重要组成部分.注意: 维修费用在不同的运行年份可能是不同的, 如大修年份预防性维修费用可能很高; 对老的车辆的纠正性维修成本可能要远高于初始高峰故障已经过去的车辆.4. 纠正性维修成本(CM Cost)的计算是LCC分析中的重要部分.一般, 两阶段维修模型在LCC分析中被用于计算CM Cost:1)故障元件被从储存在仓库里的好的备件替换掉, 以便使车辆可以尽快地工作.2)可修理的元件(LRU)将在修理工场(CWS)中被修理; 对于不可修理的LRU, 损坏的将被处置掉, 同时备件库中增加一个LRU.页脚内容30因此, 对于可修理的LRU, 有两部分进入CM Cost:-更换有缺陷的LRU的人工成本(可维修性, 主动维修时间的成本)-在修理工场修好有缺陷的LRU的成本.对于不可修理的LRU, 下面两部分进入CM Cost:-更换有缺陷的LRU的人工成本(可维修性, 主动维修时间的成本)-新的备件的成本(适用时, 还包括处置有缺陷的LRU的成本).在LCC模型中, 每个LRU的CM Cost可以用下式计算:CMcost = 故障率*(更换时间*单位时间人工成本+ 在修理工场修理的成本包括人员成本和材料费用)这里: 故障率: 故障次数/百万km,更换时间: Man.hours,单位时间人工成本: 元/h,在修理工场修理的成本指的是-对于不可修理的LRU, 新的LRU的价格;-对于可修理的LRU, 修好有缺陷的LRU的价格.因此一个LRU每年的CM Cost为:页脚内容31CMcost,yearly = CMcost * 车辆每年的运行距离(百万km)页脚内容32例题:1.不可修理的LRU. 故障率= 4 / 百万km; 更换时间: 0.75h, 2个人; 单位时间人工成本: 50元/h; 新的LRU的价格: 480元/个; 车辆每年运行的距离: 0.08 百万km/年. 计算: 该LRU每年的纠正性维修成本(CM Cost).2. 可修理的LRU. 故障率= 2.5 / 百万km; 更换时间: 1.5h, 1个人; 单位时间人工成本: 50元/h; 新的LRU 的价格: 2500元/个; 修理费用:估计为新部件价格的15%; 车辆每年运行的距离: 0.3 百万km/年. 计算: 该LRU每年的纠正性维修成本(CM Cost).页脚内容33答案:1. CMcost,yearly = 4*(2*0.75*50 + 480) *0.08 = 177.6元/年.2. CMcost,yearly = 2.5*(1.5*50 + 2500*15%) *0.3 = 337.5元/年.注意: 维修的成本是很难准确确定的. 因为故障的类型是很多的, 尤其是在投标阶段, 很难准确了解故障类型, 修理时间. 相对来说, 更换时间可以比较准确地确定. 因此, 纠正性维修成本只能是粗略的.纠正性维修成本要在实际的运营中加以确认.页脚内容34预防性维修成本(PM Cost)的计算相对来说, 预防性维修成本的计算要简单一些. 它是基于时间间隔或行程间隔而安排的维修活动. 如: -周维修-季度维修-年度维修-每5年一次的大修-每15年一次的大修一般来说, 更长时间间隔的维修项目包括了小一些时间间隔的维修项目.平衡性维修Balanced maintenance: 指的是某个维修活动被分为几个小的部分, 每个部分在车辆不太繁忙时被实施.状态维修Condition-based maintenance(CBM): 指的是维修活动根据磨损的准则来实施. 以此维修策略制订出的预防性维修将更为经济.以可靠性为中心的维修Reliability-centred maintenance(RCM): 它是一种通过成本/性能的比较分析为基础页脚内容35的优化的成本有效性维修系统的技术. 譬如比较一个维修活动的成本和无此维修时导致的故障的成本, 从而决定维修的策略.RCM包括了功能分解, FMECA(Failure Mode Critical Effect Analysis, 故障模式关键影响分析)和决定树, 考虑了不同被选因素的相对重要性, 如安全, 故障类别, 有效性, 与CM相比较的PM的成本和CBM的有效性.页脚内容36例题车辆转向架的季度维修项目如下: (每30 Tkm)单位时间人工成本: 50元/h.计算: 一个转向架每年的预防性维修成本(PM Cost).页脚内容37答案:每季度每个预防性维修项目的成本:目视检查地刷的成本: 0.25*1*50*2=25元润滑轮轴承的成本: (0.15*1*50+2)*4=38元目视检查刹车块的成本: 0.1*1*50*4=20元因此, PMcost, yearly = (25 + 38 +20)*4 = 332元.页脚内容38LCC分析用于设计比较的例子比较两种不同设计方案的LCC.第一种方案: 现有的已在运行的情况. 部件由LRU A(1个), LRU B(2个), LRU C(2个), LRU D(1个), LRU E(3个)插接在一起组成. 各种LRU的故障率, 价格见表1. 这些LRU均是可修复的, 其修复成本均为新的备件的价格的20%.表1:第二种方案: 由于SMD技术的发展, 可以将这些LRU集成成一个LRU X. 据粗略估计, LRU X的价格约为6000元, 故障率大约为20次/(10**6h). LRU X也是可修复的, 其修复成本初步估计为新的备件的5%.请比较这两种方案的LCC(仅考虑购置成本和CM成本), 以判定新方案(第二种)是否应该研发.部件的整个生命周期在50km/h时为10百万km行程. 各种LRU(A, B, C, D, E, X)的平均故障修复时间均为0.5h, 1人. 单位时间人工成本为30元/h.页脚内容39第三种情况: 现在新的方案研发出来了, 并在实际中得到了运用. 虽然价格保持在了原来的目标(6000元), 但实际运行表明, 其故障率和故障修复成本均比预计的要高, 分别达到30次/(10**6h)和新备件价格的8%(即实际的可靠性指标和可维修性指标未能达到预期的水平). 请计算实际研发出来的LRU X的LCC.页脚内容40答案:在整个生命周期里的总的运行时间: 10*10**6 / 50 = 0.2* 10**6 h每次更换故障的LRU的成本: 0.5*1*30 = 15元第一种情况:CMcost, life cycle, LRU A = 故障率*总的运行时间*(每次更换故障LRU的成本+ 每次修好故障的LRU的成本) *部件中LRU A的数目= 6 * 0.2 * (15 + 2500*20%) * 1= 618元.CMcost, life cycle, LRU B = 4.5 * 0.2 * (15 + 750*20%) * 2= 297元.CMcost, life cycle, LRU C = 3 * 0.2 * (15 + 300*20%) * 2= 90元.CMcost, life cycle, LRU D = 5 * 0.2 * (15 + 900*20%) * 1= 195元.CMcost, life cycle, LRU E = 4 * 0.2 * (15 + 550*20%) * 3= 300元.CMcost, life cycle,整个部件= CMcost, life cycle, LRU A + CMcost, life cycle, LRU B + CMcost, life cycle, LRU C + CMcost, life cycle, LRU D + CMcost, life cycle, LRU E = 618 + 297 + 90 + 195 + 300 =1500元.部件的购置成本=2500*1 + 750*2 + 300*2 + 900*1 + 550*3 = 7150元页脚内容41整个部件的LCC = 7150 + 1500 = 8650 元.第二种情况:整个部件的LCC = 6000*1 + 20*0.2*(15 + 6000*5%)*1 = 6000 + 1260 = 7260 元< 8650元(第一种方案的LCC)因此, 应该研制新的方案.第三种情况:整个部件的LCC = 6000*1 + 30*0.2*(15 + 6000*8%)*1 = 6000 + 2970 = 8970 元> 8650元(第一种方案的LCC) > 7260元(新研制方案预估的LCC)为了准确预测故障情况, 应当使用FMEA或FTA(Fault Tree Analysis,故障树分析)分析, 以尽量降低风险. (在这个例子中是可靠性和可维修性风险).页脚内容42问题讨论:LCC方法的局限性有哪些?页脚内容43RAMS和LCC工作程序1. 作用RAMS/LCC过程的作用有三个:1) 研究故障的后果以及它们对用在风险评估中有害和其它不希望事件的影响, 以确定减少风险的措施;2) 以我们产品的可靠性性能和可维修性性能为基础计算在确定的产品生命周期内维修(纠正性维修和预防性维修)的成本.3) 用来检查在这个领域客户的要求是否被满足, 以及用于确认要求的/同意的可靠性数值, 修复时间和维修成本.2. 过程页脚内容44页脚内容45页脚内容46页脚内容47页脚内容48页脚内容493. 定义和公式(略)4. 变更EHD负责设计和验证/确认过程的变更对RAMS/LCC的影响将被检查, 并就下列方面进行评估: -针对内部和外部危害的防护机械进入电气进入过热过压火和烟环境损害-故障识别指示故障信息-功能部件的变更页脚内容50。
RAMS及LCC控制程序

精心整理RAMS及LCC控制程序1.目的产品在生命周期内,通过执行的一系列活动以确保在每个阶段完成为产品确定的RAMS要求,并符合和满足顾客提出的RAMS目标。
2.范围本程序适用于公司产品论证开始到质保期,延伸到产品使用维护期间的相关跟踪活动结束。
3.4.4.14.2销售部负责本程序运行过程中与用户的联系和协调;4.3质量控制部负责本程序运行过程中的质量管理、质量评审工作,负责产品安全事例的管理、建立、更新工作;4.4研发部负责具体产品RAMS程序策划、建立工作及相关文件的编制、更改工作。
4.5财务部负责商业风险分析工作。
5.控制程序5.1研发部确定产品RAMS应收集的资料,销售部和质量控制部负责在产品生命周期内收集相关数据和信息,收集的信息交研发部,该信息用作RAMS分析活动的输入内容。
5.2RAMS/LCC程序见表5-1:《RAMS/LCC程序表》RAMS/LCC程序表表5-15.3.3.2.1一般情况下,分析范围是产品整个生命周期5.3.3.2.2出于比较各种方案时,可能只分析产品生命周期中的某个阶段5.3.4确定限制条件和假设在LCC分析前,应确定有关的限制、假设,例如:●产品使用环境、维护条件等●产品规格性能要求●产品的RAMS要求,如MTBF要求等●资金限制、价格限制等5.3.5确定LCC结构估计。
成本。
汇5.3.6.2.3利率为10%5.3.6.2.4除了应考虑增值税外,不考虑其它如所得税、营业税等5.3.6.2.5汇率为估计时的年汇率5.4.6.3LCC估计结果记入《LCC分析报告》。
5.3.7LCC估计结果分析5.3.7.1应尽量使用图表显示LCC分析结果,例如:5.3.7.1.1各种方案下的LCC比较5.3.7.1.2LCC中各成本的比例或总额比较5.3.7.1.3本公司支付的成本和顾客支付的成本比较5.3.7.2LCC分析结果记入《LCC分析报告》。
5.3.8LCC报告、评审和应用5.3.8.1《LCC分析报告》应得到总工程师的确认。
RAMS与LCC培训资料
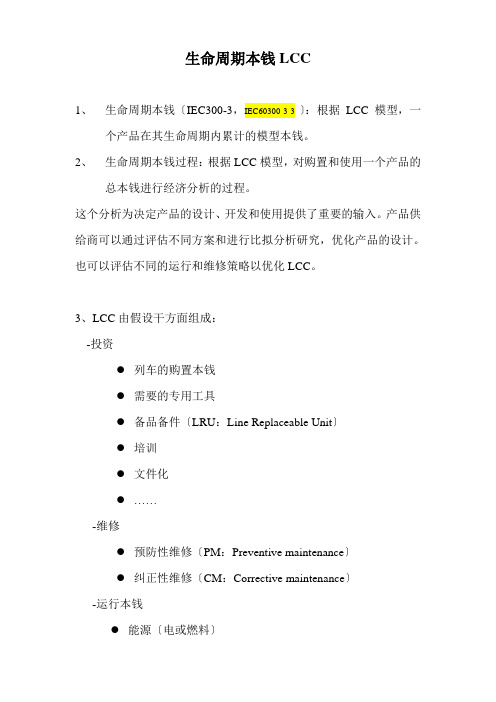
生命周期本钱LCC1、生命周期本钱〔IEC300-3,IEC60300-3-3 〕:根据LCC模型,一个产品在其生命周期内累计的模型本钱。
2、生命周期本钱过程:根据LCC模型,对购置和使用一个产品的总本钱进行经济分析的过程。
这个分析为决定产品的设计、开发和使用提供了重要的输入。
产品供给商可以通过评估不同方案和进行比拟分析研究,优化产品的设计。
也可以评估不同的运行和维修策略以优化LCC。
3、LCC由假设干方面组成:-投资●列车的购置本钱●需要的专用工具●备品备件〔LRU:Line Replaceable Unit〕●培训●文件化●……-维修●预防性维修〔PM:Preventive maintenance〕●纠正性维修〔CM:Corrective maintenance〕-运行本钱●能源〔电或燃料〕●轨道的使用〔*〕●运行人员〔*〕-生命结束本钱●处置本钱〔*〕注:〔*〕- 这些工程一般不包括在LCC的合同中。
3、LCC的作用:-投标-比拟不同的方案-工程控制-本钱预测-……可靠性Reliability1、定义〔IEC50 191-02-06〕可靠性指的是一个部件履行要求的功能的能力:-在给定的条件下和-在给定的时间内。
2、测量方法1)R(t), 可靠性概率: 一个部件在给定条件下、在给定的时间间隔内能够履行要求的功能的概率。
当= 常数时,t 可以是以下任何一种参数:-时间(日历时间, 车辆运行时间, 部件运行时间, 旅行时间)-运行的距离-工作循环或类似的.2) 故障概率F(t) = 1-R(t)3) 故障概率密度f(t) = d F(t) / d t4) 故障率= f(t) / R(t)当故障率为常数时, 即不随时间和行程变化时,= 1/MTTF, 对于不可修复部件;= 1/MTBF, 对于可修复部件;= 1/MDBF, 通常是对车辆.这里, MTTF: Mean Time To Failure到故障的平均时间MTBF: Mean Time Between Failures故障间的平均时间(指运行时间)MDBF: Mean Distance Between Failures故障间的平均行程注意: 一般情况下, 是随时间变化的, 譬如在运行初期和末期故障率都会比拟高(浴盆曲线).MDBF是经常被作为标准使用的.MDBF = 在一段时间里的运行行程/ 这段时间总的故障次数3、故障分类(EN 50 126)1)特大故障(Significant, Immobilizing Failure)具有以下特征的故障:-产生危害和/或-列车无法移动或者导致效劳延迟大于某一规定时间和/或引起本钱高于某一规定水平.2)大故障(Major, Service Failure)具有以下特征的故障:-系统必须调整以到达规定的性能, 并且-不满足特大故障的条件.3)小故障(Minor)具有以下特征的故障:-不阻止系统到达规定的性能, 并且-不满足大故障或特大故障的条件.可靠性确定的例题:5辆机车在24个月内的故障情况如下表. 所有机车每月的行程为20 Tkm. 故障之后立即被修理好并返回到运行. 要求确定机车的MDBF. (24个月平均; 前12个月平均; 后12个月平均)1. 用全部24个月数据:MDBF = 5*480 / 20 = 120 Tkm故障率= 1/MDBF = 0.83 次/ 100 Tkm2. 用前12个月数据:MDBF = 5*240 / 14 = 85.7 Tkm故障率= 1/MDBF = 1.17 次/ 100 Tkm3. 用后12个月数据:MDBF = 5*240 / 6 = 200 Tkm故障率= 1/MDBF = 0.5 次/ 100 Tkm4. 每辆机车的MDBF, 故障率= ?5. 行程-累计故障次数曲线6. M(d)程序有效性Availability1. 定义(IEC50 191-02-05)一个部件在履行要求功能的状态的能力-在给定的条件下-在给定的时间内或在给定的时间间隔内-假定要求的外部资源已被提供.2. 有效性的测量A = 有效时间up time / (有效时间up time +无效时间down time)= up time / 总的时间total time= 1 - down time / total time有效时间up time: 部件在有效状态的时间间隔无效时间down time: 部件在无效状态的时间间隔1)固有有效性inherent availability (Ai)Ai = 纠正性维修时间/ 总的时间= MTBF / (MTBF + MTTR)MTBF: Mean Time Between Failure平均故障时间MTTR: Mean Time To Restoration 平均恢复时间纠正性维修时间corrective maintenance time (主动维修时间active maintenance time):-故障定位时间-零件更换时间(包括进入到更换位置)-修完后的复查时间但不包括: 效劳时间, 路途时间, 休息时间和作决定的时间.2)技术有效性technical availability (At)At = (纠正性维修时间+ 预防性维修时间) / 总的时间预防性维修时间Preventive maintenance time:-维修方案中包括的平安措施和工作准备时间-纯维修时间-修完后的复查时间但不包括: 效劳时间, 路途时间, 休息时间和作决定的时间.作为一个规那么, 预防性和纠正性维修时间不包括在维修工场中修理, 大修或重新调试被更换零件的时间, 因为这不会影响到车辆的有效性. 但是如果被换下的零件修好后要被重新安装在原车辆中, 这个时间要被计入作为计算有效性.4)运行有效性Operational availability (Ao)除纠正性, 预防性维修时间之外, 还将物流和管理性延迟时间也计入无效时间.5)车辆有效性Fleet availability (Afleet)Afleet = 可运行的车辆数/ (可运行的车辆数+ 现在维修的车辆数)=可运行的车辆数/ 总的车辆数专用非有效性(special unavailability):由于纠正性维修而不有效的车辆数/ 总的车辆数一般, Ai, At, 专用非有效性会在合同中用到.例题:车辆每天运行18h (一年按365天计). 每年纠正性维修的时间为100h, 预防性维修的时间是200h. 请计算Ai, At.1.时间按h计算.2. 时间按天计算, 每天按24小时计.3. 时间按天计算, 每天按8小时工作时间计.1. Ai = (18*365-100)/(18*365)=0.98484. 如何改良车辆的有效性-改良可靠性-在适宜时加大维修间隔-减少维修时间(用尽可能多的有用的工人人数, 用优化的程序)-改善可维修性(maintainability): 快速故障探测, 易进入, 很好诊断, 对更换频繁的部件很容易进入, 更换时不需重工或调整等)-将维修活动放在运行不太繁忙的时间里-将维修时间换到车辆不运行时.可维修性Maintainability1.定义(IEC50 191-02-07)一个部件的能力:-在给定的使用条件下-被维持在-或被恢复到-一个它能履行要求的功能的状态-当在给定的条件和使用规定的程序和资源执行维修时.MTTR: Mean Time To Restoration平均恢复时间恢复时间具有统计分布特性, 一般用对数正态分布来表示.恢复Restoration: 通过更换缺陷件(LRU: Line Replaceable Unit在线可更换件)将车辆恢复到正常运行状态. 缺陷件随后在维修工场被修理.3. 恢复时间Restoration time, 主动维修时间Active maintenance time, 可维修性Maintainability可维修性可以被描述为在规定的维修和运行条件下易于效劳程度和易修理程度的特性.其主要特点是:-可进入性(accessibility)-可测试性(testability)-可更换性(exchangeability)可进入性(accessibility): 要测量部件的特性或进行维修, 部件必须容易进入(人员和工具的空间, 尽可能少地移出其它部件).可测试性(testability): 故障之后要进行的检查要使用简单的, 不相互矛盾的测试(故障识别和定位, 即诊断的准确性).可更换性(exchangeability):故障发生后, 有缺陷的部件要用储存的备件去更换, 要没有调整和其它形式的重工.可测试性(testability): 更换缺陷部件后, 需要用另一个简单的测试去检查故障是否已被消除.因此, 可以用3个时间之和(故障定位, 更换, 复核)来表示检查和修理过程, 称为〞主动维修时间〞(Active maintenance time). 效劳时间(可进入性)也被计入主动维修时间.主动维修时间:-故障定位时间, 包括进入-缺陷部件更换时间-复核时间主动维修时间也就是恢复时间, 具有统计分布特性, 一般用对数正态分布来表示. 其平均值就是MTTR(平均恢复时间) –可维修性的量测方法.4. 可维修性和维修(Maintainability & Maintenance)维修Maintenance: 所有技术性和行政性措施的组合, 包括管理措施, 其目的是维持部件在或将其恢复到能够履行要求的功能的状态.可维修性是一个部件的内在特性, 这个特性是部件制造商的职责.维修是由维修团队应用技能和资源来实施的一种活动, 这是维修者的职责.理想状况: 可维修性和维修应该彼此和谐.不理想: -差的可维修性可以被好的维修补偿掉(但有一定限度)-好的可维修性可以被差的维修所毁掉-内装式零件的好的可维修性可以被差的系统集成所毁掉5. 可维修性的验证5.1 Sample analysis样本分析5.2 Test Restoration恢复测试可从FMEA分析中的故障里随即选取一些做试验.平安性Safety1.定义(IEC 50 126)Freedom from unacceptable risk. 平安性指的是免于不可接受的风险.风险: 故障后果的严重性和故障发生概率的组合.Combination of the severity of a failure consequence and the probability of occurrence of the failure.根据有害事件发生的严重性和其频率, 风险的水平可以分为: (IEC 50 126)-不可接受的Unacceptable-不希望的Undesirable-可忍受的Tolerable-可忽略的Negligible有害事件发生的频率风险水平有害事件发生的严重度低---------------------------------------------------------高风险会与以下因素相关:-乘客-运行和管理人员-铁路系统之外的人员(行人, 汽车司机)-维修人员-环境-铁路系统或子系统本身最根本的平安特性:-出轨-刹车和牵引力的控制-门的控制-结构损坏-碰撞(同其它车辆或铁路系统之外的东西)-防火-触电平安性不仅是一个技术问题, 也是一个运行和维修的平安程序问题. 实际上, 大局部平安问题是由于人员的错误或失误引起的.铁路系统的平安性目标是聚焦在事故预防(Error proof), 而不是减轻事故的后果.3. 平安性的量测有害故障率(Hazarduous Failure Rate)预防性和纠正性维修Preventive & Corrective Maintenance1.定义(IEC50)维修: 所有技术性和行政性措施的组合, 包括管理措施, 其目的是维持部件在或将其恢复到能够履行要求的功能的状态.纠正性维修: 故障之后所实施的维修, 目的是将部件恢复到其能履行要求的功能的状态.预防性维修: 按照预先确定的间隔或根据预先定义的准那么实施维修, 其目的是降低故障发生或部件功能降低的概率.维修费用. 可以有多种形式:-每车每年的维修本钱-每车每km的维修本钱-每座每km的维修本钱维修费用可分为人员本钱(或man.hours)和设备本钱. 维修本钱是LCC的重要组成局部.注意: 维修费用在不同的运行年份可能是不同的, 如大修年份预防性维修费用可能很高; 对老的车辆的纠正性维修本钱可能要远高于初始顶峰故障已经过去的车辆.4. 纠正性维修本钱(CM Cost)的计算是LCC分析中的重要局部.一般, 两阶段维修模型在LCC分析中被用于计算CM Cost:1)故障元件被从储存在仓库里的好的备件替换掉, 以便使车辆可以尽快地工作.2)可修理的元件(LRU)将在修理工场(CWS)中被修理; 对于不可修理的LRU, 损坏的将被处置掉, 同时备件库中增加一个LRU.因此, 对于可修理的LRU, 有两局部进入CM Cost:-更换有缺陷的LRU的人工本钱(可维修性, 主动维修时间的本钱) -在修理工场修好有缺陷的LRU的本钱.对于不可修理的LRU, 下面两局部进入CM Cost:-更换有缺陷的LRU的人工本钱(可维修性, 主动维修时间的本钱)-新的备件的本钱(适用时, 还包括处置有缺陷的LRU的本钱).在LCC模型中, 每个LRU的CM Cost可以用下式计算:CMcost = 故障率*(更换时间*单位时间人工本钱+ 在修理工场修理的本钱包括人员本钱和材料费用)这里: 故障率: 故障次数/百万km,更换时间: Man.hours,单位时间人工本钱: 元/h,在修理工场修理的本钱指的是-对于不可修理的LRU, 新的LRU的价格;-对于可修理的LRU, 修好有缺陷的LRU的价格.因此一个LRU每年的CM Cost为:CMcost,yearly = CMcost * 车辆每年的运行距离(百万km)1.不可修理的LRU. 故障率= 4 / 百万km; 更换时间: 0.75h, 2个人; 单位时间人工本钱: 50元/h; 新的LRU的价格: 480元/个; 车辆每年运行的距离: 0.08 百万km/年. 计算: 该LRU每年的纠正性维修本钱(CM Cost).2. 可修理的LRU. 故障率= / 百万km; 更换时间: 1.5h, 1个人; 单位时间人工本钱: 50元/h; 新的LRU的价格: 2500元/个; 修理费用:估计为新部件价格的15%; 车辆每年运行的距离: 0.3 百万km/年. 计算: 该LRU每年的纠正性维修本钱(CM Cost).注意: 维修的本钱是很难准确确定的. 因为故障的类型是很多的, 尤其是在投标阶段, 很难准确了解故障类型, 修理时间. 相对来说, 更换时间可以比拟准确地确定. 因此, 纠正性维修本钱只能是粗略的.纠正性维修本钱要在实际的运营中加以确认.预防性维修本钱(PM Cost)的计算相对来说, 预防性维修本钱的计算要简单一些. 它是基于时间间隔或行程间隔而安排的维修活动. 如:-周维修-季度维修-年度维修-每5年一次的大修-每15年一次的大修一般来说, 更长时间间隔的维修工程包括了小一些时间间隔的维修工程.平衡性维修Balanced maintenance: 指的是某个维修活动被分为几个小的局部, 每个局部在车辆不太繁忙时被实施.状态维修Condition-based maintenance(CBM): 指的是维修活动根据磨损的准那么来实施. 以此维修策略制订出的预防性维修将更为经济.以可靠性为中心的维修Reliability-centred maintenance(RCM): 它是一种通过本钱/性能的比拟分析为根底的优化的本钱有效性维修系统的技术. 譬如比拟一个维修活动的本钱和无此维修时导致的故障的本钱, 从而决定维修的策略.RCM包括了功能分解, FMECA(Failure Mode Critical Effect Analysis, 故障模式关键影响分析)和决定树, 考虑了不同被选因素的相对重要性, 如平安, 故障类别, 有效性, 与CM相比拟的PM的本钱和CBM 的有效性.例题车辆转向架的季度维修工程如下: (每30 Tkm)单位时间人工本钱: 50元/h.计算: 一个转向架每年的预防性维修本钱(PM Cost).答案:每季度每个预防性维修工程的本钱:目视检查地刷的本钱: 0.25*1*50*2=25元润滑轮轴承的本钱: (0.15*1*50+2)*4=38元目视检查刹车块的本钱: 0.1*1*50*4=20元因此, PMcost, yearly = (25 + 38 +20)*4 = 332元.LCC分析用于设计比拟的例子比拟两种不同设计方案的LCC.第一种方案: 现有的已在运行的情况. 部件由LRU A(1个), LRU B(2个), LRU C(2个), LRU D(1个), LRU E(3个)插接在一起组成. 各种LRU的故障率, 价格见表1. 这些LRU均是可修复的, 其修复本钱均为新的备件的价格的20%.表1:第二种方案: 由于SMD技术的开展, 可以将这些LRU集成成一个LRU X. 据粗略估计, LRU X的价格约为6000元, 故障率大约为20次/(10**6h). LRU X也是可修复的, 其修复本钱初步估计为新的备件的5%.请比拟这两种方案的LCC(仅考虑购置本钱和CM本钱), 以判定新方案(第二种)是否应该研发.部件的整个生命周期在50km/h时为10百万km行程. 各种LRU(A, B, C, D, E, X)的平均故障修复时间均为0.5h, 1人. 单位时间人工本钱为30元/h.第三种情况: 现在新的方案研发出来了, 并在实际中得到了运用. 虽然价格保持在了原来的目标(6000元), 但实际运行说明, 其故障率和故障修复本钱均比预计的要高, 分别到达30次/(10**6h)和新备件价格的8%(即实际的可靠性指标和可维修性指标未能到达预期的水平). 请计算实际研发出来的LRU X的LCC.答案:在整个生命周期里的总的运行时间: 10*10**6 / 50 = 0.2* 10**6 h每次更换故障的LRU的本钱: 0.5*1*30 = 15元第一种情况:CMcost, life cycle, LRU A = 故障率*总的运行时间*(每次更换故障LRU的本钱+ 每次修好故障的LRU的本钱) *部件中LRU A的数目= 6 * 0.2 * (15 + 2500*20%) * 1= 618元.CMcost, life cycle, LRU B = 4.5 * 0.2 * (15 + 750*20%) * 2= 297元. CMcost, life cycle, LRU C = 3 * 0.2 * (15 + 300*20%) * 2= 90元. CMcost, life cycle, LRU D = 5 * 0.2 * (15 + 900*20%) * 1= 195元. CMcost, life cycle, LRU E = 4 * 0.2 * (15 + 550*20%) * 3= 300元.CMcost, life cycle,整个部件= CMcost, life cycle, LRU A + CMcost, life cycle, LRU B + CMcost, life cycle, LRU C + CMcost, life cycle, LRU D + CMcost, life cycle, LRU E = 618 + 297 + 90 + 195 + 300 =1500元.部件的购置本钱=2500*1 + 750*2 + 300*2 + 900*1 + 550*3 = 7150元整个部件的LCC = 7150 + 1500 = 8650 元.第二种情况:整个部件的LCC = 6000*1 + 20*0.2*(15 + 6000*5%)*1 = 6000 + 1260 = 7260 元< 8650元(第一种方案的LCC)因此, 应该研制新的方案.第三种情况:整个部件的LCC = 6000*1 + 30*0.2*(15 + 6000*8%)*1 = 6000 + 2970 = 8970 元> 8650元(第一种方案的LCC) > 7260元(新研制方案预估的LCC)为了准确预测故障情况, 应当使用FMEA或FTA(Fault Tree Analysis,故障树分析)分析, 以尽量降低风险. (在这个例子中是可靠性和可维修性风险).问题讨论:LCC方法的局限性有哪些?RAMS和LCC工作程序1. 作用RAMS/LCC过程的作用有三个:1) 研究故障的后果以及它们对用在风险评估中有害和其它不希望事件的影响, 以确定减少风险的措施;2) 以我们产品的可靠性性能和可维修性性能为根底计算在确定的产品生命周期内维修(纠正性维修和预防性维修)的本钱.3) 用来检查在这个领域客户的要求是否被满足, 以及用于确认要求的/同意的可靠性数值, 修复时间和维修本钱.2. 过程,3. 定义和公式(略)4. 变更EHD负责设计和验证/确认过程的变更对RAMS/LCC的影响将被检查, 并就以下方面进行评估:-针对内部和外部危害的防护●机械进入●电气进入●过热●过压●火和烟●环境损害-故障识别●指示●故障信息-功能部件的变更●供给商●型式●备件价格-变更(设计, 零件)对可维修性的影响●进入●可互换性●修复的时间检查和评估的结果必须被记录在〞图纸修改通知〞上.如果有影响, 相关的RAMS文件必须被更新, 必要的措施必须被方案并实施.。
(CAMELLIA)RAMS控制程序
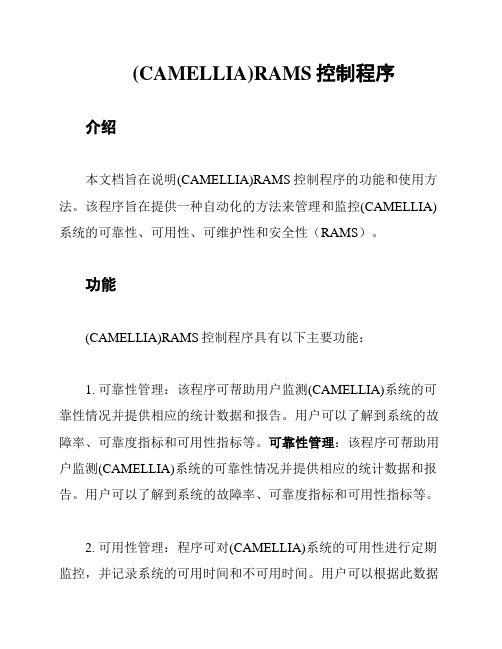
(CAMELLIA)RAMS控制程序介绍本文档旨在说明(CAMELLIA)RAMS控制程序的功能和使用方法。
该程序旨在提供一种自动化的方法来管理和监控(CAMELLIA)系统的可靠性、可用性、可维护性和安全性(RAMS)。
功能(CAMELLIA)RAMS控制程序具有以下主要功能:1. 可靠性管理:该程序可帮助用户监测(CAMELLIA)系统的可靠性情况并提供相应的统计数据和报告。
用户可以了解到系统的故障率、可靠度指标和可用性指标等。
可靠性管理:该程序可帮助用户监测(CAMELLIA)系统的可靠性情况并提供相应的统计数据和报告。
用户可以了解到系统的故障率、可靠度指标和可用性指标等。
2. 可用性管理:程序可对(CAMELLIA)系统的可用性进行定期监控,并记录系统的可用时间和不可用时间。
用户可以根据此数据评估系统的可用性水平,并作出相应的改进措施。
可用性管理:程序可对(CAMELLIA)系统的可用性进行定期监控,并记录系统的可用时间和不可用时间。
用户可以根据此数据评估系统的可用性水平,并作出相应的改进措施。
3. 可维护性管理:程序可追踪和记录(CAMELLIA)系统的维护工作,包括计划维护和应急维护。
用户可以根据维护记录进行维护工作的安排和评估。
可维护性管理:程序可追踪和记录(CAMELLIA)系统的维护工作,包括计划维护和应急维护。
用户可以根据维护记录进行维护工作的安排和评估。
4. 安全性管理:程序可监控(CAMELLIA)系统的安全性,并记录安全事件和漏洞。
用户可以根据记录的数据来评估系统的安全性,并采取相应的安全措施。
安全性管理:程序可监控(CAMELLIA)系统的安全性,并记录安全事件和漏洞。
用户可以根据记录的数据来评估系统的安全性,并采取相应的安全措施。
使用方法安装步骤2. 打开安装包,按照提示完成安装过程。
3. 安装完成后,将程序图标添加到桌面或开始菜单,以便方便启动程序。
配置设置在首次运行程序之前,需要进行以下配置设置:1. 打开程序,进入配置页面。
LCC管理控制程序

LCC管理控制程序————————————————————————————————作者:————————————————————————————————日期:Q/SFC 南车四方车辆有限公司企业标准Q/SFCG04-29-2013LCC管理控制程序2013-08-30 发布2013- 08-30 实施南车四方车辆有限公司发布前言本标准由产品开发部提出。
本标准由产品开发部负责起草。
本标准主要起草人:朱林。
本标准审核人:王晓峰。
本标准批准人:夏春生。
本标准由产品开发部归口并负责解释。
本标准于2012年07月首次发布。
2013年07月第一次修订。
修订说明:1.3.1条款更改寿命周期的概念。
2.文件中所有“寿命周期成本”统一为“寿命周期费用”。
3.3.2条款改为“是指产品从开始酝酿,经过论证、研究、设计、生产、使用一直到最后报废的整个寿命周期内所耗费的研究开发设计费用、生产费用、使用和保障费用及最后废弃处理费用的总和。
对用户来说,则是指在系统的整个寿命周期内,为获取并维持系统的运营(包括处置)所花费的总费用”。
4.3.3条款改为“产品在寿命周期内或其中一部分的(比较各种方案时,可能只分析产品生命周期中的某个阶段)寿命周期内进行费用评估的经济分析过程”。
5.增加了5.1.3条款在LCC分析前,应确定有关的限制条件、假设。
6.原文中5.1.3条款及以下的条款号向下顺延,原5.1.3 条款“LCC工作小组负责确定LCC构成,按照产品具体结构及其他相关因素确定LCC分析模型,并发送财务部。
费用分解结构可根据顾客合同进行相应剪裁”改为“LCC工作小组负责确定LCC 构成,按照产品具体结构及其他相关因素确定LCC分析模型,并发送财务部。
费用分解结构可根据顾客合同进行相应剪裁。
通常顾客仅关心购置费、使用能耗费用、保障费用等,并不关心研发费、试验费等,因此提供给顾客的LCC一般按附件二的内容进行统计、计算”。
7.增加了“附件二 LCC结构图”,原附件序号向下顺延。
RAMSLCC介绍

RAMS L设C计C 质量
15
16
8
二、RAMS/LCC的意义
RAMS好,质量就好,那么质量意味着……
市场? 形象?
成本?
17
18
9
19
20
10
1 : 10 : 100 规则
1
10
100
如果未进行预防活动,那么流到下一个阶段发生的损失费用会更大. 如果在工程上检出到不良时,所损失的费用只有1USD 在顾客处发现时损失的费用会增加到10USD 最终顾客消费者处发生不良时其损失费用会上升到 100USD.
》 当前产品的可靠性水平是多少 ? 新产品的可靠性水平 又是多少?
》 对于一个未来的新产品,每年需要多少人力和资金来 处理突发故障?
》 故障处理是否有预定的流程,按流程走了吗?闭环率 是多少?
33
二、RAMS/LCC的意义
》 产品在设计评审阶段能控制风险吗?依靠“人”的因 素来控制还是依靠“程序”控制?
关键件重要件清单 工艺质量控制计划 产品验证试验计划
产品维护/修手册 产品备件清单
以后,我们该这样回答…
提出RAMS要求 RAMS协同设计 RAMS要求验证
产品设计方案 强度分析 疲劳分析 工艺分析
RAMS
可靠性分析 设计 FMECA 工艺 FMEA
RCMA 维修任务分析 保障资源分析
29
关键件重要件清单 产品验证试验计划 工艺质量控制计划 产品维护/修手册
21
第1部分 引言 (三)解决途径
22
11
23
24
12
二、RAMS/LCC的意义
RAMS/LCC
RAMS
LCC
RAMS控制程序

5.3 RAMS的计划与管理
5.3.1 在RAMS的计划与开发、质保、制造、采
购等部门成员。
5.3.2 由RAMS工作小组应建立产品的《RAMS保证计划
》说明如何计划、管理及监控在其服务范围内的整体系
统的RAMS要求,确保能有效地在设计、开发、生产、试
5 作业流程
责任部门
业务流程
控制要点
记录/备注
技术开发部
RAMS要求 识别
5.1 RAMS要求的识别 5.1.1 在与顾客达成供货协议之前,技术开发部应尽可 能全面识别产品的RAMS要求,获取产品图纸和产品规格 等信息。 5.1.2 用以识别RAMS所需的信息(包括但不限于): 5.1.2.1 产品功能、性能要求、与其它产品的相互关系 和接口。 5.1.2.2 有关法律法规和行业要求,如产品标准、行业 安全政策等。 5.1.2.3 产品运行的环境条件(如高温、高腐蚀、水 下)、地理条件(如风沙、地震、多雨雪等)、以及产 品的运行策略(如每天运行小时数、每年运行天数)。 5.1.2.4 产品维护条件、后勤保障条件、维护策略(如 维护周期等)。
5.3.2.4 详述RAMS保证任务、安全分析方法及证明系统
安全方法,及能达到可靠性、可用性及可维护性目标的
方法。
5.3.2.5 RAMS保证任务及递交文件的时间表。
5.3.2.6 内部审核方案。
技术开发部 质保部 采购员
RAMS 要求实施
5.4 RAMS要求的实施
5.4.1 RAMS设计原则:在设计过程中,充分利用RAMS 《FMECA》
有关的设计准则,如模块化、通用性、互换性、冗余设 《隐患登记
计等,并综合考虑与新技术、新工艺以及LCC之间的平 册/初步危害
- 1、下载文档前请自行甄别文档内容的完整性,平台不提供额外的编辑、内容补充、找答案等附加服务。
- 2、"仅部分预览"的文档,不可在线预览部分如存在完整性等问题,可反馈申请退款(可完整预览的文档不适用该条件!)。
- 3、如文档侵犯您的权益,请联系客服反馈,我们会尽快为您处理(人工客服工作时间:9:00-18:30)。
RAMS 及LCC 控制程序
1. 目的
产品在生命周期内,通过执行的一系列活动以确保在每个阶段完成为产品确定的RAMS要求,并符合和满足顾客提出的 RAM目标。
2. 范围
本程序适用于公司产品论证开始到质保期,延伸到产品使用维护期间的相关跟踪活动结束。
3. 定义
3.1RAMS可靠性、可用性、可维修性和安全性的统称。
3.1.1 可靠性: 产品在规定条件下和规定时间内,完成(或保持)规定功能的能力。
3.1.2 可用性 : 产品在任一随即时刻需要和开始执行任务时,处于可工作或可使用状态的程度。
简单的说:可用性就是产品处于可工作状态的可能性。
3.1.3 可维修性 : 在规定的条件下和规定的时间内,按规定的程序和方法进行维修时,保持或恢复到规定状态的能力。
3.1.4 安全性 :不发生危险事件的能力。
3.1.5 产品生命周期 : 从产品的初始概念阶段一直到产品停用和处置的整个阶段。
3.1.6 系统的寿命周期费用(LCC): 在系统的整个寿命周期内,为获取并维持系统运营(包括处置)所花费的总费用。
3.1.7不良品质成本:简称COPQ指因产品不良产生的并由本公司承担的成本,包括内部损失成本和外部损失成本,不包括在品质成本统计中所提到的鉴定成本、预防成本、外部品质成本等,也不考虑现行会计制度之外的其它隐性损失,如品牌损失、名誉损失等。
4. 职责和权限
4.1总工程师负责组织 RAMS评审工作;
4.2 销售部负责本程序运行过程中与用户的联系和协调;
4.3 质量控制部负责本程序运行过程中的质量管理、质量评审工作 , 负责产品安全事例的管理、建立、更新工作;
4.4研发部负责具体产品RAMS程序策划、建立工作及相关文件的编制、更
改工作。
4.5财务部负责商业风险分析工作。
5. 控制程序
5.1研发部确定产品RAMS应收集的资料,销售部和质量控制部负责在产品生命周期内收集相关数据和信息,收集的信息交研发部,该信息用作RAMS分析活动的输入内容。
5.2RAMS/LCC程序见表5-1 :《RAMS/LC(程序表》
RAMS/LCC 程序表表5-1
5.3 LCC控制程序
531建立项目编号
对于新产品或新项目,项目经理应在项目策划阶段建立项目编号,以便对 LCC进行统计分析。
5.3.2分析时机
1)对于新产品或新项目,在策划论证阶段分析
2)对于单个生命周期阶段的LCC分析,则在对该阶段方案(例如使用方案或者维护方案等)进行论证时
5.3.3分析目的和范围
5.3.3.1 LCC分析主要有以下三个目的:
5.3.3.1.1 评估产品LCC总量
5.3.3.1.2 确定LCC的主要成分评估
5.3.3.1.3各种设计、生产、使用、维护、报废处置等方案
5.3.3.2出于以上目的,LCC的分析范围主要有以下两种情况:
5.3.3.2.1 一般情况下,分析范围是产品整个生命周期
5.3.3.2.2出于比较各种方案时,可能只分析产品生命周期中的某个阶段5.3.4
确定限制条件和假设
在LCC分析前,应确定有关的限制、假设,例如:
产品使用环境、维护条件等产品规格性能要求产品的RAMS要求,如 MTBF
要求等
资金限制、价格限制等
535确定LCC吉构
可参照表5-2来确定LCC吉构:
5-2
536 LCC估计
536.1 小组应根据确定的LCC成本结构,从上述的各种可能的信息来源收集信息,用于估计LCC此外,以往对类似产品的 LCC分析和监控结果也可用于LCC估计。
536.2 依据LCC成本结构估计的所有成本汇总在一起就是产品的LCC 成本。
汇总时应使用以下计算假设:
5.3.
6.2.1以估计当日为基准日,折算为单位产品的净现值
53622 不考虑通货膨胀率
53623 利率为10%
53624 除了应考虑增值税外,不考虑其它如所得税、营业税等
5.3.
6.2.5 汇率为估计时的年汇率
5.4.
6.3LCC估计结果记入《LCC分析报告》。
5.3.7 LCC 估计结果分析
5.3.7.1应尽量使用图表显示LCC分析结果,例如:
537.1.1 各种方案下的LCC比较
5.3.7.1.2LCC 中各成本的比例或总额比较
5.3.7.1.3 本公司支付的成本和顾客支付的成本比较
5.3.7.2 LCC分析结果记入《LCC分析报告》。
5.3.8 LCC 报告、评审和应用
5.3.8.1《LCC分析报告》应得到总工程师的确认。
538.2 确认后的《LCC分析报告》应该在产品及工艺设计中阶段评审,以评选方案或确定采取其它措施,如修改设计方案、工序设计方案、产品使用方案等,以取得LCC和产品性能要求、RAMS要求之前的平衡。
5.3.8.2修改方案后,应组织再次进行LCC估计、分析、报告和评审,直到得到满意结果或主动终止该项目。
5.3.9 LCC 监控
5.3.9.1 随产品的实际进展,在后续的产品设计、工序开发、生产制造阶段可以不断地获得实际成本数据。
各阶段的LCC分析责任人应统计这些实际成本,提交项目小组进行讨论、分析,并更新《LCC分析报告》。
5.3.9.2 当进入使用、维护、报废和处置阶段,包括质保期内和质保期后
的阶段,负责与该顾客联系的人员应从顾客抱怨信息和售后服务活动中了解可能发生的变化,统计和监控这些成本,提交项目小组进行讨论、分析,并更新
《LCC分析报告》。
5.3.9.3 这些分析和监控活动包括:
5.3.9.3.1与LCC估计结果进行比较,检查所确定的成本结构是否合理,成本估计是否准确等
53932与以往LCC监控结果进行比较,检查成本实际结构是否发生重大变化
5.3.9.3.3 寻找产品设计、生产制造、使用维护等方案的改进机会,并提供建议
5.3.10 LCC 更新
除
依照535 536 中的对分析进行外,在工程前,各析责应组拟变方案LCC估较,并程变监控新分析告》。
了应本
文和
早节规
定
《LCC
报告》更
新实施
变更
LCC分任
人织对
更的进
行计、比
在工更
后,并更
《LCC
报
5.3.11不良品质成本COPQ
5.3.11.1 COPQ 数据来源
5311.2 COPQ统计、分析、改善和报告
531121统计:由质量控制部在每月上旬,使用《COPQ^计分析表》统计上月所发生的COPQ并记录造成不良的原因、责任和改善措施。
5.3.11.2.2分析:由质量控制部每月对 COP奄计结果进行分析,包括年趋势图和最近连续12个月的月趋势图(内部损失成本、外部损失成本、总COPQ 等。
5.3.11.2.3 改善:质量控制部应确保所有COPQ5目均有原因分析和改善措施,尤其是成本大幅上升或连续上升、目标无法实现等情况下。
5.3.11.2.4报告:质量控制部应在COP①析完成后,报告给制造部经理、质量控制部经理等。
不良品质成本统计分析应在管理评审会议中进行评审。
6. 支持性文件
6.1《新产品研发及项目管理程序》
6.2《记录控制程序》
6.3《知识管理控制程序》
7. 记录
7.1《项目建议书》--《新产品研发及项目管理控制程序》
7.2《项目登记表》--《新产品研发及项目管理控制程序》
7.3《设计和开发评审记录表》--《新产品研发及项目管理控制程序》
7.4《可靠性、可用性及可维护性(RAMS分析》
7.5《预防性维护分析》
7.6《MTBF预测》
7.7《纠正性维护分析及MTTF预测》
7.8《故障模式影响及危害性分析表分析》
7.9《风险矩阵》
7.10《关键件安全性符合表》
7.11《备品备件清单》一《备品备件管理办法》
7.12《专用工具清单》
7.13《测试报告》一引用《真空断路器出厂试验记录》
7.14《产品全寿命周期维护费用分析报告》7.15《COP奄计分析表》
RAM保证计划.doc。