品质管理-PE培训资料-8D手法(PPT 80页)
合集下载
品质管理8D实战案例培训资料8D实施方法PPT78页

5
了解問題
1、成立小組
2.清楚 描述問題
3.执行和确认 临时措施
识別可能原因
选择最有可能 的原因
5、确定及 验证纠正措施
6、执行永久 纠正措施
最有可能的原因 是否是根本原因
7、避免再发生
识別可能的 解决方案
8、恭贺小組
6
1D (Use Team Approach )—— 成立小组
小组成员具备工艺/产品的知识,有配给的时间并授予了权限 ,同时应具有所要求的能解决问题和实施纠正措施的技术素质。 小组必须有一个指导和小组长。
31
D6、验证纠正措施
1. 换完电线后,至今尚没有发现连接点松动的迹象。 2. 断开电流接触器的电路进行试验,一旦电压不正常,转子 将自动停止工作,直至没电镀的产品从线上取下。 以上工作,小组共同进行了验证,并提请顾客事先的批准。
32
D7、防止再发生的措施
❖电镀工作指导书被修改增加了如下内容: 1)当生产线不正常停止时,操作者不仅要挑选出缺陷产品 ,而且要在工作记录记下数量及当班QC的名字。 2)在电镀线在每天早上启动前,电流接触器的连接点和电 线必须检查。以上,由杨星在12月15日完成。 ❖开发一个包括每天需检查事项的检查清单,例如生产线停 止,不管缺陷产品是否被挑选,制造部和QA需进行审核。 ❖ 依次类推,如果有类似问题,该小组负责纠正并采取适 当的预防措施。
4
何謂8D
• 此方式須通过“8D 报告”。 • 所谓“八个步骤”,其每个步骤意义及其流程请参
阅附图.该图虽已列出解决问题的各个步骤,但各 个步骤的先后順序可视问题的困难度及复杂程度 而异,不必拘泥于图示順序.且问题解决经过应有书 面记录. • 如:某一问题发生及团队组成时,可能制造人员已 经先行采取临时对策,惟其永久解决方案,则可能尚 需小组人员的共同参与,经多方研讨后才能产生。
了解問題
1、成立小組
2.清楚 描述問題
3.执行和确认 临时措施
识別可能原因
选择最有可能 的原因
5、确定及 验证纠正措施
6、执行永久 纠正措施
最有可能的原因 是否是根本原因
7、避免再发生
识別可能的 解决方案
8、恭贺小組
6
1D (Use Team Approach )—— 成立小组
小组成员具备工艺/产品的知识,有配给的时间并授予了权限 ,同时应具有所要求的能解决问题和实施纠正措施的技术素质。 小组必须有一个指导和小组长。
31
D6、验证纠正措施
1. 换完电线后,至今尚没有发现连接点松动的迹象。 2. 断开电流接触器的电路进行试验,一旦电压不正常,转子 将自动停止工作,直至没电镀的产品从线上取下。 以上工作,小组共同进行了验证,并提请顾客事先的批准。
32
D7、防止再发生的措施
❖电镀工作指导书被修改增加了如下内容: 1)当生产线不正常停止时,操作者不仅要挑选出缺陷产品 ,而且要在工作记录记下数量及当班QC的名字。 2)在电镀线在每天早上启动前,电流接触器的连接点和电 线必须检查。以上,由杨星在12月15日完成。 ❖开发一个包括每天需检查事项的检查清单,例如生产线停 止,不管缺陷产品是否被挑选,制造部和QA需进行审核。 ❖ 依次类推,如果有类似问题,该小组负责纠正并采取适 当的预防措施。
4
何謂8D
• 此方式須通过“8D 报告”。 • 所谓“八个步骤”,其每个步骤意义及其流程请参
阅附图.该图虽已列出解决问题的各个步骤,但各 个步骤的先后順序可视问题的困难度及复杂程度 而异,不必拘泥于图示順序.且问题解决经过应有书 面记录. • 如:某一问题发生及团队组成时,可能制造人员已 经先行采取临时对策,惟其永久解决方案,则可能尚 需小组人员的共同参与,经多方研讨后才能产生。
8D培训教材课件
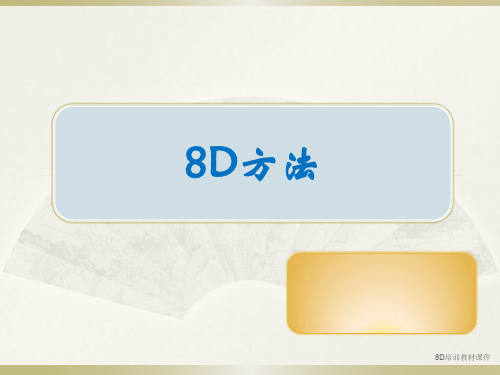
1、要求仓库人员,及时对库存产品进行隔离;
2、要求组装部进行返工;
3、品质SQC封箱前检查,要保证每箱都确认才能出货。
38
8D培训教材课件
2 8D实施步骤
D5 选择和验证永久对策
用确定的词语来描述措施的效果,例如:
× ×月× ×部件淘汰率降低到300DPPM 从×月×日到×月×日× ×显卡共使用300块,无1块花屏故障
验证措施有效性时需注意:
A、所观测样本大小是否足以说明问题? B、跟踪周期是否充分、适宜? C、是否因措施的实施发生了新的问题?
现场QC抽检不严格 出现不良品流出
√
……Байду номын сангаас
……
注:“√”表原因确认保留,“×”表原因剔除
28
8D培训教材课件
D4 定义和验证根本原因
拟定执行暂时对策
中兴客诉
问题
可能原因
原因确认
P825F10 后壳耳机 孔装饰片 热熔后为 什么会发 生脱落/ 松动?
热压治具 热熔设定 温度太高
热熔柱高 度不够
加工中操 作不正确
Who: (中兴福盛驻厂) Where: Complained By
How many:
当日上线500PCS. 脱落不良率1%, 松动不良率约3%
How much:
2013-05-22
中兴客户组装厂 龙岗福盛电子产
线
停线2H*2万元
17
8D培训教材课件
2 8D实施步骤
D3 临时控制措施
18
8D培训教材课件
制定新的SOP,将保压时间由原来2S 调整到3S
更新SIP,加严抽检标准和允收水准 对所有QC进行培训宣导,制作不良看板
8D培训经典教材ppt课件
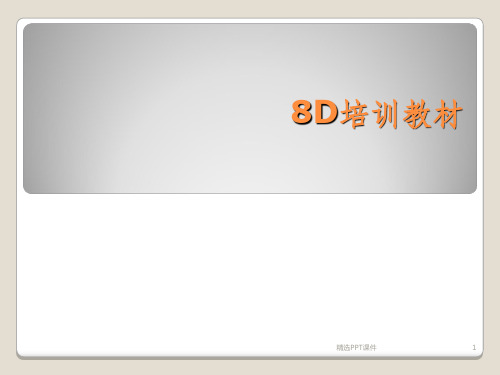
小组的领导: 谁来推动?
小组的资源: 谁提供支持?
小组的成员: 合作及分工?
人员的数量: 多少为宜?
精选PPT课件
10
D1—四成.立8工D步作团骤队—D1建立小组
选择小组成员的准则
小组成员的 人数控制在4到 10个之间
选择具有相 应技能、知识、 资源、权力等 的人作为团队 成员
各类成员之 间职责、任务 合理搭配
需要考虑的问题:
1.列可能 原因时要 周全。
2. 原因和结 果要有论证, 说得通。
3.原因一定是根本 原因,而非表面
原因。
精选PPT课件
21
四. 8D步骤—D4原因分析
头脑风 暴:
列出所 有可能 的疑点
进一步明确问题
(不良解析)
从流程分析
(流程图)
质量问题5M1E分析
(鱼骨图分析)
各个可疑原因排查
对现场人机料环法
测进行观察测量,
有历史数据的对数据
疑
进行初步分析
点
验
证
关键原因确认
统计分析
DOE验证
关键原因-是否为根本原因
5-WHY分析
精选PPT课件
22
四. 8D步骤—D4原因分析
头脑风暴法
头脑风暴法规则:
– 快速思考,轮流发言,暂时没有想法 可跳过此轮。
– 数量重于质量,所有想法都记录下来。
何时 采用 8D
精选PPT课件
7
0 问题初步了解
四. 8D步骤
原因分析
4
确定可能原因
5
长期对策
1
建立小组
2
问题描述
3
临时对策
选择最可能原因
8D 培训资料精品PPT课件
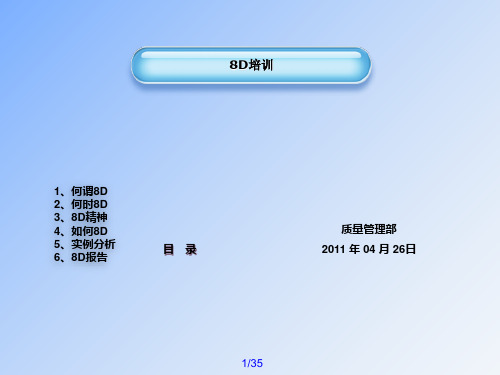
3.收集所需的输入 过程流程 控制图 拒收单 特采单 相关的过程查核清单和程序
13/35
D3:实施并验证临时措施 目的:为了保护顾客避免受额外的损失 步骤: 1. 隔离并验证临时措施 2.保证连续作业
可以通过增加额外的工序和增加临时人员 来保证 3.迅速采取措施,列出所有急症措施,日期 和有效百分比 4. 验证临时措施
题的解决。
2/35
此方式是团队运作导向以事实 为基础,避免个人主见的介入, 使问题的解决能更具条理。
此方式宜由公司各部门人员的 共同投入,求得创造性及永久 性的解决方案。
3/35
此方式可适用于任何问题,而且能促进相关 目标的各部门间有效的沟通。 此方式须通过“8D 报告”。 此方式可以为从统计过程控制作业,如何走 向品质实际提升之间,提供一项具体的联系。
用5W2H叙述问题 WHO 谁在抱怨? WHAT 什么发生了? WHERE 在何处发生? WHEN 何时发生? WHY 为什么说它是个问题? HOW 如何发生? HOW MUCH 问题有多大?
12/35
2. 回答五个为什么问题 五个为什么为针对一个问题尽量多问为什么,
直到停止在不知道的层极上。 注意:不要假设!
21/35
5. 更新下列内容: 过程FEMA 控制计划 操作或工厂标准作业指导书;过程规范;SPC运用; 服务规范;信息处理程序;实验规范 6.考虑其他产品或服务,类似过程,其他工厂和
目前/将来的发展 7.更新8D报告
22/35
活动的规则 1. 每个人的观点都很重要,不要批评别人 2. 参与,每个人都参加会议 3. 按时开会和闭会 4. 记录整个过程 5. 达成共识后再做决定 包括的文件 小组成员名单 会议日程 会议议程 实施计划 启动8D报告
13/35
D3:实施并验证临时措施 目的:为了保护顾客避免受额外的损失 步骤: 1. 隔离并验证临时措施 2.保证连续作业
可以通过增加额外的工序和增加临时人员 来保证 3.迅速采取措施,列出所有急症措施,日期 和有效百分比 4. 验证临时措施
题的解决。
2/35
此方式是团队运作导向以事实 为基础,避免个人主见的介入, 使问题的解决能更具条理。
此方式宜由公司各部门人员的 共同投入,求得创造性及永久 性的解决方案。
3/35
此方式可适用于任何问题,而且能促进相关 目标的各部门间有效的沟通。 此方式须通过“8D 报告”。 此方式可以为从统计过程控制作业,如何走 向品质实际提升之间,提供一项具体的联系。
用5W2H叙述问题 WHO 谁在抱怨? WHAT 什么发生了? WHERE 在何处发生? WHEN 何时发生? WHY 为什么说它是个问题? HOW 如何发生? HOW MUCH 问题有多大?
12/35
2. 回答五个为什么问题 五个为什么为针对一个问题尽量多问为什么,
直到停止在不知道的层极上。 注意:不要假设!
21/35
5. 更新下列内容: 过程FEMA 控制计划 操作或工厂标准作业指导书;过程规范;SPC运用; 服务规范;信息处理程序;实验规范 6.考虑其他产品或服务,类似过程,其他工厂和
目前/将来的发展 7.更新8D报告
22/35
活动的规则 1. 每个人的观点都很重要,不要批评别人 2. 参与,每个人都参加会议 3. 按时开会和闭会 4. 记录整个过程 5. 达成共识后再做决定 包括的文件 小组成员名单 会议日程 会议议程 实施计划 启动8D报告
8D方法培训资料ppt课件
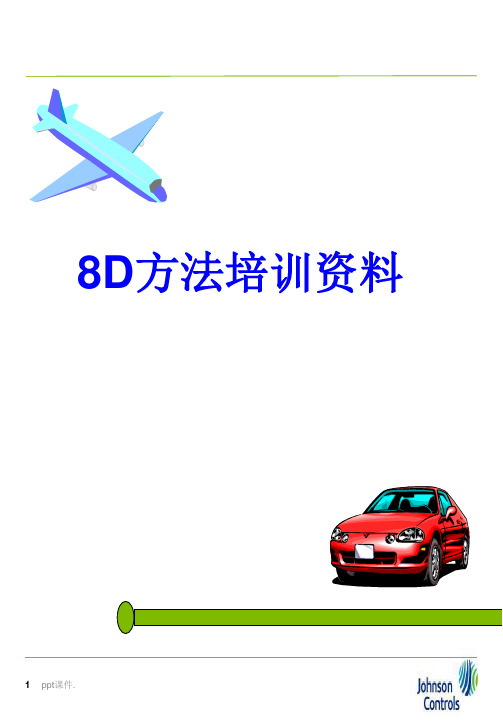
D0 8D前准备过程
D1 确定团队
D2 描述问题 ( 问题是什么?)
( 案例分析)
D3 实施并验证临时性纠正措施
D4 确定和验证问题的根本原因 (问题如何解决?)
D5 选择和验证永久性纠正措施
D6 实施和证实永久性纠正措施
D7 防止问题再次发生 (将来该问题如何预防?)
D8 表扬个人和小组的贡献
3 ppt课件.
8D方法培训资料
1 ppt课件.
8D方法培训的主要内容
8D 概述 8D 课程的目标 8D 对供应商的好处 8D 报告的审核 8D 过程要点 8D 过程介绍
2 ppt课件.
8D 概述
8D过程是福特公司的方法,它将解决问题的努力标准化。 客观地确定、定义和解决问题并防止相似问题的再次发生。 由8个步骤和1个准备步骤组成:
5 ppt课件.
8D 报告的审核
在8D关闭前,确定以下问题已经被回答: 对零件知识/系统有了充分的了解; 完全确定了根本原因,并聚焦于该原因; 逃逸点已经被识别; 确定了与根本原因相匹配的纠正措施; 纠正措施计划的验证已经被确认; 包括了实施纠正措施的时间计划; 有证据显示已把纠正措施纳入了整个系统。
Date Issue Closed/关闭日期: 07.11.19
Champion Title 负责人职位 售后工程师 Title(s) 职位 检验工程师 工艺工程师 高级班长
Champion Phone Number 负责人电话号码 0510-85224694 Phone Number(s) 电话号码 0510-85224607 0510-85224239 0510-85224160
组织并综合一组所需能力人员及必须的资源;
编号:Q0711010 Form: QA-022 Rev: A
D1 确定团队
D2 描述问题 ( 问题是什么?)
( 案例分析)
D3 实施并验证临时性纠正措施
D4 确定和验证问题的根本原因 (问题如何解决?)
D5 选择和验证永久性纠正措施
D6 实施和证实永久性纠正措施
D7 防止问题再次发生 (将来该问题如何预防?)
D8 表扬个人和小组的贡献
3 ppt课件.
8D方法培训资料
1 ppt课件.
8D方法培训的主要内容
8D 概述 8D 课程的目标 8D 对供应商的好处 8D 报告的审核 8D 过程要点 8D 过程介绍
2 ppt课件.
8D 概述
8D过程是福特公司的方法,它将解决问题的努力标准化。 客观地确定、定义和解决问题并防止相似问题的再次发生。 由8个步骤和1个准备步骤组成:
5 ppt课件.
8D 报告的审核
在8D关闭前,确定以下问题已经被回答: 对零件知识/系统有了充分的了解; 完全确定了根本原因,并聚焦于该原因; 逃逸点已经被识别; 确定了与根本原因相匹配的纠正措施; 纠正措施计划的验证已经被确认; 包括了实施纠正措施的时间计划; 有证据显示已把纠正措施纳入了整个系统。
Date Issue Closed/关闭日期: 07.11.19
Champion Title 负责人职位 售后工程师 Title(s) 职位 检验工程师 工艺工程师 高级班长
Champion Phone Number 负责人电话号码 0510-85224694 Phone Number(s) 电话号码 0510-85224607 0510-85224239 0510-85224160
组织并综合一组所需能力人员及必须的资源;
编号:Q0711010 Form: QA-022 Rev: A
8D培训教材 ppt课件

8D简介
QC七大手法
机理分析法
FMEA
统计过程控制
以上4种也是质量工具,后续会有专业的同仁授课,敬请期待~。
8D简介
D5 长期对策
当根本原因找出后,长期对策往往应运而生,但是如何针对性的制定最佳改善对策,以避免问 题再发,仍需要整个团队讨论决议。
值得注意的是一个原因可能有几条措施,同步实施时需要保障解决最根本问题的措施务必被贯 彻落实。
8D简介
D4 根因探究: 寻真因如求医问诊,误诊或诊断不全,后患无穷。 1.不良解析 解析即要求对不良现象的充分了解,包括其历史背景,弄清不良的特性(外观? 性能?)和规格(国标?安全?)。 2.排定可能原因 2.1 如有历史数据,统计分析观察集中性、趋势性。 2.2 与一线员工充分沟通,如有可能现时、现地、现物 2.3 向相关专家咨询请教,推敲问题可能造成的原因 3.验证可疑原因 选用合适的方法找出根本原因
1
装配 合格
150mA
60s
焊穿
B
2
不合格
150mA
50s
合格
A
2
合格
B
1
不合格
在这组实验中,我们优先固定1组参数,另一组取其 上下限进行实验,当两者都超出我们的要求时,选 取中值达到要求。
我们仍可以进行其他组合实验,但实际情况中,我 们总会有一定的倾向,可以缩减排列组合数量。 比如自产能考量,我们会优先选择焊接速度40s不变, 调整焊接电流来达到我们要的结果。
交叉实验法是在已知不合格状态下,通过单因素变动 寻找不良再现。上组实验中A外壳无论搭配内胆1还是2 都是合格状态,但B外壳无论搭配内胆1和2都是不合格 状态,不良嫌疑集中在B外壳。 注意:当实验进行到A+2合格时,并不能完全判定B外
8D培训课件(PPT 42张)
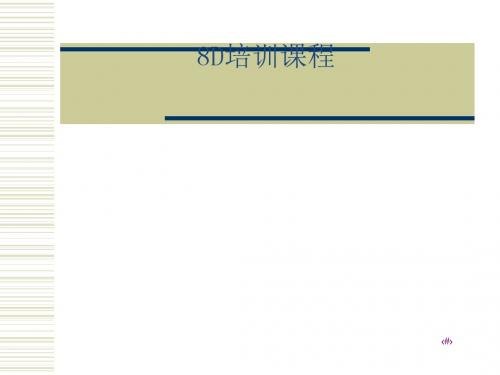
‹#›
‹#› 6
解決根本性問題
丰田员工提出“5个为什么”。要找出问题的根 本原因,必须至少依次提出5个“为什么?”这 就象一层层剥洋葱一样。例如,焊接到膜盒上 的一根毛细管发生了泄漏:
为什么样会泄漏?
焊接密封不好。 在毛细管内有沉积物。 清洗管子时没有清洗掉。
‹#›
‹#› 7
为什么焊接的密封不好?
‹#›
‹#› 5
Root Cause Case 2
地面上有油渍 为什么地面上有油渍 因为A机器漏油 为什么A机器漏油 因为橡胶密封不好 为什么橡胶密封不好 因为密封橡胶质量不好 所以橡胶密封要换,但如果再换不佳的橡胶那么不多久 又要再换了,所以不但要换,而且要换好的橡胶密封。 Deming在上课时一直追问为什么、为什么、为什么,一 直到无法拆解下去,那么才能算为根本原因。
‹#›
‹#› 12
何时采用8D
该方法适用于解决各类可能遇到的简单或复杂 的问题;(但也不是任何事情都需要) 8D方法就是要建立一个体系,让整个团队共享 信息,努力达成目标。 8D本身不提供成功解决问题的方法或途径,但 它是解决问题的一个很有用的工具; 亦适用于过程能力指数低于其应有值时有关问 题的解决; 面对顾客投诉及重大不良时,提供解决问题的 方法。 ‹#›
‹#›
‹#› 4
Root Cause Case 1
有一台汽车故障不能行走 为什么汽车不能行走 因为引擎故障 为什么引擎故障 因为火花塞不点火 为什么火花塞不点火 因为火花塞潮湿沾水 为什么火花塞潮湿沾水 因为引擎盖的密封漏水,以致水进入 所以如果只是把火花塞换了,汽车是可以走了,但是不 用多久火花塞又要潮湿,汽车又要不动了,但如果把密 封也换了,那么火花塞就可以使用寿命比较长了。
‹#› 6
解決根本性問題
丰田员工提出“5个为什么”。要找出问题的根 本原因,必须至少依次提出5个“为什么?”这 就象一层层剥洋葱一样。例如,焊接到膜盒上 的一根毛细管发生了泄漏:
为什么样会泄漏?
焊接密封不好。 在毛细管内有沉积物。 清洗管子时没有清洗掉。
‹#›
‹#› 7
为什么焊接的密封不好?
‹#›
‹#› 5
Root Cause Case 2
地面上有油渍 为什么地面上有油渍 因为A机器漏油 为什么A机器漏油 因为橡胶密封不好 为什么橡胶密封不好 因为密封橡胶质量不好 所以橡胶密封要换,但如果再换不佳的橡胶那么不多久 又要再换了,所以不但要换,而且要换好的橡胶密封。 Deming在上课时一直追问为什么、为什么、为什么,一 直到无法拆解下去,那么才能算为根本原因。
‹#›
‹#› 12
何时采用8D
该方法适用于解决各类可能遇到的简单或复杂 的问题;(但也不是任何事情都需要) 8D方法就是要建立一个体系,让整个团队共享 信息,努力达成目标。 8D本身不提供成功解决问题的方法或途径,但 它是解决问题的一个很有用的工具; 亦适用于过程能力指数低于其应有值时有关问 题的解决; 面对顾客投诉及重大不良时,提供解决问题的 方法。 ‹#›
‹#›
‹#› 4
Root Cause Case 1
有一台汽车故障不能行走 为什么汽车不能行走 因为引擎故障 为什么引擎故障 因为火花塞不点火 为什么火花塞不点火 因为火花塞潮湿沾水 为什么火花塞潮湿沾水 因为引擎盖的密封漏水,以致水进入 所以如果只是把火花塞换了,汽车是可以走了,但是不 用多久火花塞又要潮湿,汽车又要不动了,但如果把密 封也换了,那么火花塞就可以使用寿命比较长了。
品质部培训8D课程PPT培训课件

详细描述:8D方法强调团队协作,各相关部门共同参 与问题解决,加强了部门间的沟通和合作。
总结词:预防措施
详细描述:在汽车行业中,8D方法不仅解决问题,还 注重预防类似问题的再次发生,通过根本原因分析和改 善措施来降低质量风险。
案例二:电子行业中的8D应用
在此添加您的文本17字
总结词:高效解决问题
在此添加您的文本16字
培训者或回答者总结 并重申关键点。
参与者提问,培训者 或指定的回答者回答 问题。
注意事项
确保问题与主题相关,避免偏离主题。
尊重每个参与者的观点,避免争论或 攻击性语言。
THANKS FOR WATCHING
感谢您的观看
和精准度。
05 Q&A环节
总结
01
确保所有参与者都有机会提问和 回答问题,以促进交流和互动。
02
鼓励开放和诚实的对话,以便更 好地理解问题和解决方案。
目的
提供机会让参与者提问和分享他们的 观点和经验。
帮助解答参与者在培训过程中可能产 生的疑问。
步骤
培训者宣布Q&A环 节开始,并解释规则 和流程。
预防再发生
对问题进行总结和归纳,完善预 防措施,防止类似问题的再次发 生。
02 8D课程详解
成立问题解决小组
总结词
成立一个跨部门的问题解决小组,成 员包括问题领域的专家和具有解决问 题能力的人员。
详细描述
针对出现的问题,从各个部门抽调人 员,组成一个结构合理、专业性强、 经验丰富的问题解决小组,确保问题 得到全面、专业的分析和解决。
详细描述
根据问题解决的各个阶段,撰写详细的8D 报告,记录问题的现象、分析、解决过程和 效果评估等,为今后的工作提供经验和参考。
总结词:预防措施
详细描述:在汽车行业中,8D方法不仅解决问题,还 注重预防类似问题的再次发生,通过根本原因分析和改 善措施来降低质量风险。
案例二:电子行业中的8D应用
在此添加您的文本17字
总结词:高效解决问题
在此添加您的文本16字
培训者或回答者总结 并重申关键点。
参与者提问,培训者 或指定的回答者回答 问题。
注意事项
确保问题与主题相关,避免偏离主题。
尊重每个参与者的观点,避免争论或 攻击性语言。
THANKS FOR WATCHING
感谢您的观看
和精准度。
05 Q&A环节
总结
01
确保所有参与者都有机会提问和 回答问题,以促进交流和互动。
02
鼓励开放和诚实的对话,以便更 好地理解问题和解决方案。
目的
提供机会让参与者提问和分享他们的 观点和经验。
帮助解答参与者在培训过程中可能产 生的疑问。
步骤
培训者宣布Q&A环 节开始,并解释规则 和流程。
预防再发生
对问题进行总结和归纳,完善预 防措施,防止类似问题的再次发 生。
02 8D课程详解
成立问题解决小组
总结词
成立一个跨部门的问题解决小组,成 员包括问题领域的专家和具有解决问 题能力的人员。
详细描述
针对出现的问题,从各个部门抽调人 员,组成一个结构合理、专业性强、 经验丰富的问题解决小组,确保问题 得到全面、专业的分析和解决。
详细描述
根据问题解决的各个阶段,撰写详细的8D 报告,记录问题的现象、分析、解决过程和 效果评估等,为今后的工作提供经验和参考。
8D报告知识培训ppt课件
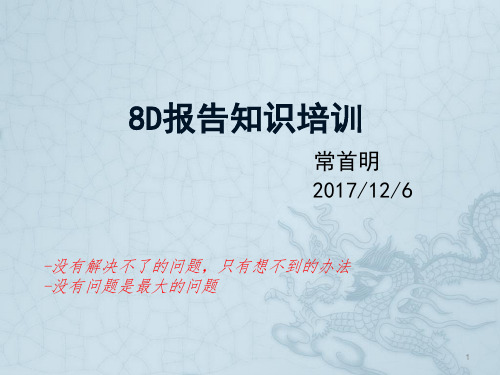
执行永久性的纠正措施,并监视其长期效果
11
8、 D7:预防再发生标准化
目的:修改现有的管理系统、操作系统、工作惯例、设计与规程以防 止这一问题与所有类似问题重复发生。 关键要点:选择预防措施;验证有效性;决策 ;组织、人员、设备、环境、 材料、文件重新确定
修正必要的系统,包括方针、运作方式、 程序,将永久对策标准 化,写入文件之中。以避免此问题及类似问题的再次发生。必要时, 要提出针对体系本身改善的建议。
FMEA
严重度(S)、频率(O)、侦测度(D)
5
2、 D1:小组成立
目的:成立一个小组,小组成员具备工艺/产品的知识,有配给的时间并授予 了权限,同时应具有所要求的能解决问题和实施纠正措施的技术素质。小组 必须有一个指导和小组长。
关键要点: 成员资格,具备工艺、产品的知识;目标 ;分工 ;程序 ;小组建设
8D报告知识培训
常首明 2017/12/6
-没有解决不了的问题,只有想不到的办法 -没有问题是最大的问题
1
➢ 8D分析手法 ➢ 8D工作方法 ➢ 适用范围 ➢ 案例分析 ➢ 解释:鱼骨图、5W1H 分析法
2
一、 8D分析手法
8D又称团队导向问题解决方法、8D问题求解法是福特公司处 理问题的一种方法,它提供了一套符合逻辑的解决问题的方法, 同时对于统计制程管制与实际的品质提升架起了一座桥梁。8D最 早是美国福特公司使用的经典质量问题分析手法。
确保 D4 问题不会再次发生的后续行动方案,如人员教育训练、改 善案例分享、作业标准化等
12
9、 D8:小组祝贺
目的:承认小组的集体努力,对小组工作进行总结并祝贺。 关键要点: 有选择的保留重要文档;流览小组工作,将心得形成文件;了 解小组对解决问题的集体力量,及对解决问题作出的贡献;必要的物质、 精神奖励
11
8、 D7:预防再发生标准化
目的:修改现有的管理系统、操作系统、工作惯例、设计与规程以防 止这一问题与所有类似问题重复发生。 关键要点:选择预防措施;验证有效性;决策 ;组织、人员、设备、环境、 材料、文件重新确定
修正必要的系统,包括方针、运作方式、 程序,将永久对策标准 化,写入文件之中。以避免此问题及类似问题的再次发生。必要时, 要提出针对体系本身改善的建议。
FMEA
严重度(S)、频率(O)、侦测度(D)
5
2、 D1:小组成立
目的:成立一个小组,小组成员具备工艺/产品的知识,有配给的时间并授予 了权限,同时应具有所要求的能解决问题和实施纠正措施的技术素质。小组 必须有一个指导和小组长。
关键要点: 成员资格,具备工艺、产品的知识;目标 ;分工 ;程序 ;小组建设
8D报告知识培训
常首明 2017/12/6
-没有解决不了的问题,只有想不到的办法 -没有问题是最大的问题
1
➢ 8D分析手法 ➢ 8D工作方法 ➢ 适用范围 ➢ 案例分析 ➢ 解释:鱼骨图、5W1H 分析法
2
一、 8D分析手法
8D又称团队导向问题解决方法、8D问题求解法是福特公司处 理问题的一种方法,它提供了一套符合逻辑的解决问题的方法, 同时对于统计制程管制与实际的品质提升架起了一座桥梁。8D最 早是美国福特公司使用的经典质量问题分析手法。
确保 D4 问题不会再次发生的后续行动方案,如人员教育训练、改 善案例分享、作业标准化等
12
9、 D8:小组祝贺
目的:承认小组的集体努力,对小组工作进行总结并祝贺。 关键要点: 有选择的保留重要文档;流览小组工作,将心得形成文件;了 解小组对解决问题的集体力量,及对解决问题作出的贡献;必要的物质、 精神奖励
8D方法ppt课件

16
附:8D分析表
1、小组组成: 组长:召集相关部门来共同讨论和解决问题 组员:
2、问题描述: 将所发生的问题、现象、现状清楚地描述出来。
3、遏制措施: 限制不合格及其造成的损失进一步扩大而采取的临时措施,须验证有效性。
4、原因分析: 调查问题产生的根本原因,并确认它们是真正的根本原因。
5、确定不合格品处置行动:规定消除现有问题的行动, 负责人 并通过实验/试运行验证是否有效。
员或管理人员、相关的质量工程师组成。
9
四、《8D》的问题处理描述
2D:描述问题 为了容易找到问题症结所在防止问题再
发生,应使用合理的思考及统计工具来详细 地描述问题:发生了什么问题?发生地点? 发生时间?问题的大小和广度?从这几方面 围堵行动 为使外部或内部的客户都不受到该问题的
1
目录
一、推广应用《8D》的目的 二、《8D》方法介绍 三、《8D》的问题处理图 四、《8D》的问题处理描述
2
一、推广应用《8D》的目的
1、及时解决客户对公司的投诉; 2、公司各部门以此举一反三; 3、倡导企业的团队精神。
3
二、《8D》方法介绍
8D(Eight-Discipline)也可称为TOPS(Team Oriented Problem Solving) 即团队导向问题解 决对策。
4
二、《8D》方法介绍
主要特点之一: 团队作战
由一组人来共同对一个问题进行 研究,对问题分析更全面、更透彻, 有利于找出根本原因,以彻底纠正永 不再犯。
5
二、《8D》方法介绍
主要特点之二:以事实为基础的问题解析技术
强调精确地陈述问题,并使用 合理的思考与统计工具来详细的描 述问题。分析测验一切可能原因, 找出并验证真因。
附:8D分析表
1、小组组成: 组长:召集相关部门来共同讨论和解决问题 组员:
2、问题描述: 将所发生的问题、现象、现状清楚地描述出来。
3、遏制措施: 限制不合格及其造成的损失进一步扩大而采取的临时措施,须验证有效性。
4、原因分析: 调查问题产生的根本原因,并确认它们是真正的根本原因。
5、确定不合格品处置行动:规定消除现有问题的行动, 负责人 并通过实验/试运行验证是否有效。
员或管理人员、相关的质量工程师组成。
9
四、《8D》的问题处理描述
2D:描述问题 为了容易找到问题症结所在防止问题再
发生,应使用合理的思考及统计工具来详细 地描述问题:发生了什么问题?发生地点? 发生时间?问题的大小和广度?从这几方面 围堵行动 为使外部或内部的客户都不受到该问题的
1
目录
一、推广应用《8D》的目的 二、《8D》方法介绍 三、《8D》的问题处理图 四、《8D》的问题处理描述
2
一、推广应用《8D》的目的
1、及时解决客户对公司的投诉; 2、公司各部门以此举一反三; 3、倡导企业的团队精神。
3
二、《8D》方法介绍
8D(Eight-Discipline)也可称为TOPS(Team Oriented Problem Solving) 即团队导向问题解 决对策。
4
二、《8D》方法介绍
主要特点之一: 团队作战
由一组人来共同对一个问题进行 研究,对问题分析更全面、更透彻, 有利于找出根本原因,以彻底纠正永 不再犯。
5
二、《8D》方法介绍
主要特点之二:以事实为基础的问题解析技术
强调精确地陈述问题,并使用 合理的思考与统计工具来详细的描 述问题。分析测验一切可能原因, 找出并验证真因。
8D介绍ppt课件
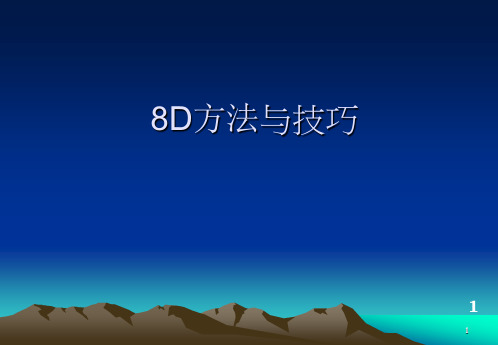
人 人 人 人 人 方法 设备
11.1% 11.1%
从上表可以看出,在导致失误的原因中,人占了绝大部分77.8%
20
D5提出长期改善对策
1.传统的失误防止出发点 人为失误所占的比重很大,长期以来,各公司采取防止失误的主要措施是”培训与惩罚”,即对
作业者进行大量培训,管理人员每每劝导作业者工作要更加认真和努力,确实通过培训, 可以避免相当一部分人为失误,比如由对过程/作业不熟悉,缺乏工作经验,但由于人为疏 忽,忘记等所造成的失误却很防止,惩罚与教育相结合的方式并不怎么成功. 2.防呆法:
14
14
过程介绍—D4原因分析
• 何谓真正的原因,问5个为什么,不三次要因
四次要因
五次要因 影響度
調薪幅度偏小
調薪制度不完善
薪水偏低
入職薪水偏低
招聘新人薪資未與 市場接軌
調薪制度不完善
調薪制度不完善 ◎ A
品
內部員工晉升QC 時薪水調整過少
內部晉升調薪幅度 未與市場薪資接軌
主导8D分析过程的进行,较好的完成8D Report. ➢能够对问题进行深入的分析,找到真因,并予以彻底
解决.
3
3
8D过程概述
• 8D:解决问题的8个步骤/ 8Disciplines of Problem Solving;
D1 描述问题
D2
成立8D 小组
D3 提出并实施短期对策
D4 原因分析
D8
改善效果总结 /表彰
在油泵轴上安装过滤器。
➢ 追问到此,最终的原因就算找到了,给油泵装上过泸器,再换上保险丝,机器就正常运行了,如果
不进行一番追问的话,也许简单的换上一根保险丝,机器照样立即转动,但是用不了多久,机器
相关主题
- 1、下载文档前请自行甄别文档内容的完整性,平台不提供额外的编辑、内容补充、找答案等附加服务。
- 2、"仅部分预览"的文档,不可在线预览部分如存在完整性等问题,可反馈申请退款(可完整预览的文档不适用该条件!)。
- 3、如文档侵犯您的权益,请联系客服反馈,我们会尽快为您处理(人工客服工作时间:9:00-18:30)。
• 問1:為什麼機器停了?
• 問2:為什麼機器會超 載?
• 問3:為什麼軸承會潤 滑不足?
• 問4: 為什麼潤滑幫浦 會失靈?
• 答1:因為機器超載, 保 險絲燒斷了
• 答2: 因為軸承的潤滑 不足
• 答3: 因為潤滑幫浦失 靈了
• 答4: 因為幫浦的輪軸 耗損了
5 Why 範例: 為何停機
• 問1:為什麼機器停了?
• 答1:因為機器超載, 保 險絲燒斷了
• 答2: 因為軸承的潤滑 不足
5 Why 範例: 為何停機
• 問1:為什麼機器停了?
• 問2:為什麼機器會超 載?
• 問3:為什麼軸承會潤 滑不足?
• 答1:因為機器超載, 保 險絲燒斷了
• 答2: 因為軸承的潤滑 不足
• 答3: 因為潤滑幫浦失 靈了
5 Why 範例: 為何停機
客戶Release good Hold reject
工程師待 客戶指示
Hold Yield 太高不合理
客戶要求作 工程分析
客戶一直 未回覆
待客戶 新程式
平面度不佳關聯圖解析
QA未執行 分散抽樣
Rework產品 未確實check
加班 精神不佳
疏忽
Loading 過多
熬夜
規格認識 不夠
打帶動作 不確實
cause,但複雜的或許要5 Why, 6 Why, 7 Why…最後要加 1H,How to fix it.
Page 12 of 110
5 Why 範例: 為何停機
• 問1:為什麼機器停了? • 答1:因為機器超載, 保 險絲燒斷了
5 Why 範例: 為何停機
• 問1:為什麼機器停了?
• 問2:為什麼機器會超 載?
• 問2:為什麼機器會超 載?
• 問3:為什麼軸承會潤 滑不足?
• 問4: 為什麼潤滑幫浦 會失靈?
• 問5: 為什麼潤滑幫浦 的輪軸會耗損?
• 答1:因為機器超載, 保 險絲燒斷了
• 答2: 因為軸承的潤滑 不足
• 答3: 因為潤滑幫浦失 靈了
• 答4: 因為幫浦的輪軸 耗損了
• 答5: 因為雜質跑到裡 面去了
Page 1 of 110
8D 的本質: 問題解決程序
當我們觀察到 或發現………時
這現象是否正常 跟標準或目標比較的差 異(偏離程度) 其差異是否不該在
為什麼會發生異常 ?
如何改善異常 ? 如何控制發生異 常的 原因 ?
現
象
確認並定義問題
例如: 人員出勤率93%
WHAT, WHEN, WHERE, WHO, WHY, HOW, HOW MUCH
• 2)什麼是問題的型態? 1.異常性問題 (s 太大) 2.結構性問題 (Xbar 太低)
• 3)如何發掘問題? 把問題視作一座冰山 ( 使用工具: 5 Why, 親和圖法,關連圖法..)
Page 5 of 110
先提昇製程水準 (Xbar ) 還是降低異常 (s )
變異很小, 但卻不準確
Page 7 of 110
G8D 步驟
D0
徵兆/ 緊急反應措施
D1
成立改善小組
D2
描述問題
D3
暫時性的對策實施及確認
D4
原因分析及証實
D5
永久改善行動效果確認
D6
永久改善行動的對策實施及確認
D7
避免再發生/ 系統性預防建議
D8
完成
G8D Additional Portions
D0
徵兆/ 緊急反應措施
D1
成立改善小組
D2
描述問題
治本對策 (永久)
5 Why & 關連圖
系統通知到 別的工程師
工程師未 被通知
工程師出差 受訓或請假
PC/MFG滿載 排不上線測試
產品待重測
L/B,P/C,Tester Hander 問題
工程師不知 有Hold Lot
ON HOLD LOT 太多
工程師太忙 沒時間處理
工程師未 作處置
工程師忘記 有Hold Lot
準確, 但變異卻很大
Page 8 of 110
Cpk=0.816
Cpk=0.852
0 10 20 30 40 50 60
-6 4 14 24 34 44 54 64 74
Cpk=1.694
Cpk=0.852
-5 5 15 25 35 45 55 65
-6 4 14 24 34 44 54 64 74
把問題想像成一座冰山
現象
現在
why
看得到的, 可感覺 , 可測量
問題
緊急處理
過去
why真因
why
真因
一次因 (近因)
治標對策 (暫時)
why
真因
why
真因
真因
n 次因
治本對策
(遠因)
(永久)
5 Why 1H 工具
• 豐田生產方式: “反覆提出五次為什麼” • 垂直式思考, 針對問題一層又一層地深入 • 通常第一個答案不會是真正的答案 • 5 Why 可以找出真正的原因 • 找原因用5Why+想方法用1How • 簡單的案子可能4W,3W或2W即找出root
問
題
分析原因 WHY
原
因
人員出勤率的目標為95% 低了2個百分比,而此差 異幅度根據以往資料判斷 差異過大為異常狀況。
請假人數太多
設定改善目標 並形成解決方案
對
策
處置:問題發生立即採 公佈人員出勤狀況取 治的標措:施解決問題的手段 強化請假 管治制本:避免問題再發生加強員工向心力的方法
衡量、追蹤及控制改善成效
8D:8 DISCIPLINES
• 8D: 8 Discplines of Problem Solving 解決問題的8個步驟
• 8D 是解決問題一種工具,通常是客戶所抱 怨的問題要求公司分析,並提出永久解決 及改善的方法
• 比改善行動報告 (Corrective Action Report) 更加地嚴謹
方法缺失
工作 不專心
材料問題
TRAY 設計不良
產品定位 不良
D3
暫時性的對策實施及確認
D4
原因分析及証實
D5
永久改善行動效果確認
D6
永久改善行動的對策實施及確認
D7
避免再發生/ 系統性預防建議
D8
完成
% Effective
% Effective % Contribution
% Effective Va問題”? 問題是實際與理想之間的差距 (Gap).
5 Why 的分佈層次
現象
為什麼機器停了? 現在
why
看得到的, 可感覺 , 可測量
問題
緊急處理
為什麼機器會超載?
過去
為什麼軸承會潤滑不足?
why真因
why
真因
一次因 (近因)
治標對策 (暫時)
改善行動
為什麼潤滑幫浦會失靈?
why
真因
防呆設計
為什麼潤滑幫浦的 輪軸會耗損?
why
真因 真因
n 次因 Page 18 of 110(遠因)