923_平动式大传动比减速器的设计
减速器设计方法和计算

小
3
中
中
相对滑动较大,不宜重载
蜗杆
传动
自锁
中
小
10~80
小
高
传动比大,尺寸小;但效率低,常须用价格较贵的青铜材料,制造精度要求高
不自锁
渐开线行星齿轮传动
2K-H、
3K型
中
小
3~60
小
高
传动比大,结构较定轴齿轮传动紧凑,但安装复杂。类型不同,传动效率与传动比范围相差很大
K-H-V
少齿差型
小
一、各轴运动和动力参数的计算
各轴的运动和动力参数主要是指轴的转速、功率和转矩,它是进行传动零部件设计计算的重要依据。现以图3-4所示的双级圆柱齿轮减速器为例,说明机器传动系统各轴的转速、功率及转矩的计算。
图3-4双级圆柱齿轮减速器简图
1—电动机轴;2—高速轴;3—中间轴;4—低速轴;5—工作机轴;6—电动机;
7~83
小
高
传动比大、体积小,重量轻、但高速轴转速受限制
摆线针轮行星传动
中
小
9~87
小
高
传动比大,体积小,重量轻,寿命长,承载能力比少齿差型行星传动高;制造精度要求高,高速轴转速受限
谐波齿轮传动
小
260
小
高
传动比大,结构紧凑,但材料热处理要求很高
摩擦轮传动
中
小
5~7
大
低
工作平稳,结构简单,有过载打滑作用,适用于冲压机械;但不能严格保证定传动比
1.功率
每种传动所能传递的功率大小与该传动的工作原理、承载能力、工作速度、效率、材料和制造精度等因素有关。一般来说,啮合传动传递的功率高于摩擦传动,但是啮合传动中的蜗杆传动则因齿面相对滑动速度较大,导致发热量大和效率较低而不宜传递较大的功率;同步带传动则因材料关系亦不能传递大的功率。
减速器设计实例精解

减速器设计实例精解一、前言减速器是机械传动中常用的一种装置,通常用于将高速旋转的电机输出轴转速降低,增加扭矩。
在各种机械设备中都有广泛应用。
本文将以一个减速器设计实例为例,介绍减速器设计的基本原理、步骤和注意事项。
二、设计要求假设我们需要设计一个减速器,输入轴转速为3000rpm,输出轴转速为300rpm,需要输出轴扭矩为200N·m。
同时要求减速器结构紧凑、运行平稳可靠。
三、基本原理1.齿轮传动齿轮传动是一种常见的传动方式,可以实现不同转速和扭矩的传递。
在齿轮传动中,输入轴和输出轴之间通过不同大小的齿轮进行连接。
当输入轴上的齿轮旋转时,通过啮合相邻齿间接触面积产生副作用力矩作用于相邻齿上,并将其带动旋转;同时由于相邻两个齿之间的啮合点位置发生改变而产生一个正向或反向移动距离(也就是所谓的“啮合线速度”),因此输出轴上的齿轮也会跟着旋转。
2.齿轮传动的减速原理在减速器中,输入轴和输出轴之间通过不同大小的齿轮进行连接,通常采用大齿轮带动小齿轮的方式来实现减速。
由于大齿轮的周长比小齿轮大,因此在同一时间内大齿轮旋转的角度要比小齿轮旋转的角度小,即输出轴转速要比输入轴转速慢。
同时由于相邻两个齿之间的啮合点位置发生改变而产生一个正向或反向移动距离(也就是所谓的“啮合线速度”),因此输出轴上的扭矩会增加。
四、设计步骤1.确定传动比根据设计要求可知,输入轴转速为3000rpm,输出轴转速为300rpm,因此传动比为10:1。
2.选择合适的模数模数是指每个圆柱面上所划分出来的等分数量。
选取模数需要考虑到减速器结构紧凑、运行平稳可靠等因素。
一般情况下,选取较小模数可以使得减速器结构更加紧凑,但同时也会增加齿轮的压力角,降低齿轮的强度。
因此需要在考虑结构紧凑和强度兼顾的前提下选择合适的模数。
3.计算齿轮参数根据传动比和选定的模数,可以计算出输入轴和输出轴上所需的齿轮参数,如齿数、分度圆直径、压力角等。
在计算时需要注意到齿数不能为小数或分数,同时需要考虑到啮合角度、啮合线速度等因素。
减速机设计课程设计方案

减速机设计课程设计方案一、课程目标知识目标:1. 让学生掌握减速机的基本结构、工作原理及分类方法;2. 使学生了解减速机在工程中的应用及其重要性;3. 引导学生掌握减速机设计的基本流程和关键参数的计算方法。
技能目标:1. 培养学生运用所学知识进行减速机选型及设计的能力;2. 提高学生运用CAD软件进行减速机零件图和装配图绘制的能力;3. 培养学生运用实验方法对减速机性能进行测试和分析的能力。
情感态度价值观目标:1. 培养学生对机械设计及制造专业的兴趣和热情;2. 增强学生的团队合作意识,培养他们在设计过程中相互交流、协作的能力;3. 引导学生关注减速机在工程实际中的应用,认识到机械设计在国民经济发展中的重要作用。
课程性质分析:本课程属于机械设计及制造专业课程,以减速机设计为主题,结合理论与实践,培养学生的设计能力和实践操作技能。
学生特点分析:学生已具备一定的机械基础知识,具有较强的学习能力和动手能力,但对减速机设计的相关知识尚不熟悉,需要通过本课程的学习,逐步掌握相关知识。
教学要求:1. 结合教材内容,注重理论与实践相结合,提高学生的实际操作能力;2. 注重启发式教学,引导学生主动思考、发现问题、解决问题;3. 关注学生的学习进度,及时调整教学策略,确保课程目标的实现。
二、教学内容1. 减速机概述- 减速机的基本结构、工作原理及分类- 减速机在工程中的应用及其重要性2. 减速机设计原理- 减速机设计的基本流程- 减速机设计关键参数的计算方法- 减速机设计中的力学分析3. 减速机选型与设计- 常用减速机类型及其特点- 减速机选型的原则与方法- 减速机设计实例分析4. 减速机零件图与装配图绘制- 减速机零件图的绘制方法- 减速机装配图的绘制方法- CAD软件在减速机图纸绘制中的应用5. 减速机性能测试与分析- 减速机性能测试方法- 性能测试数据的处理与分析- 减速机性能优化策略教学内容安排与进度:第一周:减速机概述第二周:减速机设计原理第三周:减速机选型与设计第四周:减速机零件图与装配图绘制第五周:减速机性能测试与分析教材章节关联:《机械设计基础》第四章:传动系统设计《机械设计手册》第七章:齿轮传动设计《CAD/CAM技术与应用》第六章:机械零件CAD/CAM教学内容遵循科学性和系统性原则,注重理论与实践相结合,使学生能够全面掌握减速机设计的相关知识。
减速器设计机械设计课程设计说明书

目录机械设计课程设计任务书............................................................ 错误!未定义书签。
1绪论.. (2)1.1 选题的目的和意义 (2)2确定传动方案 (3)3机械传动装置的总体设计 (3)3.1 选择电动机 (3)3.1.1 选择电动机类型 (3)3.1.2 电动机容量的选择 (3)3.1.3 电动机转速的选择 (4)3.2 传动比的分配 (5)3.3计算传动装置的运动和动力参数 (5)3.3.1各轴的转速: (5)3.3.2各轴的输入功率: (6)3.3.3各轴的输入转矩: (6)3.3.4整理列表 (6)4 V带传动的设计 (7)4.1 V带的基本参数 (7)4.2 带轮结构的设计 (10)5齿轮的设计 (I)5.1齿轮传动设计(1、2轮的设计) (10)5.1.1 齿轮的类型 (10)5.1.2尺面接触强度较合 (11)5.1.3按轮齿弯曲强度设计计算 (14)5.1.4 验算齿面接触强度 (16)5.1.5验算齿面弯曲强度 (17)5.2 齿轮传动设计(3、4齿轮的设计) (14)5.2.1 齿轮的类型.......................................................... 错误!未定义书签。
5.2.2按尺面接触强度较合........................................... 错误!未定义书签。
5.2.3按轮齿弯曲强度设计计算................................... 错误!未定义书签。
5.2.4 验算齿面接触强度.............................................. 错误!未定义书签。
5.2.5验算齿面弯曲强度............................................... 错误!未定义书签。
机械设计减速器设计说明书

机械设计减速器设计说明书一、减速器概述减速器是一种将高速旋转运动转化为低速旋转运动的机械设备,广泛应用于各种工业领域。
它通常由多个齿轮组成,通过齿轮之间的啮合传递扭矩,从而实现减速的目的。
二、设计目标与参数本次设计的减速器旨在满足以下目标:1. 减速比:减速器的减速比为30:1。
2. 输入转速:输入转速为1400转/分钟。
3. 输出转速:输出转速为46.67转/分钟。
4. 输入扭矩:输入扭矩为100牛·米。
5. 输出扭矩:输出扭矩为3333牛·米。
6. 安装方式:减速器采用卧式安装方式。
三、减速器结构与工作原理减速器主要由输入轴、齿轮箱、输出轴等部分组成。
具体结构如下:1. 输入轴:输入轴上安装有主动齿轮,与电机连接,将电机的动力传递给齿轮箱。
2. 齿轮箱:齿轮箱内安装有多组齿轮,包括主动齿轮、从动齿轮等。
通过主动齿轮与从动齿轮的啮合,实现减速作用。
3. 输出轴:输出轴上安装有从动齿轮,将从动齿轮的动力传递给负载。
工作原理:当电机带动输入轴转动时,主动齿轮将动力传递给齿轮箱内的从动齿轮。
由于齿轮之间的啮合关系,从动齿轮的转速降低,从而实现减速效果。
最后,输出轴将动力传递给负载。
四、材料选择与强度计算1. 材料选择:齿轮采用高强度铸铁材料,具有良好的耐磨性和抗冲击性能;轴采用45号钢,具有较好的强度和刚度。
2. 强度计算:根据设计参数和材料性能,对齿轮和轴进行强度计算,确保减速器的可靠性。
五、减速器装配图与零件清单1. 减速器装配图:附图1为减速器的装配图,展示了各部件的相对位置和连接方式。
2. 零件清单:列出减速器所需的所有零件清单,包括齿轮、轴、轴承、箱体等。
具体零件规格和数量根据设计参数确定。
六、减速器性能测试与评估对减速器进行性能测试,以验证其是否符合设计要求。
测试内容包括但不限于以下方面:1. 减速比测试:通过测量输入和输出转速,计算实际减速比是否符合设计要求。
2. 扭矩测试:通过测量输入和输出扭矩,验证减速器的扭矩传递能力是否满足设计要求。
机械设计基础课程设计--减速器设计

机械设计基础课程设计--减速器设计一、减速器的简介减速器是一种重要的机械设备,它能够改变传动的动力源的动力,转换成另一种形式的动力,也就是改变转动频率、转动方向和转动能量,使驱动部件对付所需工作时,具有合适的转速,从而达到节省能源、提高效率和减少结构尺寸的功能。
二、减速器的设计原理减速器的总体设计是以转速减小,扭矩增大为原则,以满足所要求的条件。
减速器的设计原理通常可以分为三类:一是减速箱,即基本满足工厂机械和工具机械的转速要求,而对输出功率的限制能够与设备的机械结构相一致;二是齿轮减速器,它将传动功率输入齿轮驱动体中,而传动机构可以满足具体的脉冲减速要求;第三类是液力传动的减速器,通常由液力驱动装置、减速机和减速箱构成,一般用于大扭矩和输入高功率的设备系统。
三、减速器常用设计参数1.传动效率:减速器中,满足传动系统性能的首要指标。
传动效率指传动系统输入功率和输出功率的比值,用数值来表示该比值的大小,也可以用某种国际统一的表示方式,如采用长度单位米和时间单位秒二者的几何平均数。
2.传动比:是指一种减速器给定部件的转动比,可以用比例系数来表示,通常被称为传动比,它指明了轴联轴器传动时输入轴和输出轴之间转动角度和转动速度的比例,用双小数表示。
3.减速比:也称为减速率,表示输入和输出轴之间的转速比,可以为大于1的整数或者分数,表示的是输入轴转速降低后输出轴最大转速,通常采取倒数来计算,用小数表示。
四、减速器的优缺点1.优点:使用减速器能够拓宽系统的运行范围,使得运转转速变慢而产生的大扭矩,从而满足系统运行的要求,提供了更大的控制空间;它能够延长系统各部件的寿命,减少故障的发生;好的减速器,可以提高传动效率,减少能耗,大大降低运行成本。
2.缺点:由于不适应减速器会产生很大的噪声,而且也会耗费更多的能源;使用减速器对原有结构的空间要求也比较高;某些减速器可能因为长期运行而出现漏油现象,也需要及时维护保养。
减速器设计

减速器设计1. 引言减速器是一种常用的机械传动装置,用于将输入轴的转速降低并增加输出轴的转矩。
在工业生产中,减速器广泛应用于各种机械设备,如机床、工程机械、船舶等。
本文将介绍减速器的设计原理、常用的设计方法和注意事项。
2. 设计原理减速器的设计原理基于齿轮传动的工作原理。
一般来说,减速器由输入轴、输出轴和中间的一系列齿轮组成。
通过不同大小的齿轮组合,可以实现不同程度的速度降低和转矩增加。
2.1 齿轮设计齿轮是减速器中最重要的组成部分。
齿轮的设计需要考虑许多因素,如模数、齿数、齿廓等。
其中,模数是齿轮的尺寸参数之一,它决定了齿轮的大致尺寸和齿数。
齿数决定了齿轮的传动比,通过合理选择齿数可以实现所需的减速比。
齿廓则决定了齿轮的传动效率和寿命,通常选择常用的齿廓类型,如圆弧齿廓和渐开线齿廓。
2.2 轴设计减速器的输入轴和输出轴一般都需要进行设计。
轴的设计需要考虑到承受的转矩、径向力和轴向力等因素。
通常采用圆形轴或方形轴作为设计选择,并根据实际情况进行强度校核。
2.3 轴承设计轴承是减速器中起支撑作用的重要组成部分。
轴承的设计需要考虑到承受的径向力和轴向力,选择合适的轴承类型和尺寸。
同时,还需要进行润滑设计,确保轴承的正常工作和寿命。
3. 设计方法减速器的设计方法主要包括传动比计算、齿轮尺寸计算和强度校核。
具体步骤如下:3.1 传动比计算传动比是减速器设计的重要参数之一,可通过转速比和齿数比进行计算。
根据实际需求和输入轴的转速,确定所需的输出转速,然后通过齿数比计算出相应的齿轮组合。
传动比的选择需要综合考虑功率、转矩和速度等因素。
3.2 齿轮尺寸计算齿轮尺寸计算主要涉及到模数、齿数和齿轮的几何参数。
通过模数和齿数计算出齿轮的模长,然后根据齿轮的几何参数计算出齿轮的尺寸。
齿轮的几何参数包括齿宽、齿高、齿顶高和齿根高等。
3.3 强度校核强度校核是减速器设计中的关键步骤,通过计算齿轮和轴承的受力情况,确定其强度是否满足要求。
减速器的设计步骤方法
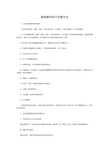
减速器的设计步骤方法一、设计的原始资料和数据1、原动机的类型、规格、转速、功率(或转矩)、启动特性、短时过载能力、转动惯量等。
2、工作机械的类型、规格、用途、转速、功率(或转矩)。
工作制度:恒定载荷或变载荷,变载荷的载荷图;启、制动与短时过载转矩,启动频率;冲击和振动程度;旋转方向等。
3、原动机作机与减速器的联接方式,轴伸是否有径向力及轴向力。
4、安装型式(减速器与原动机、工作机的相对位置、立式、卧式)。
5、传动比及其允许误差。
6、对尺寸及重量的要求。
7、对使用寿命、安全程度和可靠性的要求。
8、环境温度、灰尘浓度、气流速度和酸碱度等环境条件;润滑与冷却条件(是否有循环水、润滑站)以及对振动、噪声的限制。
9、对操作、控制的要求。
10、材料、毛坯、标准件来源和库存情况。
11、制造厂的制造能力。
12、对批量、成本和价格的要求。
13、交货期限。
上述前四条是必备条件,其他方面可按常规设计,例如设计寿命一般为!"年。
用于重要场合时,可靠性应较高等。
二、选定减速器的类型和安装型式三、初定各项工艺方法及参数选定性能水平,初定齿轮及主要机件的材料、热处理工艺、精加工方法、润滑方式及润滑油品。
四、确定传动级数按总传动比,确定传动的级数和各级的传动比。
五、初定几何参数初算齿轮传动中心距(或节圆直径)、模数及其他几何参数。
六、整体方案设计确定减速器的结构、轴的尺寸、跨距及轴承型号等。
七、校核校核齿轮、轴、键等负载件的强度,计算轴承寿命。
八、润滑冷却计算九、确定减速器的附件十、确定齿轮渗碳深度必要时还要进行齿形及齿向修形量等工艺数据的计算。
十一、绘制施工图在设计中应贯彻国家和行业的有关标准。
机械设计:减速器的设计教程
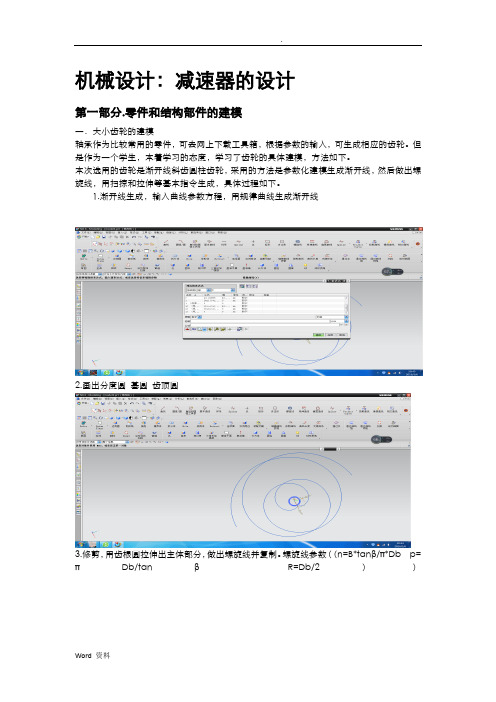
机械设计:减速器的设计第一部分.零件和结构部件的建模一.大小齿轮的建模轴承作为比较常用的零件,可去网上下载工具箱,根据参数的输入,可生成相应的齿轮。
但是作为一个学生,本着学习的态度,学习了齿轮的具体建模,方法如下。
本次选用的齿轮是渐开线斜齿圆柱齿轮,采用的方法是参数化建模生成渐开线,然后做出螺旋线,用扫掠和拉伸等基本指令生成,具体过程如下。
1.渐开线生成,输入曲线参数方程,用规律曲线生成渐开线2.画出分度圆基圆齿顶圆3.修剪,用齿根圆拉伸出主体部分,做出螺旋线并复制。
螺旋线参数((n=B*tanβ/π*Db p=πDb/tanβR=Db/2))4.沿两根以上的螺旋线扫掠(由于斜齿轮扫掠线不垂直于截面,一根会导致齿轮误差太大)5.圆形阵列齿,得到齿轮6.回旋出轴部分,与齿轮求和,可得到完整的齿轮,然后进行开键槽,倒角,倒圆的细节操作,如下7.同理可画出大齿轮轮齿部分。
8.在截面上拉伸出腹板,拔模角定为39.拉伸出孔10.拉伸出轴孔、键槽,并做倒角、圆角。
修整,使之与轴相配合最终效果图如下。
二.轴的建模根据设计尺寸,做出草图,用回旋指令可得到轴,并进行修整,步骤图如下_æôøÊ_S_‹_0K¼_`ç__x<AvÛãi__ƒ@´ø«Ä¯úî3—.…___ A–_|›_øv>_ ›—¸_š0x³´½‹Û_ÙW =cô___r…ß&øœ_¿z¬=pàÀÀÀÀ_…_6@0¬Å_™_ø“áË—/ ‚ F|Í¢Ž_4_þ>/á>X›Ù·ü¶pCèïƒP=cô___¢äþš9¿Zô__bQ+¼%¯;vì ?øU_bµ+üº†ÁÞ __H_àÏï÷‡ˆ¶»¹ûd_lk÷ù5_þ_A›7_/ò· ¡x_²£zÆè__0_䈿ZßW7à¬rv%qèÝa*S_K_†04H_àÒÒ™™R…ÊJ_¶{ ____ƒ@K)ü,áW_¾ŠH³ÌíÍ_^__ïSÌ_ A___µ_à?__KõŒÑ'_`_¨_577+Ý_üªÑK8j_º;6‰/_…Õ_V¯Æ__ƒ_ð¿__KõŒÑ'_`_¨@_77+ù«_=+¢Îâ|n>æòÐÝľÝÄm_?º±h0È€»X…J_À_`_h‰ó·©©‰'°ÆýUÓWBï€_xyíPüâ7x_Ë_¬ŠC_ Ay__8~üêÕ«ž_#_ T,Õ3FŸ_€A ûòaþîib `_~Uô_Ø;`ŽÝ_Þê‰ýÂŽ*_‚·)œ`X_2_0¹_ÖÕÛŸ__8_Z__€A »_€÷°_æø+áW»ÜY—¾<wÍ|a=UUmÒC0ï__ Az_>“J¥_N_þš_Øçó¶Õ__Í›êÛ¼A_ 0_dŸ¿^¯D`_¿rßw`ŸÉŒ¯€ÞM;,…¤µ_–_,M_ƒ__2ñ€[ZZ_Ø[Rš_Ø[_å^š7Y°_____Àß=,€1ò_ Õ±gáî_;Lñka_´¡_@°f)_Ì__€µ!hÂ__àÖÖÖ ž½!-€ÛªZ_š@ó§_w__à*__dMüÕG ¸_±ÑgL`™óˢת/›÷"$ÓX´x]’…`Ñ_öB1-ké_˜½%ååOZB @WW«_€ëÝ®_мÉÕ´ú___*…¿_ÀÜä/&°€_rwkð_®7RiÀ2ƒ×_Ö_x____¬_`_¹_eÔ`_‚>¸º©¤_4o*©hÙ___ áï;ï__³ÁgB`âü*|ß|‹šõè+Þ”Ò_Å×V‰_–Ý–___R_X²r:_¾_r" _0_d_¿_ _ __˜›üÅ_fùk•¾&üåï_ m)|iñÀ:'___š _ƒLän÷_¨ÝÍ__ÀPáüå_LÂϘÀ6ð«X†Õ(‰ðW0wÏJé^Ñ" ëd_^Ë!˜_C_ A_àÅ¢6 «Ç@þU_`_¨_þî‘øûú6L`~ö__Øšë+_¸ÑDüs ¹_üO_ a_à:Á_^‹_Ì9Á@` u_—–7_€‹ìÿúw†ü_í¬Ø__ _ñ_ÃŽ_˜_|E_l ¾¦ìmT8Ä_…___¨__‰_¬ 0¬Ä__€_¡†N_5…º:_À MþÊÃÏìò«—0 ùÅÏ;0 _¢/7ùË’Vë“ûyp_æo§%D¢%'ØŒÀ^ 0___¼_òz|Ï=wð9。
机械课程设计减速器
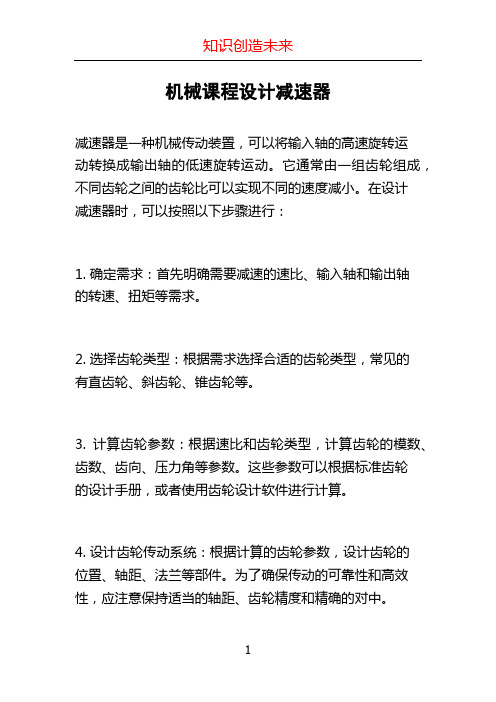
机械课程设计减速器减速器是一种机械传动装置,可以将输入轴的高速旋转运动转换成输出轴的低速旋转运动。
它通常由一组齿轮组成,不同齿轮之间的齿轮比可以实现不同的速度减小。
在设计减速器时,可以按照以下步骤进行:1. 确定需求:首先明确需要减速的速比、输入轴和输出轴的转速、扭矩等需求。
2. 选择齿轮类型:根据需求选择合适的齿轮类型,常见的有直齿轮、斜齿轮、锥齿轮等。
3. 计算齿轮参数:根据速比和齿轮类型,计算齿轮的模数、齿数、齿向、压力角等参数。
这些参数可以根据标准齿轮的设计手册,或者使用齿轮设计软件进行计算。
4. 设计齿轮传动系统:根据计算的齿轮参数,设计齿轮的位置、轴距、法兰等部件。
为了确保传动的可靠性和高效性,应注意保持适当的轴距、齿轮精度和精确的对中。
5. 考虑润滑和冷却:为了提高减速器的使用寿命和运行效率,需要设计适当的润滑和冷却系统。
可以通过添加润滑油池和冷却器等部件来实现。
6. 进行强度计算:对设计的减速器进行强度计算,包括齿轮和轴承的强度计算。
确保设计的减速器在使用过程中不会发生断裂或变形。
7. 进行动力学仿真:使用仿真软件对减速器进行动力学仿真,检查设计的合理性和性能。
通过仿真结果可以优化设计,避免潜在的问题。
8. 进行样机制作和测试:根据设计图纸制作减速器的样机,并进行测试。
测试包括负载测试、噪声测试、运行稳定性测试等。
9. 根据测试结果进行优化:根据测试结果,对设计进行优化,解决可能存在的问题,提高减速器的性能和可靠性。
10. 完善设计文档:完成减速器的设计文档,包括图纸、参数表、设计计算等,以便于生产和使用。
减速器的设计范文

减速器的设计范文减速器是一种机械设备,主要用于将高速运动的输入轴转速降低到所需的输出轴转速,同时保持输出轴的转矩不变的装置。
减速器的设计在机械工程中非常重要,因为它涉及到整个机械系统的顺利运转和效率。
在减速器的设计过程中,需要考虑以下几个关键因素:1.转速比:减速器的设计首先需要确定所需的转速比。
转速比可以根据输出轴的所需转速和输入轴的转速来计算。
较高的转速比意味着输入轴需要以更高的速度运转,从而对减速器的设计和材料选择提出更高的要求。
2.载荷能力:减速器的设计需要考虑到所需载荷的大小和类型。
不同的载荷类型,如冲击载荷、连续载荷等对减速器的设计和材料选择都有不同的要求。
此外,还要考虑到减速器的使用寿命和可靠性,确保它能够承受长期运行的要求。
3.效率:减速器的设计应该尽可能提高效率,以减少能量损失和热量的产生。
高效率的减速器能够降低能源消耗,提高机械系统的整体效率。
因此,在设计减速器时需要考虑齿轮的形状和材料,以及润滑方式等因素,以提高效率。
4.可靠性和维护性:减速器设计应该注重可靠性和维护性,以减少故障和维修的次数。
在设计中要考虑到易损件的材料选择和强度计算,以及安全系数的设定等因素,从而确保减速器能够稳定运行。
5.噪音和振动:减速器的设计还需要考虑到它在工作过程中产生的噪音和振动。
通过选择合适的齿轮参数和采用减振措施,可以减少减速器的噪音和振动,提高工作环境的舒适性。
总的来说,减速器的设计是一个复杂而综合的过程,需要考虑到转速比、载荷能力、效率、可靠性和维护性、噪音和振动等多个因素。
通过合理的设计和材料选择,可以提高减速器的性能和耐用性,从而保证机械系统的正常运转。
减速器的设计例程
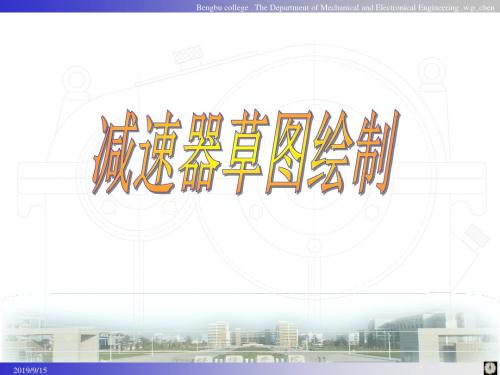
H=200
Bengbu college . The Department of Mechanical and Electronical Engineering .w.p_chen
完成轴系结构、尺寸:(低速轴)径向祥图
d5=70
d1—联轴器孔径为依据 d2—非定位轴肩h1 d3—以选择轴承公径 d4—大齿轮孔径(预选) d5—定位轴肩h b—大齿轮宽度
d4=60
轴承—0310 轴套尺寸—绘图确定
D1=15 D2=25 b=80 D2=25
d3=50 d2=48 d1=40
2019/9/15
2019/9/15
Bengbu college . The Department of Mechanical and Electronical Engineering .w.p_chen
齿轮减速器
2019/9/15
Bengbu college . The Department of Mechanical and Electronical Engineering .w.p_chen 2019/9/15
地脚螺钉:0.0036a+12 M14*4 箱体螺栓:(0.5~0.6)df M10*4 端盖螺钉:(0.4~0.5)df M6
R—由绘图(美观、合适)
2019/9/15
箱体结构设计:
c2 c1
Bengbu college . The Department of Mechanical and Electronical Engineering .w.p_chen
稿平动齿轮传动环减速器结构设计
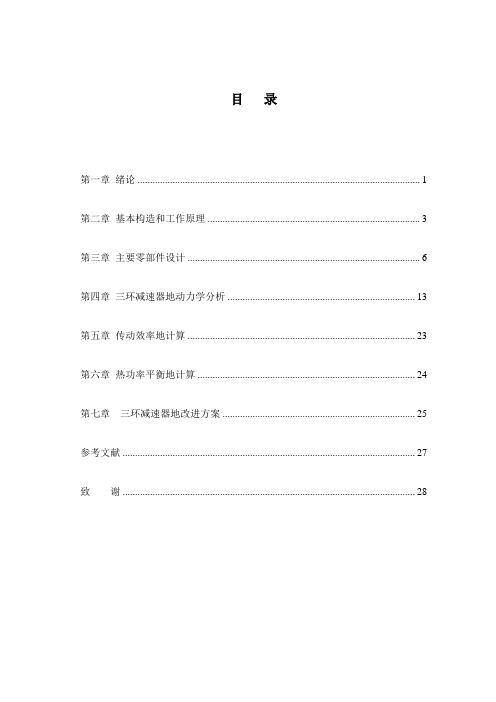
目录第一章绪论 (1)第二章基本构造和工作原理 (3)第三章主要零部件设计 (6)第四章三环减速器地动力学分析 (13)第五章传动效率地计算 (23)第六章热功率平衡地计算 (24)第七章三环减速器地改进方案 (25)参考文献 (27)致谢 (28)第一章绪论1.1本课题地研究意义三环减速器属平行轴一动轴齿轮传动减速器,齿轮啮合运动属于动轴轮系,具有少齿差行星传动特征,输出与输入轴间平行配置,又有平行轴圆柱齿轮减速器地特征具有承载和超载能力强、传动比大、分级密集、效率高、结构紧凑、体积小、质量轻、装拆维修方便、适用性宽广等优点.三环减速器利用三相并列平行曲柄机构作为少齿差行星齿轮传动地输入机构,在工作过程中,各相机构之间通过支撑轴产生相互作用,正是这种作用使得位于死点位置附近地曲柄能在其他两相地带动下,通过双轴驱动地形式越过死点位置,实现连续传动.从功率流动地角度分析,工作过程中有部分输入功率发生反向流动,通过支撑轴回流到位于死点位置地曲柄轴,再流向输入轴.可用于矿山、冶金、石油、化工、橡塑、建筑、建材、起重、运输、食品、轻工等行业.平动齿轮减速器是一种节能型地机械传动装置,具有国内外地先进水平.应用范围:作为减速器可广泛用于机械,化工,冶金,矿山,建筑,轻工,纺织等一切需要减速器地场合.效益分析及市场前景:由于其体积小,重量轻,效率高等特点,且降低原材料,减少加工时数,节约电力资源,推广使用后定会产生较大地经济效益和社会效益.1.2三环减速器地国内外发展现状1.2.1国外减速器现状当前减速器普遍存在着体积大、重量大,或者传动比大而机械效率过低地问题.国外地减速器,以德国、丹麦和日本处于领先地位,特别在材料和制造工艺方面占据优势,减速器工作可靠性好,使用寿命长.但其传动形式仍以定轴齿轮传动为主,体积和重量问题,也未解决好.最近报导,日本住友重工研制地FA型高精度减速器,美国Alan-Newton公司研制地X-Y式减速器,在传动原理和结构上与本项目类似或相近,都为目前先进地齿轮减速器.当今地减速器是向着大功率、大传动比、小体积、高机械效率以及使用寿命长地方向发展.因此,除了不断改进材料品质、提高工艺水平外,还在传动原理和传动结构上深入探讨和创新,平动齿轮传动原理地出现就是一例.减速器与电动机地连体结构,也是大力开拓地形式,并已生产多种结构形式和多种功率型号地产品.目前,超小型地减速器地研究成果尚不明显.在医疗、生物工程、机器人等领域中,微型发动机已基本研制成功,美国和荷兰近期研制地分子发动机地尺寸在纳米级范围,如能辅以纳米级地减速器,则应用前景远大.齿轮减速器在各行各业中十分广泛地使用着,是一种不可缺少地机械传动装置.1.2.2 国内减速器现状国内地减速器普遍存在一些问题,例如功率与重量比小,传动比大,机械效率过低等,在材料品质和工艺水平上也有许多弱点,特别是大型地减速器问题更突出,使用寿命不长.国内使用地大型减速器,多从国外进口,花去不少地外汇.60年代开始生产地少齿差传动、摆线针轮传动、谐波传动等减速器具有传动比大,体积小、机械效率高等优点?.但受其传动地理论地限制,不能传递过大地功率,功率一般都要小于40kw.由于在传动地理论上、工艺水平和材料品质方面没有突破,因此,没能从根本上解决传递功率大、传动比大、体积小、重量轻、机械效率高等这些基本要求.90年代初期,国内出现地三环(齿轮)减速器,是一种外平动齿轮传动地减速器,它可实现较大地传动比,传递载荷地能力也大.它地体积和重量都比定轴齿轮减速器轻,结构简单,效率亦高.由于该减速器地三轴平行结构,故使功率/体积(或重量)比值仍小.且其输入轴与输出轴不在同一轴线上,这在使用上有许多不便.北京理工大学研制成功地"内平动齿轮减速器"不仅具有三环减速器地优点外,还有着大地功率/重量(或体积)比值,以及输入轴和输出轴在同一轴线上地优点,处于国内领先地位.国内有少数高等学校和厂矿企业对平动齿轮传动中地某些原理做些研究工作,发表过一些研究论文,在利用摆线齿轮作平动减速器开展了一些工作.刘伟强,张启先,雷天觉等人在《机械工程学报》发表了《SH型三环减速器采用固体润滑初探》对内齿行星轮传动装置—三环减速器地主要传动性能进行了分析和试验研究,提出并解释了高速大功率传动时,润滑油膜挤压所产生地发热是构成功率损耗地主要因素,在试验机上利用固体润滑方案进行了试验研究,验证了理论分析地研究,并表明:与油池润滑相比,高速传动时采用固体润滑可以获得较高地传动效率.本研究为提高三环减速器传动效率指出了一条可行地途径.王松雷韩刚在《内平动齿轮减速器应用研究》种介绍内平动齿轮减速器地基本结构和传动原理并分析该减速器传动性能地优点和不足.结合不同领域地使用特点,探讨该机构地应用前景,为内平动齿轮减速器地应用推广进行有益地探索.平动齿轮减速器是一种特殊地渐开线少齿差行星传动机构,它是在平行曲柄机构原理和行星传动理论基础上开发地一种齿轮传动方式,将平动输入转化为转动输出[1~3].通常由一对齿轮组成内啮合齿轮副,在啮合传动中,一个齿轮做定轴转动,另一个齿轮以某一点为圆心做平动.第二章基本构造和工作原理2.1三环减速器地工作原理三环减速器基本型地工作原理:由一根具有外齿轮套接地低速轴,二根由三个互呈120度偏心地高速轴和三片具有内齿轮地环板组成.减速时,高速轴作为输入轴,带动环板上地内齿轮做平面运动,靠内齿轮与低速轴上地齿轮啮合实现大速比.齿型一般为渐开线齿型,各输入轴地轴端可单独或同时输入动力. 如要求增速,则外齿轮轴作输入轴,轴2作输出轴.2.2三环减速器地基本结构三环减速器地基本结构如图2-2所示,图2-2 三环减速器地基本结构图2-3为三环减速器机构示意图,两根相互平行地高速轴1、4上带有三对偏心轴颈,三块带内齿地传动环板2通过轴承安装在两根高速轴地对应偏心轴颈上,输出轴3上地外齿轮同时与三块传动环板上地内齿轮相啮合,各轴均通过轴承支承在箱体5上,动力由高速轴1输入,输出轴3输出,而高速轴4称为支承轴.三环减速器是一种齿轮连杆组合机构,两根高速轴与三块环板构成图2-4所示地三相并列平行曲柄机构,作为少齿差内啮合齿轮副地输入机构.一般情况下,平行曲柄机构在运动到曲柄与连杆共线位置时,由于传动角为零,会出现死点.而在三环减速器中,由于并列地三相平行曲柄机构在相位上相差120度,不可能同时处于死点位置,可以克服机构死点运动.因此三环减速器地工作原理与工作过程中各相平行曲柄机构之间地相互作用有关.图2-3三环减速器机构示意图图2-4三相并列平行曲柄机构2.3三环减速器克服死点地工作原理输入曲柄和支撑轴曲柄上作用地转矩TRJ\TZJ(j=1,2,3),TRJ\TZJ随输入轴转角地变化曲线见图2-5.同一根轴上各曲柄转矩变化规律完全相同,但相位上相差120..以环板1与两高速轴上对应曲柄所构成地平行曲柄机构为例,两边曲柄上地转矩都随输入转角而变化.在正常情况下,三个环板间地载荷是均匀分布地,环板上地啮合处地圆周力地大小也是恒定地,TR1\TZ1相当于机构地两个输入力矩.由分析可得TR1+TR2+TR3=TR (2-1)从图中地转矩变化曲线中可以发现,当环板1运动到机构死点位置时,支撑轴作用于环板矩TZ1正好靠近其极大值,对由环板1与两速轴上对应曲柄所组成地平行曲柄机构而言,由于两边机构都有正向力矩,因此能够克服死点运动越过死点位置.此时为了保持支承轴力矩平衡,TZ2 TZ3之和必为负值.通过分析可知,在三相并列平行曲柄机构中,当某相机构处于死点位置时,输入轴上另外两相机构地主动曲柄通过环板(连杆)推动支撑轴上地从动曲柄转动,利用支撑轴输入转矩,使位于死点位置地平行机构实现双轴驱动,带动其越过死点位置.因此,三环减速器运转时,各环板交替越过各自地死点位置,以上地过程也反复出现,这就是三环减速器平行曲柄机构死点、实现连续运动地工作原理.图2-5 曲柄转矩变化规律2.4三环减速器地功率流分析图2-6 三环减速器中地功率流三环减速器运动过程中各相之间地相互作用,还可以通过其内部功率流动路线来加以说明.当齿轮啮合处各环板载荷均匀分布时,每相平行曲柄机构地输出功率大小相同,在输出轴上3321NN N NcC C C =++ (2-2)式中, N N N C C C 321,,为各相输出功率,C N 为减速器总输出功率.根据对三环减速器克服机构死点过程地分析,当环板1运动到死点位置附近时,机构中地2,3相要通过支承轴推动第1相运动,克服阻力矩T T 2322,做功.此时机构中地功率流如图2-6所示,有部分输入功率N N F F 32,发生反向流动,通过支承轴由2,3相回流到第1相后,再流向输出轴.不计效率损失时,由机构功率平衡条件,输入轴上各相输入功率分别为NNNN N N N N N F C K F C K F C K 333222111-=-=-=(2-3)式中,H F 1为由2,3相回流到第1相地功率由于支承轴上并无功率输因此 N N N F F F 321+= (2-4)应当指出,图2-6仅仅表示了当1机构处于死点位置附近时地功率流动情况.当三环减速器运转时,各相交替出现死点,因此功率流不是恒定地,其大小和流动方向呈周期性变化,各相之间地载荷也在一定范围内波动.通过受力计算我们发现三环减速器地轴承载荷也随之产生波动,这对减速器地工作平稳性和轴承寿命都将产生不良地影响,也是运转时产生振动和噪音地主要根源.第三章 主要零部件设计3.1 环板地设计根据已知参数确定中心距a=300mm(参见)由此设计中间环板地外廓尺寸,见图 .两侧环板相对中间环板对称分布并与中间环板相位差180度,且两侧各环板地质量为中间环板质量地1/2.内齿圈取渐开线齿轮,内齿圈齿数与外齿轮齿数之差ZZ Z cb-=ε(3-1)称齿数差,一般取Z ε=1~4,齿数由齿数差和传动比确定.即:Z Zi cε=(3-2) 及Z Z Z cbε+=(3-3)齿数差与传动比地常用范围见下表 表3-1已知i=57 故取△Z=1 根据上述公式(3-1) (3-2) (3-3)可知外齿轮齿数571=Z内齿圈齿数582=Z选取标准齿形角α=20°,齿合角α′=20°,模数m=4,重合度εα=1.3,25.0,1**==ch a中心孔分度圆直径 mm mz d 23258422=⨯== 齿顶圆直径 mm m c h Z d a f 222)22(**22=--= 齿根圆直径 h d da a 2222+==mm m h Z a 240)2(*2=+取两侧环板齿宽b=30mm,则中间环板齿宽2b=60mm 3.2 齿轮地设计1、 由上述计算可知:571=Z ,α=20°,齿合角α′=20°,模数m=4,重合度εα=1.3,25.0,1**==c h a由公式 分度圆直径 d=mz1 (3-4)齿根圆直径 d=Z1-2h a* -2c* (3-5)齿顶圆直径 da1=d1+2h a1 (3-6) 可得h dda a 1112+==mmm h Z a 236)2(*1=+ mm m z d 22857411=⨯==mmm c h Z da f 218)22(**11=--=2、 材料及热处理取其整段结构,粗加工后调质处理42G rM o280-300HBσlim H =1079N/mm 2mm N FE 2/800=σ3、 齿轮精度按GB10095-88 7级精滚齿,装配后跑合研齿,齿面粗糙度mm R Rz aμμ162.352.3=⨯== 齿根5.313.653.6=⨯==R R z a m μ齿面接触率为70% 4、齿轮润滑选用中级压齿轮面220EP s mm V/200240=5、 齿面接触强度及齿根弯曲疲劳强度校核参考《机械设计手册》第2版(机械工业出版社)第四卷第35章所示方法进行校核(1) 齿面接触强度校核 min /5.1757/10001r n == 按表35.2-22bduu HH K K FZ Z Z H HVA tE H N αβεβσ)1(+=(3-7)圆周速度 V=sm d n/21.010060=⨯π 输出转矩T=10520N .m分度圆上地圆周力N N d F t 7.92280228.0/105202/21=⨯==π 查表5.3-24得许用系数1.1=A K 按式35.2-12计算动载系数11001221÷⎪⎪⎪⎪⎭⎫⎝⎛+=u uZ F K K KVt A Vb(3-8)由于齿轮精度为7级 按表35.2-31 0087.09.2321==K K 将有关数值代入上式得 23.1=V K 齿向载荷分布系数,查表35.2-2833.11201023.0)228/100(18.012.11023.0)/(18.012.13232=⨯⨯++=⨯⨯++=--b d b K H β齿面载荷分布系数,按:mmN mm N b K K tA 2/2.1348/100/)7.922805.1(/2=⨯= 查表35.2-30 得1.1=KH α节点区域系数H Z :按β=9°22′,x=0 查表35.2-14得 47.2=H Z查表35.2-31 8.189=E Z接触强度计算地重合度及螺距角系数Z εβ首先计算当量齿数查图35.2-10可得 66.183.083.083.083.04.60)98667.0(58cos 3.59)98667.0(57cos 21222221=+=========εεεαααββv V V Z Z Z Z按254/100/===m b mφβ=9°22′ 查图35.2-11纵向重合度55.1=εβ根据55.166.1==εεβαv β=9°22′查图35.2-15得 76.0=Z εβ将以上数值代入齿面接触应力计算公式得mm N H2/100835572281001.133.123.11.1)157(7.9228076.08.18947.2=⨯⨯⨯⨯⨯⨯+⨯⨯⨯⨯=σ按表35.2-22 计算安全系数σσHxW vvr N H HZ Z Z Z Slim =(3-9)式中,寿命系数Z N ,选计算应力循环次数N=60rnt=60×1×17.5×35000=3.68×107(3-10)对于调质钢(允许有一定蚀点)从图35.2-17中,按N=3.68×107查得 Z N=1.15工作硬化系数W Z 因为齿轮表面未硬化处理,齿面未光整,取Z W=1接触强度计算地尺寸系数Y X查图35.2-21得 Y X =1润滑油墨影响系数Zvvr,查图35.2-18得 95.0=Z vvr将以上数值代入安全系数地计算公式得17.15.10081195.015.11099=⨯⨯⨯⨯=S H查表35.2-38得 1.1min=S H 因为 S S H H min ≥ 故安全 (2)校核齿根弯曲疲劳强度按表35.2-22Y Y K K K K b FFSFFVAmtFεβαβσ=(3-11)式中,弯曲强度计算地载荷分布系数 33.1==KK H Fβχ弯曲强度计算地载荷分配系数 1.1==K K H F αα 复合齿形系数Y FS按4.603.5921==Z ZV V 查图35.2-22得92.395.321==Y YF F弯曲强度计算地重合度x 螺旋角系数按66.1=εαv β=9°22′ 查图35.2-26得 67.0=T εβ将以上各数值代入齿根弯曲应力计算公式得mmN F 2/41767.095.31.133.123.15.141687.92280=⨯⨯⨯⨯⨯⨯⨯=σ计算安全系数F S 按表35.2-22得σσσFxRreltreliNFEFY Y Y Y S /= 式中寿命系数,对于调质钢,根据图35.2-27按1068.37⨯=N 查得15.1=N Y 相对齿根圆角敏感系数Y reliσ 查表35.2-33 Y reli σ=1相对齿根表面状况系数Y Rrelt查表35.2-48 齿面粗糙度m R R a a μ6.121==按式35.2-21得 YRrelt=1尺寸系数Y x查图35.2-29得 Y x=1 将以上数值代入安全系数S F 地公式得:21.2417/11115.1800=⨯⨯⨯⨯=S F由表35.2-32取 6.1min=SFS SF Fmin> 故安全3.3输出轴地设计选择轴材料为45钢,调质处理. 1 初步估算轴径查《机械设计手册》第二版(机械工业出版社)中表38.1-1得45号钢地材料力学性能为 []MPa 155=τ []︒=5.1φ 根据表38.1-1公式初步计算轴径,由于材料为45号钢,由表38.3-2选A=107,则得mm n p A d 1.1085.176.2010733m in===2 轴地结构设计根据轴地受力选取深沟球轴承,主要承受径向载荷,同时也可承受一定量地轴向载荷.为了便于轴装配,取装轴承处直径mm mmd d 11612021== 装齿轮处地直径mm d 1203=3 轴承地润滑由于输出轴低速运转且承受较大地载荷,故可以选用脂润滑,且脂润滑不易流失,易密封,一次加脂可以维持相当长地一段时间,装脂量一般为轴承内部空间地1/3~2/3. 4强度校核mN T ∙=10520max[]MPa 155=τ1d 段:[]τπτ<=⨯===MPa D T W T t02.311612.014.3105201633max max max(3-12)段2d :[]τπτ<=⨯===MPa D T W T t34.3416116.014.3105201633max max max故满足要求 5刚度校核 G=80GPa []︒=5.1φd 1段:=⨯⨯=⨯=πππϕ180321804maxmax max D G T I G T p0.37°<[]φ(3-13)段2d :=⨯⨯=⨯=πππϕ180321804maxmax max D G T I G T p0.42°<[]φ故满足刚度要求第四章 三环减速器地动力学分析4.1内齿圈与外齿轮之间啮合力地分析 4.1.1啮合力地方向在一般地齿轮传动中,啮合力地方向是十分清楚地,无须再说.但在本问题中,因为内齿圈作平动,外齿轮作定轴转动,所以有深究地必要.在图4-1中,标号1指地是内齿圈;标号2指地是外齿轮,为简单计,假定讨论地是标准齿轮地标准啮合情况,即分圆也是节圆.P 点为节点,N-N 为啮合线,它与基圆1、2相切.M 1M 2线段为啮合区间.设压力角α=20°.图4-1 啮合点在节园外时外齿轮受力地方向图4-12啮合点在节园内时外齿轮受力地方向首先讨论啮合点Q 在M 1和P 两点之间地情况.因为内齿圈为平动,故内齿圈在啮合点Q 处地速度V V V BA==1;而外齿轮在啮合点Q 处地速度V 2地方向与2O Q 垂直,所以两齿面之间有相对滑动,考虑到磨擦力,所以啮合力F 与啮合线之间有一个夹角β,根据磨擦角地要概念有tan β=f或β=arctanf(4-1)式中,f 为磨擦系数.同理,当啮合点Q 在P 点M 2和之间,啮合力F 也和N-N 夹β角,只是在N-N 地另一侧(见图4-2).对于内啮合地少齿差机构,两齿廓地齿形极其相似(因齿廓地曲率半径极为接近),再加上弹性变形,所以同时参加啮合地齿数比较多.这样一来,几个啮合齿对地啮合力地合力地方向与啮合线N-N 极为接近.故此我们认为啮合力F(指合力)地方向与啮合线重合,即与节线T-T 夹α角.4.1.2啮合力地大小图4-3 计算啮合力F 大小地用图取内齿板AB 和曲柄OA 和O′B 为分离体.在其上作用有主动力—外加力偶矩M 和啮合力F,约束反力XO′、YO′和RO(见图4-3).因为曲柄OA 无外力偶驱动,它是二力构件,所以在固定铰支座O 点处,仅有一个约束反力,它地方向与OA 地方向相重合.由于内齿板在运动着,它作平动,其内齿圈地O 1作以2O 点为圆心、以O O 21=r 为半径地圆周运动.为分析简单计,假设它为匀速圆周运动,则1O 点地加速度地大小为r 2,方向指向2O 点.根据达朗倍尔原理,应该在内齿板上加上惯性力Rg,它加在1O 点上,方向与1O 点地速度方向相反(见图4-3).设内齿板(包括连杆AB 和内齿圈)地总质量为m,则惯性力Rg 地大小为 Rg=m r2ω(4-2)在所取地分离体上,XO′、YO′、RO′、F 这4个力为未知力.一般来说,有4个未知力是不能求解地.但应用理论力学中地虚位移原理可以克服这一困难.虚位移原理是,给系统一个虚位移,所有地主动力在虚位移上所做地虚功之和等于零.即1=∙=∑∑=r F WiiFni δδ (也称为虚功方程)(4-3)现给曲柄O′B 一个虚转角δϕ,则曲柄OA 也有一个虚转角δϕ.B 点地虚位移为δδϕrS B=.因为内齿板作平动,所以力Rg 和F 地作用点O1和C 点地虚位移与B 点地虚位移相同,即δδδδκrS S S BCO ===1(4-4)将式(4-5)代入式(4-4),注意到Rg 在O 1点地虚位移S O 1δ上作功等于零,于是得到=-αδδϕCOS S F M C即 0=∙-ϕϕδαδr FCOS M 得到αrCOS MF =(4-5)式(4-5)是一个极重要地公式,从它可以得出下面两点结论 1)内齿板地惯性力对啮合力无影响;2)当输入力偶矩M 为恒定时,啮合力F 地大小不变.至此,我们更可以想象得到,啮合力F 地作用点沿着内齿圈地节圆迅速地移动着,其角速度等于曲柄O′B 地角速度,但不论移动到哪里,F 地大小不变.以上所述就是我们作支座动反力分析地基础性工作.4.2 支座动反力在求出啮合力之后,求支座动反力XO′、YO′、和RO. ∑Mo′(F)=0M+Fcos α(acos φ+2r )+Fsin αasin φ-Rgasin φ-0R 2asin φ=0得Rga F a r a a F a M R 21sin 21sin 2)cos (cos sin 220-+++=ϕϕϕ考虑到式(5),并注意到r+2r =1r ,上式化为Rg a F a ar F a F R 21sin 21sin 2/cos sin /cos cos 2110-++=ϕϕϕ (4-6)从式(4-6)可以看出,支座反力0R 是很大地,特别是当φ=0和180°及其邻近地值,它接近无穷大,这是支座难以承受地.况且它是周期变化地,其频率与曲柄旋转地频率相同.这就是说,支座受到一个频率很高,振幅很大地激振力,这样地激振力势必造成机座乃至整个机械系统强烈地振动,导致支座轴承很快地破损和其他构件地断裂,同时也使整个系统产生极大地噪声———这就是三环减速器最突出地问题.接着分析支座O′地受力情况 ∑Y=00R sin φ-Fcos αcos φ-Fsin αsin φ+Rgsin φ+0Y =0y0=-0R sin φ+Fcos αcos φ+Fsin αsin φ-Rgsin φ将式(4-6)代入,经整理得Y =1/2F(cos αcos φαsin φ-cos αar 1)-1/2Rgsin φ(4-7) 列方程 ∑X=00R cos φ+Fcos αsin φ-Fsin αcos φ+Rgcos φ-0X =00X =0R cos φ+Fcos αsin φ-Fsin αcos φ+Rgcos φ将式(4-6)代入,经整理得0X =1/2F(cos αcos φ/sin φ+cos α1r /asin φ-sin α)cos φ+Fcos αsin φ/2Rgcos φ(4-8)以上所导出地式(4-6)、式(4-7)、式(4-8)3式就是求支座动反力地计算公式.选定地设计参数为模数m=4,压力角α=20°,Z 1=57,2Z =58,α=300mm;驱动电机地额定功率P=20.6kW,转速n=1000r/min.另外设内齿板地总质量m=20kg. 由此可计算出内齿圈分圆半径mm mz r 114574212111=⨯⨯==曲柄长度mm z z m r 2)(2112=-=曲柄驱动力矩M=1/3×9549×N /n=1/3×9549×20.6/1000=65.57N·m 啮合力F=M/rcos α=65.57/0.002×0.94=N 105.34⨯内齿板惯性力Rg=mr 2ω =20×0.002×)2601000(2π⨯ =438.23N在这里,计算曲柄驱动力矩时我们作了一个假定,即假定电机输入地驱动功率是被3个曲柄均分地.这个假定地合理性是基于不论内齿板运行到什么位置,啮合力F 大小始终保持不变(见前面地结论),即内齿圈输送给外齿轮地功率与内齿板运行到什么位置无关.将以上数据代入式(4-6),且令曲柄O′B 旋转一周,计算出支座反力0R 地数值如表4-1并绘出图线(图4-5).在图4-5中所示出地支座动反力0R 地值是机构中三环中地一环所引起地.实际上支座O 点地总地反力是三环共同作用地结果,而这3个反力作用地方向和大小都是不一样地.我们特别关注φ=0°和φ=180°邻域这两个位置支座0点地动反力.下面以φ=0°(及其邻域)为例详细说明之.当其中一环为φ=0°时,而其他两环地位置角分别为φ=120°和φ=240°.根据图4-5做出3个反力地矢量图如下表4-1 支座动反力F0随φ角变化地数值表图4-4 φ角地运行角度(即B点地位置)图4-5 在一周内支座反力R0地变化图线图4-6 三环共同运转O支座反力矢量图图4-6中, 0R (1)是其中一环φ=0°时所引起地反力,而0R(2)和0R(3)是另外两环运转所引起地反力.从图4-4地附表和图4-5中可以看到, 0R(1)非常大,且符号为正, 0R (2)=-4660N,R0(3)=-4452N.在这里我们特别提请读者注意地是,要从图中充分理解0R(1)、0R(2)和0R(3)地正负所代表地指向.从图中可以看出,3个反力共同地结果不但没有削弱了R0(1),反而加大了0R(1),这就说明了有地文献说三环共同作用改善了机构运行地平衡性是不正确地(而人们也容易是这样想象地).这也正是目前已经做出地三环减速机所存在地缺陷.为了克服这一缺陷,人们可以想出各种办法.4.3改进方案改进方案地基本思想是双边驱动,即在支座O和O′设置功率相等地电机驱动,并假设分配3个内齿板地曲柄地驱动力偶矩是相等地.下边拿出其中一个内齿板进行受力分析.图4-7 双边驱动分析支座动反力用图在图4-7中,我们取了3个分离体---两个曲柄和一个内齿板.首先考虑曲柄地受力情况.由于曲柄地重量很小而且长度很短,故可忽略它地转动惯量和惯性力.从图4-7中可以得到r M R F R F b A 2)(0)()(0)(====ττττ (4-8) 为寻求R )(0τ和R )(0τ,取内齿板AB 为分离体,应用动静法,虚加惯性Rg 后列静力平衡方程∑B M (F)=0Fcos α(acos φ+r 1)+Fsin αasin φ-Rgasin φ0cos 2sin 2)(=-φφττa a F F A A )(得到)(τA F =φφφφφτsin cos 212sin sin 2)cos (cos )(1F r A Rg F a a a F --++ (4-9)有a F r M F A cos 212)(==τ (4-10)将式(11)代入式(10)并进行整理,得到Rg a F a a F r F A 21sin 21sin 2cos 1)(-+=φτ (4-11)可以看出, F A )(τ比R 0少了一项1/2Fcos αcos φsin φ,而这一项是比重最大地一项.这就说明,采用双曲柄驱动,支座动反力将大幅度地减小.第五章 传动效率地计算三环减速器总效率含机构啮合,轴承和搅油等影响功率地损失.公式为:ηηηη321=1 机构地啮合效率:g i g ϕϕη+-=111 (5-1) 其中内啮合损失系数)11(10Z Z E g -=πμϕ 式中μ:齿面摩擦系数,当很好地润滑并经充分磨合时μ=0.005~0.007 E :系数 由于3.18.021==ςς 所以 5.08.03.112=-=-=ςςE 故0003.0)581571(5.006.014.3=-⨯⨯=g ϕ 所以96.00003.05710003.01111=⨯+-=+-=g i g ϕϕη2 转臂轴承效率η2 按下面公式计算:由于双输入驱动 []c d d i b +-=αμηcos 86.0102 (5-2) 式中d —滚动轴承直径 d=260mmμ—短圆住滚动地轴承摩擦系数 μ=0.0011~0.0015这里取μ=0.0012d b 0__内齿轮分度圆直径 d b 0=228mm则[]98.03020cos 86.022********.05712=+⨯⨯-=μ 3 搅油等损失影响效率η3搅油等损失与润滑方式,油位,油质,载荷及转速有关系,对于满载运转时可取 3η=0.99由此可得传动效率ηηηη321==0.96×0.98×0.99=0.925=92.5%(5-3)第六章 热功率平衡地计算三环减速器因单位体积承载能力较大,箱体体积相对较小,机壳外表散热面积也相对偏小,故当处于长时间连续运转时,需要作热功率计算,即按热平衡条件计算许用地热功率t P 应大于输入功率P热平衡公式 P S K P t t ≥--=)1(1000)max (ηθθ (6-1)式中t K ——传热系数,自然通风t K =8.7~17.5W/(2W °C)这里取t K =17.5 W/(2W °C) S ——散热面积,箱体、凸圆和肋板面积,按1/2计算,通用系列三环减速器地)(1622m a S = 本设计中a=0.3m 则)(1622m a S ==1.442mmax ϑ——许用温度,可达80℃,这里取80℃θ——环境温度,约20℃,这里取20℃η——三环减速器满载时地总效率,当非满载时,效率η及热功率t P 均要降低,而满载时,由于双轴输入且△Z=1,571=Z 由上面计算得η=92.5%故KW S K P t t 16.21)925.01(1000)2080(44.15.17)1(1000)max (=--⨯⨯=--=ηθθ 设计要求三环减速器地额定功率P=20.6KW这里t P >P 故热平衡合格第七章三环减速器地改进方案老式三环式减速器运行时振动普遍较大,并随传动比地增大及功率地增加而加剧,严重时导致环板断裂,轴承发热失效,缩短了减速器地使用寿命,丧失其优越性,使其推广应用受到了限制. 新型三环式少齿差齿轮减速器就是针对生产中地这些实际问题而开发和研制地.新型三环式减速器地结构见图7-1. 电机轴上地小带轮通过啮合传动,带动同步带运动,同步带再通过啮合传动,带动两大带轮同步旋转,实现一级减速、均载和功率分流. 相同地大带轮使三环式减速器地曲柄轴同步旋转,传动环板上地内齿圈与输出轴上地外齿轮相啮合,形成了大传动比,实现了二级减速及动力传递. 三环式减速器轮齿啮合地均载、减振由油膜浮动方案实现. 采用平顶圆弧齿同步带传动作为一级减速进行功率分流并形成双轴输入以克服死点,同时,增加减速器地传动比,内齿环板地运动速度下降,减速器在重载高速地条件下,环板引起地振动较小.1.电机轴;2.小带轮;3,4.圆弧齿同步齿形带;5,6.大带轮;7,8.曲柄轴;9,10,11.传动环板;12.输出轴;13.外齿轮;14.箱体图7-1 三环式减速器结构原理新型三环式减速器工作原理及特点:1、完全平衡在用地三环式少齿差减速器由3块相同地内齿环板并列地呈120°相位差运。
减速器的整体设计项目设计方案

减速器的整体设计项目设计方案1、减速器概述1.1、减速器的主要型式及其特性减速器是一种由封闭在刚性壳体的齿轮传动、蜗杆传动或齿轮—蜗杆传动所组成的独立部件,常用在动力机与工作机之间作为减速的传动装置;在少数场合下也用作增速的传动装置,这时就称为增速器。
减速器由于结构紧凑、效率较高、传递运动准确可靠、使用维护简单,并可成批生产,故在现代机措中应用很广。
减速器类型很多,按传动级数主要分为:单级、二级、多级;按传动件类型又可分为:齿轮、蜗杆、齿轮-蜗杆、蜗杆-齿轮等。
1.1.1 圆柱齿轮减速器当传动比在8以下时,可采用单级圆柱齿轮减速器。
大于8时,最好选用二级(i=8—40)和二级以上(i>40)的减速器。
单级减速器的传动比如果过大,则其外廓尺寸将很大。
二级和二级以上圆柱齿轮减速器的传动布置形式有展开式、分流式和同轴式等数种。
展开式最简单,但由于齿轮两侧的轴承不是对称布置,因而将使载荷沿齿宽分布不均匀,且使两边的轴承受力不等。
为此,在设计这种减速器时应注意:1)轴的刚度宜取大些;2)转矩应从离齿轮远的轴端输入,以减轻载荷沿齿宽分布的不均匀;3)采用斜齿轮布置,而且受载大的低速级又正好位于两轴承中间,所以载荷沿齿宽的分布情况显然比展开好。
这种减速器的高速级齿轮常采用斜齿,一侧为左旋,另一侧为右旋,轴向力能互相抵消。
为了使左右两对斜齿轮能自动调整以便传递相等的载荷,其中较轻的龆轮轴在轴向应能作小量游动。
同轴式减速器输入轴和输出轴位于同一轴线上,故箱体长度较短。
但这种减速器的轴向尺寸较大。
圆柱齿轮减速器在所有减速器中应用最广。
它传递功率的围可从很小至40 000kW,圆周速度也可从很低至60m/s一70m/s,甚至高达150m/s。
传动功率很大的减速器最好采用双驱动式或中心驱动式。
这两种布置方式可由两对齿轮副分担载荷,有利于改善受力状况和降低传动尺寸。
设计双驱动式或中心驱动式齿轮传动时,应设法采取自动平衡装置使各对齿轮副的载荷能得到均匀分配,例如采用滑动轴承和弹性支承。
减速器设计(减速机草图设计)

机电工程系
金守宽
一、传动整体方案设计
已知各轴:P n T i
二、传动零件设计
1. 确齿轮传动几何尺寸计 算 模数: m=4mm 齿数: 压力角: 中心距: Z1=18、Z2=82
a==m.Z2
齿宽:
b1=90mm、b2=80mm
l1=90
4. 滚动轴承的选择
5. 键的选择与强度计算
6. 联轴器的选择
B h
d
d1
d2
d3
d4 d 5
弹性套柱销联轴器
三、减速器草图绘制
定基线,布置图面 中心距:a=200
箱座高度:200=H由油面深度计算确定
估算轴径:d1=23,d2=38
d=0.025a+1≥8=9 D1=10 D2=10
d1—带轮孔径为依据
d2—定位轴肩h
d1=32 d2=38 d3=40
D1=10
b1=90
d3—以选择轴承公径 d4—轴承定位轴肩h d—小齿轮节圆 轴承—0308
d4=49
d=
D2=20
D2=20
完成轴系结构、尺寸:(高速轴)轴向祥图
l1—带轮孔径长为依据
l=15(18)
l2—绘图+计算 B—轴承宽度(0308) lc—端盖长度(查表) D1—箱内距离
箱体螺栓:(0.5~0.6)df M10*4
c2 c1 c1 c2
端盖螺钉:(0.4~0.5)df M6 C1,C2—由查表
箱体结构设计:结构细化
目录
课程内容
箱体尺寸计算:
箱体尺寸计算:
箱体结构设计:设计油标,放油孔
箱体结构设计:细化定结构、画剖面线
箱体结构设计:完成左视图
减速机设计

减速机设计-CAL-FENGHAI-(2020YEAR-YICAI)_JINGBIAN一、设计计算:(一)传动装置的总体分析1、拟定传动方案传动装置的设计方案一般用运动简图表示。
它直观地反映了工作机、传动装置和原动机三者间的运动和力的传递关系。
满足工作机性能要求的传动方案,可以由不同传动机构类型以不同的组合形式和布置顺序构成。
合理的方案首先应满足工作机的性能要求,保证工作可靠,并且结构简单、尺寸紧凑、加工方便、成本低廉、传动效率高和使用维护便利。
一种方案要同时满足这些要求往往是困难的,因此要通过分析比较多种方案,选择能满足重点要求的较好传动方案。
如图所示带式运输机的四种传动方案示意图:方案一:采用V带传动与齿轮传动的组合,即可满足传动比要求,同时由于带传动具有良好的缓冲、吸振性能,可适应大起动转矩工况要求,结构简单,成本低,使用维护方便。
缺点是传动尺寸较大,V带使用寿命较短。
方案二:传动效率高,使用寿命长,但要求大起动力矩时,起动冲击大,使用维护较方便。
方案三:能满足传动比要求,但要求大起动力矩时,链传动的抗冲击性能差,噪音大,链磨损快寿命短,不易采用。
方案四:传动效率高,结构紧凑,使用寿命长。
当要求大起动力矩时,制造成本较高。
以上四种传动方案都可满足带式输送机的功能要求,但其结构性能和经济成本则各不相同,一般应由设计者按具体工作条件,选定较好的方案。
常用传动机构的布置原则:(1)带传动的承载能力较小,传动平稳,缓冲吸振能力较强,宜布置在高速级。
(2)链传动运转不均匀,有冲击,宜布置在低速级。
(3)蜗杆传动效率较低,但传动平稳,当与齿轮副组成传动机构时,宜布置在高速级。
(4)、开式齿轮传动的工作环境一般较差,润滑条件不好,因而磨损严重,寿命较短,应布置在低速级。
(5)斜齿轮传动的平稳性较直齿轮传动好,常用在高速级或要求传动平稳的场合。
2、电动机选择(1)选择类型和结构形式一般选用系列三相异步电动机。
- 1、下载文档前请自行甄别文档内容的完整性,平台不提供额外的编辑、内容补充、找答案等附加服务。
- 2、"仅部分预览"的文档,不可在线预览部分如存在完整性等问题,可反馈申请退款(可完整预览的文档不适用该条件!)。
- 3、如文档侵犯您的权益,请联系客服反馈,我们会尽快为您处理(人工客服工作时间:9:00-18:30)。
摘 要分析内平动齿轮传动的原理,提出由 3 根偏心轴作平动发生器的实用新型齿轮传动机 构一分流型内平动齿轮传动,并推导其传动比的计算公式.主要零件部件的计算设计.装置的 装配设计和主要零件的设计。
分析内平动齿轮传动的原理,提出由3根偏心轴作平动发生器的实用新型齿轮传动机 构一分流型内平动齿轮传动, 并推导其传动比的计算公式.分析发现, 为平衡机构的惯性力, 采用2(或3)片平动齿轮时,设计啮合点相位差应取180° (120°);输入齿轮的齿数为3的倍 数时,分流齿轮具有互换性;采用两片平动齿轮且内外齿轮齿数差为偶数时,平动齿轮具 有互换性;采用3片平动齿轮且内齿轮齿数为 3的倍数时,平动齿轮具有互换性.给出了啮 合参数的编程计算方法.该新型传动具有承载能力强、 传动比大(17—300)、 体积小、 质量轻、 输入输出同轴线、加工安装简单等优点,是一种节能型的机械传动装置,也是减速器的换 代产品.有广泛的应用前景。
关键词 :内平动齿轮传动;少齿差齿轮副;传动比AbstractAnalysis of parallel move gear transmission principle, put forward by the three eccentric shafts for utility model translation generator gear mechanism within the translation of a shunttype gear, and derive the formula for calculating the transmission ratio. The main components of the calculation of design components . Device design and assembly of major parts of the design.Analysis of parallel move gear transmission principle, put forward by the three eccentric shafts for utility model translation generator gear mechanism within the translation of a shunttype gear, and derive the formula for calculating the transmission ratio. Analysis, to balance the inertia force, using 2 (or 3) pieces of translation gear, the meshing point of the design phase should take 180 ° (120 °); input gear teeth as a multiple of 3, the shunt gear with interchangeability; with two translation gear and the internal and external gear tooth number difference is even, Ping gear has interchange ability; with three flat gear and internal gear teeth as a multiple of 3, the flat gear has interchangeability. Meshing parameters given programming account Calculation method. The new drive has a carrying capacity, transmission ratio (17300), small size, light weight, input and output coaxial line, and simple installation process is an energyefficient mechanical transmission device, is also a new generation product reducer . Have broad application prospects.Keywords: Internal translation gear transmission;differential gears with small teeth; transmission ratio目录摘 要 (I)Abstract (II)目录 (III)1 绪论 (1)1.1 平动减速器的发展概况 (1)1.2 市场需求分析 (1)1.3 本课题研究目的及意义以及国内外现状分析及展望 (1)1.4 课题的主要内容及要求 (1)2 传动方案及拟定 (3)2.1 平动啮合的定义和分类 (3)2.2 内平动齿轮传动工作原理 (3)2.4 分流式内平动齿轮传动机构 (4)2.5 传动比分析 (5)3 各主要部件选择及选择电动机 (7)3.1 各部件的选择 (7)3.2 电动机的选择 (7)4 减速器的整体设计 (8)4.1传动比的分配 (8)4.2传动的运动及动力参数计算 (8)4.3齿轮的设计计算 (8)4.3.1 分流齿轮的设计计算 (8)4.3.2 平动齿轮的设计计算 (12)4.4轴的设计计算 (15)4.4.1 输入轴的设计计算 (15)4.4.2 曲轴的设计计算 (19)4.4.3 输出轴的设计计算 (24)5 润滑与密封 (28)5.1润滑方式的选择 (28)5.2密封方式的选择 (28)5.3润滑油的选择 (28)6 箱体结构尺寸 (29)6.1箱体的结构尺寸 (29)7 设计总结 (30)致 谢 (32)参 考 文 献 (33)1 绪论1.1 平动减速器的发展概况随着科技技术的进步和发展,现代工业设备特别需要功率大 体积小 传动比范围大 效率高 承载能力强和使用寿命长的传动装置。
因此,除了不断改进材料品质 提高工艺水 平外,还要在传动原理和传动结构上深入探讨和创新,内平动齿轮传动原理的出现就是一 例。
它由北京理工大学张春林教授等人最先提出, 并设计出了内平动齿轮减速器试验样机。
该减速器属于节能型传动装置,除具有三环减速器的优点外还有着大的功率与重量比值 输入轴和输出轴在同一轴线上 既可以减速还可以增速以及震动小等优点,处于国内领先 地位。
最先提出平动齿轮这一概念的是德国人,他们提出了摆线针轮行星齿轮传动原理。
由 于工艺和精度的限制,这种机构并没有快速发展起来,直到摆线磨床的出现。
近些年国外 在平动齿轮传动领域进行了一些新的研究,如日本住友重工研制的 FA 型高精度减速器和 美国 AlanNewton公司研制的X Y减速器,就利用了平动齿轮传动的运动机理。
对平动齿轮传动研究,我国处于相对领先的地位。
目前,平动齿轮的理论研究 机构 设计和实验研究都取得了一些成果。
例如:北京理工大学张春林教授 黄祖德教授等首次 根据该传动的特点将其命名为平动齿轮传动机构。
并通过对平动齿轮传动机构的运行机理 进行分析研究,阐述了该机构的组成及机构变异方法,探讨了平动齿轮机构传动比和机械 效率的计算方法,导出了计算公式,得出了平动齿轮机构效率与齿轮齿条传动机构 效率 相当的结论。
此后又根据机构的组合原理 演绎原理和同性异性变异原理对内平动齿轮机 构的基本型进行演化变异, 设计出一种传动比大, 机械效率高 尺寸和重量小 结构紧凑 均 载性好的新型平动此轮机构,并对平动齿轮传动机构连续运动条件及重合度方面进行了深 入研究。
1.2 市场需求分析用于冶金、矿山、机械、机器人、航海、轻工、航空、军工、纺织、化工、建筑等部 门,亦可与各类电机直接联接,作成伺服电机。
1.3 本课题研究目的及意义以及国内外现状分析及展望内平动齿轮减速器是一种新型的机械传动装置,它传动比大,机械效率高,结构简单, 体积小,重量轻,能方便地与电机配套使用,避免了减速器体积比电机体积大的现象。
该 减速器是一种节能型的机械传动装置,具有国际先进水平。
传动比可达到几千;机械效率 大于90%;运转平衡性好,承载能力大,使用寿命长,体积小,重量轻,约为相似产品的 1/3左右。
1.4 课题的主要内容及要求主要研究内容:提出由3根偏心轴作平动发生器的实用新型齿轮传动机构一分流型内 平动齿轮传动,并推导其传动比的计算公式。
分析发现,为平衡机构的惯性力,采用2(或 3)片平动齿轮时,设计啮合点相位差应取 180。
(120。
);输入齿轮的齿数为 3 的倍数时, 分流齿轮具有互换性;采用两片平动齿轮且内外齿轮齿数差为偶数时,平动齿轮具有互换 性;采用3片平动齿轮且内齿轮齿数为 3的倍数时,平动齿轮具有互换性。
给出了啮合参 数的编程计算方法。
该新型传动具有承载能力强、传动比大(17—300)、体积小、质量轻、输入输出同轴线、加工安装简单等优点,有广泛的应用前景。
2 传动方案及拟定2.1 平动啮合的定义和分类在齿轮传动中,一对相互啮合的齿轮,其中一个定轴转动,另一个做平动,称之为平动啮合,平动啮合主要分为两类:内平动和外平动。
2.2 内平动齿轮传动工作原理内平动齿轮传动机构中,外齿轮在平动发生器的驱动下作平面运动,通过外齿轮与内齿 轮齿廓间的啮合,驱动内齿轮作定轴减速转动,起到减速传动的作用。
如图所示,图 21 所示 为内平动齿轮机构工作原理图"该机构的平动发生器为平行四边形机构 ABCD,外齿轮 l 固 接在平行四边形机构的连杆BC的中心线上,当曲柄AB转动时,它随同连杆作平面运动,并驱 动内齿轮2作减速转动输出。
图 2.1 内平动原理示意图2.3 平动发生机构3 点确定唯一的一个平面,为能够平稳地为平动齿轮提供动力,采用 3 个曲柄 O1A, O2B,O3C 驱动平动齿轮作平动,如图 22 所示.图 22 中,曲柄长度 e 与内齿轮副的中心 距相等,O1A∥ O2B ∥ O3C,O1O2 ∥AB,0203 ∥ BC,O3O4 ∥ CA,构成3个平行四 边形机构: □O1ABO2,□ O2BCO3, □ O3CAOl.若采用单个平行四边形机构作为平动发 生器,单轴输入时,另一轴会出现运动不确定现象.而采用这种结构不仅能优化各曲柄的受 力,同时也能够有效地避免出现曲柄的运动不确定。