浅析小直径回转体零件变薄拉深时的底厚变化情况
4-1拉深过程分析(模具设计与制造)

2021/1/14
教育部十一五规划教材《模具设计与制造》
第4章 拉深工艺与拉深模具
绪论
用拉深方法来制造薄壁空心件,生产效率 高,材料消耗小,零件的强度和刚度高,而 且工件的精度也较高。拉深件的加工范围非 常广泛,从几毫米的小零件直至轮廓尺寸达2 ~ 3 m,厚度为200 ~ 300 mm的大型零 件。因此,在汽车、拖拉机、航宇航天、国 防、电器、仪表、电子等工业部门以及日常 生活用品生产中,拉深成形占据相当重要的 地位。
2021/1/14
教育部十一五规划教材《模具设计与制造》
第4章 拉深工艺与拉深模具
4.1.2 拉深件与拉深模的分类
(3)在单动压力机上工作的拉深模,按拉深 工序又可分为首次拉深模和再次拉深模。
(4)按有无压边装置可分为有压边装置拉深 模和无压边装置拉深模。
(5)一般板料的拉深要经过数道拉深工序才 能完成,一副拉深模一般只能完成一道拉深 工序,所以拉深模多为单工序模。较复杂拉 深件可采用落料拉深复合模等。
2021/1/14
教育部十一五规划教材《模具设计与制造》
第4章 拉深工艺与拉深模具
4.1.1拉深过程分析 b图表示有压边的拉深过程。
2021/1/14
教育部十一五规划教材《模具设计与制造》
第4章 拉深工艺与拉深模具
4.1.1拉深过程分析
拉深凸模和凹模与冲裁模
不同的是其工作部分没有锋
利的刃口,而是分别有一定
2021/1/14
教育部十一五规划教材《模具设计与制造》
第4章 拉深工艺与拉深模具
4.1.2 拉深件与拉深模的分类
2.拉深工艺分类 拉深工艺可分为不变薄拉深和变薄拉深两
种。后者在拉深后的零件壁部厚度与毛坯厚度 相比较,有明显变薄。生产中主要应用不变薄 拉深。
网目实验法分析拉深件侧壁厚度变化规律

网目实验法分析拉深件侧壁厚度变化规律0 引言用平面板坯制作杯形件的冲压成形工艺﹐又称拉延。
通过拉深可以制成圆筒形﹑球形﹑锥形﹑盒形﹑阶梯形﹑带凸缘的和其他复杂形状的空心件。
采用拉深与翻边﹑胀形﹑扩口﹑缩口等多种工艺组合﹐可以制成形状更复杂的冲压件。
冲压的本质是利用模具和冲压设备使金属板坯料产生塑性流动D 从而使其发生所需要的形状改变。
弯曲、拉深、翻边、翻孔、胀形、扩口、缩口和旋压等是冲压所涵盖的几种基本工艺过程、其中拉深是将板料毛坯在具有一定圆角半径的凸5 凹模作用下加工成各类零件的工艺手段,它在汽车、仪表、航天等领域均有广泛应用。
在拉深成形过程中,通常需要安装压边装置产生摩擦抗力,以增加板料中的拉应力,控制材料的流动D 避免起皱。
[1]拉深是板料成形中的一种重要工艺方法,广泛应用于汽车、航空航天、家用电器制造等方面。
拉深时,板料的壁厚会发生变化,在拉深件的口部增厚, 筒底发生变薄, 在筒底圆角处变薄量最大。
如果壁厚变化太大, 拉深件的强度会降低,不但影响拉深件的使用性能,而且壁部最薄的地方在拉深过程中,由于最大拉应力超过材料的强度极限,材料将被拉裂,造成产品报废。
[2]1网目实验法2壁厚2.1摩擦因数与拉深件最大壁厚变薄率的关系表4是在其他参数固定的情况下, 计算得到的在不同摩擦因数的情况下,拉深件的壁厚最大变薄率。
分析表4中的数据可以得出, 摩擦因数与拉深件最大壁厚变薄率的关系如图2所示。
从图2可以看出,在其他参数固定,凸模、凹模和压边圈的摩擦因数取值相同的情况下, 工件最大壁厚变薄率与摩擦因数呈线性增长关系,但增长幅度并不大。
而当凸模与坯料接触面的摩擦因数取为0.25, 凹模和压边圈与坯料接触面的摩擦因数取为 0.1 时, 拉深件的最大壁厚变薄率为8.99%, 远小于凸模、凹模、压边圈的摩擦因数都为0.08 的最大壁厚变薄率10.13%。
因此, 要求在模具设计与制造时,压边圈、凹模与坯料接触的工作面的粗糙度应小些,尽量光滑平整, 降低拉深过程中的阻力;凸模工作面应做得比较粗糙些, 以增大凸模与板料之间的摩擦力,阻止危险断面的发生。
拉深工艺及拉深模具设计复习题答案

第四章拉深工艺及拉深模具设计复习题答案一、填空题1.拉深是是利用拉深模将平板毛坯压制成开口空心件或将开口空心件进一步变形的冲压工艺。
2.拉深凸模和凹模与冲裁模不同之处在于,拉深凸、凹模都有一定的圆角而不是锋利的刃口,其间隙一般稍大于板料的厚度。
3.拉深系数m是拉深后的工件直径和拉深前的毛坯直径的比值,m越小,则变形程度越大。
4.拉深过程中,变形区是坯料的凸缘部分。
坯料变形区在切向压应力和径向拉应力的作用下,产生切向压缩和径向伸长的变形。
5.对于直壁类轴对称的拉深件,其主要变形特点有:(1)变形区为凸缘部分;(2)坯料变形区在切向压应力和径向拉应力的作用下,产生切向压缩与径向的伸长,即一向受压、一向收拉的变形;(3)极限变形程度主要受传力区承载能力的限制。
6.拉深时,凸缘变形区的起皱和筒壁传力区的拉裂是拉深工艺能否顺利进行的主要障碍。
7.拉深中,产生起皱的现象是因为该区域内受较大的压应力的作用,导致材料失稳_而引起。
8.拉深件的毛坯尺寸确定依据是面积相等的原则。
9.拉深件的壁厚不均匀。
下部壁厚略有减薄,上部却有所增厚。
10.在拉深过程中,坯料各区的应力与应变是不均匀的。
即使在凸缘变形区也是这样,愈靠近外缘,变形程度愈大,板料增厚也愈大。
11.板料的相对厚度t/D越小,则抵抗失稳能力越愈弱,越容易起皱。
12.因材料性能和模具几何形状等因素的影响,会造成拉深件口部不齐,尤其是经过多次拉深的拉深件,起口部质量更差。
因此在多数情况下采用加大加大工序件高度或凸缘直径的方法,拉深后再经过切边工序以保证零件质量。
13.拉深工艺顺利进行的必要条件是筒壁传力区最大拉应力小于危险断面的抗拉强度。
14.正方形盒形件的坯料形状是圆形;矩形盒形件的坯料形状为长圆形或椭圆形。
15.用理论计算方法确定坯料尺寸不是绝对准确,因此对于形状复杂的拉深件,通常是先做好拉深模,以理论分析方法初步确定的坯料进行试模,经反复试模,直到得到符合要求的冲件时,在将符合要求的坯料形状和尺寸作为制造落料模的依据。
二拉深变形拉深件主要质量问题凸缘变形区的起皱

不变薄拉深: 把毛坯拉压成空心体,或者把空心体拉压成外形更小而板厚没有明显变化 的空心体的冲压工序。 变薄拉深是指凸、凹模之间间隙小于空心毛坯壁厚,把空心毛坯加工成侧 壁厚度小于毛坯壁厚的薄壁制件的冲压工序。 拉深是冲压基本工序之一。可以加工旋转体零件,还可加工盒形零件及其 它形状复杂的薄壁零件。 拉深使用设备:单动、双动、三动压力机或液压机
子弹(弹壳为大批量连续拉深(含变薄拉深))
二
拉深件主要质量问题
拉深变形
拉深过程中的质量问题:主要是凸缘变形区的起皱和筒 壁传力区的拉裂。
凸缘区起皱:由于切向压应力引起板料失去稳定而产生 弯曲;
传力区拉裂:由于拉应力超过抗拉强度引起板料断裂。
二 拉深变形
拉深件主要质量问题 1 凸缘变形区的起皱
毛坯凸缘拉深时应力、应变及起皱
四 落料拉深复合模
落料、正、反拉深模(实物)
谢谢!
拉深 不变薄拉深 变薄拉深
拉深模:拉深工序所使用的模具。 拉深模特点:结构相对较简单,与冲裁模比较,工作部分有较大的圆角, 表面质量要求高,凸、凹模间隙略大于板料厚度。
常见拉深零件
拉深件示例
不规则件多次拉深
拉深实例零件
不变薄拉深件
变薄拉深件
拉深实例零件
不锈钢餐具(深拉深件)
油底壳(复杂拉深件)
பைடு நூலகம் 二 拉深变形
拉深件主要质量问题
2
筒壁的拉裂
三 常用拉深模结构
(一) 首次拉深模 1 带压边装置的首次拉深模
带压边圈正装首次拉深模
带锥形压边圈的倒装拉深模
三 常用拉深模结构
(一) 首次拉深模 2 带压边装置的首次拉深模
压边装置
弹性压边装置
精选拉深变形过程及拉深工艺

(2)材料流过凹模圆角半径产生弯曲变形的阻力 可根据弯曲时内力和外力所作功相等的条件按下式计算: (3)材料流过凹模圆角后又被拉直成筒壁的反向弯曲力仍按式上式进行计算: 拉深初期凸模圆角处的弯曲应力也按上式计算,即:
(4)材料流过凹模圆角时的摩擦阻力 通讨凸模圆角处危险断面传递的径向拉应力即为: 由上式把影响拉深力的因素,如拉深变形程度,材料性能,零件尺寸,凸、凹模圆角半径,压边力,润滑条件等都反映了出来,有利于研究改善拉深工艺。 拉深力可由下式求出:
(2)计算拉深次数 例如: 可知该零件要拉深四次才行 。半成品尺寸确定 (1)半成品直径 拉深次数确定后,再根据计算直径 应等于 的原则对各次拉深系数进行调整,使实际采用的拉深系数大于推算拉深次数时所用的极限拉深系数。
图4.2.3 锥形凹模
1-首次拉深; 2-二次拉深图 4.2.4 首次拉深与二次拉深的拉深力
4.2.3无凸缘圆筒形拉深件的拉深次数和工序件尺寸的计算 试确定如下图所示零件(材料08钢,材料厚度 =2mm)的拉深次数和各拉深工序尺寸。 计算步骤如下:1.确定切边余量 根据 ,查教材表4.2.1,并取: 。2.按教材表4.2.3序号1的公式计算毛坯直径
3.确定拉深次数 ⑴ 判断能否一次拉出 对于图示的零件,由毛坯的相对厚度: 从表 4.2.4中查出各次的拉深系数 : =0.54, =0.77, =0.80, =0.82。则该零件的总拉深系数 。 即 : ,故该零件需经多次拉深才能够达到所需尺寸。
2.拉裂 拉深后得到工件的厚度沿底部向口部方向是不同的(如图4.1.9) 防止拉裂: 可根据板材的成形性能,采用适当的拉深比和压边力,增加凸模的表面粗糙度,改善凸缘部分变形材料的润滑条件,合理设计模具工作部分的形状,选用拉深性能好的材料。3.硬化 拉深是一个塑性变形过程,材料变形后必然发生加工硬化,使其硬度和强度增加,塑性下降。 加工硬化的好处是使工件的强度和刚度高于毛坯材料,但塑性降低又使材料进一步拉深时变形困难。
材料拉深

第4章 拉 深
• 把平面毛坯拉压成空心体,或者把空心体拉压成外形更小而 板厚没有明显变化的空心体的冲压工艺叫拉深,可分为普通 拉深和变薄拉深,拉深属于成形工序。 • 拉深工艺可分为不变薄拉深和变薄拉深两类,变薄拉深应用 较少,本章主要讨论不变薄拉深。 • 用拉深方法可以制成筒形、阶梯形、盒形、锥形、球形和其 它各种不规则形状的薄壁零件,生产效率高、精度较高、材 料消耗少、零件的强度和刚性较高,因而,在电子、电器、 仪表、汽车、航空、以及日常生活用品中,拉深工艺占居相 当重要的地位。
• d1=m1D • d2=m2d1 • …… • dn=mndn-1
• • (2)工序件圆角半径的确定,圆角半径确定方法将在本章第六节详细讨论。 (3)工序件高度的计算,根据无凸缘圆筒形件毛坯尺寸的计算公式推导出各次 工序件高度的计算公式为:
见公式(4-12)
4.3.5 带凸缘圆筒形件拉深方法及工序件尺寸的确定
4.3 圆筒形件的拉深系数和拉深次数的确定
• 4.3.1 拉深系数及其极限
• 拉深变形程度的大小可以用拉深件的高度和直径的比值,即相对高度 表示,比值小的变形程度小,比值大的变形程度大。 • 但在模具设计时,为了确定拉深次数,通常用拉深系数作为计算的依 据。拉深系数是以拉深后的直径与拉深前的毛坯(工序件)直径之比 d1 表示(图4-7)即 第一次拉深系数
4.3.2 影响极限拉深系数的因素
•
极限拉深系数的数值取决于筒壁传力区最大拉应力与危险断面的抗 拉强度。因此,凡是影响筒壁传力区的最大拉应力和危险断面的抗拉 强度的因素都会影响极限拉深系数。 1、材料的力学性能
•
一般来说,材料组织均匀,晶粒大小适当,屈强比小,材料的伸 长率大,塑性好,拉深性能好,极限拉深系数较小。
网目实验法分析拉深件侧壁厚度变化规律

网目实验法分析拉深件侧壁厚度变化规律0 引言用平面板坯制作杯形件的冲压成形工艺﹐又称拉延。
通过拉深可以制成圆筒形﹑球形﹑锥形﹑盒形﹑阶梯形﹑带凸缘的和其他复杂形状的空心件。
采用拉深与翻边﹑胀形﹑扩口﹑缩口等多种工艺组合﹐可以制成形状更复杂的冲压件。
冲压的本质是利用模具和冲压设备使金属板坯料产生塑性流动D 从而使其发生所需要的形状改变。
弯曲、拉深、翻边、翻孔、胀形、扩口、缩口和旋压等是冲压所涵盖的几种基本工艺过程、其中拉深是将板料毛坯在具有一定圆角半径的凸5 凹模作用下加工成各类零件的工艺手段,它在汽车、仪表、航天等领域均有广泛应用。
在拉深成形过程中,通常需要安装压边装置产生摩擦抗力,以增加板料中的拉应力,控制材料的流动D 避免起皱。
[1]拉深是板料成形中的一种重要工艺方法,广泛应用于汽车、航空航天、家用电器制造等方面。
拉深时,板料的壁厚会发生变化,在拉深件的口部增厚, 筒底发生变薄, 在筒底圆角处变薄量最大。
如果壁厚变化太大, 拉深件的强度会降低,不但影响拉深件的使用性能,而且壁部最薄的地方在拉深过程中,由于最大拉应力超过材料的强度极限,材料将被拉裂,造成产品报废。
[2]1网目实验法2壁厚2.1摩擦因数与拉深件最大壁厚变薄率的关系表4是在其他参数固定的情况下, 计算得到的在不同摩擦因数的情况下,拉深件的壁厚最大变薄率。
分析表4中的数据可以得出, 摩擦因数与拉深件最大壁厚变薄率的关系如图2所示。
从图2可以看出,在其他参数固定,凸模、凹模和压边圈的摩擦因数取值相同的情况下, 工件最大壁厚变薄率与摩擦因数呈线性增长关系,但增长幅度并不大。
而当凸模与坯料接触面的摩擦因数取为0.25, 凹模和压边圈与坯料接触面的摩擦因数取为 0.1 时, 拉深件的最大壁厚变薄率为8.99%, 远小于凸模、凹模、压边圈的摩擦因数都为0.08 的最大壁厚变薄率10.13%。
因此, 要求在模具设计与制造时,压边圈、凹模与坯料接触的工作面的粗糙度应小些,尽量光滑平整, 降低拉深过程中的阻力;凸模工作面应做得比较粗糙些, 以增大凸模与板料之间的摩擦力,阻止危险断面的发生。
12.1 拉深变形过程分析

材料转移
如将平板毛坯的三 角形阴影材料去掉, 留下等宽度狭条,将 其沿直径d的圆周弯折, 焊接,就可以成为一 个圆筒形工件。高度 h=(D-d)/2。但实际阴 影部分材料只是产生 了塑性流动转移,拉 深后工件高度> =(Dd)/2。厚度也变化。
2、变形分析
在毛坯上画作出距离为a的等距离的同心圆与 相同弧度b辐射线组成的网格,然后将带有网格 的毛坯进行拉深。 拉深后: 拉深后:工件底部的网格变化很小,而侧壁 上的网格变化很大,以前的等距同心圆,变成了 与工件底部平行的不等距的水平线,并且愈是靠 近工件口部,水平线之间的距离愈大,同时以前 夹角相等的半径线在拉深后在侧壁上变成了间距 相等的垂线。以前的扇形毛坯网格变成了拉深后 的矩形网格。来自(4)凸模圆角部分 )
属于过渡区,材料 承受径向和切向拉应 力σ1和σ3,还承受凸 模圆角压力和弯曲作 用产生压应力σ2。
拉深过程中的应力应变
(5)筒底部分 )
材料基本不变形,由 于底部圆角的拉深力, 材料承受双向拉应力, 厚度略有变薄。
拉深过程的力学分析 坯料各区的应力与应变是很不均匀的。
拉深成形后制件壁厚和硬度分布
拉深过程中的应力应变
(2)凹模圆角部分 )
属于过渡区,变形 比较复杂,除凸缘部 分相同的特点,还承 受凹模圆角压力和弯 曲作用产生压应力σ2。
拉深过程中的应力应变
(3)筒壁部分 )
材料已经变形成为 筒壁,凸模的拉深力 通过筒壁传递到凸缘 部分,承受单向拉应 力σ1,产生少量伸长 和减薄。
拉深过程中的应力应变
扇形单 元的受 力分析 拉深网格的变化
变形过程归纳
(1)拉深过程中,材料变形主要发生在凸 缘部分; (2)拉深变形实质就是凸缘处材料在径向 拉应力和切向压应力共同作用下产生塑性 变形,凸缘不断收缩而转化为筒壁的过程; (3)凸缘处的塑性变形程度最大。
板料拉深变形过程及其特点

冲压工艺与模具设计板料拉深变形过程及特点
主讲人:慕东
第四章拉深工艺及模具设计
拉深是利用拉深模具将冲裁好的平板毛坯压制成各种开口的空心件,
或将已制成的开口空心件加工成其他形状空心件的一种加工方法。
1—凸模;2—压边圈;3—凹模;4—毛坯; 5—拉深件
图4-2 拉深件示意图
4.1 拉深变形过程分析
4.1.1 板料拉深变形过程及其特点
图 4-3 毛坯的三角形阴影部分材料减去三角形阴影部分,然后折弯,并焊接缝隙,测量:直径为d ,高度为h=(D-d)/2
拉深后测量:直径为d ,高度为h>(D-d)/2
变形特点
(1)a1>a2>a3>…>a;
(2)b1=b2=b3=…=b;
(3)筒壁高度:H>(D-d)/2;
(4)制件底部几乎不变;
(5)扇形网格dA1→矩形dA2。
图4-4 拉深网格的变化
径向被拉长;
切向被压缩
图4-5 拉深网格的挤压变形
拉深变形过程:
1.毛坯受凸模拉深力的作用,在凸缘毛坯的径向产生拉伸应力σ1,切向产生压缩应力σ3;
2.在两力的共同作用下,凸缘变形区材料发生塑性变形,并不断拉入凹模内形成筒形拉深件。
谢谢观看。
(4-1、2)圆筒形件拉深变形分析

第四章 拉深工艺与拉深模设计
第二节 圆筒形件拉深变形分析
2.筒壁的拉裂
最易拉裂的位置:当筒壁拉应力超过筒壁材料的抗拉强
度时,拉深件就会在底部圆角与筒壁 相切处的危险断面产生破裂。
最易拉裂的时刻:当Rt=(0.7~0.9)R0时,1max 达到最大值 [(1max)max]
防止拉裂:
一方面要通过改善材料的力学性能,提高筒壁抗拉强度; 另一方面通过正确制定拉深工艺和设计模具,降低筒壁所 受拉应力。
第一节 概述
拉深:
又称拉延,是利用拉深模在压力机的压力作用下,将平板坯 料或空心工序件制成开口空心零件的加工方法。
它是冲压基本工序之一。可以加工旋转体零件,还可加工盒 形零件及其它形状复杂的薄壁零件。
拉深 不变薄拉深
变薄拉深
拉深模: 拉深所使用的模具。
拉深模特点:结构相对较简单,与冲裁模比较,工作部分有较
毛坯的三角形阴影部分材料
第四章 拉深工艺与拉深模设计
拉深变形过程
第四章 拉深工艺与拉深模设计
拉深网格的变化
第四章 拉深工艺与拉深模设计拉深过 Nhomakorabea程
的
应
下标1、2、3分 别代表坯料径向、
力
厚度方向、切向
与
的应力和应变
应
变
状
态
第四章 拉深工艺与拉深模设计
下标1、2、3分 别代表坯料径向、 厚度方向、切向 的应力和应变
直径为d高度为H的圆筒形件(H>(D-d)/2)
第四章 拉深工艺与拉深模设计
第二节 圆筒形件拉深变形分析
二、拉深过程中坯料内的应力与应变状态
拉深过程中某一瞬间坯料所处的状态
1.凸缘部分 应力分布图
拉深系数和影响拉深系数的因素(模具设计与制造)

教育部十一五规划教材《模具设计与制造》
第4章 拉深工艺与拉深模具
4.3.3 极限拉深系数的确定
极限拉深系数的大小与被拉深毛坏的材料 性质有密切的关系。可以通过实验的方法来测 得某一材料的极限拉深系数,适用于低碳钢圆 筒形件的极限拉深系数见表4.2。
2020/7/24
教育部十一五规划教材《模具设计与制造》
2020/7/24
教育部十一五规划教材《模具设计与制造》
第4章 拉深工艺与拉深模具
4.3.2 影响拉深系数的因素
(5)模具工作部分圆角半径及间隙的影响 凸模的圆角半径过小时,在毛坯的圆筒部分
与底部的过渡区的弯曲变形加大,使危险断面的 强度进一步削弱,拉深系数只能取得大些;凹模 的圆角半径过小时,毛坯沿凹模圆角滑动的阻力 增加,使毛坯侧壁内的拉应力增大,容易被拉破, 这时拉深系数不能取得过小。凸模和凹模的间隙 过大,拉入间隙的毛坯易起皱;间隙过小,毛坯 进入间隙的阻力增大,筒壁内的拉应力变大,容 易拉破。只有取合理间隙,才能使拉深系数取得 小些。 另外,毛坯与凹模处的润滑条件好,拉 深系数也可取得小些。
(4 – 1 )
第2次拉深系数:m 2 = d 2/d1
(4 – 2 )
第n次拉深系数:m n = d n/d n一1
(4 – 3 )
式中,D0——为毛坯直径(mm);
d1、d2、…、 d n一1 、dn——为各次拉深工序后工件的直径
(mm),当板厚t > 1mm时,取工件的中线尺寸。
2020/7/24
教育部十一五规划教材《模具设计与制造》
第4章 拉深工艺与拉深模具
4.3.2 影响拉深有:
板料的内部组织和机械性能、毛坯的相对厚度t/
D0、模具工作部分的圆角半径及间隙、拉深模的结
拉深变形分析

2.凸缘圆角部分
过渡区,材料变形较复杂,除有与平面凸缘部 分相同的特点外,还承受凹模圆角的压力和弯 曲作用而产生压应力σ2。
3.筒壁部分
继续拉深时,凸模的拉深力经筒壁传递 到凸缘部分,承受单向拉应力σ1的作用, 发生少量的纵向伸长和变薄。
4.底部圆角部分
过渡区,材料承受径向拉应力σ1和切向拉应力 σ3,在厚度方向承受压应力σ2。
拉深变形的基本原理
拉深: 利用模具使平板毛坯变成为开口的空心 零件的冲压加工方法。
拉深工艺可以制成筒形、 阶梯形、球形、锥形、抛 物面形、盒形和其他不规 则形状的薄壁零件。
一、变形过程
拉深模的工作部分没有锋利 的刃口,而是有一定的圆角 半径,并且其间隙也稍大于 板材的厚度。
金属流动过程的实验:
拉深变形过程可归结如下:
在拉深力作用下,毛坯内部的小单元体在径向 产生拉应力,在切向产生压 应力。
在这两种应力作用下,凸缘 区的材料发生塑性变形并不断 地被拉入凹模内,成为圆筒形 零件。
二 拉深过程中毛坯的应力应变状态
拉深件各部分的厚度变化不一致:
底部略为变薄; 壁部上段增厚,越靠上 缘增厚越大; 壁部下段变薄,越靠下 部变薄越多,在壁部向 底部转角稍上处,则出 现严重变薄。
拉深毛坯应力应变状态的5个区域:
1.平面凸缘区
径向拉应力σ1和切向压应力σ3、厚度方向压应力σ2的作 用下,发生塑性变形而逐渐进入凹模。材料的流动主 要是径向延展,同时也向毛坯厚度方向流动而加厚。 越靠外缘需要转移的材料越多,外缘材料变得越厚, 硬化也越严重。
若不用压边圈,则σ2=0。此时的ε2 要比有压 边圈时大。当需要转移的材料面积较大而板材 相对又较薄时,毛坯的凸缘部分,尤其是最外 缘部分,受切向压应力σ3的作用极易失去稳定 而拱起,出现起皱。
(23) 4.1-4.2拉深变形的分析及拉深件的工艺性

图4-3 拉深时坯料的应力、应变状态
4.1 拉深变形分析
1.平面凸缘部分 平面凸缘部分为拉深时的主要变形区。材料产生径向拉应 力s1。同时,材料在切向产生压缩变形,相邻材料之间由 s1。同时,材料在切向产生压缩变形,相邻材料之间由 于相互挤压而产生切向压应力s3。当使用压边装置时,压 于相互挤压而产生切向压应力s3。当使用压边装置时,压 边力使平面凸缘部分材料产生厚向压应力s2。 边力使平面凸缘部分材料产生厚向压应力s2。 由于平面凸缘部分材料在拉深时径向拉长,切向缩短,分 别产生径向拉应变e1和切向压应变e3。其中,切向压应变 别产生径向拉应变e1和切向压应变e3。其中,切向压应变 e3的绝对值大于径向拉应变e1,故根据体积不变原则,材 e3的绝对值大于径向拉应变e1,故根据体积不变原则,材 料将产生厚向拉应变e2,厚度增加。 料将产生厚向拉应变e2,厚度增加。 2.筒壁部分 筒壁部分为已变形区。在拉深过程中,该部分材料起到向 变形区传递拉深力的作用,因而也称为传力区。筒壁部分 在拉深时可近似认为受单向拉应力s1作用,应变状态为轴 在拉深时可近似认为受单向拉应力s1作用,应变状态为轴 向产生拉应变e1,厚向产生压应变e3,厚度减薄。 向产生拉应变e1,厚向产生压应变e3,厚度减薄。
4.1 拉深变形分析
4.1.2 拉深变形过程中坯料的应力、应变状态 拉深变形过程中坯料的应力、 在拉深过程中,坯料可分为平面凸缘部分、凸缘圆角部分、 筒壁部分、底部圆角部分、筒底部分等五个区域,如图4 筒壁部分、底部圆角部分、筒底部分等五个区域,如图41(b)所示。各部分材料在拉深过程中具有不同的应力应 变状态,如图4 变状态,如图4-3所示。
变薄拉深相关资料
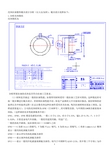
壳体拉深整形模具设计分析(以大众为例),模具设计流程如下:1.分析壳体图纸壳体图纸为分析所要拉深的壳体是否符合拉深工艺要求。
(1)材料是否满足一般的拉深性能。
如果所用材料采用一般拉深工艺即可得到,这种情况即可按一般步骤进行模具设计。
若材料拉深性能不好,但是产品图纸又不可做相应修改,做好材料的前处理以及中间处理过程(在过去像壳体这种拉深件采用多次拉深,每次拉深材料出现加工硬化,这样就需要退火)。
公司的壳体材料为SPHE(日本牌号),其可塑性很强。
与中国的10#钢含碳量基本相似,(这种钢的很多性能参数查不到)SPHC、SPHD、SPHE都是低碳低硅钢,一般C小于0.12%,硅小于0.03%,锰0.25-0.5%,P、S小于0.020%,主要是家电汽车面板,一般民用建筑用板,用途广泛。
一般的热轧中碳钢,抗拉强度340——430MPA之间SPHC——S为钢Steel的缩写,P为板Plate 缩写,H为热Heat的缩写,C商业Commercial整体表示一般用热轧钢板及钢带SPHD——表示冲压用热轧钢板及钢带SPHE——表示深冲热轧钢板及钢带SPCC——表示一般用冷轧碳素钢薄板及钢带,相当于中国牌号Q195-215A。
其中第三个字母C为冷Cold 的缩写。
需保证抗拉实验时,在牌号末尾加T为SPCCTSPCD——表示冲压用冷轧碳素钢薄板及钢带,相当于中国08AL(13237)优质碳素结构钢。
SPCE——表示深冲用冷轧碳素钢薄板及钢带,相当于中国08AL(5213)深冲钢。
需保证非时效性时,在牌号末加N为SPHEN。
1MPA=10大气压力=10.3323kg/cm2. 即相当于10.332kg/cm3压力.(2)尺寸要求是否合理对拉深工艺影响最大的尺寸为红框里的两个尺寸,这两个人尺寸涉及到拔模斜度。
任何拉深出的工件内壁都不会一点锥度都不带,因为没有锥度会给在模具拔模造成难度。
拔模斜度越大所用的拔模力越小,拔模斜度的确定应在满足要求的前提下尽量放大。
第四章拉深一

• • • • 工件的命名: 筒:侧面呈封闭形,一端开口,另一端存在底面。 管:侧面呈封闭形,两端开口。 拉深:板料或筒坯在凸模作用下通过凹模孔,形成筒状工 件,这种冲压工序称为拉深。 拉深可将平板毛坯直接拉成筒状工件,也可将筒状毛 坯拉成直径变小、长度变长的筒状工件。(P72表4-1) 拉深分类(按拉深件厚度): 1.不变薄拉深:材料的厚度在拉深前后基本不变。 2.变薄拉深:材料的厚度在拉深后变薄(筒状毛坯长度变长, 直径变化很小。)
2 0
2
2 0
2 ( Rr
ห้องสมุดไป่ตู้
2
r ) Rr 2 r
2 2
2
在本拉深圆筒中 R
4
1 2
d底
2 2
A
( rd 底+ 2 r ) 2 rd 底+8 r 2
2
4
1
• 其中d底=d口-2r h为直壁高度,应加上修边余量Δ h。P88表4 -4示出圆筒件的修边余量Δ h可供选用。
一.圆筒件拉深的变形过程
• 拉深时筒底拐弯区形成 以后,变形位置在凸缘部 位(Ⅰ区)和凹模入口的 圆角处(Ⅱ区)。 1.圆筒件拉深时各区的应 力应变状态示于图4.1 根据应力应变状态的不同,可将拉深毛坯划 分为Ⅰ~Ⅴ五个区域:
• Ⅰ区:凹模口的凸 缘部分(法兰区)。 这是拉深变形的主 要区域。受到径向 拉应力σ ρ 和切向 (圆周方向)压应 力σ θ,并在径向和 切向分别产生伸长 和压缩变形,逐渐 进入凹模,在轴向 板厚稍有增大。
二.圆筒件拉深工艺计算及其模具设计
• 1.拉深零件的毛坯尺寸 计算依据:因为拉深前后体积不变(塑性变形假设)、厚度不 变(不变薄拉深),所以(中间层)面积ΣA(右图三部分 之和P88)不变。 圆筒件的毛坯圆片状直径为:
拉深模的基本原理

拉深模的基本原理拉深模的基本原理(一)拉深是利用模具将平板毛坯或半成品毛坯拉深成开口空心件的一种冷冲压工艺。
拉深工艺可制成的制品形状有:圆筒形、阶梯形、球形、锥形、矩形及其它各种不规则的开口空心零件。
拉深工艺与其它冲压工艺结合,可制造形状复杂的零件,如落料工艺与拉深工艺组合在一起的落料拉深复合模。
日常生活中常见的拉深制品有:旋转体零件:如搪瓷脸盆,铝锅。
方形零件:如饭盒,汽车油箱复杂零件:如汽车覆盖件。
圆形拉深的基本原理一、拉深的变形过程用座标网格试验法分析。
拉深时压边圈先把中板毛坯压紧,击模下行,强迫位于压边圈下的材料(击缘部分)产生塑性变形而流入击凹模间隙形成圆筒侧壁。
观察拉深后的网格发现:底部网格基本保持不变,筒壁部分发生较大变化。
1〃原间格相等的同心圆成了长度相等,间距增大的圆周线,越接近筒口,间距增大。
2〃原分度相等的辐射线变成垂直的平行线,而且间距相等。
3〃击缘材料发生径向伸长变形和切向压缩变形。
总结:拉深材料的变形主要发生在击缘部分,拉深变形的过程实质上是击缘处的材料在径向拉应力和切向压应力的作用下产生塑性变形,击缘不断收缩而转化为筒壁的过程,这种变形程度在击缘的最外缘为最大。
二、各种拉深现象由于拉深时各部分的应力(受力情况)和变形情况不一样,使拉深工艺出现了一些特有的现象:1〃起皱:A.拉深时击缘部分的切向压应力大到超出材料的抗失稳能力,击缘部分材料会失稳而发生隆起现象,这种现象称起皱.起皱首先在切向压应力最大的外边缘发生,起皱严重时会引起拉度.B.起皱是拉深工艺产生废品的主要原因之一,正常的拉深工艺中是不允许的.常采用压力圈的压力压住击缘部分材料来防止起皱.C.起皱的影响因素:a). 相对厚度:t/D其中t----毛坯厚度,D----毛坯直径判断是否起皱的条件:D-d<=2Zt, d ----工件直径.b). 拉深变形程度的大小但是在拉深变形过程中,切向压应力及击缘的抗失稳能力都是随着拉深进行,切向压应力是不断增大,变形区变小,厚度相对增加,变形失稳抗力增加,两种作用的相互抵消,使击缘最易起皱的时刻发生于拉深变形的中间阶段,即击缘宽度大约缩至一半左右时较易发生起皱现象.2.变形的不均匀:拉深时材料各部分厚度都发生变化,而且变化是不均匀的. 击缘外边缘材料厚度变化最大,拉深件成形后,拉深件的坯口材料最厚,往里逐渐减薄,而材料底部由于磨擦作用(拉深击模与底部材料间)阻止材料的伸长变形而使底部材料变薄较小,而底部圆角部分材料拉深中始终受击模圆角的顶力及弯曲作用,在整个拉深中一直受到拉应力作用,造成此处变薄最大.所以拉深中厚度变薄主要集中于底部圆角部分及圆筒侧壁部分,我们把这一变薄最严重的部位称作危险断面.拉深过程中,圆筒侧壁起到传递击模拉力给击缘的作用,当传力区的径向拉应力超出材料极限,便出现拉破现象.3.材料硬化不均匀拉深后材料发生塑性变形,引起材料的冷作硬化.由于各部分变形程度不一样,冷作硬化的程度亦不一样,其中口部最大,往下硬化程度降低,拉近底部时,由于切向压缩变形较小,冷作硬化最小,材料的屈服极限和强度都较低,此处最易产生拉裂现象。
- 1、下载文档前请自行甄别文档内容的完整性,平台不提供额外的编辑、内容补充、找答案等附加服务。
- 2、"仅部分预览"的文档,不可在线预览部分如存在完整性等问题,可反馈申请退款(可完整预览的文档不适用该条件!)。
- 3、如文档侵犯您的权益,请联系客服反馈,我们会尽快为您处理(人工客服工作时间:9:00-18:30)。
另一种加工方法是热挤压预成型 , 再经多次冷挤 压变薄拉深成型。此种加工方法的优点是材料利用率 高, 成本很低, 适合大批量生产 , 以下做详细介绍。
2冷挤压变薄拉深模具装配结构
变薄拉深模具装配结构见图 2 。该模具上模 由上
图 2模具结构
作者简介 : 军伟 , 17 魏 男, 9 8年生 , 河南鲁 山人, 从事有 色金 主要 属加工的工艺研 究及工装设计工作 。
、
在半模角的作用下 , 零件底部参 与变形的金属体积流
人底部 的那部 分金属要使外 径大的零件底部厚度增 厚, 需要更 多的金属 , 因此直径 大的零件底部厚度增
加量小 。而外径小的零件在拉深时 , 底部参与变形的 金属一部分流人底部 , 这时 由于零件外径小 。及底部
意, 经过在工作中的试验和认真分析发现底部增厚的
:
变 薄拉深工序的工作过 程如下 : 模具工作 时由设 备的活动横梁带动整体上模 上升 , 模具开启。这 时把
需要拉深的零件放人拉深模子中。同时设备的活动横
梁带动整体上模下降 , 冲子插入零件 内径与零件 内径
配合 。并带动拉深零件进入拉深模 子 中进行变薄拉
深 ,同时拉深零件通过拉深模子后并进入退料器 , 当
( )底厚增加量与变薄拉深时零件 的直径大小 2
有一定 的关系。试验证 明变薄拉深零件 的外径越小 , 底 部厚 度的增 加量越 大 , 反之零件 的直径越大 , 底部
变薄拉 深零件全部通过退料器时 , 这时设备的活动横
梁带动整体上模上升 , 同时退料器把拉深零件从 冲子
上把料卸下。活动横梁带动整体上模继续t升并回到 原始位置进入下一个工作循环过程。
原 因如 下 :
j
( )底部增厚与变薄拉深时 的模具 0 角有 关 1 【
系 。见 图 3 。
体积小 , 而流人底部的这部分金属足以使底部厚度增
加较多, 使得底度增厚。 ( )变薄拉深时底部厚度 的增加量 与零件拉深 3 时壁厚及加工率有关 。对相同直径而壁厚及加工率不
。
-
壁量大时 , 其拉 深力也大 , 底部参与 变形 的金属量也
多 ,变薄拉深时参与变形的金属流向底部的金属量也 多, 当然底部厚度量也就越多。反之底部的增加量就少。 ( )变薄拉深时底部厚度的增加量与零件本身 4
同的零件进行试验 , 结果发现壁薄的零件通过变薄拉
图 3 模具 o [角
:
.
深后其底部厚度增加量少 , 而壁厚的零件通过变薄拉
深后其底部增加量较多。这是因为减壁拉深时 , 当减
这是 因为拉深时在半模角 的作用下 ,半制 品 内底平面以下参与变形 的金属会有一部分流 向底 部 ,
厚度 的增加量就越小。试验 中在同一工序采用相同的
拉深模子半角 ,及拉深前壁厚相 同的零件进行试验 ,
但在拉深后底部的厚度增加量却不同 。例如对外径
q6 m  ̄O m的零件和外径 3 r 0 m的零件在 同工序采用 a
相同的模子半角 ,相同的壁厚及相同的底厚进行 试
4冷挤压变薄拉深时存在的问囊及解决方法
下边 并座 在底 座 上 。整个 下模 固定 在 设 备的 下工
作 台上 。
图 1零件
上述零件 的加工即机械加工成型
法, 诸如传统的车削 、 钻孔等 。此种加工方法材料利用
率极低 , 成本很高, 不适合大批量 生产 , 在此故不详细
维普资讯
丝
2 0 .o6总 6 0 6N 3期
浅析小直径 回转体零件变薄 拉深 时的底厚变化情况
魏军伟 于连顺 高大伟 黄坤 李英辉 河南江河机械有限责任公司 河南鲁 山 4 7 3 637
摘
要: 较好的分析 了小直径 、 体长 、 底厚的零件变薄拉深工序 中底部增厚 的变化规
3 冷挤压变薄拉深工序的工作过程
中3r 0 m底厚 1r a 6 m的圆形零件拉深时 ,当模子的半 a
角 没计 为 l。 0时, 一次拉深后底厚就增加 了 3 4 n  ̄ma 。 同一工序 , 当对模子 半角设计为 I。 , 5时 在变薄拉深过 后, 底厚只增加 了 2 3 m  ̄ m 。试验结果证明小直径底厚 零件在变薄拉深 中底厚增厚量与模子半角有关系。
1 底座 2横粱 3模圈 4 模盖 5螺栓 6 垫圈 7 压盖 8垫板 9上模板 1 螺钉 0
1垫1 1 2螺母 1 3螺钉 1 4圆柱销 1 5连接器 1 冲子 1 6 7模子 1 退料器 8
w wcm oa r 4 w m nd o 5 o cn
维普资讯
律及其成 因 。 并为这类零件的工艺 、 工装设计 及机械加工方面提 供 了科学 的依 据 。 对
生产 中出现 的问题也提出了相应的注意事项。
关键词 : 变薄拉深 模子半角 加工率
1零件的加工方法
模板 9 连接器 l 、 、 5压盖 7 上冲头组成 。连接器 l 与 、 5 上模板 9 通过螺钉 1 连接 ,冲子通过压盖 7 的螺 0 上 纹与连接器 1 连接。整体上模 固定在设备的活动横 5
在我们 的实际生产过程 中经常会遇到小直径 、 体 长, 而壁薄底部又很厚的回转体零件 , 见图 l 。
梁上。下模 由模盖 4 模圈 3 横梁 2 底座 1退料器 、 、 、 、 、
模子等零件组成 。模盖 、 圈 、 模 横梁 、 底座通过螺栓 5
固定在一起 , 拉深 模 子 座 在横 梁 上 , 料 器 在横 梁 退
在采用变薄拉深加工成型的过程 中, 发现这类零
件在变薄拉深过程中有不同程度的底部增厚的现象 , 这种现象直接影响着工件后续的加工 , 给以后工序 并 加工带来很多麻烦, 这不得不引起在生产过程 中的注
验 。结果底厚增加量却不相 同, 直径大的零件底厚增
加量要小于直径小的底厚增加量 。而且在试验 中得知 零件的直径越大底厚增加量越小 。这是因为拉深零件