简单盘套类零件的编程及仿真加工 PPT
合集下载
盘套类零件加工工艺 PPT

案例教学
一单元 盘套类零件的功用、结构特点、技术要求、材料与毛坯
(一)盘类零件 1、盘类零件的功用及结构特点
盘类零件在机器中主要起支承、连接作用。 主要由端面、外圆、内孔等组成,一般零件直 径大于零件的轴向尺寸,如齿轮、带轮、法兰盘、 端盖、模具、联轴节、套环、轴承环、螺母、垫圈 等。 一般用于传递动力、改变速度、转换方向或起 支承、轴向定位或密封等作用。 零件上常有轴孔;常设计有凸缘、凸台或凹坑 等结构;还常有较多的螺孔、光孔、沉孔、销孔或 键槽等结构;有些还具有轮辐、辐板、肋板以及用 于防漏的油沟和毡圈槽等密封结构。 各类盘类零件见图2-3(1)(2)所示。
盘套类零件加工工艺的设计与实施
重点:
1. 盘套类零件的加工工艺分析; 2. 盘套类零件的定位基准确定; 3. 盘套类零件的加工路线的确定; 4. 加工经济性分析。
难点:
盘套类零件的加工路线的确定及加工经济性分析。
盘套类零件加工工艺的设计与实施
第二部分 过程设计描述
该情境的学习与工作流程如下图:
资讯
分组点评 每小组选派4人(含组长),对前期所进行的资讯内容中的1、2、
3项进行畅谈。最后由老师进行归类评述,并对资讯方法进行点评 和指导。
学习情景2 常规特征零件的数控车削加工
大家有疑问的,可以询问和交流
精品课程
可以互相讨论下,但要小声点
9
盘套类零件加工工艺的设计与实施
第三部分 学习情境
步骤一:资讯
图2-4 套筒类零件案例
a)滑动轴承 b)滑动轴承 c)钻套 d)衬套 e)气缸 套 f)油缸
盘套类零件加工工艺的设计与实施
第三部分 学习情境
步骤一:资讯
案例教学 一单元 盘套类零件的功用、结构特点、技术要求、材料与毛坯
项目八 简单盘套类零件的编程及仿真加工(一)
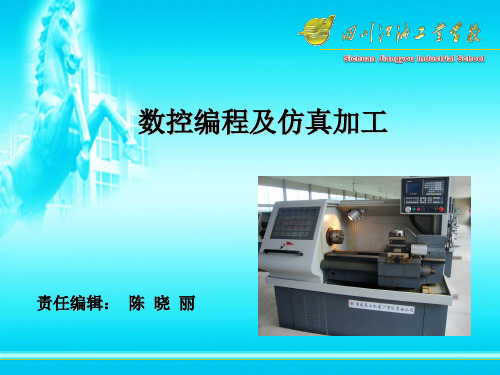
3、定位心轴
盘套类零件内孔精度要求较高,针对需多次工序才能完成的盘套类零件, 为保证其精度要求,须以内孔为定位基准,才能保证外圆轴线和内孔轴线的 同轴度要求,此时要用心轴定位。 ① 圆柱心轴 利用心轴的圆柱表面与工件定位配合,并保持较小的间隙,便于工件的装卸; 夹紧力较大,但定心精度较锥度心轴低,工件靠螺母压紧,如图8-1-5。
3、形状、位置精度
形位公差,是零件精度要求的重要内容,也是确定和影响车削工艺的 重要因素,尤其是按照其要求确定零件的定位基准和测量基准的重要指标。
项目八 简单盘套类零件的编程及仿真加工 图8-1-1 盘套类零件的技术要求
项目八 简单盘套类零件的编程及仿真加工
二、盘套类零件的装夹与定位方法
盘套类零件的内/外圆柱面、端面与基准轴线都存在相应的形位精度要求, 盘类零件的精基准可以选择外圆,但常以中心孔及一个端面为精加工基准。
图8-1-2 三爪卡盘装夹工件
项目八 简单盘套类零件的编程及仿真加工
② 薄壁套类零件的刚度差,装夹不当或夹紧力过大,易导致工件变形, 则需要采用开口套装夹,或者扇形卡爪,如图8-1-3所示。
图8-1-3 薄壁套类零件的装夹
任务八 简单盘套类零件的编程与仿真加工
2、四爪单动卡盘
四爪可以单独移动,夹紧力较大,适用于
定性和精度。当使用大直径镗孔刀杆时,稳定性便得到增强;但由于受零件 孔径所允许的空间限制,这种可能性也经常受到限制,故此,必须考虑到排 屑和刀具的径向移动。
项目八 简单盘套类零件的编程及仿真加工
四、盘套类零件刀具及其切削用量的选用
加工内孔是盘套类零件的特征之一,根据内孔的工艺要求,加工方法较 多,常用的有钻孔、扩孔、铰孔、镗孔和磨孔等。内孔加工时常用的刀具有 中心钻、麻花钻及内孔镗刀等。 1、钻孔
盘套类零件内孔精度要求较高,针对需多次工序才能完成的盘套类零件, 为保证其精度要求,须以内孔为定位基准,才能保证外圆轴线和内孔轴线的 同轴度要求,此时要用心轴定位。 ① 圆柱心轴 利用心轴的圆柱表面与工件定位配合,并保持较小的间隙,便于工件的装卸; 夹紧力较大,但定心精度较锥度心轴低,工件靠螺母压紧,如图8-1-5。
3、形状、位置精度
形位公差,是零件精度要求的重要内容,也是确定和影响车削工艺的 重要因素,尤其是按照其要求确定零件的定位基准和测量基准的重要指标。
项目八 简单盘套类零件的编程及仿真加工 图8-1-1 盘套类零件的技术要求
项目八 简单盘套类零件的编程及仿真加工
二、盘套类零件的装夹与定位方法
盘套类零件的内/外圆柱面、端面与基准轴线都存在相应的形位精度要求, 盘类零件的精基准可以选择外圆,但常以中心孔及一个端面为精加工基准。
图8-1-2 三爪卡盘装夹工件
项目八 简单盘套类零件的编程及仿真加工
② 薄壁套类零件的刚度差,装夹不当或夹紧力过大,易导致工件变形, 则需要采用开口套装夹,或者扇形卡爪,如图8-1-3所示。
图8-1-3 薄壁套类零件的装夹
任务八 简单盘套类零件的编程与仿真加工
2、四爪单动卡盘
四爪可以单独移动,夹紧力较大,适用于
定性和精度。当使用大直径镗孔刀杆时,稳定性便得到增强;但由于受零件 孔径所允许的空间限制,这种可能性也经常受到限制,故此,必须考虑到排 屑和刀具的径向移动。
项目八 简单盘套类零件的编程及仿真加工
四、盘套类零件刀具及其切削用量的选用
加工内孔是盘套类零件的特征之一,根据内孔的工艺要求,加工方法较 多,常用的有钻孔、扩孔、铰孔、镗孔和磨孔等。内孔加工时常用的刀具有 中心钻、麻花钻及内孔镗刀等。 1、钻孔
《套类零件的加工》课件

在磨削加工中,工件安装在磨床的工作台上, 通过高速旋转和切削刀具的进给运动实现切削 加工。
磨削加工具有极高的加工精度和表面质量,适 用于对精度要求极高和对表面质量要求严格的 零件加工。
套类零件的其他加工方法
01
套类零件除了车削、铣削和磨削 等常见加工方法外,还包括钻削 、铰削、镗削、攻丝等加工方法 。
05
套类零件的加工质 量控制与检测
套类零件的加工精度控制
加工工艺流程
详细介绍套类零件的加工 工艺流程,包括毛坯准备 、粗加工、半精加工和精 加工等阶段。
加工设备选择
根据零件特点和加工精度 要求,选择合适的机床和 工具,确保加工过程的稳 定性和精度。
热处理和表面处理
介绍套类零件在加工过程 中可能涉及的热处理和表 面处理方法,以及它们对 零件精度的影响。
套类零件的尺寸检测与测量方法
尺寸检测原则
明确套类零件的尺寸检测原则,确定检测项目和检测方法。
测量工具选择
根据套类零件的尺寸和精度要求,选择合适的测量工具,如卡尺 、千分尺、量规等。
测量方法与操作技巧
详细介绍套类零件的测量方法与操作技巧,确保测量结果的准确 性和可靠性。
THANKS
感谢您的观看
套类零件的表面质量检测
表面粗糙度检测
表面涂层质量检测
使用表面粗糙度测量仪对套类零件的 表面粗糙度进行检测,确保符合设计 要求。
对套类零件表面的涂层进行质量检测 ,包括涂层厚度、硬度、附着力等方 面的检测。
表面缺陷检测
通过目视检查、无损检测等方法,检 查套类零件表面是否存在裂纹、气孔 、夹渣等缺陷。
套类零件的加工实 例
实例一:轴承套的加工
总结词
工艺流程复杂,需要高精度加工
磨削加工具有极高的加工精度和表面质量,适 用于对精度要求极高和对表面质量要求严格的 零件加工。
套类零件的其他加工方法
01
套类零件除了车削、铣削和磨削 等常见加工方法外,还包括钻削 、铰削、镗削、攻丝等加工方法 。
05
套类零件的加工质 量控制与检测
套类零件的加工精度控制
加工工艺流程
详细介绍套类零件的加工 工艺流程,包括毛坯准备 、粗加工、半精加工和精 加工等阶段。
加工设备选择
根据零件特点和加工精度 要求,选择合适的机床和 工具,确保加工过程的稳 定性和精度。
热处理和表面处理
介绍套类零件在加工过程 中可能涉及的热处理和表 面处理方法,以及它们对 零件精度的影响。
套类零件的尺寸检测与测量方法
尺寸检测原则
明确套类零件的尺寸检测原则,确定检测项目和检测方法。
测量工具选择
根据套类零件的尺寸和精度要求,选择合适的测量工具,如卡尺 、千分尺、量规等。
测量方法与操作技巧
详细介绍套类零件的测量方法与操作技巧,确保测量结果的准确 性和可靠性。
THANKS
感谢您的观看
套类零件的表面质量检测
表面粗糙度检测
表面涂层质量检测
使用表面粗糙度测量仪对套类零件的 表面粗糙度进行检测,确保符合设计 要求。
对套类零件表面的涂层进行质量检测 ,包括涂层厚度、硬度、附着力等方 面的检测。
表面缺陷检测
通过目视检查、无损检测等方法,检 查套类零件表面是否存在裂纹、气孔 、夹渣等缺陷。
套类零件的加工实 例
实例一:轴承套的加工
总结词
工艺流程复杂,需要高精度加工
简单轴类零件的编程及加工PPT课件
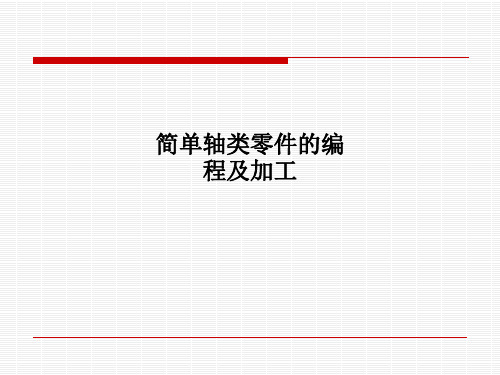
注:刀尖圆弧半径忽略不计
单一切削循环指令G90
G90是单一形状固定循环指令,该循环主要用于轴类零件的外圆、锥面的加工。 外圆切削循环指令G90 指令格式:G90 X(U)__Z(W)__F__ 式中:X、Z取值为圆柱面切削终点坐标值; U、W取值为圆柱面切削终点相对循环起点的坐标分量。 如图5-20 所示的循环,刀具从循环起点开始按矩形1R→2F→3F→4R循环,最后又回到循环起点。图中虚线表示按R快速移动,实线表示按F指定的工件进给速度移动。 锥面切削循环指令G90 指令格式:G90 X(U)__Z(W)__ R__F__ 式中:X、Z取值为圆锥面切削终点坐标值; U、W取值为圆锥面切削终点相对循环起点的坐标分量; R取值为圆锥面切削始点与圆锥面切削终点的半径差,有正、负号。 如图5-21 所示的循环,刀具从循环起点开始按梯形1R→2F→3F→4R循环,最后又回到循环起点。图中虚线表示按R快速移动,实线表示按F指定的工件进给速度移动。
沿圆弧所在平面(如X-Z平面)的垂直坐标轴的负方向(Y)看去,顺时针方向为G02,逆时针方向为G03。数控车床是两坐标的机床,只有X轴和Z轴,那么如何判断圆弧的顺、逆呢?应按右手定则的方法将Y轴也加上去来考虑。观察者让Y轴的正方向指向自己(即沿Y轴的负方向看去),站在这样的位置上就可正确判断X-Z平面上圆弧的顺、逆了。圆弧的顺、逆方向可按如图5-9(a)所示的方向判断:沿与圆弧所在平面(如X-Z平面)相垂直的另一坐标轴的负方向(Y)看出,顺时针为G02,逆时针为G03,如图5-9(b)所示为车床上圆弧的顺逆方向。
车凸圆(C→D)
N070
G02 X22 Z9 R11
车凹圆(D→E)
N080
G01 Z0
车外圆(E→F)
单一切削循环指令G90
G90是单一形状固定循环指令,该循环主要用于轴类零件的外圆、锥面的加工。 外圆切削循环指令G90 指令格式:G90 X(U)__Z(W)__F__ 式中:X、Z取值为圆柱面切削终点坐标值; U、W取值为圆柱面切削终点相对循环起点的坐标分量。 如图5-20 所示的循环,刀具从循环起点开始按矩形1R→2F→3F→4R循环,最后又回到循环起点。图中虚线表示按R快速移动,实线表示按F指定的工件进给速度移动。 锥面切削循环指令G90 指令格式:G90 X(U)__Z(W)__ R__F__ 式中:X、Z取值为圆锥面切削终点坐标值; U、W取值为圆锥面切削终点相对循环起点的坐标分量; R取值为圆锥面切削始点与圆锥面切削终点的半径差,有正、负号。 如图5-21 所示的循环,刀具从循环起点开始按梯形1R→2F→3F→4R循环,最后又回到循环起点。图中虚线表示按R快速移动,实线表示按F指定的工件进给速度移动。
沿圆弧所在平面(如X-Z平面)的垂直坐标轴的负方向(Y)看去,顺时针方向为G02,逆时针方向为G03。数控车床是两坐标的机床,只有X轴和Z轴,那么如何判断圆弧的顺、逆呢?应按右手定则的方法将Y轴也加上去来考虑。观察者让Y轴的正方向指向自己(即沿Y轴的负方向看去),站在这样的位置上就可正确判断X-Z平面上圆弧的顺、逆了。圆弧的顺、逆方向可按如图5-9(a)所示的方向判断:沿与圆弧所在平面(如X-Z平面)相垂直的另一坐标轴的负方向(Y)看出,顺时针为G02,逆时针为G03,如图5-9(b)所示为车床上圆弧的顺逆方向。
车凸圆(C→D)
N070
G02 X22 Z9 R11
车凹圆(D→E)
N080
G01 Z0
车外圆(E→F)
《套类零件的加工》课件

使用火焰将金属加热到熔点,然后将套
类零件进行焊接。
3
氩弧焊
通过电弧和氩气的保护,将套类零件进 行高质量的焊接。
成形加工
1
冲压
使用冲床将金属板材冲压成所需形状的
拉伸
2
套类零件。
将金属材料拉伸成套类零件所需的形状 和尺寸。
加工技巧
选择合适的机床及工具
根据套类零件的要求,选择适当的机床和工具。
合理的切削参数
调整切削参数以达到最佳的加工效果和质量。
合适的夹紧方式
使用正确的夹紧方法来保持套类零件的稳定性。
加工过程中监控加工状态
密切关注加工过程中的状态和质量,进行必要 的调整和控制。
加工案例
套环零件的铣削
展示套环零件的铣削过程和加工 效果。
套筒零件的冲压
演示套筒零件的冲压加工步骤和 成品。
盘式零件的拉伸
说明盘式零件的拉伸技术和应用。
套类零件的加工
本课件介绍套类零件的加工方法、工艺和技巧,以及加工案例,总结套类零 件加工的要点和未来发展趋势。
套类零件的概念及种类
概念
了解套类零件的基本定义和用途。
种类
掌握套类零件的不同分类,例如套环、套筒和 盘式零件。
套类零件的加工特点
1 复杂度
理解套类零件加工过程中的复杂度和难度。
2 精确度
要求加工出的套类零件具有高度的准确性和精度。
3 持久性
确保套类零件具有足够的耐用性和寿命。Fra bibliotek切削加工
1
铣削
使用铣床进行套类零件的切削加工。
2
钻削
使用钻床进行套类零件的切削加工。
3
内外圆磨削
采用磨床对套类零件的内外圆进行切削和精加工。
项目四 简单套类零件加工编程21页PPT

16、业余生活要有意义,不要越轨。——华盛顿 17、一个人即使已登上顶峰,也仍要自强不息。——罗素·贝克 18、最大的挑战和突破在于用人,而用人最大的突破在于信任人。——马云 19、自己活着,就是为了使别人过得更美好。——雷锋 20、要掌握书,莫被书掌握;要为生而读,莫为读而生。——布尔沃
项目四 简单套类零件加工编程
11、用道德的示范来造就2、法律是无私的,对谁都一视同仁。在每件事上,她都不徇私情。—— 托马斯
13、公正的法律限制不了好的自由,因为好人不会去做法律不允许的事 情。——弗劳德
14、法律是为了保护无辜而制定的。——爱略特 15、像房子一样,法律和法律都是相互依存的。——伯克
END
数控加工工艺、编程与操作06项目六 盘套类零件加工

(a)通孔车刀
(b)盲孔车刀
图6-3 内孔车刀
6.2 知识学习
⑵内孔车刀的选用 圆柄车刀(图6-4a)多用于车削加工中心。 矩形和方形刀柄(图6-4b)多用于使用四方刀 架的车床。 尽量选择大截面尺寸的刀杆,且刀杆的 伸出量应尽量小,一般小于刀杆直径的4倍。
(a)圆柄内孔车刀 (b)方柄内孔车刀
⑶车削内孔应采取的工艺措施
6.3 套筒零件加工项目实施
5. 数控加工工序卡的编制 套筒加工工序卡见表6-3、6-4。
6.3.2编制加工程序 为保证加工精度,按尺寸中值编程。套筒左端数控加工程序O0601见表6-5,套 筒右端数控加工程序O0602见表6-6。
6.4 盘类零件加工项目实施
6.4.1工艺分析 1.零件图分析 图6-2端盖零件Φ 160mm和孔Φ 100mm有公差要求,粗糙度要求较高;Φ 160mm外圆对 Φ 100mm孔轴线有同轴度0.02mm的要求;外阶梯面对Φ 100mm孔轴线有端面跳度0.05mm要求。材 料HT200,外径Φ 210mm,厚50mm,孔径Φ 70mm,余量较大。 2.装夹方案的确定 此零件外形比较简单,精基准选择外圆柱面。首先,夹住毛坯右端车左端,完成Φ 200mm 外圆加工、左端内外形加工;然后,以Φ 200mm精车外圆为定位基准,采用软爪卡盘装夹,完成 右端内外形加工。 3.加工顺序和进给路线的确定 ⑴工序一 ①三爪卡盘夹毛坯外圆伸出约25mm,车平左端面,对刀,设置Z坐标。 ②粗、精车Φ 200mm外圆。 ③车端面槽。 ④粗、精车Φ 80mm内孔。 ⑵工序二 ①工件调头,用软爪卡盘夹持左端φ 200mm外圆。车平右端面保证总长45mm。重新对刀, 设置Z坐标。 ②粗、精车Φ 100mm内孔。先加工内孔,再加工端面,可减少总的加工面积。 ③车沟槽。 ④粗、精车Φ 160mm外圆及阶梯面。
项目四 简单套类零件加工编程PPT课件

第3页/共19页
一、学习编程指令
(一)SIEMENS 802S系统编程指令
(5)LCYC95的指令动作执行过程
纵向、外部加工方式
横向、外部加工方式 第4页/共19页
一、学习编程指令
(一)SIEMENS 802S系统编程指令
(5)LCYC95的指令动作执行过程
【粗切削动作执行过程】 ①用G0方式从初始点至循环加工起始点(系统内部计算)。 ②按照参数R109下的编程角度进行深度进给。 ③在坐标轴平行方向用G1以粗切进给率切削至粗切削交点。 ④用G1/G2/G3方式按粗切进给率进行粗加工。 ⑤在每个坐标轴方向按参数R110中所编程的退刀量退刀,并用G0返回。 ⑥重复以上过程,直至加工至最后深度。
第6页/共19页
一、学习编程指令
(二)FANUC 0i系统编程指令
(3)G71指令段内部参数说明(见下图所示) CNC装置首先根据用户编写的精加工轮廓,在预留出X和Z向精加工余量△u和△w后,计 算出粗加工实际轮廓的各个坐标值。刀具按层切法将余量去除(刀具向X向进刀d,切削 外圆后按e值450退刀,循环切削直至粗加工余量被切除)。此时工件斜面和圆弧部分行 程台阶状表面,然后再按精加工轮廓光整表面最终形成在工件X向留有△u大小的余量、Z 向留有△w大小余量的轴。粗加工结束后,可使用G70指令完成精加工。
⑥在粗车削循环过程中,刀尖半径补偿功能无效。
①U(+) W(+)为零件外轮廓纵向粗车复合循环;②U(-) W(+)为零件内轮廓纵向 粗车复合循环;③U(+) W(-)为零件内轮廓横向粗车复合循环;④U(+) W(-)为 零件内轮廓横向粗加工复合循环;
第8页/共19页
一、学习编程指令
一、学习编程指令
(一)SIEMENS 802S系统编程指令
(5)LCYC95的指令动作执行过程
纵向、外部加工方式
横向、外部加工方式 第4页/共19页
一、学习编程指令
(一)SIEMENS 802S系统编程指令
(5)LCYC95的指令动作执行过程
【粗切削动作执行过程】 ①用G0方式从初始点至循环加工起始点(系统内部计算)。 ②按照参数R109下的编程角度进行深度进给。 ③在坐标轴平行方向用G1以粗切进给率切削至粗切削交点。 ④用G1/G2/G3方式按粗切进给率进行粗加工。 ⑤在每个坐标轴方向按参数R110中所编程的退刀量退刀,并用G0返回。 ⑥重复以上过程,直至加工至最后深度。
第6页/共19页
一、学习编程指令
(二)FANUC 0i系统编程指令
(3)G71指令段内部参数说明(见下图所示) CNC装置首先根据用户编写的精加工轮廓,在预留出X和Z向精加工余量△u和△w后,计 算出粗加工实际轮廓的各个坐标值。刀具按层切法将余量去除(刀具向X向进刀d,切削 外圆后按e值450退刀,循环切削直至粗加工余量被切除)。此时工件斜面和圆弧部分行 程台阶状表面,然后再按精加工轮廓光整表面最终形成在工件X向留有△u大小的余量、Z 向留有△w大小余量的轴。粗加工结束后,可使用G70指令完成精加工。
⑥在粗车削循环过程中,刀尖半径补偿功能无效。
①U(+) W(+)为零件外轮廓纵向粗车复合循环;②U(-) W(+)为零件内轮廓纵向 粗车复合循环;③U(+) W(-)为零件内轮廓横向粗车复合循环;④U(+) W(-)为 零件内轮廓横向粗加工复合循环;
第8页/共19页
一、学习编程指令
工艺典型零件的加工盘套类PPT课件
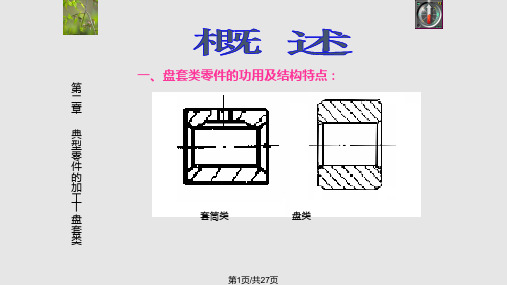
二 章
力、残余应力和切削热等因素的影响而产生变形。为
了防止变形,应注意以下几点:
典
(1)为减少切削力与切削热的影响:粗、精加工应分
型 零 件
开进行,使其变形在精加工过程中得以纠正; (2)为减少夹紧力的影响:工艺上可即把径向夹紧改
的 加 工
为轴向夹紧。 对于精度要求较高的精密套筒(如孔的圆度要求
—
盘 套
—
依靠研具与工件的相对运动,由磨料去除一层极
盘 套 类
微薄金属的光整加工方法。研磨后达到的精度: IT6~IT4,Ra0.1~0.01µm.
第22页/共27页
3、珩磨
第
用带有磨条的珩磨头对工件进行精细加工的一中
二 章
高效率光整加工方法。机械加压式珩磨头结构如图所:
示磨条以一定的压力与内孔表面接触,珩磨头在主轴
第
1、保证盘套类零件各表面位置精度的方法:
二
章
从盘套类零件的技术要求可知,其主要位置精度
典
是内、外圆表面的同轴度及端面与轴线之间的垂直度
型
要求。在加工过程中一般常采用下述方法:
零 件
(1)在一次装夹过程中完成内外表面及端面的加工:
的 加
这种加工方法消除了工件的装夹误差,可获得很
工
高的相对位置精度。但是,这种加工方法的工序比较
—
加 工
表面粗糙度Ra0.8~0.4µm。可在内 圆、万能外圆磨床磨削,多采用纵
盘 套
磨法。如图所示:
Байду номын сангаас
类
第19页/共27页
磨孔与磨外圆的比较:
第
1)磨孔的表面粗糙度略粗大。
二 章
这是因为内圆磨头的砂轮直径小,转速低,很难
- 1、下载文档前请自行甄别文档内容的完整性,平台不提供额外的编辑、内容补充、找答案等附加服务。
- 2、"仅部分预览"的文档,不可在线预览部分如存在完整性等问题,可反馈申请退款(可完整预览的文档不适用该条件!)。
- 3、如文档侵犯您的权益,请联系客服反馈,我们会尽快为您处理(人工客服工作时间:9:00-18:30)。
1、三爪自定心卡盘
三爪自定心卡盘装夹方便、快捷、对中性好且无需找正。三爪卡盘夹紧 力较小,只适合夹紧重量较轻的工件;定心精度存在误差,不适合于同轴 度要求高的工件二次装夹。
① 适用于一次装夹完成的端面、内/ 外圆、倒角、切断的小型盘套类 零件,如图8-1-2所示;
图8-1-2
三爪卡盘装夹工件
② 薄壁套类零件的刚度差,装夹不当或夹紧力过大,易导致工件变形,
利用心轴的圆柱表面与工件定位配合,并保持较小的间隙,便于工件的装卸;
夹紧力较大,但定心精度较锥度心轴低,工件靠螺母压紧,如图8-1-5。
图8-1-5
圆柱心轴
② 锥度心轴 锥度心轴是一种刚性心轴,其外圆呈锥体,锥度为1:1000~1:5000。
工件压入锥度心轴时,工件内孔产生弹性变形而胀紧工件,并借压合处 的摩擦力传递转矩带动工件旋转;锥度心轴不需夹紧元件,心轴与安装孔之 间无间隙,故定位精度高,但能承受的切削力小;工件在心轴的轴向位移误 差较大,不能加工端面;锥度心轴适用于同轴度要求较高的工件的精加工。
一、盘套类零件的技术要求
1、尺寸精度
重要尺寸都有公差或公差带代号,公差值是判断车削工艺能否达到要 求,同时进行尺寸换算的尺寸依据。
2、表面粗糙度
零件表面粗糙度也是评定零件表面质量的一项技术指标,它对零件的配 合性质、工作精度、耐磨性、抗腐蚀性、密封性、外观等都有影响。一般而 言,只要零件上有配合要求或有相对运动的表面,表面粗糙度要求越高,其 参数值越小。
图8-1-10
扩孔钻
3、铰孔 铰孔属于精加工,可达到的尺寸公差等级 为IT9~IT6,表面粗糙度值Ra为3.2~0.2um, 如图8-1-11所示。 4、镗孔
图8-1-11 铰刀
内孔镗削时,由于刀具受到孔径的限制,装夹部分结构要求简单、紧凑,
夹紧件最好不外露,夹紧可靠。为增强刀具刚性尽量选用大断面尺寸刀杆, 减少刀杆长度。内孔加工的断屑、排屑可靠性比外圆车刀更为重要,因而刀 具头部要留有足够的排屑空间。
数控编程及仿真加工
任务 一 简单盘套类零件加工的工艺知识
盘套类零件在机器设备中应用非常普遍,常与轴类零件配合使用。
盘类零件一般指径向尺寸比轴向尺寸大,且最大与最小内外圆直径差
较大,并以端面面积大为主要特征的零件;套类零件一般指内外圆直
径差较小,并以内孔为主要特征的零件。简单盘套类零件主要由端面、
内外圆柱面、形状 常用的镗刀其截面
形状有圆形、矩形和正方形。圆柄车刀多用 于数控车床和车削中心;矩形和方形柄多用 于普通车床,使用时优先选用圆柄车刀(其 刀尖高度是柄部高度的1/2,且柄部是圆形, 有利于排屑),如图8-1-12所示。
孔径所允许的空间限制,这种可能性也经常受到限制,故此,必须考虑到排
屑和刀具的径向移动。
四、盘套类零件刀具及其切削用量的选用
加工内孔是盘套类零件的特征之一,根据内孔的工艺要求,加工方法较 多,常用的有钻孔、扩孔、铰孔、镗孔和磨孔等。内孔加工时常用的刀具有
中心钻、麻花钻及内孔镗刀等。
1、钻孔 钻孔属于粗加工,可达到的尺寸公差等级为IT13~IT11,表面粗糙度值 Ra为25~12.5um。由于麻花钻长度较大,钻芯直径较小而刚性差,又有 横刃的影响,故钻孔有以下工艺特点:
则需要采用开口套装夹,或者扇形卡爪,如图8-1-3所示。
图8-1-3
薄壁套类零件的装夹
任务八
简单盘套类零件的编程与仿真加工
2、四爪单动卡盘
四爪可以单独移动,夹紧力较大,适用于 装夹大型的盘套类或不规则的零件;但需要经
过找正安装,装夹速度慢,不适合批量生产,
如图8-1-4所示。
图8-1-4 四爪单动卡盘
在车床上用四爪卡盘和百分表找正后将工件夹紧,可加工出与外圆同
轴度很高的内孔;对于盘类零件,安装时既要以外圆为准找正与轴线平
行,又要找正端面与轴线垂直。
3、定位心轴
盘套类零件内孔精度要求较高,针对需多次工序才能完成的盘套类零件,
为保证其精度要求,须以内孔为定位基准,才能保证外圆轴线和内孔轴线的 同轴度要求,此时要用心轴定位。 ① 圆柱心轴
知识点
盘套类零件的技术要求 盘套类零件的装夹与定位方法 套类零件的内孔加工的主要特点和要求 内孔加工刀具及其切削用量的选择
由于功能和用途的不同,盘套类零件的结构和尺寸有很大差异,但其结 构上仍存在共同点:大都带有“中孔”,如衬套、齿轮等;主要表面为同轴 度要求较高的内外圆表面;零件壁的厚度较薄且易变形。盘套类零件的内孔 一般做为配合和装配基准,精度要求较高.
图8-1-6
锥度心轴
③ 胀力心轴 依靠锥形弹性套受轴向挤压而产生径向弹性变形来定位夹紧工件,如图8-1-7; 装夹方便,定位精度高,同轴度一般可达 0.01~0.02mm;
适合零件的半精加工和精加工,应用较
为广泛。
图8-1-7 胀力心轴
三、套类零件的内孔加工的主要特点和要求
图8-1-8
内孔加工
1、内孔加工是在工件内部进行的,尤其是加工又深又小的孔时,观察切 削比较困难;刀柄由于受到孔径和孔深的限制,不能制造得太粗或太短;排屑 和冷却比较困难;孔径的测量比较困难。 2、孔加工的一般原则 总是使用刀具悬伸最小并选择尽可能大的刀具尺寸,以便获得最高的稳 定性和精度。当使用大直径镗孔刀杆时,稳定性便得到增强;但由于受零件
3、形状、位置精度
形位公差,是零件精度要求的重要内容,也是确定和影响车削工艺的 重要因素,尤其是按照其要求确定零件的定位基准和测量基准的重要指标。
图8-1-1
盘套类零件的技术要求
二、盘套类零件的装夹与定位方法
盘套类零件的内/外圆柱面、端面与基准轴线都存在相应的形位精度要求,
盘类零件的精基准可以选择外圆,但常以中心孔及一个端面为精加工基准。
① 钻头容易偏斜
图8-1-9
中心钻和麻花钻
② 孔径容易扩大,但孔轴线仍然是直的
③ 孔的表面质量较差
④ 钻削时轴向力大
2、扩孔
扩孔属于孔的半精加工,常作铰削前的预加工或精度不高的孔的最终加
工,可在一定程度上校正钻孔的轴线误差。扩孔可达到的尺寸公差等级为 IT11~IT10,表面粗糙度值为12.5~6.3um,如图8-1-10所示。