循环流化床脱硫过程及其影响因素分析
循环流化床锅炉炉内脱硫原理及影响因素浅析

活性对脱硫性能的影响很 大。如果石灰石的产地不同 ,那么 它们 的活性也是不同的 ,而且差别 比较大。燃烧后表面积大表现 出来 的脱硫效果好 ,表面积大则意味着在反应时接触面积较大。 因此 ,要对石灰石进行选择 ,在选择过程 中要采用科学的方法。 3 . 3 煤 的种类不 同 煤 的种类不 同,脱硫产生效果 也不同 。循环流化床炉 内脱 硫效 率的高低取决于煤 中的含硫 量。一般来说 ,煤在燃烧 中含 硫量越 高 ,那么这种煤 的脱硫效率 就越高 ,但是在此过程 中硫 的排放量 也是很大 的。 目前 为止 ,我国硫 的排放量还没有达 到 国家标 准。如果想要降低硫 的排放量 ,那 么就要尽量使用低硫 煤 。我国循 环流化床锅炉炉 内的脱硫技术 还需要进一步改进 , 要通过提高脱硫效率来减少二氧化硫 的排 出 ,从 而降低成本 。
2 0 1 4 年 第3 期
S c i e n c e a n d T e c h n o l o g y &I n n o v a t i o n I 科 技与创 新
循环流 化床 锅炉炉 内脱硫原理及影 响 因素浅析
支 0 红 娟
( 北京北科欧远科技有 限公 司山西分公 司 ,山西 太原 0 3 0 0 0 6) 摘 要 :众所周知 ,煤在燃烧过程 中会产 生污染性 气体二氧化硫 。如果 想要 对产 生的污染气体进行 有效的控 制 ,就需要 找 到工业生产 中减5 " - 氧化硫产生的方 法。 目前 ,脱硫技术在 实际的生产 中得到 了广泛的应用 ,循 环流化床锅 炉炉 内脱 硫就是 一种有效脱硫方法。
一
是很 重要 的两个部分 ,这两部分对脱硫效率有着很大的影响 。
3 . 2 . 1 石 灰 石 的粒 度
影响循环流化床炉内脱硫效率的因素及实例

影响循环流化床炉内脱硫效率的因素及实例摘要:循环流化床锅炉的燃烧属于低温燃烧(燃烧温度在850~950℃),比较大的热灰颗粒在燃烧系统内循环燃烧,携带密相区的热量,把热量传递给蒸发受热面或过热受热面。
正是由于热灰的循环和燃烧生成SO2在850~900℃的条件下极易与CaO结合为锅炉提供廉价的脱硫措施创造了条件。
关键词:循环流化床锅炉;Ca/S摩尔比;脱硫效率前言:循环流化床锅炉因其环保性能受到中小热电厂的青睐,但因影响脱硫的因素复杂,需要控制的因素较多,使用单位往往片面追求脱硫效率,导致锅炉运行和碱性灰渣处理增加成本以及热效率降低,下面根据循环流化床锅炉的特点具体分析影响脱硫效率的因素及具体计算实例。
一、影响循环流化床脱硫效率的因素1.Ca/S摩尔比的影响Ca/S摩尔比是影响脱硫效率和SO2排放的首要因素。
不加石灰石时,燃料硫约有28.5%的硫分残留于灰渣中,71.5%则以气体的形式排放出来。
采用添加石灰石进行脱硫,脱硫效率在Ca/S比低于2.5时增加很快,而继续增加Ca/S比或脱硫剂量时,脱硫效率增加很少,同时继续增加脱硫剂会增加灰渣热物理损失、增加灰渣处理成本、影响燃烧工况、富余的CaO将使N0x排放升高等。
对循环流化床而言,较为经济的Ca/S比一般在1.5~2.5之间。
2.床温的影响床温的影响主要在于改变了脱硫剂的反应速度、固体产物分布及孔隙堵塞特性,从而影响脱硫效率和脱硫剂的利用率。
从燃烧效率、CO和氮氧化物的排放上考虑,循环流化床锅炉的最佳运行温度在900℃左右,并在900℃左右达到最高的脱硫效率。
3.粒度的影响采用较小的脱硫剂粒度,脱硫效果较好,脱硫粒度越小,对NOX 的刺激作用也越小,而且对于小的脱硫粒度,脱硫温度也可以较高。
循环流化床锅炉的分离和返料系统保证了细颗粒的循环,故一般采用0~2mm,平均100~500μm的石灰石粒度。
粒度太小或者太易磨损的石灰石会增大飞灰的逃逸量,增加静电除尘器负担,并使脱硫效率下降。
循环流化床烟气脱硫影响因素研究
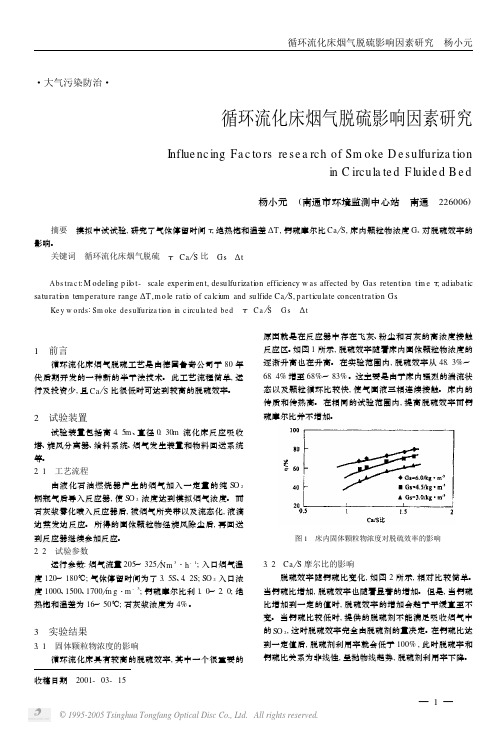
收稿日期 2001-03-15・大气污染防治・循环流化床烟气脱硫影响因素研究Influe nc ing Fa c to rs re s e a rch of Sm oke D e s ulfuriza tionin C ircula te d F luide d B e d杨小元 (南通市环境监测中心站 南通 226006)摘要 摸拟中试试验,研究了气体停留时间Σ,绝热饱和温差∃T ,钙硫摩尔比Ca S ,床内颗粒物浓度G s 对脱硫效率的影响。
关键词 循环流化床烟气脱硫 Σ Ca S 比 Gs ∃tAbs tra c t :M odeling p ilo t -scale experi m en t ,desu lfu rizati on efficiency w as affected by Gas reten ti on ti m e Σ,adiabaticsatu rati on temperatu re range ∃T ,mo le rati o of calcium and su lfide Ca S ,particu late concen trati on Gs.Ke y w o rds :Sm oke de sulfuriza tion in c ircula te d be d Σ C a S Gs ∃t1 前言循环流化床烟气脱硫工艺是由德国鲁奇公司于80年代后期开发的一种新的半干法技术。
此工艺流程简单,运行及投资少,且Ca S 比很低时可达到较高的脱硫效率。
2 试验装置试验装置包括高4.5m 、直径0.30m 流化床反应吸收塔、旋风分离器、给料系统、烟气发生装置和物料回送系统等。
2.1 工艺流程由液化石油燃烧器产生的烟气加入一定量的纯SO 2钢瓶气后导入反应器,使SO 2浓度达到模拟烟气浓度。
而石灰浆雾化喷入反应器后,被烟气所夹带以及流态化,液滴边蒸发边反应。
所得的固体颗粒物经旋风除尘后,再回送到反应器继续参加反应。
循环流化床炉内脱硫影响因数及脱硫组合工艺

表明, 增加 炉 内压力 可 以提 高脱硫效 率 , 因是压 原 力 的提高 可 以提高脱 硫反 应 速度 。 当炉 内压 力从
常压增 至 0 5MP . a时 , 脱硫 效 率 明显 提 高 , 佳脱 最 硫 窗 口温度 也 提 升 了 , 这对 脱 硫 非 常 有 利 。国 内
De u f r z to c o s a d Co b n d s lu i a i n Fa t r n m i e Pr c s e f CFB i r o e s so Bo l e
u n mi
( hn ogBa c o e l t f h aA u iu n ut , io 5 0 , hn ) S a dn rn hP w rPa i lm n m Id s y Zb 5 5 C ia noC n r 2 1
是 当加 入过 多 的脱 硫 剂 时 , 硫 效 率 增 加 得很 缓 脱
炉 内压力是 影 响脱硫 的又一 因素 。运行 结果
慢 , 仅 浪 费 了脱硫 剂 , 加 运 行成 本 , 且 多余 不 增 而
的 C O又 是 生 成 N x的催 化 剂 , N x排 放 量 a O 使 O
增加。
C C + a +C 一 1 3k / l a O— C 0 O, 8 J mo
到 40℃ 时就开 始分解 , 0 但对 不 同煤种 略有 差异 。
一
般 认为 , 机 硫 首 先 分解 为 中问 产 物 ( 有 主要 是
.
H S , 后在 遇氧 和其他 氧 化性 自由基 时逐 步 被 )而 氧化 为 S , O。 无机物 硫 ( e 在 氧 化性 气 氛 下 , 直 接 氧 FS) 可
哪些因素会影响循环流化床锅炉脱硫脱硝效果?

我国大气污染以煤烟型大气污染为主,其主要污染物为烟尘和二氧化硫,大气中二氧化硫的87%来自于煤的燃烧。
近日,国家能源委员会会议明确提出宜煤则煤、推动煤炭清洁高效利用的观点。
在政策的强力引导下,环保型的循环流化床锅炉或将迎来新的发展机遇。
循环流化床锅炉采用流态化燃烧,具有燃料适应性广、环保性能优异、负荷调节范围广、灰渣易于综合利用等优点。
循环流化床锅炉主要包括燃烧设备、物料循环系统、燃煤制备系统、风烟系统和除渣、除灰系统几大部分。
循环流化床锅炉脱硫燃烧技术是一种经济有效的清洁的燃烧技术,接下来我们一起了解下循环流化床锅炉脱硫脱硝效果具体受哪些因素影响。
循环流化床锅炉脱硫工艺的特点是反应在气、固、液三相中进行,循环流化床锅炉脱硫利用烟气显热蒸发水分,最终产物为干粉态,一般与布袋除尘器结合使用。
循环流化床锅炉脱硫技术具有系统简单、初投资和运行费用低、占地面积小、脱硫产物为干态、易于处理等优点,得到了一定的应用,主要的缺点是脱硫率低,吸收剂利用率低。
循环流化床锅炉脱硫效率受到许多因素影响,如脱硫剂的种类粒径、床深气流速度、床温(燃烧温度)、Ca/S等,其中在选定脱硫剂的条件下主要的影响因素有床温、Ca/S等。
1.钙硫比脱硫剂所含钙与煤中硫之摩尔比称为钙硫比(Ca/S)。
在影响脱硫效率的所有参数中,Ca/S影响最大。
各种循环流化床锅炉Ca/S(c)对脱硫率(R)的影响不同,但可用一经验式近似表达:其中m是其他主要性能参:床深、流化速度、脱硫剂颗粒尺寸脱硫剂种类床温和运行压力等的函数,但对固定型号的循环流化床锅炉来讲,m更多地受床温和脱硫剂性能的影响。
国内有关石灰石脱硫特性的研究试验结果,表明在给定的炉型和石灰石粒度运行床温等条件下,随钙硫化的增加其脱硫效率不断提高,且呈现负指数规律增长。
2. 床温循环流化床锅炉的燃烧温度一般控制在800℃~950℃之间。
燃烧温度对脱硫效率的影响也比较大,对于循环流化床锅炉来说存在一个适宜脱硫温度区,大约在800℃~900℃。
循环流化床炉内脱硫影响因素分析试验方案

循环流化床炉内脱硫影响因素分析试验方案1 编制目的1.1 循环流化床锅炉炉内脱硫工艺是近年来迅速发展起来的一种新型脱硫技术。与常规煤粉燃烧过程中的尾部烟气脱硫技术不同,在流化床燃烧中,可以在床层内直接加入钙基脱硫剂,达到减少SO2排放的目的。通过试验分析,探索钙硫比、床温、负荷、石灰石粒径对炉内脱硫的影响特性,发现和排除石灰石系统设备存在的缺陷,为锅炉洁净燃烧、排放达标创造条件。1.2 为了确保循环流化床锅炉安全运行和炉内脱硫试验正常进行,特制定本方案。2 编制依据2.1 《电站锅炉性能试验规程》GB10184-19882.2 《循环流化床锅炉性能试验规程》DL/T964-20052.3 《火电厂环境监测技术规范》DL/T414-20042.4 《火电厂大气污染物排放标准》GB13223-20032.5 《火电厂燃料试验方法飞灰和炉渣可燃物测定方法》DL/T567.6—952.6 工程设计图纸及设备说明书上海锅炉厂编写的“产品说明书”编号802-1-8601上海锅炉厂编写的“锅炉使用说明书”编号802-1-8603克莱德贝尔格曼华通物料输送有限公司编写的“石灰石粉输送系统操作维护手册”等3 系统及主要设备技术规范3.1 系统简介山西平朔煤矸石发电有限责任公司位于山西省朔州市平朔安太堡露天煤矿工业广场,占地面积23.3公顷。目前建有2*50MW+2*300MW直接空冷循环流化床机组。二期选用两台上海锅炉厂生产的SG-1060/17.5-M802型亚临界中间再热、单锅筒自然循环循环流化床锅炉。锅炉采用岛式布置,全钢构架,紧身密闭。锅炉采用支吊结合的固定方式,锅炉主要操作平台标高为7600。锅炉采用单锅筒自然循环、集中下降管、平衡通风、绝热式旋风气固分离器、循环流化床燃烧方式、风水冷流化床冷渣器和滚筒冷渣器相结合,后烟井内布置对流受热面,过热器采用3级喷水调节蒸汽温度,再热器采用外置床调节蒸汽温度为主,事故喷水装置调温为辅。设计煤种为平朔煤矸石(属高硫烟煤)。公司采用循环流化床炉内脱硫技术来控制SO2的排放。循环流化床炉内脱硫工艺是近年来迅速发展起来的一种新型脱硫技术,其工作原理是燃料和作为吸收剂的石灰石粉送入燃烧室下部,一次风从布风板下送入,二次风从燃烧室中部送入,气流使燃料颗粒、石灰石粉和循环灰一起在循环流化床内强烈扰动并充满燃烧室,石灰石在炉内经过煅烧后分解生成CaO,CaO与SO2反应生成CaSO4,于是原煤中的硫分就被固化为硫酸钙进入灰渣中,最后排出床层,以达到脱硫的目的。影响循环流化床炉内脱硫有很多因素,诸如Ca/S摩尔比、石灰石的品质(粒径、纯度、反应活性)、床温、气相停留时间、固体停留时间、炉膛高度、物料循环倍率、旋风分离的效率、负荷变化的影响、氧浓度、煤种等。3.2 锅炉主要设计参数。3.3 脱硫控制系统技术参数4 试验内容4.1 试验目的:循环流化床炉内脱硫是近年来随着循环流化床机组的特殊结构构造和特殊燃烧方式应运而生的新型脱硫技术。流化床中煤和石灰石一起给入炉膛,燃烧后煤中之后与脱硫剂反应而固定,而且脱硫系统简单。在燃料适应性广、的硫份生成SO2燃烧效率等方面循环流化床燃烧技术向前推进了一步,在钙硫摩尔比为2左右时就可以达到85%-90%的脱硫效率,因而是一种很有前途的技术。不过,现在许多专家学者对炉内脱硫这项不成熟的技术都在一定程度上持怀疑的态度,不太相信炉内脱硫能够达到如此好的效果。众说纷纭,莫衷一是。1) 通过本次试验,对炉内脱硫工艺和设备特性进行分析、优化;2) 通过本次试验,分析钙硫比、床温、负荷、石灰石粒径对炉内脱硫的影响特性;3) 通过本次试验,分析试验数据,指导炉内脱硫效率的提高;4) 通过本次试验,对炉内脱硫进行对象特性分析,建立炉内干法脱硫的数学模型,为实现石灰石系统的自动控制提供理论依据。4.2 试验机组:二单元#4 300MW机组。4.3 试验时间:2010年1月——2011年3月。4.4 试验参与部门:生产技术部、安环部、发电二部、产业部、化验中心、烟气在线监测。4.5 试验组人员构成:组长:副组长:成员:安环部监督员、运行锅炉专工、运行值长及当值运行人员、化验室化验员、仪电部、在线监测值班员。要求:各节点必须派专人负责,便于统一协调。4.6 试验内容:1) 分析煤的水分、灰分、挥发份、硫含量、发热量、粒径;2) 分析石灰石的水分、纯度、粒径;3) 分析底渣、飞灰中的可燃物含量和过剩CaO的含量等;4) 在高负荷(≥280MW)条件下,稳定负荷、煤量、床温、床压、一次风量、二次风量、返料量等条件,做钙硫比和脱硫效率关系的试验;5) 在较高负荷(220~240MW)条件下,稳定负荷、煤量、床温、床压、一次风量、二次风量、返料量等条件,做钙硫比和脱硫效率关系的试验;6) 在较高负荷(220~240MW)条件下,稳定负荷、煤量、钙硫摩尔比、床压、一次风量、二次风量、返料量等条件,做床温和脱硫效率关系的试验;7) 在较高负荷(220~240MW)条件下,改变石灰石的粒径(D=1.1),稳定负荷、煤max量、床温、床压、一次风量、二次风量、返料量等条件,做钙硫比和脱硫效率关系的试验。5 试验应具备的条件石灰石脱硫影响因素分析试验的成功与否,首要前提是保证机组的安全运行,所以试验期间必须保证是机组设备、系统的正常运行。5.1石灰石制粉车间制粉车间提供满足试验要求所需的石灰石粉量,所制备的石灰石粉品质符合要求;5.2 脱硫控制系统运行、维护部门要确保脱硫控制系统设备正常运行,出现故障时要及时处理;5.3 烟气在线监测烟气在线监测员要确保CEMS烟气在线监测系统的正常运行,采集数据准确、及时,数据保存完整备查;5.4 煤化验室实验室人员要对化验设备、测量仪器校核准确,确保实验数据的准确性;5.5 仪电部门要对#4炉各测点的准确性进行校验、确保试验数据的准确性;5.6 运行人员调整控制运行工况稳定,符合试验要求。6 组织分工试验组组长:负责整个试验过程的安全、技术,以及各个方面、各个部门之间的协调。试验组副组长:负责指导试验工作的具体实施,重要节点把关,整理分析试验数据,撰写试验报告。试验组成员:在试验组组长、副组长领导下,各司其职、密切配合、保障试验工作的顺利进行。7 试验步骤7.1 试验准备工作——仪表的校准(1)皮带秤的校准。校准方案:(2)温度、压力、电流测点的校准。校准方案:(3)烟气在线监测系统的校准。校准方案:1)利用便携式烟气分析仪对水平烟道的污染物成份进行测量;2)测量的数据和在线监测系统的污染物实时数据进行比对;3) 根据比对结果对在线监测系统烟气分析仪的量程和零点进行校准。(4)石灰石给料机的转速和石灰石给料量实时对应的校准。石灰石输送系统在设计与安装时,对石灰石瞬时流量有个计算公式:/100瞬时流量F=(0.03m3/min*60*1.2t/m3)*S转速校准方案:1) 对#4炉石灰石粉库清空;2) 向#4炉石灰石粉库装入1车的石灰石粉,石灰石粉运输车车需要过磅,计算出入库的石灰石粉量T;3) 记录下石灰石投运前的加入石灰石累加量A1;4) 给料机进行正常输粉,密切关注给料机电流和压缩空气的压力变化,保证输粉正常;5) 待石灰石仓库输粉完毕后,记录粉库清空所用时间,并记录石灰石的累加量A2。6) 根据石灰石的累加量可以算出根据计算所得的石灰石用量A=A2-A1,把它与入库的石灰石粉量T,进行比较;7) 进行三次平行试验;8) 若A=T,说明转速和给料量的关系是准确的。如有偏差,分析原因,进行校正。7.2 试验工况(1)在高负荷(≥280MW)条件下,稳定机组负荷,控制床温870±5℃,床压7±0.3kPa,煤量、一次风量、二次风量、返料量等条件基本不变,获取钙硫比和脱硫效率关系的相关试验曲线组。第一步,控制钙硫比在 1.8(投石灰石粉量的数据由试验组提供指导)不变化,观的浓度,保持试验时间不少于3小时;察SO2的浓度变化趋势,同时观察相关参数第二步,把钙硫比从1.8调整到2.0,观察SO2的变化情况,并保持钙硫比在2.0情况下试验时间不少于3小时;第三步,把钙硫比从2.0调整到2.2(Ca/S=2.2是设计值),观察SO的浓度变化趋2势,同时观察相关参数的变化情况,并保持钙硫比在2.2情况下试验时间不少于3小时;的浓度变化趋势,同时观察相关参数第四步,把钙硫比从2.2调整到2.4,观察SO2的变化情况,并保持钙硫比在2.4情况下试验时间不少于3小时;的浓度变化趋势,同时观察相关参数第五步,把钙硫比从2.4调整到2.6,观察SO2的变化情况,并保持钙硫比在2.6情况下试验时间不少于3小时。(2)在较高负荷(220~240MW)条件下,稳定机组负荷,控制床温820±5℃,床压7±0.3kPa,保持煤量、一次风量、二次风量、返料量等条件基本不变,获取钙硫比和脱硫效率关系的相关试验曲线组。第一步,控制钙硫比在 1.8(投石灰石粉量的数据由试验组提供指导)不变化,观的浓度,保持试验时间不少于3小时;察SO2的浓度变化趋势,同时观察相关参数第二步,把钙硫比从1.8调整到2.0,观察SO2的变化情况,并保持钙硫比在2.0情况下试验时间不少于3小时;的浓度变化趋第三步,把钙硫比从2.0调整到2.2(Ca/S=2.2是设计值),观察SO2势,同时观察相关参数的变化情况,并保持钙硫比在2.2情况下试验时间不少于3小时;的浓度变化趋势,同时观察相关参数第四步,把钙硫比从2.2调整到2.4,观察SO2的变化情况,并保持钙硫比在2.4情况下试验时间不少于3小时;的浓度变化趋势,同时观察相关参数第五步,把钙硫比从2.4调整到2.6,观察SO2的变化情况,并保持钙硫比在2.6情况下试验时间不少于3小时。(3)在较高负荷(220~240MW)条件下,稳定机组负荷,控制钙硫比 2.2±0.1,床压7±0.3kPa,保持煤量、一次风量、二次风量、返料量等条件基本不变,获取床温和脱硫效率关系的相关试验曲线组。浓度,保持试验时间不少于3小第一步,控制密相区床温在800℃不变化,观察SO2时;第二步,通过调整二次风量,把密相区床温从800℃调整到810℃,观察SO的浓度2变化趋势,同时观察相关参数的变化情况,并保持床温在810℃不变化、试验时间不少于3小时;第三步,通过调整二次风量,把密相区床温从810℃调整到820℃,观察SO的浓度2变化趋势,同时观察相关参数的变化情况,并保持床温在820℃不变化、试验时间不少于3小时;第四步,通过调整二次风量,把密相区床温从820℃调整到830℃,观察SO的浓度2变化趋势,同时观察相关参数的变化情况,并保持床温在830℃不变化、试验时间不少于3小时;第五步,通过调整二次风量,把密相区床温从830℃调整到840℃,观察SO的浓度2变化趋势,同时观察相关参数的变化情况,并保持床温在840℃不变化、试验时间不少于3小时。(4) 在较高负荷(220~240MW)条件下,稳定机组负荷,控制床温870±5℃,床压7±0.3kPa ,保持煤量 、一次风量 、二次风量 、返料量 等条件基本不变,获取钙硫比和脱硫效率关系的相关试验曲线组。第一步,控制钙硫比在 1.8(投石灰石粉量的数据由试验组提供指导)不变化,观察SO 2的浓度,保持试验时间不少于3小时;注:这次改变石灰石粉的粒径,把它D max =1.6(试验工况(1)~(3)用石灰石粉粒径D max =1.6)改为D max =1.1,与试验工况(2)进行试验对比,验证石灰石粒径对脱硫效果的影响。第二步,把钙硫比从1.8调整到2.0,观察SO 2的浓度变化趋势,同时观察相关参数的变化情况,并保持钙硫比在2.0情况下保持试验时间不少于3小时;第三步,把钙硫比从2.0调整到2.2(Ca/S=2.2是设计值),观察SO 2的浓度变化趋势,同时观察相关参数的变化情况,并保持钙硫比在 2.2情况下保持试验时间不少于3小时;第四步,把钙硫比从2.2调整到2.4,观察SO 2的浓度变化趋势,同时观察相关参数的变化情况,并保持钙硫比在2.4情况下保持试验时间不少于3小时;第五步,把钙硫比从2.4调整到2.6,观察SO 2的浓度变化趋势,同时观察相关参数的变化情况,并保持钙硫比在2.6情况下保持试验时间不少于3小时。7.3 试验相关工作(1) 燃煤实验室人员在试验进行中,及时对入炉煤质进行一次检测;将所测数据提供试验组,(煤质检测项目包括煤的水分、灰分、挥发份、硫含量、发热量、粒径)。(2) 燃煤实验室人员在试验进行中,及时对入炉石灰石品质进行一次检测,将所测数据提供试验组,(石灰石成分分析项目包括水分、CaO 含量、粒径)。(3) 燃煤实验室人员在试验进行中,及时对炉渣、飞灰的可燃物含量、过剩CaO 含量进行一次检测,将所测数据提供试验组。8 试验数据的分析、整理每天试验结束后,应对运行记录和试验数据进行整理、分析,以便及时了解运行情况、脱硫情况、试验措施存在的问题以及脱硫系统对机组运行造成的影响,为后续试验提供参考,指导接下来的试验工作,圆满地完成该阶段的各项试验,为试验报告的书写提供依据。9 事故预案机组安全注意事项按各岗位“运行规程”执行,针对本次试验,提出几点相关的事故预案:9.1 在试验开始前,须得到当班值长的许可与批准;9.2 试验过程中出现的返料不正常的情况,应及时加启流化风机;9.3 试验过程中,随着石灰石的给入量的增加,床压会随之升高。一旦床压升高至9kPa 及以上,应立即停止试验;9.4 试验过程中机组出现异常工况时,立即停止试验,运行人员按规定处理。试验过程中,试验组成员应坚守岗位,各司其职、积极配合。运行人员要做好预想并根据情况及时调整、及时消除故障,以确保试验工作的安全、顺利地进行。后附:1、煤质测量方案2、石灰石纯度试验方案3、筛分分析法4、试验质量控制点5、脱硫试验数据记录表附录1 煤质测量方案一、煤﹑飞灰、炉渣和石灰石的采样和分析项目按照实验方案在实验前2天采取准备用来做实验的煤样做全水、内水、灰分、挥发份、发热量、全硫、粒度以上全项目分析,并初步确定试验期间的钙硫比,1.在煤堆上采样方法按照以下步骤执行依据煤堆形状在煤堆的顶部(距顶面0.5m),底部(距底部0.5m)和中部(顶部到底部的中央).先除去0.2m的表层煤,用煤样铲采取一铲,将每个样迅速装入塑料样品袋,并贴好标签。迅速送往实验室。入炉煤按照各实验阶段分别采样,间隔为1小时,化验全硫。其他工业分析项目取每阶段混合样进行分析,项目为全水、内水、灰分、挥发份、发热量、粒度。2 .飞灰的采样根据实际情况安排采样地点和间隔。每次0.5kg。3. 炉渣的采样按照各实验阶段分别采样,间隔为1小时,每次0.5kg。取每阶段混合样进行分析可燃物、粒度、氧化钙含量。4.石灰石的采样在准备实验前,由制粉车间工作人员在出料皮带口取样,间隔1小时,每次0.5kg。取每批次石灰石混合样进行水分、氧化钙含量、粒度的分析。5.关于样品的保存样品统一使用现在我厂二期入厂煤使用的塑料样品袋保存,每次取样后贴好标签,注明取样时间、地点、取样人和样品名称,封口后送往化验室。送样人员应配合实验人员做好废样的处理工作。二、煤质测量方案1.全水分的测定(国标D法)1.1分析步骤a准确称取粒度小于13mm的煤样500g(精确至0.5g)于预先称重并干净的浅盘内。b将盘内煤样均匀地摊平,放入预先鼓风并加热到105-110℃的干燥箱内,在此条件下干燥2小时。c从干燥箱中取出浅盘,立即称重(称准至0.5g)并记数。d进行检查性干燥,每次30分钟,直到连续两次干燥煤样的质量减少不超过0.5g或质量增加为止。在后一种情况下,采用质量增加前一次的质量为计算依据。全水分小于2.0%,不必进行检查性试验。1.2计算 Mt =m1/m×100式中: Mt—煤样的全水份, % ;m1—干燥后煤样减少的质量,g ;m —煤样的质量,g 。2. 空气干燥基水分的测定(空气干燥法)2.1分析步骤a.在预先干燥并已称量过的称量瓶内称取粒度小于0.2mm的空气干燥煤样(1±0.1)g,称准到0.0002g,平摊在称量瓶中。b.打开称量瓶盖,放入预先鼓风并已加热到105~110℃干燥箱内。在一直鼓风的条件下,烟煤干燥1h,无烟煤干燥1~1.5h。注:预先鼓风是为了使温度均匀。将装有煤样的称量瓶放入干燥箱前3~5min开始鼓风。c.从干燥箱中取出称量瓶,立即盖上盖,放入干燥器中冷却至室温(约20min)后称量。d.进行检查性干燥,每次30min,直到连续两次干燥煤样的质量减少不超过0.0010g或质量增加时为止。在后一种情况下,采用质量增加前一次的质量为(%)计算依据。水分在2.0%以下时.不必进行检查性干燥。2.2结果的计算空气干燥煤样的水分按下式计算:m1M=──× 100 --------------------(1)adm——空气干燥煤样的水分,单位为%。式中: Madm ——称取的空气干燥基样的质量,单位g。m——煤样干燥后失去的质量,单位g。13.灰分的测定(快速灰化法)3.1分析步骤a 在预先灼烧至质量恒定的灰皿中,称取粒度小于 0.2 mm的空气干燥煤样(1±0.1) g,称准至0.0002g,均匀地摊平在灰皿中。b 将马弗炉加热到850℃,打开炉门,将放有灰皿的耐热瓷板或石棉板缓慢地推入马弗炉中,先使第一排灰皿中的煤样灰化。待5~10min后煤样不再冒烟时,以每分钟不大于2cm的速度把其余各排灰皿顺序推入炉内炽热部分(若煤样着火发生爆燃,试验应作废)。c 关闭炉门,在(815±10)℃温度下灼烧40min。d从炉中取出灰皿,放在空气中冷却5min左右,移入干惧燥器中冷却至室温(约20min)后,称量。e进行检查性灼烧,每次20min,直到连续两次灼烧后的质量变化不超过0.0010g为止。以最后一次灼烧后的质量为计算依据。如遇检查性灼烧时结果不稳定,应改用缓慢灰化法重新测定。灰分低于15.00%时,不必进行检查性灼烧。灰分结果的计算3.2 空气干燥煤样的灰分按下式计算:m1A= ———× 100adm式中: A ad——空气干燥煤样的灰分,单位%。m ——称取的空气干燥煤样,单位g。——灼烧后残留物的质量,单位g。m14.挥发分的测定4.1分析步骤a.在预先于900℃温度下灼烧至质量恒定的带盖瓷坩埚中,称取颗粒小于0.2mm的空气干燥煤样(1±0.01)g(称准至0.0002g),然后轻轻振动坩蜗,使煤样摊平,盖上盖。放在坩埚架上。b.将马弗炉预先加热至920℃左右。打开炉门,迅速将放有坩埚的架子送入恒温区,立即关上炉门并计时,准确加热7min。坩埚及架子放入后,要求炉温在3min内恢复到(900±10)℃.此后保持在(900±10) ℃,否则此次试验作废。加热时间包括温度恢复时间在内。c.从炉中取坩埚,放在空气中冷却5min左右,移入干燥器中冷却至室温(约20min)后称量。4.2挥发分结果的计算空气干燥煤样的挥发分按下式计算:m1Vad = ———× 100 - Madm式中:Vad──空气干燥煤样的挥发分,单位%。m1──空气干燥煤样的质量,单位g。m──煤样加热后减少的质量,单位g。Mad──空气干燥煤样的水分,单位%。5.煤中全硫测定方法(GB/T214-1996:库仑滴定法)5.1试验步骤a将自动定硫仪升温至1 150℃ ,开动抽气泵,将电解液吸入电解池中。b 在前3个瓷舟中称取非测定用煤样并覆盖三氧化钨,于以后瓷舟中称取粒度小于0.2mm的空气干燥煤样0.05g(称准至0.0002g),将重量对应编号输入定硫仪操作软件中。c在煤样上盖一薄层三氧化钨,将瓷舟置于送样托盘上,开始实验,煤样即自动送进炉内,测定随即开始。5.2挥发分结果的计算试验结束后,显示出煤样中硫的百分含量。6.发热量的测定6.1测定步骤a 在不锈钢坩埚中精确称取粒度小于0.2mm的空气干燥机试样0.9~1.1g(称准到0.0002g)。放入坩埚支架中,绑好点火丝,往氧弹中加入10mL蒸馏水。小心拧紧氧弹盖,注意避免燃烧皿和点火丝的位置因受振动而改变,往氧弹中缓缓充入氧气,直到压力到2.8~3.0Mpa,充氧时间不得小于15s。b将氧弹放入对应的内桶。然后输入相应的数据,全水分、空气干燥基水分、全硫、氢含量,进行试验。c若出现点火失败,在确定是煤质差的情况下,应取出重新试验,先于坩埚中加入0.15g(准确至0.0002g)的已知热量的苯甲酸,再称量0.85g(准确至0.0002g)的试样,输入计算机进行试验。6.2发热量结果的计算试验结束后,即可得出弹筒发热量Qb 、空干基高位发热量Qgr,ad、收到基低位发热量Qnet,ar。7.飞灰和炉碴可燃物的测定方法7.1分析步骤同GB212中快速灰化法测定灰、渣的灰分(Aad%)。7.2结果计算CMad =100-Aad式中:CMad──空气干燥基灰渣样的可燃物含量,%。附录2 石灰石纯度试验方案试剂:EDTA标准溶液 0.02mol/L;铬黑T指示剂;钙指示剂;三乙醇胺1:1;HCl溶液1:1;NaOH溶液20%;氨性缓冲溶液PH=10.0;酒石酸钠溶液5%。实验步骤:1)试液的制备:取石灰石试样Wg,放入250ml烧杯,徐徐加入8-10mlHCl溶液,盖上后加热至近沸,用HCl溶液检查试样溶解是否完全,确认以后,冷却后,转入250 ml容量瓶,稀释至刻度,摇匀,待用。2)取25..00ml试液于250ml锥形瓶,加水20ml,加5%酒石酸钠,三乙醇胺各5ml,摇匀,加NaOH溶液10ml,调节PH值到12-14,再加0.01g钙指示剂。用EDTA溶液滴定至溶液由红色变成蓝色,记下体积读数V2,。平行测定2-3次。3)计算:其中:V2——滴定钙时所用EDTA体积,单位ml;——EDTA的浓度,单位g/mol;W——试样质量,单位g;——CaO摩尔质量,单位g/mol。附录3 筛分分析法附录4 试验质量控制点机组名称:平朔煤矸石电厂#4机组专业:锅炉系统名称:脱硫控制系统试验调试负责人:附录5 脱硫试验数据记录表脱硫试验数据记录注:以上数据十分钟记录一次,最后绘制成图像。脱硫试验原料分析数据记录。
浅析循环流化床锅炉脱硫

摘 要 : 用 循 环 硫 化 燃 烧 理 论 所 设 计 出来 的 节 能 高 效 且 环 保 的 技 术 就 是 数 量 成 比例 也 是 随 着 钙 量 的 增 加 也 在 不 断 的 增 加 。 当钙 硫 比 超 过 运 循 环流 化 床 锅 炉 脱 硫 技 术 ,该 技 术 不 仅 能 有 效 降 低 污 染 物 的 产 出和 排 污 系 25时 , 断投 入钙 量 也 无 法 起 到 提 高 脱 硫 效 率 的效 果 , 样 既 造 成 . 不 这 数 , 能 有 效 地 节 约 生 产 成 本 , 经 济 效 益 和 环 境 效 益 上 , 实 现 双 赢 效 果 。 脱 硫 剂 的浪 费 , 使 得 灰 渣 的物 理 热 损 失 大 为增 加 。 还 在 能 也 本 文就 循 环 流 化 床 锅 炉 脱 硫 展 开 了探 讨 。 关键词 : 环流化床锅炉 循 脱硫 原理 影 响 因素
24 床 料 粒 度 脱 硫 效 率 还 会 受 到 脱 硫 剂 和 燃 料 的 粒 度 , . 以及 二 者 之 间 粒径 的 分 布 的 影 响 。 为 了使 S 扩 散 到 脱 硫 剂 的核 心 处 , O, 并 煤 炭 一 直 是 我 国的 主 要 能 源 之 一 , 全 国 总 能 源 消 费 中 , 炭 消 在 煤 增 大参 与 反 应 面 积 , 于 脱 硫 , 以采 用 较 小 粒 径 的 石灰 石 。 而 , 利 可 然 也 耗 就 占 了将 近 7 % , 0 而用 煤 大 户 之 一就 为 火 力 发 电。 在 燃 烧 煤 的过 不 能用 粒 度 过 小 的 石 灰 石 , 是 所 使 用 的 石灰 石 太 易磨 损 , 就 会 加 或 这 程 中 , 有 大 量 的 S 、 尘 、 O 等 有 害
循环流化床脱硫过程及其影响因素分析

直 接 影 响 到 装 置 的 脱 硫 效 率 和 钙 硫 比 C a / S。 通常要求 , C a O含量 大 于 8 0 %, 粒
度小于2 毫米 ; 活 性 指 标 比较 严 格 , 要 求 达
到 小 于4 ai r n。 ( 3 ) 颗 粒物 浓 度 。
1 技术特 点
3Байду номын сангаас影响脱 硫的主要因素
工业技术
S C I E N C E & T E C H N O L O 0 Y 。 2 0 。 1 3 N 0 。 . 1 1 . 1 j 2 圆
循 环 流 化 床 脱 硫 过 程 及 其 影 响 因素 分 析
胡 晓波 金伟 王广 廷 ( 林州 市环 境保护局 河南林 州 4 5 6 5 5 0 )
烟 气 循环 流 化 床脱 硫 ( C F B -F GD ) 工 艺 C a ( OH) 2 + H2 C a S 0 3 ‘ H2 0+H2 0 是2 0 世纪 8 0 年 代 德 国 鲁奇 ( L u r g i ) 公 司开 发 ( 3 ) 的一种新 型半干法脱 硫工艺 。 目前 烟 气 循 部分 C a S O  ̄ ・ 0被 烟 气 中 的 D 2 氧化 : 环 流化 床 脱 硫 工 艺 已 经达 到 工 业 应 用 水 平 Ca SOs ‘ 0 + o2+ H2 0 C a S O4 ・ 2 0 的 主要 有 以 下 几 种 工 艺 流程 : 德国L u r g i 公 ( 4 ) 司 开 发 的 典 型 烟 气 循 环 流 化 床 脱 硫 工 艺 烟 气 中 的 H C I 和 等 酸 性 气 体 同 时 ( C F B ) , 德 国Wu l f f 公 司开发 的烟 气 回流式 循 a ( O H) , 脱除: 环流化床 脱硫 工 艺( RC F B ) I 丹麦 L . F . S m i t h 也被 C C a ( O H) 2 + Ⅳ c f c f 2 +2 0 ( 5 ) 公 司 开 发 的 气 体 悬 浮 吸 收 烟 气 脱 硫 工 艺 ( GS A) 等。 C a ( O H) 2 +胛 c a G +2 H2 O ( 6 )
2、循环流化床燃烧脱硫法解析
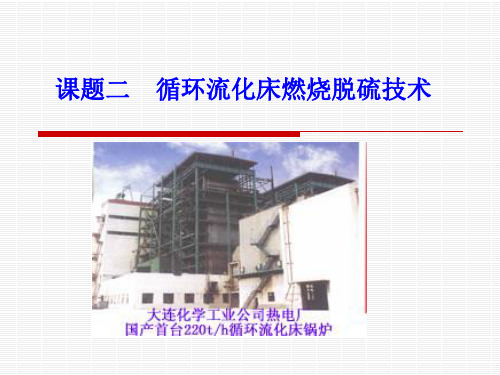
三、影响脱硫的主要因素
2、燃烧温度 对于常压流化床锅炉,有一最佳脱硫温度范 围,为800—850℃左右。 3、运行压力 在增压鼓泡流化床中,往往采用易于煅烧的 白云石。而在增压循环流化床中,则通常从 炉膛下部加入石灰石让其煅烧,煅烧后的石 灰石在主燃烧区进行脱硫。
三、影响脱硫的主要因素
4、床深及气流速度 增大床深或减小气体流速可提高脱硫效果, 这两个参数的作用大体相等,但影响方式相 反。 通常定义一个“表观气体停留时间”ts(即 床深与表观气体流速之比)来表示它们的影 响。
课题二
循环流化床燃烧脱硫技术
循环流化床燃烧脱硫技术
流化床技术简介 流化床燃烧脱硫的化学过程 影响脱硫效果的主要参数 改进流化床燃烧脱硫的措施
一、流化床燃烧脱硫技术应用概况
(一)应用概况 流化床技术首先是作为一种化工处理技术于 20世 纪 20年代由德国人发明的。 将流化床技术应用于煤的燃烧的研究始于20世纪 60年代。 由于流化床燃烧技术具有煤种适应性宽、易于实现 炉内脱硫和低NOx排放等优点。 在能源和环境等诸方面显示出鲜明的发展优势。 如今,流化床燃烧作为更清洁、更高效的煤炭利用 技术之一,正受到世界各国的普遍关注。
三、影响脱硫的主要因素
6、脱硫剂的孔隙直径分布 小孔能在单位脱硫剂重量下提供大的孔隙表 面积,但其入口容易堵塞; 大孔可提供通向脱硫剂内部的便利通道,却 又不能提供大的反应表面。 良好的脱硫剂应在大、小孔之间找到适当的 平衡,并提供很大的孔隙容积。
三、影响脱硫的主要因素
7、脱硫剂种类 目前普遍采用天然石灰石和白云石作脱硫剂 。 (1)常压运行时,倾向于采用石灰石作脱硫剂; (2)增压鼓泡流化床锅炉采用白云石较好。增 压循环流化床锅炉,可在炉膛下部加入石灰石, 使其在还原性气氛中预先煅烧。 (3)脱硫剂的来源也直接制约着脱硫剂的选择。
循环硫化床锅炉脱硫率主要影响因素

脱硫效率更高、 脱硫成本低 , 操作简单 、 无水污染等特
点 。通常 人 们 将 煤 燃 烧 对 原 煤 散 烧 在 相 同锅 炉 出力 下 S O : 排放 量下 降 的百分 率来 表示 脱硫 率 。 随着 我 国社会 经济 的高 速发 展 , 环 境 问题 日益 突
第2 9卷
第1 期
2 0 1 3年 1月
1 . 2 燃 煤 中 的硫 以黄 铁 矿 、 硫 酸盐 、 有机硫 、 元 素 硫
循 环 流化 床 锅 炉 之所 以在 近 年 来 能 得 到 很 大 的 发展 , 除 了其 燃烧 适 应 性 广 、 负荷 调 节 性 好 、 燃 烧 效 率 高 以外 , 一 个 重 要 的原 因是 它具 有 优 良的环 保 性 能 。
一
因素分 析概 括 , 以期 对 即将 投 人 到脱 硫 工 作 的技 术 工 作 者起 到抛 砖 引玉 的作用 。 下面 , 简单 阐述循 环 流 化 床锅 炉 添 加 石 灰石 脱 硫
A di s c u s s i o n o n t h e ma i n f a c t o r s a fe c t i ng t he de s u l f ur i z a t i o n r a t e o f t h e lu f i di z e d bo i l e r
出, 已成为 全 面建设 和谐 社 会 的制 约 因素 之 一 。 国家
节能减排工作力度 的加强 , 使供热锅炉达标排放 已将
成 为供 热 企 业 迫 在 眉 睫 的 重 要 工 作 之 一 。所 以怎 样
全, 不过使 用石 灰 石作 为 脱硫 吸收 剂 时还 要 考 虑 石灰 石 的纯度 和活性 , 因为 石 灰石 与氧 二化 硫 的反 应 速度 主要 取决 于石 灰 石 的粒 度 和 颗 粒 比表 面 积 。循 环 流
循环流化床锅炉脱硫系统存在的常见问题及解决方案
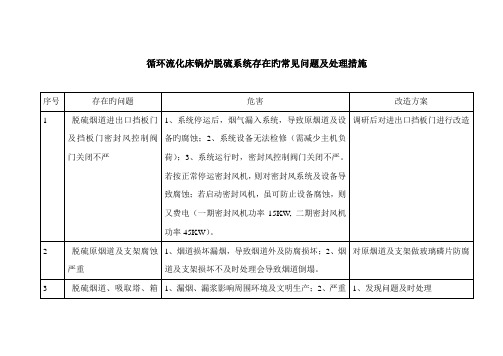
2
脱硫原烟道及支架腐蚀严重
1、烟道损坏漏烟,导致烟道外及防腐损坏;2、烟道及支架损坏不及时处理会导致烟道倒塌。
对原烟道及支架做玻璃磷片防腐
3
脱硫烟道、吸取塔、箱罐及衬胶管道(包括管件)防腐局部损坏
1、漏烟、漏浆影响周围环境及文明生产;2、严重威胁脱硫安全稳定运行
1、发现问题及时处理
2、对某些管径在600以上旳浆液管道,根据不一样旳磨损状况,逐年进行改造,由本来旳衬胶管道改为某些防磨饰旳管道(根据不一样工况,可更换为玻璃钢、TSS涂覆、内衬陶瓷等管道);3、对管径在600如下旳浆液管道、管件,根据不一样旳磨损状况,逐年进行改造,由本来旳衬胶管道改为PP-H管道。
4
浆液循环泵叶轮、入口护套及机械密封等过流部件磨蚀严重
1、工艺水箱进水电动闸阀不能正常调整;2、一台脱硫管道检修,另一台也不能正常运行;3、除雾器水管易冻;4、冲洗水管检修,脱硫系统也得停运;5、回水不畅导致氧化风机油箱进水。如将冷却水直排吸取塔地坑,吸取塔液位无法控制,直排污水管道挥霍水源
对二期脱硫工艺水系统进行改造
10
#3、#4氧化风机噪声大,隔音罩小
1、在脱水机排泥口安装控制阀门2、在排泥斗装一排水管排到石膏脱水地坑
19
烟道及设备旳保温铝板边角不牢固
1、刮风时,保温铝皮常常掉落,会导致对人员及设备旳伤害2、恢复工作量大
对烟道及设备旳保温铝板边角加固
20
#3-#4脱硫浆液循环泵减速机振动、噪声大
损坏设备轴承,设备不能正常工作
对减速机或联轴器改造
21
1、影响周围环境。
对#3、#4氧化风机隔音罩加大改造
11
二期真空皮带脱水机、脉冲悬浮泵电机温度高
循环流化床锅炉石灰石炉内脱硫影响因素研究
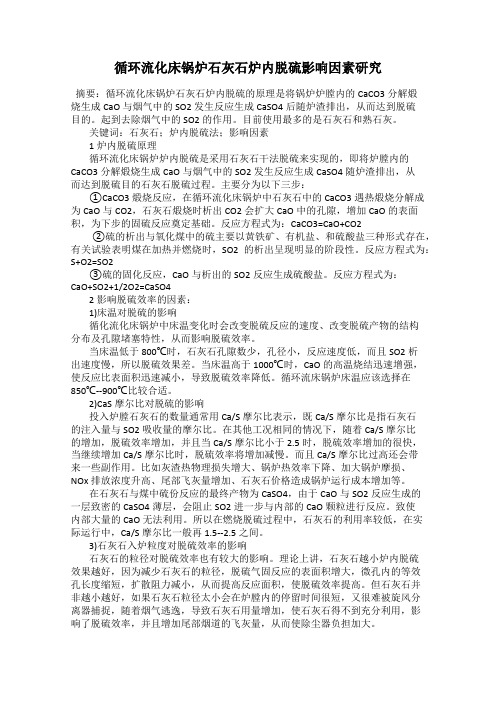
循环流化床锅炉石灰石炉内脱硫影响因素研究摘要:循环流化床锅炉石灰石炉内脱硫的原理是将锅炉炉膛内的CaCO3分解煅烧生成CaO与烟气中的SO2发生反应生成CaSO4后随炉渣排出,从而达到脱硫目的。
起到去除烟气中的SO2的作用。
目前使用最多的是石灰石和熟石灰。
关键词:石灰石;炉内脱硫法;影响因素1炉内脱硫原理循环流化床锅炉炉内脱硫是采用石灰石干法脱硫来实现的,即将炉膛内的CaCO3分解煅烧生成CaO与烟气中的SO2发生反应生成CaSO4随炉渣排出,从而达到脱硫目的石灰石脱硫过程。
主要分为以下三步:①CaCO3煅烧反应,在循环流化床锅炉中石灰石中的CaCO3遇热煅烧分解成为CaO与CO2,石灰石煅烧时析出CO2会扩大CaO中的孔隙,增加CaO的表面积,为下步的固硫反应奠定基础。
反应方程式为:CaCO3=CaO+CO2②硫的析出与氧化煤中的硫主要以黄铁矿、有机盐、和硫酸盐三种形式存在,有关试验表明煤在加热并燃烧时,SO2的析出呈现明显的阶段性。
反应方程式为:S+O2=SO2③硫的固化反应,CaO与析出的SO2反应生成硫酸盐。
反应方程式为:CaO+SO2+1/2O2=CaSO42影响脱硫效率的因素:1)床温对脱硫的影响循化流化床锅炉中床温变化时会改变脱硫反应的速度、改变脱硫产物的结构分布及孔隙堵塞特性,从而影响脱硫效率。
当床温低于800℃时,石灰石孔隙数少,孔径小,反应速度低,而且SO2析出速度慢,所以脱硫效果差。
当床温高于1000℃时,CaO的高温烧结迅速增强,使反应比表面积迅速减小,导致脱硫效率降低。
循环流床锅炉床温应该选择在850℃--900℃比较合适。
2)CaS摩尔比对脱硫的影响投入炉膛石灰石的数量通常用Ca/S摩尔比表示,既Ca/S摩尔比是指石灰石的注入量与SO2吸收量的摩尔比。
在其他工况相同的情况下,随着Ca/S摩尔比的增加,脱硫效率增加,并且当Ca/S摩尔比小于2.5时,脱硫效率增加的很快,当继续增加Ca/S摩尔比时,脱硫效率将增加减慢。
循环流化床锅炉炉内脱硫效率影响因素分析

及元素硫 是可燃硫,占煤中 硫分的90%以上 ,硫酸
盐硫是不可燃硫,是煤中灰分的组成部分。
煤在燃烧 期间,所有的 可燃硫在受热过 程中都
从煤中释放出来。在氧化气氛中,又会被氧化而生成
SO:,有机硫在加热至400℃时即开始大量分解,煤
中有机硫和元 素硫在燃烧过程中基本上 都会氧化生
成SO:。黄铁矿硫在300℃时即开始失去硫份,形成 黄铁 矿和赤 铁矿 。黄铁 矿硫的 大量 分解是 在650 ℃
验、分析和总结。以期从技术、运行参数控制等多方 面寻求解决问题的对策,提高该锅炉脱硫效率,降低 脱硫成本。 2锅炉炉型选择
炉型选择 原则:锅炉要具 有较高的热效 率和炉 内脱硫效率,其中实现低成本脱硫是关键,因此,对 炉型选择 进行了认真比对和 论证,最终选择 了型号 为SHFx35一1.27/270一P的低循环倍率锅炉,锅炉的 相关技术参数如下:
冶 金动 力
2012年第2期
38
METALLURGI cAL蹦牦R
总第150 期
循环流化床锅炉炉内脱硫效率影响因素分析
邓先录
( 街阳华菱钢管有限公司能源分厂,湖南衡阳42l ∞1)
【摘 要】 介绍 了煤 在循 环流化 床锅 炉燃 烧过 程中 s 0: 生成机 理和 脱硫 机理 ,分 析了脱 硫效 率的 影响 因素 ,
hl s i de Ci r cI I l at i ng Fl ui di zed Bed Boi l er
DENG Xi an—l u
陬研s D叭el 肋w^砌峨胁,彤啊日l ‘af 沁瓤eZ me co.,玩,胁呦伽品日E∞l 铊j D虬c^讯矽
【A搬r act 】The f oma t i on t l l eor y of s 02 dur i ng coal coI Il bus t i on i n ci r cul at i ng nui di zed
循环流化床脱硫效率影响因素浅谈.

循环流化床脱硫效率影响因素浅谈1、引言我国已经成为世界三大酸雨区之一,且我国的酸雨主要为硫酸型的。
分析其主要原因是煤的不洁净燃烧所造成。
控制和减少火电厂SO2的排放对于改善我国目前严峻的环境问题和实现电力行业的持续发展意义重大。
我国目前火电厂燃煤中,优质低硫煤少,而高硫煤所占比重较大。
所以,必须对电厂燃煤烟气中的SO2排放严格控制。
烟气脱硫就显得尤为重要,烟气脱硫常用的方法有干法、半干法、湿法等。
循环流化床烟气脱硫属于半干法脱硫,以消石灰(Ca(OH)2)为脱硫剂。
山西长治漳山发电公司2×300MW机组采用此法,效果良好。
2、循环流化床烟气脱硫系统的基本流程及脱硫原理漳山发电公司循环流化床脱硫与电除尘器相结合,其基本工艺流程如图2-1所示。
烟气先进入预除尘器,预除尘器的作用是除去烟气中的大颗粒粉煤灰,收尘效率设计为85%左右。
经预除尘的烟气进入脱硫塔,在位置2处喷入脱硫剂即消石灰,在位置1处进行喷水降温、增湿。
烟气中的硫氧化物在脱硫塔内上升过程中与消石灰反应生成CaSO3和CaSO4,从而达到脱硫的目的。
漳山发电公司的后除尘器共有四级即四个电场,其中一二电场共用一个灰斗,三电场和四电场各有一个灰斗。
由于喷入脱硫塔的消石灰不可能完全反应。
所以,一二电场将粉煤灰与消石灰的混合物回收参与再循环,通过回料斜槽的气动调阀控制回灰量的大小,三电场在一二电场灰量不足时也会参与循环以维持脱硫塔内的差压。
四电场回收的灰中消石灰很少且活性低,所以将灰全部输走。
后除尘器的收尘效率设计为99.9%,后除尘器出来的烟气经过烟囱排入大气。
半干法脱硫的基本原理是SO2和SO3与Ca(OH)2的化学反应,即:Ca(OH)2 + SO2 → CaSO3+ H2O (2-1)Ca(OH)2 + SO3 → CaSO4 + H2O (2-2)其中,烟气中的硫氧化物以SO2为主,所以反应以2-1为主。
3、脱硫效率影响因素如何让喷入的消石灰更加充分的与烟气中的硫氧化物反应,怎么样提高脱硫效率?这是我们要考虑的主要问题。
提高循环流化床锅炉炉内脱硫效率分析
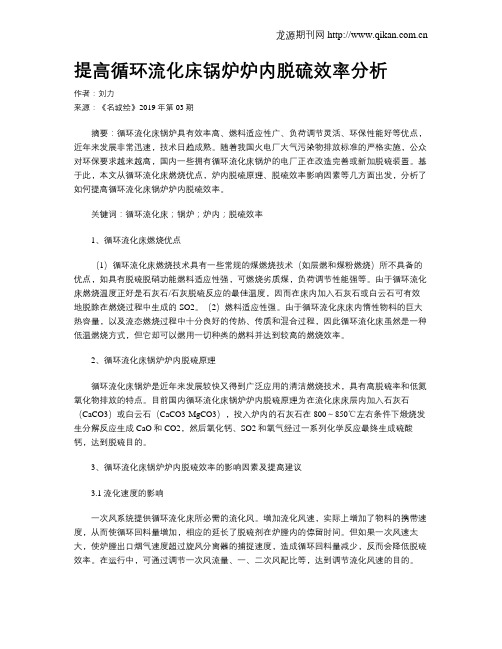
提高循环流化床锅炉炉内脱硫效率分析作者:刘力来源:《名城绘》2019年第03期摘要:循环流化床锅炉具有效率高、燃料适应性广、负荷调节灵活、环保性能好等优点,近年来发展非常迅速,技术日趋成熟。
随着我国火电厂大气污染物排放标准的严格实施,公众对环保要求越来越高,国内一些拥有循环流化床锅炉的电厂正在改造完善或新加脱硫装置。
基于此,本文从循环流化床燃烧优点,炉内脱硫原理、脱硫效率影响因素等几方面出发,分析了如何提高循环流化床锅炉炉内脱硫效率。
关键词:循环流化床;锅炉;炉内;脱硫效率1、循环流化床燃烧优点(1)循环流化床燃烧技术具有一些常规的煤燃烧技术(如层燃和煤粉燃烧)所不具备的优点,如具有脱硫脱硝功能燃料适应性强,可燃烧劣质煤,负荷调节性能强等。
由于循环流化床燃烧温度正好是石灰石/石灰脱硫反应的最佳温度,因而在床内加入石灰石或白云石可有效地脱除在燃烧过程中生成的SO2。
(2)燃料适应性强。
由于循环流化床床内惰性物料的巨大热容量,以及流态燃烧过程中十分良好的传热、传质和混合过程,因此循环流化床虽然是一种低温燃烧方式,但它却可以燃用一切种类的燃料并达到较高的燃烧效率。
2、循环流化床锅炉炉内脱硫原理循环流化床锅炉是近年来发展较快又得到广泛应用的清洁燃烧技术,具有高脱硫率和低氮氧化物排放的特点。
目前国内循环流化床锅炉炉内脱硫原理为在流化床床层内加入石灰石(CaCO3)或白云石(CaCO3·MgCO3),投入炉内的石灰石在800~850℃左右条件下煅烧发生分解反应生成CaO和CO2,然后氧化钙、SO2和氧气经过一系列化学反应最终生成硫酸钙,达到脱硫目的。
3、循环流化床锅炉炉内脱硫效率的影响因素及提高建议3.1流化速度的影响一次风系统提供循环流化床所必需的流化风。
增加流化风速,实际上增加了物料的携带速度,从而使循环回料量增加,相应的延长了脱硫剂在炉膛内的停留时间。
但如果一次风速太大,使炉膛出口烟气速度超过旋风分离器的捕捉速度,造成循环回料量减少,反而会降低脱硫效率。
影响循环流化床锅炉炉内脱硫效率的因素及控制

影响循环流化床锅炉炉内脱硫效率的因素及控制循环流化床锅炉因其具有高效、低污染和清洁燃烧等特点,在国内外得到迅速推广。
文章简述了循环流化床锅炉的脱硫原理;结合在我公司蒸汽锅炉运行实践,从Ca/S摩尔比、床温、脱硫剂粒度、循环倍率等方面分析了影響该循环流化床炉脱硫效率的主要因素及其控制方法。
标签:循环流化床锅炉;脱硫;效率前言循环流化床锅炉由于其具有燃料适应性广、燃烧效率高、污染物排放低、炉膛单位截面积热负荷高、负荷调节范围大、调节速度快等特点,目前已在全世界范围内被广泛的应用,且具有炉内脱硫脱硝功能,以低成本实现低污染排放。
循环流化床锅炉燃烧温度是适合以石灰石作为脱硫剂的脱硫反应的最佳温度区段。
在燃烧时向炉内加入适量的石灰石。
能得到90%-97%以上的脱硫率;同时,较低的燃烧温度以及燃烧空气分级送人炉膛,能有效地控制NOX排放。
本文根据山西潞安煤基合成油有限公司CIRCOFLUID型150t/h循环流化床锅炉炉内脱硫运行实际情况,对影响循环流化床锅炉炉内脱硫效率的因素进行了分析。
1 循环流化床锅炉燃烧机理循环流化床锅炉炉内流化风速较高(一般为4~8m/s),在炉膛出口加装了气固物料分离器。
循环流化床锅炉燃烧所需的一次风和二次风分别从炉膛的底部和侧墙送入,燃料的燃烧主要在炉膛中完成,炉膛四周布置有水冷壁用于吸收燃烧所产生的部分热量。
由气流带出炉膛的固体物料在气固分离装置中被收集并通过返料装置送回炉膛。
床上大的颗粒被一次风吹起来,处在悬浮状态,这部分具有流体的性质,小的颗粒被吹走,气流带出炉膛的固体物料在气固分离装置中被收集并通过返料装置送回炉膛,这部分成了循环燃烧。
2 循环流化床锅炉的脱硫机理循环流化床锅炉的脱硫采用炉内燃烧室添加石灰的方式实现,其机理和操作过程都相对简单,适用于低硫煤燃烧过程中的脱硫。
循环流化床锅炉炉内脱硫最常使用的脱硫剂是石灰石粉,循环流化床锅炉工作温度为830-900℃,在此温度下石灰石颗粒受热发生化学变化分解为氧化钙,氧化钙与炉膛内煤中馏分燃烧产生的二氧化硫进行盐化反应生成硫酸钙,最终硫酸钙以固体形式与炉渣一起排出实现锅炉烟气脱硫的目的。
浅析影响循环流化床锅炉脱硫效率的因素

浅析影响循环流化床锅炉脱硫效率的因素摘要:因为循环流化床锅炉燃烧过程之中炉内自脱硫能力的充分发挥,其对脱硫作用具有一定的贡献,基于此,本文论述了循环流化床锅炉脱硫效率的因素分析。
关键词:循环流化床锅炉;脱硫效率;因素引言我国经济发展正处于投资推动和高效增长的阶段,其中重工业的高耗能产业增长速度很快,对能源的需求量逐渐增加,也存在很大压力。
重工业对环境的污染很大,特别是高耗能的经济增长方式产生严重污染,因此做好节能减排脱硫具有深远的意义。
国家把节能减排作为重点,推动锅炉节能减排脱硫工作的实施是我国经济发展的长远战略,大力推进燃煤锅炉的技术改造,对技术指标落后、能耗较高污染较重的生产线进行改造,是企业乃至整个国家实现可持续发展的重要一环。
循环流化床在锅炉中的应用具有很大的优势,可以减少环境污染,达到国家环保的要求,是企业可持续发展的必由之路。
1.国内烟气脱硫现状以我国目前的经济条件和技术条件,还不允许像发达国家那样投入大量的人力和财力进行技术研发。
而且我国对SO2的治理方面起步较晚,国内一些电力的烟气脱硫装置大部分引进欧洲、美国、日本的技术。
有些技术还处于实验阶段,设备处理烟气量小,技术尚不成熟。
由于近几年国家严格的环保要求,脱硫工程是所有新建电厂必须建设脱硫工程,因此我国开始逐步在国外的技术的基础上研制适合我国的脱硫技术,不断加快对国外先进技术的消化吸收,使其国产化、低成本化。
2.循环流化床锅炉脱硫技术的介绍循环流化床锅炉脱硫技术是利用石灰石干法来实现炉内脱硫技术,也就是将炉膛内的碳酸钙经过高温煅烧后分解成为氧化钙,再同烟气里的二氧化硫产生反应出硫酸钙,之后再随炉渣排出炉体,进而达到脱硫的目的。
2.循环流化床锅炉脱硫技术特点,循环流化床锅炉脱硫技术一般是采用炉内喷钙干法进行脱硫,这是国内外常用脱硫方法中比较成功的应用,一般是针对一些小型锅炉和炉龄较长的锅炉的,这种脱硫技术具有工艺简单、脱硫效果很明显、占地面积也不大,而且整体投资较低、实施起来很方便等优点。
循环流化床锅炉炉内脱硫系统存在问题及优化脱硫方案解析

循环流化床锅炉炉内脱硫系统存在问题及优化脱硫方案循环流化床锅炉具有效率高、燃料适应性广、负荷调节灵活、环保性能好等优点,近年来发展非常迅速,技术日趋成熟。
随着我国对环保要求越来越高,环保电价政策的出台,国内一些拥有循环流化床锅炉的电厂正在抓紧改造或新加脱硫装置。
近几年,一些采用循环流化床锅炉的电厂还是被环保部门坚决要求进行锅炉尾部烟气脱硫,主要原因就是CFB锅炉炉内脱硫的效率令人怀疑。
传统的粗糟的炉内脱硫系统设计及设备制造使脱硫效率低下,同时脱硫固化剂'>脱硫固化剂的消耗量却非常可观,即使采用廉价的石灰石脱硫也使发电成本显著增加。
加之出现了锅炉灰渣的综合利用受到脱硫固化剂'>脱硫固化剂品种的影响,有的电厂只能将灰渣当做废品的废品抛弃掉。
更可靠、更实用、更经济的CFB锅炉炉内脱硫系统优化设计方案的重点是强化系统防堵设计、合理布置炉膛接口、选择合适脱硫固化剂'>脱硫固化剂,能够保证循环流化床锅炉烟气脱硫效率90%以上,烟气能够达标排放,灰渣能够综合利用。
下文中按习惯称呼的石灰石(粉)实际上泛制指脱硫固化剂'>脱硫固化剂(粉)。
1 循环流化床锅炉炉内烟气脱硫特点循环流化床(CFB)锅炉炉内稳定的870℃左右的温度场使其本身具有了炉内烟气脱硫条件,炉外的脱硫装置实际上就是石灰石的制粉、存储及输送系统,并科学经济实用地选择脱硫固化剂'>脱硫固化剂。
一般电厂大多是外购满足要求的石灰石粉,由密封罐车运至电厂内,通过设置于密封罐车上的气力卸料系统将石灰石粉卸至石灰石粉储仓。
在石灰石粉储仓底部,安装有气力输送系统,将石灰石粉通过管道输送至炉膛进行SO2吸收反应。
循环流化床脱硫的石灰石最佳颗粒度一般为0.2~1.5mm,平均粒径一般控制在0.1~0.5mm范围。
石灰石粒度大时其反应表面小,使钙的利用率降低;石灰石粒径过细,则因现在常用的旋风分离器只能分离出大于0.075mm的颗粒,小于0.075mm的颗粒不能再返回炉膛而降低了利用率(还会影响到灰的综合利用)。
循环流化床锅炉影响炉内脱硫率的主要因素和脱硫率与排放浓度及排放量

青岛建筑工程学院解鲁生摘要本文阐述循环流化床锅炉影响炉内脱硫率的主要因素和脱硫率与排放浓度及排放量的关系。
从工业或实验室测试实例的数据说明当Ca/S=1.5~2时,炉内脱硫率达80%以上比较困难。
并提出如何提高脱硫率的意见。
关键词循环流化床锅炉钙硫比脱硫率循环流化床锅炉,必须在煤中加入固硫剂同时燃烧,才会产生脱硫的作用,而不是循环流化床锅炉不加固硫剂,设备本身就有脱硫的作用。
常用固硫剂为石灰石粉,其脱硫率的大小与以下因素有关:(1)钙硫比(Ca/S)固硫剂所含钙与煤中含硫的摩尔比称为“钙硫比”。
所用煤质一定,煤中含硫量也是定值,Ca/S 越大就表示固硫剂使用的越多,它是表示固硫剂用量的一个指标。
当温度一定时,Ca/S越高,脱硫率也越高,从图1的曲线可以看出。
但是Ca/S越高, 石灰石粉的利用率越低,残留的CaO越多而不经济。
一般认为Ca/S为1.5或2时较为经济。
(2)燃烧温度从图1可看出, Ca/S一定时,温度与脱硫率的关系。
有的试验数据说明最佳温度为800~850℃,也有的试验则为850~900℃时最佳,温度过低,合成反应缓慢温度过高钙的硫酸盐产生热分解,一般循环流化床锅炉的燃烧温度在最佳脱硫范围内,这是它脱硫效率高的一个很主要的因素。
(3)固硫剂的颗粒度及其在炉内停留的时间石灰石粉颗粒越细,反应的比表面积越大,脱硫率会提高;这从图2的曲线可以看出;炉内气流速度越低,石灰石粉在炉内停留时间越长,反应越趋于完全,这二者可提高脱硫率,这很容易理解。
但是这两者有矛盾,颗粒越细小,在炉内停留的时间就越短,而且过细的颗粒被扬析出床的固硫剂越多,其利用率就降低。
一般认为采用石灰石粉,其颗度为0.1~0.3mm最佳。
通常循环流化床加入炉内石灰石粉过粗的现象较为普遍。
有的锅炉房只将石灰石破碎就加入,其脱硫效果必然较差。
(4)原煤含硫量的影响一定的Ca/S下,原煤的含硫量越高,实际固硫剂的用量越大,脱硫率也越高,如图3所示。
分析影响循环流化床烟气脱硫效率的床结构因素
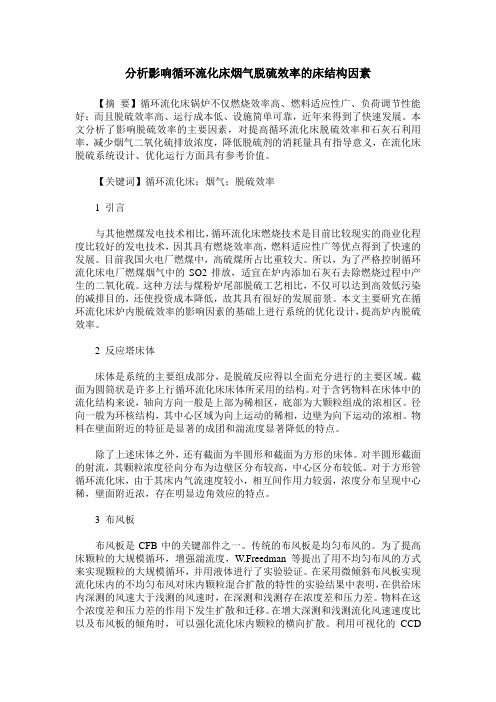
分析影响循环流化床烟气脱硫效率的床结构因素【摘要】循环流化床锅炉不仅燃烧效率高、燃料适应性广、负荷调节性能好;而且脱硫效率高、运行成本低、设施简单可靠,近年来得到了快速发展。
本文分析了影响脱硫效率的主要因素,对提高循环流化床脱硫效率和石灰石利用率,减少烟气二氧化硫排放浓度,降低脱硫剂的消耗量具有指导意义,在流化床脱硫系统设计、优化运行方面具有参考价值。
【关键词】循环流化床;烟气;脱硫效率1 引言与其他燃煤发电技术相比,循环流化床燃烧技术是目前比较现实的商业化程度比较好的发电技术,因其具有燃烧效率高,燃料适应性广等优点得到了快速的发展。
目前我国火电厂燃煤中,高硫煤所占比重较大。
所以,为了严格控制循环流化床电厂燃煤烟气中的SO2排放,适宜在炉内添加石灰石去除燃烧过程中产生的二氧化硫。
这种方法与煤粉炉尾部脱硫工艺相比,不仅可以达到高效低污染的减排目的,还使投资成本降低,故其具有很好的发展前景。
本文主要研究在循环流化床炉内脱硫效率的影响因素的基础上进行系统的优化设计,提高炉内脱硫效率。
2 反应塔床体床体是系统的主要组成部分,是脱硫反应得以全面充分进行的主要区域。
截面为圆筒状是许多上行循环流化床床体所采用的结构。
对于含钙物料在床体中的流化结构来说,轴向方向一般是上部为稀相区,底部为大颗粒组成的浓相区。
径向一般为环核结构,其中心区域为向上运动的稀相,边壁为向下运动的浓相。
物料在壁面附近的特征是显著的成团和湍流度显著降低的特点。
除了上述床体之外,还有截面为半圆形和截面为方形的床体。
对半圆形截面的射流,其颗粒浓度径向分布为边壁区分布较高,中心区分布较低。
对于方形管循环流化床,由于其床内气流速度较小,相互间作用力较弱,浓度分布呈现中心稀,壁面附近浓,存在明显边角效应的特点。
3 布风板布风板是CFB中的关键部件之一。
传统的布风板是均匀布风的。
为了提高床颗粒的大规模循环,增强湍流度,W.Freedman等提出了用不均匀布风的方式来实现颗粒的大规模循环,并用液体进行了实验验证。
- 1、下载文档前请自行甄别文档内容的完整性,平台不提供额外的编辑、内容补充、找答案等附加服务。
- 2、"仅部分预览"的文档,不可在线预览部分如存在完整性等问题,可反馈申请退款(可完整预览的文档不适用该条件!)。
- 3、如文档侵犯您的权益,请联系客服反馈,我们会尽快为您处理(人工客服工作时间:9:00-18:30)。
循环流化床脱硫过程及其影响因素分析
作者:胡晓波金伟王广廷
来源:《科技资讯》2013年第11期
摘要:本文对循环流化床脱硫过程进行了分析,得出影响循环流化床脱硫反应的影响因素有床层温度、脱硫剂粒度和反应活性、颗粒物浓度、钙硫摩尔比四个方面,并提出了解决问题的几点建议。
关键词:循环流化床脱硫影响因素
中图分类号:X521 文献标识码:A 文章编号:1672-3791(2013)04(b)-0111-01
烟气循环流化床脱硫(CFB-FGD)工艺是20世纪80年代德国鲁奇(Lurgi)公司开发的一种新型半干法脱硫工艺。
目前烟气循环流化床脱硫工艺已经达到工业应用水平的主要有以下几种工艺流程:德国Lurgi公司开发的典型烟气循环流化床脱硫工艺(CFB);德国Wulff公司开发的烟气回流式循环流化床脱硫工艺(RCFB);丹麦L.F.Smith公司开发的气体悬浮吸收烟气脱硫工艺(GSA)等。
3 影响脱硫的主要因素
影响循环流化床脱硫效率的主要因素有床层温度、颗粒物浓度、钙硫比、脱硫剂粒度和反应活性。
(1)床层温度对脱硫效率的影响。
一般来说温度升高有助于提高化学反应速度。
但是经过实验研究发现:在循环流化床烟气脱硫工艺中,绝热饱和温差决定了脱硫效率。
指脱硫塔出口烟气温度与相同状态下的烟气绝热饱和温度之差。
由图1可见,烟气温度越低(也就是越小),脱硫效率越高,这正与我们的直觉相反。
这是由于在很大程度上决定了浆液滴的蒸发干燥特性和脱硫反应特性。
一方面,降低时,使浆滴液相蒸发趋于缓慢。
与脱硫剂的反应时间增大,使得二者的化学反应过程更充分。
另一方面,过低又会引起烟气结露,对反应塔的腐蚀增强,从而增加设备的初始投资成本和运行维护费用。
(2)脱硫剂粒度和反应活性。
循环流化床脱硫中,脱硫剂可以是消石灰也可以是生石灰粉。
一般说来,使用消石灰,多喷入浆液。
使用生石灰,多数喷入干粉。
对于生石灰粉,比表面积和反应活性直接影响到装置
的脱硫效率和钙硫比。
通常要求,含量大于80%,粒度小于2毫米;活性指标比较严格,要求达到小于4 min。
(3)颗粒物浓度。
在反应塔中飞灰、粉尘和脱硫剂在高浓度下接触反应是流化床具有较高脱硫效率的重要原因。
通常浓度可达0.5~2.0kg/m3,是一般反应塔的50~100倍。
这主要由于塔内强烈的湍流
状态和较高的颗粒循环倍率增加了接触面积,颗粒之间的碰撞使得反应产物亚硫酸钙不断磨损脱落,避免了脱硫剂表面被堵塞,从而不会影响物质的传质过程和脱硫剂活性的下降。
(4)钙硫摩尔比。
对脱硫效率的影响被许多研究者验证,由图2可见,脱硫效率随着的增加而增加。
但当增加到一定值时,脱硫效率的增加趋于平缓。
也就是当钙硫比达到一定值后,脱硫剂使用效率下降。
在实际运行中,由于固体颗粒物的多次循环,脱硫塔内实际的远大于进料时的,从而使脱硫装置在较低的进料条件下,维持较高的脱硫效率。
参考文献
[1] 米浩林,马国骏.回流式烟气循环流化床脱硫技术[J].热力发电,1998,(2):57-61.
[2] 张凤兰,程岩.小龙潭发电厂烟气循环流化床脱硫工程评述[J].电力环境保护,2003,19.
[3] 董勇,马春元,徐夕仁.双循环流化床烟气悬浮脱硫工艺[J].电站系统工程,2002,18(6).。