切削速度与雕刻材料
论述激光雕刻材料及其雕刻技术

论述激光雕刻材料及其雕刻技术影响激光雕刻的4个最根本的要素是:雕刻速度、激光功率、雕刻精度、材料。
在特定材料上如要达到一定的雕刻效果,就要求吸收一定能量的激光,这一能量应看作是材料吸收的激光能量=激光功率/雕刻速度。
简单地讲就是要提高材料吸收的激光能量,就应提高激光功率或是降低雕刻速度,至于说最后采用哪种方法就要看材料和最终的雕刻效果。
一般来讲用户都会避免高低速度,因为那会降低生产效率。
其实影响雕刻效率的不仅是雕刻速度,雕刻精度也对其有非常大影响。
从我们的实践经验来看使用500dpi同600dpi精度雕刻出的物品从内眼看夫太大差别,可所费时间大约有20~30%的出入。
一般情况下用户会使用500dpi来完成大多数的工作,只有在切割或是需要高密度能量的时候才会采用600dpi或更高的设置,因此对最终的雕刻效果起决定影响的恐怕还是雕刻材料。
新用户一般对材料的特性都不十分了解,对不同材料的雕刻表现形式也无深刻的认识,势必会对客户造成一定的损失。
下面就一些常用的雕刻材料及其雕刻的表现方法作一个介绍,代参考:一、灰度的表现普通的机械雕刻不能以经济的方式雕刻粗细不一的点,因而不具有灰度的表现形式。
激光雕刻是以打点方式实现雕刻,具有在灰度表现方面的天然优势。
为此在雕刻设计时可尽量采用灰度表现形式,这样的好处是一方面减少了着色工艺,节约了费用;另一方面丰富了雕刻的再现手段,增加了图形的层次。
用户在使用时,先将图形内做不同的灰度填充(文字要先转化成图形),雕刻输出选择黑白模式,可试一下不同网点的效果,精度一般不超过500dpi。
二、雕刻材料1、木材A、原木(未加工的木材)木头是迄今止最常用的激光加工材料,很容易雕刻和切割。
浅色的木材象桦木、樱桃木或者枫木能很好地被激光气化,因而比较合适雕刻。
每种木材都有处身的特点,有的致密一些,如硬木,在雕刻或切割时就要用更大的激光功率。
我们建议雕刻不太熟悉的木材前,要首先研究其雕刻特性。
高速切削刀具材料
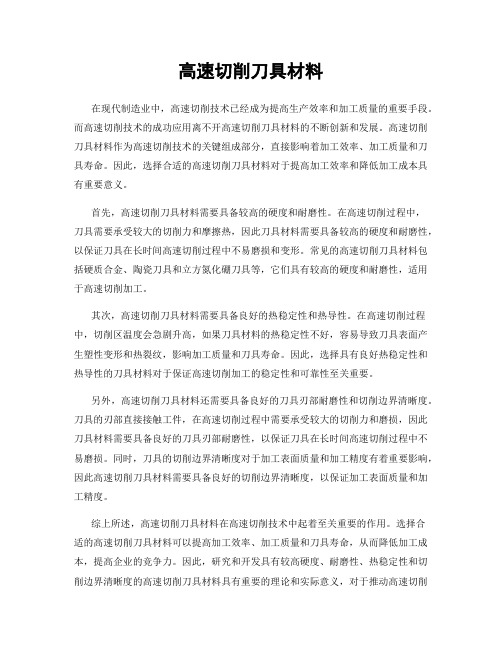
高速切削刀具材料在现代制造业中,高速切削技术已经成为提高生产效率和加工质量的重要手段。
而高速切削技术的成功应用离不开高速切削刀具材料的不断创新和发展。
高速切削刀具材料作为高速切削技术的关键组成部分,直接影响着加工效率、加工质量和刀具寿命。
因此,选择合适的高速切削刀具材料对于提高加工效率和降低加工成本具有重要意义。
首先,高速切削刀具材料需要具备较高的硬度和耐磨性。
在高速切削过程中,刀具需要承受较大的切削力和摩擦热,因此刀具材料需要具备较高的硬度和耐磨性,以保证刀具在长时间高速切削过程中不易磨损和变形。
常见的高速切削刀具材料包括硬质合金、陶瓷刀具和立方氮化硼刀具等,它们具有较高的硬度和耐磨性,适用于高速切削加工。
其次,高速切削刀具材料需要具备良好的热稳定性和热导性。
在高速切削过程中,切削区温度会急剧升高,如果刀具材料的热稳定性不好,容易导致刀具表面产生塑性变形和热裂纹,影响加工质量和刀具寿命。
因此,选择具有良好热稳定性和热导性的刀具材料对于保证高速切削加工的稳定性和可靠性至关重要。
另外,高速切削刀具材料还需要具备良好的刀具刃部耐磨性和切削边界清晰度。
刀具的刃部直接接触工件,在高速切削过程中需要承受较大的切削力和磨损,因此刀具材料需要具备良好的刀具刃部耐磨性,以保证刀具在长时间高速切削过程中不易磨损。
同时,刀具的切削边界清晰度对于加工表面质量和加工精度有着重要影响,因此高速切削刀具材料需要具备良好的切削边界清晰度,以保证加工表面质量和加工精度。
综上所述,高速切削刀具材料在高速切削技术中起着至关重要的作用。
选择合适的高速切削刀具材料可以提高加工效率、加工质量和刀具寿命,从而降低加工成本,提高企业的竞争力。
因此,研究和开发具有较高硬度、耐磨性、热稳定性和切削边界清晰度的高速切削刀具材料具有重要的理论和实际意义,对于推动高速切削技术的发展和应用具有重要意义。
希望在未来的研究和实践中,能够不断创新和发展高速切削刀具材料,为推动高速切削技术的发展和应用做出更大的贡献。
vc切削速度公式

vc切削速度公式VC切削速度公式是机械加工中常用的一个重要公式,它表达了切削速度与刀具直径、旋转速度之间的关系。
这个公式在金属切削、雕刻、雕铣、切割等领域都非常有用。
那么,让我们来详细了解一下VC切削速度公式吧。
首先,VC公式中的V代表切削速度,一般用m/min来表示。
C代表理论周长,单位为mm,通常是指刀具周长。
我们可以将公式表示为:Vc=π×C×n/1000其中,n表示刀具转速,单位为r/min。
这个公式的意义在于,在机械加工中,可以通过合理地计算刀具的切削速率来提高生产效率,减少加工时间和成本,并且可以降低刀具磨损和制造废品的风险。
这对生产效率和经济效益都非常重要。
对于不同的材料和加工方式,VC公式中的参数也会有所不同。
例如,对于铸铁,由于其具有较低的切削性和硬性,VC值通常较低;而对于钢材,VC值较高。
同样的,刀具的直径和转速也会因材质和加工要求而异。
除此之外,在使用VC公式时,还需要注意以下几点:1. 刀具要做好切削前的准备。
要保证刀具的清洁和正确安装,避免出现偏差或其他不必要的问题。
2. 要进行准确的切削速度计算。
不要盲目地提高切削速度,否则会导致刀具的损坏或不稳定的加工质量。
3. 要定期检查刀具的切削性能。
这些包括切削力、切削温度、切削深度和刀具磨损等指标。
总之,VC切削速度公式是机械加工中不可或缺的公式之一。
通过合理使用这个公式,我们可以提高生产效率和经济效益,实现机械加工的高品质和高效率。
对于从事机械加工的工人和工程师来说,这个公式是必须要掌握并善加利用的。
刀具高速切削加工技术特点

刀具高速切削加工技术特点
高速切削加工技术中的“高速”是一个相对概念,对于不同的加工方法和工件材料与刀具材料,高速切削加工时应用的切削速度并不相同。
通常把切削速度比常规高出5~10倍甚至以上的切削加工叫作高速切削或超高速切削。
以德国达姆施塔特工业大学H.Schulz教授提出的铣削速度范围比较具有代表性:铝合金1000~7000m/min,铸铁800~3000m/min,钢500~2000m/min,钛合金100~1000m/min,镍基合金50~500m/min。
传统硬质合金类刀具加工铝合金壳体切削速度一般在150~300m/min之间,而聚晶石(PCD)类刀具的切削速度能达到2000m/min以上,实现高速切削。
高速切削加工时,高切削速度在材料剪切区短时释放大量热能。
因此,随着切削速度的增加,切削的剪切区、切屑压缩区和变形区内材料的单位切削力反而下降。
总切削力和必需的切削功率同样下降。
高速切削工艺典型的小切削深度结合高进给速度和高主轴转速,将降低切削刃切入工件的时间,或称接触时间。
刀具监控系统在高速切削加工过程中还应该考虑的一个问题是刀柄与机床主轴锥孔的连接方式,常用的锥柄有BT、HSK、CAT及CAPITO等多种形式,但是在高速切削时HSK因其的双面接触过定位结构可以保证刀尖很高的跳动要求,,特别适合高转速工况。
第 1 页共 1 页。
CNC车床的各种刀具与加工材质的给进率与转速相关资料

CNC車床的各種刀具與加工材質的給進率與轉速相關資料V=πDN/1000V:切削速度(m/mm) D:工件直徑(mm) N:每分鐘回轉速(rpm)V=πDN/1000V:切削速度(m/mm) D:工件直徑(mm) N:每分鐘回轉速(rpm)(1) 旋徑:又稱擺度。
表示工件在床面的最大旋轉直徑。
(2) 切削速度︰車刀切削迴轉工件時,每一分鐘內所切出的切屑長度。
以每分鐘公尺長度或英呎長度表示。
V=πDN/1000V:切削速度(m/mm) D:工件直徑(mm) N:每分鐘回轉速(rpm)(3) 進給︰又稱進刀量或走刀量,指刀具沿工件表面或進入工件表面的前進率。
以主軸每轉的距離來表示。
(4) 切削深度︰刀具在工件上所切除的切屑厚度。
個刀角之作用A.後斜角(1)控制屑流方向及減少排屑阻力(2)複後斜角可保護刀具光點B.邊斜角(1)控制屑流方向及減少排屑阻力(2)刀具材料之強度愈大則邊斜角愈大C.前間隙角(1)工具材料抗剪及衝擊強度愈大前間隙角可愈大反之則愈小(2)工件材料愈硬愈強愈韌則前間隙角愈小反之則愈大D.邊間隙角(1)刀具作側向進刀時能補償因工件每轉一周刀架鞍座前進所產生的螺旋角之用並使切削作用集中於切削邊E.刀端角(1)減低顫震及增進刀口之使用壽命可避免車刀前端與表面摩擦高速鋼車刀角度表高速鋼車刀角度表邊隙角前隙角後斜角邊斜角低碳鋼12816.514中碳鋼10-1288-16.512-14高碳鋼108812鎳合金鋼1081012高速鋼108812不銹鋼1081015-20鑄鐵108512鋁1283515電木12800黃銅10800-(-4)青銅10800-(-4)鎳銅合金1513814鎳1513814橡皮20150-(-5)0-(-7)工具鋼108812碳化車刀角度表前隙角邊隙角後斜角邊斜角鋁6-86-810-2010-20銅6-86-8420黃銅6-86-804青銅6-86-80-43-8鑄鐵6-86-80-42-4前隙角邊隙角後斜角邊斜角低碳鋼(SAE1020-1035)6-86-803高碳鋼(SAE1095)6-86-803鎳合金鋼(SAE2315-2335)6-86-803鎳鉻合金鋼(SAE3140-3250)6-86-803鉬合金鋼(SAE4015)6-86-803鉻釩合金鋼(SAE6145)6-86-803--------------------------------------------------------------------------類別/ 組成元素/ 識別/ 切削材料K/ wc-Co/紅/鑄鐵.石材.非鐵金屬(脆性材)P/ wc-Co-Tic/ 藍/鋼.鑄鋼(延性材料)M/ wc-Co-Tic-Tac/ 黃/ 不鏽鋼(強軔材)1.每類又有多種編號(如P01-P40 K01-K40......)2.號數大者適合低速重切削,號數小適合高速輕切削3.碳化物刀具磨削時,不可以急冷於水中,以免產生裂痕4.刀具通常以粉末冶金製成5.在高溫切削時不失硬度(此硬度稱紅熱硬度)耐熱度達1200度c 刀具壽命的單位是什麼?要如何計算?有哪些邊界條件會影響刀具壽命?一般我們是以加工刀多少小時為單位,而使用條件確實會對刀具壽命有很大影響,主要包括加工深度、每刃進给量、加工材質、切削液使用狀況(散熱與排屑)。
激光切割雕刻设备的工艺参数

激光切割雕刻设备的工艺参数1 激光切割雕刻工艺介绍激光切割雕刻是一种先进的技术,可以利用激光精确准确的切割和雕刻材料,用于制作各种复杂的形状的零件。
在激光切割雕刻中,激光束受到电气控制作为切割和雕刻工具,激光可以准确的实现精密的规定的尺寸,特别是一些复杂的表面的零件。
激光切割雕刻的原理是:利用激光束的高热量照射数据材料,在误差范围内快速精准的加工加工图形。
因此,在工艺参数设定方面,很重要。
2激光切割雕刻工艺参数激光切割雕刻工艺参数包括切割速度,聚焦方式,停止时间,激光功率,激光波长,激光电流,雾化喷嘴等等。
(1)切割速度:这是指激光切割雕刻机刀头在切割/雕刻表面的平均移动速度,它影响切割/雕刻速度和质量。
该参数受到激光能量,材料和夹具等参数的影响。
(2)聚焦方式:激光切割机在切割/雕刻过程中,可以选择空调方式或轨迹聚焦方式,这也是影响切割/雕刻质量的一个重要参数。
(3)停止时间:激光切割雕刻机在加工完表面后停止的时间,这是非常重要的参数,影响着激光切割/雕刻的质量。
(4)激光功率:激光切割/雕刻工艺参数中,激光功率是最重要的参数,它直接决定着激光切割/雕刻的质量。
(5)激光波长:激光波长是决定激光切割/雕刻材料类型的参数,以选择合适的激光波长切割/雕刻的效果最好。
(6)激光电流:此参数决定激光的发射能力,激光切割/雕刻机在加工材料前,必须调整激光电流参数。
(7)雾化喷嘴:激光切割雕刻工艺的雾化喷嘴也是影响切割/雕刻质量的重要参数之一,此参数决定材料蒸发程度。
3 工艺参数的调整激光切割雕刻工艺参数在调整方面,主要是根据实际需求,结合加工材料的类别,考虑激光束束能量,光束穿透力以及加工深度等诸多因素,综合调整上述的参数,以达到精确的激光加工效果。
4 结论激光切割雕刻是一种高效率的加工工艺,它在行业中拥有着广泛的应用。
其中,工艺参数是激光切割雕刻质量、效果和准确性最重要的因素之一,它在激光切割雕刻工艺中起着关键性作用。
机械制造中的激光切割与雕刻技术

机械制造中的激光切割与雕刻技术激光切割与雕刻技术是在机械制造领域中应用广泛的一种技术。
它以高能激光束作为工具,通过对材料进行照射和烧蚀来实现切割和雕刻的目的。
本文将介绍激光切割与雕刻技术在机械制造中的应用,并探讨其优点和挑战。
一、激光切割技术在机械制造中的应用激光切割技术在机械制造中具有广泛的应用,尤其适用于金属材料和非金属材料的切割。
激光切割的优势在于其精度高、速度快、无需刀具更换等特点。
1. 金属材料的切割对于金属材料的切割,激光切割技术可以实现高精度、高速度的切割过程。
激光束在照射金属表面时,会迅速将其加热至融点以上,进而形成熔池,最终通过气体喷射将熔化的金属排出,完成切割过程。
激光切割技术可以处理各种形状和尺寸的金属材料,广泛应用于汽车制造、航空航天等领域。
2. 非金属材料的切割与雕刻除了金属材料,激光切割技术在非金属材料的切割与雕刻方面也有着重要的应用。
对于一些脆性材料如玻璃、陶瓷等,传统的切割方法往往会导致破损和损耗,而激光切割技术可以实现无接触切割,减少了材料的破损情况。
同时,激光切割技术还可以进行精细的雕刻工艺,广泛应用于工艺品加工、电子零部件加工等领域。
二、激光切割与雕刻技术的优点激光切割与雕刻技术作为一种高精度、高效率的加工方法,在机械制造中具有许多优点。
1. 高精度激光切割与雕刻技术可以实现非常高的加工精度。
由于激光束的直径非常小,因此能够创造出非常细腻的切割和雕刻效果。
这在一些对加工精度要求较高的行业,如微电子、光电子等领域中得到广泛应用。
2. 高效率激光切割与雕刻技术具有高效率的特点,其加工速度快,能够快速完成大批量的工作。
与传统的机械切割方法相比,激光切割技术不需要物理接触,避免了刀具磨损和切割速度受限的问题,从而提高了生产效率。
3. 无接触加工激光切割与雕刻技术采用无接触加工方式,减少了对材料的损伤。
在一些对材料要求较高、易破损的领域,如医疗器械、玻璃加工等,激光切割技术可以更好地满足加工需求。
切削速度与雕刻材料

切削速度与每刃每转吃刀量一、切削速度刀具旋转时的线速度:V=πDN/1000(m/min)其中 D ——刀具直径( mm) N——(F1)刀具转速(rpm)表1 切削速度V 推荐参数表2 刀具切削速度一览表二、每刃每转吃刀量单刃吃刀量f a f a =F/n F—进给速度,n—转速,刀具每转过1刀刃与工件的相对位移(mm)表3 单刃吃刀量一览表(单刃)1常用雕刻材料切削性能一、材料加工特性概述雕刻行业常用的材料可以分为金属材料和非金属材料。
金属材料又可分为铸铁、碳钢、合金钢、有色金属及合金四类。
确决定材料的加工性能的重要因素是硬度,当然还与韧性、粘性有关。
总体来说,金属材料的硬度通常要大于非金属材料,刀具要有较大的切削力,考虑的多是刀具磨损、刀具强度、防止断刀等问题,而非金属材料多为软材料,对刀具的锋利程度要求较高,更多考虑如何保证排屑和侧边质量等问题。
以金属中最为常见的三种材料59号铜、紫铜、Cr12模具钢为例,59#铜这种材料强度低、脆性高、硬度低(164HB),且导热性好,具有良好的切削加工性。
在加工时,吃刀深度和走刀速度也可以加大。
紫铜,这种材料的特点是导电性能好,强度低、硬度最低(35HB),属于软材料,材料的粘性大,不易断削,在加工中,考虑到它的粘性,开槽深度和走刀速度要相应的降低。
Cr12模具钢,这种材料具有高强度、高硬度(未经热处理的材料硬度在200~250HB),相对59#铜较难切削,加工中,要采用较低的开槽深度和走刀速度。
二、常用雕刻材料性能比较下面比较5种常用雕刻材料的切削加工性能:表4 几种常用雕刻材料性能比较结论:在加工不同材料时要综合机床性能,选择参数合适的刀具,并设置相应的主轴转速和进给参数!2。
如何用刻刀进行木工雕刻的速度和灵敏度掌握

如何用刻刀进行木工雕刻的速度和灵敏度掌握在木工雕刻这门古老而精细的艺术中,使用刻刀是常见的工具之一。
它既可用于粗糙的切割,亦可用于细致的雕刻。
然而,要想掌握刻刀进行木工雕刻的速度和灵敏度,需要经验和技巧的积累。
在本文中,将介绍一些关于如何使用刻刀进行木工雕刻的方法和技巧,以帮助提高掌握速度和灵敏度。
首先,了解刻刀的类型和用途非常重要。
刻刀有许多不同的形状和大小,每个刀具都有其独特的用途。
在使用刻刀进行雕刻前,应该熟悉不同形状刀具的特点和适用范围。
例如,V型刻刀适用于雕刻细节和切割直线,而U型刻刀适用于凹槽和较大的凹陷部分。
选择正确的刻刀有助于提高工作效率和灵敏度。
其次,正确的握持刻刀也是关键。
握持刻刀时,要确保手柄牢固地握住手掌,并用食指和拇指控制刀刃。
这种握持方式可以提供更好的控制和操作性,并减少手部疲劳。
同时,要确保刀刃的方向与手部的运动方向一致,以免引起刀具失控和意外伤害。
除此之外,要学会控制刻刀的力度和角度。
对于速度和灵敏度的掌握,力度和角度的控制是至关重要的。
在进行精细雕刻时,刀刃应该轻轻地滑过木材表面,力度适中,以避免过度切割和木材的损坏。
对于粗糙部分的切割,可以适度增加力度,但也要小心不要过度用力。
此外,角度的控制对于不同的刻刀形状也很重要。
不同的角度可以产生不同的刻痕效果,通过实践和经验的积累,掌握角度的变化可以更好地控制刻刀的速度和灵敏度。
此外,练习和实践是提高刻刀速度和灵敏度的重要方法。
通过持续的练习和实践,可以逐渐熟悉刻刀的使用和操作。
开始时,建议先从简单的雕刻项目开始,逐渐增加难度和复杂度。
在练习过程中,要保持耐心和恒心,不断地尝试和改进技术。
与其他木工和雕刻艺术家的交流也是非常有益的,可以从他们的经验中学到更多技巧和窍门。
最后,在进行木工雕刻时,安全要放在首位。
刻刀是一种锋利的工具,使用不当可能会导致严重的伤害。
因此,在开始雕刻之前,务必佩戴安全手套和护目镜等个人防护装备。
常见材料的雕刻机床主轴转速设置

在加工正常的情况下,影响木工雕刻机刀具使用寿命最主要的参数是木工雕刻机主轴转速。
在同样的条件下,主轴转速越低,刀具使用寿命越长。
为了延长刀具的使用寿命,希望设置较低的主轴转速,但是主轴电动机的转速并不是可以无限制的降低,当主轴电动机的转速太低时,在同样的进给速度的条件下,切削力度变大,使刀具难以承受。
所以在加工某种材料时,主轴转速是有一个合理的转速范围的。
木工雕刻机加工各种材质加工速度与主轴转速配比表:具体情况具体分析,仅供一般材质的参考一、切割1、有机玻璃(压克力)厚度速度转速20mm 5-6 20000-2200015mm 6-7 19000-2100010mm 8-9 18000-200005mm 10-12 18000-200003mm 10-14 16000-180002、PVC(注:逆时针切割)厚度速度转速20mm 8-12 18000-2000015mm 10-14 16000-1800010mm 15-20 16000-180003、弗龙板(注:逆时针切割)厚度速度转速20mm 15-20 18000-1900015mm 20-25 16000-1800010mm 20-25 16000-180004、密度板(注:单刃刀切割)厚度速度转速18mm 6-8 18000-2000015mm 8-10 18000-2000010mm 10-14 17000-19000(注:以上全部是3.175铣刀参数)5、双色板厚度速度转速1.5mm 12-20 12000-14000二、雕刻1、双色板雕刻参数(1)、胸牌速度:18-24转速:12000-14000(2)、大的门牌速度:25-35转速:12000-140002、大角度刀雕刻三维字速度:15-18转速:16000-18000。
雕刻刀具的知识
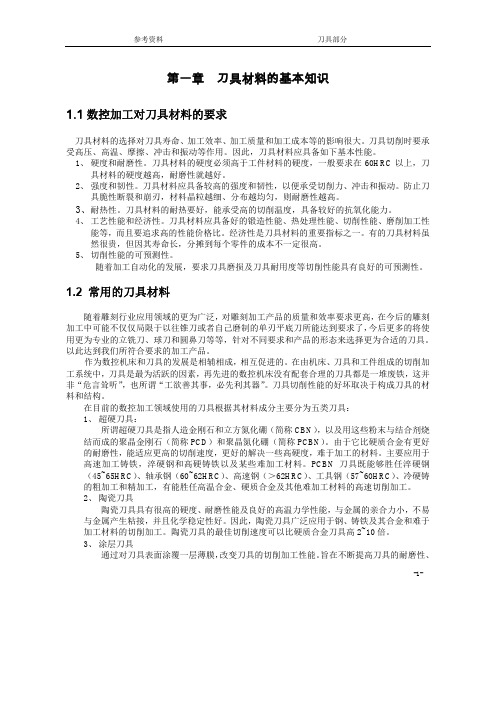
TIALN 是含有铝的 PVD 涂层,TIALN 化学性能稳定,抗氧化磨损能力强,加工高合金
钢、不锈钢、钛合金时,比 TIN 涂层刀具使用寿命提高 3~4 倍,在切削过程中,该涂层刀
具的涂层表面会生成一层很薄的非晶体三氧化二铝,形成一层硬度惰性保护膜,从而起到抗
氧化和抗扩散磨损的作用,可更为有效的实现高速切削加工,在高速切削时,TIALN 涂层
1.3 刀具材料的硬度
所谓硬度,通常可以理解为金属表面局部体积内抵抗外物压入而引起塑性变形的抗力。 下列是常见的高速钢材料与硬质合金材料性能对比:
-3-
参考资料
刀具部分
维洛 氏硬度 氏硬度
洛氏硬 度
抗弯 强度
密 相当 度 ISO 牌号
HV H 30 RA
HRC
N/m
g/c
m2
m3
185 93 相当于
少粘接和减轻摩擦。降低切削力和切削温度。
TIC 是一种高硬度的耐磨化合物,是最早出现的涂层材料,也是目前应用最为广的一种
涂层材料之一,有良好的的抗后刀面磨损和抗月牙洼磨损能力,同时它与基体附着牢固,在
制备多层涂层时常将 TIC 最为与基体接触的底层膜。
TIN 涂层是继 TIC 涂层以后非常广泛的一种涂层,是 TIC 的激烈竞争者。TIC 的硬度比
用的刀具材料是硬质合金和涂层两种,下面再针对这两类刀具进行材料的成分
的介绍。
z 涂层刀具
涂层刀具的种类可分为两大类:硬涂层刀具和软涂层刀具。硬涂层刀具最求的主要目标
是高的硬度和耐磨性,其主要的优点是硬度高、耐磨性好,典型的是 TIC、TIN 和 TIALN
涂层。软涂层刀具追求目标是低摩擦系数,它与材料的摩擦系数很低,只有 0.1 左右。可减
数控加工中的材料切削特性与加工参数选择

数控加工中的材料切削特性与加工参数选择随着现代制造技术的不断发展,数控加工已经成为工业生产中不可或缺的一部分。
在数控加工中,材料的切削特性和加工参数的选择是至关重要的。
本文将探讨数控加工中的材料切削特性以及如何选择合适的加工参数。
首先,我们需要了解不同材料的切削特性。
不同材料具有不同的硬度、韧性、热膨胀系数等特性,这些特性决定了材料的切削性能。
常见的材料包括金属、塑料、陶瓷等。
金属材料通常具有较高的硬度和韧性,因此在切削过程中需要选择适当的切削速度和进给量,以确保切削效果和刀具寿命。
塑料材料通常较软,切削时容易产生切削热,因此需要控制切削速度和进给量,防止过热导致材料变形或熔化。
陶瓷材料具有较高的硬度和脆性,切削时容易产生裂纹,因此需要选择适当的切削速度和刀具材料,以避免切削过程中的损坏。
其次,我们需要了解加工参数的选择对切削效果的影响。
加工参数包括切削速度、进给量、切削深度等。
切削速度是指切削工具在单位时间内切削的距离,是衡量切削效率的重要指标。
切削速度过高会导致切削温度升高,刀具磨损加剧,而切削速度过低则会降低加工效率。
进给量是指切削工具在单位时间内进给的距离,对切削效果和刀具寿命有着重要影响。
进给量过大会导致切削力增大,刀具振动,进而影响加工质量;进给量过小则会降低加工效率。
切削深度是指切削工具在一次切削中所切削的距离,对切削力和切削温度有着重要影响。
切削深度过大会导致切削力增大,刀具磨损加剧,而切削深度过小则会降低加工效率。
因此,在选择加工参数时需要综合考虑切削效果和加工效率,找到一个合适的平衡点。
最后,我们需要根据具体情况选择合适的刀具和刀具材料。
刀具的选择对切削效果和加工质量有着重要影响。
不同材料的切削特性要求使用不同类型的刀具。
例如,对于切削硬度较高的金属材料,通常使用硬质合金刀具,而对于切削脆性较高的陶瓷材料,通常使用多晶金刚石刀具。
此外,刀具材料的选择也是关键,不同刀具材料具有不同的硬度、耐磨性和耐热性。
适用高速与超高速切削的刀具材料

适用高速与超高速切削的刀具材料目前适用于高速切削的刀具主要有:涂层刀具、金属陶瓷刀具、陶瓷刀具、立方氯化硼(CBN)刀具及聚晶金刚石(PCD)刀具等。
1.涂层刀具涂层在刀具基体上涂复硬质耐磨金属化合物薄膜以达到提高刀具表面的硬度和耐磨性的目的。
常用的刀具基体材料主要有高速钢、硬质合金、金属陶瓷和陶瓷等。
涂层TiN,TiC,Al2O3,TiCN,TiAlN,TiAlCN等;涂层可以是单涂层,也可以是双涂层或多涂层,甚至是几种涂层材料复合而成的复合涂层。
复合涂层可以是TiC-Al2O3-TiN,TiCN和 TiAlN多元复合涂层,最新又发展了TiN/NbN,TiN/CN等多元复合薄膜。
如商品名为“Fire”的孔加工刀具复合涂层,是用TiN作底层,以保证与基体间的结合强度;由多层薄涂层构成的中间层为缓冲层,以用来吸收断续切削产生的振动;顶层是具有良好耐磨性和耐热性的TiAlN层。
还可在“Fire”外层上涂减磨涂层。
其中,TiAlN层在高速切削中性能优异,最高切削温度可达800℃。
近年开发出的一些PVD硬涂层材料,有CBN、氮化碳(CN)、Al2O3、氮化物(TiN/NbN,TiN/CN)等,在高温下具有良好的热稳定性,很适合高速与超高速切削。
金刚石膜涂层刀具主要用于有色金属加工。
C-C3N4超硬涂层的硬度有可能超过金刚石。
软涂层刀具,如 MoS2和 WS2作为涂层材料的高速钢刀具主要用于高强度铝合金、钛合金等的加工。
此外,最新开发的纳米涂层材料刀具在高速切削中的应用前景也很广阔。
如日本住友公司的纳米TiAlN复合涂层铣刀片,共2000层涂层,每层只有2.5nm厚。
2.金属陶瓷刀具金属陶瓷主要包括高耐磨性能的TiC基硬质合金(TiC+Ni或Mo)、高韧性的TiC基硬质合金( TiC+TaC+WC)、强韧的TiN基硬质合金和高强韧性的TiCN基硬质合金(TiCN+NbC)等。
这些合金做成的刀具可在υc=300m/min~500m/min范围内高速精车钢和铸铁。
切削和研磨材料PPT课件
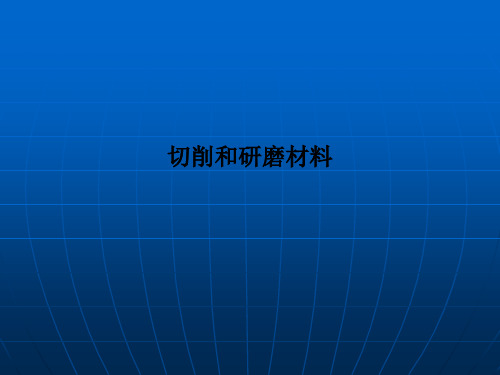
欧洲工业发达国家也相
(3)修复体不能放入过热的清洁液中,以防清洁液爆 溅造成化学性烧伤。
(三)义齿清洁剂
义齿戴入口腔内后,由于受到口腔内外各种因 素如唾液、微生物、食物碎屑、烟、茶等的影响, 将会在义齿表面沉积吸附上一层污物、烟渍、色 素及结石等,这些沉积吸附污物对患者的口腔卫生、 咀嚼功能以及义齿的审美效果都有不同程度的影 响,因此应当予以清除。根据义齿清洁的方法,可 分为机械清洁剂和化学清洁剂。
机械加工包括:灯丝电源绕组、激光切 割、重 型加工 、金属 粘结、 金属拉 拔、等
离子切割、精密焊接、辊轧成型、金 属板材 弯曲成 型、模 锻、水 喷射切 割、精 密焊接 等。
机械加工:广意的机械加工就是
指能用机械手段制造产品的过程;狭 意的是 用车床 (Lathe Machine)、铣床(Milling Machine)、钻床(Driling Machine)、磨
二、 切削、研磨材料的种类和性能
(一)切削、研磨工具 1. 金刚石磨具(diamondpoint wheel)
金刚石具有极高的硬度和良好的热稳定性, 非常适于切削牙体硬组织,特别是牙釉质。
金刚石钻针:是将金刚石粉末,用电镀的方法, 固定在具有某种外型的金属切削表面上。 对切削发挥重要作用的是粉末颗粒的锐角 角度、粒度分布、电镀层的厚度、层数等 因素。
机械加工是一种用加工机械对工件的 外形尺 寸或性 能进行 改变的 过程。 按被加 工的工 件处于 的温度 状态﹐ 分为冷 加工和 热加工 。
一般在常温下加工,并且不引起工件 的化学 或物相 变化﹐ 称冷加 工。一 般在高 于或低 于常温 状态的 加工﹐ 会引起 工件的 化学或 物
相变化﹐称热加工。冷加工按加工方 式的差 别可分 为切削 加工和 压力加 工。热 加工常 见有热 处理﹐ 煅造﹐ 铸造和 焊接。
数控机床加工铝青铜材料的最佳切削参数选择方法

数控机床加工铝青铜材料的最佳切削参数选择方法摘要:数控机床在现代制造业中起着重要作用,而切削参数的选择对于保证加工质量和效率至关重要。
本文介绍了数控机床加工铝青铜材料时选择最佳切削参数的方法,包括切削速度、进给速度和切削深度等关键参数的选择原则以及实际应用案例。
1. 引言随着工业制造技术的不断发展,数控机床已经成为现代制造业中不可或缺的工具。
数控机床加工铝青铜材料时的切削参数选择直接影响着加工质量和效率,因此合理选择最佳切削参数是非常重要的。
2. 切削参数的选择原则2.1 切削速度切削速度是加工过程中最直接影响切削温度和切削力的参数之一。
对于铝青铜材料而言,过高的切削速度会导致切削温度过高,容易引起刀具磨损和表面粗糙度增加。
过低的切削速度则会导致加工效率低下。
因此,在选择切削速度时应综合考虑加工质量、切削温度和刀具磨损等因素,并根据具体材料的特性和实际情况进行调整。
2.2 进给速度进给速度是指刀具在单位时间内前进的距离,也是影响加工效率和加工质量的重要参数之一。
对于铝青铜材料而言,过高的进给速度会导致切削过程中切屑过多,容易造成刀具卡刃、表面质量差等问题。
过低的进给速度则会导致加工效率低下。
因此,进给速度的选择应结合切削速度和刀具性能等因素进行综合考虑,并根据具体材料的特性和实际情况进行调整。
2.3 切削深度切削深度是指刀具切入工件的深度,也是影响加工质量和切削力的重要参数之一。
对于铝青铜材料而言,过大的切削深度会导致切削力过大,容易引起加工振动、表面质量差等问题。
过小的切削深度则会导致加工效率低下。
因此,在选择切削深度时应结合工件的精度要求、刀具性能和加工稳定性等因素进行综合考虑,并根据具体材料的特性和实际情况进行调整。
3. 数控机床加工铝青铜材料的实际应用案例为了验证切削参数选择方法的有效性,本文选取了一家机械制造企业进行实际应用案例分析。
该企业使用数控铣床加工铝青铜材料,制作零部件。
通过对该企业生产线上10个不同型号的零部件进行加工实验,记录了不同切削参数下的加工质量和效率数据。
金属高速切削原理与刀具材料的选择

金属高速切削原理与刀具材料的选择金属高速切削是一种广泛应用于金属加工领域的切削技术,它的原理是通过旋转的刀具快速切削工件上的金属材料以达到所需形状和尺寸。
刀具的材料选择对于金属高速切削过程的效率和切削品质具有重要影响。
本文将讨论金属高速切削的原理和刀具材料的选择。
金属高速切削的原理主要涉及两个方面,即削减原理和切削时产生的热量控制。
首先,削减原理指的是刀具将金属工件上的金属材料削减下来,形成所需的形状和尺寸。
刀具旋转时,刀尖与工件接触形成剪切力,将金属材料从工件上脱离。
对于高速切削来说,切削速度较快,所产生的剪切力也更大,因此切削力的平衡和控制非常重要。
其次,切削过程会产生大量的热量,这也是需要控制的关键。
高速切削时,热量会导致切削区域的变形、硬度降低和刀具磨损等问题。
因此,切削时需要采取措施,例如冷却液的引入和切削区域的冷却,以控制切削过程中产生的热量。
刀具的选择对于金属高速切削的效果和效率至关重要。
刀具的材料选择应考虑以下几个方面:硬度、热稳定性、抗磨性和韧性。
首先,刀具的硬度是切削效果的关键因素。
刀具材料需要具有足够的硬度,以抵抗金属工件上的金属材料的削减。
常见的刀具材料有硬质合金、陶瓷和超硬材料等。
硬质合金由钴基和硬质颗粒组成,具有较高的硬度和耐磨性,适用于大多数金属的高速切削。
陶瓷刀具具有较高的硬度和耐磨性,适用于切削高硬度和脆性材料。
超硬材料(如金刚石和立方氮化硼)具有极高的硬度,适用于切削硬度非常高的金属。
其次,刀具的热稳定性也是刀具材料选择的重要考虑因素。
高速切削时,刀具会受到高温环境的影响,因此需要选择具有良好热稳定性的材料。
硬质合金在高温下有较好的稳定性,能够耐受高温和高切削速度条件下的切削过程。
陶瓷刀具和超硬材料具有较低的导热性,能够减少切削时产生的热量。
另外,刀具的抗磨性也是刀具材料选择的重要因素之一。
高速切削会引起切削力的增加和较大的摩擦力,这对刀具材料的抗磨性提出了要求。
不同刀具材质切削加工切削速度表

不同刀具材质切削加工切削速度表
当切削深度和进给量选好以后,切削速度也应选取较为合理的数值。
应当做到既能发挥车刀的切削性能,又能发挥车床的潜力,并且保证加工表面质量和降低成本。
选择切削速度的一般原则如下:1)车刀材料使用硬质合金车刀可比高速工具钢车刀的切削速度快。
2)工件材料切削强度和硬度较高的工件时,因为产生的热量和切削力都比较大,车刀容易磨损,所以切削速度应选得低些。
脆性材料如铸铁工件,虽然强度不高,但车削时形成崩碎切屑,热量集中在切削刃附近,不易传散。
因此,切削速度也应取得低一些。
3)表面粗糙度要求表面粗糙度值小的工件,如用硬质合金车刀车削,切削速度应取得高些;如用高速工具钢车刀车削,切削速度应取得低些。
各材质的铣削参数

不锈钢
0.15
0.25
0.08
0.13
0.13
0.20
0.10
0.15
0.05
0.08
0.05
0.08
Al-Mg合金
0.55
0.5
0.28
0.25
0.45
040
0.32
0.30
0.18
0.15
0.13
0.13
黄铜丶青铜
快削
0.55
0.5
0.28
0.25
0.45
0.4
0.32
0.3
0.18
0.15
--
--
每一切削刃进给量
f(mm/刃)
即一次只用一片切削刃进行切削。
--
--
切削宽度b(mm)
铣刀切削一回,切削工件的宽度。切削时,也会因铣刀直径丶刃数和切削宽度大小关系而发生震动。
--
--
切削速度:
铸铁(软)
32
50-60
120-150
铸铁(硬)
24
30-60
75-100
可锻铸铁
24
30-75
50-100
钢(软)
27
30-75
150钢(硬)15源自2530铝合金
150
95-300
300-1200
黄钢(软)
60
240
180
黄钢(硬)
50
150
300
青铜
50
75-150
150-240
铜
50
150-240
240-300
硬橡胶
60
240
450
纤维
白钢铣刀切削参数

白钢铣刀切削参数白钢铣刀是现代机械加工中常用的一种切削工具,具有切削效率高、使用寿命长、适用范围广等优点。
在进行白钢铣刀的切削加工时,需要合理设置切削参数,以实现高效、精确的加工效果。
下面将从刀具材料、切削速度、进给速度、切削深度、冷却润滑等方面,详细介绍关于白钢铣刀的切削参数。
一、刀具材料白钢铣刀的主要材料是白钢,它具有良好的硬度、耐磨性和热稳定性,适用于高速切削。
选择合适的白钢材料,能够保证刀具在切削过程中具有较好的刚性和切削性能,从而保证加工质量和效率。
二、切削速度切削速度是白钢铣刀切削参数中最为关键的一个指标。
在选择切削速度时,需要考虑刀具材料、工件材料、刀具直径等多种因素。
通常情况下,切削速度过高会导致刀具磨损加快、发生断刀等问题,而切削速度过低则会影响加工效率。
在设定切削速度时,需要充分考虑刀具的质量和工件的要求,合理确定切削速度。
三、进给速度进给速度是指刀具在每分钟内切削所移动的距离。
合理的进给速度能够保证切屑顺利排出、减小切削温度、降低刀具磨损、提高加工表面质量。
进给速度过大会导致切削力增大,刀具寿命缩短,而进给速度过小则会影响切削效率。
在确定进给速度时,需要结合切削性能、工件材料和加工要求进行综合考虑。
四、切削深度切削深度是指刀具在切削过程中进入工件的距离。
切削深度的选择直接影响到加工的进给量、切削力和切削温度等因素。
在设定切削深度时,需要根据工件材料、刀具材料、刀具结构以及切削稳定性等因素进行合理的选择,以确保切削过程中的稳定性和安全性。
五、冷却润滑在白钢铣刀的切削加工中,合理的冷却润滑是确保刀具寿命和加工质量的关键因素。
冷却润滑可以有效降低切削温度、减小切削力、延长刀具寿命。
常用的冷却润滑方式包括刀具内冷却、刀具外冷却、切削区冷却等。
选择合适的冷却润滑方式,能够有效提高切削效率,减少刀具磨损,保证加工质量。
白钢铣刀的切削参数包括刀具材料、切削速度、进给速度、切削深度、冷却润滑等多个方面。
- 1、下载文档前请自行甄别文档内容的完整性,平台不提供额外的编辑、内容补充、找答案等附加服务。
- 2、"仅部分预览"的文档,不可在线预览部分如存在完整性等问题,可反馈申请退款(可完整预览的文档不适用该条件!)。
- 3、如文档侵犯您的权益,请联系客服反馈,我们会尽快为您处理(人工客服工作时间:9:00-18:30)。
切削速度与每刃每转吃刀量
一、切削速度
刀具旋转时的线速度:
V=πDN/1000(m/min)
其中 D ——刀具直径( mm) N——(F1)刀具转速(rpm)
表1 切削速度V 推荐参数
表2 刀具切削速度一览表
二、每刃每转吃刀量
单刃吃刀量f a f a =F/n F—进给速度,n—转速,刀具每转过1刀刃与工件的相对位移(mm)
表3 单刃吃刀量一览表(单刃)
单位mm
1
常用雕刻材料切削性能
一、材料加工特性概述
雕刻行业常用的材料可以分为金属材料和非金属材料。
金属材料又可分为铸铁、碳钢、合金钢、有色金属及合金四类。
确决定材料的加工性能的重要因素是硬度,当然还与韧性、粘性有关。
总体来说,金属材料的硬度通常要大于非金属材料,刀具要有较大的切削力,考虑的多是刀具磨损、刀具强度、防止断刀等问题,而非金属材料多为软材料,对刀具的锋利程度要求较高,更多考虑如何保证排屑和侧边质量等问题。
以金属中最为常见的三种材料59号铜、紫铜、Cr12模具钢为例,59#铜这种材料强度低、脆性高、硬度低(164HB),且导热性好,具有良好的切削加工性。
在加工时,吃刀深度和走刀速度也可以加大。
紫铜,这种材料的特点是导电性能好,强度低、硬度最低(35HB),属于软材料,材料的粘性大,不易断削,在加工中,考虑到它的粘性,开槽深度和走刀速度要相应的降低。
Cr12模具钢,这种材料具有高强度、高硬度(未经热处理的材料硬度在200~250HB),相对59#铜较难切削,加工中,要采用较低的开槽深度和走刀速度。
二、常用雕刻材料性能比较
下面比较5种常用雕刻材料的切削加工性能:
表4 几种常用雕刻材料性能比较
结论:在加工不同材料时要综合机床性能,选择参数合适的刀具,并设置相应的主轴转速和进给参数!
2。