怎么计算各中加工中心刀具的切削速度
加工中心进给速度的计算公式

加工中心进给速度的计算公式在机械加工的世界里,加工中心就像是一位技艺精湛的大厨,而进给速度则是决定这道“机械大餐”品质的关键调料。
咱们今天就来好好聊聊加工中心进给速度的计算公式,这可是个相当重要的玩意儿。
我还记得有一次,在一家工厂里,一位年轻的操作工小王正对着加工中心发愁。
他刚刚接到一个新的加工任务,需要加工一批精密零件,可是对于进给速度的设置,他心里完全没底。
他一脸迷茫地看着操作面板,手都不知道该往哪儿放。
咱们先来说说什么是进给速度。
简单来讲,进给速度就是刀具在加工过程中移动的速度。
这个速度要是设置得不合适,那可就麻烦啦!太快了,刀具容易磨损,甚至可能导致零件报废;太慢了,加工效率低下,老板的脸色可就不好看喽!那这进给速度到底是怎么算出来的呢?其实啊,它主要取决于几个因素。
首先就是切削速度,这就好比是汽车的最高时速,决定了刀具能跑多快。
然后是刀具的每齿进给量,这就像是汽车的轮子每转一圈能前进多少距离。
还有就是刀具的齿数,这就相当于汽车有几个轮子在同时工作。
具体的计算公式是这样的:进给速度 = 切削速度 ×刀具齿数 ×每齿进给量。
比如说,切削速度是 100 米/分钟,刀具齿数是 3,每齿进给量是0.1 毫米,那进给速度就是 100 × 3 × 0.1 = 30 毫米/分钟。
但是,这只是一个理论值,实际情况可要复杂得多。
因为在加工过程中,还得考虑材料的硬度、刀具的材质、机床的性能等等因素。
就像小王那次,他按照理论公式计算出了一个进给速度,结果一开始加工,就发现刀具磨损得特别快。
后来经过仔细检查,才发现是材料的硬度比预计的要高,所以他不得不重新调整进给速度。
在实际操作中,经验也起着非常重要的作用。
老师傅们往往能根据自己多年的经验,一眼就看出大概应该设置什么样的进给速度。
但对于新手来说,就得一步一步地摸索,不断地尝试和调整。
总之,加工中心进给速度的计算公式虽然看起来简单,但要真正掌握好,还得结合实际情况,不断积累经验。
加工中心常用计算公式

1.tanθ=b/a θ=tan-1b/a2.Sinθ=b/c Cos=a/cVc=(π*D*S)/1000Vc:线速度(m/min) π:圆周率(3.14159) D:刀具直径(mm) S:转速(rpm)例题. 使用Φ25的铣刀Vc为(m/min)25求S=?rpmVc=πds/100025=π*25*S/1000S=1000*25/ π*25S=320rpmF=S*Z*FzF:进给量(mm/min) S:转速(rpm) Z:刃数Fz:(实际每刃进给)例题.一标准2刃立铣刀以2000rpm)速度切削工件,求进给量(F 值)为多少?(Fz=0.25mm)F=S*Z*FzF=2000*2*0.25F=1000(mm/min)Scallop=(ae*ae)/8RScallop:残料高(mm) ae:XYpitch(mm) R刀具半径(mm)例题.Φ20R10精修2枚刃,预残料高0.002mm,求Pitch为多少?mmScallop=ae2/8R0.002=ae2/8*10ae=0.4mmΦ=√2R2 X、Y=D/4Φ:逃料孔直径(mm) R刀具半径(mm) D:刀具直径(mm)例题. 已知一模穴须逃角加工(如图),所用铣刀为ψ10;请问逃角孔最小为多少?圆心坐标多少?Φ=√2R2Φ=√2*52Φ=7.1(mm)X、Y=D/4X、Y=10/4X、Y=2.5 mm圆心坐标为(2.5,-2.5)Q=(ae*ap*F)/1000Q:取料量(cm3/min) ae:XYpitch(mm)ap:Zpitch(mm)例题. 已知一模仁须cavity等高加工,Φ35R5的刀XYpitch是刀具的60%,每层切1.5mm,进给量为2000mm/min,求此刀具的取料量为多少?Q=(ae*ap*F)/1000Q=35*0.6*1.5*2000/1000Q=63 cm3/minFz=hm * √(D/ap )Fz:实施每刃进给量hm:理论每刃进给量ap:Zpitch(mm)D:刀片直径(mm)例题(前提depo XYpitch是刀具的60%)depoΦ35R5的刀,切削NAK80材料hm为0.15mm,Z轴切深1.5mm,求每刃进给量为多少?Fz=hm * √(D/ap )Fz=0.2*√10/1.5Fz=0.5mm冲模刀口加工方法刀口加工深度=板厚-刀口高+钻尖(0.3D)D表示刀径钻头钻孔时间公式T(min)=L(min)/N(rpm)*f(mm/rev)=πDL/1000vfL:钻孔全长N:回转数f:进刀量系数D:钻头直径v:切削速度如图孔深l钻头孔全长L则L=l+D/3T=L/Nf=πDL/1000vf系数表f直径mm进刀mm/rev1.6~3.2 0.025~0.0753.2~6.4 0.05~0.156.4~12.8 0.10~0.2512.8~25 0.175~0.37525以上0.376~0.625管牙计算公式1英寸=25.4mm=8分25.4/牙数=牙距例如25.4/18=1.414牙距为5/16丝攻马力(枪钻)W=Md*N/97.410W:所要动力(KW)Md:扭矩(kg-cm)N:回转数(r.p.m)扭矩计算公式如下:Md=1/20*f*ps*f为进给量mm/rev系数r为钻头半径赛(mm)α:切削抵抗比值ps.在小进给时,一般钢为500kg/m㎡;一般铸铁为300kg/m㎡;。
加工中心常用计算公式

CNC常用计算公式一、三角函数计算1.tanθ=b/aθ=tan-1b/a2.Sinθ=b/c Cos=a/c二、切削速度的计算Vc=(π*D*S)/1000Vc:线速度(m/min) π:圆周率(3.14159) D:刀具直径(mm)S:转速(rpm)例题. 使用Φ25的铣刀Vc为(m/min)25 求S=?rpmVc=πds/100025=π*25*S/1000S=1000*25/ π*25S=320rpm三、进给量(F值)的计算F=S*Z*FzF:进给量(mm/min) S:转速(rpm) Z:刃数Fz:(实际每刃进给)例题.一标准2刃立铣刀以2000rpm)速度切削工件,求进给量(F值)为多少?(Fz=0.25mm)F=S*Z*FzF=2000*2*0.25F=1000(mm/min)四、残料高的计算Scallop=(ae*ae)/8RScallop:残料高(mm) ae:XY pitch(mm) R刀具半径(mm)例题. Φ20R10精修2枚刃,预残料高0.002mm,求Pitch为多少?mmScallop=ae2/8R0.002=ae2/8*10ae=0.4mm五、逃料孔的计算Φ=√2R2X、Y=D/4Φ:逃料孔直径(mm) R刀具半径(mm) D:刀具直径(mm)例题. 已知一模穴须逃角加工(如图),所用铣刀为ψ10;请问逃角孔最小为多少?圆心坐标多少?Φ=√2R2Φ=√2*52Φ=7.1(mm)X、Y=D/4X、Y=10/4X、Y=2.5 mm圆心坐标为(2.5,-2.5)六、取料量的计算Q=(ae*ap*F)/1000Q:取料量(cm3/min)ae:XY pitch(mm) ap:Z pitch(mm)例题. 已知一模仁须cavity等高加工,Φ35R5的刀XY pitch是刀具的60%,每层切1.5mm,进给量为2000mm/min,求此刀具的取料量为多少?Q=(ae*ap*F)/1000Q=35*0.6*1.5*2000/1000Q=63 cm3/min七、每刃进给量的计算Fz=hm * √(D/ap )Fz:实施每刃进给量hm:理论每刃进给量 ap:Z pitch(mm)D:刀片直径(mm)例题 (前提depo XY pitch是刀具的60%)depoΦ35R5的刀,切削NAK80材料hm为0.15mm,Z轴切深1.5mm,求每刃进给量为多少?Fz=hm * √(D/ap )Fz=0.2*√10/1.5Fz=0.5mm冲模刀口加工方法刀口加工深度=板厚-刀口高+钻尖(0.3D)D表示刀径钻头钻孔时间公式T(min)=L(min)/N(rpm)*f(mm/rev)=πDL/1000vfL:钻孔全长N:回转数f:进刀量系数D:钻头直径v:切削速度如图孔深l钻头孔全长L则L=l+D/3T=L/Nf=πDL/1000vf系数表f直径mm进刀mm/rev1.6~3.2 0.025~0.0753.2~6.4 0.05~0.156.4~12.8 0.10~0.2512.8~25 0.175~0.37525以上0.376~0.6251英寸=25.4mm=8分25.4/牙数=牙距管牙计算公式例如25.4/18=1.414牙距为5/16丝攻马力(枪钻)W=Md*N/97.410W:所要动力(KW)Md:扭矩(kg-cm)N:回转数(r.p.m)扭矩计算公式如下:Md=1/20*f*ps*f为进给量mm/rev系数r为钻头半径赛(mm)α:切削抵抗比值ps.在小进给时,一般钢为500kg/m㎡;一般铸铁为300kg/m㎡;。
加工中心常用计算公式

加工中心常用计算公式加工中心是一种高效的机械化设备,广泛应用于零件的制造和加工领域。
在加工中心的使用过程中,常常需要进行各种计算公式的使用,以确保零件加工的精度和质量。
以下是加工中心常用的计算公式及其应用。
1.液压缸的推力计算公式液压缸是加工中心中常用的执行元件之一,常用于控制机械臂的运动。
液压缸的推力计算公式如下:F=P×A其中,F表示液压缸的推力,单位为牛顿(N);P表示液压缸的工作压力,单位为帕斯卡(Pa);A表示液压缸的有效面积,单位为平方米(m²)。
2.旋转轴承的径向载荷计算公式Fr=C×(N/1000)×(n/60)^2其中,Fr表示旋转轴承的径向载荷,单位为牛顿(N);C表示旋转轴承的基本动载荷额定值,单位为牛顿(N);N表示旋转轴承的转速,单位为转每分钟(rpm);n表示旋转轴承的转速,单位为转每秒(rps)。
3.表面粗糙度的计算公式表面粗糙度是衡量零件表面加工质量的指标之一,加工中心通常需要控制表面粗糙度在一定范围内。
表面粗糙度的计算公式如下:Ra=(1/n)×Σ(Zi)×l其中,Ra表示表面粗糙度,单位为微米(μm);n表示采样点数;Zi 表示采样点的表面离差值,单位为微米(μm);l表示采样长度,单位为长度单位。
4.切削速度的计算公式Vc=π×D×n/1000其中,Vc表示切削速度,单位为米每分钟(m/min);D表示刀具的直径,单位为毫米(mm);n表示刀具的转速,单位为转每分钟(rpm)。
5.进给速度的计算公式进给速度是加工中心中工件或刀具在进给方向上的运动速度。
进给速度的计算公式如下:Vf=f×Z×n其中,Vf表示进给速度,单位为毫米每分钟(mm/min);f表示每刀的进给量,单位为毫米(mm);Z表示每刀的切削刃数;n表示刀具的转速,单位为转每分钟(rpm)。
以上是加工中心常用的计算公式及其应用,通过这些公式的应用,可以实现加工中心的高效和精确的加工过程,提高零件的加工质量和生产效率。
加工中心刀具切削用量表

线速度(米/分钟) 铝 高速钢铣刀 镀层硬质合金铣刀 硬质合金铣刀
加工中心刀具切削用量表
45# 60 100~300 100~300
淬硬钢 15~20
60
铸铁 15~20
30
15~20 60 30
S(转速)=线速度×1000/(直径×3.14) F(进给量)=刃数×每刃切削量×转速
每刃切削量 粗加 ~ 0.05
例:20MM硬质合金4刃铣刀精铣45#钢,线速度取60。每刃切0.05。则转速=60×1000/(20×3.14) =955,进给量=4×0.05×955=191。
以上是比较笼统的概括,适用于大多数铣刀、钻头、镗刀(不包括绞刀)加工工艺的计算。在实 际加工中还要针对不同实际情况做出调整。如:工件形状、余量大小、冷却条件、刀具磨损等。
每刃切削量参数的选择:如果太小小于0.02,那不是在切削,是在磨刀,如果太大大于0.2,那也 不是切削,是在撞击。所以并非转速越高,进给量越小越好切削,刀具必须处在一个合理的运动 状态下,才是均质、稳定的切削。
刀具加工中,对刀具寿命影响最大的是线速度,刀具商提供刀具的同时,应该会提供一份刀具针 对各种材料的线速度表,但刀具供应商的参数是在理想状态下得到的,在实际加工中,得打个 7~8折的。
工艺参数计算方法
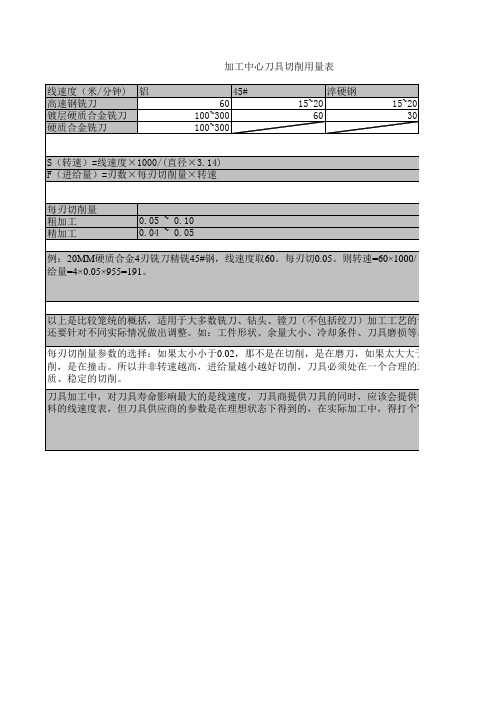
每刃切削量参数的选择:如果太小小于0.02,那不是在切削,是在磨刀。所以并非转速越高,进给量越小越好切削,刀具必须处在一个合理的运动状态下,才是 质、稳定的切削。
刀具加工中,对刀具寿命影响最大的是线速度,刀具商提供刀具的同时,应该会提供一份刀具针对各种 料的线速度表,但刀具供应商的参数是在理想状态下得到的,在实际加工中,得打个7~8折的。
加工中心刀具切削用量表 线速度(米/分钟) 高速钢铣刀 镀层硬质合金铣刀 硬质合金铣刀 铝 60 100~300 100~300 45# 15~20 60 淬硬钢 15~20 30
S(转速)=线速度×1000/(直径×3.14) F(进给量)=刃数×每刃切削量×转速 每刃切削量 粗加工 精加工
0.05 ~ 0.10 0.04 ~ 0.05
铸铁 15~20 60 30
=60× 1000/(20× 3.14)=955,进
加工工艺的计算。在实际加工中 刀具磨损等。
如果太大大于0.2,那也不是切 一个合理的运动状态下,才是均
应该会提供一份刀具针对各种材 中,得打个7~8折的。
例:20MM硬质合金4刃铣刀精铣45#钢,线速度取60。每刃切0.05。则转速=60× 1000/(20× 3.14)=955, 给量=4× 0.05× 955=191。
以上是比较笼统的概括,适用于大多数铣刀、钻头、镗刀(不包括绞刀)加工工艺的计算。在实际加工 还要针对不同实际情况做出调整。如:工件形状、余量大小、冷却条件、刀具磨损等。
怎么计算各中加工中心刀具的切削速度

质量+效率+成本控制=效益怎么计算各中加工中心刀具的切削速度?浏览次数:202次悬赏分:10 | 解决时间:2011-3-3 10:15 | 提问者:zhaoqizhi521问题补充:例如:(16,20,25,32,50,63,80,125)平面铣刀,(1~20)涂层合金立铣刀,(1~30)钨钢钻,(6~80)镗刀((求切削速度切削用量))不是公式,公式我知道,就是刀具的切削用量,切削速度!!最佳答案 S=Vc*1000/3.1415*DF=S*fz*z刀具线速度(刀具商提供)乘以1000再除去3.1415再除掉刀具直径就等于主轴转数;主轴转数乘以每齿进刀量(刀具不同进刀量不同)再乘以刀具总齿数就等于进给速度;高速钢铣刀的线速度为50M/MIN硬质合金铣刀的线速度为150M/MIN切削用量的话是每齿切削0.08-0.2之间。
切削速度为转速*齿数*每齿进给。
不锈钢的话*80%铝合金本身材料很软,主轴转速应当高点(刀具能承受的情况下),进给速度要竟量小点,如果进给大的话排屑就会很困难,只要你加工过铝,不难发现刀具上总会有粘上去的铝,那说明用的切削液不对,做铝合金进给可以打快一点每一刀也可以下多一点转数不能打的太快10MM F150020MM F120050MM F1000加工中心-三菱系统的操作步骤与刀具应用 (2009-04-23 09:02:03)转载标签:数控刀具转速进给杂谈三菱系统操作:1,打开机床开关—电源接通按钮2,归零:将旋钮打到ZRN—按循环启动键,三轴同时归零。
(也可以xyz分开来归零:将旋钮打到ZRN—按Z+,X+,Y+,一般要先将Z轴归零)注意:每次打开机床后,就要归零。
3,安装工件(压板或虎口钳)4,打表(平面和侧面)侧面打到2丝之内,表面在5丝之内,最好再打一下垂直度。
5,中心棒分中,转速500.6,打开程序,看刀具,装刀具,注意刀具的刃长和需要的刀长,绝不能装短了。
7,模拟程序—传输程序。
加工中心常用计算公式

加工中心常用计算公式加工中心作为一种高精度、高效率的数控机床,广泛应用于航空、汽车、电子、模具、仪器仪表等领域,用于进行零件的精密加工。
在加工中心的加工过程中,有一些常用的计算公式,用于确定刀具的尺寸、工件的位置、加工速度等参数,下面介绍一些常见的加工公式。
一、刀具尺寸计算公式在加工中心的加工过程中,刀具的尺寸是非常关键的,直接影响到加工精度和表面质量。
以下是一些常见的刀具尺寸计算公式:1. 切削深度(a)的计算公式:a = (D1 - D2) × cosα其中,D1为刀具刃口直径,D2为末刃直径,α为刀具倾角。
2.刀具半径(R)的计算公式:R=(D1-D2)/23. 圆柱刀具的公法圆半径(Rc)的计算公式:Rc = R / cos(α/2)其中,α为圆柱刀具的圆锥度。
二、工件位置计算公式在加工中心的加工过程中,确定工件在机床坐标系中的位置是非常重要的。
以下是一些常见的工件位置计算公式:1. 相对初始位置(X,Y,Z)的计算公式:X = X0 + l × cosα × cosβ,Y = Y0 + l × sinα × cosβ,Z = Z0 + l × sinβ其中,(X0,Y0,Z0)为初始位置坐标,l为距离,α为水平方向角度,β为竖直方向角度。
2. 相对初始位置(X,Y)的计算公式(仅在水平加工中使用):X = X0 + l × cosα,Y = Y0 + l × sinα其中,(X0,Y0)为初始位置坐标,l为距离,α为方向角度。
三、进给速度计算公式进给速度是指刀具在加工过程中前进的速度,是保证加工精度和效率的重要参数。
以下是一些常见的进给速度计算公式:1.进给速度(V)的计算公式:V=N×f×z其中,N为主轴转速,f为切削速度,z为刀具刃口数量。
2.切削速度(f)的计算公式:f=π×D×N其中,D为刀具直径,N为主轴转速。
加工中心常用计算公式

CNC常用计算公式一、三角函数计算θ=b/aθ=tan-1b/aθ=b/c Cos=a/c二、切削速度的计算Vc=(π*D*S)/1000Vc:线速度(m/min) π:圆周率 D:刀具直径(mm)S:转速(rpm)例题. 使用Φ25的铣刀Vc为(m/min)25 求S=rpmVc=πds/100025=π*25*S/1000S=1000*25/ π*25S=320rpm三、进给量(F值)的计算F=S*Z*FzF:进给量(mm/min) S:转速(rpm) Z:刃数Fz:(实际每刃进给)例题.一标准2刃立铣刀以2000rpm)速度切削工件,求进给量(F值)为多少(Fz=F=S*Z*FzF=2000*2*F=1000(mm/min)四、残料高的计算Scallop=(ae*ae)/8RScallop:残料高(mm) ae:XY pitch(mm) R刀具半径(mm)例题. Φ20R10精修2枚刃,预残料高,求Pitch为多少mmScallop=ae2/8R=ae2/8*10ae=五、逃料孔的计算Φ=√2R2X、Y=D/4Φ:逃料孔直径(mm) R刀具半径(mm) D:刀具直径(mm)例题. 已知一模穴须逃角加工(如图),所用铣刀为ψ10;请问逃角孔最小为多少圆心坐标多少Φ=√2R2Φ=√2*52Φ=(mm)X、Y=D/4X、Y=10/4X、Y=mm圆心坐标为,六、取料量的计算Q=(ae*ap*F)/1000Q:取料量(cm3/min)ae:XY pitch(mm) ap:Z pitch(mm)例题. 已知一模仁须cavity等高加工,Φ35R5的刀XY pitch是刀具的60%,每层切,进给量为2000mm/min,求此刀具的取料量为多少Q=(ae*ap*F)/1000Q=35***2000/1000Q=63 cm3/min七、每刃进给量的计算Fz=hm * √(D/ap )Fz:实施每刃进给量hm:理论每刃进给量 ap:Z pitch(mm)D:刀片直径(mm)例题 (前提depo XY pitch是刀具的60%)depoΦ35R5的刀,切削NAK80材料hm为,Z轴切深,求每刃进给量为多少Fz=hm * √(D/ap )Fz=*√10/Fz=冲模刀口加工方法刀口加工深度=板厚-刀口高+钻尖(0.3D)D表示刀径钻头钻孔时间公式T(min)=L(min)/N(rpm)*f(mm/rev)=πDL/1000vfL:钻孔全长N:回转数f:进刀量系数D:钻头直径v:切削速度如图孔深l钻头孔全长L则L=l+D/3T=L/Nf=πDL/1000vf系数表f直径mm进刀mm/rev~ ~~ ~~ ~~25 ~25以上~1英寸=25.4mm=8分25.4/牙数=牙距管牙计算公式例如25.4/18=1.414牙距为5/16丝攻马力(枪钻)W=Md*N/97.410W:所要动力(KW)Md:扭矩(kg-cm)N:回转数(r.p.m)扭矩计算公式如下:Md=1/20*f*ps*f为进给量mm/rev系数r为钻头半径赛(mm)α:切削抵抗比值ps.在小进给时,一般钢为500kg/m㎡;一般铸铁为300kg/m㎡;。
切削速度计算公式

切削速度计算公式切削速度是切削加工中一个十分重要的参数,它表示刀具在切削过程中每分钟切削的长度。
切削速度的计算公式可以通过根据工件材料、切削刀具和刀具直径来确定。
以下是常见的切削速度计算公式。
1.单刃铣刀的切削速度计算公式:Vc=π*Dc*n其中,Vc表示切削速度(单位:m/min),Dc表示刀具直径(单位:mm),n表示主轴转速(单位:rpm)。
2.钢材的切削速度计算公式:Vc=(π*Dc*n)/1000其中,Vc表示切削速度(单位:m/min),Dc表示刀具直径(单位:mm),n表示主轴转速(单位:rpm)。
3.车削加工中的切削速度计算公式:Vc=(π*Dc*n)/1000其中,Vc表示切削速度(单位:m/min),Dc表示刀具直径(单位:mm),n表示主轴转速(单位:rpm)。
4.钻削加工中的切削速度计算公式:Vc=(π*Dc*n)/1000其中,Vc表示切削速度(单位:m/min),Dc表示刀具直径(单位:mm),n表示主轴转速(单位:rpm)。
5.铣削加工中的切削速度计算公式:Vc = nc * fz * z其中,Vc表示切削速度(单位:mm/min),nc表示铣削系数(单位:mm/z),fz表示进给速度(单位:mm/min),z表示齿数。
需要注意的是,以上计算公式中的单位可能有所不同,具体应根据实际情况进行转换。
切削速度的选择直接影响到加工效率和工件表面质量,因此在具体应用中需要综合考虑工件材料特性、刀具耐磨性和工艺要求等因素,选择合适的切削速度。
同时,切削过程中应注意刀具的冷却润滑,以减少切削热量对刀具和工件的损伤。
加工中心切削速度和进给速度参数
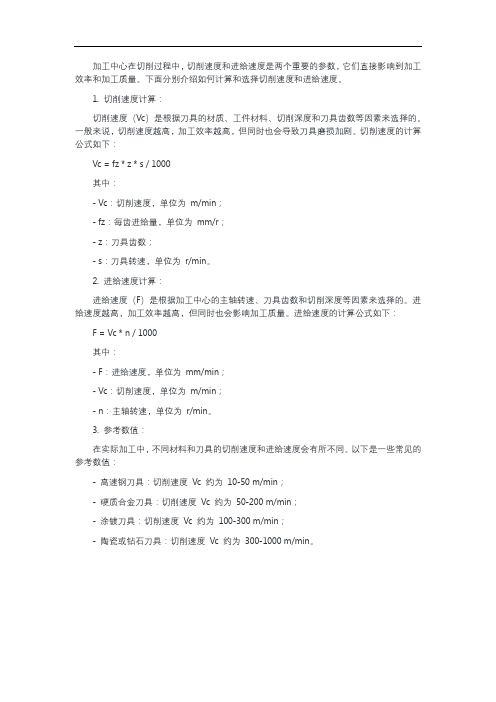
加工中心在切削过程中,切削速度和进给速度是两个重要的参数,它们直接影响到加工效率和加工质量。
下面分别介绍如何计算和选择切削速度和进给速度。
1. 切削速度计算:
切削速度(Vc)是根据刀具的材质、工件材料、切削深度和刀具齿数等因素来选择的。
一般来说,切削速度越高,加工效率越高,但同时也会导致刀具磨损加剧。
切削速度的计算公式如下:
Vc = fz * z * s / 1000
其中:
- Vc:切削速度,单位为m/min;
- fz:每齿进给量,单位为mm/r;
- z:刀具齿数;
- s:刀具转速,单位为r/min。
2. 进给速度计算:
进给速度(F)是根据加工中心的主轴转速、刀具齿数和切削深度等因素来选择的。
进给速度越高,加工效率越高,但同时也会影响加工质量。
进给速度的计算公式如下:
F = Vc * n / 1000
其中:
- F:进给速度,单位为mm/min;
- Vc:切削速度,单位为m/min;
- n:主轴转速,单位为r/min。
3. 参考数值:
在实际加工中,不同材料和刀具的切削速度和进给速度会有所不同。
以下是一些常见的参考数值:
- 高速钢刀具:切削速度Vc 约为10-50 m/min;
- 硬质合金刀具:切削速度Vc 约为50-200 m/min;
- 涂镀刀具:切削速度Vc 约为100-300 m/min;
- 陶瓷或钻石刀具:切削速度Vc 约为300-1000 m/min。
加工中心线速度的计算方法
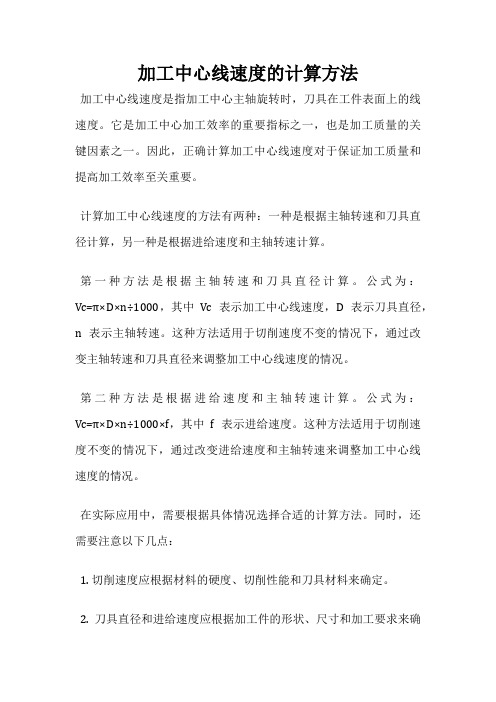
加工中心线速度的计算方法
加工中心线速度是指加工中心主轴旋转时,刀具在工件表面上的线速度。
它是加工中心加工效率的重要指标之一,也是加工质量的关键因素之一。
因此,正确计算加工中心线速度对于保证加工质量和提高加工效率至关重要。
计算加工中心线速度的方法有两种:一种是根据主轴转速和刀具直径计算,另一种是根据进给速度和主轴转速计算。
第一种方法是根据主轴转速和刀具直径计算。
公式为:Vc=π×D×n÷1000,其中Vc表示加工中心线速度,D表示刀具直径,n表示主轴转速。
这种方法适用于切削速度不变的情况下,通过改变主轴转速和刀具直径来调整加工中心线速度的情况。
第二种方法是根据进给速度和主轴转速计算。
公式为:Vc=π×D×n÷1000×f,其中f表示进给速度。
这种方法适用于切削速度不变的情况下,通过改变进给速度和主轴转速来调整加工中心线速度的情况。
在实际应用中,需要根据具体情况选择合适的计算方法。
同时,还需要注意以下几点:
1. 切削速度应根据材料的硬度、切削性能和刀具材料来确定。
2. 刀具直径和进给速度应根据加工件的形状、尺寸和加工要求来确
定。
3. 主轴转速应根据切削速度、刀具直径和进给速度来确定。
4. 加工中心线速度应根据加工件的材料、形状和加工要求来确定。
正确计算加工中心线速度是保证加工质量和提高加工效率的重要保障。
在实际应用中,需要根据具体情况选择合适的计算方法,并注意切削速度、刀具直径、进给速度和主轴转速等因素的综合影响。
加工中心切削速度的计算公式
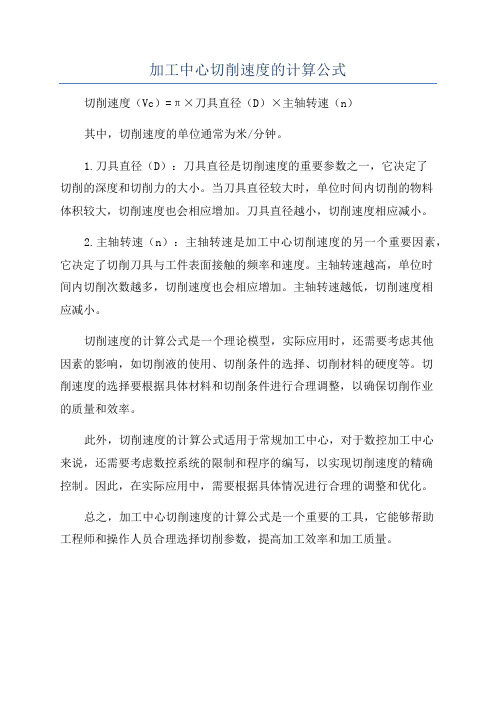
加工中心切削速度的计算公式
切削速度(Vc)=π×刀具直径(D)×主轴转速(n)
其中,切削速度的单位通常为米/分钟。
1.刀具直径(D):刀具直径是切削速度的重要参数之一,它决定了
切削的深度和切削力的大小。
当刀具直径较大时,单位时间内切削的物料
体积较大,切削速度也会相应增加。
刀具直径越小,切削速度相应减小。
2.主轴转速(n):主轴转速是加工中心切削速度的另一个重要因素,它决定了切削刀具与工件表面接触的频率和速度。
主轴转速越高,单位时
间内切削次数越多,切削速度也会相应增加。
主轴转速越低,切削速度相
应减小。
切削速度的计算公式是一个理论模型,实际应用时,还需要考虑其他
因素的影响,如切削液的使用、切削条件的选择、切削材料的硬度等。
切
削速度的选择要根据具体材料和切削条件进行合理调整,以确保切削作业
的质量和效率。
此外,切削速度的计算公式适用于常规加工中心,对于数控加工中心
来说,还需要考虑数控系统的限制和程序的编写,以实现切削速度的精确
控制。
因此,在实际应用中,需要根据具体情况进行合理的调整和优化。
总之,加工中心切削速度的计算公式是一个重要的工具,它能够帮助
工程师和操作人员合理选择切削参数,提高加工效率和加工质量。
加工中心切削参数计算公式

加工中心切削参数计算公式一、切削速度(Vc)1. 计算公式。
- Vc=π dn/1000- 其中:- Vc:切削速度(m/min)- d:刀具直径(mm)- n:主轴转速(r/min)2. 示例。
- 已知刀具直径d = 10mm,主轴转速n = 1000r/min,求切削速度Vc。
- 解:根据公式Vc=π dn/1000,将d = 10mm,n = 1000r/min代入公式。
- Vc=π×10×1000/1000 = 10π≈31.4m/min二、主轴转速(n)1. 计算公式。
- n = 1000Vc/π d- 其中各参数意义同上。
2. 示例。
- 已知切削速度Vc = 50m/min,刀具直径d = 8mm,求主轴转速n。
- 解:将Vc = 50m/min,d = 8mm代入公式n = 1000Vc/π d。
- n=(1000×50)/(π×8)≈1990r/min三、进给量(f)与进给速度(Vf)1. 进给量(f)- 进给量是指刀具在进给运动方向上相对工件的位移量,单位为mm/r(每转进给量)或者mm/min(每分钟进给量)。
- 对于不同的加工工艺(如粗加工、精加工),进给量的取值范围不同。
例如,在粗加工时,为了提高加工效率,可以选择较大的进给量;在精加工时,为了保证加工精度和表面质量,进给量要较小。
2. 进给速度(Vf)- 计算公式:Vf = fn- 其中:- Vf:进给速度(mm/min)- f:进给量(mm/r)- n:主轴转速(r/min)3. 示例。
- 已知主轴转速n = 2000r/min,进给量f = 0.2mm/r,求进给速度Vf。
- 解:根据公式Vf = fn,将n = 2000r/min,f = 0.2mm/r代入公式。
- Vf=0.2×2000 = 400mm/min四、切削深度(ap)1. 定义与取值原则。
- 切削深度是指待加工表面与已加工表面之间的垂直距离,单位为mm。
加工中心刀具切削参数
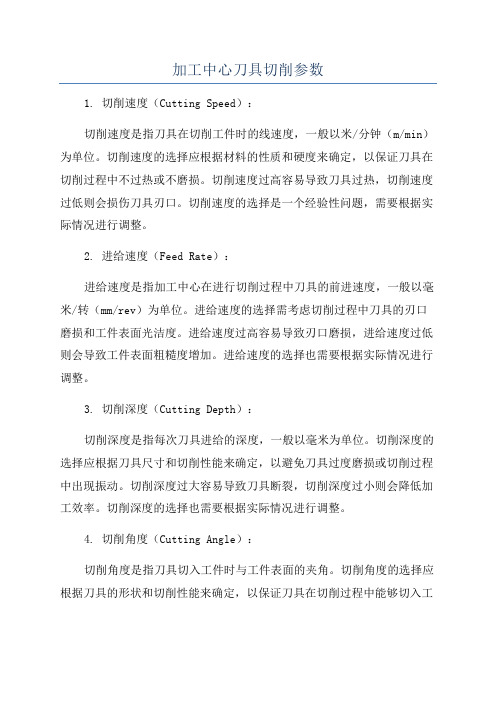
加工中心刀具切削参数1. 切削速度(Cutting Speed):切削速度是指刀具在切削工件时的线速度,一般以米/分钟(m/min)为单位。
切削速度的选择应根据材料的性质和硬度来确定,以保证刀具在切削过程中不过热或不磨损。
切削速度过高容易导致刀具过热,切削速度过低则会损伤刀具刃口。
切削速度的选择是一个经验性问题,需要根据实际情况进行调整。
2. 进给速度(Feed Rate):进给速度是指加工中心在进行切削过程中刀具的前进速度,一般以毫米/转(mm/rev)为单位。
进给速度的选择需考虑切削过程中刀具的刃口磨损和工件表面光洁度。
进给速度过高容易导致刃口磨损,进给速度过低则会导致工件表面粗糙度增加。
进给速度的选择也需要根据实际情况进行调整。
3. 切削深度(Cutting Depth):切削深度是指每次刀具进给的深度,一般以毫米为单位。
切削深度的选择应根据刀具尺寸和切削性能来确定,以避免刀具过度磨损或切削过程中出现振动。
切削深度过大容易导致刀具断裂,切削深度过小则会降低加工效率。
切削深度的选择也需要根据实际情况进行调整。
4. 切削角度(Cutting Angle):切削角度是指刀具切入工件时与工件表面的夹角。
切削角度的选择应根据刀具的形状和切削性能来确定,以保证刀具在切削过程中能够切入工件并顺利进行切削。
切削角度对切削力和刀具寿命有着显著的影响。
切削角度的选择也需要根据实际情况进行调整。
5. 切削液(Cutting Fluid):切削液是指在切削过程中用于冷却刀具和工件的液体。
切削液可以有效降低切削温度、减少切削力和刃口磨损,提高加工质量和刀具寿命。
切削液的选择应根据加工材料和切削性能来确定,以保证切削效果的最佳化。
综上所述,加工中心刀具切削参数是切削加工中的重要参数,对于加工质量和效率具有重要意义。
在实际操作中,需要根据材料性质、刀具特点和切削要求来灵活调整这些参数,以达到最优的加工效果。
切削速度的计算公式

切削速度的计算公式切削速度是金属切削加工中一个非常重要的概念,它对于保证加工质量、提高生产效率以及合理选择刀具和机床都有着至关重要的作用。
那咱们就来好好唠唠切削速度的计算公式。
先给您来个简单的定义,切削速度就是刀具切削刃上的某一点相对于待加工表面在主运动方向上的瞬时速度。
简单说,就是刀具“跑”得多快。
切削速度的计算公式是:v = πdn / 1000 (m/min)。
这里的 v 代表切削速度,d 是刀具或工件的直径(mm),n 是主运动的转速(r/min)。
我给您举个例子哈,比如说咱们要车削一根直径为 50mm 的轴,车床主轴的转速是 500r/min。
那这时候切削速度是多少呢?咱们就把数字往公式里一代:v = 3.14×50×500÷1000 = 78.5(m/min)。
您瞧,这就算出来啦!在实际的加工过程中,切削速度的选择那可是大有讲究。
选得太快,刀具磨损得厉害,加工质量也可能受影响;选得太慢,生产效率又上不去。
这就好比您跑步,跑太快了容易累趴下,跑太慢了又达不到锻炼效果。
我记得有一次在工厂里,有个新手师傅在加工零件的时候,没有好好计算切削速度,就凭着感觉来。
结果呢,刀具磨损得特别快,加工出来的零件表面粗糙度也很差。
这可把他急坏了,后来还是老师傅出马,根据零件的材料、刀具的材质还有机床的性能,重新计算并调整了切削速度,这才解决了问题,加工出了合格的零件。
不同的材料,切削速度也不一样。
像加工钢材和加工铝材,那速度能一样吗?钢材硬度高,切削速度相对就得慢一些;铝材比较软,切削速度就可以适当快一点。
还有啊,刀具的材质也会影响切削速度。
比如说硬质合金刀具,它比高速钢刀具能承受更高的切削速度。
另外,机床的性能也得考虑进去。
好的机床,精度高、稳定性好,能支持更高的切削速度。
总之,切削速度的计算和选择是一门大学问,需要综合考虑各种因素。
只有选对了切削速度,才能既保证加工质量,又提高生产效率,让咱们的加工工作顺顺利利的。
数控加工切削参数计算公式

注:在红色字体位置处,输入你们刀具或工件的实际直径,以及刀具齿数,即可自动计算出相关主轴转速和进给速度。
1.切削速度=3.14*直径*转速/1000;
2.每转进给量=每齿进给量*刀具齿数;
3.每分钏进给量=主轴转速*每转进给量
1000
Dn
V c π=
f
Z f *=
切削速度背吃刀量
每转进
给量
主轴转速
((((
))))
外圆
粗加
工
4010.240318.4713376外圆
精加
工
200.150.0841155.351872切槽
加工
200.0830212.3142251外圆
粗加
工
100 1.50.235909.9181074外圆
精加
工
1300.40.0550828.0254777切槽
加工
1000.0845707.7140835
外圆
粗加
工
150 1.50.2351364.877161外圆
精加
工
1500.40.05401194.267516
切槽加工1000.0845707.7140835
2.每转进给量=每齿进给量*刀具齿数;
3.每分钏进给量=主轴转速*每转进给量
车床切削参数计算参考
刀具材料高速钢
硬质合金钢加工
类型
工件直径
z
f
Z
n
nf
F*
*
=
=
z
f
Z
f*
=
;量
;量。
加工中心切削速度的计算公式

加工中心切削速度的计算公式数控加工中心的切削转速和进给速度:1:主轴转速=1000Vc/πD2:一般刀具的最高切削速度(Vc):高速钢50 m/min;超硬工具150 m/min;涂镀刀具250 m/min;陶瓷·钻石刀具1000 m/min 3加工合金钢布氏硬度=275-325时高速钢刀具Vc=18m/min;硬质合金刀具Vc=70m/min(吃刀量=3mm;进给量f=0.3mm/r)主轴转速有两种计算方法,下面举例说明:①主轴转速:一种是G97 S1000表示一分钟主轴旋转1000圈,也就是通常所说的恒转速。
另一种是G96 S80是恒线速,是由工件表面确定的主轴转速。
进给速度也有两种G94 F100表示一分钟走刀距离为100毫米。
另一种是G95 F0.1表示主轴每转一圈,刀具进给尺寸为0.1毫米。
数控加工中刀具选择与切削量的确定一、数控加工常用刀具的种类及特点数控加工刀具必须适应数控机床高速、高效和自动化程度高的特点,一般应包括通用刀具、通用连接刀柄及少量专用刀柄。
刀柄要联接刀具并装在机床动力头上,因此已逐渐标准化和系列化。
数控刀具的分类有多种方法。
根据刀具结构可分为:①整体式;②镶嵌式,采用焊接或机夹式连接,机夹式又可分为不转位和可转位两种;③特殊型式,如复合式刀具,减震式刀具等。
根据制造刀具所用的材料可分为:①高速钢刀具;②硬质合金刀具;③金刚石刀具;④其他材料刀具,如立方氮化硼刀具,陶瓷刀具等。
从切削工艺上可分为:①车削刀具,分外圆、内孔、螺纹、切割刀具等多种;②钻削刀具,包括钻头、铰刀、丝锥等;③镗削刀具;④铣削刀具等。
为了适应数控机床对刀具耐用、稳定、易调、可换等的要求,近几年机夹式可转位刀具得到广泛的应用,在数量上达到整个数控刀具的30%~40%,金属切除量占总数的80%~90%。
数控刀具与普通机床上所用的刀具相比,有许多不同的要求,主要有以下特点:⑴刚性好(尤其是粗加工刀具),精度高,抗振及热变形小;⑵互换性好,便于快速换刀;⑶寿命高,切削性能稳定、可靠;⑷刀具的尺寸便于调整,以减少换刀调整时间;⑸刀具应能可靠地断屑或卷屑,以利于切屑的排除;⑹系列化,标准化,以利于编程和刀具管理。
- 1、下载文档前请自行甄别文档内容的完整性,平台不提供额外的编辑、内容补充、找答案等附加服务。
- 2、"仅部分预览"的文档,不可在线预览部分如存在完整性等问题,可反馈申请退款(可完整预览的文档不适用该条件!)。
- 3、如文档侵犯您的权益,请联系客服反馈,我们会尽快为您处理(人工客服工作时间:9:00-18:30)。
质量+效率+成本控制=效益怎么计算各中加工中心刀具的切削速度浏览次数:202次悬赏分:10 | 解决时间:2011-3-3 10:15 | 提问者:zhaoqizhi521
问题补充:
例如:(16,20,25,32,50,63,80,125)平面铣刀,(1~20)涂层合金立铣刀,(1~30)钨钢钻,(6~80)镗刀((求切削速度切削用量))不是公式,公式我知道,就是刀具的切削用量,切削速度!!
最佳答案 S=Vc*1000/*D
F=S*fz*z
刀具线速度(刀具商提供)乘以1000再除去再除掉刀具直径就等于主轴转数;
主轴转数乘以每齿进刀量(刀具不同进刀量不同)再乘以刀具总齿数就等于进给速度;
高速钢铣刀的线速度为50M/MIN
硬质合金铣刀的线速度为150M/MIN
切削用量的话是每齿切削之间。
切削速度为转速*齿数*每齿进给。
不锈钢的话*80%
铝合金本身材料很软,主轴转速应当高点(刀具能承受的情况下),进给速度要竟量小点,如果进给大的话排屑就会很困难,只要你加工过铝,不难发现刀具上总会有粘上去的铝,那说明用的切削液不对,
做铝合金进给可以打快一点
每一刀也可以下多一点
转数不能打的太快10MM F1500
20MM F1200
50MM F1000
加工中心-三菱系统的操作步骤与刀具应用 (2009-04-23 09:02:03)转载标签:数控刀具转速进给杂谈
三菱系统操作:
1,打开机床开关—电源接通按钮
2,归零:将旋钮打到ZRN—按循环启动键,三轴同时归零。
(也可以xyz分开来归零:将
旋钮打到ZRN—按Z+,X+,Y+,一般要先将Z轴归零)注意:每次打开机床后,就要归零。
3,安装工件(压板或虎口钳)
4,打表(平面和侧面)侧面打到2丝之内,表面在5丝之内,最好再打一下垂直度。
5,中心棒分中,转速500.
6,打开程序,看刀具,装刀具,注意刀具的刃长和需要的刀长,绝不能装短了。
7,模拟程序—传输程序。
8,将旋钮打到DNC,进给打到10%,RAPID OVERRIDE打到0%—然后在RAPID上在0%~25%上快速转换。
刀具会在工件上方50mm处停顿一下,当刀具靠近工件时需要特别注意。
进给需要打到零。
看看刀具与工件的距离与机床显示的残余值是否对应。
9,最后调整转速与进给。
刀具的进给快慢与材料的硬度有关系。
以下为45号钢。
D63R6:开粗 S800 F3500 吃刀量60丝
精修 S1200 F400
D63R6一般用于粗铣大平面。
D30R5:开粗 S1600 F3000 吃刀量40丝
精修 S2000 F400
:开粗 (开槽) S1800 F2400(1800,3000,2700皆可,看情况而定)
精修底面 S3000 F300-500(45#钢很难把底面铣光)
中修侧面(绕)S1800 F2400(3000因为中修还有精修,所以进给可以打快点)
精修侧面(绕)S3000 F2400
中修侧面与精修侧面的区别在与吃刀量的不同。
D16:一般用于精铣侧面白钢刀S420 F200 (喷油)
钨钢刀S2000 F200(精修侧面一般分两次光,第一次吃刀量大一些,进给可以
稍打快些,500-600,但第二次必须要打慢些200-300)
D10:开粗(开槽) S1800 F2100
精修(底面) S3000 F300
精修(侧面) S3000 F300(精修侧面一般分两次光,第一次吃刀量大一些,进给可以
稍打快些,500-600,但第二次必须要打慢些200-300)
D8:开粗(开槽)S2400 F2100
精修底面 S3000 F300
精修侧面 S3600 F200-300(与D16,D10原理相同)
D25 精修侧壁 S420 F200-300(喷油)白钢刀铣侧壁要喷油
D6 开粗 S2400 F1800
精修侧壁(绕)S3600 F1500
光平面 S3600 F300
清角 S3600 F1200(1500)(清角最后几刀的时候,进给需要打慢些,因为铣到底部的时候,
刀具可能会铣到底部,而且余量也比较多)
D4:开粗 S3600 F1200
精修底部 S4400 F200-300
精修侧壁(绕) S4400 F1200(900)
清角 S4400 F1200(与D6相同)
D4以下的刀,一般用于精修,不用于开粗
D3,D2,D1 S4400 F900
8R1(直径为8,刀尖有1的R角):不用于开粗,因为刀尖有圆角。
精修侧壁(绕)S3000 F1800
6R1,: 精修侧壁 S3600 F1500
球刀用于开流到与中,精修斜面,曲面,不用于开粗。
R5开流道:S2100 F1500 最后一刀打慢些,F400
R3开流道:S3000 F1200 最后一刀打慢些,F400
R5中修斜面,曲面:S2100 F3000
精修:S3000 F2400(3000)
R3精修 S3600 F2100
R1精修 S4400 F1500
精修 S4400 F1800
R2精修 S3600 F1800
倒角器:S1200 F400
钻头:直径越大,转速越慢,进给一般可以打到F20-30 转速:500-1200
D15:S500 F20-30
D10:S600 F20-30
D6:S800 F20-30
D4:S1200 F20-30
一般情况下刀具直径越大,转速越慢,进给越快。