单泵驱动双液压马达系统的仿真分析
《液压与气压传动技术》项目9液压仿真软件Fluidsim精选全文

• 在“选项”菜单下,执行“仿真”命令,用户可以定义颜色与状态值 之间的匹配关系,暗红色管路的颜色浓度与压力相对应,其与最大压 力有关,FluidSIM软件能够区别三种管路颜色浓度颜色浓度与压力关 系见表9. 3。
上一页 下一页 返回
任务2 Fluidsim仿真软件Байду номын сангаас
• 3新建回路图 • 通过单击按钮 或在“文件”,菜单下,执行“新建’,命令,新
建空白绘图区域,以打开一个新窗口如图9. 6所示。只能在编辑模式 下新建或修改回路图,每个新建绘图区域都自动含有一个文件名,且 可按该文件名进行保存。这个文件名显示在新窗口标题栏上。通过元 件库右边的滚动条,用户可以浏览元件。利用鼠标用户可以从元件库 中将元件“拖动”和“放置”在绘图区域上:将鼠标指针移动到元件 库中的元件上,这里将鼠标指针移动到液压缸上,按下鼠标左键。在 保持鼠标左键期间,移动鼠标指针。则液压缸被选中,鼠标指针由箭 头变为小 ,元件外形随鼠标指针移动而移动。将鼠标指针移动到 绘图区域,释放鼠标左键,则液压缸就被拖置绘图区域里如图9. 7所 示,采用这种方法,可以从元件库中“拖动”每个元件,并将其放到 绘图区域中的期望位置上。按同样方法,也可以重新布置绘图区域中 的元件。
《2024年基于AMESim的液压系统建模与仿真技术研究》范文
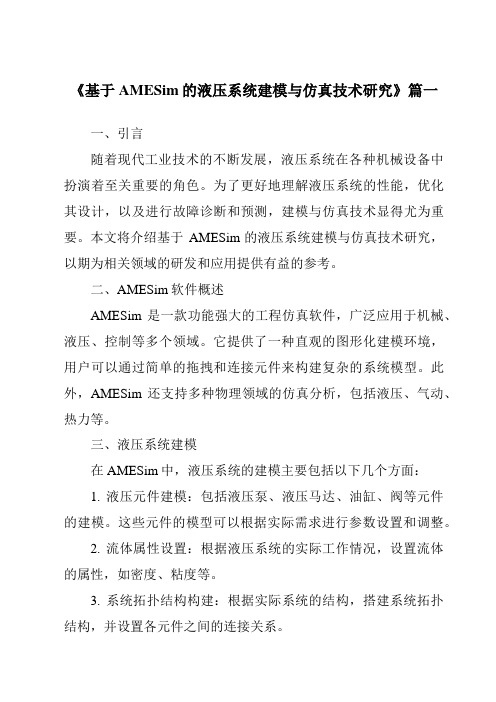
《基于AMESim的液压系统建模与仿真技术研究》篇一一、引言随着现代工业技术的不断发展,液压系统在各种机械设备中扮演着至关重要的角色。
为了更好地理解液压系统的性能,优化其设计,以及进行故障诊断和预测,建模与仿真技术显得尤为重要。
本文将介绍基于AMESim的液压系统建模与仿真技术研究,以期为相关领域的研发和应用提供有益的参考。
二、AMESim软件概述AMESim是一款功能强大的工程仿真软件,广泛应用于机械、液压、控制等多个领域。
它提供了一种直观的图形化建模环境,用户可以通过简单的拖拽和连接元件来构建复杂的系统模型。
此外,AMESim还支持多种物理领域的仿真分析,包括液压、气动、热力等。
三、液压系统建模在AMESim中,液压系统的建模主要包括以下几个方面:1. 液压元件建模:包括液压泵、液压马达、油缸、阀等元件的建模。
这些元件的模型可以根据实际需求进行参数设置和调整。
2. 流体属性设置:根据液压系统的实际工作情况,设置流体的属性,如密度、粘度等。
3. 系统拓扑结构构建:根据实际系统的结构,搭建系统拓扑结构,并设置各元件之间的连接关系。
4. 仿真参数设置:根据仿真需求,设置仿真时间、步长等参数。
四、液压系统仿真在完成液压系统的建模后,可以通过AMESim进行仿真分析。
仿真过程主要包括以下几个方面:1. 初始条件设置:设置系统的初始状态,如初始压力、流量等。
2. 仿真运行:根据设置的仿真时间和步长,运行仿真程序。
3. 结果分析:通过AMESim提供的可视化工具,分析仿真结果,如压力、流量、温度等参数的变化情况。
五、技术应用与优势基于AMESim的液压系统建模与仿真技术具有以下优势:1. 高效性:通过图形化建模环境,可以快速构建复杂的液压系统模型,提高建模效率。
2. 准确性:AMESim提供了丰富的物理模型和算法,可以准确模拟液压系统的实际工作情况。
3. 灵活性:用户可以根据实际需求,灵活地调整模型参数和仿真条件,以获得更符合实际的结果。
AMESim仿真技术及其在液压系统中的应用

结论与展望
通过深入研究液压系统的动态特性,可以为工程机械液压系统的维护和检修 提供更加精确的理论依据和技术支持。这些研究成果将有助于提高工程机械的运 行效率,降低设备的维修成本,具有重要的工程应用价值和发展前景。
谢谢观看
案例分析
案例分析
以某型工程机械液压系统中的故障为例,利用AMESim进行仿真分析。该故障 表现为液压油缸在行程终端时无法实现自锁。首先,建立该型液压系统的AMESim 模型,包括液压泵、液压缸、液压阀等关键元件。然后,对模型进行仿真,并观 察液压缸在行程终端时的状态。
案例分析
通过调整仿真参数,可以发现液压缸在行程终端时无法实现自锁的原因在于 液压缸的密封件磨损严重,导致密封性能下降。这一结果与实际情况基本一致, 说明AMESim在工程机械液压系统故障仿真中的可靠性。
结论与展望
结论与展望
本次演示介绍了基于AMESim的工程机械液压系统故障仿真研究。通过建立液 压系统的AMESim模型,可以对液压系统的工作状态进行实时监控和调整,从而实 现液压系统的优化设计。在未来的研究中,可以进一步拓展AMESim在工程机械液 压系统故障仿真中的应用,如开展多种故障的耦合仿真、引入算法进行故障预测 和预防等方面的研究。
AMESim仿真技术及其在液 压系统中的应用
目录
01 引言
03 原理与实现
02 概述 04 参考内容
引言
引言
液压系统在各种工业领域中具有广泛的应用,如机械制造、航空航天、石油 化工等。随着科技的不断进步,对液压系统的性能和稳定性要求越来越高,因此 仿真技术在液压系统设计、优化和故障诊断中发挥着越来越重要的作用。AMESim 是一种先进的仿真技术,可以针对复杂液压系统进行高精度、高效率的仿真分析。 本次演示将介绍AMESim仿真技术在液压系统中的应用意义、基本原理、应用案例 以及前景展望。
单泵驱动双马达速度同步可实现的负载特性分析

采用Mt 5 b. aI 6 进行数字仿真。同步控制器采用常规的PD a I控制方式。
参数取值如下:
阻尼系数: , 2 .Nmsa 基础负载转矩:T T 1 Nm B= = 1 ""r B 08 /d , 20 " = = 0
预 步 速: 0 r 设同 转 7 p 0 m
s 1s t 5的仿真曲线 =
图 J J 04 Nmsa 5 =f .3 "r 6 , 8 Nm , 3 " /d T - " = 0
: 1s t 5的仿真曲线 =
图 仿真了马达的负载比小于排量比的 4 情况,显然两个马达实现了 速度同步。
从图5 所示仿真结果可以看出,双马达没有达到速度同步。 这是由于马达的最小排量
J, r k-
s 一一 t
马 , 转 惯 ( -2 达1 的 动 量 k m) 2 g
干扰开始时间 ( s )
图
- I 一 -、
; _ 一-一 曰 入 _ -- __ - 。_ -
: 、・- 一 ’/- 一-一 {- 厂- 、-
川
加
J
J
i
了
却
J
目
』 一仁 J
。
es 卜 1 1
四 I ,
L eeJ s ee e ee i s s e e s Le ss s ss s e s s e s s e e
底盘模拟驱动装置进行加载,考核其在各种载荷模式下底盘液压驱动装置的工作性能。 一次元件采用德国RXOH公司的型号为 AV02 带 MOIG ERT 4S15 ORN 控制的恒压变量泵/ 马
达,配四 个蓄能器组成蓄能器组, 形成恒压网 一次元件排量 1 ml 用以 络。 2 lo 5 r
基于AMEsim的液压系统建模与仿真
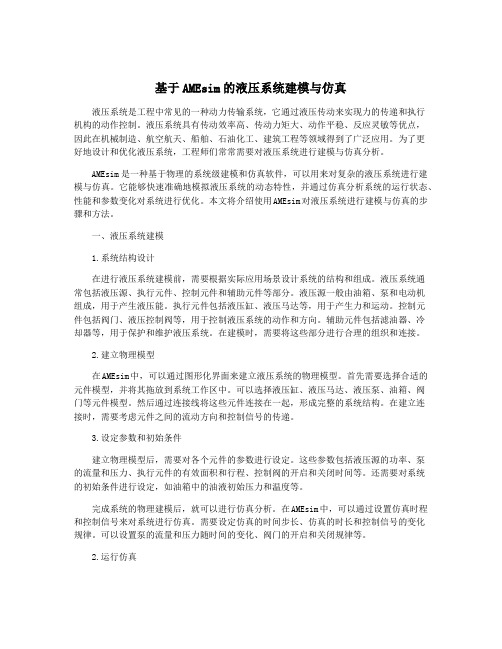
基于AMEsim的液压系统建模与仿真液压系统是工程中常见的一种动力传输系统,它通过液压传动来实现力的传递和执行机构的动作控制。
液压系统具有传动效率高、传动力矩大、动作平稳、反应灵敏等优点,因此在机械制造、航空航天、船舶、石油化工、建筑工程等领域得到了广泛应用。
为了更好地设计和优化液压系统,工程师们常常需要对液压系统进行建模与仿真分析。
AMEsim是一种基于物理的系统级建模和仿真软件,可以用来对复杂的液压系统进行建模与仿真。
它能够快速准确地模拟液压系统的动态特性,并通过仿真分析系统的运行状态、性能和参数变化对系统进行优化。
本文将介绍使用AMEsim对液压系统进行建模与仿真的步骤和方法。
一、液压系统建模1.系统结构设计在进行液压系统建模前,需要根据实际应用场景设计系统的结构和组成。
液压系统通常包括液压源、执行元件、控制元件和辅助元件等部分。
液压源一般由油箱、泵和电动机组成,用于产生液压能。
执行元件包括液压缸、液压马达等,用于产生力和运动。
控制元件包括阀门、液压控制阀等,用于控制液压系统的动作和方向。
辅助元件包括滤油器、冷却器等,用于保护和维护液压系统。
在建模时,需要将这些部分进行合理的组织和连接。
2.建立物理模型在AMEsim中,可以通过图形化界面来建立液压系统的物理模型。
首先需要选择合适的元件模型,并将其拖放到系统工作区中。
可以选择液压缸、液压马达、液压泵、油箱、阀门等元件模型。
然后通过连接线将这些元件连接在一起,形成完整的系统结构。
在建立连接时,需要考虑元件之间的流动方向和控制信号的传递。
3.设定参数和初始条件建立物理模型后,需要对各个元件的参数进行设定。
这些参数包括液压源的功率、泵的流量和压力、执行元件的有效面积和行程、控制阀的开启和关闭时间等。
还需要对系统的初始条件进行设定,如油箱中的油液初始压力和温度等。
完成系统的物理建模后,就可以进行仿真分析。
在AMEsim中,可以通过设置仿真时程和控制信号来对系统进行仿真。
液压系统建模和仿真SimHydraulics

--液压系统建模和仿真SimHydraulics是液压传动和控制系统的建模和仿真工具,扩展了Simulink®的功能。
使用这个工具可以建立起含有液压和机械元件的物理网络模型,可用于跨专业领域系统的建模。
SimHydraulics提供了构成液压系统的元器件模块库,库中也包括了用于构造其它元件的基本元素模块。
SimHydraulics适用于汽车,航空,国防和工业装备等领域中的各种应用,例如自动变速器,舵面操纵系统和重载驱动装置的建模分析。
SimHydraulics同SimMechanics,SimDriveline和SimPowerSystems一同使用,能够支持对复杂机液系统和电液系统的建模,以分析他们相互交联的影响。
主要功能•液压和液压机械系统的物理建模环境•超过75个液压和机械元器件模型,包括泵,阀,蓄能器和管路•基本液压构造元素库,还有基本机械和运算单元•可定制的常用液压流体工作介质SimHydraulics可在Simulink下建立液压系统回路的网络模型,模型表达基于ISO1219流体传动系统标准,并且建立的模型可以同机械和控制器模型相结合。
机械液压和液压系统网络建模使用SimHydraulics可以建立起完整的液压系统模型,过程如同组建一个真实的物理系统。
SimHydraulics使用物理网络方式构建模型:每个建模模块对应真实的液压元器件,诸如油泵,液压马达和控制阀;元件模块之间以代表动力传输管路的线条连接。
这样,就可以通过直接描述物理构成搭建模型,而不是从基本的数学方程做起。
SimHydraulics库提供了75个以上的流体和液压机械元件,包括油泵,油缸,蓄能器,液压管路和一维机构单元,大部分商品化元器件都可以找到对应模型。
SimHydraulics的模型符号符合ISO1219流体动力系统标准,SimHydraulics可以自动从模型原理图综合出描述系统行为特征的方程组。
SimHydraulics得到的是直接使用Simulink的求解器求解的方程组形式,而不是采用同步仿真方法,这样液压系统模型就完全同其它Simulink模型部分集成在一起。
单泵多马达液压行走系统同步方式与动力学研究
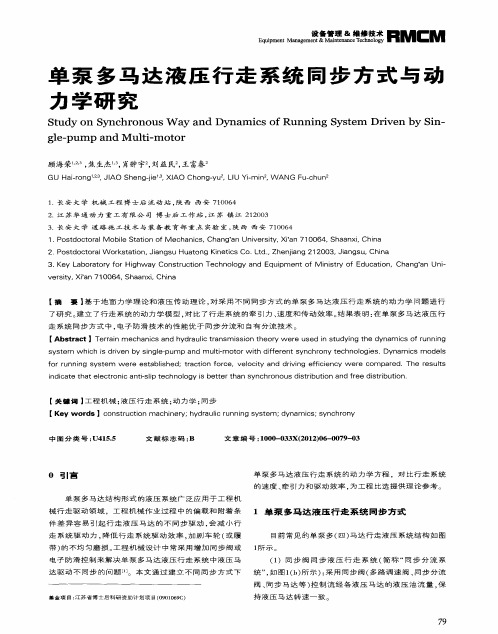
【 键词 】 程 机 械 ; 压行 走 系统 ; 力学 ; 步 关 工 液 动 同 【 e od K yw r s】c n tu t nma hn r; y rui rn igs se ; y a i ; y c rn o srci c ie h da l u nn y tm d n m c s n ho y o y c s
1 .长 安 大 学 机 械 工 程 博 士 后 流 动 站 , 西 西 安 7 0 6 陕 104
2 .江 苏 华 通 动 力 重 工 有 限 公 司 博 士 后 工 作 站 , 苏 镇 江 21 0 3 江 20
3 .长 安 大 学 道 路 施 工 技 术 与 装 备 4- 部 重 点 实 验 室 , 西 西 安 71 0 4 q育 陕 06
设备 管理 & 维 修技术
Eq m e tM a a e e t M an e a c c n l g mp n ng m n & i tn n e Teh oo y
单 泵 多 马 达 液 压 行 走 系 统 同 步 方 式 与 动 力 学 研 究
S ud on ync ono a a n a i s o t y S hr us W y nd Dy m c fRunni ys e i n by S n- ng S t m Drve i
中 图 分 类 号 : 1 . U4 55
液压系统建模与仿真分析教学设计

液压系统建模与仿真分析教学设计引言液压系统是一种广泛应用于机械、工程和设备控制中的动力系统。
它能将液体强制送入管道或设备中,通过压力进行工作和控制,具有输送能力大、能量损失少、工作平稳等优点。
因此,液压系统已成为航空、制造业、汽车工业、生产线等领域的核心技术之一。
本文将介绍一种液压系统建模与仿真分析的教学设计,以提高学生对液压系统的理解和掌握能力。
课程设计课程内容本教学设计主要分为以下三个部分:1.液压系统基本原理和组成部分:包括液体、泵、储油箱、液压马达、液压缸、液压阀门等组成部分的作用和工作原理,以及常见的液压系统组成。
2.液压系统建模:介绍液压系统建模的方法和步骤,如需进行液压系统仿真分析,需要先建立数学模型,然后在仿真软件中进行仿真分析,从而观察液压系统的动态响应、能耗和效率等性能指标。
3.液压系统仿真分析:介绍如何进行液压系统仿真分析并观察系统的动态响应、能耗和效率等性能指标,以及分析仿真结果的意义和价值。
教学方法本课程设计采用如下教学方法:1.理论授课:讲解液压系统的基本原理和组成部分,重点介绍液压系统的建模方法和步骤,以及液压系统仿真分析的方法和意义。
2.实例演示:选取一个简单的液压系统进行建模和仿真分析,通过示范的方式让学生了解具体的建模步骤和仿真过程。
3.实践操作:要求学生在课后自行完成一组液压系统组装和仿真分析,并将仿真结果进行报告、分析和讨论。
教学媒介为了使学生更好地掌握液压系统建模与仿真分析的知识,本课程设计将采用以下教学媒介:1.实物展示:展示液压马达、液压缸等液压系统组成部分,让学生直观了解液压系统的组成和工作原理。
2.仿真软件:使用MATLAB、SimHydraulics等液压系统仿真软件进行实际操作和实验。
同时,远程授课也可以借助在线虚拟仿真实验室或虚拟仿真软件等方式进行。
3.PPT展示:使用PowerPoint等演示工具进行液压系统建模与仿真分析的课程介绍和教学辅助。
基于AMEsim的液压系统建模与仿真

基于AMEsim的液压系统建模与仿真一、引言1. 液压系统建模的基本原理在进行液压系统建模之前,首先需要了解液压系统的基本组成和工作原理。
液压系统由液压液、液压泵、执行元件、阀门等组成,液压液在系统中传递压力和动能,实现各种动作和动作控制。
建模液压系统的关键在于将系统分解为各个子系统,并建立各个子系统之间的相互作用关系和能量传递关系。
2. AMESim建模工具AMESim软件具有直观的界面和强大的建模工具,能够快速实现复杂系统的建模。
通过AMESim的图形化界面,用户可以方便地将液压系统的各个组成部分以及它们之间的相互作用关系用图形化符号表示出来,然后通过参数设置和连接进行建模,建模过程相对比较简单和直观。
在基于AMESim进行液压系统建模时,一般可按照以下步骤进行:(1)系统分析:首先需要对待建模的液压系统进行整体分析,明确系统的工作原理和各个组成部分之间的关系。
(2)建立模型:根据系统分析的结果,利用AMESim的建模工具逐步建立系统的各个组成部分的模型,并通过参数设置和组件连接等方式将各个子系统组合成一个完整的液压系统模型。
(3)参数设置:根据实际系统参数和运行条件,对系统模型中的各种参数进行设置,以确保模型的真实性和准确性。
(4)验证模型:建模完成后,需要对系统模型进行验证,确保系统的动态特性和静态特性符合实际情况。
AMESim软件不仅可以用于建立液压系统的模型,还可以用于进行系统的仿真。
通过AMESim的仿真工具,用户可以模拟系统在不同工况下的性能,包括系统的动态特性、稳态特性和瞬态响应等。
2. 液压系统仿真的内容(1)性能预测:通过仿真模拟系统在不同工况下的性能,包括负载变化、工作速度变化等条件下系统的输出响应和能耗变化情况。
(2)系统优化:利用仿真结果,可以对系统的参数进行优化,以提高系统的性能和效率,减小系统的能耗和噪音等。
(3)系统分析:通过仿真结果,可以对系统的工作特性进行深入分析,包括系统的动态特性、稳态特性、瞬态响应和系统的可靠性等。
工作报告 液压实训报告

液压实训报告液压实训报告实习报告一实习的目的和意义经过四年的大学学习,大四时一个关键的时期,理论与实践的一个过渡。
大四是毕业的最后一个学期,面临着毕业还有一个毕业设计,我的课题是“单斗液压挖掘机液压系统设计”。
我的社会阅历较少尤其是这种大型机械的内部构造,这个学期我有幸在工厂完成了这个设计,通过现场的观察是我知道许多不是课本多能提供到的,做为一名学生,就需要我们有良好的沟通和学习的能力,通过多问多学多去动手,这才是实习的意义。
二实习单位简介我实习的单位在大连,是一家大型化工机械厂大连市旅顺口区佐竹机械厂。
主要生产重型机械,我做的这个课题就是工厂里面的一个项目,挖掘机的回路设计。
企业凭借实力铸品牌,以诚信求发展,采用先进的生产技术,建立完善的质保体系,依托日本、韩国先进液压技术,研制生产适合国情的高配置、低价位、高性价比的优良产品。
三实习的内容和时间三月中旬,我来到工厂开始正式接触这个课题的内容,我由工厂的师傅带领参观了车间的每个工作流程,这是我从来没见过的。
设计液压回路首先要知道内部的构造和用途,先从液压油开始,这是一个关键的所在。
工程机械使用的液压油,主要是抗磨液压油,液力油为液力传动油。
每台设备有其指定标号的用油,这主要考虑系统的工作条件,如液压泵的类型(齿轮泵、柱塞泵、叶片泵)、工作压力、温度、液压元件使用的金属、密封件的性质。
液压系统工作的可靠性及元件的寿命与系统用油的清洁有极密切的关系;另外,为保证油的质量,加注或更换油时须过滤,保持清洁,防止水或异物进入,液压系统维护或更换新的液压元件,也要非常注意清洁。
中、小型液压挖掘机的液压系统有向变量系统转变的明显趋势。
因为变量系统在油泵工作过程中,压力减小时用增大流量来补偿,使液压泵功率保持恒定,亦即装有变量泵的液压挖掘机可经常性地充分利用油泵的最大功率;当外阻力增大时则减少流量(降低速度),使挖掘力成倍增加;采用三回路液压系统,产生三个互不成影响的独立工作运动,实现与回转机构的功率匹配,将第三泵在其他工作运动上接通,成为开式回路第二个独立的快速运动。
典型液压传动系统实例分析
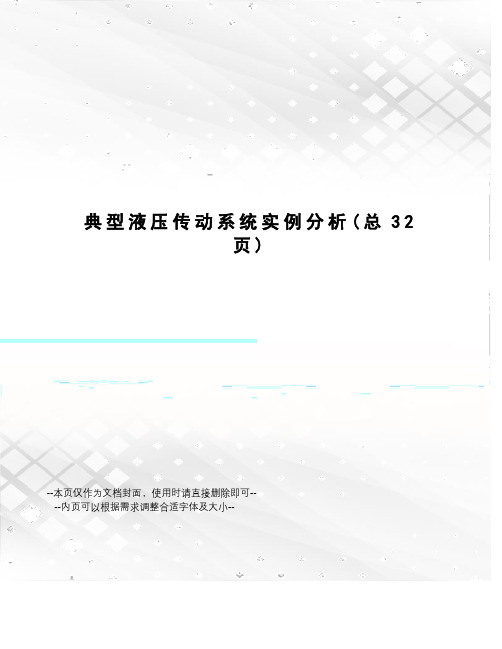
典型液压传动系统实例分析(总32页)--本页仅作为文档封面,使用时请直接删除即可----内页可以根据需求调整合适字体及大小--第四章典型液压传动系统实例分析第一节液压系统的型式及其评价一、液压系统的型式通常可以把液压系统分成以下几种不同的型式。
1.按油液循环方式的不同分按油液循环方式的不同,可将液压系统分为开式系统和闭式系统。
(1)开式系统如图所示,开式系统是指液压泵1从油箱5吸油,通过换向阀2给液压缸3(或液压马达)供油以驱动工作机构,液压缸3(或液压马达)的回油再经换向阀回油箱。
在泵出口处装溢流阀4。
这种系统结构较为简单。
由于系统工作完的油液回油箱,因此可以发挥油箱的散热、沉淀杂质的作用。
但因油液常与空气接触,使空气易于渗入系统,导致工作机构运动的图开式系统不平稳及其它不良后果。
为了保证工作机构运动的平稳性,在系统的回油路上可设置背压阀,这将引起附加的能量损失,使油温升高。
70在开式系统中,采用的液压泵为定量泵或单向变量泵,考虑到泵的自吸能力和避免产生吸空现象,对自吸能力差的液压泵,通常将其工作转速限制在额定转速的75%以内,或增设一个辅助泵进行灌注。
工作机构的换向则借助于换向阀。
换向阀换向时,除了产生液压冲击外,运动部件的惯性能将转变为热能,而使液压油的温度升高。
但由于开式系统结构简单,因此仍为大多数工程机械所采用。
(2)闭式系统如图所示。
在闭式系统中,液压泵的进油管直接与执行元件的回油管相联,工作液体在系统的管路中进行封闭循环。
闭式直系统结构较为紧凑,和空气接触机会较少,空气不易渗入系统,故传动的平稳性好。
工作机构的变速和换向靠调节泵或马达的变量机构实现,避免了在开式系统换向过程中所出现的液压冲击和能量损失。
但闭式系统较开式系统复杂,由于闭式系统工作完的油液不回油箱,油液的散热和过滤的条件较开式系统差。
为了补偿系统中的泄漏,通常需要一个小容量的补油泵进行补油和散热,因此这种系统实际上是一个半闭式系统。
液压挖掘机液压系统的设计要求分析
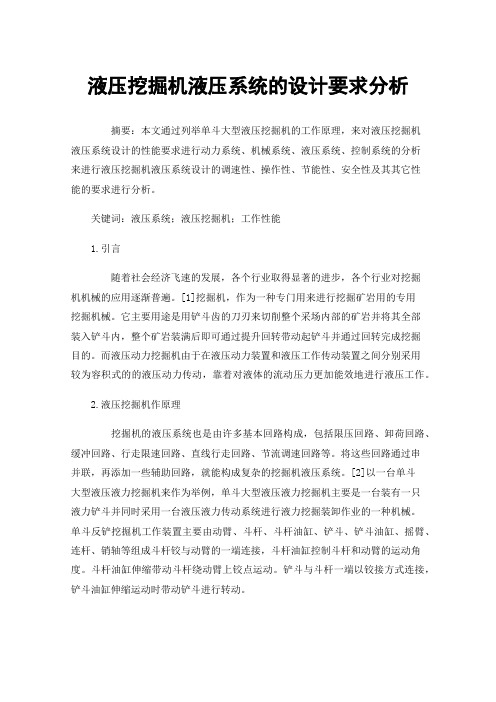
液压挖掘机液压系统的设计要求分析摘要:本文通过列举单斗大型液压挖掘机的工作原理,来对液压挖掘机液压系统设计的性能要求进行动力系统、机械系统、液压系统、控制系统的分析来进行液压挖掘机液压系统设计的调速性、操作性、节能性、安全性及其其它性能的要求进行分析。
关键词:液压系统;液压挖掘机;工作性能1.引言随着社会经济飞速的发展,各个行业取得显著的进步,各个行业对挖掘机机械的应用逐渐普遍。
[1]挖掘机,作为一种专门用来进行挖掘矿岩用的专用挖掘机械。
它主要用途是用铲斗齿的刀刃来切削整个采场内部的矿岩并将其全部装入铲斗内,整个矿岩装满后即可通过提升回转带动起铲斗并通过回转完成挖掘目的。
而液压动力挖掘机由于在液压动力装置和液压工作传动装置之间分别采用较为容积式的的液压动力传动,靠着对液体的流动压力更加能效地进行液压工作。
2.液压挖掘机作原理挖掘机的液压系统也是由许多基本回路构成,包括限压回路、卸荷回路、缓冲回路、行走限速回路、直线行走回路、节流调速回路等。
将这些回路通过串并联,再添加一些辅助回路,就能构成复杂的挖掘机液压系统。
[2]以一台单斗大型液压液力挖掘机来作为举例,单斗大型液压液力挖掘机主要是一台装有一只液力铲斗并同时采用一台液压液力传动系统进行液力挖掘装卸作业的一种机械。
单斗反铲挖掘机工作装置主要由动臂、斗杆、斗杆油缸、铲斗、铲斗油缸、摇臂、连杆、销轴等组成斗杆铰与动臂的一端连接,斗杆油缸控制斗杆和动臂的运动角度。
斗杆油缸伸缩带动斗杆绕动臂上铰点运动。
铲斗与斗杆一端以铰接方式连接,铲斗油缸伸缩运动时带动铲斗进行转动。
液压传动挖掘机系统可以细分为:机械动力系统、机械系统、液压传动系统、控制传动系统。
液压传动挖掘机系统作为一个有机的整体,其机械性能的整体优劣不仅与内部工作传动装置内部机械以及零部件本身性能优劣有关,还与内部液压传动系统、控制器等系统设备性能优劣有关。
(1)动力系统挖掘机负荷倾斜移动工作的主要运行性能物理特点之一也就是由于工作期和环境物理条件由于温度大和季节移动变化大,灰尘以及其他污物经常堆积的比较多,负荷移动强度季节变化大,经常需要进行各种倾斜大和移动大的工作,维护期和运行环境条件差。
《单作用双定子泵变量机构的研究》范文

《单作用双定子泵变量机构的研究》篇一一、引言随着现代工业技术的不断发展,液压传动技术作为重要的动力传输方式,在各个领域得到了广泛的应用。
单作用双定子泵作为液压传动系统中的关键部件,其性能的优劣直接影响到整个系统的运行效率和稳定性。
因此,对单作用双定子泵变量机构的研究具有重要的理论意义和实际应用价值。
本文旨在探讨单作用双定子泵变量机构的工作原理、性能特点及优化方法,为相关领域的研究和应用提供参考。
二、单作用双定子泵的基本原理与结构单作用双定子泵是一种常见的液压泵,其基本原理是利用两个定子之间的容积变化来产生压力差,从而实现液体的吸入和排出。
该泵主要由定子、转子、轴承、密封件等组成。
其中,定子是固定不动的部分,转子则在其内部进行旋转运动。
在单作用双定子泵中,转子的旋转运动会使得液体的流向发生变化,从而产生压力差。
而双定子的设计则能够有效减小泵的体积和重量,提高其工作效率。
此外,该泵还具有结构简单、维护方便等优点,因此在液压传动系统中得到了广泛的应用。
三、单作用双定子泵变量机构的研究单作用双定子泵的变量机构是实现泵的流量和压力调节的关键部分。
通过对变量机构的研究和优化,可以提高泵的适应性和工作效率。
1. 变量机构的工作原理单作用双定子泵的变量机构主要通过改变转子的偏心距或偏心角度来实现流量的调节。
当偏心距或偏心角度增大时,泵的输出流量也会相应增大;反之,则会减小。
此外,通过控制液压系统的压力,还可以实现泵的自动调节,以满足不同工况下的需求。
2. 变量机构的性能特点单作用双定子泵的变量机构具有以下性能特点:(1)流量调节范围广:通过改变转子的偏心距或偏心角度,可以实现大范围的流量调节。
(2)响应速度快:变量机构能够快速响应系统的压力变化,实现流量的实时调节。
(3)节能环保:通过自动调节泵的输出流量和压力,可以降低系统的能耗,减少对环境的污染。
3. 变量机构的优化方法为了进一步提高单作用双定子泵的性能,可以对变量机构进行以下优化:(1)采用先进的控制策略:通过引入先进的控制算法和传感器技术,实现对泵的精确控制,提高其响应速度和稳定性。
《单作用双定子泵变量机构的研究》范文
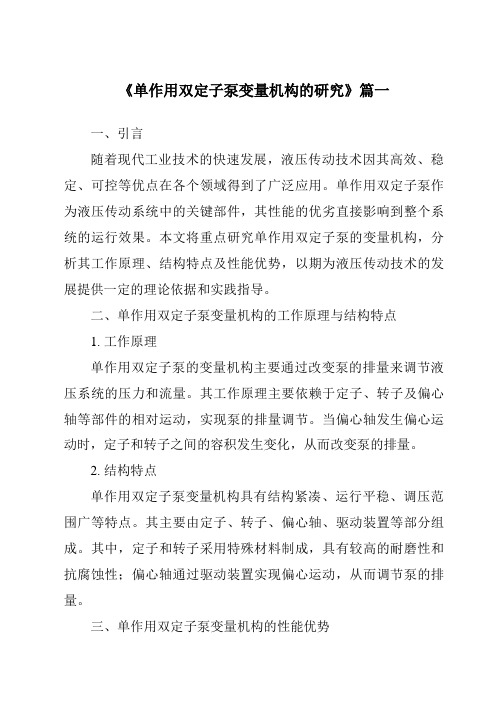
《单作用双定子泵变量机构的研究》篇一一、引言随着现代工业技术的快速发展,液压传动技术因其高效、稳定、可控等优点在各个领域得到了广泛应用。
单作用双定子泵作为液压传动系统中的关键部件,其性能的优劣直接影响到整个系统的运行效果。
本文将重点研究单作用双定子泵的变量机构,分析其工作原理、结构特点及性能优势,以期为液压传动技术的发展提供一定的理论依据和实践指导。
二、单作用双定子泵变量机构的工作原理与结构特点1. 工作原理单作用双定子泵的变量机构主要通过改变泵的排量来调节液压系统的压力和流量。
其工作原理主要依赖于定子、转子及偏心轴等部件的相对运动,实现泵的排量调节。
当偏心轴发生偏心运动时,定子和转子之间的容积发生变化,从而改变泵的排量。
2. 结构特点单作用双定子泵变量机构具有结构紧凑、运行平稳、调压范围广等特点。
其主要由定子、转子、偏心轴、驱动装置等部分组成。
其中,定子和转子采用特殊材料制成,具有较高的耐磨性和抗腐蚀性;偏心轴通过驱动装置实现偏心运动,从而调节泵的排量。
三、单作用双定子泵变量机构的性能优势1. 调压范围广:单作用双定子泵变量机构可通过改变排量来调节液压系统的压力和流量,满足不同工况下的需求。
2. 运行平稳:该机构采用特殊设计,使得泵在运行过程中保持平稳,减少振动和噪音。
3. 结构紧凑:相比传统泵类,单作用双定子泵变量机构的结构更加紧凑,节省了空间。
4. 耐磨、抗腐蚀:定子和转子采用特殊材料制成,具有较高的耐磨性和抗腐蚀性,延长了泵的使用寿命。
四、单作用双定子泵变量机构的应用领域单作用双定子泵变量机构因其优异的性能在各个领域得到了广泛应用。
在工程机械、冶金机械、船舶制造、航空航天等领域,该机构能够提供稳定的压力和流量,保证设备的正常运行。
此外,在高压、大流量、高效率的液压传动系统中,单作用双定子泵变量机构也得到了广泛应用。
五、实验研究与性能分析为了进一步了解单作用双定子泵变量机构的性能,我们进行了大量的实验研究。
《单作用双定子泵变量机构的研究》范文

《单作用双定子泵变量机构的研究》篇一一、引言在流体传动和动力系统中,泵的变量机构作为核心部分,对于系统性能的优化起着至关重要的作用。
近年来,单作用双定子泵因其在高压力、大流量以及高效能方面的突出表现,逐渐成为研究的热点。
本文旨在深入研究单作用双定子泵的变量机构,探索其工作原理及性能特点,以期为泵的优化设计和应用提供理论依据。
二、单作用双定子泵概述单作用双定子泵是一种具有两个定子的泵,其工作原理是通过定子之间的相对运动,实现泵的吸入和排出过程。
相比传统泵,单作用双定子泵具有更高的压力和流量范围,且在运行过程中具有较低的噪音和振动。
三、变量机构的工作原理单作用双定子泵的变量机构是实现泵流量调节的关键部分。
该机构主要通过改变定子之间的相对位置,从而调节泵的吸入和排出量。
具体而言,变量机构通过调整定子的倾斜角度、偏心距等参数,改变泵的排量,以适应不同工况下的流量需求。
四、变量机构的组成与特点单作用双定子泵的变量机构主要由倾斜调整机构、偏心调整机构和锁紧装置等组成。
其中,倾斜调整机构用于改变定子的倾斜角度,偏心调整机构用于调整定子的偏心距。
这些机构通过精确的机械结构和控制系统的配合,实现泵的流量调节。
单作用双定子泵的变量机构具有以下特点:1. 结构紧凑,占用空间小;2. 调节范围广,可适应不同工况;3. 调节精度高,可实现连续、平滑的流量调节;4. 具有良好的自适应性,可根据系统需求自动调整排量。
五、性能分析与实验研究通过对单作用双定子泵变量机构的性能分析,我们发现该机构在高压、大流量工况下表现出色,具有较高的工作效率和较低的能耗。
为了进一步验证其性能,我们进行了实验研究。
实验结果表明,单作用双定子泵的变量机构在调节过程中具有较高的稳定性和可靠性,可实现精确的流量调节。
此外,该机构还具有较好的适应性,可广泛应用于各种流体传动和动力系统中。
六、结论与展望本文对单作用双定子泵的变量机构进行了深入研究,分析了其工作原理、组成特点及性能表现。
《单作用双定子泵变量机构的研究》
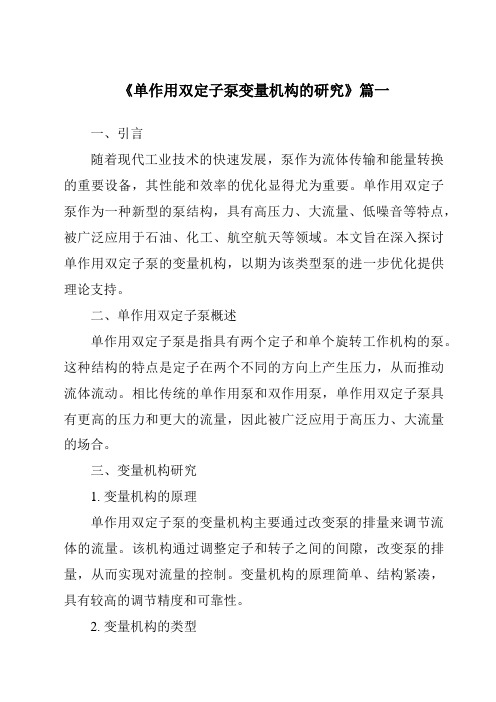
《单作用双定子泵变量机构的研究》篇一一、引言随着现代工业技术的快速发展,泵作为流体传输和能量转换的重要设备,其性能和效率的优化显得尤为重要。
单作用双定子泵作为一种新型的泵结构,具有高压力、大流量、低噪音等特点,被广泛应用于石油、化工、航空航天等领域。
本文旨在深入探讨单作用双定子泵的变量机构,以期为该类型泵的进一步优化提供理论支持。
二、单作用双定子泵概述单作用双定子泵是指具有两个定子和单个旋转工作机构的泵。
这种结构的特点是定子在两个不同的方向上产生压力,从而推动流体流动。
相比传统的单作用泵和双作用泵,单作用双定子泵具有更高的压力和更大的流量,因此被广泛应用于高压力、大流量的场合。
三、变量机构研究1. 变量机构的原理单作用双定子泵的变量机构主要通过改变泵的排量来调节流体的流量。
该机构通过调整定子和转子之间的间隙,改变泵的排量,从而实现对流量的控制。
变量机构的原理简单、结构紧凑,具有较高的调节精度和可靠性。
2. 变量机构的类型根据不同的结构形式,单作用双定子泵的变量机构可分为机械式、液压式和电子式等类型。
机械式变量机构通过手动或机械装置调节定子和转子之间的间隙;液压式变量机构则通过调节控制阀的压力或流量来改变排量;电子式变量机构则通过电子控制系统实现对排量的精确控制。
3. 变量机构的性能分析通过对单作用双定子泵的变量机构进行性能分析,可以发现其具有以下优点:首先,调节范围广,可以满足不同工况下的流量需求;其次,调节精度高,可以实现流量的精确控制;最后,结构紧凑,占用空间小,便于安装和维护。
然而,也存在一些不足,如易受杂质影响、调节过程中存在泄漏等问题。
四、实验研究为了验证单作用双定子泵变量机构的性能,我们进行了实验研究。
实验结果表明,该变量机构具有较高的调节精度和可靠性,能够满足不同工况下的流量需求。
同时,我们也对变量机构中存在的问题进行了分析和改进,以提高其性能和可靠性。
五、结论与展望通过对单作用双定子泵的变量机构进行深入研究,我们可以得出以下结论:首先,该变量机构具有较高的调节精度和可靠性,能够满足不同工况下的流量需求;其次,该机构具有结构紧凑、占用空间小等优点;最后,通过实验研究,我们可以对变量机构中存在的问题进行改进和优化。
单作用双泵双速马达专用换向阀设计与研究

换向阀的结构设计
换向阀的组成: 阀体、阀芯、阀 座、弹簧等
阀芯的设计:根 据不同的工作状 态,设计不同的 阀芯形状和尺寸
阀座的设计: 根据阀芯的形 状和尺寸,设 计相应的阀座 形状和尺寸
弹簧的设计: 根据阀芯和阀 座的配合关系, 设计相应的弹 簧形状和尺寸
阀体的设计:根 据阀芯、阀座和 弹簧的设计,设 计相应的阀体形 状和尺寸
优化方案验证
仿真模型建立:建立单作用双泵双速马达专用换向阀的仿真模型
仿真参数设置:设置仿真参数,如压力、流量、温度等
仿真结果分析:分析仿真结果,如压力波动、流量波动、温度变化等 优化方案验证:验证优化方案的可行性和有效性,如压力波动减小、流量波动减小、温 度变化减小等
Part Five
单作用双泵双速马 达专用换向阀的实
换向阀的材料选择
材料类型:不锈钢、铝合 金、铜合金等
材料性能:耐磨、耐腐蚀、 耐高温、耐冲击等
材料成本:考虑成本效益, 选择合适的材料
材料加工:考虑加工工艺, 选择易于加工的材料
材料应用:根据换向阀的 使用环境和要求,选择合 适的材料
换向阀的控制方式
手动控制:通过 手动操作换向阀,
实现换向功能
电动控制:通过电 动机驱动换向阀,
换向阀的耐 久性测试结 果
换向阀的故 障率测试结 果
换向阀的维 修成本测试 结果
实验结果与仿真结果的对比分析
实验结果:换向阀在不同工况 下的性能表现
仿真结果:换向阀在不同工况 下的仿真性能表现
对比分析:实验结果与仿真结 果的一致性和差异性
结论:实验结果与仿真结果基 本一致,验证了换向阀的设计 与研究结果。
实现换向功能
气动控制:通过 气压驱动换向阀,
机电液压系统仿真与应用实验报告-A14机电
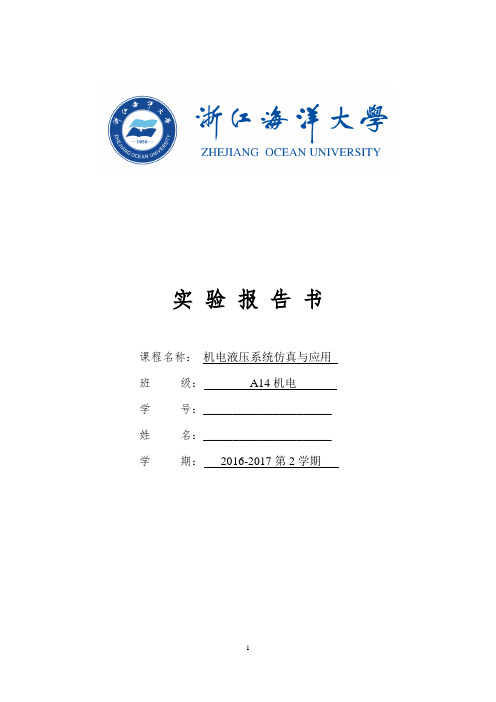
实验报告书
课程名称:机电液压系统仿真与应用班级:A14机电
学号:______________________ 姓名:______________________ 学期:2016-2017第2学期
课程实验项目目录
仿真条件:输入的压力:在10s内,压力从-1bar 升到5bar
四、实验操作步骤
、在子模型模式选择子模型
、在参数模式下设置仿真所需参数、绘制仿真曲线图
四、实验操作步骤
搭建该元件模型的步骤:
、仿真模型草图搭建
)柱塞运动单元仿真模型
表3.1元件参数设置
值
3.2元件参数设置
5)柱塞泵完整仿真模型搭建
2、在子模型模式选择子模型
3、在参数模式下设置仿真所需参数
将1-5个的超级元件的angular displacement分别设置为0、72、144的旋转速度设置为650r/min。
4、运行仿真,选择元件15,绘制端口2的流量。
5、绘制仿真曲线图
五、实验数据处理
搭建该元件模型的步骤:
、仿真模型草图搭建
、在子模型模式选择子模型
、在参数模式下设置仿真所需参数
四、实验操作步骤
3)确认通流面积4)确认可变容积
2、在子模型模式选择子模型
3、在参数模式下设置仿真所需参数、绘制仿真曲线图
四、实验操作步骤
搭建该元件模型的步骤:
四、实验操作步骤
搭建该元件模型的步骤:
31。
- 1、下载文档前请自行甄别文档内容的完整性,平台不提供额外的编辑、内容补充、找答案等附加服务。
- 2、"仅部分预览"的文档,不可在线预览部分如存在完整性等问题,可反馈申请退款(可完整预览的文档不适用该条件!)。
- 3、如文档侵犯您的权益,请联系客服反馈,我们会尽快为您处理(人工客服工作时间:9:00-18:30)。
20T5年9月机床与液压S e p.2015第 43 卷第 T7 期M A C H I N E T O O L3H Y D R A U L I C S Yol.43 N o. 17D O I:10.3969/j. issn. 1001-3881. 2015. 17. 039单泵驱动双液压马达系统的仿真分析李志刚弓海霞2!张印桐屈慧刚2!姜瑛王立权2(1.海洋石油工程股份有限公司,天津300461$2.哈尔滨工程大学机电工程学院,黑龙江哈尔滨150001)摘要:液压系统实际工作时会用一个液压菜同时给两个液压马达供油,如果两个液压马达工作时所受到的负载力不 同,即系统压力不同时,液压油液会优先流经压力较小的马达,造成马达转速不能满足设计要求。
为了解决这一问题,分 别在两个马达支路上各安装一个调速阀,调速阀由定差减压阀和节流阀串联组成,按照仿真数值调整调速阀参数从而解决 由于节流口的压力变化而引起的流量变化,即实现负载力的变化不影响调速阀的工作性能。
最后通过仿真软件A M E S i对 该液压系统进行了建模仿真分析,验证液压系统参数变化与液压回路设计的合理性。
关键词:单菜液压系统;液压马达;调速阀;仿真中图分类号:T H46 文献标志码:A文章编号!T00卜388T(20T5) T7-T57-3Simulation Analysis of Single Pump Driving Double Hydraulic Motors SystemLI Zhi/a n/1,G O N G H a i x i a2,Z H A N G Y i n t o/1,Q U H u i/a n/2,J I A N G Y i n/1,W A N G L i q u a n2(1. Offsliore Oil Engineerin/ C o.,Ltd.,Tianjin 300461,C h i n a;2.School of Mechatronics E n/ineerin/,Har b i n E n/ineerin/ University,Harb in Heilon/ian/ 150001,C h i n a)Abstract:O n some hydraulic pressure system applications in practice,sin/le hydraulic p u m p drives do time. I f load torque of the two hydraulic motors in workin/ was different,that was at the time of different systemp would flowto the motor with the lower pressure in priority,causin/ rotational speed unable to meet desi/n requirement. In order to solve this problem,a hydraulic proportional f l o w c ontrol valve was installed on each branch circuit of the double motors.The f l o w control vvlve was composed of connectin/ in series of throttle vvlve and relief valve of fixed difference.The parameters of the flow control vvlve were adjusted accordin/ to simulation values so as to solve flow chan/es caused by changin/ in pressure at throttlin/ /ly the workin/ performance of fowcontrol valve was not affected by chan/es at the load torque.Finally a system i s established and analyzed with the A M E S i m simulation software to verify parameters chan/es of the sonableness of desi/n of the hydraulic circuit.K e y w o r d s:Hydraulic pressure system with sin/le p u m p; Hydraulic motors;Flow control valve;Si〇前言现代液压技术的发展是国家工业竞争力的重要指 标之一,它在海洋机械、航空航天、农业机械、工业 领域等方面得到广泛应用[1又液压动力与电传动相比,具有功率重量比大、结构简单、传动平稳等优 点[4]。
液压源实际工作时,有时会碰到一个液压栗同 时给两个液压马达供油的工况。
如果两个液压马达负 载相同,则液压马达分别转动实现预定功能,如果两 个液压马达所受负载力不同,则油液会优先流经压力 较小的液压马达,此时马达转速不满足设计要求,文 中研究了-种用调速阀織该问题的方法,最终使其 能够实现预定功能。
1调速阀分析调速阀由定差减压阀和节流阀串联组成,调速阀的进油口压力@经减压阀后变为@,然后经过节流 阀油液压力变为@。
节流阀的进出油口与定差减压 阀相通,即作用在定差减压阀阀芯两端的压力差等于 节流阀进出油口的压力差,作用在阀芯上的弹簧力 !与阀芯的作用面积)的比值即等于压力差。
当定 差减压阀阀芯受力平衡时,即A p=@-@= !/d为定 值,使节流阀的流量不受进出油口压力变化的影响,通过节流阀的流量大小与阀开口面积成正比。
在调定 节流阀的阀口大小后,如果系统由于负载变化而引起 调速阀进油口压力@和出油口压力@变化,通过定 差减压阀的压力补偿,使节流阀进出油口压力差不变,因此保证通过调速阀的流量稳定不变。
下面分 析调速阀的静态特性,首先来分析油液流经定差减压 阀阀口时的流量,用P来表示,则:收稿日期!20T4-07-2T基金项目:国家十二五重大专项资助项目(20T T Z X05027-04-005)作者简介:李志刚(#965$),男,博士研究生,高级工程师,主要研究方向为水下作业装备技术等。
E-irnil:lizhi/ang@ cooec.c o m.c n 。
•158•机床与液压第 43 卷Pi槡^(@-2)⑴式中!K i为定差减压阀阀口流量系数;)?(>)为定差减压阀阀口面积;@为定差减压阀进油口压力;@为定差减压阀出油口压力,即节流阀进油 口压力。
定差减压阀阀芯受力平衡方程为!@)-@)-:(>0+g--) +2'd1N;cos〇(@--2)二 0式中!)为定差减压阀阀芯受力面积;@为节流阀出油口压力;:为定差减压阀的弹簧刚度;4为定差减压阀的预开口长度;>0为定差减压阀的弹簧预压缩量;N为定差减压阀阀口的面积梯度;>为定差减压阀的阀口开度;〇为定差减压阀的阀口射流角。
流经节流阀阀口的流量P为:P= 'A W槡^(@_@#(2)式中:'?为节流阀阀口流量系数;)(R)为节流阀阀口面积。
如果不计调速阀工作过程中的泄漏,根据流体连 续性原理,则流经调速阀的流量为p=p=p。
联合以 上方程,在理论上能够求得调速阀的压力流量特性,但是由于高次方程求解困难,因此由前面式子来求得 节流阀进出油口压力差的表达式来间接分析调速阀的 压力流量特性。
@-3=1[:(>0+4-)-2'iN>osa(@-@)](3)由此可知定差减压阀在检测到外界压力变化后,其阀芯在弹簧作用力下开始移动,进行系统压力补偿以保证节流阀进出油口压力差@-3不变。
定差减 压阀在压力补偿时,由于其阀口开度>变化的同时,除了弹簧力:(>。
+4->)改变外还会引起液动力2'd iN>osa(@-@)的变化,由此可见并不是完全的恒定值,其变化量只是较小而已。
为了减小节流 阀进出油口压力差的波动,主要可以采取以下 3种方式,-是增大定差减压阀的弹簧预压缩量,二 是增大定差减压阀的阀芯受力面积,二是米用液动力 补偿结构来减小液动力对的影响。
通常调速阀 在负载压力变化时所引起的流量变化不超过±5k,即变化相对较小,由压差变化引起的流量变化 在该机具的可接受范围内[5]。
比例调速阀的原理框图如图1所示,图中实线表 示利用弹簧来实现的位移-力反馈,虚线表示用位移 传感器的直接位置反馈。
该图为直接控制式的比例调速阀原理,由于电/机械转换器推力有限,因此直接 控制式的比例调速阀通常用于10 m m以下通径,大 通径的比例调速阀通常采用先导控制的形式。
输入信号厂比例放大器I电/机械转换器调速阀位篇知處)反1Q图1直接控制式比例调速阀原理2液压系统建模仿真当液压系统采用单泵驱动双液压马达进行工作 时,利用比例调速阀来控制各液压马达的流量是一种 抗支路干扰的方法。
我们对该液压系统采用a m e s c 软件进行仿真分析。
分析该液压系统的意义在于,系统在工作时,是由一个液压泵同时给两个液压马达供 油,由于两个液压马达工作时所受到的扭矩不同,即两个马达所受的负载力不同,目此系、统压力不同。
由一个液压泵供油时,油液优先流经压力较小的马 达,马达转速不能满足设计要求。
为了解决这一问 题,分别在两个液压马达系统各安装一个调速阀,调 速阀由定差减压阀和节流阀串联组成,从而解决了节 流阀由于进出油口压力变化而引起的流量变化,即负 载力的变化不影响调速阀的工作性能。
对于中低压液 压系统,通常选定调速阀内的定差减压阀的压力差为 0.5 M Pa。
考虑到泄漏等情况,液压泵供给系统的流 量略大于两个液压马达所需流量总和。
这样在理论上 即能够实现-台液压泵同时带动两个液压马达工作,并且两个马达之间互不影响。
下面通过对液压系统的 仿真分析,验证上述方法的可靠性。
首先利用Hydraulic Component D esi/n设计库来建 立比例调速阀的模型,如图2所示。
在AM ESim草图模式的环境下进行液压系统建模,系统建模时主要用到4个应用库,即Hydraulic 应用库、M echanical应用库、Si/nal/Control应用库和 Hydraulic Component Desi/n设计库。